TPS基础、作业三票
TPS标准作业教程

③标准拥有量(工程内最少的仕挂品)
●关于T.T (一天)的劳动时间(定时)
T.T = (一天)的必要数量
(贩卖速度:一个或一台用几分几秒做好呢)
C.T (实质作业时间):作业者一人标准作业,在不勉强的情 况下最快的一次作业实绩(包括步行时间) 。但是无等待时 间的场合,T.T=C.T
596 3
41
2
分解号码
观测者 着眼点 (段取时间)
2.现场观察的心得
(1)通过时间观测
①依据算出的循环时间,把握一个循环时间的离中趋势及真正 的原因。
②把握几次中会发生一次附带作业(如操作空箱,品质检查 等)。
③时间观测结果如图《山积图的表示方法的窍门》
区分(a)循环时间(b)附带作业(c)离中趋势这三项进行合计。
④安全的维持 这是绝对条件。 (4)作业改善和设备改善 “时间是动作的影子。” ①作业改善的着眼点---详细观察作业 •看脚•看手•看物•看视线 •高水准的改善用录象来看(用肉眼看不到的地方可以用录象
看到秒以下的世界。) ②作业改善的进行方法 ●步行的缩短---部品的配置、设备的配置 ●作业程序组合的变更---除去空动作、废弃等待作业 ●作业动作的改善---使用两手、启动按纽的位置的变更
第四步 求出每一个循环时间
▲用红字记入在一个循环时间栏里。(右侧时间值减去左侧时间值,把答案 记入在一个循环时间栏里)
第五步 决定循环时间
▲观测十次左右,选择当中的最小值,记入在要素作业时间栏里的最下段。 (但不包括在连续作业可能的时间里的异常值。)
第六步 求出各要素作业的时间
▲用红字记入在下段里(把下段的时间值减去上段值,得出的结果记入在下 段中)
TPS的问题点

[原创]TPS基础知识问答(4)13、什么是“定数量”?定数量是指规定物品存放的数量,减少不必要的库存。
14、什么是“定容器”?定容器是指规定物品的存放容器,以便于将零部件种类分清,同时指定容器有利于保护零部件。
15、什么是“定位置”?定位置是指规定物品的摆放位置,以便于物品的取用,减少无效劳动时间,例如:寻找的时间。
16、什么是“定时间”?定时间是指规定物品的运送时间,是实施看板管理的基础。
17、结合工厂的实际说明做好“5定、5S”可以起到哪些作用?①保证生产安全:整洁、有序的工作环境可有效防止以外事故的发生,良好的习惯是防止事故,提高安全性的首要因素;②保证产品质量:工作环境的整洁、有序将会减少工作过程(例如制造及检验)中的误差,从而减少不合格的发生;③提高工作效率:良好的环境和氛围会有助于员工提高工作热情,精力集中,使工作效率提高。
良好的工作环境将要求有序而严谨的工作方式,物品摆放有序,有助于工作效率提高。
④起到预防的作用:养成良好习惯是防止事故发生的关键,及时的整理、整顿是事先消除隐患的有效措施。
18、结合我们的生产现场,简要说明5S与安全的联系?多余的物品和零部件库存逐渐削减后,生产现场变得清晰明朗,磕碰等吃一惊吓一跳的安全隐患更加容易发现和减少,更容易确保安全。
19自働化(人字旁的自动化)与安全的联系是什么?当安全事故即将发生时,设备的自动停止装置迅速启动,发挥作用,使机器自动停止,避免安全事故的发生。
20、KYT是指什么?危险预知训练。
21、海因里希法则的内容是什么?每一件重伤事故的背后,都隐藏着29件轻伤事故,进而隐藏着300件以上的吓出冷汗下一跳的险情。
22、海因里希法则对我们有什么启发?这条法则告诉我们,在发生重伤事故后惊慌失措,不如查找和排除造成事故的原因更为重要。
在尽早消除危险状态的同时,也要绝对做到不让工人进行危险的行为,通过采取永久措施让事故不再发生。
23、什么是安全?安全就是将不幸的伤痛从我们的工作和家庭中驱赶出去,就是“不接触、不做危险的事情、不进行危险的操作”。
TPS理论知识考试题库

第一部分TPS知识试题一、填空题1.标准作业指在指在节拍时间内,以有效的操作顺序,在同一条件下反复进行的操作。
2.合格工位要求1个作业循环中,作业部位不能超过3个,这样的目的是避免多余的步行。
3.生产中的七种浪费:制造过剩的浪费、库存的浪费、搬运的浪费、等待的浪费、加工的浪费、动作的浪费、不良品的浪费。
4.精益生产的两大支柱:自働化和准时化生产。
5.准时化生产的前提条件:平准化包含种类平准化、数量平准化两个面。
6.解决问题与改进流程必须追溯源头、亲自观察,然后验证所得数据。
7.评价合格工位的五项内容为:作业区域、作业干涉、部品的放置区域、作业部位、往返次数。
8.标准作业的前提条件应考虑①作业方面②人的方面③设备及生产线方面④品质方面。
9.决定标准手持时有哪些注意点:①作业顺序②有无设备自动加工③完成品不计入④有无自动取出装置⑤温度⑥检查作业。
10.没有问题是最大的问题!管理者需要跳出现场去观察现场。
11. 全员生产保全涵盖四大内容:预防保全;事后保全;改良保全;设备设计。
12.5S是通过整理、整顿、清扫来强化管理,通过清洁来巩固效果。
13.解决问题的八个步骤为:明确问题、分解问题、设定目标、把握真因、制定对策、贯彻实施对策、评价结果和过程、巩固成果。
14.改善的顺序作业改善、设备改善、工序改善。
15.现场监察的观察点: 1、瓶颈作业2、堆积 3、材料流动 4、等待5、步行6、身体的动作7、手的动作 8、眼睛的动作。
16.时间观测表要求至少连续观测 10 个循环。
17.实现“准时化生产”的方式看板方式、后工序取用方式、单个流动方式、平准化生产。
18.平准化生产的优点使工人操作更容易、更熟练,提高了对市场的反应速度,降低了库存,缩短了每台产品的制造周期。
19.QC小组活动的主要特点明显的自主性、广泛的群众性、高度的民主性、严密的科学性。
20.T.T=1日的生产时间/1日的必要生产量,不是根据设备能力和人员来定的。
标准作业三票

1、定义: 标准作业是以人的动作为中心制定的、安全、高效、无浪费地生产高质量产品的生产方式。
2、目的 (a) 明确生产方式的原则通过明确制造方法,保证任何人进行生产操作都能够保证同样的质量、数量、交货期、成本和安全。
如果 每个人都按照各自不同的随意方式进行生产,就无法保证质量、数量、生产、安全和交货期。
(b) · 改善的工具 无标准的现场(没有正常·异常区分的现场)就没有改善标准是进行改善的原点,即“没有标准的地方就无法进行改善。
”管理监督人员就无法尽责地发挥作用。
· 发现浪费、过载、不均的工具 首先确定标准,进行实施,不断进行完善非常重要3、标准作业的前提 ① 以人的活动为中心 ② 是重复作业(同样适用于重复作业不多的现场)4、标准作业的 3 要素 ① 节拍时间(决定人的动作) ② 作业顺序(不是工序的顺序,而是人的作业顺序) ③ 工序内标准在制品库存 ① 节拍时间 节拍时间 =(T.T)标准作业的 3 要素(1天)的劳动时间(定时) (460’×60”=27,600 秒) (1 天)的必要产量(售出的速度„„用几分几秒的时间生产 1 个或者1台的时间为最佳) 循环时间(C.T.)„„1 名工人在按照标准作业顺利操作的情况下,手工操作 1 个循环所需的实际最短 时间〈包括步行时间〉 。
它是(真正〈作业〉时间) ,但是不包含停工待料等待的时间。
・测量手工作业时,所测时间必须工人按照作业标准毫无困难地完成操作的时间。
②作业顺序 不是生产产品时先后的加工工序顺序,而是指工人能够最有效率地生产合格产品的作业顺序 ・必须是多能工 ③工序内标准在制品库存 依照作业顺序进行作业时,能够保证反复以相同的顺序・动作进行作业的工位内最小限度的在制品库存。
5.标准作业与改善 (1)标准作业是改善的工具 (a)安全 (b)品质 (c)容易实行 (d)完善的环境(2)标准作业改善步骤1① 明确改善的需求(目标设定) ② 仔细观察作业的现状。
TPS讲义

4、库存是万恶之源
库存 的浪费
库存的浪费
寻找浪费
他在做什么? 有浪费存在吗?
寻找浪费
寻找浪费
寻找浪费
你能识别是那些浪费吗?
四、TPS的两大支柱
• 准时化:在必要时间按必需的数量,生产必要的合格产品,
基本原则1 工序流程化(水流不能断开) 基本原则2 根据需求数制定生产节拍( 基本原则3 取货制____后道工序领取 (1、看板方式 2、搬运)
按步骤实施自主保全
人才培养 ⇒ 提高职场能力
自主保全活动内容
一、防止劣化 1、基本条件整备
(清扫、给油、锁紧)
二、发现劣化 1、测试劣化 2、日常点检
三、改善劣化 1、迅速处置异常 (救火)
(简单零件替换等应急 处置)
2、正确操作
用五感检查 发现潜在缺陷
2、援助突发性修理 3、记录异常 4、排除人为的强制 劣化 3、早期发现异常
此后,精益生产方式已被运用到一切 经营领域,引起全世界的瞩目,各国企业
纷纷学习和效仿。
4、从精益生产到精益思想
• 从精益生产到精益企业,从精益企业到精益思想
– 《机器)一书阐述了精益生产方式的形态,却没能说 明怎么能做成这样的企业——关键 – 为了说明怎么能做成精益企业, 美 国人又利用四年多的时间,通过对 众多推行精益生产的企业进行研究, 出版了《精益思想》一书。确立了 做成精益企业的原则和一些行动案 例。企图用此来指导工厂建立精益 企业。
6、对TPS的最新认识
• TPS之所以被称为丰田生产方式,是继泰勒制(Taylor System )和福 特制(Fordism)之后的第三个生产管理里程碑。他继承了泰勒制的优 点,创造了标准作业前提下,在福特式的流水生产线上,如何低成本地 进行小批量多品种的规模化生产。 • TPS是一种制造技术,它不是简单的工业工程(IE),更具有深刻的管理 内涵和理念的外延。也是员工能力的具体体现。与传统生产技术的区别, 在于它不仅仅是一种技术,同时也是一种管理,一种意识,一种思维方 法,一种文化。在追求持续改善这一管理本质的前提下,最大限度地发 挥每个员工智慧,提高思考力、执行力和创造力。
TPS的概念

TPS知识1.TPS的框架:一个基础:改善与持续改善;2个支柱:准时化和自働化;3个目标:降低成本、提高质量、提高交货期。
2.丰田生产方式的最终目的:通过彻底消除浪费、降低成本,产生效益。
3.准时化:也被称为是在必要的时间、只生产(搬运)必要数量的必要产品。
4.实现准时化方式:“推动式生产”转成“拉动式方式。
5.手段:看板。
6.看板定义:圆滑地管理各工序生产量的信息系统。
7.看板使用前提条件:1、生产的均衡化;2、作业转换时间的缩短;3、设备布局的筹划;4、作业的标准化;5、自働化;6、改善活动。
8.看板作用:1、生产・搬运的指示信息;2、目视化管理的工具:①抑制生产过剩;②检验工位的进展情况;3、作业改善的工具。
9.看板种类:生产指示看板;领取看板。
10.实现看板的五项规则:1、后工序必需在必须的时间,按所必须的数量,从前工序领取必须的物品;2、前工序仅按被领走数量生产被后工序领取的物品;3、不合格品绝不能送到后工序;4、必须把看板枚数减少到最小枚数;5、看板必须适应小幅度的需求变化。
11.均衡生产也被称为平准化生产,就是把产品的流量的波动仅可能控制在最小程度。
12.均衡生产的方式:包括“总量均衡”和“按品种和数量均衡”。
13.总量均衡:将连续两个时间段相互间的总生产量的波动控制到最小程度,简单的说,是指每个时间段(一般指一天)都生产相同的数量。
14.少人化:企业根据市场需求的变化而减少作业人数的做法。
15.节拍:一个零件(总成)、一辆车的生产或装配作业按需要应该在多长时间内完成。
16.按品种的数量均衡作用:产品生产与销售速度同步;品种、数量均衡可以按产品的平均节拍正常生产。
17.自働化:自动地监视和管理不正常情况的手段。
18.自働化意义:防止不合格品从前工序流入后工序,不使后工序造成混乱,并以次保证准时化。
19.目视管理定义:利用形象直观,色彩适宜的各种视觉感知信息来组织现场生产活动,达到提高劳动生产率的一种管理手段,是一种以公开化和视觉化为特征的管理方式。
TPS常用概念

1、TPS是指什么?}TPS是指丰田生产方式(是Toyota Production System 的简称),T代表丰田、P代表生产、S代表方式。
Ta 2、丰田生产方式的真正目的(宗旨)是什么?LS9,通过排除浪费降低成本。
%L3、丰田生产方式的两大支柱是什么?H3准时化(JIT)和自働化(带人字旁的自动化)。
<S86wP4、准时化(JIT)是指什么?zE A).准时化,简称JIT,即Just in Time,是指在必要的时候生产必要数量的必要产品。
*PM-l5、什么是准时生产的重要基础?PoG标准作业是准时生产的重要基础。
G6、自働化(Jidouka,带人字旁的自动化)是指什么?$它与我们通常说的“自动化”不一样,在丰田生产方式里面说的“自働化(带人字旁的自働化)”是指对设备赋予人的智能,当出现异常情况(例如生产出不合格品时)时设备能够自动停止,或者是当生产任务完成时设备能够自动停止。
0U;!oe7、丰田生产方式中所说的7种浪费是指哪7种浪费,其中危害最大的浪费是哪种浪费?+q等待的浪费、动作的浪费、搬运的浪费、返工的浪费、加工本身的浪费、库存的浪费、生产过剩的浪费,其中最大的浪费是生产过剩的浪费。
Xr8、七大浪费的含义分别是什么?@(1)生产过剩的浪费:生产的产品多于市场需要的或生产的速度快于市场需求的速度。
例如:市场需要3000台车,而实际生产出3500台车,或者市场平均一天卖出100台车,而我们却每天生产150台车。
:y3'^1(2)库存的浪费:任何超过客户或者后道作业需求的供应。
ZZV r(3)作业等待的浪费:人员以及设备等资源的空闲。
例如:生产线因缺件或设备损坏,导致生产线停线,人员在等待开线;或者由于上下工序作业时间不一样,下工序完成一个产品了而上工序还没完成造成下工序在等待。
;I2?<(4)搬运的浪费:对物料的任何移动。
>G(5)动作的浪费:对产品不产生价值的任何人员和设备的动作。
TPS教程(张秋萍)

由客户的需要和设备能力来决定
理想状态是100%
(由市场来决定)
(根据企业的努力来决定)
但是、普通的企业觉得是用大量生产来降低成本的・・・
根据企业想制造的速度 (稼働率100%)
> 作为客户的需求速度
导致制造过多的浪费!!(最大的浪费)
(2)稼动率和可动率
个/日
960
960 需要
生产
生产
責任
实绩
经营管理
TPS 基 础 教 程
什麼是TPS? トヨタ生産方式
TOYOTA Production System
• 所谓的TPS是以彻底排除浪费的思 想为基础,追求以最合理的制造方法 贯穿于整个生产过程的一种生产方 式的体系。
研修的内容
1. 丰田生产方式的目的
2. 丰田生产方式的基本想法
2.1 降低成本的观点
改善 平准化 标准作业
安定性←问题解决
3.1 TPS的2大支柱之一准時化
在必要的时候按必需的量生产和运送必需的产品
(1)准时化生产目的是缩短生产过程时间 所谓的生产过程时间是指工厂从接到订货到生产出产品发货 为止的时间。 (不仅仅是指产品的加工,而且也包括信息的加工)
生产过程时间=A+B+C
A:产品的生产指示信息的停滞时间 B:从产品的材料到货开始到完成成品为止的时间
停止时间
OR
销售管理
480
-80
-40
-
24
-144
480
制造管理
400
360
336
336
0
能力
稼动率 50%
可动率 100%
设备停止 不良 作业延迟
应该为零!
TPS作业改善知识培训

〔改善工具〕 ・标准作业表 ・标准作业组合表 ・有效运用山积表
・标准作业的3要素
① 节拍 ② 作业步骤 ③ 标准在制品库存
TPS作业改善知识培P训age 7
标准作业概要
TPS作业改善知识培训
标准作业的概念
标准作业是以较少的工数(工时),生产出高品质的产 品的一种工作手法。是将作业人员、作业顺序、工序设 备的布置、物流过程等问题作最适当的组合,以达到生 产目标而设立的作业方法。
操作人数的弹性化 (「少人化」)
标准作业的修订
小批量化
在同期化生产线基础上的 一个流生产
缩短换产时间
设备(工序) 多能工 布局 (一人多工序)
尊重人性/持续改善
标准作业
TPS作业改善知识培训
标准作业的概念定义
标准作业是以人的动作为中心、并排除在作业中的浪费,以没有浪费的操 作顺序有效地进行生产的作业方法
TPS作业改善知识培训
2020/11/1
TPS作业改善知识培训
为何要改善?
TPS作业改善知识培训
马蹄钉的故事
1485年,一位国王要面临一场重要的战争,这场战争关系到国家的生死存亡 。在战斗开始之前,国王让马夫去备好自己最喜爱的战马。马夫立即找到铁 匠,吩咐他快点给马掌蹄。铁匠钉了三个掌后,在钉第四个掌时发现还差一 个钉子,马掌当然不牢固。马夫将这个情况报告给国王,眼看战斗即将开始 ,国王也没太在意。战场上,国王骑着马领着他的士兵冲锋陷阵,左突右奔 ,英勇杀敌。突然间,一只马蹄脱落了,战马仰身跌翻在地,国王也被重重 地摔在了地上。没等他再次抓住缰绳,惊恐的畜牲就跳起来逃走了。一见到 国王倒下,士兵们自顾逃命,军队瞬时分崩离析。敌军俘虏 了国王。国王在 被俘那一刻痛苦地喊道:“钉,马蹄钉,我的国家就倾覆在这颗马蹄钉上。 ” 这位国王是真的,他就是英国国王理查三世;这场战役也是真的,就是波斯 沃斯战役。在这场战役中,理查三世失掉了整个英国。
TPS《标准作业》

作业顺序安排的示例参见教材第5页。
③.标准手持 标准手持的计算 入料口、成品货店上的库存不算标准手持。 标准手持包括生产线内设备上正在加工的零件数量和工序间 滑道规定保持的零件个数 标准手持的计算基本原则——顺流0,逆流1;手动0,自动1
一 档 齿 坯
10 标准手持
精车
9
插齿
8
~~~~ ~
剃齿
7
一 档 成 品
T.T=
循环时间(C.T) 作业者一个人进行标准作业时,毫不困难的、最快的、一个循环的 实际作业时间(包括步行时间),但不包括空手等待时间。 标准中间在库(标准手持) 按照标准作业规定的作业顺序进行操作时,为了能够反以相同的循 序、动作操作生产而在工序内持有的最少限度的待加工品。(入料 口和成品货店的在库不属于标准手持)
加工能力=
1班的运转时间(定时) 完成时间/件+交换刀具时间/件
表样及工序能力表的填写方法参见教材第13~第15页。
②.标准作业组合票
作用:考察标准作业中每个作业者承担的作业范围。 说明:制定的前提条件是现场测量出C.T和已经核算出T.T。 标准作业组合票的填写步骤 步骤 1 2 内容说明 在作业时间的时间轴上用红色笔画上T.T时间值的线。 估计一个人承担的作业范围 从工序能力表的手动合计栏中的时间值将步行时间也加进去,与T.T比 较,来估计作业者的作业范围。 按步骤2估计的作业范围,在作业组合票中的作业内容栏中将手工作业 的内容逐项填写上。 在时间栏里填写上手动作业时间、设备自动加工时间和步行时间,数 据从时间观测表传记而来。 决定作业内容,手动作业用实线、设备自动加工时间用点划线、步行 时间用波折线在时间轴上依次画出。
③付带作业 (换算成1个循环时间的)
标准作业-标准三票制作要领

标准作业-标准三票制作要领标准三票制作要领1目的通过科学的方法研究生产工艺顺序及作业内容,通过数据的统计研究,寻找浪费点进行改善,不断固化作业标准,规范标准节拍、作业顺序与标准手持,形成标准作业指导性文件,指导员工有序按标准进行生产,保证产品的生产品质。
2适用范围太仓中集标准作业推进班组3定义3.1标准作业三要素标准作业三要素:标准节拍、作业顺序、标准手持3.2标准三票工序能力表、标准作业组合票或山积票、标准作业票3.3工序能力表表示在各工序加工零件各工序的生产能力。
3.4标准作业组合票以生产节拍为基准,将手工作业与机械作业进行组合,确认人与机械的作业分担的比例和作业顺序的工具。
3.5山积票表示一个工序完整作业周期内各项作业单元的作业时间,并将作业时间累积起来作为整个工序的生产节拍。
3.6标准作业票以图表表示每个作业者的作业范围与作业顺序。
是管理监督者表达让作业者怎样操作的管理者意图的手段,是明确作业顺序,用眼睛看得见得管理工具。
4职责4.1 标准作业专员4.1.1负责对生产部门管理者、班长进行标准三票的制作培训与指导。
4.1.2协助编制完善标准三票,转换成标准三票正式版本。
4.1.3负责对标准三票的受控、发布、更新记录并归档 4.2 生产一线班组长4.2.1负责编制标准三票、验证、修改。
4.3 生产一线工段长4.3.1负责对标准三票的检查与校对。
4.5 生产部经理4.5.1负责对标准三票的检查与审批。
5程序 5.1流程图OKNG重新完善标准三票制作正式标准三票编制初期标准三票作业观察记录作业内容与作业时间验证制定标准三票编制计划5.2工序能力表编制要领5.2.1在工序能力表上填写好产品型号、工序名称、生产线名称、生产节拍TT等相关信息。
5.2.2依据工序工时测量记录表,将产品生产的各个工序名称填入工序能力表的工序名称栏内,并将各个工序的工时测量记录表内作业单元中的手作业时间与设备作业时间分别整理出来填入工序工时测量记录表内。
TPS基础知识

TPS基础知识一、定义1.丰田生产方式的精髓是:彻底消除无效劳动和各种浪费;2.制造过程中的七种浪费:生产过剩的浪费;制作不良的浪费;搬运的浪费;停工等待的浪费;加工过程本身的浪费;动作的浪费;库存的浪费;3.整理:将需要与不需要的物品加以区分,将不需要的部分加以处理;4.整顿:将需要的物品整齐放置在规定的地点;5.清扫:对自己周围和工作场所打扫干净;6.清洁:保持整理、整顿、清扫的良好状态,保持卫生;7.素养:掌握4S和工厂各种规章制度并加以遵守;8. 山积表:以T·T(节拍时间)为基准,测定各作业者之间作业量的差异,并作为高效率配置作业的判断基准的基础资料;9. 标准作业:是以人的动作为中心制定的、无浪费的、安全高效地生产高质量产品的方法(持续改进);三要素是:循环时间、标准作业顺序、标准持有量;10. 标准化:对于一项任务将目前认为最好的实施方法作为标准,让所有做这项工作的人执行这个标准并不断完善它,整个过程称之为“标准化”;11。
看板方式:是实现准时生产的工具,它是作为后工序从前工序领取零部件的“拉动方式”而闻名的方式;12. PDCA循环改善的基本程序:即建立计划-—实施-—检查——处理——PDCA循环作为改善工具;13。
实情说明书:是在改善活动中运用PDCA循环原理方法,分析问题、解决问题的改善工作的记录、总结,学习与交流的固化格式;14. 看板:是实现准时生产的工具,通常是一张装入长方形塑料袋里的卡片;二、简答题1.何为“TPS”?答:TPS是丰田生产方式,是指运用多种现代管理方法和手段,以社会需求为依据,以充分发挥人的作用为根本,有效配置和合理使用企业资源,最大限度地为企业谋求经济效益的一种新型生产方式.2.TPS的精髓是什么?答:目标:最大限度的获取利润;核心:彻底消除无效劳动和浪费;思维方式:逆向思维,后工序向前工序拉动,后工序视为前工序的用户,建立良好的上下工序协作关系;两大支柱:准时化和自働化;基础:5定5S、均衡生产、团队协作精神;质量保证:从研发到销售,拉动式过程自我保证;中心点:尊重人格、实施人性化管理,全员参与,落实过程,数量管理及质量控制管理,不断实施改善;3.丰田生产方式追求的目标是什么?答:是以无废品、零库存、低成本、多品种为不断追求的目标,工作上持续改善,追求尽善尽美,旨在以最优品质、最低成本、最高效率对市场需求作出最迅速的相应,最大限度地获取利润。
标准作业三票一表

(1)通过时间观测
①依据算出的循环时间,把握每个循环时间的不均衡及其真正原因。
②把握第几次中发生的附带作业(例:空箱处置,品质检查等)的内容。
(2)通过定点站立观测目的
(a) 为降低设备故障与急停,及作业时间的不均衡,站在能够很好观察生产线状况的位置,在现场
现物中把握真正问题,以便进一步改善。
(b) 为减少品质问题,在现场现物中捕捉真正的问题所在,加以改善.
4、标准作业的 3 要素
标准作业的 3 要素
① 节拍时间(决定人的动作) ② 作业顺序(不是工序的顺序,而是人的作业顺序)
③ 工序内标准在制品库存
① 节拍时间
节拍时间 =
(T.T)
(1天)的劳动时间(定时) (460’×60"=27,600 秒) (1 天)的必要产量
(售出的速度……用几分几秒的时间生产 1 个或者1台的时间为最佳)
①减少工时数
步骤 1 把握现状
・测定全部作业的作业时间
・停顿多的生产线
・停顿少的生产线
(加班等较多的生产线) (问题隐藏起来的,最糟糕的生产线)
T.T
T.T
步骤 2
A BC D 新标准作业
A BC D
T.T 进一步改善
省人
A BC D 改善的着眼点(当人成为瓶颈时)
※ 通过改变作业组合平衡作业
※ 缩短步行距离 ※ 缩短手工操作时间(包括不均衡) ※ 人的工作与机器设备的工作的分离
步骤 7 确定各要素作业时间。
* 要素作业时间之和,要对应循环时间。(不变更循环时间值。)
※ 算测量尚未测定的要素作业
※例外作业的内容及时间测定
(2)自动传送时间的观测
①测定从按下开关,各个目的作业完成,直到返回原位置的时间。(可以随时进入下一个作业的状态)
精益生产管理知识及考试试题

精益生产管理知识及考试试题一、填空题1.精益生产的五项原则是定义价值、价值流、流动、拉动、追求完美。
2.标准作业由节拍时间、标准作业顺序、标准在制品量三个要素构成,缺一不可。
3.整顿的“三定原则”指的是:定点定容定量4.定置的“三要素”指的是:场所方法标识5.精益生产的“三现原则”:现场现实现物6.TPS的两大支柱是什么?准时化、自动化7.TPS中所说的生产现场7种浪费是指哪7种浪费?生产过剩的浪费、库存的浪费、等待的浪费、搬运的浪费、加工的浪费、动作的浪费、不良品的浪费8.什么是SMART原则?明确性、可衡量性、可实现性、相关性、时限性9.4M变化点管理中4M指的是:人(man)、设备(machine)、材料(maternal)、方法(method)10.TPM发展的5个阶段:事后保全(BM)、改良保全(CM)、预防保全(PM)、保全预防(MP)和生产维护(PM)。
11.自主保全中防止设备劣化的三要素:清扫、加油、紧固。
12.10.改善四要法ECRS指什么?取消(Eliminate)、合并(Combine)、重排(Rearrange)、简化(Simplify)。
13.标准作业的四大名表是指什么?工程能力表、时间观测表、标准作业组合票、标准作业票。
14.“四数、五品”是指什么?四数:投入数、产出数、周转数、废品数;五品:成品、在制品、半成品、返修品、废品。
二、单选题1.平衡生产线就是令生产线上各工位的作业时间尽可能趋近于(D)A.各工位的平均作业时间B.各工位中最短的作业时间C.各工位中最长的作业时间D.节拍时间2.价值流分析的结果是形成三个文件,不包括(B)A.价值流现状图B.总结报告C.价值流未来图D.实施计划3..以下不属于精益生产看板分类的是(A)A.管理看板B.领取看板C.生产指示看板D.特殊看板4.以下不属于自主保全四大基本功的是(A)A.设备的整顿和掌握设备的整顿基准B.设备的润滑和掌握设备的润滑基准C.设备的紧固和掌握设备的紧固基准D.设备的点检和掌握设备的点检基准5.推行设备U型布置的要点包括设备布置的流水线化、站立式作业、人与设备分离和(A)A.培养多能工B.单能工C.生产节拍D.生产任务6.生产看板控制工序间的(D)A.物流、价值流B.信息流C.物流D.物流、信息流7.推行TPM(全面生产设备管理)的三要素不包括(D)A.提高工作技能B.改进精神面貌C.改善操作环境D.事后维修8.设备零故障管理以(C)为主?A.选用贵重设备B.定期大修C.预防性修理D.更换故障设备9.均衡化生产包括(B)A.产量均衡和计划均衡B.产量均衡和种类均衡C.人员均衡和产量均衡D.人员均衡和种类均衡10.在工厂的七大浪费中,号称是“万恶之源”的浪费是( C )A、动作浪费B、搬运浪费C、库存浪费D、等待浪费11.为每一个零部件或工具规划固定的放置地点,属于5S 中哪项(B)。
TPS基础

-
确保利润是重大目的之一
通过确保利润,保障企业的存续和员工的生活 确保利润
3
利润和成本
售价
利润 = 售价 ー 成本
售价 增加利润 ① 提高售价 利润 …由市场决定 ② 降低成本 …由制造方法决定
售价 = 成本 + 利润
成本
①
4
②
成本的构成
外围:由制造方法产生变化 内侧:单价相同
节拍= 节拍=
计划工作时间/ 计划工作时间/班 必要数/ 必要数/班
10
物品的制造方法和成本
物品的流程
手工作业 10″ 机器时间 10″ 1号机
2
20″ 10″ 2号机
2 3 1 3
15″ 5″ 3号机
2 1 3
15″ 5″ 4号机
2 1 3
若 有 30 秒
1
手工作业 10″ 机器时间 10″ 1号机
〈平准化生产〉
26
平准化生产的2个意思
1.如果后工程把物品堆积起来一起取走,会怎样呢?
加工工程 A品种 B品种
组装生产线(1条生产线) C C C 事例1 ABCABCABC…… 事例2 AAABBBCCC CCC……
C品种 事例1★加工工程(ABC),每个是3分钟节拍就可以了 C 事例2★加工工程(ABC)每个是1分钟节拍,另外, C 在加工工程和组装工程之间,组装工程持有领取 分量的库存
非 常 设 F 备 P
40
价格和品质的平衡
能卖出
好
例1 卖不出 品质
不好
例2
价格
便宜 贵
41
基本原则1
在工序中打造品质
〈一般的品质保证的方法〉
标准作业三票一表

·无标准的现场(没有正常·异常区分的现场)就没有改善
标准是进行改善的原点,即“没有标准的地方就无法进行改善。”管理监督人员就无法尽责地发挥作用。
·发现浪费、过载、不均的工具首先确定标准,进行实施,不断进行完善非常重要
3、标准作业的前提
①以人的活动为中心②是重复作业(同样适用于重复作业不多的现场)
(1)标准作业是改善的工具
(a)安全(b)品质(c)容易实行(d)完善的环境
(2)标准作业改善步骤
1明确改善的需求(目标设定)
2仔细观察作业的现状。
各工序的能力表标准作业组合票标准作业票
3为实现重复作业,整理作业并且进行训练
4发现问题、浪费,探求原因进一步推进改善
5 制定新的作业标准
6反复进行这个循环非常重要
标准作业三票一表
标准作业三票
1、定义:
标准作业是以人的动作为中心制定的、安全、高效、无浪费地生产高质量产品的生产方式。
2、目的
(a)明确生产方式的原则
通过明确制造方法,保证任何人进行生产操作都能够保证同样的质量、数量、交货期、成本和安全。如果每个人都按照各自不同的随意方式进行生产,就无法保证质量、数量、生产、安全和交货期。
注:有关要素作业分析的填写
a、不能填写准备工作,不能填写返回;
b、两秒以内的作业要素可以合并;
c、不定期及例外作业(如取十台车的标准件)放在最后算例外作业;
d、两个人同时用同一把气枪,有一人等待20秒以上的等待算一个作业要素;
e、在现场发现的问题及时记录;
f、步行大于5秒的要素作业单列;
g、检查在于5秒的要素作业列出。
・测量手工作业时,所测时间必须工人按照作业标准毫无困难地完成操作的时间。
精益生产(TPS)知识试题

20、TPS对利润的理解是什么? 利润=(售价-成本)*数量,根据以上公式可知,企业要增加利润可采用哪几 种途径:提高产品售价。增加产品数量,降低产品成本。 21、标准作业是指什么? 是指在节拍时间内,以有效的操作顺序,在同一条件下反复进行的操作。 22、合格工位要求1个作业循环中作业部位不能超过3个,这样的目的是避免多 余的动作。 23、准时化生产的前提是什么? 平准化,包含种类平准化、数量平准化两个方面。 24、解决问题与改进流程是什么? 必须追溯源头、亲自观察,然后验证所得数据。 25、评价合格工位的五项内容是什么? 作业区域、作业干涉、部品的放置区域、作业 部位、往返次数。
39、什么是合格工位? 均衡员工作业、消除作业干涉、减少作业等待及走动浪 费。 40、顾客的含义? 包括内部顾客和外部顾客,内部顾客强调:下道工序是上道工序的顾客。 41、TPS精神是什么? 纪律、决心 、改善 、创造力 、执行力。 42、丰田模式的两大支柱是什么? 持续改善和尊重员工。 43、改善的目标是什么? 工作轻松、质量更好 、速度加快、成本降低。 44、目视管理的目的是什么? 使异常问题显现化,把应该管理、控制的项目明确表示出来,提高管理效 率。
FORD TOYOTA 自动化 自働化 机械并非人为的操作,而是靠机械或电气来操控的技术! 将人的智慧赋于机器,自动工作!
5、丰田生产方式所说的七种浪费是指哪七种浪费,其中危害最大的浪费是哪 种浪费? 1)等待的浪费 2)动作的浪费 3)搬运的浪费 4)返工的浪费 5)加工 本身的浪费 6)库存的浪费 7)生产过剩的浪费,其中危害最大的浪费是生 产过剩的浪费。 6、通常所讲的“三现主义”中的“三现”是指什么? 三现是指现地、现物、现实(现状)。“三现主义”是指亲自到现场(现 地)、 亲自接触实物(现物) 、亲自了解现实情况。 7、TPS推进的核心理念是什么? 行为改变,习惯就会改变;习惯改变,态度就会改变;态度改变,观念就会改 变;观念改变,人格就会改变;人格改变,命运就会改变;命运改变,人生就 会改变。 8、5定是指什么? 定容器、定位置 、定标识 、定数量 、定时间。
TPS教材(标准三票)
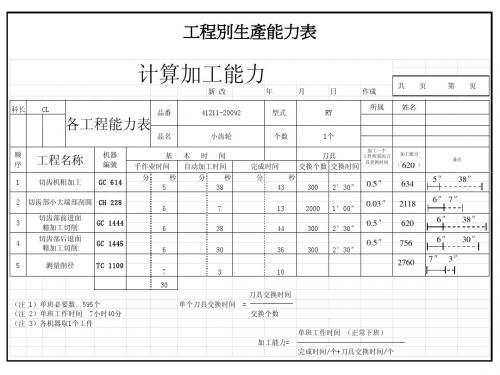
新 改年月日作成科长所属姓名交换个数交换时间分秒分秒分秒538433002′30″671320001′00″638443002′30″630363002′30″731030(注 1)单班必要数…595个单个刀具交换时间 =(注 2)单班工作时间…7小时40分(注 3)各机器取1个工件单班工作时间 (正常下班)完成时间/个+刀具交换时间/个机器編號交换个数刀具交换时间共 页 第 页计算加工能力切齿部后退面精加工切削型式 加工一个工件所需的刀具更换时间测量削径切齿部前进面精加工切削刀具手作业时间备注RY 41211-20092加工能力( )GC 614个数CLGC 1444GC 1445 加工能力=顺序123TC 1100工程名称45基 本 时 间CH 228切齿机粗加工切齿部小大端部刮圆自动加工时间完成时间品番品名1个小齿轮各工程能力表工程別生產能力表0.5″6206″38″27607″3″0.5″6345″38″0.5″7566″30″0.03″21186″7″620作 业 时 间 (单位刻度 1秒)12345合等待计作业顺序作 业 名时间手作业自动步行个手 作 业设备自动运 转步 行工 程所 属节拍时间秒品番·品名标 准 作 业 组 合 票制成年月日单班必要数51020152530354050455560657080758590標準作業組合票切齿机粗加工切齿部小大端部刮圆切齿部前进面精加工切削切齿部后退面精加工切削测量削径566673873830322222C.T T.T 630105954641211-20092小齿轮小齿轮加工表从作成 修订年 月 日年 月 日到共1页第1页标准作业票作业内容品质确认 注意安全 标准手持 标准手持数 节拍时间 循环时间 分解番号標準作業票切齿机粗加工测量削径546″40″1/1表123四工程45动作经济的原则:A 有关身体部位的使用原则:a.两手同时相反或对称方向移动.b.身体的运动部分尽量减少.c.相对较轻便的作业,通过手,前腕的运动比上腕,肩上的运动比较好.d.避免紧急的改变运动方向,需选择没有拘束﹑限制动作的自由运动.e.不自然的姿势,身体的重心上上下下等的动作需避开.f.适应动作的顺序,附带节奏感.g.尽量(尽可能)将注意力减少,可以不费事的进行动作。
- 1、下载文档前请自行甄别文档内容的完整性,平台不提供额外的编辑、内容补充、找答案等附加服务。
- 2、"仅部分预览"的文档,不可在线预览部分如存在完整性等问题,可反馈申请退款(可完整预览的文档不适用该条件!)。
- 3、如文档侵犯您的权益,请联系客服反馈,我们会尽快为您处理(人工客服工作时间:9:00-18:30)。
粗材を取る
完成品を置く
から まで
班名
班 観測技能員記号
全 ページ中 ページ
作業順 作業順 作業順
(2)作業標動準作業組作合せ票分(例) 析ができ、標準作業の見直しができる。 班名
班名
品番・品名 工 班程
17111-24060 インテークマニホルド 観測イン技テー能クマ員ニホ記ルト号゙ ブースター穴加工
为此,首先要赢利,使公司长期生存下去。
8
2. 不降低成本就无法提高利润
(1) 销售价 = 成本 + 利润
成本主义
(2)
利润 = 销售价 - 成本
降低成本
(1) 成本主义
(2) 降低成本
利润
销售价
成本
利润 销售价
成本
增加利润的方法
1.提高销售价格… 需求>供给 2.降低成本… 需求≦供给
销售价由顾客决定
21
Ⅲ.丰田生产方式的源流(Video)
22
Ⅳ. 丰田生产方式
如何将“顾客第一 ”具体化
2大支柱
J.I.T
适时地
适时地、低成本地 生产高品质产品
资金短缺时 如何快速回收
彻底消除
“不合理、浪费、不均衡 ”
低成本 高品质
自働化
23
『丰田生产体系』
丰田的
核心理念 经营哲学 丰田思想的原点
不仅是生产部门,其它部门也要展开
丰田生产方式与改善的步骤
TPS (TM)研修
GTMC
1
TPS教育 [TM研修] 的目标
(1)理解TPS (2)能够遵守标准作业 (3)能够了解改善的步骤
(1)作業組合せができ、必要人員と配置の提標準作案業票 ができる作改成訂 。62年11月30日
標準作業組合せ票 (例) 標準作業組合せ票 (例)
作業内容
31
3.关于准时化的前提—平准化
【前 提】
・平准化 ・根据销售情况生产
J.I.T
必要的时候 只生产和搬 运必要数量 的必要产品
缩短从 新车开发 ~生准的 周期时间
缩短量产 的总周期 时间
销售的 周期时间
车辆生产的 周期时间
部品生产 的周期时间
加工时间长
流程复杂
停滞时间 长
制造方法的不合理 物流的不合理
ー 25 21
3 2 32
21 11
3 2
21
32 11
52 ー
22 ー
2 2 2 2
T.T
⑥ 4
TP5-1101 ネジ径を測定する ワーク取り外し取付け、送りをかける
52 ー
2
3 11
2
6
完成品を置く
22 ー
(3)ムダ、ムラ、ムリを把握し改善ができる。 5
ネジ径を測定する
5ー
2
完成品
DR2424
③
タイム
分秒
手作業
75 ″自動8送0 ″り 歩行
MI1764
手作業 3〝 自動送り 25〝
品番・品名 工程
17イ1ン112テ1ー-ク2作4マ0ニ6ホ0ルワ粗Mトー業゙イIク取材-ン1りを7フ外゙テ6し名4取ースー取るタ付ークけ穴マ称、送加ニり工をホかルけるド
時 間2 ー 手 標送準3作歩5 ″業組102合″ せ15票″
1. 什么是Just in time?
必要的时候 只生产和搬运必要数量的
必要产品
1.1 禁忌找借口
“ 大前提
平准化”
26
1.2 衡量尺度的不同决定Just in time的水平
怎样才是Just in time?
(1)任何地方都在实行Just in time? (2)衡量Just in time的尺度不同?
向各级员工渗透,且要明白易懂
丰田纲领
1935年制定
丰田基本理念 1992年制定
TOYOTA WAY 2001年制定
24
丰田生产方式
如何将“顾客第一 ”具体化
2大支柱
J.I.T
适时地
适时地、低成本地 生产高品质产品
资金短缺时 如何快速回收
彻底消除 “不合理、浪费、不均衡”
低成本 高品质
自働化
25
1 Just in time
需配置更多的人员去运营
(不能达到平均值)
37
若实施平准化生产呢?
组装线 :1分钟生产节拍
ab c abc ab c
1.2分 1.2分 1.2分
1.0分 1.0分 1.0分 1.0分
0.8分 0.8分 0.8分
可按平均值(1.0分)工作
适当的人员配置可保证运营
平均
38
5.将丰田生产方式具体化的道具 =(かんばん)「看板」 的作用
(1)实现后工序领取、后补充生产的道具
①明确生产、搬运的优先顺序(优先顺序提示功能) ②防止制造过剩、搬运过剩(库存管理功能)
JIT
JIT
27
2.决定Just in time水平的周期时间
1)对企业而言的周期时间
投资
规划 设计 设备采购
生产计划 生产 物流 销售
同步管理
资金回收
丰田 生产方式
28
2)生产活动中的周期时间
生产计划 生产 物流 销售
资金回收 周期时间
29
3)生产现场中的周期时间
口入
加工L/T 生产的L/T
必要生产频度
前A
6000
150
3’
工B
6000
150
3’
序C
6000
150
3’
后工序
18000
450
1’
A
平准化生产
B
批量式生 产
C
后工序
批量式生产会导致什么样的结果? 34
(3)平准化的两层含义
1)如果后工序进行批量式生产会出现什么结果?
加工工序(前工序):3分钟生产节拍 组装工序(后工序):1分钟生产节拍
9
3. 降低成本 = 提高生产性
生产性 ≠ 劳动生产性
生产性
劳动生产性 设备生产性 材料生产性
(更少的人数) (更低成本的设备投资)
(更低成本的材料,更高合格率)
设计起决定性作用, 但生产方式的不同也会改变成本
10
4. 生产方式改变成本
成本的构成
即使用同样的设计、设备、材料,不 同的物流方式也会造成成本的变化
口出
生产的 周期时间
= 加工时间 +
停滞时间
30
冲压生产线的例子
口入
卷材
切割
300个 批量
5秒/张
搬运 300 个
冲压
300个 批量
5秒/张
口出
搬运 300 个
总装
1分/个 使用
生产的周期时间
加工时间 + 停滞时间
600 分 + 10 秒
=
10 秒
600 分
加工时间 : 停滞时间 = 1 : 3600
可动率 表示某机器能正常运转状态的百分比 →保持100%是理想状态
17
8. 整体效率高于局部效率
赛艇
18
轴承工厂的例子
超大型轴承
B Dd
内轮 1个 50万日元
内轮加工生产线
外轮加工生产线
19
9. 提高劳动生产性与强化劳动的区别
提高劳动生产性 将“動”转化为“働”
浪费 動 働
强化劳动
不改善而加强劳动强度
観1測7イ1ン技1テ1ー能-ク2作4マ員0ニ6ホ記0ルト号業゙インフデ名ースーターク穴マ称加ニ工ホルド
時間 手 標送準作歩5 ″業組10合″ せ15票″
20 ″
作成 年月日 25 ″ 30 ″ 所属
T.T62.11.30 35 上″ 郷 40 機″ 械部45 ″
直当り 必要数
920/ 直
個
50 ″タク全5ト5 ″ ペ6ー0 ″ジ中3065 ″ ペ7ー0 ″ジ
Aa
批量式生产
Bb
a a a bb b c c c
Cc
1分 1分
加工线(A、B、C) 的生产能力各为
1分钟
或者
加工工序与组装工序之间 设置可确保组装线 持续生产的库存
35
后工序若按平准化生产会怎样?
加工工序(前工序):3分钟生产节拍
Aa
c
Bb
组装工序(后工序):1分钟生产节拍 平准化生产
a3分b c a b c a b c
・货架、货物箱的增加 ・搬运车、叉车的增加
产生新的浪费
・新建仓库
15
6. 表面生产性与实际生产性的区别
表面生产性
10人 100个/日 10人 120个/日
必要量: 100个/日
实际生产性
10人 120个/日 20个是过剩产品
8人 100个/日=改善
16
7. 稼动率与可动率的区别
稼动率 需求数量与班内时间的生产能力之比 →可能大于或小于100%
Ⅱ.支撑丰田生产方式的经营观点・理念
Ⅲ.丰田生产方式的源流
Ⅳ.丰田生产方式
1. Just in time
2. 自働化
Ⅴ.标准作业 Ⅵ.改善的步骤 Ⅶ.丰田生产方式的精神支柱=尊重人性 Ⅷ.丰田生产方式的总结
3
Ⅰ.汽车是如何制造出来的
4
汽车生产・销售的流程
生产计划(VLT)
订单
GTMC生产管理部 GTMC销售部
間2 送 3歩
ー
ワーク取り外し取付け、送りをかける
25
ワワ粗MDーー34IRクク取 取材--12り りを74外 外62し し44取取 取ワワDTるーー付 付46RPクク5取 取け け--21り り、、送 送41外 外20り りし し41を を取 取ワか かTネー付 付Pクけ け完取け け-ジる る1り、、成送 送1径外0り り品し1をを を取をか か測付け け置け定る る、く送すりるを332かける