科技有限公司生产制程管理程序
生产制程

1、目的
1.1对过程中影响产品品质的各个因素进行控制,确保产品品质满足规定的要求。
2、概述
2.1 本程序文件适用于生产过程控制及适当环境下生产。
2.2 生产过程包括装配、注塑、车缝及五金加工。
3、职责
3.1PC部负责有效安排生产计划,确保资源的充分利用,以最低的成本按时完成生产,
确保货期的准时达成。
3.2生产部通过有效管理,负责确保全部生产操作符合规定之作业要求,以保证品质的
制造过程,同时达到生产计划的有效执行和要求。
3.3PE部负责制定[工程流程图]、[检查指导书]、[作业指导书]及必要时提供技术支援
和有效之工夹具,以确保生产效率的提高和品质问题的减少。
4、程序
4.1当PC部收到[生产通知单]后,即作合同评审(COP3.1)。
4.2若能通过评审的[生产通知单],有关人员需每周制定或更新一份[生产计划]/ [加工计
划](加工车间用)交PC负责人确认后,发出给有关使用部门(COP3.1)。
4.3生产部收到[生产计划]/[加工计划]后,应考虑是否有能力按生产计划生产,如以下
几种因素:
A.物料的实际状况。
B.人员的满足状况。
C.PD交货期的缓急状况。
D.机器、工夹具的准备状况。
4.4如生产部无法满足以上要求时,则由PC提出并作以下处理:
A.在满足客户要求的前提下,由PC变更生产计划。
B.如不能满足客户要求,通知销售支援部与客户进行沟通修改订单的要求(方法
参照[合同评审程序])。
4.5当生产之前准备资源满足后,可安排有效之生产。
4.6生产部依据[生产计划]和[物料需求单]中“实际用量”栏之数量发出[领料单],将[领
工厂生产管理流程及制度

工厂生产管理流程及制度
一、生产计划编制与发布
1. 生产计划编制:根据市场需求、销售订单及库存情况,生产管理部门制定生产计划,确定生产任务和生产周期。
2. 生产计划发布:将生产计划发布给相关部门,包括生产车间、采购部门和物流部门等,确保各部门了解生产计划,做好准备。
二、原材料采购与供应
1. 供应商选择与评估:采购部门根据工厂的原材料需求,选择合格的供应商,并定期进行供应商的评估,以确保原材料质量和供应的可靠性。
2. 订单下达与跟踪:采购部门向供应商下达订单,并及时跟踪订单进展,确保按时供货,以避免原材料短缺导致生产延误或停产。
三、生产执行与监控
1. 车间生产安排:生产管理部门根据生产计划和订单情况,合理安排车间生产任务,确保生产效率和质量。
2. 生产进度监控:生产管理部门监控车间生产进度,及时排查和解决生产过程中的问题,确保生产任务按时完成。
3. 生产质量控制:质量管理部门对生产过程进行质量控制,确保产品符合质量标准,减少不良品率。
4. 及时反馈与协调:各部门之间及时沟通、反馈和协调工作,确保生产进程顺利进行。
四、生产物流与仓储管理
1. 物流计划与安排:物流部门根据生产计划和订单情况,制定物流计划,包括运输路线、运输方式等,确保产品在正确的时间送达目的地。
2. 仓储管理:仓储部门负责对生产出来的产品进行妥善的仓储管理,包括货物分类、存储条件控制及库存管理等,确保产品安全、便捷地储存和交付。
3. 物流信息管理:物流部门及时更新物流信息系统,跟踪货物运输状态,确保及时了解物流动态,提供准确的物流信息。
SOP与SIP
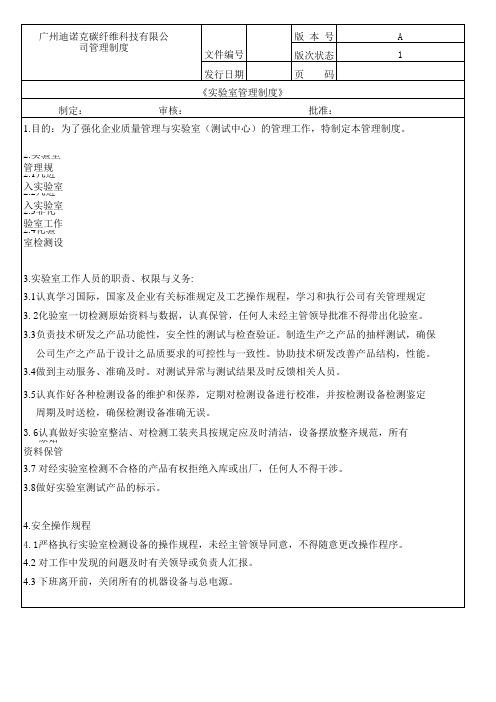
发行日期生产步骤
生产过程生产作业方法工序参数生产治具技术文件/表单无 1.领料数与实际发料是否一致《领料单》外包装透明袋是2-1取回的纱料轻放在室内,拿去纸箱把纱料放至
否完好,若有破在解冻区铁架上解冻(解冻时间为24小时以上)
损用透明胶带补好或更换包装。3-1将已解冻的纱料放至在划纱台面上
定量尺寸一美工刀 1.角度,尺寸符《制造指令单》3-2按照划料单上的规格,尺寸,数量进行划料
般为长2M 直尺3-3划纱时依据模板进行角度定位裁纱模板》的要求
模板 2.纱料表面无斑
无马线,扭曲,破
损等不良状况。4-1撕掉织板表面薄膜
常规角度有角度模板 1.不可以出现皱《结构图》
4-2按照不同角度,尺寸进行叠纱
20°/30°/45°直尺褶,气泡等状况铅笔生产日期标示清楚。 2.对折处无间隙美工刀 3.产品有无标示记号笔无标示立即核对标示区分。合《制造指令单离型纸背面的左下角。每裁纱必须保留此标示,直到此张全部用完。记号笔例:T700SC/250G/30°/1划纱
叠纱
材料解冻 1.解冻时不能损坏1.注意重叠面的2010.12.06统一标示于纱
作业指导管理文件文件编号版 本 号版次状态页 码1/2
《裁纱工序作业指导书》
制定: 审核: 批准:工序作业要点工序自检要点或打开密封袋2.划纱不可歪斜23
1.注意尺寸,角度3.纱料边缘与模板线槽
对齐其它物品取料1-1依生管派工由仓库取出所需纱料
24~48H 1.不能沾水和不能夹带4 2.角度,位置,规格,型号
生产生产过程生产作业方法
工序参数生产治具技术文件/表单5-1把已叠好的纱料放入滚压机中进行滚压
产品外协加工操作规范及流程
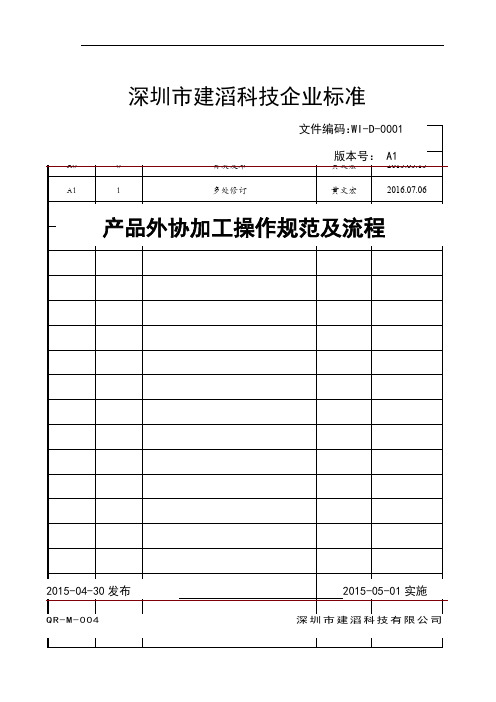
一.目的:
保证本公司外协生产的成品及半成品加工质量,并确保本公司产品质量及企业信誉。同时为指导、规范公司外协加工行为,使外协生产有序、顺利进行,确保外协加工厂的生产过程能够满足本公司对成品质量的要求,特制订本标准。
二.适用范围:
本标准规定了建滔科技有限公司产品、半成品外协加工生产全过程控制的基本要求,主要包括:外协厂供应商资格审核、技术资料准备、首件确认、生产制程控制、包装出货要求、异常处理、制程优化、质量考核等基本要求。建滔科技外发生产的执行部门必须遵照执行。
三.基本流程:
1.外协加工厂审查
1.1 PMC根据订单和公司内部产能评估,确认外发生产的需求,向供应链提出申请,确认、引进外发协作生产厂家。
1.2 供应链牵头,品质部、生产部、业务部参与对协作厂家的实地审查,确认其质量保证体系及设备、现场、人员对产能、品质的保证能力。
1.3 参与部门的相关人员填写《外协生产厂家考察表》,审核合格通过后交PMC 备案执行外发。
1.4 供应链负责与协作厂家签订《外协生产质量及交期保证协议书》及相关服务价格等业务往来合同。
2.外协生产准备事宜
2.1 PMC按BOM备齐外发产品的全部物料。同时沟通辅料是否由我公司提供,如果协作厂家自备,辅料的品质是否符合要求:如是否为无铅工艺、是否客户指定的辅料品牌等。
2.2 技术资料的准备和提供。技术中心负责提供生产技术文件及BOM,工程部提供作业指导书,一并交付PMC提交外协加工厂。
2.3 工装、治具及特殊设备及仪器的准备。工程部与外协加工厂沟通,负责准备缺少工装、夹具及设备等,并通过PMC交付给外协加工厂。
生产设备管理制度相关管制程序样板
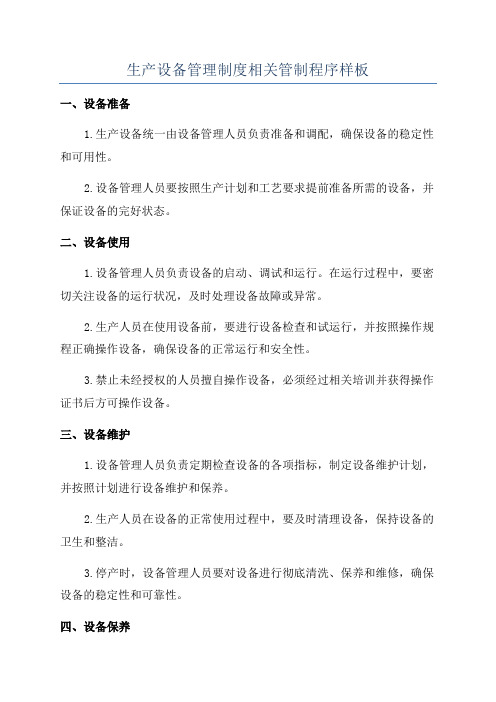
生产设备管理制度相关管制程序样板
一、设备准备
1.生产设备统一由设备管理人员负责准备和调配,确保设备的稳定性和可用性。
2.设备管理人员要按照生产计划和工艺要求提前准备所需的设备,并保证设备的完好状态。
二、设备使用
1.设备管理人员负责设备的启动、调试和运行。在运行过程中,要密切关注设备的运行状况,及时处理设备故障或异常。
2.生产人员在使用设备前,要进行设备检查和试运行,并按照操作规程正确操作设备,确保设备的正常运行和安全性。
3.禁止未经授权的人员擅自操作设备,必须经过相关培训并获得操作证书后方可操作设备。
三、设备维护
1.设备管理人员负责定期检查设备的各项指标,制定设备维护计划,并按照计划进行设备维护和保养。
2.生产人员在设备的正常使用过程中,要及时清理设备,保持设备的卫生和整洁。
3.停产时,设备管理人员要对设备进行彻底清洗、保养和维修,确保设备的稳定性和可靠性。
四、设备保养
1.设备管理人员要制定设备保养计划,并按照计划进行设备保养工作,包括设备的清洁、润滑、调整和更换磨损部件等。
2.设备保养时,要使用合适的工具和润滑剂,严禁使用不符合要求的
工具和材料,以免对设备造成损坏或污染。
3.设备保养完毕后,要及时记录设备保养情况,并进行设备功能测试,确保设备的正常运行。
五、设备报废
1.设备管理人员要定期对设备进行评估和检测,根据设备的技术状况
和经济效益,制定设备报废标准和程序。
2.设备达到报废标准时,设备管理人员要及时报废设备,并按照相关
规定进行设备的清理和处理。
3.报废设备的处理应符合环保要求,并进行相应的安全措施,以防止
P17-东莞塑胶制品有限公司-生产制程管理程序
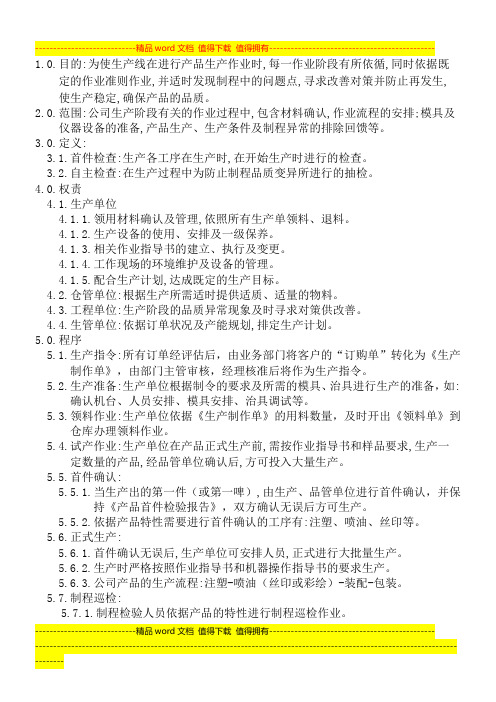
1.0.目的:为使生产线在进行产品生产作业时,每一作业阶段有所依循,同时依据既
定的作业准则作业,并适时发现制程中的问题点,寻求改善对策并防止再发生,使生产稳定,确保产品的品质。
2.0.范围:公司生产阶段有关的作业过程中,包含材料确认,作业流程的安排;模具及
仪器设备的准备,产品生产、生产条件及制程异常的排除回馈等。
3.0.定义:
3.1.首件检查:生产各工序在生产时,在开始生产时进行的检查。
3.2.自主检查:在生产过程中为防止制程品质变异所进行的抽检。
4.0.权责
4.1.生产单位
4.1.1.领用材料确认及管理,依照所有生产单领料、退料。
4.1.2.生产设备的使用、安排及一级保养。
4.1.3.相关作业指导书的建立、执行及变更。
4.1.4.工作现场的环境维护及设备的管理。
4.1.
5.配合生产计划,达成既定的生产目标。
4.2.仓管单位:根据生产所需适时提供适质、适量的物料。
4.3.工程单位:生产阶段的品质异常现象及时寻求对策供改善。
4.4.生管单位:依据订单状况及产能规划,排定生产计划。
5.0.程序
5.1.生产指令:所有订单经评估后,由业务部门将客户的“订购单”转化为《生产
制作单》,由部门主管审核,经理核准后将作为生产指令。
5.2.生产准备:生产单位根据制令的要求及所需的模具、治具进行生产的准备,如:
确认机台、人员安排、模具安排、治具调试等。
5.3.领料作业:生产单位依据《生产制作单》的用料数量,及时开出《领料单》到
仓库办理领料作业。
5.4.试产作业:生产单位在产品正式生产前,需按作业指导书和样品要求,生产一
GRR管理办法

4.职责:
4.1生技部确定量测特性及设定测试计划,根据制造部提供的测试数据进行仪器设备制程能力的指数计算,若不合格则设定改善或训练计划并对其实施改善。
4.2品质部配合生技部及制造部对仪器设备的制程能力进行测试,并确认其改善结果.
5.1.3根据测试所得的数据进行准确度及GRR%值的计算,并根据《仪器的重复性和再现性能力检讨记录》中“GRR%比率判定”项,判定该仪器设备的制程能力是否合格。若不合格则设定改善计划或人员训练计划,以对量测仪器之能力进行改善。
XXXX电子
科技有限公司
GRR管理办法
编号
页次
第4页,共4页
5.1.4对量测仪器设备能力改善OK后再次进行测试、计算准确度及GRR%值,并判定是否合格。若NG则修改量测程序,以使生产的仪器设备能力达到正常以至精密程度。
5.3.2品管部应在量测仪器能力没有得到改善时,与生技部、制造部共同研讨并修改量测程序,以使生产线所有仪器设备及人员的制程能力达到正常以至精密程度.
6.参考文件
无
7.附件
表单编码
表单名称
保管单位
保存期限
仪器的重复性和再现性能力检讨记录
管理单位
一年
5.2制造部:
5.2.1仪器设备的量测人员于测试的过程中将所得的数据记录《仪器的重复性和再现性能力检讨记录》中。
供应商监察报告
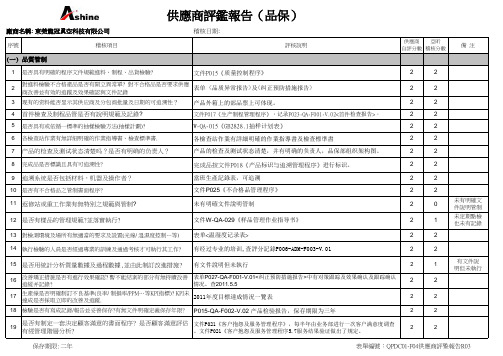
1是否具有明確的程序文件規範進料、制程、出貨檢驗?
文件P015《质量控制程序》222對進料檢驗不合格產品是否有開立異常單? 對不合格品是否要求供應
商改善並有效的追蹤及效果確認與文件記錄
表单 <品质异常报告>及<纠正预防措施报告>
223现有的资料能否显示其供应商及分包商批量及日期的可追溯性?
产品外箱上的部品票上可体现。
224首件檢查及制程品管是否有說明規範及記錄?
文件P017《生产制程管理程序》,记录P023-QA-F001-V.02<首件检查报告>。
225是否具有或依循一標準的抽樣檢驗方法(抽樣計劃)?W-QA-015《GB2828.1抽样计划表》
226各檢查站作業有無詳細明確的作業指導書、檢查標準書.
各檢查站作業有詳細明確的作業指導書及檢查標準書
227产品的检查及测试状态清楚吗?是否有明确的负责人?
产品的检查及测试状态清楚,并有明确的负责人,品保部组织架构图。228完成品是否標識且具有可追溯性?
完成品按文件P018《产品标识与追溯管理程序》进行标识。229
追溯系统是否包括材料,机器及操作者?
當班生產記錄表,可追溯2210是否有不合格品之管制書面程序?文件P025《不合格品管理程序》2211返修站或重工作業有無特別之規範與管制?未有明確文件說明管制
2012
是否有樣品的管理規範?並落實執行?
文件W-QA-029《样品管理作业指导书》2113對檢測環境及場所有無適當的要求及設置(光線/ 溫濕度控制…等)表单<温湿度记录表>
2214執行檢驗的人員是否經過專業的訓練及通過考核才可執行其工作?有经过专业的培训,查評分記錄P006-ADM-F003-V.012
生产制程管理程序文件(5页)

1、目的
1.1对过程中影响产品品质的各个因素进行控制,确保产品品质满足规定的要求。
2、概述
2.1 本程序文件适用于生产过程控制及适当环境下生产。
2.2 生产过程包括装配、注塑、车缝及五金加工。
3、职责
3.1PC部负责有效安排生产计划,确保资源的充分利用,以最低的成本按时完成生产,
确保货期的准时达成。
3.2生产部通过有效管理,负责确保全部生产操作符合规定之作业要求,以保证品质的
制造过程,同时达到生产计划的有效执行和要求。
3.3PE部负责制定[工程流程图]、[检查指导书]、[作业指导书]及必要时提供技术支援
和有效之工夹具,以确保生产效率的提高和品质问题的减少。
4、程序
4.1当PC部收到[生产通知单]后,即作合同评审(COP3.1)。
4.2若能通过评审的[生产通知单],有关人员需每周制定或更新一份[生产计划]/ [加工计
划](加工车间用)交PC负责人确认后,发出给有关使用部门(COP3.1)。
4.3生产部收到[生产计划]/[加工计划]后,应考虑是否有能力按生产计划生产,如以下
几种因素:
A.物料的实际状况。
B.人员的满足状况。
C.PD交货期的缓急状况。
D.机器、工夹具的准备状况。
4.4如生产部无法满足以上要求时,则由PC提出并作以下处理:
A.在满足客户要求的前提下,由PC变更生产计划。
B.如不能满足客户要求,通知销售支援部与客户进行沟通修改订单的要求(方法
参照[合同评审程序])。
4.5当生产之前准备资源满足后,可安排有效之生产。
4.6生产部依据[生产计划]和[物料需求单]中“实际用量”栏之数量发出[领料单],将[领
制程品质异常管理规定
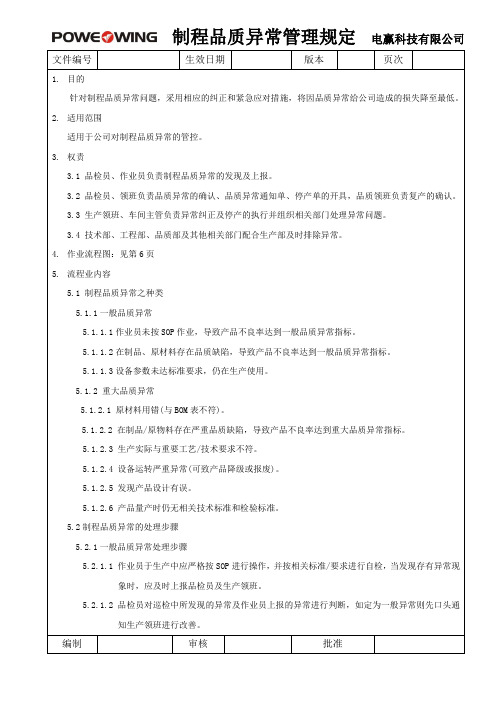
编制
审核
批准
制程品质异常管理规定
文件编号
车间 配料 涂布 工序 正极 负极 正极 负极 正极裁大片 负极裁大片 正极刮粉 负极刮粉 正极片对辊 负极片对辊 正极裁小片 负极裁小片 正极冲片 负极冲片 正极对小辊 卷绕正极分 切 卷绕负极分 切 负极刮凹槽 正极片焊接 负极片焊接 叠片正极外 观 卷绕正极挑 片 叠片负极挑 外观 卷绕负极挑 外观 备料 裁隔膜 冲切包装膜 卷绕外观 装配一 叠片外观 全检短路
记录
异常性质确认 品质部
一般品质异常
重大品质异常 《品质异常联络单》 停产通知 品质部 《停/复产通知单》 停机执行
异常通知
生产部
原因分析
技术部
《品质异常联络单》
纠正执行
责任部门
《品质异常联络单》
效果跟踪
与相关部门联络及异常排除
品质部
《标识卡》 《品质异常联络单》
NO
复产确认
品质/生产部
YES 恢复生产
编制
审核
批准
制程品质异常管理规定
文件编号
15 分钟内完成。 5.3.2 重大品质异常
电赢科技有限公司
页次
生效日期
版本
车间领班在接到『停/复产通知单』后,必须在 2 分钟内安排产线停产并同时上报车间主管,车 间主管应 5 分钟内进行临时应急措施填写,并传递给相关部门同时上报生产经理,相关部门必 须放下手头的工作,5 分钟内到现场解决处理并出具处理意见,整个过程必须控制 在 30 分钟 内完成并恢复生产,若超过 30 分钟仍无法解决,则车间安排相关员工离岗待通知。 5.4 品质异常反馈渠道 5.4.1 一般品质异常和重大品质异常反馈渠道见 5.2。 5.4.2『品质异常通知单』和『停/复产通知单』在执行过程中,如果遇到任何阻力,由生产部即时上 报分管副总,请求解决办法。 5.4.3 品质部在每天品质日报的过程信息栏,需记载当天发生的品质异常状况及处理结果,次日以邮 件发送给公司领导以及相关人员。 5.4.4 同类品质异常累计超过 3 次时,由技术部立项解决。 5.5 具体工序品质异常类别之界定 5.5.1 品管在巡检过程中发现不良品比率达到下表异常标准时,均属于品质异常;若比率≥140%时, 属于重大异常。 5.5.2 对部分工序具体品质异常类别界定如下:
如何做好生产制程管理

如何做好生产制程管理
生产制程管理是指在生产过程中对生产制程进行计划、组织、协调和
控制的一系列活动。它的目的是提高生产效率、降低生产成本、提高产品
质量和满足客户需求。下面是关于如何做好生产制程管理的一些建议。
1.制定明确的生产计划:生产计划是制程管理的基础,要根据市场需求、公司能力和资源进行合理的制定。生产计划应该包括产品的数量、质
量标准、交付时间等要素,同时要考虑到物料的供应、人力资源的配备等
因素,确保生产过程的顺利进行。
2.优化生产流程:生产流程是生产制程的核心,要通过流程优化来提
高效率和质量。首先,要明确每个环节的工作内容和工作顺序,确保生产
过程的合理性和连贯性。然后,要对每个环节的工作进行分析和改进,通
过提高工艺和设备的性能,减少不必要的工序和重复工作,优化操作流程,提高生产效率。
3.良好的人力资源管理:人力资源是制程管理的重要因素,要合理调
配和管理人力资源,确保人员在正确的岗位上发挥最大的作用。首先,要
根据生产计划和工序的特点,确定所需的人员数量和技能要求。然后,要
进行培训和技能提升,确保员工具备必要的技能和知识。同时,要建立激
励机制,激发员工的积极性和创造力,提高团队的凝聚力和合作效率。
4.严格的质量控制:质量是制程管理的核心目标,要通过严格的质量
控制来提高产品的质量。首先,要建立并执行严格的质量控制标准,包括
产品的外观、尺寸、性能等方面的要求。然后,要进行质量检验和测试,
确保产品符合质量控制要求。同时,要建立反馈机制,及时发现和解决质
量问题,避免质量问题对生产计划的影响。
GRR管理办法
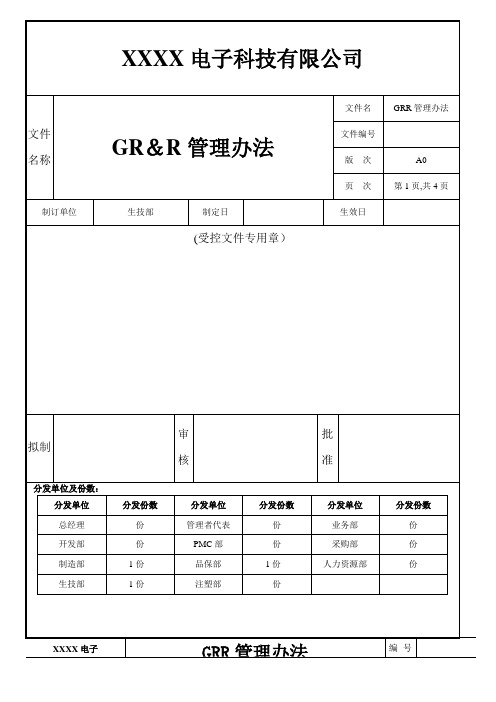
和 再 现 性 能 力 检 讨 记 录 》中“ GRR%比 率 判 定 ”项 ,判 定 该 仪 器 设 备 的 制 程
能 力 是 否 合 格 。若 不 合 格 则 设 定 改 善 计 划 或 人 员 训 练 计 划 ,以 对 量 测 仪 器
之能力进行改善.
XXXX 电子 科技有限公司
GRR 管理办法
分发份数 份 份
1份 份
批 准
分发单位 业务部 采购部 人力资源部
分发份数 份 份 份
XXXX 电子
GRR 管理办法
编号
科技有限公司
页 次 第 2 页,共 4 页
1。 0 目 的 :
为了进一步提高生产制程的稳定性,从而对制程中的测试仪器、 设备、人员的管
制 ,减 少 因 人 、仪 器 、设 备 而 造 成 的 量 测 误 差 , 以 提 供 最 准 确 的 制 程 统 计 技 术 数 据 .
5。 程 序 内 容 :
5.1 作业 流程图
XXXX 电子 确定 量测特性
科技有限公司
GRR 管理办法
编号
页次
第 3 页,共 4 页
设定 测试计划
执行 测试计划
OK
量测仪器能力
NG
设定改善计划
或训改练善Βιβλιοθήκη Baidu否划?
修改 量测程序
5.2 制 造 技 术 部完计成算制程 能准力确研度究
生产过程质量控制程序
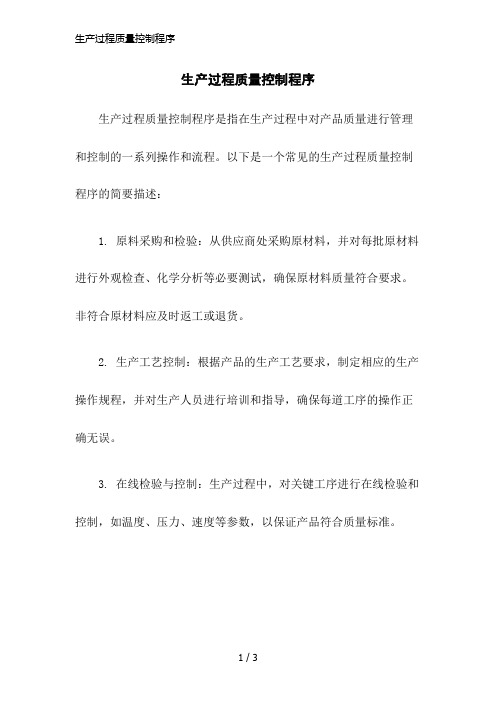
生产过程质量控制程序
生产过程质量控制程序是指在生产过程中对产品质量进行管理和控制的一系列操作和流程。以下是一个常见的生产过程质量控制程序的简要描述:
1. 原料采购和检验:从供应商处采购原材料,并对每批原材料进行外观检查、化学分析等必要测试,确保原材料质量符合要求。非符合原材料应及时返工或退货。
2. 生产工艺控制:根据产品的生产工艺要求,制定相应的生产操作规程,并对生产人员进行培训和指导,确保每道工序的操作正确无误。
3. 在线检验与控制:生产过程中,对关键工序进行在线检验和控制,如温度、压力、速度等参数,以保证产品符合质量标准。
4. 中间产品检验与调整:在生产过程中,对中间产品进行抽样
检验,确保中间产品质量合格,并根据检验结果及时进行调整和优化。
5. 成品检验:生产完成后,对成品进行完整的检验,包括外观、功能、性能等方面的测试,以确保产品质量符合客户要求。
6. 不良品处理:对于不良品,要及时进行分类、记录和处理,
包括返工、报废等,以便找出问题原因并采取相应措施进行改进。
7. 数据分析和改进:定期分析生产数据,找出潜在问题和改进
机会,并根据分析结果进行相关改进措施的制定和实施。
8. 文件管理和记录:建立和维护相关的文件管理系统,包括生
产记录、检验记录、不良品记录等,以便追溯和验证产品质量。
9. 定期审核和评估:定期对质量控制程序进行审核和评估,以
确保程序的有效性和适应性,并进行必要的调整和改进。
以上是一个常见的生产过程质量控制程序的概述,实际的程序还需要根据具体的生产过程和产品特性进行调整和完善。
IPQC岗位操作准则

深圳市鑫昆鹏电源科技有限公司
文件编号
KPA-QAD-004
标准文件
版 别
文件名称:IPQC岗位操作准则
页 码
3of3
5.9.2IPQC工程师对IPQC技术员提出的改善联合研发、工程、生产进行评估,得出解决问题的方法,从而制定预防方案。
5.9.3QC技术员对预防方案的实施情况进行跟进。
6.参考文件
6.7《制程检验规范》 (KPA-QAD-008)
6.8《内部改善措施管理程序》 (KPP-QAD-124)
6.9《QC工程表》 (KPA-QAD-ቤተ መጻሕፍቲ ባይዱ18)
6.10《首件生产管理办法》(KPA-QAD-610)
7.质量记录
7.1《IPQC技术员工作日志》 (KPR-QAD-139)
7.2《内部改善行动要求》(KPR-QAD-119)
5.7 不合格品处理
线上不合格品之原物料、半成品由生产部收集、标示,交IPQC技术员复查,由IPQC工程师签署同意退料、返工、报废等处理意见。
5.8 品质异常之反馈与处理IPQC技术员在巡检过程中,若发现有品质异常现象时,按如下方式执行:
5.8.1若IPQC技术员可自行判定时,由IPQC技术员与生产相关人员进行沟通,提出异常之处,共同提出纠正措施,并跟进整改效果,处理过程IPQC技术员必须如实将改善情况反馈给IPQC工程师。
- 1、下载文档前请自行甄别文档内容的完整性,平台不提供额外的编辑、内容补充、找答案等附加服务。
- 2、"仅部分预览"的文档,不可在线预览部分如存在完整性等问题,可反馈申请退款(可完整预览的文档不适用该条件!)。
- 3、如文档侵犯您的权益,请联系客服反馈,我们会尽快为您处理(人工客服工作时间:9:00-18:30)。
`
1、目的
1.1对过程中阻碍产品品质的各个因素进行操纵,确保产品品质满足规
定的要求。
2、概述
2.1 本程序文件适用于生产过程操纵及适当环境下生产。
2.2 生产过程包括装配、注塑、车缝及五金加工。
3、职责
3.1PC部负责有效安排生产打算,确保资源的充分利用,以最低的成
本按时完成生产,确保货期的准时达成。
3.2生产部通过有效治理,负责确保全部生产操作符合规定之作业要
求,以保证品质的制造过程,同时达到生产打算的有效执行和要求。
3.3PE部负责制定[工程流程图]、[检查指导书]、[作业指导书]及必
要时提供技术支援和有效之工夹具,以确保生产效率的提高和品质
问题的减少。
4、程序
4.1当PC部收到[生产通知单]后,即作合同评审(COP3.1)。
4.2若能通过评审的[生产通知单],有关人员需每周制定或更新一份
[生产打算]/ [加工打算](加工车间用)交PC负责人确认后,发出
给有关使用部门(COP3.1)。
4.3生产部收到[生产打算]/[加工打算]后,应考虑是否有能力按生产
打算生产,如以下几种因素:
A.物料的实际状况。
B.人员的满足状况。
C.PD交货期的缓急状况。
D.机器、工夹具的预备状况。
4.4如生产部无法满足以上要求时,则由PC提出并作以下处理:
A.在满足客户要求的前提下,由PC变更生产打算。
B.如不能满足客户要求,通知销售支援部与客户进行沟通修改订
单的要求(方法参照[合同评审程序])。
4.5当生产之前预备资源满足后,可安排有效之生产。
4.6生产部依据[生产打算]和[物料需求单]中“实际用量”栏之数量发
出[领料单],将[领料单]副本交到仓库领料,并按各型号之[工程流程图]进行排拉生产。非流水线生产车间的作业及检测人员的安排见[非流水车间人员配制要领]。
4.7生产部依照[作业指导书]及[生产通知单]要求作业,直至包装后的
成品存放于待检区,待FQC作最终检查(COP10.1)。
4.8每个生产工序的半成品,均由生产线检测工按[检查指导书]及[生
产通知单]要求进行所需之制程中检查.(COP10.1) 生产线检测工检查位置依照[工程流程图]要求。
4.9 [作业指导书]内容包括各工序半成品作业步骤、注意事项、部
件及设备状况、技术要求等。[检查指导书]内容包括各工序半成品检查步骤、注意事项、仪器设备及技术参数等。
4.10生产部负责人负责监督每个工序,确保所有制作按工艺文件要求