螺旋锥齿轮数字化制造过程关键技术概述
大模数螺旋锥齿轮的加工
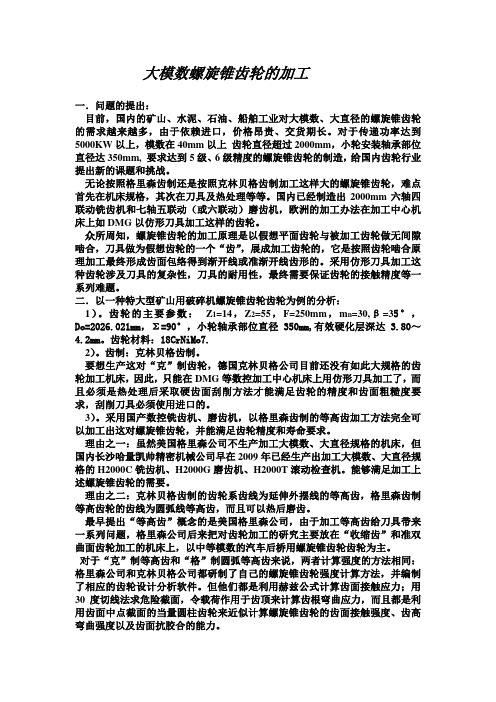
大模数螺旋锥齿轮的加工一.问题的提出:目前,国内的矿山、水泥、石油、船舶工业对大模数、大直径的螺旋锥齿轮的需求越来越多,由于依赖进口,价格昂贵、交货期长。
对于传递功率达到5000KW以上,模数在40mm以上齿轮直径超过2000mm,小轮安装轴承部位直径达350mm, 要求达到5级、6级精度的螺旋锥齿轮的制造,给国内齿轮行业提出新的课题和挑战。
无论按照格里森齿制还是按照克林贝格齿制加工这样大的螺旋锥齿轮,难点首先在机床规格,其次在刀具及热处理等等。
国内已经制造出2000mm六轴四联动铣齿机和七轴五联动(或六联动)磨齿机,欧洲的加工办法在加工中心机床上如DMG以仿形刀具加工这样的齿轮。
众所周知,螺旋锥齿轮的加工原理是以假想平面齿轮与被加工齿轮做无间隙啮合,刀具做为假想齿轮的一个“齿”,展成加工齿轮的,它是按照齿轮啮合原理加工最终形成齿面包络得到渐开线或准渐开线齿形的。
采用仿形刀具加工这种齿轮涉及刀具的复杂性,刀具的耐用性,最终需要保证齿轮的接触精度等一系列难题。
二.以一种特大型矿山用破碎机螺旋锥齿轮齿轮为例的分析:1)。
齿轮的主要参数:Z1=14,Z2=55,F=250mm,m n=30,β=35°,Do=2026.021mm,Σ=90°,小轮轴承部位直径350mm,有效硬化层深达 3.80~4.2mm。
齿轮材料:18CrNiMo7.2)。
齿制:克林贝格齿制。
要想生产这对“克”制齿轮,德国克林贝格公司目前还没有如此大规格的齿轮加工机床,因此,只能在DMG等数控加工中心机床上用仿形刀具加工了,而且必须是热处理后采取硬齿面刮削方法才能满足齿轮的精度和齿面粗糙度要求,刮削刀具必须使用进口的。
3)。
采用国产数控铣齿机、磨齿机,以格里森齿制的等高齿加工方法完全可以加工出这对螺旋锥齿轮,并能满足齿轮精度和寿命要求。
理由之一:虽然美国格里森公司不生产加工大模数、大直径规格的机床,但国内长沙哈量凯帅精密机械公司早在2009年已经生产出加工大模数、大直径规格的H2000C铣齿机、H2000G磨齿机、H2000T滚动检查机。
螺旋锥齿轮加工机床发展综述
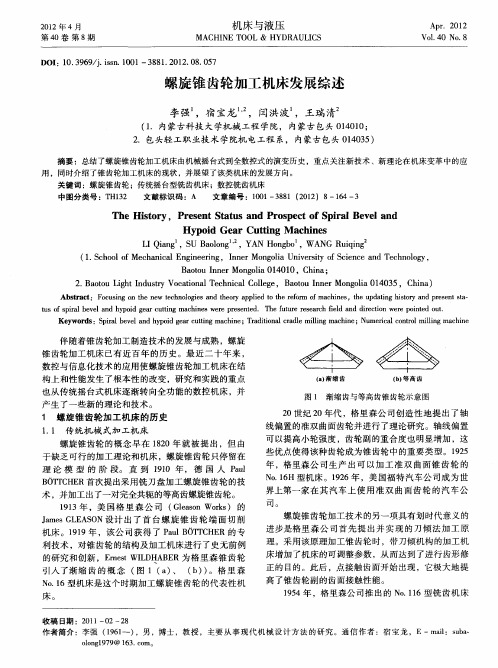
2 B o uLgt n ut oa o a T c ncl o ee atuIn r no a0 4 3 ,C ia . at i d syV ct nl eh i l g ,B o e gl 10 5 hn ) o hI r i aC l o n Mo i
螺旋 锥 齿轮 加工 机 床发 展 综述
李强 ,宿 宝龙 ,闰洪波 ,王瑞清
(.内蒙古科技 大学机械 工程 学院 ,内蒙 古 包头 04 1 ; 1 100 2 .包头轻 工职 业技 术 学院机 电工程 系,内蒙古 包头 0 4 3 ) 1 0 5
摘要 :总结了螺旋锥齿轮加工机床 由机械摇台式到全数控式的演变历史 ,重点关 注新技术 、薪理论在 机床变革 中的应
21 0 2年 4月
机床 与液压
MACHI NE T0OL & HYDRAULI CS
Ap .2 2 r 01 Vo. 0 No 8 14 .
第4 0卷 第 8 期
DO :1 . 9 9 j i n 1 0 I 0 3 6 / .s . 0 1—3 8 . 0 2 0 . 5 s 8 12 1. 80 7
11 9 3年 ,美 国 格 里 森 公 司 ( l snWo s 的 Ge o r ) a k
线偏置 的准双 曲面齿 轮并进行 了理论研究 。轴线偏置 可 以提高小轮强度 ,齿轮副 的重合度也 明显增加 ,这 些优点使得该种齿轮成为锥齿 轮中的重要类 型。12 95 年 ,格里森公 司 生产 出可 以加工 准 双 曲面锥 齿轮 的 N .6 o 1H型机床 。12 9 6年 ,美 国福特汽 车公司成 为世 界上第一家在 其 汽车上 使 用准 双 曲面齿 轮 的汽 车公
网络化螺旋锥齿轮齿面加工集成制造系统
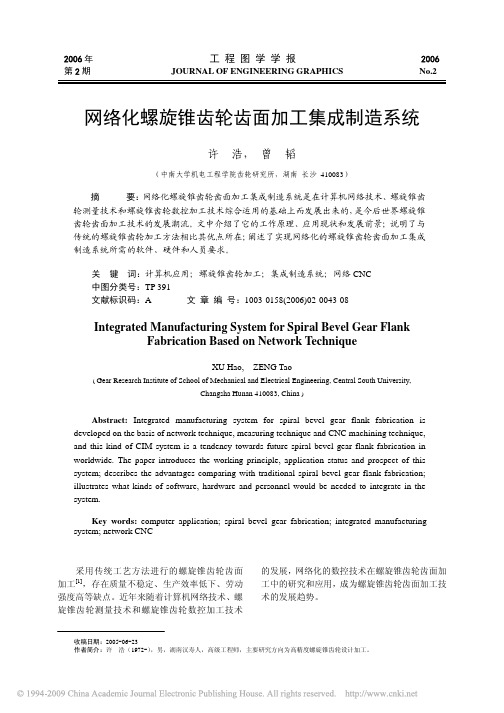
采用传统工艺方法进行的螺旋锥齿轮齿面加工[1],存在质量不稳定、生产效率低下、劳动强度高等缺点。
近年来随着计算机网络技术、螺旋锥齿轮测量技术和螺旋锥齿轮数控加工技术的发展,网络化的数控技术在螺旋锥齿轮齿面加工中的研究和应用,成为螺旋锥齿轮齿面加工技术的发展趋势。
2006年 工 程 图 学 学 报2006第2期 JOURNAL OF ENGINEERING GRAPHICS No.2网络化螺旋锥齿轮齿面加工集成制造系统许浩,曾韬(中南大学机电工程学院齿轮研究所,湖南长沙 410083)摘要:网络化螺旋锥齿轮齿面加工集成制造系统是在计算机网络技术、螺旋锥齿轮测量技术和螺旋锥齿轮数控加工技术综合运用的基础上而发展出来的,是今后世界螺旋锥齿轮齿面加工技术的发展潮流。
文中介绍了它的工作原理、应用现状和发展前景;说明了与传统的螺旋锥齿轮加工方法相比其优点所在;阐述了实现网络化的螺旋锥齿轮齿面加工集成制造系统所需的软件、硬件和人员要求。
关键词:计算机应用;螺旋锥齿轮加工;集成制造系统;网络CNC中图分类号:TP 391文献标识码:A 文章编号:1003-0158(2006)02-0043-08Integrated Manufacturing System for Spiral Bevel Gear FlankFabrication Based on Network TechniqueXU Hao, ZENG Tao( Gear Research Institute of School of Mechanical and Electrical Engineering, Central South University,Changsha Hunan 410083, China )Abstract: Integrated manufacturing system for spiral bevel gear flank fabrication is developed on the basis of network technique, measuring technique and CNC machining technique, and this kind of CIM system is a tendency towards future spiral bevel gear flank fabrication in worldwide. The paper introduces the working principle, application status and prospect of this system; describes the advantages comparing with traditional spiral bevel gear flank fabrication;illustrates what kinds of software, hardware and personnel would be needed to integrate in the system.Key words: computer application; spiral bevel gear fabrication; integrated manufacturing system; network CNC收稿日期:2005-06-231 网络化螺旋锥齿轮齿面加工集成制造系统的定义网络化螺旋锥齿轮齿面加工集成制造系统,就是将计算机技术、螺旋锥齿轮数控加工技术和齿轮检测技术通过计算机网络有机地结合起来,组成完整闭环控制系统的新型螺旋锥齿轮齿面加工新技术。
新型螺旋锥齿轮数控铣齿机的结构模型设计

De s i g n o f t he St r u c t ur a l M o d e l o f Ne w CN C S pi r a l Be ve l Ge a r M i l l i ng M a c hi n e DI NG Ha n,ADAYI ・Xi e e r y a z i d a n
c h i n e t o o l we r e i mp r o v e d,a n d n e w c u t t e r me c h a n i s m h a d t wo me s h i ng c u t t e r r e l a t i v e l y i n t h e pa r a l l e l a x — e s . Ad d i t i o n a l l y, i t d e s i g n e d t wo l i n k a g e t a b l e s m e c h a n i s m h a d i ma g i n a r y f la t — t o p p e d g e a r s wi t h t h e
第 1 0期
2 0 1 3年 1 O月
组 合 机 床 与 自 动 化 加 工 技 术
M o du l a r M a c h i ne To o l& Aut om a t i c Ma nuf a c t ur i ng Te c h ni que
NO. 1 0
oc t .2 01 3
ma c h i n e t o o l wi t h n i n e a x e s e i g h t l i n k a g e s ,a n d ma y wo r k o u t a p a i r o f c o n j u g a t e d g e a r d r i v e s s i mu l t a n e —
螺旋锥齿轮数字化制造技术

螺旋锥齿轮数字化制造技术作者:王山城来源:《科技创新与应用》2014年第19期摘要:航空锥齿轮的啮合印痕要求十分严格,且模数大小不一,螺旋角差别大,啮合印痕要求各异。
因其齿型面复杂,精度要求高等原因难以保证较高的精度。
传统的一对一配对加工方法,存在加工一致性差,质量不稳定,效率低下的缺点已经越来越难以满足发展的需要,为此,先进的数字化制造方法已成为发展的必然趋势。
关键词:螺旋锥齿轮;数字化;制造技术1 螺旋锥齿轮数字化加工的必要性传统的确定航空螺旋锥齿轮的最终的齿面接触区的方法,是依靠设计者的经验和粗略的计算,先确定一个大致的齿面接触区,然后进行多次的试加工和试车,不断的调整修正齿面接触区,最后才能得到一个较为理想的齿面接触区。
以往我公司在锥齿轮加工中采用的办法是先按照图纸要求加工大齿轮,根据大齿轮配小齿轮,通过实际加工结果、根据加工经验对机床磨齿参数进行调整,然后反复此操作。
这样的方法,需要消耗大量的人力物力和时间,同时存在人为因素影响大,过程不受控,质量稳定性差,调整周期长等缺点,而且交付时为配对交付,这样导致锥齿轮没有互换性,只要一对锥齿轮中有一件报废,与其配对的锥齿轮也不能使用。
并且热处理前后的齿面形貌不一定吻合,这样就会导致齿面的渗碳层不均匀,齿面各处的硬度不一致,零件容易在工作的过程中局部产生点蚀,剥落,甚至产生断齿的危险,零件质量不稳定。
目前国际上较多采用的加工方法为螺旋锥齿轮齿面数字化加工方法。
很好的解决了传统方法带来的弊端。
2 螺旋锥齿轮数字化简介2.1 形貌图简介形貌图就是锥齿轮齿面坐标形态,一般锥齿轮加工形貌图采取9×5点,即在整个齿面上,分别从距齿面大端、小端、齿顶、齿根约为整个齿面的5%处开始,采取9列5行,采取45个坐标点来表示整个齿面的形态(见图)1。
采取9×5点,是因为如果太密,采样点的误差可导致拟合齿面局部区域曲率变化很大,对数字化接触分析不利,并且计算量也会按级数增大。
小模数航空螺旋锥齿轮全工序法铣齿法综述
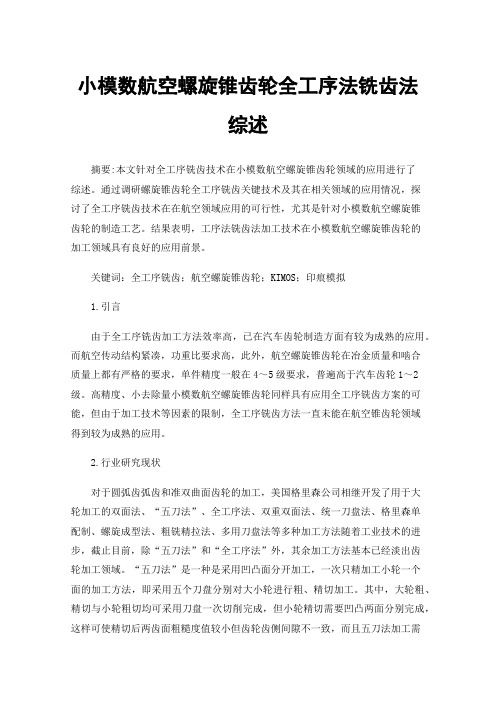
小模数航空螺旋锥齿轮全工序法铣齿法综述摘要:本文针对全工序铣齿技术在小模数航空螺旋锥齿轮领域的应用进行了综述。
通过调研螺旋锥齿轮全工序铣齿关键技术及其在相关领域的应用情况,探讨了全工序铣齿技术在在航空领域应用的可行性,尤其是针对小模数航空螺旋锥齿轮的制造工艺。
结果表明,工序法铣齿法加工技术在小模数航空螺旋锥齿轮的加工领域具有良好的应用前景。
关键词:全工序铣齿;航空螺旋锥齿轮;KIMOS;印痕模拟1.引言由于全工序铣齿加工方法效率高,已在汽车齿轮制造方面有较为成熟的应用。
而航空传动结构紧凑,功重比要求高,此外,航空螺旋锥齿轮在冶金质量和啮合质量上都有严格的要求,单件精度一般在4~5级要求,普遍高于汽车齿轮1~2级。
高精度、小去除量小模数航空螺旋锥齿轮同样具有应用全工序铣齿方案的可能,但由于加工技术等因素的限制,全工序铣齿方法一直未能在航空锥齿轮领域得到较为成熟的应用。
2.行业研究现状对于圆弧齿弧齿和准双曲面齿轮的加工,美国格里森公司相继开发了用于大轮加工的双面法、“五刀法”、全工序法、双重双面法、统一刀盘法、格里森单配制、螺旋成型法、粗铣精拉法、多用刀盘法等多种加工方法随着工业技术的进步,截止目前,除“五刀法”和“全工序法”外,其余加工方法基本已经淡出齿轮加工领域。
“五刀法”是一种是采用凹凸面分开加工,一次只精加工小轮一个面的加工方法,即采用五个刀盘分别对大小轮进行粗、精切加工。
其中,大轮粗、精切与小轮粗切均可采用刀盘一次切削完成,但小轮精切需要凹凸两面分别完成,这样可使精切后两齿面粗糙度值较小但齿轮齿侧间隙不一致,而且五刀法加工需要不断更换刀盘并重新调整刀具参数,降低了加工效率。
由于齿轮模数小,齿厚薄,在加工调整中极易产生干涉现象且不易被发现,造成质量风险、产品交付困难,急需解决。
全工序法是一种是采用凹凸面同时加工,一次成型的加工方法,该方法又称双重螺旋法,既可以提高零件表面粗糙度,保证齿隙的一致性,又可以保证渗层的均匀性,对提高产品质量具有重要意义。
螺旋锥齿轮(螺伞)数控加工的简化计算

螺旋锥齿轮(螺伞)数控加工简易计算摘要:进入21世纪,我国经济进入了突飞猛进的发展期,国内中小特别是小型企业迅猛发展;同时,国内外机加工设备也在全面向着数字化变革,带来了加工工业的变革。
一些老的理论以及工艺已经不能完全适应当前这种需求。
本文通过对螺旋锥齿轮的调整计算、加工的现状分析,提出了简化计算及加工方法,尤其适用于数控加工。
一.螺旋锥齿轮加工现状螺旋锥齿轮又叫弧齿锥齿轮、螺旋伞齿轮,俗称螺伞齿轮、盆角齿轮。
因相对使用较少,设备昂贵,原一般由国营大型企业加工。
其加工参数计算繁琐,且根据单号单面法、固定安装法、双面法等不同加工方法有不同计算公式,同时老式机床调整也复杂。
近年来,随着我国经济迅猛发展,对螺旋锥齿轮的需求也逐步增加,中小企业也开始参与到锥齿轮加工中来。
对于小型生产企业,可以购买新式数控机床,但是不可能掏出上万甚至几十万来购买计算模拟软件,普遍对于螺旋锥齿轮的计算及加工感到困难。
下面根据相关基本理论,结合实践,阐述简明的计算、加工过程。
二.调整计算,确定加工所需项目参数(以复合双面法为基础、综合固定安装法、单面法,使用最少刀盘,获得最高效率为目标)实例:Z1/Z2=8/33,m=5.85齿宽b=33螺旋角β=35轴交角Σ=90齿高变位系数χ=0.475全齿高=10.46 (0.8/0.188)1.几何计算:略2.刀具选用:(全部采用双精刀盘)-刀盘直径根据经验,选用中点锥距2倍左右即可,例如:中点锥距计算为82.821,我们可以选用6英寸刀盘(理论直径φ152.4)。
-刀号根据复合双面法刀号公式:N#=540*tgβ[1-(Lsinβ/r)] / (tgα*Zc)= 11.52 (理论刀号)式中:r-刀盘半径,L-中点锥距,α-压力角,Zc-当量齿数此处采用10.5#刀盘。
(根据经验,为了减少刀盘数量,可以全部采购10.5#刀盘)。
根据刀号通用公式:N#=(γ1+γ2) /20 * sinβ(γ1和γ2为大小轮齿根角,单位:分),将实际刀号10.5代人,反求得螺旋角β为:31.73°(后面计算均按此螺旋角计算,接触区会更容易达到理想状态)-错刀距根据复合双面法公式:W=mL[π/2*cosβ-2tgα(f+c)]/Le =2.77 (复合双面法理论错刀距)式中:m-模数,L-中点锥距,α-压力角,Le-大端锥距,f-齿高系数(0.8),c-顶隙系数(0.188)(此处插入一些说明:复合双面法采用同一把刀盘加工大、小轮,且均为一次成型,成本低,效率较高,所以在满足要求的情况下,企业均希望采用此种加工方法;而根据传统理论,此加工方法适用条件为:模数最大2.5,小轮齿数最少16,且齿高、顶隙系数定义也不同,这就很大程度限制了此加工方法的使用。
螺旋锥齿轮——准双曲面齿轮讲解
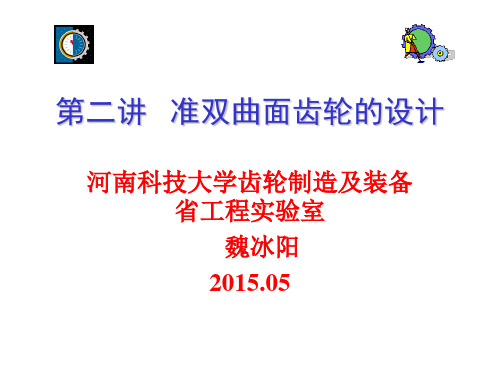
面/大轮凸面总是小于小轮凸面/大轮凹面压力角
a 21 15' , a* 8
0
0 0 0
0 0
0
a1 21 15'8 13 15'
a2 21 15'8 29 15'
0
3.极限压力角与压力角
新的设计理念——非对称设计,工作侧与非工
•H1、H2节锥顶点 •H1P小轮锥距R1 •H2P大轮锥距R2 1小轮节锥角 2大轮节锥角 ’ 偏置角
O1 A2
Z O2
H2
ZP
r2 R2
-G
H1ZGຫໍສະໝຸດ R1A1P
r1
K1
1.准双曲面齿轮副的节面模型
• 节平面为两节锥 的共切面 • 节锥面为单叶双 曲面的近似
K2
A2
H2
r2 R2
第二讲 准双曲面齿轮的设计
河南科技大学齿轮制造及装备 省工程实验室 魏冰阳 2015.05
一.绪论
• 螺旋锥齿轮的发展历史 • 准双曲面齿轮的概述
1. 螺旋锥齿轮的发展历史
• 1913年格里森公司发明了曲线齿锥齿轮 加工机床 ,宣告了螺旋锥齿轮的诞生。 • 1946年E.威尔德哈伯(Ernest Wildhaber)
• 如果螺旋角1不满足要求,通过改变r1来 满足 • 如果极限曲率半径不符合标准刀盘尺寸, 通过改变小轮轴截面偏置角来满足 • 过程通常由计算机叠代完成
5.准双曲面齿轮的设计过程
• 三参数(d2,1,)确定双曲线齿轮的节锥
1 r2 (d 2 b2 sin 2 ) 2 z2 sin ' tg 2 1.2( z1 z2 cos)
螺旋锥齿轮数字化制造的关键技术及研究现状
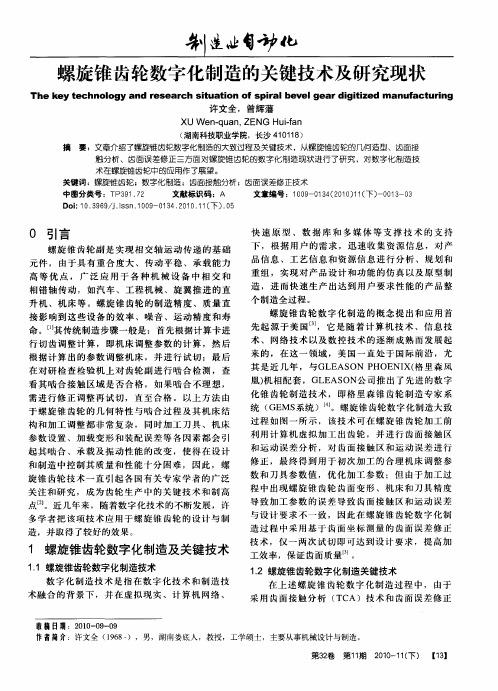
修 正 , 最终 得 到 用 于 初 次加 工 的合 理 机 床调 整 参
数 和 刀具 参 数 值 ,优化 加 工 参 数 ;但 由 于加 工 过
程 中出现 螺旋 锥 齿 轮 齿 面变 形 、机 床 和 刀具 精 度
导 致 加工 参 数 的误 差导 致齿 面 接 触 区 和运 动 误 差
过 程 如 图 一所 示 ,该 技 术 可在 螺旋 锥 齿 轮加 工 前 利 用 计 算机 虚 拟 加 工 出齿 轮 ,并 进 行 齿 面 接触 区 和 运 动 误 差分 析 ,对 齿 面 接 触 区和 运 动 误 差进 行
于 螺 旋 锥 齿轮 的几 何 特性 与啮 合 过 程 及其 机 床 结
1 螺旋锥齿轮数字化制造及关键技术
11螺旋锥齿轮数字化制造技术 .
数 字 化 制 造技 术是 指 在 数 字 化 技 术 和 制造 技
技 术 ,仅 一 两 次试 切 即可 达 到设 计 要 求 ,提 高加
工效率 ,保 证齿面 质量 。
1 螺旋锥齿轮数字化制造关键技术 . 2
在 上 述 螺 旋 锥 齿 轮 数 字化 制 造 过 程 中 , 由于 采用 齿 面 接 触 分析 ( C T A)技 术 和齿 面误 差 修 正
术融 合 的 背景 下 ,并 在 虚拟 现 实 、计 算 机 网 络 、
收稿日期 :2 1- 9 0 00 0 - 9 作者简介:许文全 (9 8一 1 6 ),男,湖南娄底人 ,教授 ,工学硕士 ,主要从事机械设计与制造 。 第 3卷 2 第 1期 1 2 1 — 1下 ) 【3 00 1 ( 1】
快 速 原 型 、数 据 库 和 多媒 体 等 支 撑 技 术 的 支 持 下 , 根 据用 户 的需 求 , 迅速 收集 资 源 信 息 ,对 产 品 信 息 、工 艺 信 息 和 资 源信 息 进 行 分析 、规 划 和 重 组 , 实现 对 产 品设 计 和功 能 的 仿 真 以及 原 型 制
螺旋锥齿轮数字化制造过程关键技术概述
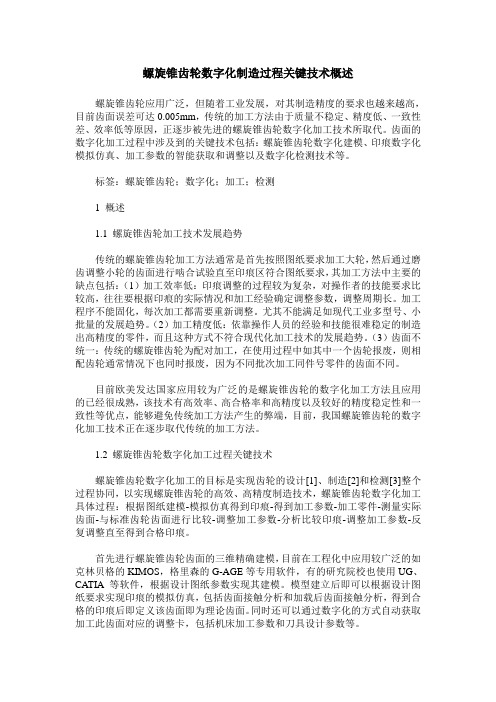
螺旋锥齿轮数字化制造过程关键技术概述螺旋锥齿轮应用广泛,但随着工业发展,对其制造精度的要求也越来越高,目前齿面误差可达0.005mm,传统的加工方法由于质量不稳定、精度低、一致性差、效率低等原因,正逐步被先进的螺旋锥齿轮数字化加工技术所取代。
齿面的数字化加工过程中涉及到的关键技术包括:螺旋锥齿轮数字化建模、印痕数字化模拟仿真、加工参数的智能获取和调整以及数字化检测技术等。
标签:螺旋锥齿轮;数字化;加工;检测1 概述1.1 螺旋锥齿轮加工技术发展趋势传统的螺旋锥齿轮加工方法通常是首先按照图纸要求加工大轮,然后通过磨齿调整小轮的齿面进行啮合试验直至印痕区符合图纸要求,其加工方法中主要的缺点包括:(1)加工效率低:印痕调整的过程较为复杂,对操作者的技能要求比较高,往往要根据印痕的实际情况和加工经验确定调整参数,调整周期长。
加工程序不能固化,每次加工都需要重新调整。
尤其不能满足如现代工业多型号、小批量的发展趋势。
(2)加工精度低:依靠操作人员的经验和技能很难稳定的制造出高精度的零件,而且这种方式不符合现代化加工技术的发展趋势。
(3)齿面不统一:传统的螺旋锥齿轮为配对加工,在使用过程中如其中一个齿轮报废,则相配齿轮通常情况下也同时报废,因为不同批次加工同件号零件的齿面不同。
目前欧美发达国家应用较为广泛的是螺旋锥齿轮的数字化加工方法且应用的已经很成熟,该技术有高效率、高合格率和高精度以及较好的精度稳定性和一致性等优点,能够避免传统加工方法产生的弊端,目前,我国螺旋锥齿轮的数字化加工技术正在逐步取代传统的加工方法。
1.2 螺旋锥齿轮数字化加工过程关键技术螺旋锥齿轮数字化加工的目标是实现齿轮的设计[1]、制造[2]和检测[3]整个过程协同,以实现螺旋锥齿轮的高效、高精度制造技术,螺旋锥齿轮数字化加工具体过程:根据图纸建模-模拟仿真得到印痕-得到加工参数-加工零件-测量实际齿面-与标准齿轮齿面进行比较-调整加工参数-分析比较印痕-调整加工参数-反复调整直至得到合格印痕。
螺旋锥齿轮的三维参数化建模_概述说明以及解释
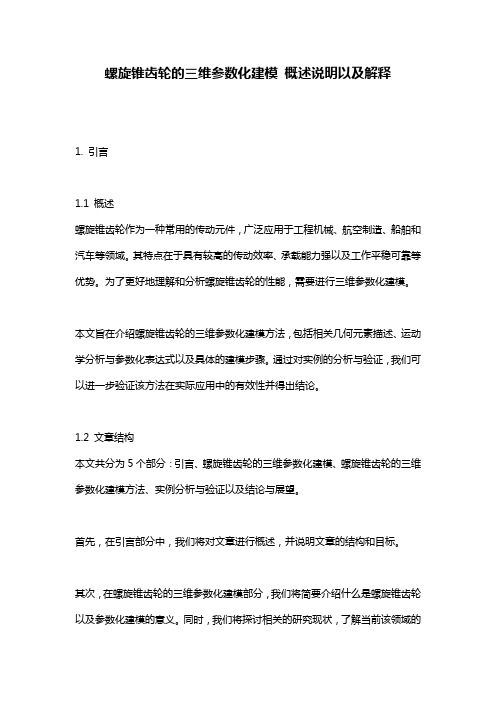
螺旋锥齿轮的三维参数化建模概述说明以及解释1. 引言1.1 概述螺旋锥齿轮作为一种常用的传动元件,广泛应用于工程机械、航空制造、船舶和汽车等领域。
其特点在于具有较高的传动效率、承载能力强以及工作平稳可靠等优势。
为了更好地理解和分析螺旋锥齿轮的性能,需要进行三维参数化建模。
本文旨在介绍螺旋锥齿轮的三维参数化建模方法,包括相关几何元素描述、运动学分析与参数化表达式以及具体的建模步骤。
通过对实例的分析与验证,我们可以进一步验证该方法在实际应用中的有效性并得出结论。
1.2 文章结构本文共分为5个部分:引言、螺旋锥齿轮的三维参数化建模、螺旋锥齿轮的三维参数化建模方法、实例分析与验证以及结论与展望。
首先,在引言部分中,我们将对文章进行概述,并说明文章的结构和目标。
其次,在螺旋锥齿轮的三维参数化建模部分,我们将简要介绍什么是螺旋锥齿轮以及参数化建模的意义。
同时,我们将探讨相关的研究现状,了解当前该领域的研究进展。
接着,在螺旋锥齿轮的三维参数化建模方法部分,我们将详细描述基本几何元素的描述方式,并进行运动学分析与参数化表达式的探讨。
最后,我们将给出具体的三维参数化建模步骤。
在实例分析与验证部分,我们将选择适当的实例,并收集相关数据。
然后,我们将实现参数化建模算法,并展示结果。
最后,通过结果对比和分析,评估该方法的有效性和可靠性。
最后,在结论与展望部分,我们将总结主要工作及创新点,并指出研究中存在不足之处以及改进方向。
1.3 目的本文旨在提供一种有效、可行的方法来进行螺旋锥齿轮的三维参数化建模。
通过对相关几何元素描述、运动学分析与参数化表达式以及具体建模步骤的介绍与探讨,可以为螺旋锥齿轮设计和优化提供参考依据。
此外,通过实例分析和验证,可以进一步验证该方法的有效性,为相关领域的研究和应用提供支持。
最终,本文将总结主要工作及创新点,并指出改进方向,以期对未来的研究产生积极影响。
2. 螺旋锥齿轮的三维参数化建模:2.1 什么是螺旋锥齿轮螺旋锥齿轮是一种常见的传动装置,广泛应用于机械领域。
螺旋锥齿轮制造技术对比研究及应用_李党育
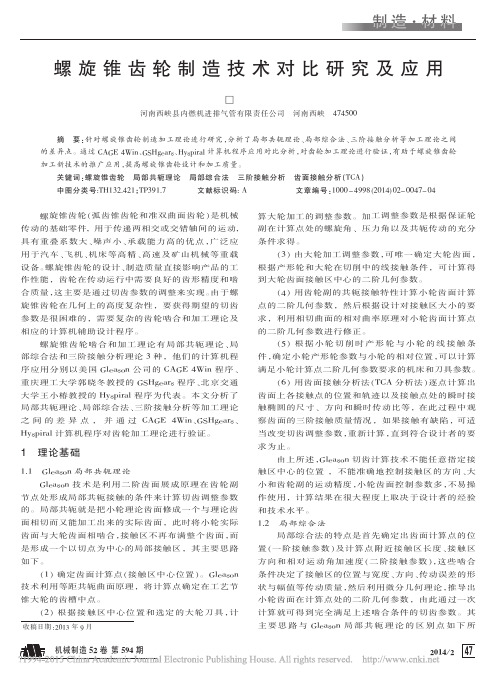
加工新技术的推广应用,提高螺旋锥齿轮设计和加工质量。
关键词:螺旋锥齿轮 局部共轭理论 局部综合法 三阶接触分析 齿面接触分析(TCA)
中 图 分 类 号 :TH132.421;TP391.7
文献标识码: A
文章编号:1000 - 4998 (2014) 02- 0047- 04
螺旋锥齿轮(弧齿锥齿轮和准双曲面齿轮)是机械 传动的基础零件, 用于传递两相交或交错轴间的运动, 具有重叠系数大、噪声小、承载能力高的优点,广泛应 用于汽车、飞机、机床等高精、高速及矿山机械等重载 设备 。 螺旋锥齿轮的设计 、制造质量直接影响产品的工 作性能, 齿轮在传动运行中需要良好的齿形精度和啮 合质量 ,这主要是通过切齿参数的调整来实现 。 由于螺 旋锥齿轮在几何上的高度复杂性, 要获得期望的切齿 参数是很困难的, 需要复杂的齿轮啮合和加工理论及 相应的计算机辅助设计程序。
CAGE GSHgears Hyspiral
●
●
●
●
●
●
●
○
加载 TCA 计算 根切计算检查
●
○
○
●
●
●
齿面失配图形 机床调整数据
●
○
○
●
滚检修正 测量中心测量网格数据计算
○
○
●
●
●
●
基于测量误差的切齿调整参数自动修正 ○
●
●
切齿加工过程仿真
○
●
○
小轮粗、精切齿面比较(精切余量分布)的 ○
●
●
计算模块
(5) 根 据 小 轮 切 削 时 产 形 轮 与 小 轮 的 线 接 触 条 件,确定小轮产形轮参数与小轮的相对位置,可以计算 满足小轮计算点二阶几何参数要求的机床和刀具参数。
螺旋锥齿轮齿廓高精高效倒圆倒角技术

螺旋锥齿轮是航空发动机的关键传动部件,传统的手工打磨的加工方式存在加工效率低、批次零件质量一致性差等问题,直接影响到螺旋锥齿轮的实际使用寿命,乃至对飞行安全造成隐患。
螺旋锥齿轮倒角倒圆不规整或尖角、台阶、缺料等缺陷,会导致锥齿轮在高载荷运转下因局部应力集中而出现裂纹,须对传统手工打磨技术采用数字化手段进行升级改造。
创新团队应用在线测量、自适应数控加工、齿面模型重建等方法,开发了螺旋锥齿轮齿廓高效高精倒角倒圆技术,解决了人工倒圆倒角加工质量一致性差等问题。
总体思路为了突破航空发动机螺旋锥齿轮倒角倒圆高效高精加工的技术瓶颈,创新团队通过数控加工的方式提高产品质量的一致性、稳定性、可靠性。
总体思路主要是以被加工齿轮齿面实测数据为基础,建立逼近产品实物的实体模型,并以五轴加工中心为平台,结合高精度机床测头,设计一套自适应加工系统实现五轴联动加工路径的精确控制,最终实现螺旋锥齿轮齿顶齿廓倒角倒圆的高精度、高效率、智能化加工。
创新团队制定的技术开发流程如图1所示:将齿轮的实体模型导入到自适应软件平台中,并基于该模型规划合适的测量路径;将齿轮零件装夹到五轴数控加工中心上,通过在线测量采集齿轮的实际位置和形状信息;将测量点数据代入到位置配准算法中,计算得到零件从当前实际装夹位置到所期望的理论装夹位置之间的刚体变换;将该刚体变换作用到导入的理论刀路中,从而得到实际位置的加工刀路;将实际加工刀路进行后置处理得到数控代码,并将数控程序传输给数控机床进行加工。
图1 技术开发流程关键技术研究创新团队通过对开发流程的梳理,确定了以下几项关键技术加以研究和掌握。
模型创建通过理论齿面建立的模型不能完全与实际加工齿面相符,用理论模型建立的倒角或圆角特征与实际齿轮会存在一定偏差,不能用于刀路轨迹的规划与自动加工。
要想得到与实际相符的准确齿面模型,只能采取逆向建模的方式实现。
逆向建模的常用方式有两种,一种是采用光学扫描建模,另一种是采用齿面实测数据导入专用建模软件建模。
螺旋锥齿轮知识
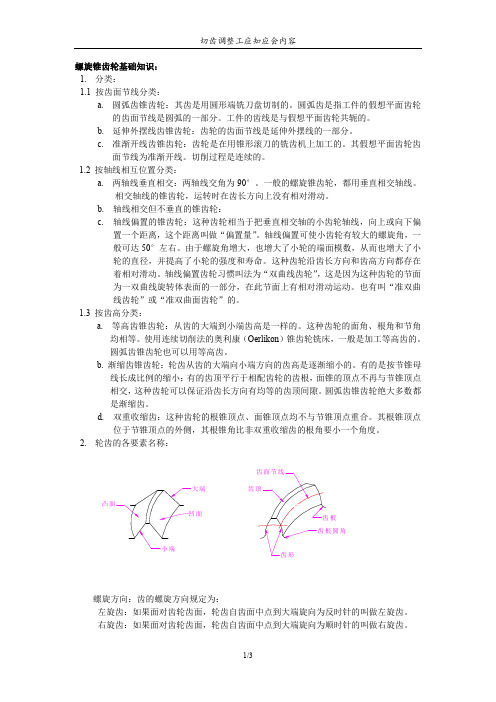
螺旋锥齿轮基础知识:1.分类:1.1 按齿面节线分类:a.圆弧齿锥齿轮:其齿是用圆形端铣刀盘切制的。
圆弧齿是指工件的假想平面齿轮的齿面节线是圆弧的一部分。
工件的齿线是与假想平面齿轮共轭的。
b.延伸外摆线齿锥齿轮:齿轮的齿面节线是延伸外摆线的一部分。
c.准渐开线齿锥齿轮:齿轮是在用锥形滚刀的铣齿机上加工的。
其假想平面齿轮齿面节线为准渐开线。
切削过程是连续的。
1.2 按轴线相互位置分类:a. 两轴线垂直相交:两轴线交角为90°。
一般的螺旋锥齿轮,都用垂直相交轴线。
相交轴线的锥齿轮,运转时在齿长方向上没有相对滑动。
b.轴线相交但不垂直的锥齿轮:c.轴线偏置的锥齿轮:这种齿轮相当于把垂直相交轴的小齿轮轴线,向上或向下偏置一个距离,这个距离叫做“偏置量”。
轴线偏置可使小齿轮有较大的螺旋角,一般可达50°左右。
由于螺旋角增大,也增大了小轮的端面模数,从而也增大了小轮的直径,并提高了小轮的强度和寿命。
这种齿轮沿齿长方向和齿高方向都存在着相对滑动。
轴线偏置齿轮习惯叫法为“双曲线齿轮”,这是因为这种齿轮的节面为一双曲线旋转体表面的一部分,在此节面上有相对滑动运动。
也有叫“准双曲线齿轮”或“准双曲面齿轮”的。
1.3 按齿高分类:a. 等高齿锥齿轮:从齿的大端到小端齿高是一样的。
这种齿轮的面角、根角和节角均相等。
使用连续切削法的奥利康(Oerlikon)锥齿轮铣床,一般是加工等高齿的。
圆弧齿锥齿轮也可以用等高齿。
b. 渐缩齿锥齿轮:轮齿从齿的大端向小端方向的齿高是逐渐缩小的。
有的是按节锥母线长成比例的缩小;有的齿顶平行于相配齿轮的齿根,面锥的顶点不再与节锥顶点相交,这种齿轮可以保证沿齿长方向有均等的齿顶间隙。
圆弧齿锥齿轮绝大多数都是渐缩齿。
d.双重收缩齿:这种齿轮的根锥顶点、面锥顶点均不与节锥顶点重合。
其根锥顶点位于节锥顶点的外侧,其根锥角比非双重收缩齿的根角要小一个角度。
2.轮齿的各要素名称:螺旋方向:齿的螺旋方向规定为:左旋齿:如果面对齿轮齿面,轮齿自齿面中点到大端旋向为反时针的叫做左旋齿。
- 1、下载文档前请自行甄别文档内容的完整性,平台不提供额外的编辑、内容补充、找答案等附加服务。
- 2、"仅部分预览"的文档,不可在线预览部分如存在完整性等问题,可反馈申请退款(可完整预览的文档不适用该条件!)。
- 3、如文档侵犯您的权益,请联系客服反馈,我们会尽快为您处理(人工客服工作时间:9:00-18:30)。
传 统 的螺 旋 锥 齿 轮 加 _ r 方 法 通 常 是 首 先 按 照 冈 纸 要 求 加 工 大 轮, 然后 通 过 磨 捌 枢小 轮 的齿 面进 行 啮 合 试验 直 至 印 痕 区 符合 图 纸要求 , 肌_ r 疗 法 中 主要 的 缺 点 包 括 : ( I ) 加 工 效 率低 : 印 痕 调 整 的过程较为复杂 , 对 操 作 者 的 技 能 要求 比较 高 , 往 往 要 根 据 印痕 的 实 际情 况 相l h l l  ̄ T 经 验 确定 调整 参 数 , 调 整 周 期 长 。加 工 程 序 不能 同 化, 每次J J l 1 ‘ 1 鄙 需 要重 新 调 整 。 尤其 不 能满 足 如 现代 工 业 多 型号 、 小 批 量 的 发腱 趋势 ( 2 ) 加_ r 精度低: 依靠 操 作 人 员的 经验 和 技 能很 难 稳 定 的制 造 … 高精 度 的零 件 , 而目 . 这 种 方 式 不符 合 现 代 化 加 工技 术 的 发展 趋 势 ( 3 ) 齿 州/ f 统一 : 传 统 的 螺旋 锥 齿轮 为 配对 加 工 , 在 使 J H 过程中 『 』 I 1 其 中 一 个 齿 轮 报废 ,则 相 配 齿 轮 通 常 情 况 下 也 同时 报 废, 因为 小 同批 次 加 1 问件 号零 件 的 齿 面不 间 目前 欧 荚 发达 围家 应 用 较 为 广 泛 的 是 螺 旋 锥 齿 轮 的数 字 化 加 T 方法且应J 1 J 的 已 经 很成 熟 , 该 技 术 有 高效 率 、 高 合 格 率 和 高 精 度 以及较 好 的 精 度稳 定 性 车 1 J 一致性等优点 , 能 够避 免 传 统 加 工 方法 产 生的弊端 , l J } j i 『 , 我 螺 旋 锥 齿 轮 的数 字 化 加 l I 技 术 正 在 逐 步取 代 传统的加 r : 疗法: 1 . 2 螺旋 锥 齿 轮数 字 化 加 I 过 程 关键 技 术 螺 旋 锥 街轮数 字 化 加 T的 目标是 实现 齿 轮 的 设计 _ 】 I 、 制造l : I 和榆 测【 l 整 个 过 协 同 , 以实 现 螺 旋 锥 街 轮 的 高效 、 高 精 度 制造 技 术 , 螺 旋 锥 齿 轮数 宇 化 加 体过 程 : 根 据 图纸 建 模 一 模 拟 仿 真 得 到 印痕 一 得 到 加 1 : 参数一 加l 1 零 件一 测量实际齿面一 与 标 准 齿 轮 齿 面 进 行 比 较一 调整J J l 】 T 参数一 分 析 比较 印痕 一 调整加二 r 参 数一 反 复 调整 直 至 得 到 合格 印痕 。 首 先进 行螺 旋锥 轮 齿 面 的 i维 精确 建 模 , 目前在 工 程 化 中应 『 H 较 广 泛 的 如 克林 n 1 格的 K I M O S ,格 里森 的 G — A G E等 专 用 软 件 , 有 的研 究院 校 也使 H 】 U G、 C A T I A等 软 件 , 根 据设 计 图 纸 参 数 实现 其 建 模 一模 建立 后 即 可以根 据 设 计 图 纸要 求 实 现 印 痕 的模 拟 仿 真 , 包 括 齿 面接 触 分 析和 加 载后 齿 面接 触 分 析 . 得 到合 格 的 印 痕 后 即定 义陔齿 面 即为理 论 齿 向 同时 还 可 以通 过 数 字化 的 方式 自动 获取 加 ’ 1 此齿 面对 应 的 调整 , 包括 机 床 加 T 参数 和 刀具 设 计 参数 等 。 建模 过 程 中涉 及 剑理 沦齿 i f I = 『 、 实 测 齿 面 和 形貌 图 的 概 念 , 在 齿 面检测 后 可 以 获 得实 测 齿 面数 据 , 进 一 步 同 理论 齿 面 对 比得 到 齿 面 形貌冈 , 然 后 根据 形 貌榆 测 数 据 调 整 加 T 参 数 . 目前 常 用 的齿 面形 貌 冈 通 常 是 整 个 内 面 取 9列 5行 共 4 5个 点 来 表 示 齿 面 的 形态 ,
科技创新与应用 I 2 0 1 5 年 第1 4 期
工 业 技 术
螺 旋 锥 齿轮 数 字化制 造 过程 关键 技术概 述
王 增 强 聂 峻 峰 赵 兴 福 张彦 飞
( 哈 尔滨 东安发动机( 集团) 有限公司 , 黑龙江 哈 尔滨 l 5 0 0 0 0 )
摘 要: 螺旋 锥 齿轮 应 用 广 泛 , 但 随着 工 业发 展 , 对 其 制造 精 度 的要 求也越 来越 高 , 目前齿 面误 差 可 达 0 . 0 0 5 am, r 传统的h_ r - 方法 由 于质 量 不稳 定 、 精 度低 、 一致性差 、 效率低等原因, 正逐 步被 先 进 的 螺旋 锥 齿 轮 数 字化 加 工技 术 所取 代 。 齿 面的 数 字 化加 工过
程 中涉及到的关键技术 包括 : 螺旋锥齿轮数字化建模 、 印痕数字化模拟仿 真、 加工参数的智能获取和调整以及数 字化 检测技术
等 关键词: 螺 旋锥 齿轮 ; 数 字化 ; h_ z - ; 检 测
1 慨 述
1 . 1螺 旋 锥 轮 J Leabharlann f 】 】 技 术发 肥 趋势
标准齿轮中的 4 5 个 坐 标点 是通 过 啮 合 仿 真得 到 合 格 印痕 后 对 应 的 齿 面的 坐 标 , 可 以认 为 是 理 论 坐标 。 进 行 齿 面 I ^ 标 点 测 量 时
如图 1
同样使用数字化的手段 , 使用 坐标或齿轮专用测量机 往进行相应 的模块 升 级 后 可 以读 取标 准 齿 轮 的模 型 , 『 1 动生 成 检测 程 序 并 生 成
更 精 确 的检 测 报告 , 如图 2 。事 实 上 , 离 线 榆测 编 程技 术最 近几 年 嘘 用 推 广 的较 为 广 泛 , 如离 心 叶 轮 、 大 型零 件 的复 杂 曲 面 等检 测 , 应 用 这 种 检测 方 法 不 仅提 高 了检 测 效 率 , 在 提 高零 件 的 制 造精 度 方 面 起 到 重要 作 用 。