【EP3546069A1】SPRAYGUNANDCOMPONENTSFORSPRAYINGPAINT
非干扰分析燃油喷射特性的灵活测试系统说明书
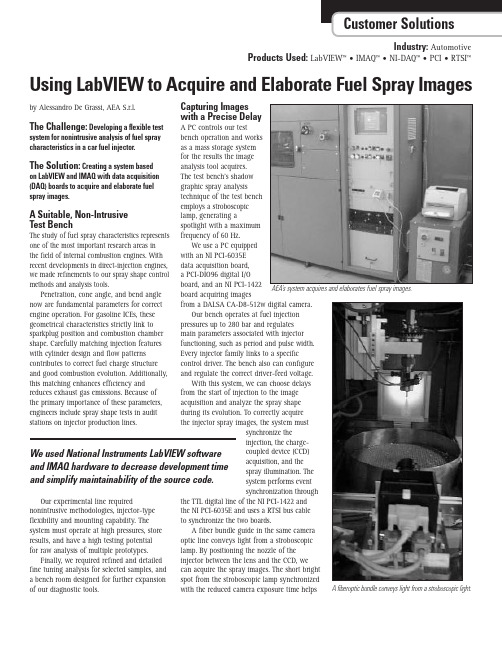
by Alessandro De Grassi, AEA S.r.l.The Challenge:Developing a flexible test system for nonintrusive analysis of fuel spray characteristics in a car fuel injector.The Solution:Creating a system basedon LabVIEW and IMAQ with data acquisition (DAQ) boards to acquire and elaborate fuel spray images.A Suitable, Non-IntrusiveTest BenchThe study of fuel spray characteristics represents one of the most important research areas in the field of internal combustion engines. With recent developments in direct-injection engines, we made refinements to our spray shape control methods and analysis tools.Penetration, cone angle, and bend angle now are fundamental parameters for correct engine operation. For gasoline ICEs, these geometrical characteristics strictly link to sparkplug position and combustion chamber shape. Carefully matching injection features with cylinder design and flow patterns contributes to correct fuel charge structure and good combustion evolution. Additionally, this matching enhances efficiency and reduces exhaust gas emissions. Because of the primary importance of these parameters, engineers include spray shape tests in audit stations on injector production lines.Our experimental line required nonintrusive methodologies, injector-typeflexibility and mounting capability. The system must operate at high pressures, store results, and have a high testing potentialfor raw analysis of multiple prototypes.Finally, we required refined and detailed fine tuning analysis for selected samples, and a bench room designed for further expansion of our diagnostic tools.Capturing Imageswith a Precise DelayA PC controls our testbench operation and worksas a mass storage systemfor the results the imageanalysis tool acquires.The test bench’s shadowgraphic spray analysistechnique of the test benchemploys a stroboscopiclamp, generating aspotlight with a maximumfrequency of 60 Hz.We use a PC equippedwith an NI PCI-6035Edata acquisition board,a PCI-DIO96 digital I/Oboard, and an NI PCI-1422board acquiring imagesfrom a DALSA CA-D8-512w digital camera.Our bench operates at fuel injectionpressures up to 280 bar and regulatesmain parameters associated with injectorfunctioning, such as period and pulse width.Every injector family links to a specificcontrol driver. The bench also can configureand regulate the correct driver-feed voltage.With this system, we can choose delaysfrom the start of injection to the imageacquisition and analyze the spray shapeduring its evolution. To correctly acquirethe injector spray images, the system mustsynchronize theinjection, the charge-coupled device (CCD)acquisition, and thespray illumination. Thesystem performs eventsynchronization throughthe TTL digital line of the NI PCI-1422 andthe NI PCI-6035E and uses a RTSI bus cableto synchronize the two boards.A fiber bundle guide in the same cameraoptic line conveys light from a stroboscopiclamp. By positioning the nozzle of theinjector between the lens and the CCD, wecan acquire the spray images. The short brightspot from the stroboscopic lamp synchronizedwith the reduced camera exposure time helpsIndustry: Automotive Products Used: LabVIEW™• IMAQ™• NI-DAQ™• PCI • RTSI™We used National Instruments LabVIEW software and IMAQ hardware to decrease development time and simplify maintainability of the source code.Using LabVIEW to Acquire and Elaborate Fuel Spray ImagesAEA’s system acquires and elaborates fuel spray images.A fiberoptic bundle conveys light from a stroboscopic light.us acquire clear images of the spray as it appears dark on a white background. For the measurement systems, the 60 Hzoutput of the light source limits the image acquisition frequency. As a result, the system carries out spray behavior analysis through “common averages.” A study on the evolution of the single-event injection requires a high-acquisition frequency of thousands of frames per second. Tocharacterize the spray average behavior, we acquire different images with a precise delay respective to a fixed event. Forexample, we consider the signal arriving at the injector’s control driver as the start of the trigger chain. After image acquisition, the PC converts them to a digital format and calculates the intensity average value of each pixel, resulting in an average image with a precise delay. By repeating the procedure for different delays, we receive a complete characterization of the spray average evolution.Once the system acquires the images, we extract the spray geometrical characteristics. The system then:• Sharply separates the image of the spray from the background using the binarization procedure • Coordinates computation• Measures the geometrical parameterssetups and verifies thehardware bench status with the software utilities.We used National Instruments LabVIEW software and IMAQ hardware to decreasedevelopment time and simplify maintainabilty of the source code. We separated the benchmanagement from the acquisition and elaboration of the spray images with modular software. With the NI PCI-1422 frame grabber and NI-IMAQ driver, we can separate the CCD software from the hardware, so we can replace the CCD camera,now a DALSA CA-D8, with another model to improve the image characteristics.The modularity of the software eases the development of new types of analysis and measurements, so we can adapt to the market’s demands. ■For more information, contact Alessandro De Grassi, AEA S.r.l.,Via Fiume 16,Angeli di Rosora (AN), Tel: 0731/816282,E-Mail:************************361815A -01*361815A -01041503AEA acquires different images with a precise delay.© 2002 National Instruments Corporation. All rights reserved. Product and company names listed are trademarks or trade names of their respective companies.Tel: 02 41309215 • Fax: 02 41309215 • Tel: 06 520871 (Roma)***************•/italy。
使用喷枪(Spraygun)时所需注意的八大点-中英对照
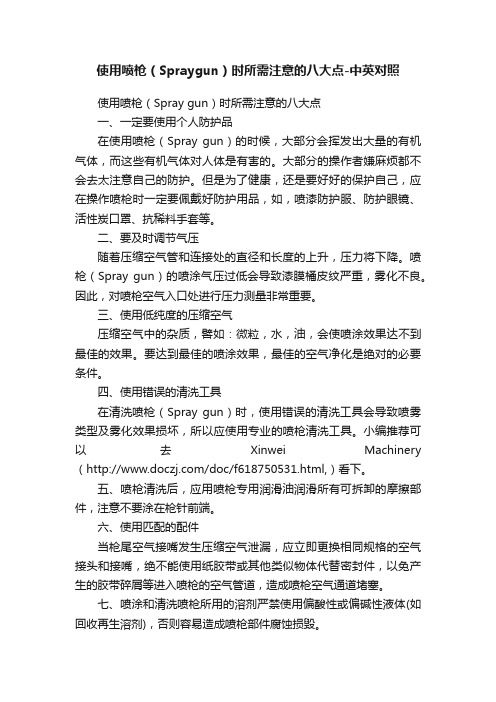
使用喷枪(Spraygun)时所需注意的八大点-中英对照使用喷枪(Spray gun)时所需注意的八大点一、一定要使用个人防护品在使用喷枪(Spray gun)的时候,大部分会挥发出大量的有机气体,而这些有机气体对人体是有害的。
大部分的操作者嫌麻烦都不会去太注意自己的防护。
但是为了健康,还是要好好的保护自己,应在操作喷枪时一定要佩戴好防护用品,如,喷漆防护服、防护眼镜、活性炭口罩、抗稀料手套等。
二、要及时调节气压随着压缩空气管和连接处的直径和长度的上升,压力将下降。
喷枪(Spray gun)的喷涂气压过低会导致漆膜橘皮纹严重,雾化不良。
因此,对喷枪空气入口处进行压力测量非常重要。
三、使用低纯度的压缩空气压缩空气中的杂质,譬如:微粒,水,油,会使喷涂效果达不到最佳的效果。
要达到最佳的喷涂效果,最佳的空气净化是绝对的必要条件。
四、使用错误的清洗工具在清洗喷枪(Spray gun)时,使用错误的清洗工具会导致喷雾类型及雾化效果损坏,所以应使用专业的喷枪清洗工具。
小编推荐可以去Xinwei Machinery (/doc/f618750531.html,)看下。
五、喷枪清洗后,应用喷枪专用润滑油润滑所有可拆卸的摩擦部件,注意不要涂在枪针前端。
六、使用匹配的配件当枪尾空气接嘴发生压缩空气泄漏,应立即更换相同规格的空气接头和接嘴,绝不能使用纸胶带或其他类似物体代替密封件,以免产生的胶带碎屑等进入喷枪的空气管道,造成喷枪空气通道堵塞。
七、喷涂和清洗喷枪所用的溶剂严禁使用偏酸性或偏碱性液体(如回收再生溶剂),否则容易造成喷枪部件腐蚀损毁。
八、使用数字喷枪(Spray gun)时,除非更换电池,否则不得打开电池盒!每次打开电池盒,都必须更换整套电池套装。
如果使用已用过的电池盒密封盖,会造成电池密封不严,同时产品无权享受保修。
Eight Points for Attention when using the spray gunFirst, we must use personal protectionWhen using the spray gun, a large majority of the volatile organic gases and organic gases which are harmful to human body. Most of the operators will not be bothered too much attention to their protection. However, to health, or have to carry to protect themselves, should be in operation when the gun must wear good protective equipment, such as, painting protective clothing, safety glasses, activated carbon masks, anti-thinner gloves.Second, to timely adjust air pressureJunction with the compressed air pipe and the diameter and length increase, the pressure will drop. Low pressure spray gun paint orange peel pattern will lead to serious adverse atomization. Therefore, at the entrance to the air gun pressure measurement is very important.Third, the use of low purity of compressed airCompressed air impurities, such as: particles, water, oil, spray effects will not achieve optimal results. Spray to achieve the best results, the best air purification is an absolute requirement.Fourth, using the wrong cleaning toolWhen the Spray gun cleaning, use the wrong type of cleaning tool will lead to spray and spray effect damage, so you should use a professional spray gun cleaning tool.Writer recommended to go Xinwei Machinery (/doc/f618750531.html,) see next.Fifth, spray gun cleaning, the application of special oil spraylubrication friction of all removable parts, be careful not to spread on the front needle gun.Sixth, using the matching accessoriesWhen the gun air filter tipped tail compressed air leak occurs, immediately replace the same specifications and tipped the air connector, can not paper tape, or other similar objects instead of seals to avoid debris from entering the tape gun in the air duct, channel blockage caused by the air gun.Seventh, spraying and gun cleaning solvents used in non-acidic or alkaline to use liquid (such as recycling solvent), or likely to cause corrosion damage to gun parts.Eighth, Digital spray gun, unless replacement battery, you may not open the battery box! Each time you open the battery box, must replace the entire battery set. If you have used the battery box lids, will cause the battery Mifengbuyan, while products are not entitled to warranty.。
泵式溅剂器说明书

CAUTIONS Failure to follow m a n u f a c t u r e r s recommendation on use and care of unit will void any expressed or im-plied warranty.Do not use chlo-rine or clorox. It will permanently damage pump system .SPO-0199Rev. 01We would like to congratulate you on the purchase of your new SP1. The sprayer that allows you the easiest, most com-fortable way of carrying out your farm and garden projects with the revolutionary diaphragm pump (patented), that all but eliminates the problems inherent in most sprayers.As a new owner of the skillfully engineered SP1, we strongly recommend you carefully read and follow all the information on this sheet before use, and then save for future reference.Please read the attached trouble shooting guide.HOW TO ASSEMBLE 1.Attach spray wand to spray gun and tighten firmly.2.Take pump handle Kit 7 (solid) and insert into the tube on the pump lever Kit 5 ("T" shape lever on sprayer), you will notice holes drilled through both sides of both the pump handle and the pump lever. Align these holes, take the "R"pin provided and place through the holes. This affixes the handle in place and is ready for use.For storage reverse process and then place "R" pin through the pump lever Kit 5 to keep from losing "R" pin.3.Instructions for installing shoulder strap plastic buckle:First put the sprayer on a hard flat surface, take the white plastic buckle and while holding the sprayer up slightly, place buckle under the tubular metal frame. Slowly push down forcing the frame into the buckle. Repeat the same procedure for other side.HOW TO PREPARE YOUR UNIT FOR USE 1.Remove cap.2.Mix solution in a separate receptacle, following manufacturers directions on the container.3.Pour pre-mixed solutions into sprayer and cap.4.Place sprayer on back and pressurize tank by pumping approximately 10 to 15 times. For best results, the sprayer should be pumped every 5 seconds on a continuous basis. This will maintain your spraying pressure. If you do not pump, you will not have pressure to spray.5.Always oil the seal on cap of unit as well as the check valve, this will extend life of seal and is important for obtaining proper seal with no leaks.6. A unit that has been used with herbicides should never be used to spray insecticides, unless the sprayer has been properly cleaned and all other chemicals neutralized. Failure to do this could cause you to kill plants that have been sprayed. Consult with the manufacturer of the chemicals in use to obtain proper instructions.HOW TO CLEAN AND MAINTAIN 1.Remove cap and pour out remaining solution, then rinse all parts thoroughly with clean water.2.Leaving approximately 1/2 gallon of fresh water in tank, pressurize and flush pumping system by depressing trigger at least 2 minutes, then drain all remaining water.3.Always store tank clean and empty in a dry, shaded location.Before using, filling or cleaning any sprayer, read all parts of the operating instructions.Make sure to set up the sprayer exactly as explained in the printed operating instructions, reminder tags and/or stickers.Wear protective clothing, respirator, gloves, eye protection, etc. whenever using, filling, or cleaning sprayer.Periodically re-grease lid gasket as well as lid vent and pump cylinder, where applicable.To ensure good performance, keep lid vent free of obstruction. Before and after each use, make sure all connections are well tightened. Service and replace worn parts as required.Read and follow all instructions of the chemical suppliers.As a rule, mix your chemicals in a separate container from which to fill the sprayer. Do not mix formulas inside the sprayer.Where an exception is made (e.g. with liquid fertilizers), fill sprayer with water BEFORE adding the active ingredient.Always sift formula through the screen. If there is no built-in strainer, use a screened funnel.Never fill the sprayer with hot liquids. Max. 30ºC, or 85ºF.This sprayer is made to handle agrichemicals in their usual water or oil solutions. Do not use flammable, corrosive or caustic solutions.Never use gasoline or other flammable materials.Before cleaning or servicing the sprayer, allow all pressure to escape. Do not store or transport sprayer under pressure.After each use, wash the sprayer—including hose, lance and shut-off valve—with plenty of fresh water. Unless spraying is to be continued within hours, drain chemical formula and thoroughly rinse the tank and all liquid ducts.Never store chemicals in your sprayer for any length of e the sprayer only for the kind of jobs for which it was designed. When in doubt, ask your dealer.Do not leave the sprayer in reach of children or persons not qualified to handle it in proper fashion.When not in use—and especially during prolonged storage—keep your sprayer in a protected place away from direct solar heat.Make sure the spray hose loops freely without kinking or squeezing.Always use SP Systems original replacement parts.___________________Please read and follow all instructions before using sprayer.The SP0 Backpack Sprayer。
Spray Painting

Spray pump is not properly earthed.
W
2
T
1.17Ensure spray pump is earthed to ship structure on deck.
2.11Before fitting of spray gun and nozzle tip, always shut off air supply to spray pump and lock spray guns.
Expose to air contaminant
Y
2
N
2.12Painters to wear air-fed mask with constant clean air supplied.
2.17Check staging before used.
Health hazard
Z
2
N
2.18Wear proper attire and gloves when handling solvent and spray painting.
2.19Air-fed mask for painter
2.20Cartilage mask for pot men.
批注本地保存成功开通会员云端永久保存去开通
Table 5:Spray Painting
No
Job Scope
Hazards
C
P
Risk Level
Current Control
Additional Control
1.
Set up painting equipment.
Prodigy

Prodigy ® Color-on-Demand ® instant color selector is designed for precision dispensing and ultra-fast contamination-free color change.Features of Prodigy Manual Gun SystemFeatures of Prodigy Manual Gun SystemHDLV technology for more powder with less air Lower powder velocity Higher transfer efficiency (TE) Efficient coating at faster line speeds Better coverage in corners and cavitiesProdigy Color-on-Demand with HDLV ® TechnologyProdigy Color-on-Demand with HDLV (high-density powder, low-volume air) technology is all about ultra-fast color changes in less than 20 seconds for more color changes per shift and higher productivity.The Prodigy Color-on-Demand instant color selector* combined with the Prodigy manual gun system*, provides an integrated solution for precision dispensing and ultra-fast, contamination-free color change.The system features a touch-screen color display with user-configurable buttons that can be set for size and color identification at the touch of a button.Prodigy Color-on-Demand can accommodate up to 28 colors at one time for more color changes per shift, higher throughput, and just-in-time manufacturing for zero inventory and improved production efficiency.Features of Prodigy Color-on-DemandLess than 20-second color change Full-color touch-screen display User-configurable buttonsfor size and color identificationAccommodates up to 28 colors per operator Automatic purge cycle cleans entire feed line from hopper to gunNo manual changing of colors required*Patents applied forProdigy ® manual spray gun is automaticallypurgeable with either continuous or pulse purge.© 2012 Nordson Corporation All Rights Reserved PWL-12-3737 Revised 9/12For more information, speak with your Nordson representative or contact your Nordson regional office.United States Amherst, Ohio+1.800.626.8303 Phone +1.888.229.4580 FaxCanadaMarkham, Ontario+1.905.475.6730 Phone +1.800.463.3200 Phone +1.905.475.8821 FaxEuropeErkrath, Germany+49.211.9205.141 Phone +49.211.9252.148 Fax JapanTokyo, Japan+81.3.5762.2700 Phone +81.3.5762.2701 Fax Asia/Australia/ Latin America Amherst, Ohio+1.440.985.4000 Phone24-hour message service:+1.440.985.4797Prodigy ® Color-on-Demand ®Instant Color SelectorPowder Hopper Color 1Powder Hopper Color 2Powder Hopper Color 3Powder Hopper Color 4Powder Hopper Color 5Powder Hopper Color 6Prodigy Manual GunController(Controls gun and pump)HDLV PumpSuction Line ProdigyColor-On-DemandManifoldScrap to Booth CollectorAccomodates up to 28 colors, loaded and ready to go+1.440.985.4000 Nordson Corporation 300 Nordson DriveAmherst, Ohio 44001, USA。
EPG SPRINT操作说明书综述
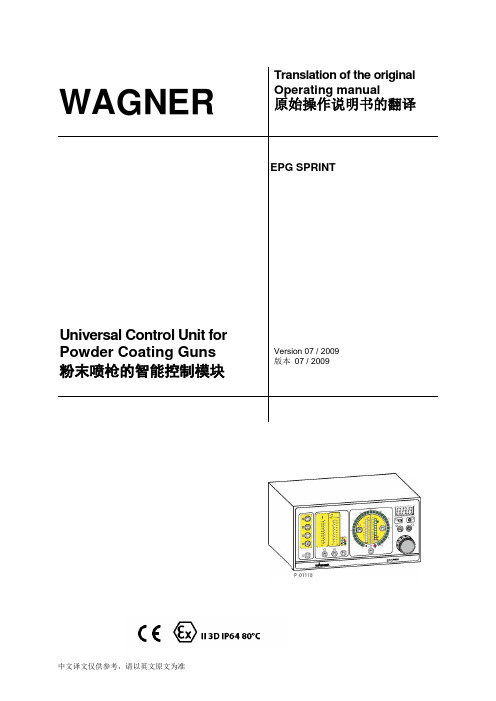
WAGNERTranslation of the original Operating manual原始操作说明书的翻译Universal Control Unit for Powder Coating Guns 粉末喷枪的智能控制模块EPG SPRINTVersion 07 / 2009 版本 07 / 2009VERSION 07/2009 ORDER NUMBER DOC 2305222版本07/2009 订购编号DOC 2305222OPERATING MANUAL 操作说明书Contents 目录1 ABOUT THESE INSTRUCTIONS 5关于操作说明1.1Languages 5语言版本1.2 Warnings, notes and symbols in these instructions 5警告,注意事项以及操作说明中的标记图标2 GENERAL SAFETY INSTRUCTIONS 6一般安全说明2.1 Safety instructions for the operator 6操作人员安全指示2.1.1 Electrical plant and units 6电气设备和装置2.1.2 Personnel qualifications 6操作人员资格2.1.3 A safe work environment 6安全的工作环境2.2 Safety instructions for staff 7工作人员安全指示2.2.1 Safe handling of WAGNER powder spray units 7瓦格纳尔尔粉末喷涂装置的安全使用2.2.2 Earth the unit 7部件接地2.2.3 Material hoses 7原料粉管2.2.4 Cleaning 7清洗2.2.5 Handling powder paints 8操作粉末涂料2.3 Using in accordance with the instructions 8按照说明指示来使用2.4 For use in potentially explosive areas 8潜在爆炸危险区域的使用2.4.1 Using in accordance with the instructions 8按照说明指示来使用2.4.2 Explosion protection identification 8防爆识别2.5 Safety features 9安全特征3 WARRANTY AND DECLARATION OF CONFORMITY 10产品质量保证以及合格证声明3.1 Important notes on product liability 10有关产品责任的重要注意事项3.2 Warranty 10产品质量保证3.3 CE-conformity 11 CE合格证4 DESCRIPTION 13说明4.1 Fields of application, using in accordance with the instructions 13应用领域,严格按照说明指示进行操作4.2 Delivery scope 14配送范围4.3 Technical data 14技术数据4.4 Control functions 16控制功能4.4.1 Operating elements frontside 16操作元件前端正视图4.4.2 Connections on the rear side of the EPG SPRINT unit 20位于EPG SPRINT设备后面板上的接头5 PREPARATIONS FOR STARTING UP 22启动之前的准备工作5.1 Connecting the manual gun 23连接手动喷枪5.2 Connecting the automatic spray guns 24连接自动喷枪5.3 Grounding 25接地5.3.1 Grounding of the powder coating system 26粉末喷涂系统的接地6 STARTING UP AND OPERATING 27启动和操作6.1 Preparations for starting up 27启动之前的准备工作6.1.1 Gun detection 27喷枪检测6.1.2 Basic and factory settings 28基本设置和出厂设置6.2 Coating programs 28喷涂程序6.2.1 “Double click“ program (high dynamic remote) 29“鼠标双击”程序(动态远程)6.3 Air high output mode (high powder output) 30气体高输出模式(高粉末输出)6.3.1 Combining the air outputs 30结合气体输出6.3.2 Activate high output mode (C17) 31激活高输出模式 (C17)3VERSION 07/2009版本07/2009 OPERATING MANUAL 操作说明书ORDER NUMBER DOC 2305222订购编号DOC 2305222EPG-SPRINT.Contents 目录6.4 Changing and saving programs 34更改和保存程序6.4.1 Programs no. 1-4 34程序编号1-46.4.2 Programs no. 5-50 35程序编号5-506.5 Setting and changing the coating parameters 36设置和更改喷涂参数6.5.1 Setting the overall air quantity 36设置总的气体量6.5.2 Setting the powder feed quantity 37设置粉末供应量6.5.3 Setting the additional air (atomizing/ionising/Tribo air quantity) 38设定多余的气体(雾化的/电离的/摩擦气体量)6.5.4 Setting the high-voltage 39设定高电压6.5.5 Display of actual high-voltage value 40实际高压值的显示6.5.6 Setting the current limiting 41设定电流限流值6.5.7 Displaying actual value of current limiting 42真实电流限流值的显示6.5.8 Setting the U/I characteristics 43设置U/I特性6.6 Rinse function 45清洗功能6.6.1 Hose purge function 45粉管清理功能6.6.2 Cleaning purge function 45气洗排除功能6.6.3 Procedure for cleaning purging 46清理冲洗的步骤6.7 Disposal 47处理7 ELIMINATION OF FAULTS 48故障的排除7.1 Warnings E01-E04 48警告E01-E047.2 Malfunctions E11-E43 50功能故障E11-E438 S PA RE PA RTS 52零备件8.1 How to order spare parts? 52如何订购零备件?8.2 EPG SPRINT control unit 53EPG SPRINT控制设备8.3 Accessories 53附件ATTACHMENT DEVICE CONFIGURATION 54附属设备的配置BRIEF DESCRIPTION 63简要说明1 Changing the parameters 64更改参数2 Calling / changing / saving programs 1-4 64调用/更改/保存程序1-43 Calling / changing / saving programs 5-50 64调用/更改/保存程序5-504VERSION 07/2009版本07/2009 OPERATING MANUAL 操作说明书ORDER NUMBER DOC 2305222订购编号DOC 2305222EPG-SPRINT.1 ABOUT THESE INSTRUCTIONS关于操作说明This operating manual contains information on the operation, repair and maintenance ofthe unit.此操作说明书包含元件操作,修理以及日常维护的相关信息。
Airofog CS-series压缩喷雾器说明书
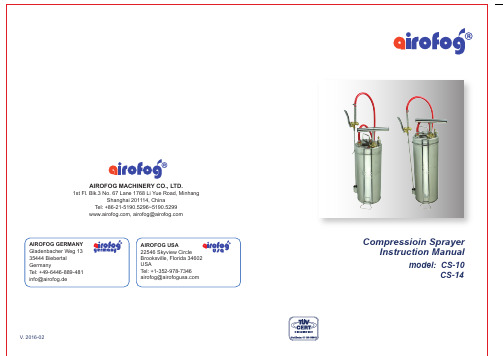
Airofog CS-series compression sprayer 8.5 liter and 10 liter referred to in this document are designed for use by qualified and experienced personnel. Please read this instruction thoroughly before usage.Safety Instruction● Keep out of reach of children.● Before usage, check condition and proper function of the sprayer.● Only pumping up and using sprayer in upright or vertically hanging position.● Do not leave sprayer filled with pesticide in the sun.● Note the wind direction, do not spray against wind and prevent droplets from drifting onto areas which must not be treated.● Never spray into electric outlets or cable boxes.● Do not spray to person or pet.● Do not operate the sprayer if there are visible symptoms of a problem.● Wear personal protective equipment when handling dangerous substances.● Application of insecticides should follow recommendations of manufacturers and be in compliance with local regulations controlling the application ofpesticides. We are not liable for consequence of improper applications.● When unscrewing, never point the lance at others or yourselves.● Never blow through clogged nozzles or valves with the mouth.● Before repair and maintenance, drain the sprayer and release all pressure.● Always replace damaged or malfunctioning parts immediately.OperationA) open tank lid● release the tank pressure by rotating the twist handle to open position● open the tank lidB) filling & mixing chemicals● always follow label instructions when mixing insecticides● measure liquid quantity to meet actual requirements● first fill half of the required water into the tank● add the insecticide according to correct proportion● close filler opening● shake the mixture● open filler opening● add the remaining amount of water and close filler openingC) close tank lid● replace the tank lid and secure position by rotating the twist handleD) pressurize the sprayer● unlock the pump handle by turning locking lever● pump plunger up and down until the required pressure is reached● lock the pump handle by turning locking leverRepair and Spare Part● do not modify the sprayer, this may cause a risk of harm and may damage the sprayer● if any part shows signs of damage or wear, replace it immediately● always use original spare parts for repair or maintenanceCautions:It is the operator’s responsibility to ensure the safe use of sprayer and he is fully compliant with national or local regulations governing compression sprayer and application of pesticide.AIROFOG is not liable for damages or consequences occurred due to improper use/repair/maintenance, the use of non-recommended/unoriginal parts, and acceptance of damaged/broken sprayers by any reason.Care and MaintenanceA) After using:● empty the tank and drain the hose and lance after each use● carefully inspect all gaskets and hoses as well as all other fittingsof wear and tear,replace when necessary.B) Cleaning the sprayer● rinse the tank thoroughly with water● add water and detergent into the tank● attach pump cap and tighten it● shake to clean the tank● pressurize the tank● flush the hose and nozzle● empty the tank and refill with clean water● flush the hose and trigger valve once more● empty the remaining water● the sprayer should be cleaned thoroughly at least once a weekC) Cleaning clogged nozzle● do not insert metal objects into the tip orifices● clean with a soft bristle brush such as a tooth-brush to free clogs● cleaning detergents or solvents can be used to soak the tip(do not use ammonia – it can corrode brass)● soak the nozzle in warm, soapy water● blow compressed air through back of nozzleD) Maintenance of pump and trigger valve● pump cup (1.7) and trigger valve o-ring (9.6) should be oiled from time to time ● check valve at the bottom of the pump cylinder prevents liquid from entering the pump, if liquid leaks into the pump, the valve should be inspected orreplaced● if liquid leaks out of the trigger valve or any connection, the valve seal/gasket or the connection should be inspected or replaced● if air leaks can not be easily located, test the fitting by applying a soapysolution Specification※ Specifications subject to change without notice or obligation.NOTE: CONVERSION FACTORS:1 yard = 3 feet = 0.91 metre1 metre = 39.37 inches = 1.09 yards1 metre/sec = 2.237 miles per hr = 196.9 ft/min1 US gal = 0.83 Imp gal = 3.78 litres1 Imp gal = 1.20 US gals = 4.54 litres1 litre = 0.26 US gal = 0.22 Imp gal1 US pint = 16 US fl ounces = 0.47 litre1 Imp pint = 20 Imp fl ounces = 0.57 litre1 pound = 16 ounces = 0.45 kilogram1 kilogram = 2.20 pounds = 35.3 ounces1 ounce = 28.35 grams1 pound/sq inch = 0.068 atmosphere = 0.067 bar1 atmosphere = 14.70 pounds/sq in = 1.01 bar1 bar = 14.50 pounds/sq in = 0.98 atmosphere1 kilopascal = 0.01 bar = 0.145 pounds/sq in。
OSHA现场作业手册说明书
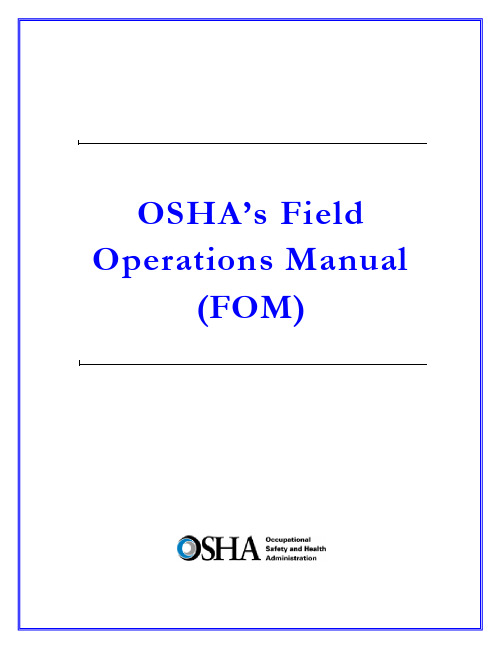
DIRECTIVE NUMBER: CPL 02-00-150 EFFECTIVE DATE: April 22, 2011 SUBJECT: Field Operations Manual (FOM)ABSTRACTPurpose: This instruction cancels and replaces OSHA Instruction CPL 02-00-148,Field Operations Manual (FOM), issued November 9, 2009, whichreplaced the September 26, 1994 Instruction that implemented the FieldInspection Reference Manual (FIRM). The FOM is a revision of OSHA’senforcement policies and procedures manual that provides the field officesa reference document for identifying the responsibilities associated withthe majority of their inspection duties. This Instruction also cancels OSHAInstruction FAP 01-00-003 Federal Agency Safety and Health Programs,May 17, 1996 and Chapter 13 of OSHA Instruction CPL 02-00-045,Revised Field Operations Manual, June 15, 1989.Scope: OSHA-wide.References: Title 29 Code of Federal Regulations §1903.6, Advance Notice ofInspections; 29 Code of Federal Regulations §1903.14, Policy RegardingEmployee Rescue Activities; 29 Code of Federal Regulations §1903.19,Abatement Verification; 29 Code of Federal Regulations §1904.39,Reporting Fatalities and Multiple Hospitalizations to OSHA; and Housingfor Agricultural Workers: Final Rule, Federal Register, March 4, 1980 (45FR 14180).Cancellations: OSHA Instruction CPL 02-00-148, Field Operations Manual, November9, 2009.OSHA Instruction FAP 01-00-003, Federal Agency Safety and HealthPrograms, May 17, 1996.Chapter 13 of OSHA Instruction CPL 02-00-045, Revised FieldOperations Manual, June 15, 1989.State Impact: Notice of Intent and Adoption required. See paragraph VI.Action Offices: National, Regional, and Area OfficesOriginating Office: Directorate of Enforcement Programs Contact: Directorate of Enforcement ProgramsOffice of General Industry Enforcement200 Constitution Avenue, NW, N3 119Washington, DC 20210202-693-1850By and Under the Authority ofDavid Michaels, PhD, MPHAssistant SecretaryExecutive SummaryThis instruction cancels and replaces OSHA Instruction CPL 02-00-148, Field Operations Manual (FOM), issued November 9, 2009. The one remaining part of the prior Field Operations Manual, the chapter on Disclosure, will be added at a later date. This Instruction also cancels OSHA Instruction FAP 01-00-003 Federal Agency Safety and Health Programs, May 17, 1996 and Chapter 13 of OSHA Instruction CPL 02-00-045, Revised Field Operations Manual, June 15, 1989. This Instruction constitutes OSHA’s general enforcement policies and procedures manual for use by the field offices in conducting inspections, issuing citations and proposing penalties.Significant Changes∙A new Table of Contents for the entire FOM is added.∙ A new References section for the entire FOM is added∙ A new Cancellations section for the entire FOM is added.∙Adds a Maritime Industry Sector to Section III of Chapter 10, Industry Sectors.∙Revises sections referring to the Enhanced Enforcement Program (EEP) replacing the information with the Severe Violator Enforcement Program (SVEP).∙Adds Chapter 13, Federal Agency Field Activities.∙Cancels OSHA Instruction FAP 01-00-003, Federal Agency Safety and Health Programs, May 17, 1996.DisclaimerThis manual is intended to provide instruction regarding some of the internal operations of the Occupational Safety and Health Administration (OSHA), and is solely for the benefit of the Government. No duties, rights, or benefits, substantive or procedural, are created or implied by this manual. The contents of this manual are not enforceable by any person or entity against the Department of Labor or the United States. Statements which reflect current Occupational Safety and Health Review Commission or court precedents do not necessarily indicate acquiescence with those precedents.Table of ContentsCHAPTER 1INTRODUCTIONI.PURPOSE. ........................................................................................................... 1-1 II.SCOPE. ................................................................................................................ 1-1 III.REFERENCES .................................................................................................... 1-1 IV.CANCELLATIONS............................................................................................. 1-8 V. ACTION INFORMATION ................................................................................. 1-8A.R ESPONSIBLE O FFICE.......................................................................................................................................... 1-8B.A CTION O FFICES. .................................................................................................................... 1-8C. I NFORMATION O FFICES............................................................................................................ 1-8 VI. STATE IMPACT. ................................................................................................ 1-8 VII.SIGNIFICANT CHANGES. ............................................................................... 1-9 VIII.BACKGROUND. ................................................................................................. 1-9 IX. DEFINITIONS AND TERMINOLOGY. ........................................................ 1-10A.T HE A CT................................................................................................................................................................. 1-10B. C OMPLIANCE S AFETY AND H EALTH O FFICER (CSHO). ...........................................................1-10B.H E/S HE AND H IS/H ERS ..................................................................................................................................... 1-10C.P ROFESSIONAL J UDGMENT............................................................................................................................... 1-10E. W ORKPLACE AND W ORKSITE ......................................................................................................................... 1-10CHAPTER 2PROGRAM PLANNINGI.INTRODUCTION ............................................................................................... 2-1 II.AREA OFFICE RESPONSIBILITIES. .............................................................. 2-1A.P ROVIDING A SSISTANCE TO S MALL E MPLOYERS. ...................................................................................... 2-1B.A REA O FFICE O UTREACH P ROGRAM. ............................................................................................................. 2-1C. R ESPONDING TO R EQUESTS FOR A SSISTANCE. ............................................................................................ 2-2 III. OSHA COOPERATIVE PROGRAMS OVERVIEW. ...................................... 2-2A.V OLUNTARY P ROTECTION P ROGRAM (VPP). ........................................................................... 2-2B.O NSITE C ONSULTATION P ROGRAM. ................................................................................................................ 2-2C.S TRATEGIC P ARTNERSHIPS................................................................................................................................. 2-3D.A LLIANCE P ROGRAM ........................................................................................................................................... 2-3 IV. ENFORCEMENT PROGRAM SCHEDULING. ................................................ 2-4A.G ENERAL ................................................................................................................................................................. 2-4B.I NSPECTION P RIORITY C RITERIA. ..................................................................................................................... 2-4C.E FFECT OF C ONTEST ............................................................................................................................................ 2-5D.E NFORCEMENT E XEMPTIONS AND L IMITATIONS. ....................................................................................... 2-6E.P REEMPTION BY A NOTHER F EDERAL A GENCY ........................................................................................... 2-6F.U NITED S TATES P OSTAL S ERVICE. .................................................................................................................. 2-7G.H OME-B ASED W ORKSITES. ................................................................................................................................ 2-8H.I NSPECTION/I NVESTIGATION T YPES. ............................................................................................................... 2-8 V.UNPROGRAMMED ACTIVITY – HAZARD EVALUATION AND INSPECTION SCHEDULING ............................................................................ 2-9 VI.PROGRAMMED INSPECTIONS. ................................................................... 2-10A.S ITE-S PECIFIC T ARGETING (SST) P ROGRAM. ............................................................................................. 2-10B.S CHEDULING FOR C ONSTRUCTION I NSPECTIONS. ..................................................................................... 2-10C.S CHEDULING FOR M ARITIME I NSPECTIONS. ............................................................................. 2-11D.S PECIAL E MPHASIS P ROGRAMS (SEP S). ................................................................................... 2-12E.N ATIONAL E MPHASIS P ROGRAMS (NEP S) ............................................................................... 2-13F.L OCAL E MPHASIS P ROGRAMS (LEP S) AND R EGIONAL E MPHASIS P ROGRAMS (REP S) ............ 2-13G.O THER S PECIAL P ROGRAMS. ............................................................................................................................ 2-13H.I NSPECTION S CHEDULING AND I NTERFACE WITH C OOPERATIVE P ROGRAM P ARTICIPANTS ....... 2-13CHAPTER 3INSPECTION PROCEDURESI.INSPECTION PREPARATION. .......................................................................... 3-1 II.INSPECTION PLANNING. .................................................................................. 3-1A.R EVIEW OF I NSPECTION H ISTORY .................................................................................................................... 3-1B.R EVIEW OF C OOPERATIVE P ROGRAM P ARTICIPATION .............................................................................. 3-1C.OSHA D ATA I NITIATIVE (ODI) D ATA R EVIEW .......................................................................................... 3-2D.S AFETY AND H EALTH I SSUES R ELATING TO CSHO S.................................................................. 3-2E.A DVANCE N OTICE. ................................................................................................................................................ 3-3F.P RE-I NSPECTION C OMPULSORY P ROCESS ...................................................................................................... 3-5G.P ERSONAL S ECURITY C LEARANCE. ................................................................................................................. 3-5H.E XPERT A SSISTANCE. ........................................................................................................................................... 3-5 III. INSPECTION SCOPE. ......................................................................................... 3-6A.C OMPREHENSIVE ................................................................................................................................................... 3-6B.P ARTIAL. ................................................................................................................................................................... 3-6 IV. CONDUCT OF INSPECTION .............................................................................. 3-6A.T IME OF I NSPECTION............................................................................................................................................. 3-6B.P RESENTING C REDENTIALS. ............................................................................................................................... 3-6C.R EFUSAL TO P ERMIT I NSPECTION AND I NTERFERENCE ............................................................................. 3-7D.E MPLOYEE P ARTICIPATION. ............................................................................................................................... 3-9E.R ELEASE FOR E NTRY ............................................................................................................................................ 3-9F.B ANKRUPT OR O UT OF B USINESS. .................................................................................................................... 3-9G.E MPLOYEE R ESPONSIBILITIES. ................................................................................................. 3-10H.S TRIKE OR L ABOR D ISPUTE ............................................................................................................................. 3-10I. V ARIANCES. .......................................................................................................................................................... 3-11 V. OPENING CONFERENCE. ................................................................................ 3-11A.G ENERAL ................................................................................................................................................................ 3-11B.R EVIEW OF A PPROPRIATION A CT E XEMPTIONS AND L IMITATION. ..................................................... 3-13C.R EVIEW S CREENING FOR P ROCESS S AFETY M ANAGEMENT (PSM) C OVERAGE............................. 3-13D.R EVIEW OF V OLUNTARY C OMPLIANCE P ROGRAMS. ................................................................................ 3-14E.D ISRUPTIVE C ONDUCT. ...................................................................................................................................... 3-15F.C LASSIFIED A REAS ............................................................................................................................................. 3-16VI. REVIEW OF RECORDS. ................................................................................... 3-16A.I NJURY AND I LLNESS R ECORDS...................................................................................................................... 3-16B.R ECORDING C RITERIA. ...................................................................................................................................... 3-18C. R ECORDKEEPING D EFICIENCIES. .................................................................................................................. 3-18 VII. WALKAROUND INSPECTION. ....................................................................... 3-19A.W ALKAROUND R EPRESENTATIVES ............................................................................................................... 3-19B.E VALUATION OF S AFETY AND H EALTH M ANAGEMENT S YSTEM. ....................................................... 3-20C.R ECORD A LL F ACTS P ERTINENT TO A V IOLATION. ................................................................................. 3-20D.T ESTIFYING IN H EARINGS ................................................................................................................................ 3-21E.T RADE S ECRETS. ................................................................................................................................................. 3-21F.C OLLECTING S AMPLES. ..................................................................................................................................... 3-22G.P HOTOGRAPHS AND V IDEOTAPES.................................................................................................................. 3-22H.V IOLATIONS OF O THER L AWS. ....................................................................................................................... 3-23I.I NTERVIEWS OF N ON-M ANAGERIAL E MPLOYEES .................................................................................... 3-23J.M ULTI-E MPLOYER W ORKSITES ..................................................................................................................... 3-27 K.A DMINISTRATIVE S UBPOENA.......................................................................................................................... 3-27 L.E MPLOYER A BATEMENT A SSISTANCE. ........................................................................................................ 3-27 VIII. CLOSING CONFERENCE. .............................................................................. 3-28A.P ARTICIPANTS. ..................................................................................................................................................... 3-28B.D ISCUSSION I TEMS. ............................................................................................................................................ 3-28C.A DVICE TO A TTENDEES .................................................................................................................................... 3-29D.P ENALTIES............................................................................................................................................................. 3-30E.F EASIBLE A DMINISTRATIVE, W ORK P RACTICE AND E NGINEERING C ONTROLS. ............................ 3-30F.R EDUCING E MPLOYEE E XPOSURE. ................................................................................................................ 3-32G.A BATEMENT V ERIFICATION. ........................................................................................................................... 3-32H.E MPLOYEE D ISCRIMINATION .......................................................................................................................... 3-33 IX. SPECIAL INSPECTION PROCEDURES. ...................................................... 3-33A.F OLLOW-UP AND M ONITORING I NSPECTIONS............................................................................................ 3-33B.C ONSTRUCTION I NSPECTIONS ......................................................................................................................... 3-34C. F EDERAL A GENCY I NSPECTIONS. ................................................................................................................. 3-35CHAPTER 4VIOLATIONSI. BASIS OF VIOLATIONS ..................................................................................... 4-1A.S TANDARDS AND R EGULATIONS. .................................................................................................................... 4-1B.E MPLOYEE E XPOSURE. ........................................................................................................................................ 4-3C.R EGULATORY R EQUIREMENTS. ........................................................................................................................ 4-6D.H AZARD C OMMUNICATION. .............................................................................................................................. 4-6E. E MPLOYER/E MPLOYEE R ESPONSIBILITIES ................................................................................................... 4-6 II. SERIOUS VIOLATIONS. .................................................................................... 4-8A.S ECTION 17(K). ......................................................................................................................... 4-8B.E STABLISHING S ERIOUS V IOLATIONS ............................................................................................................ 4-8C. F OUR S TEPS TO BE D OCUMENTED. ................................................................................................................... 4-8 III. GENERAL DUTY REQUIREMENTS ............................................................. 4-14A.E VALUATION OF G ENERAL D UTY R EQUIREMENTS ................................................................................. 4-14B.E LEMENTS OF A G ENERAL D UTY R EQUIREMENT V IOLATION.............................................................. 4-14C. U SE OF THE G ENERAL D UTY C LAUSE ........................................................................................................ 4-23D.L IMITATIONS OF U SE OF THE G ENERAL D UTY C LAUSE. ..............................................................E.C LASSIFICATION OF V IOLATIONS C ITED U NDER THE G ENERAL D UTY C LAUSE. ..................F. P ROCEDURES FOR I MPLEMENTATION OF S ECTION 5(A)(1) E NFORCEMENT ............................ 4-25 4-27 4-27IV.OTHER-THAN-SERIOUS VIOLATIONS ............................................... 4-28 V.WILLFUL VIOLATIONS. ......................................................................... 4-28A.I NTENTIONAL D ISREGARD V IOLATIONS. ..........................................................................................4-28B.P LAIN I NDIFFERENCE V IOLATIONS. ...................................................................................................4-29 VI. CRIMINAL/WILLFUL VIOLATIONS. ................................................... 4-30A.A REA D IRECTOR C OORDINATION ....................................................................................................... 4-31B.C RITERIA FOR I NVESTIGATING P OSSIBLE C RIMINAL/W ILLFUL V IOLATIONS ........................ 4-31C. W ILLFUL V IOLATIONS R ELATED TO A F ATALITY .......................................................................... 4-32 VII. REPEATED VIOLATIONS. ...................................................................... 4-32A.F EDERAL AND S TATE P LAN V IOLATIONS. ........................................................................................4-32B.I DENTICAL S TANDARDS. .......................................................................................................................4-32C.D IFFERENT S TANDARDS. .......................................................................................................................4-33D.O BTAINING I NSPECTION H ISTORY. .....................................................................................................4-33E.T IME L IMITATIONS..................................................................................................................................4-34F.R EPEATED V. F AILURE TO A BATE....................................................................................................... 4-34G. A REA D IRECTOR R ESPONSIBILITIES. .............................................................................. 4-35 VIII. DE MINIMIS CONDITIONS. ................................................................... 4-36A.C RITERIA ................................................................................................................................................... 4-36B.P ROFESSIONAL J UDGMENT. ..................................................................................................................4-37C. A REA D IRECTOR R ESPONSIBILITIES. .............................................................................. 4-37 IX. CITING IN THE ALTERNATIVE ............................................................ 4-37 X. COMBINING AND GROUPING VIOLATIONS. ................................... 4-37A.C OMBINING. ..............................................................................................................................................4-37B.G ROUPING. ................................................................................................................................................4-38C. W HEN N OT TO G ROUP OR C OMBINE. ................................................................................................4-38 XI. HEALTH STANDARD VIOLATIONS ....................................................... 4-39A.C ITATION OF V ENTILATION S TANDARDS ......................................................................................... 4-39B.V IOLATIONS OF THE N OISE S TANDARD. ...........................................................................................4-40 XII. VIOLATIONS OF THE RESPIRATORY PROTECTION STANDARD(§1910.134). ....................................................................................................... XIII. VIOLATIONS OF AIR CONTAMINANT STANDARDS (§1910.1000) ... 4-43 4-43A.R EQUIREMENTS UNDER THE STANDARD: .................................................................................................. 4-43B.C LASSIFICATION OF V IOLATIONS OF A IR C ONTAMINANT S TANDARDS. ......................................... 4-43 XIV. CITING IMPROPER PERSONAL HYGIENE PRACTICES. ................... 4-45A.I NGESTION H AZARDS. .................................................................................................................................... 4-45B.A BSORPTION H AZARDS. ................................................................................................................................ 4-46C.W IPE S AMPLING. ............................................................................................................................................. 4-46D.C ITATION P OLICY ............................................................................................................................................ 4-46 XV. BIOLOGICAL MONITORING. ...................................................................... 4-47CHAPTER 5CASE FILE PREPARATION AND DOCUMENTATIONI.INTRODUCTION ............................................................................................... 5-1 II.INSPECTION CONDUCTED, CITATIONS BEING ISSUED. .................... 5-1A.OSHA-1 ................................................................................................................................... 5-1B.OSHA-1A. ............................................................................................................................... 5-1C. OSHA-1B. ................................................................................................................................ 5-2 III.INSPECTION CONDUCTED BUT NO CITATIONS ISSUED .................... 5-5 IV.NO INSPECTION ............................................................................................... 5-5 V. HEALTH INSPECTIONS. ................................................................................. 5-6A.D OCUMENT P OTENTIAL E XPOSURE. ............................................................................................................... 5-6B.E MPLOYER’S O CCUPATIONAL S AFETY AND H EALTH S YSTEM. ............................................................. 5-6 VI. AFFIRMATIVE DEFENSES............................................................................. 5-8A.B URDEN OF P ROOF. .............................................................................................................................................. 5-8B.E XPLANATIONS. ..................................................................................................................................................... 5-8 VII. INTERVIEW STATEMENTS. ........................................................................ 5-10A.G ENERALLY. ......................................................................................................................................................... 5-10B.CSHO S SHALL OBTAIN WRITTEN STATEMENTS WHEN: .......................................................................... 5-10C.L ANGUAGE AND W ORDING OF S TATEMENT. ............................................................................................. 5-11D.R EFUSAL TO S IGN S TATEMENT ...................................................................................................................... 5-11E.V IDEO AND A UDIOTAPED S TATEMENTS. ..................................................................................................... 5-11F.A DMINISTRATIVE D EPOSITIONS. .............................................................................................5-11 VIII. PAPERWORK AND WRITTEN PROGRAM REQUIREMENTS. .......... 5-12 IX.GUIDELINES FOR CASE FILE DOCUMENTATION FOR USE WITH VIDEOTAPES AND AUDIOTAPES .............................................................. 5-12 X.CASE FILE ACTIVITY DIARY SHEET. ..................................................... 5-12 XI. CITATIONS. ..................................................................................................... 5-12A.S TATUTE OF L IMITATIONS. .............................................................................................................................. 5-13B.I SSUING C ITATIONS. ........................................................................................................................................... 5-13C.A MENDING/W ITHDRAWING C ITATIONS AND N OTIFICATION OF P ENALTIES. .................................. 5-13D.P ROCEDURES FOR A MENDING OR W ITHDRAWING C ITATIONS ............................................................ 5-14 XII. INSPECTION RECORDS. ............................................................................... 5-15A.G ENERALLY. ......................................................................................................................................................... 5-15B.R ELEASE OF I NSPECTION I NFORMATION ..................................................................................................... 5-15C. C LASSIFIED AND T RADE S ECRET I NFORMATION ...................................................................................... 5-16。
- 1、下载文档前请自行甄别文档内容的完整性,平台不提供额外的编辑、内容补充、找答案等附加服务。
- 2、"仅部分预览"的文档,不可在线预览部分如存在完整性等问题,可反馈申请退款(可完整预览的文档不适用该条件!)。
- 3、如文档侵犯您的权益,请联系客服反馈,我们会尽快为您处理(人工客服工作时间:9:00-18:30)。
[0001] This application claims the benefit of U.S. Pro- 5 between the first end and the second end, a cartridge
visional Application No. 62/651,188 filed April 1, 2018 for
(30) Priority: 01.04.2018 US 201862651188 P 02.01.2019 US 201962787671 P
(74) Representative: Miller Sturt Kenyon 9 John Street London WC1N 2ES (GB)
(54) SPRAY GUN AND COMPONENTS FOR SPRAYING PAINTS AND OTHER COATINGS
(22) Date of filing: 01.04.2019
(51) Int Cl.: B05B 9/01 (2006.01) B05B 12/00 (2018.01)
B05B 1/30 (2006.01)
(84) Designated Contracting States: AL AT BE BG CH CY CZ DE DK EE ES FI FR GB GR HR HU IE IS IT LI LT LU LV MC MK MT NL NO PL PT RO RS SE SI SK SM TR Designated Extension States: BA ME Designated Validation States: KH MA MD TN
outlet extending through the first end, a chamber within
"SPRAY GUN AND COMPONENTS FOR SPRAYING
the housing, and a plurality of ports extending through
PAINTS AND OTHER COATINGS," by J. Johnston and
(57) A spray gun includes a valve cartridge configured to be axially installed and removed as a single piece. The valve cartridge includes the wear components of the spray gun. A trigger of the spray gun is configured to actuate a slider of the valve cartridge to control spraying by the spray gun. The trigger includes arms that are mounted to the spray gun by a pivot mechanism. The pivot mechanism can be disengaged from the arms to allow the trigger to slide between a spray position, where the trigger prevents forward axial movement of the valve cartridge, and a repair position, where the valve cartridge can move axially forward. The trigger also includes upper and lower portions that are movable relative to each other, such that the length of the trigger can be adjusted.
(71) Applicant: Graco Minnesota Inc. Minneapolis, MN 55413 (US)
(72) Inventors: • JOHNSTON, Justin G Rogers, MN Minnesota 55374 (US) • WROBEL, Steve J Rogers, MN Minnesota 55374 (US)
EP 3 546 069 A1
Printed by Jouve, 75001 PARIS (FR)
1
EP 3 546 069 A1
2
Description
a seal assembly disposed within the housing, a spring
disposed within the housing, a slider disposed at least
(19)
TEPZZ¥546Z69A_T
(11)
EP 3 546 069 A1
(12)
EUROPEAN PATENT APPLICATION
(43) Date of publication: 02.10.2019 Bulletin 2019/40
(21) Application number: 19166594.2
CROSS-REFERENCE TO RELATED APPLICATION(S)
partially outside of the housing, and a stem. The housing
has a first end, a second end, a housing body extending
the housing and in fluid communication with the chamber.
S. Wrobel, and of U.S. Provisional Application No.
The seal assembly is configured to control the flow of