用导套刀杆半精车深孔
内孔表面加工常用方法大汇总

内孔表面加工方法较多,常用的有钻孔、扩孔、铰孔、镗孔、磨孔、拉孔、研磨孔、珩磨孔、滚压孔等。
一、钻孔用钻头在工件实体部位加工孔称为钻孔。
钻孔属粗加工,可达到的尺寸公差等级为IT13~IT11,表面粗糙度值为Ra50~12.5μm。
钻孔有以下工艺特点:1.钻头容易偏斜。
在钻床上钻孔时,容易引起孔的轴线偏移和不直,但孔径无显著变化;在车床上钻孔时,容易引起孔径的变化,但孔的轴线仍然是直的。
因此,在钻孔前应先加工端面,并用钻头或中心钻预钻一个锥坑,以便钻头定心。
钻小孔和深孔时,为了避免孔的轴线偏移和不直,应尽可能采用工件回转方式进行钻孔。
2.孔径容易扩大。
钻削时钻头两切削刃径向力不等将引起孔径扩大;卧式车床钻孔时的切入引偏也是孔径扩大的重要原因;此外钻头的径向跳动等也是造成孔径扩大的原因。
3.孔的表面质量较差。
钻削切屑较宽,在孔内被迫卷为螺旋状,流出时与孔壁发生摩擦而刮伤已加工表面。
4.钻削时轴向力大。
这主要是由钻头的横刃引起的。
因此,当钻孔直径d﹥30mm时,一般分两次进行钻削。
第一次钻出(0.5~0.7)d,第二次钻到所需的孔径。
由于横刃第二次不参加切削,故可采用较大的进给量,使孔的表面质量和生产率均得到提高。
二、扩孔扩孔是用扩孔钻对已钻出的孔做进一步加工,以扩大孔径并提高精度和降低表面粗糙度值。
扩孔可达到的尺寸公差等级为IT11~IT10, 表面粗糙度值为Ra12.5~6.3μm,属于孔的半精加工方法,常作铰削前的预加工,也可作为精度不高的孔的终加工。
扩孔方法如图7-4所示,扩孔余量(D-d),可由表查阅。
扩孔钻的形式随直径不同而不同。
直径为Φ10~Φ32的为锥柄扩孔钻,如图7-5a所示。
直径Φ25~Φ80的为套式扩孔钻,如图7-5b所示。
扩孔钻的结构与麻花钻相比有以下特点:1.刚性较好。
由于扩孔的背吃刀量小,切屑少,扩孔钻的容屑槽浅而窄,钻芯直径较大,增加了扩孔钻工作部分的刚性。
2.导向性好。
导柱导套详细加工工艺

三、模具导套的机械加工实例例图3-40所示为一冷冲模具的导套,材料为20钢,淬火、低温回火58-62HRC。
1.结构工艺性分析该零件是典型的套类零件,主要加工方法为钻、镗、车、磨。
2.技术要求分析(1)主要表面及其加工方案主要表面为内圆柱面Ø32H7 Ra0. 2um,外圆柱面Ø45r6 Ra0. 4um,其加工方案:内圆柱面:钻—粗镗(扩)—半粗镗—粗磨—精磨;对于外圆柱面:粗车—半精车—粗磨—精磨。
(2)定位基准根据基准选择的原则选用内、外圆柱面互为基准。
(3)热处理如导套材料为20钢渗碳,则热处理为渗碳,淬火、低温回火;如导套材料为T10A钢,则热处理为淬火低温回火。
(4)技术关键及其采取的措施1主要表面为内圆柱面,尺寸公差等级高,表面粗糙度值Ra值小。
采取的措施:划分加工阶段,工艺路线采用:钻—粗镗(扩)—半精镗(铰)—粗磨—精磨—研磨;选择精密机床;控制切削用量;充分冷却。
2由于外圆柱面的尺寸公差等级高,表面粗糙度值Ra值小,故采取的措施是:在加工阶段划分、机床选用、切削用量的控制方面的要求与内圆柱面加工相同。
此外,工艺路线为:粗车—半精车—粗磨—精磨。
3外圆柱Ø45r6对内孔Ø32H7径向跳动要求高,采取的措施之一:以非配合外圆柱面定位夹紧,一次装夹磨削内孔Ø32H7、外圆柱Ø45r6,即“一刀下”的方法。
但此方法调整机床频繁,辅助时间长,生产效率低,仅适用于单件生产。
采取的措施之二:利用内圆柱面采用锥度心轴限位,以心轴两端中心孔定位磨削外圆柱面。
此方法操作简便,生产效率高,质量稳定可靠,但需要制造专用机床夹具,因此,适用于成批生产。
3.机械加工顺序安排车端面-车外圆-钻孔-镗孔-磨孔。
其中内孔的精加工应在外圆表面的精加工之前进行。
4.加工阶段的划分整个加工过程划分为:粗加工、半精加工、热处理、精加工四个加工阶段。
5.机械加工工艺规程表:冷冲模导套机械加工工艺规程。
机械机床毕业设计77半精镗及精镗气缸盖导管孔组合机床设计

机械机床毕业设计77半精镗及精镗气缸盖导管孔组合机床设计本文基于毕业设计要求,设计一个半精镗及精镗气缸盖导管孔组合机床。
文章将从机床结构设计、主要工艺流程、关键技术和机床性能等方面进行详细描述。
一、机床结构设计该机床采用传统的加工中心结构。
主要包括床身、床身划分、主轴箱、工作台、工件夹持装置和刀库等部分。
床身选用高强度铸铁材料,并采用合理的结构设计,以提高刚性和抗震性能。
主轴箱采用铸铁材料,具有较好的刚性和减震性能。
二、主要工艺流程1.半精镗工艺流程:(1)定位夹紧;(2)粗铰;(3)精铰;(4)标定。
2.精镗气缸盖导管孔工艺流程:(1)定位夹紧;(2)预孔;(3)切割孔;(4)粗镗;(5)精镗;(6)检验。
三、关键技术1.夹紧装置的设计:合理的夹紧装置设计可以确保工件在加工过程中的稳定性和精度。
夹紧装置要考虑到工件形状、加工力和切削力等因素,采用合适的夹紧方式和夹紧力。
2.切削工具的选择:根据不同工艺要求选择合适的切削工具。
要考虑到切削速度、切削力和切削稳定性等因素,提高切削效率和质量。
3.镗削精度的控制:通过采用精密镗削技术和合适的工艺参数控制,可以提高镗削的精度和表面质量。
同时,要进行适当的工艺监控和反馈控制,以保证加工精度。
四、机床性能1.主轴转速:可调范围广,适应不同加工要求。
2.进给速度:采用伺服电机控制,可调范围广,满足不同工艺要求。
3.加工精度:粗镗和精镗均达到高精度要求,满足零件加工的精度要求。
4.生产效率:由于采用自动化控制,提高了生产效率,降低了劳动强度。
总结:本文针对机械机床毕业设计课题,设计了一台半精镗及精镗气缸盖导管孔组合机床。
该机床具有合理的结构设计、完善的工艺流程和关键技术控制,以及良好的机床性能,能够满足零件加工的要求。
同时,通过采用自动化控制和高效率工艺,提高了生产效率,降低了劳动强度。
机械加工方法(总结)

机械加⼯⽅法(总结)2.1 零件常⽤的传统机械加⼯⽅法机械加⼯⽅法⼴泛运⽤于模具制造。
模具的机械加⼯⼤致有以下⼏种情况:(1) ⽤车、铣、刨、钻、磨等通⽤机床加⼯模具零件,然后进⾏必要的钳⼯修配,装配成各种模具。
(2) 精度要求⾼的模具零件,只⽤普通机床加⼯难以保证⾼的加⼯精度,因⽽需要采⽤精密机床进⾏加⼯。
(3) 为了使模具零件特别是形状复杂的凸模、凹模型孔和型腔的加⼯更趋⾃动化,减少钳⼯修配的⼯作量,需采⽤数控机床(如三坐标数控铣床、加⼯中⼼、数控磨床等设备)加⼯模具零件。
2.1.1 车削加⼯1.车削加⼯的特点及应⽤车削加⼯是在车床上利⽤车⼑对⼯件的旋转表⾯进⾏切削加⼯的⽅法。
它主要⽤来加⼯各种轴类、套筒类及盘类零件上的旋转表⾯和螺旋⾯,其中包括:内外圆柱⾯、内外圆锥⾯、内外螺纹、成型回转⾯、端⾯、沟槽以及滚花等。
此外,还可以钻孔、扩孔、铰孔、攻螺纹等。
车削加⼯精度⼀般为IT8~IT7,表⾯粗糙度为Ra6.3~1.6µm;精车时,加⼯精度可达IT6~IT5,粗糙度可达Ra0.4~0.1µm。
车削加⼯的特点是: 加⼯范围⼴,适应性强,不但可以加⼯钢、铸铁及其合⾦,还可以加⼯铜、铝等有⾊⾦属和某些⾮⾦属材料,不但可以加⼯单⼀轴线的零件,也可以加⼯曲轴、偏⼼轮或盘形凸轮等多轴线的零件;⽣产率⾼;⼑具简单,其制造、刃磨和安装都⽐较⽅便。
由于上述特点,车削加⼯⽆论在单件、⼩批,还是⼤批⼤量⽣产以及在机械的维护修理⽅⾯,都占有重要的地位。
2.车床车床(Lathe)的种类很多,按结构和⽤途可分为卧式车床、⽴式车床、仿形及多⼑车床、⾃动和半⾃动车床、仪表车床和数控车床等。
其中卧式车床应⽤最⼴,是其他各类车床的基础。
常⽤的卧式车床有C6132A,C6136,C6140等⼏种。
2.1.2 铣削加⼯1.铣削加⼯的范围及其特点1) 铣削加⼯的范围铣削主要⽤来对各种平⾯、各类沟槽等进⾏粗加⼯和半精加⼯,⽤成型铣⼑也可以加⼯出固定的曲⾯。
车工高级工鉴定考试模拟题与答案
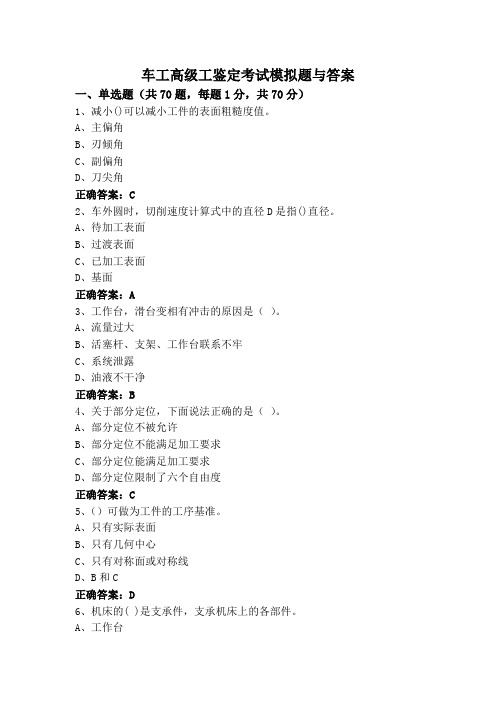
车工高级工鉴定考试模拟题与答案一、单选题(共70题,每题1分,共70分)1、减小()可以减小工件的表面粗糙度值。
A、主偏角B、刃倾角C、副偏角D、刀尖角正确答案:C2、车外圆时,切削速度计算式中的直径D是指()直径。
A、待加工表面B、过渡表面C、已加工表面D、基面正确答案:A3、工作台,滑台变相有冲击的原因是()。
A、流量过大B、活塞杆、支架、工作台联系不牢C、系统泄露D、油液不干净正确答案:B4、关于部分定位,下面说法正确的是()。
A、部分定位不被允许B、部分定位不能满足加工要求C、部分定位能满足加工要求D、部分定位限制了六个自由度正确答案:C5、()可做为工件的工序基准。
A、只有实际表面B、只有几何中心C、只有对称面或对称线D、B和C正确答案:D6、机床的( )是支承件,支承机床上的各部件。
A、工作台B、床身C、床鞍D、尾座正确答案:B7、杠杆千分尺的分度值有mm和()两种。
A、0.01mmB、0.004mmC、0.003mmD、0.002mm正确答案:A8、闭锁回路所采用的主要液压元件为()。
A、溢流阀B、压力继电器C、节流阀和调速阀D、换向阀和液控单向阀正确答案:D9、百分表的示值范围通常有: 0-3mm, 0-5mm和()三种。
A、0-12mmB、0-15mmC、0-8mmD、0-10mm正确答案:D10、粗车时为了提高生产率,选用切削用量时,应首先取较大的(A、切削速度B、主轴转速C、进给量D、背吃刀量正确答案:D11、导套支架安装于主轴箱与刀架床鞍之间,用于刀杆( )。
A、方向B、导向C、指向D、加长正确答案:B12、不符合着装整洁文明生产要求的是()。
A、优化工作环境B、在工作中吸烟C、按规定穿戴好防护用品心D、遵守安全技术操作规程正确答案:B13、薄壁工件加工刚性差时,车刀的前角和后角应选()。
A、大些B、小些C、零值D、负值正确答案:A14、机床导轨的直线度可以用()测量。
A、框式水平仪B、内径千分尺C、百分表D、量块正确答案:A15、根据()的不同,控制阀分为方向控制阀、压力控制阀和流量控制阀。
高级车工试题库及参考答案
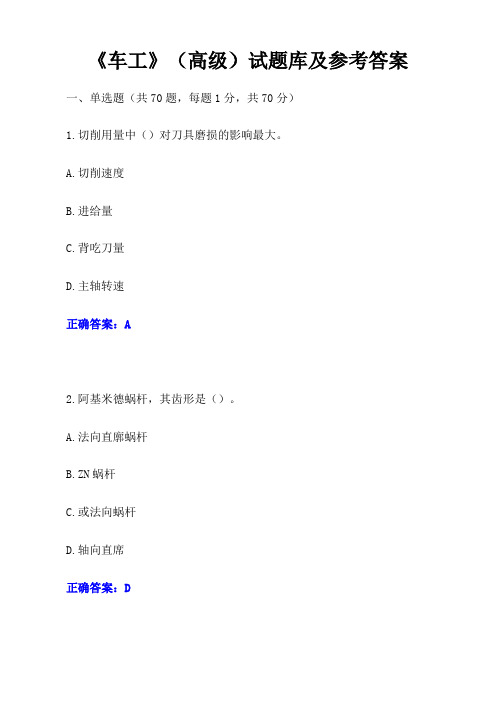
《车工》(高级)试题库及参考答案一、单选题(共70题,每题1分,共70分)1.切削用量中()对刀具磨损的影响最大。
A.切削速度B.进给量C.背吃刀量D.主轴转速正确答案:A2.阿基米德蜗杆,其齿形是()。
A.法向直廓蜗杆B.ZN蜗杆C.或法向蜗杆D.轴向直席正确答案:D3.磨高速钢螺纹车刀后面,必须使刀柄与砂轮外圆水平方向成()A.45°B.30°C.20°D.60°正确答案:B4.车床开始操作前,应先低速开机空运转1-2(),以使润滑油散布到各润滑处。
A.sB.minC.hD.D正确答案:B5.过切削刃选定点,通过切刃并直于基面的平面叫()。
A.前面B.正交平面C.切削平面D.基面正确答案:C6.主初削刃在基面上的投影与进给方向的夹角称为()A.主前角B.副偏角C.刃倾角D.刀尖角正确答案:A7.工件装夹后受力的作用产生变形,对工件形状产生影响,加工有色金属薄壁件时应尽最采取工序()原则。
A.分次装夹加工B.集中C.就地加工D.分散正确答案:B8.螺纹的导程Ph,和螺距P的关系是()(n是螺纹的线数)。
A.Ph=2nPB.P=PhC.P=nPhD.Ph=nP正确答案:D9.常用()来表达物体局部结构的断面形状,并用粗实线绘制。
A.半剖视图B.移出剖面C.重合剖面D.全剖视正确答案:B10.()可以对深孔进行综合检测。
A.内径百分表B.内径千分尺C.塞规D.游标卡尺正确答案:C11.划线平台一般用()。
A.铜B.塑料C.铸铁D.钢正确答案:C12.进给箱内的齿轮和轴承,除了用齿轮溅油法进行润滑外,还可用()润滑。
A.弹子油杯B.油绳C.浇油D.油脂杯正确答案:B13.车床主轴及轴承间的间隙过大或松动,加工时使被加工零件发生振动而产生()误差。
A.平行度B.圆度C.垂直度D.直线正确答案:B14.车削45°外斜沟槽时,可用专用车刀进行。
车削时,将小滑板转过(),用小滑板车削至尺寸要求。
高精度深孔螺纹加工工艺
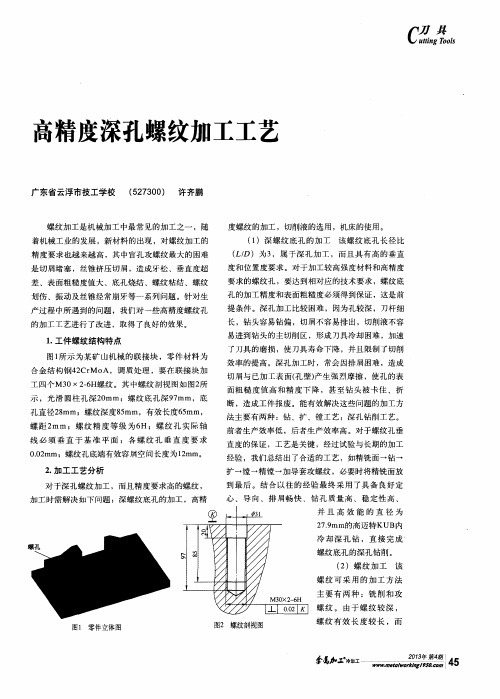
面粗糙 度值 高和精 度下降 ,甚至钻 头被卡住 、折
断 ,造 成 工 件 报 废 。能 有 效 解 决这 些 问题 的加 工方 法 主 要 有 两 种 :钻 、扩 、镗 工 艺 ;深 孔 钻 削工 艺 。
螺 距2 mm;螺 纹精 度 等级 为6 H;螺纹 孔实 际轴
线 必 须 垂 直于 基 准 平 面 ;各 螺纹 孔 垂 直 度 要 求 0 . 0 2 mm;螺纹孔底端有效容屑空间长 度为 1 2 a r m。
十分 昂贵 ,因此 应 用不 广 。 内冷 式 丝锥 则需 要机 床 冷 却 系统 的 配合 。要 保 证 稳 定 的 质量 ,必须 选 用适
( 4 )机床精度 机床精度也是影 响加 工质量 的因素之一 ,包括几何精度和运动精度。该工件的 螺孔 虽然不多,但是螺纹孔尺寸精度和轴线垂直度 要求较高 ,因此必须考虑机床重复定位精 度对加工 质量的影响。在钻孔及攻螺纹的路线上也应考虑反 向间隙的影响。在加工该螺纹的时候 由于机床定位 精度不是非常好 ,采用 了一步到位的做法 。即将机 床停 留在某一螺纹孔位置上 ,直到将该螺纹底孔及 螺纹孔切 削完成后 ,才移动机床主轴再加工下一个
( 3 )切 削液 合理使用切削液 ,对提高刀具寿
命 和加 工 表 面 质量 、j j  ̄ q - 精 度起 着 重 要 作用 。对 于
这样的螺纹孔加 工,必须保证切 削液到达切削 刃, 以减少切 削过程中的摩擦和 降低切 削温度 。为改进
切 削 液 的流 量 ,可对 丝 锥进 行 改 进 ,如 在 丝锥 的 刃 背上 开冷 却 槽 。
前者生产效率低 ,后者生产效率高 。对于螺纹孔垂 直度的保证 ,工艺是关键 ,经过试验与长期的加工
经验 ,我 们 总 结 出 了合 适 的 工艺 ,如 精 铣面 一钻 一 扩 一镗 一精 镗 一加 导 套攻 螺 纹 ,必 要 时将 精 铣 面放
车削加工工艺规范

车削加工工艺规范操作者必须受过车削加工的专业培训,并经过考核合格取得上岗证后,才有资格进行车削加工。
在加工前的准备和实际加工过程中,必须遵守以下守则。
一、加工前的准备1、操作者加工前要检查图纸资料是否齐全,坯件是否符合要求。
2、认真消化全部资料,掌握工装的使用要求和操作方法。
3、检查加工所用的机床设备,准备好各种附件,对机床按规定进行润滑和试运行。
二、装夹和加工1、在装夹各种刀具前,一定要把刀柄、刀杆、导套等擦干净。
2、工件装夹前,应将其定位面、夹紧面、垫铁和夹具的定位面擦干净,不得有毛刺。
3、车刀刀杆伸出刀架不宜太长,一般长度不宜超过刀杆直径/宽度的4倍。
4、车刀刀杆中心线应与走刀方向垂直或平行。
5、用三爪盘装夹工件进行粗车或精车,工件直径小于30MM时,其伸长长度不宜大于直径的5倍;工件直径大于30MM时,用顶尖。
必要时使用中心架和跟刀架。
6、用四爪盘、花盘和角铁装夹不规则偏重心工件时,需加配重。
7、车削台阶轴时,为了保证车削时的刚性一般先车直径较大部分后车直径较小部分。
在轴类工件上切槽时,应在精车前进行,以防变形。
8、钻孔前应将工件端面车平,必要时打中心孔。
9、当工件的有关表面有位置公差要求时,尽量在一次装夹中完成车削。
10、车削放磨削的余量,根据工件的长短和变形的可能一般外圆单面放0.2-0.4,圆孔单面放0.15-0.3。
11、在批量生产中必须进行首件检查,合格后方能继续加工。
三、加工后处理1、工件在加工后,应做到无屑、无水、无脏物,并在规定的位置摆好,以免碰伤。
2、工件装备用完后要擦干净放到规定的位置。
3、图纸资料保持整洁。
四、车削加工留磨余量及切削参数选择1、车削留磨余量2、(1) 车削外圆留磨余量(单边)3、注:不需热处理的和Cr12、Cr12MoV取小值,需热处理后加工的取大值。
(2)车削内圆留磨余量(单边)注:不需热处理的和Cr12、Cr12MoV取小值,需热处理后加工的取大值。
电机定子工件内孔吊装工具
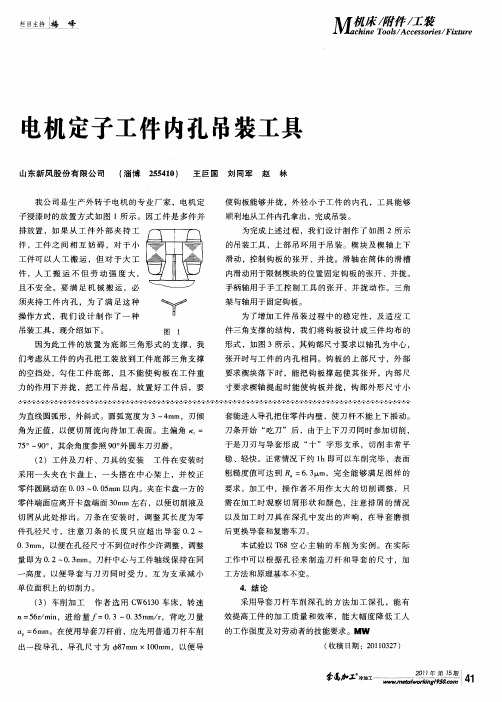
为 直线 圆弧 形 ,外斜 式 。圆弧 宽 度为 3一 m , m,刃倾 4 角 为正 值 ,以便 切 屑 流 向待 加 工 表 面 。主 偏 角 K =
7 。~9 。 5 O ,其余 角 度参照 9 。 圆车刀 刃磨 。 0外 ( ) 工件 及 刀杆 、刀具 的安 装 2 工 件 在 安 装 时
拦 持 梅 峰 主
To l/ c s o is os Ac e s re /Fi t r xu e
/CP I装 g e/
电机定子工件内孔吊装工具
山东新风股份 有限公 司 ( 淄博 2 5 1 ) 王 巨国 5 4 0 刘 同军 赵 林
我公 司 是 生 产 外 转 子 电机 的 专业 厂 家 ,电 机 定 子浸 漆 时的 放 置 方 式 如 图 1所 示 。因 工 件 是 多 件 并
采用 一 头 夹在 卡 盘 上 ,一头 搭 在 中心 架 上 ,并 校 正 零件 圆跳 动 在 0 0 . 3~0 0 rm 以 内。夹在 卡盘 一方 的 .5 a
零件 端 面应离 开 卡盘端 面 3 r 0 m左 右 ,以便 切 削液及 a 切屑 从此 处 排 出。刀 条 在 安 装 时 ,调 整其 长 度 为 零
套 能进入 导孔 把住 零 件 内壁 ,使 刀 杆不 能 上下 报 动 。 刀条 开始 “ 刀 ”后 ,由于上下 刀 刃 同时参 加 切 削 , 吃
于是 刀 刃与 导 套 形成 “ ” 字 形 支 承 ,切 削 非 常平 十 稳 、轻快 。正 常情况 下 约 1 h即可 以车 削 完毕 ,表 面 粗糙 度值 可 达 到 R =6 3z .I , m,完 全 能 够 满 足 图样 的 要求 。加 工 中 ,操 作 者 不 用 作 太 大 的 切 削 调 整 ,只 需在 加工 时 观 察 切 屑形 状 和颜 色 ,注意 排 屑 的情 况 以及 加工 时 刀 具 在 深孔 中发 出 的声 响 ,在 导 套 磨 损 后更 换导 套和 复磨 车刀 。
导套加工工艺过程制定课件

加强质量数据分析
定期收集和分析质量数据,找 出影响导套加工质量的因素, 并采取相应的改进措施。
建立质量信息反馈机制
建立有效的质量信息反馈机制,及 时收集和处理客户反馈的质量问题 ,持续优化导套的加工工艺和质量 。
CHAPTER 06
导套加工工艺案例分析
检查设备是否有异常声音或振动,确保设备 正常运行。
定期清洗和润滑
对设备进行清洗和润滑,防止设备生锈和磨 损。
定期更换易损件
如刀具、轴承等,确保设备加工精度和延长 使用寿命。
定期校准设备精度
确保设备加工精度符合要求,提高产品质量 。
CHAPTER 04
导套加工工艺参数制定
切削参数的确定
切削速度
根据导套材料和刀具材料 选择合适的切削速度,以 保证切削效率和加工质量 。
根据表面处理工艺要求,合理设置处理温度和时 间,以保证表面处理质量和效果。
CHAPTER 05
导套加工质量检测与控制
导套加工质量检测方法
外观检测
尺寸检测
通过目视、触摸等方式检查导套的表面质 量,如是否有划痕、毛刺、裂纹等缺陷。
使用测量工具对导套的关键尺寸进行测量 ,如内径、外径、长度等,确保尺寸符合 设计要求。
导套加工设备与工具
导套加工设备的种类与功能
数控车床
主要用于导套外圆和端 面的加工,具有高精度
、高效率的特点。
磨床
用于导套内孔和外圆的 精磨,可实现超精密加
工。
铣床
用于导套槽和异形结构 的加工,能够处理复杂
形状。
钻床
用于导套孔的钻削和铰 孔加工,满足不同孔径
和深度的加工需求。
第3章2圆柱形零件的加工

4)硬度选择 (1)砂轮硬度:是指磨粒受力后从砂轮表层脱落的难易程度。主要取决于结合剂的性质、数 量及砂轮制造工艺 。 (2)砂轮硬度选择原则: 工件材料越硬,应选越软的砂轮;反之,选越硬砂轮。对有色金属宜选用较软砂轮,以避免堵 塞砂轮。 磨削接触面积较大时,应选较软砂轮。 精磨和成型磨削时,应选较硬砂轮。 砂轮粒度号较大时,应选较软砂轮。 5)砂轮形状和尺寸及表示方法
2)内排屑深孔钻加工特点及应用 (1)加工精度和表面粗糙度:IT7~IT9, Ra3.2 (2)生产效率高于外排屑深孔钻(3倍以上) (3)应用范围:Ø6~ Ø60,深径比:L/D>100
3. 喷吸钻 1)喷吸钻结构与原理 (1)新型内孔排屑钻 (2)利用喷射效应排屑:内管后端四周有月牙形喷嘴 (3)切削液压力低: 1~2MPa
(1)磨料选择 磨料种类的选择与工件材料有关,如淬硬钢可选用白刚玉(WA)未淬硬钢可选用
普通棕刚玉(A);磨料的粒度与加工所要求的粗糙度有关,如Ra0.2~0.1,选用W40~W14, Ra0.1以下,选用W14~W10。
(2)液态研磨剂
由研磨粉、硬脂酸、航空气油、煤油等 辅料配制而成。常用研磨剂配方为:
工件速度与砂轮速度有关,一般情况下:
( Vs / Vw) =60~150(外圆磨)40~80(内圆磨) 3)纵向进给量fa
纵向进给量:工件每转一转相对砂轮在纵向进给运动方向移动的距离。(mm/r)
对钢件:粗磨:fa (0.3 ~ 0.7)bs
精磨:fa (0.1 ~ 0.3)bs 式中:bs—砂轮宽度,mm
三、 圆柱形零件加工方法 (一) 车削加工
镗孔切削参数
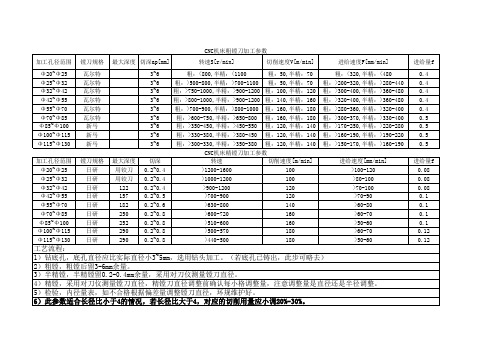
加工孔径范围 Φ20~Φ25 Φ25~Φ32 Φ32~Φ42 Φ42~Φ55 Φ55~Φ70 Φ70~Φ85 Φ85~Φ100 Φ100~Φ115 Φ115~Φ130 加工孔径范围 Φ20~Φ25 Φ25~Φ32 Φ32~Φ42 Φ42~Φ55 Φ55~Φ70 Φ70~Φ85 Φ85~Φ100 Φ10速S[r/min] 切削速度V[m/min] 粗:<800,半精:<1100 粗:50,半精:70 粗:>500-800,半精:>700-1100 粗:50,半精:70 粗:>750-1000,半精:>900-1200 粗:100,半精:120 粗:>800-1000,半精:>900-1200 粗:140,半精:160 粗:>700-900,半精:>800-1000 粗:160,半精:180 粗:>600-750,半精:>650-800 粗:160,半精:180 粗:>350-450,半精:>450-550 粗:120,半精:140 粗:>330-380,半精:>380-450 粗:120,半精:140 粗:>300-330,半精:>350-380 粗:120,半精:140 CNC机床精镗刀加工参数 转速 切削速度[m/min] >1200-1600 100 >1000-1200 100 >900-1200 120 >700-900 120 >630-800 140 >600-720 160 >510-600 160 >500-570 180 >440-500 180
直径深孔数控枪钻机床设计

小直径深孔数控枪钻机床设计摘要::枪钻机床主要采用的是外排屑深孔钻削技术。
枪钻系统主要由中心架、导向排屑器、钻杆联结器和冷却润滑油路系统组成。
枪钻系统的工作原理是:切削液通过钻杆箱上受油孔进入钻杆内部,到达钻头头部进行冷却润滑,并将切屑从钻头外部的V型槽排出。
该系统主要用于小直径的深孔加工。
数控枪钻机床的主电机通常是交流电机,进给电机选用直流伺服电机,主轴箱的电机选用变频电机。
系统运动方式为直线控制系统,以便进行平行与机床主轴轴线的钻削加工。
主运动系统是钻头的旋转运动,为了合理选择钻削速度,使其换速平稳,实现不停车自动换速,选无极变速系统。
进给运动系统是主轴的直线运动,为保证一定的传动精度和平稳性,尽量减小摩擦力,选用滚珠丝杠直线导轨传动。
通过枪钻机床设计,阐述了枪钻在数控车床上的深孔应用,包括枪钻的加工原理和枪钻的结构以及机床各部件。
这里包括进给系统设计,主轴箱的设计,授油器的设计,工作台的设计。
这说明:枪钻具有加工精度高,加工时间短,钻头寿命高,排屑好的特点,尤其应用在数控车床上,相对应用专用的枪钻设备来说,所需的工装夹具少,备件少,成本低。
本课题还介绍了D F系统的工作原理及授油器原理,并将DF系统机理应用于外排屑深孔钻削中,设计出了外排屑小直径深孔钻削系统。
本文从经济性、实用性出发,针对小直径深孔钻削系统进行了较为详细的介绍,对外排屑DF系统的主要装置授油器作了详细的设计说明。
关键词:小直径深孔枪钻;数控车床;主轴箱;授油器;钻削系统The Design of Small Diameter Deep Hole Drilling MachineCNC gunAbstract: Gun drill machine is mainly outside the BTA deep hole drilling technique. Gun drill system consists of center frame ,oriented chip conveyor ,drill pipe couplings and cooling lubricating oil system components. Gun drill system works by:cuting fluid through the drill pipe into the drill hole by the boxes within,cooling and lubicationg to reach the head drill,and drill cutings from the discharge outside the V-groove.The syetem is mainly used for small diameter deep hole C gun drill machine are usually AC motor of main motor,feed motor DC servo motoe selction,headstock frequecy electrical motor selection .Mode of motion is linear control syetem for parallel with the axis of the drilling spindle.Main movetment is a bie of rotation syetem for drilling speed to a reasonable choice and to smooth exchange rate,without stopping the automatic change-speeg,infinitely variable speed selection systen.Feed motion is the main axis of linear motion systems,in oder to guarantee the transmission accuracy and smoothness to minimize friction,use ball screw linear guide drive.Thruogh the gun drill machine tool design,demonstrates the application for hole machining of gun drill, contains machining theory,structure and various parts of machine tools.The design has feeding system ,headstock,oil coolet grant and table.It shows that gun drill has characteristic on high precision ,quic machine ,long life ,good chip break,especially application on NC laths,it takes on less tools and spare parts ,low cost.The main topics on the DF system and the principle of Oil granted,and DF system mechanism for debris from outside escape of chips deep hole drilling,designed the small diameter deep hole drilling system. This article from the economic,practical starting, for small diameter deep hole drilling system a more detailed introduction and outside escape of chips DF system's main oil installations award for a detailed description of the design.Key words:small-diameter deep-holes gun drill;NC laths; headstock; oil coolet grant; drilling system目录1 绪论 (1)1.1本课题的背景及研究目的 (1)1.2国内外研究现状 (2)1.3枪钻机床的特点和设计 (2)1.4枪钻的结构 (4)1.5课题的研究方法 (4)1.6深孔加工的类型及特点 (5)1.6.1 深孔加工的特点 (5)1.6.2 深孔加工中要解决的主要问题 (5)2 深孔加工系统的类型及选择 (7)2.1常用深孔加工系统的简介 (7)2.1.1 枪钻系统 (7)2.1.2 BTA系统 (7)2.1.3 DF系统 (8)2.1.4 喷吸钻系统 (8)2.2DF系统的设计理论 (9)2.2.1 外排屑DF系统 (9)2.2.2 DF系统的抽屑机理 (10)3 数控枪钻机床总体方案设计 (12)3.1总体方案的设计 (12)3.2小直径数控枪钻机床钻削系统的设计 (13)3.2.1 授油器的分类及原理 (13)3.2.2 授油器的结构设计 (15)3.2.3 主轴箱的设计 (16)3.2.4 带传动的设计 (20)4 枪钻机床进给系统设计 (24)4.1进给系统的组成及特点 (24)4.2进给系统的电机选择 (25)4.3滚珠丝杠幅的安装 (25)4.4滚珠丝杠幅的计算 (27)4.5滚珠丝杠幅的防护和润滑 (32)4.6滚珠丝杠在高速数控机床上的应用 (32)4.7联轴器的选择 (33)4.8导轨的选择 (34)结论 (38)参考文献 (39)1绪论1.1本课题的背景及研究目的在机械加工过程中,经常会碰到深孔加工的难题,而深孔钻削在核能,航空航天,石油和天然气等行业有着广泛的应用。
各种机械加工工艺规程(标准)
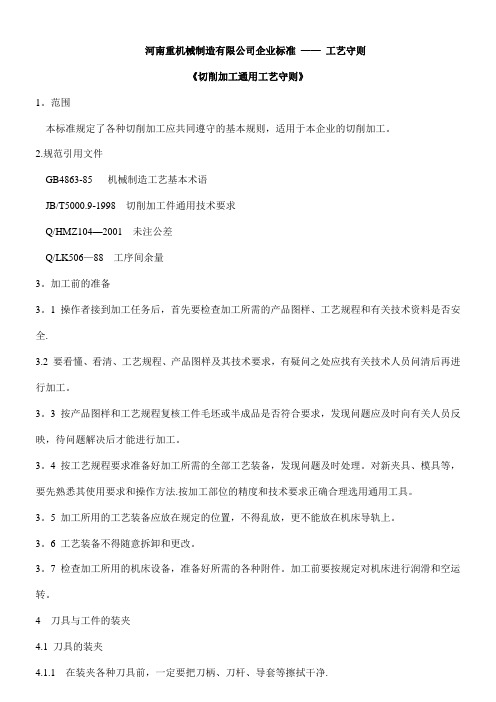
河南重机械制造有限公司企业标准——工艺守则《切削加工通用工艺守则》1。
范围本标准规定了各种切削加工应共同遵守的基本规则,适用于本企业的切削加工。
2.规范引用文件GB4863-85 机械制造工艺基本术语JB/T5000.9-1998 切削加工件通用技术要求Q/HMZ104—2001 未注公差Q/LK506—88 工序间余量3。
加工前的准备3。
1 操作者接到加工任务后,首先要检查加工所需的产品图样、工艺规程和有关技术资料是否安全.3.2 要看懂、看清、工艺规程、产品图样及其技术要求,有疑问之处应找有关技术人员问清后再进行加工。
3。
3 按产品图样和工艺规程复核工件毛坯或半成品是否符合要求,发现问题应及时向有关人员反映,待问题解决后才能进行加工。
3。
4 按工艺规程要求准备好加工所需的全部工艺装备,发现问题及时处理。
对新夹具、模具等,要先熟悉其使用要求和操作方法.按加工部位的精度和技术要求正确合理选用通用工具。
3。
5 加工所用的工艺装备应放在规定的位置,不得乱放,更不能放在机床导轨上。
3。
6 工艺装备不得随意拆卸和更改。
3。
7 检查加工所用的机床设备,准备好所需的各种附件。
加工前要按规定对机床进行润滑和空运转。
4 刀具与工件的装夹4.1 刀具的装夹4.1.1 在装夹各种刀具前,一定要把刀柄、刀杆、导套等擦拭干净.4.1。
2 刀具装夹后,应用对刀装置或试切等检查其正确性。
4。
2 工件的装夹。
4。
2。
1 在机床工作台上安装夹具时,首先要擦净其定位基面,并要找正其与刀具相对位置.4.2。
2 工件装夹前应将其定位面、夹紧面及垫铁和夹具的定位夹紧面擦拭干净,并不得有毛刺。
4.2。
3 按工艺规程中规定的定位基准夹紧。
若工艺规程中未规定装夹方式,操作者可自行选择定位基准和装夹方式,选择定位基准应按以下原则:a.尽可能使定位基准与设计基准重合;b.尽可能使各加工面采用同一定位基准;c.毛基准的选择首先考虑加工工艺基准的要求,并应保持加工工件的壁厚均匀;d.粗加工定位基准应尽量选择不加工或加工余量比较小的平整表面,而且只能使用一次;e.精加工工序定位基准应是已加工面;f.选择的定位基准必须使工件定位夹紧方便,加工时稳定可靠。
【精品】质量精细化控制
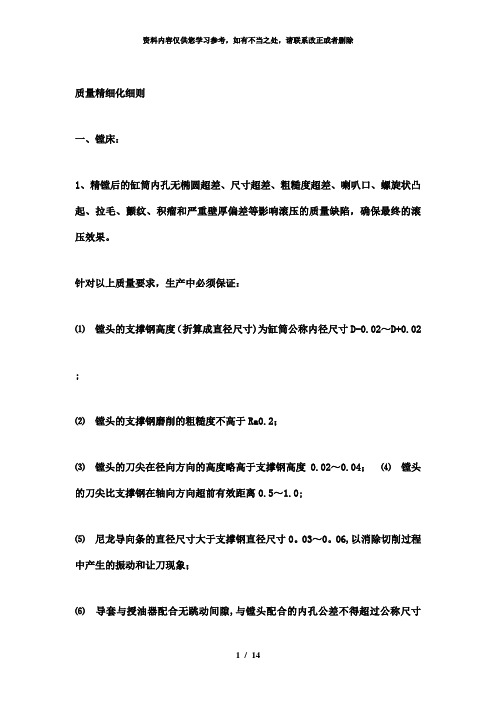
质量精细化细则一、镗床:1、精镗后的缸筒内孔无椭圆超差、尺寸超差、粗糙度超差、喇叭口、螺旋状凸起、拉毛、颤纹、积瘤和严重壁厚偏差等影响滚压的质量缺陷,确保最终的滚压效果。
针对以上质量要求,生产中必须保证:⑴镗头的支撑钢高度(折算成直径尺寸)为缸筒公称内径尺寸D-0.02~D+0.02;⑵镗头的支撑钢磨削的粗糙度不高于Ra0.2;⑶镗头的刀尖在径向方向的高度略高于支撑钢高度0.02~0.04;⑷镗头的刀尖比支撑钢在轴向方向超前有效距离0.5~1.0;⑸尼龙导向条的直径尺寸大于支撑钢直径尺寸0。
03~0。
06,以消除切削过程中产生的振动和让刀现象;⑹导套与授油器配合无跳动间隙,与镗头配合的内孔公差不得超过公称尺寸+0。
2;⑺定位锥盘的止口与母止口配合紧密,锥面与工件的工艺倒角配合可靠;⑻根据镗削精度要求调整进给量,当刀尖圆角R1.2时精镗进给量推荐为0.45mm/r, 当刀尖圆角R0。
8时精镗进给量推荐为0.35mm/r;⑼根据缸径变化调整主轴转速,当刀尖圆角R0.8时推荐精镗速度VC=100m/min (如:Φ280缸径,110r/min;Φ230缸径,140r/min;Φ180缸径,180r/min),当刀尖圆角R1。
2时推荐精镗速度VC=130m/min(如:Φ280缸径,140r/min;Φ230缸径,180r/min;Φ180缸径,230r/min),要合理调整。
2、滚压后的缸筒内孔不允许有椭圆超差、尺寸超差、粗糙度超差、夹带毛刺、局部凹坑、脱皮和内表面生锈等缺陷,确保缸筒内孔质量.针对以上质量要求,生产中必须保证:(如:Φ280缸径,90r/min;Φ230缸径,110r/min;⑴推荐滚压速度VC=80m/min,Φ180缸径,140r/min)要根据缸径变化,合理调整转速;⑵推荐进给量f=1~1。
5mm/r;⑶滚珠过盈挤压量根据缸径变化合理调整,一般控制在0。
20~0.25,过盈量太小粗糙度偏大,过盈量太大表面易脱皮;⑷镗削的缸筒内孔尺寸公差偏差较大时,应采取分组的方式调整滚压头滚珠直径公差进行滚压加工,以保证适宜的过盈挤压量;⑸滚珠、滚道经常检查,表面无挤伤、麻坑等缺陷,确保滚压质量;⑹切削油(液)沉淀、过滤可靠,无颗粒状杂质,要及时清理确保清洁;⑺切削液浓度不低于5%,确保起到冷却、润滑、防锈作用;⑻严禁反工序加工,特别是不允许缸筒车口后进行滚压加工,以防止内孔被杂质挤伤和200工艺倒角挤出尖棱;⑼有镗削缺陷的缸筒,不能直接进行滚压加工,经辅助处理(如珩磨等)并经质检人员确认后方可进行滚压加工。
- 1、下载文档前请自行甄别文档内容的完整性,平台不提供额外的编辑、内容补充、找答案等附加服务。
- 2、"仅部分预览"的文档,不可在线预览部分如存在完整性等问题,可反馈申请退款(可完整预览的文档不适用该条件!)。
- 3、如文档侵犯您的权益,请联系客服反馈,我们会尽快为您处理(人工客服工作时间:9:00-18:30)。
T 8空 心 主 轴 内孑 的车 削 要 求 如 下 :材 料 为 4 6 L 5钢调 质 T 3 外 圆为 10 内 孔 孑 径 为 8 。加 工 工 件孑 的 25, 3, L 7 L 长 度 为 9 0 m,加 工 前 孔 的尺 寸 为 7 。粗 糙 度 要 求 为 8m 5
费 的 时 间 约 为 1小 时 。 而 且 是 低 速 车 削 不 用 考 虑 中 心 架
作 者结 合 自己 的经 验及 多 次 的试 验 之后 。 总结 出 了一 个 深 孔 的车 削 加工 方 法 , 能有 效 的解 决 上述 问题 。此方 法 的核 心 就 是 制造 一 根 带 导 套 的 刀 杆 。 在车 削加 工 中用 导
的 切 削 调 整 ,只 用 在 加 工 时 观 察 切 屑 的 形 状 和 颜 色 注 意
S mi fns Tu n n De p e - ih i r ig e Ho e b Gu d S e v ’ l y i e le es
Cute bo t r Ar r
U e W i
大 幅度 的降低 工 人 的工作 强度 及 对 劳动 者 的技能 要求 。
参 考 文 献
作 者 选 用 C 10车 床 ,转 速 为 5 W6 3 6转 / ,走 刀量 分
F 03 O3 , 吃 刀 量 为 a= m 。 使 用 导 套 刀 杆 前 , 先 = .~ .5 背 p6 m 在 应 用 普 通 刀 杆 车 削 出 一 段 导 孔 , 孔 尺 寸 为 8 0 。 以 导 7x10
21第2 总 0期 0 1 期 第2 1
( 诸 城 采 用 导套 刀 杆 车 削 深 孔 的 方法 加 工 深孔 能 2)
杆 中心 与工 件 轴 线保 持 在 同一 高度 。 以便 导套 与 刀 刃 同 ‘ 时受 力 , 为 支承 减小 单位 面 积上 的切 削 力 。 互
2 3 车 削 加 工 .
孔 尺 寸 0 2 03 i .~ .r 。 a n
长 , 杆 造 多长 , 就 能 车 多 长 。 由 于是 一 次 走 刀 车 削 完 刀 也 毕 ,不 用 两 头接 刀 车 削 ,从 而 有效 的保 证 了孔 的形 位 公
差 , 糙 度 也 可 以 达 到 63级 , 足 了 图 纸 要 求 , 且 减 少 粗 . 满 并 了工作 者 的 劳动 强度 。
用 工 件 两 头 掉 头 车 削 。 刀 杆 悬 臂 长 为 4 0 m, 于 刀 杆 刚 5m 由
零 件端 面 应 离 开 卡盘 端 面 3 m 左 右 , 以便冷 却 液 及 切 屑 0m 从 此 处 排 出 。刀 条 在 安 装 时 ,调 整其 长 度 为 零 件 孑 径 尺 L 寸 ,注 意 刀条 的长 度 只应 超 出导 套 02 0 3 m,以便 在孑 .— .m L
性差 , 动 大 , 振 切削 用 量都 相 应 的减 小 。每加 工一 件孔 , 所
耗 费 的 时 间 约 为 3小 时 。加 工 中 要 让 工 件 “ 头 ” 并 实 时 掉 ,
现 制 术 装 代 造技 与 备
径 尺 寸 不 到 位 时 作 少 许 调 整 ,调 整 量 即 为 02 03 n 刀 .— . 。 r m
[ ]陈昭 莲 . 1 加工 大 直径 深孔 的 新方 法 . 械 ,0 3年第 3 机 20 0卷 曾
刊 :3 2 1~2 3 3.
便 导套 能 进入 导孔 把 住零 件 内壁 。使 刀 杆不 能上 下 振动 ,
刀 条 开 始 “ 刀 ” , 于 上 下 刀 刃 同 时 参 加 切 削 , 是 刀 吃 后 由 于 刃 与 导 套 形 成 “ ” 形 支 承 , 削 非 常 平 稳 、 快 。 正 常 十 字 切 轻
工 中经 常 会遇 到 这 类 零 件 ,车 削加 工 是 这 类 零 件 的 主要
加 工 方 法 之 一 …。深 孔 车 削 加 工 由 于 受 到 零 件 几 何 尺 寸 和
形 状 的 约束 ,刀 杆 的 外 形 尺 寸 比所 要 加 工 的 孔 的 最小 孔 径 还 小 , 致 刀 杆 自身长 径 比大 、 导 刚性 差 。 当刀 杆 刚性 不 能 克 服 切 削力 而 产 生 弯 曲 变形 时 ,导 致 刀 杆 容 易 产 生振 动 , 吃 ” 起 刀[。 这种 情 况下 加 工效 率 低 下 , “ 不 2在 1 刀具 损耗 过大 , 而且 勉 强 加 工 出来 的孔 也 会 粗 糙度 过 大 , 寸精 度 尺 也往 往 难 以保 证 。
1 实 例 分 析
刀杆 : 料 4 材 5钢 HRC3 3 2 ̄ 5
图 1 刀 杆 图 纸
作 者在 车 削 “ 6 ”空 心 主 轴 内孔 的过 程 中就 遇 到 了 T8
类 似 的 情 况 。如 果 采 用 两 头 “ 刀 ” 削 内 孔 , 然 可 以 车 接 车 虽
观察 和 调整 切 削用 量 并调 整 中心架 。工 作者 劳 动强 度 大 , 对 工 作者 的技 能 等级 要求 高 。而 用 导套 刀杆 车 削深 孔 , 刀
[]吴 昌 木 朱 玉 麟 .壳 式 长轴 类 零 件 深 孔 车 削 技 术 的 改进 . 2 纺
织 机 械 ,0 7年 第 2期 : 8~3 . 20 2 0
[ ]杜志 勇.多 台阶精 密 深孔 的 车 削. 属加 工 ,0 8年第 6期 : 3 金 20
~
3 6
情 况 下约 1 时 即 可 以车 削完 毕 , 糙度 可 以达 到6 3完 小 粗 . 全 能 够满 足 图 纸 的要 求 。加 工过 程 中 工作 者 不 用作 太大
本 试 验 以 T 8空心 主轴 的车削 为 实例 。 实 际工 作 中 6 在 可 以根据 孔 径 来 制造 刀 杆 和 导套 的尺 寸 ,加 工方 法 和原
理 基本 不 变 。 3 结 论
( ) 用导 套刀 杆 车削 深孔 的 方法 加工 深孑 能 有效 的 1采 L
提高 工件 的加工 质量 和 效率 ;
杆 长 度 为 10 m 。刀 条 长 度 调 整 至 合 适 尺 寸 , 次 “ 刀 ” 00m 一 走
削成 功 。但 是 要 反 复 装 夹零 件 , 动 强度 大 , 劳 而且 零 件 的
形位 公差 也 难 以保 证 。
孔 就 可 以加 工 完毕 。在 加 工过 程 中 , 工作 者 只要 观察 一下 出 屑情 况 即可 。由于 不用 让 零件 “ 头 ” 车 削一 件孔 所 耗 掉 ,
efce c . b t lo e u e a o ne st s n s i rq ie ns f fiin y u as rd c lb r itn ie a d kl e urme t i 1 o
wo k r . r e s Ke r s:g i e se v ’ c t r a b r, u i g, e p h l y wo d u d le es u t r o t r n d e oe e n
现 以 车削 加 工 “ 6 ” 孑 为 例 , T8深 L 阐述 使 用 导 套 刀 杆 车
削 深孔 的 加工 方 法 。
车 削用 的 刀具 为 1 6×1 6×8 6的 高速 钢 刀条 。刀 具应 刃 磨 成 两边 一 上 一 下都 开 刃 , 屑槽 为直 线 圆 弧形 , 断 外斜 式 。圆弧 宽度 为 3 4 m,  ̄ m 刃倾 角 为正 值 , 以便 切 削 流 向待加 工 表 面 。 偏 角 K 59 主 仁7 ~ O度 , 其余 角度 参照 9 0外 圆 车刀 0
1 5。 2.
22 工件 及 刀杆 、 具 的安 装 刀 工件 在 安 装时 采 用一 头 夹在 卡 盘上 , 头 搭在 中心架 一
上 。 校 正 零 件 跳 动 在 00 ~ .5 m 内 。 在 卡 盘 一 方 的 并 .3 00 r 以 a 夹
刀 杆 图 纸 如 图 1 :
由 于孑 是 “ 孔 ” 在 没 有 采 用 导 套 刀 杆 之前 , 者采 L 过 , 作
Absr c I h s p p r s a x mp e o 6 h H w pi l o e t a t: n t i a e ,a n e a l f T 8 o o s nd e h l t r i g h t o s n d p cfc r c s t u n d e h l b g i e u n n ,t e meh d a s e i p o e s o t r e p oe y u d i se v ’ u tr r o ae e c i e l e es c t a b r r d s r d.Tu i g h d e h l b g i e e b n r n t e e p o e y u d se v ’ u t r r o c n t n y mp o e h p o e s n u i a d l e es c te a b r a n o o l i r v t e rc si g q a t n l y
套 与 刀 具 相 互 支 承 , 成 一 个 “ ” 形 的 支 承 点 , 此 增 形 十 字 以 加 了 刀 杆 的 刚 性 , 制 刀 杆 的 上 下 振 动 。 这 样 刀 具 的 左 右 抑 刃 同 时 参 加 切 削 , 散 了切 削 力 。 如 果 条 件 允 许 , 用 多 分 不 次 “ 刀 ” 一 次 走 刀 就 可 以 车 削 出 深 孑 。理 论 上 是 孔 有 多 吃 , L
发 热 而 “ 死 ” 件 , 以工 作 者 在 加 工 过 程 中 劳 动 强 度 抱 零 所 低 , 工 作 者 的技 能等 级 要求 也 低 。 对
2 具体 操 作步 骤 : ’
2 1 导套 及 道 具 的准 备 . 加工 零 件 之前 应 先 车削 出若 干 个导 套 , 以便在 导 套磨 损 后 更换 。 个 导套 大 概 可 以车 削 7 8件 零件 。导套 材料 每 ~ 选 用 铸铁 HB 2 ~ 5 导 套 与刀 杆 为 间 隙配 合 并用 止 头螺 2 0 2 0, 钉定位 , 防止 导 套在 孔 内转 动 。导 套外 圆的 尺寸 应小 于 导