硅烷与磷化对比~
问题]-硅烷与磷化成本对比
![问题]-硅烷与磷化成本对比](https://img.taocdn.com/s3/m/04996ba31a37f111f0855b0a.png)
问题]硅烷处理和磷化前处理各有什么优缺点啊?还有就是硅烷技术目前是否成熟!!![建议]比较环保的除耐盐雾试验时间只有350h外,各项性能都优于磷化,那要看你用在什么件上,如耐腐蚀条件高的不适用。
磷化与硅烷成本优势分析硅烷产品的高效节能主要体现在以下几个方面:1、热能:磷化(以磷化温度40-50度计算)目前国内喷淋磷化线热能消耗在70元/千平方米左右硅烷(仅冬天加热到15度以上)预计热能消耗在10元/千平方米热能方面:磷化比硅烷贵了60元/千平方米以月均处理10000平方米计算,磷化共贵了600元2、动能:(以目前每年运行2000小时计算)采用硅烷工艺,可以关闭表调槽泵和钝化槽泵,以4.0KW的功率计算,每年电费(以电价1元计算)2*2000*4.0=16000元,全年计算,磷化共贵了16000元3、废水处理磷化中磷酸根约15000PPM,锌、镍、锰合计约3000PPM,水洗因子以100计算,后道水洗达到溢流动态平衡时,废水中含磷酸根约1500PPM,锌、镍、锰合计约300PPM,处理每吨废水约8元。
硅烷中不含磷,硅含量约40PPM,锆含量约200PPM,水洗因子以100计算,后道水洗达到溢流动态平衡时,废水中含硅约4PPM,锆约20PPM,处理每吨废水不到1元。
以月均处理10000 平方米,每平方米约产生4L 废水计算,全年约处理480 吨废水,磷化共贵了3360元。
磷化槽液处理一段时间就会有磷化渣,而硅烷没有,不需要除渣设备。
综上统计:以全年生产120000平方米计算,使用硅烷产品比磷化节约19960元RMB。
随着磷产品和锌、镍产品、能源价格的不断上涨,硅烷产品在综合成本上的优势将更加不可动摇。
另外,硅烷产品还具有以下的突出优势:1、环保性硅烷产品和磷化相比,不含锌、镍、锰等重金属,显著减少水耗量,显著减少废水处理量;室温工作,不含磷,不含氧化还原剂,无氮氧化物废气排放,几乎无渣(所有金属出渣量<0.1g/m2),由于出渣量低,可完全闭路水处理,循环用水,不产生废水。
硅烷-前处理2016

硅烷处理
硅烷处理
电泳涂装
电泳涂装后耐冲击性测试 中达到50kg.cm
电泳涂装
电泳涂装后在NSS(中性盐 雾)测试中达到800小时
优点
• 硅烷技术形成的超薄有机膜可以替代传统的磷化膜 • 磷化膜的重量通常为2-3g/㎡, OXSILAN涂层膜重仅仅
0.1 g/㎡,相差20倍左右。 • 单耗大大降低。
脱脂
水洗 纯水洗
硅烷
纯水洗
电泳
磷化与硅烷处理技术在使用条件方面的区别化与
项目 温度 时间 成渣量 换槽周期 耗水量/m2 膜层密度 膜重 膜厚 晶型 检测参数
磷化 35-55℃
3分 3-12g/m2
2-6个月 4升
1.5g/cm2 2-3g/m2 1-2µm
晶体 游离酸、总酸、促进剂、氟硅酸 含量、锌、镍、锰含量等
金属表面处理剂
Metal surface treatment
上海耀岩化学品有限公司
Shanghai yaoyan chemical Co., Ltd.
代替传统磷化-硅烷处理剂
传统磷化工艺的缺陷
含磷,废水 处理困难
需加热 能耗高
废水产生多, 费用高
缺陷
废渣多 处理难
含致 癌物
有害的重 金属离子
工序多,投 资成本高
废水处理的要求越来越高,成本也呈上升趋势 渣产出量小于0.1g/m2,而锌系磷化一般产渣量在1-5gm2 省却了对磷化槽和管路中磷化渣的定期清理和使用大量清洗化学品 避免了磷化废渣对环境的影响和污染,降低处理费用 废水量少,减轻了废水处理的压力 废水处理更容易,处理设备和占地更少 目前大多数磷化工艺使用亚硝酸钠作为促进剂 亚硝酸钠被证明是一种致癌物质
硅烷薄膜工艺对车身耐腐蚀和外观的影响

生态需求。
目前前处理市场上常用的有锌锰镍三元
锌系磷化前处理、硅烷处理、锆化处理以及硅烷和
图1 硅烷薄膜前处理原理
⽊㒘㵲䐍㵲䐍⽊㒘㵲䐍㵲䐍㯏㻕
㯏㻕㯏㻕
㯏㻕⪠㯏㻕
⪠㯏㻕⪠㯏㻕⪠㯏㻕
⪠㯏㻕⪠㯏㻕
ⰼ⿐
㯏㻕⢎⮘㾠㻖㑸⿐
图3
循环
(a)磷化
硅烷薄膜前处理工艺与磷化前处理工艺对比(电镀锌板)
(a)薄膜(a)磷化(b)磷化硅烷薄膜前处理工艺与磷化前处理工艺对比(铝硅镀层热成型板)
硅烷薄膜前处理工艺与磷化前处理工艺对比
(无镀层板)
硅烷薄膜工艺生产问题及改进
艺参数范围内)对热镀锌板材有不良反应,电镀锌板材通过该参数范围符合质保石击要求。
初步分析。
硅烷技术-磷化技术的革命性变革

硅烷技术----磷化技术的革命性变革陈慕祖周杰(上海大众汽车有限公司201805)摘要:硅烷技术可以替代磷化技术,给表面预处理技术带来革命性的变革。
本文介绍了硅烷技术的原理、技术特点以及应用现状和前景。
1前言在各种金属预处理方法中,磷化处理是最为广泛采用的方法。
在家用电器、自行车、摩托车和汽车等行业中,为了保证涂层优良的耐久性和防腐蚀性能,都采用磷化处理作为涂装的前处理。
自1906年美国伯明翰的Thomas Watts Coslett首创磷化技术以来,磷化技术已有百年历史。
百年来,磷化技术经久不衰,不断发展,从30年代的锌系磷化技术和铁系磷化技术到60~70年代的改良锌系磷化技术,随后到90年代初期的无镍磷化技术,最终到2002年氧化铁系磷化技术。
随着磷化技术的不断发展创新,其应用领域越来越广,为防腐蚀事业作出了突出贡献。
为了贯彻清洁生产的标准,开发更加环保的技术和产品,近年来有一些新的磷化技术得到开发及应用,具体应用状况如图1所示:图1 近年来预处理环保技术的应用状况尽管人们做了很大的努力,依然无法从根本上改变磷化过程。
传统预处理工艺具有高能耗、重金属离子含量高、含致癌物、废水废渣排放多等缺陷。
随着环保和节能呼声的日渐增高,预处理技术正朝着保护环境、降低成本、提高质量和操作简便等方向发展。
硅烷技术是预处理技术的最新发展方向,它具有环保、节能、操作简便、成本低等磷化技术无可替代的优点。
目前硅烷技术在普通工业中已开始逐步取代铁系和锌系磷化,在汽车工业中正在开发试验过程中。
硅烷技术是采用OXSILAN超薄有机涂层替代传统的结晶型磷化保护层,在金属表面吸附了一层超薄的类似磷化晶体的三维网状结构的有机涂层,同时在界面形成的Si-O-Me共价键(其中:Me=金属)分子间力很强,将与金属表面和随后的油漆涂层形成良好的附着力。
硅烷技术的成功应用给磷化技术带来革命性的变革。
2 硅烷技术原理硅烷技术的反应机理如下:2.1 在使用过程中,水解后的OXSilane分子(≡Si(OR)3)中的SiOH基团与金属表面的MeOH基团形成氢键,快速吸附于金属表面。
硅烷化和磷化的防锈能力

硅烷化和磷化的防锈能力
硅烷化和磷化是两种常见的金属表面处理方法,它们都可以用
于提高金属材料的防锈能力。
首先我们来看硅烷化,硅烷化是利用
硅化合物对金属表面进行化学处理,形成一层硅化合物的保护膜,
从而防止金属表面与空气中的水和氧气发生反应,减少金属的氧化
腐蚀。
硅烷化处理后的金属表面具有良好的耐腐蚀性能,能够在潮
湿或腐蚀性环境中保持较长时间的良好外观和性能。
而磷化是将金属表面处理成磷化层,磷化层可以有效地减少金
属与外界环境的接触,从而减少金属的氧化反应,提高金属的耐腐
蚀性能。
磷化层通常具有较高的硬度和耐磨性,能够有效地延长金
属的使用寿命,并且可以提高金属表面的润滑性能,降低摩擦系数,减少磨损。
总的来说,硅烷化和磷化都是有效的金属表面处理方法,可以
提高金属材料的防锈能力。
它们可以在不同的工业领域中得到广泛
应用,例如汽车制造、航空航天、建筑等领域,以保护金属制品免
受腐蚀和氧化的影响。
当然,选择何种方法还需要根据具体的金属
材料和使用环境来进行综合考虑和选择。
精选汽车涂装新技术概述

2-3 g/m2 氧化锆转化膜重 : 附0着.0力2-0和.2耐g蚀/m性2 能与 磷化膜相当
汽车涂装预处理新技术
(2)省去表调、钝化处理,可在脱脂清洗 或酸洗后处理,磨层耐酸碱、机械性 能和热稳定性能良好,与原有涂装工 艺和设备基本相容,无需进行大的设 备改造
(3)槽液非常稳定且容易控制,平时生产 中只需控制好温度和pH值,而锌系磷 化每天都要定期检测总酸、游离酸、 促进剂以及锌、镍、锰的含量等许多 参数,这样就节省了大量的工艺管理 费用
应用:范围广,大多数零部件
汽车涂装技术概述
(3)静电喷涂 概念:在喷涂设备上加一定电压的静电电量, 使喷出涂料带有一定电压的静电,利用 静电吸附原理将涂料涂布于被涂物表面 的涂装方法
特点:涂料浪费较少、对操作人员技术水平要 求不高、对喷涂设备要求较高、对环境 影响较小
应用:大多数零部件
汽隔离雨水作用-雨淋后集聚的水珠
汽车涂装技术概述
(2)装饰作用 汽车涂装的装饰性主要取决于涂层的色彩 、光泽、鲜艳程度和外观等。
不同角度变色漆的不同颜色
汽车涂装技术概述
(3)特殊标识作用 标识作用通过涂料的颜色来体现。 在汽车上涂装不同颜色和图案以便区别不同 的用途。例如: 消防车涂成大红色; 邮政车涂成橄榄绿,字号车号为白色; 救护车为白色并做红十字标记等; 工程车涂成黄黑色相间的条纹,字号车号 用黑色等。
涂装的定义
涂装是指各种车辆的车身及其零部件的涂漆 装饰。根据涂装对象不同,汽车涂装可分 为新车涂装和修补涂装两大体系。
具体地说:涂装是将涂料涂覆于经过处理的 基底表面上,经干燥成膜的一种表面处理 工艺。已经固化的涂料膜称为涂膜或漆膜 ,有两层以上涂膜组成的复合层称为涂层 。汽车表面涂装就是典型的多涂层涂装。
硅烷和磷化综合对比分析

传统磷化和硅烷综合对比分析
硅烷与一般锌系磷化是各有利弊,不可替代!
硅烷在使用工艺上是简便了,但是它的膜薄容易腐蚀,而传统磷化膜厚可以放置长时间不生锈。
硅烷在价格方面还是比传统磷化液要高一些,虽说它只是一组分, 可磷化液的其他组分用量也很小,开槽剂只开槽使用,调整剂促进剂也只是千分之几的添加。
另外传统磷化在使用中范围挺宽,也不用经常调。
硅烷对水质要求高,而传统磷化液对水质没什么要求,任何水都可以配制。
硅烷是有机物,且对工艺要求较高,只能用去离子水,所以硅丸稳定性极差,且有渣。
就目前市场情况来看,硅烷虽然有处理面积大,沉渣少,有一定的环保性的优点;但也有一定的缺点:对水质要求高、防腐周期短、工艺要求严格,各工序间不允许有混槽、串槽现象。
所以推广使用的不如传统磷化液广泛。
可见传统磷化液的使用及功能也是硅烷无法替代的!。
硅烷+电泳”与“磷化+电泳”配套性能的对比

硅烷+电泳”与“磷化+电泳”配套性能的对比作者:渠二朝来源:《理论与创新》2017年第28期摘要:硅烷前处理技术完全可以替代磷化前处理技术,以适应节能和环保的双重要求。
但硅烷处理技术的进一步推广还有很多工作要做,相信在不久的将来,硅烷技术一定会和磷化技术一样成熟地应用于汽车涂装领域。
关键词:硅烷+电泳;磷化+电泳;配套性能;对比1概述文章介绍了一种有机硅烷钝化液,它可以用于阴极电泳的前处理。
对钝化膜的耐碱性及电泳后漆膜的附着力、耐冲击、耐腐蚀等性能进行测试,并与使用传统磷化液前处理的电泳工艺进行比较。
结果表明:经有机硅烷前处理后的阴极电泳漆膜的性能符合相关行业要求,证明有机硅烷处理和阴极电泳漆完全配套,可以在汽车及相关行业中推广应用。
硅烷化处理是以有机硅烷为主要原料对金属材料进行表面处理的过程,与传统磷化处理相比具有以下优点:①硅烷化处理无有害重金属离子;不含磷;不需要加温;②硅烷处理不会产生沉渣,处理时间短,控制简便;③硅烷化处理步骤少,不用表调工序,槽液可重复使用;④有效提高涂料对基材的附着力;⑤可共线处理铁板、镀锌板、铝板等多种基材。
目前,家电行业喷漆或喷粉前处理多采用磷化以及铬钝化处理,但这两种方法均存在较大的缺陷,对于环保方面来说:磷化含锌、锰、镍等重金属离子并且含有大量的磷;铬钝化处理本身就含有严重毒性的铬,因此这两种方法不能适应国家对于涂装行业的环保要求。
同时在使用成本方面:磷化处理过程中会产生磷化渣,需要安装配套的除渣装置,并且磷化需要30~50℃下进行,因此还需要对磷化槽进行加热;并且磷化及铬钝化后需要大量的水对工件进行漂洗。
以上两种方法在环保性及使用成本方面存在缺陷,因此一种新型的,环保、节能、低排放、低使用成本的前处理技术就因此而诞生了——那就是硅烷化处理技术。
2“硅烷+电泳”与“磷化+电泳”配套性能的对比2.1底材、薄膜干燥方式和前处理品种对电泳漆膜厚的影响在底材和电泳漆都一样的条件下,使用A前处理产品时,前处理薄膜的干燥方式对电泳漆膜厚基本无影响。
磷化处理和硅烷处理的区别

磷化处理和硅烷处理的区别项目 磷化处理 硅烷处理工艺原理 磷化处理就是金属表面与磷化液接触发生化学反应,在金属表面生成稳定的不溶性的无机化合物膜层的化学处理方法,所生成的膜被称为磷化膜。
磷化膜的作用是在充分脱脂的基础上能提供清洁、均一、无油的表面。
硅烷化处理是以有机硅烷为主要原料对金属或非金属材料进行表面处理的过程。
是利用氟锆酸与硅烷的水解反应,在金属表面形成一种由氧化锆ZrO2和氧化硅SiO2组成的三维网状化合物,该化合物在被处理的金属表面起到耐腐蚀并增加附着力的作用。
工艺流程 脱脂-水洗-新水洗-表调-磷化-水洗-水洗-纯水洗:8道工序脱脂-水洗-新水洗-硅烷-水洗-水洗-纯水洗:7道工序硅烷工艺无需表面调整。
表面调整的目的是促使磷化,形成晶粒细致、密实的磷化膜,以及提高磷化速度。
表面调整剂主要有两类,一种是酸性表调剂,如草酸,另 一种是胶体钛。
前者还兼有除轻锈 (工件运行过程中形成的“水锈”及“风锈”)的作用。
在磷化前处理工艺中,是否选用表面调整工序和选用哪一种表调剂都是由工艺与磷化膜的要求决定的。
一般原则是:涂装前打底磷化、快速低温磷化需要表调。
如果工件在进入磷化槽时已经二 次生锈,最好采用酸性表调。
工艺技术 工艺流程需要表面调整;含磷及锌镍锰铬等重金属;污染物大;耗能高(35℃-55℃);处理时间长(120s-180s);沉渣多工艺流程无需表面调整;无磷及锌镍锰铬等重金属;污染物排放量较少;无需加热(室温);处理时间较短(60s-120s);几乎无渣皮膜 皮膜构造:磷酸锌结晶;皮膜厚:2-3g/m²;耐酸碱性:溶解。
皮膜构造:非晶态混合薄膜;皮膜厚:0.2-0.4g/m²;耐酸性:氢氟酸HF以外全不溶解;耐碱性:不溶解。
沉渣 磷化反应机理大致分为酸蚀反应和磷化反应。
磷化反应是金属表面与磷化液中的磷酸盐反应,最终以磷酸锌的形式在被处理物表面结晶,形成保护膜的化学过程。
替代磷化的硅烷的好处
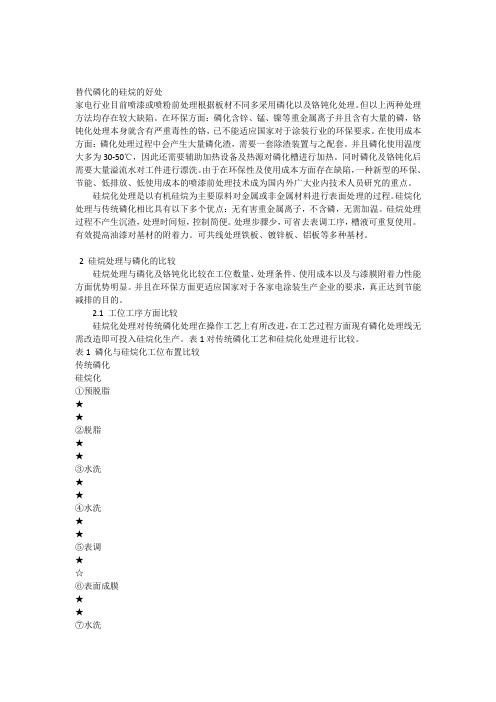
替代磷化的硅烷的好处家电行业目前喷漆或喷粉前处理根据板材不同多采用磷化以及铬钝化处理。
但以上两种处理方法均存在较大缺陷。
在环保方面:磷化含锌、锰、镍等重金属离子并且含有大量的磷,铬钝化处理本身就含有严重毒性的铬,已不能适应国家对于涂装行业的环保要求。
在使用成本方面:磷化处理过程中会产生大量磷化渣,需要一套除渣装置与之配套。
并且磷化使用温度大多为30-50℃,因此还需要辅助加热设备及热源对磷化槽进行加热。
同时磷化及铬钝化后需要大量溢流水对工件进行漂洗。
由于在环保性及使用成本方面存在缺陷,一种新型的环保、节能、低排放、低使用成本的喷漆前处理技术成为国内外广大业内技术人员研究的重点。
硅烷化处理是以有机硅烷为主要原料对金属或非金属材料进行表面处理的过程。
硅烷化处理与传统磷化相比具有以下多个优点:无有害重金属离子,不含磷,无需加温。
硅烷处理过程不产生沉渣,处理时间短,控制简便。
处理步骤少,可省去表调工序,槽液可重复使用。
有效提高油漆对基材的附着力。
可共线处理铁板、镀锌板、铝板等多种基材。
2 硅烷处理与磷化的比较硅烷处理与磷化及铬钝化比较在工位数量、处理条件、使用成本以及与漆膜附着力性能方面优势明显。
并且在环保方面更适应国家对于各家电涂装生产企业的要求,真正达到节能减排的目的。
2.1 工位工序方面比较硅烷化处理对传统磷化处理在操作工艺上有所改进,在工艺过程方面现有磷化处理线无需改造即可投入硅烷化生产。
表1对传统磷化工艺和硅烷化处理进行比较。
表1 磷化与硅烷化工位布置比较传统磷化硅烷化①预脱脂★★②脱脂★★③水洗★★④水洗★★⑤表调★☆⑥表面成膜★★⑦水洗☆⑧水洗★☆注:★需要☆不需要由表1可见,硅烷化处理与磷化处理相比较可省去表调及磷化后两道水洗工序。
因硅烷化处理时间短,因此在原有磷化生产线上无需设备改造,只需调整部分槽位功能即可进行硅烷化处理:(1)对于悬链输送方式改造,可将①预脱脂、②脱脂、④水洗、保留;③水洗改为脱脂槽;⑤表调、⑥磷化改为水洗槽;⑦水洗改为硅烷化处理;⑧备用。
硅烷化处理
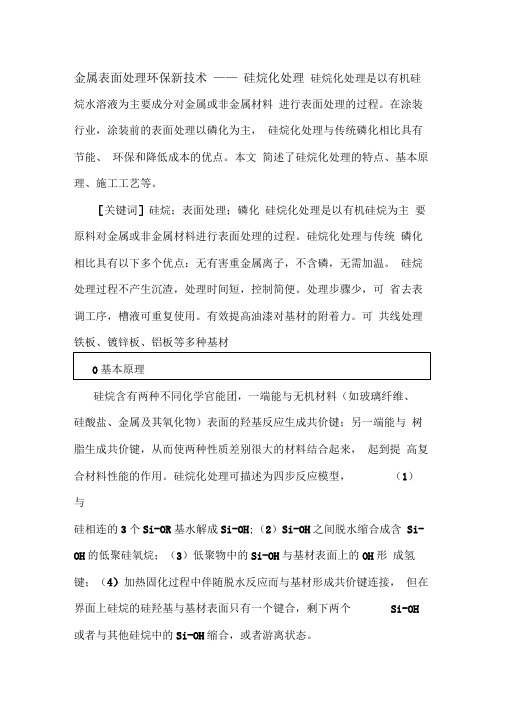
金属表面处理环保新技术——硅烷化处理硅烷化处理是以有机硅烷水溶液为主要成分对金属或非金属材料进行表面处理的过程。
在涂装行业,涂装前的表面处理以磷化为主,硅烷化处理与传统磷化相比具有节能、环保和降低成本的优点。
本文简述了硅烷化处理的特点、基本原理、施工工艺等。
[关键词]硅烷;表面处理;磷化硅烷化处理是以有机硅烷为主要原料对金属或非金属材料进行表面处理的过程。
硅烷化处理与传统磷化相比具有以下多个优点:无有害重金属离子,不含磷,无需加温。
硅烷处理过程不产生沉渣,处理时间短,控制简便。
处理步骤少,可省去表调工序,槽液可重复使用。
有效提高油漆对基材的附着力。
可共线处理铁板、镀锌板、铝板等多种基材硅烷含有两种不同化学官能团,一端能与无机材料(如玻璃纤维、硅酸盐、金属及其氧化物)表面的羟基反应生成共价键;另一端能与树脂生成共价键,从而使两种性质差别很大的材料结合起来,起到提高复合材料性能的作用。
硅烷化处理可描述为四步反应模型,(1)与硅相连的3个Si-OR基水解成Si-OH;(2)Si-OH之间脱水缩合成含Si-OH的低聚硅氧烷;(3)低聚物中的Si-OH与基材表面上的OH形成氢键;(4)加热固化过程中伴随脱水反应而与基材形成共价键连接,但在界面上硅烷的硅羟基与基材表面只有一个键合,剩下两个Si-OH 或者与其他硅烷中的Si-OH缩合,或者游离状态。
为缩短处理剂现场使用所需熟化时间,硅烷处理剂在使用之前第步是进行一定浓度的预水解①水解反应:在水解过程中,避免不了在硅烷间会发生缩合反应,生成低聚硅氧烷。
低聚硅氧烷过少,硅烷处理剂现场的熟化时间延长,影响生产效率;低聚硅氧烷过多,则使处理剂浑浊甚至沉淀,降低处理剂稳定性及影响处理质量。
②缩合反应:成膜反应是影响硅烷化质量的关键步骤,成膜反应进行的好坏直接影响涂膜耐蚀性及对漆膜的附着力。
因此,对于处理剂的PH值等参数控制显的尤为重要。
并且对于硅烷化前的工件表面状态提出了更高的要求:1、除油完全;2、进入硅烷槽的工件不能带有金属碎屑或其他杂质;3、硅烷化前处理最好采用去离子水。
硅烷皮膜剂价格
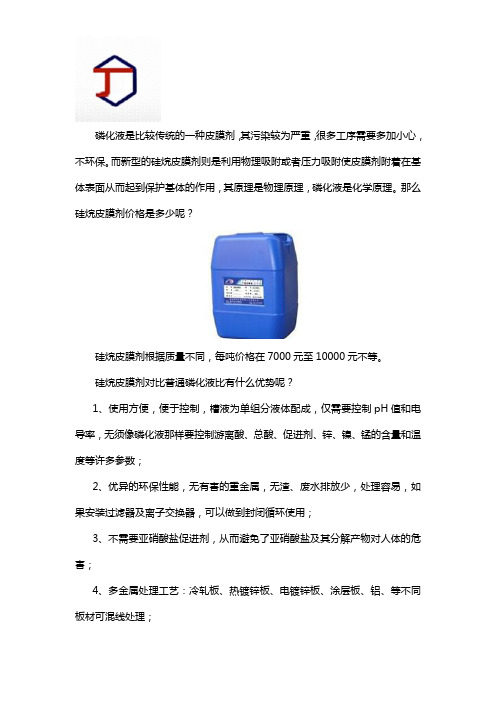
磷化液是比较传统的一种皮膜剂,其污染较为严重,很多工序需要多加小心,不环保。
而新型的硅烷皮膜剂则是利用物理吸附或者压力吸附使皮膜剂附着在基体表面从而起到保护基体的作用,其原理是物理原理,磷化液是化学原理。
那么硅烷皮膜剂价格是多少呢?硅烷皮膜剂根据质量不同,每吨价格在7000元至10000元不等。
硅烷皮膜剂对比普通磷化液比有什么优势呢?1、使用方便,便于控制,槽液为单组分液体配成,仅需要控制pH值和电导率,无须像磷化液那样要控制游离酸、总酸、促进剂、锌、镍、锰的含量和温度等许多参数;2、优异的环保性能,无有害的重金属,无渣、废水排放少,处理容易,如果安装过滤器及离子交换器,可以做到封闭循环使用;3、不需要亚硝酸盐促进剂,从而避免了亚硝酸盐及其分解产物对人体的危害;4、多金属处理工艺:冷轧板、热镀锌板、电镀锌板、涂层板、铝、等不同板材可混线处理;5、硅烷处理没有表调、钝化等工艺过程,较少的生产步骤和较短的处理时间有助于提高工厂的产能;新建生产线可缩短,节约设备投资和占地面积;6、常温使用,节约能源。
硅烷槽液不需要加温,传统磷化一般需要35℃~55℃;7、与现有设备工艺不冲突,无须设备改造可直接替换磷化,与原有涂装处理工艺相容,能与目前使用的各类油漆和粉末涂装相匹配;8、硅烷处理后形成的超薄有机膜完全可以替代传统的磷化膜,磷化膜厚通常为2~3um,硅烷处理后的膜厚为0.5um,每公斤硅烷处理剂可处理200~300平方米,性价比远高于磷化处理产品。
硅烷皮膜剂在实际使用中应该注意哪些事项呢?(1)为了获得品质优良的皮膜性能,就需使用纯水。
同时为了延长槽液的使用寿命,硅烷槽液需使用纯水。
一般要求自来水也可正常生产。
(2)不可使用铸铁槽体。
为了减少对槽体侵蚀及由此引起的硅烷有效成分的损失,槽体建议使用铸铁外的其它材质,如304以上不锈钢、有玻璃钢内衬或硬PVC和PE内衬的铸铁槽体。
(3)传统磷化线改用硅烷时只需将磷化渣冲洗干净即可。
金属表面硅烷处理技术
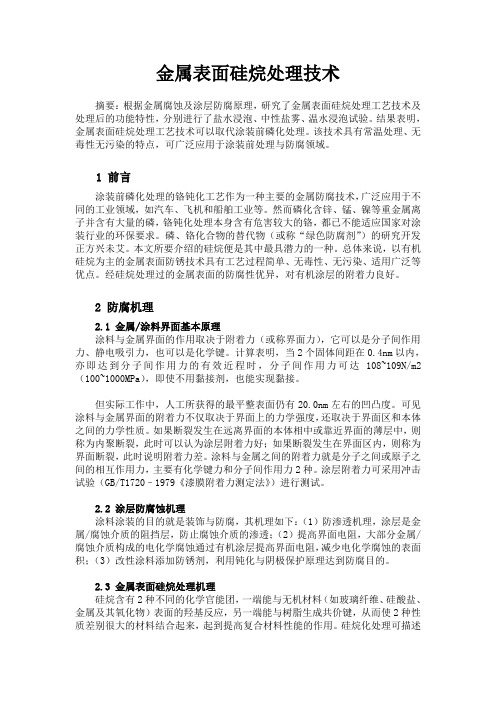
金属表面硅烷处理技术摘要:根据金属腐蚀及涂层防腐原理,研究了金属表面硅烷处理工艺技术及处理后的功能特性,分别进行了盐水浸泡、中性盐雾、温水浸泡试验。
结果表明,金属表面硅烷处理工艺技术可以取代涂装前磷化处理。
该技术具有常温处理、无毒性无污染的特点,可广泛应用于涂装前处理与防腐领域。
1 前言涂装前磷化处理的铬钝化工艺作为一种主要的金属防腐技术,广泛应用于不同的工业领域,如汽车、飞机和船舶工业等。
然而磷化含锌、锰、镍等重金属离子并含有大量的磷,铬钝化处理本身含有危害较大的铬,都已不能适应国家对涂装行业的环保要求。
磷、铬化合物的替代物(或称“绿色防腐剂”)的研究开发正方兴未艾。
本文所要介绍的硅烷便是其中最具潜力的一种。
总体来说,以有机硅烷为主的金属表面防锈技术具有工艺过程简单、无毒性、无污染、适用广泛等优点。
经硅烷处理过的金属表面的防腐性优异,对有机涂层的附着力良好。
2 防腐机理2.1 金属/涂料界面基本原理涂料与金属界面的作用取决于附着力(或称界面力),它可以是分子间作用力、静电吸引力,也可以是化学键。
计算表明,当2个固体间距在0.4nm以内,亦即达到分子间作用力的有效近程时,分子间作用力可达108~109N/m2(100~1000MPa),即使不用黏接剂,也能实现黏接。
但实际工作中,人工所获得的最平整表面仍有20.0nm左右的凹凸度。
可见涂料与金属界面的附着力不仅取决于界面上的力学强度,还取决于界面区和本体之间的力学性质。
如果断裂发生在远离界面的本体相中或靠近界面的薄层中,则称为内聚断裂,此时可以认为涂层附着力好;如果断裂发生在界面区内,则称为界面断裂,此时说明附着力差。
涂料与金属之间的附着力就是分子之间或原子之间的相互作用力,主要有化学键力和分子间作用力2种。
涂层附着力可采用冲击试验(GB/T1720–1979《漆膜附着力测定法》)进行测试。
2.2 涂层防腐蚀机理涂料涂装的目的就是装饰与防腐,其机理如下:(1)防渗透机理,涂层是金属/腐蚀介质的阻挡层,防止腐蚀介质的渗透;(2)提高界面电阻,大部分金属/腐蚀介质构成的电化学腐蚀通过有机涂层提高界面电阻,减少电化学腐蚀的表面积;(3)改性涂料添加防锈剂,利用钝化与阴极保护原理达到防腐目的。
涂装前处理的硅烷处理与传统磷化的比较

涂装前处理的硅烷处理与传统磷化的比较作者:安奕娜来源:《科学与财富》2016年第16期摘要:空调用压缩机的涂装前处理一直采用传统磷化技术,利用磷化反应成膜,起到提高被处理工件的耐腐蚀性,此种加工工艺存在一定弊端。
随着表面处理工业技术的发展和进步,硅烷技术逐步替代了传统磷化。
本文主要从反应原理、工艺流程、工艺参数等维度对磷化和硅烷技术进行比较说明。
关键词:空调压缩机;磷化;硅烷一、磷化处理与硅烷处理简介1、磷化处理所谓磷化处理,就是金属表面与磷化液接触发生化学反应,在金属表面生成稳定的不溶性的无机化合物膜层的化学处理方法,所生成的膜被称为磷化膜。
磷化膜的作用:1.1在充分脱脂的基础上能提供清洁、均一、无油的表面。
1.2由于物理与化学作用,增强曲轴本身的耐磨性。
2、硅烷处理硅烷化处理是以有机硅烷为主要原料对金属或非金属材料进行表面处理的过程。
是利用氟锆酸与硅烷的水解反应,在金属表面形成一种由氧化锆(ZrO2)和氧化硅(SiO2)组成的三维网状化合物,该化合物在被处理的金属物表面起到耐腐蚀并增加附着力的作用。
二、磷化处理与硅烷处理比对1、工艺流程1.1磷化工艺流程磷化的加工工艺流程:脱脂→水洗→新水洗→表调→磷化→水洗→水洗→纯水洗,共8道工序。
1.2硅烷工艺流程硅烷的加工工艺流程:脱脂→水洗→新水洗→表调→硅烷→水洗→水洗→纯水洗,共7道工序。
2、工艺技术3、皮膜组成对比4、原子力2D图三、磷化处理与硅烷处理的优劣势分析磷化反应机理可大致分为酸蚀反应和磷化反应。
其中磷化反应可简单定义为:压缩机金属表面与磷化液中的磷酸盐反应,最终以磷酸锌的形式在被处理物表面结晶,形成保护膜的化学过程。
在整个反应过程中,由于溶解下来的金属离子被氧化,所以会产生大量沉淀。
沉淀的产生是伴随磷化反应过程同步生成的,因此,无法消除。
最终大量的沉淀沉积在槽体内,覆盖在加热管路表面,导致磷化槽温度升高缓慢,磷化液温度控制异常,大量蒸汽损失产生浪费。
硅烷于磷化氢反应方程式

硅烷于磷化氢反应方程式1 硅烷与磷化氢反应硅烷与磷化氢反应是一种化学反应,即硅烷与磷化氢之间形成复杂的化合物的反应,这种复杂的化合物称为硅氯磷酸盐(SiCl3PO3)。
当温度升高时,由于反应产物的极性,剩余的液体可使反应更加有效且易于控制。
2 基本反应式硅烷与磷化氢反应的反应式为:Si(CH3)4+ 2H3PO3 ->SiCl3PO3+ 4CH3OH。
硅烷由四个甲基(CH3)组成,当与磷化氢反应时,其键的稳定性更强,它们形成的化合物比硅烷分子本身更容易发生反应。
3 反应动力学硅烷与磷化氢反应的反应速率及动力学参数都决定了反应的效率。
这种反应的反应速率随着反应温度的升高而加快,但活化能增大后,反应速率减缓。
羧基硅烷比较脆,当加热时,所有基团受热破坏,分子重新组合,从而促进反应。
4 主要产物硅烷与磷化氢反应的主要产物是硅氯磷酸盐,其分子式为SiCl3PO3,有时也称为硅磷酸盐。
它是一种具有极性结构的固体,其表面具有不同的电荷,常用于混合液体中,以稳定液体。
有时也称为硅氯磷酸盐,它的主要用途是制备有机溶剂和火药,并可作为表面处理剂用于涂层实验中。
5 实际应用硅烷与磷化氢反应的实际应用极为广泛,尤其在制造农业肥料、制造火药和有机溶剂、用于表面处理、制备有机油等方面。
此外,它还可以用于制造农药、聚合物、模塑料塑料、应用印染材料等。
硅氯磷酸盐用作肥料时,可以帮助植物增加矿物质和氮含量,增加作用效果。
总之,硅烷与磷化氢反应的反应机理、反应动力学和产物有着复杂的化学性质,是一种具有重要意义的化学反应。
它广泛应用于农业、冶金、胶粘剂、涂料、表面处理和医药等领域,可满足不同领域的需求。
硅烷化处理
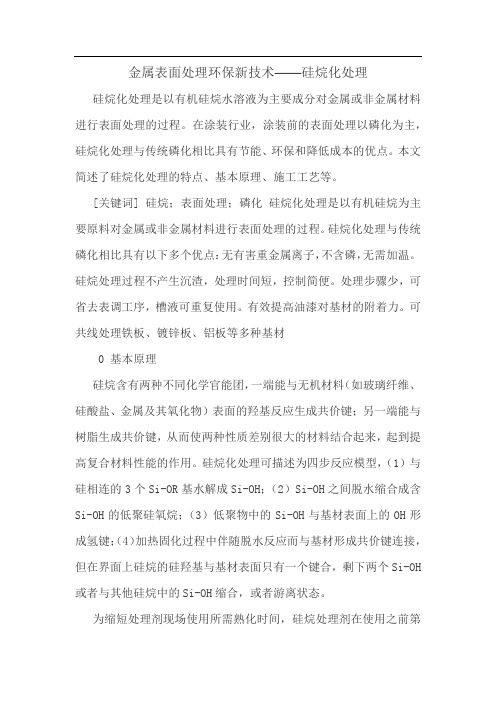
金属表面处理环保新技术——硅烷化处理硅烷化处理是以有机硅烷水溶液为主要成分对金属或非金属材料进行表面处理的过程。
在涂装行业,涂装前的表面处理以磷化为主,硅烷化处理与传统磷化相比具有节能、环保和降低成本的优点。
本文简述了硅烷化处理的特点、基本原理、施工工艺等。
[关键词] 硅烷;表面处理;磷化硅烷化处理是以有机硅烷为主要原料对金属或非金属材料进行表面处理的过程。
硅烷化处理与传统磷化相比具有以下多个优点:无有害重金属离子,不含磷,无需加温。
硅烷处理过程不产生沉渣,处理时间短,控制简便。
处理步骤少,可省去表调工序,槽液可重复使用。
有效提高油漆对基材的附着力。
可共线处理铁板、镀锌板、铝板等多种基材0 基本原理硅烷含有两种不同化学官能团,一端能与无机材料(如玻璃纤维、硅酸盐、金属及其氧化物)表面的羟基反应生成共价键;另一端能与树脂生成共价键,从而使两种性质差别很大的材料结合起来,起到提高复合材料性能的作用。
硅烷化处理可描述为四步反应模型,(1)与硅相连的3个Si-OR基水解成Si-OH;(2)Si-OH之间脱水缩合成含Si-OH的低聚硅氧烷;(3)低聚物中的Si-OH与基材表面上的OH形成氢键;(4)加热固化过程中伴随脱水反应而与基材形成共价键连接,但在界面上硅烷的硅羟基与基材表面只有一个键合,剩下两个Si-OH 或者与其他硅烷中的Si-OH缩合,或者游离状态。
为缩短处理剂现场使用所需熟化时间,硅烷处理剂在使用之前第一步是进行一定浓度的预水解。
①水解反应:在水解过程中,避免不了在硅烷间会发生缩合反应,生成低聚硅氧烷。
低聚硅氧烷过少,硅烷处理剂现场的熟化时间延长,影响生产效率;低聚硅氧烷过多,则使处理剂浑浊甚至沉淀,降低处理剂稳定性及影响处理质量。
②缩合反应:成膜反应是影响硅烷化质量的关键步骤,成膜反应进行的好坏直接影响涂膜耐蚀性及对漆膜的附着力。
因此,对于处理剂的PH值等参数控制显的尤为重要。
并且对于硅烷化前的工件表面状态提出了更高的要求:1、除油完全;2、进入硅烷槽的工件不能带有金属碎屑或其他杂质;3、硅烷化前处理最好采用去离子水。
硅烷化
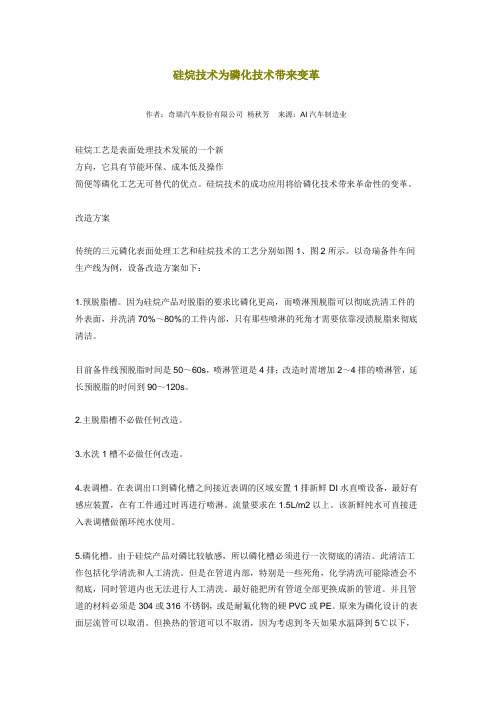
硅烷技术为磷化技术带来变革作者:奇瑞汽车股份有限公司 杨秋芳 来源:AI 汽车制造业硅烷工艺是表面处理技术发展的一个新方向,它具有节能环保、成本低及操作简便等磷化工艺无可替代的优点。
硅烷技术的成功应用将给磷化技术带来革命性的变革。
改造方案传统的三元磷化表面处理工艺和硅烷技术的工艺分别如图1、图2所示。
以奇瑞备件车间生产线为例,设备改造方案如下:1.预脱脂槽。
因为硅烷产品对脱脂的要求比磷化更高,而喷淋预脱脂可以彻底洗清工件的外表面,并洗清70%~80%的工件内部,只有那些喷淋的死角才需要依靠浸渍脱脂来彻底清洁。
目前备件线预脱脂时间是50~60s ,喷淋管道是4排;改造时需增加2~4排的喷淋管,延长预脱脂的时间到90~120s 。
2.主脱脂槽不必做任何改造。
3.水洗1槽不必做任何改造。
4.表调槽。
在表调出口到磷化槽之间接近表调的区域安置1排新鲜DI 水直喷设备,最好有感应装置,在有工件通过时再进行喷淋。
流量要求在1.5L/m2以上。
该新鲜纯水可直接进入表调槽做循环纯水使用。
5.磷化槽。
由于硅烷产品对磷比较敏感,所以磷化槽必须进行一次彻底的清洁。
此清洁工作包括化学清洗和人工清洗。
但是在管道内部,特别是一些死角,化学清洗可能除渣会不彻底,同时管道内也无法进行人工清洗。
最好能把所有管道全部更换成新的管道。
并且管道的材料必须是304或316不锈钢,或是耐氟化物的硬PVC 或PE 。
原来为磷化设计的表面层流管可以取消。
但换热的管道可以不取消,因为考虑到冬天如果水温降到5℃以下,还是需要把硅烷槽液加热到15℃左右,以保证处理的质量。
6.水洗2区不必做任何改造。
7.水洗3区不必做任何改造。
8.新鲜DI水喷淋不必做任何改造。
图1 传统的三元磷化表面处理工艺图2 采用硅烷技术的工艺成本对比1.化学品成本比较磷化(以磷化价格含税12元、促进剂价格含税5元计算,表调价格含税20元计算):每1?000m2价格约为12×10+5×3+20×1=155元;硅烷(以9810/1含税250元、9905含税40元计算):每1000m2价格约为250×0.5+40×1=165元。