FMEA补充讲义
FMEA工程应用培训讲义

FMEA工程应用培训讲义FMEA (Failure Mode and Effects Analysis)是一种常用的风险管理工具,广泛应用于工程设计和制造过程中,旨在提前识别和消除潜在的故障和缺陷。
FMEA可以帮助工程师在设计和制造过程中确定风险,并制定相应的措施来降低潜在故障和缺陷的发生概率。
一、FMEA的基本原理1.1 FMEA的概念FMEA是一种通过系统化的方法,对产品、设计或工作过程中的潜在故障模式进行分析和评估的方法。
通过找出故障模式的潜在原因和效应,可以采取相应的预防措施来减少故障的发生。
1.2 FMEA的目的FMEA的主要目的是通过提前识别和消除潜在的故障和缺陷,提高产品和流程的可靠性和质量。
它能够帮助工程师在设计和制造的过程中识别可能导致产品故障的因素,并制定相应的改进措施。
二、FMEA的应用步骤2.1 选择要分析的过程或产品首先确定要进行FMEA分析的具体产品或过程。
这可以是一个正在开发的新产品,也可以是一个现有产品的改进过程。
2.2 组织FMEA团队确定一个专门的团队来进行FMEA分析。
该团队应由各个领域的专家组成,包括设计工程师、制造工程师和质量控制专家。
2.3 确定潜在故障模式分析可能导致产品故障的各个环节,包括设计、制造、运输、安装和使用过程。
对每个环节,确定可能发生的故障模式。
2.4 评估故障模式的严重性对每个故障模式,评估其可能对产品或过程的影响程度,包括安全性、可靠性和成本等方面。
2.5 确定故障模式的原因对每个故障模式,找出可能导致其发生的潜在原因。
这些原因可以是设计缺陷、制造误差、操作错误等。
2.6 评估故障模式的概率对每个故障模式,评估其发生的概率。
这可以通过历史数据、专家访谈等方式进行评估。
2.7 评估故障模式的可探测性对每个故障模式,评估其是否可以通过检测手段及时发现。
如果不能及时发现,应考虑改进措施。
2.8 制定改进措施根据故障模式的严重性、原因、概率和可探测性,制定相应的改进措施。
FMEA我的讲义

FMEA的实施 FMA:Failure Mode Analysis
FMA(失效模式分析) FMEA(潜在失效模式及后果分析)
失效已经产生
失效还未产生,可能发生,但不是一 定要发生
核心:纠正
核心:预防
诊断已知的失效
评估风险和潜在失效模式的影响
开始于产品设计和工艺开发活动之前
指引开发和生产
指引贯穿整个产品周期
• 4、1985年由国际电工委员会(IEC)出版的FMECA 国际标准(IEC812),即参考MIL-STD-1629A加以部分 修改而成。
13
FMEA 之適用範圍
• 1、ISO9004 8.5節FMEA作為設計審核的要項,另 FTA(失效樹分析)風險分析亦是。
• 2、CE標志,以FMEA作為安全分析方法。
E: Effect 後果
Effect談三種: 1.對本身的立即影響
2.對同一水平的影響, 也可能對下一工序的影響 3.對產品使用者的影響
6
FMEA定義
後果的通常表現形式:
人身安全 不舒服的氣味 不穩定 作業中斷 無法繫緊 無法安裝 損壞裝備
手感不良
作業過多
無法操作
操作不良
車控不良
顧客不滿意
滲漏
外觀不良
12
FMEA 之沿革
• 1、FMEA的前身為FMECA,是在1950由格魯曼飛機 提出,用在飛機主控系統的失效分析
• 2、波音與馬丁公司在1957年正式編訂FMECA的作业 程序,列在其工程手冊中
• 3、60年代初期,美太空总署将FMECA成功的应用于 太空计划。美军同时也开始应用FMECA技术,并于 1974年出版MIL-STD-1629 FMECA作业程序。
DFMEA培训讲义

三种FMEA的差异
设计FMEA 用来在产品交付生产前分析产品 分析重点 由设计缺陷引起的潜在产品失效模式 过程FMEA 用来分析制造与装配过程 分析重点 由制造或装配过程缺陷引起的潜在产品失效模式
三种FMEA的差异
系统FMEA 用来早期构思系统阶段,分析系统与子系统 分析重点 由系统缺陷引起的与系统功能相联系的 潜在失效模式分析 一个系统与其他系统间的相互作用 系统单元间的相互作用
克莱斯勒召回46.4万辆“PT漫步者”
PT漫步者是2001年才投入量产的新 车型,甫一上市即大受欢迎,两年间共生产 464315辆,其中已售出42.5万辆, 今年上半年PT漫步者的销量比去年同期增 长5%,已成为克莱斯勒最畅销的车型。 (杨钧)
气囊系统不合格——通用招回72万辆 问题车
【新华网 】北京2002年8月20日专电 据法新社19日报道,美国通用汽车公司当日宣布,已经开始召回72万辆气囊 系统存在问题的汽车。 通用公司在声明中说,这72万辆车中有57万辆在发生事故时气囊可能无法展 开,原因是感应和判断系统存在问题,对气囊的展开信号的顺序产生干扰。另15万 辆车气囊系统的焊接有问题,气囊展开时焊缝可能会断裂,并产生飞散的碎片,并且 气囊也可能无法充分展开。
必须有整体性的规划,并且 循序渐进地逐步改善企业的 研发环境
FMEA的产生
FMEA是一种实用的解决问题的方法,
可适用于许多工程领域(核电厂、水库、卫
星、飞机、十大召回事件… … ),目前世界
许多汽车生产商和电子制造服务商(EMS)都
已经采用这种模式进行设计和生产过程的管
理和监控。
因发动机问题日产公司召回30多万辆汽车
日本尼桑公司将召回百万辆有故障汽车
FMEA讲义课件
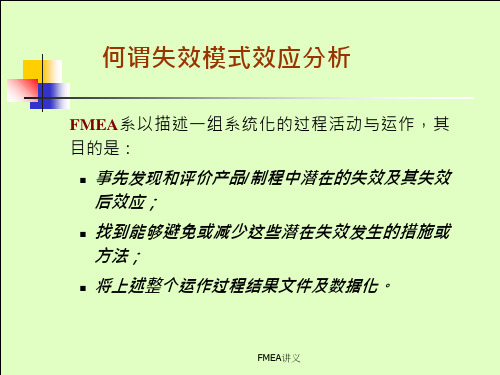
设计FMEA流程图
流 程
说 明
设计工程师应负责确认各项改正行动均经完成或均经通知负责人确实执行。
对RPN之项目应最优先采取必要措施,其目的在降低严重性、发生性及侦测性之分数。若不采有效之改正措施则制程FMEA之成效将受局限。
将风险领先指数做成柏拉图并决定建议之措施
将已采取之改正行动之内容及其完成日期填入记录,重新预估并记录改正后之严重性、发生性及侦测性之结果;计算新的RPN值。如果必要时,采取适当行动以降低RPN值。
9
很高
产品功能不能运作,丧失基本功能
8
高
产品功能能运作,但功能降低,顾客严重不满
7
中等
功能可运作,但舒适性及方便性降低,顾客使用时不满意
6
低
功能能运作,但舒适性及方便性降低,顾客使用时有些不满意
5
很低
如功能性、外观及结构等不合要求,大多数顾客注意到的了缺陷
4
微小
如功能性、外观等不合要求,一般顾客可注意到的缺陷
4
高
设计控制将会侦测出潜在原因/机制和随后的失效模式
3
非常高
设计控制有很高的机会侦测出潜在原因/机制和随后的失效模式
2
几乎肯定
设计控制几乎会侦测出潜在原因/机制和随后的失效模式
1
D-FMEA导入时机与展开
IN PUT
OUT PUT
产品主要功能
.
发生性系指预测该不良模式发生之频
度,不
良之
预防必须加以考虑
.
侦
测性系对该零件或装配件送交生产前,其可
能
存在之设计弱点是否能经设计
验证而查出之能
力
.
设计工程师应负责确认各项改正行动均经完成
FMEA讲义~电子版
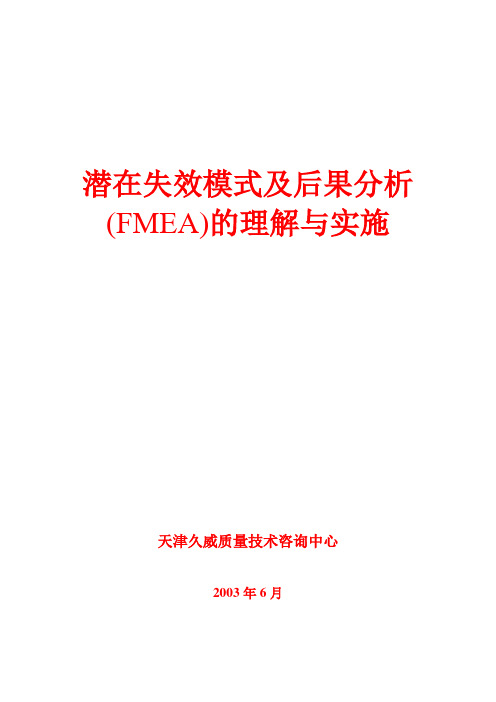
潜在失效模式及后果分析(FMEA)的理解与实施天津久威质量技术咨询中心2003年6月第一部分~~~~~~~~~~~~~~~~基本原理什么是FMEAFMEA是糸统的分析方法FMEA分析的方法第二部分~~~~~~~~~~~设计FMEA(D-FMEA)D-FMEA的基本要求D-FMEA报告的栏目解释D-FMEA的实施第三部分~~~~~~~~~~~过程FMEA(P-FMEA)P-FMEA的基本要求P-FMEA报告的栏目解释P-FMEA的实施潜在失效模式及后果分析(FMEA)的理解与实施~~~基本概念潜在失效模式及后果分析(FMEA)的理解与实施第一部分基本原理一、什么是FMEA●FMEA的定义:在设计阶段/更改设计阶段,对产品/零件/制造过程进行分析,找出潜在失效模式,分析其可能的后果,评估其风险,预先采取措施,减少失效模式的严重程度,降低发生的概率,有效提高可靠性,确保顾客满意的系统化活动。
●实施FMEA的时机:◆开发新产品、实施新技术、开发新过程时应用;◆对现有产品/过程实施更改;◆现有产品/过程应用于新的环境、场所时;●实施FMEA的目的:◆寻找产品及加工过程中的潜在失效及其后果;◆确定消除或减少潜在失效发生的措施;◆将全部分析过程文件化,以供评审;●FMEA是事前行为◆通过FMEA确定的措施为预防措施;◆各类失效模式均为“潜在”,即可能会发生;实施◆潜在失效模式是凭经验和对以往事故的评估获得; ●FMEA 是为各类设计/更改设计做准备的活动◆FMEA 是对“设计策划”环节的补充活动;◆在设计策划过程中,通过FMEA 明确如何使顾客满意; ●FMEA 是集休分析的产物 ●FMEA 的分类◆D-FMEA(设计FMEA):在产品设计过程中使用,分析对像为:总成/分总成/零件;◆P-FMEA(过程FMEA):在工艺设计过程中使用,分析对像为加工工序及各物流过程;二、FMEA 是系统的分析方法三、FMEA分析的基本方法●基本方法:运用失效链,连问为什么。
FMEA讲义(mqe)
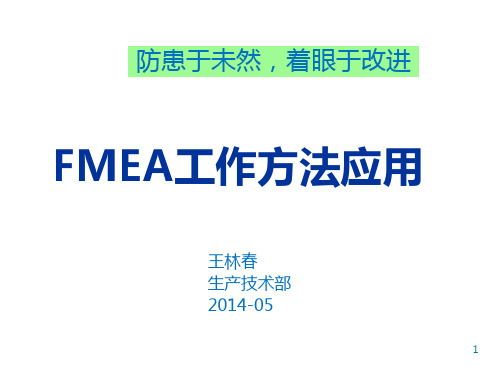
• FMEA从局部失效入手,分析其对上一级系统、
相关部分、下游程序以及总体系统的后果。分析 路径“由下至上”。 • FTA一般由系统的失效模式入手、分析造成该失 效产生的原因。分析路径“由上至下”。
7
第 1 章 概论
新的 更改的 设计 评价 方框图
设计 FMEA
DFMEA
产品 过程 特性 过程流 程图 过程 FMEA
过程
PFMEA
1.2 FMEA种别
• •
8
SFMEA– 系统FMEA; DFMEA– 设计FMEA;PFMEA– 过程FMEA AFMEA—应用FMEA;SFMEA—服务FMEA;PFMEA—采购FMEA
第 1 章 概论
1. 3 FMEA主要用途
设计用 设计分析及改 善 设计品质/可靠 度 制程分析及改 善 提升制程能力 1设计改进; 2保养、维修、稽 核 制度及清单 3 sop sop制程管制 重点 系统及方法
5
第 1 章 概论
1. 1 什么是FMEA?
FMEA 与8D(Failure Mode Analysis) 分析 的区别:
• FMEA是一种事前行为; • 8D是一种事后行为;
• 8D报告是进行FMEA的重要的资料。
公开课-FMEA培训讲义

• 分析方法:从局部入手,分析对总成的影响
4
第四页,共69页。
FMEA实施的十大步骤
按照?GB7826-1987S失效模式和后果分析程序?规定:
1、定义系统及其功能和要求
2、拟定功能和工艺流程图
3、确定分析的根本原那么 4、找出失效模式、原因及后果 5、找出失效的监测、纠正措施
19
第十九页,共69页。
设计 FMEA的标准表
系统 子系统
零部件
车型年/车辆类型
核心小组
(8)
潜在失效模式及后果分析
(2) 设计责任 (5) 关键日期
〔设计FMEA〕
(3年) 年 (6)
FMEA编号:
(1)
共 页,第 页
编日制期人 〔编:制〕(4)〔修订〕
(7)
FMEA
等
项目 潜在
失效
模式
功能要
求
突出对高优先度的失效模式进行工程评定。 要注意符号的一致性:DFMEA、PFMEA和控制方案, 工艺文件,作业指导书,检验文件都要标注。
30
第三十页,共69页。
(14〕失效的潜在起因/机理
• 所谓失效的潜在起因是指设计薄弱局部的迹象,其结果就 是失效模式。
• 尽可能地列出每一失效模式的每一个潜在起因和/或失效 机理。起因/机理应尽可能简明而全面的列出,以便有针 对性地采取补救的努力。
公开课-FMEA培训讲义
1
第一页,共69页。
根本概念
• 失效:产品/过程失去本身功能。
• 失效模式:产品/过程失效时所表现的形式。 • 失效模式分析:对已出现的失效模式进行分析,是一种事后
行为。 • 潜在失效模式分析:对可能要发生的失效模式进行分析,是
FMEA 培训讲义
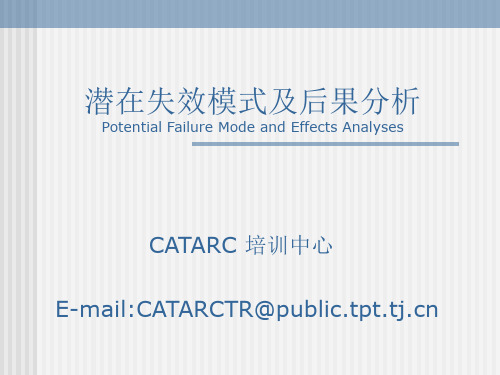
FMEA评估指标
严重度:是对产品或客户最严重的影响后果的严 重程度的评价指标 频度:指具体的失效原因或机理发生的频率 探测度:是指产品在投产前,采用现行设计或现 行过程控制方法中最有效的方法,找出潜在失效 起因/机理的可能性评价指标或后序发生的失效 模式的可能性的评价指标。
探测度
探测性
评价准则:在下一个或后续过程前,或零部件离开制造或装配工位之前,利用过程控 制方法找出缺陷存在的可能性
7、FMEA编制日期:填入编制FMEA原始稿的日期及最新修订日期;
8、核心小组:列出被授权确定和执行任务的责任部门和个人姓名; 9、过程功能/要求:简单描述被分析的过程或工序;及要求
表格填写2
10、潜在失效模式:是指过程可能发生的不满足过程要求和/或设计意图的形 式,是对某具体工序不符合要求的描述; 11、潜在失效后果:指失效模式对顾客的影响;
FMEA特点
失效还未产生,可能发生、但不一定要发生。 时机:在设计或过程开发阶段前开始。 合作:由各方面有经验和专业知识的人构成 FMEA分析的文件 ------记录专用表格 ------作为动态文件使用 ------按照过程/产品/服务寿命周期期间要求更改。 核心:预防 对潜在失效模式的风险和后果进行评定 指导贯穿整个过程、产品和服务周期
表格填写4
18、风险顺序数(RPN):风险顺序数(RPN)是严重度(S),频度(O)和探测度 (D)的乘积。
RPN=(S)×(O)×(D) 这个值可用于对过程中那些担心的事项进行排序。如果风险系数很高,小组必须采 取纠正措施,努力减小该值。在实践中,不管RPN的结果如何,当严重度(S)高时, 就应予特别注意。 19、建议措施:当失效模式按RPN值排出先后次序后,应首先对排列在最前面的问题和 最关键的项目采取纠正措施。 若失效的起因不详,则建议采用的措施应通过统计试验 设计(DOE)来确定。 20、责任(对建议措施):把负责建议措施的组织和个人,以及预计完成的日期填在本 栏中。 21、采取的措施:当实施一项措施后,简要记录具体的措施和生效日期。 22、措施后的RPN:当明确了纠正措施后,估算并记录措施后的频度、严重度和探测度。 计算并记录纠正后的RPN值。
FMEA讲义~电子版

潜在失效模式及后果分析(FMEA)的理解与实施第一部分~~~~~~~~~~~~~~~~基本原理什么是FMEAFMEA是糸统的分析方法FMEA分析的方法第二部分~~~~~~~~~~~设计FMEA(D-FMEA)D-FMEA的基本要求D-FMEA报告的栏目解释D-FMEA的实施第三部分~~~~~~~~~~~过程FMEA(P-FMEA)P-FMEA的基本要求P-FMEA报告的栏目解释P-FMEA的实施潜在失效模式及后果分析(FMEA)的理解与实施~~~基本概念潜在失效模式及后果分析(FMEA)的理解与实施第一部分基本原理一、什么是FMEA●FMEA的定义:在设计阶段/更改设计阶段,对产品/零件/制造过程进行分析,找出潜在失效模式,分析其可能的后果,评估其风险,预先采取措施,减少失效模式的严重程度,降低发生的概率,有效提高可靠性,确保顾客满意的系统化活动。
●实施FMEA的时机:◆开发新产品、实施新技术、开发新过程时应用;◆对现有产品/过程实施更改;◆现有产品/过程应用于新的环境、场所时;●实施FMEA的目的:◆寻找产品及加工过程中的潜在失效及其后果;◆确定消除或减少潜在失效发生的措施;◆将全部分析过程文件化,以供评审;●FMEA是事前行为◆通过FMEA确定的措施为预防措施;◆各类失效模式均为“潜在”,即可能会发生;实施◆潜在失效模式是凭经验和对以往事故的评估获得; ●FMEA 是为各类设计/更改设计做准备的活动◆FMEA 是对“设计策划”环节的补充活动;◆在设计策划过程中,通过FMEA 明确如何使顾客满意; ●FMEA 是集休分析的产物 ●FMEA 的分类◆D-FMEA(设计FMEA):在产品设计过程中使用,分析对像为:总成/分总成/零件;◆P-FMEA(过程FMEA):在工艺设计过程中使用,分析对像为加工工序及各物流过程;二、FMEA 是系统的分析方法三、FMEA分析的基本方法●基本方法:运用失效链,连问为什么。
FMEA讲义
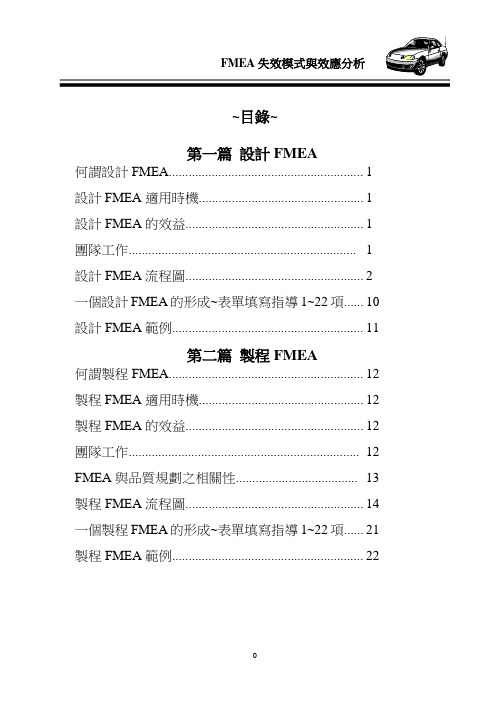
~目錄~第一篇設計FMEA何謂設計FMEA (1)設計FMEA適用時機 (1)設計FMEA的效益 (1)團隊工作 (1)設計FMEA流程圖 (2)一個設計FMEA的形成~表單填寫指導1~22項 (10)設計FMEA範例 (11)第二篇製程FMEA何謂製程FMEA (12)製程FMEA適用時機 (12)製程FMEA的效益 (12)團隊工作 (12)FMEA與品質規劃之相關性 (13)製程FMEA流程圖 (14)一個製程FMEA的形成~表單填寫指導1~22項 (21)製程FMEA範例 (22)何謂設計FMEA?為一系統化的分析技術,用以評估某一可能缺點的發生機率,及其發生後造成的影響。
而且針對高風險(RPN Risk Priority Number)項目,事先評估其製程能力,俾能訂定適當的製程管制。
設計FMEA適用時機在產品品質規劃(APQP)之構想階段(第一階段),先將顧客的期望轉換成可靠度,再從產品設計與開發驗證階段(第二階段)導入DFMEA。
設計FMEA視為一份持續檢討的文件,應在設計概念完成之前或之時就開始實施,隨著變化的出現或在整個生產開發階段額外訊息的隨取而持續改進提升,且在生產圖面公佈前研議應採取之改正措施及設計修改。
設計FMEA的效益⏹有助於對設計要求和設計抉擇的客觀評估。
⏹有助於有關製造和裝配要求的初次設計。
⏹提供額外訊息,有助於全面的、有效的設計測詴及開發方案的規劃。
⏹開發出一套按它們對“顧客”的影響來排列的潛在失效模式,因此為設計改進和開發測詴建立了一個優先系統。
⏹為推薦和跟蹤減少風險行動提供了一種開放式格式。
⏹提供未來參考,以助於分析實地問題,評估設計變更和開發先期設計。
團隊工作(Team effort):在最初的設計之潛在FMEA過程中,責任工程師預計會直接地和積極地讓來自所有受影響領域的代表參與其中。
這些領域應該包括,但不限定於:裝配、製造、材料、品質、服務和供應商,還有負責下次裝配的設計領域。
PFMEA 讲义
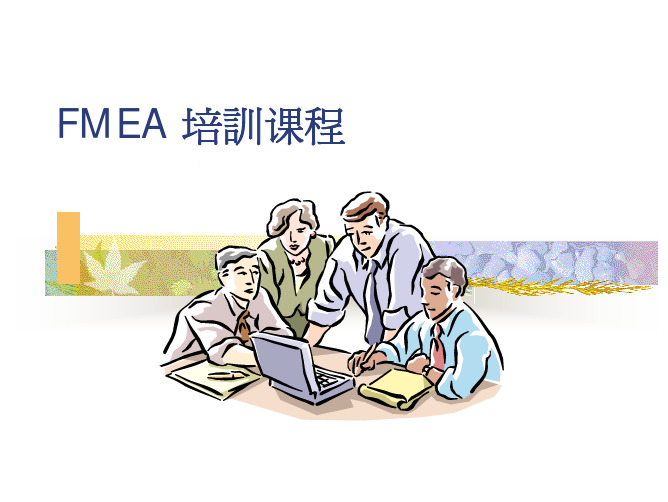
根據零件、分系統、系統的工藝特性,對應特 定的工作道次列出每一個潛在的失效模式
製程工程師或小組要提出和回答下列問題:
製程或零組件為何不符合規格? 不考慮工程規格,什麼是客戶(最終使用者、下工程、或服 務)所不滿意的?
FMEA 表格填寫- 5
項目功 潛在失 潛在失 嚴重度 特殊特 潛在失 發生率 現行預 現行檢 難檢度 關鍵 能需求 效模式 效效應 (S) 性分類 效原因 (O) 防管制 測管制 (D) 指數 RPN
特殊特性分類 : • 特殊過程或客戶要求重點的符號標示 • 嚴重度高的(安全,法規……) • 任何特殊(關鍵)過程管制項目都應於FMEA表 中被標示(CTQ)
1. 及時性是成功實施FMEA的最重要因素之一。 2. 它是“事前的預防"而不是“事後的追悔"。 3. 事先花時間進行FMEA分析,能夠容易且低成本 地對產品設計或製程進行修改,從而減輕事後修 改的危機。 4. FMEA能夠減少或消除因修改而帶來更大損失的 機會,它是一個相互作用的過程,永無止境的改 善活動。
DFMEA 设计(Design)失效模式 及效应分析
FMEA分类
PFMEA 过程(Process)失效模式 及效应分析
1.3 FMEA的實施時機
1. 一般的原則:FMEA之使用要越早越好,如此才能消除或減少設 計錯誤之發生; 2. 當設計新的系統、產品、零件、制程、設備時,在作概念設計 或草圖時即可開始FMEA;(制程規劃初期) 3. 當系統、產品、零件、制程、設備有變更時; 4. 當現有的系統、產品、零件、制程、設備有新的應用時; 5. 當現有系統、產品、零件、制程、設備被考慮要改善時. 6. 定期更新
DFMEA讲义5044

© USI proprtary and confidential
7
FMEA的原理
FMEA 引導有經驗者專注於研究開發一 市場/ 客戶所需要的產品,
及促使能證明當初所選擇的範疇/ 目標(例如一系統、產品或專案)
的技術。
.
FMEA 在研究開發階段可被應用如設計管制及風險 (危害)分析
之工具, FMEA同樣亦能被應用於制訂製程計劃、製程管制、供應商
Detection (檢 出) --* 在 發 生 之 後 驗 明 或 檢 出 失 效. * 強 調 以 鑑 定 的 技 法 或 檢 出 的 方 法 使 能 準 確 的 找 出 發 生 的 失 效. * 專 注 點 為 --- 有 效 的 檢 出 力. * Remember --- 不 良、瑕 疵 事 件 已 經 發 生, 額 外 的 成 本 已 經 發 生; 有 人 須 為 了它 多 付 出.
專 注 於 design 階 段, 透 過 使 用 有 系 統 的 FMEA 引 導, 使 潛 在 的 風 險 被 識 別、排 除 或 減 到 最 少 的 衝 擊 程 度, 以 使 現 在 的 情 況 能 達 到 可 以 接 受 的 一 種 技 能。
從 設 計 工 程 方 面 的 竭 力及 質 與 量 的 資 源 面 , 優 先 進 行 任 何 對 產 品 潛 在 失 效 的 衝 擊 之 分 析, 甚 至 對 產 品 的 最 終 客 戶 端。
15
步驟一
瞭解產品開發目標
➢ 市調情報:相關產品在市場分佈、需求及反應狀況。 ➢ 客戶需求:有關客戶對產品功性能規格及其他有關產品
開發事項之需求。
➢ 相關法規:有關產品在製造、使用及安全等方面之法規
限制。
➢ 環保考量:有關產品開發在設計、材料選用對於環境保
- 1、下载文档前请自行甄别文档内容的完整性,平台不提供额外的编辑、内容补充、找答案等附加服务。
- 2、"仅部分预览"的文档,不可在线预览部分如存在完整性等问题,可反馈申请退款(可完整预览的文档不适用该条件!)。
- 3、如文档侵犯您的权益,请联系客服反馈,我们会尽快为您处理(人工客服工作时间:9:00-18:30)。
因
•
以及它的基本條件
•步驟5----敍述失效效應----關心到客戶可能注意或經驗
•
到的事項.
•步驟6----列出管制方法----預防可能發生的失效模式,
或
•
者,偵測將會發生的失效模式
.
•步驟7----計算風險(風險優先)----將憂慮的事情排成等
級
•
順序.
•步驟8----防錯的設計----想出規劃好的措施,藉以獲得
•爲什麽這項設計,沒有照著 •工程師所期望的那樣來動作呢?
•而制程設計的FMEA,提供了回答另外一 種不同的詢問:
•正當生産制程,照著工程需求, •穩定地製造産品的時候,爲什麽 •卻沒有辦法有效地作業了呢?
•
书山有路勤为径, 学海无涯苦作舟
•F M E A 步 驟 的 全 貌 •FMEA已被定義爲一種系統化的方法,透過各階段步驟 來鑒定和調查潛在設計弱點的原因和效應,以及建立明 確而有系統的矯正措施,藉以降低在功能方面的失敗效 應. •系統化的步驟具有8項基本的要素
•如何?
•需要維持的環境
•風 •雨 •灰塵 •噪音 •温度
•門關起來
•提供封堵
•爲何 •?
•産上 •品的 •功缺 • 能陷
•一項缺陷,只是一椿功能的失敗
书山有路勤为径, 学海无涯苦作舟
•
书山有路勤为径, 学海无涯苦作舟
•在這個階段有沒有什麽可能會出差錯?
•步驟1
•步驟2
•若是“A” •查證
若是B •步驟3
•A公 司
•時間 90%完成於14個月前 開始生産
•
书山有路勤为径, 学海无涯苦作舟
•額外時間矯正措施的成本 •在問題發生之後才來矯正,就像“滅火”那樣 的重要,因爲,我們必需改正我們的錯誤。 不過將矯正措施定位在“發現和修理”的做法 上,它的成本將是非常昂貴的,而且,在經 營事業的作爲上,不利於品質,成本和時效 。 •·顧客階段所面臨到的産品問題,不僅昂貴, • 而且可能不利於未來的行銷。 •·製造和加工所産生的問題,不利於産品的品 • 質,作業的生産力以及産品交期的時效。 •·針對新産品或制程驗證,當問題發生之後, • 才來描述問題,以及採用“發現和修理”的做 • 法,來應付“時間至上”的論點,將會産生以 • 下之結果: •-很多晚期的設計變更。 •-晚期的工具,設備和産品的變更,其花費將 • 更昂貴。 •-晚期的變更,通常在倉卒之間完成,並未適 • 當地評估。
•
书山有路勤为径, 学海无涯苦作舟
•發現和修理跟預防的比較 • • 在前一頁,是一份兩家公司的研究結 果,每家公司在它們的工業領域,都具有領 導地位,在逐行産品驗證作業的評估時,以 圖表的方式,來呈現出産品設計的效果。A 公司,普遍地採用“發現和修理”的做法(在 測試和建立原型式樣方面),透過新款式的 開發和初期的生産規劃,把接連不斷和頻乃 的産品變更,當作正常的作業。相反地,觀 察B公司的績效,它們將努力集中在有效地 企劃預防問題方面,雖然也只採用測試和建 立原型式樣的方式,來確認産品設計的效果 ,在産品開發的作業上,卻達到了截然不同 的績效。 • B公司的管理,要求員工貢獻其績效的 方式是透過一種重要的做法,那就是有效的 開發作業,以及採用失效模式與效應分析, 藉以在設計完成之前鑒別設計上的弱點。
•描述“可能出錯的事情” •潛在的失效模式可以定義爲一種現象:一項 零件裝配或制程,爲要符合設計方面預期的效 果和/或滿足顧客的期望,卻又可能會遭到潛 在的失敗.這項潛在的失敗模式也有可能是處 於高層次裝配作業中,潛在失效模式的原因, 或者是低層次零件裏頭的一項效應. •特別是,有極多的情況可能會造成功能的失 敗.建議的起點是從檢討過去的FMEA開始,舉 凡試驗報告,品質,保證,耐久性和可靠度所關 心的,以及小集團的“腦力激蕩”…..等.
最
•
书山有路勤为径, 学海无涯苦作舟
•功能樹
•門
•能夠進出
•提供出入口 •旋轉門
•開門
•推/拉門
•逃生方向 •安全方向
•當門開著時 •正确的容量
•提供 •安全
•防止傷害
•安全的效力 •當門關著時
•當門正在關 •防止損傷 •的時候
•門閂的可靠性
•提供 •防護
•防止盜竊
•牢固的門閂 •可靠的門閂
•需要排除的環境
•
书山有路勤为径, 学海无涯苦作舟
•額外花費時間用於矯正措施的成本
•成本
•措施
•1000 •客戶抱怨
•100 •製造加工
•10 •設計驗證
•1 •FMEA
•産品企劃期 •設計期 •製造 •使用期
期
•時間
•變更的比程
•預防的做法
•方
•面
•的
•設
•計
•B公
•變
司
•更
•發 •現 •和 •修 •理 •預 防
•步驟1----敍述産品或制程----能夠很清楚地讓人瞭解到
•
製造産品或逐行制程的內涵,從而導向簡單化
•
和持續的進步.
•步驟2----定義功能----我們希望産品或制程能夠做些什
•
麽?
•步驟3----鑒定潛在失效模式----敍述“可能做錯的事情”
•步驟4----敍述原因—分解造成潛在失效模式的根本肇
FMEA补充讲义
书山有路勤为径, 学海无涯苦作舟
2020年4月10日星期五
书山有路勤为径, 学海无涯苦作舟
•爲 何 需 要 F M E A
•“失效”或“問題”是很平常的事,所有組織都有 這方面的經驗,大型公司,在任何期間,大約存在著 10,000個問題。歷年來,企業界所面臨的工作,便 是將解決老問題的比率,等於或大於産生新問題的比 率。 •估計,在公司裏,花在解決問題方面的努力,大約 占了全部經營事業工作量的80%。同時期,花在經營 事業的企劃和問題預防措施上的工作量,卻分別只占 了大約10%-20%假如您很仔細地觀察一下任何組織, 您會發現以下的一些問題: • 問題的發生“很平常”。 • 佔用了人力資源的80%。 • 迫使我們處理“過去”的工作。 • 問題都不曾解決,並且累積起來,連帶地造成 全面 • 品質水準的衰退。 • 有效地解決問題,能夠帶領進步。 • 問題關係到所有的組織。 •在組織和它們的産品方面,更加複雜的情況是,問 題 •的衆多和嚴重性,卻偏偏會在同一個期間發生。
•
书山有路勤为径, 学海无涯苦作舟
•FMEA的形式 •失效模式與效應分析的方式,通常大多用來 評估:産品設計和制程設計 •重要的是要瞭解到産品設計的FMEA和制程 設計的FMEA,在結構上是類似的。同時,其 說明,評估和評監的方式也是完全相同的。 •雖然這兩種FMEA,基本上,它們在結構的 方式上是完全相同的,但是,它們卻具有非 常不同的目的,然而,卻又是相輔相成的。 •産品設計的FMEA,回答了以下的詢問: