2012油液监测分析案例分析-挤压造力机故障案例
浅析挤压造粒机堵料的原因及处理措施

浅析挤压造粒机堵料的原因及处理措施摘要:本文通过对乙烯3#聚丙烯装置PK401挤压造粒机组在开车时出现常见堵料现象进行原因分析,发现少见的双螺杆芯轴断裂,并对主减速器的可靠性技术评估,快捷有效检修,迅速恢复生产。
关键词:挤压造粒机;堵料;主减速器;螺杆芯轴断轴前言:3#聚丙烯挤压造粒机组PK401于2014年11月投用,机组运行状态良好。
2019年12月14日7:30机组突然异响,离合器打滑干磨出现冒烟,紧急手动停车,检查发现摩擦离合器打滑严重干磨,主减速器输出轴油封座出现严重漏油,主减速器输出轴与R螺杆联轴器锁帽松动;因生产需要,更换离合器和旋转接头,更换主减速器输出轴油封,主减速器输出轴与螺杆的联轴器紧固,仪表探头复位,在15日试车,但不成功,现象是挤压机在盘车电机工作时正常在排料阀下料,主电机工作时不下料,在下料斗处有堵料现象。
我们通过分析和拆检找出机组故障原因,科学检修,消除了机组故障。
1.挤压机组的工艺流程及结构挤压造粒机组PK401为某公司化工分部3#聚丙烯装置关键特护机组之一,由大连橡胶塑料机械股份有限公司设计制造,机组型号:SJSHL-Z320×24B,功率9050KW,同向双螺杆混炼挤压造粒机。
工艺流程是计量喂料系统将被加工的聚合物和添加剂预混后连续地加入到双螺杆混炼挤出机第一段机筒(喂料机筒)上方的料斗中。
将氮气以与物料流动相反的方向充入到料斗、管道及计量系统中,以防止聚合物在大气中氧化。
物料进入双螺杆混炼机中在输送段(第1、2节机筒)被挤压和输送;物料在塑化段(第3、4 、5节机筒)被剪切、混炼而熔融塑化;在均化段(第6、7、8、9节机筒)物料及各种添加剂被进一步混合、分散、塑化后被输送到挤出造粒系统[1]。
挤压机的螺杆结构如图1所示,其功能:①芯轴尾部花键用于与主减速箱的联接,前部花键用于安装螺杆元件,花键长度比螺杆元件总长度短约 20 ㎜,用于螺杆元件、螺杆芯轴锁紧后的变形补偿。
挤压造粒机异常振动分析_解决

·71· 套和筒体前端磨损严重 ,证实了我们的判断。下面对解体的 过程及记录进行一下阐述 ,为以后作业及分析提供依据。
313螺杆挤压段磨损情况 新旧螺旋套磨损对比 :最大磨损量 66 mm;最小磨损量
10 mm;平均磨损量 38 mm。
Y 313. 55 310. 79 307. 01 307. 24 305. 13 301. 84 297. 44 295. 65 295. 64 294. 34 293. 94 290. 34 289. 48 287. 94 287. 31 285. 64 285. 64 281. 04 276. 14 276. 94 269. 87 268. 66 267. 20
R轴 1 2 3 4 5 6 7 8 9 10 11 12 13 14 15 16 17 18 19 20 21 22 23
X 315. 12 312. 54 308. 87 307. 64 305. 84 301. 56 297. 44 296. 76 296. 14 295. 74 294. 64 291. 24 289. 14 286. 24 287. 04 286. 04 286. 14 275. 96 273. 04 275. 84 274. 26 265. 26 268. 54
Key words: abnormal sound; screw; analysis; data; transformation
1 基本情况
2009年 1月 4日大庆炼化公司 30万吨 /年聚丙烯厂挤压 造粒机组 (型号为 CMP335 ×Ⅱ- 24. 5AW - V)运转声音异常 , 伴随低频振动声 ,为了防止设备故障恶化 ,决定停机检查。此 机组为日产大型进口设备 ,为保证检修一次成功 ,制定了详尽 的检修方案 ,解体至螺杆挤压段发现磨损严重 ,由于当时无备 件 ,等件期间低负荷运行 ,防止设备损坏加剧。
挤压造粒机常见故障分析及处理

挤压造粒机常见故障分析及处理挤压造粒机组集机、电、仪高度一体化,自动化控制水平高。
因此,在实际运行中将出现较多难以诊断的故障,导致处理时间过长,从而影响整套聚丙烯装置的正常运行,大大地降低了生产经济效益。
笔者结合挤压造粒生产过程的理论知识以及十余年实际生产运行的管理经验,对该机组在运行中出现故障的常见原因进行分析判断,制定了相应的解决措施及处理方法,从而确保其长周期的稳定运行。
故障原因在挤压造粒机组中,导致挤压造粒机组在运行中出现摩擦离合器脱开,机组联锁停车的原因可分为四大类:主电机系统故障1、主电机扭矩过高或过低;2、主电机转速过低;3、主电机轴承温度过高;4、主电机绕组温度过高;5、主电机水冷的冷却器出入口温度过高;6、主电机轴承润滑油泵出口流量过低;7、主电机轴承润滑油泵出口压力过低;8、主电机水冷的冷却器水泄漏量过高等。
传动系统故障1、齿轮箱变速杆位置偏离;2、摩擦离合器的仪表风压力过高;3、摩擦离合器速度差过大;4、齿轮箱润滑油泵出口压力过低;5、齿轮箱润滑油泵出口油温过高;6、摩擦离合器内部故障等。
挤压造粒机螺杆工艺段故障1、节流阀前后熔体压力过高;2、机头熔体压力过高;3、换网器前后熔体压差过大;4、开车阀转动故障等。
水下切粒系统故障1、切粒电机绕组温度过高;2、切粒机转速过低;3、切粒机扭矩过高;4、颗粒水旁通自动切换故障;5、颗粒水压力过高或过低;6、颗粒水流量过低;7、切粒机夹紧螺栓未把紧;8、切粒室旁路水阀未关;9、切粒机液压夹紧压力过低;10、切粒电机故障;11、液压切刀轴向进给压力过低等。
在上述故障原因中,出现频次较多的有:主电机系统的主电机扭矩过高或过低;传动系统的摩擦离合器故障;挤压造粒机螺杆工艺段系统的熔体压力高;水下切粒机系统故障等。
下文将对这些常见的故障原因进行详细的分析,给出相应的解决方法。
wodeai常见故障原因分析及解决措施主电机扭矩过高原因分析:油润滑系统故障,主电机输出轴与齿轮箱出入轴对中不良,电机及离合器振动等原因都将损坏主电机轴承,导致扭矩过高。
挤压造粒机异常振动分析、解决

挤压造粒机异常振动分析、解决挤压造粒机是一种常用的颗粒制造设备。
如项目出现了挤压造粒机异常振动,可能会严重影响生产效率和产品质量,甚至会导致设备的损坏。
因此,深入分析挤压造粒机异常振动的原因,找到解决办法是非常关键的。
一、异常振动的原因(一)构造问题挤压造粒机结构简单,由进料机构、挤压部分、取料机构、电控部分组成。
如果其中任何一个部件出现问题,都可能会导致振动异常。
有些厂商为了追求低成本,使用了低质量材料生产造粒机,导致机器寿命短,使用寿命结束后容易出现问题。
(二)设计问题挤压造粒机的设计和选择也是导致异常振动的主要原因之一。
挤压造粒机的设计应尽可能地精细化,且必须考虑工作原理和流程,满足实际生产需求。
如果设计不合理,机器各部件间间隙过大或过小,都有可能导致振动过大。
(三)零部件松动挤压造粒机在使用的过程中,由于长时间的振动,零部件之间可能会松动,导致异常振动。
例如,螺旋轴连通轴套筒松动,螺旋轴和壁板之间的间隙变大等。
这也是造成挤压造粒机异常振动的常见原因之一。
二、解决办法(一)加强检查定期检查各部分的零部件,确保它们没有松动。
因为挤压造粒机使用的时间长,因此有时出现零部件松动的情况也是很正常的。
只有经常进行检查,将有问题的部分及时处理或更换,让机器处于良好状态,才能保证设备的正常运行。
(二)优化结构挤压造粒机的结构设计应充分考虑到使用的环境和待处理物料的特点,使结构设备充分利用材料的特性,保证设备在高效率和低噪音的基础上实现优化比例。
此外,在振动的设计处理上,需要通过减震、减振等措施,降低振动水平,进一步缩小振动范围。
(三)改善配件针对经常出现故障的零部件,应该适时对其进行更换或者改善,以便提高零部件的耐用性,减小故障发生的频度。
(四)维修意识挤压造粒机在工作之前需要经过维修检查,这样才能保证设备在使用中更加安全。
因此,管理人员需要加强对工人的培训,提高维修检查的意识,定期对挤压造粒机进行维修保养,减共振损伤,提高生产效率。
聚丙烯装置挤压造粒机运行故障分析及处理措施

聚丙烯装置挤压造粒机运行故障分析及处理措施摘要:聚丙烯装置粉末产品转化过程的关键过程是挤压造粒机的运行。
挤压造粒机是聚丙烯装置能否正常转换的关键发电机组机械设备。
随着工业生产技术的不断发展,相关负责人不断提高挤压造粒机的自动化水平。
此外,它还具有高度的自动化程度。
因此,挤压造粒机的安全运行需要相关负责人的重视。
本文详细介绍了聚丙烯装置挤压造粒机使用中存在的故障和处理方法,希望进一步提高聚丙烯装置的转换效率。
关键词:聚丙烯装置;挤压造粒机;问题解决;中国石化沧州炼化公司聚丙烯装置,现有1万吨/年造粒系统一套。
在聚丙烯造粒设备中,挤压造粒机占据核心地位,其正常使用将与聚丙烯装置的安全、稳定、高效和良好工作有关。
此外,它还非常有利于设备的绿色制造,可以在一定程度上提高聚丙烯的经济效益,有利于制造业的现代化发展。
一、挤压造粒机简介(一)挤压造粒机最基本的介绍和原理挤压造粒机的应用本质是一个干造粒过程,主要通过工作压力促进固体材料团聚,其驱动设备通常是两个反向旋转工作辊挤压成型、液压传动系统或工作辊停止环,挤压造粒机将首先让原材料气体进行挤压成型,去除间隙。
(二)挤压造粒机应注意的事项挤压造粒机在出发前和驾驶过程中停车时,相关负责人应高度重视,做好驾驶前的准备工作,在运行过程中注意速度。
二、简要介绍聚丙烯装置挤压造粒机的运行故障(一)挤压造粒机相关异常问题相关负责人发出驾驶命令后,在塑料造粒机运行的过程中,刀轴没有向前移动到抛光部分,这将促进模板与切割刀之间的大间隙,这将导致涂层切割问题,影响挤压造粒机的正常使用,一般管道下,塑料造粒机动刀部分异常有两个原因,一方面是机械设备相关问题,另一方面,液压泵系统软件存在问题。
液压泵系统软件过旧或故障会导致下刀部位异常。
在解决这种情况的过程中,相关负责人要拆卸液压油泵中的齿轮油。
(二)挤压造粒机动刀后模板涂膜问题挤压造粒机动刀后模板涂层的常见故障具体表现为过度抛光效果。
聚丙烯装置挤压机组造粒不规则成因分析及对策

聚丙烯装置挤压机组造粒不规则成因分析及对策摘要:针对聚丙烯(PP) 装置挤压机组生产过程中多次出现不规则颗粒的问题,对影响 PP产品颗粒外观的因素,如模板、切刀、进刀风压、进料量、切粒水温度等进行了科学分析,并提出了相应的改进措施,从而降低不规则颗粒发生的频次。
关键词:PP 挤压机模板切刀进刀风压切粒水温抚顺石化公司乙烯厂90kt/a聚丙烯(PP) 装置以上游乙烯裂解生产的丙烯为原料,采用巴塞尔公司spheripol液相本体法工艺路线,可以生产均聚、无规共聚、抗冲共聚等共计51种牌号的 PP产品。
与PP装置配套的同向啮合双螺杆挤压机组由德国WP引进,型号为ZSK240。
作为PP装置的关键设备,挤压机组的运行状况不仅制约着上游聚合工段操作的平稳性,而且也影响到出厂产品的质量等级。
自装置生产出合格PP产品至今,挤压机组总体运行平稳,但受不同牌号产品切换的影响,同时受模板、切刀以及进刀风压、进料量、切粒水温度等操作参数的影响,导致产品中多次出现不规则颗粒。
颗粒大小不均匀不仅降低了粒料的堆密度,而且影响了分级筛选机的正常运行,使大量外形尺寸超标的颗粒进入成品料仓,严重时甚至导致挤压工段非计划停车。
因此,科学地分析各种可能导致不规则颗粒发生的因素,同时借鉴同类装置的成功经验,采取针对性的改进措施对提高 PP产品外观等级,保证装置长周期平稳运行都具有重要的意义。
1造粒流程简介PP粉料与助剂通过料斗进入挤压机,在高温条件下混合并熔融。
在同向啮合双螺杆的挤压、剪切、均化作用下,从造粒模板成型孔处挤出的熔融树脂进入切粒水室,然后被高速旋转的切刀切成粒料,粒料经切粒水冷却、固化后输送至预水分离器、大块剔除器、离心干燥器。
脱水后的颗粒进入分级筛选机,筛选出的合格颗粒进入掺混料仓掺混,最终由包装车间包装出厂。
2不规则颗粒的成因分析颗粒外观是否规则是评价PP产品的一个重要质量指标。
根据国内同行业普遍遵循检验方法定义,不规则粒料指的是任意方向上尺寸大于 5mm 的粒子(包括连粒)或者小于 2mm的粒子(包括碎屑和碎物)。
挤压造粒机组常见故障分析及处理

推动 切刀刀轴 活动 的是 1 个 由气压 转换至 液 压的控制单元 。正常运行时 ,模板前物料压力为 4 . 6 MP a , 当液 压 缸漏 油 时 ,刀轴 向前 的推 力 会 下 降 , 导 致 推 力不 足 。 当模 板 后 树 脂 压 力 大 于进 刀 压力 后 ,就 会 发生退 刀现 象 。
( 2 ) 油 路带 气
液 压 油 在 工 作 时 必 须 保 证 无 气 体 。若液 压 油
铝进 入树脂 中造成色粒 ;④树脂下料 系统氧含量 高,导致物料在高温和氧的作 用下发生 了分解 ;
第9 期
张鑫 挤压造粒机组 常见故 障分析 及处理
一 5 5.
⑤ 因异常 而进 入系 统 的其他 物 质造 成 色粒 。
相 对 较 大 的液 压 缸 时 ,会 发 生 体 积变 化 ,造 成 进 刀压 力不 稳 ,从而 引起 刀轴跳 动 。
( 3 1 进 刀不及 时
切 粒 机 开 车 过 程 中 , 需 要 手 动 进 行 切 粒 室
锁 紧 。锁 紧切 粒 室 与 切 粒机 启 动之 间有 一 个 短 暂 的 时 间 间 隙 ,在 此 期 间 ,模 板 依 然 会 流 出部 分 树 脂 , 待通 水 进 刀 后 ,树 脂 冷 却粘 在 切 刀 盘 上 ,形 成 垫 刀 。 因此 在 进 行 合模 操 作 时 ,应 尽 可 能 将模
产 生蛇 皮 粒 的主 要 原 因 是 切 刀 刀 刃 不 锋 利 或 刀 刃 背 面 不 光 滑 。切 下 的物 料 不 能 及 时 与 切 刀脱 离 , 随着 切 刀 不 断 切 下物 料 ,最 终 形 成蛇 皮状 物
Hale Waihona Puke 出 ,进 而 导 致 整 个 切 粒 室和 后 系 统 管 线 被 物 料 堵 满 ,发生 “ 灌 肠 ”事故 。
挤压造粒机组设备结构及常见故障分析判断

骨架油封 迷宫密封 滑动轴承
风机
风机
冷却器
主电机
冷却水进 冷却水出
升压油泵 润滑油泵 过滤器 冷却器
冷却水进 冷却水出
润滑油箱
• 1.2 主电机 • 由电机、润滑油系统、冷却系
统组成 • 主电机是挤压机的主要动力源,
它通过减速器带动两根螺杆同 向旋转。当盘车电机达到额定 转速或额定转矩后,主电机自 动启动,一般也可以手动启动。 • 润滑油系统的目的是:电机启 动前由升压油泵给转子一个上 升力,使转子轴与轴承之间形 成油膜,减小主电机启动扭矩 及保护轴承;当电机启动后, 润滑油泵启动,为轴承提供润 滑,此时升压油泵停止运行。 • 冷却系统的目的:由于主电机 功率都较大,运转过程中将产 生大量的热,仅靠风机强制通 风不能将热量带走,尤其在夏 季,因此需要将空气冷却后再 进入电机才能达到保证电机正
挤压造粒的目的是将聚丙烯粉料和加入的各 种添加剂通过通过加热融融,经过挤压机螺 杆的掺和、混炼,使添加剂均匀分布到融融 的聚丙烯物料中,再通过切粒机形成内在质 量稳定的聚丙烯颗粒料。
二、挤压造粒单元
• 挤压造粒单元流程示意图
冷却水出
过滤器
换 热 器
切粒水 水箱
冷却水进 切粒水水泵
离心 干燥器
预脱水器
1.3摩擦离合器 主电机与减速器之间一般都 装有离合器。摩擦离合器又叫 滑擦离合器,其主要目的是保 证设备安全。
由图可知,当挤压机主减速 机侧出现问题,造成扭矩上升, 超过摩擦盘与推力盘的摩擦阻 力时,摩擦盘与推力盘将产生 相对滑动,主电机的力矩将无 法传递给主减速机,从而保证 了主减速机和螺杆轴的安全。 在摩擦离合器的主减速机侧和 主电机侧均安装由测速探头, 当两个测速探头的速差超过 5rpm时,主电机将联锁停车。
聚丙烯装置国产挤压造粒机组故障分析
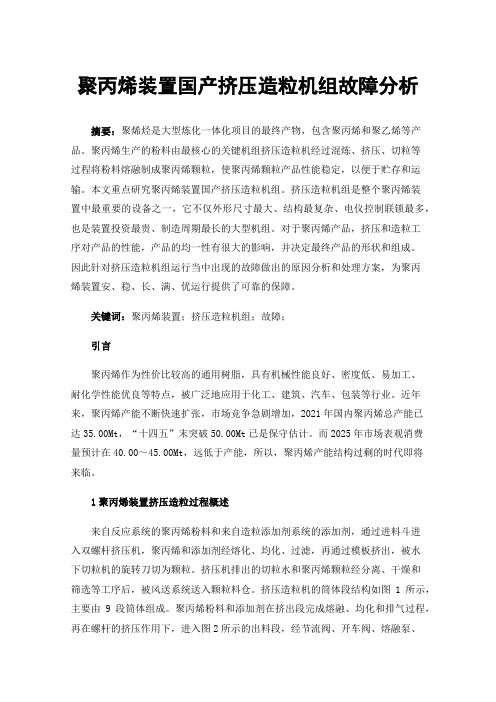
聚丙烯装置国产挤压造粒机组故障分析摘要:聚烯烃是大型炼化一体化项目的最终产物,包含聚丙烯和聚乙烯等产品。
聚丙烯生产的粉料由最核心的关键机组挤压造粒机经过混炼、挤压、切粒等过程将粉料熔融制成聚丙烯颗粒,使聚丙烯颗粒产品性能稳定,以便于贮存和运输。
本文重点研究聚丙烯装置国产挤压造粒机组。
挤压造粒机组是整个聚丙烯装置中最重要的设备之一,它不仅外形尺寸最大、结构最复杂、电仪控制联锁最多,也是装置投资最贵、制造周期最长的大型机组。
对于聚丙烯产品,挤压和造粒工序对产品的性能,产品的均一性有很大的影响,并决定最终产品的形状和组成。
因此针对挤压造粒机组运行当中出现的故障做出的原因分析和处理方案,为聚丙烯装置安、稳、长、满、优运行提供了可靠的保障。
关键词:聚丙烯装置;挤压造粒机组;故障;引言聚丙烯作为性价比较高的通用树脂,具有机械性能良好、密度低、易加工、耐化学性能优良等特点,被广泛地应用于化工、建筑、汽车、包装等行业。
近年来,聚丙烯产能不断快速扩张,市场竞争急剧增加,2021年国内聚丙烯总产能已达35.00Mt,“十四五”末突破50.00Mt已是保守估计。
而2025年市场表观消费量预计在40.00~45.00Mt,远低于产能,所以,聚丙烯产能结构过剩的时代即将来临。
1聚丙烯装置挤压造粒过程概述来自反应系统的聚丙烯粉料和来自造粒添加剂系统的添加剂,通过进料斗进入双螺杆挤压机,聚丙烯和添加剂经熔化、均化、过滤,再通过模板挤出,被水下切粒机的旋转刀切为颗粒。
挤压机排出的切粒水和聚丙烯颗粒经分离、干燥和筛选等工序后,被风送系统送入颗粒料仓。
挤压造粒机的筒体段结构如图1所示,主要由9段筒体组成。
聚丙烯粉料和添加剂在挤出段完成熔融、均化和排气过程,再在螺杆的挤压作用下,进入图2所示的出料段,经节流阀、开车阀、熔融泵、滤网,最后通过模板挤出。
筒体段和出料段的温度由导热油系统控制,不同的熔融指数对应不同的温度参数。
图1挤压造粒机筒体段的结构图2挤压造粒机的出料段结构2挤压造粒机组和辅助系统常见故障2.1挤压机筒体螺杆尾部密封处泄漏粉料大橡塑挤压造粒机SJSH-350P螺杆尾部密封为填料和氮气吹扫组合式密封,启动前要先投用氮气吹扫,氮气吹扫压力为0.08MPa。
挤压造粒机异常振动分析、解决

从传 动机构 、 做功部件等部位进 行了逐一分析 。
21传 动 部 分 .
传动部分产生异音的部位 主要 涉及齿 轮 、 摩擦 离合器 、 轴承。如果上述部件出现故 障易造成异 常声 音 , 例如齿 轮出 现磨损 、 间隙超 差 、 断齿等 现象 ; 轴承滚 动 体缺 陷 、 持架 损 保 坏、 配合松动等现象 ; 离合器间隙大 、 磨损等现象 ; 减速箱 另外 内进入异物等均 有可 能造成 振动 。若要 彻底 检查 上述部 位 必须进行减速箱解体 ( 1 。 图 ) 图 1为 减 速箱 效 果图 , 减速箱 是 日本 该 JW 公司生产 , S 有两 个 输 出 轴 , 部 结 构 复 内
s i l e eh d . pr t m t o s as o f
K e r a n r ls u d;ce a l ss; t ta fr ain y wo ds: o ma o n sr w;nay i daa;rnso b m t o
l 基本 情况
2O O9年 1月 4日大庆炼化公 司 3 万吨/ 聚丙烯厂挤压 ( 】 年
-
7 ・ O
挤压 造粒 机 异 常振 动 分 析 、 决 解
王瀚 伦 , 曲淑 艳 , 王保庆 , 张鸿韬
( 大庆 炼化公 司 机 电仪厂 , 黑龙 江 大庆 13 1 ) 64 1
、
、
摘 3万 / 要: 吨 年聚丙 挤压造 在生 运行中 发异常 音, 产负 o 烯 粒机 产 突 声 生 荷达不 产的 到生 基本要求, 严重影响亍 丙 ’ 烯产品的 綦 生
发现两个螺杆挤 压段 螺旋 套磨损情 况较年初 更为严重 , 螺旋
挤压造粒机组常见故障分析处理

961 挤压造粒机组的常见故障挤压造粒机组在运行过程中,离合器由于摩擦作用导致分离脱开,造成机组连锁停车的主要原因有:1)机组的主电机发生故障;2)传动系统故障;3)挤压造粒机螺杆工艺段发生故障;4)水下切粒系统发生故障。
这些主要原因中最常见的故障就是:主电机系统的主电机扭矩过高或过低;传动系统的摩擦离合器故障;挤压造粒机螺杆工艺段系统的熔体压力过高以及水下切粒机系统故障。
2 挤压造粒机的常见故障及应对措施2.1 主电机系统的主电机扭矩过高出现这种现象的主要原因是:润滑油系统发生故障,主电机输出轴与齿轮箱出入轴的中心位置对中不良,电机以及离合器振动等原因都会损坏主电机轴承,造成电机的扭矩过高。
不仅如此,造粒机进料负荷过大或物料熔融不良也会引起主电机扭矩过大。
应对措施:首先,定期对机组内的润滑系统进行检查、清洗,定期更换润滑油,对主机电机轴承进行检查,测定主电机的空载电流值以及运转温度或是运行功率,确定是否在规定值的范围内运行,否则应考虑是否需要更换主电机轴承。
其次,定期检查主电机输出轴与齿轮箱输入轴之间的对中情况,及时对轴承进行校核。
再次,进行电气测试检查,找出轴承转子不稳定的原因,并对离合器的振动速度进行检测,确保离合器振动速度在规定的范围内,若超出规定值,及时调整离合器的动平衡。
最后,应当定期对机组内的加热、冷却系统进行检查,保证进料的温度均匀,熔融状态好,不仅如此,还要控制好进料速度以及进料量,保证主电机功率稳定。
2.2 摩擦离合器发生故障这种现象发生的主要原因是:主电机的瞬间启动电压过低,使得摩擦盘过热,进而加速老化损坏,或是摩擦盘内的空气压力过低均可引起摩擦离合器脱开。
应对措施:机组的主电机启动运转时,尽量避免用电高峰期,减轻机组的进料负荷,延长主电机重新启动的时间间隔。
在环境温度较高时,连续两次及以上启动主电机时,不仅要确保足够长的时间间隔,还应及时将主电机的温度冷却下来。
定时清理摩擦盘和摩擦片的表面灰迹,检查摩擦盘和摩擦片是否能够正常使用,若破损严重应当及时更换。
挤压造粒机组常见故障分析处理

挤压造粒机组常见故障分析处理作者:周炬鲜杨岩桢杜冠宇来源:《中国科技博览》2019年第05期[摘要]挤压造粒机组是造粒生产线中的核心生产设备,其集机械、电气和仪表于一体,在使用过程中需要较高的自动化控制水平,因此在该机组运行的过程中易出现难以察觉的故障,并对机组的整体运行效果产生影响,损害机组的经济效益。
本文通过结合造粒生产过程中的基础理论对挤压造粒机组运行过程中可能发生的故障进行分析,总结故障原因,并提出针对性解决策略,从而保证机组运行稳定。
[关键词]挤压造粒机组故障原因解决策略中图分类号:G157.3 文献标识码:A 文章编号:1009-914X(2019)05-0006-01在整体生产加工环节中,挤压造粒机作为大投资的成套设备,整体机组具有极其复杂的内部状态。
许多故障都会造成离合脱离等关键问题,下文便针对挤压造粒机组在运行过程中所产生的问题进行详细分析。
1.挤压造粒机组常见障碍1.1主电机扭矩过高造成该故障的原因主要有:(1)挤压造粒机组的主电机输出轴与齿轮箱出入轴二者的中心位置未能良好对接电机。
(2)离合器自身产生的震动对主电机轴承造成部分损坏。
(3)挤压造粒机的润滑油系统出现故障。
(4)物料未能良好的进行熔融或者是喂料对造粒机产生巨大负荷。
1.2摩擦离合器出现故障造成该故障的原因主要有:(1)主电机在瞬间启动的过程中,电压过低,从而造成摩擦盘产生巨大热量,加速摩擦离合器的老化或是直接造成损害。
(2)摩擦盘内部空气压力过低,导致摩擦离合器脱开。
1.3挤压造粒机螺旋工艺部分故障造成该故障的主要原因有:(1)节流阀前后熔体具有过大压力。
(2)换网器周围熔体压力差距过大(3)开车阀门转动故障(4)机头熔体压力过大。
1.4水下切粒机系统出现故障造成该故障的主要原因有:(1)切粒机自身的切刀严重磨损。
(2)切粒机振动频率过高。
(3)颗粒水流量低下。
(4)切刀与模版之间的切合面未能贴紧。
(5)物料熔融指数具有较大波动,从而导致物料流速产生差异。
聚丙烯装置挤压造粒机运行问题分析及处理

聚丙烯装置挤压造粒机运行问题分析及处理关键词:聚丙烯;挤压造粒机;安装控制点;开车调试引言SJSH-350P挤压造粒机是大榭石化四期30万吨/年聚丙烯的关键生产设备,由中国大连橡胶塑料机械有限公司生产,单机最大负载可达到47t/h,采用11000kW主电机和1400kW的齿轮泵,其作用是将聚丙烯粉末与助剂混合熔融,经过切粒机在水下切粒冷却固化进入下游辅助设备干燥和筛分,再送往掺混料仓,切粒的作用便于储存和运输。
挤压造粒成套系统主要设备包括:主电机,减速箱和气动摩擦离合器,螺杆和筒体,换网器,齿轮泵,切粒机和其他辅助设备组成。
整套设备多,调试周期长,质量控制点多,本文将针对减速箱、螺杆、齿轮泵、切粒机等的具体安装和调试要点进行分析和阐述。
1聚丙烯装置挤压造粒机的设备和零部件安装分析1.1减速箱减速箱是传动装置的核心部件,它的作用是把传动装置所产生的动能,通过减速、增扭,分别传递到两个螺杆上,使两个螺杆同向旋转,承受在输送熔融粉料时,螺杆产生的反作用力。
减速箱是转矩分流和轴向作用力的传动变速箱。
根据聚丙烯年产量和设计需求,选择功率为11000kW和1485rpm的大功率主电机,而在输出端采用低扭矩、高扭力的闭式斜齿轮的扭矩分流传动的减速箱。
因此,对于减速箱来说,扭矩保护是非常重要的[1]。
主电动机与减速箱的输入端联接采用了气动摩擦离合器,主要由摩擦盘,弹性联轴器、速度传感器组成。
它有两块金属摩擦盘,每块摩擦盘两边固定安装摩擦片,摩擦片由螺栓固定,摩擦片一般使用石墨或聚四氟润滑材质。
工作时,压缩气体将压板轴向压缩,靠摩擦片和压板之间的摩擦力传递扭矩,具有扭矩限制保护功能,保护设备的安全运行。
在挤压造粒机正常运行时,气动摩擦离合器处于闭合状态,气动摩擦离合器配置一个气控箱,气源动力为仪表风,用于控制摩擦离合器的分离和闭合,当气控压力达到设定压力时,摩擦离合器处于闭合状态,当气控压力低于设定值时,靠复位弹簧使摩擦片处于分离状态。
聚丙烯挤压造粒机组典型故障处理

P K 8 0 3 是 中石 油 大 港 石 化 公 司 1 0 万t , a 聚 丙 烯 装 置 的关 键
障信息为“ F E E D I N G S Y S T E M S T O P ” 。确认是 P K 8 0 2故障引发 的机组停车( 该故障 占挤压造粒机组停 车原 因比例较大 ) 。
其他故障水下切粒系统故障故障原因主要有切粒水泵p81ab停粒料料斗d87料位高高切刀磨损不均匀磨损严重或切刀刀刃损伤切粒水流量过低切粒机振动过大切刀与模板贴合度不佳切粒水温度过高切粒机水室排水阀未关等也会造成pk83停车
聚丙烯挤压造粒机 组典型故 障处理
孙亚玲
( 中国石 油大港石化公 司 天 津)
摘要 挤 压造粒机 组典 型故 障, 如料斗 ¥ 8 0 1 料位 高报 , 上游喂料 系统 ( P K 8 0 2 ) 故 障, 主 电机 电流低报等故 障处理过程 。分析 故
障原 因, 给 出解 决措施及应对操作手法。 关键词 聚丙烯设 备 故障 处理
B 中图 分 类 号 T Q 3 4 0 . 5 文 献 标识 码
处理过程 。
下料量超范围 、 B Y P A S S阀位置不到位等故障 ) 和P K 8 0 2 其他设
备故障引起的联锁停 车。 P K 8 0 2采用 C o mp a s s B u l k H a n d l i n g S y s t e m P t e .L t d . 提 供 的s 7 — 3 0 0 P L C控 制系统 , 内部控制 较复杂 , 维护难度较 大。首
P K 8 0 3 正式投入生产 , 至今共计 停车 5 3次 , 主要原 因 : ①聚合工 段 出现 问题 , 计 划停 车 1 3次 ; ② 拉丝 料 、 块 料过 多 , 导致 料斗 ¥ 8 0 1 等设 备堵塞 , 造粒机联 锁停 车 1 2次 ; ③喂料 系统 ( P K 8 0 2 ) 故障 , 停车 1 2次 ; ④晃 电 , 造 粒机停车 6次 ; ⑤造 粒机主 电机 电 器故 障, 粒料输送罗茨风机 C 8 0 4备机 电器故 障不能正常切换 , 造粒变电所 U P S故障等电气 故障 , 停车 5次 ; ⑥其他原 因停 车 3 次; ⑦检修正常停车 2次 。下 面介 绍几 例 P K 8 0 3典型停车故 障
挤压造粒机组常见故障和解决措施

工艺与装备155挤压造粒机组常见故障和解决措施李廷尧张佐(中天合创能源有限责任公司化工分公司,鄂尔多斯017000)摘要:挤压造粒机组是工业生产的一个重要组成部分。
本文研究挤压造粒机组常见故障,分析液压缸漏油、油路带气、进刀不及时、异常颗粒、颗粒的水流量少以及切刀的磨损程度较大产生的故障原因,给出挤压造粒机 组常见故障的解决措施,从而能够有效处理挤压造粒机组常见故障。
关键词:挤压造粒机组漏油油路带气异常颗粒磨损引言生产加工过程中,挤压造粒机组是投资大且装置成套 的装备。
由于其内部关联状态复杂,很多故障都使得装置 出现离合脱离、造粒机组停车等间题。
本文以大连橡塑生 产的型号为CME-450A,布置模式为L型的挤压造粒机组为 例。
整个机组的外形尺寸长度为21.8m,宽度约为10.2m。
整个挤压造粒机组的产量,最少为23182kg/h,即18.92 万吨每年;正常产量为37500kg/h,即35万吨每年。
1挤压造粒机组常见故障1.1推导障碍刀盘在运行中产生后退状况,使得切刀不再与刀板结 合。
物料由于处于切刀及模板中间,使得从模板孔中溢出 的物料缠绕在刀盘装置上,使得切粒空间及系统管线均被 物料堵塞,进而产生灌肠状况及退刀状况。
1.2颗粒外形异常状况1.2.1蛇皮粒以及拖尾粒的产生蛇皮粒是类似蛇皮的带状树脂状态,拖尾粒则是由于 切粒状况不到位发生的具有锥角以及毛刺的颗粒。
拖尾粒 外形为常见物料并带有锥角、毛刺以及拖尾的状况。
1.2.2色粒色粒为深褐色的颗粒和除去树脂颜色外的其他颗粒。
1.2.3大颗粒和小颗粒国标中,针对大颗粒给出的界定为任意角度都大于5mm 的粒子,包含连粒;而小粒则界定为任意角度均小于2mm 的粒子,包含碎屑、碎粒。
1.3颗粒的水流量很低当颗粒的水流量低于联锁结果时,使得切粒装置停止 工作,进而使得模孔导出的物料不能及时从切粒室送出,使得切粒室及后续管线部分被物料堵塞并产生“灌肠”状况。
聚丙烯装置挤压造粒机运行故障分析及处理措施

油 温度 。 最 后视 情 况可稍 微提 高 摩擦离 合器 的 空气压 力 。 3挤 压造 粒机 常见 故 障 的处 理措 施
3 . 1磨 刀程 序运 行故 障处理 磨刀程 序运 行 的好坏 , 直接 关系 到造 粒开车 成功 率和切 刀切 粒效 果 。 磨刀
1挤 压造粒 机 流 程简 介
理论广角
I ■
C h i n a s c i e n c e a n d T e c h n o l o g y R e v i e w
聚 丙 烯 装 置 挤 压造 粒机 运 行 故 障 分 析 及 处 理 措 施
杜 娟 李
辽宁
森
抚顺 1 1 3 0 0 0 )
( 抚 顺石 化 公司 烯烃 厂
[ 摘 要] 本 文针 对某 石 化工 厂 聚丙 烯装 置挤 压 造粒 机在 运行 中出现 过 的故 障原 因进 行 了分析 , 制 定相 应 的解 决措施 , 并从 中总结 出 规范 性 的操作 , 优化 了 造粒 机 的操作 , 减少 了停 车事件 的 发生 , 保 障 了装置 的长 周期运 行 。 [ 关键 词3 聚丙 烯 、 造 粒机 、 故障、 措 施 中图 分类号 : TQ 3 2 5 . 1 4 文献 标识 码 : A 文章编 号 : 1 0 0 9 — 9 1 4 x ( 2 0 1 4 ) 4 4 — 0 3 1 8 一O l
挤 压机 主要作 用 是将 聚丙烯粉 料 与添加 剂均 匀混合 , 加热、 融熔 、 混炼、 挤
压 和切 粒 , 负 责将 聚丙烯 从粉 料转 化成成 品料 的工 艺过 程 。 同 向啮合 的双螺 杆 由主 电机驱 动 , 经 过减速 器 二级转 速输 出 , 聚丙 烯粉料 和添 加剂 由计 量秤计 量
关于挤压造粒机正常生产过程中异常停车原因的研究与解决方法
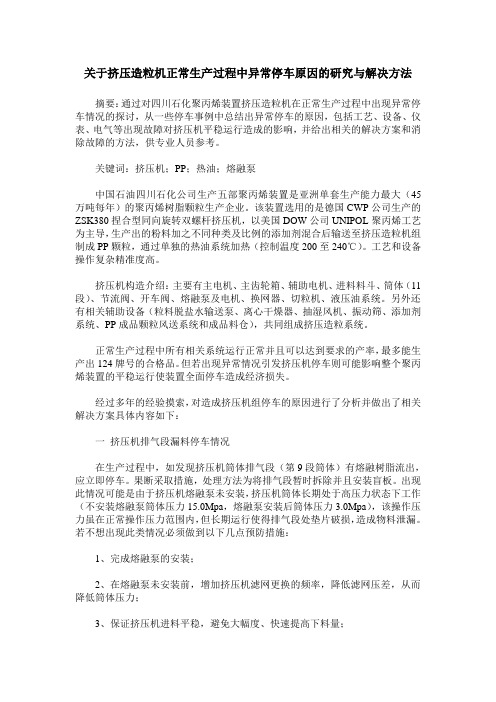
关于挤压造粒机正常生产过程中异常停车原因的研究与解决方法摘要:通过对四川石化聚丙烯装置挤压造粒机在正常生产过程中出现异常停车情况的探讨,从一些停车事例中总结出异常停车的原因,包括工艺、设备、仪表、电气等出现故障对挤压机平稳运行造成的影响,并给出相关的解决方案和消除故障的方法,供专业人员参考。
关键词:挤压机;PP;热油;熔融泵中国石油四川石化公司生产五部聚丙烯装置是亚洲单套生产能力最大(45万吨每年)的聚丙烯树脂颗粒生产企业。
该装置选用的是德国CWP公司生产的ZSK380捏合型同向旋转双螺杆挤压机,以美国DOW公司UNIPOL聚丙烯工艺为主导,生产出的粉料加之不同种类及比例的添加剂混合后输送至挤压造粒机组制成PP颗粒,通过单独的热油系统加热(控制温度200至240℃)。
工艺和设备操作复杂精准度高。
挤压机构造介绍:主要有主电机、主齿轮箱、辅助电机、进料料斗、筒体(11段)、节流阀、开车阀、熔融泵及电机、换网器、切粒机、液压油系统。
另外还有相关辅助设备(粒料脱盐水输送泵、离心干燥器、抽湿风机、振动筛、添加剂系统、PP成品颗粒风送系统和成品料仓),共同组成挤压造粒系统。
正常生产过程中所有相关系统运行正常并且可以达到要求的产率,最多能生产出124牌号的合格品。
但若出现异常情况引发挤压机停车则可能影响整个聚丙烯装置的平稳运行使装置全面停车造成经济损失。
经过多年的经验摸索,对造成挤压机组停车的原因进行了分析并做出了相关解决方案具体内容如下:一挤压机排气段漏料停车情况在生产过程中,如发现挤压机筒体排气段(第9段筒体)有熔融树脂流出,应立即停车。
果断采取措施,处理方法为将排气段暂时拆除并且安装盲板。
出现此情况可能是由于挤压机熔融泵未安装,挤压机筒体长期处于高压力状态下工作(不安装熔融泵筒体压力15.0Mpa,熔融泵安装后筒体压力3.0Mpa),该操作压力虽在正常操作压力范围内,但长期运行使得排气段处垫片破损,造成物料泄漏。
2#聚丙烯造粒机仪表典型故障分析及处理
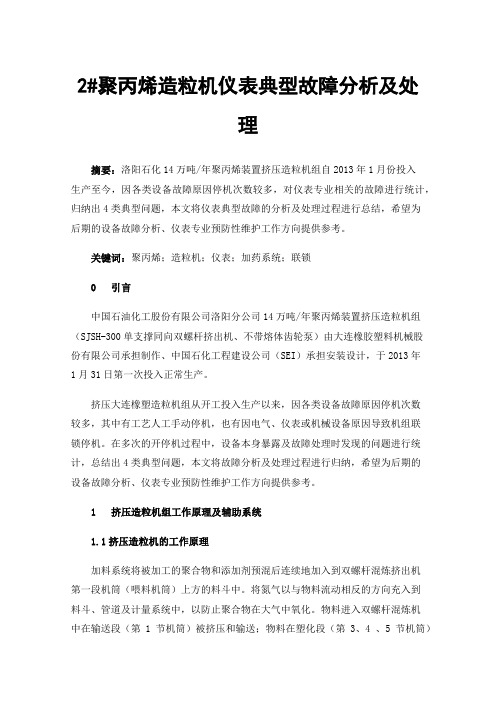
2#聚丙烯造粒机仪表典型故障分析及处理摘要:洛阳石化14万吨/年聚丙烯装置挤压造粒机组自2013年1月份投入生产至今,因各类设备故障原因停机次数较多,对仪表专业相关的故障进行统计,归纳出4类典型问题,本文将仪表典型故障的分析及处理过程进行总结,希望为后期的设备故障分析、仪表专业预防性维护工作方向提供参考。
关键词:聚丙烯;造粒机;仪表;加药系统;联锁0 引言中国石油化工股份有限公司洛阳分公司14万吨/年聚丙烯装置挤压造粒机组(SJSH-300单支撑同向双螺杆挤出机、不带熔体齿轮泵)由大连橡胶塑料机械股份有限公司承担制作、中国石化工程建设公司(SEI)承担安装设计,于2013年1月31日第一次投入正常生产。
挤压大连橡塑造粒机组从开工投入生产以来,因各类设备故障原因停机次数较多,其中有工艺人工手动停机,也有因电气、仪表或机械设备原因导致机组联锁停机。
在多次的开停机过程中,设备本身暴露及故障处理时发现的问题进行统计,总结出4类典型问题,本文将故障分析及处理过程进行归纳,希望为后期的设备故障分析、仪表专业预防性维护工作方向提供参考。
1 挤压造粒机组工作原理及辅助系统1.1挤压造粒机的工作原理加料系统将被加工的聚合物和添加剂预混后连续地加入到双螺杆混炼挤出机第一段机筒(喂料机筒)上方的料斗中。
将氮气以与物料流动相反的方向充入到料斗、管道及计量系统中,以防止聚合物在大气中氧化。
物料进入双螺杆混炼机中在输送段(第1节机筒)被挤压和输送;物料在塑化段(第3、4 、5节机筒)被剪切、混炼而熔融塑化;在均化段(第6、7、8、9节机筒)物料及各种添加剂被进一步混合、分散、塑化后被输送到挤出造粒系统。
熔融物料首先进入到节流换向阀,调节节流阀的调节板,可以改变物料的停留时间,从而调节物料的混炼效果。
当开车时物料塑化没有达到要求,或者后续设备出现异常时,将开车阀打到排料工位将物料排出。
当物料塑化良好时,将开车阀打到正常工作位,物料进入到换网装置,并定量供给换网装置。
挤压造粒系统事故案例汇编

挤压造粒系统事故案例汇编1.上海:F803堵,停车检修注:F803(类似于3PPD801、D802上方的滤袋)事故原因:D803无料位指示,而当时挤出机又不正常,D803高料位后无从知晓,PK801被迫停车。
把D803内料放出,换F803滤袋,再开车。
教训及措施:(1)D803(3PP的D801A/B)必须在高位以下操作,否则会因PK801出现故障停车。
(2)KCV801必须完好,否则F803滤袋堵塞,造成PK801停。
(3)F803滤袋与F301滤袋同,必须抗静电等级达到一定要求。
2.上海:D902均化料仓闪燃事故经过及处理:2000年2月9日,2PP装置均化料仓发生过两次闪燃事故,使两批料共400吨左右的PP均因炭黑污染而降为次品。
故障原因:汽蒸系统料位控制不稳定,使进入D501的粉料脱除丙烯单体效果不良,粉料夹带丙烯气体进入后续工序,即进入D502、D803。
含有丙烯的粉料经造粒送入均化料仓后,丙烯气体就在料仓内,从粒料表面不断逸出,而装满料的料仓容积有限,其丙烯浓度很快能达到爆炸极限,一旦粒子间产生的静电积累到放电,则产生的电火花就使达到爆炸极限的丙烯爆炸闪燃。
教训及措施:粉料从F301进入D501时,含有约2.5%的单体,在汽蒸器工作正常情况下,会全部被汽蒸去除,送往乙烯厂作燃气。
但当D501因各种原因未能建立正常料位时,就不能全部去除。
上述两批料的损失是巨大的,影响是严重的。
为此,对于汽蒸操作必须做到以下:(1)建立40%-60%料位,以保证足够的汽蒸时间,由于3PP产量增大,而D501增容不多,因此D501内滞留时间在同样料位下会更短,在满足操作弹性的要求下尽可能建立高的料位。
(2)保证TIC502、TIC503温度达120℃,按操作法设定FIC501、FIC502的蒸汽流量。
(3)PK501确保正常运转,使D501内有较低压力,以利D501内单体的逸出。
(4)关注氮气干燥系统内烃类气体分析仪AI531测出的量。
挤压造粒机组抽吸系统的故障分析与改进措施研究
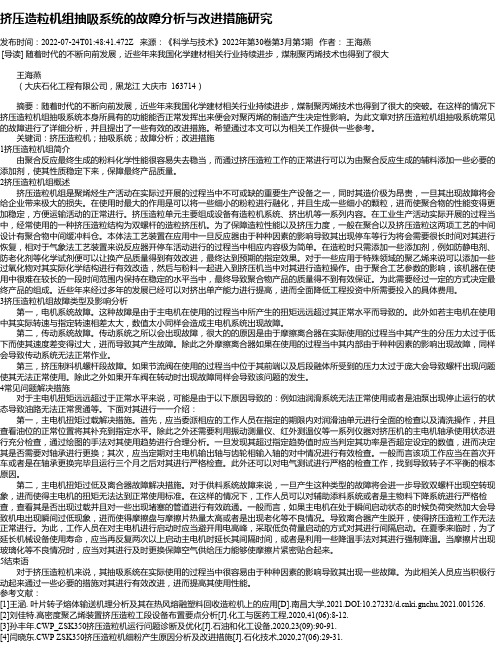
挤压造粒机组抽吸系统的故障分析与改进措施研究发布时间:2022-07-24T01:48:41.472Z 来源:《科学与技术》2022年第30卷第3月第5期作者:王海燕[导读] 随着时代的不断向前发展,近些年来我国化学建材相关行业持续进步,煤制聚丙烯技术也得到了很大王海燕(大庆石化工程有限公司,黑龙江大庆市 163714)摘要:随着时代的不断向前发展,近些年来我国化学建材相关行业持续进步,煤制聚丙烯技术也得到了很大的突破。
在这样的情况下挤压造粒机组抽吸系统本身所具有的功能能否正常发挥出来便会对聚丙烯的制造产生决定性影响。
为此文章对挤压造粒机组抽吸系统常见的故障进行了详细分析,并且提出了一些有效的改进措施。
希望通过本文可以为相关工作提供一些参考。
关键词:挤压造粒机;抽吸系统;故障分析;改进措施1挤压造粒机组简介由聚合反应最终生成的粉料化学性能很容易失去稳当,而通过挤压造粒工作的正常进行可以为由聚合反应生成的辅料添加一些必要的添加剂,使其性质稳定下来,保障最终产品质量。
2挤压造粒机组概述挤压造粒机组是聚烯烃生产活动在实际过开展的过程当中不可或缺的重要生产设备之一,同时其造价极为昂贵,一旦其出现故障将会给企业带来极大的损失。
在使用时最大的作用是可以将一些细小的粉粒进行融化,并且生成一些细小的颗粒,进而使聚合物的性能变得更加稳定,方便运输活动的正常进行。
挤压造粒单元主要组成设备有造粒机系统、挤出机等一系列内容。
在工业生产活动实际开展的过程当中,经常使用的一种挤压造粒结构为双螺杆的造粒挤压机。
为了保障造粒性能以及挤压力度,一般在聚合以及挤压造粒这两项工艺的中间设计有聚合物中间缓冲料仓。
本体法工艺装置在应用中一旦反应器由于种种因素的影响导致其出现停车等行为将会需要很长时间对其进行恢复,相对于气象法工艺装置来说反应器开停车活动进行的过程当中相应内容极为简单。
在造粒时只需添加一些添加剂,例如防静电剂、防老化剂等化学试剂便可以让换产品质量得到有效改进,最终达到预期的指定效果。
- 1、下载文档前请自行甄别文档内容的完整性,平台不提供额外的编辑、内容补充、找答案等附加服务。
- 2、"仅部分预览"的文档,不可在线预览部分如存在完整性等问题,可反馈申请退款(可完整预览的文档不适用该条件!)。
- 3、如文档侵犯您的权益,请联系客服反馈,我们会尽快为您处理(人工客服工作时间:9:00-18:30)。
5、 粘着磨损谱片加热前与Fra bibliotek热后对比图分析:加热后磨粒颜色没有发生变化 结论:在此证明此粘着磨损颗粒属于铸铁 综合以上图谱信息诊断结论如下: 由于润滑油的润滑不良,或者超负荷运行,导致齿轮过度疲劳,形成大量的疲劳磨损, 使得该机器处于严重的异常磨损状态,建议立即停机检测。
油液监测技术交流群:244069742 邮件:pw@
现场停机检测图片:
3、 正常磨损图谱
该机器正常磨损在 15um,片状颗粒图谱。
4、 疲劳磨损谱片加热前与加热后对比图
分析:铸铁磨粒加热后颜色不会发生变化还是黄色 钢磨粒加热颜色会变蓝(钢淬火表面是蓝色) 结论:此齿轮表面发生了严重的疲劳磨损(齿轮一般由铸铁构成,轴承一般是不锈钢),排 除了轴承疲劳磨损的可能。
油液监测技术交流群:244069742 邮件:pw@
2、粘着磨损图谱
分析:此磨粒周围表面发黑,铁、钢在高温下氧化,形成黑色的四氧化三铁,磨粒也在 30um 以上,故此磨粒粘着磨损严重。 结论:由于润滑严重不良或过负载导致摩擦副直接接触产生高温,温度偏高产生四氧化三 铁。粘着磨损的主要成分是铁。
油液监测技术交流群:244069742 邮件:pw@
油液监测技术交流群:244069742 邮件:pw@
2012 年某钢铁企业挤压造力机油液监测诊断分析案例
挤压造力机油液分析铁谱检测,谱图如下: 1、 疲劳磨损图谱:
分析:磨粒尺寸在 30um 以上,所以严重的疲劳磨损,一般而言疲劳磨损磨粒在 15um 以下 属于正常磨损。 结论:设备润滑不良,过载、寿命