2.1.5 车床
普通车床和铣床基本知识

编辑本段普通车床操作规程
1 .开车前的检查 1.1 根据机床润滑图表加注合适的润滑油脂。
1.2 检查各部电气设施,手柄、传动部位、防护、限位装置齐全可靠、灵 活。
1.3 各档应在零位,皮带松紧应符合要求。 1.4 床面不准直接存放金属物件,以免损坏床面。 1.5 被加工的工件、无泥砂、防止泥砂掉入拖板内、磨坏导轨。 1.6 未夹工件前必须进行空车试运转,确认一切正常后,方能装上工件。 2 .操作程序 2.1 上好工件,先起动润滑油泵,使油压达到机床的规定,方可开动。 2.2 调整交换齿轮架,调挂轮时,必须切断电源,调好后,所有螺栓必须 紧固,扳手应及时取下,并脱开工件试运转。 2.3 装卸工件后,应立即取下卡盘扳手和工件的浮动物件。 2.4 机床的尾架、摇柄等按加工需要调整到适当位置,并紧固或夹紧。 2.5 工件、刀具、夹具必须装卡牢固。浮动力具必须将引刀部分伸入工件, 方可启动机床。 2.6 使用中心架或跟刀架时,必须调好中心,并有良好的润滑和支承接触 面。 2.7 加工长料时,主轴后面伸出的部份不宜过长,若过长应装上托料架, 并挂危险标记。 2.8 进刀时,刀要缓慢接近工作,避免碰击;拖板来回的速度要均匀。换 刀时,刀具与工件必须保持适当距离。 2.9 切削车刀必须紧固,车刀伸出长度一般不超过刀厚度的 2.5 倍。 2.1.0 加工偏心件时,必须有适当的配重,使卡盘重心平衡,车速要适当。 2.1.1. 盘卡超出机身以外的工件,必须有防护措施。 2.1.2 对刀调整必须缓慢,当刀光离工件加工部位 40-60 毫米时,应改 用手动或工作进给,不准快速进给直接吃刀。 2.1.3 用锉刀打光工件时,应将刀架退至安全位置,操作者应面向卡盘, 右手在前,左手在后。表面有键槽,方孔的工件禁止用锉刀加工。 2.1.4 用砂布打光工件外圆时,操作者按上条规定的姿势,两手拉着砂布 两头进行打光。禁止用手指夹持砂布打磨内孔。 2.1.5 自动走刀时,应将小刀架调到与底座平齐,以防底座碰到卡盘。 2.1.6 切断大、重工件或材料时,应留有足够的加工余量。 3 .停车操作 3.1 切断电源、卸下工件。 3.2 各部手柄打倒零位,清点工器具,打扫清洁。
(完整版)数控车床主轴设计

绪论随着市场上产品更新换代的加快和对零件精度提出更高的要求,传统机床已不能满足要求。
数控机床由于众多的优点已成为现代机床发展的主流方向。
它的发展代表了一个国家设计、制造的水平,在国内外都受到高度重视。
现代数控机床是信息集成和系统自动化的基础设备,它集高效率、高精度、高柔性于一身,具有加工精度高、生产效率高、自动化程度高、对加工对象的适应强等优点。
实现加工机床及生产过程的数控化,已经成为当今制造业的发展方向。
可以说,机械制造竞争的实质就是数控技术的竞争。
本课题的目的和意义在于通过设计中运用所学的基础课、技术基础课和专业课的理论知识,生产实习和实验等实践知识,达到巩固、加深和扩大所学知识的目的。
通过设计分析比较机床的某些典型机构,进行选择和改进,学习构造设计,进行设计、计算和编写技术文件,达到学习设计步骤和方法的目的。
通过设计学习查阅有关设计手册、设计标准和资料,达到积累设计知识和提高设计能力的目的。
通过设计获得设计工作的基本技能的训练,提高分析和解决工程技术问题的能力,并为进行一般机械的设计创造一定的条件。
一、设计题目及参数1.1 题目本设计的题目是数控车床的主轴组件的设计。
它主要由主轴箱,主轴,电动机,主轴脉冲发生器等组成。
我主要设计的是主轴部分。
主轴是加工中心的关键部位,其结构优劣对加工中心的性能有很大的影响,因此,在设计的过程中要多加注意。
主轴前后的受力不同,故要选用不同的轴承。
1.2参数床身回转空间400mm尾架顶尖与主轴端面距离1000mm主轴卡盘外径Φ200mm最大加工直径Φ600mm棒料作业能力50~63mm主轴前轴承内和110~130mm最大扭矩480N·m二、主轴的要求及结构2.1主轴的要求2.1.1旋转精度主轴的旋转精度是指装配后,在无载荷,低转速的条件下,主轴前端工件或刀具部位的径向跳动和轴向跳动。
主轴组件的旋转精度主要取决于各主要件,如主轴、轴承、箱体孔的的制造,装配和调整精度。
数控车床操作规程(3篇)

数控车床操作规程一、工作前准备1.携带并佩戴个人防护用品,包括安全眼镜、耳塞、手套等。
2.检查数控车床的各个部件是否正常,如电源、控制系统、主轴等。
3.检查工作区域是否整洁,确保没有杂物。
4.检查工件与夹具是否正确安装,夹具是否紧固。
5.根据工艺要求设置好数控车床的刀具,包括刀具的进给量、转速等参数。
二、开机操作1.打开数控车床的电源开关,并确保控制面板上的开关处于关机状态。
2.将电源和控制系统连接。
3.操作人员根据工艺要求启动数控车床,确保主轴的转速正常。
4.根据工艺要求调整刀具的切削深度,并开始数控车床的工作。
三、操作规程1.操作人员应保持警觉,注意观察数控车床的运行状态,确保安全。
2.操作人员应掌握数控编程操作,按照工艺要求进行编程。
3.操作人员应根据工件的形状和尺寸,选择合适的刀具,并调整刀具的位置和角度。
4.开始加工前,操作人员应检查刀具的质量和磨损情况,及时更换。
5.操作人员应根据工艺要求调整数控车床的进给速度和主轴转速。
6.操作人员应注意数控车床的润滑和冷却系统是否正常工作,及时调整。
四、加工操作1.操作人员应严格按照工艺要求,合理安排加工顺序。
2.操作人员应精确控制数控车床的进给量和主轴转速,确保加工质量。
3.操作人员应根据实际情况,合理调整刀具的进给速度和切削深度。
4.操作人员应根据工件的特点,灵活应用刀具的进给方式和切削方法。
5.加工过程中,操作人员应随时注意数控车床的运行状态,及时排除故障。
6.操作人员应合理利用数控车床的各项功能,提高加工效率。
五、加工结束1.加工结束后,操作人员应关闭数控车床的电源。
2.操作人员应对数控车床进行清洁和维护,保持其良好状态。
3.操作人员应将使用过的刀具归位,并及时更换需要修整的刀具。
4.操作人员应整理工作区域,清理杂物和废料。
5.操作人员应记录加工过程中的关键参数和故障情况,以便后期分析和改进。
六、安全注意事项1.操作人员应严格遵守安全操作规程,禁止违章操作。
数控车床的加工范围及特点
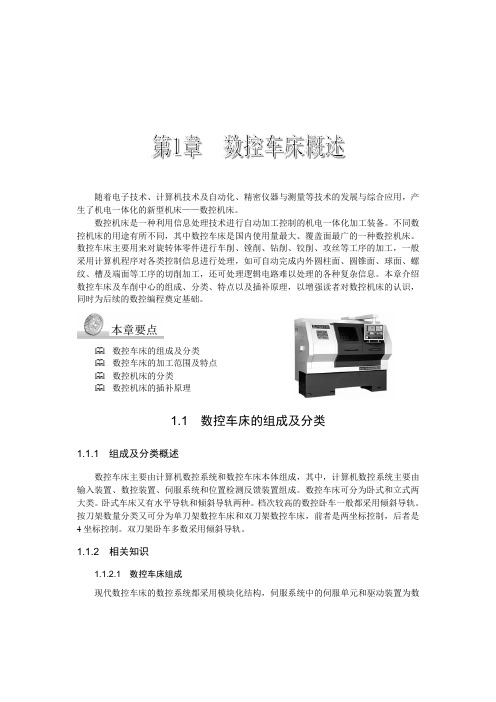
随着电子技术、计算机技术及自动化、精密仪器与测量等技术的发展与综合应用,产生了机电一体化的新型机床——数控机床。
数控机床是一种利用信息处理技术进行自动加工控制的机电一体化加工装备。
不同数控机床的用途有所不同,其中数控车床是国内使用量最大、覆盖面最广的一种数控机床。
数控车床主要用来对旋转体零件进行车削、镗削、钻削、铰削、攻丝等工序的加工,一般采用计算机程序对各类控制信息进行处理,如可自动完成内外圆柱面、圆锥面、球面、螺纹、槽及端面等工序的切削加工,还可处理逻辑电路难以处理的各种复杂信息。
本章介绍数控车床及车削中心的组成、分类、特点以及插补原理,以增强读者对数控机床的认识,同时为后续的数控编程奠定基础。
本章要点数控车床的组成及分类数控车床的加工范围及特点数控机床的分类数控机床的插补原理1.1 数控车床的组成及分类1.1.1 组成及分类概述数控车床主要由计算机数控系统和数控车床本体组成,其中,计算机数控系统主要由输入装置、数控装置、伺服系统和位置检测反馈装置组成。
数控车床可分为卧式和立式两大类。
卧式车床又有水平导轨和倾斜导轨两种。
档次较高的数控卧车一般都采用倾斜导轨。
按刀架数量分类又可分为单刀架数控车床和双刀架数控车床,前者是两坐标控制,后者是4坐标控制。
双刀架卧车多数采用倾斜导轨。
1.1.2 相关知识1.1.2.1 数控车床组成现代数控车床的数控系统都采用模块化结构,伺服系统中的伺服单元和驱动装置为数SIEMENS数控车床编程与实训2 控系统的一个子系统,输入/输出装置也为数控系统的一个功能模块,所以数控车床主要由计算机数控系统和数控车床本体组成,如图1-1所示。
输入/输出装置车床本体位置检测反馈装置图1-1 数控车床的组成1.输入装置数控车床是按照编程人员编制的程序运行的。
通常编程人员将程序以一定的格式或代码存储在一种载体上,如穿孔带或磁盘等,通过数控车床的输入装置输入到数控装置中。
此外,还可以使用数控系统中的RS232接口或DNC接口与计算机进行信号的高速传输。
广州数控-用户手册-GSK928TEa车床数控系统使用手册2.

在本使用手册中,我们将尽力叙述各种与该系统操作相关的事项。
限于篇幅限制及产品具体使用等原因,不可能对系统中所有不必做或不能做的操作进行详细的叙述。
因此,本使用手册中没有特别指明的事项均视为“不可能”或“不允许”进行的操作。
本使用手册的版权,归广州数控设备有限公司所有,任何单位与个人进行出版或复印均属于非法行为,广州数控设备有限公司将保留追究其法律责任的权利。
GSK928TEa 车床数控系统 使用手册II 前 言尊敬的客户:对您选用广州数控设备有限公司的产品,本公司深感荣幸并表示感谢! 本使用手册详细介绍了GSK928TEa 车床数控系统的编程、操作及安装连接事项。
为了保证产品安全、正常与有效地运行工作,请您务必在安装、使用产品前仔细阅读本使用手册。
在系统开始使用之前,请注意以下事项:● 连接好系统的急停按钮。
由于本系统的急停输入采用常闭触点,如不接好急停按钮或错接为常开触点,系统通电后会产生急停报警而不能正常工作(这不属于系统故障)。
● 根据刀具的实际安装位置设置好程序参考点,如不设置好参考点就使用回程序参考点功能,将可能发生意外!安 全 警 告操作不当将引起意外事故,必须要具有相应资格的人员才能操作本系统。
特别提示: 安装在机箱上(内)的系统电源,是仅为本公司制造的数控系统提供的专用电源。
禁止用户将这个电源作其他用途使用。
否则,将产生极大的危险!安全注意事项本手册内容如有变动,恕不另行通知。
IIIGSK928TEa 车床数控系统 使用手册IV安 全 事 项在本系统连接、使用之前,请务必仔细阅读安全说明。
用户必须遵守安全操作规程,以确保人身及设备安全。
用户操作时还必须遵守由本公司提供的使用手册中指明的相关安全规程,在完全熟悉本使用手册内容后,方可操作本系统。
用户还必须遵守由机床厂商随行提供的机床使用说明书中指明的与机床有关的安全操作规程。
用户必须在完全熟悉本使用手册以及由机床制造厂随行提供的机床使用说明书的内容后,才能操作机床或编制程序来控制机床。
车床毕业论文

摘要随着工业技术的不断发展,车床作为一种重要的金属切削机床,在机械制造行业中扮演着至关重要的角色。
本文旨在探讨车床的工作原理、结构特点、应用领域以及发展趋势,通过对车床的深入研究,为我国机械制造业的发展提供理论支持和实践指导。
关键词:车床;工作原理;结构特点;应用领域;发展趋势第一章引言1.1 研究背景随着我国经济的快速发展,机械制造业在国民经济中的地位日益重要。
车床作为一种常见的金属切削机床,其性能和精度直接影响着产品的质量和生产效率。
因此,对车床的研究具有重要的理论意义和实际应用价值。
1.2 研究目的本文通过对车床的工作原理、结构特点、应用领域以及发展趋势的研究,旨在提高我国车床制造技术水平,为机械制造业的发展提供有力支持。
第二章车床的工作原理2.1 车床的切削过程车床的切削过程主要包括切削、进给、切削力、切削温度和切削液等方面。
本文将对这些方面进行详细阐述。
2.2 车床的传动系统车床的传动系统主要由主轴、进给箱、变速箱、齿轮箱等组成。
本文将对这些部件的工作原理和作用进行介绍。
第三章车床的结构特点3.1 车床的总体结构车床的总体结构包括床身、主轴箱、进给箱、溜板箱、刀架、尾座等部分。
本文将对这些部分的功能和特点进行详细分析。
3.2 车床的控制系统车床的控制系统主要包括电气控制系统、液压控制系统和气动控制系统等。
本文将对这些控制系统的组成和作用进行介绍。
第四章车床的应用领域4.1 车床在机械制造中的应用车床在机械制造中具有广泛的应用,如汽车、航空、船舶、军工等行业。
本文将对车床在这些行业中的应用进行探讨。
4.2 车床在其他领域的应用除了在机械制造中的应用,车床还在航空航天、医疗器械、精密仪器等领域有着重要的应用。
本文将对这些领域的应用进行介绍。
第五章车床的发展趋势5.1 车床技术的发展方向随着科技的不断进步,车床技术也在不断发展。
本文将对车床技术的发展方向进行展望。
5.2 车床的智能化、自动化发展趋势智能化、自动化是车床发展的必然趋势。
数控车床的加工范围及特点

随着电子技术、计算机技术及自动化、精密仪器与测量等技术的发展与综合应用,产生了机电一体化的新型机床——数控机床。
数控机床是一种利用信息处理技术进行自动加工控制的机电一体化加工装备。
不同数控机床的用途有所不同,其中数控车床是国内使用量最大、覆盖面最广的一种数控机床。
数控车床主要用来对旋转体零件进行车削、镗削、钻削、铰削、攻丝等工序的加工,一般采用计算机程序对各类控制信息进行处理,如可自动完成内外圆柱面、圆锥面、球面、螺纹、槽及端面等工序的切削加工,还可处理逻辑电路难以处理的各种复杂信息。
本章介绍数控车床及车削中心的组成、分类、特点以及插补原理,以增强读者对数控机床的认识,同时为后续的数控编程奠定基础。
数控车床的组成及分类数控车床的加工范围及特点SIEMENS 数控车床编程与实训2 数控机床的分类数控机床的插补原理1.1 数控车床的组成及分类1.1.1 组成及分类概述数控车床主要由计算机数控系统和数控车床本体组成,其中,计算机数控系统主要由输入装置、数控装置、伺服系统和位置检测反馈装置组成。
数控车床可分为卧式和立式两大类。
卧式车床又有水平导轨和倾斜导轨两种。
档次较高的数控卧车一般都采用倾斜导轨。
按刀架数量分类又可分为单刀架数控车床和双刀架数控车床,前者是两坐标控制,后者是4坐标控制。
双刀架卧车多数采用倾斜导轨。
1.1.2 相关知识 1.1.2.1 数控车床组成现代数控车床的数控系统都采用模块化结构,伺服系统中的伺服单元和驱动装置为数控系统的一个子系统,输入/输出装置也为数控系统的一个功能模块,所以数控车床主要由计算机数控系统和数控车床本体组成,如图1-1所示。
输入/输出装置 车床本体位置检测反馈装置图1-1 数控车床的组成1.输入装置数控车床是按照编程人员编制的程序运行的。
通常编程人员将程序以一定的格式或代码存储在一种载体上,如穿孔带或磁盘等,通过数控车床的输入装置输入到数控装置中。
此外,还可以使用数控系统中的RS232接口或DNC 接口与计算机进行信号的高速传输。
车床的发展简史及发展类型

车床的发展简史及发展类型引言概述:车床是机械加工中常用的一种工具,它的发展历史可以追溯到古代。
随着科技的进步和工业的发展,车床也不断演变和改进,出现了多种类型的车床。
本文将从车床的起源开始,介绍车床的发展简史,并详细阐述现代车床的五个主要类型。
一、车床的起源和早期发展1.1 中国古代的车床中国古代的车床起源于战国时期,当时的车床主要用于木工和铁工的加工。
它们通常由木材制成,操作简单,适用于较小的工件加工。
1.2 古希腊和古罗马的车床古希腊和古罗马时期,车床的发展取得了一定的进步。
他们开始使用更复杂的机械结构,如滑板和导轨,使车床能够加工更大尺寸的工件。
1.3 工业革命对车床的影响工业革命时期,车床经历了巨大的改变。
发明了蒸汽机和电动机,使车床能够自动化操作。
此外,还出现了更高精度的车床,使得工件加工更加精确和高效。
二、现代车床的类型2.1 手动车床手动车床是最早出现的车床类型之一,操作者通过手动控制工件的加工过程。
它适用于简单的工件加工,但效率相对较低。
2.2 数控车床数控车床是现代车床的主流类型之一。
它通过计算机控制系统来自动控制工件的加工过程,具有高精度、高效率和多功能的特点。
数控车床广泛应用于航空航天、汽车制造等领域。
2.3 多轴车床多轴车床是一种具有多个工作轴的车床,可以同时进行多个加工操作。
它适用于复杂的工件加工,能够提高生产效率和加工精度。
三、车床的应用领域3.1 金属加工车床在金属加工领域有着广泛的应用。
它可以加工各种金属材料,如钢、铁、铝等,制造各种零部件和工件。
3.2 木工加工除了金属加工,车床还可以用于木工加工。
它可以加工木材,制造家具、工艺品等。
3.3 玻璃加工一些特殊的车床还可以用于玻璃加工。
它可以加工玻璃材料,制造玻璃器皿、灯具等。
四、车床的发展趋势4.1 自动化和智能化随着科技的不断进步,车床将趋向于自动化和智能化。
自动化技术可以提高生产效率和加工精度,智能化技术可以使车床更加智能化和人性化。
车床作业指导书

车床作业指导书一、引言车床作业指导书旨在为车床操作人员提供详细的操作步骤和注意事项,以确保安全、高效地完成车床作业任务。
本指导书涵盖了车床的基本操作流程、安全要求、常见故障排除方法等内容,帮助操作人员顺利完成车床作业。
二、车床基本操作流程1. 准备工作在进行车床作业之前,操作人员需要进行以下准备工作:- 检查车床的工作环境是否安全,如地面是否平整、周围是否有杂物等;- 检查车床的各项安全装置是否完好,如刀具保护装置、紧急停机按钮等;- 确保车床上的刀具、夹具等工具齐全,并进行必要的清洁和维护。
2. 车床操作步骤2.1 打开车床电源- 确保车床的电源插头已正确接入电源插座;- 打开车床的电源开关,确保车床正常通电。
2.2 车床的手动操作- 调整车床的进给手柄和主轴手柄,使刀具和工件之间的距离适当;- 手动操作车床,观察刀具和工件之间的间隙,确保安全。
2.3 车床的自动操作- 根据工件的要求,设置车床的自动操作参数,如进给速度、主轴转速等;- 将工件夹紧在车床上,并确保夹具牢固可靠;- 启动车床的自动操作模式,观察刀具和工件之间的加工情况,及时调整参数。
3. 车床安全要求3.1 个人防护- 操作人员在进行车床作业时,必须佩戴符合安全标准的个人防护装备,如安全眼镜、防护手套等;- 长发的操作人员应将头发束起,以防止卷入车床中。
3.2 刀具安全- 在更换刀具或调整刀具位置时,必须确保车床处于停机状态,并等待主轴完全停止旋转后才能进行操作;- 刀具的安装和调整应按照车床操作手册的要求进行,确保刀具固定可靠。
3.3 工件夹紧安全- 在夹紧工件时,必须使用合适的夹具,并确保夹具的牢固可靠;- 夹紧工件时,应保持手部远离夹具和刀具,以防止意外伤害。
3.4 紧急停机- 在发生紧急情况时,操作人员应立即按下车床上的紧急停机按钮,以停止车床的运转;- 在解决紧急情况之前,不得擅自恢复车床的运转。
4. 常见故障排除方法4.1 车床无法启动- 检查车床的电源是否正常连接;- 检查车床的电源开关是否打开;- 检查车床的保险丝是否熔断。
机床分类

全国机床产品目录1金属切削机床1.1车床1.1.1 台式仪表车床 1.1.27 动轮车床1.1.2 仪表六角车床 1.1.28 动轮轴颈车床,动轮曲拐销车床1.1.3 仪表卧式车床 1.1.29 轧辊车床1.1.4 单轴自动车床 1.1.30 钢锭车床,钢锭模车床1.1.5 单轴六角自动车床 1.1.31 高效自动车床1.1.6 多轴棒料自动车床 1.1.32 活塞车床1.1.7 多轴卡盘自动车床 1.1.33 多用车床1.1.8 立式半自动车床 1.1.34 多功能工具机1.1.9 回轮、转塔式六角车床 1.1.35 轴承车床,轴承车削自动线1.1.10 曲轴车床 1.1.36 数控纵切自动车床1.1.11 凸轮轴车床 1.1.37 数控卡盘,端面车床1.1.12 立式车床 1.1.38 数控卧式车床1.1.13 卧式车床(普通车床) 1.1.39 数控立式车床1.1.14 数显卧式车床 1.1.40 数控曲轴车床1.1.15 马鞍车床 1.1.41 数控轧辊车床1.1.16 重型卧式车床 1.1.42 数控车轴车床1.1.17 落地车床 1.1.43 数控车轮车床1.1.18 卡盘、端面车床 1.1.44 数控轮毂车床1.1.19 无丝杠车床 1.1.45 数控单轴、双轴立式车床1.1.20 球面车床,球面车磨床 1.1.46 数控轴承车床1.1.21 仿形车床 1.1.47 数控管螺纹车床1.1.22 卡盘多刀车床 1.1.48 数控气缸套镗车床1.1.23 多刀车床 1.1.49 超精密数控球面车床1.1.24 铲齿车床 1.1.50 数控四轴车床1.1.25 车轮车床,不落轮对车床 1.1.51 中间驱动数控车床1.1.26 车轴车床,轮对轴颈车床1.2 钻床1.2.1 摇臂钻 1.2.6 平端面打中心孔钻床(铣端面打中心孔钻床)1.2.2 滑座、万向式摇臂钻床 1.2.7 钻铣床,钻铣镗床,钻铣镗磨床1.2.3 台式钻床 1.2.8 排式钻床1.2.4 立式钻床 1.2.9 其他钻床1.2.5 深孔钻床 1.2.10 数控钻床,数控钻铣床1.3 镗床1.3.1 卧式铣镗床(卧式镗床) 1.3.11 气门座镗床1.3.2 立式铣镗床 1.3.12 其他镗床1.3.3 单柱坐标镗床 1.3.13 数控镗铣床,数控刨台式、卧式铣镗床1.3.4 双柱坐标镗床 1.3.14 数控卧式仿形镗铣床1.3.5 卧式坐标镗床 1.3.15 数控立式铣镗床1.3.6 落地铣镗床(落地镗床) 1.3.16 数控龙门镗铣门1.3.7 深孔钻镗床 1.3.17 数控坐标镗床1.3.8 精镗床(金刚镗床) 1.3.18 数控双柱坐标镗床1.3.9 气缸镗床(镗缸机)制动鼓镗床(镗制动鼓机) 1.3.19 数控落地铣镗床1.3.10 缸体轴瓦镗床(镗瓦机)连杆瓦镗床1.4 磨床1.4.1 无心磨床 1.4.31 圆锥滚子球形基面磨床1.4.2 外圆磨床 1.4.32 圆锥滚子无心磨床1.4.3 万能外圆磨床 1.4.33 油针磨床1.4.4 内圆磨床 1.4.34 活塞环磨床1.4.5 坐标磨床 1.4.35 汽阀挺杆球面磨床1.4.6 研磨机 1.4.36 立式珩磨床1.4.7 导轨磨床 1.4.37 深孔珩磨床1.4.8 万能工具磨床 1.4.38 气门锥面磨床,气门小端面磨床1.4.9 刀具刃磨床 1.4.39 气门座研磨机1.4.10 拉刀刃磨床 1.4.40 深孔磨床1.4.11 钻头刃磨床 1.4.41 龙门平面磨床1.4.12 滚刀刃磨床 1.4.42 抛光机1.4.13 卧轴矩台平面磨床 1.4.43 超精机1.4.14 立轴矩台平面磨床 1.4.44 数控龙门平面磨床1.4.15 卧轴圆台平面磨床,立轴圆台平面磨床 1.4.45 数控无心磨床1.4.16 双端面磨床 1.4.46 数控内圆磨床1.4.17 凸轮轴磨床 1.4.47 数控坐标磨床1.4.18 轧辊磨床 1.4.48 数控导轨磨床1.4.19 花键轴磨床 1.4.49 数控工具磨床1.4.20 曲轴磨床 1.4.50 数控卧轴矩台平面磨床1.4.21 卡规磨床 1.4.51 数控外圆磨床1.4.22 可转们刀片双端面研磨机,可转们刀片周边磨床 1.4.52 数控凸轮轴磨床1.4.23 刀齿刃磨床 1.4.53 数控轧辊磨床1.4.24 曲线磨床 1.4.54 数控花键轴磨床1.4.25 模具工具磨床 1.4.55 数控曲轴磨床1.4.26 多用磨床 1.4.56 数控可转们刀片周边磨床1.4.27 磨刀机 1.4.57 数控珩磨机1.4.28 轴承内,外圈沟道超精加工机 1.4.58 数控气门锥面磨床1.4.29 轴承圈沟道超精加工机 1.4.59 数控球笼窗口磨床1.4.30 轴承内圈,外圈沟道磨床,轴承套 1.4.60 数控瓦楞辊磨床1.5齿轮加工机床1.5.1 弧齿锥齿轮拉齿机 1.5.13 锥齿轮滚动检查机1.5.2 弧齿锥齿轮粗切机 1.5.14齿轮噪声检查机1.5.3 弧齿锥齿轮铣齿机 1.5.15珩齿机1.5.4 直齿锥齿轮刨齿机 1.5.16数控弧齿锥齿轮轮铣齿机1.5.5 滚齿机 1.5.17数控剃齿机1.5.6 剃齿机 1.518数控插齿机1.5.7 插齿机 1.5.19数控扇形齿轮插齿机1.5.8 齿条插齿机 1.5.2 0数控花键轴铣床1.5.9 花键轴齿床 1.5.21数控齿轮磨齿床1.5.10 齿轮磨齿机 1.5.22数控锥齿轮研齿机1.5.11 齿轮条铣齿机 1.5.23齿轮淬火机1.5.12 齿轮倒棱机,弧齿锥齿轮倒棱机,齿轮倒角机1.6螺纹加工机床1.6.1攻丝机 1.6.4数控螺纹铣床1.6.2螺纹铣床 1.6.5数控丝锥磨床,丝杆磨床1.6.3丝锥磨床1.7铣床1.7.1单柱平面铣床,双柱平面铣床,端面铣床 1.7.15梅花头铣床1.7.2龙门铣床,龙门镗铣床 1.7.16螺杆泵转子专用铣床,螺纹钢轧辊铣床1.7.3仿形铣床 1.7.17碳块铣床,曲轴铣床1.7.4立式升降台铣床 1.7.18数控仪表铣床1.7.5立式炮铣床 1.7.19数控龙门镗铣床1.7.6万能摇臂铣床 1.7.20数控仿形铣床1.7.7卧式升降台铣床 1.7.21数控立式升降台铣床1.7.8万能升降台铣床 1.7.22数控万能摇臂铣床1.7.9万能回转头铣床 1.7.23数控卧式升降台铣床1.7.10床身铣床(工作台不升降铣床) 1.7.24数控床身铣床1.7.11万能工具铣床 1.7.25数控万能工具铣床1.7.12圆工作台铣床 1.7.26超精密数控铣床1.7.13单仿、三仿铣床 1.7.27数控万能回转头铣床1.7.14键槽铣床1.8刨床,插床1.8.1 悬臂刨床(单臂刨床) 1.8.5 牛头刨床1.8.2 龙门刨床 1.8.6 液压移动式牛头刨床1.8.3 龙门刨铣床 1.8.7 刨边机1.8.4 插床1.9拉床1.9.1深孔螺旋拉床 1.9.3专用拉床1.9.2拉床1.10特种加工床1.10.1电火花小孔加工机床 1.10.5其他电加工机床1.10.2电火花成型机,数控电火花成型机 1.10.6数控激光加工机床1.10.3电火花线切割机,数控电火花线切割机 1.10.7数控火焰,等离子加工机床1.10.4电解加工机床1.11锯床1.11.1弓锯床 1.11.3圆锯床1.11.2带锯床,自动带锯床 1.11.4带锯床1.12加工中以,柔性加工单元1.12加工中心,柔性加工单元1.12.1车削加工中心 1.12.8柔性加工单元1.12.2 立式加工中心 1.12.9虚拟轴机床1.12.3卧式加工中心1.12.4立式钻削加工中心,卧式钻削加工中心1.12.5落地铣镗加工中心1.12.6龙门式加工中心1.12.7车削柔怀加工单元1.14组合机床2锻压机械2.1机械压力机2.1.1台式压力机 2.1.14液压螺旋压力机,液压快速压力机2.1.2开式固定台压力机 2.1.15电动螺旋压力机2.1.3开式固定台数控压力机 2.1.16压砖机2.1.4液压机械压力机 2.1.17复合式压砖机2.1.5固定台深喉口压力机 2.1.18切边机2.1.6开式可倾压力机 2.1.19 高速、精密压力机2.1.7开式底传动压力机 2.1.20 精压机2.1.8闭式单点压力机 2 .1.21 挤压机2.1.9开、闭式双点、四点压力机 2.1.22仿形步冲压力机2.1.10开闭式底传动拉坤压力机 2.1.23轮圈整形机2.1.11闭式双点动拉坤压力机 2.1.24数控冲模回转头压力机2.1.12多工位自动压力机 2.1.25数控步冲压力机2.1.13双盘摩擦压力机2.2液压机 2.3自动锻机2.2.1单柱液压机 2.3.1双击整模自动冷镦机2.2.2双柱、四柱液压机 2.3.2搓丝机,滚丝机2.2.3单动、双动、联动液压机 2.3.3 钢球自动冷镦机2.2.4校正压装液压机 2.3.4螺母自动冷镦机2.2.5金属屑压块液压机 2.3.5多工位自动冷镦机2.2.6金属制品成型液压机 2.3.6多工位冷成型机2.2.7挤压液压机 2.3.7制钉自动机2.2.8冲压液压机 2.3.8自动弯曲机2.2.9精密冲裁液压机 2.3.9管端成型机2.2.10龙门式液压机 2.3.10冷轧带筋钢筋生产线2.2.11框式液压机2.2.12磁性材料液压机2.2.13金刚石液压机2.2.14数控液压机2.2..15其他液压机2.4锤类 2.5锻压机2.4.1空气锤 2.5.1液压模锻锤2.4.2楔形横轧机 2.5.2电热镦机2.4.3带式落锤 2.5.3辗环机2.4.4电液锤 2.5.5数控辗环机2.5.6其他锻机2.6剪板机2.6.1剪板机 2.6.6剪断机2.6.2液压剪板机 2.6.7角钢自动生产线2.6.3冲型剪切机 2.6.8数显、数控剪板线2.6.4双盘剪切机 2.6.9数显、数控液压剪板机2.6.5多功能、联合冲剪机 2.6.10数控变压器铁芯横剪生产线2.7弯曲校正机2.7.1三辊、四辊卷板机 2.7.8液压板料折弯压力机2.7.2型材弯曲机 2.7.9自动坡口机2.7.3弯管机 2.7.10坡口机2.7.4多辊角钢校直机 2.7.11校平机2.7.5开卷校平剪切生产线 2.7.12板材校平机2.7.6折边机 2.7.13数控弯管机2.7.7板料折弯压力机 2 .7.14数控开卷校平剪切机2.8其他锻压机2.8.1液压铆接机 2.8.10汽车轮辐冲孔专用压力机2.8.2旋压机 2.8.11装出料机2.8.3锻造操作机 2.8.12弯头推制机2.8.4轮辋用机 2.8.13翅形管绕机2.8.5辊锻机 2.8.14液压动力头2.8.6摆辗压机 2.8.15双槽连续挤压包覆机2.87自辊锻机 2.8.16数控强力旋压机2.8.8渐开线花键冷轧机 2.8.17 锻压机机器人2.8.9花键滚轧机床 2.8.18程控轮辋滚形机3铸造机械3.1砂处理设备 3.2造型及制芯设备3.1.1辗轮式混砂机 3.2.1造型设备3.1.2松砂机 3.2.2制芯盒设备3.1.3筛砂设备 3.2.3制芯设备3.1.4远红外型芯干炉 3.2.4 旋转壳芯机3.1.5滚筒式型砂冷却机 3.2.5造型自动线3.1.6磁分离设备3.3清理设备 3.4金属型设备3.3.1转台抛丸机 3.4.1冷室压铸机3.3.2吊钩式抛丸清理机 3.4.2 热室压铸机3.3.3全自动抛丸机 3.4.3金属型铸造机3.3.4履带式抛丸清理机 3.4.4低压铸造机3.3.5通过式抛丸清理机3.5熔炼设备 3.6运输设备3.5.1冲天炉 3.6.1带式输送机3.5.2旋转式单轨加料机 3.6.2 鳞板输送机3.5.3爬式加料机 3.6.3铸型输送机3.5.4翻斗加料机 3.6.4 斗式提升机3.7给料设备 3.8其他铸造机械3.7.1螺旋给料机 3.8.1回转反吹布袋除尘器3.7.2定量给料机 3.8.2型芯烘干炉3.8.3烧冒口去除机金属切削机床:车床钻床镗床磨床齿轮加工机床螺纹加工机床铣床刨床,插床拉床特种加工床锯床加工中心,柔性加工单元锻压机械:机械压力机液压机自动锻机锤类锻压机弯曲校正机其他锻压机铸造机械:砂处理设备造型及制芯设备清理设备金属型设备熔炼设备运输设备给料设备其他铸造机械。
微型精密车床的设计

摘要微型精密车床的设计,它主要包括以下几个主要部分:床身、主轴箱组件、尾架组件、变速齿轮箱、丝杠等。
床身主要起支撑的作用,所有其他主要部件都安装在床身上,通常在床身上面有内外两组平行的导轨。
主轴箱组件是机床实现旋转运动的执行件,是机床上的一个关键组件。
主轴组件由主轴,主轴支撑和安装在主轴上的传动件,密封件组成。
尾座组件主要由三部分组成。
底座与床身的内侧导轨配合,并可以在导轨上做纵向移动,底座上有一个可以使整个尾座组件夹紧在任意位置上的装置。
变速箱主要通过齿轮的变速最终使刀具按主轴的转数纵向地或横向地精确移动。
采用滚珠丝杠,减小摩擦,提高了运动精度。
本设计主要设计进给部分,包括溜板箱的设计,丝杆的设计,步进电动机的选型和校核计算,刀架的设计。
由于微型精密车床体积小,质量轻,便于运输。
所以微型精密车床得到了广泛的应用关键词微型精密滚珠丝杠溜板箱组件刀架步进电动机AbstractMicro precision lathes design, it mainly includes the following main parts: lathe bed, headstock assembly, tailstock assembly, quick-change gear box ,leadscrew, etc. The bed`s main effect is supporting, all other major components are installed in bed, usually in bed with internal and external two groups of parallel ways. headstock assembly is the realization of rotating machine tools, implementation is a key component. headstock assembly is made up of spindle, spindle support and installed in the transmission shaft and seals. tailstock assembly mainly consists of three parts. Pedestal and the inside of the bed, and can guide ways longitudinal move in on a pedestal, can make whole tailstock assembly clamping device in any position. The quick-change box mainly though changegears eventually made by cutting the number of vertical shaft by turning horizontally o r precise movement. Using the leadscrew, reducing friction, improve the motion precision. This design mainly design the feed part, including the carriage design, leadscrew design, the design of stepping motor selection and design of the check calculation, the tool post design. Because the micro precision lathe, small size, light quality, easy to transport. So the micro precision lathes are widely applied. Keywords micro precision leadscrew carriage assembly tool post stepping motor目录前言 (5)1.绪论 (6)1.1 设计的目的和意义 (6)1.2 微型机械加工技术发展现状趋势分析 (6)1.3 微型精密车床的现状 (7)2.微型精密车床总体方案拟定 (9)2.1 进给部分电动机的选用 (9)2.1.1 步进电动机及其发展 (9)2.1.2步进电动机的特点 (10)2.1.3 步进电动机的类型 (10)2.1.4 步进电机的工作原理 (11)2.1.5 步进电机的常用参数 (12)2.1.6 步进电机具有如下优点 : (13)2.2 丝杆螺母的选用 (14)2.3机床导轨及尾座的设计 (14)2.4 机床床身的设计 (14)3.纵向进给机构设计 (17)3.1 进给系统的概述和总体方案设计 (17)3.2 滚珠丝杠螺母的概述 (17)3.2.1 滚珠丝杠螺母工作原理及其特点 (17)3.2.2 滚珠丝杠螺母的结构循环方式 (18)3.3 丝杆螺母副的选择 (21)3.3.1内循环与外循环的选用说明 (21)3.3.2 滚珠丝杠的轴向间隙调整和预紧方法 (21)3.3.3.滚珠丝杠的安装 (21)3.4 滚珠丝杠螺母副的计算 (22)3.5 滚珠丝杠螺母副的验算 (24)3.5.1 刚度计算 (24)3.5.2 稳定性验算: (25)3.5.3丝杠系统的刚度计算: (26)3.5.4 反向死区的验算: (26)3.6 滚珠丝杠的设计与计算 (27)3.6.1 切削力的计算 (28)3.6.2 滚珠丝杠设计计算 (29)3.7 纵向步进电动机的验算 (30)3.8 消隙齿轮的计算 (34)3.9 消隙轴的设计 (39)3.10 动力计算 (44)3.10.1 小齿轮的转动惯量 (44)3.10.3 计算工作台的转动惯量JW (45)3.10.4 计算丝杠的转动惯量Js (45)4.横向进给机构的设计 (46)4.1 横向滚珠丝杠螺母副的型号选择与校核步骤 (46)4.1.1型号选择 (46)4.1.2 横向滚珠丝杠的校核 (46)4.2 横向进给系统的设计和计算 (47)4.2.1 横向进给系统的设计 (47)4.2.2 横向进给系统的设计和计算 (47)4.2.3 滚珠丝杠设计计算 (48)4.2.4 动载强度计算 (49)4.2.5 静强度计算 (51)4.2.6 临界转速校核 (51)4.2.7 额定寿命的校核 (52)4.3 横向进给步进电机的计算 (52)5. 刀架的设计 (54)5.1 减速传动机构的设计 (54)5.2 自动回转刀架的工作原理 (55)结论 (60)致谢 (61)参考文献 (62)前言大学的学习生活即将结束,大学学习生活中的最后一个环节也是最重要一个环节——毕业设计,它是对所学知识和技能的综合运用和检验。
车床加工作业指导书

车床加工作业指导书
1. 引言
车床加工是一项重要的金属加工技术,广泛应用于机械制造、
航空航天、汽车等领域。
本指导书旨在为车床操作人员提供详细的
作业指导,以确保安全高效地完成车床加工作业。
2. 车床加工基础知识
2.1 车床类型及结构
车床可分为传统车床和数控车床。
传统车床主要由主轴、进给
机构和刀架组成,数控车床则具备自动化程度更高的数控系统。
2.2 刀具和切削参数
刀具的选择根据加工材料和加工要求进行,常见的刀具有车刀、螺纹刀、切槽刀等。
切削参数包括进给速度、转速和切削深度,需
要根据加工材料和工艺要求进行合理设定。
3. 车床加工操作步骤
3.1 准备工作
3.1.1 检查车床是否正常运作,如润滑油是否充足,各零部件是否正常。
3.1.2 将需要加工的工件安装到车床上,注意固定牢固,避免加工过程中移动。
3.2 选择合适的刀具
根据加工要求和材料选择合适的刀具,确定刀具安装的位置和方向。
3.3 设定切削参数
设定进给速度、转速和切削深度,确保在合理范围内,避免刀具损坏和加工质量问题。
3.4 开始加工
3.4.1 打开车床电源,启动车床主轴,确保转速正常。
3.4.2 根据设定的切削参数,将刀具逐步进给到工件上,开始加工。
车床安全操作规程
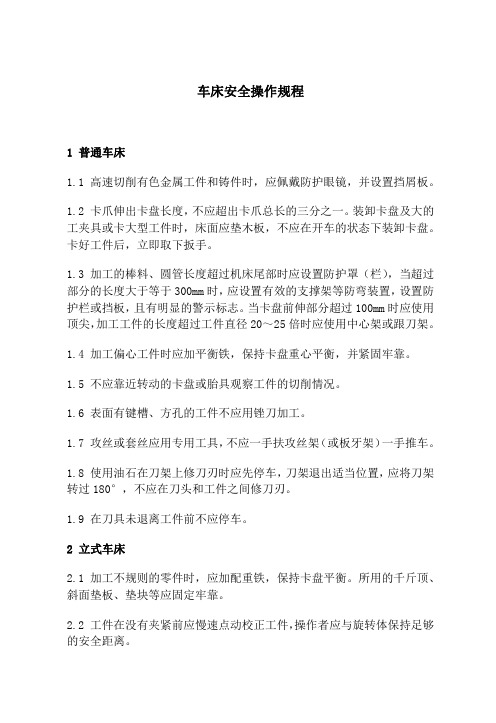
车床安全操作规程1普通车床1.1高速切削有色金属工件和铸件时,应佩戴防护眼镜,并设置挡屑板。
1.2卡爪伸出卡盘长度,不应超出卡爪总长的三分之一。
装卸卡盘及大的工夹具或卡大型工件时,床面应垫木板,不应在开车的状态下装卸卡盘。
卡好工件后,立即取下扳手。
1.3加工的棒料、圆管长度超过机床尾部时应设置防护罩(栏),当超过部分的长度大于等于300mm时,应设置有效的支撑架等防弯装置,设置防护栏或挡板,且有明显的警示标志。
当卡盘前伸部分超过100mm时应使用顶尖,加工工件的长度超过工件直径20~25倍时应使用中心架或跟刀架。
1.4加工偏心工件时应加平衡铁,保持卡盘重心平衡,并紧固牢靠。
1.5不应靠近转动的卡盘或胎具观察工件的切削情况。
1.6表面有键槽、方孔的工件不应用锉刀加工。
1.7攻丝或套丝应用专用工具,不应一手扶攻丝架(或板牙架)一手推车。
1.8使用油石在刀架上修刀刃时应先停车,刀架退出适当位置,应将刀架转过180°,不应在刀头和工件之间修刀刃。
1.9在刀具未退离工件前不应停车。
2立式车床2.1加工不规则的零件时,应加配重铁,保持卡盘平衡。
所用的千斤顶、斜面垫板、垫块等应固定牢靠。
2.2工件在没有夹紧前应慢速点动校正工件,操作者应与旋转体保持足够的安全距离。
2.3作业人员不应站在旋转台上调整机床和操作按钮。
2.4加工件外形超过卡盘时,应采取防护措施,避免碰撞立柱、横梁或撞伤人。
2.5对刀时应缓慢进行,自动对刀刀头接近工件40mm~60mm时应停止自动对刀,采用手摇进给。
2.6机床运转中不应变换工作台的转速和旋转方向。
2.7高速切削时,在铁屑飞出方向应设置防护挡板。
2.8在切削过程中,刀具未退离工件前不应停车。
3数控车床3.1开车前检查卡盘夹紧状态,开动前应关闭机床防护门。
3.2开车前应先试车、移动各轴,主轴应低速旋转3min~5min后方可换档。
3.3启动新程序或长期未用的程序时,右手作按停止按钮准备,程序在运行当中手不能离开停止按钮,如有紧急情况应立即按下停止按钮。
车床培训计划内容有哪些
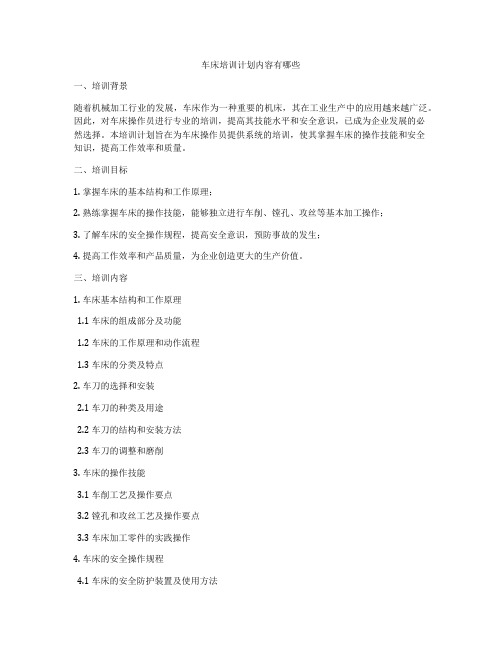
车床培训计划内容有哪些一、培训背景随着机械加工行业的发展,车床作为一种重要的机床,其在工业生产中的应用越来越广泛。
因此,对车床操作员进行专业的培训,提高其技能水平和安全意识,已成为企业发展的必然选择。
本培训计划旨在为车床操作员提供系统的培训,使其掌握车床的操作技能和安全知识,提高工作效率和质量。
二、培训目标1. 掌握车床的基本结构和工作原理;2. 熟练掌握车床的操作技能,能够独立进行车削、镗孔、攻丝等基本加工操作;3. 了解车床的安全操作规程,提高安全意识,预防事故的发生;4. 提高工作效率和产品质量,为企业创造更大的生产价值。
三、培训内容1. 车床基本结构和工作原理1.1 车床的组成部分及功能1.2 车床的工作原理和动作流程1.3 车床的分类及特点2. 车刀的选择和安装2.1 车刀的种类及用途2.2 车刀的结构和安装方法2.3 车刀的调整和磨削3. 车床的操作技能3.1 车削工艺及操作要点3.2 镗孔和攻丝工艺及操作要点3.3 车床加工零件的实践操作4. 车床的安全操作规程4.1 车床的安全防护装置及使用方法4.2 车床操作中的安全注意事项4.3 车床事故的预防和处理4. 车床维护和保养4.1 车床的日常维护和保养4.2 车床的故障排除和维修5. 车床操作实操5.1 车床操作技能的实操训练5.2 不同工件的车床加工实例演练四、培训方式1. 理论讲授:由资深的车床操作员进行理论知识的讲解,讲解内容贴近实际生产,重点突出实用性。
2. 操作演示:由培训教师进行车床操作的现场演示,让学员们直观地了解车床的操作技巧和注意事项。
3. 实操训练:学员们进行车床的实操演练,由教师进行指导和指导。
五、培训时间安排本培训计划分为三个阶段,共计36学时,时间安排如下:第一阶段(8学时):车床基础知识的讲解和操作演示;第二阶段(16学时):车床操作技能的理论讲解和实操训练;第三阶段(12学时):车床安全操作规程的讲解和车床操作实操。
车床安全培训计划

车床安全培训计划一、培训目的车床是加工金属材料的重要设备,在使用过程中存在一定的安全风险。
为了确保员工安全操作车床,提高生产效率,特制定车床安全培训计划,旨在帮助员工了解车床的安全操作规范,掌握正确的操作技巧,降低事故风险,提高工作效率,保障员工的人身安全。
二、培训对象公司全体使用车床操作的员工。
三、培训内容1. 车床的基本结构和工作原理1.1 车床的主要组成部分1.2 车床的工作原理1.3 车床的功能和用途2. 车床的安全操作规范2.1 车床的安全操作流程2.2 车床的停车和启动操作2.3 车床的刀具更换和调整2.4 车床的操作注意事项3. 车床的常见故障和维护3.1 车床的常见故障及处理方法3.2 车床的日常维护保养3.3 车床的定期检修和保养工作4. 车床的安全防护装置4.1 车床的安全防护装置介绍4.2 车床的安全防护装置的使用方法4.3 车床的安全防护装置的维护保养5. 车床的应急措施5.1 车床的常见事故原因及预防方法5.2 车床事故的应急处理程序5.3 车床事故的报告和记录要求四、培训形式1. 理论教学通过讲解、示范以及多媒体资料等形式,向员工讲解车床的基本结构和工作原理,安全操作规范,常见故障及维护,安全防护装置以及应急措施等内容。
2. 案例分析结合实际案例,对员工进行案例分析讨论,使员工更好地理解和应用安全操作规范,提高应对紧急情况的能力。
3. 现场操作通过实际操作车床,指导员工掌握正确的操作技巧,加强对车床的操作流程和安全防护装置的使用方法的理解。
4. 考核评估进行安全操作规范和技能操作的考核评估,确保员工掌握了正确的操作规范和技能,达到安全操作要求。
五、培训时间和地点培训时间:预计为期2天培训地点:公司车间六、培训教材和设备1. 培训教材《车床安全操作规范手册》《车床常见故障和维护手册》《车床应急措施手册》多媒体教学资料2. 培训设备车床设备七、培训师资和方法培训师资:公司专业技术人员培训方法:理论教学、案例分析、现场操作、考核评估八、培训效果评估1. 考核评估对员工进行安全操作规范和技能操作的考核评估,合格者发放《车床安全操作规范证书》。
车床转速和走刀的比例
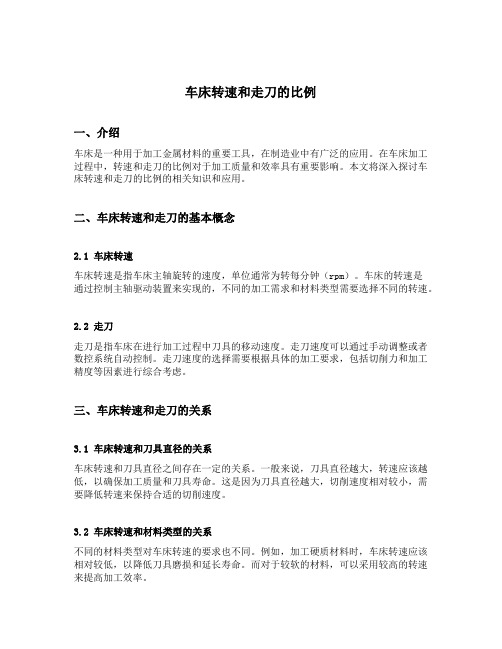
车床转速和走刀的比例一、介绍车床是一种用于加工金属材料的重要工具,在制造业中有广泛的应用。
在车床加工过程中,转速和走刀的比例对于加工质量和效率具有重要影响。
本文将深入探讨车床转速和走刀的比例的相关知识和应用。
二、车床转速和走刀的基本概念2.1 车床转速车床转速是指车床主轴旋转的速度,单位通常为转每分钟(rpm)。
车床的转速是通过控制主轴驱动装置来实现的,不同的加工需求和材料类型需要选择不同的转速。
2.2 走刀走刀是指车床在进行加工过程中刀具的移动速度。
走刀速度可以通过手动调整或者数控系统自动控制。
走刀速度的选择需要根据具体的加工要求,包括切削力和加工精度等因素进行综合考虑。
三、车床转速和走刀的关系3.1 车床转速和刀具直径的关系车床转速和刀具直径之间存在一定的关系。
一般来说,刀具直径越大,转速应该越低,以确保加工质量和刀具寿命。
这是因为刀具直径越大,切削速度相对较小,需要降低转速来保持合适的切削速度。
3.2 车床转速和材料类型的关系不同的材料类型对车床转速的要求也不同。
例如,加工硬质材料时,车床转速应该相对较低,以降低刀具磨损和延长寿命。
而对于较软的材料,可以采用较高的转速来提高加工效率。
3.3 走刀速度和加工精度的关系走刀速度对于加工精度同样具有重要影响。
走刀速度过快可能导致加工精度下降,而走刀速度过慢则会影响加工效率。
在选择走刀速度时,需要综合考虑加工要求和机床性能等因素。
3.4 走刀速度和刀具切削力的关系走刀速度和刀具切削力之间存在直接的关系。
走刀速度越大,切削力也越大。
合适的走刀速度可以平衡加工效率和刀具寿命。
通过合理选择走刀速度,可以减小切削力,降低刀具磨损和断刀风险。
四、车床转速和走刀的优化4.1 车床转速和走刀速度的选择方法为了优化车床的加工效率和加工质量,需要选择合适的转速和走刀速度。
选择转速和走刀速度的方法可以从经验和实验两个方面考虑。
经验法是根据加工人员的经验积累和实际情况选择转速和走刀速度。
车床培训计划内容
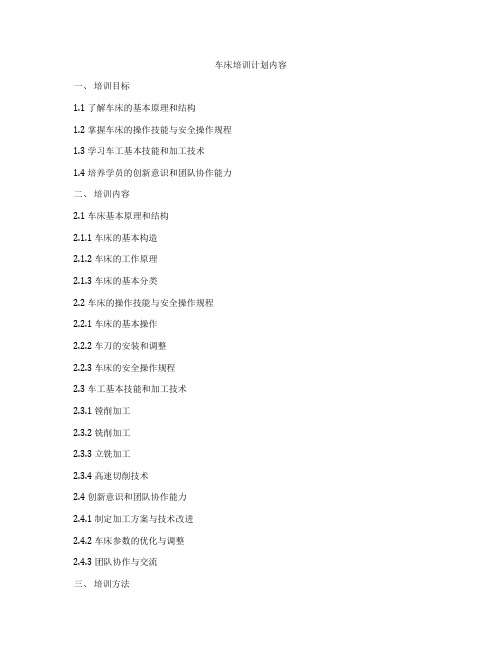
车床培训计划内容一、培训目标1.1 了解车床的基本原理和结构1.2 掌握车床的操作技能与安全操作规程1.3 学习车工基本技能和加工技术1.4 培养学员的创新意识和团队协作能力二、培训内容2.1 车床基本原理和结构2.1.1 车床的基本构造2.1.2 车床的工作原理2.1.3 车床的基本分类2.2 车床的操作技能与安全操作规程2.2.1 车床的基本操作2.2.2 车刀的安装和调整2.2.3 车床的安全操作规程2.3 车工基本技能和加工技术2.3.1 镗削加工2.3.2 铣削加工2.3.3 立铣加工2.3.4 高速切削技术2.4 创新意识和团队协作能力2.4.1 制定加工方案与技术改进2.4.2 车床参数的优化与调整2.4.3 团队协作与交流三、培训方法3.1 理论教学培训老师通过课件、讲解和案例分析等形式,对车床的基本原理和结构、操作技能与安全操作规程、车工基本技能和加工技术等进行讲解和培训。
3.2 实操训练学员进行现场操作演练,学习车床的实际操作技能和安全操作规程,掌握车工基本技能和加工技术。
3.3 案例分析通过真实案例分析,学员分析并解决加工中遇到的问题,培养其创新意识和解决问题的能力。
3.4 团队合作安排学员组成团队,共同完成一些车床加工项目,培养学员的团队合作和交流能力。
四、培训安排4.1 培训时间:5天4.2 日程安排第一天:车床的基本原理和结构的理论教学第二天:车床的操作技能与安全操作规程的理论教学第三天:车工基本技能和加工技术的实操训练第四天:创新意识和团队协作能力的案例分析和团队合作第五天:总结与考核五、培训考核5.1 考核形式培训结束后进行理论和实际操作的考核,以及个人总结和团队合作项目的评估。
5.2 考核标准理论知识考核:包括车床的基本原理和结构、操作技能与安全操作规程、车工基本技能和加工技术等方面的考核。
实操技能考核:对学员进行车床的实际操作,包括车刀的安装和调整、镗削加工、铣削加工、立铣加工、高速切削技术等方面的考核。
机加设备技术标书

机加工通用设备技术规格一﹑采购货物一览表:所有设备的技术参数与以下技术参数不符的必须在投标文件作出特殊说明,并且保证厂房建设完工后,设备进场安装.特别要求:本批设备是交钥匙工程,是一批完整的设备单元,除水、电、气外,不需要甲方增加任何硬件即可进行生产并满足使用要求。
二、配置及要求2。
1 立式车床设备用途:本设备用于混凝土泵车回转底座及转台的端面、阶梯面、内外圆柱面的加工。
加工工件材质为Q345、45和WELDOX700、WELDOX900等进口高强钢。
带两个垂直刀架,适用于高速钢刀具和硬质合金刀具,可进行内外圆柱面、内外圆锥面、内孔、端面、车槽和切断等,最大工件尺寸不大于φ2000×1800mm。
2.1.1 型号:C5225(数显)1台、C5231(数显)1台2.1。
2 工作环境:1)工作温度: -20℃— 40℃,保证在此环境温度下长期稳定运行。
2)工作湿度:90%以下3)设备噪音:≤75dB.4)电源条件:频率50Hz±1 Hz 电压380/220V AC ±10%(三相四线)2.1.3 工作模式:二班制,每班工作时间8小时,全年工作250天。
工作制式:连续2。
1。
4基本要求(1)机床具有大功率主轴,适合重载加工;机床各结构件设计合理,具有足够的静态、动态、热态刚性;机械系统精度及可靠性高;机床造型美观。
(2)设备必须运用国际上同行业中的先进设计、制造技术,采用新的工艺、新材料和新技术。
(3)设备具有良好的操作性能,人性化的操作界面,维护、维修方便、较高的安全性和全面的防护措施,不对环境产生噪声、污水等影响。
(4)投标人在投标时应提供完整的产品主要技术文件,其中包括产品的样板、主要性能、技术参数、适用范围及外形图样、安装尺寸及电器控制及数控系统使用说明书(中文)等。
(5)设备交验必须附带标准卡爪等试机刀具、工具、夹具.2.1。
5 技术参数2。
1。
6 主要结构及性能本机床由立柱,主变速箱,工作台,横梁升降机构,垂直刀架,电气系统,液压系统等组成。
- 1、下载文档前请自行甄别文档内容的完整性,平台不提供额外的编辑、内容补充、找答案等附加服务。
- 2、"仅部分预览"的文档,不可在线预览部分如存在完整性等问题,可反馈申请退款(可完整预览的文档不适用该条件!)。
- 3、如文档侵犯您的权益,请联系客服反馈,我们会尽快为您处理(人工客服工作时间:9:00-18:30)。
安徽工程科技学院教师备课教案本章节讲稿共 6 页教案第 1 页备课时间:06年2月2日教师签名:汪太平2.1 金属切削机床2.1.5 典型机床传动系统一、CA6140卧式车床的传动系统1.概述1)车床上的加工类型车各种轴类、套筒类和盘类零件上的回转表面,如:内圆柱面、圆锥面、环槽及成形回转面;车端面;车螺纹;钻扩铰孔和滚花等。
2)车床的运动主轴旋转为主运动、刀架的移动为进给运动。
一般地,两个运动是相互独立的,但车螺纹时,工件的旋转主运动与刀具的移动进给运动必须保持严格的运动关系,形成复合成形运动。
加工曲线回转体时,纵向和横向两个进给运动必须保持严格的运动关系,形成复合成形运动。
3)车床类型卧式、立式、落地式;转塔车床;多刀半自动车床;仿形车床;单轴和多轴自动车床;数控车床;专用车床等。
其中卧式车床应用最为广泛,如图2-10,应熟悉各部件名称及其位置。
4)2.主要结构1)主轴箱支撑主轴,实现换向、制动和变速。
2)溜板箱实现进给运动或快速移动,使刀架实现纵横向或正反向机动走刀或快速移动。
3) 主轴组件 图5-15前支承双列短圆柱滚子轴承3只承受径向力;主轴向左的轴向力由推力球轴承7承受;向右的轴向力以及后支承径向力由角接触球轴承8承受。
主轴轴承径向间隙调整:通过调整螺母5,推动套筒4和轴承内圈,由于轴颈1:12的锥度,使轴承内圈伸缩,从而调整轴承径向间隙。
4) 传动件28根轴、16个滑移齿轮、9个离合器。
5) 双向多片式摩擦离合器M1 p107图5-14作用:控制主轴,中位停止,左位正转切削加工,右位时主轴反转、快速退刀。
6) 内齿离合器M2和滑移齿轮Z50作用:控制主轴速度高低,左位高速,Z58空转;右位中低速,Z58通过M2传动VI 轴。
7) 背轮机构轴III-IV -V 间的两个双联滑移齿轮和4个固定齿轮。
3. 主运动传动链 1) 传动件分析6根轴I ~VI 、4个滑移齿轮、2个离合器; 2) 主运动传动路线表达式 方法是“抓两端,连中间”:首先找到两端件:主电动机和主轴,然后按照运动传递关系,依次写出传动比、轴和离合器。
21111450r /m in75kw6356395038()4151130304323050(I V I )22503458()3430M M M M φφ⎧⎫⎧⎫-----------⎧⎫⎪⎪⎪⎪⎪⎪⎪⎪⎪⎪-----⎨⎬⎪⎪⎪⎪⎪⎪⎪⎪⎪⎪⎪⎪-------⎩⎭⎨⎬⎨⎬⎪⎪⎪⎪⎪⎪⎪⎪⎪⎪⎪⎪⎩⎭---⎪⎪⎩⎭⇓ .分(高速)正转电皮 ⅠⅡ(背 Ⅲ轮动带中空转,停转机轮机 构)Ⅶ反转220208080505150256580M ⎧⎫⎧⎫⎪⎪⎪⎪⎧⎫⎪⎪⎪⎪⎪⎪⎪⎪-⎨⎬⎪⎪⎪⎪-⎪⎪⎪⎪--⎨⎬⎨---⎪⎪⎪⎪⎬⎪⎪⎪⎪⎪⎪⎪⎭⎩⎭⎩⎭⎪⎩ (中低速) ⅥⅤⅣ(主轴)合主轴转速级数主轴正转时,轴Ⅱ有2种转速,其中每种使轴Ⅲ获得3种转速。
背轮机构有两对双联滑移齿轮,可得4种传动比,其中有2种基本相等,即:1505150501≈⨯=μ ,41802050502=⨯=μ , 41505180203≈⨯=μ ,161802080204=⨯=μ因此主轴Ⅵ实际获得2×3×(2×2-1+1)=24级中低速。
同理,主轴反转时,获得1×3×(2×2-1+1)=12级转速。
3) 运动平衡式按运动平衡式可计算主轴及中间各传动轴的各级转速:ⅣⅢⅢⅡⅡⅠ电主---⨯⨯-⨯⨯=μμμε)1(230130n n(4-1)式中ε——V 带轮的滑动系数,可取ε=0.02;ⅡⅠ-μ——为轴I 和轴Ⅱ间的传动比,其余类推。
主轴反转高速,用于车螺纹时刀架快返到起始位置,不断开主轴和刀架间传动联系,以免下次走刀发生“乱扣”同时节省退刀时间。
4. 进给运动传动链两端件是主轴和刀架。
作用是实现刀具纵向或横向移动、变速与换向。
包括车螺纹进给运动传动链和机动进给运动传动链。
1) 车螺纹进给运动传动链 (1) 可车削螺纹种类① 标准螺纹:公制、英制、模数制和径节制 ② 非标准螺纹 ③ 大导程螺纹 ④ 较精密螺纹⑤ 左、右旋螺纹。
车螺纹时,主轴与刀架必须保持严格的传动关系,即主轴每转一周,刀具应均匀准确地移动一个导程。
其运动平衡式为:1主轴×U x ×S 丝=S 工因此,工件螺纹导程S 工正比于主轴到丝杆的总传动比U x 。
车不同螺纹时,必须调整U x 。
公制螺纹的标准螺距见p103,是分段等差数列。
(2) 螺纹种类变换机构分析① 左右螺纹换向机构:IX 轴至XI 轴间,U =1,滑移齿轮Z33,左位车左螺纹,右位车右螺纹。
② 挂轮机构:XI 轴至XII 轴间,挂轮Z100,与Z63、Z75啮合时,则车公制和英制螺纹;与Z64、Z97啮合时,则车模数和径节螺纹。
③ 离合器开合功能见表2-6,在进给箱中M5—丝杆离合器,在XVII 轴上,车螺纹时常合,通过滑移齿轮Z28右移接合;一般车削时,Z28左移与M5脱开、与Z56 啮合接光杆。
M3—螺纹种类切换离合器,XII 轴上滑移齿轮Z25右移时接合。
M3、M4同时脱开,且XV 轴上滑移齿轮Z25右位时,车公制和模数螺纹;M3接合,M4脱开,且XV 轴上滑移齿轮Z25左位时车英制和径节螺纹。
M3接合,XIII 轴和XIV 轴的主被动关系颠倒,使基本组传动比成倒数关系。
惰性轮Z36空套在XIII 轴上。
M4—螺纹种类切换离合器,在XVII 轴上,双联滑移齿轮Z28、Z48左移时接合。
与M3同时合上时,车非标准和较精密螺纹,运动由主轴经挂轮直接传到丝杆;一般车削时脱开。
(3) 螺纹导程变换机构分析① 基本组:在进给箱中,XIII 轴上9个固定齿轮,XIV 轴上4个滑移齿轮。
传动比Uj 有8种,为等差数列(见表2-4)。
② 增倍组:在进给箱中,XVI 轴上的3个固定齿轮,XV 和XVII 轴上的2个双联滑移齿轮。
传动比Ub 有4种,为等比数列(见表2-4)。
③ 移换机构:XV 轴上滑移齿轮Z25,右位时,M3脱开,U 移1=25/36×25/36×36/25;左位时,M3接合,U 移2=36/25。
④ 扩大螺距机构:在主轴箱中,M2与轴IX 上滑移齿轮Z58同时右移,与背轮机构一起构成。
当工件螺纹导程大于12mm 时采用。
(4) 车公制螺纹传动路线① 两端件为:主轴Ⅵ和刀架。
M3和M4脱开,M5接合。
② 传动路线表达式为:(M 3)((Z25))()3363100()33100755825V I IX X I X II X III 58363364100X ()33102520972536U j X IV X V U b X V II 536255M ⎧⎫⎧⎫⨯⎪⎪⎪⎪⎪⎪⎪⎪-----------⎨⎬⎨⎬⎪⎪⎪⎪⎪⎪⎪⎪--⨯⎩⎭⎩⎭------⨯--------脱开基本组增倍组移右位换机构(右螺纹)公制主轴(左螺纹)模数(左右螺纹换向机构)(挂轮机构)(合X V III(--)丝杆)刀架③ 车公制螺纹的运动平衡式要求:主轴每转一周,刀架移动一个导程L583363100252536L 112583310075363625j b u u m m =⨯⨯⨯⨯⨯⨯⨯⨯⨯⨯(主轴)由L =7 Uj Ub 可得导程值8⨯4=32种,其中标准值20种(表2-4)。
2) 机动进给运动传动链用于车外圆或端面,为了减少螺纹传动链中丝杆与开合螺母磨损,保证螺纹传动链的精度,机动进给由光杆经溜板箱传动。
(1) 两端件为:主轴Ⅵ和刀架。
M4、M5脱开,光杆XIX 接通,运动经超越离合器M6、安全离合器M7和蜗杆涡轮,分别传至牙嵌式双向离合器M8与齿轮齿条机构、M9与横向进给丝杠XXVII ,使刀架作纵向和横向机动进给。
(2) 机动进给传动路线40848403093048408484030930482836324V I X V II X IX ()M 6M 7X X 56325629M 28()X X II X X III Z1280M X X I M 4859()X X V X X V II(4818M -----⨯-----⎡⎤⎣⎦⎧⎫⎡⎤-⎪⎪-------⎢⎥⨯-⎪⎪⎢⎥⎣⎦--⎨⎬⎡⎤-↑⎪⎪---⨯--⎢⎥⎪⨯-↓⎣⎦⎩⎭螺纹传动路线光杆(进)纵向齿条(进)横向丝杆)-⎪刀架① 纵向机动进给运动平衡式要求:主轴每转一周,刀架纵向移动f 纵j b 583363100252536283632440281u u 2.512m m /r583310075363625563236294880=⨯⨯⨯⨯⨯⨯⨯⨯⨯⨯⨯⨯⨯⨯⨯⨯⨯⨯zfp f 纵=0.71 Uj Ub② 横向机动进给传动链当横向与纵向进给的传动路线一致时,所得的横向进给量是纵向进给量的一半。
f 横=f 纵/2通过改变进给箱中基本组Uj 和倍增组Ub 的值、以及变换主轴箱中的扩大螺距机构,可获得纵向和横向进给量各64种。
5. 刀架空行程快速机动传动链在溜板箱中,通过快速电动机,由牙嵌式双向离合器M8和M9控制方向,使刀架实现纵向和横向快进快退。
由超越离合器M6和安全离合器M7保证实现高速转动。
传动路线表达式为:89M M 22⎧⎫---⎨⎬⎩⎭134快速移动电动机--XX-XXI 99(纵向)刀架(横向)。