CE 并行工程
并行工程的优势分析
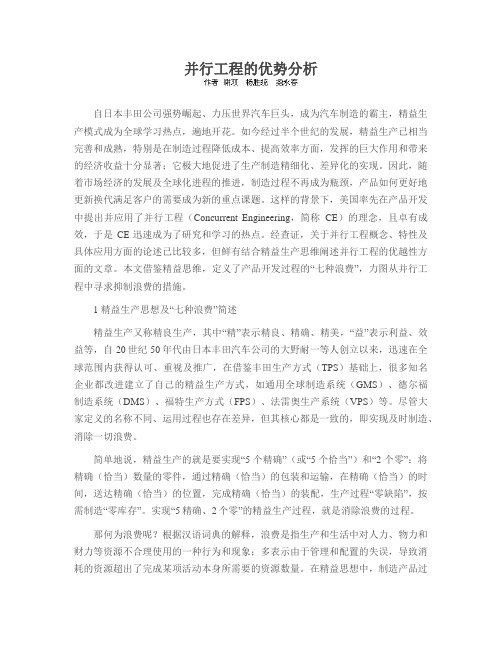
并行工程的优势分析自日本丰田公司强势崛起、力压世界汽车巨头,成为汽车制造的霸主,精益生产模式成为全球学习热点,遍地开花。
如今经过半个世纪的发展,精益生产已相当完善和成熟,特别是在制造过程降低成本、提高效率方面,发挥的巨大作用和带来的经济收益十分显著;它极大地促进了生产制造精细化、差异化的实现。
因此,随着市场经济的发展及全球化进程的推进,制造过程不再成为瓶颈,产品如何更好地更新换代满足客户的需要成为新的重点课题。
这样的背景下,美国率先在产品开发中提出并应用了并行工程(Concurrent Engineering,简称CE)的理念,且卓有成效,于是CE迅速成为了研究和学习的热点。
经查证,关于并行工程概念、特性及具体应用方面的论述已比较多,但鲜有结合精益生产思维阐述并行工程的优越性方面的文章。
本文借鉴精益思维,定义了产品开发过程的“七种浪费”,力图从并行工程中寻求抑制浪费的措施。
1 精益生产思想及“七种浪费”简述精益生产又称精良生产,其中“精”表示精良、精确、精美,“益”表示利益、效益等,自20世纪50年代由日本丰田汽车公司的大野耐一等人创立以来,迅速在全球范围内获得认可、重视及推广,在借鉴丰田生产方式(TPS)基础上,很多知名企业都改进建立了自己的精益生产方式,如通用全球制造系统(GMS)、德尔福制造系统(DMS)、福特生产方式(FPS)、法雷奥生产系统(VPS)等。
尽管大家定义的名称不同、运用过程也存在差异,但其核心都是一致的,即实现及时制造、消除一切浪费。
简单地说,精益生产的就是要实现“5个精确”(或“5个恰当”)和“2个零”:将精确(恰当)数量的零件,通过精确(恰当)的包装和运输,在精确(恰当)的时间,送达精确(恰当)的位置,完成精确(恰当)的装配,生产过程“零缺陷”,按需制造“零库存”。
实现“5精确、2个零”的精益生产过程,就是消除浪费的过程。
那何为浪费呢?根据汉语词典的解释,浪费是指生产和生活中对人力、物力和财力等资源不合理使用的一种行为和现象;多表示由于管理和配置的失误,导致消耗的资源超出了完成某项活动本身所需要的资源数量。
并行工程
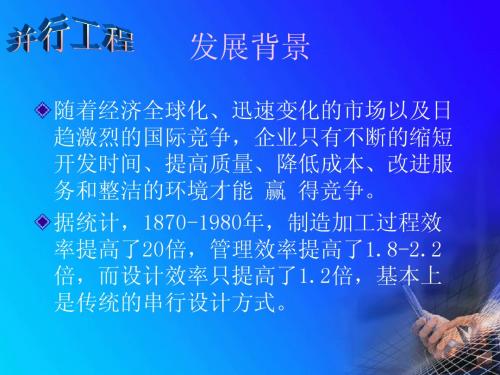
(2)采用IPT工作模式, 根据客车公司的实际情况 组建项目团队, 采用预发布和反馈的办法,并逐步 使之制度化。在方案设计和结构设计的一定阶段, 信向相关后续单位提前发布信息,一方面, 及时得 到息反馈, 以提高工艺性, 可加工性;另一方面, 由于后续单位提前参与设计, 使他们及时了解体 会设计意图, 同时可在适当时候进行工艺和生产 准备。
编辑任务设计书 方案设计 CAD CAE NO 评审 YES 初步设计 NO 评审 YES 详细设计 制定采 购方案 评审 YES 外协外购 件采购 样车试 制 NO NO 评审 YES 装配方案设计 NO 评审 YES 工艺规程编制 NO 评审 YES 编制工 艺 总方案
并行开发流程
工装预设计 CAD DFA CAE
案例
上海客车制造有限公 司对SK6115HP2-3 新 型客车的开发过程中 为满足客户需求, 开 拓市场,将原有串行 的开发过程转变为并 行的产品开发过程, 大量缩短产品开发周 期, 减少更改次数。
SK6115HP2-3
市场调查 方 案 设 计 方案设计 性能设 计 方案评审 初步设计 初步产品设计 详细产品设计 采购计 划 工装设计 采购 试 制 工装制造 样车制造 小批量试生 产 生产详细设 计 生产线设计 制定工艺总方案 装配方案设计 工艺过程设计 生产规划
传统串行工程的产品开发模式
用户
产品 需求分析
产品 设计
工艺 设计
生产 准备
加工 装配
质量 检验
修改 设计
串行产品开发过程
这种方式的缺陷是设计与制造的严重分离。 这种方式的缺陷是设计与制造的严重分离。设计 师只负责按照功能要求把产品设计出来, 师只负责按照功能要求把产品设计出来,至于如 何加工生产,则是工艺师的事, 何加工生产,则是工艺师的事,这被一些国外学 者形象地称为“扔过墙” wall)式的设 者形象地称为“扔过墙”(Over the wall)式的设 计。
第五章 并行工程

为解决这一问题,设计人员往往也应用 一些朴素的并行思想,如协商解决冲突, 提前发布信息等,但毕竟在产品开发过程 中,从宏观上描述开发活动的时序关系是 串行开发,并行思想只存在于设计人员的 潜在意识中,而且具有很大的随意性,这 将会造成对产品开发过程的管理松散,最 终导致开发周期的拖延。
2. 并行工程 并行工程是一种系统的集成方法,它采用 并行方法处理产品设计及其相关的过程, 包括制造过程和支持过程,它要求产品开 发人员从设计一开始就能考虑到产品整个 生命周期中从概念设计到产品报废处理的 所有因素,包括质量、成本、进度计划和 用户要求等等。
1.传统设计方法 长期以来,新产品的开发研制大多沿用传统的串行工程 方法,产品开发过程是顺序的、迭代式的,产品总是从一个 部门递交到另一个部门(例如:设计部门→工艺部门→制造 加工部门→总装测试部门等),每个部门都根据各自需要进 行修改,由于顺序工程设计方法在初始设计阶段不能全面地 考虑后续过程的多种需要(可制造性、可装配性、可测试性、 质量保证等),使所制造的产品存在许多缺点。因此,对原 设计必须进行必要的修改,从概念设计到工艺过程设计一直 到最终产品定型,可能在不同的环节中多次重复这一过程, 致使对原设计改动过大,推迟新产品上市时间。另外,由于 产品成本的70%是在概念设计阶段确定的,但概念设计修改 只占总费用的7%~10%,而采用顺序工程方法的代价是, 详细设计的修改费用是概念设计修改的10倍,生产制造工艺 阶段修改的费用是详细设计修改费用的10倍,从而使新产品 成本成倍提高,开发周期延长。因此,传统的设计方法无法 适应激烈市场竞争的需要,研究探索产品开发新方法是当务 之急。
5.2 串行工程与并行工程
1.串行工程 在传统的工程生产中,从市场需求分析至形 成原型产品,信息在整个产品开发过程中是以顺 序方式传递的,是在每个环节工作结束后才传递 至下一环节的,这种工作模式称为串行工程 (Sequential Engineering),也称顺序工程 (Serial Engineering),工作流程图见图5-1。整 个产品开发过程只是一个静态的、顺序的和互相 分离的流程。
并行工程与传统串行工程的比较

并行工程和传统串行工程的比较并行工程是对产品及其相关过程(包括制造过程和支持过程)进行并行、集成化处理的系统方法和综合技术。
1988年美国国家防御分析研究所(IDA—Institute of Defense Analyze)完整地提出了并行工程(CE—Concurrent Engineering)的概念,即“并行工程是集成地、并行地设计产品及其相关过程(包括制造过程和支持过程)的系统方法。
这种方法要求产品开发人员在一开始就考虑产品整个生命周期中从概念形成到产品报废的所有因素,包括质量、成本、进度计划和用户要求。
并行工程的目标为提高质量、降低成本、缩短产品开发周期和产品上市时间。
并行工程的具体做法是:在产品开发初期,组织多种职能协同工作的项目组,使有关人员从一开始就获得对新产品需求的要求和信息,积极研究涉及本部门的工作业务,并将所需要求提供给设计人员,使许多问题在开发早期就得到解决,从而保证了设计的质量,避免了大量的返工浪费.在产品的设计开发期间,将概念设计、结构设计、工艺设计、最终需求等结合起来,保证以最快的速度按要求的质量完成。
各项工作由与此相关的项目小组完成。
进程中小组成员各自安排自身的工作,但可以定期或随时反馈信息并对出现的问题协调解决。
依据适当的信息系统工具,反馈与协调整个项目的进行。
利用现代CIM 技术,在产品的研制与开发期间,辅助项目进程的并行化。
并行工程本质特点:1.并行工程强调面向过程和面向对象。
并行工程强调面向过程(Process-oriented)和面向对象(Object-oriented)一个新产品从概念构思到生产出来是一个完整的过程(process)。
传统的串行工程方法是基于二百多年前英国政治经济学家亚当·斯密的劳动分工理论。
该理论认为分工越细,工作效率越高。
因此串行方法是把整个产品开发全过程细分为很多步骤,每个部门和个人都只做其中的一部分工作,而且是相对独立进行的,工作做完以后把结果交给下一部门。
(智能制造)先进制造技术试题与答案
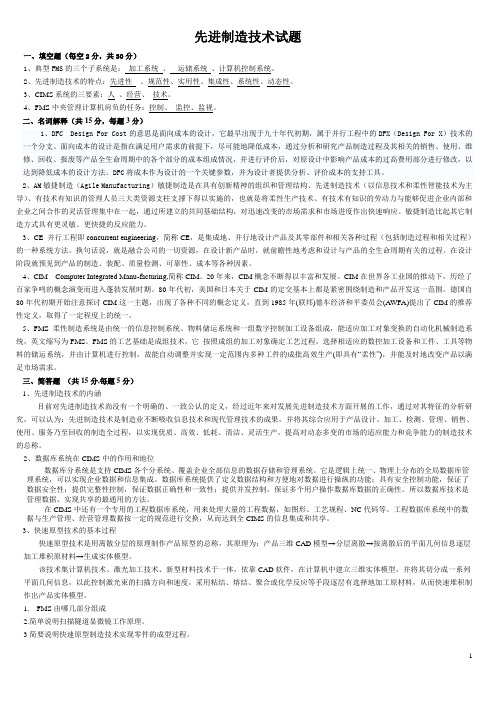
先进制造技术试题一、填空题(每空2分,共30分)1、典型FMS的三个子系统是:加工系统、运储系统、计算机控制系统。
2、先进制造技术的特点:先进性、规范性、实用性、集成性、系统性、动态性。
3、CIMS系统的三要素:人、经营、技术。
4、FMS中央管理计算机肩负的任务:控制、监控、监视。
二、名词解释(共15分,每题3分)1、DFC Design For Cost的意思是面向成本的设计,它最早出现于九十年代初期,属于并行工程中的DFX(Design For X)技术的一个分支。
面向成本的设计是指在满足用户需求的前提下,尽可能地降低成本,通过分析和研究产品制造过程及其相关的销售、使用、维修、回收、报废等产品全生命周期中的各个部分的成本组成情况,并进行评价后,对原设计中影响产品成本的过高费用部分进行修改,以达到降低成本的设计方法。
DFC将成本作为设计的一个关键参数,并为设计者提供分析、评价成本的支持工具。
2、AM敏捷制造(Agile Manufacturing)敏捷制造是在具有创新精神的组织和管理结构、先进制造技术(以信息技术和柔性智能技术为主导)、有技术有知识的管理人员三大类资源支柱支撑下得以实施的,也就是将柔性生产技术、有技术有知识的劳动力与能够促进企业内部和企业之间合作的灵活管理集中在一起,通过所建立的共同基础结构,对迅速改变的市场需求和市场进度作出快速响应。
敏捷制造比起其它制造方式具有更灵敏、更快捷的反应能力。
3、CE 并行工程即concurrent engineering,简称CE,是集成地、并行地设计产品及其零部件和相关各种过程(包括制造过程和相关过程)的一种系统方法。
换句话说,就是融合公司的一切资源,在设计新产品时,就前瞻性地考虑和设计与产品的全生命周期有关的过程。
在设计阶段就预见到产品的制造、装配、质量检测、可靠性、成本等各种因素。
4、CIM Computer Integrated Manu-facturing,简称CIM。
并行工程和传统串行工程两者的比较
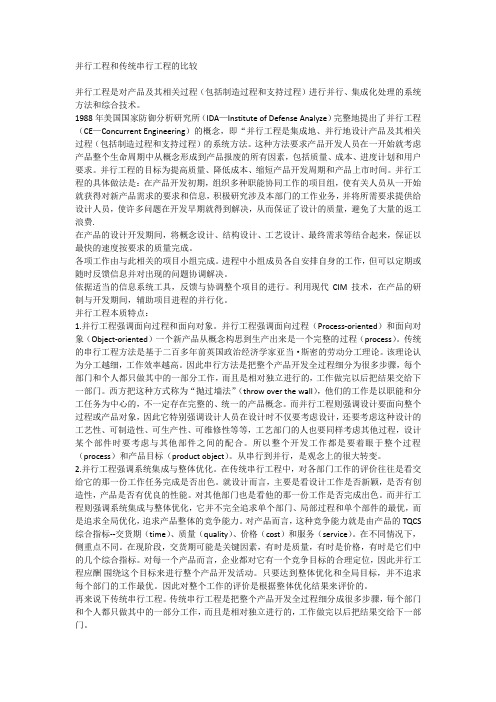
并行工程和传统串行工程的比较并行工程是对产品及其相关过程(包括制造过程和支持过程)进行并行、集成化处理的系统方法和综合技术。
1988年美国国家防御分析研究所(IDA—Institute of Defense Analyze)完整地提出了并行工程(CE—Concurrent Engineering)的概念,即“并行工程是集成地、并行地设计产品及其相关过程(包括制造过程和支持过程)的系统方法。
这种方法要求产品开发人员在一开始就考虑产品整个生命周期中从概念形成到产品报废的所有因素,包括质量、成本、进度计划和用户要求。
并行工程的目标为提高质量、降低成本、缩短产品开发周期和产品上市时间。
并行工程的具体做法是:在产品开发初期,组织多种职能协同工作的项目组,使有关人员从一开始就获得对新产品需求的要求和信息,积极研究涉及本部门的工作业务,并将所需要求提供给设计人员,使许多问题在开发早期就得到解决,从而保证了设计的质量,避免了大量的返工浪费.在产品的设计开发期间,将概念设计、结构设计、工艺设计、最终需求等结合起来,保证以最快的速度按要求的质量完成。
各项工作由与此相关的项目小组完成。
进程中小组成员各自安排自身的工作,但可以定期或随时反馈信息并对出现的问题协调解决。
依据适当的信息系统工具,反馈与协调整个项目的进行。
利用现代CIM技术,在产品的研制与开发期间,辅助项目进程的并行化。
并行工程本质特点:1.并行工程强调面向过程和面向对象。
并行工程强调面向过程(Process-oriented)和面向对象(Object-oriented)一个新产品从概念构思到生产出来是一个完整的过程(process)。
传统的串行工程方法是基于二百多年前英国政治经济学家亚当·斯密的劳动分工理论。
该理论认为分工越细,工作效率越高。
因此串行方法是把整个产品开发全过程细分为很多步骤,每个部门和个人都只做其中的一部分工作,而且是相对独立进行的,工作做完以后把结果交给下一部门。
并行工程:介绍及应用

④ 技术集成:产品开发全过程中涉及的多学科知识以及各种技术、 方法的集成,形成集成的知识库、方法库。
BACK
四:并行工程实例分析
随着商业飞机的不断发展,波音公司在原有模式下的 产品成本不断增加,并且积压的飞机越来越多。在激烈的 市场竞争当中,波音公司是如何用较少的费用设计制造高 性能的飞机?资料分析表明,产品设计制造过程中存在着 巨大的发展潜力,节约开支的有效途径是减少更改、错误 和返工所带来的消耗。 一个零件从设计完成后,要经过工艺计划、工装设计 制造、制造和装配等过程,在这一过程内,设计约占15% 的费用,制造占85%的费用,任何在零件图纸交付前的设 计更改都能节约其后85%的生产费用。
三:并行工程的特点特性
并行特性 整体特性 协同特性 集成特性
并行特性
CE的最大特点是把时间上有先有后的作业过程转 变为同时考虑和尽可能同时(或并行)处理的过 程; 在产品的设计阶段就并行地考虑了产品整个产品 生命周期中的所有因素,研制周期将明显地缩短。 这样设计出来的产品不仅具有良好的性能,而且 易于制造、检验和维护。
并行工程发展趋势
我国关于并行工程的研究工作主要集中在高校中, 据不完全统计如下表所示:
单位名称 清华大学 华中理工大学 主要研究方向 面向CE的CAD/CAPP/CAM的集成研究、DFM等 并行设计的零件信息模型、面向CE的设备环境建模等
上海交通大学
北京航空航天大学 西安交通大学 西北工业大学 北京理工大学 天津大学
程)进行并行、一体化设计的一种系统化工作模式。这种
工作模式力图使开发者从一开始就考虑到产品全生命周期 应避免的几个误解
不是通过简单的并行来缩短 产品开发周期, 而是通过过 CE是设计与制造的并行或同步 程分解、IPT成员之间的信 息和知识共享等方法, 打破 传统的专业壁垒, 增加设计 CE是设计活动的并发或并行 科学的管理思想和先进 活动间的协作, 从而获取更 技术的集成 高的效益
机械制造的新工艺和新方法
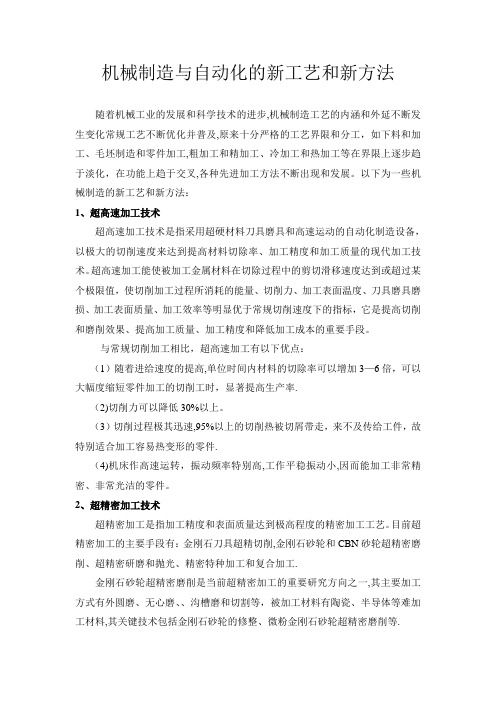
机械制造与自动化的新工艺和新方法随着机械工业的发展和科学技术的进步,机械制造工艺的内涵和外延不断发生变化常规工艺不断优化并普及,原来十分严格的工艺界限和分工,如下料和加工、毛坯制造和零件加工,粗加工和精加工、冷加工和热加工等在界限上逐步趋于淡化,在功能上趋于交叉,各种先进加工方法不断出现和发展。
以下为一些机械制造的新工艺和新方法:1、超高速加工技术超高速加工技术是指采用超硬材料刀具磨具和高速运动的自动化制造设备,以极大的切削速度来达到提高材料切除率、加工精度和加工质量的现代加工技术。
超高速加工能使被加工金属材料在切除过程中的剪切滑移速度达到或超过某个极限值,使切削加工过程所消耗的能量、切削力、加工表面温度、刀具磨具磨损、加工表面质量、加工效率等明显优于常规切削速度下的指标,它是提高切削和磨削效果、提高加工质量、加工精度和降低加工成本的重要手段。
与常规切削加工相比,超高速加工有以下优点:(1)随着进给速度的提高,单位时间内材料的切除率可以增加3—6倍,可以大幅度缩短零件加工的切削工时,显著提高生产率.(2)切削力可以降低30%以上。
(3)切削过程极其迅速,95%以上的切削热被切屑带走,来不及传给工件,故特别适合加工容易热变形的零件.(4)机床作高速运转,振动频率特别高,工作平稳振动小,因而能加工非常精密、非常光洁的零件。
2、超精密加工技术超精密加工是指加工精度和表面质量达到极高程度的精密加工工艺。
目前超精密加工的主要手段有:金刚石刀具超精切削,金刚石砂轮和CBN砂轮超精密磨削、超精密研磨和抛光、精密特种加工和复合加工.金刚石砂轮超精密磨削是当前超精密加工的重要研究方向之一,其主要加工方式有外圆磨、无心磨、、沟槽磨和切割等,被加工材料有陶瓷、半导体等难加工材料,其关键技术包括金刚石砂轮的修整、微粉金刚石砂轮超精密磨削等.金刚石砂轮的修整包括整形和修锐两部分,对于密实型无气孔的金刚石砂轮,如金属结合剂金刚石砂轮,一般在整形后还需要修锐;有气孔型陶瓷结合剂金刚石砂轮在整形后即可使用。
CE案例-福特

Additional Reading 3并行工程案例--福特Taurus早在20世纪80年代初,福特就开始了一种新型的前轮驱动中型车的早期策划。
当时的商业环境包括了一些不利的因素:激烈的国际竞争、市场份额减少和油价开始大幅度上涨。
针对这些情况,福特得出的结论是,用一种新的方法来设计车型是非常重要的。
这种新方法的基础是“顾客满意度”并结合了Taurus车型要做同类车中最好产品的目标。
这个“同类车型中最好的”着重点使得福特公司采取一些不同寻常的方法来进行策划。
其中一项打破传统的方法是产生了进行Taurus车型策划的组织。
按惯例,新车型的设计要使用传统的组织结构4-4。
在这样一个传统的组织结构中,主要的活动是按顺序进行的:策划部门研究顾客的需求然后交给工程师;工程师制定详细的规格要求;最后将这一系列的成果交付生产。
然后,这种顺序的方法导致了在设计过程中部门与部门之间很少进行沟通——每一个部门都将它们的成果“扔过墙”到下一个部门,这种缺少沟通经常会给接下来的内部顾客部门带来问题。
在Tarurs车型策划过程中,福特在项目的开始阶段组建了项目团队。
例如,在详细的规格要求最终定下来之前,生产部门与设计部门同工作。
这种方法使得团队在制定规格要求时将重点放在产品的可生产性上。
现在我们来解释Taurus和野马项目是怎样进行的。
1.确定项目。
这个步骤有三个具体的子步骤:a.进行使命陈述——目的、范围和项目的目标。
b.组建团队来做策划。
c.对方案的执行进行计划——责任、计划安排、资源和达到的效果。
一些用来确定项目的工具包括竞争性分析、竞争性评价和目标展开。
对于早期的福特(20世纪80年代初期),其质量目标是该类别中最好的。
对于1994年的福特野马,共有4个量化的质量目标,如“每1000个产品的错误率”。
野马团队是跨职能的团队,其中包括来自不同部门的代表。
这些部门包括设计工程、生产和组装、销售和市场、采购和财务部门。
这个团队的作用相当与质量策划项目团队。
并行工程
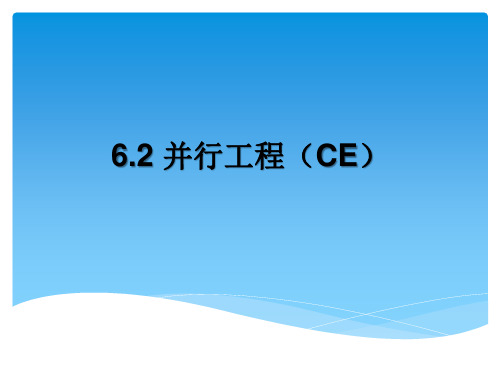
并行工程的特征
2.整体特征
◆CE认为,制造系统(包括制造过程)是一个有机的整体,在空间 中似乎相互独立的各个制造过程和知识处理单元之间,实质上 都存在着不可分割的内在联系。 ◆CE强调全局性的考虑问题,即产品研制者从一开始就考虑到 产品整个生命周期中的所有因素。 ◆并行工程追求的是整体最优。有时为保证整体最优,甚至可 能不得不牺牲局部的利益。
并行工程关键技术
2.集成的产品信息模型
并行工程强调产品设计过程上下游协调与控制, 以及多专 家系统协调工作,因此一个集成的产品信息模型就成为关键问 题。 集成的产品信息模型应能够全面表达产品信息、工艺信息、 制造信息以及产品生命周期内各个环节的信息,能够表达产品 各个版本的演变历史,能够表示产品的可制造性、可维护性和 安全性,能够使设计小组成员共享模型中的信息。这样的模型 应基于STEP标准对产品所有信息进行定义和描述,包括用户 要求、产品功能、设计、制造、材料、装配、费用和评价等各 类特征信息;采用Express语言和面向对象的技术,对产品信息 模型进行描述和表达;并把Er-press语言中各个实体映射到C+ + 语言中的类,生成STEP中性文件,为产品设计(CAD)、工艺设 计(CAPP)、 可制造性评价以及制造过程(CAM) 的集成与并行 实施提供充分的信息。
并行工程的运行模式
并行工程与CIM一样,也是企业管理的一种新 模式、新思想,两者所追求的目标相同即“提高企 业市场竞争能力,赢得市场竞争”。然而,两者的 着眼点和运行模式却有所区别。CIM强调的是企业 内的信息集成,保证企业各部门的信息流通畅无阻; 而并行工程强调的是企业产品开发过程的集成。
并行工程的运行模式
并行工程的特征
3.协同特征
并行工程
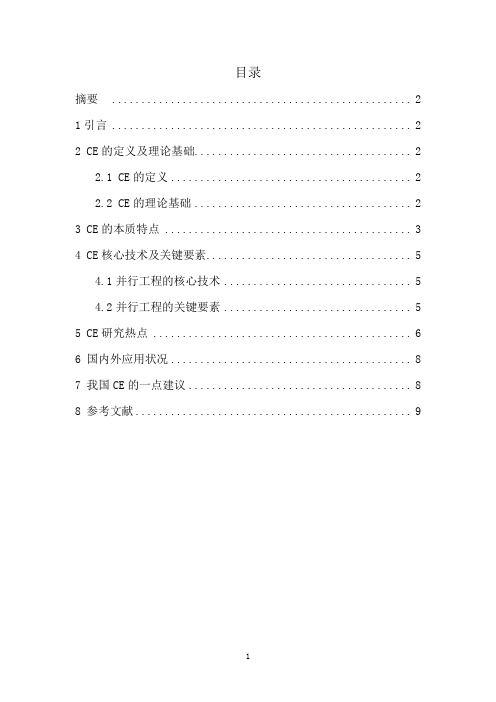
目录摘要 (2)1引言 (2)2 CE的定义及理论基础 (2)2.1 CE的定义 (2)2.2 CE的理论基础 (2)3 CE的本质特点 (3)4 CE核心技术及关键要素 (5)4.1并行工程的核心技术 (5)4.2并行工程的关键要素 (5)5 CE研究热点 (6)6 国内外应用状况 (8)7 我国CE的一点建议 (8)8 参考文献 (9)并行工程摘要并行工程自上世纪80年代产生以来,已经在制造业,服务业等众多产业及领域产生了显著的经济效益。
本文从并行工程(CE)产生背景,定义及理论基础,CE的本质,核心技术及关键要素,CE的研究热点,国内外应用状况,及结论和给我国实行CE的建议来探讨并行工程。
关键字:并行工程(CE) 核心技术关键要素1引言新产品的开发长期以来一直采用“串行”方式进行:市场调研→产品计划→产品设机→修改设计→工艺准备→正式投产。
在这种开发模式中,以上诸环节需按固定顺序进行,多个环节不能同时进行。
若前期某个环节出现问题,往往会影响后期环节的开发。
这会使产品开发过程成为设计、加工、测试、修改、设计大循环。
造成产品设计工作量大,产品开发周期长,成本增加。
20 世纪80 年代中期以来,同类商品日益增多,企业之间的竞争愈来愈激烈,而且越来越具有全球性。
竞争焦点就是满足用户的TQCS(上市时间、产品质量、产品成本和售后服务)等指标,竞争的核心问题就是时间。
为解决上述问题,提高市场竞争力,以最快的速度设计出高质量的产品,并尽快投放市场,在20世纪80年代末,制造业提出了并行工程(Concurrent Engineering, CE)的思想。
2 CE的定义及理论基础2.1 CE的定义l988年美国国防分析研究所(简称IDA)为了改进国防武器和军用产品的生产,缩短生产周期,降低成本,首次提出了并行工程的概念,即并行工程是对产品及其相关过程(包括制造和支持过程)进行集成并行设计的系统化工作模式,这种方法要求产品开发人员在设计一开始就考虑产品整个周期(从概念形成到报废)中的各种因素,包括质量、成本、进度及用户需求等,以便最大限度提高产品的开发效率和一次性成功率。
并行工程在先进制造技术中的应用

并行工程在先进制造技术中的应用摘要在市场经济大潮中,企业之间的竞争主要是交货期、质量、成本和服务,即所谓的TQCS(Time,QuaIity,Cost and Service)之间的竞争。
并行工程的思想改变了传统的生产管理模式,经过精心组织,能够有效地缩短交货期,降低生产成本,改善产品质量。
因此,一经提出即成为众多企业革新的主要内容,也成为许多企业赢得竞争的法宝。
关键词:并行工程;CAx; DFx;过程建模;结构化分析并行工程的提出传统的产品开发过程是按顺序从上一个部门递交给下一个部门,每个部门则根据各自的需要或工艺特点对产品进行修改,这种方式被形象地称为“抛过墙”设计开发过程或串行工程。
由于这种方式在设计时不能全面考虑后续环节的各种合理要求(如制造性、装配性、测试性、质量保证等),因此到达下一环节后不得不对原设计方案提出修改意见,再返回上游环节进行修改。
这种状况有时候会在同一个环节中反复多次,以致于大大延长产品的开发周期,而且在部门协调过程中不可避免地造成对原设计方案大的改动,假如部门之间的要求一时难以协调,那么所制造出来的产品必将存在较多缺陷或隐患。
这种方式的长期有在无疑将削弱企业的信誉和竞争力,甚至导致一个企业的破产和倒闭。
因此,面对日益激烈的竞争,各个企业都在寻找一种更加能够适应市场需求的产品开发模式。
研究表明,产品成本的70%是由概念设计阶段确定的,而概念设计修改只占总费用的7%一10%,后续环节的修改费用则是上游环节修改费用的10倍,如详细设计的修改费用是概念设计修改费用的10倍,生产工艺制造阶段修改费用是详细设计修改费用的10倍。
也就是说,在产品开发过程中把一个问题带入下一个环节将导致产品成本成倍提高,如果可以在产品开发初期就很好考虑后续环节的需求、并认真予以解决,即改变原来把产品开发只作为研究开发部门的任务的组织模式,认为产品开发是设计、工艺、制造、销售、维护部门之间的直接触合,组成产品开发小组(Teamwork),那么不但可以降低成本,还可以大大缩短产品开发周期,改善产品质量。
并行工程

结语
虽然并行工程在实际应用中产生 了如此巨大的效果,但是也还存在一些不 易解决的问题,如:在设计中考虑后 续工作增加了当前工作的难度,支持并 行工程的主模型还未统一,工 程数据库还没有完全成熟等。
谢谢大家
并行工程的体系结构
(3) 质量管理分系统
以质量功能配置为核心,对产品开发过程全生命 周期中的各个环节进行分析,提出质量功能要求,以 保证所生产的产品能最大限度地满足用户和市场的需 求。
(4)生产制造分系统
其主要工作是生产计划与调度、工况监控、设备 运行等。
并行工程的体系结构
(5)支持环境分系统
并行工程的概念
这种方法要求产品开发人员在一开始就 考虑产品整个生命周期中从概念形成到 产品报废的所有因素,包括质量、成本、 进度计划和用户要求。并行工程的目标 为提高质量、降低成本、缩短产品开发 周期和产品上市时间。
并行工程的概念
并行工程的具体做法是: 在产品开发初期,组织 多种职能协同工作的项 目组,使有关人员从一 开始就获得对新产品需 求的要求和信息,积极 研究涉及本部门的工作 业务,并将所需要求提 供给设计人员,使许多 问题在开发早期就得到 解决,从而保证了设计 的质量,避免了大量的 返工浪费.
二 并行工程的特点
1.
并行工程不是某一种系 统或结构,不能象软件 或硬件系统一样买来安 装上即可运行,它是一 种自顶向下进行规划、 自底向上进行实施的一 种哲理和方法论。其特 点为:
2.
3.
4. 5.
6. 7.
8.
突出人的作用,强调人的协同 作用。 一体化、并行地进行产品及其 相关过程的设计。 重视满足客户的要求,注重产 品质量。 持续地改善产品有关过程。 注重信息与知识财富的开发利 用与管理。 注重目标的不变性。 并行工程不能省去串行工作中 任何环节。 并行工程不是使设计与制造重 叠或同时进行。
并行工程案例分析
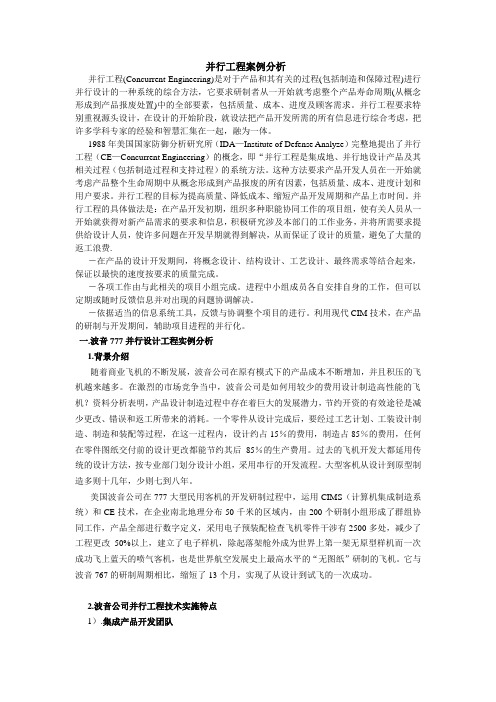
并行工程案例分析并行工程(Concurrent Engineering)是对于产品和其有关的过程(包括制造和保障过程)进行并行设计的一种系统的综合方法,它要求研制者从一开始就考虑整个产品寿命周期(从概念形成到产品报废处置)中的全部要素,包括质量、成本、进度及顾客需求。
并行工程要求特别重视源头设计,在设计的开始阶段,就设法把产品开发所需的所有信息进行综合考虑,把许多学科专家的经验和智慧汇集在一起,融为一体。
1988年美国国家防御分析研究所(IDA—Institute of Defense Analyze)完整地提出了并行工程(CE—Concurrent Engineering)的概念,即“并行工程是集成地、并行地设计产品及其相关过程(包括制造过程和支持过程)的系统方法。
这种方法要求产品开发人员在一开始就考虑产品整个生命周期中从概念形成到产品报废的所有因素,包括质量、成本、进度计划和用户要求。
并行工程的目标为提高质量、降低成本、缩短产品开发周期和产品上市时间。
并行工程的具体做法是:在产品开发初期,组织多种职能协同工作的项目组,使有关人员从一开始就获得对新产品需求的要求和信息,积极研究涉及本部门的工作业务,并将所需要求提供给设计人员,使许多问题在开发早期就得到解决,从而保证了设计的质量,避免了大量的返工浪费.-在产品的设计开发期间,将概念设计、结构设计、工艺设计、最终需求等结合起来,保证以最快的速度按要求的质量完成。
-各项工作由与此相关的项目小组完成。
进程中小组成员各自安排自身的工作,但可以定期或随时反馈信息并对出现的问题协调解决。
-依据适当的信息系统工具,反馈与协调整个项目的进行。
利用现代CIM技术,在产品的研制与开发期间,辅助项目进程的并行化。
一.波音777并行设计工程实例分析1.背景介绍随着商业飞机的不断发展,波音公司在原有模式下的产品成本不断增加,并且积压的飞机越来越多。
在激烈的市场竞争当中,波音公司是如何用较少的费用设计制造高性能的飞机?资料分析表明,产品设计制造过程中存在着巨大的发展潜力,节约开资的有效途径是减少更改、错误和返工所带来的消耗。
10_Concurrent_Engineering

10. Concurrent Engineering并行工程并行工程(Concurrent Engineering)是随着CAD、CIMS技术发展提出的一种新哲理、新的系统工程方法。
这种方法的思路,就是并行的、集成的设计产品及其开发的过程。
According to Department of Defense (DoD) Regulations 5000.1 and 5000.2, concurrent engineering (CE) will be used for development of all future military systems. The primary requirements for successfully implementing a CE philosophy are management support, enhanced communication, team building and appropriate tool use. Where CE has been successful, much credit is attributed to the involvement of senior management in establishing goals of improved quality, cost and schedule; in forming teams of qualified people; and in providing teams with the necessary tools and resources. Management must commit the necessary funding and resources for a successful CE program, and they must allow ample time for the new philosophy to generate benefits.根据国防部(DoD)条例5000.1和5000.2,并行工程(CE)将用于所有未来军事系统的发展。
ce并行工程师名词解释

ce并行工程师名词解释嘿,朋友!今天咱来聊聊“CE 并行工程师”这个听起来有点神秘的名词。
你知道吗,CE 并行工程师就像是战场上的多面手!他们可不是那种只会在一条道上闷头走的人。
打个比方,咱们平常盖房子,有负责设计图纸的,有搬砖砌墙的,还有搞装修的。
但 CE 并行工程师呢,就像是那个既懂设计,又能砌墙,还晓得怎么把房子装修得漂漂亮亮的全能选手。
CE 并行工程师得有很广的知识面,就像武侠小说里的大侠,十八般武艺样样精通。
他们要懂硬件,知道那些电子元件咋工作;也要懂软件,清楚程序代码怎么写。
这就好比你既要会骑马射箭,又要会舞刀弄剑,是不是挺牛?他们还得有超强的协调能力。
想象一下,一个大项目就像一场盛大的音乐会,有拉小提琴的,有吹笛子的,还有敲鼓的。
CE 并行工程师就是那个指挥家,得让各个部分和谐有序,不能乱了套。
如果没协调好,这“音乐会”不就成了噪音大杂烩啦?而且啊,他们要有敏锐的洞察力。
就像猎人在森林里,能迅速发现猎物的踪迹。
在复杂的项目中,能一眼看出问题的关键所在,及时解决,避免小问题变成大麻烦。
CE 并行工程师还得有很好的抗压能力。
项目紧,任务重,各种问题一股脑儿涌来,要是没点抗压的本事,早就被压垮啦。
这就像在暴风雨中航行的船,得稳稳地掌好舵。
他们的工作可不轻松,常常要加班加点,和时间赛跑。
但正是因为有了他们,很多复杂的项目才能顺利推进,就像火车在轨道上稳稳地飞驰。
所以说,CE 并行工程师是一群了不起的人,他们用自己的智慧和汗水,为科技的发展添砖加瓦。
他们是幕后的英雄,虽然可能不被大众所熟知,但他们的付出和努力,实实在在地推动着社会的进步。
你说,咱们能不佩服他们吗?。
- 1、下载文档前请自行甄别文档内容的完整性,平台不提供额外的编辑、内容补充、找答案等附加服务。
- 2、"仅部分预览"的文档,不可在线预览部分如存在完整性等问题,可反馈申请退款(可完整预览的文档不适用该条件!)。
- 3、如文档侵犯您的权益,请联系客服反馈,我们会尽快为您处理(人工客服工作时间:9:00-18:30)。
CE 并行工程第一节并行工程的理论一、并行工程的产生背景并行工程产生之前,产品功能设计、生产工艺设计、生产准备等步骤以串行生产方式进行。
这样的生产方式的缺陷在于:后面的工序是在前一道工序结束后才参与到生产链中来,它对前一道工序的反馈信息具有滞后性。
一旦发现前面的工作中含有较大的失误,就需要对设计进行重新修改、对半成品进行重新加工,于是会延长产品的生产周期、增加产品的生产成本、造成不必要的浪费。
产品的质量也不可避免地受到影响。
1986年,美国国防工程系统首次提出了“并行工程”的概念,初衷是为了改进国防武器和军用产品的生产,缩短生产周期,降低成本。
由于该方法的有效性,不久,各国的企业界和学术界都纷纷研究它,并行工程方法也从军用品生产领域扩展到民用品生产领域。
二、并行工程的概念关于并行工程有很多定义,但是,至今得到公认的是1986年美国国防分析研究所在其R-338研究报告中提出的定义: “并行工程是对产品及其相关过程(包括制造过程和支持过程)进行并行的一体化设计的一种系统化的工作模式。
这种工作模式力图使开发者们从一开始就考虑到产品全生命周期(从概念形成到产品报废) 中的所有因素,包括质量、成本、进度和用户需求”。
简要地来讲,并行工程即Concurrent Engineering,CE,是集成地、并行地设计产品及其零部件和相关各种过程(包括制造过程和相关过程)的一种系统方法。
换句话说,就是融合公司的一切资源,在设计新产品时,就前瞻性地考虑和设计与产品的全生命周期有关的过程。
在设计阶段就预见到产品的制造、装配、质量检测、可靠性、成本等各种因素。
并行工程使企业在设计阶段就预见到产品的整个生命周期,是一种基于产品整个生命周期的具备高度预见性和预防性的设计。
需要指出的是,有人把并行工程简单地等同于并行生产或者并行工作,认为并行工程就是同时或者交错地开展生产活动。
这种看法是错误的。
并行工程最大的一个特点是强调所有的设计工作要在生产之前完成。
第二节并行工程的实施一、并行工程的实施方法并行工程方法的实质就是要求产品开发人员与其他人员一起共同工作,在设计阶段就考虑产品整个生命周期中从概念形成到产品报废处理的所有因素,包括质量、成本、进度计划和用户的要求。
从上述定义可以看出,要想开展并行工程,必须从如下几个方面来努力:团队工作方式并行工程在设计一开始,就应该把产品整个生命周期所涉及的人员都集中起来,确定产品性能,对产品的设计方案进行全面的评估,集中众人的智慧,得到一个优化的结果。
这种方式使各方面的专才,甚至包括潜在的用户都汇集在一个专门小组里,协同工作,以便从一开始就能够设计出便于加工、便于装配、便于维修、便于回收、便于使用的产品。
并行工程需要成员具备团队精神,这样不同专业的人员才能在一起协同工作(Team work)。
这样的工作方式从相当大程度上克服了原来串行生产模式的弊病。
过去,由于单个设计人员的知识和经验的局限性,很难全面地考虑到产品生产中各个阶段的要求;加上设备、工艺、材料的复杂性和多样性,难以对多个设计方案进行充分的评价和筛选,在时间紧迫的情况下,设计人员大多选择最方便的方案,而不是最适宜的方案。
于是返工现象就在所难免。
技术平台实施并行工程,必须有相应的技术支持,才能完成基于计算机网络的并行工程。
技术平台包括:(1)一个完整的公共数据库,它必须集成并行设计所需要的诸方面的知识、信息和数据,并且以统一的形式加以表达。
(2)一个支持各方面人员并行工作、甚至异地工作的计算机网络系统,它可以实时、在线地在各个设计人员之间沟通信息、发现并调解冲突。
(3)一套切合实际的计算机仿真模型和软件,它可以由一个设计方案预测、推断产品的制造及使用过程,发现所隐藏的阻碍并行工程实施的问题。
对设计过程进行并行管理技术平台是并行工程的物质基础,各行业专家是并行工程的思想基础。
并行工程是基于专家协作的并行开发。
但是,并不是说有了专家和技术平台,就自然而然地产生效益,还要对这个并行过程进行有效地管理。
由于每个专业的人士受其专业知识的限制,往往对产品的某一个方面的因素考虑得较多,而忽视了产品的整体指标,因此要确定一个全面的设计方案,需要各专家多次的交流、沟通和协商。
在设计过程中,团队领导要定期或者不定期地组织讨论,团队成员都畅所欲言,可以随时对设计出的产品和零件从各个方面进行审查,力求使设计出的产品不仅外观美、成本低、便于使用;而且便于加工,便于装配,便于维修,便于运送,在产品的综合指标方面达到一个满意值。
这种并行工程方式与传统方式相比,可以保证设计出的最终原型能够集中各方面专家的智慧,是一个现行情况下最完美的模型,在很大程度上可以避免设计缺陷造成产品返工,由于设计反复修改引起人、财、物的浪费。
图6.1和6.2表现了传统设计方式与并行工程方式的区别。
图6.1 传统设计过程图6.2 并行设计过程强调设计过程的系统性并行设计将设计、制造、管理等过程纳入一个整体的系统来考虑,设计过程不仅出图纸和其它设计资料,还要进行质量控制、成本核算,也要产生进度计划等。
比如在设计阶段就可同时进行工艺(包括加工工艺、装配工艺和检验工艺)过程设计,并对工艺设计的结果进行计算机仿真,直至用快速原型法产生出产品的样件。
见图6.3:基于网络进行快速反馈并行工程往往采用团队工作方式,包括虚拟团队。
在计算机及网络通讯技术高度发达的今天,工作小组完全可以通过计算机网络向各方面专家咨询,专家成员既包括企业内部的专家,也包括企业外部的专家。
工作方式见图6.4。
图6.4 基于网络的设计团队这样专家可以对设计结果及时进行审查,并及时反馈给设计人员。
不仅大大缩短设计时间,还可以保证将错误消灭在“萌芽”状态。
图中的计算机、数据库和网络是并行工程必不可少的支撑环境。
二、并行工程的实施效益实施并行工程,会为企业带来许多明显的效益:缩短产品投放市场的时间顾客正要求越来越短的交货期。
在产品供不应求的时代,顾客主要考虑产品的功能,要求功能的完善程度和实用性,其它的要求则放在次要的位置。
随着制造技术的发展,商品充足,顾客看重产品的价格。
当制造商通过诸如精益生产等方式尽力降低成本,把价格降到一定程度后,顾客又注重产品质量。
市场的发展态势表明,缩短交货期将会成为下一阶段的主要特征。
并行工程技术的主要作用就是可以大大缩短产品开发和生产准备时间。
据报道,由于实施了并行工程的虚拟产品开发策略,福特公司和克莱斯勒公司将他们新型汽车的开发周期由36个月缩短至24个月。
设计和试制周期仅为原来的50%。
降低成本并行工程可在三个方面降低成本:首先,它可以将错误限制在设计阶段。
据有关资料介绍,在产品生命周期中,错误发现的愈晚,造成的损失就愈大。
其次,并行工程不同于传统的“反复试制样机”、“反复做直到满意”的作法,强调“一次达到目的”。
这种“一次达到目的”的要求是靠软件仿真和快速样件生成实现的,省去了昂贵的样机试制;其三,由于在设计时考虑到加工、装配、检验、维修等因素,强调了产品的整体成本优化,因此,产品的全生命周期成本就降低了,既有利于顾客,也有利于制造者。
提高质量采用并行工程技术,尽可能将所有质量问题消灭在设计阶段,使所设计的产品便于制造,易于维护。
这就为质量的“零缺陷”提供了基础,使得制造出来的产品甚至用不着检验就可上市。
事实上,根据现代质量控制理论,质量首先是设计出来的,其次才是制造出来的,并不是检验出来的。
检验只能去除废品,而不能提高质量。
并行工程技术主要是从根本上保证了质量的提高。
例如福特(Ford)公司和克莱斯勒(Chrysler)公司与IBM合作开发的虚拟制造环境用于其新型车的研制。
在样车生产之前,发现其定位系统的控制及其他许多设计缺陷,避免了公司以后的损失。
增强功能的实用性由于并行工程在设计过程中,同时有销售人员参加,有时甚至还包括顾客,这样的设计方法紧贴市场趋势,反映了用户的需求,从而保证去除顾客不需要的冗余功能,降低设备的复杂性,提高产品的可靠性和实用性。
另外并行工程增强了企业的市场竞争能力。
由于并行工程可以较快地推出适销对路的产品并投放市场,而且设计模型合理使生产制造成本降低,同时保证产品质量,因而,企业的市场竞争能力将会得到加强。
第三节并行工程的实例目前,并行工程广泛地应用在国防、飞机、汽车、电子、机械制造等行业,产品从简单零件的开发到诸如飞机、计算机等复杂系统的开发,从单件产品(如车载导弹装置)发展到批量产品(如汽车)。
下面举几个例子来说明。
一、并行工程在国外的应用波音公司的飞机生产美国波音飞机制造公司投资40多亿美元,研制波音777型喷气客机,采用庞大的计算机网络来支持并行设计和网络制造。
从1990年10月开始设计到1994年6月仅花了3年零2个月就试制成功,进行试飞,一次成功,即投入运营。
在实物总装后,用激光测量偏差,飞机全长63.7米,从机舱前端到后端50米,最大偏差仅为0.9毫米。
波音777 的整机设计、部件测试、整机装配以及各种环境下的试飞均是在计算机上完成的,使其开发周期从过去8年时间缩短到3年多,甚至在一架样机未生产的情况下就获得了订单。
如果没有并行工程技术的应用,设计如此庞大的设备,要想在这么短的时间内,达到这样高的精度,几乎是不可能的。
波音公司在其它的飞机制造中也广泛地使用了并行工程技术。
波音—西科斯基公司在设计制造RAH-66直升机时,使用了全任务仿真的方法进行设计和验证,通过使用数字样机和多种仿真技术,花费4590小时的仿真测试时间,却省却了11590小时的飞行时间,节约经费总计6.73亿美元,获得了巨大收益。
同时,数字式设计使得所需的人力减到最少,在CH-53E 型直升机设计中,38名绘图员花费6个月绘制飞机外形生产轮廓图,而在RAH-66中,一名工程师用一个月就完成了。
AT&T公司的产品生产AT&T公司在生产计算机配套印刷组产品时,由于原来的设计中未考虑生产工艺性问题,致使产品质量低下,合格率仅为5%。
采用并行设计以后,利用计算机虚拟检测,找出设计中的缺陷,使产品合格率达到90%。
HP公司的产品开发HP公司采用并行工程来改进产品质量,其实施要点包括管理部门的支持、对用户的关注、统计过程控制、系统的问题解决过程以及全体人员参与五个方面。
实施的结果是公司全部产品的综合故障降低了83%,制造成本减少了42%,而产品开发周期缩短了35%。
二、并行工程在中国的应用齐车公司是我国一家专门生产铁路货车的大型工业企业。
过去,在企业的铁路货车产品开发过程中,产品开发周期长。
体现在:设计过程中,数据传递速度慢,不能集成与共享,数据的一致性与完整性难以保证;更改管理过程不规范,易产生意外错误;手工纸质管理方式管理繁杂、查询困难,使利用已有资源受到限制,而铁路货车产品的继承性较强,这就严重影响了已有资源的有效利用,难以进行快速开发。