注塑模具设计
注塑模具设计
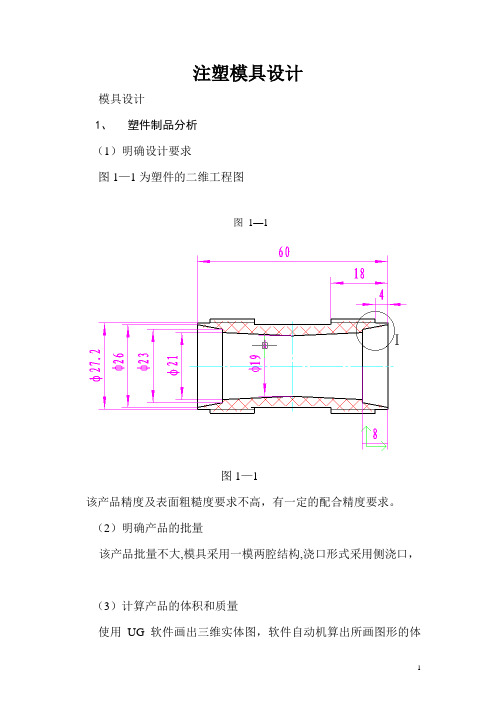
注塑模具设计
模具设计
1、塑件制品分析
(1)明确设计要求
图1—1为塑件的二维工程图
图1—1
图1—1
该产品精度及表面粗糙度要求不高,有一定的配合精度要求。(2)明确产品的批量
该产品批量不大,模具采用一模两腔结构,浇口形式采用侧浇口,
(3)计算产品的体积和质量
使用UG软件画出三维实体图,软件自动机算出所画图形的体
积。
通过计算得塑件的体积V塑=13.85cm3
塑件的质量M塑=ρV塑=1.04×13.85=14.4g
式中ρ---塑料的密度,g/cm3.
流道凝料的质量m2还是个未知数,可按塑件质量的0.6倍来估算。
浇注系统的质量M浇=ρV浇=8.6g
浇注系统的体积V浇=8.30cm3.
故V总= 2×V塑+V浇= 2×13.85cm3 +8.30cm3.= 36cm3 M总=2×M塑+M浇=2×14.4g+8.6g= 43g
2.注塑机的确定
选择注射机型号 XS—ZY—250
主要技术规格如下:
螺杆直径:65mm
注射容量:250cm3
注射压力:1300MPa
锁模力:1800kN
最大注射面积:500cm3
模具厚度:最大350mm
最小250mm
模板行程:350mm
喷嘴:球半径 18mm
孔直径4m
定位孔直径:125mm
顶出:两侧孔径 40mm
两侧孔距 280mm
3.浇注系统的设计
(1)主流道形式
浇注系统是指模具从接触注射机喷嘴开始到型腔未知的塑料流动通道,起作用是使塑料熔体平稳且有顺序的填充到型腔中,并在填充和凝固过程中把注射压力充分传递到各个部位,已获得组织机密、外形清晰地塑件。浇注系统可分为普通浇注系统和无流道凝料系统。考虑浇注系统设计的基本原则:适应塑料的成型工艺性、利于型腔内气体的排出、尽量减少塑料熔体的热量和压力损失、避免熔料直冲细小型芯、便于修正和不影响塑件外观质量、便于减少塑料损失和减小模具尺寸等。
注塑模模具设计开题报告
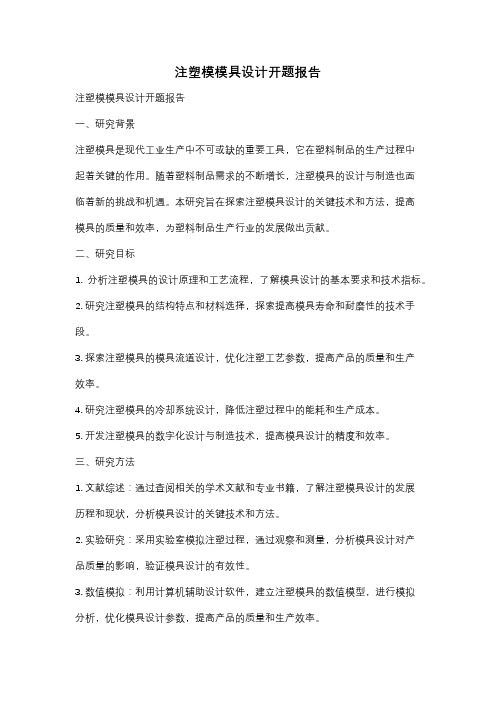
注塑模模具设计开题报告
注塑模模具设计开题报告
一、研究背景
注塑模具是现代工业生产中不可或缺的重要工具,它在塑料制品的生产过程中
起着关键的作用。随着塑料制品需求的不断增长,注塑模具的设计与制造也面
临着新的挑战和机遇。本研究旨在探索注塑模具设计的关键技术和方法,提高
模具的质量和效率,为塑料制品生产行业的发展做出贡献。
二、研究目标
1. 分析注塑模具的设计原理和工艺流程,了解模具设计的基本要求和技术指标。
2. 研究注塑模具的结构特点和材料选择,探索提高模具寿命和耐磨性的技术手段。
3. 探索注塑模具的模具流道设计,优化注塑工艺参数,提高产品的质量和生产
效率。
4. 研究注塑模具的冷却系统设计,降低注塑过程中的能耗和生产成本。
5. 开发注塑模具的数字化设计与制造技术,提高模具设计的精度和效率。
三、研究方法
1. 文献综述:通过查阅相关的学术文献和专业书籍,了解注塑模具设计的发展
历程和现状,分析模具设计的关键技术和方法。
2. 实验研究:采用实验室模拟注塑过程,通过观察和测量,分析模具设计对产
品质量的影响,验证模具设计的有效性。
3. 数值模拟:利用计算机辅助设计软件,建立注塑模具的数值模型,进行模拟
分析,优化模具设计参数,提高产品的质量和生产效率。
4. 数据分析:通过统计和分析实验数据,总结模具设计的经验和规律,为模具
设计提供科学依据。
四、研究内容
1. 注塑模具的设计原理和工艺流程:对注塑模具的结构、功能和工作原理进行
分析,了解模具设计的基本要求和流程。
2. 注塑模具的结构特点和材料选择:研究模具的结构特点和材料性能,探索提
注塑模具设计总结
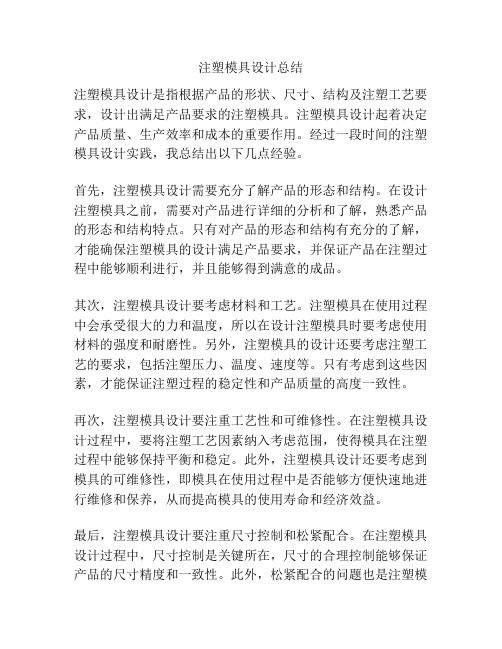
注塑模具设计总结
注塑模具设计是指根据产品的形状、尺寸、结构及注塑工艺要求,设计出满足产品要求的注塑模具。注塑模具设计起着决定产品质量、生产效率和成本的重要作用。经过一段时间的注塑模具设计实践,我总结出以下几点经验。
首先,注塑模具设计需要充分了解产品的形态和结构。在设计注塑模具之前,需要对产品进行详细的分析和了解,熟悉产品的形态和结构特点。只有对产品的形态和结构有充分的了解,才能确保注塑模具的设计满足产品要求,并保证产品在注塑过程中能够顺利进行,并且能够得到满意的成品。
其次,注塑模具设计要考虑材料和工艺。注塑模具在使用过程中会承受很大的力和温度,所以在设计注塑模具时要考虑使用材料的强度和耐磨性。另外,注塑模具的设计还要考虑注塑工艺的要求,包括注塑压力、温度、速度等。只有考虑到这些因素,才能保证注塑过程的稳定性和产品质量的高度一致性。
再次,注塑模具设计要注重工艺性和可维修性。在注塑模具设计过程中,要将注塑工艺因素纳入考虑范围,使得模具在注塑过程中能够保持平衡和稳定。此外,注塑模具设计还要考虑到模具的可维修性,即模具在使用过程中是否能够方便快速地进行维修和保养,从而提高模具的使用寿命和经济效益。
最后,注塑模具设计要注重尺寸控制和松紧配合。在注塑模具设计过程中,尺寸控制是关键所在,尺寸的合理控制能够保证产品的尺寸精度和一致性。此外,松紧配合的问题也是注塑模
具设计中需要注意的重要问题,合理的松紧配合能够防止模具在使用过程中的松动和变形。
总之,注塑模具设计是一个复杂的工程,需要综合考虑产品的形态、材料、工艺等因素。只有全面考虑这些因素,才能设计出满足产品要求的注塑模具,保证产品质量和生产效率。在注塑模具设计过程中,还需要不断总结经验,不断提高设计水平,以适应不断变化的市场需求和技术发展。
注塑模具设计说明书
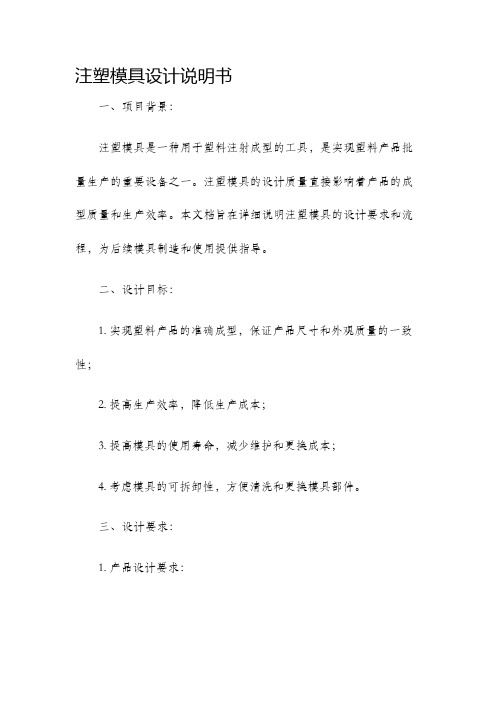
注塑模具设计说明书
一、项目背景:
注塑模具是一种用于塑料注射成型的工具,是实现塑料产品批量生产的重要设备之一。注塑模具的设计质量直接影响着产品的成型质量和生产效率。本文档旨在详细说明注塑模具的设计要求和流程,为后续模具制造和使用提供指导。
二、设计目标:
1. 实现塑料产品的准确成型,保证产品尺寸和外观质量的一致性;
2. 提高生产效率,降低生产成本;
3. 提高模具的使用寿命,减少维护和更换成本;
4. 考虑模具的可拆卸性,方便清洗和更换模具部件。
三、设计要求:
1. 产品设计要求:
a. 确定产品的尺寸和外观要求,提供详细的产品图纸和规格说明;
b. 需要考虑产品的材料特性,如塑料的热胀冷缩性,流动性等;
c. 确定产品的成型方式和注塑工艺参数。
2. 模具结构设计要求:
a. 考虑产品的成型方式,确定模具的结构类型,如单腔模具、多腔模具等;
b. 在满足产品尺寸和外观要求的基础上,尽量减小模具的尺寸和重量;
c. 考虑模具的使用寿命,采用耐磨、耐腐蚀的材料,优化工艺和热处理;
d. 考虑模具的冷却系统,保证注塑过程中材料的快速冷却和成型周期的缩短;
e. 考虑模具的导向系统和定位系统,确保模具运动的准确性和稳定性;
f. 考虑模具的拆卸性,方便清洗和更换模具部件。
3. 模具零件设计要求:
a. 模具芯、模具腔、模具板等零件的尺寸要与产品尺寸要求一致;
b. 避免尺寸过小、壁厚过薄等问题,确保零件的强度和刚性;
c. 考虑零件的加工工艺,尽量减少加工难度和成本;
d. 避免零件之间的干涉和碰撞,确保模具的正常运作;
e. 采用标准化零件,方便制造和更换。
模具注塑产品设计方案模板
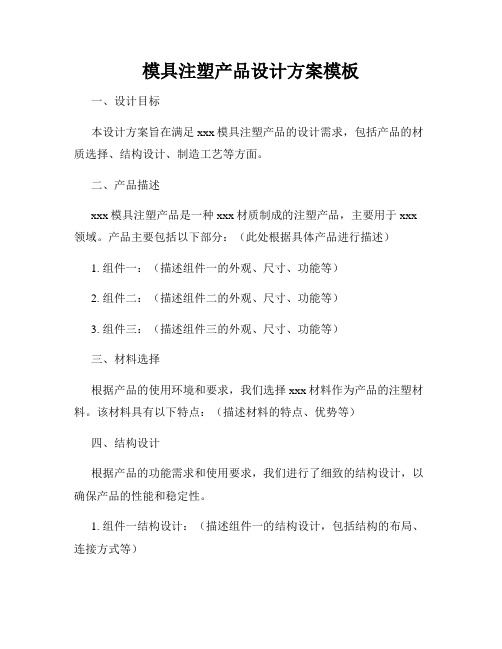
模具注塑产品设计方案模板
一、设计目标
本设计方案旨在满足xxx模具注塑产品的设计需求,包括产品的材质选择、结构设计、制造工艺等方面。
二、产品描述
xxx模具注塑产品是一种xxx材质制成的注塑产品,主要用于xxx 领域。产品主要包括以下部分:(此处根据具体产品进行描述)
1. 组件一:(描述组件一的外观、尺寸、功能等)
2. 组件二:(描述组件二的外观、尺寸、功能等)
3. 组件三:(描述组件三的外观、尺寸、功能等)
三、材料选择
根据产品的使用环境和要求,我们选择xxx材料作为产品的注塑材料。该材料具有以下特点:(描述材料的特点、优势等)
四、结构设计
根据产品的功能需求和使用要求,我们进行了细致的结构设计,以确保产品的性能和稳定性。
1. 组件一结构设计:(描述组件一的结构设计,包括结构的布局、连接方式等)
2. 组件二结构设计:(描述组件二的结构设计,包括结构的布局、连接方式等)
3. 组件三结构设计:(描述组件三的结构设计,包括结构的布局、连接方式等)
五、制造工艺
为实现设计方案,我们采用了以下制造工艺来生产xxx模具注塑产品。
1. 模具制造:选择优质的钢材,开展精密的数控加工,制造符合精度要求的模具。
2. 注塑成型:通过将注塑材料加热熔化后注入模具中,冷却后获取最终成型的产品。
3. 后处理:对成型产品进行去除模具余料、修整边缘、表面处理等工艺,使产品达到要求。
六、检测与质量控制
为确保产品的质量,我们采用以下检测方法和质量控制措施:
1. 外观检测:检查产品的表面光洁度、色彩、图案等外观要素。
2. 尺寸检测:使用合适的测量工具对产品的尺寸进行严格检测。
注塑模具设计知识与精髓
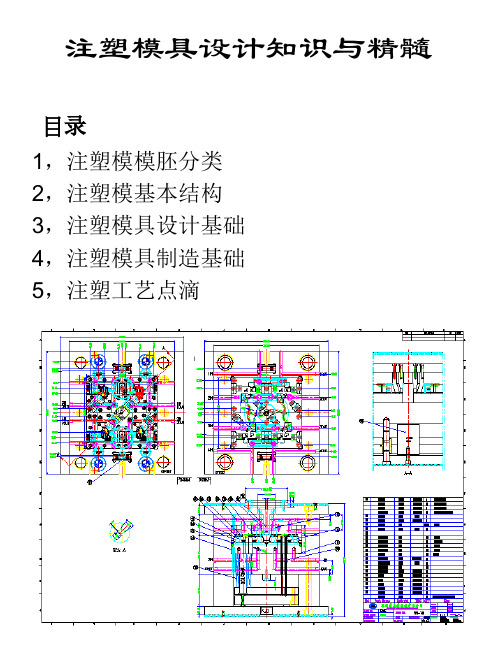
常用锥管螺纹底孔表
常用螺丝底孔表
油槽开法如图,不能通边。 凡是有相对滑动的面,其中一面要开油槽, 一般开在垫板与压条。
油槽不能太多 否则面变粗糙 摩擦力变大 油槽深0.2~0.3
排气槽尺寸
2
0.5mm
1
树脂名称 PE PP PS ABS SAN ASA POM
b=5
Section A-A
各种树脂的排气槽深度h
闭模状态
冷却水隔水片的做法
开模状态
胶圈的做法
B,排气方式 a.分 型 面 排 气。 b. 成 型 芯 排 氣。 c.中 心 頂 杆 排 氣 d.頂 針 排 氣
e.側 型 芯 排 氣
流道截面形状
名称
圆 形 正六边形
U形
正方形 梯 形
半圆形
矩形
流 图形 道 及尺 截 寸代 面号
效 通用 率 表达 (P 式 =S /L) 值
0.250D
截面 面积 S =πR 2时 的P 值
排气槽深度(mm)
树脂名称
3
排气槽深度(mm)
0.02 0.02 0.02 0.03 0.03 0.03 0.02
PA(含玻纤) PA
PC(含玻纤) PC
PBT(含玻纤) PBT PMMA
0.03~0.04 0.02
0.05~0.07 0.04
0.03~0.04 0.02 0.04
注塑模具设计操作流程
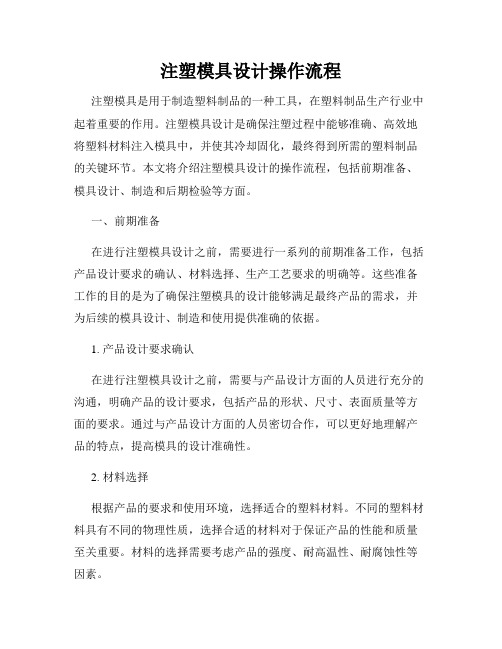
注塑模具设计操作流程
注塑模具是用于制造塑料制品的一种工具,在塑料制品生产行业中起着重要的作用。注塑模具设计是确保注塑过程中能够准确、高效地将塑料材料注入模具中,并使其冷却固化,最终得到所需的塑料制品的关键环节。本文将介绍注塑模具设计的操作流程,包括前期准备、模具设计、制造和后期检验等方面。
一、前期准备
在进行注塑模具设计之前,需要进行一系列的前期准备工作,包括产品设计要求的确认、材料选择、生产工艺要求的明确等。这些准备工作的目的是为了确保注塑模具的设计能够满足最终产品的需求,并为后续的模具设计、制造和使用提供准确的依据。
1. 产品设计要求确认
在进行注塑模具设计之前,需要与产品设计方面的人员进行充分的沟通,明确产品的设计要求,包括产品的形状、尺寸、表面质量等方面的要求。通过与产品设计方面的人员密切合作,可以更好地理解产品的特点,提高模具的设计准确性。
2. 材料选择
根据产品的要求和使用环境,选择适合的塑料材料。不同的塑料材料具有不同的物理性质,选择合适的材料对于保证产品的性能和质量至关重要。材料的选择需要考虑产品的强度、耐高温性、耐腐蚀性等因素。
3. 生产工艺要求明确
在确定了产品的设计要求和材料选择之后,需要明确生产工艺要求。生产工艺要求涉及到注塑过程中的各个环节,包括注塑机的选择、注
塑温度的控制、注塑时间的控制等。明确生产工艺要求可以帮助设计
师更好地进行模具的设计。
二、模具设计
模具设计是注塑模具设计操作流程中的核心环节,包括模具结构设
计和模腔设计。
1. 模具结构设计
模具结构设计是根据产品的形状和要求,确定模具的结构,包括模
注塑模具课程设计
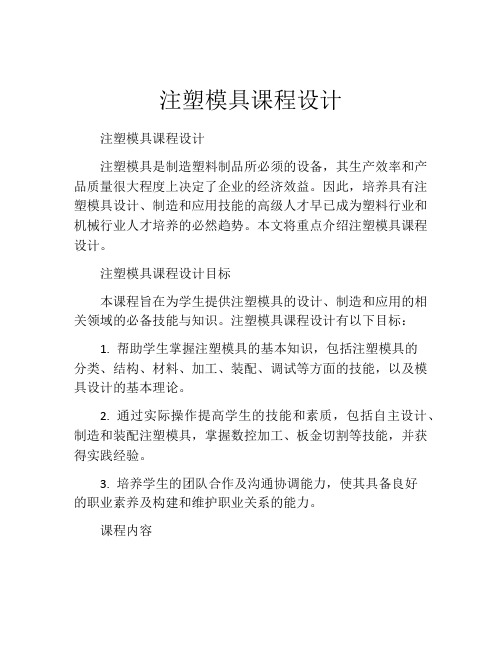
注塑模具课程设计
注塑模具课程设计
注塑模具是制造塑料制品所必须的设备,其生产效率和产品质量很大程度上决定了企业的经济效益。因此,培养具有注塑模具设计、制造和应用技能的高级人才早已成为塑料行业和机械行业人才培养的必然趋势。本文将重点介绍注塑模具课程设计。
注塑模具课程设计目标
本课程旨在为学生提供注塑模具的设计、制造和应用的相关领域的必备技能与知识。注塑模具课程设计有以下目标:
1. 帮助学生掌握注塑模具的基本知识,包括注塑模具的
分类、结构、材料、加工、装配、调试等方面的技能,以及模具设计的基本理论。
2. 通过实际操作提高学生的技能和素质,包括自主设计、制造和装配注塑模具,掌握数控加工、板金切割等技能,并获得实践经验。
3. 培养学生的团队合作及沟通协调能力,使其具备良好
的职业素养及构建和维护职业关系的能力。
课程内容
1. 注塑模具的基本知识:注塑模具的定义、分类和功能,模具的构成要素,模具材料及影响因素,注塑模具的制造工艺等。
2. 注塑模具的设计理论:模具的设计过程及其要素,模
具设计参数的选取,模具外形及构造设计,模具零部件的设计,注塑模具设计的新技术和研究成果。
3. 模具制造工艺过程:模具制造工艺要点,模具金加工,模具板金工艺,模具装配及调试。
4. 数控加工及电脑辅助设计技术的应用:数控加工中心
的技术原理、应用范围和特点,数控加工的编程,数控加工的优化及控制,电脑辅助设计及其基本原理。
5. 模具修理及维护:注塑模具的灰口维护,模具损坏原
因的分析,维修工艺和维修方法。
6. 模具加工预备知识和实践:熟悉毛坯的形状和尺寸,
塑料模具设计步骤
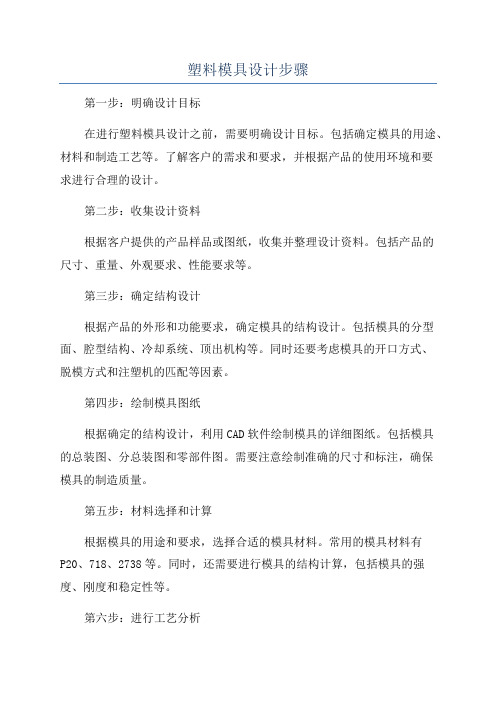
塑料模具设计步骤
第一步:明确设计目标
在进行塑料模具设计之前,需要明确设计目标。包括确定模具的用途、材料和制造工艺等。了解客户的需求和要求,并根据产品的使用环境和要
求进行合理的设计。
第二步:收集设计资料
根据客户提供的产品样品或图纸,收集并整理设计资料。包括产品的
尺寸、重量、外观要求、性能要求等。
第三步:确定结构设计
根据产品的外形和功能要求,确定模具的结构设计。包括模具的分型面、腔型结构、冷却系统、顶出机构等。同时还要考虑模具的开口方式、
脱模方式和注塑机的匹配等因素。
第四步:绘制模具图纸
根据确定的结构设计,利用CAD软件绘制模具的详细图纸。包括模具
的总装图、分总装图和零部件图。需要注意绘制准确的尺寸和标注,确保
模具的制造质量。
第五步:材料选择和计算
根据模具的用途和要求,选择合适的模具材料。常用的模具材料有
P20、718、2738等。同时,还需要进行模具的结构计算,包括模具的强度、刚度和稳定性等。
第六步:进行工艺分析
对模具的制造工艺进行分析和确定。包括分析模具的加工工序、加工
工艺和设备要求等。根据模具的复杂程度和加工难度,合理安排加工顺序,确保模具的制造周期和质量。
第七步:模具制造
根据绘制的模具图纸和工艺分析,开始进行模具的制造。包括模具的
零部件加工、热处理、组装和调试等。在制造过程中,需要严格按照图纸
要求进行加工,并进行质量检查和控制,确保模具的精度和质量。
第八步:模具试模和调试
在模具制造完成后,进行模具的试模和调试。将模具安装到注塑机上,进行试模产出。根据试模的结果进行调整和优化,确保产品的质量和满足
模具设计原理及考虑

制件设计的一般考虑
工程塑料制品大部分是用注射成型方法加工而成的,制件的设计必须在满足使用要求和符合塑料本身的特性前提下,尽可能简化结构和模具、节省材料、便于成型。制件设计中应分别考虑如下因素:
一、制件的形状应尽量简单、便于成型。
在保证使用要求前提下,力求简单、便于脱模,尽量避免或减少抽芯机构,如采用下图例中(b)的结构,不仅可大大简化模具结构,便于成型,且能提高生产效率。
二、制件的壁厚确定应合理。
塑料制件的壁厚取决于塑件的使用要求,太薄会造成制品的强度和刚度不足,受力后容易产生翘曲变形,成型时流动阻力大,大型复杂的制品就难以充满型腔。反之,壁厚过大,不但浪费材料,而且加长成型周期,降低生产率,还容易产生气泡、缩孔、翘曲等疵病。因此制件设计时确定制件壁厚应注意以下几点:
1.在满足使用要求的前提下,尽量减小壁厚;
2.制件的各部位壁厚尽量均匀,以减小内应力和变形;
3.承受紧固力部位必须保证压缩强度;
4.避免过厚部位产生缩孔和凹陷;
5.成型顶出时能承受冲击力的冲击。
国外的一些常用塑料的推荐壁厚如下表:
三、必须设置必要的脱模斜度
为确保制件成型时能顺利脱模,设计时必须在脱模方向设置脱模斜度,其大小与塑料性能、制件的收缩率和几何形状有关,对于工程塑料的结构件来说,一般应在保证顺利脱模的前提下,尽量减小脱模斜度。
下表为根据不同材料而推荐的脱模斜度:
具体确定脱模斜度时应考虑以下几点:
1.对于收缩率大的塑料制件应选用较大的脱模斜度;
2.对于大尺寸制件或尺寸精度要求高的制件应采用较小的脱模斜度;
3.制件壁厚较厚时,成型收缩增大,因此脱模斜度应取大;
注塑模具设计实训报告
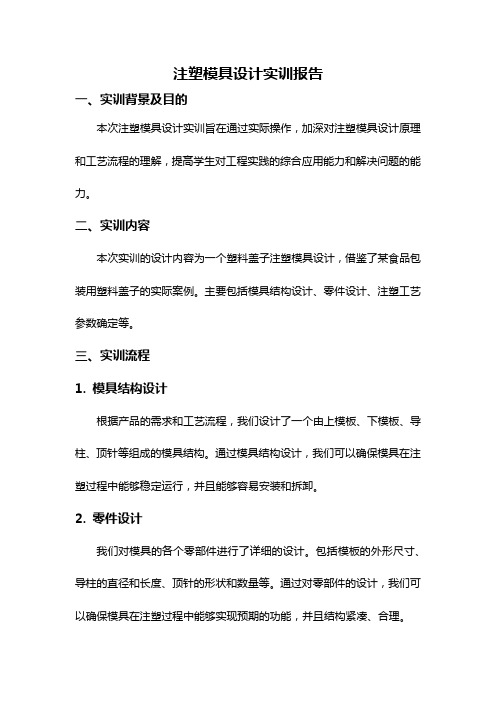
注塑模具设计实训报告
一、实训背景及目的
本次注塑模具设计实训旨在通过实际操作,加深对注塑模具设计原理和工艺流程的理解,提高学生对工程实践的综合应用能力和解决问题的能力。
二、实训内容
本次实训的设计内容为一个塑料盖子注塑模具设计,借鉴了某食品包装用塑料盖子的实际案例。主要包括模具结构设计、零件设计、注塑工艺参数确定等。
三、实训流程
1. 模具结构设计
根据产品的需求和工艺流程,我们设计了一个由上模板、下模板、导柱、顶针等组成的模具结构。通过模具结构设计,我们可以确保模具在注塑过程中能够稳定运行,并且能够容易安装和拆卸。
2. 零件设计
我们对模具的各个零部件进行了详细的设计。包括模板的外形尺寸、导柱的直径和长度、顶针的形状和数量等。通过对零部件的设计,我们可以确保模具在注塑过程中能够实现预期的功能,并且结构紧凑、合理。
3. 注塑工艺参数确定
根据模具结构和产品需求,我们确定了注塑的工艺参数。包括注塑机的射胶压力、注塑速度、射胶时间、保压时间等。通过合理设置工艺参数,我们可以保证产品注塑的质量、生产效率和模具寿命。
4. 模具制造和调试
在完成模具设计后,我们进行了模具的制造和调试工作。这包括使用数控机床进行模具零部件的加工,组装模具,以及在注塑机上进行模具的调试。通过制造和调试的过程,我们可以发现并解决模具设计和制造中的问题,确保模具的正常使用。
四、实训成果
经过本次实训,我们掌握了注塑模具设计的基本原理和方法,并且熟练应用到实际操作中。我们设计和制造了一个塑料盖子注塑模具,并成功进行了注塑工艺调试,最终得到了符合要求的塑料盖子产品。
低压注塑成型模具
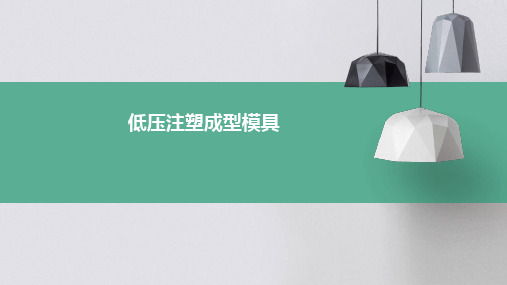
目的和目标
目的
研究低压注塑成型模具的设计、制造 、使用和维护,以提高塑料制品的生 产效率、降低生产成本、提高产品质 量。
目标
掌握低压注塑成型模具的基本原理、 设计要点、制造工艺和使用规范,了 解其发展趋势和应用前景。
02
低压注塑成型模具概述
THANKS
详细描述:该案例重点探讨了低压注塑成型模具的制造过程,强调精细制造的重要性。通过严格控制材料、加工工艺和装配 精度,确保模具性能稳定可靠,提高产品质量和生产效率。
案例三
总结词:经验分享
详细描述:该案例分享了某工厂在使用低压注塑成型模具过程中的经验教训,涉及模具维护、调试、 故障排除等方面。通过实际案例分析,总结出实用的操作技巧和注意事项,为其他工厂提供参考和借 鉴。
06 案例分析
案例一:某产品低压注塑成型模具设计
总结词:优化设计
详细描述:该案例主要介绍了如何根据产品特点和生产需求,进行低压注塑成型 模具的优化设计。通过对模具结构、浇注系统、冷却系统等方面的改进,提高模 具的稳定性和生产效率,降低生产成本。
பைடு நூலகம்
案例二:某公司低压注塑成型模具制造过程
总结词:精细制造
04
按照预定的注射程序进行注射,观察模具的开 启和关闭是否顺畅,检查塑料是否填充均匀,
注塑模具的设计主要内容
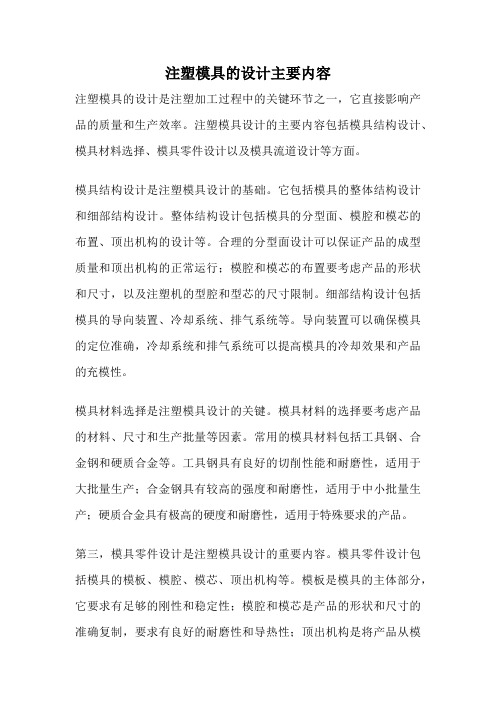
注塑模具的设计主要内容
注塑模具的设计是注塑加工过程中的关键环节之一,它直接影响产品的质量和生产效率。注塑模具设计的主要内容包括模具结构设计、模具材料选择、模具零件设计以及模具流道设计等方面。
模具结构设计是注塑模具设计的基础。它包括模具的整体结构设计和细部结构设计。整体结构设计包括模具的分型面、模腔和模芯的布置、顶出机构的设计等。合理的分型面设计可以保证产品的成型质量和顶出机构的正常运行;模腔和模芯的布置要考虑产品的形状和尺寸,以及注塑机的型腔和型芯的尺寸限制。细部结构设计包括模具的导向装置、冷却系统、排气系统等。导向装置可以确保模具的定位准确,冷却系统和排气系统可以提高模具的冷却效果和产品的充模性。
模具材料选择是注塑模具设计的关键。模具材料的选择要考虑产品的材料、尺寸和生产批量等因素。常用的模具材料包括工具钢、合金钢和硬质合金等。工具钢具有良好的切削性能和耐磨性,适用于大批量生产;合金钢具有较高的强度和耐磨性,适用于中小批量生产;硬质合金具有极高的硬度和耐磨性,适用于特殊要求的产品。
第三,模具零件设计是注塑模具设计的重要内容。模具零件设计包括模具的模板、模腔、模芯、顶出机构等。模板是模具的主体部分,它要求有足够的刚性和稳定性;模腔和模芯是产品的形状和尺寸的准确复制,要求有良好的耐磨性和导热性;顶出机构是将产品从模
腔中顶出的装置,要求有足够的顶出力和顶出平稳性。
模具流道设计是注塑模具设计的关键环节。模具流道设计包括喷嘴、主流道和分流道的设计。喷嘴是将熔融塑料注入模腔的装置,要求有良好的导向性和密封性;主流道是将熔融塑料从注塑机到模具的流动通道,要求有足够的流动性和冷却效果;分流道是将熔融塑料从主流道分配到各个模腔的流动通道,要求有均匀的分配和充模性。注塑模具的设计主要包括模具结构设计、模具材料选择、模具零件设计以及模具流道设计等方面。合理的模具设计可以提高产品的质量和生产效率,降低生产成本,是注塑加工过程中不可或缺的环节。通过科学的设计和不断的改进,可以不断提高注塑模具的设计水平,满足不同产品的生产需求。
注塑件设计与模具设计

注塑件设计与模具设计
注塑件设计与模具设计是现代制造业中非常重要的环节。注塑件设计是指在注塑成型过程中所用到的零件的设计。注塑成型是现代加工生产的基本方法之一,注塑件作为加工零件的一种,已广泛应用于家电、汽车、通信、电子等领域。
注塑件设计的主要任务是寻找最合适的注塑工艺,并在此基础上设计尺寸、形状和结构等方面的要求。注塑件的设计始终围绕着成型工艺,对于加强注塑件的结构性能、减少生产成本、提高生产效率都起到了至关重要的作用。
优秀的模具设计是注塑件质量的保障,也是生产效率的重要保障。模具设计是指根据注塑成型工艺要求和产品结构,设计出使产品在注塑成型过程中能正确地成型出来的模具。在具体实施中,要充分考虑模具的结构、精度、耐用性等因素,以确保模具的高效、稳定运行。
下面简单介绍一下注塑件设计与模具设计的主要步骤和注意事项:
一、注塑件设计
1.了解注塑成型工艺:在进行注塑件设计前,首先需要了解整个注塑成型工艺的流程,包括原材料、注塑机、模具等方面,以便于正确地设计注塑件。
2.确定注塑件的结构:注塑件的结构要根据具体的生产需求进行设计,包括构造尺寸、孔穴尺寸、壁厚、倾斜度等方面。
3.选择优化的材料:不同的材料对于注塑制品的性能和外观有着决定性的影响,应该适当的选择材料。
4.设计合理的放样方案:注塑时将会产生收缩,因此注塑件在设计过程中需要进行放样,需要制定合理的放样方案。
5.验证注塑件的可行性:通过设计工具对设计的注塑件进行验证,得到最合适的方案并进行完善。
二、模具设计
1.选择正确的材料:根据不同的生产场合和要求,选择一定的材料。
注塑模具设计实例100例
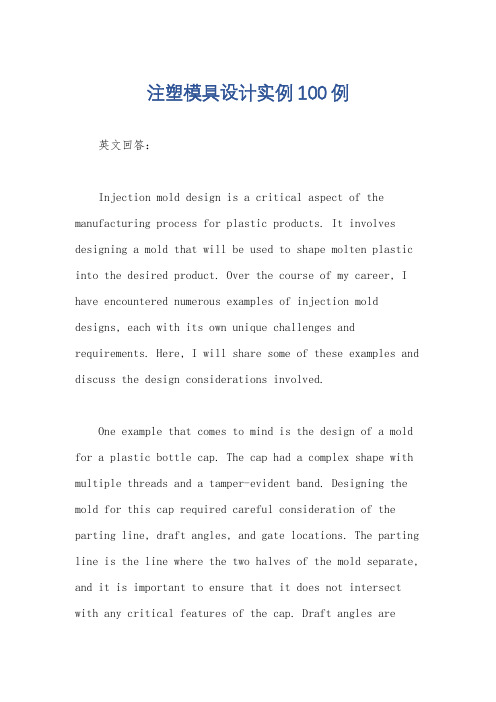
注塑模具设计实例100例
英文回答:
Injection mold design is a critical aspect of the manufacturing process for plastic products. It involves designing a mold that will be used to shape molten plastic into the desired product. Over the course of my career, I have encountered numerous examples of injection mold designs, each with its own unique challenges and requirements. Here, I will share some of these examples and discuss the design considerations involved.
One example that comes to mind is the design of a mold for a plastic bottle cap. The cap had a complex shape with multiple threads and a tamper-evident band. Designing the mold for this cap required careful consideration of the parting line, draft angles, and gate locations. The parting line is the line where the two halves of the mold separate, and it is important to ensure that it does not intersect with any critical features of the cap. Draft angles are
注塑模具的制作工艺流程
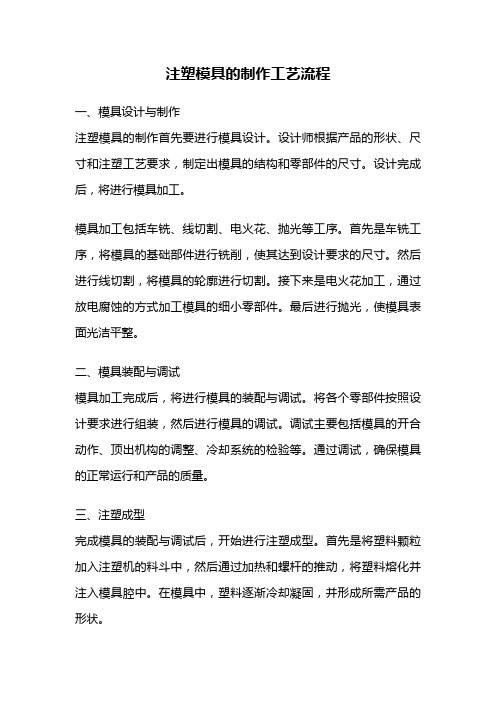
注塑模具的制作工艺流程
一、模具设计与制作
注塑模具的制作首先要进行模具设计。设计师根据产品的形状、尺寸和注塑工艺要求,制定出模具的结构和零部件的尺寸。设计完成后,将进行模具加工。
模具加工包括车铣、线切割、电火花、抛光等工序。首先是车铣工序,将模具的基础部件进行铣削,使其达到设计要求的尺寸。然后进行线切割,将模具的轮廓进行切割。接下来是电火花加工,通过放电腐蚀的方式加工模具的细小零部件。最后进行抛光,使模具表面光洁平整。
二、模具装配与调试
模具加工完成后,将进行模具的装配与调试。将各个零部件按照设计要求进行组装,然后进行模具的调试。调试主要包括模具的开合动作、顶出机构的调整、冷却系统的检验等。通过调试,确保模具的正常运行和产品的质量。
三、注塑成型
完成模具的装配与调试后,开始进行注塑成型。首先是将塑料颗粒加入注塑机的料斗中,然后通过加热和螺杆的推动,将塑料熔化并注入模具腔中。在模具中,塑料逐渐冷却凝固,并形成所需产品的形状。
四、冷却与脱模
注塑成型后,需要进行冷却与脱模。冷却系统通过循环的冷却水将模具中的热量带走,使塑料迅速冷却。冷却完成后,打开模具,将脱模装置推动,使产生的制品从模具中脱落。
五、修整与检验
脱模后,还需要进行修整与检验。修整主要是去除模具留下的切削边和冲击痕迹,使产品表面光滑。检验则是对产品进行尺寸、外观质量等方面的检查,确保产品符合要求。
六、模具保养与维护
完成一次注塑成型后,需要进行模具的保养与维护工作。保养工作包括清洁模具、防锈处理、润滑等,以延长模具的使用寿命。维护工作包括定期检查模具的磨损情况,及时更换损坏的零部件。
- 1、下载文档前请自行甄别文档内容的完整性,平台不提供额外的编辑、内容补充、找答案等附加服务。
- 2、"仅部分预览"的文档,不可在线预览部分如存在完整性等问题,可反馈申请退款(可完整预览的文档不适用该条件!)。
- 3、如文档侵犯您的权益,请联系客服反馈,我们会尽快为您处理(人工客服工作时间:9:00-18:30)。
课程设计:注塑模具设计设计零件:带螺纹圆桶
设计人:蒙帮爱(254)组员:符祥龙(245)
梁超(250)
1.零件材料以及特点
电绝缘性(尤其高频绝缘性)优良,无色透明,透光率仅次于有机玻璃,着色性耐水性,化学稳定性良好,强度一般,但质脆,易产生应力脆裂,不耐苯.汽油等有机溶剂.适于制作绝缘透明件.装饰件及化学仪器.光学仪器等零件.
成型性能
1.无定形料,吸湿小,不须充分干燥,不易分解,但热膨胀系数大,易产生内
应力.流动性较好,可用螺杆或柱塞式注射机成型.
2.宜用高料温,高模温,低注射压力,延长注射时间有利于降低内应力,防止
缩孔.变形.
3.可用各种形式浇口,浇口与塑件圆弧连接,以免去处浇口时损坏塑件.脱
模斜度大,顶出均匀.塑件壁厚均匀,最好不带镶件,如有镶件应预热。
其密度为1.05g/cm3,伸长长度:3–4%,成型收缩率:0.6-0.8% ,成型温度:170-250℃。
2.零件要求和零件图
要求:塑料制品内壁有凸槽以及外形要求美观,不得有痕迹。
内径为114mm,外径为120mm,长度为130mm,厚度2mm
零件图:proe三维图
3.拟定模具结构
(1)模具结构形式确定
该模型为一模一腔,内斜滑块分型抽芯脱模,产品光滑,深度大,由于带有螺纹,因此使用嵌件制造出外螺纹。
(2)注射机型号
注射量的计算
塑件体积:V=18.2cm3
塑件质量:m=ρV=18.2x1.05=11.41g
浇注系统初步估计
V总=V(1+0.3)=23.66cm3
注射机选择
V注射机=V/0.8=29.58cm3
xs-z30/25
(3)注射机相关参数校核
压力校核
聚苯乙烯的注射压力应视制品的特点、原料情况、模具以及设备条
件等情况综合考虑选择的,大致可在60 ~150MPa 较宽的范围
内选取,大浇口、厚壁制品可低些(约60 ~80M Pa),而薄壁
长流程复杂制品或大面积小浇口制品压力则要求大些(约120M
Pa 以上)。另外,柱塞式注塑机由于注射压力损失较大,故压力
要求比螺杆式注塑机大得多。因此,通过综合考虑取p=70MPa,
注射机安全系数k=1.25~1.4,取1.4.
KP=1.4x70=98<116MPa,则该注射机压力满足
锁模力校核
投影面积:A=11304mm2
由于浇注面积不算因此,模具型腔内熔料压力:
F涨=AP模=11304x30=339.12kN(其中,P模取注射压力的
0.2~0.4,即为23.6~47.2MPa)
此外锁模力为F锁模=250kn,安全系数为1.1~1.2,这里取k2=1.2。
则k2F涨=1.2x339.12=406.9>250,因此初定方案不符合。
则另选注射机参数
xs-zy1000/450
由KP=98<120MPa则为合格。
k2F涨=1.2x339.12<4500完全符合
(4)浇注系统设计
由于成型塑件便面要求没有痕迹,采用点浇口进行浇注,使得成型
后脱模容易,以及质量好,下端直径0.4mm,上端为1.2mm,结构
如图所示:
4.模架选取
根据塑件的外形,浇注系统结构,弯销等,根据参考,初步选定DCI5050即500mm×500mm
1.各模板尺寸
(1)定模板
定模板要开腔装入整体嵌入型腔,加上定模板上还要开设有冷却系统,
加之零件体积大小限定,保证一定刚度,选择80mm。
(2)滑块厚度
由塑件外形,要设立两侧分型有滑块作用,保证定位、精度以及刚度,
还要确保分型是滑块稳定,则取30mm厚度
(3)型芯固定板
在此模具中加入型芯固定板,主要起到固定和确保一定刚度,可取其
厚度为30mm
(4)动模板尺寸
动模板的选取主要是其受到注射时候承受的压力而定,在注射塑件时
为了能够承受压力,此外在模具中还承担着导向作用,厚度相对要大
些,取90mm。
(5)模脚尺寸
模脚高度=顶出行程+推板厚度+顶出固定板厚度+5=235mm
由上述综合考虑,初步定出模具高度为550mm,也就是550mm×500mm×525mm。2.模架校核
1)模具平面尺寸
550mmX500mm<650mmX550mm,得出其合格。
2)模具高度尺寸
300mm<525mm<700mm,校验合格。
3.模具的开模行程
180+130*2+10=450mm<700mm,校验合格。
5.冷却系统设计
为满足塑件需要,在型芯内部装有水套,水通过水套循环进行冷却。水套和连接杆通过套筒进行配合,水套和套筒过盈配合,而套筒和连接杆则是间隙配合,保证了行程,也保证了工作时精确度,冷却系统结构上满足冷却均匀,水循环呈螺旋流通。成型温度:170-250℃,则初定成型温度为180℃,冷却温度用水。
如图所示,水套和型芯之间半圆孔就是螺旋形冷却通道。
6. 型芯设计
型芯为圆柱形状,内部有水套以及通过的连接柱,上端为推块并与型芯端面光滑平整,保证塑件成型与精度。斜度取值8。,抽芯距为4mm ,则侧型芯顶出距离为28.46mm 。
7. 一些标准件选取
浇口套:基本尺寸25,极限偏差+0.015
+0.002,头部外径30,内径3.2,浇口球面半径19,总长50. 限位钉:选择以下两种
圆柱销:选用长度为25,30,35,50几种规格