焊接检验标准17714
焊接质量检验标准

焊接质量检验标准焊接在电子产品装配过程中是一项很重要的技术,也是制造电子产品的重要环节之一。
它在电子产品实验、调试、生产中应用非常广泛,而且工作量相当大,焊接质量的好坏,将直接影响到产品的质量。
电子产品的故障除元器件的原因外,大多数是由于焊接质量不佳而造成的。
因此,掌握熟练的焊接操作技能对产品质量是非常有必要的。
(一)焊点的质量要求:对焊点的质量要求,应该包括电气接触良好、机械接触牢固和外表美观三个方面,保证焊点质量最关键的一点,就是必须避免虚焊。
1.可靠的电气连接焊接是电子线路从物理上实现电气连接的主要手段。
锡焊连接不是靠压力而是靠焊接过程形成牢固连接的合金层达到电气连接的目的。
如果焊锡仅仅是堆在焊件的表面或只有少部分形成合金层,也许在最初的测试和工作中不易发现焊点存在的问题,这种焊点在短期内也能通过电流,但随着条件的改变和时间的推移,接触层氧化,脱离出现了,电路产生时通时断或者干脆不工作,而这时观察焊点外表,依然连接良好,这是电子仪器使用中最头疼的问题,也是产品制造中必须十分重视的问题。
2.足够机械强度焊接不仅起到电气连接的作用,同时也是固定元器件,保证机械连接的手段。
为保证被焊件在受振动或冲击时不至脱落、松动,因此,要求焊点有足够的机械强度。
一般可采用把被焊元器件的引线端子打弯后再焊接的方法。
作为焊锡材料的铅锡合金,本身强度是比较低的,常用铅锡焊料抗拉强度约为3-4.7kg/cm 2,只有普通钢材的10%。
要想增加强度,就要有足够的连接面积。
如果是虚焊点,焊料仅仅堆在焊盘上,那就更谈不上强度了。
3.光洁整齐的外观良好的焊点要求焊料用量恰到好处,外表有金属光泽,无拉尖、桥接等现象,并且不伤及导线的绝缘层及相邻元件良好的外表是焊接质量的反映,注意:表面有金属光泽是焊接温度合适、生成合金层的标志,这不仅仅是外表美观的要求。
典型焊点的外观如图1所示,其共同特点是:① 外形以焊接导线为中心,匀称成裙形拉开。
焊接件检验标准

焊接件检验标准焊接件是工程中常见的零部件,其质量直接关系到工程的安全性和稳定性。
为了保证焊接件的质量,必须对其进行严格的检验。
本文将介绍焊接件检验的标准和方法,以期为工程施工和质量管理提供参考。
首先,焊接件的检验标准应当符合国家相关标准和规定。
在我国,焊接件的检验标准主要包括《焊接工艺评定规程》、《焊接质量等级》和《焊接工程质量验收标准》等。
这些标准和规定对焊接件的材料、工艺、质量等方面都有详细的规定,对于焊接件的检验提供了重要的参考依据。
其次,焊接件的检验应当包括外观检查、尺寸检验、材料分析和力学性能测试等内容。
外观检查主要是对焊接件的表面质量进行检查,包括焊缝的形状、焊接变形、气孔和裂纹等情况。
尺寸检验则是对焊接件的尺寸进行精确的测量,以确保其符合设计要求。
材料分析和力学性能测试则是对焊接件的材料成分和力学性能进行检验,以验证其质量和可靠性。
另外,焊接件的检验还应当根据其使用环境和作用要求进行相应的特殊检验。
例如,在高温、低温、腐蚀等特殊环境下使用的焊接件,需要进行相应的耐温、耐蚀性能测试;在受到冲击、振动等作用时需要进行冲击、振动试验等。
这些特殊的检验项目可以有效地评估焊接件在特殊环境和作用下的可靠性和安全性。
最后,焊接件的检验应当由具有相应资质和能力的检验机构进行。
检验机构应当具有国家认可的检验资质和先进的检验设备,能够对焊接件进行全面、准确的检验。
同时,检验机构应当具有丰富的检验经验和专业的检验人员,能够为焊接件的质量提供可靠的保障。
总之,焊接件的检验是确保其质量和可靠性的重要环节,应当严格按照国家相关标准和规定进行。
通过外观检查、尺寸检验、材料分析和力学性能测试等多种手段,对焊接件的质量进行全面、准确的评估。
同时,应当根据其使用环境和作用要求进行特殊检验,并由具有相应资质和能力的检验机构进行检验。
只有这样,才能保证焊接件的质量和可靠性,为工程的安全和稳定提供可靠的保障。
焊接检验标准
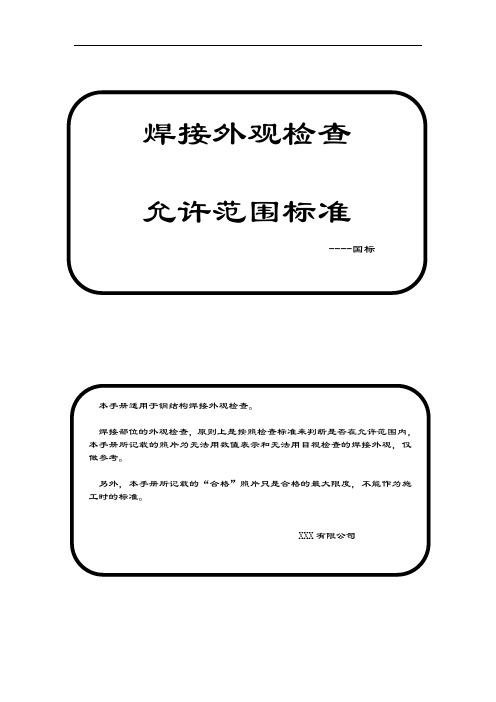
名称图例允许偏差(mm)测量工具测量方法⑴焊接尺寸焊规极限量规⑵脚焊饱满高度C hf≤6时c为0-1.5hf>6时c为0-3.0焊规⑶全焊透对接接缝的饱满高度hhf≥(t4)+4且≤10焊规极限量规焊接外观检查标准名称图例允许偏差(mm)测量工具测量方法⑷全焊透T 接缝的饱满高度hf≥(t2)+4且≤10焊规极限量规⑸咬边二级:≤0.05t且≤0.5mm,连续长度≤100mm,且焊缝两侧咬边总长≤10%焊缝长度三级:≤0.1t且≤1mm,长度不限咬边焊规名称 图例允许偏差(mm )测量工具测量方法⑹对接焊缝错边 d一,二级:d<0.15t且≤2.0 三:d<0.15t 且≤3.0金属制角尺 金属制直尺 量隙规 焊规 测定夹具⑺接头错位模片和 翼板之 间的偏et 1≥t 2 e ≤2 t1/15或e ≤3mm t 1 <t 2e ≤t 1/6或e ≤4m m凸面卷尺 量隙规 测定夹具焊接外观检查标准名称 图例允许偏差(mm )测量工具测量方法⑻焊道表面不整齐e焊道表面凹凸高低差为焊接长度或缝宽在25mm 围时允许偏差在2.5mm 一下在焊接长度在150mm 围缝宽不整齐偏差允许在5mm 一下金属制直尺量规 凸面卷尺--⑼ 气孔二级:不允许 三级:每50mm 长度焊缝允许存在直径<0.4t 且≤3mm 的气孔2个:孔距≥6倍孔径放大镜一般情况下目视判断焊高8mm 焊高16mm检查标准名称图例允许偏差(mm)脚焊焊厚a脚焊焊厚图例②合格测量脚焊焊厚方法②焊缝余高2.0mm 焊缝余高2.5mm图例堆焊高度5mm检查标准名称图例允许偏差mm咬边e二级:≤0.05t且≤0.5mm,连续长度≤100mm,且焊缝两侧咬边总长≤10%焊缝长度三级:≤0.1t且≤1mm,长度不限咬边图例⑤合格不合格咬边在现场施工的对比图例⑤咬边咬边咬边错边量0.5mm 错边量0.3mm检查标准名称图例允许偏差(mm)焊道表面不整齐e焊道表面不整齐图例⑧合格不合格焊道宽度差6mm焊道表面不整齐(焊道宽度)对比图例⑧卷边焊道接头不连续包角不连续包角处咬边包角不圆润卷边焊道成形不美观电弧刮伤图例孔径在1mm一下每300mm长有1个视为合格存在密集气孔视为不合格孔径在1mm一下每300mm长有一个视为合格孔径超过2mm以上为不合格多处飞溅多处飞溅压痕深度超过0.5mm 以上为不合格母材表面缺陷,深度超过0.5mm 以上为不合格螺孔周边翻卷。
焊接件检验标准

焊接件检验标准焊接是一种常见的金属连接方式,广泛应用于工业生产和制造领域。
焊接件作为连接件,在使用过程中需要经过严格的检验标准,以确保其质量和安全性。
本文将介绍焊接件检验标准的相关内容,包括检验方法、标准要求等方面的内容。
首先,焊接件的检验标准包括外观检查、尺寸检查、力学性能检查等多个方面。
外观检查主要包括焊缝的表面质量、焊接件的外观形状等方面的检查,以确保焊接件外观无裂纹、气孔、夹渣等缺陷。
尺寸检查主要包括焊接件的尺寸精度、形位公差等方面的检查,以确保焊接件的尺寸符合设计要求。
力学性能检查主要包括焊接件的拉伸强度、冲击韧性等方面的检查,以确保焊接件具有足够的强度和韧性。
其次,焊接件的检验标准需要参照国家标准或行业标准进行执行。
国家标准是对焊接件检验的一般性规定,包括焊接工艺、焊接材料、焊接设备等方面的要求。
而行业标准是针对特定行业或特定产品的检验标准,通常是在国家标准的基础上进行细化和补充。
在执行焊接件检验标准时,需要严格按照相关标准的规定进行操作,确保检验结果的准确性和可靠性。
另外,焊接件的检验标准还需要考虑焊接件的使用环境和使用要求。
不同的使用环境和使用要求对焊接件的质量和性能有不同的要求,因此在进行检验时需要充分考虑这些因素。
例如,在海洋工程领域使用的焊接件,需要考虑其耐腐蚀性能;在航空航天领域使用的焊接件,需要考虑其高温性能和轻量化要求等。
最后,焊接件的检验标准是确保焊接件质量和安全性的重要手段。
通过严格执行检验标准,可以有效地避免因焊接件质量问题导致的事故和损失,保障生产和使用的安全。
因此,各个相关行业和企业都应高度重视焊接件的检验工作,确保焊接件的质量符合要求。
综上所述,焊接件的检验标准涉及多个方面,包括外观检查、尺寸检查、力学性能检查等,需要参照国家标准或行业标准进行执行,并需要考虑使用环境和使用要求的影响。
通过严格执行检验标准,可以有效地确保焊接件的质量和安全性,为生产和使用提供保障。
焊接的检验标准和流程
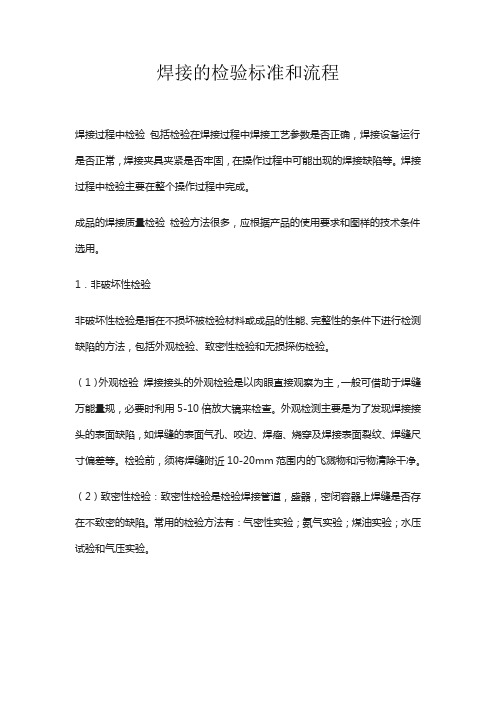
焊接的检验标准和流程焊接过程中检验包括检验在焊接过程中焊接工艺参数是否正确,焊接设备运行是否正常,焊接夹具夹紧是否牢固,在操作过程中可能出现的焊接缺陷等。
焊接过程中检验主要在整个操作过程中完成。
成品的焊接质量检验检验方法很多,应根据产品的使用要求和图样的技术条件选用。
1.非破坏性检验非破坏性检验是指在不损坏被检验材料或成品的性能、完整性的条件下进行检测缺陷的方法,包括外观检验、致密性检验和无损探伤检验。
(1)外观检验焊接接头的外观检验是以肉眼直接观察为主,一般可借助于焊缝万能量规,必要时利用5-10倍放大镜来检查。
外观检测主要是为了发现焊接接头的表面缺陷,如焊缝的表面气孔、咬边、焊瘤、烧穿及焊接表面裂纹、焊缝尺寸偏差等。
检验前,须将焊缝附近10-20mm范围内的飞溅物和污物清除干净。
(2)致密性检验:致密性检验是检验焊接管道,盛器,密闭容器上焊缝是否存在不致密的缺陷。
常用的检验方法有:气密性实验;氨气实验;煤油实验;水压试验和气压实验。
(3)无损探伤检验:是非破坏性检验中的一种特殊的检验方式,是利用渗透,磁粉,超声波,射线等检验方法来发现焊缝表面的细微缺陷及存在于焊缝内部的缺陷。
目前,这类检验方法已在重要的焊接结构中被广泛应用。
2.破坏性检验破坏性检验是从焊件或试件上切取试样或以产品的整体破坏做试验,以检查其力学性能等的检验方法。
它包括力学性能试验,化学分析,腐蚀试验,金相试验,焊接性试验等。
在生产中,焊接成品的质量检验很重要占有很重要的地位。
它不仅在于发现焊接缺陷,检验焊接接头的性能,以确保产品的焊接质量和安全使用,严重的缺陷可导致受压容器的爆炸,造成直接经济损失或灾难性事故而且通过各种检验可对缺陷作出客观的判断,才能对焊缝作出可靠的结论,看其是否所规定的技术要求和保证结构使用的安全可靠。
下面介绍几种检验焊缝质量的方法:(1)气密性实验:一般检验管道,盛器,密闭容器上焊接是否存在不致密的缺陷,以便及时发现,进行排除并修复。
焊接检验标准

焊接检验标准焊接是工程中常见的一种连接方法,它的质量直接关系到工程结构的安全性和稳定性。
因此,对焊接质量的检验就显得尤为重要。
焊接检验标准是评定焊接质量的依据,下面将从焊接检验的标准要求、常见的检验方法和检验过程中需要注意的问题等方面进行介绍。
首先,焊接检验的标准要求包括焊接工艺规范、焊接质量等级和焊接检验方法等内容。
焊接工艺规范是指在进行焊接作业时,应按照相关的工艺规范进行操作,包括焊接材料的选用、焊接设备的调试和操作、焊接工艺参数的设定等。
焊接质量等级是指对焊缝的质量进行评定,一般包括焊缝的外观质量、内部质量和力学性能等指标。
焊接检验方法是指对焊接质量进行检测和评定的方法,包括目测检验、非破坏检验和破坏性检验等。
其次,常见的焊接检验方法包括目测检验、渗透检验、超声波检测、X射线检测和磁粉检测等。
目测检验是指通过肉眼观察焊缝的外观质量,包括焊缝的形状、尺寸、气孔、裂纹等情况。
渗透检验是指利用渗透剂和显像剂对焊缝进行检测,以发现表面裂纹和气孔等缺陷。
超声波检测是指利用超声波对焊缝进行检测,以发现焊缝内部的缺陷。
X射线检测是指利用X射线对焊缝进行检测,以发现焊缝内部的缺陷和夹杂物等。
磁粉检测是指在焊缝表面涂覆磁粉,利用磁场对焊缝进行检测,以发现表面和近表面的裂纹和夹杂物等。
最后,焊接检验过程中需要注意的问题包括检验人员的资质和操作规程、检验设备的校准和维护、检验环境的要求和焊接工艺的影响等。
检验人员应具备相关的焊接检验资质,并严格按照操作规程进行操作。
检验设备应定期进行校准和维护,以确保检验结果的准确性和可靠性。
检验环境应符合相关的要求,以保证检验的准确性和可靠性。
同时,焊接工艺的影响也会对焊接质量产生重要影响,因此在进行焊接检验时,应充分考虑焊接工艺的影响因素。
综上所述,焊接检验标准是保证焊接质量的重要依据,通过严格遵守焊接工艺规范、选择合适的焊接质量等级和采用适当的检验方法,可以有效地评定焊接质量,保证工程结构的安全性和稳定性。
焊接质量检验标准

焊接质量检验标准焊接是一种常见的金属连接方法,广泛应用于工业制造、建筑和维修等领域。
为了确保焊接连接的质量和安全,需要进行焊接质量检验。
本文将介绍一些常见的焊接质量检验标准和方法。
一、焊接质量检验的重要性焊接连接是通过加热和熔化金属材料,使其形成牢固的连接。
然而,焊接过程中可能存在焊缺陷、裂纹、气孔和夹杂物等问题,这些都会对焊接连接的质量和强度产生负面影响。
因此,进行焊接质量检验是非常必要的,可以有效地发现和修复焊接缺陷,确保焊接连接的安全可靠。
二、焊接质量检验标准1.国际标准国际上广泛采用的焊接质量检验标准是ISO 5817:2014《焊接质量评定》。
该标准规定了不同焊接方法下的焊缝形状尺寸和焊接缺陷的容许限值。
根据焊缝质量的评定,可分为4个等级:A级、B级、C级和D级,从高到低表示焊缝的质量逐渐下降。
2.国内标准中国国家标准中,GB/T 9444-2002《焊接材料焊接试样制备和焊接接头检验》是常用的焊接质量检验标准。
该标准详细说明了焊缝制备、焊接接头的形状尺寸和外观质量评定方法。
三、焊接质量检验方法1.外观检验外观检验是最简单也是最直观的一种质量检验方法。
这种方法通过目视检查焊缝的表面,判断是否存在表面缺陷、气孔、裂纹等问题。
外观检验需要依据相应的焊接质量标准来评定焊缝的外观质量,包括焊缝是否均匀、光滑,焊接缺陷是否超过容许限值。
2.尺寸检验尺寸检验是通过测量焊接接头的尺寸来判断焊接质量。
该方法通过对焊缝的长度、角度、结构等进行测量,与相应的标准进行比较,以确定焊接接头的尺寸是否符合规定。
3.无损检测无损检测是一种通过检测焊缝内部的缺陷来评估焊接质量的方法。
常用的无损检测方法包括X射线检测、超声波检测和涡流检测。
这些方法可以有效地发现焊接接头中的裂纹、气孔等内部缺陷,并对其进行评估和分类。
4.机械性能测试焊接接头的机械性能测试是评估焊接质量的重要指标之一。
机械性能测试包括抗拉强度、屈服强度和冲击韧性等指标的测试。
焊接件检验标准

焊接件检验标准焊接是一种常见的连接工艺,而焊接件的质量直接关系到工程结构的安全性和稳定性。
因此,对焊接件进行严格的检验是非常必要的。
本文将介绍焊接件检验的标准和方法,以确保焊接件的质量符合要求。
首先,焊接件的外观检验是非常重要的一步。
外观检验主要包括焊缝的形状、尺寸和表面质量等方面。
焊缝的形状应该符合设计要求,焊接表面应该光滑平整,无裂纹、气孔和夹渣等缺陷。
此外,还需要检查焊接件的变形情况,确保焊接后的结构尺寸符合要求。
其次,焊接件的力学性能是焊接质量的重要指标之一。
力学性能检验包括拉伸试验、冲击试验和硬度测试等。
拉伸试验可以检测焊接件的抗拉强度和屈服强度,冲击试验可以检测焊接件的韧性和抗冲击能力,硬度测试可以检测焊接件的硬度值。
这些力学性能的检验可以全面评估焊接件的质量状况。
另外,焊接件的非破坏检测也是必不可少的。
非破坏检测主要包括超声波检测、磁粉检测和射线检测等。
这些方法可以检测焊接件内部的缺陷和疵点,如裂纹、气孔、夹渣等。
通过非破坏检测,可以及时发现焊接件的质量问题,确保焊接件的可靠性和安全性。
最后,焊接件的化学成分和金相组织也需要进行检验。
焊接件的化学成分应符合设计要求,金相组织应均匀致密。
通过化学成分和金相组织的检验,可以评估焊接件的材料质量和组织结构,为焊接件的使用提供可靠的保障。
综上所述,焊接件的检验标准涵盖了外观检验、力学性能检验、非破坏检测和化学成分及金相组织检验等多个方面。
只有严格按照标准进行检验,才能确保焊接件的质量符合要求,从而保障工程结构的安全性和稳定性。
希望本文的介绍能够对焊接件的检验工作有所帮助,提高焊接件质量,确保工程安全。
非正式EN 1714-2002 中文版 焊缝的无损检验 焊接连接件的超声波检验 允许极限值
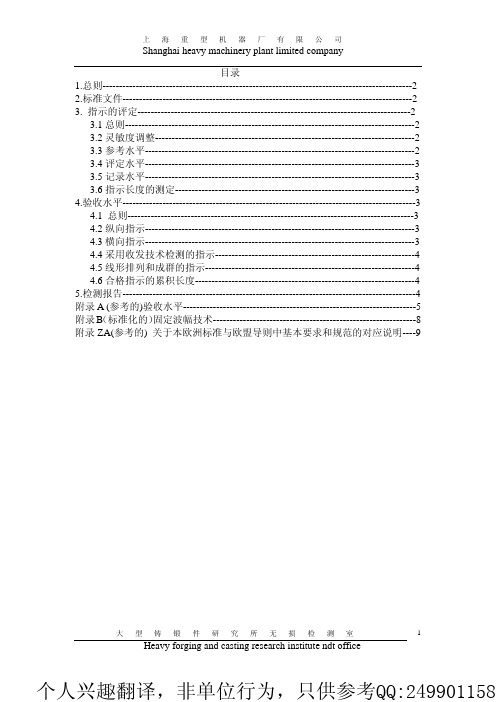
大型铸锻件研究所无损检测室1目录1.总则---------------------------------------------------------------------------------------------22.标准文件---------------------------------------------------------------------------------------23. 指示的评定----------------------------------------------------------------------------------2 3.1总则---------------------------------------------------------------------------------------2 3.2灵敏度调整------------------------------------------------------------------------------2 3.3参考水平---------------------------------------------------------------------------------2 3.4评定水平---------------------------------------------------------------------------------3 3.5记录水平---------------------------------------------------------------------------------3 3.6指示长度的测定------------------------------------------------------------------------34.验收水平----------------------------------------------------------------------------------------3 4.1 总则--------------------------------------------------------------------------------------3 4.2纵向指示---------------------------------------------------------------------------------3 4.3横向指示---------------------------------------------------------------------------------3 4.4采用收发技术检测的指示------------------------------------------------------------4 4.5线形排列和成群的指示---------------------------------------------------------------4 4.6合格指示的累积长度------------------------------------------------------------------45.检测报告----------------------------------------------------------------------------------------4 附录A (参考的)验收水平----------------------------------------------------------------------5 附录B (标准化的)固定波幅技术-------------------------------------------------------------8 附录ZA(参考的) 关于本欧洲标准与欧盟导则中基本要求和规范的对应说明----9w ww .b zf x w.c om大型铸锻件研究所无损检测室2EN 1714—2002焊缝的无损检测—焊接接头的超声检测 验收级别(包括修订文件A1:2002) 1. 总则本欧洲标准规定了铁素体全焊透焊缝的验收级别2,3级,它们分别对应EN25817中的B 和C 级,当有特殊对定时可以采用其它验收级别。
焊接检验标准(+目录)
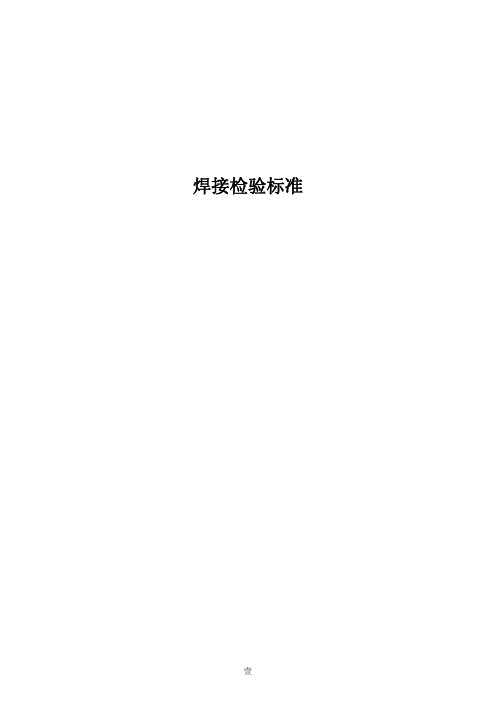
-壹-
前言
1.适用范围: 本焊接检验标准适用于本公司各个过程的对印制板焊接的外观检验——IQC 入库检(外协产品)、
IPQC 过程检及 FQC 终检; 本焊接检验标准适用于贴装、焊装印制板的外观检验;
2.参考文件: IPC-A-610C&PC-A-610D;
3.本标准中有四级验收条件: 标准条件、可接受条件、缺陷条件和制程警示条件; 标准条件:指的是合格即符合要求的条件; 可接受条件:指的是产品在使用环境下运行,能保证完整、可靠,不影响使用; 缺陷条件:指的是产品不合格,即不符合要求的条件; 过程警示条件:主要针对生产过程中的检验,发现问题后应对其进行监控,并分析、改进;
4.标准中用到的几个术语: 焊接起始面:指印制板用于焊接的那一面,通用是印制板进行波峰焊、浸焊或拖焊的辅面。采 用手工焊接时,焊接起始面也可能是主面; 焊接终止面:指印制板焊锡流向的那一面。
-壹-
目录
焊接检验标准............................................................................................................................................................................. 壹 前言 ........................................................................................................................................................................................ 壹 第一部
焊接质量检验标准.
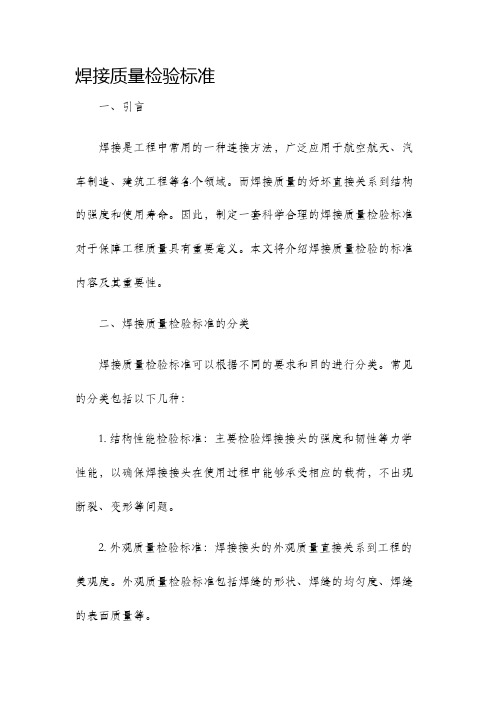
焊接质量检验标准一、引言焊接是工程中常用的一种连接方法,广泛应用于航空航天、汽车制造、建筑工程等各个领域。
而焊接质量的好坏直接关系到结构的强度和使用寿命。
因此,制定一套科学合理的焊接质量检验标准对于保障工程质量具有重要意义。
本文将介绍焊接质量检验的标准内容及其重要性。
二、焊接质量检验标准的分类焊接质量检验标准可以根据不同的要求和目的进行分类。
常见的分类包括以下几种:1. 结构性能检验标准:主要检验焊接接头的强度和韧性等力学性能,以确保焊接接头在使用过程中能够承受相应的载荷,不出现断裂、变形等问题。
2. 外观质量检验标准:焊接接头的外观质量直接关系到工程的美观度。
外观质量检验标准包括焊缝的形状、焊缝的均匀度、焊缝的表面质量等。
3. 金属组织检验标准:焊接接头的金属组织对于焊接质量具有重要影响。
金属组织检验标准主要针对焊缝的晶粒尺寸、晶界和非金属夹杂物等进行检验。
4. 检测方法标准:不同的焊接质量检验需要使用不同的检测方法。
例如,常用的焊缝探伤检测方法包括超声波检测、射线检测等。
检测方法标准主要规定了不同检测方法的应用范围、操作步骤以及结果评定等。
三、焊接质量检验标准的重要性焊接质量检验标准对于确保焊接接头的质量具有重要意义。
以下是几个重要原因:1. 保证结构的强度和稳定性:焊接接头的质量直接关系到结构的强度和稳定性。
通过制定焊接质量检验标准,能够确保焊接接头能够承受设计要求的力学载荷,并保持长期稳定。
2. 提高工程质量:焊接接头是工程中常见的连接方式,其质量直接关系到工程的总体质量。
通过严格遵循焊接质量检验标准,能够提高工程质量,避免因焊接质量问题引发的事故和故障。
3. 减少维修和更换成本:焊接接头的质量问题容易导致结构损坏和功能失效。
通过实施焊接质量检验,可以及时发现和修复质量问题,减少后期维修和更换的成本。
4. 形成统一的检验标准:焊接质量检验标准可以统一不同行业、不同企业之间的检验要求,使得焊接质量的评定更加科学、客观。
EN1714焊缝的无损检测—焊接接头的超声波检测
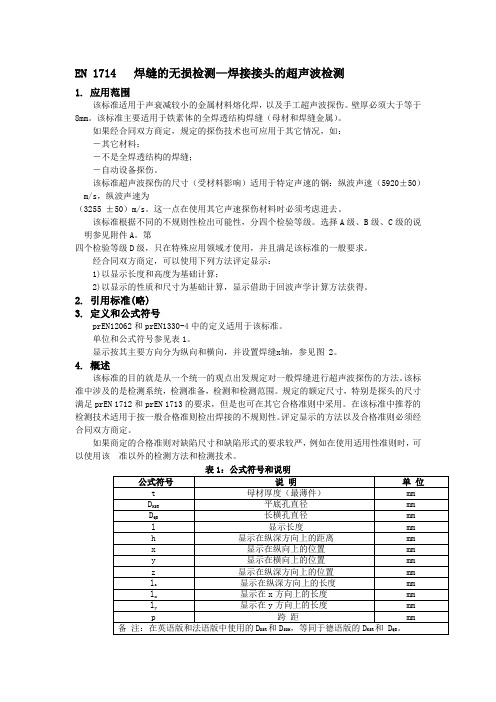
EN 1714 焊缝的无损检测—焊接接头的超声波检测1. 应用范围该标准适用于声衰减较小的金属材料熔化焊,以及手工超声波探伤。
壁厚必须大于等于8mm。
该标准主要适用于铁素体的全焊透结构焊缝(母材和焊缝金属)。
如果经合同双方商定,规定的探伤技术也可应用于其它情况,如:-其它材料;-不是全焊透结构的焊缝;-自动设备探伤。
该标准超声波探伤的尺寸(受材料影响)适用于特定声速的钢:纵波声速(5920±50)m/s,纵波声速为(3255 ±50)m/s。
这一点在使用其它声速探伤材料时必须考虑进去。
该标准根据不同的不规则性检出可能性,分四个检验等级。
选择A级、B级、C级的说明参见附件A。
第四个检验等级D级,只在特殊应用领域才使用,并且满足该标准的一般要求。
经合同双方商定,可以使用下列方法评定显示:1)以显示长度和高度为基础计算;2)以显示的性质和尺寸为基础计算,显示借助于回波声学计算方法获得。
2. 引用标准(略)3. 定义和公式符号prEN12062和prEN1330-4中的定义适用于该标准。
单位和公式符号参见表1。
显示按其主要方向分为纵向和横向,并设置焊缝x轴,参见图 2。
4. 概述该标准的目的就是从一个统一的观点出发规定对一般焊缝进行超声波探伤的方法。
该标准中涉及的是检测系统,检测准备,检测和检测范围。
规定的额定尺寸,特别是探头的尺寸满足prEN 1712和prEN 1713的要求,但是也可在其它合格准则中采用。
在该标准中推荐的检测技术适用于按一般合格准则检出焊接的不规则性。
评定显示的方法以及合格准则必须经合同双方商定。
如果商定的合格准则对缺陷尺寸和缺陷形式的要求较严,例如在使用适用性准则时,可以使用该准以外的检测方法和检测技术。
表1:公式符号和说明公式符号说明单位t 母材厚度(最薄件)mmD KSR平底孔直径mmD QB长横孔直径mml 显示长度mmh 显示在纵深方向上的距离mmx 显示在纵向上的位置mmy 显示在横向上的位置mmz 显示在纵深方向上的位置mml z显示在纵深方向上的长度mml x显示在x方向上的长度mml y显示在y方向上的长度mmp 跨距mm 备注:在英语版和法语版中使用的D DSR和D SDH,等同于德语版的D KSR和 D QB。
焊接检验标准

焊接检验标准1. 引言焊接是一种连接金属材料的常用工艺,为了确保焊接接头的质量和可靠性,需要进行焊接检验。
焊接检验的目的是验证焊接接头的质量是否符合相关标准和要求,以确保焊接接头的使用安全。
2. 焊接检验的分类焊接检验可以分为破坏性检验和非破坏性检验两大类。
2.1 破坏性检验破坏性检验是通过对焊接接头进行破坏性试验,以评估焊接接头的强度和韧性等性能。
常见的破坏性检验方法包括拉伸试验、弯曲试验和冲击试验等。
2.1.1 拉伸试验拉伸试验是通过对焊接接头进行拉伸,测量材料的断裂强度和延伸性能等指标来评估焊接接头的质量。
试验过程中需要根据相关标准对试样的几何形状和尺寸进行规定,以确保测试结果的可靠性。
2.1.2 弯曲试验弯曲试验是将焊接接头弯曲至一定角度,通过观察和测量试样的断裂形式和角度等指标来评估焊接接头的质量。
弯曲试验常用于评估焊接接头的韧性和抗裂性能。
2.1.3 冲击试验冲击试验是通过在焊接接头上施加冲击载荷,评估焊接接头的抗冲击性能。
常用的冲击试验方法有冲击试验机试验和夏比冲击试验等。
2.2 非破坏性检验非破坏性检验是在不对焊接接头造成永久性损伤的情况下,通过对焊接接头表面或内部进行检测,评估焊接接头的质量。
常见的非破坏性检验方法有涡流检测、超声波检测和X射线检测等。
2.2.1 涡流检测涡流检测是利用涡流原理进行的一种表面缺陷检测方法,适用于检测焊接接头表面的裂纹、夹渣等缺陷。
2.2.2 超声波检测超声波检测是利用超声波在材料中的传播和反射特性进行的一种内部缺陷检测方法,适用于检测焊接接头内部的缺陷,如气孔、夹渣和裂纹等。
2.2.3 X射线检测X射线检测是利用X射线通过材料的不同密度和吸收能力来进行的一种内部缺陷检测方法,适用于检测焊接接头内部的缺陷,如气孔、夹渣和裂纹等。
3. 焊接检验标准与规范焊接检验需遵循一系列的标准与规范,以确保检验过程的科学性和统一性。
常见的焊接检验标准与规范有国际标准、行业标准和企业标准等。
焊接检验标准

焊接检验标准焊接检验标准⽬录⼀、⽬的2⼆、适⽤范围本公司2三、定义2四、引⽤标准2五、焊缝质量分级3六、检验标准(单位为mm)3本规范由编制,由负责解释。
13⼀、⽬的:指导焊⼯及焊接检验⼈员⼯作,明确检验⽅法,建⽴判定标准,确保产品质量。
适⽤范围:本公司定义:焊接质量(weldingquality)是指焊接产品符合设计技术要求的程度。
焊接质量不仅影响焊接产品的使⽤性能和寿命,更重要的是影响⼈⾝和财产安全;引⽤标准:本标准的尺⼨未注单位皆为mm,未注公差按以下国标IT13级执⾏GB/T1800.3-1998极限与配合标准公差和基本偏差数值表GB/T1800.4-1998极限与配合标准公差等级和孔、轴的极限偏差表GB/1804-2000⼀般公差未注公差的线性和⾓度尺⼨的公差未注形位公差按GB/T1184–1996形状和位置公差未注公差值执⾏。
焊缝质量分级根据缺陷性质和数量将焊缝质量分为4级:Ⅰ级:应⽆裂纹、未熔合、未焊透和条状夹渣;Ⅱ级:应⽆裂纹、未熔合和未焊透;Ⅲ级:应⽆裂纹、未熔合及双⾯焊或加垫板的单⾯焊缝中的未焊透,不加垫板的单⾯焊中的未焊透允许长度按条状夹渣长度Ⅲ级评定(此等级为修理后降级使⽤);Ⅳ级:焊缝缺陷超过Ⅲ级者(直接判废)。
检验标准(单位为mm)1、?焊脚尺⼨:⽬测、焊缝检验尺a、?图纸标有焊脚尺⼨的焊脚公差SPEC+25.0%0.0%(焊脚为10mm时,允许值为10~12.5mm,焊脚尺⼨不允许有负公差)b、?图纸未注焊脚尺⼨:检验⽅法:⽬测、焊缝检验规项⽬图⽰?内容质量等级备注1级2级3级焊脚尺⼨t1=t2母材厚度6以下s≥t-1s≥t-1s≥t-26~9s≥t-2s≥t-2s≥t-312s≥9s≥9s≥619s≥14s≥14s≥1020s≥15s≥15s≥1022s≥16s≥16s≥1125s≥18s≥18s≥1226t以上?以薄钢板厚度为厚度基准,焊缝尺⼨为母材厚度的75%以上,公差取0~+25%?2、?咬边:检验⽅式:⽬测、深度尺项⽬图⽰?内容质量等级备注1级2级3级咬边上下部咬边t≤3.6不允许不允许孤⽴的短的允许a≤0.2+0.05t末端切⼝部分的平滑过渡不视为咬边t≥3.6不允许孤⽴的短的允许a≤0.5孤⽴的短的允许a≤1.0t>3.6单独孤⽴短的允许a≤0.2单独孤⽴短的允许a≤0.5孤⽴的短的a≤1.0?3、?焊缝表⾯⽓孔:检验⽅式:⽬测项⽬图⽰?内容质量等级备注1级2级3级⽓孔针状⽓孔焊缝上⼩的孤⽴的允许Φ1mm⽓孔1个以下焊缝上⼩的孤⽴的允许Φ1mm⽓孔2个以下焊缝上⼩的孤⽴的允许Φ1mm⽓孔3个或Φ2mm⽓孔1个以下对于焊接末端部位除外夹渣⾓焊缝对接焊缝夹渣不允许焊缝上孤⽴的⼩的允许Φ1mm2个以下焊缝上孤⽴的⼩的允许Φ1mm2个以下Φ2mm1个以下对于2个以上的密集⽓孔不允许a、焊缝的概念指的是焊缝从起弧到收弧的距离b、焊缝表⾯连续出现的线状或群集状⽓孔,均判定为不合格4、?焊瘤:检验⽅式:⽬测项⽬图⽰?内容质量等级备注1级2级3级焊瘤ΦΦ≤90°时判定为焊瘤不允许不允许⼩的局部的允许??5、?未焊透:检验⽅式:⽬测适⽤部位:适⽤外观上可进⾏检查的⾓焊缝及对接焊缝末端部位项⽬图⽰?内容质量等级备注1级2级3级未焊透双⾯焊发⽣的未焊透现象不允许不允许孤⽴的⼩的缺陷,缺陷厚度≤0.5?6、背⾯余⾼(烧穿、焊漏):检验⽅式:⽬测项⽬图⽰?内容质量等级备注1级2级3级背⾯余⾼对接接头背⾯余⾼aa≤1+0.1b最⼤不允超过2局部稍⾼允许a≤1+0.15b最⼤不允许超过3局部稍⾼允许a≤1+0.15b最⼤不允许超过43级以上判定为烧穿余⾼对接接头余⾼hh≤1+0.05c最⼤余⾼h≤2,c=10则h≤1.5c=20则h≤2.0h≤1+0.1ch≤3,c=10则h≤2c=20则h≤3h≤1+0.2ch≤3焊缝与母材不能有尖锐夹⾓,修磨或重焊7、?未融合:检验⽅式:⽬测适⽤于从外观上可以检查的部位项⽬图⽰?内容质量等级备注1级2级3级未熔合坡⼝⾯和焊道及焊道之间未融合不允许不允许不允许内部缺陷8、?焊缝裂纹:检验⽅式:⽬测由于母材分层引起的也适⽤于本标准项⽬图⽰?内容质量等级备注1级2级3级裂纹焊接接头内、外部裂纹不允许不允许不允许9、?弧坑:检验⽅式:⽬测弧坑裂纹不允许,需要返修项⽬图⽰?内容质量等级备注1级2级3级弧坑不允许弧坑部的凹陷深度在1mm以下a≤1mm弧坑部的凹陷深度在2mm以下a≤2mm对于对接焊端部,不允许?10、焊缝连接(余⾼):检验⽅式:⽬测、焊缝检验规项⽬图⽰?内容质量等级备注1级2级3级接头缺陷焊缝最⼤厚度差a≤1mma≤2mma≤3mm包括焊缝宽度不均匀11、焊缝形状:检验⽅式:⽬测项⽬图⽰?内容质量等级备注1级2级3级形状缺陷根部凹陷不允许局部浅的允许a≤1mm局部浅的允许a≤1mm余⾼过⼤t≤3.6a≤1+0.1b局部稍⾼允许a≤1+0.15b局部稍⾼允许a≤1+0.2bt>3.6a≤1+0.05b局部稍⾼允许a≤1+0.1b最⼤允许到5mm局部稍⾼允许a≤1+0.2b最⼤允许到5mm未填满t≤3.6不允许局部允许a≤0.1+0.01?t局部允许a≤0.1+0.07?tt>3.6不允许a≤0.2+0.02?t局部允许a≤0 .2+0.04t?12、焊脚不对称:检验⽅式:⽬测适合图纸中标注的等⾓焊缝项⽬图⽰?内容质量等级备注1级2级3级焊脚不对称过⼤的不对称焊脚Z2-Z1≤0.5+0.15aZ2-Z1≤1+0.15a允许局部稍⾼Z2-Z1≤2+0.2允许局部稍⾼A为设计尺⼨?13、飞溅:检验⽅式:⽬测项⽬图⽰?内容质量等级备注1级2级3级飞溅焊接飞溅不允许1、长度≤1000内,⼤⼩≤0.5允许3~5个2、长度≥1000,⼤⼩≤0.5允许6~10个1、长度≤1000内,⼤⼩≤1允许3~5个2、长度≥1000,⼤⼩≤1允许6~10个??14、?错边:检验⽅式:⽬测项⽬图⽰?内容质量等级备注1级2级3级错边双⾯焊接e<0.1te≤2e<0.15te≤3不允许两项均符合单⾯焊接e<0.1te≤2e<0.15te≤2不允许两项均符合T型焊接圆周焊e<0.1te≤1e<0.15te≤2不允许两项均符合15、漏焊:检验⽅式:⽬测与形成部位⽆关,均判为不合格焊接长度不⾜也视为漏焊,判定为不合格16、重复缺陷:检验⽅式:⽬测项⽬图⽰?内容质量等级备注1级2级3级多重缺陷2种缺陷的重复分别确定缺陷等级,并以最差的级别作为缺陷等级3种以上缺陷的重复不允许17、焊缝打磨:检验⽅式:⽬测、⼿摸a、图纸中标注的焊缝打磨?应满⾜图纸要求,由于打磨引起的切⼝打磨过度,母材损伤等,不允许使⽤b、图纸未注焊缝打磨的对于焊缝打磨,原则上不允许,仅允许为了焊缝返修的焊缝母材的打磨项⽬图⽰?内容质量等级备注1级2级3级?弧坑及焊接起始点处的打磨不允许局部打磨痕迹及凹陷允许a≤0.5局部打磨痕迹及凹陷允许a≤1.0?焊缝打磨t≤3.6不允许不允许局部打磨痕迹及凹陷允许a≤0.5?t≥3.6不允许不允许不允许为去除缺陷对母材打磨有不良影响的不允许局部打磨痕允许a≤0.5局部打磨痕迹及凹陷允许a≤1.0⼀般尺⼨公差和形位公差检测⽅法:游标卡尺、⽶尺、⾼度尺、深度尺、直⾓尺、⾓度尺a、线性尺⼨公差b、⾓度尺⼨公差测量时应采⽤⾓度的短边作为基准,其长度可以延长⾄某特定的基准点,在这种情况下,基准点应标注在图纸上。
焊接质量检验方法及标准

焊接质量检验方法和标准1目的规定焊接产品的表面质量、焊接质量、确保产品满足客户的要求,适用范围:适用于焊接产品的质量认可。
2责任生产部门,品质部门可参照本准则对焊接产品进行检验。
一、熔化极焊接表面质量检验方法和标准C O2保护焊的表面质量评价主要是对焊缝外观的评价,看是否焊缝均匀,是否有假焊、飞溅、焊渣、裂纹、烧穿、缩孔、咬边等缺陷,以及焊缝的数量、长度以及位置是否符合工艺要求,具体评价标准详见下表缺陷类型说明评价标准假焊系指未熔合、未连接焊缝中断等焊接缺陷(不能保证工艺要求的焊缝长度)不允许气孔焊点表面有穿孔焊缝表面不允许有气孔裂纹焊缝中出现开裂现象不允许夹渣固体封入物不允许咬边焊缝与母材之间的过度太剧烈H≤0.5mm允许H>0.5m m不允许烧穿母材被烧透不允许飞溅金属液滴飞出在有功能和外观要求的区域,不允许有焊接飞溅的存在过高的焊缝凸起焊缝太大H值不允许超过3mm位置偏离焊缝位置不准不允许配合不良板材间隙太大H值不允许超过2mm二、焊缝质量标准保证项目1、焊接材料应符合设计要求和有关标准的规定,应检查质量证明书及烘焙记录。
2、焊工必须经考核合格,检查焊工相应施焊条件的合格证及考核日期。
3、I 、II级焊缝必须经探伤检验,并应符合设计要求和施工及验收规范的规定,检验焊缝探伤报告焊缝表面I、II级焊缝不得有裂纹、焊瘤、烧穿、弧坑等缺陷.II级焊缝不得有表面气孔夹渣、弧坑、裂纹、电焊擦伤等缺陷,且I级焊缝不得有咬边,未焊满等缺陷基本项目焊缝外观:焊缝外形均匀,焊道与焊道、焊道与基本金属之间过渡平滑,焊渣和飞溅物清除干净。
表面气孔:I、II级焊缝不允许;III级焊缝每50MM长度焊缝内允许直径≤0。
4t;气孔2个,气孔间距≤6倍孔径咬边:I级焊缝不允许。
II级焊缝:咬边深度≤0.05t,且≤0.5mm,连续长度≤100mm,且两侧咬边总长≤10%焊缝长度.III级焊缝:咬边深度≤0.1t,,且≤1mm.注:,t为连接处较薄的板厚。
焊接质量检验标准.

XX 机械制造有限公司
焊接质量检验标准
1.目的
通过正确定义焊接质量的检验标准,保证员工在焊接、检验过程中制造出合格的产品。
2.范围
适用于焊接车间。
3.工作程序
焊接质量标准根据生产制造现场工艺实际情况,可采用边界样本目视化来清楚地分辨出焊接质量是否符合要求。
3.1电阻点焊焊点不合格质量的界定和CO 2气体保护焊焊点、焊缝不合格质量的界定。
3.1.1以下8 种电阻焊点被认为是不可接受的,界定为不合格质量: 3.1.1.1虚焊(无熔核或者熔核的尺寸小于4mm )焊点,代号为L 。
3.1.1.2沿着焊点周围有裂纹的焊点,代号为C 。
3.1.1.3烧穿,代号为B 。
3.1.1.4
3.1.1.5
3.1.1.6钢板变形超过25度的焊点,代号为D
3.1.1.7压痕过深的焊点(材料厚度减少50%),代号为I 。
3.1.1.8漏焊,代号为M 。
3.1.2以下10种CO 2气体保护焊焊点、焊缝被认为是不可接受的,界定为不合格质量: 3.1.2.2焊缝金属裂纹;
3.1.2.2夹杂(焊缝中夹杂着除母材和焊丝外的物质或氧化物); 3.1.2.3气孔(焊逢中产生气孔); 3.1.2.4咬边;
缺陷B :烧穿
3.1.2.5未熔合;
3.1.2.9飞溅。
飞溅,焊缝堆积过高,焊缝不连续
3.1.3
以下4个凸点焊螺母的焊接质量是3个是可接受的,
1个是不可接受的。
焊接质量检测标准

质量检验标准PCB板部分1、检验要求与检验方法1.1 尺寸检验1.1.1 检验要求1.1.2 检验方法用测量精度小于等于0.02mm的游标卡尺检测外形尺寸、厚度,用量角器量角度。
项目要求备注SMT焊盘尺寸公差SMT焊盘公差满足+20%定孔位公差公差≤±0.076mm之内孔径公差类型/孔径 PTH NPTH0-0.3mm +0.08mm/-∞±0.05mm 0.31-0.8mm ±0.08mm ±0.05mm0.81-1.60mm ±0.10mm ±0.08mm1.61-2.5mm ±0.15mm +0.1mm/-02.5-6.3mm ±0.30mm +0.3mm/-0板弓曲和扭曲对SMT板≤0.7%,特殊要求SMT板≤0.5% 对SMT板≤1.0%,对非SMT板≤1.5%;板厚公差厚度应符合设计文件的要求板厚≤1.0mm,公差±0.10mm;板厚≥1.0mm,公差为±10%外形公差外形尺寸应符合设计文件的要求板边倒角(30º、45º、70º)±5º;CNC铣外形:长宽小于100mm公差±0.2mm; 长宽小于300mm公差±0.25mm;长宽大于300mm公差±0.3mm;键槽、凹槽开口:±0.13mm;位置尺寸:±0.20mmV形槽V槽深度允许偏差为设计值的±0.1mm;槽口上下偏移公差K:±0.15mm;D≤0.8mm,余留基材厚度S=0.35±0.15mm;0.8<D<1.6mm,余留基材厚度S=0.4±0.15mm;D≥1.6mm,余留基材厚度S=0.5±0.15mm;槽型角度:20º、30º、45º、60º1.2 外观检验1.2.1 检验要求项目要求备注成品板边板边不出现缺口或者缺口/白边向内深入≤板边间距的50%,且任何地方的渗入≤2.54mm;UL板边不应露铜;板角/板边损伤板边、板角损伤未出现分层露织纹织纹隐现,玻璃纤维被树脂完全覆盖凹点和压痕直径小于0.076mm,且凹点面积不超过板子每面面积的5%;凹坑没有桥接导体;表面划伤划伤未使导体露铜、划伤未露出基材纤维;铜面划伤每面划伤≤5处,每条长度≤15mm镀金插头插头根部与导线及阻焊交界处露铜小于0.13mm,凹痕/压痕/针孔/缺口≤0.15mm且不超过3处,总面积不超过所有金手指的30%,不准许上铅锡;电镀孔内空穴(铜层)破洞不超过1个,破孔数未超过孔总数5%,横向≤90º,纵向≤板厚度的5%。
- 1、下载文档前请自行甄别文档内容的完整性,平台不提供额外的编辑、内容补充、找答案等附加服务。
- 2、"仅部分预览"的文档,不可在线预览部分如存在完整性等问题,可反馈申请退款(可完整预览的文档不适用该条件!)。
- 3、如文档侵犯您的权益,请联系客服反馈,我们会尽快为您处理(人工客服工作时间:9:00-18:30)。
焊 接 检 验 标 准编制/日期:审批/日期:1、适用范围本检验方法适用于公司生产所需之结构件的焊接过程。
2、施工准备2.1材料和主要机具2.1.1所需施焊的钢材、钢铸件必须符合国家现行标准和设计要求。
2.1.2根据设计要求选用适宜的焊条、焊丝、焊剂、电渣焊熔嘴等焊接材料,并应符合现行国家行业标准。
2.1.3施工机具:交流电焊机、直流弧焊机、半自动CO2弧焊机、氩弧焊焊机、熔化嘴电渣焊机、焊条烘箱、焊条保温筒、焊接检验尺等。
2.2作业条件2.2.1施工前焊工应复查组装质量和焊接区域的清理情况,如不符合技术要求,应修整合格后方可施焊。
2.2.2气温、天气及其它要求:(1)气温低于0℃时,原则上应停止焊接工作。
(2)强风天,应在焊接区周围设置挡风屏,雨天或湿度大的场合应保证母材的焊接区不残留水分。
(3)当采用气体保护焊时,若环境风速大于2m/s,原则上应停止焊接。
2.3焊工必须经考试合格并取得合格证书,持证焊工必须在其考试合格项目及其认可范围内施焊,焊工均应经过质量技术交底、安全交底和有关环境保护的交底。
3、操作工艺3.1工艺流程焊前准备→引弧→沿焊缝纵向直线运动,并作横向摆动→向焊件送焊条→熄弧3.2焊前准备:根据钢种、板厚、接头的约束度和焊缝金属中含氢量等因素来决定预热温度和方法。
预热区域范围为焊接坡口两侧各80~100mm,预热时应尽可能均匀。
3.3引弧3.3.1严禁在焊缝区以外的母材上打火引弧,在坡口内引弧的局部面积应熔焊一次,不得留下弧坑。
3.3.2对接和T形接头的焊缝,引弧应在焊件的引入板开始。
3.3.3引弧处不应产生熔合不良和夹渣,熄弧处和焊缝终端为了防止裂缝应充分填满坑口。
3.4焊接姿势3.4.1平焊姿势:该姿势为焊接施工最理想姿势,因此尽可能创造条件采用平焊。
3.4.2船形焊接姿势:该姿势不易产生咬边、下垂等缺陷,一般对角焊缝要求成凹形时常采用。
3.4.3横向焊接姿势:该姿势熔化金属由于重力作用容易下淌,而使上侧产生咬边,下侧产生焊瘤以及未焊透等缺陷。
因此焊接时宜采用小直径焊条、适当的电流和短弧焊接。
3.4.4立焊姿势:该姿势熔化金属由于重力作用容易下淌,而使焊缝成型困难,易产生焊瘤、咬边、夹渣及焊缝成型不良等缺陷。
因此宜采用小直径焊条和较小的电流,并采用短弧焊接。
3.4.5仰焊姿势:必须保持最短的弧长,宜选用不超过4mm直径的焊条,焊接电流一般介于平焊与立焊之间。
3.5焊接顺序和熔敷顺序3.5.1尽可能减少热量的输入,并必须以最小限度的线能量进行焊接。
3.5.2不要把热量集中在一个部位,尽可能均等分散。
3.5.3采用“先行焊接产生的变形由后续焊接抵消”的施工方法。
3.5.4平行的焊缝尽可能地沿同一焊接方向同时进行焊接。
3.5.5从结构的中心向外进行焊接。
3.5.6从板的厚处向薄处焊接。
3.6多层焊3.6.1多层焊焊接接头应连续施焊一次完成,每一层焊道焊完后应及时清理。
若发现有影响焊接质量的缺陷,必须清除后再焊。
3.6.2对于重要结构处的多层焊必须采用多层多道焊,不准摆宽道焊接。
3.6.3多层焊过程中的层间温度若无特殊要求一般应与预热时的温度相同。
3.7 背面清根在电弧焊接过程中,当接头有全熔透要求时,背面的第一层焊缝容易未焊透、夹渣或裂纹等缺陷,要从背面彻底清除后再行焊接。
常用的方法是碳弧气刨。
3.8熄弧:熄弧应在焊件的引出板终止。
3.9焊后处理3.9.1焊接结束后的焊缝及其两侧,必须彻底清除焊渣、飞溅和焊瘤等。
3.9.2焊接结束后,如发现焊缝出现裂纹时,焊工不得擅自处理,应申报技术负责人查清原因后,订出修补措施方可处理。
4、质量标准4.1强制性条文4.1.1钢材、钢铸件的品种、规格、性能等应符合现行国家产品标准和设计要求。
进口钢材产品的质量应符合设计和合同规定标准的要求。
检查数量:全数检查。
检验方法:检查质量合格证明文件等。
4.2主控项目4.2.1焊接材料的品种、规格、性能等应符合现行国家产品标准和设计要求。
检查数量:全数检查。
检验方法:检查焊接材料的质量合格证明文件等。
4.2.2重要钢结构采用的焊接材料应进行抽样复验,复验结果应符合现行国家产品标准和设计要求。
检查数量:全数检查。
检验方法:检查复验报告。
4.2.3焊条、焊丝、焊剂、电渣焊熔嘴等焊接材料与母材的匹配应符合设计要求及国家现行行业标准的规定。
焊条、焊剂、药芯焊丝、熔嘴等在使用前,应按其产品说明书及焊接工艺文件的规定进行烘焙和存放。
检查数量:全数检查。
检验方法:检查质量证明书和烘焙记录。
4.2.4焊工必须经考试合格并取得合格证书。
持证焊工必须在其考试合格项目及其认可范围内施焊。
检查数量:全数检查。
检验方法:检查焊工合格证及其认可范围、有效期。
4.2.5 分包单位对其首次采用的钢材、焊接材料、焊接方法、焊后热处理等,应进行焊接工艺评定,并应根据评定报告确定焊接工艺。
检查数量:全数检查。
检验方法:检查焊接工艺评定报告。
4.2.6设计要求全焊透的一、二级焊缝应采用超声波探伤进行内部缺陷的检验,超声波探伤不能对缺陷作出判断时,应采用射线探伤,其内部缺陷分级及探伤方法应符合现行国家标准《钢焊缝手工超声波探伤方法和探伤结果分级法》GB11345或《钢熔化焊对接接头射线照相和质量分级》GB3323的规定。
焊接球节点网架焊缝、螺栓球节点网架焊缝及圆管T、K、Y形节点相关线焊缝,其内部缺陷分级及探伤方法应分别符合国家现行标准《焊接球节点钢网架焊缝超声波探伤方法及质量分级法》JBJ/T3034.1、《螺栓球节点钢网架焊缝超声波探伤方法及质量分级法》JBJ/T3034.2、《建筑钢结构焊接技术规程》JGJ81的规定。
一级、二级焊缝的质量等级及缺陷分级应符合表4.2.5的规定。
检查数量:全数检查。
检验方法:检查超声波或射线探伤记录。
一、二级焊缝质量等级及缺陷分级表4.2.54.2.7T形接头、十字接头、角接接头等要求熔透的对接和对接组合焊缝,其焊脚尺寸不应小于t/4;设计有疲劳验算要求的吊车梁或类似构件的腹板与上翼缘连接焊缝的焊脚尺寸为t/2,且不应大于10mm。
焊脚尺寸的允许偏差为0~4mm。
检查数量:资料全数检查;同类焊缝抽查10%,且不应少于3条。
检验方法:观察检查,用焊缝量规抽查测量。
4.2.8焊缝表面不得有裂纹、焊瘤等缺陷。
一级、二级焊缝不得有表面气孔、夹渣、弧坑裂纹、电弧擦伤等缺陷。
且一级焊缝不得有咬边、未焊满、根部收缩等缺陷。
检查数量:每批同类构件抽查10%,且不应少于3件;被抽查构件中,每一类型焊缝按条数抽查5%,且不应少于1条;每条检查1处,总抽查数不应少于10处。
检验方法:观察检查或使用放大镜、焊缝量规和钢尺检查,当存在疑义时,采用渗透或磁粉探伤检查。
4.3一般项目4.3.1焊条外观不应有药皮脱落、焊芯生锈等缺陷;焊剂不应受潮结块。
检查数量:按量抽查1%,且不应少于10包。
检验方法:观察检查。
4.3.2对于需要进行焊前预热或焊后热处理的焊缝,其预热温度或后热温度应符合国家现行有关标准的规定或通过工艺试验确定。
预热区在焊道两侧,每侧宽度均应大于焊件厚度的1.5倍以上,且不应小于100mm;后热处理应在焊后立即进行,保温时间应根据板厚按25mm板厚1h确定。
检查数量:全数检查。
检验方法:检查预、后热施工记录和工艺试验报告。
4.3.3二级、三级焊缝外观质量标准应符合GB50205标准附录A中表A.0.1的规定。
三级对接焊缝应按二级焊缝标准进行外观质量检验。
检查数量:每批同类构件抽查10%,且不应少于3件;被抽查构件中,每一类型焊缝按条数抽查5%,且不应少于1条;每条检查1处,总抽查数不应少于10处。
检验方法:观察检查或使用放大镜、焊缝量规和钢尺检查。
4.3.4焊缝尺寸允许偏差应符合GB50205标准附录A中表A.0.2的规定。
检查数量:每批同类构件抽查10%,且不应少于3件;被抽查构件中,每种焊缝按条数各抽查5%,但不应少于1条;每条检查1处,总抽查数不应少于10处。
检验方法:用焊缝量规检查。
4.3.5焊成凹形的角焊缝,焊缝金属与母材间应平缓过渡;加工成凹形的角焊缝,不得在其表面留下切痕。
检查数量:每批同类构件抽查10%,且不应少于3件。
检验方法:观察检查。
4.3.6焊缝感观应达到:外形均匀、成型较好,焊道与焊道、焊道与基本金属间过渡较平滑,焊渣和飞溅物基本清除干净。
检查数量:每批同类构件抽查10%,且不应少于3件;被抽查构件中,每种焊缝按数量各抽查5%,总抽查处不应少于5处。
检验方法:观察检查。
5、成品保护5.1焊后不准砸焊缝周边,不准往刚焊完的焊缝上浇水。
5.2低温下操作应采取预热、缓冷措施。
5.3不准在焊缝外母材上引弧。
5.4低温焊接后不准立即清渣,应等焊缝降温后方可清渣。