子午线轮胎结构设计
半钢子午线轮胎设计规范

半钢子午线轮胎设计规范一、轮胎结构设计规范:1.轮胎应采用半钢子午线结构,具有内外两层体带和一层钢丝帘线,以提供合适的强度和稳定性。
2.内层体带应采用高强度的尼龙材料,以提高耐受性和减少变形可能性。
3.外层体带应采用高强度的尼龙材料,并且在胎面上覆盖一层硫化橡胶,以增加抗刮擦性能。
4.钢丝帘线应采用优质的钢丝材料,具有较高的拉伸强度和耐久性。
二、轮胎尺寸设计规范:1.轮胎的尺寸应符合国家和地区的标准规定。
2.轮胎的宽度和直径应根据车辆的重量和用途确定,以确保合适的载荷和舒适性。
3.轮胎的壁厚应符合国家和地区的安全标准。
三、轮胎花纹设计规范:1.轮胎的花纹应根据车辆的用途和路况特点进行设计,以提供良好的抓地力和操控性能。
2.花纹应具有良好的排水性能,以减少在雨天行驶时的滑行风险。
3.花纹中的花纹块应具有合理的密度和深度,以提供合适的稳定性和耐磨性。
4.轮胎的花纹应采用耐磨橡胶材料,以增加使用寿命。
四、轮胎硬度设计规范:1.轮胎的硬度应根据车辆的用途和路况特点进行设计,以提供合适的舒适性和操控性能。
2.硬度应通过实验和测试来确定,以确保在不同场景下的表现一致性。
五、轮胎使用寿命规范:1.轮胎的使用寿命应符合国家和地区的标准规定。
一般情况下,轮胎的使用寿命应不少于5年。
2.轮胎应在适当的空气压力下使用,以减少磨损和热量积累。
3.轮胎在使用过程中应定期检查,并及时更换磨损严重或损坏的轮胎。
六、轮胎质量控制规范:1.轮胎生产过程应遵循严格的质量控制标准,包括原材料的选择和检验,生产过程的监控和质量检测等。
2.轮胎出厂前应进行全面的质量检测和性能测试,确保轮胎的合格率和可靠性。
综上所述,以上是关于半钢子午线轮胎设计规范的详细说明。
这些规范旨在确保轮胎的质量和性能,提高车辆的安全性和驾驶体验。
制定和遵守这些规范对轮胎制造商和车辆使用者来说都是非常重要的。
子午线轮胎结构设计与制造技术

子午线轮胎结构设计与制造技术
子午线轮胎是一种高性能轮胎,由于其特殊的结构设计和制造技术而得到广泛应用。
其主要特点是采用平行于中心线的钢丝束作为骨架材料,能够提供优秀的耐磨性和抗拉强度,使轮胎能承受高强度、高速度和长时间运行的要求。
子午线轮胎的结构设计和制造技术包括以下几个方面:
1.骨架结构设计:子午线轮胎采用钢丝束作为骨架材料,一般包含两到三层。
骨架材料的种类、材质和层数均影响了轮胎的性能。
通过优化骨架结构设计,可以提高轮胎的抗拉强度和耐磨性。
2.胎面花纹设计:胎面花纹是轮胎与路面之间的唯一接触面。
子午线轮胎的花纹设计对于轮胎的性能有着重要的影响。
通过优化花纹设计,可以提高轮胎的防滑性和抓地力。
3.胎侧加强结构设计:轮胎的胎侧加强结构对于轮胎的耐磨性和抗撞击性具有重要意义。
子午线轮胎一般采用加强胎侧结构,以提高轮胎耐用性和安全性。
4.制造工艺技术:子午线轮胎的制造工艺技术包括轮胎胎体的成型、钢丝束的辊压、轮胎胎面花纹切割、轮胎成型和贴合等工序。
制造工艺技术的精度和质量直接影响轮胎的性能。
综上所述,子午线轮胎的结构设计和制造技术是决定轮胎性能和品质的重要因素。
如今,随着科技的不断发展和制造工艺的不断升级,子午线轮胎的性能和质量有了大幅提升。
子午线轮胎的结构特点及其生产工艺

子午线轮胎的结构特点及其生产工艺1.子午线结构:子午线轮胎的主体部分由多根尼龙帘布纤维组成,这些纤维以等距的直线形式穿插在胎面和胎侧之间形成子午线结构。
相对于传统的斜交帘布结构,子午线结构可以提供更好的稳定性和均匀的车辆支撑力。
2.高强度胎帘:子午线轮胎采用高强度的尼龙帘布纤维,这些纤维具有较高的拉伸强度和耐磨性,能够承受更大的胎压和车辆负荷。
3.胎侧加强片:子午线轮胎的胎侧部分会加入加强片,以增强胎侧的刚度和稳定性,提高轮胎的侧向稳定性和抗侧滑能力。
4.花纹设计优化:子午线轮胎的胎面花纹经过精心设计和优化,以提供更好的牵引力、制动性能和排水能力。
不同类型的子午线轮胎可以根据不同的用途和路况设计适合的花纹。
1.帘布纤维制备:首先需要制备高强度的尼龙帘布纤维。
通常采用的方法是将尼龙纤维浸泡在特定的化学溶剂中,经过纤维融合、纺丝和拉伸等工艺步骤制备出高强度的帘布纤维。
2.胎体制备:将制备好的帘布纤维通过机械设备进行编织或织造,形成胎体的骨架结构。
这个骨架会进一步与其他材料结合来提供轮胎的整体性能。
3.胎面胎侧制备:根据轮胎的设计要求,对胎面和胎侧进行加工处理。
通常会使用硫磺进行胶料的硫化反应,以提高胶料的强度和弹性。
4.胎面花纹制作:将轮胎花纹设计的模具放置在硫化胶料上,通过机械设备进行压实和固化,形成轮胎的胎面花纹。
5.组装和调试:将胎体、胎面和胎侧等部件进行组装,并进行胎压和动平衡等工艺调试。
最终形成成品轮胎。
总之,子午线轮胎通过使用子午线结构和高强度帘布纤维等先进材料,在结构和性能上有显著的改进。
其生产过程中涉及到帘布纤维制备、胎体制备、胎面胎侧制备、花纹制作和组装调试等多个步骤。
子午线轮胎的结构特点和生产工艺的不断创新,使其在汽车行业得到广泛应用,并为车辆提供了更好的操控性、舒适性和安全性能。
12R22.5_全钢载重子午线轮胎的设计

45中国橡胶应用技术APPLIED TECHNOLOGY46应用技术APPLIED TECHNOLOGY很小,一般仅增加1~5mm ,根据以往设计经验,本次设计外直径膨胀率(D ′/D )取1.001,D 为1077mm 。
全钢载重子午线轮胎的断面宽设计应考虑到不同胎体帘线的伸长性能、轮胎断面轮廓、带束层角度等因素的影响。
本次断面宽膨胀率(B ′/B )取1.016,B 为295mm 。
2.行驶面宽度(b )和弧度高(h )b 和h 是决定胎冠轮廓的主要参数,适当调整b 和h 可以优化轮胎接地面的形状和大小,均衡胎冠接地面各部位的压力,提高轮胎的牵引性能和耐磨性能。
b 值选取主要与扁平率和带束层刚性有关,同时对轮胎的耐磨性能、牵引性能、操纵稳定性和滚动阻力有影响。
具有多层钢丝帘线带束层的轮胎h 应取较小值,如果h 较大,将会减小接地面积,从而对胎面胶耐磨性及磨耗均匀性、轮胎抓着性有很大的不良影响。
为保证轮胎与路面之间有较大的接地面积,本次设计h 与断面高(H )之比取0.032,h 为8.1mm ,b /B 取0.81,b 为239mm 。
3.胎圈着合直径(d )和着合宽度(C )d 的取值应满足轮胎装卸方便和着合紧密的要求。
胎圈与轮辋装配过盈量过大时,轮胎装卸困难,且影响胎圈安全性能;过盈量过小时,轮胎不能与轮辋紧密配合,造成无内胎轮胎漏气。
根据轮胎和轮辋的使用情况,d 应比轮辋直径小1~2mm ,本设计d 取569.8mm 。
C 按照“预应力设计法”进行设计,即C 与标准轮辋宽度之差为12.7~50.8mm 。
预应力设计法尤其适用于子午线轮胎的C 值设计,特别是对于无内胎子午线轮胎,可使两胎圈边缘紧贴轮辋,充气时轮胎很快就能达到标准充气压力。
本设计C 值放大16.2mm ,取244.8mm 。
4.断面水平轴位置(H 1/H 2)断面水平轴位于轮胎断面最宽处,是轮胎法向变形最大部位,也是胎侧最薄处。
第六部分 带束层设计子午线轮胎设计
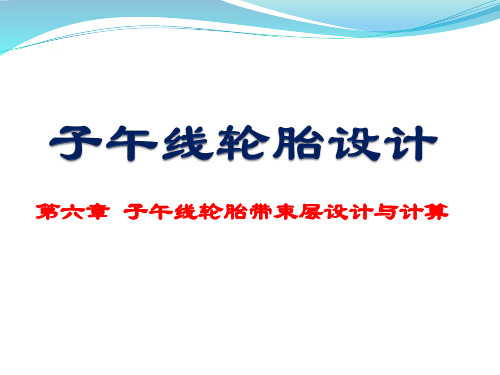
(2)三层结构 一般中型载重车的全钢丝子午线轮胎多数采用三层结构的带束层,第1层仍为过渡层,2层和3层帘线角度排列基本上与四层结构相仿,仅把第4层保护层取消。见图6-8 (b)所示。它有减轻轮胎重量和简化工艺的优点。
图6-12轮胎径向膨胀和扁平率的关系
普利司通公司为了解决这方面的课题,开发出可抑制带束层变形的新技术“波形带束层结构”,从而成功地使带束层的耐久性得到提高。抑制轮胎外径增大的最有效方法就是在带束层上置放冠带层。扁平轿车子午胎通常采用在交叉排列的钢丝带束层上缠绕0°纤维冠带层,以形成环箍效应。因帘线是有机纤维,当胎坯膨胀时帘线伸长,故不会影响硫化,但载重子午胎因纤维帘线强度不够,使用后会造成帘线断裂,所以必须采用钢丝帘线。
另外,试验表明,箍紧系数对轮胎的耐磨耗性能也有影响。据文献报道,以人造丝帘线做轿车子午胎的带束层,其箍紧系数由0. 04增至0.11时,胎面磨耗量由0.2mm/103 km下降至0.09mm/103 km。为保证子午线轮胎的使用性能,一般对轿车子午胎的K值较大(0. 11~0. 16),而载重车子午胎的K值较小(0.07~0. 08)。
图6-1带束层拉伸刚度与轮胎几何特性关系
图中(c)拉伸刚度与轮胎刚性的关系;7-Fs侧向刚度; 8-Fp周向刚度; 9-f轮胎径向弯曲。
当带束层拉伸刚度增加100×10-2N(100×10-3kg)时,滚动阻力和温度开始下降,然后在一段相当大的刚度值内保持恒定不变,直至刚度达400×10-2N(400×10-3kg)时,滚动阻力出现增大迹象,而温度成直线急剧上升,见图6-2所示
全钢子午线轮胎结构设计(2)

⑷着合直径d确实定: 依据轮胎装配的轮辋尺寸来确定着合直径 d 以12.00R20 S811 18P.R为例,d=511mm
≥24.5 ≤2°
R23
216(8.5") (36)
3.2
R≤8
≥27 ≤2°
14 R27
R≤8 2
5°
216(8.5") 32
46 Φ513.46
44.5 Φ508
8.50"X20"Ⅰ型平底轮辋
R2=〔1/4×(326-252-2×24.5)2 +(150.5-46)2〕/(326-2522×24.5)
=443.06mm.
取R2=353mm.
D
d
3.3
⑿下胎侧弧度半径
R3确实定:
依据R2和轮辋曲
线,结合其它方
法途径搜集的数
H
据,综合权衡确
B
定R3的数据。
R2
H1
以12.00R20 S811
与HF至少保证
10mm的差级;
胎体反包点到下
胎侧轮廓线的距
离DW,依据不
DN
同的规格和胎体 反包点的走式,
DW DL
一般6~12mm;
HS HF HB1 Ф HZ HB2
W
胎体反包点到胎体帘线的距离DN,依据不同的规格 和胎体的走式(下胎侧胎体帘线一般较直),一般 8~14mm;填充胶的高度HS,一般参考平衡轴的高 度H1和实际应用来确定,HS/H1=0.85~1;
2.5 16.5 22
34
42
DI DT
DJ DF
带束层宽度确实定,一般2#带束层宽B2/行驶面宽 b≥ 0.8,依据实际需要来确定,假设对带束层强度要
全钢子午线轮胎结构设计

全钢子午线轮胎结构设计
1.引言
全钢子午线轮胎是现代轮胎行业中的一种重要类型,其在汽车行业中
得到了广泛的应用。
全钢子午线轮胎一般由胎体、胎面、胎侧及胎底组成,其结构设计直接影响着轮胎的性能和使用寿命。
本文将对全钢子午线轮胎
的结构设计进行详细的介绍和分析。
2.全钢子午线轮胎的结构组成
2.1胎体
胎体是轮胎的主要组成部分,其主要作用是承载整个车辆的重量和提
供承载力。
胎体一般由多层高强度钢丝帘布叠加而成,这种结构可以提高
轮胎的稳定性和耐用性。
2.2胎面
胎面是轮胎与地面接触的部分,其主要作用是提供抓地力和减震功能。
胎面一般由橡胶混合物制成,其表面有复杂的花纹设计,以提供良好的抓
地力和抗滑性能。
2.3胎侧
胎侧是轮胎的两侧部分,其主要作用是保护胎体和提供支撑。
胎侧一
般由橡胶制成,其设计和厚度决定了轮胎的侧向刚性和防护性能。
2.4胎底
胎底是轮胎的底部部分,其主要作用是提供额外的支撑和保护。
胎底
一般由厚实的橡胶制成,其设计和结构决定了轮胎的耐磨性和抗损伤性能。
3.全钢子午线轮胎的结构设计原则
3.1强度和稳定性
3.2抓地力和耐磨性
3.3减震和舒适性
4.全钢子午线轮胎的结构设计方法
全钢子午线轮胎的结构设计通常通过计算和模拟分析来完成。
首先,通过对车辆的负荷和运行条件的分析,确定胎体的强度和层数。
然后,通过对胎面的各种花纹设计的评估和比较,选择适合的花纹形式。
最后,通过模拟分析和试验验证,确定最终的轮胎结构设计。
5.结论。
汽车子午线轮胎的结构

汽车子午线轮胎的结构汽车子午线轮胎是现代汽车上常见的一种轮胎类型,它采用了子午线结构,具有许多优点。
本文将介绍汽车子午线轮胎的结构及其特点。
一、胎体结构汽车子午线轮胎的胎体结构由多层帆布和钢丝帘构成。
其中,帆布层是由尼龙、聚酯纤维等材料制成,它可以增加轮胎的强度和耐磨性。
钢丝帘被编织成环状,以增强轮胎的刚性和稳定性。
这种结构使得轮胎能够承受车辆的重量,并具有良好的抗扭转能力。
二、胎面花纹汽车子午线轮胎的胎面花纹是由一系列凸起的线条和图案组成的。
这些花纹的设计不仅起到了美观的作用,还对轮胎的性能有着重要的影响。
胎面花纹的主要功能是提供良好的抓地力和排水性能。
凸起的线条可以增加轮胎与地面的摩擦力,提高车辆的操控性能。
同时,花纹中的槽道可以有效排除胎面下的水,减少轮胎打滑的风险。
三、侧壁结构汽车子午线轮胎的侧壁也是其重要的组成部分。
侧壁上通常印有轮胎的基本信息,如尺寸、载荷指数和速度级别等。
侧壁的材料通常是橡胶,它具有良好的弹性和耐磨性。
侧壁的设计可以提高轮胎的稳定性和舒适性,以及对路面的吸震能力。
同时,侧壁还起到保护轮胎内部结构的作用,避免因外界物体的碰撞而导致损坏。
四、气室结构汽车子午线轮胎内部有一个气室,用来装入充气的空气。
气室的结构通常由胎内衬胶和胎带组成。
胎内衬胶是一种特殊的橡胶材料,具有良好的密封性能,可以防止气体泄漏。
胎带则是一种纤维材料,用来增强气室的强度和稳定性。
气室的设计合理与否直接关系到轮胎的使用寿命和安全性,因此必须严格控制充气压力,避免过高或过低。
五、其他构造除了以上几个主要部分外,汽车子午线轮胎还包括许多其他构造。
例如,内衬胶可以起到防止气体渗透的作用;胎侧垫可以增加轮胎的刚性;胎底胶可以提高轮胎与轮毂的粘合力。
这些构造的设计和制造都需要严格遵循相关的标准和工艺要求,以确保轮胎的质量和性能。
总结起来,汽车子午线轮胎的结构包括胎体结构、胎面花纹、侧壁结构、气室结构和其他构造。
12.00R20_矿山专用全钢子午线轮胎的设计

12.00R20矿山专用全钢子午线轮胎的设计王 刚 孙成林 王金帅新途轮胎有限公司摘 要:介绍12.00R20矿山专用全钢子午线轮胎的设计。
结构设计:外直径1132mm,断面宽312mm,行驶面宽度255mm,行驶面弧度高h=8mm,Copyright©博看网. All Rights Reserved.44应用技术APPLIED TECHNOLOGY 速度50km/h 、充气压力900kPa 、单胎负荷4000kg ,胎面花纹为大块矿山型花纹。
二、结构设计1.外直径(D )和断面宽(B )根据车型、矿区环境和实际使用情况,并结合普通矿山产品出现的“大肚子”“站立性不好”等问题,以自然平衡轮廓设计理论作为数学模型、经典力学原理作为架构,通过有限元方法进行模拟分析,对肩部过渡和圈部弧线进行合理优化,最终确定外直径D 为1132mm 、断面宽B 为312mm ,该结果满足全钢子午线轮胎模具尺寸和轮胎产品标准要求。
2.行驶面宽度(b )和弧度高(h )轮胎与地面直接接触的平面称为行驶面,b 和h 是影响运动状态下轮胎稳定性和耐磨性能的关键设计参数。
该类型轮胎使用工况较为恶劣,接地稳定性和耐磨性能也至关重要。
在设计中,需要增大轮胎接地面积,并提升其抓着性能,同时也要考虑矿区路况下的通过性,综合考虑最终确定b 为255mm ,h 为8mm 。
3.胎圈着合直径(d )和着合宽度(C )根据轮辋的直径尺寸来确定着和直径d ,根据轮辋宽度Rm 来确定着合宽度C 。
此规格使用的标准轮辋为8.50。
为确保轮胎与轮辋配合紧密,获得良好的气密性能,并提高胎圈部位的刚性支撑,同时能够很好地装卸轮胎,轮胎与轮辋采用过盈配合,即d为511mm ;C 采用加宽14.1mm 设计,即C 为230mm 。
4.断面水平轴位置(H 1/H 2)为保证轮胎的综合性能,全钢子午线轮胎设计中,断面水平轴位置需与轮胎断面最宽点匹配,该部位是轮胎断面中最薄、变形最大的位置,对轮胎性能有重大影响。
全钢子午线轮胎结构设计

全钢子午线轮胎结构设计首先,材料选择是全钢子午线轮胎结构设计的关键。
全钢帘子采用尼龙帘子增强帆布,强度高、耐磨损,可以有效延长轮胎使用寿命。
胎体和胎冠采用优质橡胶,具有良好的弹性和抓地力,能够提供良好的操控性能。
胎肩和胎侧采用硬质橡胶,能够增加轮胎的刚性和稳定性。
其次,全钢子午线轮胎的结构设计分为胎体、胎冠、胎肩和胎侧四个部分。
胎体是轮胎的主体结构,它由多层钢帘子和橡胶胎面组成。
钢帘子采用交叉排列的方式,能够增加轮胎的强度和稳定性。
橡胶胎面采用帮助消耗冲击力的花纹设计,能够提供更好的舒适性和降低驾驶噪音。
胎冠是轮胎的中心部分,设计有不同的花纹,用于提供抓地力。
胎肩和胎侧负责提供额外的支撑和保护轮胎侧面,能够提高轮胎的稳定性和耐用性。
最后,全钢子午线轮胎的制造工艺主要包括胎体胶块的制作、钢丝帘子的制作和轮胎的成型。
首先,胎体胶块由橡胶和增强剂经过混炼、压片和硫化等工艺制作而成。
然后,钢丝帘子由钢丝经过拉伸、编织和卷绕等工艺制作而成。
最后,胎体胶块和钢丝帘子通过机械操作和胶粘剂粘合在一起,形成全钢帘子。
之后,胎体胶块和钢帘子经过成型机械的加工和硫化,形成最终的轮胎。
总的来说,全钢子午线轮胎的结构设计需要选用优质材料,并采用合理的结构设计和制造工艺,以确保轮胎具有耐磨损、强韧耐用、抓地力强和操控稳定等优良性能。
这些设计和工艺都需要经过长期的研究和实践,以不断提高轮胎的性能和质量,满足用户不同的需求。
全钢子午线轮胎的结构设计工作在轮胎生产企业中具有重要的意义,为提高轮胎的竞争力和市场份额提供了坚实的基础。
子午线轮胎的结构设计与制造工艺

子午线轮胎的结构设计与制造工艺学习目的与要求通过学习掌握子午线轮胎的技术设计及施工设计方法;熟练了解子午线轮胎的构造和结构特点;掌握子午线轮胎的成型工艺;了解半成品部件准备及硫化工艺。
第一节子午线轮胎的分类及组成一子午线轮胎的分类(一)按用途不同分类目前子午线轮胎按轮胎用途来分,多数为轿车子午线轮胎、轻载子午线轮胎、载重子午线轮胎等;另外许多力车胎、工程胎、农业胎、工业胎也部分进行了子午化。
(二)按所用骨架材料不同分类(1)全钢丝子午线轮胎:子午线轮胎的带束层和帘布层均为钢丝材料制作。
(2)半钢丝子午线轮胎:子午线轮胎的带束层由钢丝材料制作,帘布层为纤维材料制作。
(3)全纤维子午线轮胎:子午线轮胎的带束层和帘布层均为纤维材料制作。
一般载重胎多数为全钢丝子午线轮胎,而轿车胎和轻卡胎多为半钢丝子午线轮胎或全纤维子午线轮胎。
二子午线轮胎的组成目前子午线轮胎的种类很多,下面主要以轿车子午线轮胎、轻载子午线轮胎、载重子午线轮胎为例进行介绍子午线轮胎的组成。
(一)轿车子午线轮胎的组成轿车子午线轮胎由胎面、冠带层、带束层、胎体帘布层、气密层和胎圈等部分组成。
轿车子午线轮胎的断面图见图4-1。
1.胎面胎面由胎冠胶和胎侧胶组成。
胎冠胶为一个整体胶件,可不分基部胶和冠部胶。
胎侧胶主要用于保护胎体帘布层,一般子午胎的胎体层数少,所以胎侧胶厚度需要厚一些。
由于子午胎胎体柔软弯曲变形大,故要求胎侧胶的耐屈挠疲劳性能和耐光老化性能好。
2.冠带层冠带层附加在带束层上面,一般用1~2层尼龙帘布制成,帘线角度为90︒(即帘线与胎冠中心线平行),用于提高轿车子午线轮胎的高速性能。
图4-1 轿车子午线轮胎的断面图3.带束层是轿车子午线轮胎主要受力部件,一般由两层钢丝帘布组成,但也可选用多层模量高、变形小的纤维帘布,如芳纶纤维。
帘线角度约为65-72︒。
可根据轮胎的速度和扁平率来选择带束层的帘线角度。
4.胎体帘布层胎体一般由1~2层纤维帘布组成,帘线角度为0︒(即帘线与胎冠中心线垂直)排列。
汽车子午线轮胎的结构
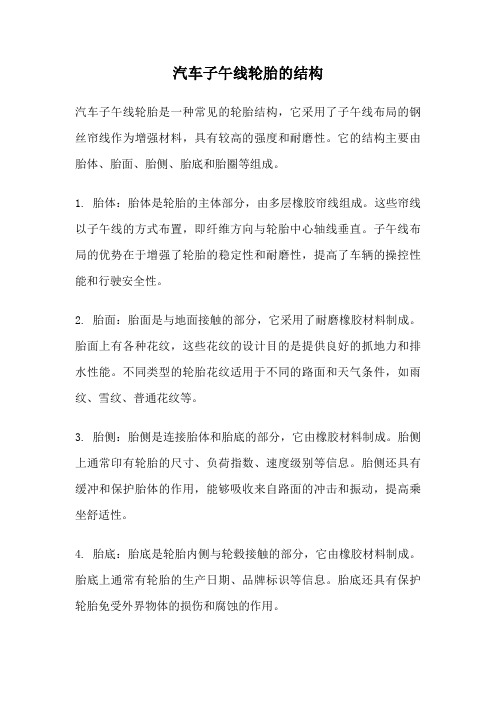
汽车子午线轮胎的结构汽车子午线轮胎是一种常见的轮胎结构,它采用了子午线布局的钢丝帘线作为增强材料,具有较高的强度和耐磨性。
它的结构主要由胎体、胎面、胎侧、胎底和胎圈等组成。
1. 胎体:胎体是轮胎的主体部分,由多层橡胶帘线组成。
这些帘线以子午线的方式布置,即纤维方向与轮胎中心轴线垂直。
子午线布局的优势在于增强了轮胎的稳定性和耐磨性,提高了车辆的操控性能和行驶安全性。
2. 胎面:胎面是与地面接触的部分,它采用了耐磨橡胶材料制成。
胎面上有各种花纹,这些花纹的设计目的是提供良好的抓地力和排水性能。
不同类型的轮胎花纹适用于不同的路面和天气条件,如雨纹、雪纹、普通花纹等。
3. 胎侧:胎侧是连接胎体和胎底的部分,它由橡胶材料制成。
胎侧上通常印有轮胎的尺寸、负荷指数、速度级别等信息。
胎侧还具有缓冲和保护胎体的作用,能够吸收来自路面的冲击和振动,提高乘坐舒适性。
4. 胎底:胎底是轮胎内侧与轮毂接触的部分,它由橡胶材料制成。
胎底上通常有轮胎的生产日期、品牌标识等信息。
胎底还具有保护轮胎免受外界物体的损伤和腐蚀的作用。
5. 胎圈:胎圈是连接轮胎和车辆轮毂的部分,它由金属材料制成。
胎圈的设计和制造质量直接关系到轮胎的安全性和稳定性。
胎圈上通常有轮胎的安装指示、最大载荷、最高允许速度等信息。
汽车子午线轮胎的结构设计合理、功能全面,能够满足各种路况和行驶条件下的需求。
子午线布局的钢丝帘线增强了轮胎的强度和耐磨性,提高了车辆的行驶稳定性和安全性。
胎面的花纹设计和胎侧的缓冲作用使得轮胎具有良好的抓地力和乘坐舒适性。
胎底的保护作用和胎圈的连接稳定性保证了轮胎的使用寿命和安全性能。
汽车子午线轮胎的结构设计经过了长期的发展和改进,它在提高车辆性能和行驶安全性方面发挥着重要的作用。
通过合理选择和使用轮胎,车主可以提高车辆的操控性能、燃油经济性和舒适性,同时降低行驶过程中的风险和事故的发生率。
因此,了解汽车子午线轮胎的结构特点对于驾驶者来说是非常重要的。
第四章子午线轮胎结构设计

第二阶段为施工设计:主要任务是: ① 确定外胎成型方法 ② 确定成型鼓直径及机头宽度 ③ 绘制材料分布图 ④ 制定施工标准表
最后提出结构设计文件(包括技术设计和施 工设计说明书)。 虽然子午胎的设计与斜交轮胎相同,但在各 个设计阶段,其设计参数的取值,特别是施工设 计与斜交轮胎差别很大,需用专门的成型机才能 完成。
二、技术要求的确定
1.子午线轮胎设计前的准备 (1)搜集技术资料作为设计依据
与斜交轮胎设计前一样,必须搜集有关的技 术资料。例如:车辆类型及技术资料 车速及路面 条件,轮轴情况,轮胎使用要求及经济性,安全 性等。
(2)确定技术性能
轮胎类型、规格、层级、帘布层数及胎面花 纹型式;最大负荷和相应内压;轮辋规格、尺寸 及轮廓曲线;充气外胎外缘尺寸等。
子午线轮胎与斜交轮胎帘线排列
第二节 子午线轮胎结构设计
• • • • • • 一、子午线轮胎结构设计程序 二、技术要求的确定 三、轮廓设计主要结构参数的选取 四、断面轮廓曲线的设计 五、子午线轮胎带束层的设计与计算 六、子午线轮胎胎体帘线的应力计算
子午线轮胎由于其结构上的特点,应与斜交 轮胎的设计方法有所不同。 设计原理:至今仍是普遍采用薄膜理论。由于 电于计算机软件技术的开发,使轮胎各部位受力均 匀的自然平衡轮廓设计方法,逐步演变为各部位应 力合理分布的非平衡轮廓设计方法,特别是有限元 分析法的引用,有可能真实地模拟轮胎在实际使用 状态下的断面轮廓形状,并分析其应力—应变的分 布合理匹配,从而得到优化方案以设讨轮胎的最佳 轮廓形状。
②胎体帘线强力得到了充分的利用,层数减少,一
般比斜交胎少40~50%,胎体层数可为偶数,也可
为奇数。 ③胎圈所受应力比斜交胎大30~40%,钢丝圈中的 钢丝根数比斜交胎多。 ④由于胎体层数少、胎侧柔软、容易变形和刺伤,
子午线轮胎的结构特点及其生产工艺

子午线轮胎的结构特点及其生产工艺一、结构特点:1.采用子午线结构:子午线轮胎采用纤维帘布及钢丝帘布交织而成,形成一个全新的胎体结构。
这种结构相比辐射线轮胎具有更高的强度和耐用性。
2.胎体材料选用优质橡胶:子午线轮胎的胎体使用高性能的橡胶材料,使其具有更好的耐磨性和耐候性。
同时,还可以提高轮胎的抓地力和操控性能。
3.均匀的接地面压力:子午线轮胎的胎体结构使得胎面能够均匀接触地面,从而能够提供更好的操控性和稳定性。
与此相比,辐射线轮胎容易产生翘边现象,导致接地面压力不均匀。
4.轻量化设计:子午线轮胎采用轻量化设计,可以降低整个车辆的重量。
这不仅能够提高燃油效率,还可以减少对悬挂系统的负荷,延长整个车辆的寿命。
5.提高操控稳定性:子午线轮胎具有更好的操控稳定性。
它的侧壁硬度较高,能够有效地提高转向的反应性能和操控精准性。
同时,胎体的强度也更好,能够有效地减少轮胎的变形和变形。
二、生产工艺:1.帘布制备:子午线轮胎的制造首先要准备帘布。
帘布包括纤维帘布和钢丝帘布。
纤维帘布使用高强度的化学纤维材料制成,而钢丝帘布则使用优质的钢丝制作。
这些帘布需要经过拉拔、涂胶等工艺处理,使其具备一定的强度和柔韧性。
2.胎体制造:将帘布和橡胶胶料进行复合,并通过压延工艺将其制成胎体。
在压延过程中,要保证帘布与橡胶充分贴合,胎体整体均匀且无气泡。
3.胎面制造:将橡胶胶料经过塑炼工艺制成带有花纹的胎面。
4.胎体与胎面的组装:将制备好的胎体与胎面进行组装,并使用机械或自动化设备进行粘合,确保它们牢固地连接在一起。
5.硫化处理:将组装好的轮胎放入硫化机中进行硫化处理。
硫化温度、时间和压力需要根据轮胎型号和要求进行调整。
6.完整性检测:对硫化后的轮胎进行外观和质量检测,确保轮胎没有质量问题。
7.成品包装:对合格的轮胎进行包装,以防止在运输和储存过程中受到损坏。
总结:子午线轮胎相比辐射线轮胎具有更好的性能和耐用性。
它的生产工艺包括帘布制备、胎体制造、胎面制造、胎体与胎面的组装、硫化处理、完整性检测和成品包装等步骤。
汽车子午线轮胎的结构

汽车子午线轮胎的结构汽车子午线轮胎是汽车上常见的轮胎类型之一,它的结构设计旨在提供优异的性能和安全性。
本文将详细介绍汽车子午线轮胎的结构,以及其各个部分的功能和作用。
一、胎体层汽车子午线轮胎的胎体层是由多层胶片和钢丝帘布组成的。
胶片主要由天然橡胶和合成橡胶混合制成,具有良好的弹性和抗疲劳性能。
钢丝帘布则被用来增强轮胎的结构强度,使其能承受车辆的重量和道路的冲击力。
二、胎面层胎面层是轮胎与地面直接接触的部分,它由耐磨橡胶制成,具有良好的抓地力和耐磨性能。
胎面上还有花纹,花纹的设计和排列方式可以影响轮胎的性能。
不同的花纹可以提供不同的抓地力、排水性能和减震效果,以适应不同的路况和驾驶需求。
三、胎侧层胎侧层连接了胎体层和胎面层,起到连接和保护的作用。
胎侧层一般由橡胶材料制成,具有一定的柔韧性和弹性,能够缓冲和吸收来自路面的冲击力。
四、胎内层胎内层是轮胎内部的一层薄膜,主要由气密性较好的橡胶材料制成。
它的作用是保持轮胎内部空气的稳定压力,以确保轮胎在行驶中保持正常的形状和性能。
五、钢丝束层钢丝束层是轮胎的骨架部分,由多根钢丝组成。
钢丝束层的作用是增强轮胎的结构强度和稳定性,使轮胎能够承受车辆的重量和道路的冲击力。
钢丝束层的设计和排列方式可以影响轮胎的强度和耐久性。
六、胎带胎带是轮胎的一种保护层,位于胎体层和胎面层之间。
它由多层轮胎带组成,一般由尼龙、聚酯纤维等材料制成。
胎带的作用是保护轮胎的胎体层,防止其受到外部物体的刺伤和破损。
总结:汽车子午线轮胎的结构设计旨在提供优异的性能和安全性。
它由胎体层、胎面层、胎侧层、胎内层、钢丝束层和胎带组成。
胎体层和胎面层通过胎侧层连接在一起,胎内层保持轮胎内部的稳定气压,钢丝束层增强轮胎的结构强度,胎带保护胎体层。
这些部分共同发挥着各自的功能和作用,使轮胎能够承受车辆的重量和道路的冲击力,并提供良好的抓地力、耐磨性和减震效果,以确保驾驶的安全和舒适性。
子午线轮胎结构设计

轮胎结构设计是指通过计算、选择、绘图等方法确定 轮胎整体及各部件的结构和尺寸并拟定出施工标准 及设计辅助工具的过程。轮胎结构设计直接影响轮 胎质量及使用性能。
装在非设计的轮辋上,一般规格是轮辋宽度每增 加或减小lcm时,充气断面宽度增加或减小0.4cm。 f.轮胎结构不同值不相同。
子午线结构的轮胎值低于斜交轮胎,H/ B>l的纤 维子午线轮胎,取值范围为1.03~1.04;H/B<1的纤 维子午线轮胎,值约为1.02。
轮胎负荷标准分为单胎负荷和双胎负荷两种。
一般具有双胎并装的载重汽车应计算双胎负荷, 双胎负荷能力较单胎负荷能力小。轿车轮胎只计算 单胎负荷。
理想轮辋:轮辋宽W与充气轮胎断面宽B1之比等于 62.5%的轮辋称之为理想轮辋。
海尔公式:负荷能力的计算公式为海尔公式,是一个 在轮辋与充气轮胎断面宽之比等于62.5%的标准条件 下(理想轮辋)得出的实验式, 若比值超出此范围, 必须换算为在标准理想轮辋的充气轮胎断面宽才能 使用此公式。
( 1 . 0 2 1 0 2 5 8 8 ) 0 . 5 8 5 2 5 . 0 4 7 1 . 3 9 ( 5 0 . 8 2 5 . 0 4 7 )
=20(KN)
W S2 0 1.1 42.8 2 (K)N(增加气压70KPa)
第三节、外胎外轮廓设计
1、外胎模型各部位尺寸代号及其它设计参数 代号
第一部分 轮胎结构设计程序
轮胎结构设计分技术设计和施工设计两个阶段进行。
第一阶段:技术设计。
- 1、下载文档前请自行甄别文档内容的完整性,平台不提供额外的编辑、内容补充、找答案等附加服务。
- 2、"仅部分预览"的文档,不可在线预览部分如存在完整性等问题,可反馈申请退款(可完整预览的文档不适用该条件!)。
- 3、如文档侵犯您的权益,请联系客服反馈,我们会尽快为您处理(人工客服工作时间:9:00-18:30)。
一般具有双胎并装的载重汽车应计算双胎负荷, 双胎负荷能力较单胎负荷能力小。轿车轮胎只计算 单胎负荷。
理想轮辋:轮辋宽W与充气轮胎断面宽B1之比等于 62.5%的轮辋称之为理想轮辋。
海尔公式:负荷能力的计算公式为海尔公式,是一个 在轮辋与充气轮胎断面宽之比等于62.5%的标准条件 下(理想轮辋)得出的实验式, 若比值超出此范围, 必须换算为在标准理想轮辋的充气轮胎断面宽才能 使用此公式。
1、外胎模型各部位尺寸代号及其它设计参数 代号
(1)外胎模型各部位尺寸代号采用英文字母表示外胎模 型各部尺寸(单位为毫米)代号,见图2-1所示。可按 所在部位分为四类: 断面形状尺寸:D、B、H; 胎冠部尺寸:b、h、Rn、Rn"; 胎侧部尺寸:H1、H2、R1、R2、R3、L; 胎圈部尺寸:c、d、R4、R5、g、α。
第二部分 施工设计 第一节、成型机头类型 第二节、成型机头直径的确定 第三节、成型机头肩部轮廓曲线设计 第四节、成型机头宽度计算 第五节、绘制外胎材料分布图 第六节、外胎施工标准表的制定 第七节、内胎、垫带的设计
轮胎结构设计是指通过计算、选择、绘图等方法确定 轮胎整体及各部件的结构和尺寸并拟定出施工标准 及设计辅助工具的过程。轮胎结构设计直接影响轮 胎质量及使用性能。
H/B<1时,轮胎断面呈扁平状,充气后断面外径增大, 断面膨胀率较小,此时胎面虽然处于伸张状态,但 胎体平直,支撑性好,高速度、利于安全操纵,适 合轿车轮胎的设计
轿车轮胎断面向扁平化发展,断面高宽比已成系 列化,H/B值分别为0.95、0.88、0.82等。低于0.82 的超低断面轮胎,大部分属子午结构,分别为78,70、 65和50系列(即H/B值为0.78,0.70,0.65,0.50)
不必乘0.231。 单胎负荷应为双胎负荷的1.14倍,气压应相应增加7OkPa。
轿车轮胎负荷计算基本公式为:
W 0.231K 0.425 9.8 103
(1.02 102P )0.585 Bd1.39(DR Bd ) Bd B0.70 0.637d
180 sin 1 W1
扁平轮胎最大断面高H=l.O2×设计断面高),cm
(3)负荷能力计算实例
以9.00-20载重轮胎负荷能力计算为例。
已知条件:D=l018.5mm,B1=259mm, W1=177.8mm, P=588kPa,DR= 508mm,KD (双胎)= 1.l, KS (单胎)= 1.l4
负荷计算公式为:
结构设计有两种方法 1、从轮胎外缘曲线开始,从外往内设计。
古典方法,历史悠久,经验丰富,但缺乏计算数据, 只凭经验数据进行
2、根据内缘平衡形状曲线,从内往外设计 有数学模型作为计算依据,是当代科学的方法
轮胎结构设计现在广泛采用的传统设计方法,是以静 态平衡轮廓理论为设计依据,用薄膜-网络理论为 原理指导轮胎设计,轮胎在模型内的轮廓用几何作 图法,从外缘轮廓向内进行设计。
在完成设计后,提出技术设计和施工设 计说明书。
轮 胎 结 构 设 计 程 序 图
设计任务 轮胎设计前的准备工作
确定技术要求 确定外胎外轮廓曲线
设计外胎胎面花纹 确定外胎内轮廓曲线
优选方案ቤተ መጻሕፍቲ ባይዱ
绘制外 胎总 图
确定成型机头型 式、直径、肩部 曲线、绘制材料 分布图
制定外胎施 工标准表
确定水胎(胶 囊)断面尺寸、 绘制断面轮廓 图
一般斜交轮胎H/B>1,值在0.9~1.17之间; H/B<l,在1.00~1.07之间。
b.W1/B值越大则值越小。 因轮胎胎体平直,膨胀变化不大。
c.胎冠角度越大则值越大。 因胎冠角度大,充气时限制胎冠外径伸张,相应
使断面宽增大。
d.帘线伸长率越大则值越大。
例如尼龙帘线初始模量小,延伸率大,断面变形 随之增大。 e.轮胎安装在不同宽度轮辋上,其值也不相同。
3. 外胎充气外缘尺寸
包括充气外直径D′和充气断面宽B′,按 国家标准(或部颁标准)所规定的尺寸执 行。暂无国家标准(或部颁标准)的轮胎, 可以按设计任务书所规定的充气轮胎外 缘尺寸或参考国外轮胎轮辋标准所规定 的尺寸进行设计。
4.负荷能力计算 (1)标准负荷和理论负荷
轮胎的负荷能力是衡量轮胎质量重要指标 之一,其最大负荷能力与速度、内压、充气 断面宽、轮辋直径和宽度有关。
(2)轮胎充气前后及使用过程中外缘尺寸的变 化。
(3)室内试验数据。 (4)实际使用中的性能及主要优缺点。 (5)使用部门的要求。
1.轮胎类型
包括轮胎规格、结构、层级、胎面花纹、胎体骨 架材料品种、规格和基本技术性能。
2.轮辋的选择
应根据轮胎类型和规格,按国家标准(或部颁标准) 及车辆技术状况和发展趋势选定。例如轿车采用深 槽式轮辋和深槽式宽轮辋,轻型载重汽车采用半深 槽式轮辋,中型和重型载重汽车一般采用平底式轮 辋和平底式宽轮辋(即5°斜底轮辋)。不同类型车辆 有其相对应的轮辋类型、规格及轮廓曲线。
2.道路情况
(1)路面性质,包括硬基路面(水泥、柏油和碎 石)、混合路面(石土或城乡间的水泥路)、 软基路面(雪、砂及土路),还有特殊的作 业环境,如矿山、林场、水田、沼泽等
(2)路面拱度、坡度和弯路。 (3)使用地区的年平均气温和降雨量。
3、国内外同规格或类似规格轮胎的结构 和使用情况
(1)技术参数,例如轮胎的层数、内压、负荷 及花纹形式等。
第 三 章
结 构 设 计
+ 通过学习掌握斜交轮胎的结构设计程序, 掌握技术设计内容:外胎外轮廓设计、胎 面花纹设计、内轮廓设计;
+ 掌握斜交轮胎的施工设计;了解内胎、垫 带、水胎和胶囊设计。
第一部分 轮胎结构设计程序 第一节、轮胎设计前的准备工作 第二节、轮胎技术要求的确定 第三节、外胎外轮廓设计 第四节、外胎胎面花纹设计 第五节、外胎内轮廓设计
B = 25.9?
25.9 141.3o
= 25.9 0.96 25.047(cm)
WD 0.231 1.1 0.425 9.8 103 (1.02 102 588)0.585 25.0471.39(50.8 25.047)
=20(KN)
WS 20 1.14 22.8(KN) (增加气压70KPa)
W 0.231K 0.425 9.8 103 (1.02 102 P )0.585 B 1.39(DR B )
180 sin 1 W1
B B1
B1 141.3
将已知数值代入上列公式中,首先求取S值,再求WD双胎负 荷,最后计算单胎负荷WS。
180o - sin- 1( 17.78 )
1.车辆的技术性能
(1)车辆类别、厂牌、型号、用途和外形尺寸。 (2)车辆自重、载重量、整车重量在各轴上的分布
和车轴所需承担的牵引负荷。 (3)车辆驱动形式、轴数、轴距、轮数和轮距。 (4)轮辋类型、代号及轮辋断面曲线。 (5)轮胎最大外缘尺寸及双轮间距离。 (6)车辆平均速度和最高速度。 (7)最小离地间隙、最小转弯半径和最大爬坡度。 (8)对轮胎的特殊要求。 (9)该车辆发展前景。
2、各部位尺寸确定
(1)断面外形尺寸
①断面宽B的确定 外胎模型断面宽根据充气断面宽和充气后断面宽
膨胀率的变化确定。轮胎处于充气条件下使用,其 充气断面宽必然大于 模型断面宽,断面宽增加程度 用膨胀率 表示
B/ B
计算公式:
B B B/ B
B-胎模型断面宽,mm
B′-轮胎充气断面宽,mm
B/ B -断面膨胀率
B1 141.3
式中:W-负荷能力,kN K-负荷系数 (K=1.1(双胎),K=1.14(单胎)) P-内压,kPa DR-设计轮辋直径,cm W1-轮辋名义宽度,cm
B- W1 为62.5%的理想轮辋上的轮胎充气断面宽,cm
B1
B1-安装在设计轮辆上的新胎充气断面宽,cm 0.231-采用公制计算的换算系数,若用英制计算,此公式
D D D/ D
一般H/B>l的人造丝斜交轮胎,D′/D<l,约为0.990~ 0,999;尼龙斜交轮胎则不同,其H/B值无论是大于或小于1, 充气外直径均增大,一般约增加0.1~2.5%。
斜交轮胎负荷计算基本公式及负荷系数K值的选 取与斜交载重轮胎和轿车轮胎负荷计算公式与负荷 系数K的选取不相同。
载重轮胎负荷计算基本公式为:
W = 0.231K创0.425 (1.02? 10- 2 P)0.585
? B1.39(DR B)创9.8 10- 3
180 sin 1 W1
B B1
轮胎结构设计分技术设计和施工设计两个阶段进行。
第一阶段:技术设计。
任务是收集为设计提供依据的技术资料; 确定轮胎的技术性能;设计外胎外轮廓曲线 和胎面花纹;设计内胎、垫带和水胎(或胶囊) 断面曲线;绘制外胎,内胎和垫带设计总图。
第二阶段:施工设计。
任务是根据技术设计确定成型机头型式、 直径及肩部轮廓;绘制外胎材料分布图;制 定外胎、内胎及水胎(或胶囊)施工标准表; 提出外胎,内胎及水胎制造附属工具的技术 要求。
确定内胎 断面尺寸、 绘制内胎 总图
制定水胎(胶囊) 制定内胎施
施工标准表
工标准表
确定垫带 断面尺寸、 绘制内胎 总图
制定垫带施 工标准表
提出外胎、内胎、垫带及水胎(胶 囊)制造附属工具的技术要求
提出结构设计文件
轮胎是车辆驱动机构的主要配件,设计时 应依据车辆的技术性能及车辆的使用条件, 适应车辆发展的需要,并应考虑轮胎结构的 合理性、经济性及发展前景,收集有关技术 资料,选用先进技术,全面分析进行设计。 一般包括车辆的技术性能、行驶道路情况、 国内外同规格或类似规格轮胎的结构与使用 情况等。