第二章 催化裂解装置大型机组试车方案
催化裂化装置介绍ppt课件
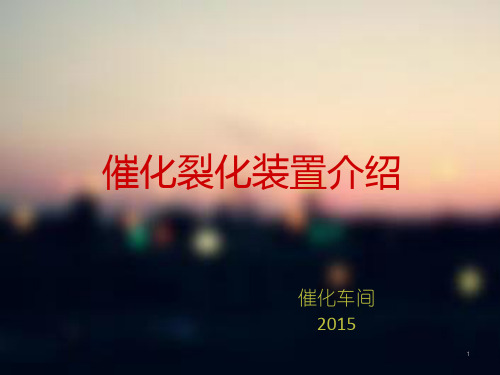
催化裂化主要设备-油浆泵
20
催化裂化主要设备-增压机
21
催化裂化主要设备-SIS自保系统
22
催化裂化主要设备-单动滑阀
23
催化裂化主要设备-双动滑阀
24
催化裂化主要设备-油站
25
催化裂化的原料和产品
新海石化加工工艺流程图
26
催化裂化的原料和产品
1.直馏减压馏分油:常减压装置减压塔侧线350-550℃馏分 油(VGO),石蜡基原油的VGO较好,环烷基原油的VGO 较差。
2.延迟焦化馏出油:焦化装置分馏塔侧线320-500℃馏出油 (CGO)也叫焦化蜡油。这种原料氮含量和芳烃含量都 很高不是理想的原料通常掺炼比为5-15%.
3.常压渣油:常减压装置常压塔底油(AR),硫含量、重 金属、残炭低的可以直接作为催化原料,如大庆和中原 原油等常压渣油。
4.减压渣油:除某些原油外减压塔底渣油(VR)一般不单 独作为原料,而是进行掺炼:掺炼的多少视减压渣油的 性质。
9
典型分馏系统流程
10
催化裂化工艺介绍
稳定系统
吸收-稳定系统主要由吸收塔、再吸收塔、解吸 塔及稳定塔组成。从分馏塔顶油气分离器出来的 富气中带有汽油组分,而粗汽油中溶解有C3、C4 组分。其作用是利用吸收与精馏的方法将分馏塔 顶的富气和粗汽油分离成干气、液化气和蒸气压 合格的稳定汽油。
11
典型稳定系统流程
催化裂化工艺介绍
分馏系统
分馏系统的主要作用是把反应器(沉降器)顶的气态产物,按沸点范围分 割成富气、汽油、轻柴油、重柴油、回炼油和油浆等产品。由反应器来的 460~510℃的反应产物油气从底部进入分馏塔,经底部的脱过热段后在分馏 段分割成几个中间产品:塔顶为汽油及富气,侧线有轻柴油、重柴油和回炼 油,塔底产品为油浆。塔顶的汽油和富气进入吸收-稳定系统;柴油经汽提、 换热、冷却后出装置;油浆用泵从脱过热段底部抽出后分两路:一路直接送 进提升管反应器回炼,若不回炼,可经冷却送出装置。另一路与原料油换热, 再进入油浆蒸汽发生器,大部分作循环回流返回分馏塔脱过热段上部,小部 分返回分馏塔底,以便于调节油浆取热量和塔底温度。
催化裂化装置开车方案

一、动工总那么1、装置检修施工所有结束,在动工指挥部一致安排下,联合检查工程质量并检验合格,现场到达工完料尽场所清,遗留问题办理达成,装置已如期经过吹扫试压,单机试运水冲洗等步骤。
2、车阀干部、技术员、操作工必定仔细学习动工方案特别是岗位工人须经考试合格前面可赞同上岗操作。
3、车阀组织对工艺和设施的整改工程交底、讲解,每位操作工做到胸有成竹。
4、动工过程中必定加强领导,协调一致,分工负责,科学地按动工网络图安排工作。
5、把安全置在首位,在动工过程中与安全有矛盾的均应遵从“安全第一〞这一原那么。
二、动工准备1、保证装置内大小通道及装置至厂内干道畅达,装置出入物料畅达,公用系统如水、电、气、风、氮等物料必定吻合工艺要求,并到达连通待用的条件。
2、装置开车在动工指挥部一致指挥下进行,并联系各职能科室、新炼公司做好动工保证工作,以便在相关单位共同下顺利进行。
3、联系部调换准备开车用的蜡油、汽油、柴油、瓦斯氮气等,做好物料调换工作。
4、联系好厂调换,确认好汽油、柴油、液态烃的成品罐及溶剂脱沥青油、重蜡油、减压渣油、轻油、油浆、燃料油等贮罐,以及将动工所需油品备齐贮足。
5、联系好解析二室及时配合好做好开车油、催化刘、碱液、氮水、酸性气及烟气等的解析工作,联系环保科做好三废治理安排及环保分析准备。
6、联系好机、电、仪等相关保镖单位到开车现场,保证开车工作顺利进行。
7、联系安全科,抵消防器材、消防设施进行检查,确认好用,装好各处消防蒸汽带,并准备相关通讯手段,如对讲机、保证安全开车。
0、联系安全科、保卫科,做好装置开车所有保运工作。
9、准备好操作记录,接班日志及其他常用工具。
10、开车用相关物料规格及用量详见“化工原资料表〞三、装置动工〔一〕、全面质量大检查1、反响系统(1〕检查反再系统检修过程中发现的问题可否整改达成,反响器、再生器、外取热器打扫干净。
(2〕吹扫和衬里烘干养护中所有改动设施和管线可否安装好。
(3〕检查盲板:反响油气线上大盲板、喷嘴处、燃烧油线上盲板应盲死,其他盲板按动工进度和生产需要,由车阀一致安排撤掉。
催化剂裂解工程施工设计方案

延长石油中煤能源化工延长石油靖边能源化工项目150万吨/年催化裂解(DCC)制乙烯装置(现场机柜室基础)施工方案编制:审核:批准:圣远建筑靖边榆能化项目部年月日目录一、编制依据 (1)二、工程概况 (1)三、现场平面设置图 (2)四、施工方案及施工部署 (3)五、施工组织设计进度计划 (8)六、质量保证措施 (14)七、工期保证措施 (22)八、施工技术措施 (24)九、安全施工措施 (30)十、文明施工措施 (32)第一章编制说明本工程施工组织设计编制的依据是:一、业主提供的施工图纸。
二、施工现场的自然条件和具体情况。
地质地形,周围环境等。
三、现行的国家建筑工程施工验收规,质量检验评定标准(1)地基与基础工程施工及验收规GB50202-2002(2)建筑地基处理技术规Q/XJ104-64(3)混凝土结构工程施工及验收规GB50204-2002(4)砖石工程施工及验收规程GB50203-2002(5)建筑地面工程施工及验收规GB50209-2002(6)钢筋焊接及验收规JGJ18-96(7)建筑工程质量检验平定标准GBJ50300-2001第二章工程概况本工程基础结构类型为框剪结构。
设计标高±0.000相当于绝对标高1323.800m,地基承载力特征值不小于160kpa。
材料:混凝土基础、柱、混凝土墙C30,构造柱、圈梁采用C25、垫层采用C15;条基采用红制粘土标砖,条基垫层采用C25混凝土。
TJ-1纵筋锚入基础或框架柱投影围长度不小于500mm,参见图集03G101-6。
基础周围回填土时应分层对称进行,压实系数不应小于0.94。
GZ-1截面240*240,配筋4Φ12、Φ6200,纵向钢筋需锚入基础或基础梁500mm,构造柱与墙体的拉结参见图集06SG614-1第24页。
填充墙与框架柱的拉结详图检图集06SG614-1节点,砌块墙拉结钢筋在墙柱中你的锚固长度不得小于250mm,剪力墙预留洞口(宽、高不大于800mm)如图构造详见DW01-0002。
140万吨重油催化裂化装置操作规程

目录第一章装置概况 (1)第一节装置简介 (1)第二节物料平衡及催化剂 (4)第三节主要工艺流程说明 (6)第四节主要设计条件及工艺计算汇总 (21)第五节消耗指标及能耗 (34)第六节装置设备规格表 (42)第七节机械规格表 (50)第八节安全阀规格表 (62)第九节装置仪表规格表 (63)第十节反再部分设备仪表管嘴明细表 (81)第十一节限流孔板表 (86)第十二节装置开工以来大的动改项目汇总 (88)第二章岗位操作法 (89)第一节反应――再生单元操作法 (89)第二节 CO焚烧炉-余热锅炉单元操作法 (131)第三节机组单元操作法 (169)第一部分三机组单元操作法 (169)第二部分备用风机操作法 (193)第三部分增压风机操作法 (202)第四部分气压机单元操作法 (209)第四节分馏单元操作法 (233)第五节吸收-稳定单元操作法 (253)第六节汽油脱臭单元操作法 (273)第七节脱硫单元操作法 (278)第八节特殊设备操作法 (291)第九节装置开停工步骤 (300)第十节装置生产运行大事记 (301)第三章装置安全常识 (307)第一节基本概念 (307)第二节基本常识 (310)第三节基本技能 (315)第四节有关规定、规章制度、标准 (317)第一章装置概况第一节装置简介一. 装置设计依据及规模中国石油化工股份有限公司济南分公司为原油一次加工能力500万吨/年的大型燃料-润滑-化工型石油加工企业。
鉴于分公司原油加工量逐年递增的实际情况,原有二次加工能力已不能满足生产发展的需要,增上本套140万吨/年重油催化裂化装置,对提高济南分公司原油加工深度及为下游化工装置提供原料将发挥重要作用。
本装置催化裂化部分由中国石化北京设计院设计,设计规模为140万吨/年,产品精制部分由济炼设计室设计,设计规模为干气10万吨/年、液化气20万吨/年、汽油70万吨/年,由中石化第二、第十建安公司建设安装。
化工项目试车方案

化工项目试车方案(共16页) -本页仅作为预览文档封面,使用时请删除本页-xxxx有限责任公司试车方案编制:审核:批准:二零一三年十二月车间试车方案第一章、总则一、试车人员:总指挥:张技术负责人:赵安全负责人:后勤保障:刘电工、保全、制冷:脱水工段负责人:离心工段负责人:环合工段负责人:干燥包装工段负责人:二、试车步骤1、单机试车2、联运试车3、水联运试车4、加料试车三、试车时间:2013年12月日第二章、试车前准备1.总体检查:(1)设备是否按设计施工,施工质量是否符合规范和标准要求。
(2)设备是否按设计要求安装,是否配套,工艺流程是否符合要求。
(3)消防设备、消防设施、劳动保护、防毒面具等是否齐全好用,安全通道是否畅通无阻。
(4)框架、构架、梯子、护栏、平台是否符合设计要求,正常巡检路线是否畅通无阻。
2.工艺流程检查:(1)按照设计施工图的工艺流程认真逐条对照检查,进出装置及与设备相连的位置是否符合设计要求,有无错接、漏接、多接的现象。
(2)工艺管线及管件、法兰、螺栓、垫片、孔板等附件是否符合设计规定的压力、温度等级要求,以及材质是否符合要求。
特别是对于高温、高压部位更应详细检查。
(3)阀门是否符合设计规定的压力、温度,盘根、压盖是否安装好,各阀门是否开关灵活(各阀门均应开关数次)、便于操作,截止阀、单向阀等有方向性的阀门安装是否正确。
(4)热力补偿结构是否符合标准要求。
管线的支撑、吊托是否完好、牢固可靠。
(5)重点检查高温、高压的管线是否符合标准规范要求,各类施工档案材料应齐全。
(6)温度计套管、热电偶套管、压力表等安装是否齐全,是否符合要求。
(7)检查各下水井、地漏是否完好畅通。
(8)装置内管线上的盲板是否按要求拆装。
(9)各管线刷漆、保温是否符合要求,介质流向是否标明。
3、塔、反应器、容器、换热器的检查:(1)所有设备是否正确安装,设备基础有无下沉、裂缝,各部螺栓是否满扣、齐整、紧固,地脚螺栓有无弯曲、变形、裂纹及螺栓是否紧固,设备及管线的支撑、吊架是否安装正确。
催化裂化开停工方案
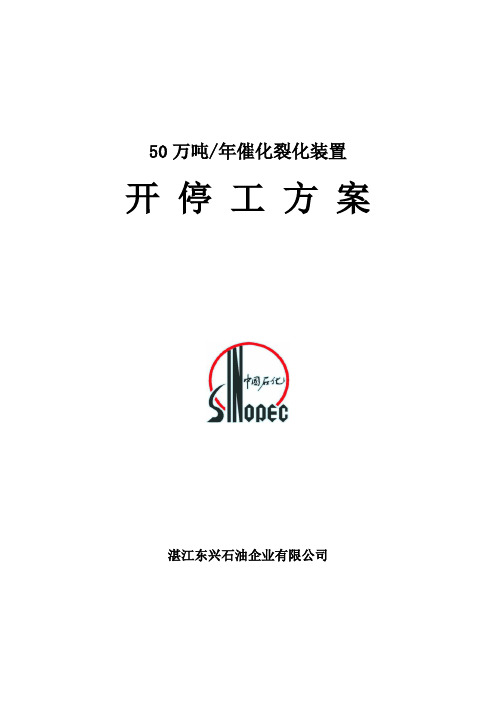
50万吨/年催化裂化装置开停工方案湛江东兴石油企业有限公司目录第一章机组试运 (2)第一节三机组的试运方案 (2)第二节气压机(J-301B)试运方案 (15)第二章开停工统筹图 (23)一、催化装置开工统筹图 (23)二、催化装置停工统筹图 (24)第三章开工方案 (25)一、全面大检查 (25)二、开工水联运方案 (27)三、外取热器系统、分馏系统和稳定系统水运及蒸汽吹扫试压 (29)四、两器气密试验 (29)五、B-201点火升温,分馏、稳定收油,原料塔外循环 (31)六、赶空气,拆大盲板,分馏塔内循环,吸收稳定收汽油三塔循环. 33七、装剂、转剂、两器流化 (35)八、提升管喷油,开气压机,全面调整操作 (37)第四章两器衬里烘干方案 (41)第五章停工方案 (44)第六章开停工吹扫试压方案 (50)第一章机组试运第一节三机组的试运方案一、机组的主要性能参数1.烟气轮机(1)型号 YL-5000D(2)制造厂兰炼机械厂(3)入口流量 1017 Nm3/min(4)入口压力 0.354 MPa (绝)(5)入口温度 670℃(6)出口温度 530℃(7)额定转速 6245 r/min(8)第一临界转速: 11500 r/min(9)跳闸转速: 6432 r/min(10)总效率 77%(11)轴功率 4900Kw(12)级数: 1级(13)平均分子量: 29烟气组成V%N: 72.452O: 11.11H2CO: 0: 12.32CO2SO: 0.0032O: 4.092催化剂含量及粒度分布:含量:≤200mg/m3粒度(w%):>10μ3~54~10μ 6~172~4μ15~400~2μ 40~802.离心式压缩机(1)型号 MCL904-23(2)制造厂沈阳鼓风机厂(3)入口压力: 0.101MPa(绝)(4)入口温度: 32.5℃(5)流量(标准): 1020 Nm3/min(6)相对湿度: 83%(7)出口压力: 0.453MPa(绝)(8)出口温度: 222℃(9)轴功率: 4877KW(10)转速: 6245r/min(11)级数: 4级(12)启动时功率: 1463kW(在32.5℃, 入口蝶阀12o时)(13)第一临界转速: 3152.7 r/min(14)第二临界转速: 9473.8 r/min(15)多变效率: 85.3 %(16)分子量: 29.13.齿轮箱(1)型式:平行轴双斜齿,渐开线齿轮(2)型号: GJR-550-5500/4.211 (3)制造厂无锡创明(4)传递功率: 5500kW(正向)(5)高速: 6245r/min(6)低速: 1483r/min(7)速比: 4.211(8)工作系数: 1.4(9)临界转速:一阶高速轴: 14050 r/min低速轴: 4437 r/min4.电动盘车机构:(1)型式:手动结合自动脱开(2)安装位置:齿轮箱高速轴自由端(3)盘车转速: 75 r/min(4)输出扭矩: 1400 N·m(5)盘车电机(6)功率: 11 kW(7)电压: 380 V5.电动/发电机(1)型号: YFKS900-4(2)制造厂南阳防爆电机厂(3)额定功率: 5500 kW(4)额定电压: 10000 V(5)满载时定子电流: 364 A(6)满载时转速: 1483 r/min(7)满载时效率: 97%(8)满载时功率因数: 0.9(9)最大转矩/额定转矩: 1.8(10)堵转电流/额定电流: 4.2(11)绝缘等级: F级(12)冷却方式:全封闭风-水冷却6.润滑油站(1)油箱容量: 10 m3(制造厂:九江707研究所)(2)油泵(电动)①型号: SNH1300R46U12.1W23②型式:三螺杆③出口压力: 0.5 MPa④电机功率: 18.5 kW⑤转速: 1450 r/min⑥电压: 380 V⑦透平泵:缺⑧润滑油牌号: ISO VG46透平油⑨输出润滑油流量: 830 L/min⑩输出润滑油压力: 0.25 MPa(3)、双联冷油器:管式冷却器①型号:②冷却面积: 58 m2③耗水量: 75 t/h(4)、双联滤油器①型号: HRC02200.00②过滤精度: 20μm(5)电加热器①型号: HRY2-220/4②功率/电压: 3x4kW/220V③排油雾风机④功率/电压: 0.75kW/380V(6)高位油箱有效容积: 2500 L二、试车目的及试车前的准备工作:1.试车目的:(1)检查机组及辅助设备的安装质量并消除缺陷及隐患。
催化裂化装置操作规程确定版

第一章概述第一节装置加工能力及组成装置设计加工能力为10×104吨/年,以原料油为混合原油的蜡油(设计比重0.9183g/cm3,残炭0.363m%)并掺炼30%的减压渣油或常压重油(设计比重0. 9839g/cm3,残炭19.208m%)为原料,多产液化石油气及高辛烷值汽油。
装置由反应再生、分馏、吸收稳定(精制)、主风、气压、司泵等部分组成,产品有汽油、轻柴油、液化气、干气等。
原料及产品性质见表达式1、2、3:第二节主要工艺技术,控制方案及特点第一条目的产品收率高,富产液化石油气,石油气中富含烯烃(尢其是丙烯、丁烯)可提供更多的化工原料。
第二条反应温度略高,在490-520℃之间,采用较低的反应压力和较长的反应停留时间一般为3~4秒,其操作灵活性大,可采用油浆全回炼和部分回炼的操作方式,以得到更多的液化石油气和汽油;采用较大的注气量,一般占总进料的~10w%,以降低油气分压;采用较大的剂油比操作,可达6~8。
第三条本装置设有回炼油系统和轻污油回炼系统。
第四条两器采用同轴式布置:两器采用沉降器在上,再生器在下的同轴式布置,这种布置型式允许的两器差压大,很好地兼顾了反应和再生对操作压力的不同要求。
另外,同轴布置具有结构简单,操作控制灵活方便,压力平衡适用范围大,抗事故干扰,尤其是抗催化剂倒流能力强、占地面积小等优点。
1、采用中CO助燃剂的完全再生方案采用该方案后,由于平均氧浓度的提高可使再生剂含碳明显降低,特别对于本装置单段再生效果更好。
2、采用单段逆流高效完全再生通过加高待生套筒使待生催化剂进入密相床上部并良好分配,然后向下流动与主风形成气固逆流接触烧焦的良好条件,由于高含氧的气体仅和低含炭的催化剂相遇,低含氧气体则同高含炭的催化剂接触。
因此,整个烧焦过程化学动力学速度比较均一,有利于提高总的烧焦强度。
3、采用待生催化剂分配技术在待生套筒出口配置特殊设计的待生催化剂分配器,使待生催化剂均匀分布于再生密相床上部,为形成单段逆流高效再生提供基本的保证。
万吨重催装置操作规程工艺说明

万吨重催装置操作规程工艺说明1第一章装置概述1.1设计依据(1)<河北中捷石化集团有限公司80万吨/年重油催化裂化装置可行性研究报告编制委托书>;(2)<河北中捷石化集团有限公司80万吨/年重油催化裂化装置工厂设计基础条件>;(3)建设单位提供的与该项目相关技术资料。
1.2 装置概况1.2.1 项目名称建设单位:河北中捷石化集团有限公司装置名称:80万吨/年重油催化裂化装置1.2.2 建设性质本项目属于新建项目。
1.2.3 建设规模及年开工时数重油管反按80×104t/a,汽油管反为16×104t/a;年开工时数:8000小时/年。
21.2.4 装置组成装置包括反应—再生部分、分馏部分、吸收稳定部分、主风机部分、气压机部分、余热回收部分。
1.2.5 设计原则(1)采用先进可靠的催化裂化技术,多产丙烯,降低汽油烯烃含量,提高企业的竞争能力和经济效益;(2)尽量采用”清洁工艺”,严格遵循国家、地方有关环境保护、消防、职业安全卫生的标准、规范,减少环境污染,确保排放物符合环保要求;(3)力求使装置操作简单灵活、抗事故能力强,同时采取行之有效的事故防范及处理措施,确保装置安全生产;1.2.6 设计范围本次设计范围为装置界区内的的全部内容。
1.2.7 工艺设计目标(1)汽油的烯烃含量~18v%;汽油的辛烷值﹙RON﹚达到96以上;(2)操作弹性满足60%~110%;(3)气压机采用背压式气轮机驱动,蒸汽做动力;3(4)催化剂的自然跑损控制在0.7㎏/t之内;(5)充分利用催化裂化装置的低温热;1.2.8 装置的主要产品主要产品:富含丙烯的液化石油气、高辛烷值低烯烃汽油;副产品:油浆和干气。
1.2.9 原料及产品方案本装置的原料油为常压渣油,硫含量3000ppm(wt)。
产品方案:以多产富含丙烯的液化石油气、高辛烷值低烯烃汽油为主要目的。
产品去向:液化石油气至产品精制。
催化裂化联合车间J-101(2)机组特护方案

设备名称:三机组编制审批修改序号第一次第二次第三次第四次第五次编制日期: 2022 年 1 月参加编制人员审批人员属地车间设备负责人分厂机动专业工程师公司机动专业工程师分厂设备主管领导公司机动主管领导公司主管领导版本0102030405设备位号: J-101/2催化裂化联合车间编制小组审核意见签名审核日期年月日年月日年月日年月日年月日年月日修改人/小组修改时间年月日年月日年月日年月日年月日一.机组概况 (4)1.机组简介 (4)2.机组工艺简介 (4)3.机组主要性能参数 (5)二.机组特护小组组织机构和职责 (8)1.特护小组成员 (8)2.特护小组职责 (9)三.机组特护范围 (13)1.生产车间特护范围 (13)2.仪表车间特护范围 (13)3.钳工车间特护范围 (15)4.电气车间特护范围 (15)四.机组特护检查内容及标准 (15)1、生产车间工艺检查内容及标准 (15)2.生产车间设备检查内容及标准 (16)3.仪表专业检查内容及标准 (17)4.电气专业检查内容及标准 (18)5.钳工专业检查内容及标准 (19)五.机组特护检查内容计划 (20)1.生产车间工艺特护检查内容计划 (20)2.生产车间设备特护检查内容计划.......................................... 2 13.仪表车间特护检查内容计划.............................................. 2 14.电气车间特护检查内容计划 (22)5.钳工车间特护检查内容计划 (22)六.关键机组特护相关附件 (22)催化裂化联合车间 J-101/2 机组是公司级关键机组,为了确保关键机组的安全、平稳、长周期运行,按照石化公司《关键机组管理规定》制定关键机组的特护管理方案。
催化裂化联合车间 J-101/2 机组是由一台烟气轮机、一台轴流风机和一台高压电动机组成。
重油催化裂化装置主要技术方案

重油催化裂化装置主要技术方案1.1 工艺技术路线①采用多产丙烯技术采用多产丙烯技术,在降低汽油中的烯烃含量的同时,增加液化石油气特别是丙烯的产率。
②采用增产丙烯专用催化剂为满足本装置生产低烯烃汽油的要求,设计考虑采用增产丙烯专用催化剂。
③重油原料雾化采用CS型高效喷嘴CS型喷嘴具有雾化效果好、焦炭产率低、轻质油收率高、操作平稳等特点,可以充分满足工艺过程的要求,且在一定程度上可降低蒸汽消耗。
④反应再生系统采用PLY型高效旋风分离器从维持反-再系统平稳操作,减少催化剂自然跑损的角度出发,反应再生系统中旋风分离器均采用分离效率高的PLY型旋风分离器。
⑤采用高效汽提技术提高汽提效果对降低再生器烧焦负荷有很大好处。
本设计重油沉降器及汽油沉降器采用了高效汽提技术并对汽提段进行特殊设计,以改善汽提蒸汽与待生催化剂的接触,提高汽提效果。
1.2 工艺技术特点1.2.1采用同轴式两器型式本设计重油沉降器与再生器采用同轴式两器布置。
该两器型式具有技术先进、操作简单、抗事故能力强、能耗低及占地少等特点。
1.2.2再生工艺方案再生方案的选择以满足降低再生催化剂的定碳、使催化剂性能得以充分恢复,同时避免采用过于苛刻的再生条件,有利于保护催化剂活性为前提。
本装置采用单段逆流再生,催化剂定碳<0.1%。
该技术由以下几种单项技术组成:⑴采取加CO助燃剂的完全再生方案采用该方案后,平均氧浓度的提高可使再生剂含碳明显降低,特别对于单段再生其效果更加明显。
⑵采用较低的再生温度较低的再生温度有利于提高剂油比并保护催化剂活性,为反应原料提供更多的活性中心。
⑶采用逆流再生通过加高待生套筒使待生催化剂进入密相床上部,并良好分配,然后向下流动与主风形成气固逆流接触,有利于提高总的烧焦强度并减轻催化剂的水热失活。
⑷采用待生催化剂分配技术在待生套筒出口配置特殊设计的待生催化剂分配器,使待生剂均匀分布于再生密相床上部,为单段逆流高效再生提供基本的保证。
催化裂化操作规程
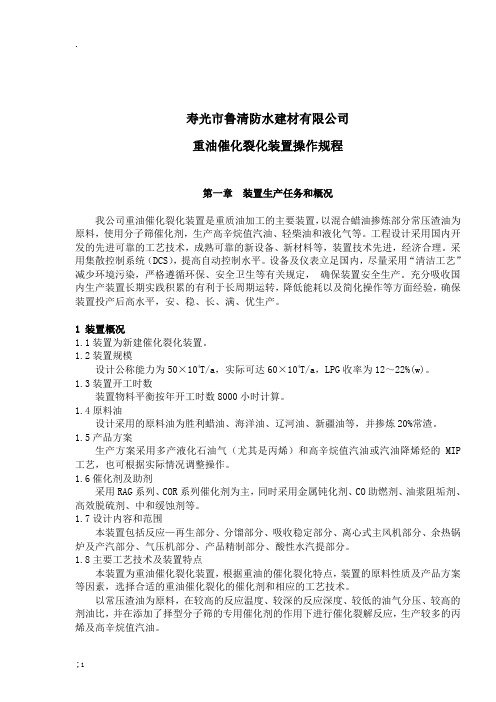
寿光市鲁清防水建材有限公司重油催化裂化装置操作规程第一章装置生产任务和概况我公司重油催化裂化装置是重质油加工的主要装置,以混合蜡油掺炼部分常压渣油为原料,使用分子筛催化剂,生产高辛烷值汽油、轻柴油和液化气等。
工程设计采用国内开发的先进可靠的工艺技术,成熟可靠的新设备、新材料等,装置技术先进,经济合理。
采用集散控制系统(DCS),提高自动控制水平。
设备及仪表立足国内,尽量采用“清洁工艺”减少环境污染,严格遵循环保、安全卫生等有关规定,确保装置安全生产。
充分吸收国内生产装置长期实践积累的有利于长周期运转,降低能耗以及简化操作等方面经验,确保装置投产后高水平,安、稳、长、满、优生产。
1 装置概况1.1装置为新建催化裂化装置。
1.2装置规模设计公称能力为50×104T/a,实际可达60×104T/a,LPG收率为12~22%(w)。
1.3装置开工时数装置物料平衡按年开工时数8000小时计算。
1.4原料油设计采用的原料油为胜利蜡油、海洋油、辽河油、新疆油等,并掺炼20%常渣。
1.5产品方案生产方案采用多产液化石油气(尤其是丙烯)和高辛烷值汽油或汽油降烯烃的MIP 工艺,也可根据实际情况调整操作。
1.6催化剂及助剂采用RAG系列、COR系列催化剂为主,同时采用金属钝化剂、CO助燃剂、油浆阻垢剂、高效脱硫剂、中和缓蚀剂等。
1.7设计内容和范围本装置包括反应—再生部分、分馏部分、吸收稳定部分、离心式主风机部分、余热锅炉及产汽部分、气压机部分、产品精制部分、酸性水汽提部分。
1.8主要工艺技术及装置特点本装置为重油催化裂化装置,根据重油的催化裂化特点,装置的原料性质及产品方案等因素,选择合适的重油催化裂化的催化剂和相应的工艺技术。
以常压渣油为原料,在较高的反应温度、较深的反应深度、较低的油气分压、较高的剂油比,并在添加了择型分子筛的专用催化剂的作用下进行催化裂解反应,生产较多的丙烯及高辛烷值汽油。
DCC操作规程修改稿

ZLDQ/ZY 01-2006 受控号:蓝星石油有限公司大庆分公司50万吨/年催化裂解(DCC)联合装置操作规程(第一分册催化裂解装置)(试行)中国蓝星大庆工业园发布日期:2006年6月操作规程审批页编写:高占峰张宏宇卢贵生审核:崔新文李树成于明春姜光武会审:赵长斌吕建明刘润浮审批:刘军生目录第一篇装置概况第一章装置简介第二章工艺基本原理及装置技术特点第三章设计数据及基本情况第四章工艺流程说明第二篇岗位操作法第一章反应岗位第一节关键变量对操作的影响第二节正常操作法第三节非正常操作第四节一般事故处理第二章分馏岗位第一节正常操作第二节产品质量控制第三节非正常情况处理第四节一般事故处理第三章吸收稳定岗位第一节正常操作第二节产品质量控制第三节非正常情况处理第四节一般事故处理第四章余热系统第一节余热锅炉简介第二节开炉前的准备第三节开锅炉第四节余热锅炉的基本操作和事故处理第五节油浆蒸汽发生器的基本操作和事故处理第六节外取热器的基本操作和事故处理第五章 75t/h燃气锅炉的基本操作和事故处理第六章锅炉汽水分析规程第三篇装置的开停工方案第一章装置开工方案第一节开工准备第二节开工前全面大检查第三节贯通、吹扫、试压、试密第四节开工程序第二章装置停工方案第一节停工原则及要求第二节停工前准备工作第三节注意事项第四节停工程序第五节停工扫线第六节分馏岗停工水运第四篇仪表及自动化控制部分第一章概述第二章集散型控制系统配置第三章集散型控制系统技术功能第四章主要控制回路说明第五篇紧急事故的处理预案第一章紧急事故处理总则第二章紧急事故处理方法第六篇装置安全规程第一章总则第二章安全规程第三章环保规程第七篇专用设备和大型机组操作规程及试车方案第一章专用设备和大型机组操作规程第一节离心泵操作规程第二节增压机操作规程第三节备用主风机操作规程第四节富气压缩机组操作规程第五节三机组操作规程第二章大型机组试车方案第一节增压机试车方案第二节备用主风机试车方案第三节富气压缩机组试车方案第四节三机组试车方案第三章设备明细表第一篇装置概况第一章装置简介催化裂解(DCC)工艺是我国自行研究开发的一种以重质油为原料,生产轻烯烃的新型石油炼制工艺。
(整理)60万吨年重油催化裂解装置大型设备吊装施工方案(修改版)
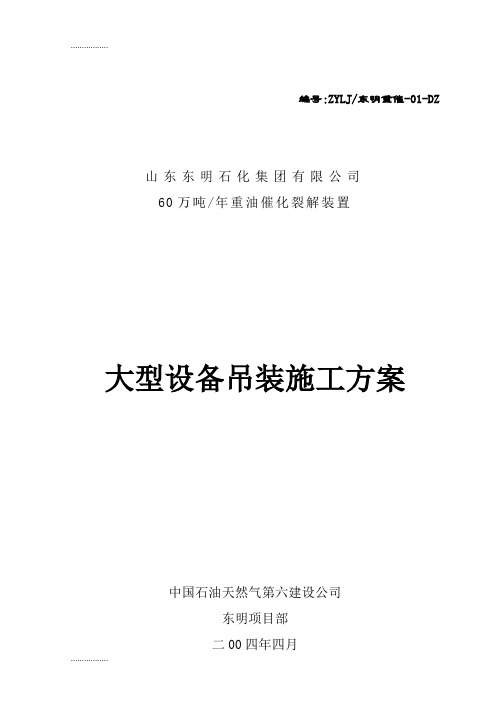
编号:ZYLJ/东明重催-01-DZ山东东明石化集团有限公司60万吨/年重油催化裂解装置大型设备吊装施工方案中国石油天然气第六建设公司东明项目部二00四年四月目录1、工程概况2、编制依据3、施工准备4、施工工艺流程及吊装过程控制5、受力计算6、质量保证措施7、健康、安全、环保(HSE)保证措施8、人力需用情况9、施工机具及手段用料10、附件1 工程概况1.1 工程简介山东东明石化集团有限公司投资新建的60万吨/年重油催化裂解装置中共有需要大型吊装机具进行吊装作业的同轴式沉降-再生器(现场制安)1台、催化剂罐(冷、热、废)3台、提升管反应器1台、外取热器1台、固定床反应器2台、塔类设备7台、容器类设备9台、换热器36台、空冷器管束22片、构-201(楼梯间)、余热锅炉1台以及高空的梯子、平台、管线等(容器、换热器、空冷器管束因就位高度较高,设备本体体积大,常规吊车难以完成)。
根据设备的高度、外形尺寸和重量,建设单位统一安排大型吊装机具采用250吨履带吊车主吊。
主要待吊装的设备规格尺寸详见附表1—《主要设备吊装参数及吊装方法一览表》。
其中,同轴式沉降-再生器、提升管反应器、外取热器、催化剂罐(冷、热、废,共3台)、催化分馏塔、吸收塔、解吸塔、稳定塔、构201为分段吊装,空中组焊。
塔类设备及分段到货设备均采用250吨履带吊主吊,40吨汽车吊、35吨汽车吊联合溜尾;容器、换热器以及空冷器管束采用250吨履带吊直接吊装。
催化装置塔类设备分段参数及设备吊装吊耳设置详见附表2。
1.2 工程特点1.2.1 由于施工工期紧,考虑到符合HSE要求,塔的梯平栏、部分内件及附塔管线等皆于地面安装,后与塔体一起吊装。
1.2.2 场地狭窄,设备倒运较多。
另外,吊装场地土地疏松,这给250吨履带吊车的行走和站位增加了难度。
1.2.3 施工季节气候炎热,空中组焊对接吊装量大,必须做好春夏季节施工技术措施以确保安全、工期与质量。
催化裂化操作规程
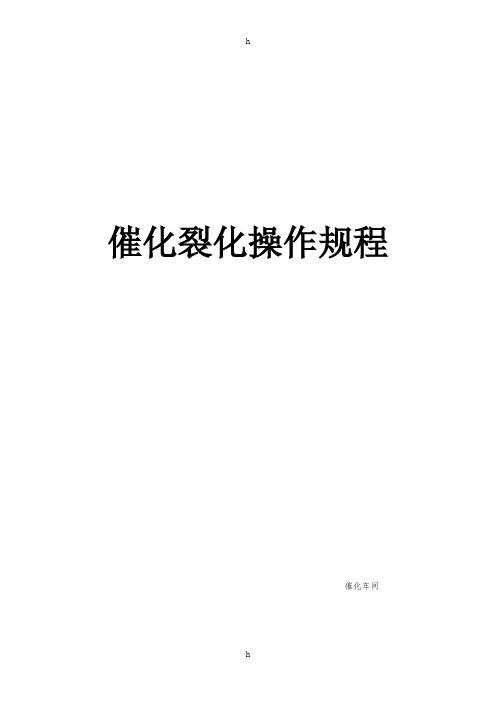
催化裂化操作规程催化车间第一章 装置概况第一节 概况一、本装置设计能力为41014 吨/年(年开工时为8000小时),由反应、分馏、吸收稳定、主风机、气压机等部分组成。
原料由大庆管道原油的常压渣油、通过催化裂化,生产93#汽油,轻柴油、液化汽等目的产品。
二、本装置工艺和设备的主要特点1、两器采用同轴式组合,具有操作弹性大、两端再生。
再生催化剂含碳低。
2、 抗金属污染好、生氢及生焦率较低轻质油收率较高,气体收率较低的系统列分子筛催化剂(具体使用的催化剂类型,根据生产需要选择)。
3、为降低装置能耗采用内取热器,回收才生余热付产蒸汽。
4、由于设计原料为大庆管道原油的常压渣油,其残炭和胶质的含量较高,所以裂化后的油浆比重较大,故在生产采用油浆,不回炼或部分回炼的方案以维持再生器的热量平衡和分馏塔底油浆的比重不超标准。
5、由于同常减压装置可以联合操作,以常压热渣油为原料,所以在开工后可以甩掉加热炉。
6、吸收稳定系统采用双塔流程。
第二节设计数据一、原料性质二、汽油馏分性质三、轻柴油馏分性质四、装置物料平衡表五、反应再生部分工艺计算汇总六、装置能耗汇总表设计进料量70000吨/年装置组成:反应再生部分,分馏部分,吸收稳定部分,碱洗部分第三节装置流程简介一、反应再生部分原料油自罐区的原料罐来经泵(P201/1.2)加压后送到至原料一—轻柴油换热器(E205/1.),再进入原料—油浆换热器(E201/1.2.)换热后,进入闪蒸罐(V203/1),经过加热炉后的原料沿管排进入闪蒸(V203/1),进入闪蒸罐内的原料汽相沿顶部汽返线进入分馏塔(T201)第二层塔盘上部,液相自罐底部抽经泵(P201/2.3)加压后进入提升管反应器。
回炼油自分馏塔第一层塔盘自流入回炼油罐(V202),经回炼油泵(P206/1.2)加压后,送到提升管反应器下部与分馏塔底油浆经泵(P207/1.2)加压后送至提升管下部的回炼油浆混合一并进入提升管反应器(R101)。
石油炼化企业催化裂化装置高压主风机启动方案

石油炼化企业催化裂化装置高压主风机启动方案作者:穆金海来源:《中文信息》2019年第01期中图分类号:TE624 文献标识码:A 文章编号:1003-9082(2019)01-0-01前言随着我国经济的不断发展,社会对于柴油、汽油等化工原料的需求成指数性增加,国民经济发展中石油炼化行业占据着重要的地位。
炼油工艺中重要的主要装置为催化裂化装置,主要是采用减压蜡油、加氢渣油等重质馏分油作为原料,高温高压下与催化剂接触,经裂化反应生成柴油、汽油等化工原料。
主风机机组是催化裂化机械系统中十分重要的装备,借助主风机,可以将压缩好的空气输入到催化裂化反应器当中,为其提供风力能够提升催化装置产品质量并且回收能量,改善环保条件,从而促进炼油行业的发展。
通常而言,催化裂化装置的功率越大,它所需要的风力供应量就越多,因此提供动力的电动机的功率要求也越大。
正常情况下,由于电动机直接起动时,起动电流会达到电机额定电流的5~7倍,特别是大功率的电机,一般上一级变压器的容量都承受不了,必须加装起动设备,否则会造成变压器跳闸。
催化裂化装置的主风机的开机顺序为,备风机电动机首先启动,工艺条件具备后,烟气轮机——主风机——电动机三机连接、一体化运行的组合结构投入运行,烟气轮机带动主风机,主风机带动电动机,再启动电动机运行带动主风机、烟气轮机。
由于在正常情况下主风机电机由烟气轮机驱动主风机可以将电动机的转速带到90%后再启动,相比很容易。
所以在整个启动过程中如何启动备风机电动机是技术人员必须认真面对的问题。
现就目前国内主风机、备风机电动机启动经常采用的几种方案进行分析:一、液阻软起动方式液阻,顾名思义,即液体电阻(又被称为水阻柜)。
此技术1985年上半年引进到中国后,在催化裂化主风机电动机启动中被广泛的采用。
液阻软起动方式基本有两种,一种为定子串液阻(对应鼠笼型电机)方式,一种为转子串液阻(对应绕线式电机)方式,目前国内设计院对催化裂化装置设计一般采用鼠笼型电机,所以液阻软起动方式中采用定子串液阻的方法,此方式通过在起动过程中改变定子回路的电阻值来逐步实现软启动的,这种启动方式要求在前期调试期间根据电动机功率、风机特性计算的加入水中电解粉理论数量,确定串入定子线圈的阻值,电机起动通电后,在水阻柜内,随着电流的热效应使液阻柜内温度逐渐升高,电解液分子活动加剧,电机端的电压逐渐由低到高,当电机转速达到(或接近)额定转速时,短接接触器,液阻柜被甩开启动完成。
- 1、下载文档前请自行甄别文档内容的完整性,平台不提供额外的编辑、内容补充、找答案等附加服务。
- 2、"仅部分预览"的文档,不可在线预览部分如存在完整性等问题,可反馈申请退款(可完整预览的文档不适用该条件!)。
- 3、如文档侵犯您的权益,请联系客服反馈,我们会尽快为您处理(人工客服工作时间:9:00-18:30)。
第二章催化裂解装置大型机组试车方案第一节增压机试车方案一、试车目的(一)、通过试车发现和解决机器运转过程中存在的问题。
(二)、检查整个机组和管道等振动情况。
(三)、考察设备及管道的严密性并将残存杂质进一步冲洗干净。
(四)、检查并调整机组各部分的运转机构,使其达到良好的啮合程度。
(五)、调整并考验整个机组的技术性能。
(六)、进行岗位练兵,熟悉增压机操作法。
二、试运前应具备的主要条件(一)、试车领导小组检查合格后方可进行。
(二)、参加试车人员必须熟悉机组性能和试车方案,并有明确分工。
(三)、卫生合格,消防器材齐全,下水畅通。
(四)、水、电、汽、风准备就绪。
三、润滑系统的冲洗(一)、打开油箱盖,清除油箱内的杂物,用和好的面团粘除杂质。
把高速轴齿轮、大齿轮、各部位轴承全部取出.切记:1、在任何情况下从下机壳、变速箱吊出高速轴齿轮、大齿轮及转子前,先把下机壳、变速箱的全部密封和油封旋转取出;转子吊进下机壳、变速箱并用止推轴承定位后,再旋入密封和油封否则转子吊起吊落稍有轴向串动,密封片极易损坏。
2、在任何情况下吊装高速轴齿轮、大齿轮时都应保护好轴颈部位、齿轮部位和半联轴器部位,不允许有任何磕碰划伤!(二)、拆除油过滤器滤芯,换上临时过滤网,把变速箱的轴向贯通孔遮档住,防止冲洗油运行时飞溅外泄(有端益的把好端盖,没端盖的在油封处用软木椽胶板阻挡)。
把滤油器芯子去掉后再封闭好壳体。
滤油器壳体进油法兰连接处夹垫200目的临时过滤网,用来判断润滑油冲洗清洁程度。
在电机轴承给油法兰处临时夹垫200目过滤网,以防冲洗时的脏油对电机轴承部位的污染。
(三)、VG46透平油运到现场后,应逐桶进行检查,并抽取油样化验分析,合格后备用。
(四)、用压力滤油机向箱内加入最大液位的VG46透平油,检查油位指标器指示是否与实际油位相符合,高油位及低油位信号是否准确.(五)、盘车检查,打开油系统各阀门,关闭各排凝阀门。
如润滑油温度较低,开启加热器。
油温18℃时电动油泵可以开启。
加热器恒温整定在35℃或油温升至35℃时停止加热。
启动油泵,检查油泵运行情况及润滑油系统泄漏倩况,两组油冷器、过滤器内充油,两油泵、油冷却器、油过滤器交替使用,使油充分流经管道系统各部。
(六)、仔细检查油管路、润滑油系统各部位部件功能是否正常,对油管路进行大于12小时的无阻挡循环冲洗,在此期间利用油冷器和油加热器使循环冲洗的油温度由冷到热变化2一3次,油温值在20℃-65℃之间:凡有切向开关的部件都应定时切换几次开关。
为了提高冲洗压力,变速箱各给油孔应安置节流垫。
定时停泵检查和清洗滤油器壳体进油法兰处临时夹垫的200目过滤网,目测观察该过滤网的清洁程度,如果清洁情况良好并且2-4小时内很稳定,进行下一步冲洗。
(七)、冲洗过程中用木棒敲击管道,特别是焊缝和弯头处。
(八)、停电动油泵,停止无阻档循环冲洗。
在油箱和冷却器最底部放油口采样,化验分析是否合格,若杂质较多,应退出冲洗油。
从油箱底部的排污阀门排掉沉淀污垢,用过滤机抽出并过滤油箱内的油。
用面团从新清洁油箱、变速箱和抽过滤器壳体,把油过滤器的芯子重新置入。
去掉滤油器壳体进油法兰临时夹垫的200目过滤网。
把用过滤机过滤好的油重新置入油箱。
更换或清洗电机给油孔处临时夹垫的200目过滤网。
(九)、用压力滤油机再次加入质量合格的润滑油,再次启动电动油泵进行第二次冲洗,每12小时化验分析一次。
包括第一次冲洗的时间在内,总共时间在24~48小时或更多。
在此期间可以定时观察油过滤器压降变化和清洗滤油器芯子。
定时切换油冷却器和滤油器的转换开关。
在正常温度下,清洁的滤油器工作时引起的压降应不大于0.35bar。
根据滤油器压降判定冲洗是否合格,并且这个压降值在4一5个小时内是否很稳定,如判定合格,则冲洗润滑系统完成。
停电动油泵。
排出油箱内润滑油和沉淀污垢,重新清洗油箱、变速箱内的污垢,冲洗滤油器芯子,用滤油器排污阀排放滤油器壳体内的沉淀污垢。
置入新的汽轮机油至最高油位线。
冲洗用过的汽轮机油经过滤和化验后再确定以后能否再使用。
(十)、化验分析油质合格后应停泵清洗滤网,拆除各临时管线,并在各轴承入口管线处安装200目滤网,将各轴承出入口线连接好,进行循环冲洗约24小时,每12小时检查各个滤网并清洗,直至油冲洗合格为止。
(十一)、吹除、清洁机壳内缸、进风口、高速轴齿轮、大齿轮,仔细检查叶片扩压器,叶轮流道内有无异物,用洗油清洗轴承和齿轮部位,在这期间不应污染清洗过的变速箱和轴承箱。
完成压缩机组、变速器以及联轴器和护罩的组装,撤除电机轴承各给油孔法兰处加垫200目临时过滤网。
安装好过滤器滤芯.四、润滑系统试运行(一)、进行润滑系统负荷试运行前的各项准备工作和检查工作。
清洗油路管线及油箱、油过滤器、油冷却器、油泵,其中油冷却器必须试压检查;油系统的设备、管线、法兰、垫片等有无泄漏。
(二)、开启电动泵进行润滑油系统循环,进行各项检查和调试工作,包括自控系统对润滑系统要求的各项检查、测试工作。
(三)、给油管路压力表(一般位于油过滤器后和供油点之间)应调至0.16-0.18MPa,主机开启后这个压力有所下降,所以开机前这个压力可调高些。
(四)、当电动泵和主油泵同时运转、供油压力高于正常供油压力时,手动停电动泵或自控停电动泵。
如果选择自控停泵,润滑系统负荷运行时应调试、检测当给油管压力达到0.25 -0.27MPa时电动泵是否自动停泵。
(五)、通过变速器观察窗查看给油齿轮啮合部位喷油嘴的喷油情况是否正常。
(六)、检查滤油器压降是否正常。
(七)、润滑系统试运行正常,完成各项调试和检测,在运行2-3小时后可停泵,进行下面操作。
五、电机试运转1.脱开电机与变速器的连轴器。
2.根据电机说明书的规定,进行电机启动前的各项准备工作和检查工作(检查电机的绝缘电阻应符合规定,盘动转子应灵活无卡阻),点动启动电机,观察电机转动方向是否正确;电流、电压、轴承温升、振动情况是否在规定范围内3.电机运行时间约5-8小时或更长。
电机试运转合格,停电机。
4.校正电机与变速器的找正是否有变动。
5.组装电机与变速器的连轴器和连轴器护罩。
六、增压机组试运行前的准备工作(一)、切断增压机出口与工艺主风管道的联接(关闭截止阀),全开旁通放空阀。
(二)、微开启进风管道调节阀,约7-15度。
(三)、检查油冷却器供水,待开机后油冷却器出油温度达40℃时供冷却水。
(四)、进行整机组手动盘车,仔细监听、检查机缸内和变速箱内有无摩擦、碰撞以及其它异样声音。
如有应揭盖检查、消除。
(五)、检查所有仪表得声光报警、启动连锁、停机连锁等功能是否正常。
检查机组所有现场监测仪表、二次仪表远传接口是否安装就位。
(六)、检查润滑油油温、油位、油质是否合格,如润滑油温度较低,开启加热器。
油温18 ℃时,电动油泵可以开启。
加热器恒温整定在35℃或油温升至35℃时停止加热。
(七)、根据润滑系统试运行规定的步骤,进行开机前的润滑系统串油运行以及各项调试、检查工作。
运行时间为0.5-1小时。
七、增压机组试运行(一)、切除电机连锁。
进行电机启动前的各项准备工作和检查工作。
(二)、启动电机,电机达到额定转速后,记录、判断电机启动时间是否符合规定的时间;对电机电流、电压、轴承温度、振动等以及电机说明书规定的其它检测内容对电机进行全面检查。
(三)、电机达到额定转速后,立即观察主油泵是否工作正常,如果油站电动泵始终不能正常停车,即电机达正常工作转速后,主油泵吸不上油,应停机检查,消除故障。
(四)、增压机组的轴承温度、轴承振动、轴位移等机械性能是否正常,轴端密封部位、机壳中分面以及油封部位是否漏气、漏油等现象进行全面检查。
监听机内各部位有无明显杂音。
油冷却器出油温度达40℃时供冷却水。
(五)、检查供油压力是否在0.11-0.15MPa。
如果压力低于这个值,应通过安全阀及时进行调节。
轴承温度过高,加大油冷却器供水量,待停机时适当扩大节流垫的通孔直径。
(六)、小负荷运行3-5分钟左右停机,打开变速器检视孔盖,目测检查变速器齿轮在小负荷下的齿轮啮合情况。
如有问题,应通过调整齿轮啮合状态消除不良现象。
(七)、重复开机前的各项准备工作,机组进行第二次开车并进行不小于4 小时的小负荷运转。
应定时检测、记录整个机组在运行期间各部位的技术性能数据。
运行一定时间后,应观察机壳与支座之间的热膨胀是否正常。
(八)、机组小负荷运行一切正常后,逐渐开启进气管道上的调节阀,直至全开为止。
其后观察出口压力表的同时关小出口放空阀开度,达到额定压力时,停止出口放空阀的升压动作,进行增压机组额定负荷运行。
关小出口放空阀升压的同时,还要注意电机电流是否超限。
增压机组的额定负荷运行可进行4-6小时或更长,期间应定时检查、记录机组运行各项技术性能数据是否符合规定要求。
(九)、增压机组经过预定时间的额定负荷运行一切正常无问题后,按正常停机规程停机。
(十)、机组试车工作结束后,由试车领导小组验收工作。
注:必须详细做好试车记录。
第二节 D1250备用主风机试运方案一、机组概述主风机在催化裂解装置具有十分重要的作用,它是催化裂解装置的核心设备之一,必须连续运转,主风机停止运转,催化裂解装置也将停止生产。
其作用主要包括①提供催化剂烧焦所需的氧气,恢复催化剂的活性。
②保证再生器、烧焦罐内的催化剂处于流化状态,使催化剂更好地烧焦,同时保证催化剂在两器内正常流动,使两器正常工作。
二、机组规格及性能参数(一)、离心式主风机厂家:陕西鼓风机(集团)有限公司型号: D1250-3.2/0.97介质:空气,相对湿度77%,分子量28.63叶轮级数: 3级进口压力(绝压):0.097MPa=0.9891kg/cm2(绝压)进口温度: 25℃进口流量: 1250m3/min出口压力(绝压):0.32MPa=3.263kg/cm2(绝压)主轴转速: 5897rpm所需功率: 3846KW旋转方向(从电机端看):顺时针一阶临界转速: 3080rpm二阶临界转速: 9420rpm(二)、增速箱厂家:南京高速齿轮箱厂型号: NGGST485传动功率: 4000KW增速比: 5897/1487主动轴转速: 1487rpm从动轴转速: 5897rpm(三)、电机厂家:上海电机厂型号: YCH710-4额定电压: 6000V额定功率: 4000KW额定转速: 1487rpm额定电流: 437A冷却方式:上水冷绝缘等级: F级(四)、油站1、润滑油压: 0.25Mpa(G)润滑油品: VG46#防锈透平油2、油系统设备:(1)、油箱规格尺寸: 6200×3907×2540油箱容量: 6300 L(2)、油泵型号: SNH660R46U12.1W23油泵流量: 648L/min油压: 0.5MPa电机功率: 11KW(3)、油冷器型号: SGLL6-100/1.6耗水量 80m3/h(4)、双联过滤器型号: LSW-A2200×20FS润滑油过滤精度:20μm(5)、高位油箱油箱容量: 1500L油箱尺寸:φ1150×1700三、机组的试运目的(一)、检验机组各设备、电路、仪表及系统各管线的制造质量。