铸造缺陷(1) PPT课件
合集下载
铸件缺陷分析PPT课件

铸件在凝固末期或刚凝固 后不久产生的裂纹。
03
铸件缺陷形成原因及机理分析
原材料因素
原材料质量
使用不合格或质量差的原材料, 如废钢、生铁等,其中含有的杂 质元素和气体可能导致铸件缺陷 。
原材料配比
原材料配比不合理,如碳、硅等 元素含量过高或过低,会影响铸 件的凝固过程和机械性能。
熔炼工艺因素
熔炼温度
介绍了常用的铸件缺陷检测与评估方法,如目视检查、无损检测、 金相分析等,以及各种方法的优缺点和适用范围。
缺陷预防与控制措施
重点讲解了铸件缺陷的预防和控制措施,包括优化铸造工艺、提高原 材料质量、加强过程监控等方面。
学员心得体会分享
知识收获
学员们表示通过本次课程,对铸件缺陷的类型、成因、检 测与评估方法有了更深入的了解,对铸件质量控制的重要 性有了更深刻的认识。
其他可能影响因素
生产环境
生产环境中的温度、湿度和清洁度等因素对铸件质量也有一 定影响。例如,湿度过高可能导致型砂粘结力下降,温度过 高则可能导致铁液冷却速度过快。
操作技能
操作工人的技能水平和经验对铸件质量也有重要影响。例如 ,合箱时定位不准确、浇注时铁液温度控制不当等都可能导 致铸件缺陷。
04
铸件缺陷预防措施与改进方法
控制熔炼温度
根据原材料成分和熔炼设备特点, 合理设置熔炼温度,避免过高或 过低的熔炼温度对铸件质量产生 不良影响。
调整化学成分
通过添加合金元素和调整废钢、生 铁等原材料的配比,控制铁水的化 学成分,提高铸件的力学性能和耐 蚀性。
减少熔炼杂质
采取过滤、除渣等措施,减少熔炼 过程中产生的氧化物、硫化物等杂 质,提高铁水的纯净度。
夹渣和夹杂物
01属夹杂物,夹杂 物则是金属或非金属杂质。
铸造常见缺陷的修补技术PPT课件
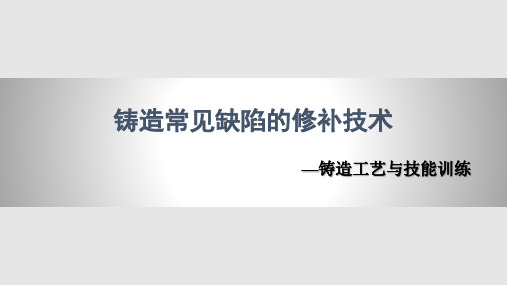
2)焊补时 ① 焊条直径可按待焊处壁厚进行选用。 ② 根据焊条直径、焊条类型、待焊铸件的壁厚等选择适当的电流。 ③ 用非石墨型焊条冷焊时,通常采取“小电流、短路、断续、分散焊” 。 ④ 用特制铸铁芯焊条冷焊时一般采取“大电流、连续、集中式操作”。 ⑤ 焊补厚壁件时可用多层堆焊的方法。 ⑥ 当焊件的材质较差、且焊缝强度高时,可用栽丝法。 ⑦ 当焊补有裂纹倾向缺陷时,可采用热态锤击法
3)焊补时注意事项 ① 难焊的铸件应在室内进行,以防风吹,最好将铸 件放置在炉旁,有助于提高整个铸件的温度。 ② 焊前若将需焊铸件局部或整体预热至100~200℃时, 则更能改善焊补区的加工性能。
(2)电弧半热焊补 电弧半热焊补常用钢芯石墨化型铸铁焊条。 常用于焊补非加工面上的各类缺陷。 1)焊补前 ① 缺陷的清理和加工与电弧冷焊基本相同。 ② 待焊的缺陷部分通常加热到400℃左右。 2)焊补时 ① 半热焊用的电流比冷焊用的电流要稍大。 ② 半热焊通常采取“连续堆焊” 的方法。 ③ 电弧通常采用长弧,但不宜太长,以免药皮中大量石墨化元素烧损;也 不宜太短,否则药皮不能充分熔化。
其修补方法是在缺陷处钻孔、精铰,采用过盈配合压入与铸件同质材料加 工的塞子,然后(分直流与交流)、软电缆、焊钳、焊条、地线夹、 面罩、清理工具等。 2. 操作步骤 (1)正确选择焊补设备、辅具、焊条及个人防护用具。 (2)根据焊条直径、焊条类型、待焊铸件的壁厚等选择 适当的电流。 (3)对焊补铸件缺陷周围进行必要的处理。
三、浸渍填补
浸渍填补是解决铸件渗漏问题的新技术,是将胶状的浸渗剂渗入铸件的 孔隙中使其硬化,与铸件孔隙内壁连成一体,达到堵漏的目的。
1. 浸渗剂 目前常用的浸渗剂有水玻璃型、合成树脂型和厌氧型三种。 2. 渗补工艺 渗补工艺因铸件结构、生产类型、浸渗剂种类、铸件缺陷位置及状态的 不同而不同。
铸锭缺陷 PPT课件
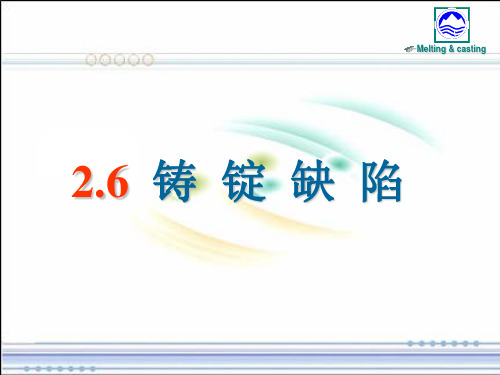
(5 )偏析瘤 是一种严重的反偏析现象,通常在铸锭的表面出现偏析瘤。
Melting & casting
枝 晶
出 现 间 隙
锡 偏 析 瘤
铸 模
铸 模
(a)-形成枝晶 (b)-出现间隙
铸 模
(c)-富锡熔体外溢
锡青铜中偏析瘤的形成 过程
(6 )防止偏析的方法 偏析是凝固过程中溶质再分布的结果。因此,一切能使成分均匀化和晶 粒 细化的方法,均有利于防止或减少偏析。 基本措施有: 增大冷却强度, 搅拌,变质处理,采用短结晶器,降低浇注温度,加强 二次水冷,使液穴浅平等。
Melting & casting
晶界偏析形成过程示意图
(3) 比重偏析
其形成原因是: (a)液相分层; (b)固相与液相比重不同。
Melting & casting
(4) 正偏析与反偏析 其形成原因是: (a)溶质分配系数K的不同, K<1时,后结 晶的固相溶质含量高,出现反偏析; (b)K>1时,后结晶的固相溶质含量低,出 现正偏析; (c)同时,与粗大的枝状晶有关。
热裂是在凝固收缩开始温度至非平衡固相线温度范围内形成的。热裂形成机理 主要有液膜理论、强度理论及裂纹形成功理论。
(a)液膜理论 凝固末期晶间残留的液膜 受铸锭收缩影响,液膜在拉应 力作用下被拉伸,当拉应力或 拉伸量足够大时,液膜就会破 裂,形成晶间热裂纹。
液膜理论示意图
(b)强度理论 强度理论认为,合金在线收缩开始温度至非平衡固相点间的有效结晶温度范 围,强度和塑性极低,故在铸造应力作用下易于热裂。
(1) 金属的凝固收缩 收缩的分类:包括凝固前的液态收缩、由液态变为固态的凝固收缩及凝固后的固态 收缩。 液态收缩率为1~2%、凝固收缩率为2~7%、固态收缩率为5~9%。
铸造缺陷组织缺陷PPT.

3、熔炼操作工艺 的,我也不知道他喜欢不喜欢这个车。” 测试不能替代面试,它是对面试的补充。 1.擦璃时,如果高处够不着,登桌子或椅子,一定要先看看桌子或椅子是否结实,或旁边有人扶着.
4、铁水的炉前处理 (1)、头部受伤后台有头晕、头痛、呕吐等症状,可能是脑震荡。这时应让病人安静平躺,头放平,头部冷敷,2~3小时内不给饮食
24
(四)防止对策: 1、适当降低碳当量; 2、合金化;均匀化。 3、孕育处理; 4、适当降低浇注温度; 5、改善铸件的温度场(如放冷铁)
25
六、魏氏石墨 (一)特征: 1、同共晶片状石墨是相互连接的; 2、石墨片延伸至珠光体基体中; 3、石墨片极薄,其厚度只有1800Å
(1.8×10-ቤተ መጻሕፍቲ ባይዱm) (二)危害:力学性能下降一半。 (三)形成原因:Pb、 H2、Al。 (四)防止对策:减少Pb、 H2、Al。
26
组织缺陷
2、说说有毒无毒蛇的区别:形态上,齿痕上。(放幻灯) 面试者需要了解空缺岗位与现有岗位之间的关联,它在整个单位结构中的位置,在现有团队工部门中的作用,新来的人将向谁汇报工 作,谁又向他汇报工作等。 二、 教学过程:
,在脑中整理出一套与客户交流的方案。 紧张,打哈欠等不良习惯具有感染性,所以有时通过观察应聘者的形体语言就可以知道你自己的形体语言如何。
2)铸型紧实度、吃砂量 大家都知道,车辆油漆的光洁度非常高,车门把手上面都是镀铬的,比较亮,只要手触摸到门把手或车身,马上会留下指纹。销售人
员在展厅里面工作的时候,随时随地要保持展车的规范清洁性。 我们要安全合理地使用体育器材。
石墨的形态: 5
1、分布特征 均匀无向性分布
2、形成条件 1)共晶成分(亚共 晶) 2)冷速较慢
3、对性能的影响 好
4、铁水的炉前处理 (1)、头部受伤后台有头晕、头痛、呕吐等症状,可能是脑震荡。这时应让病人安静平躺,头放平,头部冷敷,2~3小时内不给饮食
24
(四)防止对策: 1、适当降低碳当量; 2、合金化;均匀化。 3、孕育处理; 4、适当降低浇注温度; 5、改善铸件的温度场(如放冷铁)
25
六、魏氏石墨 (一)特征: 1、同共晶片状石墨是相互连接的; 2、石墨片延伸至珠光体基体中; 3、石墨片极薄,其厚度只有1800Å
(1.8×10-ቤተ መጻሕፍቲ ባይዱm) (二)危害:力学性能下降一半。 (三)形成原因:Pb、 H2、Al。 (四)防止对策:减少Pb、 H2、Al。
26
组织缺陷
2、说说有毒无毒蛇的区别:形态上,齿痕上。(放幻灯) 面试者需要了解空缺岗位与现有岗位之间的关联,它在整个单位结构中的位置,在现有团队工部门中的作用,新来的人将向谁汇报工 作,谁又向他汇报工作等。 二、 教学过程:
,在脑中整理出一套与客户交流的方案。 紧张,打哈欠等不良习惯具有感染性,所以有时通过观察应聘者的形体语言就可以知道你自己的形体语言如何。
2)铸型紧实度、吃砂量 大家都知道,车辆油漆的光洁度非常高,车门把手上面都是镀铬的,比较亮,只要手触摸到门把手或车身,马上会留下指纹。销售人
员在展厅里面工作的时候,随时随地要保持展车的规范清洁性。 我们要安全合理地使用体育器材。
石墨的形态: 5
1、分布特征 均匀无向性分布
2、形成条件 1)共晶成分(亚共 晶) 2)冷速较慢
3、对性能的影响 好
铸件常见铸造缺陷 PPT
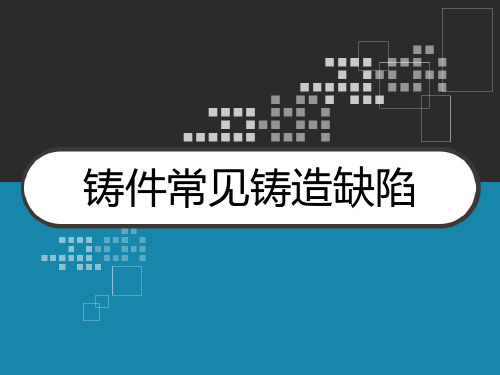
铸造常见缺陷特点
缺陷名称:黑皮(其二)
铸造常见缺陷特点
缺陷名称:气孔 缺陷特点:铸件内部或表面 有大小不同的孔眼,孔的内 壁光滑,多呈圆形。 产生原因:砂型太紧或型砂 透气性差;型砂太湿;砂芯 通气孔堵塞;浇注系统不正 确,气体排不出去
铸造常见缺陷特点
缺陷名称:缩孔(大而集中 的空洞 ) 缺陷特点:铸件厚、断面处 出现形状不规则的孔眼,孔 的内壁粗糙。 产生原因:冒口设置不正确 ;合金成分不合格,收缩过 大;浇注温度过高;铸件设 计不合理,无法进行补缩
铸造常见缺陷特点
缺陷名称:疏松(细小而分 散的空隙) 缺陷特点:铸件厚、断面处 出现形状不规则的孔眼,孔 的内壁粗糙。 产生原因:冒口设置不正确 ;合金成分不合格,收缩过 大;浇注温度过高;铸件设 计不合特点
缺陷名称:铸字不清 缺陷特点: 产生原因:型腔铸字部分起 模不畅,型砂粒度太粗
铸造常见缺陷特点
缺陷名称:披缝 缺陷特点:铸件表面在分模 面处的规则缩陷。 产生原因: 砂型或砂芯分模 面处的飞边未去除
铸造常见缺陷特点
缺陷名称:表面多肉 缺陷特点:铸件表面有多余 的部分。 产生原因:砂型或砂芯的相 应部分掉肉。
铸件常见铸造缺陷
铸造常见缺陷特点
缺陷名称:砂眼 缺陷特点:铸件内部或表面 有充满砂粒的孔眼,孔形不 规则 产生原因:型砂强度不够或 局部没舂紧,掉砂;型腔、 浇口内散砂未吹净;合箱时 砂型局部挤坏,掉砂;浇注 系统不合理,冲坏砂型
铸造常见缺陷特点
缺陷名称:砂眼(其二)
铸造常见缺陷特点
缺陷名称:砂眼(加工后)
铸造常见缺陷特点
缺陷名称:表面多肉肉(其 二)
铸造常见缺陷特点
缺陷名称:缺肉(缺料) 缺陷特点:铸件表面有缺少 一块,可能导致报废。 产生原因:浇冒口切除时带 掉一块;
(图文)压铸缺陷学习培训资料
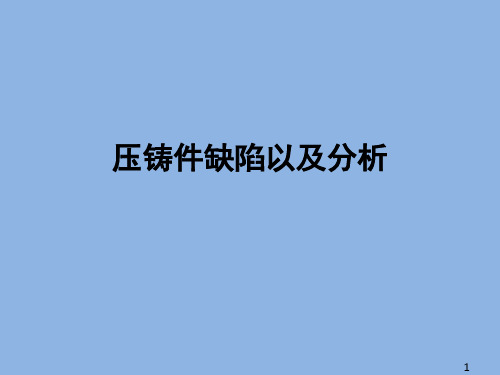
泄漏
• 压铸件经试验产生漏水、漏气或渗水 • 产生原因:
1. 压力不足。 2. 浇注系统设计不合理或铸件结构不合理。 3. 合金选择不当。 4. 排气不良。
• 改善措施:
1. 提高比压。 2. 改进浇注系统和排气系统。 3. 选用良好合金。 4. 尽量避免加工。 5. 铸件进行浸渗处理
皮下气泡
• 特征:铸件表皮下,聚集气体鼓胀所形成的泡。 • 产生原因:
2, 澆口位置不正確,流路太長,內澆口速度太低
• 改善措施:
1,改善澆口位置,调整流路以确保两股金属流能在冷却前结合。 2,提供内澆口速度。
表面缺陷
• 起皮 • 铸件表面具有很难观测到夹层和冷隔的结构,或者经过高压清洗后,表面有崩落的现
象 • 产生原因:
1. 模具温度过低,脱模剂喷涂过多, 2. 内浇口设计过小,模具装配间隙过小 3. 壓射比壓不足,填充时间过长,快压射位置过于靠后
1. 模具温度太高。 2. 填充速度太高,金属液流卷入气体过多。 3. 涂料发气量大,用量过多,浇注前未燃尽,使挥发气体被包在铸件表层。 4. 排气不畅。 5. 开模过早。 6. 合金熔炼温度过高。
• 改善措施:
1. 冷却模具至工作温度。 2. 降低压射速度,避免涡流包气。 3. 选用发气量小的涂料,用量薄而均匀,燃尽后合模。 4. 清理和增设溢流槽和排气道。 5. 调整留模时间。 6. 修整熔炼工艺。
表面收缩
• 铸件平滑表面上出现凹瘪的部分,其表面呈自然冷却状态。 • 产生原因:
1. 铸件结构设计不合理,有局部厚实部位,产生热节。 2. 合金收缩率大。 3. 内浇口截面积太小。 4. 比压低。 5. 模具温度太高
• 改善措施:
1. 改善铸件结构,使壁厚稍为均匀,厚薄相差较大的连接处应逐步缓和过渡, 消除热节。
铸造缺陷鉴别 PPT

残缺类
浇不到 5-1
未浇满 夹杂类 5-2 跑火 5-3 损伤 5-4
金属夹杂物
6-1 冷豆
6-2 内渗豆
6-3 ( 夹渣)
6-4 ( 砂眼)
6-5
铸造缺陷名称及分类(7)
性能、成分、组织不合格 7-1、物理性能不合 7-2、机械性能不合格 7-3、化学成分不合格 7-4、石墨漂浮 7-5、石墨粗大
➢ ➢
➢孔眼类
➢ ➢ ➢
1-1 气孔 1-2 缩孔 (缩松) 1-3 砂眼 多肉类
(渣眼)
1-4 铁豆
2-1批缝 (飞边)
2-2抬型 (抬箱 )
2-3 涨箱 2-4冲砂 2-5掉砂 2-6外渗豆
裂纹 冷隔类
3-1冷裂
3-2热裂 3-3冷隔
表面 缺陷类
3-4热处理裂纹
4-1鼠尾 4-2 沟槽 4-3夹砂 4-4机械粘砂 4-5化学粘砂 4-6表面粗糙 4-7皱皮 4-8缩陷
冲 砂
5、掉砂:铸 件表面上的 块状金属凸 起物,其外 形与掉砂的 砂块相似。 在铸件的其 它部位则往 往出现砂眼 或残缺。
1、冷裂往 往是穿过晶 体而不是沿 晶界断裂, 断口具有金 属光泽或呈 轻微氧化色 泽,通常为 浅褐色。
2、热裂: 热裂断口常 有严重氧化 的黑色表面, 断口沿晶粒 边界产生和 发展,所以 裂口外形曲 折而不规则, 外裂表面宽 而内部窄。
面都可能存在。
②、孔眼的大小不等,这三种孔眼缺陷都没有 固定的大小模式,在铸件中可大可小。
③、孔眼的数量不等,在铸件中产生的这三中 缺陷,数量不等, 可多可少,可成片聚积,也 可单独存在。
④、孔眼可是封闭或敞露的孔洞。
1、1 批缝:是铸件上 厚薄不均匀的薄片状 金属凸起物,长出现 在铸件分型面和芯头 部位
铸造缺陷

三、案例(开裂);
2、检验与鉴别:
1、铸件内部裂纹可采用超声波探伤(UT)、 磁粉探伤(MT)或射线探伤法(RT)进行检验; 2、铸件表面的裂纹可采用染色探伤法(PT)来 帮助确定,大部份是肉眼可直接发现的。
三、案例(开裂);
3、形成原因:
1、铸件结构或浇注系统设计不合理壁厚相差悬殊, 过渡圆角小; 2、铸造合金中有害元素(P、S等)超标,珠光体 元素过量; 3、铸件开箱过早,冷却过快; 4、合金收缩率大; 5、肋板设计不合理。
1、定义和特征: 铸件内部或表面包裹 有砂粒、砂块的缺陷。
三、案例(夹砂);
2、检验与鉴别:
1、铸件内部夹砂可采用超声波探伤(UT) 或射线探伤法(RT)进行检验; 2、铸件表面的夹砂用肉眼可确定。
三、案例(夹砂);
3、形成原因:
1、型内残砂合模前未清理干净; 2、合模后浇注系统或冒口掉入砂粒或砂块; 3、造型、下砂芯、合模时操作不当发生砂模和砂芯 损坏落砂; 4、浇注系统不合理及浇注时操作不当,发生冲砂; 5、涂料不良,浇注时涂层脱落; 6、产品结构设计不合理。
7、夹杂类缺陷
定义
缺陷名称
特征
冷豆 通常位于铸件下表面或嵌入铸件表层;
铸件中各种 金属和非金 属夹杂物的 总称
内渗物 存在于铸件孔洞类缺陷内的光滑有光 (内渗豆) 泽的豆粒状金属渗出物;
夹渣
铸件表面或内部由熔渣引起的非金属 夹杂物;
夹砂
铸件内部或表面包裹有砂粒、砂块的 缺陷;
8、性能、成份、组织不合格类缺陷
存在于铸件内的严重的空壳状残缺;
铸件受撞击而破损、断裂、残缺不全;
6、形状及重量差错类缺陷
定义
缺陷名称
特征
铸件常见铸造缺陷

缺陷名称:砂眼 (其二)
铸造常见缺陷特点
缺陷名称:砂眼 (加工后)
铸造常见缺陷特点
缺陷名称:铸字 不清 缺陷特点: 产生原因:型腔 铸字部分起模不 畅,型砂粒度太 粗
铸造常见缺陷特点
缺陷名称:披缝 缺陷特点:铸件表 面在分模面处的规 则缩陷。 产生原因: 砂型 或砂芯分模面处的 飞边未去除
铸造常见缺陷特点
缺陷名称:表面多 肉 缺陷特点:铸件表 面有多余的部分。 产生原因:砂型或 砂芯的相应部分掉 肉。
铸造常见缺陷特点
缺陷名称:表面多 肉肉(其二)
铸造常见缺陷特点
缺陷名称:缺肉 (缺料) 缺陷特点:铸件表 面有缺少一块,可 能导致报废。 产生原因:浇冒口 切除时带掉一块;
铸造常见缺陷特点
缺陷名称:表面缩 凹 缺陷特点:铸件表 面有缩凹。 产生原因:铸件内 部收缩
缺陷名称:缩孔
铸造常见缺陷特(大点而集中的空 洞) 缺陷特点:铸件厚、 断面处出现形状不 规则的孔眼,孔的 内壁粗糙。
产生原因:冒口设 置不正确
;合金成分不合格, 收缩过大;浇注温 度过高;铸件设计 不合理,无法进行 补缩
铸造常见缺陷特缺陷点名称:疏松 (细小而分散的空 隙)
缺陷特点:铸件厚、 断面处出现形状不 规则的孔眼,孔的 内壁粗糙。
铸铁常见缺陷认识
SATA (KUNSHAN) Q 部
2011 May
缺陷名称:砂眼
铸造常见缺陷特缺陷点特点:铸件 内部或表面有充 满砂粒的孔眼, 孔形不规则 产生原因:型砂 强度不够或局部 没舂紧,掉砂; 型腔、浇口内散 砂未吹净;合箱 时砂型局部挤坏, 掉砂;浇注系统
;合金成分不合格, 收缩过大;浇注温 度过高;铸件设计 不合理
铸造常见缺陷特点
铸造常见缺陷特点
缺陷名称:砂眼 (加工后)
铸造常见缺陷特点
缺陷名称:铸字 不清 缺陷特点: 产生原因:型腔 铸字部分起模不 畅,型砂粒度太 粗
铸造常见缺陷特点
缺陷名称:披缝 缺陷特点:铸件表 面在分模面处的规 则缩陷。 产生原因: 砂型 或砂芯分模面处的 飞边未去除
铸造常见缺陷特点
缺陷名称:表面多 肉 缺陷特点:铸件表 面有多余的部分。 产生原因:砂型或 砂芯的相应部分掉 肉。
铸造常见缺陷特点
缺陷名称:表面多 肉肉(其二)
铸造常见缺陷特点
缺陷名称:缺肉 (缺料) 缺陷特点:铸件表 面有缺少一块,可 能导致报废。 产生原因:浇冒口 切除时带掉一块;
铸造常见缺陷特点
缺陷名称:表面缩 凹 缺陷特点:铸件表 面有缩凹。 产生原因:铸件内 部收缩
缺陷名称:缩孔
铸造常见缺陷特(大点而集中的空 洞) 缺陷特点:铸件厚、 断面处出现形状不 规则的孔眼,孔的 内壁粗糙。
产生原因:冒口设 置不正确
;合金成分不合格, 收缩过大;浇注温 度过高;铸件设计 不合理,无法进行 补缩
铸造常见缺陷特缺陷点名称:疏松 (细小而分散的空 隙)
缺陷特点:铸件厚、 断面处出现形状不 规则的孔眼,孔的 内壁粗糙。
铸铁常见缺陷认识
SATA (KUNSHAN) Q 部
2011 May
缺陷名称:砂眼
铸造常见缺陷特缺陷点特点:铸件 内部或表面有充 满砂粒的孔眼, 孔形不规则 产生原因:型砂 强度不够或局部 没舂紧,掉砂; 型腔、浇口内散 砂未吹净;合箱 时砂型局部挤坏, 掉砂;浇注系统
;合金成分不合格, 收缩过大;浇注温 度过高;铸件设计 不合理
铸造常见缺陷特点
铸造缺陷

3)抬箱:铸件在分型面处存在着极为严重的飞边,即 有厚片状的、表面光滑的、周边不规则的金属凸出物,其厚 度有时与铸件所增加的高度相等,这种缺陷称为抬箱。
抬箱缺陷产生的原因是:砂型的压铁重量太轻;或上、 下型夹紧不当,液态金属静压力过高等。
4)跑火:又称型漏,“火”代表金属液,是指金属液 充型 超过分型面进入上砂型后,分型面处,由于种种原因有泄漏 口使金属液决口流出型外。
二次渣滓,是指金属液在浇包内挡住或除去一次渣滓 后,进行浇注直至充型过程中,由于金属液的二次氧化或其 它各种原因而形成的渣滓。
图10-12为球铁曲轴在上型中的上表面产生的夹渣,这
种夹渣声称为“黑渣”。黑渣由多种氧化物组成(MgO、 FeO、Al2O3、SiO2稀土氧化物),是一种二次渣滓的夹 渣缺陷,实际上是氧化膜的夹杂类缺陷。
有色金属铸件中,常出现金属夹杂物缺陷。主要防止措 施是:保证金属炉料的纯净度,防止混入外来金属。
2)夹渣:是指铸件内部或表面有外来的非金属夹杂 物,统称为“渣滓”。
夹渣的目视特征是:形状极不规则的孔穴内,包容着渣 滓。
按形成时间的先后,有一次渣滓和二次渣滓两类:
一次渣滓,是指合金冶炼或熔炼时的冶金熔渣(氧化渣、 还原渣、酸性渣、碱性渣等)或熔剂所形成渣滓;或金属 液同炉衬、包衬相互作用生产的渣滓;或金属液炉前处理 (孕育或变质等)生成的渣滓。
3)解释“膨胀缺陷”的“膨胀-应力理论”认 为:膨胀缺陷经过三个阶段。即:
a.砂型表面受热迅速膨胀,
b.砂型表层脱离砂型本体而凸起,
c.砂型表层(干砂层)破裂、金属侵入而造成夹 砂。
夹砂产生倾向 = 铸型表层膨胀力/高湿度弱砂带 强度。
高湿度弱砂带的热湿拉强度越低,产生夹砂的 倾向越大。
第一章 铸造缺陷
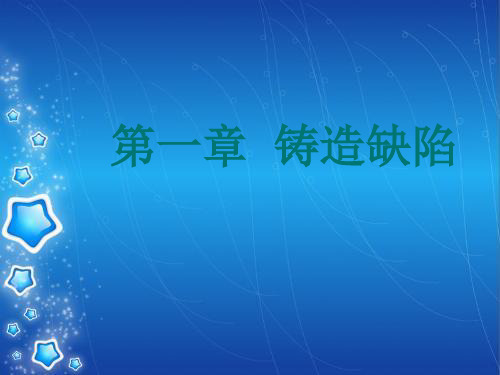
缺陷见于各种黑色金属和铜合金砂型铸件。
缺 陷 成 因 1.上型面夹砂结疤
(1)型壁形成以低强
剖 视
度的水分凝结层,接着
图
形成一层干砂层,其膨
胀受到两侧型壁阻碍,
使之受压而拱起。当液
态金属上升接触砂层时,
俯
液态金属的压力将拱起
视 图
的沙层顶回,使砂层破
裂。于是,液态金属进
入砂层背后的空间,形
成一薄层金属凸起,构
淬 裂 的 铝 合 金 铸 件
消除缺陷的措施:改用冷却速度低的淬火液,如用 热水或油。检查淬火温度,也可改进铸件的设计。
4、白点 (发裂)
钢中主要因氢的析出而引起的缺陷。在纵向 断面上, 它呈现近似圆形或椭圆形的银白色 斑点, 故称白点; 在横断面宏观磨片上, 腐蚀后则呈现为毛细裂纹, 故又称发裂
消除缺陷的措施:延长金属型的生产周期和加大金属型 的型壁斜度毅力铸件出型。操作者应认真工作,勿使铸件过 早出型。铸件的出型方向应与分型面垂直。
2、应力热裂
形状不规则,深浅不一的晶间裂纹。裂口常呈现细密 的树枝状结晶,且表面氧化。
这类缺陷最常发生在铸件上存在着内应力的最后凝固 的断面处(如厚、薄断面的交接处、内角处等)。
晶、偏析、球化不良,石墨粗大等。
第一节 多肉类缺陷
1、飞翅 (飞边)
定义:垂直于铸件表面上厚薄不均匀薄片状金属突起 物, 常产生在铸件分型面和芯头处以及铸型中任何 两个部分的交合面上。
灰铸铁 湿型
由于砂芯与芯座 之间的缝隙过大、砂 芯尺寸太小、或下芯 前砂芯磨削太多而造 成的毛刺。右上方是 夹砂结疤。
缺陷成因:
1.基本机理:合金在凝固过程中,当其温度接近固相线时受到 应力或变形的作用。
缺 陷 成 因 1.上型面夹砂结疤
(1)型壁形成以低强
剖 视
度的水分凝结层,接着
图
形成一层干砂层,其膨
胀受到两侧型壁阻碍,
使之受压而拱起。当液
态金属上升接触砂层时,
俯
液态金属的压力将拱起
视 图
的沙层顶回,使砂层破
裂。于是,液态金属进
入砂层背后的空间,形
成一薄层金属凸起,构
淬 裂 的 铝 合 金 铸 件
消除缺陷的措施:改用冷却速度低的淬火液,如用 热水或油。检查淬火温度,也可改进铸件的设计。
4、白点 (发裂)
钢中主要因氢的析出而引起的缺陷。在纵向 断面上, 它呈现近似圆形或椭圆形的银白色 斑点, 故称白点; 在横断面宏观磨片上, 腐蚀后则呈现为毛细裂纹, 故又称发裂
消除缺陷的措施:延长金属型的生产周期和加大金属型 的型壁斜度毅力铸件出型。操作者应认真工作,勿使铸件过 早出型。铸件的出型方向应与分型面垂直。
2、应力热裂
形状不规则,深浅不一的晶间裂纹。裂口常呈现细密 的树枝状结晶,且表面氧化。
这类缺陷最常发生在铸件上存在着内应力的最后凝固 的断面处(如厚、薄断面的交接处、内角处等)。
晶、偏析、球化不良,石墨粗大等。
第一节 多肉类缺陷
1、飞翅 (飞边)
定义:垂直于铸件表面上厚薄不均匀薄片状金属突起 物, 常产生在铸件分型面和芯头处以及铸型中任何 两个部分的交合面上。
灰铸铁 湿型
由于砂芯与芯座 之间的缝隙过大、砂 芯尺寸太小、或下芯 前砂芯磨削太多而造 成的毛刺。右上方是 夹砂结疤。
缺陷成因:
1.基本机理:合金在凝固过程中,当其温度接近固相线时受到 应力或变形的作用。
铸造缺陷及其对策 PPT课件
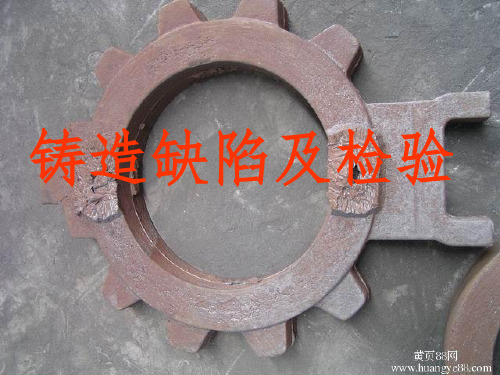
2、检验与鉴别:
1、铸件内部缩孔可采用超声波探伤(UT)、射线探 伤(RT)或加工后用染色探伤法(PT)进行检验; 2、铸件表面的缩孔用肉眼可观察到。
3、形成原因:
1、合金的液态收缩和凝固收缩大于固态收缩,凝 固时间过长; 2、浇注温度不当,过高易产生缩孔,过低易产生 缩松和疏松; 3、浇注系统、冒口、冷铁设置不合理,铸件凝固 时得不到有效补缩; 4、铸件结构不合理; 5、砂箱、芯骨钢度差,型、芯紧实度和强度低而 不均,铸件易产生胀型、缩孔、缩松; 6、原材料的遗传性。
铸造缺陷及检验
一、概念;
1、铸造缺陷是铸造生产过程中,由于种种原因, 在铸件表面和内部产生的各种缺陷的总称。 2、铸件缺陷是导致铸件性能低下、使用寿命短、 报废和失效的重要原因。 3、分析铸件缺陷的形貌、特点、产生原因及其形 成过程,目的是防止、减少和消除铸件缺陷。消除 或减少铸件缺陷是铸件质量控制的重要组成部份。
缺料(缺损) 铸件受撞击而破损、断裂、残缺不全;
5、形状及重量差错类缺陷
定义
缺陷名称
特征
尺寸不符 铸件实测尺寸不符合图面要求,超出公差;
重量不符 重量超出规定公差范围;
由于模样、铸型形状发生变化,或在铸造或热处
变形 理过程中因冷却或收缩不均等原因而引起的铸件
铸件的形状、
几何形状和尺寸与图面不符;
理后铁液停留、浇注、凝固时间过长而引起的铸铁石墨 球化率低或不球化缺陷;
三、案例
1.缩孔
缩孔
1、定义和特征:
1、铸件在凝固过程中因补缩不良而在热节或最后凝固部位形 成的宏观孔洞;
2、缩孔形状不规则,孔壁粗糙,常伴有粗大树枝晶夹杂物、气孔、 裂纹、偏析等缺陷;
3、缩孔上方或附近的铸件表面有时会出现凹陷(缩陷)。
1、铸件内部缩孔可采用超声波探伤(UT)、射线探 伤(RT)或加工后用染色探伤法(PT)进行检验; 2、铸件表面的缩孔用肉眼可观察到。
3、形成原因:
1、合金的液态收缩和凝固收缩大于固态收缩,凝 固时间过长; 2、浇注温度不当,过高易产生缩孔,过低易产生 缩松和疏松; 3、浇注系统、冒口、冷铁设置不合理,铸件凝固 时得不到有效补缩; 4、铸件结构不合理; 5、砂箱、芯骨钢度差,型、芯紧实度和强度低而 不均,铸件易产生胀型、缩孔、缩松; 6、原材料的遗传性。
铸造缺陷及检验
一、概念;
1、铸造缺陷是铸造生产过程中,由于种种原因, 在铸件表面和内部产生的各种缺陷的总称。 2、铸件缺陷是导致铸件性能低下、使用寿命短、 报废和失效的重要原因。 3、分析铸件缺陷的形貌、特点、产生原因及其形 成过程,目的是防止、减少和消除铸件缺陷。消除 或减少铸件缺陷是铸件质量控制的重要组成部份。
缺料(缺损) 铸件受撞击而破损、断裂、残缺不全;
5、形状及重量差错类缺陷
定义
缺陷名称
特征
尺寸不符 铸件实测尺寸不符合图面要求,超出公差;
重量不符 重量超出规定公差范围;
由于模样、铸型形状发生变化,或在铸造或热处
变形 理过程中因冷却或收缩不均等原因而引起的铸件
铸件的形状、
几何形状和尺寸与图面不符;
理后铁液停留、浇注、凝固时间过长而引起的铸铁石墨 球化率低或不球化缺陷;
三、案例
1.缩孔
缩孔
1、定义和特征:
1、铸件在凝固过程中因补缩不良而在热节或最后凝固部位形 成的宏观孔洞;
2、缩孔形状不规则,孔壁粗糙,常伴有粗大树枝晶夹杂物、气孔、 裂纹、偏析等缺陷;
3、缩孔上方或附近的铸件表面有时会出现凹陷(缩陷)。
铸造缺陷

iii.不充满式浇注系统而裹入气泡
表4-2 裹携气孔形成原因和防治措施图示3 充满式浇注系统(直浇道为上大下小的倒锥 形),比不充满式浇注系统(圆柱形)有利于克服裹 入气泡。
3) 析出气孔
①.定义:以原子态溶解于金属液中的氢、氮气体元素, 金属液凝固时它们以分子态气相析出,形成气泡而使铸件产 生的气孔,称为析出气孔。由于氢析出而形成的析出气孔, 称为氢气孔;由于氮析出而形成的析出气孔,称为氮气孔。
V.分布:大多数情况下,是单个或几个聚集的,尺寸较 大的气孔。有时成为局部聚集的蜂窝状气孔(如图4-10 示),很少成为弥散性气孔或针孔。
③.形成机理
分三个阶段形成:第一阶段,气体侵入金属液;第二阶 段,型壁上气泡形成;第三阶段,气泡在型腔金属液中的滞 留或排出。
侵入性气孔形成的条件是:
pA>(p0+pm+pz) pA――“金属-铸型”界面上气泡所在处的压力; p0――型腔中的气体压力,一般为标准大气压力; pm――金属液静压力,pm=ρ•g•h; pz――金属液的表面阻力。
(3)位置:气孔可分布在铸件的任何位置。可分为: 内部气孔、皮下气孔、表面气孔。
内部气孔存在于铸件的内部,目视检查无法发现;如图 4-10所示。
皮下气孔成串横列于铸件表面以下1~3mm,一般为圆球 形、团球形、泪滴形或长针形;如图4-3、图4-4所示。
表面气孔存在于铸件毛坯表面,落砂清理后可以发现, 如图4-6所示。
形成该气孔的气体来自外部气体源,所以侵入气孔是一 种外生式气孔。
②.目视特征
i.形状――圆球形、团球 形的异形孔洞;有时是梨形 气孔,如图4-11示。
ii.孔壁表面面貌:孔壁平 滑。
iii.尺寸大小:尺寸通常较 大,最大尺寸达几毫米以上。
铸造缺陷气孔与缩孔ppt课件

易吸气的合金时,合金液 在铸型内合理设施排气塞和溢流
大量吸气,造成铸件成批 槽,必要时可采用真空吸铸、真
报废。
空压铸、吹氧压铸和在惰性气体
8、树脂砂的树脂和固化 保护下浇注等方法防止铸件产生
剂加入量过多,树脂含氟 气孔。
量过高,原砂和再生砂的 6、熔模铸造、消失模铸造、壳型
角形系数过高、粒度过 铸造等可与真空吸铸相结合,以
1、气孔超出验收标 准时应报废 2、单独的大气孔可 进行焊补 3、成群分散的小气 孔可采取侵渗处理 方法进行填补,质 量要求高的铸件可 采用热等静压处理 法消除气孔
面反应,形成表面针孔与
皮下气孔
2
(1)卷入气孔:金属液在 充型过程中因卷入气体而 在铸件内形成气孔,多呈 孤立存在的圆形或椭圆形 大气孔,位置不固定,一 般偏铸件中上部 (2)侵入气孔:由型、芯 、涂料、芯撑、冷铁产生 的气孔侵入铸件表层而形 成气孔,多呈梨形或椭圆 形,尺寸较大,孔壁光 滑,表面多呈氧化色 (3)反应气孔:由金属液 内部某些成分之间或金属 液与型、芯在界面上发生 化学反应而形成群分布的 气孔。位于铸件表层的针 头形或腰圆形反应气孔称 为表面针空与皮下气孔, 由金属液与型、芯涂料发 生界面反应所至;分散或 成群分布在铸件整个断面 上或某个局部区域的针头 反应气孔通常称为针孔, 由金属液内某些成分之间 发生化学反应所引起,位 于铸件上部的反应气孔常 拌有夹渣 (4)析出气孔:溶解在金 属液中的气体在铸件成型 过程中析出而形成的气孔 呈细圆形、椭圆形或针头 形,成群分布在铸件整个 断面上或某个局部区域 内,空壁光亮,铝合金铸 件析出的气孔通常称为针 孔,在热节与厚截面处较 严重
2、缩孔、缩松 、疏松(显微缩
松)
(1)、缩孔:铸件在凝 固过程中因补缩不良而在 热节或最后凝固部位形成 的宏观孔洞,缩孔形状不 规则,孔壁粗糙,常伴有 粗大树枝品、夹杂物、气 孔、裂纹、偏析等缺陷, 缩孔上方或附近的铸件表 面有时会出现凹陷,缩孔 按分布特征可分为集中缩
铸件常见缺陷及分析方法PPT课件

3. 黏砂与夹砂 (1)黏砂 铸件表面或内腔黏附着一层难以清除的砂粒称为黏砂。根据砂粒与铸件连 接情况的不同,一般分为机械黏砂和化学黏砂。
1)机械黏砂 影响机械黏砂的主要因素如下: ① 砂型表面孔隙的大小。 ② 金属液的静压力对机械黏砂影响较大。 ③ 浇注温度越高,则金属液在铸型表面保持液态的时间就越长。 ④ 铸型表面材料的导热性能大小,影响铸件的黏砂程度。
2) 侵入性气孔缺陷的预防措施 ① 降低铸型和型芯的发气量。 ② 增加铸型(芯)的透气性。 ③ 采用合理的浇注工艺。 ④ 采用合理的浇注系统。 2. 缩孔与缩松 液态金属注入型腔后,随着温度的下降,发生凝固,在此期间发生液态 收缩和凝固收缩。在铸件最后凝固的部位,往往会出现由于补缩不良而产生 的孔洞,称为缩孔。
(2)反应性气孔 金属液与铸型(芯)或在金属液内部某些成分之间,因 发生化学反应产生的气体来不及排出所产生的气孔,称 为反应性气孔。 反应性气孔一般都位于铸件表面以下,呈分散分布的 小孔。其又分为金属液与铸型间反应性气孔和金属液内 部反应性气孔,反应性气孔类型、特征、产生原因及预 防方法等见表11-8。
(3)侵入性气孔 气体从金属液外部侵入金属液后造成的气孔称为侵入 性气孔。 侵入性气孔的特征是: 气孔出现在铸件的个别地方, 数量较少、体积(尺寸)较大、孔壁光滑、表面有光泽或 轻微的氧化色。形状多成椭圆形,一般位于铸件浇注位 置的中上部或上部。
1)造成侵入性气孔的因素 ① 浇注时,气体由浇注系统、型腔混入金属液, 导致气孔的产生。 ② 金属液和冷铁、芯撑相互作用而产生气体。 ③ 砂型或砂芯中的水分或附加物(黏结剂),在金 属液的热作用下气化、分解或燃烧产生的气体,侵入 金属液形成气孔。
(2)砂眼 砂眼是指铸件内部或表面带有砂粒的孔洞。多产度太低,或造型、合型等工序不够细致所 造成的,具体表现如下:
铸造缺陷解析课件

铸件由于化学 成分不符合铸 件技术条件的 要求,或由于 熔炼、金属液 处理、铸造、 热处理工艺不 当,导致显微 组织异常,物 理性能或力学 性能不合格
硬点
白口 反白口 球化不良 和球化衰
在第二相为石墨的铸件断口的中心部位出现白口 组织或麻口组织,外层是正常的石墨组织;
因球化剂加入量不足以使铸铁石墨充分球化,或 球化处理后铁液停留、浇注、凝固时间过长而引
三、案例(缩孔);
2、检验与鉴别: 1、铸件内部缩孔可采用超声波探伤(UT)、射线探 伤(RT)或加工后用染色探伤法(PT)进行检验; 2、铸件表面的缩孔用肉眼可观察到。
三、案例(缩孔);
3、形成原因:
1、合金的液态收缩和凝固收缩大于固态收缩,凝 固时间过长; 2、浇注温度不当,过高易产生缩孔,过低易产生 缩松和疏松; 3、浇注系统、冒口、冷铁设置不合理,铸件凝固 时得不到有效补缩; 4、铸件结构不合理; 5、砂箱、芯骨钢度差,型、芯紧实度和强度低而 不均,铸件易产生胀型、缩孔、缩松; 6、原材料的遗传性。
5、残缺类缺陷
定义 缺陷名称 浇不到 特征
铸件残缺,轮廓不完整,或轮廓虽 完整,但边、棱、角圆钝;
铸件上部残缺,残缺部份边角呈 铸件由于 未浇满 圆形,浇注糸统未充满; 各种原因 铸件分型面以上部份残缺,残缺 造成的外 跑水 表面凹陷; 形缺损缺 陷的总称 型漏(漏 存在于铸件内的严重的空壳状残 箱) 缺; 缺料(缺 铸件受撞击而破损、断裂、残缺 损) 不全;
疏松(显微 不作严格区分; 缩松)
3、裂纹、冷隔类缺陷
定义 宏观(肉眼、P T、RT、MT 、UT)或微观 (显微镜)判断 发现有开裂状纹 络 缺陷名称 冷裂 热裂 特征 断口有金属光泽或有轻微 氧化色泽; 断口严重氧化,无金属光 泽;
铸造与熔炼相关的主要缺陷PPT课件

裂纹案例分析
总结词
裂纹是铸造和熔炼过程中常见的一种缺陷, 它通常是由于金属液冷却过程中产生的收缩 应力超过了材料的强度极限而形成的。
详细描述
裂纹的形成与多种因素有关,如金属液的收 缩率、铸件的结构设计、浇注温度和浇注速 度等。如果金属液的收缩率过大,或者铸件 结构设计不合理,就可能导致裂纹的形成。 裂纹的存在会对铸件的性能产生严重影响,
谢谢观看
夹渣产生原因及防止措施
夹渣产生原因
01
02
金属液中存在杂质或氧化物,未及时清除。
浇注时金属液与模具接触面形成“薄膜”, 导致杂质或氧化物夹带在铸件中。
03
04
防止措施
控制金属液中的杂质和氧化物含量,及时 清除。
05
06
浇注时保持金属液与模具接触面的清洁, 避免形成“薄膜”。
裂纹产生原因及防止措施
熔炼的定义与特点
定义
熔炼是一种将金属加热至熔化状态,去除杂质和气泡,然后倒入模具中形成所需 形状的工艺。
特点
熔炼可以获得纯净的金属材料,具有较高的力学性能和耐腐蚀性能。熔炼过程中 ,高温熔融状态下的金属容易发生氧化和吸气,可能导致零件出现气孔、夹渣等 缺陷。
铸造与熔炼的关系
• 关系:铸造和熔炼都是金属加工工艺,二者在生产过程中存在 一定的联系和区别。熔炼是铸造的原材料制备过程,铸造则是 熔炼的后续加工过程。通过合理的工艺控制和材料选择,可以 降低缺陷的产生,提高零件的质量和性能。
缩孔案例分析
总结词
缩孔是铸造和熔炼过程中常见的一种缺陷,它通常是由 于金属液在冷却过程中产生的收缩未能得到有效的补充 而形成的。
详细描述
缩孔的形成与多种因素有关,如金属液的收缩率、铸件 的结构设计、浇注温度和浇注速度等。如果金属液的收 缩率过大,或者铸件结构设计不合理,就可能导致缩孔 的形成。缩孔的存在会对铸件的性能产生严重影响,如 降低强度、增加脆性等。