精轧变规格辊缝设定不到位问题分析与改进
精轧变规格辊缝设定不到位问题分析与改进
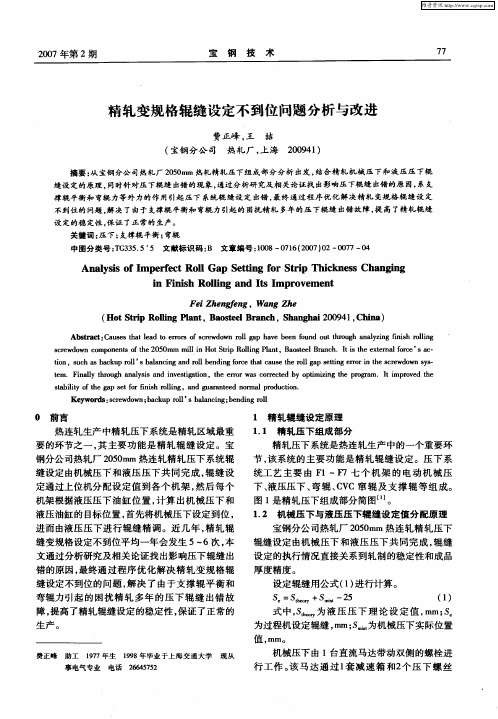
i n Fi n i s h Ro l l i n g a nd I t s m pr I o v e me nt
F e i Z h e n g f e n g ,Wa n g Z h e
( Ho t S t r i p Ro l l i n g P l a n t , B a o s t e e l B r a n c h, S h a n g h a i 2 0 0 9 4 1 , C h i n a )
关键词 : 压下 ; 支撑 3 5 . 5 5 文 献 标 识 码 : B 文章 编 号 : 1 0 0 8— 0 7 1 6 ( 2 0 0 7 ) 0 2— 0 0 7 7— 0 4
An a l y s i s o f I mp e fe r c t Ro l l Ga p S e t t i ng f o r St r i p Th i c k ne s s Cha n g i n g
O 前 言
1 精 轧 辊缝 设定 原理
热 连 轧生产 中精 轧压 下 系统是 精轧 区域 最重 要 的环节 之一 , 其 主要 功 能 是 精 轧辊 缝 设 定 。宝 钢分公 司热 轧厂 2 0 5 0 m m 热连 轧精 轧 压下 系 统辊 缝设 定 由机械 压 下 和液 压 压 下 共 同 完成 , 辊缝 设
维普资讯
2 0 0 7年 第 2期
宝
钢
技
术
7 7
精 轧变 规 格辊 缝 设 定不 到 位 问题 分析 与 改 进
轧钢辊道故障分析与预防改进
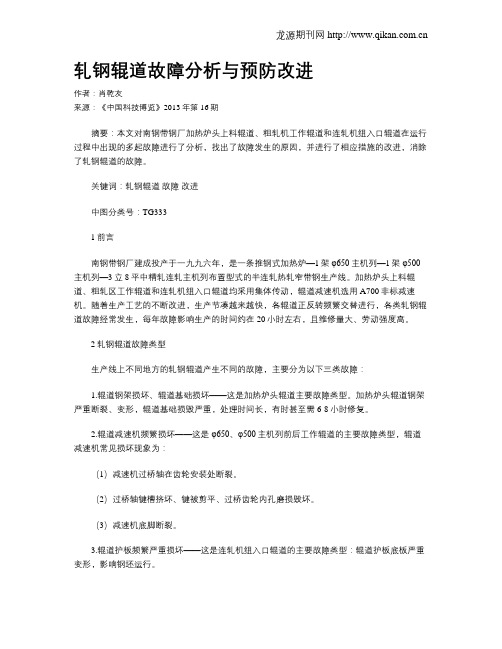
轧钢辊道故障分析与预防改进作者:肖乾友来源:《中国科技博览》2013年第16期摘要:本文对南钢带钢厂加热炉头上料辊道、粗轧机工作辊道和连轧机组入口辊道在运行过程中出现的多起故障进行了分析,找出了故障发生的原因,并进行了相应措施的改进,消除了轧钢辊道的故障。
关键词:轧钢辊道故障改进中图分类号:TG3331前言南钢带钢厂建成投产于一九九六年,是一条推钢式加热炉—1架φ650主机列—1架φ500主机列—3立8平中精轧连轧主机列布置型式的半连轧热轧窄带钢生产线。
加热炉头上料辊道、粗轧区工作辊道和连轧机组入口辊道均采用集体传动,辊道减速机选用A700非标减速机。
随着生产工艺的不断改进,生产节凑越来越快,各辊道正反转频繁交替进行,各类轧钢辊道故障经常发生,每年故障影响生产的时间约在20小时左右,且维修量大、劳动强度高。
2轧钢辊道故障类型生产线上不同地方的轧钢辊道产生不同的故障,主要分为以下三类故障:1.辊道钢架损坏、辊道基础损坏——这是加热炉头辊道主要故障类型。
加热炉头辊道钢架严重断裂、变形,辊道基础损毁严重,处理时间长,有时甚至需6-8小时修复。
2.辊道减速机频繁损坏——这是φ650、φ500主机列前后工作辊道的主要故障类型,辊道减速机常见损坏现象为:(1)减速机过桥轴在齿轮安装处断裂。
(2)过桥轴键槽挤坏、键被剪平、过桥齿轮内孔磨损毁坏。
(3)减速机底脚断裂。
3.辊道护板频繁严重损坏——这是连轧机组入口辊道的主要故障类型:辊道护板底板严重变形,影响钢坯运行。
3故障原因分析与改进措施1.加热炉头辊道钢架损坏、辊道基础损坏故障原因分析与改进措施原因分析:加热炉头辊道正反转不太频繁,但长期受较高温度的烘烤,辊道钢架必须产生一定的变形,从而导致辊面高度不一致。
在推钢机将钢坯推入加热炉时,辊子承受着轴向力,辊道钢架主动侧与自由侧钢架之间连接梁仅4根,强度不足,连接梁首先损坏断裂;8只M36基础螺栓在连接梁损坏后,强度明显不足,基础受损:基础螺栓断裂。
棒线材轧制常见堆钢事故及处理措施

棒线材轧制常见堆钢事故及处理措施一、粗中轧区事故原因分析及对策1、轧件咬入后机架间堆钢故障原因:(1)轧制速度、轧辊直径设定不正确;换辊(槽)后张力设定过小。
(2)钢温波动太大。
(3)轧辊突然断裂。
(4)由于电控系统原因引起某架轧机的电机突然升速或降速。
处理措施:(1)准确设定轧制速度、辊径和张力。
(2)保温待轧,通知加热炉看火工。
(3)更换断辊。
(4)检查电气系统。
2、轧件头部在机架咬入时堆钢故障原因:(1)轧件尺寸不符合要求。
(2)轧槽中有异物或打滑。
(3)导卫安装不良、磨损严重或导卫中夹有氧化铁皮等异物。
(4)坯料内部存在分层、夹杂或冶废等缺陷引起的轧件“劈头”。
(5)上、下辊径不同、磨损不均匀或不同步造成的轧件头部弯曲。
(6)头部钢温过低造成的咬入困难或头部开裂。
(7)轧机机架刚性不好,轧制过程中存在跑偏现象。
(8)坯料“脱方”严重。
(9)轧件出粗轧机架后翘头导致不能顺利咬入下架次或头部冲导卫,简单来说就是翘头。
处理措施:(1)对轧机辊缝作适当调整。
(2)检查、清理或打磨轧槽。
(3)检查、清理、调整或更换导卫。
(4)认真检查坯料。
(5)检查传动部件间隙或更换轧辊。
(6)改善出钢条件。
(7)对轧机机架进行加固;检查锁紧缸的工作状态。
(8)杜绝不合格钢坯入炉。
(9)认真检查前一架次进口导卫是否松动,导卫松动使轧件咬入箱型孔后受到进口导卫的压力,使轧件下部受压较大,导致下部延伸变大而造成翘头,最终未能顺利咬入轧机而堆钢。
3、轧件卡在机架内造成堆钢故障原因:(1)由于钢温过低或轧制速度过高而引起电机过载跳闸。
(2)发生设备或安全事故时紧急停车。
处理措施:应根据具体情况分析处理。
二、预精轧区事故原因分析及对策1、机架间堆钢故障原因:(1)辊径、辊缝设定错误。
(2)导卫安装不准确,导卫被堵塞或被冲掉。
(3)粗、中轧张力过大,轧件在预精轧“甩尾”。
(4)轧机或辊箱轴承烧,导致次架次料型变化。
(5)压下装置自锁性能坏,在轧制时因振动,料型产生变化。
热轧精轧机标定异常的原因分析
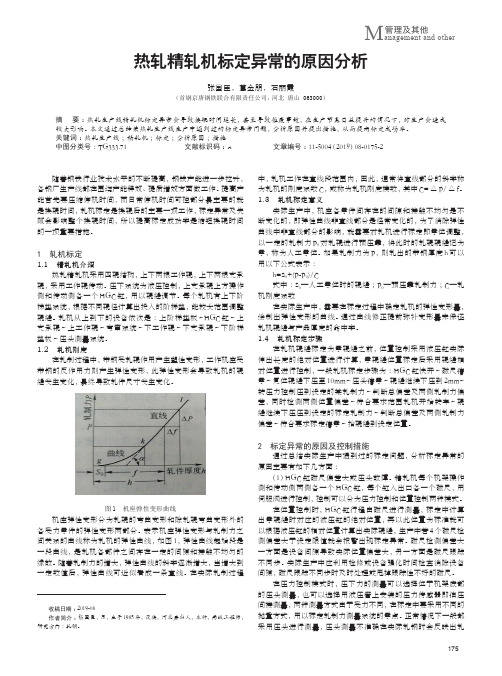
175管理及其他M anagement and other热轧精轧机标定异常的原因分析张国臣,葛金朋,石丽霞(首钢京唐钢铁联合有限责任公司,河北 唐山 063000)摘 要:热轧生产线精轧机标定异常会导致换辊时间延长,甚至导致推废事故,在生产节奏日益提升的情况下,对生产会造成较大影响。
本文通过总结某热轧生产线生产中遇到过的标定异常问题,分析原因并提出措施,从而提高标定成功率。
关键词:热轧生产线;精轧机;标定;分析原因;措施中图分类号:TG333.71 文献标识码:A 文章编号:11-5004(2019)08-0175-2收稿日期:2019-08作者简介:张国臣,男,生于1985年,汉族,河北唐山人,本科,高级工程师,研究方向:轧钢。
随着钢铁行业技术水平的不断提高,钢铁产能进一步拉升,各钢厂生产线都在围绕产能释放、提质增效方面做工作。
提高产能首先要压缩停机时间,而日常停机时间可控部分最主要的就是换辊时间,轧机标定是换辊后的主要一项工作,标定异常及失败会影响整个换辊时间,所以提高标定成功率是缩短换辊时间的一项重要措施。
1 轧机标定1.1 精轧机介绍热轧精轧机采用四辊结构,上下两根工作辊,上下两根支承辊,采用工作辊传动。
压下系统为液压控制,上支承辊上方操作侧和传动侧各一个HGC 缸,用以辊缝调节。
每个轧机有上下阶梯垫系统,根据不同辊径计算出投入的阶梯垫,能较大范围调整辊缝。
轧机从上到下的设备依次是:上阶梯垫板~HGC 缸~上支承辊~上工作辊~弯窜系统~下工作辊~下支承辊~下阶梯垫板~压头测量系统。
1.2 轧机刚度在轧制过程中,带钢受轧辊作用产生塑性变形,工作机座受带钢的反作用力则产生弹性变形,此弹性变形会导致轧机的辊缝发生变化,最终导致轧件尺寸发生变化。
图1 机座弹性变形曲线机座弹性变形分为轧辊的弯曲变形和除轧辊弯曲变形外的各受力零件的弹性变形两部分。
表示机座弹性变形与轧制力之间关系的曲线称为轧机的弹性曲线,如图1,弹性曲线起始段是一段曲线,是轧机各部件之间存在一定的间隙和接触不均匀的缘故。
轧钢厂质量异议缺陷原因分析与预防措施

连铸坯存在尺寸超差
速度ቤተ መጻሕፍቲ ባይዱ作手、
粗轧操作工等
加强连铸坯和成品检查,加大判二级力度。
起梗
带钢存在局部高点
压下、磨工等
加强CVC轧辊曲线抽查力度,减小F7负荷,保证终轧板形。
拉窄
带钢温度波动导致压下变化大,速度波动引起张力过大。
速度、自动化等
促进经验交流,根据入口温度提前调整辊缝,速度也随之进行相应的调整。
压下操作手、
速度操作手、
加热工等
1.升速轧制,提高加二速度,
2.粗轧板形允许时,放下保温罩,
3.及时投入AGC。
镰刀弯
粗轧中间坯板形不好,横向厚差大。
粗轧操作工等
粗轧及时调整压下,保证头部板形。
超差
厚度超差
1.生产计划少,过渡材比较少,
2.温度波动大,待温时间长。
压下操作手、
加热工等
根据生产计划灵活安排薄、厚、冷、热规格产品入炉,放慢轧钢节奏,减少待温时间。
轧钢厂质量缺陷责任认定细则
缺陷名称
原因分析
责任人
预防措施
波浪
单边浪
1.各机架负荷分配不合理,
2.轧辊曲线精度有误差。
压下操作手、
磨工等
1.根据板形情况随时调整各机架负荷分配,
2.加强检查,保证轧辊曲线精度。
双边浪
中浪
厚度不均
1.出钢速度过快,水梁黑印随不明显,但也存在温度低的情况,
2.精轧速度慢,尾部温降大。
2.根据实际情况对卷曲速度进行调整。
裂边
1.终轧和卷曲温度低,不利于晶粒长大。
2.层流冷却开前端水嘴,晶粒长大时间短。
速度、压下、卷取操作工等
精轧工作辊换辊系统常见故障分析l
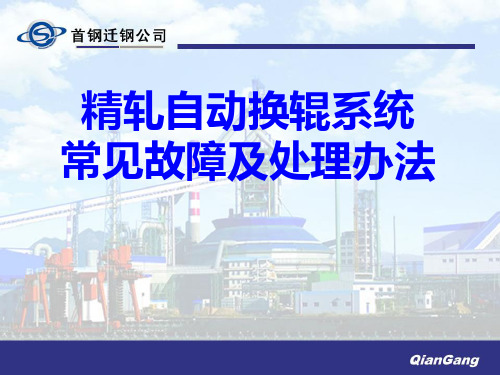
a -
b 1
a 1
b
a
30%
b 1
b PE01 YVH S 1/1-6 PE01 YV H S 2/1-6 PE 02 YVH 1/1-6
a PE03 YV H 1/1-6
b
-
0
P T
P T
P T
T
+
+
1
1
0
30%
1
OS
P E01 B S 4/1-6 I S co llapse clo se R oll gap
故障7 故障7 出入口导卫、擦辊器不到位 1、检查导卫现场实际位置及接近开关信号 2、检查擦辊器现场实际位置及压力开关显示压力值 3、必要时可先捅阀动作设备保证换辊 故障8 故障8 提升轨道 在推辊前要确认是否上升到位。 检查现场没有动作,要确认接近开关信号是否正常、机上阀台的电磁 阀的信号是否正确。如果接近开关信号正常、电磁阀已经得电,可以 在现场有人确认的情况下手动捅阀先换辊,然后再检查阀头和电磁铁, 如果手动不能捅动就要更换电磁阀;
精轧自动换辊系统 常见故障及处理办法
精轧机自动换辊分为四个阶段: 精轧机自动换辊分为四个阶段: 1、换辊前准备阶段 2、换辊前设备停机阶段 3、换辊阶段 4、换辊后设备恢复阶段
换辊前准备阶段
换辊过程: 换辊过程: 1、换辊小车从初始位置E1(磨辊间)把新辊推到精轧机前 的换辊平移盖板上(E7)(平移盖板位于飞剪侧); 2、换辊小车后退到位置E6,平移盖板向卷取机侧平移; 3、换辊小车前进到位置E11;
故障3 故障3、CVC窜辊不到位
1、换辊模式自动时序CVC窜辊不到位:确认工作辊处于平衡状态后, 可再次切换模式,重新执行自动时序; 2、长时间轧机内没有轧辊(检修恢复时),某一个CVC液压缸位置不 正确:在CVC窜辊处于手动或自动模式时,强制位置设定为0动作液压 缸:Nx_RS_WR_REF(G2) 3、如果出入口两侧位置一致且位置值在1mm内,可考虑封点操作
国产高速线材精轧机辊箱常见故障分析及处理措施之欧阳学创编

*时间:2021.03.03 创作:欧阳学国产高速线材精轧机辊箱常见故障分析及处理措施1前言承抱死等事故。
韶钢高速线材厂二线精轧机组是国产仿摩根五代高速线材轧机, 轧制速度可达 90m /s, 自 2008年 3 月投产以来, 轧机辊箱的故障较多, 延误生产时间造成人力物力消耗, 严重影响和制约了生产, 使得设备维护压力增加, 设备消耗也增加了生产成本。
针对辊箱出现的常见故障, 笔者进入了深入的分析, 并采取了相应的解决方案及预防措施, 故障大大降低, 辊箱平均使用寿命由初期的 2个月提高到平均 7个月, 部分使用寿命达到了 12个月, 取得了良好的效果, 达到国产精轧辊箱维护的先进水平。
生产中精轧机辊箱故障频繁发生给生产带来严重影响, 为此辊箱发生的一些故障进行分析总结, 并进行1. 油膜轴承5. 固定卡板2. 轧辊轴6. 铜螺丝3. 弹性垫片7. 调整丝杆4. 角接触球轴承8. 偏心套[ 1]精轧机组辊箱常见故障如下。
( 1) 轧辊轴窜动超标, 将影响到成品质量, 特别是出成品的机架, 严重则造成堆钢、辊环炸裂及轧辊轴与油膜轴承抱死等故障。
( 2) 进水问题一直严重影响正常生产, 并常使油品严重污染、乳化, 滤芯堵塞, 造成经常调闸、轴承等磨损加剧或烧油膜轴承等恶性循环现象, 经常性故障造成大量人力及备件损耗, 维护成本高。
( 3) 油膜轴承烧毁, 严重的出现轧辊轴与油膜轴3辊箱常见故障分析针对精轧辊箱出现的以上常见故障, 分别进行深入分析, 总结如下。
( 1) 造成辊箱轧辊轴窜动超标的因素弹性垫片的质量直接影响辊箱轧辊轴及轴承的使用, 弹性垫141整改。
辊箱结构如图 1所示。
到位, 轧制过程中受轧制冲击或振动等影响后弹性垫片变形后, 弹性垫片与轴承间出现间隙, 轧辊轴窜动超标, 严重的冲断轴端挡板螺栓或压盖紧固螺栓; 由于装配过程轴承压盖或端概螺栓安装力矩不均匀, 部分螺栓无有效防松措施, 受轧制冲击振动影响, 轴承压盖或端盖紧固螺栓松动或断裂, 轧辊轴窜动超标。
精轧机常见问题解决

1.精轧机组工艺调整应注意的问题有:(1)精轧机组的工艺调整一般只调整第一架次和成品架次,其他架次不得随意调整,其原因有两个:1)动了其中某一架的辊缝,会破坏各架间的微张力关系,造成产品尺寸波动;2)滚动导卫的导辊开口度是根据样棒精确调整的,若放大某一架辊缝,会造成来料变大,导致导辊使用寿命降低甚至损坏导轮而出废品;若收小某一道次辊缝,会造成来料变小,导轮夹持不稳,会出现倒钢现象。
(2)当成品尺寸高度过大,宽度也过大时,应先调第一架轧机,后调成品轧机;第一架、成品架轧机的累计调整量不得超过0.3mm。
(3)当发现钢坯表面质量不好时,应停机检查辊环、导卫中有无异物。
2.精轧机组生产工艺的特点有:采用固定道次间轧辊转速比,以单线微张力无扭转高速连续轧制的方式;进行合理的孔型设计和精确的轧件尺寸计算,配合以耐磨损的轧槽;采用较小直径的轧辊;以椭—圆孔型系统轧制多规格产品;机架中心距尽可能地小,以减轻微张力对轧件断面尺寸的影响;精轧前及精轧道次间进行轧件穿水冷却,进行轧件变形温度的控制。
3.精轧机组调整的方法在轧制过程中,应根据取样的尺寸及烧木印的情况来调整精轧机。
一般只调整精轧机第一架和最后一架,而其他架次不得随意调整。
下面举例说明:(1)成品垂直直径较大、水平直径稍小时,压小成品架次的辊缝;(2)成品垂直直径较小、水平直径正好时,放大成品架次的辊缝;(3)成品垂直直径正好、水平直径较大时,压小第一架次的辊缝;(4)成品垂直直径正好、水平直径较小时,放大第一架次的辊缝。
如经过上述调整后仍达不到要求,应检查前面机组的来料尺寸,放大或缩小前面机组的最末架次的辊缝。
一般精轧机第一架和最后一架轧机的辊缝累计调整量不得超过0.3mm。
4.精轧机组机架间堆钢的原因有:(1)导卫粘钢;(2)导轮不转或轴承烧坏;(3)轧件劈头;(4)导卫或辊环装错;(5)辊缝设定不当或来料尺寸不合要求;(6)导卫未紧固;(7)压辊键断使辊片松动;(8)辊片碎;(9)轧辊轴轴瓦磨损或破裂。
高线精轧机错辊问题的原因分析与控制措施

现代制造技术与装备
2017 第 6 期 总第 247 期
高线精轧机错辊问题的原因分析与控制措施
陈荣军 屈小波
(江苏永钢集团,张家港 215628)
摘 要:介绍了高线精轧机的运行情况,提出了辊箱错辊的危害性,并对错辊的原因从装配和维护角度进行 分析,提出了具体控制错辊的方法。 关键词:精轧机 错辊 固境因素的影响发生尺寸变化而引起辊箱的错辊。 第三,在滚动轴承的装配使用上,要严格控制轧辊轴 的轴向间隙不超过规定的 0.038mm。超过该间隙时,必须要 更换轴承。同时,要控制轴承的使用周期,一般不超过 2 年。 此外, 在设备维护过程中, 要定期更换水封, 保证油品质量, 确保润滑可靠。在紧固轴承压盖时,要严格按照工艺技术 要求执行,保证压盖螺栓紧固力矩在规定值 70N·m。同时, 要将之前的 8.8 级螺栓改为 12.9 级,并在紧固前涂抹 609 螺纹紧固胶,防止螺栓在辊箱运行中松动甚至断裂。 第四,阻尼垫圈要求装配前,轴承压盖自然放置时, 压盖与轴承座两接触端面间有 0.5 ~ 0.8mm 的间隙(可通 过塞尺检查)。当间隙值过大时,必须严格控制紧固力矩, 防止力矩值过大,导致端盖在螺栓紧固力作用下对阻尼垫圈 过分挤压,因为长时间作用会出现橡胶被挤出、缓冲垫从中 间分裂的现象。当间隙值过小(或为负数)时,在轧钢过程 中,轧辊轴在轴承座内产生轴向的微量窜动。一方面,易引 起缓冲垫的端面磨损;另一方面,轴承和缓冲垫在高频率轴 向力和振动的作用下更容易损坏,大大缩减寿命,进而造成 轴向更大的窜动。此外,在影响成品质量的道次上装配进 口的阻尼垫圈,可提高设备的可靠性和在线运转周期。 第五,在日常维护过程中,必须定期安排人员用百分 表检测在线辊箱的轴向窜动量,当轴向窜动量超过 0.15mm 时,应及时安排该辊箱离线保养。
精轧机碳化钨辊环碎辊原因浅析及相关改进

精轧机碳化钨辊环碎辊原因浅析及相关改进精轧机是一种用于将金属材料进行细致轧制的设备,碳化钨辊环是精轧机的关键件之一。
在使用过程中,碳化钨辊环很容易出现碎辊的问题,这给生产过程带来了很大的影响。
本文将对碳化钨辊环碎辊的原因进行浅析,并介绍一些相关的改进方法。
碳化钨辊环碎辊的原因可以归结为以下几个方面。
1. 材质问题:由于制造过程中的质量问题或原材料的不合格,碳化钨辊环的结构可能存在缺陷或内部应力集中。
这些缺陷和应力可能会在使用过程中逐渐累积,导致碳化钨辊环最终出现碎裂的情况。
2. 使用条件:精轧机的工作环境通常较为恶劣,温度高、压力大,并且存在着较大的冲击和振动。
这些恶劣的使用条件会对碳化钨辊环产生巨大的载荷,加速其疲劳破坏的过程,从而导致碎辊的发生。
3. 使用寿命:精轧机的使用寿命较长,碳化钨辊环通常要承受大量的工作量。
长期的高强度工作会使得碳化钨辊环的材料逐渐疲劳,最终导致碎辊的发生。
1. 材质改进:选择优质的原材料,并加强对碳化钨辊环制造过程中的质量控制,以确保碳化钨辊环的结构完整性和内部应力的均衡分布。
2. 结构设计改进:在碳化钨辊环的结构设计上,采用合理的力学原理和CAD/CAM技术,优化其形状和尺寸,以提高碳化钨辊环的抗疲劳和抗冲击性能。
3. 表面处理改进:通过表面处理方法,如镀层、喷涂等,提高碳化钨辊环的硬度和抗磨损能力,延长其使用寿命。
4. 润滑改进:在精轧机的使用过程中,确保足够的润滑剂,并根据实际情况进行润滑间隔和润滑剂类型的调整,以减少碳化钨辊环的磨损和疲劳破坏。
碳化钨辊环碎辊是精轧机中常见的问题,解决这一问题需要从材质、结构设计、表面处理和润滑等方面进行综合改进。
只有在不断优化和改进的基础上,才能提高碳化钨辊环的性能,减少碎辊的发生,从而保证精轧机的正常运行。
轧钢辊道故障分析及解决方案(最新)

轧钢辊道故障分析及其解决方案(最新)诚达机械设备其平输送辊道是轧钢生产线上数量最多的设备,也是故障最多的设备。
由于轧钢生产的连续性,轧钢生产线上任何一个辊道不转都会造成生产断续。
传统轴承座支撑的伞齿轮传动辊道,是中型以上轧钢生产线上普遍选用的结构,然而它造成的轧钢停机损失是十分惊人的。
一条年产30万吨的伞齿轮传动辊道的中型材生产线,平均每日辊道造成的停机都在两小时以上,对于这样一条生产线来说,在生产过程中停机一个小时就会造成5000元以上的煤耗和人工费损失,一年造成的经济损失就会高达三百多万。
因此,降低辊道故障率、减少辊道故障抢修时间是提高轧钢企业效益的主要途径之一。
一、轧钢辊道故障产生原因分析轧钢辊道的工作特点是输送的钢坯温度高、输送的载荷比较大。
传统轴承座支撑的辊道有两种结构,一种是链传动结构,另一种是伞齿轮传动结构,其主要故障源于两方面,一是轴承的损坏,二是伞齿轮的损坏(对伞齿轮传动而言)。
1、辊道轴承损坏的原因分析①轴承座改变了轴承的设计油隙轧钢辊道的工作特点之一就是输送的钢坯温度高,当辊道输送高温钢坯时, 热量就会通过辊道轴直接传到轴承圈上, 轴承必然从圈开始分别向轴向和径向膨胀.传统轴承座中的轴承在轴向, 由于轴承室宽度往往都大于轴承宽度10%以上, 轴承在轴向有处可胀, 轴承不会因此造成“烧损”,然而轴承在径向, 由于轴承座是上下螺栓固定的结构,轴承室的直径无法改变,当轴承圈随着温度的不断升高不断胀大时,轴承外圈却被轴承座紧固着无法胀大, 因此原始设计的轴承外圈间的油隙就会减小, 轴承就会由于外圈间的油隙过小而产生热量使轴承温度很快升高,直至“抱死”。
为了降低温度提高轴承寿命,有些企业将辊道轴承座设计成穿水结构。
这种措施对轴承有有利的一面,也有不利的一面,有利的一面是降低了轴承外圈的温度,使轴承室的润滑油不会被“烤干”,减少了轴承因缺油而损坏的因素。
不利的一面是降低轴承外圈温度后(轴承圈的膨胀仍然存在),轴承外圈间的的油隙会更加变小,反倒加快了轴承的发热和损坏。
精轧机碳化钨辊环碎辊原因浅析及相关改进

精轧机碳化钨辊环碎辊原因浅析及相关改进精轧机碳化钨辊环碎辊是精轧机重要的零部件之一,其主要作用是在精轧过程中对金属材料进行加工和压制。
在使用过程中,碳化钨辊环碎辊可能会出现磨损、开裂等问题,影响精轧机的正常生产运行。
为了解决这一问题,需要对碳化钨辊环碎辊的原因进行浅析,并提出相关的改进措施。
一、碳化钨辊环碎辊的原因浅析1. 质量问题碳化钨辊环碎辊的质量问题是导致其磨损、开裂等情况的主要原因之一。
在制造过程中,材料的选择、工艺的控制、加工的精度等都会直接影响碳化钨辊环碎辊的质量。
如果质量控制不到位,可能会导致碳化钨辊环碎辊出现内部缺陷或不均匀组织,从而在使用过程中容易出现问题。
2. 工艺问题精轧机在使用过程中,碳化钨辊环碎辊需要承受较大的压力和摩擦力,而一些不合理的工艺设计也可能会导致碳化钨辊环碎辊在工作过程中损伤。
碳化钨辊环碎辊的表面处理不当,或者工作温度过高、压力不均等都可能导致碳化钨辊环碎辊的损伤。
3. 使用条件精轧机在使用过程中,使用条件的控制也会直接影响碳化钨辊环碎辊的磨损和损伤情况。
工作温度、润滑情况、压力大小等都会对碳化钨辊环碎辊的使用寿命产生影响。
二、相关改进措施1. 提高碳化钨辊环碎辊的质量为了解决碳化钨辊环碎辊的质量问题,首先需要加强生产工艺管理,选择优质的碳化钨等原材料,并严格按照生产工艺要求进行生产,确保碳化钨辊环碎辊的质量。
对于一些关键环节,如热处理工艺的控制、表面处理工艺的改进等都应进行加强,以提高碳化钨辊环碎辊的整体质量水平。
2. 改进工艺设计在工艺设计方面,需要对碳化钨辊环碎辊的结构和表面处理进行改进。
通过优化碳化钨辊环碎辊的结构设计,提高其抗压性和抗磨损性,以减少在工作过程中的损伤。
对碳化钨辊环碎辊的表面进行特殊处理,提高其表面硬度和耐磨性,减少因摩擦而导致的损伤。
3. 控制使用条件对于碳化钨辊环碎辊的使用条件,需要加强管理和控制。
通过严格控制工作温度、润滑条件、压力大小等方面来保证碳化钨辊环碎辊在正常工作范围内运行,避免因过度负荷或条件不当导致的碳化钨辊环碎辊损伤。
精轧机碳化钨辊环碎辊原因浅析及相关改进

精轧机碳化钨辊环碎辊原因浅析及相关改进精轧机是金属加工中常用的一种设备,它能将金属材料通过一系列的轧制工艺,使其具有较高的强度和韧性。
在精轧机的运行过程中,碳化钨辊环碎辊问题是经常出现的现象,影响了设备的正常运转和产品的质量。
有必要对精轧机碳化钨辊环碎辊原因进行深入分析,并提出相关的改进措施。
一、碳化钨辊环碎辊的原因1.材料质量问题碳化钨辊环碎辊的原因之一可能是材料质量问题。
由于碳化钨辊环是用于精轧机的关键部件,对材料质量要求较高,若材料质量不过关,很容易导致碎辊的发生。
2.加工工艺问题精轧机的工艺需要经过多道工序,每一道工序都要严格控制,若加工过程中有一环出现问题,可能会影响到后续工序,导致碳化钨辊环碎辊的问题。
3.设备运行问题精轧机设备的运行状态对碳化钨辊环的使用寿命有着重要的影响,若设备运行过程中有一环不稳定或者存在问题,会直接影响到碳化钨辊环的使用寿命。
4.操作管理问题操作人员对设备的使用和维护管理不善,也会导致碳化钨辊环碎辊的问题。
二、改进措施1. 优化材料选用对碳化钨辊环的选材要求严格,要确保质量过关,可以考虑采用优质的碳化钨材料,并在生产过程中加强检测和控制,确保材料质量的稳定。
3. 定期检查设备运行状态对精轧机设备进行定期的检查和维护,确保设备运行状态良好,减少因设备运行问题导致的碳化钨辊环碎辊。
4. 加强操作管理加强操作人员的培训和管理,确保操作人员有良好的技术素养和操作规范,减少因操作管理问题导致的碳化钨辊环碎辊。
通过对碳化钨辊环碎辊原因的浅析以及相关改进措施的提出,可以有效地解决精轧机碳化钨辊环碎辊的问题,提高设备的正常运转率和产品质量,为金属加工行业的发展提供更好的支持。
轧制过程中影响辊缝的因素研究及模型设计

!
结语 辊缝的控制技术在不同类型的轧机上存在完
全不同的控制方式, 本文所论述的辊缝的计算方 式是针对中间辊串动的轧机。对于 /0/ 轧机而 言, 轧机的模量不需动态的计算, 由于轧辊的接触 长度不改变, 因此轧机的模量对同一轧辊来讲是 一个恒定值。冷轧的生产控制有两个永恒的主 题, 那就是厚度控制和板形控制, 而辊缝控制的目 的就是为了达到最理想的厚度精度, 如何验证本 文所分析的因素将是我们下一步要在现场进行实 践的工作。 编辑 王仁意
(改稿日期: $.." & .1 & $1)
(轧辊, 带钢等) 进行轧制线的重新校正, 本文所要 探讨的就是对辊缝调节有影响的多种因素, 并且 提出校零模型的优化设想。 D 辊缝校正的方式 轧机的换辊有两种方式: 有带钢换辊和无带 钢换辊。因此校辊也有两种方式, 有带钢校辊和 无带钢校辊, 校辊的具体控制由校正的执行机构 完成。这两种校辊过程存在很大的差别, 无带钢 校正是 “零” 的矫正, 即辊缝校正必须达到设定的 基准位置, 而有带钢校正继承了带钢的轧制力和 辊缝值, 校正的最终目标是达到原来的辊缝位置。 但是不管哪种方式, 在校正结束后都必须产生一 个基础的轧辊校正位置。 图 ! 是轧辊在校正时的状态描述。当然轧辊 的校正与轧辊的长度, 轧辊的弹性模量等参数都 E
式中, # 为设定的轧制力。 ! 为油膜厚度; 因此实际油膜厚度 ! * 为: ! * $! ’!, !!! 轧机弹性模量对辊缝精度的影响 轧机的弹性模量对辊缝的影响是十分大的, 而且不同的轧辊在不同的轧机上所产生的影响也 是不一样的。本文就目前世界上比较广泛的 / 辊 轧机进行分析。从轧制的原理分析, 轧制力越大, 轧辊的压下越大, 因此对辊缝的影响也大; 但是轧 机的模量与轧制力对辊缝的影响正好相反, 模量 越大, 对辊缝的影响就越小。 下面是轧机的模量对辊缝影响的计算方法。 计算也分为两种: 一是在校正时的计算, 二是在轧 制时的计算。 校正时轧机模量的计算 (+) ( &) ( ( 3 ’ ( 3*) %( $ "’+ & 01 ’ "’" . "’2 & , &) 为校正时轧机模量; 式中, %( & 为中间辊 , &) 接触长度; ( 3 为支撑辊直径; ( 3* 为实验时支撑辊 的直径; "’+ 、 "’" 、 "’2 为补偿系数。 可以看出, 校正时轧机的模量与支撑辊和中 间辊有直接的关系。 (") 轧制时轧机模量的计算 %( , &) ) %( & )5 ’ * , +. & %4 & )5 * 式中, % 为 轧 机 模 量; %4 为 工 作 辊 单 位 模 量; ) 5 为轧辊长度; * 为带钢宽度。 %$
五金辊压机辊缝偏差大的原因及处理

五金辊压机辊缝偏差大的原因及处理五金辊压机是一种常用的机械设备,用于对金属材料进行辊压加工。
在实际应用中,有时会出现辊缝偏差较大的情况,这给加工质量和生产效率带来了一定的影响。
本文将探讨五金辊压机辊缝偏差大的原因,并提出相应的处理方法。
一、原因分析1. 设备调试不当:五金辊压机在使用前需要进行调试,包括辊缝调整等。
如果调试不当,辊缝的偏差就会很大,从而影响加工效果。
因此,设备调试不当是造成辊缝偏差大的一个重要原因。
2. 辊缝磨损:五金辊压机在长时间使用后,辊缝会出现磨损现象。
当辊缝磨损严重时,其尺寸就会发生变化,导致辊缝偏差过大。
3. 材料质量问题:五金辊压机加工的材料质量也会对辊缝偏差产生影响。
如果材料硬度不均匀或厚度不一致,就会导致辊缝偏差较大。
4. 操作不规范:操作人员在使用五金辊压机时,如果操作不规范,如压力过大或过小、进给速度不稳定等,都可能导致辊缝偏差增大。
二、处理方法1. 设备调试:在使用五金辊压机前,必须进行设备调试。
调试时,要仔细调整辊缝,确保其尺寸和位置符合要求。
同时,还要检查设备的其他部件是否正常工作,确保设备能够稳定运行。
2. 定期维护:对于五金辊压机,定期维护是非常重要的。
定期检查辊缝的磨损情况,并及时更换损坏的辊缝。
此外,还要对设备进行润滑和清洁,确保其正常运行。
3. 选择合适的材料:在进行五金辊压机加工前,要选择合适的材料。
材料应具有一定的硬度和均匀的厚度,以保证加工的稳定性和精度。
4. 规范操作:操作人员在使用五金辊压机时,要严格按照操作规程进行操作。
在调整压力和进给速度时,要根据加工要求进行合理调整,避免过大或过小的压力和不稳定的进给速度。
5. 加强培训:为了提高操作人员的技能水平和操作规范性,企业应加强对操作人员的培训。
培训内容包括设备的使用方法、调试方法以及常见故障的处理方法等。
6. 质量检查:在五金辊压机加工过程中,要进行质量检查。
通过检查加工件的尺寸和表面质量,及时发现辊缝偏差大的问题,并采取相应的处理措施。
精轧机窜辊系统精度分析与提高

精轧机窜辊系统精度分析与提高目前1780生产线在品种钢研发和轧制规格上进一步的升级,自2021年上半年成功轧制1.2mm薄规格卷板后,2.0mm以下薄规格热轧板轧制量日益增多。
但其后一年时间内精轧机组窜辊间隙出现增大的趋势,窜辊系统精度降低,严重影响了轧制的稳定性。
到2021年年初情况严重时,每个工作辊辊役期间只能轧制几块到十几块2.0mm 以下薄规格产品,出现浪形和甩尾的情况越来越严重,带来的产品质量异议和降级品也不断增加,严重影响了公司的产品结构和市场销售。
对精轧窜辊系统精度控制已经成为了一个重要的研究课题。
1 窜辊结构简介1780生产线F1-F7轧机采用弯辊和窜辊结合的形式来控制上下工作辊的位置,实现板形控制。
板形控制就是消除带钢纤维内应力或控制在弹性范围内,从而得到良好的凸度和平直度。
窜辊装置可以通过扩大带钢凸度的控制范围,减小带钢横断面上的边部减薄和重新分布边缘附近的轧辊磨损来实现对带钢的板形控制,还可以提高轧辊的使用效率,延长轧辊寿命。
工作辊窜辊系统与工作辊弯辊系统配合,就会在保持良好平直度的同时得到一定的、合乎要求的板形。
窜辊系统主要由固定块、移动块、窜辊液压缸等部件组成,如图1所示。
每架轧机通过4个窜辊缸带动4个移动块来实现上下工作辊的轴向窜动。
窜辊缸活塞杆通过圆螺母锁紧到固定块上,窜辊缸缸体通过销轴连接到移动块上,移动块上镗有穿销轴的孔。
2 窜辊精度分析2021年年底1780轧制的带钢出现单边浪、1/4浪形次数逐渐增多,严重影响轧制的稳定。
由图1可以看出活塞杆与固定块通过圆螺母锁紧。
液压缸缸体通过销轴与移动块连接。
经过现场测量发现两处均有间隙,其间隙总量普遍大于3.5mm。
在这样的窜辊间隙下,必然无法保证板形质量。
精轧机工作辊为CVC辊,窜辊时要克服工作辊与支撑辊之间,弯辊块与固定块之间的双重摩擦力,使窜辊缸缸头受力较大。
精轧机窜辊缸活塞杆侧锁紧结构是球面套加单个圆螺母锁紧。
在轧机振动和轴向力双重作用下,造成圆螺母经常出现松动,严重时会出现螺纹损伤,窜辊缸杆侧间隙由此产生。
精轧振动辊痕的分析与改善

二. 軋機振動類別及要因
穿板衝擊振動:
二. 軋機振動類別及要因
扭轉振動:在產量很大的軋機上以扭轉方式震顫頻率通常在自然 頻率範圍內,及5~20Hz。因為此震動涉及軋輥和連接軸,前者 為一個旋轉的慣性元件;後者為一扭轉的彈簧。 影響: 對於軋延鋼帶的厚度波動影響是很小的。 扭轉震動引起之最大厚度變化公式: d = πft Dwθm / υ × 100% θm :震動所引起的工輥最大角偏移量 ft :扭轉振動頻率Hz Dw :工作輥直徑
二. 軋機振動類別及要因
• 盤捲曲夾輥振動:夾輥之真圓度、同心度、 水平不良或軋下間隙不當,會產生震動, 轉印在鋼帶上。
三. 震動輥痕改善對策
• 振動輥痕大多發生在精軋機組,由其後幾站精軋機對於鋼 帶表面品質影響較大,所以在F5~F7上、下工輥軸承箱上, 以及F7上下背輥軸承箱上各安裝一個加速規(共計8個加速 規)。 • 安裝線上量測系統,在精軋控制室內監測精軋機震動訊號 之波形和頻譜。 • 根據所量測到的軋機震動訊號以及頻譜,分析振動輥痕產 生之機制,由頻譜特徵,找出軋機顫振之振源。
υ :鋼帶出口速度
K: 扭轉彈性常數; J: 總轉動慣量
二. 軋機振動類別及要因
第3音頻振動(Third Octave Vibration):這種方式的振動頻率 通常在相當於音樂中的第3音階頻率範圍的波動。一般軋 機發生在128~256Hz,中鋼#2 HSM實際測試在135~160Hz之 間。
二. 軋機振動類別及要因
第五音頻振動(Fifth Octace Vibration):一般軋機振頻範 圍約在500~1000Hz之間,而CSC的No.2 HSM大多發 生在550~700Hz之間。當設備振動頻率之諧波,進入 此頻區域,該振幅將被放大5~10倍。振動輥痕間距約 為20~30mm。 發生原因:背輥偏心及固定相關組件鋼性不良。 第5音頻f5可由近似式得知: f5 = 360680/Dw 特性: 與第三音頻相反,第五音頻震動的方式是逐漸 產生,並經常在軋輥上伴有震顫痕跡現象的出現。 影響: 軋輥上這些震顫痕能夠引起軋機共振,會在鋼 帶表面上產生一些平行的條痕,由外觀和操作觀點來 看,是有害的,但不影響鋼帶厚度。
轧机质量控制要点

为规范精轧车间轧机段质量控制手法,有效因操作手法不规范或者不一致而造成的不利影响,确保轧机段质量操作的规范性运作,从而保障轧机质量的稳定与产量的规模发挥,特编制本操作规程。
合用于精轧车间中轧机、1#精轧机、2#精轧机作业指导轧坏印、轧花印、打滑印、压靠印、色差亮印、辊印、亮线、划伤、擦伤、斜纹螺旋纹、辊纹粗糙、凹坑、板型不好、公差不符1、轧坏印分析原因:因操作失误(张力设置不合理、弯辊力设置不合理、转辊压靠、辊缝调偏不及时等) 造成的铜带轧坏,导致轧辊表面损伤,进而造成大面积轧坏印。
解决办法:先查看铜带表面有没轧破,若没有轧破,可以做适当调整后继续生产,若铜带轧破了,必须即将停车换辊。
预防措施:张力值必须根据铜带厚度进行范围设置,弯辊力应根据轧制力及带型情况合理添加,杜绝转辊压靠,若辊缝调偏量较大时可采取主机点动运行进行辊缝调偏。
2、轧花印分析原因:由于加工率过大及来料偏硬导致轧不动而进行强行生产所造成的加工硬化印。
解决办法:暂无办法,根据客户表面要求高低定性是否改制。
预防措施:针对加工率较大的铜料,合理分配道次加工率,可以考虑增加道次来避免。
其次,针对轧不动铜带必须及时反馈至车间,由车间进行工艺优化。
3、打滑印分析原因:设备原因及张力设置不合理造成,主要表现在大规格方面。
当轧件的颤动频率与设备传动频率相近时发生的共振现象。
解决办法:调整张力直到铜带不抖为止,若仍不能解决,定性改制该做小规格产品。
预防措施:开机前检查设备有无异常状况,4、压靠印分析原因:轧制工作准备就绪,点击发送按钮后,轧辊压下导致轧辊切面变形量过大形成横辊印。
解决办法:若起步就看到压靠印,可以把轧制油关闭,提升轧制力,把轧辊变形均匀化,待消除后,开油调回正常轧制力,若一次不行可往复多做几次。
预防措施:轧制准备工作时,输入数据时预期轧制力设定在10-20 吨,让轧辊压下的力变小,从而使轧辊变形不明显,起步后慢慢再提升轧制力到指定公差位置,过程中弯辊力也必须同步提升。
- 1、下载文档前请自行甄别文档内容的完整性,平台不提供额外的编辑、内容补充、找答案等附加服务。
- 2、"仅部分预览"的文档,不可在线预览部分如存在完整性等问题,可反馈申请退款(可完整预览的文档不适用该条件!)。
- 3、如文档侵犯您的权益,请联系客服反馈,我们会尽快为您处理(人工客服工作时间:9:00-18:30)。
表 1 机械压下试验动作情况表
Table 1 Experiment data of screwdown moving
费正峰 助工 1977年生 1998年毕业于上海交通大学 现从 事电气专业 电话 26645752
1 精轧辊缝设定原理
1. 1 精轧压下组成部分
精轧压下系统是热连轧生产中的一个重要环
节 ,该系统的主要功能是精轧辊缝设定 。压下系
统工艺主要由 F1 ~ F7 七个机架的电动机械压
下 、液压压下 、弯辊 、CVC 窜辊及支撑辊等组成 。
要的环节之一 ,其主要功能是精轧辊缝设定 。宝 钢分公司热轧厂 2050mm 热连轧精轧压下系统辊 缝设定由机械压下和液压压下共同完成 ,辊缝设 定通过上位机分配设定值到各个机架 ,然后每个 机架根据液压压下油缸位置 ,计算出机械压下和 液压油缸的目标位置 ,首先将机械压下设定到位 , 进而由液压压下进行辊缝精调 。近几年 ,精轧辊 缝变规格设定不到位平均一年会发生 5~6次 ,本 文通过分析研究及相关论证找出影响压下辊缝出 错的原因 ,最终通过程序优化解决精轧变规格辊 缝设定不到位的问题 ,解决了由于支撑辊平衡和 弯辊力引起的困扰精轧多年的压下辊缝出错故 障 ,提高了精轧辊缝设定的稳定性 ,保证了正常的 生产 。
组合
1 2 3 4
种类
支撑辊平衡使用正常平衡 12 MPa,弯辊力设定到基本压力 12 MPa 支撑辊平衡使用正常平衡 12 MPa,弯辊力设定到系统压力 25 MPa 支撑辊平衡使用紧急平衡 25 MPa,弯辊力设定到基本压力 12 MPa 支撑辊平衡使用紧急平衡 25 MPa,弯辊力设定到系统压力 25 MPa
2007年第 2期
宝 钢 技 术
77
精轧变规格辊缝设定不到位问题分析与改进
费正峰 ,王 喆 (宝钢分公司 热轧厂 ,上海 200941)
摘要 :从宝钢分公司热轧厂 2050mm 热轧精轧压下组成部分分析出发 ,结合精轧机械压下和液压压下辊 缝设定的原理 ,同时针对压下辊缝出错的现象 ,通过分析研究及相关论证找出影响压下辊缝出错的原因 ,系支 撑辊平衡和弯辊力等外力的作用引起压下系统辊缝设定出错 ,最终通过程序优化解决精轧变规格辊缝设定 不到位的问题 ,解决了由于支撑辊平衡和弯辊力引起的困扰精轧多年的压下辊缝出错故障 ,提高了精轧辊缝 设定的稳定性 ,保证了正常的生产 。 关键词 :压下 ;支撑辊平衡 ;弯辊
机械压下动作情况
向上 、压下均能动作 向上 、压下有时能动作 向上有时能动作 ,向下不能动作 向上 、向下均不能动作
费正峰等 精轧变规格辊缝设定不到位问题分析与改进
79
通过试验验证 ,机械压下的动作情况在组合 1时能上下动作 ,组合 2和 3时处于临界状态 ,组 合 4时不能动作 。 2. 2. 2 理论计算
stability of the gap set for finish rolling, and guaranteed normal p roduction. Keywords: screwdown; backup roll’s balancing; bending roll
0 前言 热连轧生产中精轧压下系统是精轧区域最重
弯辊系统有 4 个双面作用的油缸 ,弯辊箱分 别依附在压下工作辊轴承箱上并顶住上辊轴承 箱 。弯辊工作时通过油压系统将油打入双侧油 缸 ,使其产生向上的力 (对上辊来说 ) ,在托住带 有附属轴承箱的上工作辊的同时 ,工作辊向上弯 曲从而达到想要的板形 。弯辊力由过程机根据板 形需要设定 ,基本力为 12 M Pa。而弯辊系统的最 高压力为 25 M Pa的油库系统压力 。对于在轧钢 过程中支撑辊平衡系统也可能存在两种压力 ,正 常平衡时的 12 M Pa和紧急平衡时的 25 M Pa。平 衡力和弯辊力最终都作用在机械压下丝杆上 。
2 精轧辊缝设定不到位的情况及原因分析 2. 1 精轧辊缝设定不到位的情况
正常轧钢过程中 ,在无任何故障显示情况下 , 突然出现一块钢的压下辊缝执行不到设定值 ,并且 液压油缸以一定的速度一直走到落底位置 。在正 常轧制过程中发生以上故障时 ,操作工很难发现 , 等发现时带钢已经轧制到机架中 ,只能敲紧停 ,处 理完废钢后重新设定的辊缝又一切正常 。对于这
液压压下是由 1套液压位置调节器软件来调 节伺服阀的电流 ,控制伺服阀的油流量 ,从而改变 油缸里的油压 ,使油缸缸体上下移动 ,调节辊缝 , 达到辊缝精调的目的 。此时液压油缸动作时活塞 连同压下螺栓一起不再移动 。
压下辊缝静态设定过程如下 :带钢进入飞剪 之前 ,过程机将 F1 ~F7 的压下辊缝设定值传输 给基础自动化 (BA ) ,接着将设定值分配到各个机 架 ,然后每个机架根据液压压下油缸位置 ,计算出 机械压下和液压油缸的目标位置 ,首先将机械压 下设定到位 ,进而由液压压下进行精调 [ 2 ] 。
F e i Zh en gfeng, W ang Zhe ( Hot Str ip Rolling Plan t, Baosteel Branch, Shangha i 200941, Ch ina )
Abstract: Causes that lead to errors of screwdown roll gap have been found out through analyzing finish rolling screwdown components of the 2050mm m ill in Hot Strip Rolling Plant, Baosteel B ranch. It is the external force’s ac2 tion, such as backup roll’s balancing and roll bending force that cause the roll gap setting error in the screwdown sys2 tem. Finally through analysis and investigation, the error was corrected by op tim izing the p rogram. It imp roved the
表 2 机械压下理论动作情况表
Table 2 Theoretical action of mechanical screwdown
组合
种类
机械压下所需的 驱动扭矩 / ( kN ·m )
驱动电机能提供的 驱动扭矩 / ( kN ·m )
结果
支撑辊平衡使用正常平衡 12 MPa, 弯辊力
1
设定到基本压力 12 MPa
根据精轧压下系统组成结构 ,机械压下下压 时存在的外力主要是支撑辊平衡系统和弯辊系统 形成的 。
支撑辊平衡系统有一个油缸 ,通过扁担梁托 住支撑辊 ,平衡有两种方式 :正常平衡和紧急平 衡 。能够产生 3种平衡力 :正常平衡在轧钢状态 为 12 M Pa,在换辊状态为 18 M Pa,紧急平衡在轧 钢和换辊时均为系统压力 25 M Pa。
中图分类号 : TG335. 5 + 5 文献标识码 : B 文章编号 : 1008 - 0716 (2007) 02 - 0077 - 04
Ana lysis of Im perfect Roll Gap Setting for Str ip Th ickness Chang ing in F in ish Rolling and Its Im provem en t
:
丝杆
、丝母的
牙形角
α 1
= 8°,
α 2
= 33°,导程 L
= 24 mm ,中径
d3
= 493 mm;钢 —
铜静摩擦因数 μ = 0. 15;轴承效率取 η = 0. 95。
以单个丝杆丝母上所受的力进行计算 。假设
电机力能参数 : 功率 Pd = 90 kW ,转速 nd = 715 r/m in ;齿轮箱的减速比 n1 = 2. 409 和涡轮 涡杆的传动比 n2 = 50∶2。
(1)
式中 , Stheory为 液压 压下 理论 设定 值 , mm; Se
为过程机设定辊缝 , mm; Sm ist为机械压下实际位置
值 , mm。
机械压下由 1台直流马达带动双侧的螺栓进
行工作 。该马达通过 1套减速箱和 2个压下螺丝
78
宝 钢 技 术
2007年第 2期
图 1 精轧压下组成部分简图
种“幽灵 ”故障 ,跟踪起来相当困难。精轧机架辊缝 设定不到位困扰精轧多年 ,平均一年发生 5~6次。 2. 2 原因分析
在没有预应力的情况下 ,轧制过程中变规格 时 ,新的辊缝设定如果超出液压油缸的工作行程 , 就需要机械压下动作 ,辊缝设定不到位的情况也 正是需要机械压下动作的时候 ,对于丝杆 、丝母传 动机构的机械压下 ,如果此时有一个外力刚好将 其压死 ,就会产生机械压下到位的虚假信号 ,根据 辊缝公式 ( 1) ,液压辊缝就会超出其液压油缸的 工作范围 ,液压油缸工作在异常点 ,造成油缸落 底 ,辊缝设定就不能到位 。本文分析了导致机械 压下不能动作的外力来源 。 2. 2. 1 外力的形成
辊缝执行时 ,保证支撑辊平衡力和弯辊力不能把 机械压下的丝杆丝母机构压死 。 3. 1 对支撑辊平衡系统的优化
轧钢时优先选用正常平衡 ,只有正常平衡在 压力偏差大于门槛值的一定时间后 ,才会自动跳 到紧急平衡 ,紧急平衡时为系统压力 。所以 ,对于 支撑辊平衡力 ,首先要解决使用正常平衡轧钢时 经常跳到紧急平衡的现状 。
74. 320
不能驱动Biblioteka 注 :保证驱动所需的安全系数一般取 1. 6~2. 0,故 4种组合的机械压下所需驱动扭矩乘以最小安全系数 1. 6 后可知 ,组合 1 时可靠