树脂空洞铜箔起泡分析改善报告
产品表面起泡不良8D分析报告2017-3-7

D4 根本原因分析Root Causes
3)生产影响分析验证资料附件3
生产流程:查前处理槽参数浓 度均在范围内,除12月5日高 温除油更换,电解槽无更换记 录;使用时间超出6个月有失 效风险;
D4 根本原因分析Root Causes
5)起泡不良鱼骨图分析
料
机
人
冲压件油渍过多 盐酸失效 除油剂失效 除油设计不合理
陈赛
维护
沈开文
2017-2-21
进行中
生产
沈开文
2017-2-21
进行中
检验
沈开文
2017-2-21
进行中
检验
章秋飞
2017-2-21
进行中
D6 恒久措施
NO. 问题 措施分类 槽液维护 行动 在控制计划和作业指导书中增加槽液维护更换周期,并形成 规范处理记录; 根据产线空间评估高温除油槽油脂分离溢流装置的可行性; 负责人 姜志敏 预计完成日期 2017-3-17 跟踪状态 编制中
是
2
高温除油
浮油过多带出 1.查验浓度分析记录; 1.查高温除油槽浓度分析结果OK; 交叉污染 2.目视检查槽内油渍情况; 2.槽体内表面浮油严重,有带出污染风险;
电解除油剂 1.查验浓度分析记录; 失效 2.检查除油槽维护记录; 浮油杂质污染 1.查验分析记录正常; 2.电解槽更换最近的时间 为2016年6月,长时间未进行槽体清洗,有杂质影响 除油减弱风险;
2
D1 问题描述
问题描述 球铰TX0001261起泡不良
发生日期
2017-2-13
发生地点
出货检验区
客户投诉数量
3件
客户投诉批次
2017-1-13
对应生产线
PCB用高纯铜箔的起泡性能研究

PCB用高纯铜箔的起泡性能研究高纯铜箔是电子产品中常用的材料之一,特别是在电路板(PCB)的制造过程中。
然而,高纯铜箔在制造过程中可能出现起泡的问题,这对电路板的质量和性能都会产生负面影响。
因此,研究高纯铜箔的起泡性能对于提高电路板质量至关重要。
首先,我们需要了解起泡现象的原因。
高纯铜箔的起泡主要是由气体或挥发性物质的存在引起的。
在制造过程中,当高纯铜箔受热或压力变化时,其中的气体或挥发性物质会扩散并形成气泡。
起泡会导致箔材表面不平整,影响铜箔与其他材料的粘合强度,并可能引发其他问题,例如导电性能下降和电路板寿命缩短。
为了研究高纯铜箔的起泡性能,可以采取以下方法:1.材料选择:选择高纯度、低氧含量的铜箔作为研究对象。
高纯度铜箔具有更好的导电性能和机械强度,而低氧含量可以减少气体的扩散。
2.实验设计:设计一系列实验以模拟高纯铜箔在制造过程中的热力条件变化。
例如,可以控制不同的温度和压力,观察铜箔表面的起泡情况,并测量起泡的数量和尺寸。
3.表征分析:使用扫描电子显微镜(SEM)等表征手段观察箔材表面的起泡情况。
通过观察气泡的形状、大小和分布情况,可以评估高纯铜箔的起泡性能。
4.影响因素分析:研究起泡现象的原因,分析影响起泡性能的因素。
除了温度和压力,还可以考虑材料的冷却速率、铜箔表面的处理方式等因素。
5.改进方法:基于研究结果,提出改进高纯铜箔起泡性能的方法。
可以通过改变制造工艺参数、优化材料配方或采用特殊的表面处理方法来减少起泡现象的发生。
最后,需要指出的是,研究高纯铜箔的起泡性能是一个复杂的课题,需要综合考虑多个因素。
此外,实验结果仅代表特定条件下的情况,可能需要在实际制造环境中进行进一步验证。
通过深入研究高纯铜箔的起泡性能,我们可以为电路板制造过程提供更多的理论和实践指导,以提高电路板的质量和可靠性。
过孔露铜改善评估报告

TO:奋达科技品质部CC:郑生、徐生、刘总FM:鑫鸿图:品质题目:有关过孔露铜改善评估报告关于近期生产奋达科技的PCB出现“过孔露铜”缺陷,经统计出的PCB型号、进行分析缺陷原因存在5--10%的不良风险,经公司管理层制定实效的围堵/改善行动,有效的杜绝缺陷隐患,将不良风险降至有效控制范围。
(分析)缺陷风险分析:属阻焊层过孔塞油不均在过孔的孔径位出现油墨层偏薄,孔径有轻微目视感露铜(有阻焊层防焊性能)喷锡工艺不存在上锡/连锡缺陷。
图1、2:过孔有露铜目视感,但露铜孔径处没有产生上锡及锡连。
(不排除SMT工艺磨擦后露铜被元件面连接短路)但存在外观缺陷。
我司在现有的丝印工艺暂无法做到100%的过孔盖油,不良比例在5--10%范围。
有效的改善评估及建议1、改善:A:在丝印工艺加大对丝印的压力,保证过孔的塞油饱满度。
B:、调整油墨粘稠度,保证油墨的丝印厚度≥20um阻焊层。
C:、增加丝印前油墨塞孔工艺,保证过孔塞盖油的厚度。
2、评估:经试验的结果仍无法保100%的过孔油墨盖孔厚度及外观品质,增加了PCB的制作成本(15%)及生产制程时间。
评估结论:增加制程时间及成本仍达不到品质要求,此工艺流程存在缺陷。
不可采用!3、建议:我司经与物料合作供应商开会讨论,为了满足品质要求,在现有的工艺流程作,不影响交期,不增加人工成建议改用油墨阻焊度强,感光色感较高的“广信KG33色号油墨”(ROHS及SGS及相关检测合格)改善过孔油墨阻焊层缺陷及外观。
从而达到双赢相互利效果!更改油墨色号的试验及对比图片:广信KG33深绿外观质感(更改油墨色号)广信KG25 外观质感(现用的油墨色号)品质对比:A:广信KG33深绿与广信KG25中绿有明显的色差感,B:广信KG33深绿广信KG25中绿的阻焊性能相同,但阻焊度更好,感光色度高。
建议与试产:为满足客户需求,不断提高品质要求,我司建议改用广信KG33深绿油墨进行小批量试产,并交付客户(奋达科技)进行相关品质认可,并进行相关量产程序。
铜箔表面处理过程产生的表面质量缺陷及对策

铜箔表面处理过程产生的表面质量缺陷及对策(序2)[所属分类:专家讲座][发布时间:2012-5-16][发布人:任中文][阅读次数:249][返回](接上期)5.铜箔光面黑点(暗点)5.1定义铜箔光面因粘贴上异物或受异物污染、腐蚀,呈现发暗的小点,叫光面黑点。
5. 2判定判定方法:在日光灯下用肉眼宏观检查,黑点不明显的,颜色不太深的,不仔细看,看不出来的判为合格品;照点轻微可见,但数量较少,黑点较小,总面积较小,不严重的判为二级品;黑点明显的,即使黑点较小,面积较小也判为废品。
即使黑点较小,但数量较多,或占有的面积较大判为废品。
5. 3危害影响铜箔表面质量,影响覆铜板表面质量,影响线路板贴膜质量。
5. 4产生原因分析及解决方法(1)产生原因之一:阳极板上的溶解物和附着物的粘污酸性处理槽里的阳极板上的溶解物和附着物,在电解液的搅动下从阳极板上脱落下来,随着电解液的流动落在铜箔上,或落在下导總上,当铜箔与导辘接触时,在导辐上的这些污物有的粘在铜箔上, 铜箔上的污物有的粘在导辘上。
这些污物粘在铜箔上是一个黑点,粘在导辐上的污物在与铜箔接触时有的还是粘在铜箔上,铜箔上的污物在运行时也粘在导辐上。
随着铜箔运行,导辘每转一周,导辐上的污物就粘在铜箔上一些,直至把污物粘没有了才结束。
如果粘在导辐上的是固体颗粒,当铜箔与导轻接触上后,有颗粒的地方承受的压力大,一是能把铜箔硝出凹坑,二是使铜箔与颗粒接触非常紧密,接触点铜箔上没有溶液,在铜箔与导辐接触的这段时间里,该点受到腐蚀可能比其它地方较轻,该点与铜箔其它地方的腐蚀程度不一样,没有液的地方,因没有液膜保护,反而氧化发暗,使铜箔表面颜色深浅不一样,铜箔接触颗粒被硝着的地方可能是有凹坑的原因发暗,时间长了成为黑色氧化点。
解决方法;及时刷洗阳极板,极距小要适当加大,一般极距在80— 100毫米左右,铅一银阳极可以用薄的过滤布包起来,定期清洗阳极板,更换过滤布。
最好采用铜粒可溶阳极,将铜粒装在钛筐里,随着铜粒的消耗,不断的装填补充。
渗镀,浸焊起泡,剥离强度不足原因分析及对策

渗镀,浸焊起泡,剥离强度不足原因分析及对策PCB刚性线路板及FPC软性线路板生产过程中均会时常碰到以下问题:一,线路工段出现干膜或湿膜处理后在蚀刻线路时出现侧蚀,凹蚀现象,导致线宽不足或线路不平整.究其原因不外乎与干湿膜材料选择不当,曝光参数不当,曝光机性能不良.显影,蚀刻段喷头调节,相关参数调节不合理,药液浓度范围不当,传动速度不当等系列可能导致出现问题的原因.然而我们经常会发现经过检查以上参数及相关设备性能并没有异常,然而在做板时依然会出现线路过蚀,凹蚀等问题.究竟是什么原因呢?二,在做PCB图形电镀,PCB,FPC终端表面处理如沉金,电金,电锡,化锡等工艺处理时.我们常会发现做出来的板在干湿膜边缘或阻焊层边缘出现渗镀的现象,或大部分板出现,或部分板的部分地方出现,无论是哪一种情况都会带来不必要的报废或不良为后工段加工带来不必要的麻烦,乃至最终报废,令人心痛!究其原因分析大家通常会想到是干湿膜参数,材料性能出现问题;阻焊如硬板用的油墨,软板用的覆盖膜有问题,或在印刷,压合,固化等工段出现了问题.的确,这些地方每一处都可能引起此问题发生.那么我们同样也困惑的是经检查以上工段并没有问题或有问题也解决了,但依然会出现渗镀的现象.究竟还有什么原因没查出来呢?三,线路板在出货前会做上锡试验,客户当然在使用时会上锡焊接元件.有可能两个阶段均会出现,或在某一阶段会出现浸锡或焊锡时阻焊起泡,剥离基板.乃至做胶带测试油墨剥离强度时,拉力机测试软板覆盖膜剥离强度时即会出现油墨可被明显剥离或覆盖膜剥离强度不足或不均的问题.这类问题客户尤其是做精密SMT贴装的客户是绝对不能接受的.阻焊层一旦在焊接时出现起泡剥离现象将导致无法精确贴装原件.导致客户损失大量元件及误工.线路板厂同时将面临扣款,补料,乃至丢失客户等巨大损失.那么我们平时在碰到此类问题时会在那几方面着手呢?我们通常会去分析是不是阻焊(油墨,覆盖膜)材料的问题;是不是丝印,层压,固化阶段有问题;是不是电镀药水有问题?等等...于是我们通常会责令工程师务必从这些工段一一查找原因,并改善.我们也会想到是不是天气的原因?最近比较潮湿,板材吸潮了?(基材及阻焊均易吸潮)经过一番苦战,多少能收获些效果,问题暂时得到表面上的解决.然不经意间此类问题又发生了,又是什么原因?那些可能发生问题的工段明明已经查过改善过了呀.还有什么是没注意到的?针对以上属于PCB,FPC行业广泛的困惑,难题.我们进行了大量的试验和研究,终于发现产生线路不良,渗镀,分层,起泡,剥离强度不足等问题的一个重要原因竟然在于前处理部分.包括干湿膜前处理,阻焊前处理,电镀前处理等多工段的前处理部分.说到这里,或许很多行业人士不禁要笑.前处理是最简单不过的了,酸洗,除油,微蚀.其中哪一样前处理药水,性能,参数,乃至配方,行业内很多技术人员都清楚.线路板生产过程中涉及大量复杂的表面处理药水,如沉电铜,沉电金,沉电锡,OSP,蚀刻,等.这些较为复杂的工艺在多数情况下,工艺工程师都会选择去深入钻研,分析;力求掌握这些工艺技术,并以此作为提升自身技术能力的突破点.同时多数工厂也以此来作为工程师的薪资标准,绩效考核标准.而前处理这块基本上很少有工程师人员去细心研究.要么直接从供应商处购买成品除油,微蚀剂,酸洗自已用稀硫酸作为酸洗液.乃至有不少厂微蚀也自已配,要么配过钠,过铵体系(配方已众所周知),要么购买双氧水稳定剂自已配双氧水-硫酸体系的.而除油则通过购买供应商成品除油剂或购买除油粉稀释使用.据我们的调查研究发现,众多厂家没有从根本上去认识前处理工艺中各药液的细微作用,或者说是关键作用,只注重表面外观效果.如除油段,大家可能一直认为能把板面的油污,手指印除去即可,肉眼看不到即为除油OK,殊不知除油工艺对线路板而言不仅是将已于铜面深度结合的油污剥落,同时更重要的药液要能把剥离下来的油分子分解掉.这样方能对板面不形成二次污染.市场上现在出售的除油剂,除油粉,通常只含有除油,除锈成分,而其它组分如抗蚀剂,表面活性剂,乳化剂,等重要组分为降低成本根本没加;甚至很多供应商的配方从别处购买而来,根本不了解各成分的作用,更谈不上研究,或结合线路板的实际工艺需求调配加入有效的组份.这样实际上很多线路板厂所使用的除油剂并非适用于线路板行业专用的的除油剂,而是通用于五金,矿产加工业的传统除油剂.如此产品怎么达到良好的除油效果,板面用肉眼看着除油效果不错.实际上呢?我们通过高倍显微镜或油膜测试能发现大量细微的油分子附着在板面上.这样的处理效果如何能保证后续生产抗蚀层,阻焊层,终端表面处理时良好的结合力,剥离强度,可焊性等必须性能的效果及稳定性呢.尤为严重的是我们对微蚀这一块的认识.线路板行业的微蚀工艺实际上要具备1.除去铜面锈层,氧化层,及其它异物;2.均匀粗化铜表面,形成微观凸凹,宏观平坦的粗化层.达到速率稳定的粗化效果.3.活化铜表面,并具有短时期抗气相及液相腐蚀的作用,保证后续表面加工的可操作性.4,较低的过氧化物及硫酸含量,防止药液暴沸及形成高分子有机物残留板面.而实际生产中,我们自配的或购买的微蚀液大多把微蚀当成了蚀刻液.认为只有板面的锈渍异物除去,能露出新鲜的铜面就是达到了微蚀效果.而实际上呢?我们自配的微蚀液中过氧化物如过氧化氢,过硫酸钠,过硫酸铵等,强酸如硫酸.为达到效果含量均较高,如过氧化物含量达到120乃至150克/升,硫酸含量超过5%,如此高的浓度实际上是把微蚀变成了蚀刻,大量的铜被咬蚀,且由于没有调节剂的加入,咬蚀深度粗浅不一,轻则导致板面处理效果不一致,重则二次返工即导致铜层严重被咬蚀,无法进行后工段加工,造成报废.很多配双氧水体系的还会犯以为加了双氧水稳定剂就能达到均匀微蚀作用的常见错误理解.双氧水稳定剂只是为了抑制双氧水过快分解而加入,并不能起到均匀性方面的作用.而实际上用于线路板行业的专业微蚀剂它除了应该配以低泡表面活性剂,专用湿润剂,有机络合剂,微定剂,抗蚀剂等多种添加剂.从而使过氧化物,硫酸等咬蚀速率过快,副反应产物较高的主组分含量尽可能降低,并使药液更稳定,除了除锈基本功能外更能均匀稳定的粗化铜面,形成表面宏观平坦光滑(利于终端表面处理外观),无色差,异样区或点;同时微观达到均匀一致的凸凹粗化层(利于后续抗蚀干湿膜,阻焊层的加工),实际上单靠氧化剂和强酸并不能增加理想的铜表面粗化面积,必须加入活性剂,湿润剂等方能达到良好深度粗化效果,增加铜表面粗化面积,从面提升后加工的结合力及剥离强度.经过完善和改进的线路板专用微蚀液整体应达到:药液无暴沸,无高分子副产物形成污染,良好除锈能力,良好的均匀平坦外观,深度粗化铜面,蚀铜量小.达到板面外观平滑,阻焊或镀层加工时结合强等作用.随着线路板向超薄铜型转化,我们越来越需要一种蚀铜量更小的微蚀液(同时保证除锈及粗化效果)随着线路板的线路精度要求越来越高,我们越来越需要一种前处理效果更好的除油,微蚀液.以确保抗蚀层(干湿膜)的抗渗透力.随着线路板终端表面处理的外观要求越来越高,我们需要引进优质的前处理工艺.随着表面焊接向无铅型转化,线路板需承受的焊接温度越来越高,对表面阻焊层的抗热冲击能力要求越来越高,对终端表面处理及阻焊层(油墨,覆盖膜)的剥离强度,与基底铜的结合力要求也越来越高,我们需要一种具有更佳效果的前处理工艺来做保障.随着线路板行业竞争的日益激烈,我们需要通过改良我们的工艺以使产品良率提高,以获得利润增长点.优质的前处理药水无疑能低成本帮我们的大忙.线路板产业前沿如日本,美国,韩国,台湾早已重视并启用新一代前处理工艺.使所生产的产品更具竞争力,性能更稳定.以小带大,从前处理着手确保整体工艺的稳定性.以上谨以我们的研究成果分享于广大线路行业经营者及技术工作者,不足及错误之处敬请批评指正.若您有更多问题需要探讨或对我们的前处理药水及我们所研发的更多专业线路板行业的药水,化学品需要咨询请按以下方式与我们联系,我们将及时与您联系提供相关咨询支持及产品服务.。
气泡分析

集成电路封装制品中气孔气泡问题的分析1 引言集成电路每过1-2年存储容量便增长几倍,芯片的塑封外形正向小型化。
薄型化方向发展。
因此,半导体封装业显得日益重要,对塑封模具提出了更高的要求。
封装材料(塑封料)是以环氧树脂为基水成分添加了各种添加剂的混合物,只有耐湿、耐燃、易保存、流动充填性好、电绝缘性高、应力低、强度大、可靠性好等特点,长期以来,一直应用于集成电路及半导体、无源器件的表面低压封装。
集成电路的封装工艺过程如图1所示:①给粉末状树脂加压.打模成型,制成塑封料饼;封装前,用高频顶热机给料饼预热;②预热后的料饼投入模具的料筒内;①棋具注射头给料饼施加压力,捌脂通过流道、浇口,填充满型腔;④注射头继续保持压力,树脂在模具内发生充分的交联固化反应,硬化成型;①打开模具,取出封装好的集成电路制品。
衡量集成电路塑料封装体的质量指标有很事,本文仪对封装过程小,塑封体的表面和内部产生气泡的原因进行分析,气泡的产生不仅使塑封体强度降低,而且耐湿性、电绝缘性能大大降低,对集成电路安全使用的可靠性将产生很大的影响。
情况严重的将导致集成电路制造失败,对于电器的使用留下安全隐患。
2 塑封体气孔或气泡问题的分析塑封体的表面或内部存在的气泡或气孔是—种质量缺陷。
产生这种缺陷的问题有:①塑封料没有保管好,吸收的水份在塑料高温成型时,生成气体,留在封制品中;②模具的设计不合理,塑料在充填时,模中的各种气体不能快速有效排出(包括封闭型腔中的空气,塑封料固化时产生的挥发性气体,俘获的水蒸气和各种挥发性物质):③引线框架没有充分预热,阻碍塑料的流动性能;④模具的调试工艺参数不正确。
为了保证塑封模具使用的塑封料性能不发生改变,打模后的塑封料饼需要保存在低于5℃的环境里,因而在正式使用前,冷藏的塑封料饼要提前24H放在室温里回温解冻,俗称“醒料”,才能使用。
如果回温时间不够,塑封料没有完全醒透,温度低于环境的温度,料饼在使和的时候将吸收空气中的水分。
分析注塑中产生的气泡,空洞,水纹解决方案

分析注塑中产生的气泡,空洞,水纹解决方案The appearance of bubbles, voids, sinks or blisters on an injection-molded part make up the most significant causes for part rejects due to cosmetic requirements. These troublesome "features", although not the most common of problems when injection-molding parts, can inhibit part performance and are problematic to solve.Bubbles are either pockets of trapped gas or vacuum voids. It is important to determine which type of bubble exists in your part to more quickly pinpoint the source and determine the correct adjustment to make. A simple test of warming the part area containing the bubble until it softens can be used to determine its bubble type as trapped air or void. With the test, if there is gas trapped in the bubble, the gas will warm up and want to expand the bubble as the part softens. If there is no air in the bubble and a vacuum void exists, the bubble will collapse due to the atmospheric pressure pushing on the softened walls of the part. A hot air gun is best to heat the area, a small lighter is next, and a torch if you know what you are doing.Trapped Air IssueTrapped air is a root cause of bubbles as well as blisters. Trapped gas may stem from flow front issues such as converging fronts, or jetting, to equipment and production problems such as non-vented core pins, poor venting, too much decompression, or resin degradation. The air or gas may appear from water vapor, volatiles from the resin, or decomposing by-products. The air may be trapped in ribs, threads ornon-vented projections off the nominal wall. Melt flow pattern is a major cause of bubbles. Processorsshould examine each parts flow pattern via short shots to see if the plastic flow front is coming around on itself. Note if there is a race-tracking effect or jetting that can cause air to become trapped in the polymer.Observe flow path for back flow or trapped air in blind ribs. Examine the part to determine if the rib or support areas of a part are covered before part is completely filled. If it is a flow pattern issue, run a short shot molding sequence, changing the transfer position or shot size to make various sized short shot parts ranging from 10 percent to 95 percent of the full part. Use this to find out where and how the bubble occurs. This test requires the process to be velocity controlled for the first stage (injection). This cannot be done if the first stage pressure and velocity is reduced.Other causes for trapped air leading to bubbles or blisters include inadequate venting, material flow pattern design, and gas traveling across the part surface during the fill or pack stage. Melt flow issues may indicate a need to change the gate location to avoid race tracking, trapping air or to promote uniform fillingEquipment can also be a cause for bubbles. If you are working with a hot runner tool it is possible that a venturi effect can suck air from between the plates into the hot runner, pulling air into the melt, forming a bubble. To check for this the tool must be disassembled, and a bluing agent is applied near the drops, being careful not to apply any in the flow path. If the bluing agent shows up in the part then you have found the source of the problem.One can also examine the purging of a normal shot to see if the bubble originates from the barrel or screw. General-purpose screws with dimensions of 18:1 L/D or lower can be the culprits for a bubble or blister. One solution is to raise the backpressure to 1000 to 1500 psi melt pressure. Another solution may be to pull a vacuum on the mold just before injection, so that air is pulled out. Moisture in the molding system can also be a source of trouble.Tool venting is another big issue, so vent properly or use a porous steel to eliminate gas traps. Check the number of vents as well as vent depth. Check vents with pressure sensitive paper. Clean all parting line and core vents. This can prevent the opportunity for trapping air.Avoiding Voids and SinksA void occurs during cooling, usually in thick sections of the part where there can be a significant cooling rate difference in the material forming the core and skin of the part. A sink is a depression impacting the surface of a part that does not mimic the mold steel surface.Voids and sinks are signs of internal stress and are warning signs that the part may not perform as required.Insufficient plastic can be a main reason for sinks or voids so packing more plastic into the cavity is recommended. Molders should have a consistent cushion on the press, making sure you are not bottoming out the screw. You should go for higher pressures in the hold/pack stage and longer stage time. To solve voids or sinks, trial slow fill rates, the use of gas counter-pressure, and increasing backpressure. You can open the gate for longer gate seal times to allow more packing during the second stage. Molderscan also try reducing the melt temperature.Mechanically, you can increase the runner diameter. You should determine where the sink is. Is it near the gate or farther down the flow part? If near the gate, check the gate seal time. If it is farther down the flow part, increase injection speed to decrease viscosity and allow more packing pressure.Another approach to eliminating voids or sinks is to "thin-up" the nominal wall. Thicker is not always stronger in plastic parts. Thick nominal walls should be redesigned with ribs if strength is needed. This will save plastic and cycle time also. Molders can core out the thick section if possible. Changing the gate location to fill thicker areas in the mold first, this may allow more polymer into the part (before the gate freezes). Molders may also try raising the mold temperature significantly and/or ejecting the part sooner, which can avoid voids by allowing the outside walls to collapse during cooling.For sinks, users may try cooling the part in water or between aluminum sheets rather than air. Here, inner section of the thick-sectioned part can reheat or re-melt the outside surface of the part once ejected, allowing the surface to collapse. However, this may cause a vacuum void. You might be able to diminish the vacuum void by not cooling the part surface and keeping it warm by placing on wood or insulating foam. One should expect sinks with this approach.Be Aware of BlistersBlisters, a thin film of plastic that bubbles up from the part surface, can also ruin the aesthetics of a part. Like bubbles they can be caused by gas traveling across the surface during fill or pack, or due to trappedair issues (inadequate venting, melt flow pattern or screw L/D), and the solutions are the same. However, blisters can also originate from process problems or degradation of the resin or additive package. Delamination is a serious part defect.Excessively high injection rates can cause blisters, as they can develop a highly oriented thin layer or film on the surface of a molded part. Sometimes sticking tape to the part and lifting it pulls this layer off. Try injecting the melt at a slower rate. High temperatures of steel near the gate can cause blisters also and should be made lower if possible. If the decompression of the screw is excessive, it is possible that air will be pulled into the nozzle and remains trapped. This air pocket enters the melt stream during nozzle contact with the sprue. If using a hot runner system, at injection, the trapped air is moved through the hot runner system and can create the bubble. In a cold runner system the air is ahead of the flow front and gets vented.Gas can be created by the degradation of the resin or additive, so try a new lot of material and/or use virgin material. It is best to check the melt temperature process range recommended by the resin supplier. Molders should minimize material residence time, and one way is to use the correct barrel size for the shot.Be sure that the plasticating screw be at least 20:1 L/D. If you are require longer cycle times and higher backpressure to reduce the occurrence of blisters, then it is possibly a screw design issue.消除气泡,空洞,水槽和水泡对注塑成型零件的气泡,空洞,水槽或水疱的出现弥补了部分因拒绝整容要求最显著的原因。
制程异常分析改善汇总

防焊前五项制程问题分析:一、防焊空泡:造成原因:1、前处理不良。
(H2SO4浓度、水质、吹干段角度及风量,吸水海棉清洁度、烘干温度)。
2、磨刷后放置时间过长,室内湿度偏低。
3、印刷台面沾有油墨及其它有机溶剂,反沾板面,油墨搅拌不均。
4、预烤不足。
5、曝光能量太低或太高。
6、显影侧蚀太多。
7、HAL浸助焊剂时间太长,锡槽温度太高,浸锡时间太长。
预防措施:1、前处理作业必须按SOP要求生产。
2、磨刷后放置时间不得超过2H ,室内湿度控制在50-60%之间。
3、印刷台面保持清洁,印第一面时台面上垫一张白纸,以保证板面清洁度。
4、预烤温度保持70±2℃,烤后之板保证不粘棕片。
5、曝光能量保持在9-13格。
6、显影点控制在50-60%,避免过多侧蚀。
7、后烤通风保持良好,塞孔板必须分段烘烤。
8、HAL作业须完全按照SOP操作,不可有违规作为。
二、L/Q内圈阴影:原因分析:1、油墨过期。
2、预烤时间过长,温度过高。
3、挡点印刷时,孔环处积墨过多,印刷房湿度不够。
4、曝光前,静置时间过长。
5、显影速度过快,压力过小。
6、棕片遮光度不够。
7、曝光时吸真空压力未能达到要求。
改善对策:1、油墨按照先进先出的方式使用,保证在油墨保质期内使用。
2、预烤时间和温度按SOP要求作业,且烤好后及时取出防止冷烤。
3、印刷房湿度保持在50-60%之间,挡点印刷保持连贯,且印一PNL刮一次网版。
4、预烤后板静置时间不能眼过12H,最连贯4H以内对位完。
5、显影点保持在50-60%之间。
6、选用遮光度及质量较好之棕片生产。
7、吸真空不得低于600㎜Hg,且须保持导气良好。
三、卡锡珠:原因分析:1、印刷塞孔不满(量产板)。
2、退洗板导通孔内油墨未剥除干净。
3、油墨本身质量问题。
4、HAL贴胶未贴好,某些孔呈半覆盖状态。
5、HAL浸助焊剂及浸锡时间过短。
改善对策:1、从印刷各条件去改善塞孔程度。
(刮刀压力、角度、确度、速度、网目T数量)2、选用适合的退洗液,尽可能洗净导通孔内油墨,保证塞孔效果。
吹塑不良现象改进后的总结报告

吹塑不良现象改进后的总结报告吹塑工艺是一种广泛应用的塑料加工技术,能够生产各种各样的塑料制品。
然而,在吹塑生产过程中,由于原材料、设备、工艺等多方面原因,经常会出现一些不良现象,如泡孔、壁厚不均匀、尺寸偏差等,影响产品的质量和生产效率。
为了改进吹塑不良现象,提高产品的质量和生产效率,我们进行了一系列的改进措施和实验验证,现将改进后的总结报告如下:一、问题分析及改进方向:1.泡孔现象:泡孔是吹塑制品中常见的问题,通常是由于原料中含水量过高、温度控制不当、模具设计不合理等原因导致的。
因此,我们首先对原料进行了严格的检测和筛选,确保原料中的水分含量在合理范围内;其次,在生产过程中,加强了温度控制和模具设计的优化,有效减少了泡孔问题的出现。
2.壁厚不均匀现象:壁厚不均匀是由于吹塑成型时模具的设计不合理或者气道堵塞等原因导致的。
我们对模具进行了优化设计,保证塑料在成型过程中能够均匀地流向模具的各个部位,从而避免了壁厚不均匀的问题的出现。
3.尺寸偏差现象:尺寸偏差是吹塑制品的一个重要质量指标,直接影响产品的使用效果和外观。
我们采取了精密的模具设计和优化的成型工艺,严格控制生产过程中的各项参数,确保产品的尺寸偏差在允许范围内。
二、改进措施及实验验证:1.优化原料配比和检测:我们对原料进行了严格的筛选和检测,确保原料的质量稳定和水分含量控制在合理范围内。
通过实验验证,优化后的原料配比和检测措施有效降低了产品泡孔现象的发生率。
2.强化温度控制和模具设计:我们加强了温度控制的监测和调整,并对模具进行了优化设计,确保产品在成型过程中能够完全填充模具并均匀冷却。
实验结果表明,改进后的温度控制和模具设计有效减少了产品的泡孔和壁厚不均匀现象。
3.精密模具设计和成型工艺优化:我们对模具进行了精密设计和优化,并严格控制生产过程中的各项参数,确保产品的尺寸偏差在允许范围内。
实验结果显示,改进后的模具设计和成型工艺能够有效提高产品的尺寸稳定性和一致性。
常见塑料制品缺陷原因分析

有些塑料制件在成型脱模后,很快在金属嵌件的背面或在特别厚的部位出现肿胀或鼓泡。这是因为未完 全冷却硬化的塑料在内压罚的作用下释放气体膨胀造成。 解决措施: 1.有效的冷却。降低模温,延长开模时间,降低料的干燥与加工温度。 2.降低充模速度,减少成形周期,减少流动阻力。 3.提高保压压力和时间。 4.改善制件壁面太厚或厚薄变化大的状况。
注塑制品色条色线色花的原因分析
这种缺陷的出现主要是采用色母粒着色的塑料制件较常出现的问题,虽然色母粒着色在色型稳定性、色 质纯度和颜色迁移性等方面均优于干粉着色、染浆着色,但分配性,亦即色粒在稀释塑料在混合均匀程度却 相对较差,制成品自然就带有区域性色泽差异。主要解决办法: (1)提高加料段温度,特别是加料段后端的温度,使其温度接近或略高于熔融段温度,使色母粒进入熔融段 时尽快熔化,促进与稀释均匀混合,增加液态混合机会。 (2)在螺杆转速一定的情况下,增加背压压力使料筒内的熔料温度、剪切作用都得到提高。 (3)修改模具,特别浇注系统,如浇口过宽,融料通过时,紊流效果差,温度提升不高,于是就不均匀,色 带模腔,应予改窄。
注塑制品有熔接缝的原因分析
熔融塑料在型腔中由于遇到嵌件孔洞、流速不连贯的区域、充模料流中断的区域而以多股形式汇合时, 因不能完全熔合而产生线性的熔接缝。此外在发生浇口喷射充模也会生成熔接缝,熔接缝处的强度等性能很 差。主要原因分析如下:
1.加工方面: (1)注射压力、速度过低,料筒温度、模温过低,造成进入模具的融料过早冷却而出现熔接缝。 (2)注射压力、速度过高时,会出现喷射而出现熔接缝。 (3)应增加转速,增加背压压力使塑料粘度下降,密度增加。 (4)塑料要干燥好,再生料应少用,脱模剂用量太多或质量不好也会出现熔接缝。 (5)降低锁模力,方便排气。 2.模具方面: (1)同一型腔浇口过多,应减少浇口或对称设置,或尽量靠近熔接缝设置。 (2)熔接缝处排气不良,应开设排气系统。 (3)浇道过大、浇注系统尺寸不当,浇口开设尽量避免熔体在嵌件孔洞周围流动,或尽量少用嵌件。 (4)壁厚变化过大,或壁厚过薄,应使制件的壁厚均匀。 (5)必要时应在熔接缝处开设熔合井使熔接缝脱离制件。
树脂空洞铜箔起泡分析改善报告
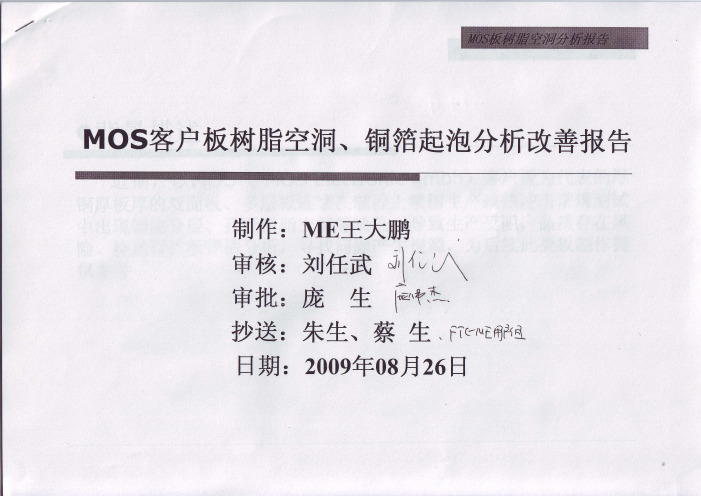
MOS板树脂空洞分析改善报告
z试板过程
喷锡及热冲击铜皮分层、PTH孔树脂空洞不良图片:
KB6165 喷锡
KB6167 喷锡
DF170 喷锡
ISOLA 喷锡
KB6165 漂锡
KB6167 漂锡
DF170 漂锡
ISOLA 漂锡
MOS板树脂空洞分析改善报告
z试板过程
喷锡及热冲击铜皮分层、PTH孔树脂空洞不良图片:
小结:使用KB6165、6167 HTG料压合喷锡后大铜皮处均出现大量 铜皮分层现象(因KB HTG无3OZ压合使用2OZ HTG压合电镀至3OZ), 而DF170、ISOLA370HR压合喷锡后无铜皮分层不良,喷锡后取PTH孔 切片分析KB6165出现有孔壁树脂空洞,其他均无,热冲击后, KB6165、6167 PTH孔均出现严重的孔壁树脂空洞,PIC DF170、 FL150、ISOLA370 HR孔壁状况良好,无树脂空洞等不良
近期,以MOS( MOS Electronic gmbh)客户板为代表的厚
铜厚板厚的双面板、多层板连续在制程上喷锡生产或热冲击常规测试 中出现铜皮分层、孔壁树脂空洞等缺陷,导致生产受阻,品质存在风 险。特进行试板评估分析,寻找问题产生根源,为后续此类板制作提 供参考
Байду номын сангаас
MOS板树脂空洞分析改善报告
z背景描述
z试板过程
3、试用不同供应商材料对比树脂空洞、喷锡铜皮分层状况; 选P/N30922采用相同结构、相同条件分别使用KB6165、KB6167、DF170、 ISOLA370 HR料试板,观察喷锡铜皮分层及热冲击树脂空洞情况,铜箔使用 KBHTG. 测试结果如下: 备注:喷锡为有铅喷锡,喷锡前烤板145℃/2小时,热冲击条件 288℃/10SEC/3次漂锡
树脂塞孔板BV-7463铜层起泡原因调查及改善总结
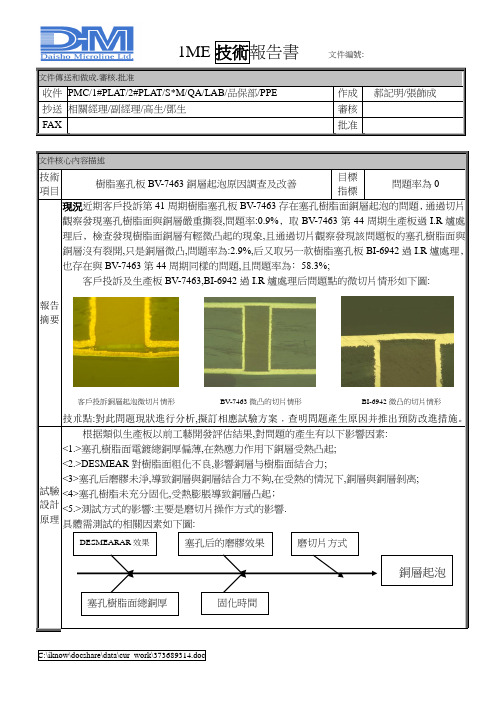
1ME
文件編號:
客戶投訴銅層起泡微切片情形 BV-7463微凸的切片情形 BI-6942微凸的切片情形
技朮點:對此問題現狀進行分析擬訂相應試驗方案﹐查明問題產生原因并推出預防改進措施。
根据類似生產板以前工藝開發評估結果,對問題的產生有以下影響因素: <1.>塞孔樹脂面電鍍總銅厚偏薄,在熱應力作用下銅層受熱凸起<2.>DESMEAR 對樹脂面粗化不良,影響銅層与樹脂面結合力
DESMEAR咬蝕狀況(2000倍)DESMEAR咬蝕狀況(5000倍)實驗室測試的P.T.H生益板料的除膠速率(11月份~12月份),結果合格,具體數據如下3/11/2006 除膠速率: 45.4mg/100cm2 24/11/2006 除膠速率:41.8 mg/100cm2
10/11/2006 除膠速率: 45.05 mg/100cm2 1/12/2006 除膠速率:52.3 mg/100cm2 SEM圖可以看出P.T.H后樹脂塞孔面蜂窩結構均勻﹐可見Desmear效果良好
理后再做切片如圖2:
圖2(經過IR爐處理)
可以發現的塞孔樹脂面銅層與前面第一次沉銅平板的銅層在塞孔平板顯然是塞孔后磨膠不干淨造成銅層與銅層的結合力不好,從而導致輕微開裂銅層起泡的切片圖與客戶投訴的BV-7463銅層起泡的切片圖相同,都是塞
銅層剝離問題的根本原因是塞孔后磨膠不干淨.
《圖
結果總結:通過對比圖1,圖2可以發現未填膠磨的切片的樹脂面與銅層結合處有裂開的跡象而填膠后磨的切片卻表明該塞孔樹脂面與銅層OK,同樣對比圖3,圖4也可以觀察到相同的現象.可見試驗<2>,<4>為正確的磨切片方式即磨切片時應將切片填膠且放置方向為平行磨輪旋轉方向.。
阻焊起泡原因分析及改善措施
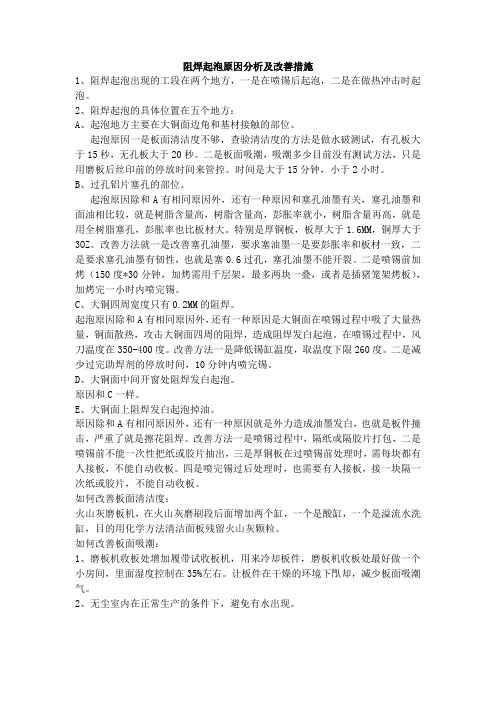
阻焊起泡原因分析及改善措施1、阻焊起泡出现的工段在两个地方,一是在喷锡后起泡,二是在做热冲击时起泡。
2、阻焊起泡的具体位置在五个地方:A、起泡地方主要在大铜面边角和基材接触的部位。
起泡原因一是板面清洁度不够,查验清洁度的方法是做水破测试,有孔板大于15秒,无孔板大于20秒。
二是板面吸潮,吸潮多少目前没有测试方法,只是用磨板后丝印前的停放时间来管控。
时间是大于15分钟,小于2小时。
B、过孔铝片塞孔的部位。
起泡原因除和A有相同原因外,还有一种原因和塞孔油墨有关,塞孔油墨和面油相比较,就是树脂含量高,树脂含量高,彭胀率就小,树脂含量再高,就是用全树脂塞孔,彭胀率也比板材大。
特别是厚铜板,板厚大于1.6MM,铜厚大于3OZ。
改善方法就一是改善塞孔油墨,要求塞油墨一是要彭胀率和板材一致,二是要求塞孔油墨有韧性,也就是塞0.6过孔,塞孔油墨不能开裂。
二是喷锡前加烤(150度*30分钟,加烤需用千层架,最多两块一叠,或者是插猪笼架烤板),加烤完一小时内喷完锡。
C、大铜四周宽度只有0.2MM的阻焊。
起泡原因除和A有相同原因外,还有一种原因是大铜面在喷锡过程中吸了大量热量,铜面散热,攻击大铜面四周的阻焊,造成阻焊发白起泡。
在喷锡过程中,风刀温度在350-400度。
改善方法一是降低锡缸温度,取温度下限260度。
二是减少过完助焊剂的停放时间,10分钟内喷完锡。
D、大铜面中间开窗处阻焊发白起泡。
原因和C一样。
E、大铜面上阻焊发白起泡掉油。
原因除和A有相同原因外,还有一种原因就是外力造成油墨发白,也就是板件撞击,严重了就是擦花阻焊。
改善方法一是喷锡过程中,隔纸戓隔胶片打包,二是喷锡前不能一次性把纸或胶片抽出,三是厚铜板在过喷锡前处理时,需每块都有人接板,不能自动收板。
四是喷完锡过后处理时,也需要有人接板,接一块隔一次纸或胶片,不能自动收板。
如何改善板面清洁度:火山灰磨板机,在火山灰磨刷段后面增加两个缸,一个是酸缸,一个是溢流水洗缸,目的用化学方法清洁面板残留火山灰颗粒。
特种印制电路板树脂塞孔及去除工序改善汇总

特种印制电路板树脂塞孔及去除工序改善汇总王劲公司PCB部门5年前在市场和产品方面启动转型,市场主要在军工客户,产品主要在HDI、射频微波、高速等特种印制板,目前基本跨上这个台阶。
公司经营打造以好和快为品牌,生产部门必须围绕这两个字开展所有工作,最终好和快是体现在产品上的质量好、交付快。
特种印制板是过去的叫法,相对于我公司以前没有的材料和工艺来确定,如:(局部)厚金工艺、厚铜蚀刻、厚铜压合、复合介质混压、背钻工艺(数控、蚀刻)、减铜工艺、真空树脂塞孔工艺、树脂去除工艺、填孔电镀工艺、埋器件工艺、台阶工艺、激光切割工艺等,目前我公司特种印制板基本由FR4、高频高速材料和这些工艺的组合加工而成。
按照公司安排对生产现场开展改善活动的要求,本人从生产质量问题最多、最不可控、最不稳定的工艺工序,特种产品基本上都会用到的工艺工序、工艺时间长的工艺工序入手,从年前一周到今天(2022年2月25日)用时20来天,对树脂塞孔、树脂去除、背钻孔清洁、铜浆塞孔、减铜工艺等进行了阶段性较为彻底的改善(目前没有文件化和标准化),仍有许多继续改善的空间。
一、该工序存在的质量问题及带给下工序的质量问题:板面大量凹坑、印制板尺寸变化大并且不一致、铜箔打穿造成局部无铜、铜箔厚度不一导致腐蚀报废、塞孔凹陷明显、塞孔树脂上部分无铜、塞孔周边铜层起泡、铜浆塞孔不平整等。
因该工序质量问题带来的整体交期无法确定、交期延误、影响其他工序质量及加工时间(侧腐蚀、腐蚀不干净等报废,因板材形变带来的一种印制板做成了几种印制板给工程、数控、丝印、文字、成型等工序增加了较多的工作量和质量隐患);质量问题带来的现场人员士气低落(质量不可控,不能做、不愿做、不敢做的心态较为明显,产品因此在现场出现停顿等待情况明显,管理人员对交期无法确定并且不能承诺);成本的增加(材料、能源、工时等没有统计,客户的信心)等。
材料供应商多次到厂未能解决问题,结合自己对我们的人机料法环测等特性的了解,改善活动主要围绕人、机、料、法、测来开展,并且会涉及到上下工序的一部分改善活动(关联工序改善会继续,如数控背钻、压合等),其改善的机理及要求在改善活动中对相关人员进行了培训,每一个改善背后的机理会在以后的文章中阐述,同时部分改善可以申请专利、可以为工厂二期建设提供参考和指导。
盲孔可靠性改善报告

盲孔可靠性改善报告一、前言:槽填孔过程中出现的空洞、凹陷值偏大、漏填等品质缺陷问题,对其产生原因进行深入分析,并通过组织相关测试手段及试验进行验证,试验结果表明:导电性不良,喷嘴堵塞是造成空洞、凹陷值偏大的主要原因。
漏填现象发生跟槽液中的气泡有关。
随着时尚消费类电子产品的不断更新换代,给PCB行业带来了更大的发展机遇。
该类电子产品具有轻薄化、多功能化、集成化、传输信号快、传输频率高等特点,要求其布线密度越来越大。
近年来HDI板产业因其高密度互连、高精细线路著称得到快速增长。
目前多阶HDI板的层间互连大多采用微孔叠孔及交错连接方式设计,一般是采用电镀铜填孔方式导通,如何运用好电镀填盲孔技术,确保填孔过程中品质,成为业界工作者考虑的问题。
毕竟电镀填孔与传统电镀有一定的差别,在工艺参数、流程设计、设备方面有着更为严格的要求。
填孔过程中的空洞、凹陷值(Dimple)、填孔药液控制稳定性等均是电镀填孔的难点。
本文将主要以实际开发应用过程中出现的填平不良(如空洞、凹陷值偏大、漏填等)缺陷进行分析,通过一系列分析和相关实验验证,得到了些改善填孔不良的思路和方法。
二、问题分析过程:1.不良现象种类:在填孔试验后通过目检发现,每块试验样板中都会出现少量盲孔填孔不良,通过对不良盲孔切片分析。
2.原因分析:通过切片确认,不良模式主要为凹陷值偏大、漏填、空洞和孔塞四种模式。
其中凹陷值值偏大、漏填比率最高,其次是空洞。
影响填孔电镀品质的因素很多,包括填孔电镀设备、电镀液组成、填孔工艺参数等各方面。
针对上述原因的分析,有重点地从以下几方面进行排查:(1)添加剂组分浓度失调:原理分析,盲孔的填孔主要是通过添加剂中各组分的协调作用、吸附差异平衡化完成,组分浓度的失控,势必造成添加剂在盲孔内吸附平衡的破坏,打破超等角填孔模式。
(2)导电性不良:每个夹头实际电流大小直接影响到该区域很大一部分盲孔的填孔效果,夹头电流大小不稳甚至夹头电流分布不均匀,势必影响到电场线在盲孔板面及孔口内分布,最终导致添加剂分布差异的失常,影响填孔效果。
气泡不良解析报告
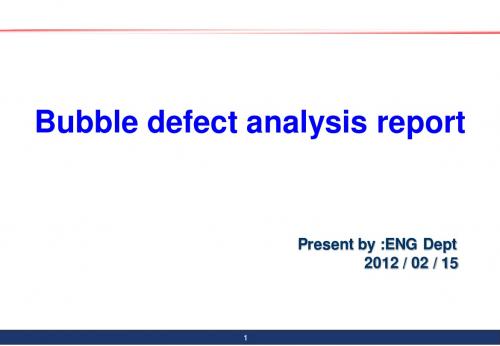
Present by :ENG Dept 2012 / 02 / 15
1
Catalogue
1. Defect information
2. Defect analysis 3. Correct action taken
2
1. Defect information
1.1 Bubble defect information :
40003 小批量试产,成品发现27pcs气泡,信息如下:
Defect Rate 24.11%
Station
Input
Bubble Defect
remark
FVBiblioteka 11227HTH贴合气泡
1.2 Defect picture :
Bubble defect picture show
结论:
气泡与OCA来料异常有关, 真因还待验证.
4
OCA设计要求
手动撕离位置
3. Correct action taken
3 : 改善措施:
3.1 满足设计要求的OCA新料验证 3.2 不同OCA的验证 3.3 生产参数的优化 3.4 HTH气泡与设备相关的改善
5
6
3
2. Defect analysis
2.1 : 气泡分布解析
Sensor 孔
位置 Sensor 孔端
数量 11(边角*4) 10(边角*5) 1
结论
Menu 孔
Menu 孔端 Two sides
1.气泡分布无明显的倒向性分布 2.气泡分布在上下两端比例大
2.2 : OCA来料异常解析
40003 采用加韵OCA, 作业时,由于轻离形与设计要求的50um不符 (实测为100um),轻离过重,导致设备无法自动撕离,需要人工手动预 撕离. 预撕离位置:OCA两侧,如图. 与气泡关系:与边角气泡会有直接关系,与所有气泡类型关系还未知
克服环氧树脂胶固化物的内在气泡问题

克服环氧树脂胶固化物的内在气泡问题环氧树脂胶固化物肯定将要产生起泡问题,假如是表面的气泡还只是导致表观或者是密封性的问题,假如是内在的气泡,简要影响到机械性能和电气性能,本文并未讨论生产胶的厂家对气泡的处理,只是简单的谈到了使用者碰到的问题,那么我们就先要了解下真空的概念和设备然后是气泡的克服问题。
真空定义指没有任何实物粒子存在的空间,地球上什么都没有的空间是不存在的就是真空不空,所以气泡对环氧树脂胶影响只能降到最低,不能完全消除。
真空度:压强低于101325帕斯卡(也即一个标准大气压强约101KPa)的气体状态,真空度的标识通常有两种方法:1、是用“绝对压力”、“绝对真空度”(即比“理论真空”高多少压力)标识;在实际情况中,真空泵的绝对压力值介于0~101.325KPa之间。
绝对压力值需要用绝对压力仪表测量,在20℃、海拔高度=0的地方,用于测量真空度的仪表(绝对真空表)的初始值为101.325KPa(即一个标准大气压)。
2、是用“相对压力”“相对真空度”(即比“大气压”低多少压力)来标识。
"相对真空度"是指被测对象的压力与测量地点大气压的差值。
用普通真空表测量。
在没有真空的状态下(即常压时),表的初始值为0。
当测量真空时,它的值介于0到-101.325KPa(一般用负数表示)之间。
例如:真空泵测量值为-75KPa,则表示泵可以抽到比测量地点的大气压低75KPa的真空状态,国际真空行业通用的“真空度”,也是最科学的是用绝对压力标识;指得是“极限真空、绝对真空度、绝对压力”,但“相对真空度”(相对压力、真空表表压、负压)由于测量的方法简便、测量仪器非常普遍、容易买到且价格便宜,因此广泛应用。
理论上二者是可以相互换算的,两者换算方法如下:相对真空度=绝对真空度(绝对压力)-测量地点的气压,例如:真空泵的绝对压力为80KPa,则它的相对真空度约为80-100=-20Kpa,(测量地点的气压假设为100KPa)在普通真空表上就该显示为-0.02MPa,常用的真空度单位有Pa、Kpa、Mpa、大气压、公斤(Kgf/cm2)、mmHg、mbar、bar、PSI等。
树脂空洞报告
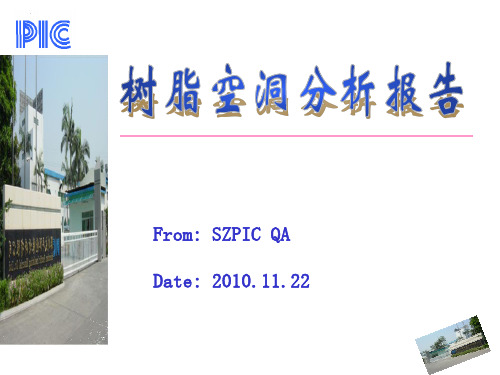
板材情况 物料规格:FL150 4mil 1/1 41*49" 来料日期:8/30/2010 MRR:0037649 P/O:K4-26500KI 来料数量 : 1800SH Lot No : 31008344 物料规格:FL150 4mil 1/1 41*49" 来料日期:8/30/2010 MRR:0037649 P/O:K4-26500KI 来料数量 : 1800SH Lot No : 11008202 物料规格:FL150 4mil 1/1 41*49" 来料日期:8/30/2010 MRR:0037649 P/O:K4-26500KI 来料数量 : 1800SH Lot No : 11008031
•10
制板编号
工序
报废数量 L2/L3 32panels Panel size: 18.42*22.35"
PH0235A
AOI
P62852C
AOI
L2/L3 2panels Panel size: 18.42*22.42"
P63056A
AOI
L2/L3 2panels Panel size: 18.35*23.35"
•11
PR
客户
物料
排板结构
缺陷描述
图片
IP4A351A
SAMSUNG
HF140
埋孔切片检查发现L2-L3层两埋 T 2 28(H/H) 孔间有树脂空洞,树脂空洞长度 2 T 为8.07mil,两埋孔间介质间距为 21.31mil,占34.62%
小结:树脂空洞为EEKP投诉的主要问题,EEKP定期将AOI挑出的不良品转 嫁给我司承担报废。 •12
5.2、工艺设备方面
1、设备组定期对压机进行保养,以保证压机温度、压 力、真空度等符合 要求 2、定期测量钢板平整度; 3、设备组对热板温度和平整度进行校正; 4、工艺优化压制工艺参数。
PTH孔无铜及吹孔改善
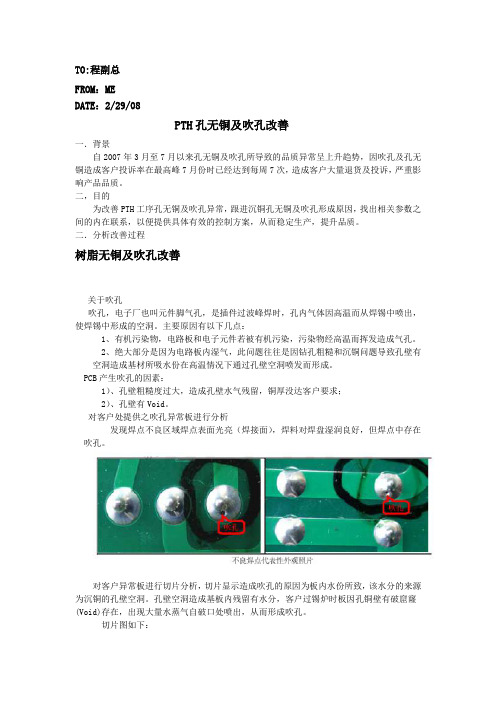
TO:程副总FROM:MEDATE:2/29/08PTH孔无铜及吹孔改善一.背景自2007年3月至7月以来孔无铜及吹孔所导致的品质异常呈上升趋势,因吹孔及孔无铜造成客户投诉率在最高峰7月份时已经达到每周7次,造成客户大量退货及投诉,严重影响产品品质。
二,目的为改善PTH工序孔无铜及吹孔异常,跟进沉铜孔无铜及吹孔形成原因,找出相关参数之间的内在联系,以便提供具体有效的控制方案,从而稳定生产,提升品质。
二.分析改善过程树脂无铜及吹孔改善关于吹孔吹孔,电子厂也叫元件脚气孔,是插件过波峰焊时,孔内气体因高温而从焊锡中喷出,使焊锡中形成的空洞。
主要原因有以下几点:1、有机污染物,电路板和电子元件若被有机污染,污染物经高温而挥发造成气孔。
2、绝大部分是因为电路板内湿气,此问题往往是因钻孔粗糙和沉铜问题导致孔壁有空洞造成基材所吸水份在高温情况下通过孔壁空洞喷发而形成。
PCB产生吹孔的因素:1)、孔壁粗糙度过大,造成孔壁水气残留,铜厚没达客户要求;2)、孔壁有Void。
对客户处提供之吹孔异常板进行分析发现焊点不良区域焊点表面光亮(焊接面),焊料对焊盘湿润良好,但焊点中存在吹孔。
对客户异常板进行切片分析,切片显示造成吹孔的原因为板内水份所致,该水分的来源为沉铜的孔壁空洞。
孔壁空洞造成基板内残留有水分,客户过锡炉时板因孔铜壁有破窟窿(Void)存在,出现大量水蒸气自破口处喷出,从而形成吹孔。
切片图如下:放大图镀铜空洞从金相切片分析镀铜空洞处为孔壁树脂上铜层空洞,且空洞处呈圆弧型,此种树脂上铜层空洞因背光不良引起,较严重的空洞会形成孔壁环切,造成孔壁镀铜断裂,电流不能导通;轻微的形成镀层空洞,在客户过高温炉时因镀铜空洞内容易藏水气引起吹孔上锡不良。
解决吹孔即为解决PTH树脂无铜,而解决背光不良为解决PTH树脂无铜的决定性因素。
我们可以从沉铜反应机理来分析影响背光效果的相关因素以期找出解决背光不良的相关控制解决方案。
沉铜的化学机理一)、流程:除油→微蚀→预活化→活化→加速→化学沉铜二)、流程步骤说明:除油:1)、Desmear后孔内呈两极现象,其中CU呈现高电位正点,环氧树脂及玻璃纤维呈负电。
【原创】注塑案例(21)--注塑产品之杯环周边气泡不良改善

【原创】注塑案例(21)--注塑产品之杯环周边气泡不良改善■产品信息:品名:量杯材料:PP透明尺寸规格:72.5mmx61.5mmx1.88mm模穴数:1 X 6 制品重量:12.5g模具规格两板模具、前模为热流道、采用气动封针封胶方式、高光面"注塑工艺:注塑机吨位:200T螺杆直径:Φ45mm炮筒温度190℃-225℃,模温设定:机水+冻水12℃,成型周期:15秒,使用4段射压及1段保压"产品后加工:无需加工,生产品外观确认,OK后直接包装"品质要求:产品表面划伤、发亮、欠注、结合线、变形、顶白、气泡等外观不良不可。
品质不良信息:产品杯环周边气泡不良高达33%。
不良产品图片作者:杨建宏,黄老师请看以下参数表:■案例改善过程信息:一、外观不良原因分析:模具开设的排气不合理,前模排气槽位太浅,排气位置也很少,型腔闭合中紧贴死,注塑填充过程,气体无法排出;所以才导致生产过程出现气泡不良。
注塑参数设定不合理(第三、第四段的射出速度太快,保压时间过长,另溶胶速度太快),所以导致生产品发生气泡不良。
模具温度设定及分配(前模温度低)不合理,加上热流道温度设定偏低,所以造成注塑填充过程树脂流道性差,出现的收缩迁移(无规则层缺陷),注塑件内部气泡不良。
二、改善对策过程:对模具(前模6个穴号全部重新开设排气槽)加排气处理,确保模具排气顺畅,改善模具困气问题。
注塑工艺参数重新调设:A.热流道温度在原基础上各段加高20度,提高树脂流动性。
B、模具温度重新布置,前模使用常温水约27度,而后模使用冻水12度。
C、第三及第四的射出速度放慢,采用多段位置精确控制走胶位置,在产品填充完成99%后转保压(短保压时间控制)。
D、熔胶速度减慢,另加大背压,确保树脂在炮筒中熔融密度增高,减少拉伸应力,控制气泡发生。
三、改善后成果展现:了解我们更多振业注塑汇 |专注于塑料行业服务本文由振业注塑汇原创,欢迎分享,禁止转载!。
- 1、下载文档前请自行甄别文档内容的完整性,平台不提供额外的编辑、内容补充、找答案等附加服务。
- 2、"仅部分预览"的文档,不可在线预览部分如存在完整性等问题,可反馈申请退款(可完整预览的文档不适用该条件!)。
- 3、如文档侵犯您的权益,请联系客服反馈,我们会尽快为您处理(人工客服工作时间:9:00-18:30)。
MOS板树脂空洞分析改善报告
z试板过程
喷锡及热冲击铜皮分层、PTH孔树脂空洞不良图片:
KB6165 喷锡
KB6167 喷锡
DF170 喷锡
ISOLA 喷锡
KB6165 漂锡
KB6167 漂锡
DF170 漂锡
ISOLA 漂锡
MOS板树脂空洞分析改善报告
z试板过程
喷锡及热冲击铜皮分层、PTH孔树脂空洞不良图片:
MOS板树脂空洞分析改善报告
z试板方案
结合以上分析,特制定以下试板方案: 1、通过不同热冲击条件,观察比较PTH孔壁树脂空洞、孔壁分离影 响的程度,并采用回流焊方式与热冲击进行比对; 2、对比钻孔参数调整以及烤板对树脂空洞改善评估; 3、试用不同供应商材料对比树脂空洞、喷锡铜皮分层状况;
MOS板树脂空洞分析改善报告
z试板过程
3、试用不同供应商材料对比树脂空洞、喷锡铜皮分层状况; 选P/N30922采用相同结构、相同条件分别使用KB6165、KB6167、DF170、 ISOLA370 HR料试板,观察喷锡铜皮分层及热冲击树脂空洞情况,铜箔使用 KBHTG. 测试结果如下: 备注:喷锡为有铅喷锡,喷锡前烤板145℃/2小时,热冲击条件 288℃/10SEC/3次漂锡
MOS板树脂空洞分析改善报告
z试板总结
3、喷锡铜皮分层与是否使用HTG铜箔无关,KB6160A使用的普通 铜箔而KB6165、6167使用的HTG铜箔喷锡后仍然出现大量铜皮分 层;KB6165、6167料热冲击后树脂空洞、树脂缩陷非常明显, KB6165在喷锡后PTH就出现树脂空洞,表明KB料整个耐热性欠佳、 Z-CTE膨胀系数相对比较大;而FL150、DF170、ISOLA370HR整 个的表现非常突出,喷锡后检查无任何铜皮分层、漂锡测试PTH孔也 无任何树脂空洞,孔壁状况良好,有轻微的树脂缩陷。表明材料性能 上的差异才是导致喷锡铜皮分层、孔壁树脂空洞的主要原因。
z试板过程
小结:通过采用优化的钻孔参数分步钻孔(主要是减少厚板钻 孔时钻咀摩擦高温对基材损伤)并配合烤板对此类孔壁 树脂空洞缺陷的改善不明显,烤板与不烤板、分步与不 分步热冲击测试的结果基本相同,即均有树脂裂纹/分 层现象. 备注:烤板条件145℃/2小时;热冲击288℃/10SEC/3次漂锡
MOS板树脂空洞分析改善报告
FL150 喷锡PTH孔
FL150漂锡PTH孔
FL150漂锡PTH孔 FL150漂锡PTH孔
MOS板树脂空洞分析改善报告
z试板总结
通过以上试板实验,对喷锡铜皮分层、PTH树脂空洞分析总结如下: 1、在热冲击测试,降低漂锡温度至270℃或漂锡前加烤145℃/2小时, 热冲击测试还是出现树脂空洞,有铅喷锡245℃PTH孔都不能幸免树 脂空洞的存在,而蚀刻外层铜皮,288℃浸锡3次,孔壁则无以上不 良,表明厚铜在喷锡或热冲击过程中镀铜孔壁吸附热量膨胀所产生的 热应力对基材内部结构破坏非常明显,主要是高温液锡进入孔腔瞬间 释放巨大热量,而回流焊测试2、3、4、5次孔壁基本未出现明显树脂 空洞,只有个别切片发现有树脂缩陷,相比较回流焊测试对基材内部 破坏性要小,主要是回流焊吸收热量比较容易释放 2、优化钻孔条件,钻孔参数采用分步钻孔并配合烤板对孔壁树脂空洞 改善效果不明显,即不采用分步钻孔与采用分步钻孔、烤板与不烤板 在树脂空洞的预防上没有任何作用,热冲击测试均出现树脂裂纹/分层。
2、对比钻孔参数调整以及烤板对树脂空洞改善评估; a:进刀速下降20%,钻咀寿命不变,磨2以内钻咀,1PNL/叠,不 烤板 b:进刀速下降20%,钻咀寿命不变,磨2以内钻咀,1PNL/叠,钻 孔前烤板 c:进刀速下降20%,钻咀寿命不变,磨2以内钻咀,1PNL/叠,采 用分步钻孔(分3次钻通),不烤板 d:进刀速下降20%,钻咀寿命不变,磨2以内钻咀,1PNL/叠,采 用分步钻孔(分3次钻通),钻孔前烤板 备注:烤板条件为145℃/2小时 测试结果如下:
备注:热冲击测试条件为:288℃/10sec/3次漂锡
MOS板树脂空洞分析改善报告
z不良板汇总
从以上统计的MOS板型号特征上看,喷锡或热冲击发现PTH孔有树 脂空洞、孔壁分离、大铜皮位喷锡铜皮分层的现象,不良板均为厚铜 厚板厚(外层铜厚均在3OZ以上,压板板厚在2mm以上),使用材料 为KB6160A。 综合以上不良信息,可能导致树脂空洞原因涉及到高铜厚板对材料 耐热性要求,厚板钻孔参数、材料性能、铜箔性能等.
2次OK
3次OK
4次有孔壁分离
5次OK
b、测试表明,回流焊测试与热冲击相比,回流焊对材料内部破坏性比漂锡要小, 尤其是通孔四周,主要是漂锡时高温液锡进入孔腔并焊在孔壁上受热膨胀产生 极大的热应力导致基材结构破坏,而回流焊吸收的热量则容易释放,相对对基 材损伤要小.
MOS板树脂空洞分析改善报告
z试板过程
\
〓●⑴ 飒 丶 菏 茸 蒜 辩 崮 J 崮漭 褂 茴 斗 茸 畔 珊 茹 玢
口 嗒 廿 册 逆 对 斋 龚o● 潴 ● ● ● ● ● 。 。涞 ●
黑日 H汁 嚣 冫 ・丶 鲨帘拂 G 一 /
计 " ' 叩 Γ
£亟 岁 ㈡
汪 3 书 〓 洳× 囗
MOS板树脂空洞分析改善报告
z背景描述
MOS板树脂空洞分析改善报告
z试板过程
38155调整钻孔参数、烤板试板
钻孔条件 状态 未焗板 未分步钻孔 焗板 3pnls 有树脂裂纹/分层 数量 3pnls 浸锡后PTH孔状态 有树脂裂纹/分层
切片图
未焗板 分步钻孔 焗板
3pnls
有树脂裂纹/分层
3pnls
有树脂裂纹/分层
MOS板树脂空洞分析改善报告
z试板过程
1、通过不同热冲击条件,观察PTH孔壁树脂空洞、孔壁分离影响的程度, 并采用回流焊方式与热冲击进行比对 取生产的板30922-1A04(缺陷有树脂空洞、树脂回缩、喷锡铜皮分层) 采用270℃/10sec/3次漂锡测试、150℃/2小时烤板后288℃/10sec/3 次漂锡测试、煲绿油蚀刻外层铜皮,光板288℃/10sec/3次浸锡测试 测试结果:降低锡炉温度到270℃漂锡3次及150℃/2小时烤板后 288℃漂 锡3次PTH孔均有树脂空洞、树脂回缩等不良,而蚀刻外层铜 皮, 288℃浸锡3次则未出现树脂空洞不良(不良图片见page8) 以上表明:厚表铜在受热情况下热量积聚所产生的热应力对材料的破坏 极大,相对要求材料高耐热承受力及非常低的Z-CTE,而KB6160特性不能 满足以上要求.
近期,以MOS( MOS Electronic gmbh)客户板为代表的厚
铜厚板厚的双面板、多层板连续在制程上喷锡生产或热冲击常规测试 中出现铜皮分层、孔壁树脂空洞等缺陷,导致生产受阻,品质存在风 险。特进行试板评估分析,寻找问题产生根源,为后续此类板制作提 供参考
MOS板树脂空洞分析改善报告
z背景描述
小结:使用KB6165、6167 HTG料压合喷锡后大铜皮处均出现大量 铜皮分层现象(因KB HTG无3OZ压合使用2OZ HTG压合电镀至3OZ), 而DF170、ISOLA370HR压合喷锡后无铜皮分层不良,喷锡后取PTH孔 切片分析KB6165出现有孔壁树脂空洞,其他均无,热冲击后, KB6165、6167 PTH孔均出现严重的孔壁树脂空洞,PIC DF170、 FL150、ISOLA370 HR孔壁状况良好,无树脂空洞等不良
PTH树脂空洞(一)
PTH树脂空洞(二)
PTH平面切片(三)
喷锡铜皮分层(四)
MOS板树脂空洞分析改善报告
z不良板汇总
MOS树脂空洞生产板情况
型号 37771-1A04 38109-1A04 38001-1A04 37900-1A04 30922-1a04 表面处理 沉锡 沉锡 有铅喷锡 有铅喷锡 有铅喷锡 板料 KB6160A KB6160A KB6160A KB6160A KB6160A 基板规格 62±5 3/3 62±5 3/3 62±5 3/3 47±5 3/3 39±3 3/3 外层铜厚 3OZ→5.6 3OZ→5.6 3OZ→5.6 3OZ→5.6 3OZ→4.2 压板厚度 122±9 122±9 133±13 90±8 88±8 PTH孔测试情况 沉锡 漂锡 沉锡 漂锡 喷锡 漂锡 喷锡 漂锡 喷锡 漂锡 / 树脂空洞 / 树脂空洞 树脂空洞 树脂空洞 树脂空洞 树脂空洞 树脂空洞 树脂空洞 铜皮分层 备注
MOS板树脂空洞分析改善报告
z结论及建议
综合以上试板测试结果及分析,导致以MOS客户板厚铜厚板厚型号 喷锡出现铜皮分层、热冲击PTH孔出现树脂空洞、树脂缩陷等缺陷的主 要原因是由于目前使用的KB料整体耐热性不佳、Z-CTE膨胀系数相对较 大,而使用ISOLA370、PIC FL150、DF170品质OK 建议: 1、对于外层铜厚≥2OZ的型号,建议使用PIC FL150、DF170改善 MOS类似结构板PTH孔树脂空洞、铜箔起泡问题,对于客户无Tg要求 的,优先选用PIC FL150材料。 2、KB研发的6165F、6167F尽快能评估并试产,目前KB6165, 6167品质表现不佳、性能上长期存在的缺陷(耐热性差、Z-CTE大引起 的白点、爆板、铜皮分层、树脂缩陷等)。
MOS板树脂空洞分析改善报告
z试板过程
270℃漂锡(一)
烤板 288℃漂锡(二)
蚀刻铜皮 288℃浸锡(三)
270℃漂锡(四)
MOS板树脂空洞分析改善报告
z试板过程
无铅回流焊条件分别2、3、4、5次对比PTH孔树脂空洞状况: a、测试结果:无铅回流焊2.3.4.5次PTH孔相对喷锡或漂锡条件树脂空 洞都有明显减轻,且大部分PTH孔切片未发现有树脂空洞不良,只有 个别切片发现有孔壁分离(如下图)
MOS板树脂空洞分析改善报告
z试板过程
30922试板测试结果
编号 ① ② ③ ④ 板料型号 KB6165 KB6167 PIC DF170、FL150 ISOLA370HR 数量pnls 6 6 6+12 6 喷锡铜皮分 层 有 有 无 无 PTH孔树脂空洞情况 喷锡 有 无 无 无 热冲击 有 有 无 无 备注