浅谈专用成形刀具重磨技术
滚刀重磨的技术要求及重要性

滚刀重磨的技术要求及重要性滚刀的重磨是在滚刀的前刃面上进行的,为了保证滚刀的精度,即重磨后滚刀的切削刃仍能位于基本蜗杆的螺旋面上,其前刃面在重磨后应满足下列三方面要求,否则会影响被切齿轮齿形的精度: (1) 容屑槽周节的误差 容屑槽周节的误差分为容屑槽周节的相邻误差和容屑槽周节的最大累积误差。
容屑槽周节的误差用于表示滚刀前刃面在圆周上分布的不均匀性。
由于滚刀在制造时刀齿的铲削是在精确等分的基础上进行的,因此前刃面若重磨得不等分,会使切削刃偏离基本蜗杆的表面,造成各排刀齿的齿厚不等。
当它们在不同的展成位置上切出齿轮时,具有圆周上正偏差的刀齿齿厚较大,因而会使齿轮齿形产生“过切”,齿面上形成凹度;反之,具有圆周上负偏差的刀齿齿厚较薄,滚切时会使齿形产生“少切”,齿面上形成凸棱,从而使齿面变得凹凸不平。
为此,滚刀重磨后得误差应在规定的公差范围内。
(2) 滚刀前刃面的导程误差 滚刀前刃面的导程误差,对于容屑槽为螺旋槽的滚刀是用前刃面的实际导程与理论导程之间的差值来表示的。
而对容屑槽为直槽的滚刀,由于其前刃面第 1 页的导程为无穷大,因此,这一误差表现为滚刀前刃面对内孔轴线的平行度。
当滚刀前刃面发生这种误差时,刀齿切削刃在全长上将逐渐偏离基本蜗杆表面,并造成滚刀外圆上的锥度。
这种滚刀在加工时,会引起被加工齿轮齿形角(压力角)的均匀畸变,使齿形产生不对称的斜角。
(3) 滚刀前刃面的径向性误差 为了制造及测量的方便,齿轮滚刀的前角一般都做成零度,即滚刀的前刃面通过滚刀的半径方向,并在径向成直线形。
重磨时,如果砂轮相对于滚刀的位置不正确,磨出的前刃面不在滚刀的半径方向,则会在滚刀上形成正前角或负前角。
前刃面的径向性误差会减小或增大刀齿的齿形角(压力角),(当滚刀为正前角时齿形角<压力角>减小,反之增大),从而使齿轮齿形角(压力角)产生相应的误差。
即滚刀为正前角时,使齿轮齿顶加厚,齿根变瘦,齿形角(压力角)减小;而为负前角时,使齿轮齿顶变瘦,齿根加厚,齿形角(压力角)增大。
刀具磨削知识点总结大全
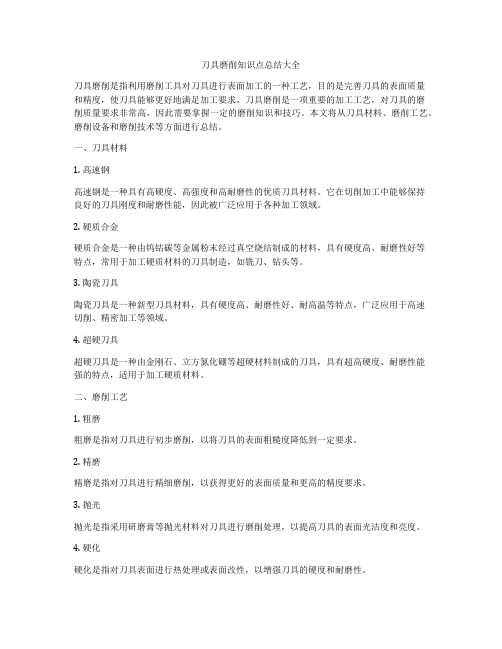
刀具磨削知识点总结大全刀具磨削是指利用磨削工具对刀具进行表面加工的一种工艺,目的是完善刀具的表面质量和精度,使刀具能够更好地满足加工要求。
刀具磨削是一项重要的加工工艺,对刀具的磨削质量要求非常高,因此需要掌握一定的磨削知识和技巧。
本文将从刀具材料、磨削工艺、磨削设备和磨削技术等方面进行总结。
一、刀具材料1. 高速钢高速钢是一种具有高硬度、高强度和高耐磨性的优质刀具材料。
它在切削加工中能够保持良好的刀具刚度和耐磨性能,因此被广泛应用于各种加工领域。
2. 硬质合金硬质合金是一种由钨钴碳等金属粉末经过真空烧结制成的材料,具有硬度高、耐磨性好等特点,常用于加工硬质材料的刀具制造,如铣刀、钻头等。
3. 陶瓷刀具陶瓷刀具是一种新型刀具材料,具有硬度高、耐磨性好、耐高温等特点,广泛应用于高速切削、精密加工等领域。
4. 超硬刀具超硬刀具是一种由金刚石、立方氮化硼等超硬材料制成的刀具,具有超高硬度、耐磨性能强的特点,适用于加工硬质材料。
二、磨削工艺1. 粗磨粗磨是指对刀具进行初步磨削,以将刀具的表面粗糙度降低到一定要求。
2. 精磨精磨是指对刀具进行精细磨削,以获得更好的表面质量和更高的精度要求。
3. 抛光抛光是指采用研磨膏等抛光材料对刀具进行磨削处理,以提高刀具的表面光洁度和亮度。
4. 硬化硬化是指对刀具表面进行热处理或表面改性,以增强刀具的硬度和耐磨性。
5. 镀层镀层是指在刀具表面涂覆一层金属或非金属材料,以提高刀具的表面硬度和耐磨性。
三、磨削设备1. 刀具磨床刀具磨床是专门用于刀具磨削加工的机床,具有磨削精度高、工作效率高等特点,能够满足各种刀具的磨削要求。
2. 精密磨削机精密磨削机是一种高精度、高速度的磨削设备,适用于对高精度刀具的磨削加工。
3. CNC磨削机CNC磨削机是一种采用数控技术的磨削设备,具有自动化程度高、加工精度高等特点,能够满足各种复杂刀具的磨削要求。
四、磨削技术1. 磨削参数磨削参数是指影响磨削加工质量和效率的各种工艺参数,如磨削速度、进给量、切削深度等。
数控机床刀具的选择与刃磨技术

数控机床刀具的选择与刃磨技术数控机床的出现和使用已经改变了工业生产的方式。
不仅提高了工具的使用效率,也减少了人类的工作量,更是提高了产品的质量和生产效率。
而机床刀具作为机床的重要组成部分,不管是选择还是刃磨技术都是非常重要的。
那么,数控机床刀具的选择与刃磨技术应如何进行呢?一、数控机床刀具的分类及选择数控机床刀具大致可以分为四类:麻花钻头、铰刀、加工刀和攻丝刀。
首先是麻花钻头,麻花钻头适用范围比较广,主要是用来打孔,且不易振动,是数控加工中必要的工具。
而铰刀的作用是切削铝制品和不锈钢。
它在使用时产生的切屑不会卡住,是非常实用的工具。
加工刀是一个更常见的工具,主要用于铣削、钻孔、扩孔等工序,并且可以分割成多种类型,包括高速钻头、钻头、MG金刚石刀头等。
最后是攻丝刀,主要用于攻丝加工,有丝锥刀、加强手柄丝锥刀、X型丝锥刀等多种规格。
根据不同的加工种类和加工材料,选择合适的数控机床刀具是非常重要的。
二、数控机床刀具的刃磨技术无论什么类型的机床刀具,都需要定期进行刃磨来保持其切削性能,延长其使用寿命。
下面是关于数控机床刀具刃磨技术的简单介绍:1. 切削角的选择。
切削角是刀具用来切削工件的部分,切削角的大小和形状对切削效果有着巨大的影响。
一般数控机床使用的刀具切削角比较小,一般在20度左右,以保证加工的精度。
2. 硬度测试。
机床刀具必须要具备很高的硬度才能持久耐用,但硬度过高会使切削角过细,从而影响切削效率,甚至磨损度过高容易出现裂纹断裂的现象。
因此,在机床刀具刃磨前需要对其硬度进行测试,以确定刀具刃磨参数。
3. 刃磨量的控制。
刀具的刃磨量对刀具几何形状有着非常大的影响。
一般来说,刃磨量不宜过大,以免让切削角过细、工件表面粗糙等。
同时,过小的刃磨量会导致刃磨效率低下,对刃磨质量也有不利的影响。
4. 刃磨质量控制。
刀具刃磨后,必须要进行质量检测,以确保刃磨的几何尺寸的精度、表面粗糙度和圆形度等均达到规定标准。
刀具磨损、崩刃及重磨
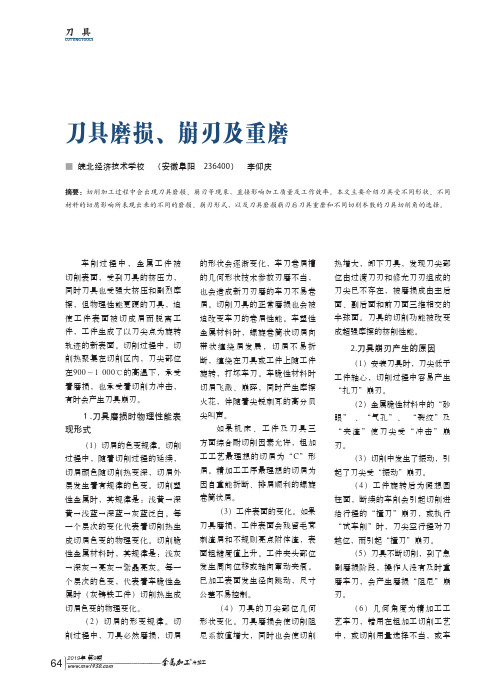
2019年 第9期冷加工64CUTTING TOOLS刀 具刀具磨损、崩刃及重磨■■皖北经济技术学校 (安徽阜阳 236400) 李仰庆摘要:切削加工过程中会出现刀具磨损、崩刃等现象,直接影响加工质量及工作效率。
本文主要介绍刀具受不同形状、不同材料的切屑影响所表现出来的不同的磨损、崩刃形式,以及刀具磨损崩刃后刀具重磨和不同切削参数的刀具切削角的选择。
车削过程中,金属工件被切削表面,受到刀具的挤压力,同时刀具也受强大挤压和剧烈摩擦,但物理性能更硬的刀具,迫使工件表面被切成屑而脱离工件,工件生成了以刀尖点为旋转轨迹的新表面。
切削过程中,切削热聚集在切削区内,刀尖部位在900~1 000℃的高温下,承受着磨损,也承受着切削力冲击,有时会产生刀具崩刃。
1.刀具磨损时物理性能表现形式(1)切屑的色变规律。
切削过程中,随着切削过程的延续,切屑颜色随切削热变深,切屑外层发生着有规律的色变。
切削塑性金属时,其规律是:浅黄→深黄→浅蓝→深蓝→灰蓝泛白。
每一个层次的变化代表着切削热生成切屑色变的物理变化。
切削脆性金属材料时,其规律是:浅灰→深灰→亮灰→紫晶亮灰。
每一个层次的色变,代表着车脆性金属时(灰铸铁工件)切削热生成切屑色变的物理变化。
(2)切屑的形变规律。
切削过程中,刀具必然磨损,切屑的形状会逐渐变化,车刀卷屑槽的几何形状技术参数刃磨不当,也会造成新刀刃磨的车刀不易卷屑。
切削刀具的正常磨损也会被迫改变车刀的卷屑性能。
车塑性金属材料时,螺旋卷筒状切屑向带状缠绕屑发展,切屑不易折断,缠绕在刀具或工件上随工件旋转,打坏车刀。
车脆性材料时切屑飞溅、崩碎,同时产生摩擦火花,伴随着尖锐刺耳的高分贝尖叫声。
如果机床、工件及刀具三方面综合耐切削因素允许,粗加工工艺最理想的切屑为“C ”形屑。
精加工工序最理想的切屑为因自重能折断、排屑顺利的螺旋卷筒状屑。
(3)工件表面的变化。
如果刀具磨损,工件表面会残留毛茸刺渣屑和不规则亮点附体渣,表面粗糙度值上升。
滚齿机的刀具磨削与修整工艺
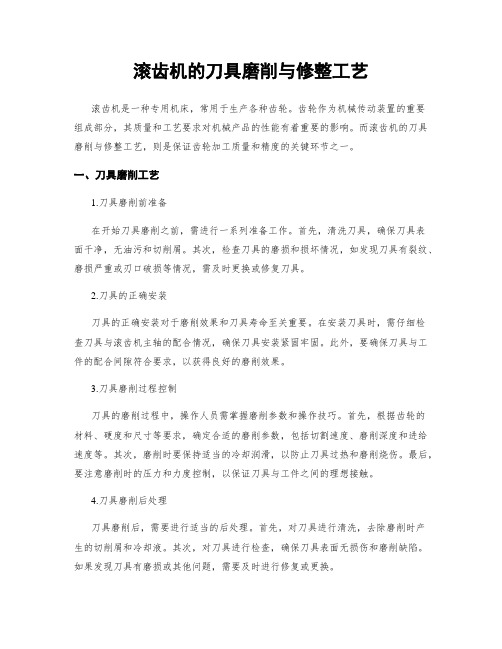
滚齿机的刀具磨削与修整工艺滚齿机是一种专用机床,常用于生产各种齿轮。
齿轮作为机械传动装置的重要组成部分,其质量和工艺要求对机械产品的性能有着重要的影响。
而滚齿机的刀具磨削与修整工艺,则是保证齿轮加工质量和精度的关键环节之一。
一、刀具磨削工艺1.刀具磨削前准备在开始刀具磨削之前,需进行一系列准备工作。
首先,清洗刀具,确保刀具表面干净,无油污和切削屑。
其次,检查刀具的磨损和损坏情况,如发现刀具有裂纹、磨损严重或刃口破损等情况,需及时更换或修复刀具。
2.刀具的正确安装刀具的正确安装对于磨削效果和刀具寿命至关重要。
在安装刀具时,需仔细检查刀具与滚齿机主轴的配合情况,确保刀具安装紧固牢固。
此外,要确保刀具与工件的配合间隙符合要求,以获得良好的磨削效果。
3.刀具磨削过程控制刀具的磨削过程中,操作人员需掌握磨削参数和操作技巧。
首先,根据齿轮的材料、硬度和尺寸等要求,确定合适的磨削参数,包括切割速度、磨削深度和进给速度等。
其次,磨削时要保持适当的冷却润滑,以防止刀具过热和磨削烧伤。
最后,要注意磨削时的压力和力度控制,以保证刀具与工件之间的理想接触。
4.刀具磨削后处理刀具磨削后,需要进行适当的后处理。
首先,对刀具进行清洗,去除磨削时产生的切削屑和冷却液。
其次,对刀具进行检查,确保刀具表面无损伤和磨削缺陷。
如果发现刀具有磨损或其他问题,需要及时进行修复或更换。
二、刀具修整工艺与刀具磨削不同,刀具修整是指对已经磨损的刀具进行修复和磨削。
刀具修整工艺的关键在于恢复刀具的几何形状和尺寸精度,以延长刀具的使用寿命。
1.刀具检查与评估在进行刀具修整之前,需要对刀具进行全面检查和评估。
包括刀具的损坏程度、磨损情况和磨损位置等。
根据评估结果,确定刀具是否需要进行修整,以及修整的方式和程度。
2.刀具的磨削与修整刀具的磨削与修整包括对刃口的修复和修整、刀身的修整和打磨等工序。
其中,对刃口的修复可以采用砂轮磨削、线切割磨削或电火花修复等技术。
机械加工中的刀具磨损分析与优化
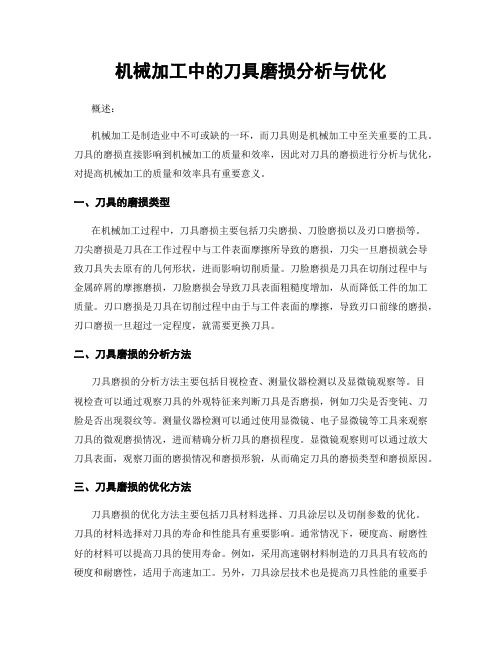
机械加工中的刀具磨损分析与优化概述:机械加工是制造业中不可或缺的一环,而刀具则是机械加工中至关重要的工具。
刀具的磨损直接影响到机械加工的质量和效率,因此对刀具的磨损进行分析与优化,对提高机械加工的质量和效率具有重要意义。
一、刀具的磨损类型在机械加工过程中,刀具磨损主要包括刀尖磨损、刀脸磨损以及刃口磨损等。
刀尖磨损是刀具在工作过程中与工件表面摩擦所导致的磨损,刀尖一旦磨损就会导致刀具失去原有的几何形状,进而影响切削质量。
刀脸磨损是刀具在切削过程中与金属碎屑的摩擦磨损,刀脸磨损会导致刀具表面粗糙度增加,从而降低工件的加工质量。
刃口磨损是刀具在切削过程中由于与工件表面的摩擦,导致刃口前缘的磨损,刃口磨损一旦超过一定程度,就需要更换刀具。
二、刀具磨损的分析方法刀具磨损的分析方法主要包括目视检查、测量仪器检测以及显微镜观察等。
目视检查可以通过观察刀具的外观特征来判断刀具是否磨损,例如刀尖是否变钝、刀脸是否出现裂纹等。
测量仪器检测可以通过使用显微镜、电子显微镜等工具来观察刀具的微观磨损情况,进而精确分析刀具的磨损程度。
显微镜观察则可以通过放大刀具表面,观察刀面的磨损情况和磨损形貌,从而确定刀具的磨损类型和磨损原因。
三、刀具磨损的优化方法刀具磨损的优化方法主要包括刀具材料选择、刀具涂层以及切削参数的优化。
刀具的材料选择对刀具的寿命和性能具有重要影响。
通常情况下,硬度高、耐磨性好的材料可以提高刀具的使用寿命。
例如,采用高速钢材料制造的刀具具有较高的硬度和耐磨性,适用于高速加工。
另外,刀具涂层技术也是提高刀具性能的重要手段。
通过在刀具表面涂覆一层超硬材料或具有特殊功能的涂层,可以显著提高刀具的耐磨性和切削性能。
此外,切削参数的优化也是降低刀具磨损的重要方法。
合理选择切削速度、进给量和切削深度等参数,可以减少刀具磨损,提高刀具的寿命。
四、冷却润滑剂在刀具磨损中的应用冷却润滑剂在减少刀具磨损方面起到了重要作用。
冷却润滑剂可以减少刀具与工件之间的摩擦,降低刀具的磨损速度。
刀具的刃磨技巧
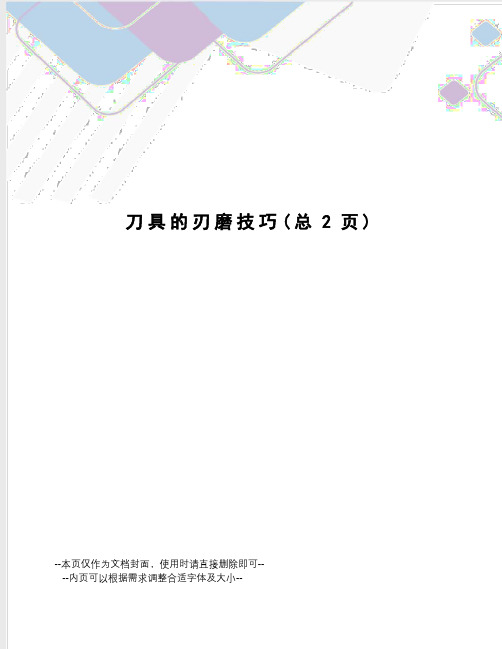
刀具的刃磨技巧(总2页)--本页仅作为文档封面,使用时请直接删除即可----内页可以根据需求调整合适字体及大小--1、砂轮的选用:(1)、氧化铝砂轮:呈白色,其砂粒韧性好,比较锋利,但硬度稍低,适用于刃磨高速钢与硬质合金的刀杆部分。
氧化铝砂轮也叫刚玉。
(2)、碳化硅砂轮:呈绿色,其砂粒硬度高,切削性能好,但较脆,适用于刃磨硬质合金车刀。
砂轮的粗细以粒度表示,粗磨时用粗粒度,精磨时用细粒度。
2、车刀的刃磨的方法和步骤:(1)、先磨去前面、后面上的焊渣,并将车刀底面磨平,可用粒度号为24-36号的氧化铝砂轮。
(2)、粗磨主后面和副后面的刀柄部分:刃磨时,在砂轮的外圆柱略高于砂轮中心的水平位置将车刀翘起一个比刀体上后角大20-30的角度,并作左右缓慢移动,以便刃磨刀体上的主后角和副后角。
可选粒度为24-36,硬度为中软的氧化铝砂轮。
(3)、粗磨刀体上的主后面:磨后刀面时,刀柄应与砂轮轴线保持平行,同时刀体的底平面向砂轮方向倾斜一个比主后角大20的角度。
刃磨时,先把车刀已磨好的后隙面靠在砂轮的外圆上,以接近砂轮的中心位置为刃磨的起始位置,然后使刃磨继续向砂轮靠近,并作左右缓慢移动。
当砂轮磨至刀刃处即可结束。
这样可同时磨出主偏角与主后角。
可选用36-60号的碳化硅砂轮。
(4)、粗磨刀体上的副后角:磨副后面时,刀柄尾部应向右转过一个副偏角的角度,同时车刀底平面向砂轮方向倾斜一个比副后角大20的角度,具体刃磨方法与粗磨刀体上主后面大体相同,不同的是粗磨副后面时砂轮应磨到刀尖处为止。
也可同时磨出副偏角和副后角。
(5)、粗磨前面:以砂轮的端面粗磨出车刀的前面,并在磨前面的同时磨出前角。
(6)、磨断屑槽:断屑槽有两种,一种是直线型,适用于切削较硬的材料;一种是圆弧型,适用于较软的材料。
手工刃磨的断屑槽一般为圆弧型,须将砂轮的外圆和端面的交角处用修砂轮的金刚石笔修磨成相应的圆弧。
若刃磨出直线型断屑槽,则砂轮的交角须修磨得很尖锐。
试论车床类刀具重磨与断屑槽调整的技术含量与推广建议

移 ,对 直 线 型 断 屑槽 而 言 ,则槽 底 角加 大 ,均 起 卷
2 .可转 位 断屑 槽 的大批 量 生产特 性
车床类 刀 具 断 屑槽 一 经 制 造 便 被 固定 下来 。 由于刃 口强 度 的 限制 ,其 深 度 不可 能 太 大 ,一 般
槽深约为槽 宽 的 1 / 1 0左 右 … , 因 此 控 制 卷 屑 的 能
可靠断屑 。 国标 ( G B 2 0 7 6 —8 7 )所 推 荐 的 2 3种 槽 形 , 以及 1 9 8 8年 以来 ,在 技术 引 进 ( 包 括模 具 进 口)
的基础上 新 开发 的 一批 新槽 形 ,大都 是 在计 算 机 辅助设计 、辅助 制 造技 术 新技 术支 撑 下 开发 出来
以 A形 断 屑槽 为例 ,其 槽底 起 主要 作 用 ,其 后壁 为避 免切 屑碰 上时产 生 过大 的冲击 而引起 系
度 ( 平 行式 )
= 4~ 4 . 5 m m,如减少 0 . 8~1 m m,
则切深需 减 少 1 m m,进 给 量 需 减 少 0 . 1 m m;如 切
削合金结构钢与工具钢 时 ,卷屑槽 宽度 ( 平 行式 )
P r o t 。 & T e c I 吲 鲺 拽
在切屑形状 与 控制 理 论所 推 荐 的 车床 类 刀具 刀头切 削部分 卷 屑槽 参数 ( 主剖 面形 状 、与 主 刀 刃之间的倾斜 角 以及 卷 屑槽 宽 度 ) 中 ,只有卷 屑
刀具刃磨技术的优化与改进

刀具刃磨技术的优化与改进篇一:刀具刃磨技术的优化与改进一、前言刀具是工业生产中不可或缺的设备,其质量和寿命对于生产效率与成本控制有着重要的影响。
随着科技的不断发展,钻头、铣刀等刀具的加工工艺日趋完善,但其刃磨技术的优化与改进也是一个持久的问题。
本文将从几个方面探讨如何优化和改进刀具的刃磨工艺,以提高其寿命和效率。
二、工艺流程的优化与改进1.精密测量:在对刀具进行刃磨前,先对其进行精密测量。
精密测量可以帮助确定刀具的实际缺口深度和切削角度,以及检测磨削后的刀具是否符合规范。
2.精细磨削:在刀具磨削时,必须确保刃口具有良好的表面粗糙度和边界质量。
因此,必须控制磨削压力、速度和润滑条件等因素,使用高精度的磨削工具和切削液,以避免刀具磨削时的微细瑕疵与划痕。
3.热成像技术:利用热成像技术监测刀具的温度,根据所得数据来调整磨削条件。
这种技术可以防止刀具因高温而产生软化、退火等影响刃口质量的情况发生。
三、配备现代化刀具刃磨设备现代化刀具刃磨设备不仅可以增加工作人员的安全系数,而且还可大幅提高刃磨精度。
现代化刀具刃磨设备主要包括CNC刀具磨床和自动化磨削线两种类型。
C刀具磨床:使用CNC刀具磨床会大大提高工作效率。
利用CNC技术,可以控制刃口的磨削过程,并轻松实现各种磨削角的精度控制。
采用这种技术的磨床通常被广泛应用于生产中大批量的刀具。
2.自动化切削线:将刀具磨削和其他工艺流程以及洁净化管理整合在一起,从而形成自动化切削线。
自动化切削线主要用于生产高效率和环保型的刀具。
四、展望刀具刃磨技术的优化与改进,有利于提高刀具使用寿命和效率,减少生产成本,从而推动制造业的可持续发展。
现代化的刃磨工艺和设备将会形成新一代的刀具刃磨技术,为工业进步做出巨大的贡献。
未来,刀具刃磨技术发展方向将会更注重绿色环保和智能化生产的方向。
刀具修磨方案

刀具修磨方案1. 引言刀具修磨是生产制造过程中不可缺少的一环。
随着刀具的使用和磨损,刀具的切削性能和精度会逐渐下降,因此定期对刀具进行修磨是必要的。
本文将介绍一套刀具修磨方案,旨在提高刀具的使用寿命和切削质量。
2. 刀具修磨的重要性刀具修磨的主要目的是恢复刀具的切削性能和精度,延长刀具的使用寿命。
刀具在使用过程中会受到磨损和热膨胀等因素的影响,导致刀具的切削效果下降,工件加工质量下降。
通过定期修磨刀具,可以恢复切削刃的锋利度,提高切削效率,降低生产成本。
3. 刀具修磨的步骤3.1 检查刀具磨损情况在修磨刀具之前,首先需要仔细检查刀具的磨损情况。
常见的刀具磨损形式包括刀口磨损、刀片磨损、刀片边缘磨损等。
通过观察磨损情况,可以确定刀具的修磨方向和修磨量。
3.2 备料准备修磨刀具之前,需要做好备料准备。
备料包括砂轮、修磨液和其他辅助工具等。
根据刀具的材质和磨损情况,选择合适的砂轮和修磨液,确保修磨效果。
3.3 修磨刀具修磨刀具是刀具修磨的核心步骤。
根据磨损情况,选择合适的修磨方式和工艺参数。
常见的修磨方式包括平面修磨、外围修磨、内圆修磨等。
根据刀具的材质和几何形状,选择合适的修磨工艺参数,如修磨速度、进给速度、修磨深度等。
3.4 检验修磨效果修磨刀具之后,需要对修磨后的刀具进行检验,确保修磨效果和修磨质量。
常见的检验方法包括目测检查、手感检查和精度测试等。
通过检验,可以判断修磨是否达到预期效果,如果有问题可以及时调整。
4. 刀具修磨注意事项4.1 安全操作修磨刀具是一个细致的工作,需要注意安全操作。
在修磨过程中,要戴好防护眼镜、口罩和手套,防止刀具碎屑对人身安全产生威胁。
同时,要熟悉修磨设备的操作规程,确保安全操作。
4.2 刀具磨损规律刀具的磨损规律是刀具修磨的重要参考依据。
不同刀具在使用过程中,磨损的位置和程度会有所不同。
了解刀具的磨损规律,可以判断刀具的修磨方向和修磨量。
4.3 修磨工艺参数选择修磨工艺参数对修磨效果和刀具寿命影响很大。
重视刀具重磨技术 降低加工成本
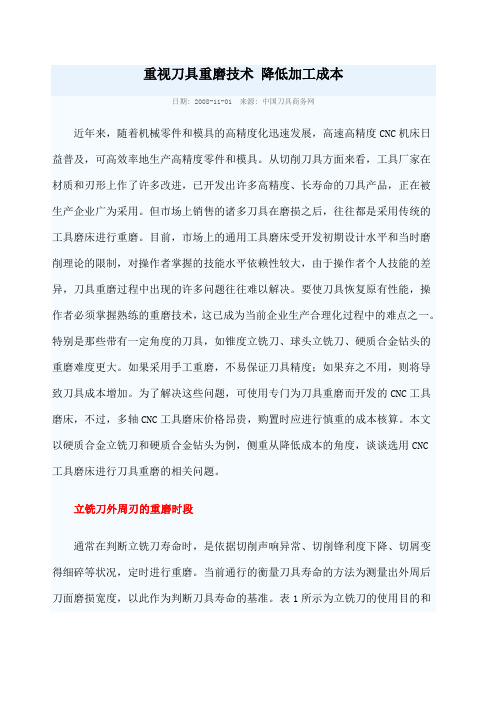
重视刀具重磨技术降低加工成本日期: 2008-11-01 来源: 中国刀具商务网近年来,随着机械零件和模具的高精度化迅速发展,高速高精度CNC机床日益普及,可高效率地生产高精度零件和模具。
从切削刀具方面来看,工具厂家在材质和刃形上作了许多改进,已开发出许多高精度、长寿命的刀具产品,正在被生产企业广为采用。
但市场上销售的诸多刀具在磨损之后,往往都是采用传统的工具磨床进行重磨。
目前,市场上的通用工具磨床受开发初期设计水平和当时磨削理论的限制,对操作者掌握的技能水平依赖性较大,由于操作者个人技能的差异,刀具重磨过程中出现的许多问题往往难以解决。
要使刀具恢复原有性能,操作者必须掌握熟练的重磨技术,这已成为当前企业生产合理化过程中的难点之一。
特别是那些带有一定角度的刀具,如锥度立铣刀、球头立铣刀、硬质合金钻头的重磨难度更大。
如果采用手工重磨,不易保证刀具精度;如果弃之不用,则将导致刀具成本增加。
为了解决这些问题,可使用专门为刀具重磨而开发的CNC工具磨床,不过,多轴CNC工具磨床价格昂贵,购置时应进行慎重的成本核算。
本文以硬质合金立铣刀和硬质合金钻头为例,侧重从降低成本的角度,谈谈选用CNC 工具磨床进行刀具重磨的相关问题。
立铣刀外周刃的重磨时段通常在判断立铣刀寿命时,是依据切削声响异常、切削锋利度下降、切屑变得细碎等状况,定时进行重磨。
当前通行的衡量刀具寿命的方法为测量出外周后刀面磨损宽度,以此作为判断刀具寿命的基准。
表1所示为立铣刀的使用目的和需进行重磨时的最大后面磨损宽度,超过表中所列磨损值,则会出现急剧磨损,这将缩短刀具寿命。
表1 立铣刀外周刀刃后面磨损宽度加工类别-立铣刀直径-后面磨损宽度-被加工材料粗加工-10mm以下-0.1~0.2mm-钢、铸铁粗加工-11~30mm-0.2~0.4mm-钢、铸铁粗加工-30mm以上-0.3~0.5mm-钢、铸铁精加工-10mm以下-0.1~0.15mm-钢、铸铁精加工-11~30mm-0.15~0.25mm-钢、铸铁精加工-30mm以上-0.2~0.3mm-钢、铸铁为了充分发挥立铣刀的切削性能,应使切削刃经常保持最佳状态,为此应及时进行重磨,避免刀具出现损伤,使刀具始终保持良好的切削性能,获得较高的使用寿命。
数控加工技术专业学习中的刀具磨削与磨削机械操作技巧

数控加工技术专业学习中的刀具磨削与磨削机械操作技巧数控加工技术是现代制造业中的重要一环,而刀具磨削与磨削机械操作技巧则是数控加工技术专业学习中的重要内容。
刀具磨削的质量直接影响到数控加工的效率和精度,因此掌握磨削技巧对于数控加工技术专业的学生来说至关重要。
刀具磨削是通过磨削机械对刀具进行修整和修复,使其恢复到最佳工作状态。
在进行刀具磨削之前,首先需要了解刀具的结构和磨削原理。
刀具通常由刀柄和刀片组成,刀片是切削加工的主要部分。
切削刃的形状和尺寸决定了切削加工的效果,而刀片的磨削和修整则是保证刀具性能的关键。
在进行刀具磨削时,需要选择合适的磨削机械和磨削工具。
常见的磨削机械有平面磨床、外圆磨床和内圆磨床等。
不同的刀具需要使用不同的磨削工具,如平面刀具可以使用平面磨床进行磨削,而圆柱刀具则需要使用外圆磨床进行磨削。
在选择磨削工具时,需要考虑刀具的材料、形状和尺寸等因素,以及磨削的要求和精度。
刀具磨削的过程可以分为粗磨和精磨两个阶段。
粗磨是将刀具的切削刃修整到大致的形状和尺寸,而精磨则是将刀具的切削刃磨削到最终的形状和尺寸。
在进行刀具磨削时,需要掌握正确的操作技巧和注意事项。
首先,要保证磨削机械的稳定性和精度,避免因机械问题导致刀具磨削不准确。
其次,要掌握磨削工具的使用方法和磨削参数,如切削速度、进给量和磨削深度等。
最后,要注意刀具的冷却和润滑,以避免因高温和摩擦引起的刀具损坏和磨削不良。
刀具磨削的质量不仅取决于磨削技巧,还与刀具的使用和保养有关。
在使用刀具时,要注意避免过度切削和碰撞,以防止刀具的损坏和磨损。
同时,要定期对刀具进行检查和保养,如清洁切削刃上的切屑和涂抹切削液等。
对于损坏或磨损严重的刀具,需要及时进行修复或更换,以保证加工的质量和效率。
总之,刀具磨削与磨削机械操作技巧是数控加工技术专业学习中的重要内容。
掌握刀具磨削的原理和技巧,选择合适的磨削机械和磨削工具,正确操作和保养刀具,都是提高数控加工技术水平的关键。
机械加工中刀具磨损机理与修复技术研究

机械加工中刀具磨损机理与修复技术研究机械加工是现代制造业中不可或缺的环节,而刀具作为机械加工中最为重要和常用的工具之一,其磨损问题一直以来都是制约机械加工质量和效率的主要因素之一。
因此,研究刀具磨损机理以及开发有效的修复技术具有重要意义。
本文将探讨机械加工中刀具磨损机理与修复技术的研究进展。
1. 刀具磨损机理刀具磨损机理是研究的基础,它关系到刀具的工作性能和使用寿命。
刀具磨损主要分为刀尖磨损、切削刃磨损和刀具侧面磨损三个方面。
一方面,刀尖磨损主要由于在切削过程中与工件直接接触,受到工件材料的冲击和剪切力,从而导致刀尖磨损,影响了切削质量和加工精度。
另一方面,切削刃磨损是指刀具切削刃齿面的磨损现象。
在机械加工中,切削刃磨损不可避免地发生,特别是在高速切削和重负荷切削情况下,切削刃的磨损会严重影响刀具的切削性能和使用寿命。
最后,刀具侧面磨损是指刀具侧面与工件相互摩擦产生的磨损现象。
刀具侧面磨损对加工表面的粗糙度和加工精度影响较大,因此,研究刀具侧面磨损机理并开发相应的修复技术具有重要意义。
2. 刀具磨损修复技术刀具磨损修复技术是解决刀具磨损问题的重要方法。
传统的刀具磨损修复技术主要包括机械磨损修复、化学磨损修复和热处理修复等几种。
这些技术虽然能够修复刀具的一些磨损问题,但是存在一些缺点,如修复效果不稳定、加工精度难以保证等。
近年来,随着纳米科技和材料科学的飞速发展,一些新型的刀具磨损修复技术被提出和研究。
例如,利用纳米材料对刀具进行表面涂覆,形成硬质薄膜,能够有效减少刀具的磨损,提高刀具的使用寿命。
同时,通过利用纳米颗粒对刀具进行纳米复合修复,可以修复刀具表面的微小划伤和磨损,提高刀具的切削性能和加工质量。
此外,利用激光技术对刀具进行修复也是一种新的研究方向。
激光修复技术能够精确控制激光加热过程,使得刀具表面受热均匀,通过熔化和凝固过程来修复刀具的磨损问题。
激光修复技术具有高精度、高效率和环保的特点,对于刀具磨损的修复具有广阔的应用前景。
成形加工机械中的刀具磨粒磨损分析与控制技术

成形加工机械中的刀具磨粒磨损分析与控制技术概述成形加工机械是现代制造业中非常重要的一种设备,它可以通过切削、磨削等方式对工件进行加工。
而刀具作为成形加工机械的核心部件,其磨粒磨损对机械加工质量和效率具有重要影响。
本文将对成形加工机械中的刀具磨粒磨损进行详细分析,并介绍相应的控制技术。
一、刀具磨粒磨损的原因刀具在使用过程中会因为工件材料的磨削、加工过程中的摩擦磨损以及其他因素的作用而产生磨粒磨损。
主要原因包括以下几点:1. 工件材料的磨削:当刀具与工件接触时,由于材料之间的摩擦力,会引起工件材料的磨屑产生。
而这些磨屑会附着在刀具表面,导致刀具的磨粒磨损。
2. 加工过程中的摩擦磨损:成形加工机械在运转时,刀具与工件之间会产生较大的摩擦力。
由于摩擦力过大,会导致刀具的表面磨损,进而产生磨粒磨损。
3. 其他因素的作用:包括刀具的材料选择、刀具的设计缺陷、切削参数的选择等因素都可能影响刀具的磨损情况。
二、刀具磨粒磨损的影响刀具的磨粒磨损会对成形加工机械的加工质量和效率产生重要影响。
具体表现在以下几个方面:1. 加工质量下降:当刀具发生磨粒磨损时,其切削能力和加工稳定性会大大降低,从而会导致加工质量下降,出现毛刺、表面粗糙等问题。
2. 加工效率降低:刀具磨粒磨损会增加切削力和切削温度,降低切削速度和进给速度,进而导致加工效率的降低。
3. 刀具寿命缩短:刀具的磨粒磨损会导致刀具的尺寸、几何形状和表面质量的变化,进而影响刀具的使用寿命。
三、刀具磨粒磨损的分析针对刀具磨粒磨损的问题,可以采用以下几种方法进行分析:1. 切削力和切削温度测量:通过测量刀具的切削力和切削温度,可以对刀具的磨粒磨损进行初步分析。
切削力和切削温度的增加通常与刀具的磨粒磨损密切相关。
2. 组织结构观察:通过对刀具的磨粒磨损刀具进行显微组织观察,可以了解磨粒磨损的程度和磨粒的类型。
不同类型的磨粒磨损表现出不同的组织特征,这可以为进一步分析磨损机理提供依据。
成形加工机械中的刀具刃部磨损分析与控制

成形加工机械中的刀具刃部磨损分析与控制随着加工技术的不断发展,各类成形加工机械在工业生产中得到了广泛应用。
在这些机械中,刀具是执行加工操作的重要工具。
然而,由于长时间的使用和材料性能的限制,刀具刃部会经历磨损现象,导致切削性能下降,甚至无法继续使用。
因此,对成形加工机械中刀具刃部磨损进行分析和控制是提高加工效率和质量的重要一环。
首先,我们需要分析成形加工机械中刀具刃部磨损的原因。
磨损主要分为两种类型,即切削磨损和切削热疲劳磨损。
切削磨损是由于材料与刀具相互作用产生的摩擦所引起的,而切削热疲劳磨损则是由于切削过程中的高温引起的刀具材料的热胀冷缩而引起的。
此外,切削力、切削速度、切削液的使用与否以及刀具的形状等因素也会对刀具刃部磨损造成影响。
为了减少刀具刃部的磨损,我们可以采取一些控制措施。
首先,选择合适的刀具材料非常重要。
目前市场上常见的刀具材料包括硬质合金、陶瓷、高速钢等。
不同材料具有不同的特性,应根据具体的加工要求选择合适的刀具材料。
其次,合理选择刀具的形状和尺寸。
刀具的形状和尺寸直接影响到切削效果和磨损情况,应根据加工要求选择合适的刀具。
另外,切削力和切削速度也是影响刀具磨损的重要因素。
合理选择切削力和切削速度,可以减少刀具的磨损,延长使用寿命。
最后,切削液的使用也是减少刀具的磨损的一种常用措施。
切削液可以起到冷却刀具和工件、减少切削热的作用,从而减少刀具的磨损。
除了控制措施,我们还可以通过监测磨损情况来及时采取措施进行刀具维护和更换。
常见的磨损监测手段包括视觉检查、量具测量和图像分析等。
视觉检查是一种简便直观的方法,通过观察刀具刃部是否存在齿翼磨损、切屑的颜色和形态等来判断刀具的磨损情况。
量具测量主要是通过测量刃部的长度和宽度来判断是否需要更换刀具。
图像分析则是运用计算机图像处理技术对刀具刃部进行分析和测量,可以提供更加准确的磨损情况。
综上所述,成形加工机械中的刀具刃部磨损分析与控制对于提高加工效率和质量至关重要。
常用刀具刃磨理论和技术

[独门秘笈]怎样磨刀才锋利——常用刀具刃磨理论和技术之一怎样磨刀才锋利?仁者见仁,智者见智,网上流传的经验和方法很多,也很有效。
本文从理论分析出发,试图发掘常用刀具的刃磨技术基本原理,并在此基础上提出新的刃磨方法和技巧以歆读者。
(文中锋利性的比较,建立在相同刃磨技术水平之上)本文内容仅代表个人浅见,鄙薄和错漏之处在所难免,敬请见谅并斧正。
一、什么样的刀刃才锋利?常用刀具的锋利性检测,目前尚没有统一的行业标准,通常根据刀具在推纸、剃毛和断发等方面的具体表现判定。
而从刀刃的结构特征分析,刀刃的锋利性主要取决于以下五个重要因素。
1.刃角刃角越小,刃部越尖,切入阻力也越小,锋利性也越高,它是影响锋利性的重要因素。
2.刃口半径刃口半径越小,切入压力也就越小,自然也越锋利,这是使刀具锋利的最关键要素。
3.刃纹刃纹方向与切割方向相同时,更容易切入,也更锋利,各刃纹相互平行且与刃口垂直(纵刃纹)时最佳.刃纹在刃缘处产生的微锯齿,也有利于提高锋利性。
4.毛边毛边会大大增加刀刃的切入阻力,是影响锋利性的重要因素,锋利的刀刃应该没有毛边。
5.微锯齿严格的说,刃缘都是有微锯齿的,齿向与切割方向一致时,切入压力越小,刀刃也越锋利。
二、刀具与锋利性的关系同一把刀,同样的刃磨方法,为什么小角度刃磨要锋利得多?(仅仅从“劈”的力学关系是根本无法解释的)同样的刃磨方法,相同的刃磨角度,同样的材料和热处理,为什么不同形状的刀具锋利性相差甚远?为什么不锈钢刀具相对更难磨?为什么手的定位误差最少也有几毫米,而磨出的刃口却可薄至数微米?为寻找上述问题的答案,请关注以下分析。
1.怎样才能使刃口半径最小?决定锋利性的五个主要因素中,刃角是事先确定的,微锯齿主要与材质有关,清理毛边属于后期处理,因此,磨刀时需要着重解决尽可能减少刃口半径和产生纵刃纹这两个问题。
要获得尽可能小的刃口半径,关键是要设法尽量延后刀刃卷口(因为一旦卷口就会产生毛边,继续磨削只会使毛边扩大,很难使刃口半径进一步减小)的时机,为此必须做到如下两点.⑴局部微力切削各油石颗粒必须以很小的力度切削刀刃,才能防止提前卷口。
任务一 成形刀具刃磨
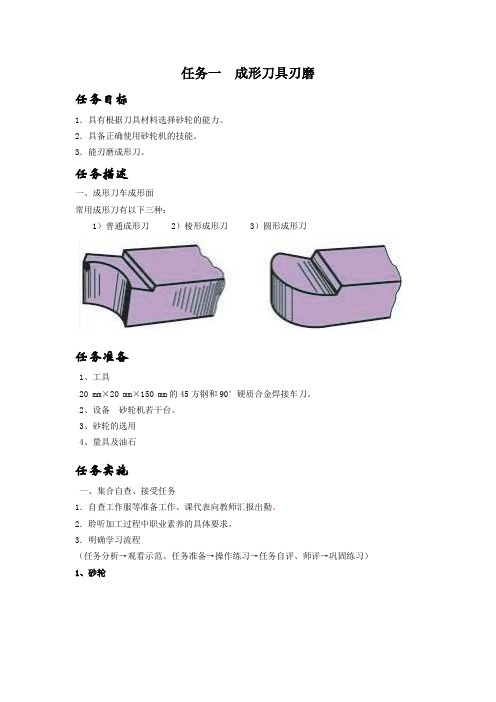
任务一成形刀具刃磨任务目标1.具有根据刀具材料选择砂轮的能力。
2.具备正确使用砂轮机的技能。
3.能刃磨成形刀。
任务描述一、成形刀车成形面常用成形刀有以下三种:1)普通成形刀 2)棱形成形刀 3)圆形成形刀任务准备1、工具20 mm×20 mm×150 mm的45方钢和90°硬质合金焊接车刀。
2、设备砂轮机若干台。
3、砂轮的选用4、量具及油石任务实施一、集合自查、接受任务1.自查工作服等准备工作、课代表向教师汇报出勤。
2.聆听加工过程中职业素养的具体要求。
3.明确学习流程(任务分析→观看示范、任务准备→操作练习→任务自评、师评→巩固练习)1、砂轮砂轮的种类和颜色和适用场合砂轮种类颜色适用场合氧化铝白色刃磨高速钢刀具和硬质合金车刀的刀柄部分碳化硅绿色刃磨硬质合金刀具的硬质合金部分2、砂轮机操作提示1)新安装的砂轮必须严格检查。
在使用前要检查外表有无裂纹,可用硬木轻敲砂轮,检查其声音是否清脆。
如果有碎裂声必须重新更换砂轮。
2)在试转合格后才能使用。
新砂轮安装完毕,先点动或低速试转,若无明显振动,再改用正常转速,空转10min,情况正常后才能使用。
3)安装后必须保证装夹牢靠,运转平稳。
砂轮机启动后,应在砂轮旋转平稳后再进行刃磨。
4)砂轮旋转速度应略小于允许的线速度,速度过高会爆裂伤人,过低又会影响刃磨质量。
5)若砂轮跳动明显,应及时修整。
平形砂轮一般可用砂轮刀在砂轮上来回修整,杯形细粒度砂轮可用金刚石笔或硬砂条修整。
6)刃磨结束后,应随手关闭砂轮机电源。
修正砂轮整形器3、刃磨姿势与方法1)刃磨车刀时,操作者应站立在砂轮机的侧面,双手握车刀,两肘应夹紧腰部,这样可以减小刃磨时的抖动。
2)刃磨时,车刀应放在砂轮的水平中心,刀尖略微上翘3°~8°,车刀接触砂轮后应作左右方向水平移动;车刀离开砂轮时,刀尖需向上抬起,以免砂轮碰伤已磨好的切削刃。
4、车刀刃磨技术1、前角的功用及刃磨1)前角在切削加工中的作用;2)前角的刃磨;3)刃磨前角时的前角值;2、车刀后角的功用及其刃磨3、车刀刃倾角的功用及其刃磨1)粗车时应刃磨负倾角;2)车削不规则或断续表面时应磨负倾角;3)精车时应磨正倾角;4)刃倾角磨制为零度的刀具;5)从操作者人身安全角度出发刃磨刃倾角;6)其他刀具刃倾角的刃磨;粗磨完毕后进行精磨,以减小各刀面和切削刃的表面粗糙度,并使几何角度符合要求。
刀具磨削技术的研究与优化

刀具磨削技术的研究与优化刀具磨削技术是切削加工的重要手段之一。
它的发展历程与数控技术的发展有着密不可分的关系。
随着制造业的不断发展,刀具磨削技术也得到了越来越广泛的应用。
刀具磨削技术的研究和优化已成为磨削技术领域的重要研究方向。
一、刀具磨削技术的研究趋势刀具磨削技术是很多行业制造工艺的重要环节,如航空工业、汽车工业、机床制造等。
随着磨削技术的不断发展,越来越多的刀具磨削技术被应用到了实际生产中。
刀具磨削技术的研究趋势主要包括以下几个方面:1、高效、高质量、低成本的刀具磨削技术研究。
刀具磨削技术的发展方向是高效化、智能化。
在高效性方面,除了磨削技术本身的效率提升外,适应性、通用性也越来越强。
在质量方面,磨削技术也应有相应改进。
低成本是磨削技术研究的另一 focuses。
2、刀具材料的研发。
随着材料科学的不断进步,出现了越来越多的新材料,如陶瓷材料、超硬合金材料等,这些材料的出现为刀具磨削技术提供了更广阔的发展空间。
刀具磨削技术研究的另外一个方向,就是开发能够适应新型材料的磨削技术。
3、数控刀具磨削技术的发展。
数控刀具磨削技术作为现代磨削技术的重要代表,以其高效、精度高、自动化程度高等优点受到了企业和科研人员的青睐。
未来,基于数控技术的刀具磨削技术将日益成熟和广泛应用。
二、刀具磨削技术的优化方向刀具磨削技术的优化工作需要从以下三个方面入手:1、工作质量的提高。
这是磨削技术优化的重点内容之一。
工作质量的提高需要依据工艺参数和刀具结构进行分析,对研磨机结构及各工作部件进行优化设计,同时研究刀具刃口的几何形状和磨削顺序等技术,提高工作效率和质量。
2、成本的优化。
磨削技术的优化在成本方面也具有重大意义。
材料的选择、耗损程度和研磨动力的选择对磨削成本的影响十分重要。
是要通过技术的优化来保证磨削成本可控。
3、制定良好的研磨规范。
研磨规范是刀具磨削技术研究的关键所在,包括刀具磨削的工艺流程和技术标准,以及适当的管理与控制措施,只要遵守研磨规范,就能获得更高质量的研磨产品。
- 1、下载文档前请自行甄别文档内容的完整性,平台不提供额外的编辑、内容补充、找答案等附加服务。
- 2、"仅部分预览"的文档,不可在线预览部分如存在完整性等问题,可反馈申请退款(可完整预览的文档不适用该条件!)。
- 3、如文档侵犯您的权益,请联系客服反馈,我们会尽快为您处理(人工客服工作时间:9:00-18:30)。
件加工需求 , 提高刀具使用寿 命 。例 如 , 在 加工 某 环 形 零件 图 1环 槽局 部放 大 图 环槽工序 时 , ( 环 槽 局 部 放 大 按 要求 划线 后 , 向 切削 刃逆 向磨 削到 划线 图见 图 1 ) ,零 件 待 加 工 部 分 由槽 宽 处 然后 再把 负 刃逐 渐磨 削 掉 , 这样 砂 轮磨 4 . 9 2 7 6 ± O . 0 2 5 4 、 1 4 . 5 。 ± 1 两 度 面 、 底 部 削 振 动 时减 少 切 削 刃 缺 口避 免裂 纹 缺 口 R1 . 0 7  ̄ 0 . 1 2 两 处 圆弧 型 组成 的环 形槽 , 圆 处 裂开 。粗 磨 后精 加工 第 二 步 , 选 用 金 刚 周 尺 寸为 1 3 3 6 m m, 零 件 加 工后 环 槽 最 厚 石砂 轮 1 0 0 粒精 磨 刀头前 角 。 第 三 步加 工 部 分为 1 . 7  ̄ 0 . 0 5 m m , 1 件需 加工 4 个环。 侧 角度 面 3 O 。 ,磨 削 时砂 轮横 向进 给 量要 利 用成 型 车 刀进 行度 面 、 R部分 成 型 精 车 小 , 避免 出现 锯齿 型 。 第 四步保 证 3 0 。 面 与 加工 , 以保 证 零 件 尺 寸 , 特 别 是保 证 相 关 R 0 . 9 1 平 行 方 向落 差 0 . 5 m m, 投影 2 O 倍 检 尺 寸一 次加 工 合格 。因加 工 条件 决 定 , 刀 查 。第五步完成 1 4 。 3 O 与R 0 . 9 1 相切 , 磨 具在进刀 、 切 削 过 程 中 磨损 严 重 , 同 时伴 削 时 采 用 梯 形 进 给 分 段 加 工 才 能 使 随打刀 、 勒 刀等 现 象 。这要 对 使用 后 可 修 1 . 3 2 a r m宽处 不易 断裂 。 第 六步 加工 R 0 . 9 1 磨 的成 形 刀具进 行 重磨 , 对 于 此类 专 用 型 可 用手 工技 巧旋 转 磨削 R 0 . 9 1 , 投影 2 0 倍 面 车刀 的重 磨来 讲 , 重 磨技 术 可 以说 是用 检 查 完 成 ,此 项 加 工 方 法 为 手动 磨 削 过 精研 和 熟练 技巧 来保 证 的 , 因硬质 合 金 刀 程 , 需 要 多年 实践加 工经 验 。另外 , 因刀具 头 的 标 准形 状 不 能 满 足 形 状 各 异 的 专用 型 面复 杂 , 也 可 利用 手动 光学 磨 和 R磨 刀 车刀, 这 样有 些 不符 合 标 准形 状 的硬 质合 ห้องสมุดไป่ตู้ 等高 精度 机 床进 行加 工 , 通 过对 不 同 型 金刀头余量过大给刃磨加工增加难度 , 专 面 的研 究 , 摸索 更加 先 进 的加 工方 法 以解 用 环形 车 刀 要 求 车刀 头 R 0 . 9 1 a r m 与 内斜 决所 有刀 具刃 磨 的技术 瓶颈 。 边 1 4 。 3 0 度 面相 切 ,一 边 3 0 。 度 面 在 6刀具 修磨 后检 验 R 0 . 9 1 a r m底 部相 连 , 形 状 就像 一把 刀 尖 上 刀具修磨后要对刀具进行检验 , 以保
工 业 技 术
2 01 3 N0. O 2 Ch i n a Ne w T e c h n o l o g i e s a n d Pr o d u c t s
浅谈专用成形 刀具重磨 技术
马金龙 傅丽红 郎 辉 ( 沈阳黎明航 空发动机 ( 集 团) 有 限责任公 司, 辽 宁 沈阳 1 1 0 0 4 3 )
须 进行 重磨 。 5 专用成 型 车刀 的磨削 专 用 成 型 车 刀 俗 称 样 板
车刀 , 其加工零件 的轮廓形状 完 全 由车 刀刀 刃 的 形 状 和 尺
寸决 定 , 对刀 具 的机 械 加 工性 能提 出 了更 高 的要 求 , 重 磨 刀 具 可 消 除 一部 分 切 削 刃 表 面 的微 崩 刃 、刃 区 微 裂 纹 等 缺 陷, 同时通过有效 、 准 确 的重 磨 可 以修 正 刀具 尺 寸 , 达 到零
1 概 述
度 ,不 仅 降低 加 工 质 量 ,严 重 时 还 会 影 响 加工 系统 的安 全和 正常 运行 。 如 果将 磨 损后的刀具废弃 , 会造成大量的浪费及大 量 增加 制 造成 本 , 从刀 具 的磨 损形 式 人 手 分 析 ,区分切 削刀 具 的可 再制 造性 , 将 可 再 制 造 的刀 具 按 照形 状 、 型号 、 材 料 进 行 初 步分 类 , 以确定 其适 用 重磨 方案 ,经 过 刀 具 的特 定部 位 的粗磨 、 精 磨 以及刃 口的 强 化处 理后 就完成 重 磨过 程 。 2 刀具磨 损 的形式 刀 具 在 切 削 过 程 中会 发 现 一 系 列 的 物 理反 应 ,主 要表 现 有刀 刃 的 塑性 变形 、 表面粘合与摩擦 等。表现形式有以下几 种: ( 1 ) 刀具 磨 损 后 , 刀尖 圆弧 半 径 增 大 , 使 刀具 与 工件 间摩 擦加 剧 , 前 刀 面严 重磨 损 ,后 角几 乎 为 零 ,后 刀 面 与 工 件 接触 面 积增 大 ,从而使机 床切削功率 增大 。 ( 2 ) 刀 具 在 切 削 不 连续 时 , 切 削 刃 会 产 生 崩刃, 损伤 部位 多 发生 在 切 削刃 与工 件 表 面 接 触 区 域 ,刀 刃 将 丧 失 了 应 有 的完 整 性。 如果继续使用 ,崩刃处将留有未切削 区域 留给剩余 刀刃切削 ,将会加剧剩余 刀 刃 的磨损 速度 。( 3 ) 刀 具前 刀面剥 落 , 刀 具 磨损 后 期 由于前 刀 面 的深 度较 大 , 实 际 切 削刃 低 于前 刀面 后部 的高度 , 前 刀 面 后 部产 生 冲击 , 发生 前刀 面剥 落 。 ( 4 ) 刀具 切 削 刃脱 落 ,磨 损 断 口面 几 乎 与 前 刀 面垂 直, 刀 具完 全丧 失 了切 削 能力 。这是 由于 刀具 前 刀 面深 度 的增加 , 是 切 削 刃强 度 减 弱 到承受 不 了切 削载荷 而产 生磨 损 。 3刀 具刃 磨与 重磨 金 属 切 削 刀 具 的 刃 磨 既 是 刀 具制 造 中的最后 一 道工 序, 也 是刀 具重 磨最 重 要 的工 序 。 刀 具刃 磨决 定 了刀具切 削部 分 的 形状及其几何精度, 是保证刀具切削性能 和产 品质 量 的关键 。 刀 具 重 磨 是 对 正 常 使用 磨 损 达 到磨 钝标准的刀具进行修磨。刀具重磨是重复 利用 资 源 的有效 形式 之 一 , 对 降低 产 品制 造成本 、 延长刀具使用寿命 , 具有重要 的 意义。 4 刀具 重磨 依据 ( 1 ) 当 刀具 正 常磨 损 达 到磨 钝标 准 时 应 对刀 具进 行重 磨 ; ( 2 ) 当切 削 时 出现 声 响 异 常 、 切 削 刃
摘 要: 因零件 特种 曲 面在h a_ - r _ 中的特 殊要 求, 需用成 形刀 具进行 型 面的粗 加 工、 半精 h a_ z . 和精 h a . z _ , 本 着降低 制造 成本 的 生 产理 念, 而又要 求 生产 出 高精 度 、 高品质 的产 品, 在 粗精 h a_ z _ 时合 理使 用 刀具后 , 依 据 刀具 的使 用 情况 分析 刀具 的磨 损状 况 , 运 用成形 刀具 重磨技 术对 刀具进 行修 磨 , 既能保 证产 品质 量又 能 降低 制造 成 本 。 关键 词 : 成形 车刀 ; 重磨 ; 刃具 中 图分类 号 : T D 4 2 1 . 5 + 4 文 献标识 码 : A 锋 利度 下 降 、切 屑 变得 细 碎 、 刀 具 在 整 个 切 削 过 程 中不 可 避 免 地 发 生 振 动 等 现 象影 响 刀 具 耐 存 在着 磨 损现 象 , 刀具 切 削状 态 的变 化 导 用度 时 可对 刀具进 行重 磨 ; 致 切 削 力增 加 、 切 削 温度 升高 , 刀 具磨 损 ( 3 ) 精加 工 时 因 刀具 本 身 会 直 接 影 响 工件 的加 工 精 度 和 表 面粗 糙 的原 因达 不 到 工 艺 要 求 时 必