汽车发动机新产品开发中的浪费与精益方法研究
精益生产与研发

精益生产与研发1. 简介精益生产与研发是一种管理方法,旨在通过优化生产和研发流程,最大程度地减少浪费,并提高产品质量和创新能力。
本文将详细介绍精益生产与研发的概念、原则和实施步骤。
2. 精益生产精益生产是一种源于日本丰田汽车公司的生产管理方法,也被广泛应用于其他制造业。
其核心思想是通过消除浪费、提高生产效率和质量,最终实现产品交付的稳定和快速。
2.1 浪费的分类在精益生产中,浪费被定义为任何不增加价值的活动、过程或资源。
根据丰田生产系统的分类,浪费可以分为以下几种类型:1.过产出:超出需求的生产,在库存和资金上产生浪费。
2.库存:过多的待加工产品、半成品或原材料,增加了成本和库存风险。
3.运输:不必要的运输和搬运,增加了交付时间和成本。
4.动作:不必要的动作或步骤,增加了生产时间和劳动成本。
5.待机:机器或设备无效运转,没有生产产值。
6.过程:不必要的工序或过程,增加了生产时间和成本。
7.库位:因不正确摆放物品导致时间浪费和寻找困难。
8.产品缺陷:制造和交付出的次品或不合格产品,增加了返工和成本。
2.2 精益生产的原则精益生产遵循以下几个核心原则,帮助企业最大限度地减少浪费,提高生产效率和产品质量:1.自动化:通过引入自动化技术,实现生产流程的标准化,提高生产效率和质量。
2.按需生产:根据市场需求和客户订单量进行生产,避免过产出和库存浪费。
3.连续流程:通过优化产品流动路径,实现生产过程的连续性和稳定性。
4.客户价值导向:根据客户需求和期望,不断改进产品和服务,提供更高的价值。
5.持续改进:通过数据分析和团队合作,持续改进生产流程和产品质量。
3. 精益研发精益研发是精益生产方法在研发领域的应用,旨在提高研发过程的效率和创新能力。
精益研发强调团队合作、迭代开发和客户导向,帮助企业快速推出高质量的创新产品。
3.1 精益研发的原则精益研发与精益生产有许多相同的原则,但也有一些针对研发过程的特殊原则:1.快速迭代:采用迭代开发模式,快速构建、测试和调整产品原型,及早发现和解决问题。
精益求精方法如何提高产品创新能力
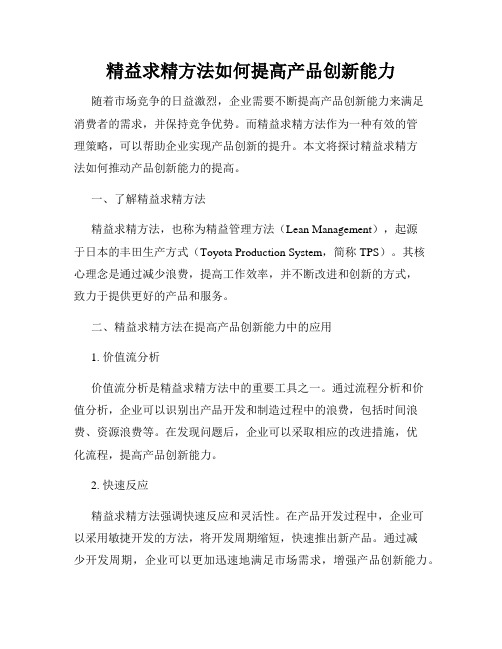
精益求精方法如何提高产品创新能力随着市场竞争的日益激烈,企业需要不断提高产品创新能力来满足消费者的需求,并保持竞争优势。
而精益求精方法作为一种有效的管理策略,可以帮助企业实现产品创新的提升。
本文将探讨精益求精方法如何推动产品创新能力的提高。
一、了解精益求精方法精益求精方法,也称为精益管理方法(Lean Management),起源于日本的丰田生产方式(Toyota Production System,简称TPS)。
其核心理念是通过减少浪费,提高工作效率,并不断改进和创新的方式,致力于提供更好的产品和服务。
二、精益求精方法在提高产品创新能力中的应用1. 价值流分析价值流分析是精益求精方法中的重要工具之一。
通过流程分析和价值分析,企业可以识别出产品开发和制造过程中的浪费,包括时间浪费、资源浪费等。
在发现问题后,企业可以采取相应的改进措施,优化流程,提高产品创新能力。
2. 快速反应精益求精方法强调快速反应和灵活性。
在产品开发过程中,企业可以采用敏捷开发的方法,将开发周期缩短,快速推出新产品。
通过减少开发周期,企业可以更加迅速地满足市场需求,增强产品创新能力。
3. 持续改进持续改进是精益求精方法的核心理念之一。
企业应该建立一个积极的改进文化,鼓励员工提出改进建议,并及时跟进和实施。
通过持续改进,企业可以不断优化产品设计和制造流程,提高产品创新能力。
4. 跨部门协作精益求精方法倡导跨部门协作和团队合作。
在产品开发过程中,不同部门需要密切合作,分享信息,共同解决问题。
通过加强协作,企业可以提高创新能力,将更好的产品带给消费者。
5. 实施标准化标准化是精益求精方法的重要手段之一。
通过制定标准化流程和工艺,企业可以提高生产效率,并减少错误和浪费。
标准化还可以帮助企业提升产品质量和一致性,提高产品创新能力。
三、精益求精方法在某企业产品创新能力提升中的应用案例以某汽车制造企业为例,通过引入精益求精方法,有效提升了产品创新能力。
浅谈发动机装配精益生产线的工艺设计规划
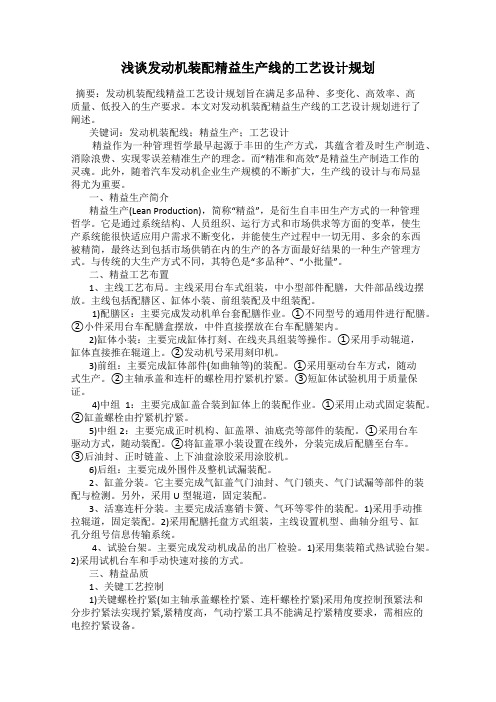
浅谈发动机装配精益生产线的工艺设计规划摘要:发动机装配线精益工艺设计规划旨在满足多品种、多变化、高效率、高质量、低投入的生产要求。
本文对发动机装配精益生产线的工艺设计规划进行了阐述。
关键词:发动机装配线;精益生产;工艺设计精益作为一种管理哲学最早起源于丰田的生产方式,其蕴含着及时生产制造、消除浪费、实现零误差精准生产的理念。
而“精准和高效”是精益生产制造工作的灵魂。
此外,随着汽车发动机企业生产规模的不断扩大,生产线的设计与布局显得尤为重要。
一、精益生产简介精益生产(Lean Production),简称“精益”,是衍生自丰田生产方式的一种管理哲学。
它是通过系统结构、人员组织、运行方式和市场供求等方面的变革,使生产系统能很快适应用户需求不断变化,并能使生产过程中一切无用、多余的东西被精简,最终达到包括市场供销在内的生产的各方面最好结果的一种生产管理方式。
与传统的大生产方式不同,其特色是“多品种”、“小批量”。
二、精益工艺布置1、主线工艺布局。
主线采用台车式组装,中小型部件配膳,大件部品线边摆放。
主线包括配膳区、缸体小装、前组装配及中组装配。
1)配膳区:主要完成发动机单台套配膳作业。
①不同型号的通用件进行配膳。
②小件采用台车配膳盒摆放,中件直接摆放在台车配膳架内。
2)缸体小装:主要完成缸体打刻、在线夹具组装等操作。
①采用手动辊道,缸体直接推在辊道上。
②发动机号采用刻印机。
3)前组:主要完成缸体部件(如曲轴等)的装配。
①采用驱动台车方式,随动式生产。
②主轴承盖和连杆的螺栓用拧紧机拧紧。
③短缸体试验机用于质量保证。
4)中组1:主要完成缸盖合装到缸体上的装配作业。
①采用止动式固定装配。
②缸盖螺栓由拧紧机拧紧。
5)中组2:主要完成正时机构、缸盖罩、油底壳等部件的装配。
①采用台车驱动方式,随动装配。
②将缸盖罩小装设置在线外,分装完成后配膳至台车。
③后油封、正时链盖、上下油盘涂胶采用涂胶机。
6)后组:主要完成外围件及整机试漏装配。
汽车发动机的燃烧控制策略改进
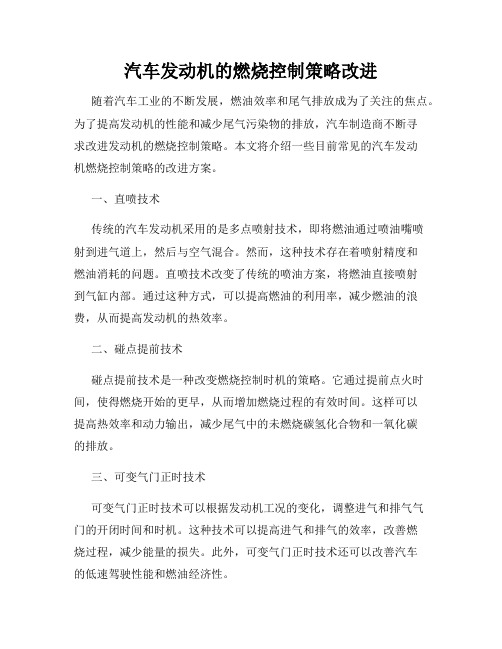
汽车发动机的燃烧控制策略改进随着汽车工业的不断发展,燃油效率和尾气排放成为了关注的焦点。
为了提高发动机的性能和减少尾气污染物的排放,汽车制造商不断寻求改进发动机的燃烧控制策略。
本文将介绍一些目前常见的汽车发动机燃烧控制策略的改进方案。
一、直喷技术传统的汽车发动机采用的是多点喷射技术,即将燃油通过喷油嘴喷射到进气道上,然后与空气混合。
然而,这种技术存在着喷射精度和燃油消耗的问题。
直喷技术改变了传统的喷油方案,将燃油直接喷射到气缸内部。
通过这种方式,可以提高燃油的利用率,减少燃油的浪费,从而提高发动机的热效率。
二、碰点提前技术碰点提前技术是一种改变燃烧控制时机的策略。
它通过提前点火时间,使得燃烧开始的更早,从而增加燃烧过程的有效时间。
这样可以提高热效率和动力输出,减少尾气中的未燃烧碳氢化合物和一氧化碳的排放。
三、可变气门正时技术可变气门正时技术可以根据发动机工况的变化,调整进气和排气气门的开闭时间和时机。
这种技术可以提高进气和排气的效率,改善燃烧过程,减少能量的损失。
此外,可变气门正时技术还可以改善汽车的低速驾驶性能和燃油经济性。
四、缸内直喷和涡轮增压技术的结合将缸内直喷技术和涡轮增压技术相结合,可以进一步提高发动机的性能和燃油效率。
涡轮增压技术通过增加进气量,提高发动机的容积效率,使发动机的功率输出更高;而缸内直喷技术则能提高燃油的利用率,降低燃油消耗。
这两种技术的结合可以实现更高效的燃烧过程和更好的动力输出。
五、电动辅助技术电动辅助技术是目前被广泛研究和应用的一种燃烧控制策略。
它通过利用电动机辅助发动机工作,实现发动机的快速启动和停止,并提供额外的动力输出。
这种技术可以减少发动机的空转损失,提高部分负载下的燃油经济性。
六、混合动力技术混合动力技术是一种综合利用内燃机和电动机的技术。
它将发动机和电动机相互配合,通过对两者的控制和调节,实现最佳燃烧控制策略。
混合动力技术在提高燃油效率的同时,还可以减少尾气污染物的排放。
汽车发动机性能改进的方法与技巧
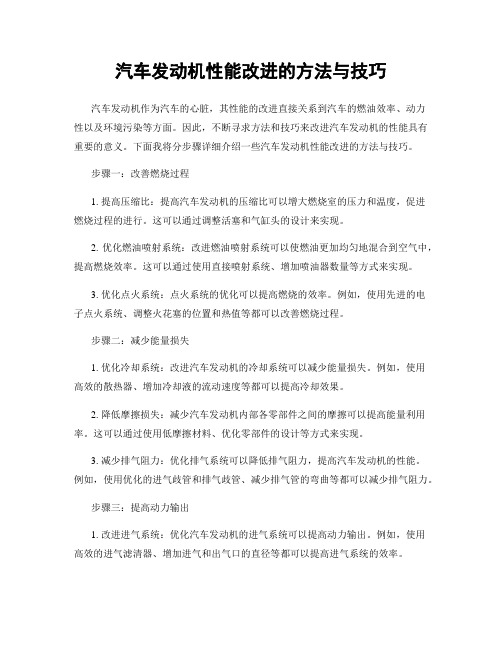
汽车发动机性能改进的方法与技巧汽车发动机作为汽车的心脏,其性能的改进直接关系到汽车的燃油效率、动力性以及环境污染等方面。
因此,不断寻求方法和技巧来改进汽车发动机的性能具有重要的意义。
下面我将分步骤详细介绍一些汽车发动机性能改进的方法与技巧。
步骤一:改善燃烧过程1. 提高压缩比:提高汽车发动机的压缩比可以增大燃烧室的压力和温度,促进燃烧过程的进行。
这可以通过调整活塞和气缸头的设计来实现。
2. 优化燃油喷射系统:改进燃油喷射系统可以使燃油更加均匀地混合到空气中,提高燃烧效率。
这可以通过使用直接喷射系统、增加喷油器数量等方式来实现。
3. 优化点火系统:点火系统的优化可以提高燃烧的效率。
例如,使用先进的电子点火系统、调整火花塞的位置和热值等都可以改善燃烧过程。
步骤二:减少能量损失1. 优化冷却系统:改进汽车发动机的冷却系统可以减少能量损失。
例如,使用高效的散热器、增加冷却液的流动速度等都可以提高冷却效果。
2. 降低摩擦损失:减少汽车发动机内部各零部件之间的摩擦可以提高能量利用率。
这可以通过使用低摩擦材料、优化零部件的设计等方式来实现。
3. 减少排气阻力:优化排气系统可以降低排气阻力,提高汽车发动机的性能。
例如,使用优化的进气歧管和排气歧管、减少排气管的弯曲等都可以减少排气阻力。
步骤三:提高动力输出1. 改进进气系统:优化汽车发动机的进气系统可以提高动力输出。
例如,使用高效的进气滤清器、增加进气和出气口的直径等都可以提高进气系统的效率。
2. 使用涡轮增压技术:涡轮增压可以通过压缩进气空气提高燃烧效率,从而提高汽车发动机的动力输出。
这可以通过安装涡轮增压器和中冷器来实现。
3. 优化排气系统:改进汽车发动机的排气系统可以提高排气效率,进而提高动力输出。
例如,使用高效的高性能消声器和尾气排放控制设备等都可以改进排气系统。
步骤四:提高燃油效率1. 提高燃油喷射系统的效率:优化燃油喷射系统可以提高燃油的利用率。
这可以通过使用高效的喷油器、调整喷油器的喷油角度和喷油时间等方式来实现。
汽车发动机研究报告

汽车发动机研究报告
近年来,汽车发动机技术得到了快速发展,不断地突破着各种技术难关。
本文旨在探讨汽车发动机研究的现状和未来发展趋势。
目前,汽车发动机的研究主要集中在以下几个方面:
一、燃烧技术的研究。
燃烧技术是发动机性能的核心,它直接影响着发动机的动力、经济性和环保性。
目前,各大汽车厂商都在致力于研究如何使燃烧更加充分、高效,从而提高发动机的功率和燃油经济性。
例如,研究新的燃烧室设计、燃油喷射技术等,都可以有效提升燃烧效率。
二、轻量化技术的研究。
随着环保理念的深入人心,越来越多的汽车厂商开始关注汽车的轻量化问题。
轻量化技术可以有效降低汽车的油耗和排放,同时也可以提高汽车的性能和安全性。
目前,汽车轻量化的主要手段包括使用轻质材料、优化车身结构、采用小型化发动机等。
三、新能源技术的研究。
随着能源危机的日益加剧和环保意识的逐渐增强,新能源汽车成为了汽车行业的一大热点。
新能源车主要分为纯电动车和混合动力车两种类型。
目前,各大汽车厂商都在积极探索新能源技术,不断研发更加高效的电池和电控系统,以实现更长的续航里程和更好的性能。
总体而言,汽车发动机技术的发展趋势是多元化、高效化和环保化。
未来,发动机研究将继续向更加先进、智能化的方向发展,为汽车行业的可持续发展做出更大的贡献。
精益求精方法提高研发创新力

精益求精方法提高研发创新力研发创新是企业发展的核心驱动力之一,通过不断改进与提升研发创新能力,企业可以在市场竞争中获得更大的优势。
而精益求精方法作为一种有效的管理工具,可以帮助企业提高研发创新力。
本文将探讨精益求精方法在提高研发创新力方面的应用。
一、了解精益求精方法精益求精方法是一种追求极致的管理模式,其目的是通过不断优化流程和提高绩效来实现持续改进。
它强调通过精确的数据分析和深入的问题分析,识别和消除各种浪费现象,从而提高效率和创新力。
二、精益求精方法在研发创新中的应用1. 结合客户需求进行迭代式创新精益求精方法强调将客户需求放在首位,通过不断与客户进行反馈和沟通,了解并满足他们的需求。
研发团队可以采用迭代式的创新模式,快速跟进用户的反馈和需求变化,并及时进行调整和改进。
这样一来,企业可以更好地解决客户问题,提供满足客户需求的产品和服务。
2. 引入精确的数据分析精益求精方法倡导以数据为基础进行决策,通过精确的数据分析来指导研发创新。
研发团队可以采集和分析大量的数据,从中发现问题和机会,并作出相应的调整和改进。
这样可以降低决策的风险,并提高研发创新的效果。
3. 推行持续改进文化精益求精方法强调持续改进的重要性,要求企业建立一种持续改进的文化氛围。
在研发过程中,鼓励团队成员不断思考和探索,主动提出改进意见,并积极参与改进措施的实施。
只有不断寻找和解决问题,才能实现研发创新的突破。
4. 优化研发流程精益求精方法提供了丰富的工具和方法,可以帮助企业优化研发流程,提高效率和创新力。
例如,价值流图可以帮助企业识别并消除研发过程中的浪费和瓶颈,而精益创业画布则可以帮助企业清晰地定义产品的核心价值和关键指标。
三、案例分析:丰田生产方式丰田生产方式作为精益求精方法的经典案例,成功地应用在研发创新中,产生了巨大的影响。
丰田通过减少浪费和优化流程,将汽车生产周期缩短到了极致。
同时,丰田也强调员工的主动参与和持续改进的文化,使得每个员工都能积极思考和提出改进意见。
精益管理:7大浪费的产生原因和消除方法

精益管理:7大浪费的产生原因和消除方法今天和大家一起聊聊丰田所说的7种浪费以及消除浪费的步骤和对策,值得制造业同仁学习。
跟你的供应商一起阅读,让大家尊重自然资源,消除浪费,提升利润率。
丰田的七种浪费1.生产过剩的浪费一心想要多销售而大量生产,结果在人员、设备、原材料方面都产生浪费。
在没有需求的时候提前生产而产生浪费。
2.不合格产品的浪费在生产过程中出现废品、次品,会在原材料、零部件、返修所需工时数、生产这些不合格产品所消耗的资源方面产生浪费。
3.待工的浪费在进行机械加工时,机器发生故障不能正常作业,或因缺乏零部件而停工等活等,在这样的状态下所产生的浪费都是停工等活的浪费。
4.动作上的浪费不产生附加价值的动作、不合理的操作、效率不高的姿势和动作都是浪费。
5.搬运的浪费除去准时化生产所必需的搬运,其他任何搬运都是一种浪费。
比如在不同仓库间移动、转运、长距离运输、运输次数过多等。
6.加工本身的浪费把与工程的进展状况和产品质量没有任何关系的加工当做是必要的加工而进行操作,此种状况下所产生的浪费。
7.库存的浪费因为原材料、零部件、各道工序的半成品过多而产生的浪费。
这些东西过度积压还会引起库存管理费用的增加。
消除七种浪费的步骤步骤①:在需要的时候适时生产需要的产品可以排除生产过剩的浪费,这需要具备严格管理的思想。
步骤②:如果经常产生不合格产品,抑制生产过剩是很困难的。
我们要消除不合格产品,消除制造不合格产品的浪费。
步骤③:对于停工等活,只要明白其要点就很容易改善。
消除停工等活的浪费,有效利用人力资源。
步骤④~⑥可以根据消除浪费的着眼点从可以实施的部分开始实施。
步骤④:对于动作的浪费,如果减少工时数(人数×时间)将会对消除浪费产生很大影响。
但是,即使是进行动作分析,清除了一些细小的浪费,也会被其他的问题所掩盖,所以必须注意。
步骤⑤:要消除搬运的浪费,就要在搬运距离和搬运次数等方面加以改进。
步骤⑥:对于加工过程中本身的浪费,要认识到不产生附加价值的一切东西都是浪费。
发动机研究报告
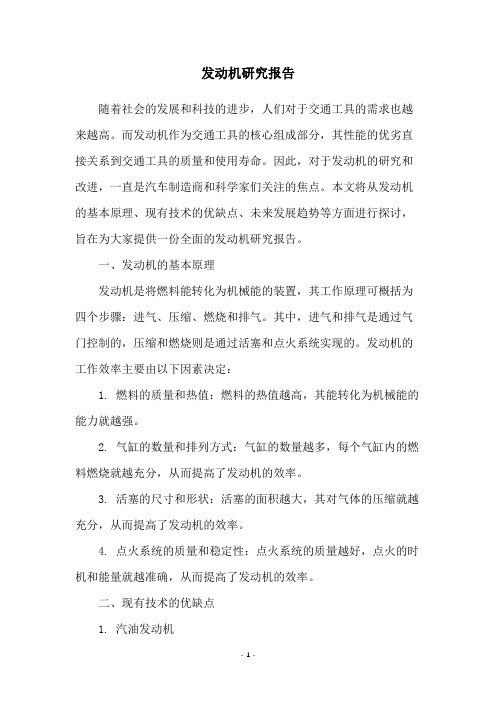
发动机研究报告随着社会的发展和科技的进步,人们对于交通工具的需求也越来越高。
而发动机作为交通工具的核心组成部分,其性能的优劣直接关系到交通工具的质量和使用寿命。
因此,对于发动机的研究和改进,一直是汽车制造商和科学家们关注的焦点。
本文将从发动机的基本原理、现有技术的优缺点、未来发展趋势等方面进行探讨,旨在为大家提供一份全面的发动机研究报告。
一、发动机的基本原理发动机是将燃料能转化为机械能的装置,其工作原理可概括为四个步骤:进气、压缩、燃烧和排气。
其中,进气和排气是通过气门控制的,压缩和燃烧则是通过活塞和点火系统实现的。
发动机的工作效率主要由以下因素决定:1. 燃料的质量和热值:燃料的热值越高,其能转化为机械能的能力就越强。
2. 气缸的数量和排列方式:气缸的数量越多,每个气缸内的燃料燃烧就越充分,从而提高了发动机的效率。
3. 活塞的尺寸和形状:活塞的面积越大,其对气体的压缩就越充分,从而提高了发动机的效率。
4. 点火系统的质量和稳定性:点火系统的质量越好,点火的时机和能量就越准确,从而提高了发动机的效率。
二、现有技术的优缺点1. 汽油发动机汽油发动机是目前使用最为广泛的发动机之一。
其优点是功率大、噪音小、加速快、排放少等。
但是,汽油发动机的缺点也很明显,比如油耗高、环保性能差、维护成本高等。
2. 柴油发动机柴油发动机的优点是燃油效率高、动力强劲、维护成本低等。
但是,柴油发动机也存在一些缺点,比如噪音大、排放污染物多、启动困难等。
3. 混合动力发动机混合动力发动机是汽油发动机和电动机的结合体,其优点是燃油效率高、排放少、动力强劲等。
但是,混合动力发动机的成本较高、重量较大等缺点也不容忽视。
4. 燃料电池发动机燃料电池发动机是利用氢气和氧气进行化学反应产生电能,从而驱动发动机工作的一种新型发动机。
其优点是环保性能好、燃料效率高等。
但是,燃料电池发动机的成本高、储氢技术尚未成熟等问题也需要解决。
三、未来发展趋势未来发动机的发展趋势主要集中在以下几个方面:1. 新能源发动机的研究和应用:随着环保意识的不断提高,新能源发动机的研究和应用将成为未来的主流趋势。
柔性、精益、零缺陷 第四届汽车发动机现代制造技术国际研讨会纪实(下)
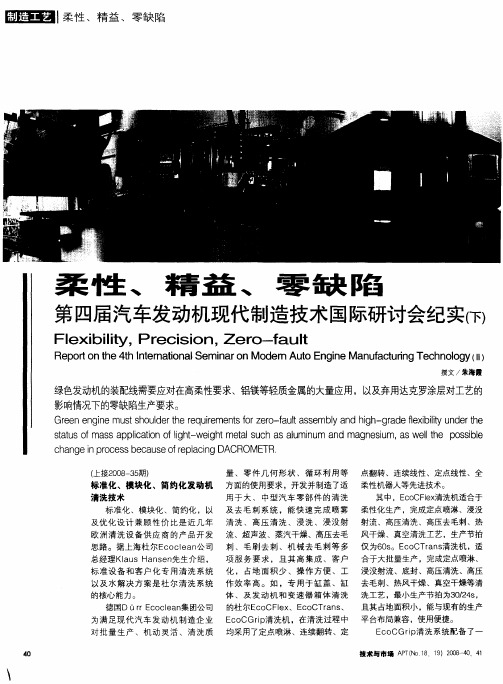
且 其 占地 面积小 ,能 与现 有的 生产
柔 性 精 益 零 缺 陷
Fl bit ,I r exl i Jr exi l y,P eci on, er b ec si , Z o aul o-f t
Re o nt e 4 h It r a in l mia n Mo e Auo E gn n f du n c n lg 1 p  ̄o t e n t a h n o Se n r d m t n ie Ma ua d gTe h oo y( ) o 1
撰文 / 朱海霞
第 四届汽车发动机现代 制造技术 国际研讨会纪实() 下
绿色发动机的装配线需要应对在高柔性要求、铝镁等轻质金属的大量应用,以 及弃用达克罗涂层对工艺的 影响情况下的零缺陷生产要求。
Gre n i s s o le e rq i me t r eo fu s e l a d h h g a ef xbl n e e e ne gn mu t h u rh ur e d t e e nsf r-a la s mby n i - rd e iiyu d rh o z t g l i t t sau f s p lai fih- ih tl u ha Imiu a d ma n s m. swelh p s il ttso ma sa pi t no g tweg t c o l mea s c sau n m n g e i u a l e o sbe t c a g rc s e a s fe l igD CR h n ei p o e sb c u eo pa n A OME R n r c T .
精益研发的各个环节存在十大浪费
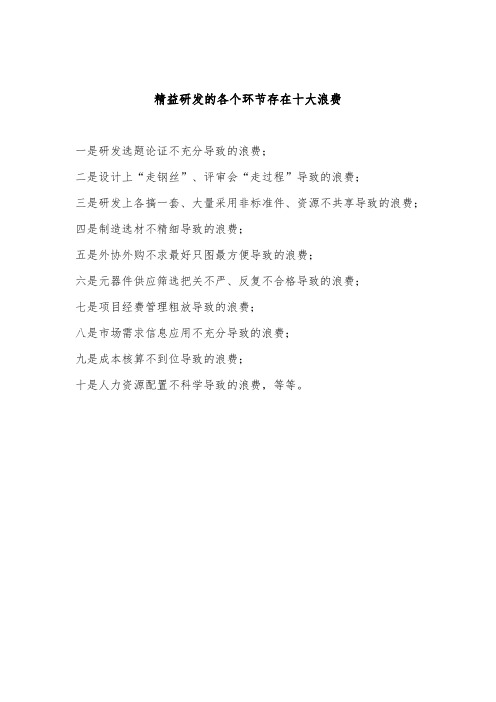
精益研发的各个环节存在十大浪费
一是研发选题论证不充分导致的浪费;
二是设计上“走钢丝”、评审会“走过程”导致的浪费;
三是研发上各搞一套、大量采用非标准件、资源不共享导致的浪费;四是制造选材不精细导致的浪费;
五是外协外购不求最好只图最方便导致的浪费;
六是元器件供应筛选把关不严、反复不合格导致的浪费;
七是项目经费管理粗放导致的浪费;
八是市场需求信息应用不充分导致的浪费;
九是成本核算不到位导致的浪费;
十是人力资源配置不科学导致的浪费,等等。
精益生产及八大浪费

特性
时间
12
实际的特性
丰田汽车生产系统改变系统过
程中的阻碍因素,通过更有效 的使用输入来改进输出
业务流程 (输入)
系统 (阻碍因素)
特性指数 (输出)
人员和过程
可变性
质量
原材料
成本
信息
浪费
非弹性/非灵活性
交货期
13
TPS的基本: 人们能看到的和看
不到的
▪ 过程同步 (例如:平衡的
生产现况板)
▪ Just in time 过程 (例如:
战争的约束引起了消沉
▪ 丰田面临着历史上最
大的罢工 由于丰田和 员工之间的工资纠纷
丰田建立
193 3
精益生产
二次大 战
主要的罢工194 68丰田需要在低产量的情况下获得大规模生产的效率,这就迫使 他们发明了丰田生产体系(TPS)
丰田建立
193 3
§ 日本的公司由于低生产性十分消沉 (麦克阿瑟说 是本只是美
8
Hudson
Renault
9
Austin
BL
10
Renault
Peugeot
2002 市场利润*
2002
USD ’000 millions
GM
27.9
Ford
22.7
Toyota
101.9
Renault/Niss VWan
64.9 *
17.8
*
Daimler/Chry Peusgleort
33.6 10.3
交货期
*Standard Operating Procedures
18
• 建立团队队长的名单
组织和能力建设
汽车发动机论文3000字

汽车发动机节能技术浅析摘要:本文通过对发动机的节能原理进行分析,提出了一些节约发动机燃油消耗的措施,对中国汽车节能提出了发展方向。
关键词:节能;原理;措施;发展一、发动机节能的原理1 提高充气效率(1)减小进气系统的流动损失。
①减小进气门处的流动损失。
可通过增大进气门的直径,选择合适的排气门直径;增加气门的数目,采用小气门;改善进气门处流体动力学性能,减小气门处流动损失;采用S(活塞形成)/D(缸径)值较小的发动机等措施可以减小进气门处的流动损失。
②减小整个进气管道的流动阻力。
进气道应该有足够的流通截面积、表面光滑、拐弯小、多段通道连接要对中;进气管应该有足够的流通截面积、表面光洁,避免急转弯和流通截面的突然变化;空气滤清器的阻力应随结构和使用时间的延长而不同。
(2)减少对新鲜充气量的加热。
凡是能降低活塞、气门等热区零件的温度和减小接触面积的措施都是有利于减小对新鲜充气量的加热。
(3)减小排气系统的阻力。
减少排气系统中排气门座、排气道、排气管、排气消声器的阻力,对降低排气压力、减小排气损失均有利。
(4)合理选择配气相位。
配气相位是否合理主要根据以下几个方面来判断。
①充气效率高,保证发动机的动力性能,主要由进气门迟闭角决定。
②必要的燃烧室扫气,以保证降低高温零件的热负荷,使发动机运行可靠,主要由进气门迟闭角决定。
③合理的排气温度,主要由排气提前角决定。
④较小的换气损失、以保证发动机的经济性,主要由进排气门重叠角决定。
2 减小机械损失可从几个方面着手(1)降低活塞、活塞环、连杆等往复运动机件的摩擦和质量。
(2)降低滑动部件的滑动速度。
(3)减少润滑油的搅拌阻力。
(4)改良润滑油,使其低粘度化。
(5)合理选择摩擦零件的材料。
二、发动机节能的措施1 发动机稀燃技术也叫发动机稀薄燃烧技术,指采用发动机的实际空燃比远大于理论空燃比的情况下进行的具有良好动力性、经济性和排放行的燃烧技术。
实现的技术途径:(1)实现稀燃混合气。
研发、制造过程中的七个浪费

制造过程中的7个浪费
①【过量生产的浪费】 ・・・过量生产有两种:一种是在所规定的时间内
生产了数量过剩的产品,一种是比规定的时间提前完成了生产任务。
制造过程中的7个浪费
⑤【库存的浪费】 ・・・由于过多制造造成的浪费。过多的制造作业等待 (预测生产、集中生产)等; ⑥【动作的浪费】 ・・・过快的组装超出节拍时间产生的浪费 。为作业者产生多余的动作
产生) ⑦【生产不合格的浪费】 ・・・质量问题的发生,连续制造出不合格件的 浪费。没有真正的解决原因只是就问题进行了处置(质量意识差)、没有努 力的作提升工序保证能力的工作等;
②【作业等待的浪费】 ・・・人和设备、人和人、人和物的工作不均衡的 时候发生的浪费。如设备故障停止 、过量生产造成的顺序等待等。
③【搬运的浪费】 ・・・ ・ 布局、工序编排的不合理造成的浪费。如过
长的运送距离 、临时放置等; ④【加工本身的浪费】 ・・・作为辅助作业,现有状态、条件下发生的浪 费。如工件的装卸等;
研发、制造过程中的七个浪费
TPS推进部 08年9月
开发设计流程中的7个浪费
①【过量生产的浪费】・・・指令下发前开始着手、完成了自工序的 业务等; ②【作业等待的浪费】・・・等待必要的信息、判断、决定等; ③【搬运的浪费】・・・・・信息等的过渡散发所需要的时间等;
④【加工本身的浪费】・・・・・现有产品的再设计、重复业务等;
中国汽车发动机企业的精益设计
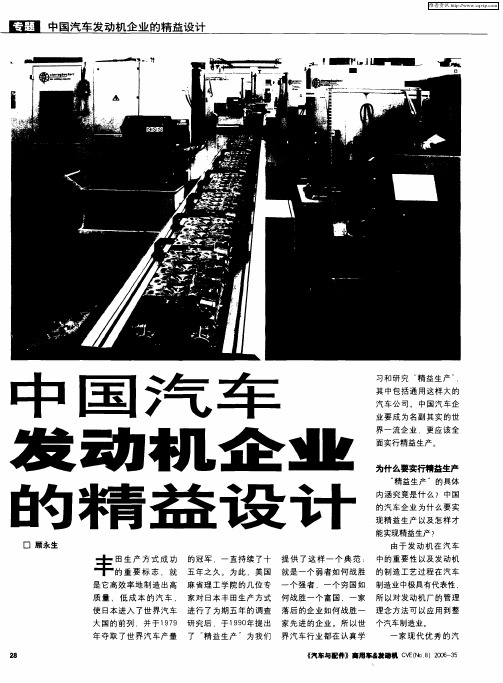
・采用精益 的工作制度可 厂应严格控制工艺投资 精益
大 的 代 价 。 目前 中 国 的 汽 车 以 保 证 设 备 的开 动 率 达 到 最 采购,降低制造成本 ;实行精
中国的许 多汽 车企 业很 早 制 造企业精益建 厂方针 是工 大 。 国 外 的 发 动 机 厂设 备 实 益 物流 ;
部 门的精益管理。
分 步 实 施 、滚 动 发 展 “ 才 是 的 工作制 度 j
・ 另外 新建 企业 必须 严
精益设计是精益企业的源 最 适 合 中 国 国 情 的 最 经 济 、
变化能 力强 ;3在技 术和管 理 头 .是决定精益企业命运的关 最 稳 妥 风 险 最 小达 到 经 济 格 控 制 自制 率 , 以发 动 机 厂 . 等 方面应是 国 内领 先且与 国外 键环节 ,因此 精益企业要实 规 模 的最佳 模式 。
一
个 强 者 一 个 穷 国如 制造 业中极具 有代表 性
家对 日本 丰 田 生产 方 式 何 战胜 一 个 富 国 一家 所 以对 发动 机 厂 的 管理
使 日本 进入 了世 界 汽 车 进 行 了 为期 五年 的调 查 落后 的企 业 如何 战胜 一 理 念 方 法可 以应 用 到 整
中 国 的 汽 车 工 业 在 建 厂 步 , 以后 分 别 为6 一1 — 化生产 (I ,消灭 一切浪 费 , —1 O 5 J T)
优 秀都是十 分重要 的 ,所 以实 的 规 模 和 工 厂 设 计 方 面 确 实 2 -2 —3 万 辆 ; 0 5 0
施 “ 精益生产”是所有汽车制 走 过 很 多 弯 路 , 并且 付 出 很
一
为 例 ,可 以只 加 工缸 体 、 缸
浅析如何减少样车试制中的物料浪费

FRONTIER DISCUSSION | 前沿探讨浅析如何减少样车试制中的物料浪费桂文池上汽通用汽车有限公司 上海市 201201摘 要: 在产品日益同质化的今天,建立自己的研发中心已经成为车企的发展趋势。
随着中国汽车市场逐渐走向饱和,价格竞争成为各企业产品之间的主要竞争手段。
如何实现减少浪费,特别是减少研发过程中的浪费也成为各大企业关注的重中之重。
本文不同于传统研究浪费的文章,从比较宏观的角度说明减少浪费的一般途径,而是根据实际物料管理工作中的经验,另辟蹊径,着重研究样车试制中各环节对减少浪费的影响,并以此发散到与这一过程相关的其它方面。
通过结合比较容易被忽略但是的确对减少浪费有效的方面入手,分析阐述如何更好地减少样车试制中的物料浪费,从而达到控制成本的目的。
关键词:样车试制;减少浪费;物料管理1 引言今年开春,汽车企业似乎进入了寒冬,一系列的降价和销量的大幅缩水,让控制浪费的需求比以往更加强烈。
通常,汽车企业主要通过以下几个环节来实现:研发环节、生产过程、物流环节、业务流程再造、信息技术应用、企业文化等[1]。
本文着重从研发环节的样车试制出发,以工作流为导向,分析整车(vehicle)和试验需求(buck/kits)从搜集需求到交付过程中可以实现的控制浪费的途径,为减少浪费提供新视角的工作方向。
2 需求搜集和确认阶段某平台某项目样车试制开始前,需要搜集用户的需求数量和需求时间。
各个部门根据验证需求和计划提出该阶段需要的Vehicle 和Buck/kits需求。
在此阶段,可以通过以下几点,减少物料浪费:优化配置:对车子没有特殊颜色和配置需求的用户,可以跟有特定需求的用户合并,减少试制中无谓的多配置和多颜色所带来的成本增加;共享样车:由于每个用户对车子试验需求的部分不同,可以综合大家的试验计划和对车的影响,将部分用户的用车需求合并,减少样车的制造数量;严格约束用户根据试验节点分开提出需求,样车试制一般分为六个阶段,分别是:Mule、IV、OTS、PPV、NS、S。
精益生产管理八大浪费与解决方法(详细版)

精益生产管理八大浪费与解决方法八大浪费是丰田生产方式中非常重要的一个观念。
丰田人认为要消除浪费,持续改善,企业才能保持良性运转,竞争力才会提升。
在丰田改善是探入人心的,有个说法就是跟他们谈话5分钟没有听到他们讲3次改善就不算丰田人。
改善的对象是浪费,认识浪费是改善的第一步,企业现场林林总总,哪些是有价值的,哪些是浪费,不是一般人可以一目了然的.丰田人在长期作业和改善过程中对于浪费的内容进行了总结,共七种,被称为七种浪费.它们分别是制造过早(多)的浪费、库存的浪费、不良修正的浪费、加工过剩的浪费、搬运的浪费、动作的浪费、等待的浪费共七种。
后来人们又加了一种浪费-管理的浪费,合称八种浪费.下面我们从实用性角度剖析这八种浪费。
一、精益生产管理中制造过早(多)的浪费定义:所谓制造过早(多)就是前制程制造太早/过多,大于客户(或后制程)当期的最小需要量。
制造过早(多)浪费是八大浪费中的首恶,在精益生产中则被视为最大的浪费。
福特式思维告诉大家,在同样的时间内,生产量越多,效率越高,成本越低,企业越赚钱,所以企业自然有大批量连续生产的初始动力。
作为一个整体的企业是如此,那么企业内各部门也是如此,特别是在一些制程较短,关联性较低的企业中,普遍实施计件工资,那么从最基础的员工开始就有多做、早做,甚至偷做的动力,在这种情况下,告知企业里所有人早(多)做是罪恶当然得不到掌声回应.那么我们就来看看制造过早(多)的浪费。
制造过早(多)浪费的后果主要有三大类。
1.直接财务问题。
表现为库存、在制品增加,资金回转率低,制造时间变长,占用资金及利息,会造成库存空间的浪费,在现金流量表上很明显。
2.产生次生问题.会产生搬运、堆积的浪费;先进先出的工作产生困难;产品积压造成不良发生,物流阻塞制程时间变长,现场工作空间变小,有滞留在库的风险,有不良品的风险.3。
掩盖问题.为什么“制造过早(多)浪费是八大浪费中的首恶,在精益生产中则被视为最大的浪费”?因为它带给人们一个安心的错觉,掩盖了各种问题,以及隐藏了由于等待所带来的浪费,没有改善的动力,失去了持续改善的时机。
精益求精方法改善产品设计

精益求精方法改善产品设计在当今竞争激烈的市场环境中,产品设计的质量和效率对企业的成功至关重要。
为了不断提升产品设计的水平,许多公司采用了精益求精的方法。
精益求精是一种追求卓越的理念,通过不断挑战自己,寻求持续改进,以实现更高的质量标准。
本文将介绍精益求精方法在产品设计中的应用,并探讨如何借助这种方法改善产品设计。
首先,精益求精方法着重于降低浪费,提高效率。
在产品设计领域,浪费的存在通常会导致不必要的成本和时间的浪费。
精益求精方法通过对生产过程进行分析和优化,识别和消除各种浪费,从而提高产品设计的效率。
例如,通过精简设计流程,减少冗余步骤和重复工作,可以节省时间和资源,加速产品的开发周期。
此外,精益求精方法还鼓励团队成员合理利用资源,避免过度投入一些不必要的环节,实现资源的最大化利用。
其次,精益求精方法注重持续改进和学习。
在设计产品的过程中,难免会出现一些问题和挑战。
精益求精方法鼓励团队对问题进行深入的分析,找出根本原因,并通过团队合作找到解决方案。
此外,精益求精方法还强调学习和知识分享的重要性。
通过从错误和失败中吸取教训,不断改进设计方法和流程,可以提高产品设计的质量和创新能力。
精益求精方法还鼓励团队成员积极参与培训和学习机会,持续提升自身的设计能力和知识水平。
此外,精益求精方法倡导团队合作和沟通。
在产品设计过程中,涉及到多个团队成员的合作和协调。
精益求精方法强调团队成员之间的有效沟通和协作,以提高设计效率和减少误解。
团队成员应该定期开展会议和讨论,分享想法和经验,及时解决问题。
此外,通过定期的评估和反馈,团队可以了解自身所面临的挑战和问题,及时进行调整和改进。
最后,精益求精方法强调客户需求的关键性。
产品设计的最终目标是满足客户的需求和期望。
精益求精方法鼓励设计团队与客户紧密合作,深入了解客户的需求,并将其融入到产品设计的各个环节中。
通过不断与客户进行沟通和反馈,团队可以及时调整设计方向,确保最终的产品能够完全符合客户的期望和需求。
汽车发动机整改报告书

汽车发动机整改报告书尊敬的领导:我司日前接受贵单位委托,对汽车发动机进行了整改工作。
在此,特向贵单位汇报整改情况,以供参考。
1. 整改背景:根据贵单位的反馈,汽车发动机出现一些问题,例如燃油消耗率高、噪音过大等,严重影响了汽车的性能和使用效果。
为了解决这些问题,我司积极响应,派遣专业团队进行了整改工作。
2. 整改目标:(1)降低燃油消耗率:通过改进燃烧系统、提高燃烧效率等方式,降低汽车的燃油消耗率。
(2)减少噪音:通过改进排气系统、降噪处理等手段,降低汽车发动机工作时产生的噪音。
(3)提高动力输出:通过调整进气系统、优化点火系统等方式,提高汽车的动力输出效果。
3. 整改措施及过程:(1)燃烧系统改进:优化喷油系统、进气系统等,使燃烧更充分,提高燃烧效率。
(2)排气系统改进:采用消声器、隔音材料等减少噪音产生,提升乘坐舒适度。
(3)点火系统优化:调整点火时机,提高点火能力,增加燃烧效率和动力输出。
(4)测试调试:在整改过程中,严格按照质量标准,对改装后的发动机进行了多项测试和调试,确保修复效果达到预期目标。
4. 整改成果:经过团队的不懈努力,整改取得了明显的效果,具体成果如下:(1)燃油消耗率降低了20%以上,使汽车的油耗性能得到了明显的提升。
(2)噪音降低了30%以上,提升了汽车的乘坐舒适度。
(3)动力输出增加了10%,使车辆的加速性能得到了明显的提升。
5. 后续建议:(1)定期维护:建议贵单位对汽车发动机进行定期的检查和维护,以保证其正常运行和长久使用。
(2)技术培训:为贵单位的相关人员提供发动机相关知识和维护技术的培训,提高其对汽车发动机的认知和处理能力。
以上是我司对汽车发动机的整改情况汇报,如有任何问题或需要进一步的合作,敬请告知。
谢谢!此致敬礼XX汽车维修有限公司日期:。
- 1、下载文档前请自行甄别文档内容的完整性,平台不提供额外的编辑、内容补充、找答案等附加服务。
- 2、"仅部分预览"的文档,不可在线预览部分如存在完整性等问题,可反馈申请退款(可完整预览的文档不适用该条件!)。
- 3、如文档侵犯您的权益,请联系客服反馈,我们会尽快为您处理(人工客服工作时间:9:00-18:30)。
汽车发动机新产品开发中的浪费与精益方法研究
杨 洁 上海交通大学机械与动力工程学院
摘 要:本文围绕精益产品开发,通过对汽车发动机新产品开发过程中的浪费现象进行识别并深入分析,有针对性的提出了精益方法的解决方案。
有利于车企提高发动机新产品开发效率,降低开发成本,增强企业竞争力。
关键词:发动机 新产品开发 浪费 精益
发动机新产品开发项目具有投资大、周期长、不可逆等高风险特点。
这使得绝大部分车企都要求发动机新产品开发项目缩短开发周期,提高开发效率,降低开发成本。
而“精益思想”创始者的丰田公司,从源头精准定位客户需求,让客户需求持续拉动开发价值流,有效调动资源,消除开发中的浪费,实现降本增效、提质提速,被誉为“世界上最赚钱的汽车企业”。
丰田的“精益思想”强调客户需求,强调价值,而识别价值的关键是识别浪费,本文就围绕丰田的精益产品开发,针对X车企在发动机新项目研发过程中的“浪费”现象进行深入分析,对于如何识别、消灭浪费进行剖析,并提供精益方法的解决思路。
一、浪费的基本概念
1.浪费的定义。
浪费可以概括为企业在整个产品开发过程中,所花费的时间和精力,从客户的角度来看,并没有产生任何增值效果。
2.浪费与精益开发的关系。
浪费与精益是一对矛盾,互为对立面。
精益开发的目的就是消灭浪费,通过价值流图分析、标准化等工具,对开发流程进行持续分析、标准化和改善,实现企业信息资源的有序流动,以达到科学决策、精管细控、降本增效的目的。
需要注意的是,精益开发是一个大量尝试、鼓励创新、柔性起止的非线性、多方向的活动,开发周期通常以月、年为单位,且有不同背景的人员参与,成果是以信息和知识构成的产品。
因此,浪费隐藏得更加隐秘,需要开发人员灵活运用各类精益工具来识别并加以应对。
二、识别X车企在发动机新产品开发过程中的浪费
1.过度设计。
过度设计存在两个方面:一方面由于前期对客户以及市场需求预估不明,以致无法锁定发动机开发配置,当后期配置调整,增加了更改成本以及验证时间。
另一方面是部分零件的设计结构强度偏强,造成发动机整体结构尺寸偏大,增加了设计成本和物料成本。
2.等待。
等待是产品开发中最普遍存在的浪费。
比如采购工程师要等工程部门发出SOR包才开始工作的串行工作方式;走纸质流程进行零件更改流转,需要工程师挨个找人签字,耗费1~2个月会签流转时间;CATIA设计权限较少,工程师需排队等候软件资源释放等。
3.冗余/重复的流程步骤。
在开发过程中,项目主管与工程师需向多方单独汇报设计状态和工作进度,造成冗余的重复汇报工作。
在与试验部门、工程师及供应商的咨询和确认过程中,累计了大量信息需要消化,易造成部分重复的试验验证,造成这些冗余/重复。
4.不正确的人员。
在大排量发动机开发项目初期,由于项目组没有完整的开发大排量发动机的项目经验,工程师缺乏相关知识经验的积累,只能摸着石头过河,造成开发效率较低。
5.库存。
在产品开发阶段,库存指的是各种信息排队等待处理,需要专人梳理鉴别,既耗时耗力又易造成信息延误、丢失。
比如设计发布时,工程师同时发布大量图纸与文档,造成技术主管待批文件很多,来不及处理。
工程师走工程更改流程时,各部门的更改协调员收集更改申请单后,统一时间进行批处理,引发库存压力。
6.废弃的知识。
在项目开发过程中,工程师们对各个零件做了对标分析,但是对标后的数据并没有有效的利用到零件开发中;而过程中总结的经验和知识也没能有效转化为更多人、更多项目的能力,重复犯错耗费资源、精力,易造成项目开发周期的延迟。
7.沟通障碍。
新项目是由多个研发中心派员参与,跨地域间的工程师主要依靠邮件和电话沟通,相对于面对面和联席会议,沟通效率较低。
三、利用精益方法消灭开发过程中的浪费
上述7种浪费虽广泛存在于开发的各个环节,但经过分类,主要集中在三大方面中:流程、工具、人员。
这三方面是相互整合、相互影响、不断演进的连贯系统,任何一方面的变化,必然会影响另外两方面。
因此,需要对整个开发过程进行精益再造,在恰当的时间、用恰当的人员、工具和技术,以完美高效的流程完成客户需求。
表1 浪费分类
1.流程:梳理价值流,再造新流程。
在开发过程中,出现浪费是不可避免的,但许多浪费并非技术原因而是管理问题。
解决问题的关键环节包括识别(价值流)-发现(浪费)-再造(开发流程)。
即通过价值流图分析,按照开发周期、交付时间、零件库存、信息流动等要素进行梳理,确立由消费者定义的价值,画出价值流图,推敲部门工作衔接中存在的浪费情况,随后有针对性的进行调整和优化,寻找真正的增值活动,再造均衡的产品开发流程。
此外,为了避免发动机开发后期出现大的设计更改,造成时间和成本的浪费,可在开发前期实施基于多方案的并行工程,由设计、工艺、质量管理、成本核算等人员组成并行工程项目小组,在前期共同验证多种方案,综合分析利弊得失,拿出最优秀的方案,而在“最优方案”执行过程中,由于小组成员从一开始就参与开发,因此能将“原汁原味”的信息提供给本部门的相关人员,从而保证了设计的质量,避免了大量的返工浪费。
2.工具:合理运用精益工具。
“工欲善其事,必先利其器”,企业要善于运用标准化和信息化工具来进行精益开发。
在标准化方面,比如工程师能重视并完善工程检查清单,在设计中能随时运用检查清单来指导零件设计。
同时,在设计评审环节,也要将清单纳入评审体系,工程师一一对标,一一销项,确保事无遗漏。
在信息化方面,通过完善信息管理系统,逐步减少纸质流程,节省等待时间,提高工作效率。
3.人员:完善知识体系,协同合作,追求卓越。
企业是由员工组成的,这就需要员工热爱工作,具有开阔的视野、专业的知识和卓越的技能。
因此需要企业致力于培养认同企业文化、追求卓越的技术精英,通过完善知识管理体系、业务培训机制以及严格的绩效考核,保持技术领先。
同时,鼓励工程师自我加压、自我完善、追求卓越。
此外,工程师也需要具备沟通协作能力和团队合作精神,打破部门壁垒,强化跨部门间的协同合作,从另一方面,也让人力资源得到充分利用。
四、结语
本文围绕精益开发,通过对X公司发动机新项目的具体分析,识别出隐藏在开发过程中的7种浪费现象,并有针对性的提出了解决方案。
实践证明,选择精益开发的项目管理方式,最大程度缩短产品开发周期,节约研发和物料成本,提高生产效率,满足客户越来越挑剔的个性化购车需求并显著提高车企适应市场的能力。
参考文献:
[1]顾佳然.汽车发动机项目投资管理模型的研究与开发[D].上海:上海交通大学,2011.
[2]James M. Morgan, Jeffrey K.Liker 著. 精益企业中国译. 丰田产品开发体系[M]. 北京:中国财政经济出版社,2008.
[3]艾伦 C·沃德(Allen C. Ward)著. 周健,赵克强译. 精益产品和流程开发[M]. 北京:机械工业出版社,2011.
[4]潘声平. 基于精益思想的产品研发项目管理方式研究[D].山东:山东大学,2012.
2016年·10月·下期经营管理者
学 术
理 论
经营管理者 Manager' Journal
81。