6063铝合金型材挤压工艺的现状及完善改进方法_韦略
铝合金挤压型材强度影响因素及措施分析

铝合金挤压型材强度影响因素及措施分析6063铝合金型材是门窗、幕墙理想的结构和装饰材料,随着门窗、幕墙行业的发展,对6063铝合金型材的力学性能提出了更高的要求。
高强度的型材可减低设计壁厚,减少结构重量,更受市场欢迎。
6063铝合金系AI—Mg—Si系列可热处理强化型铝合金,塑性高,可高速挤压成断面复杂、壁厚各异的型材。
淬火温度宽,淬火敏感性低.可实现在线风冷强制淬火,经人工时效后有中等强度。
挤压后型材表面光洁,极易阳极氧化和着色,还可生产电泳、喷涂、氟碳喷漆、木纹、断桥隔热等型材,因此在建筑型材中具有垄断地位,在我国经济的快速发展,尤其是房地产市场的高速发展中得到极广泛的应用。
在Al-Mg-Si系合金中,主要强化相是Mg2Si,合金在淬火时,固溶于基体中的Mg2Si 越多,时效后的型材强度就越高,反之,则越低。
在实际生产中,铝合金挤压型材经常出现硬度偏低或不达标的现象出现。
影响型材硬度强度的原因是多方面的(见鱼骨图),下面结合我厂的生产实际,从工艺、设备、操作等方面分析和总结影响6063铝合金型材强度的因素及采取的措施。
1、6063铝合金化学成分的控制国家标准GB/T 3190-2008和“和平”公司内控标准对6063铝合金的化学成分规定如表l所示。
表1 6063铝合金化学成分(质量分数%)该合金主要元素足Mg和Si。
他们在合金中形成金属化合物Mg:Si是合会的主要强化相。
Mg2Si中Mg和Si的比为1.73。
当Mg:Si>1.73时,尚有过剩的Mg存在,它会显著降低Mg2Si相在固态铝中的溶解度,由于过剩Mg的这种影响,使Mg2Si相在热处理时的强化效果显著降低,从而影响型材的力学性能。
合金中Si含量的增加可以改善铸造性能和焊接性能。
当Mg:Si<1.73时,合金中有过剩Si存在,它可以与铝中的其它杂质Fe、Mn等生成化合物,增加强化效果。
因此对强度要求较高时,往往合金中控制过剩Si。
6063铝合金型材挤压工艺对型材表面质量的影响论文

降低、 不均匀, 在金属通过模孔时产生的摩擦力较大, 金属之间产生严重的流速不均, 也会造成表面挤压条
纹和表面粗糙严重。只要把模具的加热温度降低, 加
3 表面质量缺陷的产生原因
31 铝合金型材表面夹渣、 . 划痕的产生原因 一般认为型材表面夹渣及划痕是铸锭夹渣或夹 灰所造成的, 而实际生产过程中, 夹渣和划痕的产生
K w r . 5 1 G D cn rrpl cdr e o s D S03 A ; v t; e e y d C 0 ; o ee u o s
1 前
言
与挤压工艺控制不严有关。挤压时, 必须严格控制铸 锭表面洁净。如果铸锭表面带有一些废的铝屑或杂 质清理不净, 在高温挤压时这些杂质浮在型材表面或 挂在模具工作带上, 必将造成型材表面夹渣或划痕。 正常挤压时, 每天应采用专用清理垫, 把挤压筒内壁 的一些杂质清理干净, 以防止这些杂质卷人模孔中, 挂在模具的工作带上或浮在型材表面上, 造成型材表 面的划痕和夹渣。再者, 挤压铸锭的压余控制, 压余 过小, 一部分残余的氧化皮及杂质会流人模孔中, 在 连续挤压时也会使型材表面划伤或造成夹渣。严重
量查起。有些表面质量问题是能够解决的, 但有些表 面质量问题单从铸锭和模具去查找原因是解决不了 的, 因为影响型材表面质量的重要因素之一与型材的 挤压工艺有着直接关系。根据我公 司几年来的挤压 生产经验, 从挤压工艺方面进行分析并找出影响型材 表面质量的原因效果显著。下面简要论述挤压工艺 对型材表面质量的影响。
(en Dn a im .L .Tn h , i , 1 , a Bjg g A m u C ,t ,o zu Big 1 1 Ci ) i oy l n o d i u g o en 0 3 h j 1 n
6063铝合金挤压型材觉缺陷及其解决方法(精)

6063铝合金挤压型材觉缺陷及其解决方法6063铝合金型材以其良好的塑性、适中的热处理强度、良好的焊接性能以及阳极氧化处理后表面华丽的色泽等诸多优点而被广泛应用。
但在生产过程中经常会出现一些缺陷而致使产品质量低下,成品率降低,生产成本增加,效益下降,最终导致企业的市场竞争能力下降。
因此,从根源上着手解决6063铝合金挤压型材的缺陷问题是企业提高自身竞争力的一个重要方面。
笔者根据多年的铝型材生产实践,在此对6063铝合金挤压型材常见缺陷及其解决办法作一总结,和众多同行交流,以期相互促进。
1 划、擦、碰伤划伤、擦伤、碰伤是当型材从模孔流出以及在随后工序中与工具、设备等相接触时导致的表面损伤。
1.1主要原因①铸锭表面附着有杂物或铸锭成分偏析。
铸锭表面存在大量偏析浮出物而铸锭又未进行均匀化处理或均匀化处理效果不好时,铸锭内存在一定数量的坚硬的金属颗粒,在挤压过程中金属流经工作带时,这些偏浮出物或坚硬的金属颗粒附着在工作带表面或对工作带造成损伤,最终对型材表面造成划伤;②模具型腔或工作带上有杂物,模具工作带硬度较低,使工作带表面在挤压时受伤而划伤型材;③出料轨道或摆床上有裸露的金属或石墨条内有较硬的夹杂物,当其与型材接触时对型材表面造成划伤;④在叉料杆将型材从出料轨道上送到摆床上时,由于速度过快造成型材碰伤;⑤在摆床上人为拖动型材造成擦伤;⑥在运输过程中型材之间相互摩擦或挤压造成损伤。
1.2解决办法①加强对铸锭质量的控制;②提高修模质量,模具定期氮化并严格执行氮化工艺;③用软质毛毡将型材与辅具隔离,尽量减少型材与辅具的接触损伤;④生产中要轻拿轻放,尽量避免随意拖动或翻动型材;⑤在料框中合理摆放型材,尽量避免相互摩擦。
2机械性能不合格2.1 主要原因①挤压时温度过低,挤压速度太慢,型材在挤压机的出口温度达不到固溶温度,起不到固溶强化作用;②型材出口处风机少,风量不够,导致冷却速度慢,不能使型材在最短的时间内降到20℃以下,使粗大的Mg2Si过早析出,从而使固溶相减少,影响了型材热处理后的机械性能;③铸锭成分不合格,铸锭中的Mg、Si含量达不到标准要求;④铸锭未均匀化处理,使铸锭组织中析出的Mg2Si相我法在挤压的较短时间内重新固溶,造成固溶不充分而影响了产品性能;⑤时效工艺不当、热风循环不畅或热电偶安装位置不正确,导致时效不充分或过时效。
6063铝合金挤压型材质量影响因素及对策
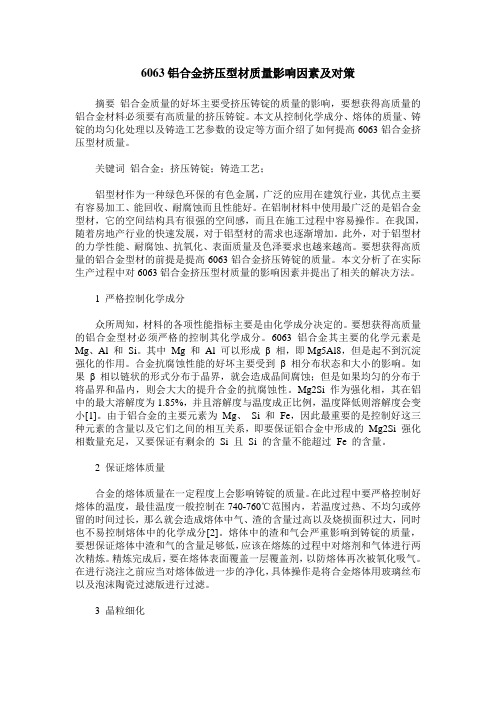
6063铝合金挤压型材质量影响因素及对策摘要铝合金质量的好坏主要受挤压铸锭的质量的影响,要想获得高质量的铝合金材料必须要有高质量的挤压铸锭。
本文从控制化学成分、熔体的质量、铸锭的均匀化处理以及铸造工艺参数的设定等方面介绍了如何提高6063铝合金挤压型材质量。
关键词铝合金;挤压铸锭;铸造工艺;铝型材作为一种绿色环保的有色金属,广泛的应用在建筑行业,其优点主要有容易加工、能回收、耐腐蚀而且性能好。
在铝制材料中使用最广泛的是铝合金型材,它的空间结构具有很强的空间感,而且在施工过程中容易操作。
在我国,随着房地产行业的快速发展,对于铝型材的需求也逐渐增加。
此外,对于铝型材的力学性能、耐腐蚀、抗氧化、表面质量及色泽要求也越来越高。
要想获得高质量的铝合金型材的前提是提高6063铝合金挤压铸锭的质量。
本文分析了在实际生产过程中对6063铝合金挤压型材质量的影响因素并提出了相关的解决方法。
1 严格控制化学成分众所周知,材料的各项性能指标主要是由化学成分决定的。
要想获得高质量的铝合金型材必须严格的控制其化学成分。
6063铝合金其主要的化学元素是Mg、Al 和Si。
其中Mg 和Al 可以形成β 相,即Mg5Al8,但是起不到沉淀强化的作用。
合金抗腐蚀性能的好坏主要受到β 相分布状态和大小的影响。
如果β 相以链状的形式分布于晶界,就会造成晶间腐蚀;但是如果均匀的分布于将晶界和晶内,则会大大的提升合金的抗腐蚀性。
Mg2Si 作为强化相,其在铝中的最大溶解度为1.85%,并且溶解度与温度成正比例,温度降低则溶解度会变小[1]。
由于铝合金的主要元素为Mg、Si 和Fe,因此最重要的是控制好这三种元素的含量以及它们之间的相互关系,即要保证铝合金中形成的Mg2Si 强化相数量充足,又要保证有剩余的Si 且Si 的含量不能超过Fe 的含量。
2 保证熔体质量合金的熔体质量在一定程度上会影响铸锭的质量。
在此过程中要严格控制好熔体的温度,最佳温度一般控制在740-760℃范围内,若温度过热、不均匀或停留的时间过长,那么就会造成熔体中气、渣的含量过高以及烧损面积过大,同时也不易控制熔体中的化学成分[2]。
6063挤压型材条纹缺陷产生原因分析及解决措施
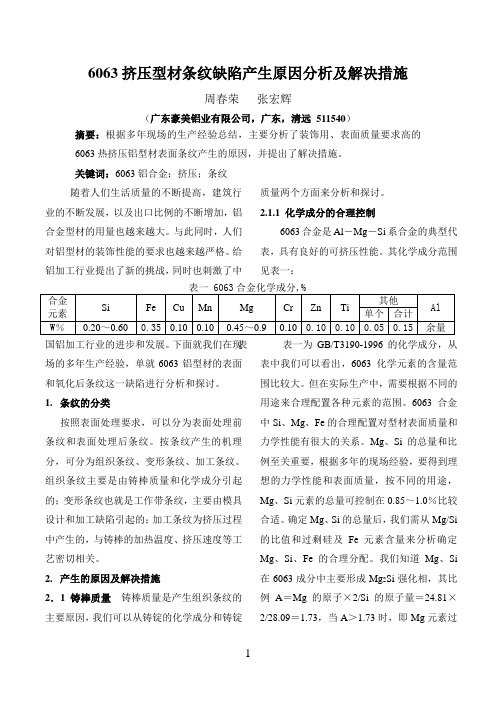
6063挤压型材条纹缺陷产生原因分析及解决措施周春荣张宏辉(广东豪美铝业有限公司,广东,清远511540)摘要:根据多年现场的生产经验总结,主要分析了装饰用、表面质量要求高的6063热挤压铝型材表面条纹产生的原因,并提出了解决措施。
关键词:6063铝合金;挤压;条纹随着人们生活质量的不断提高,建筑行业的不断发展,以及出口比例的不断增加,铝合金型材的用量也越来越大。
与此同时,人们对铝型材的装饰性能的要求也越来越严格。
给铝加工行业提出了新的挑战,同时也刺激了中国铝加工行业的进步和发展。
下面就我们在现场的多年生产经验,单就6063铝型材的表面和氧化后条纹这一缺陷进行分析和探讨。
1.条纹的分类按照表面处理要求,可以分为表面处理前条纹和表面处理后条纹。
按条纹产生的机理分,可分为组织条纹、变形条纹、加工条纹。
组织条纹主要是由铸棒质量和化学成分引起的;变形条纹也就是工作带条纹,主要由模具设计和加工缺陷引起的;加工条纹为挤压过程中产生的,与铸棒的加热温度、挤压速度等工艺密切相关。
2.产生的原因及解决措施2.1 铸棒质量铸棒质量是产生组织条纹的主要原因,我们可以从铸锭的化学成分和铸锭质量两个方面来分析和探讨。
2.1.1 化学成分的合理控制6063合金是Al-Mg-Si系合金的典型代表,具有良好的可挤压性能。
其化学成分范围见表一:表表一为GB/T3190-1996的化学成分,从表中我们可以看出,6063化学元素的含量范围比较大。
但在实际生产中,需要根据不同的用途来合理配置各种元素的范围。
6063合金中Si、Mg、Fe的合理配置对型材表面质量和力学性能有很大的关系。
Mg、Si的总量和比例至关重要,根据多年的现场经验,要得到理想的力学性能和表面质量,按不同的用途,Mg、Si元素的总量可控制在0.85~1.0%比较合适。
确定Mg、Si的总量后,我们需从Mg/Si的比值和过剩硅及Fe元素含量来分析确定Mg、Si、Fe的合理分配。
铝合金挤压提高成品率的方法

铝合金挤压提高成品率的方法
以下是提高铝合金挤压成品率的几种方法:
1. 控制挤压温度:合适的挤压温度能够使铝合金更容易挤压,降低挤压力,减少断裂和裂纹的风险。
同时,适当的挤压温度还可以改善铝合金的塑性和变形能力。
2. 优化挤压工艺参数:合理的挤压速度、挤压力以及挤压模具的设计能够提高挤压成品率。
通过调整挤压速度和挤压力,可以控制材料变形的方式和程度,减小变形应力和应变速率之间的不均匀分布,使得材料更加均匀地流动,减少裂纹和变形的风险。
3. 合适的模具设计:合适的模具设计能够减少挤压时的摩擦和变形,提高挤压成品率。
模具应该具有充分的冷却功能,以保持合适的挤压温度,并减少模具表面和挤出材料之间的摩擦,避免模具细小孔洞或凹痕对成品质量的影响。
4. 精细化挤压控制:采用先进的挤压控制系统,可以实时监测挤压过程中的参数,如温度、压力、速度等,并进行自动调整。
通过精细化的挤压控制,可以有效降低变形应力和变形速率,提高挤压成品率。
5. 优化铝合金配料:选择合适的铝合金配料,控制合金成分和杂质含量,可以提高铝合金的塑性和变形能力,降低挤压力和变形应力,减少成品的裂纹和变形问题。
综上所述,提高铝合金挤压成品率的方法包括控制挤压温度、优化挤压工艺参数、合适的模具设计、精细化挤压控制和优化铝合金配料等。
通过综合应用上述方法,可以提高铝合金挤压的成品率,降低废品率,提高生产效益。
6063铝合金挤压型材觉缺陷及其解决方法

6063铝合金挤压型材觉缺陷及其解决方法
1.毛刺:毛刺是挤压型材表面的突出物,会影响外观和触感。
毛刺的
主要原因是金属挤压时的不均匀变形和模具壁口的磨损。
解决方法包括增
加材料的充填比例,优化挤压工艺参数,增加模具壁口的滑移润滑剂等。
2.断裂:断裂是挤压型材在生产和使用过程中出现的一个严重问题。
断裂的原因可以是材料本身的强度不足、挤压工艺参数设置不当、模具设
计不合理等。
解决方法包括选择合适的6063铝合金型材,优化挤压工艺
参数,加强模具的冷却和加热控制等。
3.冷裂纹:冷裂纹是在挤压型材的表面或内部出现的长而细的裂纹。
冷裂纹的出现与材料的热处理过程和冷却速度不当有关。
解决方法包括优
化挤压工艺参数,控制冷却速度,合理设计材料的热处理过程等。
4.物理性能不稳定:6063铝合金挤压型材的物理性能,如硬度、抗
拉强度、延展性等,可能存在不稳定的情况。
这可能是由于挤压工艺中的
应力集中和不均匀变形导致的。
解决方法包括优化挤压工艺参数,增加冷
却控制,合理设计模具结构等。
5.起皮:起皮是指挤压型材表面出现的局部脱层现象,降低了型材的
使用寿命。
起皮的原因主要是模具的磨损和使用不当。
解决方法包括定期
检查和维护模具,增加模具的使用寿命,减少起皮现象的发生。
总之,6063铝合金挤压型材的觉缺陷可能会影响其质量和使用寿命。
通过合理选择材料、优化挤压工艺参数、改进模具设计和加强质量控制等
措施,可以有效地解决这些问题,提高挤压型材的质量和性能。
6063铝合金壳体系列毛坯冷挤压工艺研究

Keywords : Cold Extrusion; Aluminum Alloy; Orthogonal Experiment; Finite Element Simulation; Mold Design
IV
南昌航空大学硕士学位论文原创性声明
本人郑重声明: 所呈交的硕士学位论文, 是我个人在导师指导下, 在南昌航空大学攻读硕士学位期间独立进行研究工作所取得的成果。 尽我所知, 论文中除已注明部分外不包含他人已发表或撰写过的研究 成果。对本文的研究工作做出重要贡献的个人和集体,均已在文中作 了明确地说明并表示了谢意。本声明的法律结果将完全由本人承担。 学位论文作者签名: 日 期:
1.2 挤压成形工艺的概述和发展现状
1.2.1 挤压工艺概述 [1~5]
挤压工艺,是指将金属毛坯放入预留有孔隙的模具模腔内,在强大的压力和 一定的速度作用下,迫使金属从模腔中挤出,从而获得所需形状、尺寸以及具有 一定力学性能挤压件的一种压力加工成形方法。挤压技术作为一种高效、优质、 低消耗的少无切削加工工艺,在金属材料的塑性加工中获得了迅速发展,目前在
南昌航空大学 硕士学位论文 6063铝合金壳体系列毛坯冷挤压工艺研究 姓名:王孝文 申请学位级别:硕士 专业:材料加工工程 指导教师:王家宣 20070601
摘要
本文对铝合金 6063 的冷挤压工艺进行了研究,研究了模具表面粗糙度、冷 挤压速度、润滑剂种类、挤压材料状态四个工艺参数对冷挤压工艺的影响,通过 正交实验优化了铝合金 6063 的冷挤压工艺参数。此外利用有限元模拟软件 DEFORM 对铝合金 6063 冷挤压过程进行模拟,通过和实验结果相比较获得逼近 实际的边界条件参数, 利用验证的边界条件进一步对传感器壳体和螺塞盖的挤压 工艺进行模拟,分析成形过程中可能产生缺陷的因素,确定了成形工艺方案。 实验结果表明:铝合金 6063 冷挤压的最佳工艺方案为:快速退火的热处理 工艺方案,HB32 左右的挤压材料硬度,选用硬脂酸锌润滑剂,同时要求模具表 面硬度为 HRC60~62,表面粗糙度在 Ra0.4 。这种情况下冷挤压力最小,材料表面 润滑情况最好。 对于杯-杯状的具有阶梯孔的传感器壳体和杯-杆状的螺塞盖,利用实验所 得优化挤压参数等数据和有限元模拟相比较,得到合理的有限元分析边界条件, 分析出产品挤压力和挤压过程中可能出现的工艺问题,并找到解决方案。由模拟 数值和理论计算相比较分析理论计算出现误差的原因。 利用实验和有限元模拟为理论设计提供了更加符合实际工程应用的依据,测 得的挤压力和实际挤压力相差为 0.7%,保证了模具的经济性和安全性,采用通 用模具结构设计,简化了设计工作量,节约了模具成本。本研究结果可以用来指 导实际生产。
AL6063铝型材挤压变形机理研究及工艺参数优化
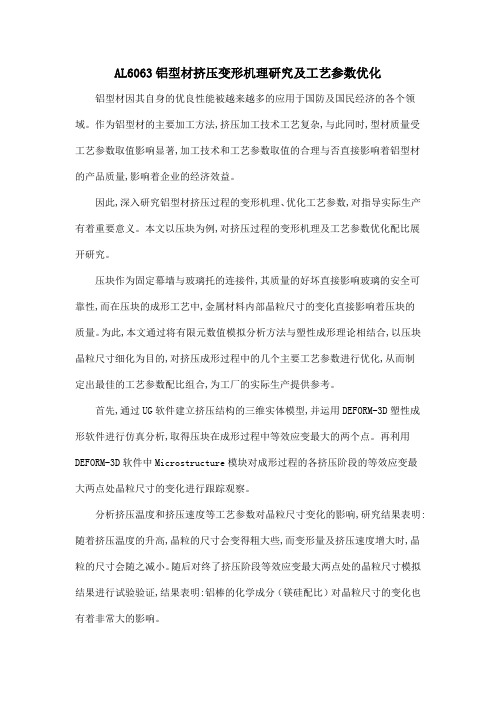
AL6063铝型材挤压变形机理研究及工艺参数优化铝型材因其自身的优良性能被越来越多的应用于国防及国民经济的各个领域。
作为铝型材的主要加工方法,挤压加工技术工艺复杂,与此同时,型材质量受工艺参数取值影响显著,加工技术和工艺参数取值的合理与否直接影响着铝型材的产品质量,影响着企业的经济效益。
因此,深入研究铝型材挤压过程的变形机理、优化工艺参数,对指导实际生产有着重要意义。
本文以压块为例,对挤压过程的变形机理及工艺参数优化配比展开研究。
压块作为固定幕墙与玻璃托的连接件,其质量的好坏直接影响玻璃的安全可靠性,而在压块的成形工艺中,金属材料内部晶粒尺寸的变化直接影响着压块的质量。
为此,本文通过将有限元数值模拟分析方法与塑性成形理论相结合,以压块晶粒尺寸细化为目的,对挤压成形过程中的几个主要工艺参数进行优化,从而制定出最佳的工艺参数配比组合,为工厂的实际生产提供参考。
首先,通过UG软件建立挤压结构的三维实体模型,并运用DEFORM-3D塑性成形软件进行仿真分析,取得压块在成形过程中等效应变最大的两个点。
再利用DEFORM-3D软件中Microstructure模块对成形过程的各挤压阶段的等效应变最大两点处晶粒尺寸的变化进行跟踪观察。
分析挤压温度和挤压速度等工艺参数对晶粒尺寸变化的影响,研究结果表明:随着挤压温度的升高,晶粒的尺寸会变得粗大些,而变形量及挤压速度增大时,晶粒的尺寸会随之减小。
随后对终了挤压阶段等效应变最大两点处的晶粒尺寸模拟结果进行试验验证,结果表明:铝棒的化学成分(镁硅配比)对晶粒尺寸的变化也有着非常大的影响。
然后,依据各工艺参数对晶粒尺寸变化的模拟结果,结合实际生产情况,采用正交试验方法对成形过程中影响压块晶粒尺寸变化的主要工艺参数进行优化。
选取铝棒的化学成分(镁硅配比)、挤压温度、挤压速度、挤压筒温、模具预热温度作为试验因素,设计了五因素四水平正交实验表L<sub>16</sub>(4<sup>5</sup>),通过对试验结果进行极差分析和方差分析,得出工艺参数对晶粒尺寸变化影响的主次顺序,并获得最优配比组合。
铝合金挤压型材常见缺陷及其解决办法
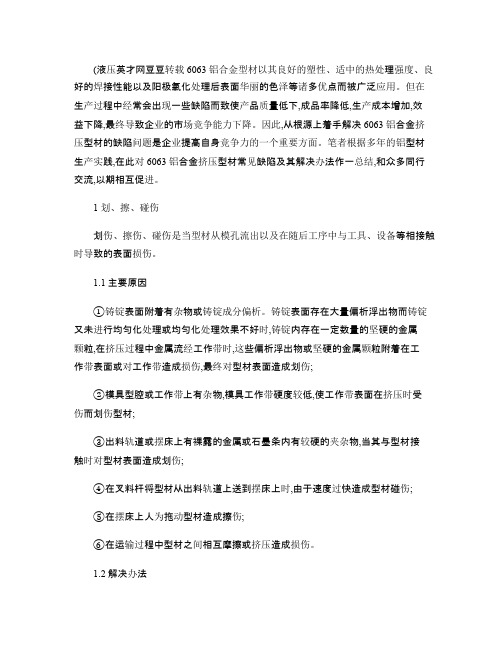
(液压英才网豆豆转载6063铝合金型材以其良好的塑性、适中的热处理强度、良好的焊接性能以及阳极氧化处理后表面华丽的色泽等诸多优点而被广泛应用。
但在生产过程中经常会出现一些缺陷而致使产品质量低下,成品率降低,生产成本增加,效益下降,最终导致企业的市场竞争能力下降。
因此,从根源上着手解决6063铝合金挤压型材的缺陷问题是企业提高自身竞争力的一个重要方面。
笔者根据多年的铝型材生产实践,在此对6063铝合金挤压型材常见缺陷及其解决办法作一总结,和众多同行交流,以期相互促进。
1划、擦、碰伤划伤、擦伤、碰伤是当型材从模孔流出以及在随后工序中与工具、设备等相接触时导致的表面损伤。
1.1主要原因①铸锭表面附着有杂物或铸锭成分偏析。
铸锭表面存在大量偏析浮出物而铸锭又未进行均匀化处理或均匀化处理效果不好时,铸锭内存在一定数量的坚硬的金属颗粒,在挤压过程中金属流经工作带时,这些偏析浮出物或坚硬的金属颗粒附着在工作带表面或对工作带造成损伤,最终对型材表面造成划伤;②模具型腔或工作带上有杂物,模具工作带硬度较低,使工作带表面在挤压时受伤而划伤型材;③出料轨道或摆床上有裸露的金属或石墨条内有较硬的夹杂物,当其与型材接触时对型材表面造成划伤;④在叉料杆将型材从出料轨道上送到摆床上时,由于速度过快造成型材碰伤;⑤在摆床上人为拖动型材造成擦伤;⑥在运输过程中型材之间相互摩擦或挤压造成损伤。
1.2解决办法①加强对铸锭质量的控制;②提高修模质量,模具定期氮化并严格执行氮化工艺;③用软质毛毡将型材与辅具隔离,尽量减少型材与辅具的接触损伤;④生产中要轻拿轻放,尽量避免随意拖动或翻动型材;⑤在料框中合理摆放型材,尽量避免相互摩擦。
2机械性能不合格:2.1主要原因①挤压时温度过低,挤压速度太慢,型材在挤压机的出口温度达不到固溶温度,起不到固溶强化作用;②型材出口处风机少,风量不够,导致冷却速度慢,不能使型材在最短的时间内降到200℃以下,使粗大的Mg2Si过早析出,从而使固溶相减少,影响了型材热处理后的机械性能③铸锭成分不合格,铸锭中的Mg、Si含量达不到标准要求;④铸锭未均匀化处理,使铸锭组织中析出的Mg2Si相无法在挤压的较短时间内重新固溶,造成固溶不充分而影响了产品性能;⑤时效工艺不当、热风循环不畅或热电偶安装位置不正确,导致时效不充分或过时效。
铝合金挤压型材强度影响因素及措施分析

铝合金挤压型材强度影响因素及措施分析6063铝合金型材是门窗、幕墙理想的结构和装饰材料,随着门窗、幕墙行业的发展,对6063铝合金型材的力学性能提出了更高的要求。
高强度的型材可减低设计壁厚,减少结构重量,更受市场欢迎。
6063铝合金系AI—Mg—Si系列可热处理强化型铝合金,塑性高,可高速挤压成断面复杂、壁厚各异的型材。
淬火温度宽,淬火敏感性低.可实现在线风冷强制淬火,经人工时效后有中等强度。
挤压后型材表面光洁,极易阳极氧化和着色,还可生产电泳、喷涂、氟碳喷漆、木纹、断桥隔热等型材,因此在建筑型材中具有垄断地位,在我国经济的快速发展,尤其是房地产市场的高速发展中得到极广泛的应用。
在Al-Mg-Si系合金中,主要强化相是Mg2Si,合金在淬火时,固溶于基体中的Mg2Si 越多,时效后的型材强度就越高,反之,则越低。
在实际生产中,铝合金挤压型材经常出现硬度偏低或不达标的现象出现。
影响型材硬度强度的原因是多方面的(见鱼骨图),下面结合我厂的生产实际,从工艺、设备、操作等方面分析和总结影响6063铝合金型材强度的因素及采取的措施。
1、6063铝合金化学成分的控制国家标准GB/T 3190-2008和“和平”公司内控标准对6063铝合金的化学成分规定如表l所示。
表1 6063铝合金化学成分(质量分数%)该合金主要元素足Mg和Si。
他们在合金中形成金属化合物Mg:Si是合会的主要强化相。
Mg2Si中Mg和Si的比为1.73。
当Mg:Si>1.73时,尚有过剩的Mg存在,它会显著降低Mg2Si相在固态铝中的溶解度,由于过剩Mg的这种影响,使Mg2Si相在热处理时的强化效果显著降低,从而影响型材的力学性能。
合金中Si含量的增加可以改善铸造性能和焊接性能。
当Mg:Si<1.73时,合金中有过剩Si存在,它可以与铝中的其它杂质Fe、Mn等生成化合物,增加强化效果。
因此对强度要求较高时,往往合金中控制过剩Si。
铝合金挤压型材常见缺陷及其解决办法(精)
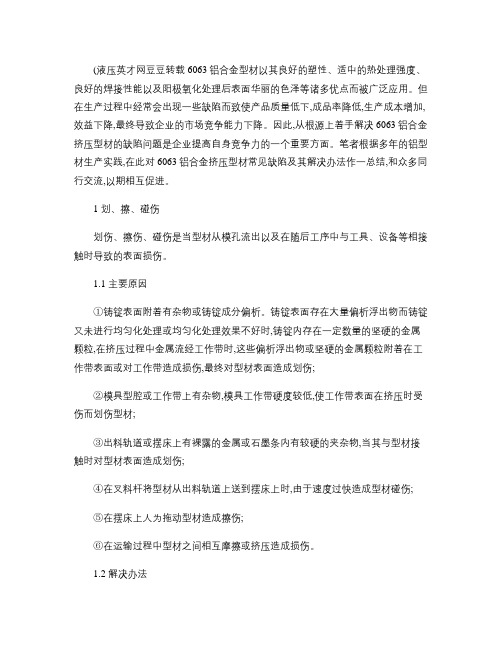
(液压英才网豆豆转载6063铝合金型材以其良好的塑性、适中的热处理强度、良好的焊接性能以及阳极氧化处理后表面华丽的色泽等诸多优点而被广泛应用。
但在生产过程中经常会出现一些缺陷而致使产品质量低下,成品率降低,生产成本增加,效益下降,最终导致企业的市场竞争能力下降。
因此,从根源上着手解决6063铝合金挤压型材的缺陷问题是企业提高自身竞争力的一个重要方面。
笔者根据多年的铝型材生产实践,在此对6063铝合金挤压型材常见缺陷及其解决办法作一总结,和众多同行交流,以期相互促进。
1 划、擦、碰伤划伤、擦伤、碰伤是当型材从模孔流出以及在随后工序中与工具、设备等相接触时导致的表面损伤。
1.1 主要原因①铸锭表面附着有杂物或铸锭成分偏析。
铸锭表面存在大量偏析浮出物而铸锭又未进行均匀化处理或均匀化处理效果不好时,铸锭内存在一定数量的坚硬的金属颗粒,在挤压过程中金属流经工作带时,这些偏析浮出物或坚硬的金属颗粒附着在工作带表面或对工作带造成损伤,最终对型材表面造成划伤;②模具型腔或工作带上有杂物,模具工作带硬度较低,使工作带表面在挤压时受伤而划伤型材;③出料轨道或摆床上有裸露的金属或石墨条内有较硬的夹杂物,当其与型材接触时对型材表面造成划伤;④在叉料杆将型材从出料轨道上送到摆床上时,由于速度过快造成型材碰伤;⑤在摆床上人为拖动型材造成擦伤;⑥在运输过程中型材之间相互摩擦或挤压造成损伤。
1.2 解决办法①加强对铸锭质量的控制;②提高修模质量,模具定期氮化并严格执行氮化工艺;③用软质毛毡将型材与辅具隔离,尽量减少型材与辅具的接触损伤;④生产中要轻拿轻放,尽量避免随意拖动或翻动型材;⑤在料框中合理摆放型材,尽量避免相互摩擦。
2机械性能不合格:2.1 主要原因①挤压时温度过低,挤压速度太慢,型材在挤压机的出口温度达不到固溶温度,起不到固溶强化作用;②型材出口处风机少,风量不够,导致冷却速度慢,不能使型材在最短的时间内降到200℃以下,使粗大的Mg2Si过早析出,从而使固溶相减少,影响了型材热处理后的机械性能③铸锭成分不合格,铸锭中的Mg、Si含量达不到标准要求;④铸锭未均匀化处理,使铸锭组织中析出的Mg2Si相无法在挤压的较短时间内重新固溶,造成固溶不充分而影响了产品性能;⑤时效工艺不当、热风循环不畅或热电偶安装位置不正确,导致时效不充分或过时效。
铝挤压产业发展现状及今后的努力方向
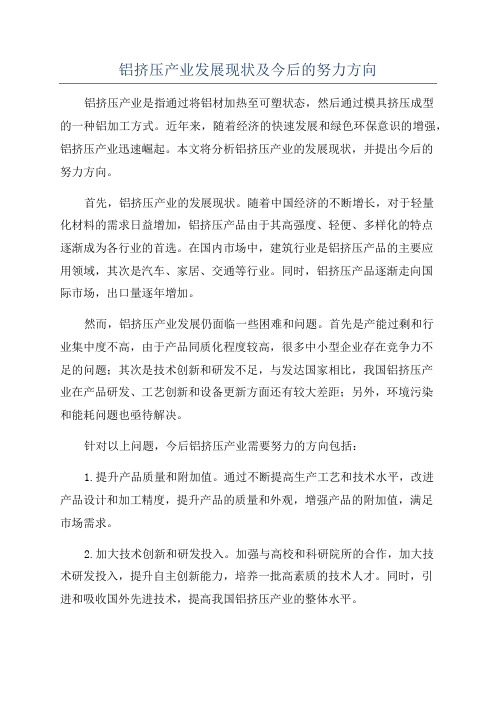
铝挤压产业发展现状及今后的努力方向铝挤压产业是指通过将铝材加热至可塑状态,然后通过模具挤压成型的一种铝加工方式。
近年来,随着经济的快速发展和绿色环保意识的增强,铝挤压产业迅速崛起。
本文将分析铝挤压产业的发展现状,并提出今后的努力方向。
首先,铝挤压产业的发展现状。
随着中国经济的不断增长,对于轻量化材料的需求日益增加,铝挤压产品由于其高强度、轻便、多样化的特点逐渐成为各行业的首选。
在国内市场中,建筑行业是铝挤压产品的主要应用领域,其次是汽车、家居、交通等行业。
同时,铝挤压产品逐渐走向国际市场,出口量逐年增加。
然而,铝挤压产业发展仍面临一些困难和问题。
首先是产能过剩和行业集中度不高,由于产品同质化程度较高,很多中小型企业存在竞争力不足的问题;其次是技术创新和研发不足,与发达国家相比,我国铝挤压产业在产品研发、工艺创新和设备更新方面还有较大差距;另外,环境污染和能耗问题也亟待解决。
针对以上问题,今后铝挤压产业需要努力的方向包括:1.提升产品质量和附加值。
通过不断提高生产工艺和技术水平,改进产品设计和加工精度,提升产品的质量和外观,增强产品的附加值,满足市场需求。
2.加大技术创新和研发投入。
加强与高校和科研院所的合作,加大技术研发投入,提升自主创新能力,培养一批高素质的技术人才。
同时,引进和吸收国外先进技术,提高我国铝挤压产业的整体水平。
3.推动行业整合和提高集中度。
加强行业协会的引导和组织,推动铝挤压行业的整合,提高行业集中度。
通过产业集群的形成,加强技术交流和协作。
4.加强环境保护和节约能源。
提高企业环保意识,加强环境管理,降低排放量。
加大投入,推广节能减排技术,提高生产效率,促进可持续发展。
5.拓展国际市场,加强品牌建设。
加大对外贸易和出口力度,拓展国际市场。
同时,加强品牌建设,提高产品在国际市场的竞争力。
总之,铝挤压产业在我国经济发展中起着重要的作用,随着经济的发展和人们对环保需求的增加,铝挤压产品的市场需求将持续增长。
6063型铝材常见不足及改善

6063型铝材常见不足之处6063铝合金型材以其良好的塑性、适中的热处理强度、良好的焊接性能以及阳极氧化处理后表面华丽的色泽等诸多优点而被广泛应用。
但在生产过程中经常会出现一些缺陷而致使产品质量低下,成品率降低,生产成本增加,效益下降,最终导致企业的市场竞争能力下降。
因此,从根源上着手解决6063铝合金挤压型材的缺陷问题是企业提高自身竞争力的一个重要方面。
笔者根据多年的铝型材生产实践,在此对6063铝合金挤压型材常见缺陷及其解决办法作一总结,和众多同行交流,以期相互促进。
1 划、擦、碰伤划伤、擦伤、碰伤是当型材从模孔流出以及在随后工序中与工具、设备等相接触时导致的表面损伤。
1.1 主要原因①铸锭表面附着有杂物或铸锭成分偏析。
铸锭表面存在大量偏析浮出物而铸锭又未进行均匀化处理或均匀化处理效果不好时,铸锭内存在一定数量的坚硬的金属颗粒,在挤压过程中金属流经工作带时,这些偏析浮出物或坚硬的金属颗粒附着在工作带表面或对工作带造成损伤,最终对型材表面造成划伤;②模具型腔或工作带上有杂物,模具工作带硬度较低,使工作带表面在挤压时受伤而划伤型材;③出料轨道或摆床上有裸露的金属或石墨条内有较硬的夹杂物,当其与型材接触时对型材表面造成划伤;④在叉料杆将型材从出料轨道上送到摆床上时,由于速度过快造成型材碰伤;⑤在摆床上人为拖动型材造成擦伤;⑥在运输过程中型材之间相互摩擦或挤压造成损伤。
1.2 解决办法①加强对铸锭质量的控制;②提高修模质量,模具定期氮化并严格执行氮化工艺;③用软质毛毡将型材与辅具隔离,尽量减少型材与辅具的接触损伤;④生产中要轻拿轻放,尽量避免随意拖动或翻动型材;⑤在料框中合理摆放型材,尽量避免相互摩擦。
2机械性能不合格2.1 主要原因①挤压时温度过低,挤压速度太慢,型材在挤压机的出口温度达不到固溶温度,起不到固溶强化作用;②型材出口处风机少,风量不够,导致冷却速度慢,不能使型材在最短的时间内降到200℃以下,使粗大的Mg2Si过早析出,从而使固溶相减少,影响了型材热处理后的机械性能;③铸锭成分不合格,铸锭中的Mg、Si含量达不到标准要求;④铸锭未均匀化处理,使铸锭组织中析出的Mg2Si相无法在挤压的较短时间内重新固溶,造成固溶不充分而影响了产品性能;⑤时效工艺不当、热风循环不畅或热电偶安装位置不正确,导致时效不充分或过时效。
6063铝合金连续挤压工艺研究_1
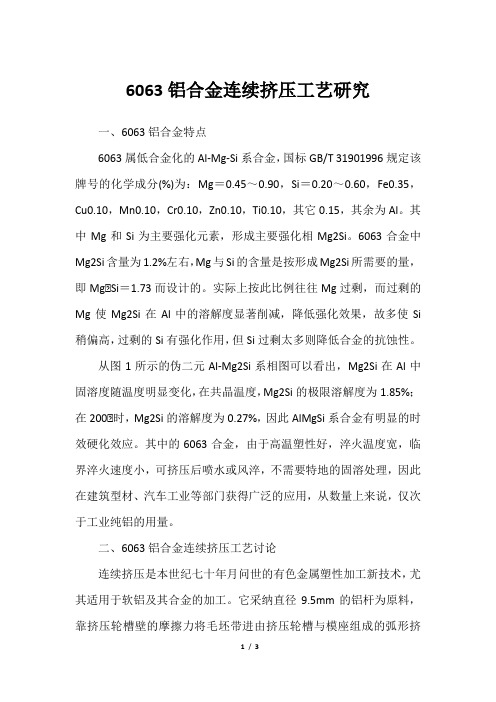
6063铝合金连续挤压工艺研究一、6063铝合金特点6063属低合金化的Al-Mg-Si系合金,国标GB/T 31901996规定该牌号的化学成分(%)为:Mg=0.45~0.90,Si=0.20~0.60,Fe0.35,Cu0.10,Mn0.10,Cr0.10,Zn0.10,Ti0.10,其它0.15,其余为Al。
其中Mg和Si为主要强化元素,形成主要强化相Mg2Si。
6063合金中Mg2Si含量为1.2%左右,Mg与Si的含量是按形成Mg2Si所需要的量,即Mg∶Si=1.73而设计的。
实际上按此比例往往Mg过剩,而过剩的Mg使Mg2Si在Al中的溶解度显著削减,降低强化效果,故多使Si 稍偏高,过剩的Si有强化作用,但Si过剩太多则降低合金的抗蚀性。
从图1所示的伪二元Al-Mg2Si系相图可以看出,Mg2Si在Al中固溶度随温度明显变化,在共晶温度,Mg2Si的极限溶解度为1.85%;在200∶时,Mg2Si的溶解度为0.27%,因此AlMgSi系合金有明显的时效硬化效应。
其中的6063合金,由于高温塑性好,淬火温度宽,临界淬火速度小,可挤压后喷水或风淬,不需要特地的固溶处理,因此在建筑型材、汽车工业等部门获得广泛的应用,从数量上来说,仅次于工业纯铝的用量。
二、6063铝合金连续挤压工艺讨论连续挤压是本世纪七十年月问世的有色金属塑性加工新技术,尤其适用于软铝及其合金的加工。
它采纳直径9.5mm的铝杆为原料,靠挤压轮槽壁的摩擦力将毛坯带进由挤压轮槽与模座组成的弧形挤压室。
坯料被伸入轮槽的挡料块拦住,在摩擦力的持续作用下,温度和压力不断上升,达到材料的屈服强度,便从设置在挡料块旁的模具中挤出形成产品。
因此连续挤压不需要毛坯加热装置,节约了设备占地面积与。
只要连续供应毛坯,便能生产出任意长度的产品。
产品的特点是小截面(最小为6mm2),高精度(直径与壁厚公差为0.05mm)。
汽车等工业部门所用6063合金产品,因其截面小精度高,过去生产用常规挤压毛坯再进行拉拔的工艺,现在看来不如采纳连续挤压工艺经济。
汽车用6063铝合金散热器的挤压工艺优化
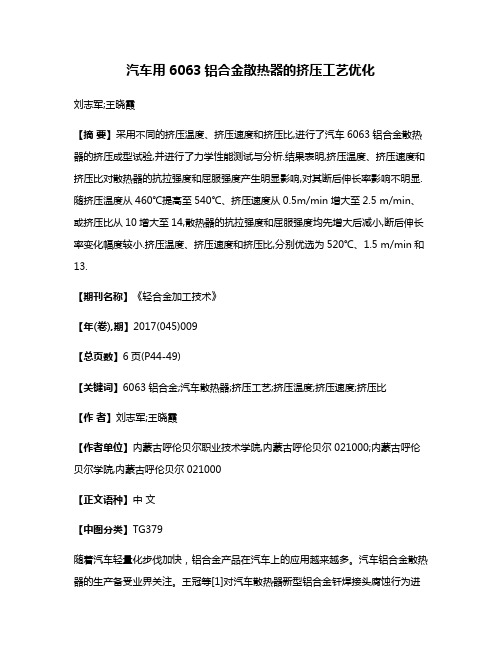
汽车用6063铝合金散热器的挤压工艺优化刘志军;王晓霞【摘要】采用不同的挤压温度、挤压速度和挤压比,进行了汽车6063铝合金散热器的挤压成型试验,并进行了力学性能测试与分析.结果表明,挤压温度、挤压速度和挤压比对散热器的抗拉强度和屈服强度产生明显影响,对其断后伸长率影响不明显.随挤压温度从460℃提高至540℃、挤压速度从0.5m/min增大至2.5 m/min、或挤压比从10增大至14,散热器的抗拉强度和屈服强度均先增大后减小,断后伸长率变化幅度较小.挤压温度、挤压速度和挤压比,分别优选为520℃、1.5 m/min和13.【期刊名称】《轻合金加工技术》【年(卷),期】2017(045)009【总页数】6页(P44-49)【关键词】6063铝合金;汽车散热器;挤压工艺;挤压温度;挤压速度;挤压比【作者】刘志军;王晓霞【作者单位】内蒙古呼伦贝尔职业技术学院,内蒙古呼伦贝尔021000;内蒙古呼伦贝尔学院,内蒙古呼伦贝尔021000【正文语种】中文【中图分类】TG379随着汽车轻量化步伐加快,铝合金产品在汽车上的应用越来越多。
汽车铝合金散热器的生产备受业界关注。
王冠等[1]对汽车散热器新型铝合金钎焊接头腐蚀行为进行了分析。
胡瑞玲等[2]分析了覆层铝合金Nocolok硬钎焊散热器的泄露情况。
余克壮等[3]研究了LF6铝合金散热器振动钎焊润湿界面的微观组织特征。
郭鹤等[4]对汽车散热器铝合金管开裂原因进行了分析。
黄雪梅等[5]对高密齿铝合金散热器型材挤压模进行了设计分析。
高飞等[6]对铝合金板翅式散热器钎焊结构的疲劳失效进行了分析,并提出了相应的改进措施。
魏继承等[7]对汽车散热器用4045/363/353铝合金复合带材的退火工艺进行了研究。
但是,目前关于汽车铝合金散热器的成型工艺研究报道较少,挤压成型是汽车铝合金散热器常用的成型工艺方法,笔者在某企业挤压生产线上,采用不同的挤压工艺参数对汽车6063铝合金散热器进行了挤压成型试验,优化了汽车6063铝合金散热器的挤压工艺,为工业化生产提供了试验数据和技术支撑基础。
6063铝合金挤压型材质量影响因素及解决方法
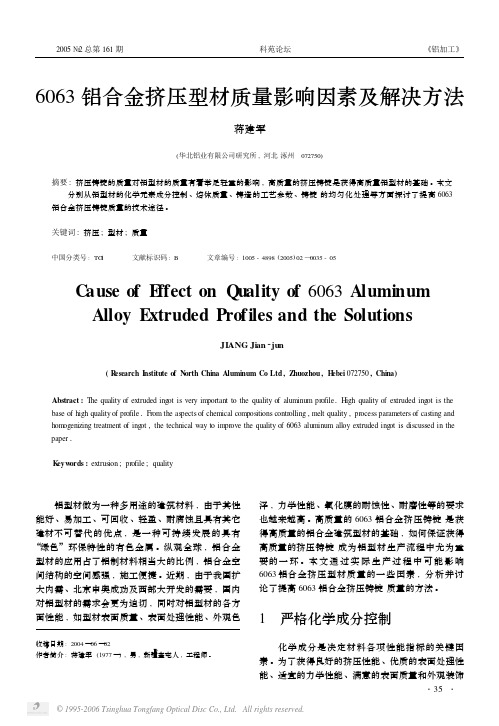
6063铝合金挤压型材质量影响因素及解决方法蒋建军(华北铝业有限公司研究所,河北涿州 072750)摘要:挤压铸锭的质量对铝型材的质量有着举足轻重的影响,高质量的挤压铸锭是获得高质量铝型材的基础。
本文 分别从铝型材的化学元素成分控制、熔体质量、铸造的工艺参数、铸锭的均匀化处理等方面探讨了提高6063铝合金挤压铸锭质量的技术途径。
关键词:挤压;型材;质量中国分类号:TG l 文献标识码:B 文章编号:1005-4898(2005)02—0035-05C ause of E ffect on Q uality of6063AluminumAlloy Extruded Profiles and the SolutionsJIANG Jian2jun(R esearch I nstitute of North China Aluminum Co Ltd,Zhuozhou,H ebei072750,China)Abstract:The quality of extruded ing ot is very important to the quality of aluminum profile1High quality of extruded ing ot is the base of high quality of profile1From the aspects of chemical compositions controlling,melt quality,process parameters of casting and hom ogenizing treatment of ing ot,the technical way to improve the quality of6063aluminum alloy extruded ing ot is discussed in the paper1K eyw ords:extrusion;profile;quality 铝型材做为一种多用途的建筑材料,由于其性能好、易加工、可回收、轻盈、耐腐蚀且具有其它建材不可替代的优点,是一种可持续发展的具有“绿色”环保特性的有色金属。
6063铝型材挤压工艺的优化铝型材挤压机工作原理

6063铝型材挤压工艺的优化铝型材挤压机工作原理铝型材挤压工艺的优化需要深入了解铝型材挤压机的工作原理。
铝型材挤压机是铝型材生产中常用的设备,通过将铝型材坯料加热至一定温度后,在挤压机的作用下,将坯料挤出成为希望形状的型材。
下面是关于铝型材挤压机工作原理的详细介绍。
铝型材挤压机的工作原理可以分为以下几个步骤:1.坯料加热:将铝坯料放入加热炉中进行加热,使其温度达到挤压温度。
加热的目的是使铝坯料在经过挤压机挤压时更容易塑性变形,减少挤出力和能耗。
2.挤压柱送料:将已加热好的铝坯料放入挤压柱内,通过液压系统将铝坯料送入挤压腔。
3.挤压过程:液压系统通过液压缸将铝坯料挤压至挤压模腔中,通过受力分析、液压力和弯曲力的作用,使铝坯料在挤压模具中塑性变形,最终形成所需要的型材。
4.冷却定型:挤压后的铝型材通过冷却装置进行冷却,使其迅速冷却并保持所需的形状。
5.切割和定长:将冷却好的铝型材通过切割设备进行切割,并根据需要进行定长。
上述是铝型材挤压机的基本工作原理。
在实际操作中,为了获得更好的挤压效果和更高的生产效率,可以进行以下的优化措施:1.加热控制:控制坯料的加热温度和时间,使其达到最佳挤压温度,并且避免过度加热造成材料的烧结和变质。
2.模具设计优化:对挤压模具进行合理的设计,包括模腔结构、冷却系统、壁厚控制等。
优化模具设计可以改善产品质量,提高生产效率。
3.润滑与冷却:在挤压过程中,适当的润滑可以减少摩擦力,提高挤压速度和形状精度。
同时,冷却装置的优化可以提高铝型材的冷却速度和定型效果。
4.挤压参数优化:合理选择挤压机的挤压速度、挤出力量和挤压比等参数,可以使铝型材获得更理想的形状和性能。
5.检测监控:在挤压过程中设置合适的监测装置,实时监测挤压力、温度、速度等参数,及时调整挤压参数,以保证产品质量的稳定和一致性。
综上所述,通过对铝型材挤压机工作原理的深入了解和优化措施的实施,可以有效提高挤压效率和产品质量,满足不同应用领域对铝型材的需求。
6063铝合金壳体系列毛坯冷挤压工艺研究

导师签名: 日 期:
期:
南昌航空大学硕士学位论文
第一章
绪论
第一章 绪论
1.1 课题的来源和意义
某工厂的传感器成套壳体的原生产工艺, 采用的是铝合金棒料直接车削加工 的成形方法,材料利用率低,生产周期长,由于采用的 2024 铝合金材质问题, 生产出的产品在进行无色阳极氧化时候出现很多黑斑等缺陷。导致合格率不足 60%,针对以上情况,提出在不改变使用性能的前提下选用合适的替代材料,在 保证使用性能的前提下,采用新工艺降低制造成本,提高成品合格率。 针对厂家提出要求,结合市场情况和材料性能拟采用 6063 铝合金代替原 2024。由于 6063 的阳极氧化性能比 2024 好的多。而且挤压后的 6063 的切削性 能也有大幅度的提高。无色阳极氧化膜不仅能够起到绝缘的作用,同时也可以弥 补冷挤压后的抗腐蚀能力降低的缺陷。6063 铝合金冷挤压性能很好,采用冷挤 压不仅仅可以提高生产效率、原材料利用率也由原来的 38%提高到了 93%,同 时由于 2024 每吨超出了 6063 近 4000 元的价格,也在生产成本方面让企业提高 了市场竞争力。另外 6063 采用冷挤压后,产品的强度也比原有 2024 材料有所提 高,加工性能也有所提高。 利用理论分析、有限元模拟和试验研究,掌握铝合金 6063 和 6A02 的挤压 变形规律,优化工艺参数,指导冷挤压生产中的模具设计和工艺设计,对提高模 具寿命和挤压件成形质量将有重要的实际意义。
Keywords : Cold Extrusion; Aluminum Alloy; Orthogonal Experiment; Finite Element Simulation; Mold Design
IV
南昌航空大学硕士学位论文原创性声明