生产计划管理培训课程.ppt
合集下载
生产计划培训教材(ppt 40页)

生产控制部门的作用有哪些?
生产控制部门的作用主要有: 1.对销售部门接到的订单能协调出一个较为合理的年度、季度、 月度销货计划。 2.对销售部门随意变更生产计划、紧急加单或任意取消单能进 行适当的限制。 3.根据产能负荷分析资料,能制定出一个合理完善的生产计划, 对生产订单的起伏、生产计划的变更有准备措施,预留“备份 程序”。 4.能准确地控制生产的进度,能对物料控制人员做好物料进度 的督促。 5.当生产进度落后时,能及时主动的跟有关部门商量对策,协 商解决办法,并采取行动,加以补救。
生产能力
决定产能的步骤有哪些?
决定产能的步骤可分为以下三步: 1.决定毛产能:
假定套管挤出车间细管挤出机器为19台,每周工作7天,每 天工作2班,每班工作12小时且没有任何停机时间,这是细管挤 出设备在完全发挥最理想的状态下的最高生产潜力。毛产能是 个理论值,它是个理想值或者可以说是个标准参考值,作为以 后计算实际产能的基准。
生产计划培训
讲师: 培训日期:
主要内容
1 生产与计划控制概论 1.1 什么是生产与物料控制(PMC)? 1.2 良好的PMC管理应该做到哪几点? 1.3 PMC管理做得差,容易造成什么现象?
2 生管的组织结构与职能 2.1 生管人员的工作职责 2.2 生管人员岗位素质要求 3 生产计划与进度控制 3.1 生产能力 3.2 销售与生产计划 3.3 生产进度控制 2
生产与计划控制概论
PMC管理做得差,容易造成什么现象?
PMC的计划能力、控制能力及沟通协调能力做得差容易造成 以下现象: 1.经常性的停工待料
因为生产无计划或物料无计划,造成物料进度经常跟不上,以 至经常性的停工待料。 2.生产上的一顿饥来一顿饱
因为经常停工待料,等到一来物料,交期自然变短,生产时间 不足,只有加班加点赶货,结果有时饿死有时撑死。 3.物料计划的不准或物料控制的不良,半成品或原材料不能衔接 上,该来的不来,不该来的一大堆,造成货仓大量堆积材料和 半成品,生产自然不顺畅。
生产控制部门的作用主要有: 1.对销售部门接到的订单能协调出一个较为合理的年度、季度、 月度销货计划。 2.对销售部门随意变更生产计划、紧急加单或任意取消单能进 行适当的限制。 3.根据产能负荷分析资料,能制定出一个合理完善的生产计划, 对生产订单的起伏、生产计划的变更有准备措施,预留“备份 程序”。 4.能准确地控制生产的进度,能对物料控制人员做好物料进度 的督促。 5.当生产进度落后时,能及时主动的跟有关部门商量对策,协 商解决办法,并采取行动,加以补救。
生产能力
决定产能的步骤有哪些?
决定产能的步骤可分为以下三步: 1.决定毛产能:
假定套管挤出车间细管挤出机器为19台,每周工作7天,每 天工作2班,每班工作12小时且没有任何停机时间,这是细管挤 出设备在完全发挥最理想的状态下的最高生产潜力。毛产能是 个理论值,它是个理想值或者可以说是个标准参考值,作为以 后计算实际产能的基准。
生产计划培训
讲师: 培训日期:
主要内容
1 生产与计划控制概论 1.1 什么是生产与物料控制(PMC)? 1.2 良好的PMC管理应该做到哪几点? 1.3 PMC管理做得差,容易造成什么现象?
2 生管的组织结构与职能 2.1 生管人员的工作职责 2.2 生管人员岗位素质要求 3 生产计划与进度控制 3.1 生产能力 3.2 销售与生产计划 3.3 生产进度控制 2
生产与计划控制概论
PMC管理做得差,容易造成什么现象?
PMC的计划能力、控制能力及沟通协调能力做得差容易造成 以下现象: 1.经常性的停工待料
因为生产无计划或物料无计划,造成物料进度经常跟不上,以 至经常性的停工待料。 2.生产上的一顿饥来一顿饱
因为经常停工待料,等到一来物料,交期自然变短,生产时间 不足,只有加班加点赶货,结果有时饿死有时撑死。 3.物料计划的不准或物料控制的不良,半成品或原材料不能衔接 上,该来的不来,不该来的一大堆,造成货仓大量堆积材料和 半成品,生产自然不顺畅。
生产计划培训课件
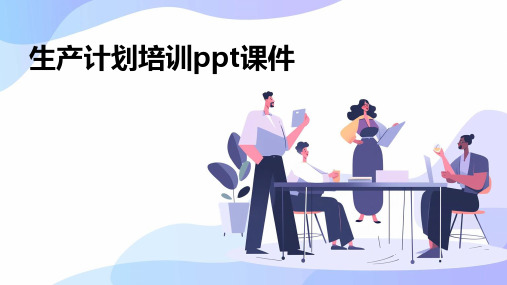
生产异常处理
异常识别
及时发现生产过程中的 异常情况,如设备故障 、质量问题、人员缺勤 等。
异常处理
采取有效措施,解决异 常情况,确保生产顺利 进行。
预防措施
分析异常原因,制定预 防措施,防止类似异常 再次发生。
06
案例分析
某企业生产计划案例
案例概述
某企业面临生产计划不准确、交货延误等问题,导致客户满意度下降。
功能
生产调度系统能够实时监控生产设备的运行状态、生产进度和产品 质量,及时发现和解决生产过程中的问题,确保生产计划的顺利实 施。
优点
生产调度系统能够提高生产效率、减少生产延误和浪费,提高产品质 量和客户满意度。
生产管理软件
定义
生产管理软件是一种集成了生产计划、生产调度、质量管 理和物料管理等功能的管理软件,能够帮助企业实现生产 过程的全面管理。
解决方案
采用先进的生产计划方法,如MRP、JIT等,优化生产流程,提高计划准确性。
实施效果
通过改进生产计划管理,企业交货准时率提高,客户满意度上升。
某企业库存管理案例
01
案例概述
某企业库存积压严重,导致库存 成本增加、资金占用和产品过时 风险。
解决方案
02
03
实施效果
采用先进的库存管理方法,如 ABC分类法、实时库存更新等, 降低库存水平。
功能
生产管理软件能够实现从销售预测、生产计划、采购管理 、生产调度到质量管理的全面集成,提高生产效率和产品 质量。
优点
生产管理软件能够提高企业的生产管理水平和信息化水平 ,降低生产成本和提高市场竞争力。
04
生产计划优化方法
资源优化
设备资源优化
生产计划管理的培训课程.pptx

运作程序
作业要点
应用表单
产销配合与存货调整
1 销售计划表
1 生产计划
物料需求计划(MRP:物料) 2 生产计划表 产能需求规划(CRP:人力、 3 产能与负荷分析表
设备)
4 成品库存表
2 過程计划
产品资料之建立与运用 经济制程之设计 生技业务之开发与改善
1 标准材料表(BOM) 2 标准途程表(SOP) 3 标准工时表(ST)
图—一般产品订货生产计划与管制作业程序图 接单
物料管制
作业准备
进度安排
工作调派
进度管制
管理策略
制定弹性的产销管理制度 做好协力厂商管理以避免欠料停工 合理选择自制或外包作业 混合性工厂布置之运用 实施小批量生产 培养多能工使工作及人员安排更有弹性 推展目视管理,重视异常问题之处理
管理策略
定期如开产销协调会
③ 其他: 有关的产销配合事宜(包括人员、设备、材 料等的准备或异常状况)
报告内容:
① 上一周产量报告。 ② 产量差异原因及分析报告。 ③ 下一周生产预定活动状况及协调事宜。 ④ 业务动态报告及协调事宜。 ⑤ 协调总决议案之报告。
日常产销配合工作之执行
图表—订货式生产工厂日常产销工作配合流程图
1 订单 2 变更单
1 销售目标 2 产销计划 3 订单、变更通知
1 生产计划 2 生产日程安排、变更 3 制造通知、修改
客户
销售
产销
1 产能设定 2 最佳排程 3 用料计划 4 产销控制
生产
1 交期答复 2 承订变更协调
1 订单内容不明反应 1 生产日报 2 交期安排、异常反应 2 异常报告
日常产销配合工作之执行
4 标准成本表(SC)
生产计划培训教材(PPT 60页)

时间
避免了生产规模的改变 库存成本增加
库存减少
时间
元宵节装饰用灯
18
公司未来三个月以均衡生产1万个灯泡。平均每天应该生产 多少? 工厂日历:第一个月:20个工作日
第二个月:21个工作日 第三个月:9个工作日 平均每天生产: 10000/(20+21+9)=200个
19
假设的需求曲线 需 求
产品外包战略 需 求
制定生产大纲的目的:最大程度地减低库存管理成本、变 更生产规模成本、以及缺货成本
22
制定计划所需信息: 计划时间内的阶段性预测 期初库存量 所希望的期末库存量 客户到期订单(到期还没有配送的订单)
23
均衡生产大纲的制定: 大致流程: 1)计划期需求汇总; 2)确定期初库存和所希望的期末库存 3)计算总生产需求: 总预测+滞后订单+期末库存-期初库存 4)计算每期需要生产的量 5)计算每期的期末库存量
11
假想产品法计算生产能力 有8台车床,每台车床年有效工作时间为4650小时
12
能力需求计划的编制
加工任务 (计划订单+确认订单+已下达订单)
工艺路线
需用能力 工艺路线
可用能力
工艺路线
能力负荷平衡表
13
能力需求计划的分析
如果工作中心的能力和负荷不平衡,调整工 作必须由计划人员人工完成。主要的调整 方式为:
工作中心利用率=实际投入工时/计划工时 工作中心效率=完成定额工时/实际投入的
工时 完成定额工时=生产的产品数量×按工艺
路线计算的定额工时
9
生产能力
▪ 代表产品与假定产品 ▪ 生产能力与生产任务 ▪ 生产能力计划(例题7-1) ▪ 生产能力的处理
生产计划管理培训课件(PPT 174页)
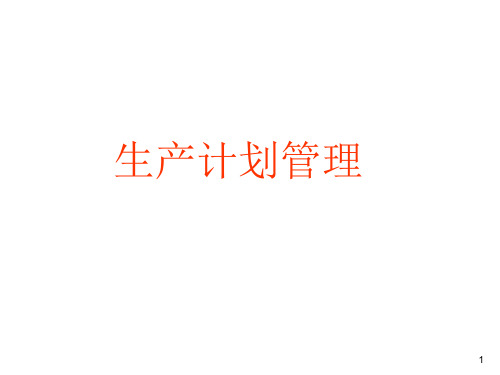
=4 × 50
=200min
21
2. 平行移动方式
• 每件产品在前道工序加工完毕后,立即转移到后道工序继 续加工,产品在各道工序上平行作业;
• 此移动方式其产品的加工时间最短,但运输频繁,当前后 工序的作业时间不相等时,设备产生停歇等待加工现象。
工序
作业时间
工序号
时间 10 20 30 40 50 60 70 80 90 100 110 120 130 140 150 160 170 180 190 200
PREP
BOARD LEVEL TESTING
CONN / PCB ASSY
MANUAL INSERT
BOARD PREP.
WAVE SOLDER
IN-CIRCUIT TEST
ANALYZE REPAIR
COATING
FINAL
ASSEMBLY
FINAL TEST
LABEL ATTACH
PACK
Q.C. AUDIT
No.
特性
多品种
1
不稳定
调整多
品种多 换线多
优化思路和方法
批量小
2
小批量
样件多 效率/成本
压力
3
交期短
4
内外部瓶颈限制
6
制造型企业的生产要素分析
企业战略规划
人力资源
财务
营销
生产运作
...
生
产
系
广 义 工
统 设 置
厂
管
理
狭 义 工 厂 管
生 产 系 统 运
理行
产品决策 产品设计 工艺设计 产品试制
厂址选择 生产规模与技术决策 生
=110min
=200min
21
2. 平行移动方式
• 每件产品在前道工序加工完毕后,立即转移到后道工序继 续加工,产品在各道工序上平行作业;
• 此移动方式其产品的加工时间最短,但运输频繁,当前后 工序的作业时间不相等时,设备产生停歇等待加工现象。
工序
作业时间
工序号
时间 10 20 30 40 50 60 70 80 90 100 110 120 130 140 150 160 170 180 190 200
PREP
BOARD LEVEL TESTING
CONN / PCB ASSY
MANUAL INSERT
BOARD PREP.
WAVE SOLDER
IN-CIRCUIT TEST
ANALYZE REPAIR
COATING
FINAL
ASSEMBLY
FINAL TEST
LABEL ATTACH
PACK
Q.C. AUDIT
No.
特性
多品种
1
不稳定
调整多
品种多 换线多
优化思路和方法
批量小
2
小批量
样件多 效率/成本
压力
3
交期短
4
内外部瓶颈限制
6
制造型企业的生产要素分析
企业战略规划
人力资源
财务
营销
生产运作
...
生
产
系
广 义 工
统 设 置
厂
管
理
狭 义 工 厂 管
生 产 系 统 运
理行
产品决策 产品设计 工艺设计 产品试制
厂址选择 生产规模与技术决策 生
=110min
生产计划管理培训教材(PPT 77页)

上中下 旬旬旬 预测计划
准备计划
实施计划
4月
上中下 旬旬旬
预测计划 准备计划
5月
上中下 旬旬旬
预测计划
19
在编制本轮实施的月作业计划时,是根据上轮编制的 月准备作业计划,考虑到外协件、配套件的供应变化以及 厂内工艺准备,劳动力情况的变化以及上轮实施月作业计 划的实际差异,对上轮准备计划进行调整、修改、补充, 使其具体化,并把它作为本轮实施的月作业计划。当发现 上轮预测作业计划不准确、不完整时,就调整、修订为本 轮第二个月的准备计划。然后继续编制本轮第三个月的预 测计划。如此类推,逐月滚动,从而保证编制的生产作业 计划更符合实际,更加可行。
⒊根据以上两项分析研究,按照企业经营目标的要求, 考虑企业的现有资源和生产潜力,提出生产经营计划 指标体系,并进行综合平衡。如品种、质量、产量、 产值、成本、利润、税收、销售额、劳动生产率、产 品合格率等。
⒋编制两套以上的不同生产计划方案,在经过分析论证 的基础上,进行综合评价和比较,选出最佳生产经营 计划方案。
章
1
第7章 生产计划
• 7.1 计划管理的一般概念 • 7.2 综合计划策略 • 7.3 MTS企业生产计划的制定 • 7.4 MTO企业生产计划的制定 • 7.5 收入管理
2
7.1 计划管理的一般概念
• 7.1.1 企业计划的层次 • 7.1.2 生产计划的层次 • 7.1.3 制定计划的一般步骤及滚动计划 • 7.1.4 生产能力
线性规划、运输问题算 法、搜索决策法则SDR 、
线性决策法则
LDR
旬、周、日 车间及有关部门 MRP、批量算法
工作日、小时、分 工段、班组、工作地
各种作业排序方法
7
准备计划
实施计划
4月
上中下 旬旬旬
预测计划 准备计划
5月
上中下 旬旬旬
预测计划
19
在编制本轮实施的月作业计划时,是根据上轮编制的 月准备作业计划,考虑到外协件、配套件的供应变化以及 厂内工艺准备,劳动力情况的变化以及上轮实施月作业计 划的实际差异,对上轮准备计划进行调整、修改、补充, 使其具体化,并把它作为本轮实施的月作业计划。当发现 上轮预测作业计划不准确、不完整时,就调整、修订为本 轮第二个月的准备计划。然后继续编制本轮第三个月的预 测计划。如此类推,逐月滚动,从而保证编制的生产作业 计划更符合实际,更加可行。
⒊根据以上两项分析研究,按照企业经营目标的要求, 考虑企业的现有资源和生产潜力,提出生产经营计划 指标体系,并进行综合平衡。如品种、质量、产量、 产值、成本、利润、税收、销售额、劳动生产率、产 品合格率等。
⒋编制两套以上的不同生产计划方案,在经过分析论证 的基础上,进行综合评价和比较,选出最佳生产经营 计划方案。
章
1
第7章 生产计划
• 7.1 计划管理的一般概念 • 7.2 综合计划策略 • 7.3 MTS企业生产计划的制定 • 7.4 MTO企业生产计划的制定 • 7.5 收入管理
2
7.1 计划管理的一般概念
• 7.1.1 企业计划的层次 • 7.1.2 生产计划的层次 • 7.1.3 制定计划的一般步骤及滚动计划 • 7.1.4 生产能力
线性规划、运输问题算 法、搜索决策法则SDR 、
线性决策法则
LDR
旬、周、日 车间及有关部门 MRP、批量算法
工作日、小时、分 工段、班组、工作地
各种作业排序方法
7
生产计划培训课件(PPT 38页)
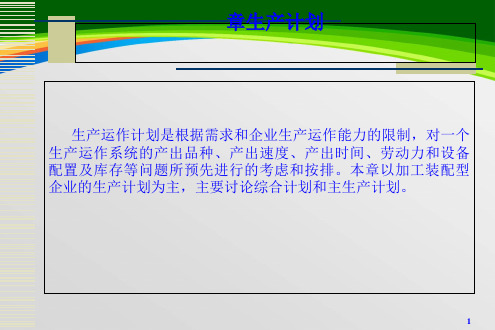
个生产周期中每一时段对关键资源的需求量; (3)综合因子法(method of overall factors)
29
(一)综合因子法
(1)全部关键工序的总劳动时间=每一MPS量×全部关键工序的直接劳动因子; (直接劳动时间/件)
(2) 某关键工序所需劳动时间估计值(负荷估计量)=某时段全部关键工序的 总劳动时间×该关键工序的负荷因子( 该关键工序的劳动时间 )
9
二、综合计划的主要目标及其相悖关系分析
表9-4 综合计划的目标
成本最小/利润最大 顾客服务最大化(最大限度满足顾客需求) 最小库存投资 生产速率的稳定性(变动最小) 人员水平变动最小 设施、设备的充分利用
10
三、两种基本的决策思路
(一)稳妥应变型 根据市场需求制定相应的计划。通常应变方法有:
MPS方案 NO
满足资源约束? YES
批准MPS MRP
23
二、制定主生产计划的基本模型
(一)计算现有库存(projected on-hand Inventory, POH)
It It 1P tM(F a t,C xt)(O 9-5) MPS产量 预计需求 准备发货的顾客订货量
(二)决定MPS的生产量和生产时间
18
表9-6 公司综合计划
调节库存=前期库存+本期库存-本期需求, 例:510=250+(450+90+20)-300
19
(二)图表法的进一步应用
改变生产能力,得最优生产计划,再比较; 考虑允许任务积压的情况。
(三)线性规划法
目标函数:成本最小; 约束条件:人员数量关系、库存量关系、加班量关系等。 多目标规划。
20
第三节 主生产计划的制定
29
(一)综合因子法
(1)全部关键工序的总劳动时间=每一MPS量×全部关键工序的直接劳动因子; (直接劳动时间/件)
(2) 某关键工序所需劳动时间估计值(负荷估计量)=某时段全部关键工序的 总劳动时间×该关键工序的负荷因子( 该关键工序的劳动时间 )
9
二、综合计划的主要目标及其相悖关系分析
表9-4 综合计划的目标
成本最小/利润最大 顾客服务最大化(最大限度满足顾客需求) 最小库存投资 生产速率的稳定性(变动最小) 人员水平变动最小 设施、设备的充分利用
10
三、两种基本的决策思路
(一)稳妥应变型 根据市场需求制定相应的计划。通常应变方法有:
MPS方案 NO
满足资源约束? YES
批准MPS MRP
23
二、制定主生产计划的基本模型
(一)计算现有库存(projected on-hand Inventory, POH)
It It 1P tM(F a t,C xt)(O 9-5) MPS产量 预计需求 准备发货的顾客订货量
(二)决定MPS的生产量和生产时间
18
表9-6 公司综合计划
调节库存=前期库存+本期库存-本期需求, 例:510=250+(450+90+20)-300
19
(二)图表法的进一步应用
改变生产能力,得最优生产计划,再比较; 考虑允许任务积压的情况。
(三)线性规划法
目标函数:成本最小; 约束条件:人员数量关系、库存量关系、加班量关系等。 多目标规划。
20
第三节 主生产计划的制定