连铸圆管坯气孔形成机理分析
优钢连铸坯气泡成因分析及防范措施
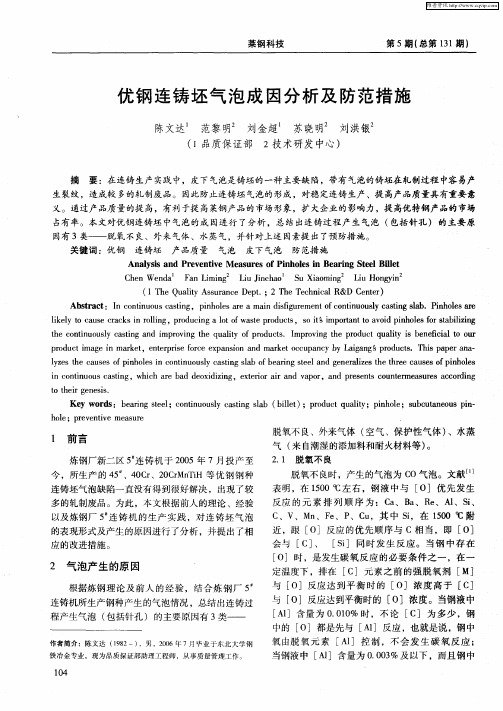
生裂纹,造成较多的轧制废品。因此防止连铸坯气泡的形成 ,对稳定连铸生产、提 高产品质量具有重要意
义。通过产品质量的提高,有利于提 高莱钢产品的市场形象,扩大企业的影响力,提高优特钢产品的市场 占有率。本文对优钢连铸坯中气泡的成 因进行 了分析 ,总结 出连铸过程产 生气泡 ( 包括针孔 )的主要原 因有 3类—— 脱氧不良、外来气体、水蒸气,并针对上述 因素提 出了预防措施 。
i o t u u a t g n c n i o sc s n ,wh c r a e xd z g xei ra ra d v p r n r s n s c u tr a u e c o d n n i ih a e b d d o i ii ,e tro i n a o ,a d p e e t o n e me s r s a c r i g n
lzstec u e f ih lsi o t u u l a t gsa f e rn te a dg n r ie etrec u e fpn oe y e h a s so n oe nc ni o s c si lb o a gs l n e ea zst he a sso ih ls p n y n b i e l h
t h i e e i. o t erg n ss
Ke o d :ba n t l o t u ul cs n lb( ie) pou t u ly i oe u ct eu i— yw r s er gs e;cni o s at gs i e n y i a bl t ; rd c q ai ;pn l;sb ua o spn l t h n
hl o e;p e e tv a u e r v n ie me s r
分析铸造过程气孔生成的原因及对策

分析铸造过程气孔生成的原因及对策铸造过程中气孔生成的原因及对策分析铸造是一种重要的金属加工方法,可用于生产各种形状的金属制品。
然而,在铸造过程中,气孔的生成是一个常见的问题,它可能会影响到铸件的质量和性能。
本文将分析铸造过程中气孔生成的原因,并提出相关的对策。
一、原因分析1. 铸造材料的问题在铸造过程中,铸造材料的纯度、含气量和化学成分会直接影响气孔的生成。
杂质和气体在熔融金属中的存在可能会形成气泡,并在凝固过程中被包裹在铸件内部。
此外,如果铸造材料中的挥发性成分含量过高,也容易导致气孔的生成。
2. 模具设计和制造的问题模具的设计和制造不当也是气孔生成的原因之一。
设计不合理的浇口和冷却系统会导致金属在流动过程中吸入空气,形成气孔。
模具的材质和表面处理也会对气孔的生成产生影响,表面粗糙度过高或使用粘结性差的涂料可能会导致铸件表面气孔的形成。
3. 浇注工艺的问题浇注工艺是影响气孔生成的关键因素之一。
浇注温度、浇注速度和浇注角度等工艺参数的控制不当可能导致金属流动不畅,气泡无法完全排出,从而形成气孔。
此外,如果铸件内部存在复杂的几何形状,也会增加气泡在凝固过程中的积累和无法排出的可能性。
二、对策措施1. 提高铸造材料的质量为了减少气孔的生成,需要选用高纯度的铸造材料,并控制好化学成分和气体含量。
可以通过加入脱气剂来减少金属中的气体含量,同时加入合适的合金元素可以改善金属的流动性和凝固性能。
2. 优化模具设计和制造合理的模具设计可以改善金属流动状态,减少气体吸入的可能性。
浇口的设计应考虑到金属的流动路径和速度,确保金属在流动过程中尽量少吸入空气。
此外,模具的材质应选用适合的材料,并进行表面处理以提高其抗粘性和耐腐蚀性能。
3. 控制好浇注工艺参数合理控制浇注温度、浇注速度和浇注角度等参数可以使金属流动顺畅,减少气泡的生成。
同时,在铸造过程中可采用自动浇注系统和真空吸气设备来排除金属中的气体。
对于复杂几何形状的铸件,可以采用分次浇注或采用喷浇工艺来减少气孔的生成。
关于铸坯气孔形态的分析
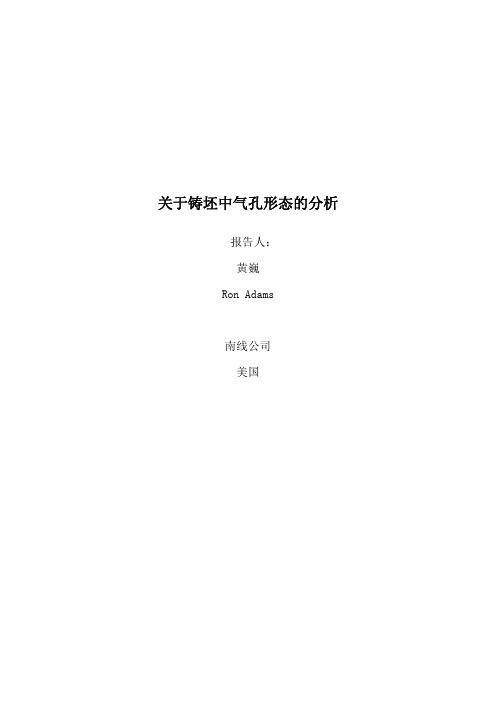
这是一个 5 平方英寸(约 3226 平方毫米)沿纵向切片的铸坯样品。沿着中心线可以看 到连续的的管状气孔。如果从横向看的话在铸坯的中央会看到一个巨大的孔洞。
由于浇铸池入口处的波动,一些空气被卷入铜水。这些卷入的气泡会向上漂浮
并逃离铸轮池口。这些气泡需要足够的速度才能逆流而上,一个气泡最终的速度和 气泡的大小成正比,还取决于它处于铸轮内的位置,这可以由下列的图和公式来说 明:
助于使用表 2 结合表 1 来研究气孔问题。
表2
问题
结果或迹象
氢导致的气泡
枝晶间的小气孔
变成水蒸气导致的大气孔
氧含量较低
目视可发现孔内比较干净
与氧有关的气泡 大气孔
可能有较高的氧含量
气孔中可见红/黑色的残留物
孔边有大量共晶氧化物集中
不 当 的 中 浇 包 温 过低
~100%的等轴晶-> 容易形成气孔
关于铸坯中气孔形态的分析
报告人: 黄巍
Ron Adams
南线公司 美国
去年九月份南线在上海以铜线断线原因、铜杆和铸坯的质量为主题举办了一次 讲座。会后收集到很多问题,很多都是有关铸坯气孔的。人们问如何就观察到的气 孔的大小和分布状况来确定可能的根本原因。
气孔问题从铸造开始的那天就存在,这是一个老问题,但从来没有被完全消除 过。根据过去的经验我们知道过度的铸坯中的气孔是由于以下两个原因导致的 1)在 低温铸造时由于冷金属具有较高的粘稠度导致气体无法逸出 2)在金属凝固过程中 过量的氢汽化。然而,气孔的形成与加工过程有关,铸造过程的复杂性也导致多变 的气孔形态,这就为寻找根本原因带来了困难。
1) 中心线明显偏向样品的钢带侧多余偏向铸轮侧。这表明钢带面的冷却需 要增加。
铸件气孔产生的原因
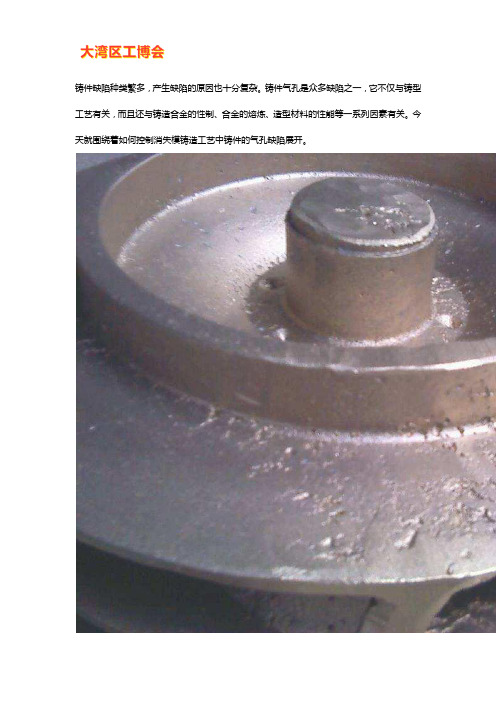
铸件缺陷种类繁多,产生缺陷的原因也十分复杂。
铸件气孔是众多缺陷之一,它不仅与铸型工艺有关,而且还与铸造合金的性制、合金的熔炼、造型材料的性能等一系列因素有关。
今天就围绕着如何控制消失模铸造工艺中铸件的气孔缺陷展开。
1、选择适宜的模型材料采用共聚泡沫模型材料,由于共聚物是拉链式分解,一次性气化程度高,液相比例小,小分子气体很容易从涂层溢出,白模密度在强度和光洁度保证的前提下尽可能小一些,减少发气总量,浇注系统采用空心直浇道并加设过滤器,对金属液进行机械挡渣、吸附梳流,使充型更平稳。
2、浇注系统及保温冒口的使用内浇道的开设要利于合金的顺利平稳快速充型,不形成死角区,在铸件的顶部设置大气压力保温冒口,集渣补缩于一体,相关部位设置随形隔砂冷铁,实现铸件的顺序凝固,把金属液内的气体、渣质及气化残留物快浮到冒口部位,减少气孔、渣孔、缩孔产生的几率。
3、提高涂料的透气性耐火骨料的粒度要适宜,采用复合粘结剂悬浮剂,配制的涂料具有高低温强度好、耐磨损、易涂刷、不开裂、排气能力强、透气性好、烧结均匀、开箱易脱落剥离,不与金属液润湿剂及化学反应,一般铸件涂刷2遍,涂层厚度2mm左右。
消失模涂料的质量管理十分关键。
在大量生产时,定期检查涂料的透气性,及时调整骨料的粒度。
由于涂料的粘结剂、悬浮剂中含有机物质,夏秋季节特别应该注意涂料的发酵酶变,合格的铸件离不开最佳的涂料,控制涂料的质量不可轻心。
4、浇注温度要适宜由于消失模的充型过程中药放热汽化泡沫,钢铁的浇注温度较砂型铸造高30-50℃。
金属液与泡沫的热作用受热浇注温度的制约,浇注温度适宜热解充分,模样的热解产物主要呈小分子气态,在负压场的作用下容易排除型腔,当浇注温度低时,模样的热解不充分,液相残留物会堵塞涂料层,热解气体排出受阻,型腔内形成反压力,充型流动性由此下降,再加上凝固速度快,液体附近的气渣来不及浮集到冒口内,生成气孔的几率增大,当然浇注温度要与冶炼的材料匹配,以避免因温度高或底而产生的其他铸造缺陷。
压铸件气孔产生的原因

压铸件气孔产生的原因产生气孔的原因有以下几点:一、氢气残留。
原材料里面还有氢气,坩埚及环境还有湿气,导致气体加热产生氢气夹裹在原材料里面,容易产生针状气孔。
二、压射室充满度不高。
压射室充满度不高会导致压射室内含空间过大,铝汤在压射前,出现回流撞击,产生涡流。
气泡是模具温度及铝温太高,容易产生气泡。
氢气,压射缸卷起,流道卷起,型腔内压力卷起,水蒸气产生气孔这些都是模具气孔的主因。
产生原因:1、金属液在压射室充满度过低(控制在45%~70%),易产生卷气,初压射速度过高。
2、模具浇注系统不合理,排气不良。
3、熔炼温度过高,含气量高,熔液未除气。
4、模具温度过高,留模时间不够,金属凝固时间不足,强度不够过早开模,受压气体膨胀起来。
5、脱模剂、注射头油用量过多。
6、喷涂后吹气时间过短,模具表面水未吹干。
解决压铸件气孔的办法:先分析出师什么原因导致的气孔,再来取相应的措施。
(1)干燥、干净的合金料。
(2)控制熔炼温度,避免过热,进行除气处理。
(3)合理选择压铸工艺参数,特别是压射速度。
调整高速切换起点。
(4)顺利填充有利于型腔气体排出,直浇道和横浇道有足够的长度(>50mm),有利于合金液平稳流动和气体有机会排出。
可改变浇口厚度、浇口方向、在形成气孔的位置设置溢流槽、排气槽。
溢流品截面积总和不能小于内浇口截面积总和的60%,否则排渣效果差。
(5)选择性能好的涂料及控制喷涂量。
预防措施:1、调整压铸工艺参数、压射速度和高压射速度的切换点。
2、修改模具浇道,增设溢流槽、排气槽。
3、降低缺陷区域模温,从而降低气体的压力作用。
4、调整熔炼工艺、5、延长留模时间,调整喷涂后吹气时间。
6、调整脱模剂、压射油用量。
气孔是压铸件中常见多发的缺陷之一。
气孔呈圆形或扁平椭圆形气泡状,直径为1mm至20mm不等,内表面光滑,覆有一层氧化层,通常分散在加工表面下。
一、气孔缺陷的成因01 金属杂质过多原材料或回收料中含有较多的氧化物和其他杂质,一些杂质(如氧化物、氢化物、油脂)在熔炼过程中会释放气体。
连铸坯中气泡产生原因分析及判断方法

Ke wo d n i u u l a ts a ( i e ) y r sCo t o s y c s l b b l t ,P n o e, g n g s p o e to n l i h l Ar o a r t c in
1 前 言
21 1 C . . 0气 泡产 生 机理
肖寄 光 王 福 明 。
( 北 京科技大学 ; 关钢 铁公司) 1 2韶
摘
方法 。
要
本文 对连铸坯气泡 的成因及特性进 行 了分析 , 并提 出了识 别气泡类 型及改善和解 决气泡问题 的
连铸坯 气泡 氩 气 保 护
关键词
An l sso u e n u gn e h d o a y i fCa s sa d J d i g M t o f
在 钢 的连 铸 过程 中 , 不论 是 连 铸“ 沸腾 钢 ” 准 还 是连 铸 高 纯 净 度 的镇 静 钢 , 内外 许 多钢 厂 都 国
遇 到过 连 铸 坯 中 的气 泡 问 题 , 且 采 取 了相 应 的 并
脱 氧不 良时 , 产生 的气 泡为 C 气泡 。 O 文献 。 ]
2 1 脱 氧不 良 .
2 6 8 5 T+ 4 6 7 6 . / . 1
因此 :
a j『 一 Po 。 XP -2 8 5 T一4 6 7 a ] c/PE [ 6 . / [ ) . 1]
钢 中碳 氧反 应c 引:
E ] [ =C C + 0] O
Ar = 一2 8 — 3 . 8 (J mo ) ( ) G。 2 1 6 8 3 6T / 1 1
铸 坯 气泡 的成 因 , 采 取 了相应 的 改进措 施 , 到 并 达
了改 善气 泡 问题 的 目的 。
铸件气孔案例分析报告

铸件气孔案例分析报告1. 引言铸造是一种常见的金属加工方法,用于生产各种复杂形状的金属零件。
然而,在铸造过程中,气体存在的问题是一个常见的挑战。
气孔是铸件中最常见的缺陷之一,它们对铸件的力学性能和表面质量都会造成负面影响。
因此,对铸件气孔现象进行分析,并采取相应的措施来减少气孔产生,是提高铸件质量和性能的关键。
2. 气孔的成因气孔的形成是由于铸造过程中存在的气体无法完全逸出,而被困在铸件内部形成的。
气体在金属液态状态下溶解度较低,在凝固过程中会析出。
以下是几种常见的气孔成因:a) 液态金属中溶解的气体:液态金属中可溶解的气体,在固化过程中会分解,产生气体泡沫形成气孔。
b) 铸型气体:在铸造过程中,砂型或其他铸型材料中的挥发物会被加热并释放出气体,形成气孔。
c) 内部形成的气体:在凝固过程中,疏松的金属结构或其他元素的分解反应会生成气体,形成气孔。
3. 气孔的影响气孔对铸件性能和表面质量产生以下负面影响:a) 降低强度和韧性:气孔导致铸件内部存在弱点和孔洞,会降低铸件的强度和韧性。
b) 引起裂纹和漏洞:气孔是裂纹和漏洞形成的起点,它们可能在应力作用下扩展,导致铸件的损坏和失效。
c) 影响铸件外观:气孔会在铸件表面形成小孔或凹陷,影响铸件的外观质量,降低其市场竞争力。
4. 案例分析以下是一个关于铸件气孔案例的分析,以展示如何识别和解决气孔问题的过程:案例背景:一家汽车制造公司的铝合金发动机块铸件出现了气孔问题,导致部分铸件在测试中出现弯曲和断裂现象,严重影响了发动机的可靠性。
分析步骤:a) 气孔检测:使用X射线或CT扫描等非破坏性检测方法,对铸件进行全面的检测,确定气孔的位置和数量。
b) 气孔成因分析:通过对铸造工艺参数、金属合金成分和砂型材料等进行分析,确定气孔产生的可能原因。
c) 工艺优化:针对气孔成因,通过调整铸造温度、压力和保温时间等工艺参数,优化铸造过程,减少气孔的形成。
d) 砂型改进:对砂型材料进行优化,选择低挥发性和低含气量的材料,减少砂型气体的释放。
铸件气孔分析及解决措施的建议
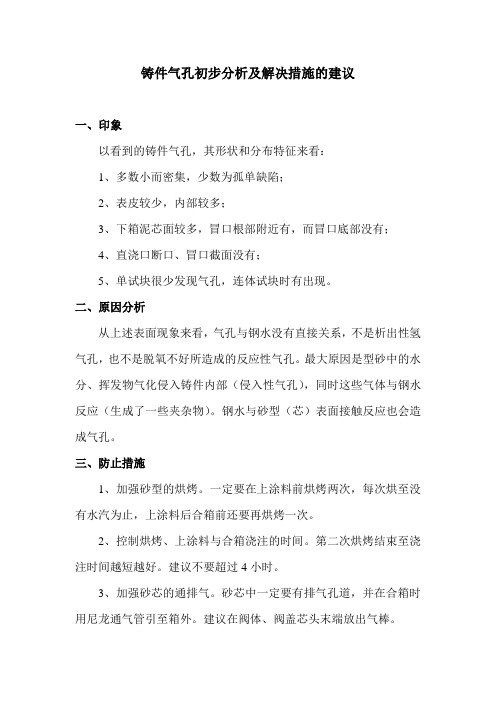
铸件气孔初步分析及解决措施的建议一、印象以看到的铸件气孔,其形状和分布特征来看:1、多数小而密集,少数为孤单缺陷;2、表皮较少,内部较多;3、下箱泥芯面较多,冒口根部附近有,而冒口底部没有;4、直浇口断口、冒口截面没有;5、单试块很少发现气孔,连体试块时有出现。
二、原因分析从上述表面现象来看,气孔与钢水没有直接关系,不是析出性氢气孔,也不是脱氧不好所造成的反应性气孔。
最大原因是型砂中的水分、挥发物气化侵入铸件内部(侵入性气孔),同时这些气体与钢水反应(生成了一些夹杂物)。
钢水与砂型(芯)表面接触反应也会造成气孔。
三、防止措施1、加强砂型的烘烤。
一定要在上涂料前烘烤两次,每次烘至没有水汽为止,上涂料后合箱前还要再烘烤一次。
2、控制烘烤、上涂料与合箱浇注的时间。
第二次烘烤结束至浇注时间越短越好。
建议不要超过4小时。
3、加强砂芯的通排气。
砂芯中一定要有排气孔道,并在合箱时用尼龙通气管引至箱外。
建议在阀体、阀盖芯头末端放出气棒。
4、浇注坑内潮湿的砂要清理掉,换成破碎机清除出来的陶口管碎屑。
5、改变浇口位置,如自封密式闸阀阀体中通道端有气孔在此处增加底注浇口。
6、树脂固化剂厂家的对比试验,某一时期固定用一家厂的树脂、固化剂,统计对比出现气孔的概率。
同一厂家的产品也要统计出现气孔的概率,看哪一家的产品好。
7、合金烘烤容易造成气孔的镍板、钼铁、金属铬等合金材料要脱氧,容易造成气孔的废钢,如不锈钢压块料要烘烤。
8、熔炼时不能用潮湿的造渣材料,吸了水的石灰一定不要用,熔炼后期加大渣量,减少功率,防止驼峰致使钢水外露吸气。
9、如有可能,弹性闸板砂芯试用水玻璃有机酯。
这种砂与碱酚醛砂不冲突,可以同时回用。
1.。
铸造工艺中气孔缺陷形成原因
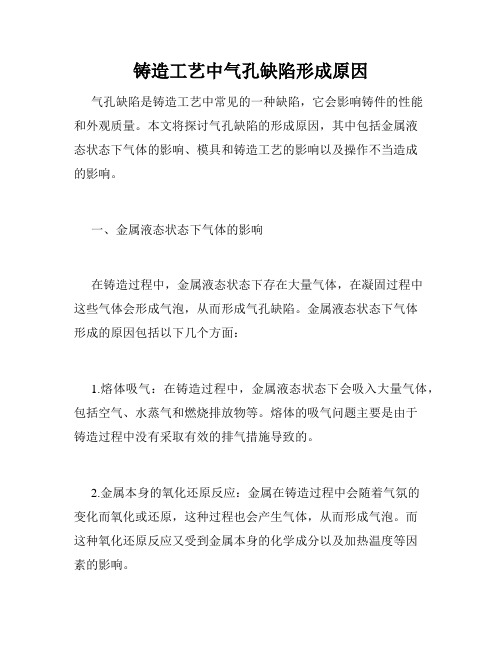
铸造工艺中气孔缺陷形成原因气孔缺陷是铸造工艺中常见的一种缺陷,它会影响铸件的性能和外观质量。
本文将探讨气孔缺陷的形成原因,其中包括金属液态状态下气体的影响、模具和铸造工艺的影响以及操作不当造成的影响。
一、金属液态状态下气体的影响在铸造过程中,金属液态状态下存在大量气体,在凝固过程中这些气体会形成气泡,从而形成气孔缺陷。
金属液态状态下气体形成的原因包括以下几个方面:1.熔体吸气:在铸造过程中,金属液态状态下会吸入大量气体,包括空气、水蒸气和燃烧排放物等。
熔体的吸气问题主要是由于铸造过程中没有采取有效的排气措施导致的。
2.金属本身的氧化还原反应:金属在铸造过程中会随着气氛的变化而氧化或还原,这种过程也会产生气体,从而形成气泡。
而这种氧化还原反应又受到金属本身的化学成分以及加热温度等因素的影响。
3.金属液态状态下气体的扩散:在金属液态状态下,气体有一定的扩散性,当扩散到形成金属凝固迹象区域时,气体就会形成气泡,产生气孔缺陷。
二、模具和铸造工艺的影响模具和铸造工艺对气孔缺陷的形成也有着重要的影响。
其中模具会影响铸造过程中气体的排放,而铸造工艺本身也会对顶底放砂、浇注速度等方面产生影响。
1.模具孔隙率:模具的孔隙率越大,就意味着模具的通气性越好,气体容易排除,从而减少了产生气泡和气孔缺陷的概率。
2.浇注温度和浇注速度:铸造工艺中,浇注温度和浇注速度都会对气孔缺陷的形成产生影响。
浇注温度过高,金属流动速度过快,就会使气体不能充分排出,从而导致气泡的形成;浇注速度过快,则会使金属渣块混入熔体中,从而形成气孔缺陷。
3.顶底放砂:顶底放砂也是导致气孔缺陷的重要因素之一。
如果模具与砂型之间的接触面太大或没有足够的转角倒圆处理,就会导致铸件内部含有较多的气泡和气孔缺陷。
三、操作不当造成的影响操作不当也是导致气孔缺陷的原因之一。
操作不当主要指铸造工艺中操作人员在操作过程中未能注意到严格按照规范操作,在浇注过程中造成阻塞以及部分处理不当都可能导致气孔缺陷。
铸件气孔缺陷的成因及防止措施
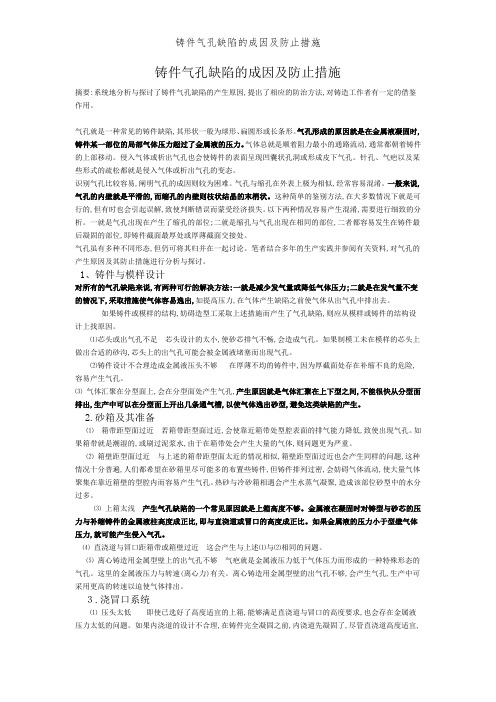
铸件气孔缺陷的成因及防止措施摘要:系统地分析与探讨了铸件气孔缺陷的产生原因,提出了相应的防治方法,对铸造工作者有一定的借鉴作用。
气孔就是一种常见的铸件缺陷,其形状一般为球形、扁圆形或长条形。
气孔形成的原因就是在金属液凝固时,铸件某一部位的局部气体压力超过了金属液的压力。
气体总就是顺着阻力最小的通路流动,通常都朝着铸件的上部移动。
侵入气体或析出气孔也会使铸件的表面呈现凹囊状孔洞或形成皮下气孔。
针孔、气疤以及某些形式的疏松都就是侵入气体或析出气孔的变态。
识别气孔比较容易,阐明气孔的成因则较为困难。
气孔与缩孔在外表上极为相似,经常容易混淆。
一般来说,气孔的内壁就是平滑的,而缩孔的内壁则枝状结晶的末梢状。
这种简单的鉴别方法,在大多数情况下就是可行的,但有时也会引起误解,致使判断错误而蒙受经济损失。
以下两种情况容易产生混淆,需要进行细致的分析。
一就是气孔出现在产生了缩孔的部位;二就是缩孔与气孔出现在相同的部位,二者都容易发生在铸件最后凝固的部位,即铸件截面最厚处或厚薄截面交接处。
气孔虽有多种不同形态,但仍可将其归并在一起讨论。
笔者结合多年的生产实践并参阅有关资料,对气孔的产生原因及其防止措施进行分析与探讨。
1、铸件与模样设计对所有的气孔缺陷来说,有两种可行的解决方法:一就是减少发气量或降低气体压力;二就是在发气量不变的情况下,采取措施使气体容易逸出,如提高压力,在气体产生缺陷之前使气体从出气孔中排出去。
如果铸件或模样的结构,妨碍造型工采取上述措施而产生了气孔缺陷,则应从模样或铸件的结构设计上找原因。
⑴芯头或出气孔不足芯头设计的太小,使砂芯排气不畅,会造成气孔。
如果制模工未在模样的芯头上做出合适的砂沟,芯头上的出气孔可能会被金属液堵塞而出现气孔。
⑵铸件设计不合理造成金属液压头不够在厚薄不均的铸件中,因为厚截面处存在补缩不良的危险,容易产生气孔。
⑶气体汇聚在分型面上,会在分型面处产生气孔,产生原因就是气体汇聚在上下型之间,不能很快从分型面排出,生产中可以在分型面上开出几条通气槽,以使气体逸出砂型,避免这类缺陷的产生。
浅谈铸件气孔的产生及其防止措施

浅谈铸件气孔的产生及其防止措施气孔是铸造生产中常见的铸件缺陷之一。
在铸件的废品中,据统计,由于气孔导致的铸件废品占废品总数的三分之一左右。
气孔是气体聚集在铸件表面、皮下和内部而形成的空洞。
气孔的孔壁光滑,无一定的形状、尺寸和位置。
气孔有各种类型,其产生的原因各不相同,按气体来源,一般将气孔分为三类:侵入性气孔、析出性气孔和反应性气孔。
一、侵入性气孔由于浇注过程中液态金属对铸型激烈的热作用,使型砂和芯砂中的发气物(水分、粘接剂等)气化、分解和燃烧,生成大量气体,加上型腔中原有的气体,这些气体部分侵入液态金属内部而不能逸出所产生的孔洞,称为侵入性气孔。
1.侵入性气孔的形成条件由于浇注时铸型在液态金属的高温作用下产生大量气体,从而使液态金属和铸型界面上的气体压力骤然增加,气体可能侵入液态金属,也有可能从型砂或冒口、出气孔中排出型外,只有在满足下列条件的情况下型(芯)砂中的气体才会侵入液态金属即P气>p液+p阻+p腔式中p气:液态金属和砂型界面的气体压力;P液:液态金属的静压力(p液=ρgh)P阻:气体侵入液态金属时,由于液态金属表面张力而引起的阻力P腔:型腔中液态金属液面上的气体压力2.防止侵入性气孔的主要方法和工艺措施(1)降低砂型(芯)界面的气体压力是最有效的手段。
如选用透气性好,发气量低的造型材料;控制型砂的水分及其它发气附加物;应用发气量低、发气速度慢、发气温度高的粘结剂;砂型(芯)排气要畅通,增加出气孔,提高铸型的排气能力;浇注后及时引火。
引火后可听到气体的爆燃声和砂箱周围燃烧的火焰,砂箱移开后,可看到下部潮湿的痕迹。
说明有大量的气体产生如H2、O2、CO、H2S等气体。
(2)适当提高浇注温度,延迟凝固时间,使侵入的气体有充分的时间从液态金属中上浮和逸出。
(3)加快浇注速度,增加上砂型高度,使有效压力头增加,提高液态金属的静压力。
(4)浇注系统在设置时,应注意液态金属流的平稳,浇注千万不能中断,防止气体卷入金属液中。
铸件气孔形成的原因及解决的措施

铸件气孔形成的原因及解决的措施在工厂的生产实践中,人们对气孔的叫法不一样。
有的叫气眼、气泡、气窝,丛生气孔,划为一体统称为“气孔”。
气孔是铸件最常见的缺陷之一。
在铸件废品中,气孔缺陷占很大比例,特别是在湿模砂铸造生产中,此类缺陷更为常见,有时会引起成批报废。
球墨铸铁更为严重。
气孔是在铸件成型过程中形成的,形成的原因比较复杂,有物理作用,也有化学作用,有时还是两者综合作用的产物。
有些气孔的形成机理尚无统一认识,因为其形成的原因可能是多方面的。
各类合金铸件,产生气孔缺陷有其共性,但又都是在特定条件下生成的,因此又都具有特殊性。
所以要从共性中分析产生气孔的一般规律,也要研究特性中的特有规律,以便采取有效的针对性措施,防止气孔缺陷的产生。
一、气孔的特征气孔大部分产生在铸件的内表面或内部、砂芯面以及靠近芯撑的地方。
形状有圆形的、长方形的以及不规则形状,直径有大的、小的也有似针状丛生孔形。
气孔通常具有干净而光滑的内孔面,有时被一层氧化皮所覆盖。
光滑的孔内颜色一般是白色,或带有一层暗蓝色,有的气孔内壁还有一个或几个小铁豆豆,常把这种气孔称作“铁豆气孔”。
距铸件表面很近的气孔,又叫“皮下气孔”,往往通过热处理、清滚或者机械加工后才被发现。
还有一种常见的气孔,叫做“气缩孔”,是气体和铸件凝固时的收缩而共同促使其产生的,形状又有其特殊性。
铸钢和高牌号铸铁都常出这种名称的缺陷,但形成的机理有所差异。
气孔和缩孔是可以区别开的,一般说来气孔是圆形或梨形的孔洞,内壁光滑。
而不像缩孔那样内表面比较粗糙。
二、气体的来源各类铸造合金在熔炼及成型过程中,总要和气体相接触的,气体就会进入并以各种形式存在于合金中,气体来源是多方面的,归纳起来,主要来自以下几个方面:1、原材料带进的。
各种铁类、铁合金、燃料、熔剂等,自身就含有气体,有的带有雨雪潮湿,有的锈蚀,有的带有浊污,在熔炼过程中都有可能产生气体,其中一部分就会滞留在合金液中。
有人提出:炉料上带的雨水、雪湿、浊污随炉料进入炉内,在炉料还是固态仅发红时,它们就已蒸发或烧掉,怎么会留存在铁水里呢?在资料里,用语言详细解释的不多,但在实践中,只要炉料(生铁、废钢、回炉料)受雨雪淋湿,湿着入炉,铁水一定会氧化,这确是事实。
连铸坯中气泡产生原因分析及判断方法

连铸坯中气泡产生原因分析及判断方法发表日期:2007-1-10 阅读次数:387摘要:本文对连铸坯气泡的成因及特性进行了分析,并提出了识别气泡类型及改善和解决气泡问题的方法。
关键词: 连铸坯气泡氩气保护1 前言在钢的连铸过程中,不论是连铸“准沸腾钢”还是连铸高纯净度的镇静钢,国内外许多钢厂都遇到过连铸坯中的气泡问题,并且采取了相应的改进措施。
有关连铸坯中气泡问题的科技文献,国内主要是侧重于连铸低硅低碳拉丝材等“准沸腾钢”,高品质钢连铸坯中的气泡问题的研究主要见诸国外文献,国内文献不多。
韶钢2号板坯连铸机于2003年5月投产,至2004年10月,所生产的Q235、Q345、45、50、船板等钢号都出现了一些气泡废品。
为此,本文根据前人的理论、经验以及韶钢的生产实践,对连铸坯气泡的表现形式及产生的原因进行了分析,推断连铸坯气泡的成因,并采取了相应的改进措施,达到了改善气泡问题的目的。
2 气泡产生的原因及表现特性分析根据炼钢理论及前人的经验,连铸过程产生气泡(包括针孔)的主要原因有3类——脱氧不良、外来气体(空气、保护性气体)、水蒸气(来自潮湿的添加料和耐火材料等)。
2.1 脱氧不良2.1.1 CO气泡产生机理脱氧不良时,产生的气泡为CO气泡。
文献表明,在1500℃左右,钢液中与[0]优先发生反应的元素排列顺序为:Ca,Ba,Re,Al,Si,C,V,Mn,Fe,P,Cu,其中的Si,在1500℃附近,跟[O]反应的优先顺序与C相当,即[O]会与[C]、[Si]同时发生反应。
当钢中存在[0]时,发生碳氧反应的必要条件之一是,在一定温度下,排在[C]元素之前的强脱氧剂[M]与[0]反应达到平衡时的[0]浓度高于[C]与[O]反应达到平衡时的[O]浓度。
钢中碳氧反应:[C]+[O]=CO△rG o=-22186-38.386 T(J/m01) (1)则:lnK=ln{(Pco/P o)/(a[c]a[0])}-2668.5/T+4.617因此:a[c]a[0]=Pco/P O EXP[-268.5/T—4.617] (2)假设CO分压为一个标准大气压,无其它气体,Pc0/P o=1,令:T=1500+273=1773K则:a[c]a[0]=0.002194 (3)设活度系数fc=fo=1,当w[c]%=0.06(低碳拉丝用钢的碳含量)和0.46(45号优质碳素钢的碳含量)时,由式 (3)计算得到:w[o]%=0.03657和0.004770 (4)这是在以上假设条件下,与[C]平衡的[O]值。
连铸坯疏松及缩孔产生的原因有哪些

1 前言某钢铁(集团)公司炼钢厂新建了一台1800mm板坯连铸机,设计铸坯规格为厚200mm、220mm、250mm,宽1400mm~1800mm。
试运行期间生产了断面为250mm×1550mm的Q235、 Q345钢板坯,低倍组织检验结果中心偏析和中心疏松较严重。
我们摘录了13个炉批号的低倍检验报告,进行对比检查(如表1),发现中心偏析一般为B2.5级,中心疏松为2级左右。
当铸坯轧制成材后,做两个断面相互垂直的焊接试验时,在氧割或切口上出现局部分层。
根据该厂生产实际情况,为尽可能减少中心偏析与中心疏松,生产高质量的铸坯,分析了中心偏析与中心疏松缺陷的形成原因,提出了具体的预防对策。
2 中心偏析与中心疏松形成原因中心偏析是指钢液在凝固过程中,溶质元素在固液相中进行丙分配时,表现为铸坯中元素分布不均匀,铸坯中心部位的C、S、P等元素含量明显高于其它部位。
在铸坯厚度中心凝固末端区域常表现为“V”偏析。
中心疏松是指钢液在凝固末期,在铸坯厚度中心的枝晶间产生微小空隙。
导致中心偏析和中心疏松产生的原因很多,且这两种缺陷往往相伴而生。
2.1 铸坯凝固组织中柱状晶过于发达中心偏析和中心疏松形成机理之一是“凝固晶桥”理论,即铸坯凝固过程中,铸坯传热的不稳定性导致柱状晶生长速度快慢不一,优先生长的柱状晶在铸坯中心相遇形成“搭桥”,液相穴内钢液被“凝固晶桥”分开,晶桥下部钢液在凝固收缩时得不到上部钢水补充而形成疏松或缩孔,并伴随中心偏析。
当凝固组织中柱状晶过于发达时,越容易形成“凝固晶桥”,铸坯中也越容易产生中心偏析和中心疏松。
2.2 钢液中易偏析溶质元素含量过高中心偏析和中心疏松形成机理之二是钢液中易偏析溶质元素析出与富集理论,即铸坯从表壳往中心结晶过程中,钢液中的溶质元素在固液相界上具有溶解平衡移动,C、S、P等易偏析元素以柱状晶粒析出,排到尚未凝固的金属液中,随结晶的继续进行,这些易偏析元素被富集到铸坯中心或凝固末端区域,由此产生中心偏析和中心疏松。
气孔形成的原因及解决的措施(二)

气孔形成的原因及解决的措施(二)三、产生气孔的原因前面叙述的是气体的主要来源和部分形成气孔的经过。
其实在具体生产作业过程中,形成气孔的原因还很多,为了便于在实践中直接操作应用,把各工序在操作中易产生气孔的具体因素归纳如下:(1)冶炼过程中,金属液氧化,溶解有大量气体。
金属液溶解的气体量与所熔炉料的质量,以及熔化设备,炉工操作技术有很大的关系。
如炉料氧化,锈蚀严重,带有油污和焦炭带有水、雨、雪潮湿。
熔化操作不当,底焦太高,过热区越大,铁水氧化越严重,风压风量太大,使金属液大量吸气而过分氧化。
(2)浇注时或金属液凝固过程中,由外界侵入的气体。
需要说明的是,由这种气体形成的气孔往往是单独存在的,气体来源型(芯)中的水分,附加材料燃烧挥发产生的气体,浇注中金属液形成涡流,将气体旋入而产生的气孔。
由经验可知这种气孔大部呈梨形状,如果梨形孔的尖部指向泥芯(图1),那么这种气孔有可能是因芯子而造成的。
如果尖部指向外型(图2),则有可能是因外型而造成的。
如果通过气孔形状判断不出气体来源,就只有根据气孔所在的位置来决定,如果气孔在芯子附近,该气孔则有可能是由芯子而造成的。
如果发生在外型附近,这种气体则有可能是由外型而造成的。
但气孔发生在中部就难以判断了。
在这种情况下,就必须从铸造全部工艺过程来分析和判断了。
(实践中常遇到这样的情况,在分析废品原因时,找到了一个认为可能是产生废品的原因,马上就被自己又否认掉,甚至找到几个可能的原因,但又都被推翻,确定不下来。
可见废品分析的困难度。
某工厂生产HT250汽车制动鼓,造型工艺没有改变,化学成分和以前的一样,但是有一段时间生产出的铸件却白口,找不出真正原因,只能认为可能是废钢中含有微量反石墨化元素。
许昌一位老板,铸造专业毕业二十多年了,现办有两个铸造工厂,他说:下辈子说啥也不搞铸造了,太难,正干的好好的,说出废品就是一批,原因就不好找。
)(3)所用的原砂过细。
山西晋城一铸造厂,因型砂过细,衬板上表面出现丛生气孔,在不能及时更换型砂的情况下,只有采用多扎气眼,型砂适当干点的措施来解决。
铸件砂眼气孔形成原因

铸件砂眼气孔形成原因铸件砂眼和气孔,这些小家伙在铸造过程中真是个“捣蛋鬼”。
想想看,当你期待着一块完美的铸件,结果却看到那些“眼睛”,心里肯定不爽。
这些砂眼和气孔到底是怎么来的呢?今天咱们就来聊聊这背后的故事,顺便让大家轻松一下。
铸造材料的准备可不是随便的。
这就像做菜,食材得新鲜。
你要是用不合格的砂子,那简直就是给自己挖坑。
想象一下,用了一堆质量不高的砂子,铸造出来的东西自然会出现问题。
这时候,砂子里的杂质就会开始捣乱,让铸件出现小洞。
真是让人哭笑不得啊。
再说了,浇铸的温度也得掌握得当。
要是温度不够高,金属流动不畅,结果就是那些小气泡跑出来,形成气孔。
想象一下,就像煮水时没开到沸腾,水里还会有气泡一样。
铸件在固化的时候,温度变化也很关键,温度骤降或者升高,都会让那些气泡有机可乘。
然后咱们得聊聊铸造的环境。
湿度、温度、风速,这些外部因素也是个大影响。
比如说,外面刮风下雨,铸件冷却不均匀,那可就完蛋了。
那些小气泡见风就是雨,像捣蛋鬼一样出现在铸件里,真是让人无奈。
想必铸造师傅们也得苦不堪言,心里想着:“这下真是竹篮打水一场空啊。
”还有一种情况,就是浇注过程中的技术问题。
如果浇得太快,金属流动太急,没时间填满每个角落,那就会留下空隙,成了气孔。
这就好比你把水倒得太快,结果溅了一地。
太慢也不行,慢吞吞的,反而会让金属氧化,形成砂眼。
就像给朋友倒酒,慢半拍,气氛都没了。
铸造的设备也得给力。
设备老旧,故障频出,可能就会导致铸造过程中产生气孔。
就好比一辆老爷车,发动不起来,你再怎么努力也没用。
这些问题叠加在一起,铸件的质量就可想而知了。
可别以为这只是小问题,出现砂眼和气孔,可能直接影响到铸件的使用寿命。
再说了,铸造工人的技术水平也至关重要。
一个经验丰富的师傅和一个新手,效果可差得远了。
熟能生巧,师傅们在浇铸的时候,心里都有数,知道什么时候加速,什么时候减慢,才能避免那些小气泡。
新手的话,可能连怎么拿铲子都要琢磨半天。
铸造合金中的气孔问题分析与解决方案

铸造合金中的气孔问题分析与解决方案铸造合金是一种重要的材料,在工业生产中广泛使用。
然而,铸造合金中存在一个常见且严重的问题,即气孔。
气孔会导致合金材料的强度和韧性下降,从而影响其使用性能。
本文将对铸造合金中的气孔问题进行分析,并提出解决方案。
一、气孔问题的原因分析在铸造合金的生产过程中,气孔问题主要由以下几个方面引起。
1.1 铸造工艺铸造过程中,金属液体在冷却凝固过程中会释放出气体。
如果冷却凝固速度过快或金属液体内气体排不出来,就会形成气孔。
此外,铸造温度、铸型设计和浇注工艺等也会对气孔产生影响。
1.2 材料质量铸造合金的气孔问题还与原材料质量有关。
例如,杂质、气体含量过高和金属液体的氧化等都可能导致气孔的形成。
1.3 设备状态铸造设备的状态也会对气孔问题产生一定影响。
如设备密封性差、过冷、过热或铸型温度控制不准确等问题都可能造成气孔的产生。
二、解决气孔问题的措施针对铸造合金中的气孔问题,我们可以从以下几个方面采取相应的解决措施。
2.1 优化铸造工艺通过优化铸造工艺,可以减少气孔的产生。
具体措施包括:合理设置铸造温度和浇注速度,控制冷却凝固速度;合理设计铸型,增加通气孔,避免金属液体内气体滞留。
2.2 优选原材料选择质量良好的原材料,并进行必要的预处理。
严格控制杂质和气体含量,以降低气孔的产生。
2.3 检查和维护设备定期检查和维护铸造设备,确保设备状态良好。
特别是要注意设备的密封性能,以防止气体的进入。
2.4 使用辅助材料在铸造过程中,可以利用一些辅助材料来减少气孔的产生。
例如,在金属液体中加入脱氧剂、鞣剂等,可以有效吸附和减少气体的释放。
2.5 增加后处理工序在铸造完成后,还可进行一些后处理工序来减少气孔问题。
例如,通过热处理、去毛刺、焊接等方式,可以进一步改善合金材料的质量。
三、实施措施之后的效果与展望在实施上述措施之后,铸造合金中的气孔问题得到了明显的改善。
通过优化铸造工艺和原材料选择,气孔的产生率显著降低。
探讨铸造铜合金气孔缺陷的生成机理及对策

探讨铸造铜合金气孔缺陷的生成机理及对策铸造铜合金是一种常见的金属加工技术,用于制造各种机械零件和装饰品。
然而,在铸造过程中,气孔缺陷的生成成为了影响铸件质量的一个重要因素。
本文将探讨铸造铜合金气孔缺陷的生成机理以及对策。
一、气孔缺陷的生成机理在铸造铜合金的过程中,气孔缺陷的生成主要受到以下几个因素的影响:1. 液态金属中的气体溶解度:铸造铜合金的熔点较高,液态金属中的气体溶解度较低。
在熔融状态下,金属容易吸收大量气体,而在凝固过程中,气体会从金属中析出,形成气孔。
2. 固态金属的收缩性:铸造铜合金在凝固过程中会发生固态收缩,这种收缩会导致周围的金属受到挤压,进而产生内部应力。
当内部应力超过金属的强度限制时,将引起气孔的形成。
3. 浇注过程中的气体吸入:在铸造过程中,金属液体经过浇注口流入模型中,会带入大量的空气,这些空气会在凝固过程中形成气孔。
4. 模型设计和制造因素:模型的设计和制造过程中可能存在不合理的孔洞或缺陷,这些孔洞或缺陷会在铸造过程中成为气孔的形成位置。
二、减少气孔缺陷的对策为了减少铸造铜合金中气孔缺陷的生成,可以采取以下对策:1. 选择合适的铸造工艺:根据铸造铜合金的特点,选择适当的铸造工艺,如真空铸造、压力铸造或注射成型等。
这些工艺可以在浇注过程中减少气体的吸入,从而减少气孔的生成。
2. 控制铸造温度和浇注速度:合理控制铸造温度和浇注速度可以提高金属液体的流动性,减少气体的溶解度,从而减少气孔的生成。
同时,控制凝固速度可以减少固态金属的收缩,减小内部应力,有利于减少气孔的形成。
3. 加入消泡剂:在铸造过程中,可以加入适量的消泡剂,来降低金属液体的表面张力,提高气泡破裂的能力,从而减少气孔的生成。
4. 优化模型设计和制造工艺:改善模型的设计和制造过程,确保模型的密封性和稳定性。
同时,检查和修复模型中的孔洞和缺陷,减少气孔的生成位置。
5. 加强质量控制:在铸造过程中加强质量控制,进行严格的操作规范和工艺参数控制,确保每个步骤都符合标准要求。
铸造缺陷-气孔的描述及分析
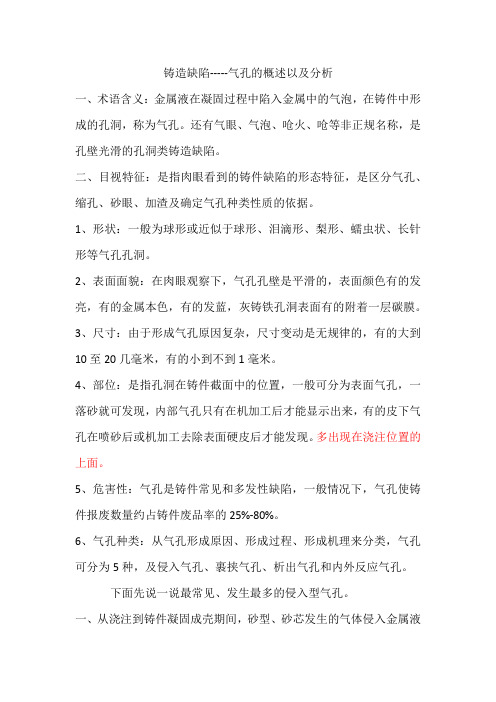
铸造缺陷-----气孔的概述以及分析一、术语含义:金属液在凝固过程中陷入金属中的气泡,在铸件中形成的孔洞,称为气孔。
还有气眼、气泡、呛火、呛等非正规名称,是孔壁光滑的孔洞类铸造缺陷。
二、目视特征:是指肉眼看到的铸件缺陷的形态特征,是区分气孔、缩孔、砂眼、加渣及确定气孔种类性质的依据。
1、形状:一般为球形或近似于球形、泪滴形、梨形、蠕虫状、长针形等气孔孔洞。
2、表面面貌:在肉眼观察下,气孔孔壁是平滑的,表面颜色有的发亮,有的金属本色,有的发蓝,灰铸铁孔洞表面有的附着一层碳膜。
3、尺寸:由于形成气孔原因复杂,尺寸变动是无规律的,有的大到10至20几毫米,有的小到不到1毫米。
4、部位:是指孔洞在铸件截面中的位置,一般可分为表面气孔,一落砂就可发现,内部气孔只有在机加工后才能显示出来,有的皮下气孔在喷砂后或机加工去除表面硬皮后才能发现。
多出现在浇注位置的上面。
5、危害性:气孔是铸件常见和多发性缺陷,一般情况下,气孔使铸件报废数量约占铸件废品率的25%-80%。
6、气孔种类:从气孔形成原因、形成过程、形成机理来分类,气孔可分为5种,及侵入气孔、裹挟气孔、析出气孔和内外反应气孔。
下面先说一说最常见、发生最多的侵入型气孔。
一、从浇注到铸件凝固成壳期间,砂型、砂芯发生的气体侵入金属液时产生的气孔称为侵入性气孔。
1、它的形状特征:团球形、梨形、泪滴形,小头所指是气体来源的方向。
2、表面面貌:孔壁平滑,铸件侵入气体主要成分是CO时,孔壁呈蓝色;是氢气时,孔壁是金属色,发亮;是水蒸气时,孔壁是氧化色,孔壁发暗,灰色。
3、一般尺寸较大,在几毫米以上。
4、部位:按浇注位置来说,常处于铸件上表面,去掉浇冒口或气针后可看到,有的粗加工后表现出来。
5、分布:大多情况下是单个或几个聚集的尺寸较大的气孔,很少成为弥散性气孔或针孔。
二、形成机理:1、砂型:砂型中的气体侵入金属液,分为两种:①不润湿型:组成砂型型砂粒度细、强度高、紧实度大(硬),如静压线造型。
- 1、下载文档前请自行甄别文档内容的完整性,平台不提供额外的编辑、内容补充、找答案等附加服务。
- 2、"仅部分预览"的文档,不可在线预览部分如存在完整性等问题,可反馈申请退款(可完整预览的文档不适用该条件!)。
- 3、如文档侵犯您的权益,请联系客服反馈,我们会尽快为您处理(人工客服工作时间:9:00-18:30)。
连铸圆管坯气孔形成机理分析
李献忠杜方
(技术中心)
摘要在实际生产中,连铸圆管坯表面存在大量气孔,并且较集中在内弧侧的两振痕之间。
本文分析了这种气孔缺陷的形成机理,据此提出了控制措施,在新的工艺条
件下生产的圆管坯Q345B表面无气孔缺陷,铸坯质量有所提高。
关键词连铸圆管坯表面气孔低倍组织
1前言
我国钢管厂在原料质量检验上最重视的通常是
管坯的表面质量问题,这一方面说明了管坯表面质量
对钢管生产的重要性,另一方面也反映了我国管坯存
在的表面缺陷中这一问题较普遍[1]。
今年,公司
“EAF+LF”工艺线所生产的连铸圆坯中发现表面气
孔缺陷,通过对此类缺陷的产生机理进行分析,找出
其形成原因,据此采取了相应的工艺整改措施。
在新
的工艺条件下生产的圆管坯Q345B表面无气孔缺
陷,铸坯质量有所提高。
2表面气孔形成机理
表面气孔形成机理:钢液凝固时,溶解在其中的
气体生成压(P CO、P H
2、P
N2
、P
H2O
)大于钢水的静压与大
气压之和时,便形成了气泡[2]。
气泡在结晶器壁钢液弯月面附近或铸坯凝固前沿被捕捉,一方面随着凝固前沿的不断推移和气体的不断析出而逐步长大,另一方面随着坯壳的凝固收缩又要被迫缩小,加上钢水静压力和坯壳内外温度梯度的作用,气泡被迫向“势能”较低的铸坯表面方向渗透,最终形成表面气泡或针孔。
3表面气孔缺陷分析
3.1实物检验
随机切取一段有气孔缺陷的圆管坯,经逐层车削后发现皮下气泡14个(图1),最深达12mm,通过观察发现气孔普遍分布于相邻两振痕之间(图2),较多集中于内弧侧,少量分布于侧弧,外弧基本没有。
取2个典型试样做解剖分析(图3、4),实测气孔深度都是4.9mm,另可看出铸坯表面气孔周围有轻微的翻皮和钢水流出的痕迹。
图1表面车削后的圆管坯
图2
圆管坯上的气孔分布
图3表面气孔的宏观形貌
1
图4
气孔剖开后截面形貌
3.2原因分析3.2.1
钢液气体含量
由图5可知:在分压1atm 下,气体(H 2、N 2)在固态纯铁中的溶解度明显低于液态,
因此铁(钢)液凝固过程中气体会不断析出;在1400 1550ħ时,纯铁由液态逐渐凝固为固态时,气体的溶解度急剧下降,此时气体析出的速度最快。
因此冶炼过程中要杜绝原材料不干燥、钢液脱氧不良、钢液二次氧化、保护浇注不到位钢液吸气等,
以防止由于钢液气体含量过高,在随后的连铸过程中气体因溶解度降低而从钢液中大量析出。
图5氢和氮在纯铁中的溶解度
[3]
3.2.2
浸入式水口插入深度
圆管坯比表面积小,水口冲击深度大,气泡上浮行程增加,
上浮时间长;加之圆管坯结晶器流场比方坯更均匀,钢液紊流影响小,气泡碰撞长大几率小、形核长大速度慢,也延长了上浮时间。
这样气泡很容易在逸出结晶器液面以前就被弯月面或凝固前沿所捕获。
因此生产圆管坯时,浸入式水口插入深度要分规格进行控制。
图6提供了2种规格圆管坯浸入式水口的最佳插入深度,可供参考。
图6圆管坯浸入式水口的最佳插入深度3.2.3
结晶器电磁搅拌
有资料指出[4]
,在未经搅拌的铸坯上存在明显
的不对称性,
内弧侧缺陷多于外弧侧,特别是在10 15mm 范围内,缺陷更多。
而电磁搅拌通过改善结晶器流场,使钢水由中心向外流动,而比重较小的夹杂和气泡则被推向中心,
逐步上浮逸出结晶器钢液面,大大减少了内外弧缺陷。
实际生产中虽采用了电磁搅拌技术,但气孔仍多集中于内弧侧,可能是电磁搅拌参数设置不当,效果不明显。
3.2.4
结晶器振动
图7
铸坯振痕形成示意
[4]
如图7,负滑脱期间(图中2 4区间),结晶器向
下运行速度大于铸坯拉速,弯月面上的液渣被吸入到坯壳与结晶器壁的缝隙中起润滑作用。
期间弯月面
2
受结晶器压力和渣圈的挤压作用而远离结晶器壁,当结晶器运行到图中位置3时,弯月面初生坯壳偏离结晶器壁距离最大,弯月面的半径也最大,弯月面的熔池最深,承受的钢水压力也最大,此时的弯月面是一个振痕周期内最薄弱的时刻,这时气泡最容易穿透坯壳而形成气孔。
另外由于弯月面初生坯壳偏离结晶器壁距离最大,弯月面捕捉气泡的几率也最大。
因此,见到的气孔往往分布在相邻两振痕之间。
结晶器振动采用非正弦模式,增加正滑脱时间,减少负滑脱时间,可有效控制弯月面偏离结晶器壁的距离,使弯月面初生坯壳均匀贴向结晶器壁,降低表面气孔形成几率。
4工艺整改措施及效果
4.1整改措施
要根本解决圆管坯表面气孔缺陷,首先要控制好钢液中的气体含量,尤其是[H]。
由此对各工序的操作要点进行了规范和调整。
1)原材料:冶炼所需要的合金、石灰、萤石球、保护渣、保温剂等要求干净和干燥,并满足公司原材料标准要求,水分≤0.5%。
2)EAF操作要点:每炉钢兑铁水量不得低于50t,终点碳必须控制在0.10%以上,确保钢水不过氧化。
3)EBT操作要点:严禁出钢下氧化渣;用硅锰合金替代硅铁,如果不能完全替代,必须将硅铁放入钢包进行烘烤,烘烤时间要求大于30min。
4)LF操作要点:精炼炉禁止使用未烘烤的硅铁,可以使用硅锰合金、硅铁粉、硅钙线等调整硅成分;喂碳线增碳,全程严禁钢水裸露;保证白渣时间≥30min,软吹时间≥15min;控制萤石球的用量;每炉钢定[H]和定[O]均不得大于6ppm。
5)CCM操作要点:严格控制大包长水口氩封效果;严格控制浸入式水口插入深度:Φ230mm、Φ180mm浸入式水口插入深度为110 140mm;Φ150mm、Φ160mm浸入式水口插入深度为80 110mm;选取合理的电磁搅拌参数,电流从680A降到480A;结晶器振动采用非正弦模式或高频率小振幅模式。
4.2Q345B试制
4.2.1冶炼控制情况
按照整改后的工艺操作要点,2010年4月3日中班共生产7炉Φ230mm Q345B。
由表1可知,EAF 终点碳控制得非常好,钢水脱氧良好,钢中[O]、[H]含量控制得较好。
表1圆管坯Q345B冶炼控制情况(%)炉号过程C Mn Si P S Als O(ppm)H(ppm)
1195EAF0.1060.060.010.0090.0271.604--LF0.1621.370.380.0120.0050.0313.64.6
1196EAF0.0860.040.020.0080.0341.094--LF0.1741.340.350.0170.0040.0315.14.8
1197EAF0.1380.060.010.0030.0301.220--LF0.1851.370.390.010.0050.0313.14.8
1198EAF0.1360.090.020.0080.0371.591--LF0.1871.330.450.0120.0020.0254.94.6
1199EAF0.1380.050.010.0020.0261.490--LF0.1841.350.380.0090.0050.0194.53.6
1200EAF0.1350.040.020.0020.0201.405--LF0.1601.330.340.0090.0040.0264.54.6
1201EAF0.1200.110.020.0110.0311.211--
LF0.1611.340.310.0130.0060.0273.14.3
3
4.2.2低倍组织检验
圆管坯Q345B表面质量良好,无表面气孔缺陷,说明采取的工艺整改措施切实可行。
低倍检验结果如表2所示。
表2圆管坯Q345B低倍检验结果(级)炉号缩孔中心偏析中心疏松中心裂纹中间裂纹柱状晶非金属夹杂皮下裂纹皮下气泡1195-0.51--0.5---1196-0.51--0.5---1197-11.5------1198-0.51--0.5---1199-0.51--0.5---1200-11--0.5---1201-0.51------
5结论
1)此类连铸圆管坯表面气孔缺陷系钢液中气体含量过高产生的气泡,在结晶器壁钢液弯月面初生坯壳偏离结晶器壁距离最大时被捕捉,在钢水静压力和结晶器振动等因素的综合作用下,穿透两个振痕中间的坯壳所致。
2)要根本解决这种连铸圆管坯表面气孔缺陷,必须降低钢液中的气体含量,尤其是[H]。
应使用不易吸潮的原辅材料,并加强其使用过程的管理。
3)优化结晶器水口插入深度和电磁搅拌参数,改善结晶器流场和温度场,可有效控制连铸圆管坯表面气孔缺陷的产生。
4)新一轮生产的圆管坯Q245B表面无气孔缺陷,说明工艺整改措施切实可行。
参考文献
[1]李国忠,沈建军.连铸连轧圆管坯表面质量分析与改进[J].钢管,2001,30(4):31.
[2]史宸兴.实用连铸冶金技术[M].北京:冶金工业出版社,1998.
[3]蔡开科.浇注与凝固[M].北京:冶金工业出版社,1992.
[4]蔡开科.连铸结晶器[M].北京:冶金工业出版社,2008.
4。