发动机轻量化途径及工艺创新
国外的发动机工艺研究
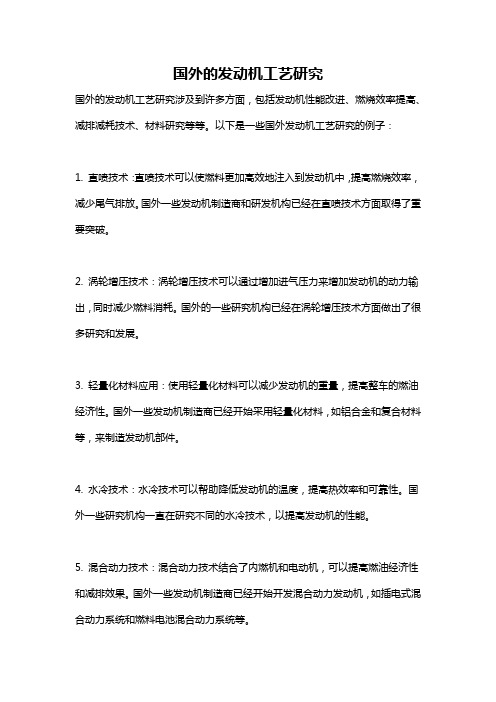
国外的发动机工艺研究
国外的发动机工艺研究涉及到许多方面,包括发动机性能改进、燃烧效率提高、减排减耗技术、材料研究等等。
以下是一些国外发动机工艺研究的例子:
1. 直喷技术:直喷技术可以使燃料更加高效地注入到发动机中,提高燃烧效率,减少尾气排放。
国外一些发动机制造商和研发机构已经在直喷技术方面取得了重要突破。
2. 涡轮增压技术:涡轮增压技术可以通过增加进气压力来增加发动机的动力输出,同时减少燃料消耗。
国外的一些研究机构已经在涡轮增压技术方面做出了很多研究和发展。
3. 轻量化材料应用:使用轻量化材料可以减少发动机的重量,提高整车的燃油经济性。
国外一些发动机制造商已经开始采用轻量化材料,如铝合金和复合材料等,来制造发动机部件。
4. 水冷技术:水冷技术可以帮助降低发动机的温度,提高热效率和可靠性。
国外一些研究机构一直在研究不同的水冷技术,以提高发动机的性能。
5. 混合动力技术:混合动力技术结合了内燃机和电动机,可以提高燃油经济性和减排效果。
国外一些发动机制造商已经开始开发混合动力发动机,如插电式混合动力系统和燃料电池混合动力系统等。
总的来说,国外的发动机工艺研究在不断进步和创新,主要关注于提高性能、减少排放和燃料消耗,以适应环保和可持续发展的趋势。
这些技术的研究成果有望在未来的汽车行业中得到广泛应用。
航空发动机零部件的轻量化与低成本制造

航空发动机零部件的轻量化与低成本制造全文共四篇示例,供读者参考第一篇示例:航空发动机作为飞机的心脏,对于飞行安全和效率起着至关重要的作用。
而发动机的零部件轻量化和低成本制造则是当前航空工业研究的热点之一。
随着航空业的快速发展和市场的竞争加剧,航空公司和飞机制造商越来越注重提高飞机的燃油效率和减少运营成本,因此需要不断创新发动机设计和制造技术,实现零部件的轻量化和低成本制造。
轻量化是航空发动机设计的重要趋势之一。
轻量化可以减少飞机的整体重量,提高飞机的燃油效率,降低对环境的影响。
发动机的零部件轻量化首先涉及材料的选择和设计优化。
与传统的金属材料相比,航空发动机零部件采用高强度、高刚度的复合材料或陶瓷材料,可以实现更轻量化的设计。
复合材料具有重量轻、强度高、抗腐蚀性好等优点,逐渐成为航空发动机零部件的首选材料。
发动机的设计也要进行优化,减少不必要的结构和部件,提高零部件的整体性能,进一步降低重量。
除了材料选择和设计优化,制造技术也是实现发动机零部件轻量化的重要手段。
传统的制造工艺如锻造、铸造、铣削等存在一定的局限性,尤其对于复合材料等新型材料的加工较为困难。
航空发动机零部件制造技术也在不断创新和进步。
先进的制造技术如增材制造(3D打印)、复合材料成型等技术被广泛应用于航空发动机零部件制造中,可以实现复杂结构的快速制造,减少材料浪费,提高生产效率。
增材制造技术可以将材料按照设计要求逐层堆积,制造出具有高度复杂结构的部件,使得发动机零部件的制造更加灵活和高效。
低成本制造也是航空发动机零部件制造的重要目标之一。
航空工业的发展离不开成本控制,高昂的制造成本会直接影响飞机的售价和市场竞争力。
如何降低航空发动机零部件的制造成本成为航空工业面临的一个重要挑战。
在不影响零部件性能和质量的前提下,采用更节约成本的材料和工艺,优化生产流程,提高生产效率,降低材料浪费等方法都可以有效降低航空发动机零部件的制造成本。
为实现航空发动机零部件的轻量化和低成本制造,航空工业需要不断创新和改进。
我国的轻量化技术发展路线
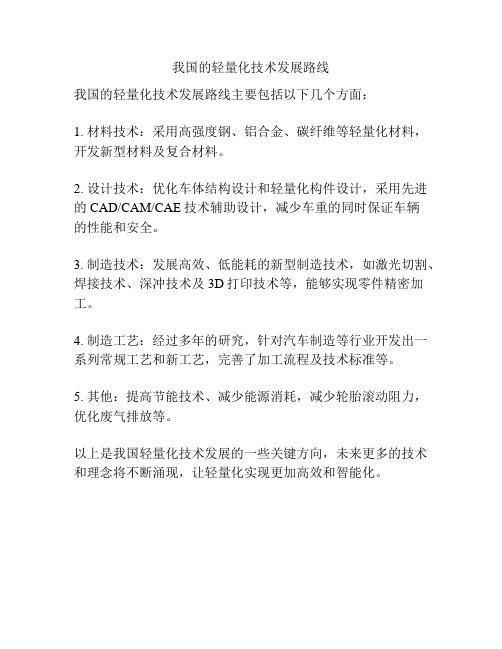
我国的轻量化技术发展路线
我国的轻量化技术发展路线主要包括以下几个方面:
1. 材料技术:采用高强度钢、铝合金、碳纤维等轻量化材料,开发新型材料及复合材料。
2. 设计技术:优化车体结构设计和轻量化构件设计,采用先进的CAD/CAM/CAE技术辅助设计,减少车重的同时保证车辆
的性能和安全。
3. 制造技术:发展高效、低能耗的新型制造技术,如激光切割、焊接技术、深冲技术及3D打印技术等,能够实现零件精密加工。
4. 制造工艺:经过多年的研究,针对汽车制造等行业开发出一系列常规工艺和新工艺,完善了加工流程及技术标准等。
5. 其他:提高节能技术、减少能源消耗,减少轮胎滚动阻力,优化废气排放等。
以上是我国轻量化技术发展的一些关键方向,未来更多的技术和理念将不断涌现,让轻量化实现更加高效和智能化。
汽车轻量化的主要措施
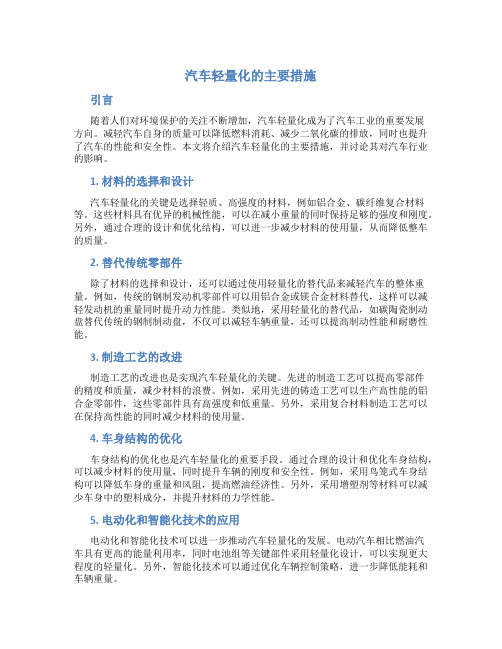
汽车轻量化的主要措施引言随着人们对环境保护的关注不断增加,汽车轻量化成为了汽车工业的重要发展方向。
减轻汽车自身的质量可以降低燃料消耗、减少二氧化碳的排放,同时也提升了汽车的性能和安全性。
本文将介绍汽车轻量化的主要措施,并讨论其对汽车行业的影响。
1. 材料的选择和设计汽车轻量化的关键是选择轻质、高强度的材料,例如铝合金、碳纤维复合材料等。
这些材料具有优异的机械性能,可以在减小重量的同时保持足够的强度和刚度。
另外,通过合理的设计和优化结构,可以进一步减少材料的使用量,从而降低整车的质量。
2. 替代传统零部件除了材料的选择和设计,还可以通过使用轻量化的替代品来减轻汽车的整体重量。
例如,传统的钢制发动机零部件可以用铝合金或镁合金材料替代,这样可以减轻发动机的重量同时提升动力性能。
类似地,采用轻量化的替代品,如碳陶瓷制动盘替代传统的钢制制动盘,不仅可以减轻车辆重量,还可以提高制动性能和耐磨性能。
3. 制造工艺的改进制造工艺的改进也是实现汽车轻量化的关键。
先进的制造工艺可以提高零部件的精度和质量,减少材料的浪费。
例如,采用先进的铸造工艺可以生产高性能的铝合金零部件,这些零部件具有高强度和低重量。
另外,采用复合材料制造工艺可以在保持高性能的同时减少材料的使用量。
4. 车身结构的优化车身结构的优化也是汽车轻量化的重要手段。
通过合理的设计和优化车身结构,可以减少材料的使用量,同时提升车辆的刚度和安全性。
例如,采用鸟笼式车身结构可以降低车身的重量和风阻,提高燃油经济性。
另外,采用增塑剂等材料可以减少车身中的塑料成分,并提升材料的力学性能。
5. 电动化和智能化技术的应用电动化和智能化技术可以进一步推动汽车轻量化的发展。
电动汽车相比燃油汽车具有更高的能量利用率,同时电池组等关键部件采用轻量化设计,可以实现更大程度的轻量化。
另外,智能化技术可以通过优化车辆控制策略,进一步降低能耗和车辆重量。
6. 汽车轻量化的影响汽车轻量化的主要措施不仅可以降低燃料消耗和减少污染物排放,还可以提高汽车的性能和安全性。
汽车制造中的轻量化材料与工艺创新

汽车制造中的轻量化材料与工艺创新随着环境保护意识的增强和能源危机的日益严重,汽车工业正迫切寻求一种更加环保、高效的解决方案。
轻量化是一个不可忽视的趋势,汽车制造中的轻量化材料与工艺创新正扮演着重要的角色。
本文将探讨汽车制造中的轻量化材料与工艺创新,并分析其对汽车工业的影响与发展。
一、轻量化材料在汽车制造中的应用随着技术的进步,新型轻量化材料被广泛应用于汽车制造中。
其中,铝合金、镁合金和碳纤维等材料具有重量轻、强度高的优势,逐渐取代传统材料的地位。
与传统钢铁相比,铝合金具有优异的耐腐蚀性和可塑性,可以实现更好的造型设计和外观效果。
镁合金具有更高的特殊强度和刚性,可以有效减轻汽车的整体重量。
碳纤维作为一种新型的复合材料,具有优异的强度和刚性,同时重量轻,被广泛应用于高端汽车制造。
二、轻量化材料对汽车性能的影响轻量化材料的应用不仅可以有效减轻汽车的总重量,还可以提高汽车的燃油经济性和性能表现。
首先,减轻汽车自身重量可以降低能源消耗,提高燃油效率,减少尾气排放。
其次,轻量化材料具有更好的刚性和强度,能够提高车辆的操控性和安全性能。
此外,减轻汽车总重量还可以降低车辆的传动系统和制动系统的负荷,延长部件的使用寿命,减少维修保养成本。
三、轻量化工艺创新与汽车制造轻量化材料的应用不仅需要材料本身的创新,还需要在汽车制造工艺方面进行创新。
制造商需要采用先进的焊接技术、粘接技术和成型技术,以确保新材料的安全可靠性。
例如,与传统焊接相比,激光焊接是一种更加灵活高效的工艺,可以减少焊接热影响区域,提高焊接强度和质量。
同时,粘接技术也成为轻量化制造中的重要工艺,其具有良好的密封性和减震性能,可以提供更好的承载能力和车身刚性。
此外,先进的成型技术,如热成型、压缩成型和注塑成型等,可以实现复杂的车身构造和形状设计,提高整体车身的强度和轻量化效果。
四、轻量化材料与工艺创新对汽车工业的影响与发展汽车工业的持续发展离不开轻量化材料与工艺的创新。
汽车发动机连杆轻量化设计研究

汽车发动机连杆轻量化设计研究汽车发动机连杆轻量化设计研究引言汽车发动机作为汽车的心脏,承担着转换能量和驱动汽车运行的重要功能。
在发动机的设计中,连杆作为一个关键部件,在发动机的运转过程中承担着极其重要的作用。
本文将从汽车发动机连杆的轻量化设计入手,探讨其对汽车发动机性能和效率的影响。
一、轻量化设计的定义和意义1. 轻量化设计的概念轻量化设计是指在满足产品性能、寿命、安全和成本等综合要求的前提下,以减轻产品自重为目的,采用新的材料、新的结构和新的工艺等手段,达到减轻产品质量的目的。
2. 轻量化设计的意义轻量化设计可以显著减少汽车部件的质量,降低汽车自身的重量,提高汽车的燃油经济性和动力性能,减少对环境的影响,同时也符合节能和减排的国家政策。
轻量化设计对于汽车的性能改进和环境保护具有重要的意义。
二、发动机连杆轻量化设计的技术要点1. 材料的选择发动机连杆的轻量化设计首先要选择合适的材料。
一般来说,铝合金、镁合金和钛合金都是常用的轻量化材料。
这些材料具有优异的比强度和比刚度,可以在减轻连杆质量的同时保证其强度和刚度。
2. 结构的优化发动机连杆的轻量化设计还需要对其结构进行优化。
通过采用空心结构、椭圆形截面等设计手段,可以在保证连杆强度的前提下减少其质量,达到轻量化的效果。
3. 工艺的改进传统的连杆制造工艺一般采用锻造和机加工,这种方式存在浪费材料和能源的问题。
而采用先进的成型工艺,如压铸、粉末冶金等,可以有效降低原材料的消耗,实现连杆的轻量化设计。
三、发动机连杆轻量化设计的影响1. 性能提升轻量化设计可以显著减少连杆的质量,降低发动机的整体质量,提高发动机的功率重量比,从而提升汽车的加速性能和燃油经济性。
2. 热效率改善减轻连杆质量可以减少发动机的惯性负荷,降低摩擦损失和热损失,提高发动机的热效率,减少燃油的消耗,降低尾气排放。
3. 减少振动和噪音轻量化设计可以改善发动机的平衡性和稳定性,减少发动机的振动和噪音,提高汽车的乘坐舒适性。
发动机轻量化技术解析
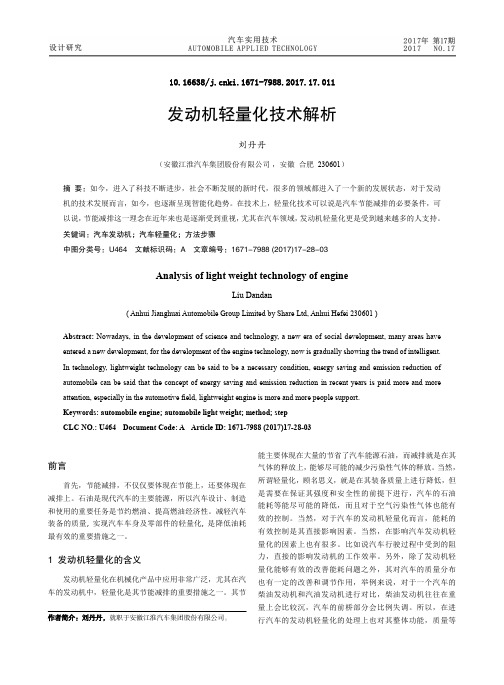
10.16638/ki.1671-7988.2017.17.011发动机轻量化技术解析刘丹丹(安徽江淮汽车集团股份有限公司,安徽合肥230601)摘要:如今,进入了科技不断进步,社会不断发展的新时代,很多的领域都进入了一个新的发展状态,对于发动机的技术发展而言,如今,也逐渐呈现智能化趋势。
在技术上,轻量化技术可以说是汽车节能减排的必要条件,可以说,节能减排这一理念在近年来也是逐渐受到重视,尤其在汽车领域,发动机轻量化更是受到越来越多的人支持。
关键词:汽车发动机;汽车轻量化;方法步骤中图分类号:U464 文献标识码:A 文章编号:1671-7988 (2017)17-28-03Analysis of light weight technology of engineLiu Dandan( Anhui Jianghuai Automobile Group Limited by Share Ltd, Anhui Hefei 230601 )Abstract: Nowadays, in the development of science and technology, a new era of social development, many areas have entered a new development, for the development of the engine technology, now is gradually showing the trend of intelligent. In technology, lightweight technology can be said to be a necessary condition, energy saving and emission reduction of automobile can be said that the concept of energy saving and emission reduction in recent years is paid more and more attention, especially in the automotive field, lightweight engine is more and more people support.Keywords: automobile engine; automobile light weight; method; stepCLC NO.: U464 Document Code: A Article ID: 1671-7988 (2017)17-28-03前言首先,节能减排,不仅仅要体现在节能上,还要体现在减排上。
航空发动机零部件的轻量化与低成本制造

航空发动机零部件的轻量化与低成本制造涉及到多个方面的考虑。
一方面,轻量化设计可以提高发动机的性能,减少燃油消耗,降低噪音,减少污染,并且更有利于提升飞机的起飞性能。
另一方面,低成本制造则需要考虑到制造成本、制造效率、质量控制等因素。
对于轻量化设计,有多种策略可以实现。
首先,优化材料选择是至关重要的,使用高强度钢、铝合金、钛合金等高性能材料可以有效减轻重量。
此外,采用复合材料技术也是一个可行的选择,如碳纤维、玻璃纤维等。
这些材料不仅具有较高的强度重量比,而且可以通过优化设计实现更好的性能。
在制造工艺方面,可以采用先进的成型工艺,如3D打印技术。
这种技术可以快速、灵活地制造复杂形状的零件,而且成本相对较低。
此外,采用数字化制造技术,如计算机辅助设计(CAD)和计算机辅助制造(CAM)等,可以实现精确的模型设计和精确的制造过程,从而减少废品率并提高生产效率。
为了实现低成本制造,还需要考虑生产规模和供应链管理。
通过优化生产计划和调度,可以实现生产效率的提高和成本的降低。
此外,采用模块化设计也是一个有效的策略,将复杂的系统分解为多个模块,可以降低研发和制造成本。
同时,通过优化供应链管理,可以降低原材料成本和物流成本。
另外,我们还需要考虑制造成本的持续优化和成本控制。
在制造过程中,采用精益生产方法可以减少浪费,提高生产效率。
此外,通过采用自动化技术,可以提高生产线的自动化程度,减少人工干预,从而降低生产成本。
同时,持续的质量控制也是降低制造成本的重要手段。
总的来说,航空发动机零部件的轻量化与低成本制造是一个复杂的过程,需要综合考虑材料选择、制造工艺、生产规模、供应链管理和成本控制等多个方面。
只有这样,我们才能实现高性能、低成本的航空发动机零部件制造。
轿车发动机机体的轻量化技术

!
铝合金机体结构必须解决的问题
灰铸铁气缸体改用铝合金铸造,必须满足一些
额外的要求, 分述如下。
!"#
确保气缸筒滑移表面耐磨, 不易变形 首先是气缸筒 $ 活塞 $ 活塞环摩擦副的耐磨性和
摩擦学问题。活塞和活塞环由于作为摩擦副的耐磨 性和摩擦学特性不好而不能直接在铸铝合金气缸筒 上工作。 解决的办法是在铝合金气缸体中铸入 (或嵌 入) 其他材料的气缸套, 或者在气缸筒上涂敷其他材 料。 其次是气缸筒之间区域的变形问题。该区域的 应力是由热应力和由于安装力、气缸的内压力引起 的机械应力叠加在一起形成的。在较高的最大爆发 压力下, 首先是动载荷提高了, 以致气缸筒之间的区 域出现明显的变形和应力。 为了改变这种局面, 必须 使气缸筒之间的区域达到足够的尺寸,还要采用合 适的形状, 同时采取有效的冷却措施。
致在气缸筒变形和气缸筒之间的薄壁区域的材料热 载荷方面出现其他问题。利用压铸镁合金可以使一 台 # % 发动机机体的质量减轻到 ). /0 以下[1] , 但是 它的成本较高。 有人认为, 镁合金作为曲轴箱材料目 前在大批量生产中没有什么吸引力。 尽管如此, 奥迪 公 司 最 近 还 是 成 功 地 将 一 台 升 功 率 达 到 "2 /3 4 % 的 . 气门、 )*5 % 涡轮增压汽油机的灰铸铁气缸体改 成了镁 6 铝混合材料气缸体,使发动机整机质量从
图$
声压级 $ -./
!"
’"
#"
0"
主轴承间隙 $ !+
主轴承间隙对发动机噪声的影响[!]
!"!
铝合金较低的弹性模量对声学和振动的影响 铝合金的弹性模量较低, 这会降低结构刚度, 增
机械设计中的轻量化设计路线

机械设计中的轻量化设计路线摘要:随着科技水平的高速发展,机械轻量化设计受到更加广泛的关注及重视。
机械轻量化设计是在保证设备的基本使用功能的要求、安全可靠的要求和生产的要求的前提下,从设备结构、整机选材、加工工艺等各方面,采用新的设计理念、选取新型材料、优化制造工艺等措施来实现对设备整机的重量的控制,以实现机械设计向“环保节能”的方向发展。
轻量化设计在机械制造业中达成了广泛的共鸣,依据不同行业、不同客户的用途,来定制开发、生产、制造相关设备,在国家发展战略《中国制造2025》提到轻量化材料作为重要的核心技术,作为工业大国要在制造强国建设的过程中作为工作重点进行。
关键词:机械设计;轻量化材料;环保节能1机械轻量化设计的重要性早期工业的发展方式相对粗犷,特别是施工机械设备、矿山机械设备等大型设备的设计理念相对滞后,施工机械设备的材质使用率不足,导致整个设备非常笨重;为了能够驱动笨重的机身、力臂等结构件,进而会造成更大的驱动系统,从而造成大量的能量消耗,加上大量钢材的使用,也很容易受材料锈蚀等危害影响,该类设备对复杂的施工环境往往无法胜任,设备使用效能比很低。
如果运用轻量化的设计理念进行重新设计,不仅能够有效克服以上难题,而且可以大大改良产品质量的稳定性和提高设备的整体品质。
机械轻量化的重要意义包括:(1)对整机结构重量的减轻,改善各结构部件间的配合关系,以更合理的方法实现驱动运行配合的动作,对机械结构精简调整,也能在较大范围上实现对材料成本的控制。
(2)通过轻量化设计能够使施工机械的生产效能提高,降低能耗,节能环保,机械设备结构部件的自重每减轻1%,可使产品运行能耗降低1.5% ,减排成效提高0.5% 。
2机械轻量化发展的现状在欧美等发达国家中,由于其工业革命的发展进行的时间较早,本身的设计水平在二十世纪九十年代时就达到很高的水平,而先进的制造技术和信息技术往往能够促进自身施工机械具备轻量化与耐用性高的优势。
先进航空发动机关键制造技术发展现状与趋势

先进航空发动机关键制造技术发展现状与趋势一、轻量化、整体化新型冷却结构件制造技术1 整体叶盘制造技术整体叶盘是新一代航空发动机实现结构创新与技术跨越的关键部件,通过将传统结构的叶片和轮盘设计成整体结构,省去传统连接方式采用的榫头、榫槽和锁紧装置,结构重量减轻、零件数减少,避免了榫头的气流损失,使发动机整体结构大为简化,推重比和可靠性明显提高。
在第四代战斗机的动力装置推重比10发动机F119和EJ200上,风扇、压气机和涡轮采用整体叶盘结构,使发动机重量减轻20%~30%,效率提高5%~10%,零件数量减少50% 以上。
目前,整体叶盘的制造方法主要有:电子束焊接法;扩散连接法;线性摩擦焊接法;五坐标数控铣削加工或电解加工法;锻接法;热等静压法等。
在未来推重比15~20 的高性能发动机上,如欧洲未来推重比15~20的发动机和美国的IHPTET 计划中的推重比20的发动机,将采用效果更好的SiC陶瓷基复合材料或抗氧化的C/C复合材料制造整体涡轮叶盘。
2 整体叶环(无盘转子)制造技术如果将整体叶盘中的轮盘部分去掉,就成为整体叶环,零件的重量将进一步降低。
在推重比15~20 高性能发动机上的压气机拟采用整体叶环,由于采用密度较小的复合材料制造,叶片减轻,可以直接固定在承力环上,从而取消了轮盘,使结构质量减轻70%。
目前正在研制的整体叶环是用连续单根碳化硅长纤维增强的钛基复合材料制造的。
推重比15~20 高性能发动机,如美国XTX16/1A变循环发动机的核心机第3、4级压气机为整体叶环转子结构。
该整体叶环转子及其间的隔环采用TiMC金属基复合材料制造。
英、法、德研制了TiMMC叶环,用于改进EJ200的3级风扇、高压压气机和涡轮。
3大小叶片转子制造技术大小叶片转子技术是整体叶盘的特例,即在整体叶盘全弦长叶片通道后部中间增加一组分流小叶片,此分流小叶片具有大大提高轴流压气机叶片级增压比和减少气流引起的振动等特点,是使轴流压气机级增压比达到3 或3 以上的有发展潜力的技术。
轿车发动机缸体轻量化的工艺改进

1 生 产 工 艺 确 定
委 托设 计 的业 主 企业 要 求 设计 规模 ,2 4 01 年 上 海 大 众 、 一 汽 大 众 E 1发 动 机 缸 体 产 能 为 A1 l 7 万 件 /,EA2 1 4 .万 件 / ;2 1 年 上 海 大 2 a 1 为 64 a 05
铝 缸体 技术 改 造项 目的 设计 工作 ,从满 足 生产 需 求 角度 出发对 生产 工艺 进行 改进 。
排 放 十 分 重 要 。研 究 显 示 ,若 汽 车 整 车 质 量 减 轻
1 %,燃油 效率前 提高6 0 %~8 %;汽 车装 备质量
每 减 少 10k , 百 公里 油 耗 可 降低 03 . O g .~06L,汽 车 质 量 减 轻 1 , 油 耗 可 降 低 07 。从 驾 驶 方 面 % .%
Zh g Jinh an a ua
( h n h i si t f c a i l lcr a E gn ei o, t.S a g a 2 0 4 , ia S a g a I tueo h nc &Ee tc l n i r gC .Ld, h n h i 0 0 0 Ch ) t n Me a i e n n
轿 车 发 动 机 缸 体 轻 量 化 的工 艺 改 进
张建华 ( 上海市机 电设计研究院有限公司,上海 2 0 4 ) 0 0 0
摘要 :分析并选择 了轿 车发动机缸体材料 ,根据铸件特点确定采用压力铸造 工艺生产铝缸体 ,
介 绍 了缸 体 产 能计 算 、 生产 设 备 及 生 产 线 布 置 。指 出采 用 铝缸 体 可 以减 轻发 动机 的质 量 ,从 而 达 到 减 少燃 料 消耗 、 降低 排 气 污 染 的 目的 。
汽车轻量化的原理和应用
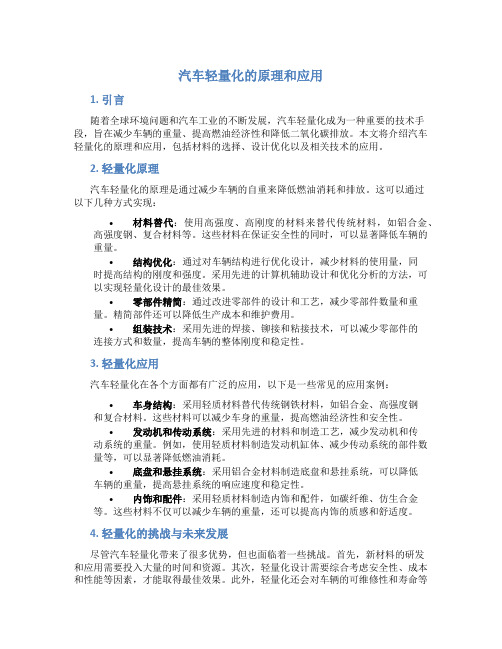
汽车轻量化的原理和应用1. 引言随着全球环境问题和汽车工业的不断发展,汽车轻量化成为一种重要的技术手段,旨在减少车辆的重量、提高燃油经济性和降低二氧化碳排放。
本文将介绍汽车轻量化的原理和应用,包括材料的选择、设计优化以及相关技术的应用。
2. 轻量化原理汽车轻量化的原理是通过减少车辆的自重来降低燃油消耗和排放。
这可以通过以下几种方式实现:•材料替代:使用高强度、高刚度的材料来替代传统材料,如铝合金、高强度钢、复合材料等。
这些材料在保证安全性的同时,可以显著降低车辆的重量。
•结构优化:通过对车辆结构进行优化设计,减少材料的使用量,同时提高结构的刚度和强度。
采用先进的计算机辅助设计和优化分析的方法,可以实现轻量化设计的最佳效果。
•零部件精简:通过改进零部件的设计和工艺,减少零部件数量和重量。
精简部件还可以降低生产成本和维护费用。
•组装技术:采用先进的焊接、铆接和粘接技术,可以减少零部件的连接方式和数量,提高车辆的整体刚度和稳定性。
3. 轻量化应用汽车轻量化在各个方面都有广泛的应用,以下是一些常见的应用案例:•车身结构:采用轻质材料替代传统钢铁材料,如铝合金、高强度钢和复合材料。
这些材料可以减少车身的重量,提高燃油经济性和安全性。
•发动机和传动系统:采用先进的材料和制造工艺,减少发动机和传动系统的重量。
例如,使用轻质材料制造发动机缸体、减少传动系统的部件数量等,可以显著降低燃油消耗。
•底盘和悬挂系统:采用铝合金材料制造底盘和悬挂系统,可以降低车辆的重量,提高悬挂系统的响应速度和稳定性。
•内饰和配件:采用轻质材料制造内饰和配件,如碳纤维、仿生合金等。
这些材料不仅可以减少车辆的重量,还可以提高内饰的质感和舒适度。
4. 轻量化的挑战与未来发展尽管汽车轻量化带来了很多优势,但也面临着一些挑战。
首先,新材料的研发和应用需要投入大量的时间和资源。
其次,轻量化设计需要综合考虑安全性、成本和性能等因素,才能取得最佳效果。
浅谈汽车发动机的轻量化

浅谈汽车发动机的轻量化作者:周巧玲来源:《科技资讯》 2011年第35期周巧玲(合肥工业大学合肥 230009)摘要:轻量化是汽车节能减排的重要措施之一。
本文论述了发动机轻量化的意义,以及发动机轻量化在新技术上的突破,在新材料上的应用,在新制造工艺上的实施。
关键词:发动机轻量化中图分类号:U464 文献标识码:A 文章编号:1672-3791(2011)12(b)-0128-02石油是现代汽车的主要能源,目前,地球上的石油储备含量有限,而汽车产量的增加也带来燃油价格的上涨。
所以汽车设计、制造和使用的重要任务是节约燃油、提高燃油经济性。
减轻汽车整备质量,实现汽车车身及零部件的轻量化,是降低油耗最有效的重要措施之一。
表1所示为汽车自身重量的主要构成比例。
可见,发动机、底盘及车身零部件是轻量化的重点。
本文介绍发动机的轻量化。
1 汽车轻量化的意义汽车轻量化必须是在保证汽车强度和安全性能的前提下,尽可能地降低汽车的整备质量,从而提高汽车的动力利用率,减少燃料消耗,降低排气污染。
汽车轻量化对于节约能源、减少废气排放十分重要。
汽车行驶时需克服的阻力有滚动阻力、空气阻力、坡度阻力、和加速阻力。
阻力越大,燃油消耗率就越大。
其中滚动阻力、坡度阻力和加速阻力与整车总质量成正比,质量越大,阻力越大。
空气阻力主要与迎风面积和车身形状有关,与整车的总质量无关。
降低汽车总质量,能减小行驶阻力,从而减小行驶驱动力,降低燃油消耗,提高燃油经济性。
汽车质量每减轻100kg,能使汽车百公里油耗减少30%以上。
根据美国1978年进行的统计表明,总质量为1360kg的汽车,当汽车总质量减少10%,燃油消耗降低约8.8%,而燃油消耗每减少1L,产生的CO2排放量则减少2.45Kg。
所以汽车轻量化也是节能环保的有效措施之一。
2 发动机的轻量化轻量化应该通过结构、材质、制造工艺的优化来取得,必须以保证汽车的安全性为最基本的前提。
根据零部件的受力、功能和要求,分析每个部件的应力和轻量化目标,进行优化设计后,再确定轻量化材料。
航空发动机零部件的轻量化与低成本制造

航空发动机零部件的轻量化与低成本制造全文共四篇示例,供读者参考第一篇示例:随着航空业的迅速发展,航空发动机作为飞机的心脏,具有至关重要的作用。
而发动机的性能直接影响飞机的飞行效率和安全性。
为了提高飞机的性能和降低成本,航空发动机的轻量化和低成本制造成为了产业发展的重要方向。
一、轻量化设计的重要性1. 提高飞机性能:航空发动机的轻量化可以减小飞机的整体重量,从而减少燃料消耗和提高飞机的续航能力,提高飞机的性能。
2. 降低空气阻力:发动机的轻量化设计可以减小发动机的体积和空气阻力,提高飞机的速度和飞行效率。
3. 减少磨损和维护成本:轻量化设计可以减少部件之间的磨损,延长零部件寿命,减少维护成本。
二、轻量化设计的方法1. 采用先进的材料:如碳纤维复合材料、铝合金等材料具有良好的强度和轻量化特性,可以用于减少发动机零部件的重量。
2. 结构优化设计:采用有限元分析等先进技术,对零部件的结构进行优化设计,减少冗余部分,提高零部件的强度和轻量化。
3. 使用先进的制造工艺:采用先进的加工技术如激光切割、3D打印等制造工艺,可以实现零部件的精确加工和减少材料浪费,同时实现零部件的轻量化。
三、低成本制造的重要性1. 降低生产成本:低成本制造可以减少材料和人力成本,降低发动机的生产成本,提高产品竞争力。
2. 提高产能效率:低成本制造可以提高生产效率,缩短生产周期,提高产量,满足市场需求。
3. 降低维修成本:低成本制造可以提高零部件的质量和寿命,减少日常维修和更换的成本。
四、低成本制造的方法1. 自动化生产线:采用自动化生产线可以提高生产效率,减少人力成本。
2. 精益生产:采用精益生产理念,优化生产流程,降低浪费,提高生产效率。
3. 合理采购:采用合理的采购策略,降低采购成本,提高成本效益。
五、结语航空发动机的轻量化和低成本制造是航空产业发展的必然趋势。
通过采用先进的材料和制造工艺,优化设计和精益生产,可以实现发动机零部件的轻量化设计和低成本制造,提高飞机的性能和降低飞机的运营成本,推动航空产业的健康发展。
汽车轻量化创新方案

汽车轻量化创新方案咱来聊聊汽车轻量化这个超酷的事儿。
一、材料革新是关键。
1. 碳纤维大显身手。
碳纤维这玩意儿可真是汽车轻量化的明星材料。
它就像汽车界的超级英雄,又轻又强。
你想啊,传统的金属材料虽然结实,但是太重了。
碳纤维呢,重量可能只有同体积金属的几分之一,但是强度却能顶得上,甚至超过那些金属。
要是汽车的车身框架、引擎盖这些地方都用上碳纤维,那汽车就像减肥成功的运动员,跑起来又快又轻松。
不过呢,碳纤维也有个小缺点,就是太贵了。
所以我们得想办法让碳纤维的生产工艺更简单、成本更低。
比如说,能不能研究出一种新的合成方法,像做蛋糕一样简单又便宜地做出碳纤维。
2. 铝合金的巧妙运用。
铝合金也是个好东西。
它比钢铁轻很多,而且还比较容易加工。
我们可以把汽车上一些不太需要超级高强度的部件,像车门、后备箱盖之类的,都换成铝合金的。
而且铝合金还有个好处,就是它看起来比较有质感,让汽车显得更高级。
不过呢,铝合金也不是完美的,它的强度在一些极端情况下可能还是不够。
那怎么办呢?我们可以给铝合金来个“强化训练”,比如通过特殊的热处理或者合金配比,让它变得更强壮,这样就能在汽车上承担更多的“责任”啦。
3. 塑料和复合材料的新玩法。
别小看塑料,现在的高性能塑料和复合材料可厉害着呢。
比如说,有些塑料可以做得像金属一样坚硬,但是重量却轻得多。
我们可以把这些塑料和复合材料用在汽车的内饰上,不仅能减轻重量,还能让内饰看起来更时尚。
而且,对于汽车的一些小部件,像仪表盘的支架之类的,也可以用这些材料来做。
这样就像给汽车穿上了轻便又时尚的“小配饰”。
但是呢,塑料和复合材料得注意防火和耐用性的问题,不然要是一着火或者用几天就坏了,那可不行。
二、设计优化也很重要。
1. 结构设计的智慧。
汽车的结构就像人的骨骼一样,设计得好就能既轻便又结实。
我们可以借鉴大自然的智慧,像蜂窝结构就很厉害。
蜂窝结构的东西,重量轻,但是能承受很大的压力。
要是把汽车的一些部件设计成蜂窝结构,那就能在保证强度的前提下减轻不少重量。
轻量化发动机技术革新
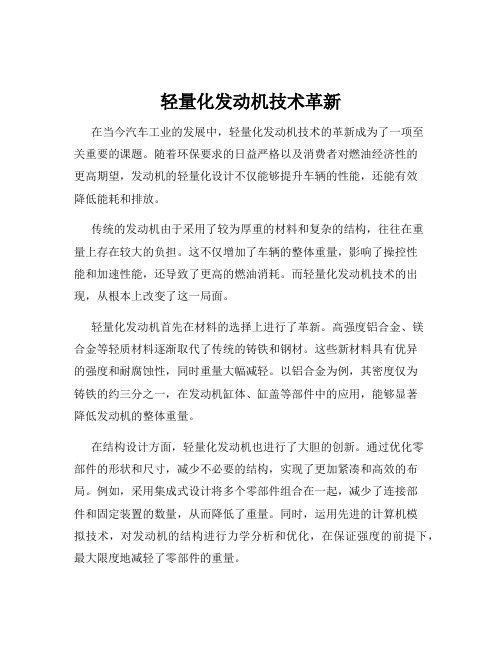
轻量化发动机技术革新在当今汽车工业的发展中,轻量化发动机技术的革新成为了一项至关重要的课题。
随着环保要求的日益严格以及消费者对燃油经济性的更高期望,发动机的轻量化设计不仅能够提升车辆的性能,还能有效降低能耗和排放。
传统的发动机由于采用了较为厚重的材料和复杂的结构,往往在重量上存在较大的负担。
这不仅增加了车辆的整体重量,影响了操控性能和加速性能,还导致了更高的燃油消耗。
而轻量化发动机技术的出现,从根本上改变了这一局面。
轻量化发动机首先在材料的选择上进行了革新。
高强度铝合金、镁合金等轻质材料逐渐取代了传统的铸铁和钢材。
这些新材料具有优异的强度和耐腐蚀性,同时重量大幅减轻。
以铝合金为例,其密度仅为铸铁的约三分之一,在发动机缸体、缸盖等部件中的应用,能够显著降低发动机的整体重量。
在结构设计方面,轻量化发动机也进行了大胆的创新。
通过优化零部件的形状和尺寸,减少不必要的结构,实现了更加紧凑和高效的布局。
例如,采用集成式设计将多个零部件组合在一起,减少了连接部件和固定装置的数量,从而降低了重量。
同时,运用先进的计算机模拟技术,对发动机的结构进行力学分析和优化,在保证强度的前提下,最大限度地减轻了零部件的重量。
制造工艺的进步也是轻量化发动机技术革新的重要支撑。
精密铸造、锻造技术以及 3D 打印技术的应用,使得发动机零部件的制造更加精确和高效。
3D 打印技术能够根据设计要求,直接制造出复杂形状的零部件,不仅减少了加工工序,还能够实现材料的最优分布,进一步减轻重量。
轻量化发动机还在燃烧系统方面进行了改进。
采用了更加先进的燃油喷射技术,如缸内直喷和多次喷射,提高了燃油的燃烧效率,减少了能量的损失。
同时,优化了进气和排气系统,提高了发动机的充气效率,使得燃烧更加充分,从而在降低油耗的同时提升了动力性能。
除了上述方面,发动机的附件系统也实现了轻量化。
例如,采用电动水泵和电动空调压缩机,取代传统的机械驱动方式,减少了发动机的机械负载,从而降低了重量和能耗。
轿车发动机机体的轻量化技术研究

《装备维修技术》2021年第6期—281—轿车发动机机体的轻量化技术研究汪 冰(安庆帝伯格茨活塞环有限公司,安徽 安庆 246005)引言:为降低燃油消耗,并减少对CO2的排放,使得汽车轻量化被社会大众所关注。
通过汽车轻量化,能够减少成本,使得汽车动力性得以提升,并达到节约材料的目的。
另外对于发动机轻量化而言,还与整车质量分布息息相关。
提升发动机功率,从而减少单位功率质量,在此基础上,有助于实现发动机轻量化。
除此之外,减轻零件质量,也可以达到轻量化的目的。
1.铝合金机体结构需要处理的问题1.1保证气缸筒滑移表面耐磨,难以产生变形 主要包含两方面的问题,一是耐磨性,二是摩擦学。
通常情况下,往往因为摩擦副的特性不够理想,从而对于活塞来讲,无法以直接的形式,在气缸筒上进行工作。
面对这样的问题,可以采取以下两种方法,一是基于气缸筒,向其涂敷别的材料;二是基于气缸体,向其中嵌入别的气缸套。
另外在气缸筒区域内,常常会出现变形问题。
以这一区域的应力来分析,其由多种力组合而成,比如压力以及热应力等。
在爆发压力很大的情况下,会使得动载荷被提升,从而在该区域中,产生较大的应力,并发生较为突出的变形。
为避免出现这样的局面,针对气缸筒的区域,需要满足一定的尺寸,同时借助适当的形状,实施合理、可行的冷却手段。
1.2符合传递力流要求 以现如今的铝合金来分析,其具备较大的强度,由此可当作气缸体材料,实际上,问题的产生,主要形成于螺纹连接部位。
往往因为装配施工,从而导致螺纹出现一些塑形膨胀。
在完成装配之后,对于作用力的承受,常常取决于前几道螺纹。
因为存在较大的静载荷,从而对于铝合金来讲,可以察看到较为常见的塑性化情况。
若在将来的维修中,频繁松开或者连接螺栓,接着再次进行装配,基于这样的情况,将会变得更加严重。
对于交变与热荷载而言,当二者进行叠加时,极容易导致材料产生疲劳,在这样的情况下,也会促使螺栓连接失效。
除此之外,还存在一种较为常见的失效方式,具体而言,基于螺纹槽底部,从而产生的裂纹。
航空发动机减重设计技术研究

航空发动机减重设计技术研究航空发动机的减重设计技术一直以来都是航空工业中非常重要和挑战性的问题,主要是因为减重能够直接影响到飞机的重量和燃油消耗,从而对飞行性能和经济性产生深远影响。
针对这一问题,许多工程师和研究人员进行了深入研究和探讨,引入了一系列创新和优化设计方法,来实现航空发动机的减重设计。
下面我们将详细介绍航空发动机减重设计技术研究的相关内容。
一、减小机身尺寸和轻量化构件对于航空发动机而言,对机身尺寸的要求非常严格,需要在保证性能的情况下尽可能缩小其体积和尺寸。
因此,在进行航空发动机的减重设计时,第一步就是寻求减小机身尺寸和减轻构件质量的方法。
这其中涉及到众多优化问题,诸如材料的选择、降低机身外壳厚度、简化机体结构和轻量化构件等。
而提高航空发动机战斗力,离不开以材料科学为基础,开展轻量化构件的研究工作,进而为全机减重提供坚实的技术支撑。
二、推进技术进步和升级航空发动机品质推进技术进步是实现航空发动机减重设计的关键。
一方面,新的设计方法、材料、技术设备和各方面专业知识的不断应用,可以大大提升航空发动机的工艺水平和项目管理能力,从而在降低成本的同时,提高其性能和品质。
同样,应用新材料和新工艺,对航空发动机进行升级和改进,也是从根本上实现减重设计的有效途径。
新材料的应用可以大大减轻发动机的重量,而新工艺的运用则可以不断优化设计,简化机体结构,缩小机身尺寸和外形,从而提升整体性能和效益。
三、关于降低原材料成本的措施航空发动机减重设计需要满足严格的工艺技术和质量要求,因此其原材料选择也是非常重要的,并且直接影响到航空发动机成本和效益。
因此,需要采取一系列措施和策略来降低原材料成本。
例如,选择性优良、质量可靠的材料,学会如何配置和使用高速加工设备等现代化工具与设备,推进现代化技术的应用,同时也需要积极开展智能化管理和数据统计分析工作,提升生产效率和质量,优化生产流程,降低生产成本。
四、环保意识的提高和绿色技术的应用在航空发动机减重设计中,环保也是一个非常重要的问题。
- 1、下载文档前请自行甄别文档内容的完整性,平台不提供额外的编辑、内容补充、找答案等附加服务。
- 2、"仅部分预览"的文档,不可在线预览部分如存在完整性等问题,可反馈申请退款(可完整预览的文档不适用该条件!)。
- 3、如文档侵犯您的权益,请联系客服反馈,我们会尽快为您处理(人工客服工作时间:9:00-18:30)。
Products & Technology产品与技术发动机轻量化途径及工艺创新中国汽车工程学会 赵宇龙汽车轻量化是实现汽车节能减排的重要途径,已经成为世界汽车发展的潮流。
研究表明,汽油乘用车每减重100kg将节油0.39L/100km;汽车质量每降低10%,可降低油耗6%~8%,排放下降4%。
发动机在乘用车整车中占整车质量的12%左右。
发动机的轻量化,除了可以提高汽车动力性、节省材料、降低成本以外,还涉及整车的质量分布。
发动机的轻量化必须保证在以工作可靠性和整车安全性为前提下,通过材料、工艺、结构的优化设计达到轻量化目标。
一、发动机轻量化途径发动机轻量化技术途径为结构优化和使用轻质材料。
具体来说是:通过拓扑优化分析相关零件结构并进行尺寸优化和形状优化,降低零件重量并同时降低零件成本;通过不同零件功能组合,进行零件模块化设计,减少零件数量,提高模块通用性。
采用先进的轻量化材料技术、加工设备及成型工艺技术,实现汽车发动机产品零件的轻量化;在具体实施的过程中应采取概念设计先行,材料与工艺相辅相成的技术路线。
二、结构优化目前在发动机设计研发行业里,发动机集成化、轻量化是设计的主流方向,同时,发动机零部件的结构创新和优化对装备和工艺也提出了新的要求。
下面列举几个结构创新的例子。
1. 气缸盖集成排气歧管近些年来,无论是大众最新的第三代EA888还是现代的Kappa,又或是通用最新的Ecotec,在这些发动机上都不太容易找到排气歧管。
难道这些发动机都不需要排气歧管吗?其实这些发动机并没有将排气歧管抛弃,而是巧妙地将排气歧管集合在了发动机缸盖里,这样从外部看起来发动机仿佛就没有了排气歧管(图1红色部分)。
扫一扫看视频由于这项技术将排气歧管集成于气缸盖内,排气歧管内的热废气能够更好的与缸盖水套进行热交换,这样同是采用发动机冷却水来冷却,那么相当于冷却系统多了一个热源,这样就能更快地实现暖机,减少冷启动造成内部构件的摩擦,使发动机更快地进入高效的工作状态,从而达到降低排放,节省油耗的目的。
由于内置式气缸盖排气歧管也起到了简化发动机零部件的作用,从而能让发动机减少3~5kg的重量,同时减少的重量位于发动机顶部,所以这对于整车的重心降低是有所裨益的。
日产汽车公司的VR30DDTT发动机机型的气缸盖将排气歧管与原气缸盖集成为一体(见图2)。
由此,能在气缸盖的排气出口处布置涡轮增压器,使得催化器可布置在气缸盖附近。
其结果表明,该举措能大幅提升起动后催化器入图 1Products & Technology产品与技术口的排气温度,使催化剂活性时间减少50%左右。
另一方面,在排气温度较高的条件下,利用气缸盖内的散热能有效降低排气温度。
2.瘦身连杆EA888发动机连杆的结构优化也十分明显, 在确保工件强度和刚性的前提下, 其杆部至围绕大头孔部分都进行了瘦身。
若取杆部中截面观察, 呈清晰的“工” 字形。
小大头孔部的上、下端面, 在绝大多数情况下都为一组平行面, 经结构优化后的这部分形状变成了锲形。
其他还有若干处也体现了去重和优化, 如连杆小大头孔凸缘部分的削薄处理以及取消孔内的衬套(见图3)等。
图 2图 33.空心凸轮轴传统的一体式凸轮轴采用单一的材料,通过铸造或锻造制坯后经多工序切削加工而成。
而在凸轮轴轻量化工作中,主要是其空心化进行的。
空心凸轮轴有三种方式,分别为加工式空心凸轮轴、铸造空心凸轮轴和组装式空心凸轮轴。
上汽大众EA888采用组合式空心凸轮轴。
组合式空心凸轮轴是由铁基粉末冶金材料制成凸轮,然后用热套连接或者滚花过盈连接的办法将凸轮固定在空心钢管上。
与铸铁件相比,中空装配式凸轮轴在减轻质量(25%~30%)、降低生产成本,提高整机性能等方面具有传统凸轮轴无法比拟的优势,越来越受到广泛关注和重视,并成为凸轮轴制造技术的发展方向。
4.缸体铸造油道传统缸体回油道是通过机械加工方式从缸体顶部打通到曲轴箱内部,对加工刀具的要求较高。
同时缸顶较窄油孔直接对着曲轴,溜回的润滑油直接到高速运转的曲轴上,增加了曲轴的阻力。
另外回油道铸造缸体对增加缸体的整体强度,增加缸体的抗变形能力起到很好作用,缸体就可以做得更紧凑。
发动机缸体铸造成型油道是新型发动机的发展趋势,这种缸体采用常规水平浇注很困难,目前采用组芯、立浇工艺较多。
立浇工艺有两种:一种是纯组芯工艺,直接浇注,这种方法现场环境难以保证;第二种是组芯与造型线结合生产工艺,即建立壳芯生产线。
5.利用3D打印技术优化结构雷诺卡车公司新设计了一款4缸5L发动机,由于一些零部件采用3D 打印技术,其质量减少了120kg,并且相关零部件的耐久性已经得到测试验证(见图4)。
目前为止,雷诺卡车公司的工程师已虚拟设计了完整的发动机,其摇臂和凸轮轴轴承盖采用金属3D打印制造,并在台架上顺利地对这款欧Ⅵ发动机进行了600h的测试(见图5)。
3D打印制造技术,给内燃机提供了全新的发展前景,它使得制造商可以利用分层材料制造零部件,并减轻装配操作强度和优化发动机部件数量。
这种技术的好处显而易见,首先是便于整合和优化零部件。
雷诺卡车公司新开发的发动机,零部件数量减少200个,相当于减少了25%。
工程师集成了80个缸体零件和45个缸盖零件。
与此同时,他们还优化了交流发电机和发动机线束的支架。
图 4图 5Products & Technology产品与技术图 7另一种典型的轻量化活塞为钢顶铝裙铰接活塞。
它的活塞顶与活塞销是两个完全独立的零件,活塞顶能相对于裙部作独立的自由摆动。
随着活塞直径的增加,铰接式活塞显示出其轻量化优势。
当活塞直径D <80mm 时,纯铝活塞质量轻;当D =80mm 时,铝活塞和铰接活塞质量基本相等;当D >80mm 时,铰接活塞轻20%。
另外,钢顶铝裙铰接活塞使压缩高比常规铝活塞更小,降低了发动机的总高度。
另外,一些发动机附件在轻量化方面也有文章可做,如博格华纳量产的新型轻量化静音链系统在链条、张紧器、SIFF(SlideIn Flat Face)中分别作了材料、设计及工艺的优化,帮助整个链系统减轻重量。
其采用8 mm/6.35 mm新型链板材料的齿形链,在保持其强度、耐磨性及NVH特性不变甚至提高的情况下,减轻重量提高传动效率。
就链条本身而言,减轻25%~30%的重量。
链系统中的张紧器采用了优化设计方案,结构减轻10%~20%重量。
SIFF也减轻结构设计,并对工艺做了从注塑成形到挤压成形的优化,其重量减轻30%~40%。
三、材料创新发动机轻量化在材料方面首先是考虑用铝合金材料、镁合金材料替代密度大的铸铁材料,在优化改进结构的基础上实现结构更强,质量更轻。
高强度结构钢使零件设计得更紧凑和小型化,有助于汽车的轻量化,主要应用于气门弹簧、齿轮、涨断连杆等。
铝合金主要应用于气缸体、缸盖、活塞、进气管、水泵壳、起动机壳体、摇臂、发动机支架、滤清器底座、齿轮室罩盖、飞轮壳、油底壳等发动机零部件。
镁合金主要应用于链条室、气门等。
根据美国铝学会的报告,汽车上每使用0.45kg铝就可减轻车1kg,理论上铝制汽车可以比钢制汽车减重40%。
1.铝合金加工中的工艺创新——缸孔喷涂技术随着汽车朝着轻量化方向发展,铝合金发动机在汽车行业的应用比例越来越高。
由于铝合金的耐磨性和力学性能不如铸铁,因此传统的铝合金发动机必须镶嵌铸铁缸套,以提高性能。
但是铸铁缸套的缺点在于缸套和缸体之间的封装,由于两种材料热容性特征不同 ,会影响铝质发动机缸体的耐用性。
对此,国外已研发出一种新的工艺技术——缸孔喷涂技术,也可称为无缸套技术。
缸孔喷涂技术是指采用热喷涂技术(电弧喷涂或等离子喷涂)对经过粗化处理的铝发动机缸孔内壁喷涂一层合金涂层或者其他复合材料,以取代传统的铸铁缸套(见图7)。
喷涂了涂层后的铝合金缸体依旧是一体式缸体,涂层的厚度仅仅0.3mm,具有降低发动机重量、降低缸孔与活塞的摩擦和磨损、提高热传导、降低油耗和CO 2排放等优点。
6.曲轴的轻量化上汽大众发动机曲轴的结构优化已在技术允许的情况下把工件的减重、轻量化做到了极致。
所采取的主要措施有减少扇板数量, 从传统的8片减少到4片;减小扇板的宽度,并进行形状优化;缩小主轴颈的尺寸,平均缩小10%,如对两款系列产品中的一同类型发动机(1.6L MPI),EA111机型的主轴颈外径为50mm, EA211则减为40mm; 在每个连杆轴颈上加钻了去重孔。
其他细节上的结构优化就更多了, 如改变过渡部位的形状,采取圆角优化, 增加多处凹坑等。
如此, 两者在自重上相比,新一代EA211发动机的曲轴重量较之EA111平均要减轻15%~20%。
另据报道,天津一汽夏利内燃机制造分公司经过技术创新,在国内首先开发出主轴颈、拐颈为空的中空曲轴,使得曲轴重量降低15%。
7.活塞的轻量化Borgo Nova公司为BMW轿车2.0L 6缸发动机开发了一种轻型X形活塞,在裙部、销孔座及相应膨胀部位呈明显的X形状,如图6所示。
左侧表示轻型X形活塞,右侧为传统收缩窗式活塞。
X形活塞重量减轻100g,而其压缩高度、连杆长度不变,同时活塞摩擦面积减小,从而降低了机械摩损和单位燃油消耗。
整体组装后,X形活塞比传统收缩窗式活塞减重96g,即17.0%。
图 6Products & Technology产品与技术扫一扫看视频2014年,日产在1.6L4缸MR16DDT发动机上采用了电弧喷涂的气缸孔镜面涂覆技术(MBC)。
MBC技术使用电弧喷射工艺替代等离子喷涂工艺。
电弧喷射工艺可在气缸工作表面上形成许多小的气孔,即使没有进行珩磨网纹槽加工,这些气孔也会储有润滑油。
其结果表明,采用表面粗糙度为Ra0.05μm级的镜面精加工,除了能提高抗爆燃性能之外,对于降低气缸孔与活塞间的摩擦也有着良好效果。
目前,缸孔喷涂技术已在德国大众的EA211发动机、 Audi A8油电发动机、VW Lupo 1.4L TSI、G M O p e l 、尼桑G T -R 发动机、宝马最新的B系列发动机、新款福特野马ShelbyGT350上的5.2L V8发动机(Voodoo)、新款日产英菲尼迪Q 50上的3.0T V 6发动机(VR30DETT)等上得到了应用。
而在国内,一些汽车厂家和发动机制造厂家也已经开始探索这项新工艺。
2. 蠕墨铸铁缸体缸盖蠕墨铸铁是一种高强度材料,它的力学性能和铸造工艺性能介于灰口铸铁和球墨铸铁之间,很适合制造强度要求较高、且要求承受热循环负荷的零件,如气缸体、气缸盖等。
蠕墨铸铁的高刚度强度,说明汽缸可以在压力更高的环境下工作,更能容易实现尾气排放的要求;其次,发动机更能满足轻量化的需求,更具紧凑性,从而更符合重型柴油机缸体材料的发展趋势。