注塑产品色差控制技术研究
塑料色料的色差量的测定

塑料色料的色差量的测定1.引言1.1 概述概述部分的内容可以如下所示:引言部分是一篇论文的开端,它为读者提供了对论文主题的整体认识和理解。
本文的主题是关于塑料色料的色差量的测定方法。
色差量是表征被测物体颜色差异的重要指标,在塑料色料行业中具有广泛的应用和意义。
塑料色料的色差量测定是指对不同批次或不同生产厂家生产的塑料色料进行颜色比较,从而了解它们之间的色差情况。
色差量的测定在塑料制品的生产过程中尤为重要,因为塑料制品通常需要一致的颜色来满足市场的需求。
如果塑料色料之间存在较大的色差量,可能会导致产品质量的不稳定性,不仅影响产品的外观,还可能影响消费者对产品的接受度。
本文将介绍色差量的定义和基本原理,以及目前常用的塑料色料色差量测定方法。
通过对比不同的测定方法,可以帮助读者了解各个方法的优缺点以及适用的场景。
此外,本文还将通过具体的实例和结果分析来展示不同方法的测定效果和精度,以期为塑料色料行业提供可行且经济有效的色差量测定方法。
最后,本文将对测定结果进行分析,总结各个方法的优缺点,并探讨实际应用中的意义。
通过对测定结果的分析和研究,可以为塑料色料生产企业提供有效的质量控制方法,进而提高产品的一致性和市场竞争力。
通过本文的研究,我们可以更好地理解塑料色料的色差量测定方法,并为塑料色料行业的技术改进和产品质量提升提供参考和借鉴。
1.2 文章结构文章结构部分的内容可以包括以下内容:文章结构的设计是为了使读者能够清晰地了解整篇文章的逻辑结构和内容安排。
本文将按照以下几个部分进行组织:1. 引言:在引言部分,我们将对本文研究的主题进行概述,并说明本文的目的和意义。
2. 正文:正文部分将包括两个主要内容,分别是色差量的定义和塑料色料的色差量测定方法。
2.1 色差量的定义:在本节中,我们将介绍色差量的基本概念和定义。
我们将探讨色差量在颜色测量中的重要性,以及常用的色差量计算公式。
2.2 塑料色料的色差量测定方法:在本节中,我们将介绍测量塑料色料色差量的常用方法和仪器。
关于注塑色差控制技术研究
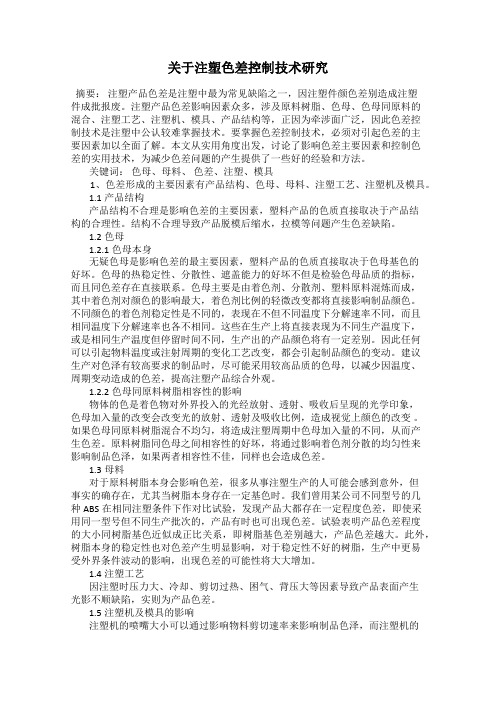
关于注塑色差控制技术研究摘要:注塑产品色差是注塑中最为常见缺陷之一,因注塑件颜色差别造成注塑件成批报废。
注塑产品色差影响因素众多,涉及原料树脂、色母、色母同原料的混合、注塑工艺、注塑机、模具、产品结构等,正因为牵涉面广泛,因此色差控制技术是注塑中公认较难掌握技术。
要掌握色差控制技术,必须对引起色差的主要因素加以全面了解。
本文从实用角度出发,讨论了影响色差主要因素和控制色差的实用技术,为减少色差问题的产生提供了一些好的经验和方法。
关键词:色母、母料、色差、注塑、模具1、色差形成的主要因素有产品结构、色母、母料、注塑工艺、注塑机及模具。
1.1产品结构产品结构不合理是影响色差的主要因素,塑料产品的色质直接取决于产品结构的合理性。
结构不合理导致产品脱模后缩水,拉模等问题产生色差缺陷。
1.2色母1.2.1色母本身无疑色母是影响色差的最主要因素,塑料产品的色质直接取决于色母基色的好坏。
色母的热稳定性、分散性、遮盖能力的好坏不但是检验色母品质的指标,而且同色差存在直接联系。
色母主要是由着色剂、分散剂、塑料原料混炼而成,其中着色剂对颜色的影响最大,着色剂比例的轻微改变都将直接影响制品颜色。
不同颜色的着色剂稳定性是不同的,表现在不但不同温度下分解速率不同,而且相同温度下分解速率也各不相同。
这些在生产上将直接表现为不同生产温度下,或是相同生产温度但停留时间不同,生产出的产品颜色将有一定差别。
因此任何可以引起物料温度或注射周期的变化工艺改变,都会引起制品颜色的变动。
建议生产对色泽有较高要求的制品时,尽可能采用较高品质的色母,以减少因温度、周期变动造成的色差,提高注塑产品综合外观。
1.2.2色母同原料树脂相容性的影响物体的色是着色物对外界投入的光经放射、透射、吸收后呈现的光学印象,色母加入量的改变会改变光的放射、透射及吸收比例,造成视觉上颜色的改变。
如果色母同原料树脂混合不均匀,将造成注塑周期中色母加入量的不同,从而产生色差。
注塑成型色差奇妙调法-叶继岙技术讲坛

叶继岙技术讲坛
注塑成型缺陷:色差:是指产品表面由于温度不同导致 产品阴亮面。产品特别清晰不被接受。
出现位置:开放试热流道熔接线位置,特别亮。 阀试热流道第二组阀口开启位置。(阀口2开启 红色位置 出现色差)。
精髓指点:如何做到料流到 红色位置温度与阀口温度 一致,色差自然解决
色差区
长条色差为例讲解
350mm 350mm
色差区
解决方案:
压力 100 80 50
工艺一
位置 350 200 60 注塑工艺如左图,左图工艺产品颜色是 阀口1颜色最亮到阀口二颜色变暗,当阀口 2开启色差明显。(工艺不合理)
速度 99 60 30
色差区
长条色差为例讲解
350mm 350mm
色差区
速度 60 99 30
谢谢查看叶继岙技术论坛 下次更新最成熟技术
阀2
0 阀1
阀2
保险杠色差
熔接线位置色差非常明显,无法接受。
色差区
长条色差为例讲解
350mm 350mm
色差区
1:材料为PP:阀口1到阀口2距离关系到色差问题,填充距离过远产品前沿温度越低 当阀口二开启时候产品温度不一致导致红色位置色差(当阀口1喷嘴温度为230度填充 到阀口2位置时候温度为220度,但是阀口2出胶温度为230度 这样就会导致红色区域 特别亮的色差)(PP材料长条一般在250-300直径无色差)(阀口1开启填充面积关系 到产品色差,填充面积越大色差越明显)如图当阀口1开启需要填充70%胶料到阀口二 这样阀口1非常吃力,热量与动力损失非常严重。
色差区
解决方案:
压力 45 100 50
距离
位置 350 250 60 左图工艺不变,阀口距离对色差影响非常 明显,阀口距离过远,产品会出现色差, 阀口距离近产品面无色差
注塑产品的色差控制
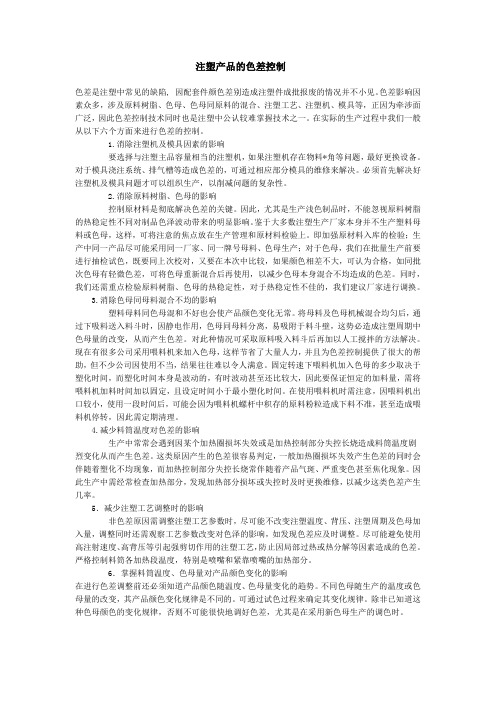
注塑产品的色差控制色差是注塑中常见的缺陷, 因配套件颜色差别造成注塑件成批报废的情况并不小见。
色差影响因素众多,涉及原料树脂、色母、色母同原料的混合、注塑工艺、注塑机、模具等,正因为牵涉面广泛,因此色差控制技术同时也是注塑中公认较难掌握技术之一。
在实际的生产过程中我们一般从以下六个方面来进行色差的控制。
1.消除注塑机及模具因素的影响要选择与注塑主品容量相当的注塑机,如果注塑机存在物料*角等问题,最好更换设备。
对于模具浇注系统、排气槽等造成色差的,可通过相应部分模具的维修来解决。
必须首先解决好注塑机及模具问题才可以组织生产,以削减问题的复杂性。
2.消除原料树脂、色母的影响控制原材料是彻底解决色差的关键。
因此,尤其是生产浅色制品时,不能忽视原料树脂的热稳定性不同对制品色泽波动带来的明显影响。
鉴于大多数注塑生产厂家本身并不生产塑料母料或色母,这样,可将注意的焦点放在生产管理和原材料检验上。
即加强原材料入库的检验;生产中同一产品尽可能采用同一厂家、同一牌号母料、色母生产;对于色母,我们在批量生产前要进行抽检试色,既要同上次校对,又要在本次中比较,如果颜色相差不大,可认为合格,如同批次色母有轻微色差,可将色母重新混合后再使用,以减少色母本身混合不均造成的色差。
同时,我们还需重点检验原料树脂、色母的热稳定性,对于热稳定性不佳的,我们建议厂家进行调换。
3.消除色母同母料混合不均的影响塑料母料同色母混和不好也会使产品颜色变化无常。
将母料及色母机械混合均匀后,通过下吸料送入料斗时,因静电作用,色母同母料分离,易吸附于料斗壁,这势必造成注塑周期中色母量的改变,从而产生色差。
对此种情况可采取原料吸入料斗后再加以人工搅拌的方法解决。
现在有很多公司采用喂料机来加入色母,这样节省了大量人力,并且为色差控制提供了很大的帮助,但不少公司因使用不当,结果往往难以令人满意。
固定转速下喂料机加入色母的多少取决于塑化时间,而塑化时间本身是波动的,有时波动甚至还比较大,因此要保证恒定的加料量,需将喂料机加料时间加以固定,且设定时间小于最小塑化时间。
注塑缺陷原因分析与改善技术2

充填不足的原因有:a、成型条件设定不适当; b、模具的设计与制作不合理; c、成型品的肉厚太薄等所致。
成型条件的对策是: 提高熔料温度(熔胶筒温度)、提高模具温度、增大注射压力
/注射速度及提高熔料的流动性;模具方面可增大主流道或分流道尺 寸或者检讨浇口位置、大小、数目等,设法使节熔融材料容易流动 到型腔的各个角落。为了使成型空间内的气体顺利疏散,可在适当 位置开设排气槽/或排气针。
A、注塑缺陷原因分析及改善方法
三、银纹(料花、水花)
银纹的行成,一般是由于注射起动过快,使熔料及模腔中 的空气无法排出,空气夹混在胶料内,使得制品表面产生银丝 即是所谓的银纹。银纹不但影响外观,而且使塑件的机械强度 降低许多;为避免发生这种缺陷,必须找出原因并予以改善 1、塑料本身含有水份或洞剂
由于塑料在制造过程时曝露于空气中,吸入水气/油剂或者在混料时掺
十三、成品表面无光泽
成型品表面失去材料本来的光泽,形成乳白色层膜,或为 模糊状态(哑色)等均称为表面无光泽。
成型品表面光泽不良,大都是由于模具表面状态不良所致。 模具表面抛光不良或有模垢时,成型品表面当然得不到良好的 光泽;使用过多的离型剂或油脂性离型剂亦是表面光泽不良的原 因。材料吸湿或含有挥发物及异质物混入(污染),亦是造成 制品表面光泽不良的原因之一。
塑胶课
讲师:林勤
认识注塑加工
注塑加工是一门知识面广、技术性和经验性强的行 业,它涉及到塑料性能、注塑模具结构、注塑机功能、 注塑工艺调校、着色技术、水口料回收/利用、品质控 制及生产管理等方面的知识。在注塑生产过程中,会 经常出现一些现象(如:喷嘴流延、漏胶、水口拉丝、 粘模、塑化噪音、螺杆打滑、开模困难等)及产品质 量缺陷(如:缩水、缺胶、披峰、夹水纹、水波纹、 气纹、流纹、料花、开裂、粘模、顶白、拖花、漏胶、 内应力、气泡、色差、盲孔、断柱、翘曲变形等), 如何快速有效地改善这些注塑不良现象,仅凭过去的 经验是不够的,需要全面系统地掌握注塑专业技术知 识和积累丰富的实践经验,学会科学分析问题和处理
塑料件批次色差产生的原因

塑料件批次色差产生的原因
首先,原材料的质量是造成塑料件批次色差的重要因素之一。
不同批次的原料可能存在微小的成分差异,比如颜料、添加剂等,这些微小的差异都有可能导致塑料成品的颜色产生变化。
另外,原料的储存条件和运输过程中的温度、湿度等环境因素也会对原料的质量产生影响,从而导致批次色差的出现。
其次,生产工艺也是产生塑料件批次色差的重要原因之一。
比如,注塑成型过程中的温度、压力、冷却时间等参数的控制不同可能会导致成品色差的出现。
另外,模具的磨损、使用寿命等因素也会对成品的色差产生影响。
此外,环境因素也可能对塑料件批次色差产生影响。
比如,生产车间的温湿度变化、灯光照射等因素都可能对成品的颜色产生影响。
综上所述,塑料件批次色差的产生是一个复杂的问题,需要从原材料、生产工艺和环境因素等多个角度进行全面分析。
只有在全面了解了这些因素的影响之后,才能有效地采取相应的措施来避免或减少塑料件批次色差的产生。
塑料色母粒生产中色差控制的分析与研究

塑料色母粒生产中色差控制的分析与研究摘要:通过对色母粒生产中存在“色差”问题的分析,分别将影响颜色差异的染、颜料选择,颜色色相与颜色配伍规律及染、颜料本身的耐热性、耐光耐候性、坚牢度、分散性、着色力、卫生性等与发生色差的因素举了实例并指出了解决办法。
对色母粒生产加工工艺的高搅、挤出提出了加料顺序、停留时间和挤出温度“宜低不宜高,能成条就行”的见解;对检验两个物体间的色差要求“同一光线下”的比对结论,实践中对减少色母粒色差、稳定色母粒质量有了很大的提高。
关键词:色差色光补色高温氧化塑料产品外观的感觉和印象是决定是否购买该产品的基本条件之一。
而工业产品表面色感、光感与触感这些外观感觉中颜色扮演着一个很重要的角色。
特别是一些由多个零件组成的产品,有时这些零部件还是用不同材料做的,其表面处理也不尽相同,在这种情况下对颜色辨认的要求非常高,同样对于一些色调变化非常细腻的颜色,尤其是灰色调,颜色的辨认难度也相当高。
在塑料制品加工工业中,塑料色母粒作为一种浓缩体着色剂,通常以1:20—100的比例来给塑料制品着色,其色母粒本身的色差控制是关键,它是衡量色母粒制造商的色母粒产品质量水平的首选指标。
在实践中,通常表现在色母粒样品与客户要求色样间的色差,色母粒样品与批量订货产品的色差,色母粒供货批次间色差,基料品种或牌号改变后产生的色差等等。
色母粒使用中发现塑料制品产生色差肯定会是客户不下订单,下了订单后投诉索赔的软肋。
因此面对入世后品质要求提到首位,品牌意识越来越高的今天,我们怎么办?色差控制必须升为每个色母粒生产商的头等大事。
首先,从实用检测产品颜色色差的几种方法来分析和认识色差的标准,然后找出产生色差的原因,再决定解决和避免产生色差的方法。
1. 国内目前普遍采用检测产品颜色色差的方法:1.1 目测检查法:直接用眼睛对两个着色制品的颜色差别作评判。
人眼评色时,一般均取两至三个色调,亮度和色彩饱和度在允差范围内的不同标准色(标准,上差,下差)用灰卡法评价色差。
塑料件色差问题处理方案以及标准建

塑料件色差问题处理方案以及标准建
随着塑料制品在各行各业的普及和应用,塑料件的色差问题也逐渐受到了关注。
塑料件色差问题的解决方案包括以下几个方面: 1. 原材料选择:不同的塑料原料的颜色、透明度和光泽度有所不同,选择适合自己产品的原材料,可以有效避免色差问题的发生。
2. 工艺控制:在生产过程中,要严格控制加工工艺,保证每个工序的操作符合标准,并在关键环节进行检测和调整,以确保产品的色差控制在可接受的范围内。
3. 色差检测:对于关键产品,可以采用色差仪进行检测,及时发现色差问题,以便及时调整工艺和原材料。
除了以上解决方案,制定塑料件色差标准也是非常必要的。
塑料件色差标准应该包括:颜色范围、透明度范围、光泽度范围等内容。
在生产过程中,应该根据标准进行检测,确保产品的色差符合标准。
同时,对于色差超标的产品,也应该有相应的处置措施。
建立完善的塑料件色差标准,不仅可以规范生产过程,还可以提高产品质量,为企业带来更多的经济效益。
- 1 -。
怎样控制注塑产品的色差
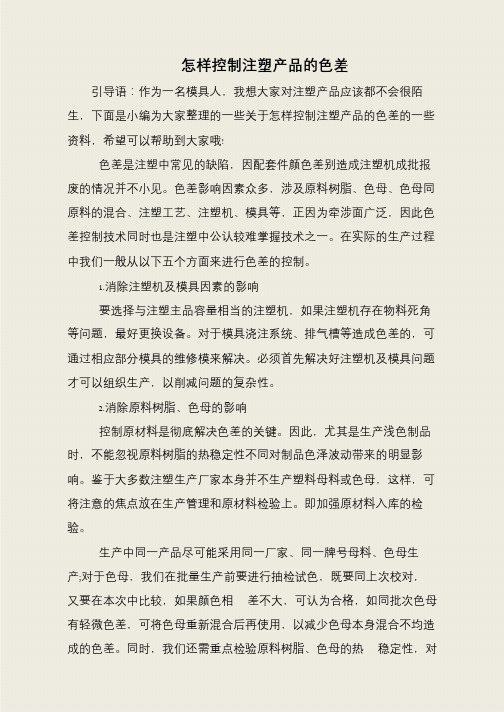
怎样控制注塑产品的色差
引导语:作为一名模具人,我想大家对注塑产品应该都不会很陌生,下面是小编为大家整理的一些关于怎样控制注塑产品的色差的一些资料,希望可以帮助到大家哦!
色差是注塑中常见的缺陷,因配套件颜色差别造成注塑机成批报废的情况并不小见。
色差影响因素众多,涉及原料树脂、色母、色母同原料的混合、注塑工艺、注塑机、模具等,正因为牵涉面广泛,因此色差控制技术同时也是注塑中公认较难掌握技术之一。
在实际的生产过程中我们一般从以下五个方面来进行色差的控制。
1.消除注塑机及模具因素的影响
要选择与注塑主品容量相当的注塑机,如果注塑机存在物料死角等问题,最好更换设备。
对于模具浇注系统、排气槽等造成色差的,可通过相应部分模具的维修模来解决。
必须首先解决好注塑机及模具问题才可以组织生产,以削减问题的复杂性。
2.消除原料树脂、色母的影响
控制原材料是彻底解决色差的关键。
因此,尤其是生产浅色制品时,不能忽视原料树脂的热稳定性不同对制品色泽波动带来的明显影响。
鉴于大多数注塑生产厂家本身并不生产塑料母料或色母,这样,可将注意的焦点放在生产管理和原材料检验上。
即加强原材料入库的检验。
生产中同一产品尽可能采用同一厂家、同一牌号母料、色母生产;对于色母,我们在批量生产前要进行抽检试色,既要同上次校对,又要在本次中比较,如果颜色相差不大,可认为合格,如同批次色母有轻微色差,可将色母重新混合后再使用,以减少色母本身混合不均造成的色差。
同时,我们还需重点检验原料树脂、色母的热稳定性,对。
注塑原材料色差管控

一.目的:规范配色操作,保障色样的标准。
二.范围:本标准适本公司的配色操作。
三.内容:影响色差的因数:A,色母或者色粉的批次或者配方B,填充物批次(填充物颜色会影响产品颜色)C,基料牌号(透光度及颜色)D,配方比例1. 配色程序配色是着色的重要环节之一,配色首选是进行初步配方的设计,然后就是对初步配方进行调整,使之适合于规模生产,且保证塑料制品颜色的均匀一致性。
1.1 初步配方的设计(1)根据塑料制品整体设计的要求,寻找出与标准色样相近似的样品作为参照物。
参照物选择得当与否,直接关系到着色效果的好坏。
为了便于寻找到较佳的着色参照物,平时应多积累、多制备些着色塑料色板或塑料色料以备参照,同时还应把自己选色经验和教训编成相应的着色配方,以供参考。
(2)在无参照物的情况下,应仔细观察分析塑料制品(样品)的颜色色光、色调及亮度等,确定颜色属性(使用五色灯箱进行多光源检查,重点检查基料是否一致,基料不一致会导致调色后有目视差异),确定所用颜色是透明色,还是不透明色,其中是否含有其他特殊颜料(如荧光颜料、金属颜料等),然后进行调色。
(3)从色调、亮度、浓淡度等方面反复比较与标准色样和参照物的差别,在此基础上对参照物的着色剂配方进行修正,拟定出初步配方。
1.2 调整配方按照拟定的初步配方进行实物着色试验,将制得着色实样与标准色样和参照物一起进行比较,进一步调整着色配方。
然后根据调整后的配方再制备实样进行比较,再调整配方,如此反复多次,直到实样色调与标准色样相同或达到最接近标准色样的令人满意的程度为止。
2.标准样板确定2.1试样色板制作完成后留底保存并送与客户确认后签收,客户送样色板若未签回或有差异,需重新打样。
2.2样板要求色差仪提供色差值数据需在签板确认前记录并抄送至客户送样标签上。
2.3签收回样板保存留底以此做为后期生产的标准色板。
2.4后期产的产品需与签收回来的标准样板颜一至。
色差仪色差值标准误差跟据客户要求或小于1.0以下。
注塑色差管控方案

注塑色差管控方案简介在注塑加工过程中,由于材料、设备、工艺等因素的影响,产生的产品色差问题是不可避免的。
色差严重影响了产品的外观质量和市场竞争力。
因此,制定一套科学有效的注塑色差管控方案,对于提高产品质量,满足客户需求具有重要意义。
本文将介绍一套注塑色差管控方案的制定步骤及关键要点,以帮助注塑加工厂有效解决色差问题。
制定步骤步骤一:确认色差等级首先,确定产品色差等级,以满足客户的要求。
常见的色差等级有9级、6级、4级等。
根据产品用途和市场需求,选择适当的色差等级。
步骤二:确定色差测量方法根据产品特点和色差等级要求,确定适合的色差测量方法。
常见的色差测量方法包括人眼观察比较法、色差仪测量法等。
根据具体情况选择合适的方法,并确保测量准确可靠。
步骤三:材料选择根据产品要求和色差控制目标,选择合适的塑料材料。
优质的材料可以提高色差的稳定性和可控性。
同时,需要对材料进行充分的检验和试验,确保材料的质量和稳定性。
步骤四:设备调试保证注塑机的稳定性和一致性是控制色差的关键。
在设备调试阶段,需要进行以下工作:1.确保注塑机温度的稳定性,特别是熔模温度和熔胶温度的控制。
2.检查注塑机的射胶速度和压力曲线,以确保注塑过程的一致性。
3.调整注射速度和保压时间,以获得最佳的注塑效果。
步骤五:工艺参数控制根据产品要求和色差测量结果,确定合适的工艺参数。
在工艺参数控制方面,需要关注以下几个要点:1.注射时间:合理控制注射时间,以避免过早或过晚冷却造成的色差问题。
2.注射速度:控制注射速度,以避免注塑过程中的温度梯度变化过大。
3.保压时间:调整保压时间,以确保产品充分填充,避免缺陷和色差问题。
4.温度控制:严格控制熔胶温度、模具温度等温度参数,以保证注塑过程的稳定性。
步骤六:过程监控与改进建立一套完善的过程监控系统,持续监测注塑过程中的关键参数,并及时采取措施进行调整和改进。
常见的过程监控手段包括SPC(统计过程控制)、CPK(过程能力指数)等。
塑胶色差管理制度

塑胶色差管理制度为了解决塑胶制品颜色差问题,制定一套科学的塑胶色差管理制度尤为重要。
这套制度应包括对原料及产品的颜色控制、颜色检测标准和颜色差管理流程等方面,以确保产品的颜色质量稳定,并在颜色问题出现时能够及时有效的解决。
一、对原料及产品的颜色控制1.原料颜色控制对于塑胶原料的颜色控制,首先要选择质量稳定、颜色一致的原料厂家,并严格按照选定的颜色标准进行采购;接着在接收原料后,要对每批原料进行颜色检测,确保其与标准颜色一致。
同时,要定期对已入库的原料进行重新检验,以确保其颜色与标准一致。
如果发现有色差的情况,要及时与供应商联系,协商解决问题。
对于未能达到标准的原料,要及时退货并追究责任。
2.产品颜色控制在生产过程中,需要设立专门的颜色检测工序,对已生产出的塑胶制品进行颜色检测,并与标准颜色进行对比。
对于颜色与标准相符的产品,要在明显位置做好颜色标记,并定期进行颜色保持检测,以确保产品的颜色与标准一致。
对于发现有色差的产品,要及时追踪问题的原因,并对生产工艺进行调整,以确保今后不再出现此类问题。
二、颜色检测标准为了对原料及产品进行颜色检测,必须要有一套科学的颜色检测标准。
针对不同类型的塑胶制品,需要有相应的颜色检测标准,包括颜色比对表、颜色质量要求及检测方法等内容。
1.颜色比对表颜色比对表是颜色检测的基础,它要以国内外通行的标准色样为基础,制定公司特有的颜色比对表,明确产品的标准颜色,以便于在生产过程中能够及时对产品的颜色进行检测。
2.颜色质量要求对不同类型的塑胶制品,应有相应的颜色质量要求,如对于透明塑胶制品和不透明塑胶制品,其颜色质量要求均不同。
同时,应在颜色质量要求中规定产品的颜色测量方法、仪器及参数等,以确保颜色检测的准确性和科学性。
3.检测方法针对不同材料的检测情况,需要制定相应的检测方法。
对于塑胶制品,常用的检测方法包括视觉检测、仪器检测等。
制定公司特有的检测方法,确保检测的全面和科学。
塑制品加工中产品颜色不均的原因分析与解决

塑制品加工中产品颜色不均的原因分析与解决造成注塑制品颜色不均的主要原因及解决方法如下:(1)着色剂扩散不良,这种情况往往使浇口附近出现花纹。
(2)塑料或着色剂热稳定性差,要稳定制件的色调,一定要严格固定生产条件,特别是料温、料量和生产周期。
(3)对结晶型塑料,尽量使制件各部分的冷却速度一致,对于壁厚差异大的制件,可用着色剂来掩蔽色差,对于壁厚较均匀的制件要固定好料温和模温。
(4)制件的造型和浇口形式,位置对塑料充填情况有影响,使制件的某些局部产生色差,必要时要进行修改。
注塑制品加工中产品白霜的原因分析与解决有些聚苯乙烯类制件,在脱模时,会在靠近分型面的局部表面发现附着一层薄薄的白霜样物质,大多经抛光后能除去。
这些白霜样物质同样会附在型腔表面,这是由于塑料原料中的易挥发物或可溶性低分子量的添加剂受热后形成气态,从塑料熔体释出,进入型腔后被挤迫到靠近有排气作用的分型面附近,沉淀或结晶出来。
这些白霜状的粉末和晶粒粘附在模面上,不单会刮伤下一个脱模制件,次数多了还将影响模面的光洁度。
不溶性填料和着色剂大多与白霜的出现无关。
白霜的解决方法:加强原料的干燥,降低成型温度,加强模具排气,减少再生料的掺加比例等,在出现白霜时,特别要注意经常清洁模面。
注塑制品加工中产品颜色不均的原因分析与解决造成注塑制品颜色不均的主要原因及解决方法如下:(1)着色剂扩散不良,这种情况往往使浇口附近出现花纹。
(2)塑料或着色剂热稳定性差,要稳定制件的色调,一定要严格固定生产条件,特别是料温、料量和生产周期。
(3)对结晶型塑料,尽量使制件各部分的冷却速度一致,对于壁厚差异大的制件,可用着色剂来掩蔽色差,对于壁厚较均匀的制件要固定好料温和模温。
(4)制件的造型和浇口形式,位置对塑料充填情况有影响,使制件的某些局部产生色差,必要时要进行修改。
塑料制品加工中产品出现熔接痕的原因分析与解决熔接痕熔融塑料在型腔中由于遇到嵌件、孔洞、流速不连贯的区域、充模料流中断的区域而以多股形式汇合时以及发生浇口喷射充模时,因不能完全融合而产生线状的熔接痕。
注塑件色差的原因及解决方法
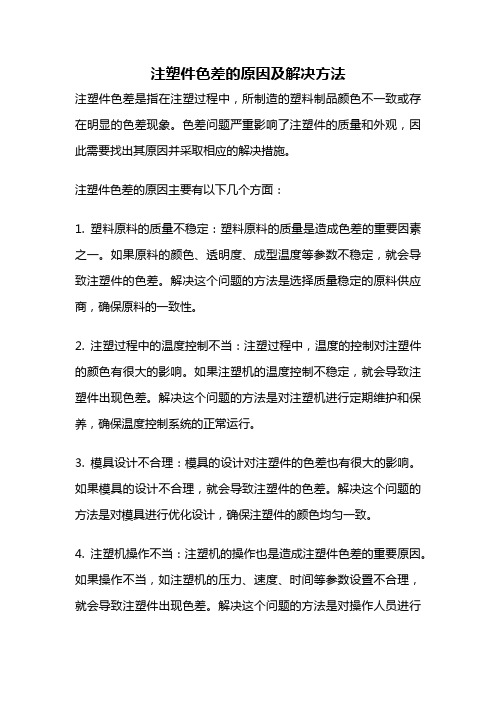
注塑件色差的原因及解决方法注塑件色差是指在注塑过程中,所制造的塑料制品颜色不一致或存在明显的色差现象。
色差问题严重影响了注塑件的质量和外观,因此需要找出其原因并采取相应的解决措施。
注塑件色差的原因主要有以下几个方面:1. 塑料原料的质量不稳定:塑料原料的质量是造成色差的重要因素之一。
如果原料的颜色、透明度、成型温度等参数不稳定,就会导致注塑件的色差。
解决这个问题的方法是选择质量稳定的原料供应商,确保原料的一致性。
2. 注塑过程中的温度控制不当:注塑过程中,温度的控制对注塑件的颜色有很大的影响。
如果注塑机的温度控制不稳定,就会导致注塑件出现色差。
解决这个问题的方法是对注塑机进行定期维护和保养,确保温度控制系统的正常运行。
3. 模具设计不合理:模具的设计对注塑件的色差也有很大的影响。
如果模具的设计不合理,就会导致注塑件的色差。
解决这个问题的方法是对模具进行优化设计,确保注塑件的颜色均匀一致。
4. 注塑机操作不当:注塑机的操作也是造成注塑件色差的重要原因。
如果操作不当,如注塑机的压力、速度、时间等参数设置不合理,就会导致注塑件出现色差。
解决这个问题的方法是对操作人员进行培训,确保他们对注塑机的操作熟练并且合理。
解决注塑件色差问题的方法有以下几点:1. 选择质量稳定的原料供应商:选择质量稳定的原料供应商可以保证原料的一致性,减少色差的发生。
2. 加强对注塑机的维护和保养:定期对注塑机进行维护和保养,确保其温度控制系统的正常运行,减少色差的发生。
3. 优化模具设计:对模具进行优化设计,确保注塑件的颜色均匀一致。
4. 做好注塑机的操作:培训操作人员,确保他们对注塑机的操作熟练并且合理,减少色差的发生。
5. 进行严格的质量控制:建立严格的质量控制体系,对注塑件进行质量检验,及时发现和解决色差问题。
注塑件色差是一个常见的问题,但可以通过选择质量稳定的原料供应商、加强对注塑机的维护和保养、优化模具设计、做好注塑机的操作和进行严格的质量控制来解决。
塑料注塑成形件光泽度与色差管理

塑料注塑成形件光泽度与色差管理一、注塑成型件的光泽度管理1. 光泽度改善类型:1.1 提高塑料制品的表面光泽度,称为增亮改性;1.2 降低塑料制品的表面光泽度,称为消光改性。
相对来说,增亮技术更为主要。
塑料的增亮即提高塑料制品的表面光泽度或光洁度,具体方法除原料的合理选取外,还有添加增亮法、共混增亮法、形态控制增亮法、成型设备光洁度的控制、二次加工增亮法及表面涂层增亮法等。
2. 树脂的选择树脂本身的特征对塑料制品的表面光泽度影响较大,是控制塑料制品表面光泽度的最有效方法。
其对相应塑料制品表面光泽的影响主要取决于如下几个方面:(1) 树脂的品种不同的树脂品种共相应制品的光泽性大不相同,一般认为下列树脂对应制品的光泽性比较好:蜜胺树脂、ABS、PP、HIPS、PA、POM、PMMA及PPO 等,其中蜜胺树脂和ABS两种光泽性最突出。
对同一种树脂而言,合成方法不同,其树脂对应制品光泽度也不相同。
例如:a、对PP而言,不同聚合方法合成品种的光泽度大小如下:无规共聚PP>均聚PP>嵌段共聚PP。
b、对PE 而言,三种不同品种的光泽度大小如下:LDPE>LLDPE>HDPE。
c、对PVC而言,乳液法PVC树脂比悬浮法PVC树脂的光泽度高。
d、对于PS树脂而言,高抗冲聚笨乙烯(HIPS)的光泽度大于通用聚苯乙烯(GPPS)(2) 树脂的特性对同一种树脂而言。
其具体特性不同,光泽度也不相同,在树脂的特性中对光泽度有影响的特性主要有如下几种:a、熔体流动速率(MFR)一般越大,其相应制品的光泽度越大。
b、分子量的影响分子量的影Ⅱ向主要体现在分子量分布宽度上。
分子量分布越宽,其相应制品的光泽度下降。
这主要是因为分子量分布宽,材料的不规整性增大了。
c、吸水率的影响吸水率高的树脂,吸水率对其相应制品的光泽度影响较大。
如分子中含有酯基(一COOR)及酞胺基(一CONH2)的PA、PI、PSF 及PC等,如不进行干燥或干燥不彻底,会在制品表面产出水波纹、气泡、银丝、斑纹、毛疵等,从而使表面光泽度大大下降。
杨老师谈注塑系列3--为什么一个产品不同部位会有色差(12)

杨老师谈注塑系列3--为什么一个产品不同部位会有色差
(12)
专注注塑工厂降本增效改善:杨建宏
注塑生产中经常遇到一个情况,一个产品
的不同部位会有色差,这是怎么回事呢?今天
简单聊下这个问题。
颜色,按照国际CIE标准,分3个维度,A,B,L,其中L值是说亮度,今天就说下L代表的亮度的差异。
同样一个产品是有亮度差异的。
为什么会?说到底,是塑料表面对于光的漫反射的差异程度造成的,这个漫反射的差异是怎么来的呢?答案是塑料制品表面的粗糙度差异。
不同的塑料表面粗糙度=>漫反射的差异=>亮度L值的差异=>色差
如图示,这个产品是我们一个客户的真实的产品,产品的中部红圈的区域与边缘的白色区域明显的色差,红圈区域颜色偏深。
为何会这样?这个产品进胶方式是背部中部顶针潜进胶,进浇口
周围的压力呀,而产品边缘的压力低。
压力大区域的熔融塑料粘附模具表面紧密,这就是我的“杨氏注塑法”常说的“复制力”,胶粘附模具砂纹面紧密,则粗糙,则产品偏暗。
而产品周围则偏亮。
所以同一个产品表面不同区域,出现色差是可以理解的。
空调柜机注塑件色差研究分析研讨
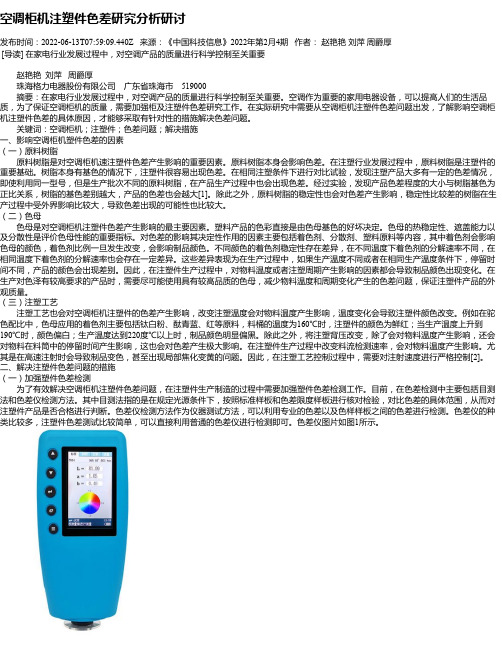
空调柜机注塑件色差研究分析研讨发布时间:2022-06-13T07:59:09.440Z 来源:《中国科技信息》2022年第2月4期作者:赵艳艳刘萍周爵厚[导读] 在家电行业发展过程中,对空调产品的质量进行科学控制至关重要赵艳艳刘萍周爵厚珠海格力电器股份有限公司广东省珠海市 519000摘要:在家电行业发展过程中,对空调产品的质量进行科学控制至关重要。
空调作为重要的家用电器设备,可以提高人们的生活品质,为了保证空调柜机的质量,需要加强柜及注塑件色差研究工作。
在实际研究中需要从空调柜机注塑件色差问题出发,了解影响空调柜机注塑件色差的具体原因,才能够采取有针对性的措施解决色差问题。
关键词:空调柜机;注塑件;色差问题;解决措施一、影响空调柜机塑件色差的因素(一)原料树脂原料树脂是对空调柜机速注塑件色差产生影响的重要因素。
原料树脂本身会影响色差。
在注塑行业发展过程中,原料树脂是注塑件的重要基础。
树脂本身有基色的情况下,注塑件很容易出现色差。
在相同注塑条件下进行对比试验,发现注塑产品大多有一定的色差情况,即使利用同一型号,但是生产批次不同的原料树脂,在产品生产过程中也会出现色差。
经过实验,发现产品色差程度的大小与树脂基色为正比关系,树脂的基色差别越大,产品的色差也会越大[1]。
除此之外,原料树脂的稳定性也会对色差产生影响,稳定性比较差的树脂在生产过程中受外界影响比较大,导致色差出现的可能性也比较大。
(二)色母色母是对空调柜机注塑件色差产生影响的最主要因素。
塑料产品的色彩直接是由色母基色的好坏决定。
色母的热稳定性、遮盖能力以及分散性是评价色母性能的重要指标。
对色差的影响其决定性作用的因素主要包括着色剂、分散剂、塑料原料等内容,其中着色剂会影响色母的颜色,着色剂比例一旦发生改变,会影响制品颜色。
不同颜色的着色剂稳定性存在差异,在不同温度下着色剂的分解速率不同,在相同温度下着色剂的分解速率也会存在一定差异。
这些差异表现为在生产过程中,如果生产温度不同或者在相同生产温度条件下,停留时间不同,产品的颜色会出现差别。
注塑件如何排除色差问题

注塑件如何排除色差问题
注塑件作为一种广泛使用的制造材料,其色彩的均匀性和稳定性是非常重要的。
然而,在生产和质检过程中,注塑件的色彩问题时有发生,这不仅会影响产品的美观度,还会对产品的品质产生不良影响。
那么,如何排除注塑件的色差问题呢?以下是我们的解决方案:首先,我们需要对注塑件的原材料仔细检查。
原材料的不同种类和不同批次之间存在色彩差异,因此我们需要在生产前检查每批原材料,以避免不同批次之间的色差问题。
其次,我们需要在注塑件的制造过程中注意颜料的混合。
颜料的添加量、混合时间、混合顺序等因素都会影响注塑件的色彩均匀性和稳定性,因此我们需要在制造过程中仔细把握这些因素,以确保注塑件的色彩稳定长久。
最后,我们需要对注塑件进行严格的质检。
通过使用严密周密的质检流程,我们可以对注塑件的色彩进行全面检查和修正,确保注塑件颜色的一致性和美观度。
总之,注塑件的色彩均匀性和稳定性是确保产品品质的关键。
我们将不断努力改进我们的工艺和技术,以确保我们为客户提供的注塑件颜色均匀、美观、稳定,打造高品质的注塑件产品。
塑料件色差检验指导书
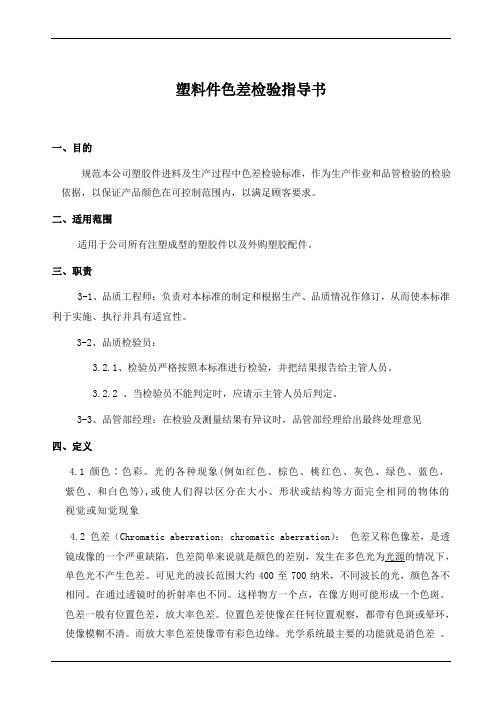
塑料件色差检验指导书一、目的规范本公司塑胶件进料及生产过程中色差检验标准,作为生产作业和品管检验的检验依据,以保证产品颜色在可控制范围内,以满足顾客要求。
二、适用范围适用于公司所有注塑成型的塑胶件以及外购塑胶配件。
三、职责3-1、品质工程师:负责对本标准的制定和根据生产、品质情况作修订,从而使本标准利于实施、执行并具有适宜性。
3-2、品质检验员:3.2.1、检验员严格按照本标准进行检验,并把结果报告给主管人员。
3.2.2 、当检验员不能判定时,应请示主管人员后判定。
3-3、品管部经理:在检验及测量结果有异议时,品管部经理给出最终处理意见四、定义4.1 颜色∶色彩。
光的各种现象(例如红色、棕色、桃红色、灰色、绿色、蓝色,紫色、和白色等),或使人们得以区分在大小、形状或结构等方面完全相同的物体的视觉或知觉现象4.2 色差(Chromatic aberration;chromatic aberration):色差又称色像差,是透镜成像的一个严重缺陷,色差简单来说就是颜色的差别,发生在多色光为光源的情况下,单色光不产生色差。
可见光的波长范围大约400至700纳米,不同波长的光,颜色各不相同。
在通过透镜时的折射率也不同。
这样物方一个点,在像方则可能形成一个色斑。
色差一般有位置色差,放大率色差。
位置色差使像在任何位置观察,都带有色斑或晕环,使像模糊不清。
而放大率色差使像带有彩色边缘。
光学系统最主要的功能就是消色差。
4.3 色差仪:广泛用于塑胶及印刷等行业,主要根据CIE色空间的L A B LCH原理,测量显示出样板和北侧产品的色差△E以及△l a b值。
4.4 色差单位五、工作流程5.1、检验条件5.1.1、在自然光或D65光源箱,目视检查需在高度在 1.5米以内条件下检查。
5.1.2、观察距离:30cm左右(使用仪器时不受距离限制)5.1.3、观察位置:被测面与水平呈45度角,观测时上下左右转动15度。
5.1.4、检测数量:注塑生产以及来料时至少检验5PCS,注塑每2小时可目视观察,如感觉有色差可用色差仪进行测量,最终结果以目视为准5.2、容差值设定5.2.1、设置容差范围时需考虑一下所测的颜色A)白色和灰色银色这样饱和度低的颜色,色差很容易被察觉B)在亮度(△L*)上的差异不易被察觉,但是在色度(△A*,△B*)上的差异就很容易被察觉C)对于鲜艳的颜色,即饱和度高的颜色,颜色上的变化不容易被察觉5.2.2 颜色标准偏差范围六、仪器操作(色差计作业标准)仪器操作可参照《色差计作业指导书》注意事项:1、即使测量的结果完全符合标准要求的偏差范围,也需要对产品进行目视评价2、当测量结果与目视结果不一致时,以目视结果作为最终评价3、在未做明确规定下所有产品颜色外观均以客户要求为准。
- 1、下载文档前请自行甄别文档内容的完整性,平台不提供额外的编辑、内容补充、找答案等附加服务。
- 2、"仅部分预览"的文档,不可在线预览部分如存在完整性等问题,可反馈申请退款(可完整预览的文档不适用该条件!)。
- 3、如文档侵犯您的权益,请联系客服反馈,我们会尽快为您处理(人工客服工作时间:9:00-18:30)。
收稿日期:2002-08-26。
作者简介:张远斌,男,合肥工业大学材料学院材料加工工程专业研究生,本科毕业后曾在荣事达橡塑有限公司从事注塑工作多年。
注塑产品色差控制技术研究张远斌 董定福 张君(合肥工业大学,230009) 摘要:色差是注塑中最常见缺陷,因其牵涉因素众多,十分难以掌握。
本文从实用角度出发,讨论了影响色差主要因素和控制色差的实用技术,为减少色差问题的产生提供了一些好的经验和方法。
关键词: 色差 色母 母料 注塑 温度 压力 色差是注塑中常见缺陷之一,因配套件颜色差别造成注塑件成批报废的情况并不少见。
色差影响因素众多,涉及原料树脂、色母、色母同原料的混合、注塑工艺、注塑机、模具等,正因为牵涉面广泛,因此色差控制技术同时也是注塑中公认较难掌握技术之一[1]。
要掌握色差控制技术,必须对引起色差的主要因素加以全面了解。
1 影响色差的主要因素1.1 原料树脂的影响对于原料树脂本身会影响色差,很多从事注塑生产的人可能会感到意外,但事实的确存在,尤其当树脂本身存在一定基色时[2]。
我们曾用某公司不同型号的几种ABS 在相同注塑条件下作对比试验,发现产品大都存在一定程度色差,即使采用同一型号但不同生产批次的,产品有时也可出现色差。
试验表明产品色差程度的大小同树脂基色近似成正比关系,即树脂基色差别越大,产品色差越大。
此外,树脂本身的稳定性也对色差产生明显影响,对于稳定性不好的树脂,生产中更易受外界条件波动的影响,出现色差的可能性将大大增加。
1.2 色母的影响无疑色母是影响色差的最主要因素,塑料产品的色质直接取决于色母基色的好坏。
色母的热稳定性、分散性、遮盖能力的好坏不但是检验色母品质的指标,而且同色差存在直接联系。
色母主要是由着色剂、分散剂、塑料原料混炼而成,其中着色剂对颜色的影响最大,着色剂比例的轻微改变都将直接影响制品颜色。
不同颜色的着色剂稳定性是不同的,表现在不但不同温度下分解速率不同,而且相同温度下分解速率也各不相同[3]。
这些在生产上将直接表现为不同生产温度下,或是相同生产温度但停留时间不同,生产出的产品颜色将有一定差别。
因此任何可以引起物料温度或注射周期的变化工艺改变,都会引起制品颜色的变动。
建议生产对色泽有较高要求的制品时,尽可能采用较高品质的色母,以减少因温度、周期变动造成的色差,提高注塑产品综合外观。
1.3 色母同原料树脂相容性的影响物体的色是着色物对外界投入的光经放射、透射、吸收后呈现的光学印象,色母加入量的改变会改变光的放射、透射及吸收比例,造成视觉上颜色的改变[4]。
如果色母同原料树脂混合不均匀,将造成注塑周期中色母加入量的不同,从而产生色差。
原料树脂同色母之间相容性的好坏,将通过影响着色剂分散的均匀性来影响制品色泽,如果两者相容性不佳,同样也会造成色差。
1.4 注塑工艺的影响改变注塑温度可直接影响物料温度从而引起制品颜色改变,以驼色PP 色母为例(着色剂主要有钛白粉、酞青蓝、红等),料筒温度160℃时注塑制品颜色明显偏红,温度上升至190℃时制品颜色偏白,当料筒温度上升至220℃以上时,制品颜色明显偏黑。
改变注塑背压不但可以直接影响物料温度,而且还对物料在料筒中的停留时间产生影响,因此会对色差影响更大。
注射速度可通过改变料流剪切速率来影响物料温度,特别是高速注射时,有时会使制品变色甚至局部焦化变黄。
但一般来说中低注射速度对制品颜色产生的影响较小。
1.5 注塑机及模具的影响注塑机的喷嘴大小可以通过影响物料剪切速率现 代 塑 料 加 工 应 用 第15卷第2期 Modern Plastics Processing and Applications 2003年4月 来影响制品色泽,而注塑机的物料死角不但对制品色泽有影响,而且会造成诸如气斑、焦化等现象。
此外,在选择注塑机时需注意注塑机容量和制品重量相适应,过裕或过紧都会引起生产制品颜色不稳定。
模具流道及浇口如果过小,将会产生有害的强剪切作用而使塑料变色,产生局部色差,特别是对那些热敏感性极高的塑料如PVC等;如果浇口过宽,则紊流效果差,温度提升不高,有可能将不均匀色带带入模腔,同样会产生色差。
模具排气不良时,塑料被绝热压缩,在高温高压下与氧剧烈反映,也会造成局部变色。
1.6 库存时间及其他因素的影响塑料制品成型后,其内部高分子材料仍然进行着复杂的物理、化学反应,虽然过程缓慢,但不可避免会使制品颜色发生改变。
对于配套件(如洗衣机的大小盖板等),如果库存时间间隔过长,产品装配时可能会发生因配套件颜色差别较大而造成成批产品报废。
为减少此类情况的发生,除了在装配中应尽可能选用生产时间较相近的配套件组装外,安排生产计划时要充分考虑到库存时间对制品色泽的影响。
影响色差的因素还有很多,如原料中的杂质(水分、屑料等)、添加剂等,这些虽然不是主要影响因素,但也需适当注意。
2 色差的控制2.1 消除注塑机及模具因素的影响要选择与注塑制品容量相当的注塑机,如果注塑机存在物料死角等问题,最好更换设备。
对于模具浇注系统、排气槽等问题造成色差的,可通过维修模具相应部分来解决。
必须首先解决注塑机及模具问题才可以组织生产,以降低问题的复杂性。
2.2 消除原料树脂、色母的影响控制原材料是彻底解决色差问题的关键。
不能忽视原料树脂的热稳定性好坏对制品色泽波动带来的明显影响,尤其是生产浅色制品时。
鉴于大多数注塑生产厂家本身并不生产塑料母料或色母,可将注意重点放在生产管理和原材料检验上,即加强原材料入库的检验;生产中同一产品尽可能采用同一厂家、同一牌号母料、色母生产;对于色母,在批量生产前要进行抽检试色,既要同上次对比,又要在本次中对比,如果颜色相差不大,可认为合格,对同批次色母如有轻微色差,可将色母重新混合后再使用,以减少色母本身混合不均造成的色差。
需重点检验原料树脂、色母的热稳定性,对于热稳定性不佳的,建议厂家更换。
2.3 消除色母同母料混合不均的影响塑料母料同色母混和不好也会使产品颜色变化无常。
采用将母料及色母机械混合均匀后通过下吸料送入料斗时,因静电作用,色母同母料分离,易吸附于料斗壁,这势必造成注塑周期中色母量的改变,从而产生色差。
对此种情况可采取原料吸入料斗后再加以人工搅拌的方法解决。
现在有很多公司采用喂料机来加入色母,节省了大量人力,并且对色差控制提供了很大的帮助,但不少公司因使用不当,结果往往难以满意。
固定转速下喂料机加入色母的多少取决于塑化时间,而塑化时间本身是波动的,有时甚至波动还比较大,因此要保证恒定的加料量,需将喂料机加料时间加以固定,且设定时间小于最小塑化时间。
使用喂料机时需注意,因喂料机出口较小,使用一段时间后,可能会因为喂料机螺杆中积存的原料粉粒造成下料不准,甚至喂料机停转,因此需定期清理。
2.4 减少料筒温度对色差的影响生产中常常会遇到因某个加热圈损坏失效或是加热控制部分失控长烧造成料筒温度剧烈变化从而产生色差。
这类原因产生的色差很容易判定,一般加热圈损坏失效产生色差的同时会伴随着塑化不均现象,而加热控制部分失控长烧常伴随着产品气斑、严重变色甚至焦化现象。
因此生产中需经常检查加热部分,发现加热部分损坏或失控时及时更换维修,以减少这类色差产生几率。
2.5 减少注塑工艺调整时的影响非色差原因需调整注塑工艺参数时,尽可能不改变注塑温度、背压、注塑周期及色母加入量,调整同时还需观察工艺参数改变对色泽的影响,如发现色差应及时调整。
尽可能避免使用高注射速度、高背压等引起强剪切作用的注塑工艺,防止因局部过热或热分解等因素造成色差。
严格控制料筒各加热段温度,特别是喷嘴和紧靠喷嘴的加热部分。
2.6 掌握料筒温度、色母量对产品颜色变化的影响在进行色差调整前还必须知道产品颜色随温度、色母量变化的趋势。
不同色母随生产的温度或色母量的改变,其产品颜色变化规律是不同的。
可通过试色过程来确定其变化规律。
除非已知道这种色母颜色的变化规律,否则不可能很快地调好色差,尤其是在采用新色母生产调色时。
・41・ 现 代 塑 料 加 工 应 用 第15卷第2期 3 色差调整因生产前已排除原料、注塑机、模具等因素,如生产中发现色差,大部分情况下只需判断是色母同原料树脂混合问题,还是注塑温度问题,是混合问题则解决混合问题,是温度问题则可通过改变温度或背压等来调整。
在知道颜色变化趋势的情况下,这是极其容易做到的。
参 考 文 献1 钟志雄.塑料注射成型技术(修订本).广州:广东科技出版社.1997.472 段予忠,张明连1塑料母料生产及应用技术1北京:中国轻工业出版社,1999.55,1413 吴增熙1塑料制品生产工艺手册1北京:化学工业出版社,2000.824 刘敏江1塑料加工技术大全1北京:中国轻工业出版社,2001.19THE CONTROL METH OD RESEARCH ABOUT INJECTIONPROD UCT CHROMATIC DIFFERENCEZhang Yuanbin Dong Dingfu Zhang J un(Hefei University of Technology)ABSTRACTChromatic difference is the most common defect in injection,and because of lot of affecting factors being mastered difficutly.This article discusses the main factors that affect chromatic difference and introduces the mehods to minimize chromatic difference and provides somes good experiences and methods to reduce chromatic differenceK eyw ords:chromatic difference;color masterbatch;masterbatch;injection temperature;pressure 扬子石化开发成功PP扩容技术扬子石化塑料厂在对引进的日本三井油化PP装置进行消化、吸收的基础上,投资不到0.6亿元,研究开发出成套的釜式本体连续PP扩容技术,使装置的生产能力由140kt/a 扩大到220kt/a,装置运行稳定,周期延长,且能耗、物耗普通下降,一年产出的经济效益可达1.75亿元。
扬子石化开发成功通用型透明PP 扬子石化研究院紧跟市场,经成功开发出高品质的透明PP产品后,又成功开发出低成本、市场前景看好的通用型透明PP产品。
该产品以通用料为原料,适应性强,可广泛应用于塑料饮料瓶、包装盒等方面,其耐热性优于目前使用的聚酯产品。