AS9100纠正和预防措施程序英文版
as9100内部审核程序英文版
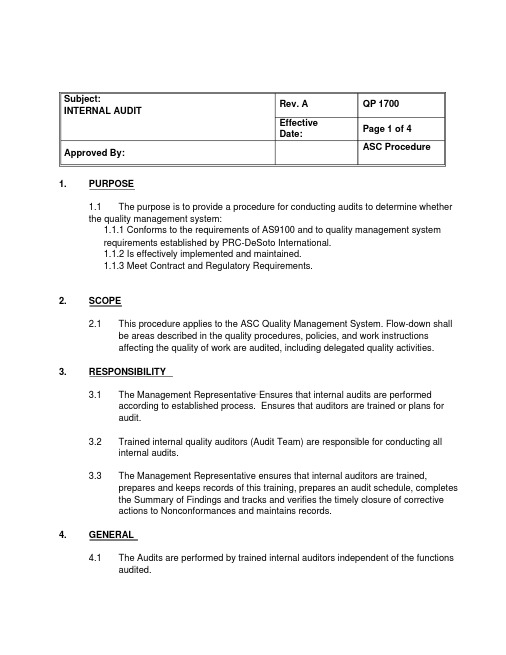
Subject:Rev. A QP 1700INTERNAL AUDITEffectivePage 1 of 4Date:ASC Procedure Approved By:1.PURPOSE1.1The purpose is to provide a procedure for conducting audits to determine whetherthe quality management system:1.1.1 Conforms to the requirements of AS9100 and to quality management systemrequirements established by PRC-DeSoto International.1.1.2 Is effectively implemented and maintained.1.1.3 Meet Contract and Regulatory Requirements.2.SCOPE2.1 This procedure applies to the ASC Quality Management System. Flow-down shallbe areas described in the quality procedures, policies, and work instructionsaffecting the quality of work are audited, including delegated quality activities.3.RESPONSIBILITY3.1 The Management Representative – Ensures that internal audits are performedaccording to established process. Ensures that auditors are trained or plans foraudit.3.2 Trained internal quality auditors (Audit Team) are responsible for conducting allinternal audits.3.3The Management Representative ensures that internal auditors are trained,prepares and keeps records of this training, prepares an audit schedule, completesthe Summary of Findings and tracks and verifies the timely closure of correctiveactions to Nonconformances and maintains records.4.GENERAL4.1 The Audits are performed by trained internal auditors independent of the functionsaudited.INTERNAL AUDITASC Procedure Page 2 of 45.DEFINITIONS5.1Audit - systematic, independent and documented process for obtaining objectiveevidence and evaluating it to determine the extent to which audit criteria arefulfilled.5.2Audit criteria - set of policies, procedures or requirements used as a reference.5.3 Auditor – Person with the competence to conduct an audit.5.4 Audit finding – Results of the evaluation of the collected audit evidence againstthe audit criteria.5.5Objective Evidence – Data that supports the existence of verification ofsomething.5.6Nonconformity – Non-fulfillment of a requirement.6.PROCEDURE6.1The Management Representative plans and implements an audit scheduleensuring that:Quality management system requirements are auditedThe frequency of audit is based on the status and importance of the process(s) andactivity audited as well as previous audit results.T he set time to complete audits iswithin the month assigned.6.2The Management Representative determines the audit scope, audit criteria andassign an auditor(s) for completion of each audit. The selection of auditors for eachassignment ensures objectivity and impartiality of the audit process and those auditors do not audit their own work.6.3Management Representative notifies the department manager of the audit byforwarding a copy of the schedule when developed and revised.6.4The internal auditor contacts the appropriate departments to schedule a pre-auditmeeting where specific audit dates/times based on department and auditor schedules are discussed. Internal auditors perform the audit.INTERNAL AUDITASC Procedure Page 3 of 46.5Auditors performs audits in a structured manner to accomplish the scope of theaudit assignment:Review assignment to determine audit scope, audit criteria.Schedule the audit with the audited.Review audit criteria, such as policies, procedures, contracts, requirements of AS9100and prepare a QPF1700-1 Audit Checklist as appropriate to accomplish audit scope.Hold an opening meeting with audited to explain purpose and scope of the audit.Execute the audit by obtaining sufficient information or objective evidence to permitconclusions to be drawn regarding the conformance/nonconformance andeffectiveness of the area being audit.Collective information and objective evidence through interviews, examination ofdocuments and records, observation of activities and conditions in the areas beingaudited.Record observations for review to determine whether Nonconformances or potentialNonconformances exist.Review observations, taking into account their significance and drawing conclusionsabout conformance/nonconformance and effectiveness of the area at meetingrequirements and achieving quality objectives.Prepare nonconformance reports according to the Corrective and Preventive Actionprocedure taking care to include sufficient details and objective evidence.Hold a closing meeting with the audited to review and clarify the results andconclusions of the audit.Prepare an audit report that summarizes the audit conclusions and forwards to theManagement Representative.Management Representative reviews the audit report and any recordedNonconforming reports; obtains clarification from the auditor(s) as appropriate.6.6 A copy of the Internal Quality Audit Nonconformance Report is sent to the audited,(department manager). The audited investigates findings/observations. Managers review audit findings. The audited completes corrective action responses and send to theManagement Representative for review and approval within stated due date defined in the NCR form. Management Representative input/close audit in the NonconformingDatabase.6.7The Management Representative assigns follow-up/verification of corrective action basedon the estimated completion date determined by the Manager.6.8Internal Quality Audit Nonconformance Reports are reviewed using the Summary ofFindings at the Management Review Meetings. The Management Representative。
不合格纠正及预防措施程序(中英文)

发行日期 (Issuing date)
生效日期 (Effective date)
页 次 (Page) 3/6页 (3 of 6 pages)
负责人 Responsible
person 2.必要时,品
品质部主管人员 Chief person in Quality Dept.
Corrective defect, the Quality Dept. shall send 《Nonconformance Improvement Report》to responsible Dept. action 2. 相关部门或相关责任人在3个工作日内将采取的纠正行动回复给发单部门。
Responsible Dept. or responsilbe person should send corrective action which is taken back to the
审否会则议,前应7在个管
理W评it审hi会n 7议上
wothrekicnogrrdeacytsive
acAtioctniotnaken by
参考文件
Reference document 6.2 预防措
S《h管eet理" s评ho审ul程d 序》
Management Review
施6.2.1 各单
位应根现据或本分
document 6.1.3 成品
"Nonconforma 《检验与试验控制程序》、《生产过程控制程序》 《Inspection and Test Control Procedure》 《Production Process Control Procedure》
检验不合格 1.送检的批量
英文版AS9100质量管理手册

Quality System Manual COLLINS AVIATION MAINTENANCESERVICES (SHANGHAI) LIMITED(Collins Shanghai Service Center)General Factory Building 4, Floor 1Waigaoqiao Free Trade ZonePudong, Shanghai 200131PR ChinaDocument Reference: CAMSSL-QSM-001Date of Original Issue: 8 Oct. 2007Revision: 0Date of Revision: -Quality System ManualCAMSSL-QSM-001 Page: 1Revision HistoryRevision Date: Revision No. Reason For Change: Sep 18, 07 Original Release Original ReleaseQuality System ManualCAMSSL-QSM-001 Page: 2Table of Contents:Paragraph Description Page No. 1.0 Scope 4 2.0 Normative Reference 4 3.0 Terms and Definitions 5 4.0 Quality Management System 5 4.1 General Requirements 5 4.2 Documentation Requirements 5, 6, 7, 8,9 4.3 Configuration Management 10 5.0 Management Responsibility 10 5.1 Management Commitment 10 5.2 Customer Focus 10 5.3 Quality Policy 10, 11 5.4 Planning 11 5.5 Responsibility, Authority and Communication 12, 13, 14 5.6 Management Review 14 6.0 Resource Management 15 6.1 Provision of Resources 15 6.2 Human Resources 15 6.3 Infrastructure 15 6.4 Work Environment 15 7.0 Product Realization 16 7.1 Planning of Product Realization 16 7.2 Customer-Related Processes 16 7.3 Design and Development 16 7.4 Purchasing 17, 18 7.5 Production and Service Provision 19, 20, 21, 22, 23 7.6 Control of Monitoring and Measuring Devices 23, 24 8.0 Measurement, Analysis and Improvement 25 8.1 General 25 8.2 Monitoring and Measurement 25, 26, 27, 28, 29 8.3 Control of Nonconforming Product 30, 31 8.4 Analysis of Data 31 8.5 Improvement 32Attachment Description PageNo. A Flow Chart of Quality Management System 1Appendix Description PageNo. A Cross Reference of QSM Clause 1 to Rockwell Collins Services Procedures.B Cross Reference of Rockwell Collins Services 1, 2, 3, 4 Procedures to QSM Clause.Quality System ManualCAMSSL-QSM-001 Page: 3List of Effective PagesPage Revision Date of Revision RemarkQuality System Manual1.0SCOPE1.1This Quality System Manual applies to all processes performed within the Collins AviationMaintenance Service (Shanghai) Limited (CAMSSL) Centers. The objective of this document is to establish an environment that provides adequate control and accountability to assure that a quality product/service is provided that meets or exceeds customer expectations and assures continual improvement of the quality management system. This Quality System Manual gives a description of the quality System requirements for the Collins Avionics Aviation Maintenance (Shanghai) LTD (Collins Shanghai Service Center):1.2The Collins Aviation Maintenance (Shanghai) Ltd comprise a total of approximately 1500square meter of space. They are accepted by the Federal Aviation Administration (FAA) to FAR-145 and other Non-Collins OEM. Approval for the repair, modification, and maintenance of customer purchased avionics equipment manufactured by Rockwell Collins, Inc.1.3Rockwell Collins, Inc., Rockwell Collins Services, Maintenance Operations, located at 400Collins Road NE, Cedar Rapids, Iowa 52498, is headquarters for Collins Avionics Service Centers located worldwide. Throughout the remainder of this manual Rockwell Collins, Inc. will be referred to as Rockwell Collins and Rockwell Collins, Inc., Rockwell Collins Services, Maintenance Operations will be referred to as Rockwell Collins Maintenance Operations.2.0NORMATIVE REFERENCEThis Quality System Manual has been developed in accordance with the Aerospace Standard AS 9100. It addresses all requirements identified in the Standard and its applicability to the Scope (Paragraph 1.0) and the Rockwell Collins quality management system documented procedures. AS 9100 includes ISO 9001:2000 quality management system requirements and specifies additional requirements for the aerospace industry.3.0TERMS AND DEFINITIONSAll Terms and Definitions are addressed within the Rockwell Collins quality management system documented procedures.4.0QUALITY MANAGEMENT SYSTEM4.0GENERAL REQUIREMENTSThe established quality management system is implemented, documented and maintained in accordance to the aerospace standard AS 9100 quality management system. The quality management system establishes quality objective(s) to support continual improvement in production processes, product quality, and service. Documented processes and their application to the organization have been identified. These processes employ measuring, monitoring and analysis methods in order to identify areas for improvement and to implement actions needed to formalize change. The sequence and interaction of theseCAMSSL-QSM-001Page: 4。
纠正与预防措施控制程序(中英文)

纠正与预防措施控制程序Corrective and Preventive Action Control Procedure1.目的Purpose:及时发现不符合,并采取有效的纠正和预防措施,以消除存在或潜在的不符合原因,实现管理体系的不断完善和持续改进。
To found non-conformity in time, and to take effective corrective and preventive action, that remove the actual or potential non-conformity reasons, to realize the management system is constantly improved and continually improved.2.范围Scope:适用于管理体系运行过程中的改进、纠正和预防措施的制定、实施和验证。
This document applies to the improvement in the process of management system, formulation, implementation and verification of corrective and preventive action.3.术语Terms:纠正—为消除已发现的不符合所采取的措施。
Corrective - the action taken to remove the non-conformity founded.纠正措施—为消除已发现的不合格或其他不期望情况的原因所采取的措施。
Corrective action - the action taken to remove the reason of the non-conformity founded or other not expected situation.预防措施—为消除潜在的不合格或其他潜在不期望情况的原因所采取的措施。
AS9100印章控制程序英文版

1.0PURPOSE1.1.To identify the initials, signature, inspection stamp, and authority of ASC personnelapproving inspections, processing steps and release documentation.2.0SCOPE2.1 This procedure applies to the use of stamps for inspections, processing steps and releasedocuments.3.0RESPONSIBILITY3.1The Quality Control Supervisor/Quality Manager is responsible for tracking of InspectionStamps and determining the limits of stamp authority for personnel who verify, certifyand release product.3.2Quality Control and Manufacturing personnel are responsible for indicating thatinspections were performed by the use of initials or Inspection Stamps.3.3Manufacturing personnel are responsible for indicating the processing steps are completeby the use of initials or Inspection Stamps.3.4Distribution personnel are responsible for indicating approval of release documents.3.5Production Control personnel are responsible for indicating that label inspections wereperformed by use of initials or Inspection Stamps.3.6The Stamp Recipient is responsible for using issued stamps within the limits of authorityand reporting worn or lost stamps.3.7The ASC Management Representative is responsible for maintaining a log of stampsissued, including facsimiles of the impression, along with the initials and signature of the personnel receiving the stamp.4.0GENERAL4.1Personnel who are authorized to perform tests and inspections and approve productand processes are identified in Quality Management System documentation.4.2Prior to issue, each stamp requires documentation defining the limits of its authorityusing a QPF1201-1 Stamp Issue Log form.4.3The stamp recipient is the only individual permitted to use the assigned stamp.4.4Worn stamps are removed from service and replaced.4.5Serial numbers of lost stamps are not reissued.5.0DEFINITIONS5.1Inspection Stamps – Issued to personnel for indicating inspection and acceptancestatus.6.0PROCEDURE6.1Inspection Stamps6.1.1Signatures, initials, and Inspection Stamp samples are entered on theStamp Issue Log (QPF 1201-1), which is maintained by the QualityControl Supervisor/Quality Manager. Unassigned stamps are accountedfor and maintained by the Quality Control Supervisor/Quality Managerand keeps un-assigned stamps in a secure area.6.1.2The Inspection Stamps are numbered are issued to Quality Control,Manufacturing, Production Control and Distribution personnel by theQuality Control Supervisor/Quality Manager. Personnel complete theStamp Issue Log (QPF 1201-1) with name, signature, stamp, initials anddate.6.1.3Quality Control stamps are different fro the rest of the inspection stamps,see Stamp Issue Log (QP 1201-1)6.1.4The Performance of inspections, tests, and processing steps are indicatedby the individual performing the inspection, test, or process. Thestamp/initials are indicated on the quality records traceable to thematerials/products.6.1.5If a stamp becomes worn or lost, Stamp Recipient notifies the QualityControl Supervisor. The Quality Control Supervisor removes the stampnumber from service and issues the individual a new stamp. Upontermination or transfer of an employee, the stamp is returned to theQuality Control Supervisor. The stamp is destroyed,not reissued.6.1.6Stamp legibility and availability is assessed during internal audits of thisprocedure.6.1.6.1 The Audit Team Member contacts each stamp holder and checksthe availability and legibility of the stamp by stamping a copy ofthe ASC Stamp Issue Log (QPF 1201-1) for each stamp issued.Stamps that are illegible are removed from service and destroyed.The numbers for lost stamps are permanently removed fromservice. Worn stamps will be replaced with same number andsymbol.6.2Quality Control Supervisor Signature Stamps6.2.1These stamps are assigned to trained Shipping personnel for thepreparation of release documents such as Certificates of Conformance.Trained personnel act in authority of the Quality Control Supervisor inapproving the release of material through stamping Certificates ofConformance.6.2.2Signature Stamps are used unless the customer requires an originalsignature.7.0REFERENCE DOCUMENTS7.1QPF1201-1 Stamp Issue Log。
纠正和预防措施程序中英文版

1.0 P URPOSE 目的1.1 The procedure defines the process for Corrective &Preventive Action and ContinuousImprovement and makes sure quality and environment management system is on continuingimprovement and continuously meets customer requirements.确定纠正预防和持续改进的流程,确保公司的质量管理体系和环境管理体系是处于持续改进的,不断满足客户需要。
2.0 S COPE 范围2.1 Apply to the products and processes which are related with quality management system andenvironment management system, such as internal products or processes required correctiveaction or improvement, customer complaint, internal/external audit and environmentnonconformity, KPI over target, and etc.适用于公司内质量管理体系和环境管理体系所涉及的产品和过程。
比如要求纠正或改进的产品、过程,客户投诉,内/外部审核和环境不符合,目标未达成,数据分析等。
3.0 D EFINITIONS定义3.1 Correction: action to eliminate a detected nonconformity. A correction can be, for example,rework or re-grade.纠正:为消除已发现的不合格所采取的措施,如返工,降级等。
AS9100-C标准中英文对照

E X T E R N A L D O C UM E N T外来文件Quality Management Systems - Requirements for Aviation, Space and Defense Organizations 1. Scope1.1 GeneralThis standard includes ISO 9001:2008 quality management system requirements and specifies additional aviation, space and defense industry requirements, definitions and notes as shown in bold, italic text.It is emphasized that the requirements specified in thisstandard are complementary (not alternative) to contractual and applicable statutory and regulatory requirements. Should there be a conflict between the requirements of this standard and applicable statutory or regulatory requirements, the latter shall take precedence.This International Standard specifies requirements for a qualitymanagement system where an organizationa) needs to demonstrate its ability to consistently provide product that meets customer and applicable statutory and regulatory requirements, andb) aims to enhance customer satisfaction through the effectiveapplication of the system, including processes for continualimprovement of the system and the assurance of conformity tocustomer and applicable statutory and regulatory requirements.NOTE 1 In this International Standard, the term “product” on ly applies toa) product intended for, or required by, a customer,b) any intended output resulting from the product realizationprocesses.NOTE 2 Statutory and regulatory requirements may be expressed as legalrequirements.1.2 ApplicationAll requirements of this International Standard are generic and are intended to be applicable to all organizations, regardless of type, size and product provided. Where any requirement(s) of this International Standard cannot beapplied due to the nature of an organization and its product, this can be considered for exclusion.Where exclusions are made, claims of conformity to thisInternational Standard are not acceptable unless these exclusions are limited to requirements within clause 7, and such exclusions do not affect the organizations ability, or responsibility, to provide product that meets customer and applicable statutory and regulatory requirements.This standard is intended for use by organizations that design develop and/or produce aviation, space and defense products; 质 量 管 理 体 系 -航 空 , 航 天 和 国 防 组 织 的 要 求1 范 围 1 .1 总 则本 标 准 包 括 I S O 9 0 0 1 :2 0 0 8 质 量 管 理 体 系 要 求 , 规 定 了 附 加 的 航 空 , 航 天 和 国 防 的 行 业 要 求 , 定 义 和 注 释 . 附 加 要 求 以 加 粗 斜 体 表 示 。
AS9100D质量手册英文版

[FULL CLIENT NAME ALL CAPS][Quality Manual Doc Title]Revision [Rev Number]Issued [Date of Issue]Conforms to AS9100 Rev. D and ISO 9001:2015(c) [Copyright Year] [Full Client Name Reg Caps]; all rights reserved. This document may contain proprietary information and may only be released to third parties with approval of management. Document is uncontrolled unless otherwise marked;uncontrolled documents are not subject to update notification.TABLE OF CONTENTS0.0Revision History and Approval (3)1.0Welcome to [Full Client Name Reg Caps] (4)2.0About The [Short Client Name] Quality Manual (4)3.0Terms and Definitions (4)4.0Context of the Organization (5)4.1Understanding the Organization and Its Context (5)4.2Understanding the Needs and Expectations of Interested Parties (5)4.3Determining the Scope of the Quality Management System (5)4.4Quality Management System and Its Processes (6)5.0Leadership (7)5.1Leadership & Commitment (7)5.1.1General (7)5.1.2Customer focus (8)5.2Policy (8)5.3Organizational Roles Responsibilities and Authorities (9)6.0Planning (9)6.1Actions to Address Risks and Opportunities (9)6.2Quality Objectives and Planning to Achieve Them (9)6.3Planning of Changes (10)7.0Support (10)7.1Resources (10)7.1.1General (10)7.1.2People (10)7.1.3Infrastructure (10)7.1.4Environment for the Operation of Processes (11)7.1.5Monitoring and Measuring Resources (11)7.1.6Organizational Knowledge (11)7.2Competence (11)7.3Awareness (11)7.4Communication (12)7.5Documented Information (12)8.0Operation (13)8.1Operational Planning and Control (13)8.1.1 Operational Risk Management (14)8.1.2 Configuration Management (14)8.1.3 Product Safety (14)8.1.4 Prevention of Counterfeit Parts (14)8.2Requirements for Products and Services (14)8.2.1Customer Communication (14)8.2.2Determining the Requirements Related to Products and Services (15)8.2.3Review of Requirements Related to Products and Services (15)8.2.4Changes to Requirements for Products and Services (15)8.3Design and Development of Products and Services (15)8.4Control of Externally Provided Processes, Products and Services (16)8.5Production and Service Provision (16)8.5.1Control of Production and Service Provision (16)8.5.2Identification and Traceability (17)8.5.3Property Belonging to Customers or External Providers (18)8.5.4Preservation (18)8.5.5Post-Delivery Activities (18)8.5.6Control of Changes (19)8.6Release of Products and Services (19)8.7Control of Nonconforming Outputs (20)9.0Performance Evaluation (20)9.1Monitoring, Measurement, Analysis and Evaluation (20)9.1.1General (20)9.1.2Customer Satisfaction (21)9.1.3Analysis and Evaluation (21)9.2Internal Audit (21)9.3Management Review (22)10.0Improvement (22)10.1General (22)10.2Nonconformity and Corrective Action (22)10.3Continual Improvement (22)Appendix A:Overall Process Sequence & Interaction (23)。
AS9100一整套程序文件英文版(航空航天质量体系)
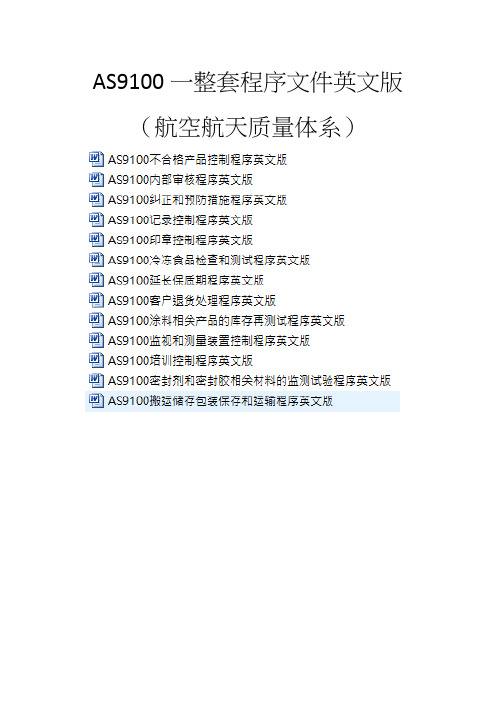
AS9100一整套程序文件英文版(航空航天质量体系)1.0P U R P O S E1.1T o e n s u r e t h a t p r o d u c t t h a t d o e s n o t c o n f o r m t o s p e c i f i e d r e q u i r e m e n t si s p r e v e n t e d f r o m u n i n t e n d e d u s e o r d e l i v e r y.2.0S C O P Ea)2.1T h i s p r o c e d u r e a p p l i e s t o p r o d u c t s t h a t d o n o t c o n f o r m t os p e c i f i c a t i o n s,o r o t h e r c r i t i c a l r e q u i r e m e n t s.T h i s i n c l u d e p r o d u c t sr e t u r n e d f r o m t h e c u s t o m e r a n d c o n f i r m e d b y t h e A p p l i c a t i o nS u p p o r t C e n t e r(A S C)t o b e n o n c o n f o r m i n g.3.0D E F I N I T I O N S3.1I n c o m i n g P r o d u c t–P r o d u c t r e c e i v e d f r o m P R C-D e S o t om a n u f a c t u r i n g s i t e s,f r o m o t h e r d i v i s i o n s o f P R C-D e S o t o(e.g.,o t h e rA S C’s),o r f r o m s u p p l i e r s.I n c o m i n g p r o d u c t i n c l u d e s b u l k m a t e r i a l sa n d r a w m a t e r i a l s t h a t w i l lb e d i r ec t l y i n c o r p o r a t ed i n t o t hef i n a lp r o d u c t a n d f i n i s h e d g o o d s.3.2P R C M a n u f a c t u r i n g S i t e–A P R C m a n u f a c t u r e r o f b u l k r a w m a t e r i a l(e.g.,M o j a v e,G l e n d a l e,S h i l d o n).3.3T r a c e a b i l i t y–T h e a b i l i t y t o t r a c e t h e h i s t o r y,a p p l i c a t i o n,o r l o c a t i o no f a n i t e m o r a c t i v i t y,o r s i m i l a r i t e m s o r a c t i v i t i e s,b y m e a n s o fr e c o r d e d i d e n t i f i c a t i o n.3.4C A I R-C o r r e c t i n g A d j u s t m e n t I n c i d e n t R e p o r t i n g.T h e C o r r e c t i n gA d j u s t m e n t/I n c i d e n t R e p o r t i n g S y s t e m(C A I R)i s i n t e n d e d t of a c i l i t a t e i n t e r n a l/e x t e r n a l c u s t o m e r f e e d b a c k.I t i s t o b e u s e d a s at o o l t o r e p o r t c u s t o m e r c o m p l a i n t s a n d o r n o n c o n f o r m i t i e s.3.5R&T–R e s e a r c h a n d T e c h n o l o g y,B u r b a n k,C a l i f o r n i a.3.6M a t e r i a l R e v i e w T e a m(M a n u f a c t u r i n g)-r e p r e s e n t a t i v e s f r o m Q u a l i t yC o n t r o l,E n g i n e e r i n g,R&T a n d/o r P R C M a n u f a c t u r i n g S i t e a n d a n yo t h e r d e p a r t m e n t a s d e e m e d n e c e s s a r y.3.7M a t e r i a l R e v i e w T e a m(A S C)-r e p r e s e n t a t i v e s f r o m Q u a l i t y C o n t r o la n d O p e r a t i o n s a n d a n y o t h e r d e p a r t m e n t a s d e e m e d n e c e s s a r y.3.8R e p e t i t i v e–E v e t n o c c u r r i n g m o r e t h a n3t i m e s w i t h i n a6m o n t hp e r i o d(s o m e d i s c r e t i o n m a y b e a p p l i e d h e r e,b a s e d o n t h e o v e r a l lf r e q u e n c y o f t h e n o n c o n f o r m i ng o o p e r a t i o n)3.9S e v e r e–I n v i o l a t i o n o f c o m p a n y p o l i c y o r p r o c e d u r e r e s u l t i n g i ns i g n i f i c a n t e f f e c t o n p e r f o r m a n c e,i m p a c t o n p r o d u c t i o n c o s t s,o r c a u s ec u s t o m e rd i s s a t i s f a c t i o n.3.10M i n o r A d j u s t m e n t–A S C r e w o r k,w h i c h i s l i m t i e d t o l a b e l i n gc o r r e c t i o n s a nd p a c k a g i n g a l te r a t i o n s.4.0R E S P O N S I B I L I T I E S4.1A l l e m p l o y e e s a r e r e s p o n s i b l e f o r t h e i d e n t i f i c a t i o n a n d s e g r e g a t i o n o fn o n c o n f o r m i n g p r o d u c t a n d f o r r e p o r t i n g n o n c o n f o r m a n c e s,i n c l u d i n gn o n c o n f o r m i n g p r o c e s s e s,t o Q u a l i t y C o n t r o l.4.2Q u a l i t y C o n t r o l p r o c e s s e s n o n c o n f o r m a n c e s a n d d i s p o s i t i o n sn o n c o n f o r m i n g p r o d u c t a t P r e l i m i n a r y R e v i e w,i f a p p r o p r i a t e.4.3T h e M a t e r i a l R e v i e w T e a m(M R T)a t A S C A t l a n t a d i s p o s i t i o n sn o n c o n f o r m i n g p r o d u c t s t h a t a r e e x p i r e d,d a m a g e d d u r i n g t r a n s i t,g e n e r a t e d d u r i n g p a k c k a g i n g.A n y o t h e r d i s p o s i t i o n i s d o n e b y M R T a tm a n u f a c t u r i n g.4.4T h e M a t e r i a l R e v i e w T e a m(M R T)a t P R C M a n u f a c t u r i n g S i t e a n dE n g i n e e r i n g a n d/o r R&T d i s p o s i t i o n s n o n c o n f o r m i n g p r o d u c t n o ta l r e a d y d i s p o s i t i o n e d a t P r e l i m i n a r y R e v i e w.4.5O p e r a t i o n s M a n a g e r o r d e l g a t e i s r e s p o n s i b l e f o r e n s u r i n g t h e M R T(A S C)d i s p o s i t i o n,r e l a t e d t o o p e r a t i o n s i s i m p l e m e n t e d.4.6C u s t o m e r S e r v i c e M a n a g e r o r d e l e g a t e i s r e s p o n s i b l e f o r o b t a i n i n g aw a i v e r f r o m t h e c u s t o m e r t o r e l e a s e a p r o d u c t t h a t d o e s n o t m e e t t h ec u s t o m e r s p e c i f i c a t i o n,w h e n r e q u i r e d,a nd t o n o t i f y c u s t o me r s if an o n c o n f o r m i n g m a t e r i a l h a s b e e n d e l i v e r e d.4.7A S C B u s i n e s s M a n a g e r i s r e s p o n s i b l e f o r a l l f i n a n c i a l b u s i n e s sd e c i s i o n s.5.0G E N E R A L5.1Q u a l i t y C o n t r o l a n a l y z e s t h e n o n c o n f o r m a n c e s f o r r e p e t i t i v e t r e n d s,a n d e f f e c t i v e n e s s o f c o r r e c t i v e a c t i o n s.5.2I n v e s t i g a t i o n s o f n o n c o n f o r m a n c e s t a k e s i n t o a c c o u n t t h e p r o c e s s t h a tp r o d u c e d t h e p r o d u c t.5.3W h e r e r e q u i r e d b y c o n t r a c t,t h e u s e o f p r o d u c t w h i c h d o e s n o t c o n f o r mt o s p e c i f i e d r e q u i r e m e n t s h a l l b e r e p o r t e d t o t h e c u s t o m e r o r t h ec u s t o m e r s r e p r e s e n t a t i v e f o r c o n c e s s i o n.5.4Q u a l i t y C o n t r o l m a i n t a i n s r e c o r d s o f c o n c e s s i o n s w h i c h s h a l l c l e a r l yn o t e t h e d e s c r i p t i o n o f t h e n o n c o n f o r m i t y t h a t h a s b e e n a c c e p t e d a n dt h e a c t u a l c o n d i t i o n o f t h e p r o d u c t.5.5R e p e t i t i v e,s e v e r e o r p o t e n t i a l l y s e v e r e n o n c o n f o r m a n c e s w i l l r e s u l t i nt h e i s s u a n c e o f a C A I R.6.0P R O C E D U R E6.1T h e r e a r e t h r e e s o u r c e s o f n o n c o n f o r m i n g p r o d u c t:1)I n c o m i n g p r o d u c t r e j e c t e d a t r e c e i p t.a)P r o d u c t f r o m s u p p l i e r s t h a t f a i l s t o m e e t P.O.o rs p e c i f i c a t i o n r e q u i r e m e n t s.b)C u s t o m e r-f u r n i s h e d p r o d u c t t h a t i s r e j e c t e d a tr e c e i p t.2)I n t e r n a l r e j e c t i o n s.a)P r o d u c t t h a t f a i l s r e q u i r e d t e s t s o r i n s p e c t i o n s o rt h a t w a s i m p r o p e r l y t e s t e d o r i n s p e c t e d.b)P r o d u c t t h a t l a c k s t r a c e a b i l i t y t o r a w m a t e r i a l so r p r o c e s s i n g c o n d i t i o n s.c)P r o d u c t w i t h i n c o r r e c t o r m i s s i n gl a b e l/i d e n t i f i c a t i o n.d)P r o d u c t t h a t e x c e e d s i t s s h e l f l i f e.e)P r o d u c t n o t m e e t i n g t h e r e q u i r e m e n t s o f aP r o c e s s C o n t r o l D o c u m e n t(P C D)3)P r o d u c t r e t u r n e d f r o m c u s t o m e r s.6.2Documented nonconformances are assigned a sequential number andrecorded in the CAIR System. The CAIR assigned shall clearly definethe nonconforming characteristic, the requirement and/or idealcondition, the disposition, and corrective action, when applicable.6.3The CAIR is distributed to the department and/ or flowdown to thesupplier responsible for investigating the root cause and determiningcorrective action.6.4Indentification/Segregation of Nonconforming product shall beidentified per WI 1300-1, and where practical, the product shall bephysically segregated from conforming product.6.5Disposition of noncomforming products are as follow6.6The data and inventory status of the material shall be reviewed byQuality Control. If the reported nonconformance affects the approvalstatus of existing inventory and a final disposition cannot be madeimmediately, an interim status of “HOLD” is made.6.6.1In the event that non-conforming product has been delivered,the customer, subcontractor, internal organization, distributor,or regulatory agency, as applicable, shall be notified within 48hours in writing. Notification shall clearly define thenon-conforming characteristic, the item and/or customers partnumber, quantity and date(s) delivered, and if determined, arequest for return.6.6.2Repetitive, severe or potentially severe nonconformances willresult in the issuance of a Corrective Action Request, per QP1400, being issued to the responsible party. (How we want todo it)6.7Q u a l i t y C o n t r o l m a i n t a i n s r e c o r d s o f a l l n o n c o n f o r m i n g m a t e r i a l sd i s p o s i t i o n s,i n c l u d i n g c a u s e/c o r re c t i v e a c t i o n.6.8P r e l i m i n a r y R e v i e w d i s p o s i t i o n s m a y b e m a d e b y t h e Q u a l i t y M a n a g e ro r d e l e g a t e,t o i n i t i a l l y d e t e r m i n e t h e n a t u r e o f t h e d e f e c t a n d t h er e s p o n s i b i l i t y f o r t h e d i s c r e p a n t m a t e r i a l.T h e a c t i o n s t a k e n d u r i n gP r e l i m i n a r y R e v i e w d o n o t r e q u i r e M R T a p p r o v a l.6.9N o n c o n f o r m i n g m a t e r i a l s t h a t a r e n o t d i s p o s i t i o n e d a t P r e l i m i n a r y R e v i e w a r ed i s p o s i t i o ne d b y M R T a t m a n uf a c t u r i n g6.9.1T h e d i s p o s i t i o n a u t h o r i t y a t P r e l i m i n a r y R e v i e w i s l i m i t e da)R e j e c t e d/S c r a p p e d–P r o d u c t t h a t d o e s n o t c o n f o r m t os p e c i f i e d r e q u i r e m e n t s.P r o d u c t d e s i g n a t e d a s s c r a p s h a l l b ec o n s p i c u o u s l y a nd pe r m a n e n t l y m a r k e d,o r p o s i t i v e l yc o n t r o l l ed u n t i l re n d e r e d p h y s i c a l l y u n u s a b l e.6.10M R T p e r s o n n e l a r e q u a l i f i e d a c c o r d i n g t o Q P1800T r a i n i n g p r o c e s su s i n g Q P F1300-4M R T C o m p e n t e n c y R e q u i r m e n t s7.0A s o c i a t e d M a t e r i a l s7.1W I1300-1R e d T a p i n g a n d T a g g i n g7.2Q P F1300-4M R T C o m p e n t e c y R e q u i r m e n t s7.3C A I R-C o r r e c t i n g A d j u s t m e n t I n c i d e n t R e p o r t i n g7.4Q P1600C o n t r o l o f Q u a l i t y r e c o r d sAS9100内部审核程序英文版1.PURPOSE1.1The purpose is to provide a procedure for conducting audits todetermine whether the quality management system:1.1.1 Conforms to the requirements of AS9100 and to quality managementsystem requirements established by PRC-DeSoto International.1.1.2 Is effectively implemented and maintained.1.1.3 Meet Contract and Regulatory Requirements.2.SCOPE2.1 This procedure applies to the ASC Quality Management System.Flow-down shall be areas described in the quality procedures, policies,and work instructions affecting the quality of work are audited,including delegated quality activities.3.RESPONSIBILITY3.1 The Management Representative – Ensures that internal audits areperformed according to established process. Ensures that auditors aretrained or plans for audit.3.2 Trained internal quality auditors (Audit Team) are responsible forconducting all internal audits.3.3The Management Representative ensures that internal auditors aretrained, prepares and keeps records of this training, prepares an auditschedule, completes the Summary of Findings and tracks and verifiesthe timely closure of corrective actions to Nonconformances andmaintains records.4.GENERAL4.1 The Audits are performed by trained internal auditors independent ofthe functions audited.5.DEFINITIONS5.1Audit - systematic, independent and documented process for obtainingobjective evidence and evaluating it to determine the extent to whichaudit criteria are fulfilled.5.2Audit criteria - set of policies, procedures or requirements used as areference.5.3 Auditor – Person with the competence to conduct an audit.5.4 Audit finding – Results of the evaluation of the collected auditevidence against the audit criteria.5.5Objective Evidence – Data that supports the existence of verification ofsomething.5.6Nonconformity – Non-fulfillment of a requirement.6.PROCEDURE6.1The Management Representative plans and implements an auditschedule ensuring that:•Quality management system requirements are audited•The frequency of audit is based on the status and importance of the process(s) and activity audited as well as previous audit results.The settime to complete audits is within the month assigned.6.2The Management Representative determines the audit scope, auditcriteria and assign an auditor(s) for completion of each audit. The selection ofauditors for each assignment ensures objectivity and impartiality of the auditprocess and those auditors do not audit their own work.6.3Management Representative notifies the department manager of theaudit by forwarding a copy of the schedule when developed and revised.6.4The internal auditor contacts the appropriate departments to schedule apre-audit meeting where specific audit dates/times based on department andauditor schedules are discussed. Internal auditors perform the audit.6.5Auditors performs audits in a structured manner to accomplish thescope of the audit assignment:•Review assignment to determine audit scope, audit criteria.•Schedule the audit with the audited.•Review audit criteria, such as policies, procedures, contracts, requirements of AS9100 and prepare a QPF1700-1 Audit Checklist as appropriate toaccomplish audit scope.•Hold an opening meeting with audited to explain purpose and scope of the audit.•Execute the audit by obtaining sufficient information or objective evidence to permit conclusions to be drawn regarding theconformance/nonconformance and effectiveness of the area being audit.•Collective information and objective evidence through interviews, examination of documents and records, observation of activities andconditions in the areas being audited.•Record observations for review to determine whether Nonconformances or potential Nonconformances exist.•Review observations, taking into account their significance and drawing conclusions about conformance/nonconformance and effectiveness of thearea at meeting requirements and achieving quality objectives.•Prepare nonconformance reports according to the Corrective andPreventive Action procedure taking care to include sufficient details andobjective evidence.•Hold a closing meeting with the audited to review and clarify the results and conclusions of the audit.•Prepare an audit report that summarizes the audit conclusions and forwards to the Management Representative.•Management Representative reviews the audit report and any recorded Nonconforming reports; obtains clarification from the auditor(s) asappropriate.6.6 A copy of the Internal Quality Audit Nonconformance Report is sent to theaudited, (department manager). The audited investigatesfindings/observations. Managers review audit findings. The audited completes corrective action responses and send to the Management Representative forreview and approval within stated due date defined in the NCR form.Management Representative input/close audit in the Nonconforming Database.6.7The Management Representative assigns follow-up/verification of correctiveaction based on the estimated completion date determined by the Manager.6.8Internal Quality Audit Nonconformance Reports are reviewed using theSummary of Findings at the Management Review Meetings. TheManagement Representative completes the Summary of Findings and tracksand verifies the timely closure of corrective actions to Nonconformances.6.9Management at the Quality Management Meetings determines theeffectiveness of implemented corrective actions and determines the need foradditional corrective actions or re-audits when necessary. If it is determined by Management that a corrective action is ineffective, the appropriateDepartment Managers are notified and are responsible for development of arevised plan for corrective action including completion dates. A new NCR is written, and this revised plan is also tracked through Management Reviews.Completion and verification of any issues are indicated on the AuditNonconformance Report.6.10Records of internal audits are kept for 7 years under the control of the QualityControl Department.7.REFERENCE DOCUMENTS7.1 QP 1600 – Control of Records7.2 QPF1700-1 Audit Checklist formAS9100纠正和预防措施程序英文版1.0PURPOSE1.1.The purpose is to provide a procedure for identifying Nonconformances andpotential Nonconformances, investigating the cause, determining and takingactions to eliminate the cause and follow-up activities to ensure agreedactions were taken and effective.2.0SCOPE2.1This procedure applies to all Nonconformances and potentialNonconformances identified within the Quality Management Systems.3.0RESPONSIBILITY3.1The Management Representative, or delegate, is responsible for:•Assigning CAR numbers•Assigning responsibility to investigate the cause and recommend action to be taken•Reviewing cause, recommended action and implementation schedule for adequacy•Assigning Internal Auditors to verify implementation and effectiveness of CARs•Forwarding copy of closed CARs to the Observer•Maintaining CAR database and copies of CARs•Analyzing appropriate information in order to detect opportunities for preventive action3.2The appropriate personnel are responsible for investigating the cause ofnonconformance/potential nonconformance, recording the results of theinvestigation, recommending appropriate action, implementing agreedaction and applying sufficient controls to ensure action is effective.3.3The Observer of a nonconformance/potential nonconformance isresponsible for originating a CAR and forwarding to the ManagementRepresentative.3.4The Internal Auditor is responsible for verifying that agreed action hasbeen implemented and is effective.4.0GENERAL4.1The Management Representative forwards a CAR to the supplier when itis determined that the supplier is responsible for the root cause. If thesupplier is internal, the CAIR process is used.5.0DEFINITIONS5.1Potential Nonconformance: The prediction that conditions exist which maylead to a nonconformance unless action is taken.5.2Nonconformance: The nonfulfillment of a requirement. Examples include:5.2.1The absence of a procedure required by the QualityManagement System.5.2.2Failure to effectively implement a procedure required by theQuality Management System.5.2.3 A confirmed customer complaint.5.2.4An out of calibration instrument or measuring device.5.2.5 A rejected product.5.2.6 A quality systems violation.5.3Corrective Action: action taken to eliminate the cause of a detectednonconformance or other undesirable situation. Corrective actions preventrecurrence.5.4Preventive Action: action taken to eliminate the cause of a potentialnonconformance or other undesirable potential situation. Preventiveactions prevent occurrence.5.5Observer: anyone observing a nonconformance/potential nonconformanceor receiving a customer complaint.5.6Immediate Action: corrective or preventive as appropriate to eliminate thecause of a nonconformance/potential nonconformance in order to preventrecurrence/occurrence.5.7Root Cause: Underlying reason of why the discrepancy occurred,determined as results of an investigation of the product, process and/orquality system.5.8Corrective Action Verification: Activity undertaken immediately afterimplementation of root cause correction to verify implementation5.9Follow-Up: Planned activity to determine if implemented root causecorrective action is effective and being adhered to.5.10CAR – Corrective Action Request generated from anynonconformance.6.0PROCEDURE6.1The Observer of a nonconformance/potential nonconformance originates aQPF1400-1 CAR form by completing the detail section of the CAR. TheObserver provides sufficient details of the nonconformance/potentialnonconformance to permit an effective investigation of the cause.6.2The Observer forwards the CAR to the Management Representative.6.3The Management Representative reviews the details provided to ensurethey are sufficient and request additional details as appropriate.6.4The Management Representative assigns a CAR number and otherinformation such as reference, procedure number, requirement sectionnumber, etc. as appropriate in the database.6.5The Management Representative assigns responsibility for investigatingthe cause of the nonconformance/potential nonconformance and forward a copy of the CAR to that individual.6.6The assigned individual investigates the cause of thenonconformance/potential nonconformance, record the results of theinvestigation, recommend appropriate action to be taken and forward the completed CAR to the Management Representative.6.7The Management Representative reviews the completed CAR to determineif the cause, recommended action and schedule for implementation areappropriate to the effects of the nonconformance encountered. TheManagement Representative re-issues using QPF 1400-2 for additional effort if the cause, recommended actions or schedule for implementation are considered inadequate.6.8The Management Representative assigns an Internal Auditor to verify thatthe agreed action was taken and was effective. The ManagementRepresentative closes the CAR if no action is recommended.6.8.1The Internal Auditor closes the CAR if the agreed action isverified as implemented and effective and forwards the CAR tothe Management Representative.6.8.2The Internal Auditor returns the CAR to the ManagementRepresentative if the agreed action was not implemented orcould not be verified as effective.6.8.2.1The Management Representative reassigns theineffective CAR requesting additional information.6.9The Management Representative forwards a copy of each closed CAR tothe Observer and update the database to reflect the status of CARs.6.10The Management Representative periodically reviews the status ofCARs in order to ensure the corrective/preventive action process is timelyand effective. The Management Representative initiates specific andappropriate action(s) to address an untimely or ineffectivecorrective/preventive action process. Actions may include, but are notlimited to:6.10.1Reporting CAR status to management responsible for the areawith request for action6.10.2Reassigning CAR to a higher management level within theorganization6.10.3Reassigning CAR to another individual6.10.4Providing assistance to resolve CAR6.10.5Providing training or other actions to improve effectiveness6.11Preventive Action6.11.1The Management Representative periodically reviewsappropriate sources of information such as complaint reports,audit results, nonconforming product, etc. in order to identifyopportunities for preventive action. The ManagementRepresentative originates a CAR for any identifiedopportunities for preventive action.6.11.2The Management Review activity potentially identifiesopportunities for preventive action as well. Refer to QP101Management Review procedure for additional details.6.11.3Internal auditors evaluate collected audit evidence in order todetermine existence of a potential nonconformance accordingto QP1700 Internal Audit procedure.7.0REFERENCE DOCUMENTS7.1QPF1400-1 CAR Form7.2QPF1400-2 Insufficient Root Cause/CAR form7.3QP 101 – Management Review7.4Ongoing CAR status database7.5CAIR databaseAS9100记录控制程序英文版1.PURPOSE1.1The purpose is to provide a procedure for the identification, storage, protection,retrieval, retention, maintenance and disposition of records.2.SCOPE2.1This procedure applies to records resulting from quality systems activities.3.RESPONSIBILITY3.1Authors/Owners – are responsible for determining the identification, storage,protection, retrieval, retention, maintenance and disposition of records.3.2Refer to the Records Table for additional details on responsibilities.4.GENERAL4.1Quality records are suitable in format, accuracy, completeness, and detail topermit analysis. Where variable data is required, the actual numerical resultsobtained are indicated. Where defective or nonconforming articles areinvolved, the records include the results of analysis and corrective actiontaken.4.2Quality records are legible, identifiable, indexed, and stored in a way that theyare readily retrievable.4.3Electronic records are password protected and are periodically backed up toprevent loss.4.4Quality records that contain confidential information are handled, distributed,and retained in a secure manner that does not violate their confidential nature.4.5A lost record may be replaced when other records are available to substantiatethe acceptance of previous operations; otherwise, tests/inspections areperformed to re-establish the lost record.4.6Where agreed contractually, quality records are available for review andevaluation by representatives of the customer, government, or regulatoryauthorities.5.DEFINITIONS5.1Identification – what records are required for the quality system todemonstrate conformity to requirements and the effective operation of thequality system.5.2 Storage/Protection – where the records are stored and how they are stored toprotect against loss, damage or deterioration.5.2Maintenance – who is responsible for maintaining the records?5.4Disposition – how are records disposed of.5.5Retention time – the minimum amount of time a record is kept.5.6Retrieval - who is authorized to retrieve records?5.7Author/Owner – process owner or individual assigned responsibility fordocumenting a process within the quality system.5.8Retrievable – Records that are kept on site are retrievable within 24 hrs. Whilerecords that are stored off site are retrievable within 72 hrs.6.PROCEDURE6.1The Author/Owner of a process, procedure, work instruction, etc. shall identifyquality related records associated with the process, including any records thatare created by or retained by suppliers, and define the controls for retentiontime, storage/protection, maintenance, retrieval and disposition of thoserecords.6.2When an error is discovered in a record, the error is lined out, not obliterated(i.e. white out), and the correction is entered and validated by the signature,initials, or stamp of the correcting party and the date.6.3Quality records are retained for a minimum of seven (7) years after completionof the contract except where specific customers, government agencies, orregulatory authorities require longer quality record retention times.6.4See attached records table for complete definition of Control of Records6.5Individuals with responsibility for collecting/maintaining records shall ensurethat:•All records are legible and traceable to the product concerned where appropriate.•All records are stored in a manner that protects against loss, damage or deterioration.•Ease of retrieval is provided for•Records are available for review by customers and regulatory authorities in accordance with contract or regulatory requirements.。
纠正和预防措施程序-中英文版本

Version: A0 Page: 1/7Status:PROCEDURE 程序文件Corrective and Preventive Actions ManagementProcedure 纠正和预防措施程序目的OBJECTIVE 2 范围SCOPE2 职责RESPONSIBILITY2 正文PROCEDURAL ELEMENTS2流程FLOW CHART 3 任务描述TASKS DESCRIPTION 4 参考文件REFERENCE DOCUMENTS 6 记录RECORDS7 定义与缩写DEFINITIONS/ ABBREVIATIONS 7___________________________________________________________________Version: A0 Page: 2/7Status:PROCEDURE 程序文件Corrective and Preventive Actions ManagementProcedure 纠正和预防措施程序Objective 目的To ensure continually improve the effectiveness of the quality management system through the use of corrective and preventive actions.利用纠正与预防措施,确保持续改进质量管理体系和环境管理体系的有效性。
__________________________________________________________Scope 范围Applied to the corrective , correction action and continual improvement. 适用于纠正、预防和持续改进。
__________________________________________________________Responsibility 职责It is the responsibility of the related departments to implement the corrective and preventive action in compliance with this procedure.相关部门负责按照此程序实施纠正与预防措施。
纠正和预防措施控制程序(中英文)
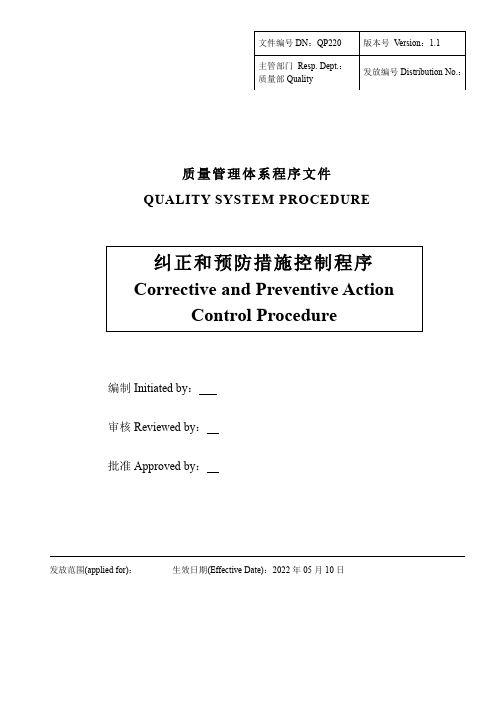
质量管理体系程序文件QUALITY SYSTEM PROCEDURE编制Initiated by:审核Reviewed by:批准Approved by:发放范围(applied for):生效日期(Effective Date):2022年05月10日文件修改履历Document History Summary目录Ta b l e o f C o n t e n t序号名称页码Item #Title Page1 目的(Purpose) (2)2 范围(Scopes) (2)3. 定义(Definitions) (2)4 职责(Responsibilities) (2)5 工作流程(Working procedures) (3)6 相关文件(Relevant Documents) (8)7 相关记录(Relevant Records) (8)8 附件(Appendixes) (8)Document History Summary (1)1 目的(Purpose)本程序规范了为消除实际或潜在的不合格而采取纠正预防措施的流程,以确保类似或潜在不合格不再发生,促进质量管理体系的持续改进。
The procedure clarifies the process to adopt corrective and preventive action to eliminate the existing or potential non-conforming and prevent similar non-conforming in the future and promote the sustained improvement of the quality management system.2 范围(Scopes)本程序适用于本公司质量管理体系范围内纠正措施和预防措施的制定、实施与有效性验证。
The procedure is applicable to the establishment, implementation and validation of corrective and preventive action within the quality management system.3. 定义(Definitions)3.1 纠正:为消除已发现的不合格所采取的措施;Correction: Action to eliminate a detected nonconformity.3.2 纠正措施:为消除已发现的不合格或其他不期望情况的原因所采取的措施;Corrective action: Action to eliminate the cause(s) of a detected nonconformity or other undesirable situation. 3.3 预防措施:为消除潜在不合格或其他潜在不期望情况的原因所采取的措施;Preventive action: Action to eliminate the cause of a potential nonconformity or other undesirable potential4 职责(Responsibilities)4.1 质量管理体系内各部门负责将质量管理体系持续改进的机会,包括不合格情况、潜在不合格情况、改进机会反馈至QA。
- 1、下载文档前请自行甄别文档内容的完整性,平台不提供额外的编辑、内容补充、找答案等附加服务。
- 2、"仅部分预览"的文档,不可在线预览部分如存在完整性等问题,可反馈申请退款(可完整预览的文档不适用该条件!)。
- 3、如文档侵犯您的权益,请联系客服反馈,我们会尽快为您处理(人工客服工作时间:9:00-18:30)。
1.0PURPOSE1.1.The purpose is to provide a procedure for identifying Nonconformances and potentialNonconformances, investigating the cause, determining and taking actions to eliminatethe cause and follow-up activities to ensure agreed actions were taken and effective.2.0SCOPE2.1This procedure applies to all Nonconformances and potential Nonconformancesidentified within the Quality Management Systems.3.0RESPONSIBILITY3.1The Management Representative, or delegate, is responsible for:∙Assigning CAR numbers∙Assigning responsibility to investigate the cause and recommend action to be taken∙Reviewing cause, recommended action and implementation schedule for adequacy∙Assigning Internal Auditors to verify implementation and effectiveness of CARs∙Forwarding copy of closed CARs to the Observer∙Maintaining CAR database and copies of CARs∙Analyzing appropriate information in order to detect opportunities for preventive action3.2The appropriate personnel are responsible for investigating the cause ofnonconformance/potential nonconformance, recording the results of the investigation,recommending appropriate action, implementing agreed action and applyingsufficient controls to ensure action is effective.3.3The Observer of a nonconformance/potential nonconformance is responsible fororiginating a CAR and forwarding to the Management Representative.3.4The Internal Auditor is responsible for verifying that agreed action has beenimplemented and is effective.4.0GENERAL4.1The Management Representative forwards a CAR to the supplier when it isdetermined that the supplier is responsible for the root cause. If the supplier isinternal, the CAIR process is used.5.0DEFINITIONS5.1Potential Nonconformance: The prediction that conditions exist which may lead to anonconformance unless action is taken.5.2Nonconformance: The nonfulfillment of a requirement. Examples include:5.2.1The absence of a procedure required by the Quality Management System.5.2.2Failure to effectively implement a procedure required by the QualityManagement System.5.2.3 A confirmed customer complaint.5.2.4An out of calibration instrument or measuring device.5.2.5 A rejected product.5.2.6 A quality systems violation.5.3Corrective Action: action taken to eliminate the cause of a detected nonconformanceor other undesirable situation. Corrective actions prevent recurrence.5.4Preventive Action: action taken to eliminate the cause of a potential nonconformanceor other undesirable potential situation. Preventive actions prevent occurrence.5.5Observer: anyone observing a nonconformance/potential nonconformance orreceiving a customer complaint.5.6Immediate Action: corrective or preventive as appropriate to eliminate the cause of anonconformance/potential nonconformance in order to prevent recurrence/occurrence.5.7Root Cause: Underlying reason of why the discrepancy occurred, determined asresults of an investigation of the product, process and/or quality system.5.8Corrective Action Verification: Activity undertaken immediately afterimplementation of root cause correction to verify implementation5.9Follow-Up: Planned activity to determine if implemented root cause corrective actionis effective and being adhered to.5.10CAR – Corrective Action Request generated from any nonconformance.6.0PROCEDURE6.1The Observer of a nonconformance/potential nonconformance originates a QPF1400-1 CAR form by completing the detail section of the CAR. The Observer providessufficient details of the nonconformance/potential nonconformance to permit aneffective investigation of the cause.6.2The Observer forwards the CAR to the Management Representative.6.3The Management Representative reviews the details provided to ensure they aresufficient and request additional details as appropriate.6.4The Management Representative assigns a CAR number and other information suchas reference, procedure number, requirement section number, etc. as appropriate in the database.6.5The Management Representative assigns responsibility for investigating the cause ofthe nonconformance/potential nonconformance and forward a copy of the CAR to that individual.6.6The assigned individual investigates the cause of the nonconformance/potentialnonconformance, record the results of the investigation, recommend appropriateaction to be taken and forward the completed CAR to the Management Representative.6.7The Management Representative reviews the completed CAR to determine if thecause, recommended action and schedule for implementation are appropriate to the effects of the nonconformance encountered. The Management Representative re-issues using QPF 1400-2 for additional effort if the cause, recommended actions or schedule for implementation are considered inadequate.6.8The Management Representative assigns an Internal Auditor to verify that the agreedaction was taken and was effective. The Management Representative closes the CAR if no action is recommended.6.8.1The Internal Auditor closes the CAR if the agreed action is verified asimplemented and effective and forwards the CAR to the ManagementRepresentative.6.8.2The Internal Auditor returns the CAR to the Management Representativeif the agreed action was not implemented or could not be verified aseffective.6.8.2.1The Management Representative reassigns the ineffective CARrequesting additional information.6.9The Management Representative forwards a copy of each closed CAR to the Observerand update the database to reflect the status of CARs.。