六、FMEA讲义
FMEA工程应用培训讲义

FMEA工程应用培训讲义FMEA (Failure Mode and Effects Analysis)是一种常用的风险管理工具,广泛应用于工程设计和制造过程中,旨在提前识别和消除潜在的故障和缺陷。
FMEA可以帮助工程师在设计和制造过程中确定风险,并制定相应的措施来降低潜在故障和缺陷的发生概率。
一、FMEA的基本原理1.1 FMEA的概念FMEA是一种通过系统化的方法,对产品、设计或工作过程中的潜在故障模式进行分析和评估的方法。
通过找出故障模式的潜在原因和效应,可以采取相应的预防措施来减少故障的发生。
1.2 FMEA的目的FMEA的主要目的是通过提前识别和消除潜在的故障和缺陷,提高产品和流程的可靠性和质量。
它能够帮助工程师在设计和制造的过程中识别可能导致产品故障的因素,并制定相应的改进措施。
二、FMEA的应用步骤2.1 选择要分析的过程或产品首先确定要进行FMEA分析的具体产品或过程。
这可以是一个正在开发的新产品,也可以是一个现有产品的改进过程。
2.2 组织FMEA团队确定一个专门的团队来进行FMEA分析。
该团队应由各个领域的专家组成,包括设计工程师、制造工程师和质量控制专家。
2.3 确定潜在故障模式分析可能导致产品故障的各个环节,包括设计、制造、运输、安装和使用过程。
对每个环节,确定可能发生的故障模式。
2.4 评估故障模式的严重性对每个故障模式,评估其可能对产品或过程的影响程度,包括安全性、可靠性和成本等方面。
2.5 确定故障模式的原因对每个故障模式,找出可能导致其发生的潜在原因。
这些原因可以是设计缺陷、制造误差、操作错误等。
2.6 评估故障模式的概率对每个故障模式,评估其发生的概率。
这可以通过历史数据、专家访谈等方式进行评估。
2.7 评估故障模式的可探测性对每个故障模式,评估其是否可以通过检测手段及时发现。
如果不能及时发现,应考虑改进措施。
2.8 制定改进措施根据故障模式的严重性、原因、概率和可探测性,制定相应的改进措施。
FMEA我的讲义

FMEA的实施 FMA:Failure Mode Analysis
FMA(失效模式分析) FMEA(潜在失效模式及后果分析)
失效已经产生
失效还未产生,可能发生,但不是一 定要发生
核心:纠正
核心:预防
诊断已知的失效
评估风险和潜在失效模式的影响
开始于产品设计和工艺开发活动之前
指引开发和生产
指引贯穿整个产品周期
• 4、1985年由国际电工委员会(IEC)出版的FMECA 国际标准(IEC812),即参考MIL-STD-1629A加以部分 修改而成。
13
FMEA 之適用範圍
• 1、ISO9004 8.5節FMEA作為設計審核的要項,另 FTA(失效樹分析)風險分析亦是。
• 2、CE標志,以FMEA作為安全分析方法。
E: Effect 後果
Effect談三種: 1.對本身的立即影響
2.對同一水平的影響, 也可能對下一工序的影響 3.對產品使用者的影響
6
FMEA定義
後果的通常表現形式:
人身安全 不舒服的氣味 不穩定 作業中斷 無法繫緊 無法安裝 損壞裝備
手感不良
作業過多
無法操作
操作不良
車控不良
顧客不滿意
滲漏
外觀不良
12
FMEA 之沿革
• 1、FMEA的前身為FMECA,是在1950由格魯曼飛機 提出,用在飛機主控系統的失效分析
• 2、波音與馬丁公司在1957年正式編訂FMECA的作业 程序,列在其工程手冊中
• 3、60年代初期,美太空总署将FMECA成功的应用于 太空计划。美军同时也开始应用FMECA技术,并于 1974年出版MIL-STD-1629 FMECA作业程序。
DFMEA培训讲义

三种FMEA的差异
设计FMEA 用来在产品交付生产前分析产品 分析重点 由设计缺陷引起的潜在产品失效模式 过程FMEA 用来分析制造与装配过程 分析重点 由制造或装配过程缺陷引起的潜在产品失效模式
三种FMEA的差异
系统FMEA 用来早期构思系统阶段,分析系统与子系统 分析重点 由系统缺陷引起的与系统功能相联系的 潜在失效模式分析 一个系统与其他系统间的相互作用 系统单元间的相互作用
克莱斯勒召回46.4万辆“PT漫步者”
PT漫步者是2001年才投入量产的新 车型,甫一上市即大受欢迎,两年间共生产 464315辆,其中已售出42.5万辆, 今年上半年PT漫步者的销量比去年同期增 长5%,已成为克莱斯勒最畅销的车型。 (杨钧)
气囊系统不合格——通用招回72万辆 问题车
【新华网 】北京2002年8月20日专电 据法新社19日报道,美国通用汽车公司当日宣布,已经开始召回72万辆气囊 系统存在问题的汽车。 通用公司在声明中说,这72万辆车中有57万辆在发生事故时气囊可能无法展 开,原因是感应和判断系统存在问题,对气囊的展开信号的顺序产生干扰。另15万 辆车气囊系统的焊接有问题,气囊展开时焊缝可能会断裂,并产生飞散的碎片,并且 气囊也可能无法充分展开。
必须有整体性的规划,并且 循序渐进地逐步改善企业的 研发环境
FMEA的产生
FMEA是一种实用的解决问题的方法,
可适用于许多工程领域(核电厂、水库、卫
星、飞机、十大召回事件… … ),目前世界
许多汽车生产商和电子制造服务商(EMS)都
已经采用这种模式进行设计和生产过程的管
理和监控。
因发动机问题日产公司召回30多万辆汽车
日本尼桑公司将召回百万辆有故障汽车
FMEA精典讲义PPT课件
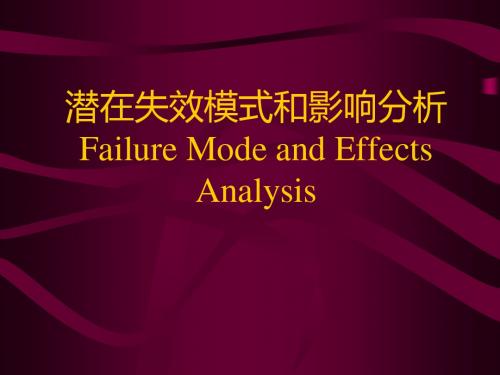
有原因, 确定对这些因素的控制,量化严重度、频度和不易探测度。 进行排序, 建议措施,进而建立改进设计和开发试验的优先控制系统降低
失效的风险。确定潜在的产品特殊特性。
响
因
控制
险
措施
现行 控制
原
现行
风
建议
因
控制
险
措施
现行 控制
18
建立设计FMEA
对工程师进行运用设计FMEA的培训, 理解设计控制概念。 了解对于顾客确定关键和特殊特性方法。 设计FMEA是一个创造性的工作,需要采用跨功能的小组。 应考虑包括每个零部件,审查产品的每个特性和功能。 需要调查研究和发挥创造力。
它用于军事项目合约。 • 1970年晚期,汽车工业将FMEA作为在对其零件设计和生产制造的会审项目的一部分。 • 1980年初,产品事故责任的费用突升和不断的法庭起诉事件发生,使FMEA成为降低事
故的不可或缺的重要工具。并由开始的500多家公司扩展到其供应商。 • 1993年包括美国三大汽车公司和美国质量管理协会在内的,美汽车工业行动集团组织采
确定特殊特性, 确定设计验证计划
第 II 阶段
设计验证计划 和报告
生产工艺流程图
开展过程FMEA
确定风险和可行性
把产品特性与生产过程相联系, 明确特殊特性
揭示变差来源, 最后确定特殊特性
第 II 阶段 第III 阶段 第III 阶段
9
设计FMEA
目的 • 设计的分析技术,分析和说明潜在失效模式及其原因和机理; 有助于对设计要求、设计方案进行分析评价; 有助于对制造、装配要求的初始设计确定; 确保潜在失效模式及其影响(对系统/整车运行)在设计和开发过程中得到
FMEA讲义
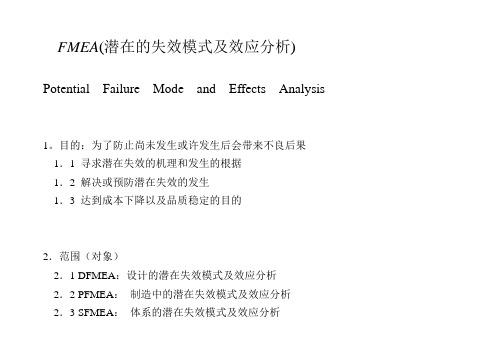
FMEA(潜在的失效模式及效应分析) Potential Failure Mode and Effects Analysis1。
目的:为了防止尚未发生或许发生后会带来不良后果1.1 寻求潜在失效的机理和发生的根据1.2 解决或预防潜在失效的发生1.3 达到成本下降以及品质稳定的目的2.范围(对象)2.1 DFMEA:设计的潜在失效模式及效应分析2.2 PFMEA:制造中的潜在失效模式及效应分析2.3 SFMEA:体系的潜在失效模式及效应分析3.定义3.1 潜在失效后果:是指失效模式对顾客的影响,从这一角度讲,顾客可以是下一道工序,后续工序或工位/代理商/车主。
4.研究方法计算公式SxOxD=RPNS(severity): 严重度O(occurrence):频度D(detection):探测度RPN:风险顺序数5.DFMEA设计中的失效模式与效应分析S--严重度数建议评价准则a)严重度是潜在失效模式对顾客的影响后果的严重程度的评价指标。
b)后果严重度数一般只能通过修改设计来实现。
c)非三大汽车厂的供应商一般从第八级开始计算。
O-- 频度数建议评价准则a)频度是指具Array体的失效起因/机理发生的频率。
b)频度的分级规则可以是采用可能的失效率来估计(参考类似产品),也可以采用统计数据如统计制程控制SPCD-- 不易探测度数的评价准则a)不易探测度:是指用现行的设计控制方式来发现失效的可能性的评价指标。
DFMEA运用流程:(1)对设计过程采用流程分析(2)对每一动作进行潜在失效的分析(针对高风险进行FMEA)(3)对各个设计作业的潜在失效进行S。
O。
D的级数判定,并提出支持理由。
(4)通过S。
O。
D级数值计算RPN值,并依大小进行排序(5)RPN的判定规则a)根据公司实际情况确定当RPN值达到一个限度时进行处理,如: RPN≧30b)将所有的RPN值按柏拉图进行排列,比如排在前10位的要处理(6)针对要处理的RPN项目采取相应的纠正预防措施,达到RPN降低的目的(7)重新排列RPN,执行(5)/(6)。
FMEA讲义
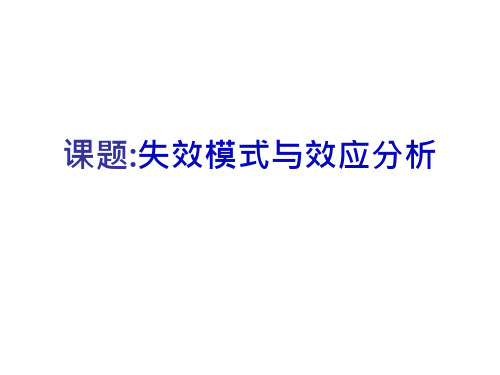
一.FMEA过程顺序
系统有那功能,特征,需要条件? 会有哪些错误?
频次
发生错误会有多惨?
那些错误是什么造成的?
严重度
发生之频率? 有哪些预防和检测? 检测方法能多好程度?
我们能做什么? -设计变更 -过程变更 -特殊控制 -改变标准程序或指南
难检度
一.风险优先数RPN
风险优先数(Risk Priority Number,RPN)
作为建立测试标准,质量管理程序(QCP),制程检验,标准操作 程序(SOP)及标准检验程序(SIP)等检验测试与管制规范的参 考。 7)可作为维护作业规划,维护保养手册编订以及备份料筹备等作 业的输入数据,也可据此制订避免导致失效的操作条件。
一.FMEA的功用
阶段
1.设计时间
2.开发阶段
功用
1.发掘所有可能的失效模式 2.依固有的技术进行设计变更 3.必要之处采用可靠性高的零组件
非常高 车辆/项目无法操作,丧失原来功能
等级 10
一.FMEA的目的
1)辅助设计与制造人员深入探讨产品各层级可能发生的失效模式, 发掘设计或制程上的弱点并改进或防范。
2)发掘可靠度关键件,列入作为设计验证及可靠度管制的重点。 3)研订失效准则,协助失效分析及改正作业,并可作为可靠度分
析的参考数据。 4)提供安全设计及可靠度评估的数据。 5)作为各研发阶段设计审查的输入数据。 6)设计初期即考虑制造组装的需求,并提供健全的失效信息基础,
一. 示例(4/5)
因素 温度太高 热电控制不当 应收帐款编号错误 打字错误 表面污染 高吊车使用时造成的 扔下电话 客户服务人数不足 釉层太薄 溶剂含量太高
一. 示例(5/5)
因素 脱胶 上胶不均匀且份量不足 鞋面破损 材质质量不良 鞋底断裂 鞋底材料配方不当 鞋面污点 模子与手套不洁所造成的 容易滑倒 鞋底材质不良,且设计不当
FMEA(讲义)

11
——零部件 零部件FMEA 零部件
子系统FMEA是子系统 是子系统FMEA的子集.示例 的子集. 子系统 是子系统 的子集 包括:刹车片是刹车总成的零部件之一, 包括:刹车片是刹车总成的零部件之一, 刹车总成又是底盘系统的一个子系统. 刹车总成又是底盘系统的一个子系统. 范围不同,小组的成员也不同. 注:范围不同,小组的成员也不同.
26
ቤተ መጻሕፍቲ ባይዱ
过程流程图和PFMEA的关系 的关系 过程流程图和
过程流程图描述的是整个过程中: 过程流程图描述的是整个过程中:从来料 到出货的流程. 到出货的流程. 包括了制造装配过程中每个步骤, 包括了制造装配过程中每个步骤,输入和 输出的要求. 输出的要求. 初始过程流程图是一种粗略描述的流程图. 初始过程流程图是一种粗略描述的流程图.
16
设计FMEA—步骤和完成时间 步骤和完成时间 设计
在生产设计发布之前, 在生产设计发布之前,完成DFMEA. .
——定义顾客 定义顾客 ——成立小组 成立小组 ——可制造性,可装配性和可服务性的考虑 可制造性, 可制造性
表
17
设计FMEA—功能要求 功能要求 设计
表
用尽可能简明的文字来说明被分析项目满足设计 意图的功能. 意图的功能. ——产品的目的和产品整体的设计目标 产品的目的和产品整体的设计目标 ——安全性 安全性 ——政府法规 政府法规 ——可靠性(功能寿命) 可靠性( 可靠性 功能寿命) ——外观 外观 设计严重度.doc表1 ——可装配性设计和制造性设计等 可装配性设计和制造性设计等
表
7
FMEA方法 成立小组 方法— 方法
FMEA开发主题 开发主题
范围 职能, 职能,要求和期望 潜在失效模式-过程和产品可能导致失效的模式 潜在失效模式 过程和产品可能导致失效的模式 失效影响和结果失效影响和结果-对内部过程或对下游顾客的影响和后果 潜在失效的原因 潜在失效发生的频率 现行预防控制的应用 现行探测控制的应用 要求的推荐措施
FMEA讲义课件
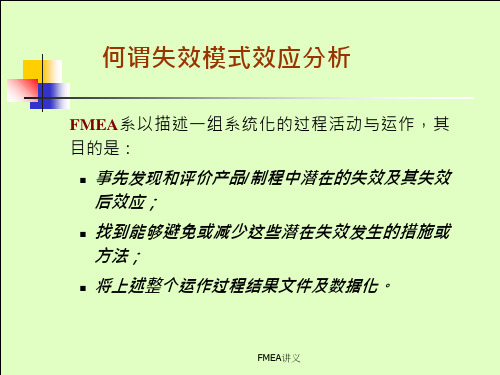
设计FMEA流程图
流 程
说 明
设计工程师应负责确认各项改正行动均经完成或均经通知负责人确实执行。
对RPN之项目应最优先采取必要措施,其目的在降低严重性、发生性及侦测性之分数。若不采有效之改正措施则制程FMEA之成效将受局限。
将风险领先指数做成柏拉图并决定建议之措施
将已采取之改正行动之内容及其完成日期填入记录,重新预估并记录改正后之严重性、发生性及侦测性之结果;计算新的RPN值。如果必要时,采取适当行动以降低RPN值。
9
很高
产品功能不能运作,丧失基本功能
8
高
产品功能能运作,但功能降低,顾客严重不满
7
中等
功能可运作,但舒适性及方便性降低,顾客使用时不满意
6
低
功能能运作,但舒适性及方便性降低,顾客使用时有些不满意
5
很低
如功能性、外观及结构等不合要求,大多数顾客注意到的了缺陷
4
微小
如功能性、外观等不合要求,一般顾客可注意到的缺陷
4
高
设计控制将会侦测出潜在原因/机制和随后的失效模式
3
非常高
设计控制有很高的机会侦测出潜在原因/机制和随后的失效模式
2
几乎肯定
设计控制几乎会侦测出潜在原因/机制和随后的失效模式
1
D-FMEA导入时机与展开
IN PUT
OUT PUT
产品主要功能
.
发生性系指预测该不良模式发生之频
度,不
良之
预防必须加以考虑
.
侦
测性系对该零件或装配件送交生产前,其可
能
存在之设计弱点是否能经设计
验证而查出之能
力
.
设计工程师应负责确认各项改正行动均经完成
FMEA讲义

续保持最新版),应该总是反映最新设计水准,及最新
的相关措施,包括生产后发生的设计更改和措施。
王昌兴
3、测量不精确; 4、热处理不当——时间、温度有误; 5、不充分的通风; 6、不足/无润滑; 7、零件漏装或错装。
王昌兴
明确描述起因/机理
应明确记录具体的错误或误操作情况(例如:操作者 未装密封圈),而不应用一些含糊不清的词语(如,操 作者错误、机器工作不正常)。
王昌兴
发生性
发生性是指具体的失效起因/机理发生的频率。 用来估计发生性的可能。就这种等级而言,只有导致 失效模式的发生性应该加以考虑。
王昌兴
探测度
是对现行控制方法下将检测出一个潜在失效起因/机 理的可能性的评价指标,或找出后续工序发生的失效模 式的可能性的评价指标。
王昌兴
风险优先序数(RPN)
RPN=(S)X(O)X(D)
如果风险优先序数很高,小组必须采取纠正措施,努 力减少该值。在一般实践中,不管RPN的结果如何,当
严重度(S)高时,就应予特别注意。
适当地加以应用,FMEA是一贯相互作用的过程,永无止
境。
王昌兴
种类、定义:
DFMEA:Design FMEA(设计 FMEA)
PFMEA:Process FMEA(过程FMEA) SFMEA: System FMEA(系统FMEA)
过程FMEA中“顾客”的定义,一般指“最终使用者”, 但也 可以是后续的或下游制造或装配工序,以及服务工作。
不起作用 工作不正常 外观不良
费力 异味 工作减弱
间歇性工作 车辆控制减弱 牵引阻力
王昌兴
如果顾客是下一个工程或后续的场所,失效的后果应
用过程/工序性能来描述。如: 不能扣紧 不衔接 不能转向 不符合 不能上升 损坏设备 不能钻孔 不匹配 伤害操作员
FMEA讲义(mqe)
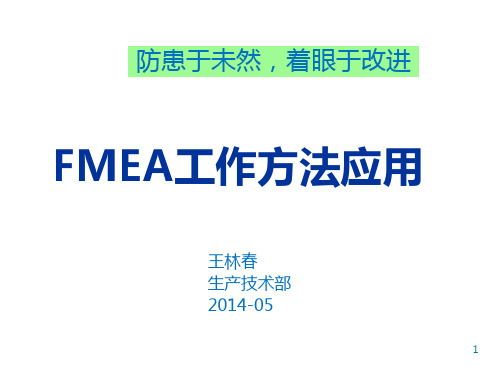
• FMEA从局部失效入手,分析其对上一级系统、
相关部分、下游程序以及总体系统的后果。分析 路径“由下至上”。 • FTA一般由系统的失效模式入手、分析造成该失 效产生的原因。分析路径“由上至下”。
7
第 1 章 概论
新的 更改的 设计 评价 方框图
设计 FMEA
DFMEA
产品 过程 特性 过程流 程图 过程 FMEA
过程
PFMEA
1.2 FMEA种别
• •
8
SFMEA– 系统FMEA; DFMEA– 设计FMEA;PFMEA– 过程FMEA AFMEA—应用FMEA;SFMEA—服务FMEA;PFMEA—采购FMEA
第 1 章 概论
1. 3 FMEA主要用途
设计用 设计分析及改 善 设计品质/可靠 度 制程分析及改 善 提升制程能力 1设计改进; 2保养、维修、稽 核 制度及清单 3 sop sop制程管制 重点 系统及方法
5
第 1 章 概论
1. 1 什么是FMEA?
FMEA 与8D(Failure Mode Analysis) 分析 的区别:
• FMEA是一种事前行为; • 8D是一种事后行为;
• 8D报告是进行FMEA的重要的资料。
六、FMEA讲义

•• 单 严重击度此(s处)(d编):辑严母重度版是文与本给样定式的失效模式最严重 • 第 后相果关二相排级符 序的 。值。严重度是在单独FMEA范围内的
•• F单M击EA此编处号编(A辑):填母入版一文个本用样于式识别PFMEA文件 • 的第数二字级列. •• 项部第目件三的(B级名):填字入. 所需分析过程的系统\子系统或零 •• 过第程四职级责(C): 输入负有过程设计职责的OEM, • 组第织五和级部门或团体,必要时,输入供方组织的名 称. • 型号年/项目(D):填入将使用或将分析过程影响 的型号年度和项目(如果知道的话)
• 单 建击议此措处施(编S)辑(k母):版一文般本来样讲式,预防措施(也就是 • 第 降 是二低防级发错生过率程)设比计探的测使措用施比更随可机取的.这质样量的检例验子 • 第 或三相级关检验更好。
• 第 任四何级建议措施的意图是降低以下指标的排 • 第 序五等级级:严重度\发生率和探测率。以下是对
• 第 对等三级级9或10的不建议修改标准,等级为1的失效模
•
•
第 式分不类四(应级e)再:这进栏一可步用分于析强。调高优先权失效模式或可能
• 第 要求五额级外工程评估的要因,(为标识特殊特性)。
• FMEA中严重度等级识别为9或10的特殊特性,由 于这可能影响工程文件,应该通知负有设计责任的 工程师。
• 第 措四施级结果(m-n): 这个部分识别任何完成措施 • 第 的五结级果和它们对S\O\D级别和RPN的影响。 • 措施采取和完成日期(m):在措施得到执行以
后,填入对采取措施的简要描述和实际完成 日期。
FMEA讲义

等现象。
金品质
潜在失效模式: *系统、子系统或零部件有可能未达到设计意 图的形式。
*过程可能发生的不满足过程要求和/或设计意图的形式
是对某具体工序不符合要求的描述。
潜在失效后果:是指失效模式对顾客的影响。
分类:
本参考手册介绍了两种类型的FMEA,采用QS-9000或其等
金品质
PFMEA过程失效模式及后果分析
PFMEA——填表头 包括FMEA编号,系统、子系统或零 部件名称及编号,设计负责人,编制人,
金品质
年型,关键日期,FMEA日期,核心小组
名单。
—所谓关键日期是指初次完成PFMEA的日
期,该日期不应超过计划的投入生产日期。
PFMEA过程失效模式及后果分析
过程功能/要求:
PFMEA过程失效模式及后果分析
PFMEA——探测度(D) 探测度是与过程控制栏中所列的最佳探测控制相 关联的定级数。 假定失效模式已经发生,然后评价所有的现行控 制的能力,以防止具有此种失效模式或缺陷的零件 金品质 被发运出去。 ——随机质量抽查不太可能探测出一个孤立的缺陷 的存在并且不应该影响探测度数值的大小 ——以统计原理为基础的抽样检测是一个有效的探 测控制施
DFMEA设计失效模式及后果分析
金品质
潜在失效模式及后果分析(表格)12页;
PFMEA过程失效模式及后果分析
确定过程功能和要求
确定与产品和过程相关的潜在的失效模式
评价潜在失效对顾客产生的影响 确定潜在制造或装配过程起因并确定要采取控制来降 金品质 低失效产生频度或失效条件探测度的过程变量 确定过程变量以此聚焦于过程控制 编制一个潜在失效模式的分级表,以便建立一个考虑 预防/纠正措施的优选体系 记录制造或装配过程的结果
FMEA讲义~电子版

潜在失效模式及后果分析(FMEA)的理解与实施第一部分~~~~~~~~~~~~~~~~基本原理什么是FMEAFMEA是糸统的分析方法FMEA分析的方法第二部分~~~~~~~~~~~设计FMEA(D-FMEA)D-FMEA的基本要求D-FMEA报告的栏目解释D-FMEA的实施第三部分~~~~~~~~~~~过程FMEA(P-FMEA)P-FMEA的基本要求P-FMEA报告的栏目解释P-FMEA的实施潜在失效模式及后果分析(FMEA)的理解与实施~~~基本概念潜在失效模式及后果分析(FMEA)的理解与实施第一部分基本原理一、什么是FMEA●FMEA的定义:在设计阶段/更改设计阶段,对产品/零件/制造过程进行分析,找出潜在失效模式,分析其可能的后果,评估其风险,预先采取措施,减少失效模式的严重程度,降低发生的概率,有效提高可靠性,确保顾客满意的系统化活动。
●实施FMEA的时机:◆开发新产品、实施新技术、开发新过程时应用;◆对现有产品/过程实施更改;◆现有产品/过程应用于新的环境、场所时;●实施FMEA的目的:◆寻找产品及加工过程中的潜在失效及其后果;◆确定消除或减少潜在失效发生的措施;◆将全部分析过程文件化,以供评审;●FMEA是事前行为◆通过FMEA确定的措施为预防措施;◆各类失效模式均为“潜在”,即可能会发生;实施◆潜在失效模式是凭经验和对以往事故的评估获得; ●FMEA 是为各类设计/更改设计做准备的活动◆FMEA 是对“设计策划”环节的补充活动;◆在设计策划过程中,通过FMEA 明确如何使顾客满意; ●FMEA 是集休分析的产物 ●FMEA 的分类◆D-FMEA(设计FMEA):在产品设计过程中使用,分析对像为:总成/分总成/零件;◆P-FMEA(过程FMEA):在工艺设计过程中使用,分析对像为加工工序及各物流过程;二、FMEA 是系统的分析方法三、FMEA分析的基本方法●基本方法:运用失效链,连问为什么。
FMEA讲义
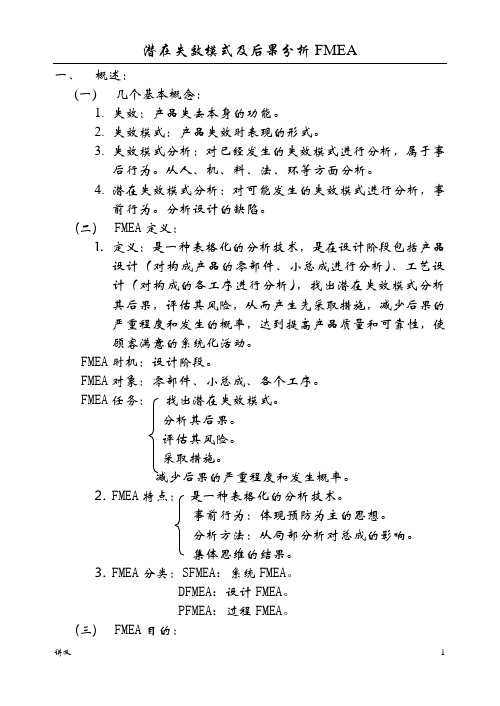
一、概述:(一)几个基本概念:1.失效:产品失去本身的功能。
2.失效模式:产品失效时表现的形式。
3.失效模式分析:对已经发生的失效模式进行分析,属于事后行为。
从人、机、料、法、环等方面分析。
4.潜在失效模式分析:对可能发生的失效模式进行分析,事前行为。
分析设计的缺陷。
(二)FMEA定义:1.定义:是一种表格化的分析技术,是在设计阶段包括产品设计(对构成产品的零部件、小总成进行分析)、工艺设计(对构成的各工序进行分析),找出潜在失效模式分析其后果,评估其风险,从而产生先采取措施,减少后果的严重程度和发生的概率,达到提高产品质量和可靠性,使顾客满意的系统化活动。
FMEA时机:设计阶段。
FMEA对象:零部件、小总成、各个工序。
FMEA任务:找出潜在失效模式。
分析其后果。
评估其风险。
采取措施。
减少后果的严重程度和发生概率。
2.FMEA特点:是一种表格化的分析技术。
事前行为:体现预防为主的思想。
分析方法:从局部分析对总成的影响。
集体思维的结果。
3.FMEA分类:SFMEA:系统FMEA。
DFMEA:设计FMEA。
PFMEA:过程FMEA。
(三)FMEA目的:1.减少或避免将来产品使用时出现失效模式,造成很大浪费。
2.有助于对制造和装配的初始设计:同步技术。
3.为制定一个全面有效地试验大纲和控制计划提供了可靠的依据。
FMEA——控制计划——编制工艺文件、检验文件、作业指导书4.识别特殊特性的重要工具。
(四)什么时候进行DFMEA?1.在设计概念形成之前,设计方案初步确定时,产品的功能确定后,开始进行DFMEA。
2.在设计的各重要阶段,只要设计更改,就要修订DFMEA。
3.在设计施工图全部完成前,结束DFMEA。
4.DFMEA是一个动态的文件,它总是在追求一个最新、最佳的方案,更新产品时就要更新DFMEA。
5.所有的新产品更改的产品,老产品用于新环境时,都有要进行DFMEA。
(五)什么时候进行PFMEA?1.生产工装准备前、工艺设计可行性分析阶段或之前,要开始进行PFMEA。
公开课-FMEA培训讲义
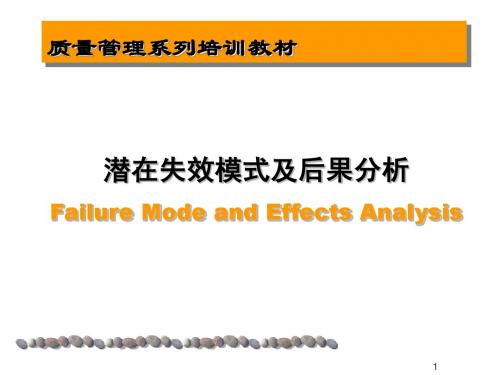
22
7)FMEA日期 填入编制FMEA原始稿的日期及最新修订的日期 (如下图)。
原始稿日期 第一版 第二版 第三版 最新修订日期 8)核心小组
列出有权确定和/或执行任务的责任部门的名称和个人的姓 名(建议所有参加人员的姓名、部门、电话、地址等都 应记录在一张分发表上。)
23
(9)项目/功能
填入被分析项目的名称和编号。
5
FMEA分类
DFMEA——设计FMEA
PFMEA——过程FMEA SFMEA——系统FMEA
6
什么时候进行DFMEA
新产品设计时,设计方案初步确定,产品功能确定后 开始进行。 在产品设计的各阶段,当设计有变化时,修订 DFMEA。 设计图纸完成前,全部结束。
7
什么时候进行PFMEA
过程可行性分析阶段或之前进行PFMEA。
3
为什么进行FMEA
可以早期识别问题,以便确定最佳设计方案。 可以识别特殊特性。 为制定设计试验大纲和控制计划提供可靠的依据。 FMEA输出给控制计划→编织工艺、检验文件 是一种事前行为,体现预防为主的思想 分析方法:从局部入手,分析对总成的影响
4
FMEA实施的十大步骤
按照《GB7826-1987S失效模式和后果分析程序》规定: 1、定义系统及其功能和要求 2、拟定功能和工艺流程图 3、确定分析的基本原则 4、找出失效模式、原因及后果 5、找出失效的监测、纠正措施 6、找出设计和工作中的预防措施 7、确定事件的危害度 8、估计失效概率 9、相关失效分析 10、建议措施
• 应力过大
• 维护说明书不充分
• 算法不正确
31
(14)失效的潜在起因/机理
•规定的磨擦材料不当 维护说明书不当 • 过热 • 软件规范不当 • 规定的公差不当 • 表面精加工规范不当 • 行程规范不足 典型的失效机理包括但不限于: 屈服 化学氧化 疲劳 电移 材料不稳定性 蠕变 磨损 腐蚀
- 1、下载文档前请自行甄别文档内容的完整性,平台不提供额外的编辑、内容补充、找答案等附加服务。
- 2、"仅部分预览"的文档,不可在线预览部分如存在完整性等问题,可反馈申请退款(可完整预览的文档不适用该条件!)。
- 3、如文档侵犯您的权益,请联系客服反馈,我们会尽快为您处理(人工客服工作时间:9:00-18:30)。
• FMEA帮助我们了解
• 哪里可能出错? • 造成的影响是什么? • 影响多严重? • 造成的原因是什么? • 发生概率多高? • 管制的方式是什么? • 管制多有效? • 整体风险多高? • 如何降低风险?
• 使用FEMA的好处
• 提高产品的质量、产品的可靠性和安全性。 • 帮助增加客户满意度。 • 减少产品开发时间和成本。 • 减少返工、维修和报废的数量。 • 记录并跟踪为减少风险而采取的行动。 • 优先考虑各缺点,关注改进努力。
二、FMEA与APQP (先期产品品质 规划)之关系
三、FMEA-Excel 表格
四、PFMEA的表头(A-H区域)
• FMEA编号(A):填入一个用于识别PFMEA文件 的数字列.
• 项目(B):填入所需分析过程的系统\子系统或零 部件的名字.
• 过程职责(C): 输入负有过程设计职责的OEM, 组织和部门或团体,必要时,输入供方组织的名 称.
用来改进质量的 非统计工具
Defects
哪个项目?
故障
该工具可以用于任何地方, 任何“系统”或“过程”!设计、制造、装 配、书面工作和管理等等。
一种系统方法, 用来: • 识别、分析、排序和记录潜在失效模式 • 确定失效模式对系统、产品和过程的影响 • 确定故障的可能原因 • 确定可以减少风险的行动
• FMEA维护的另一个要素包括周期性的评审 。特定的焦点应该放在发生率和探测率的排 序上。
• 不是一种”单独存在”的文件,和过程流程图\过 程控制计划,SOP,SIP等相关。
• 要求(a2): 列出所分析的过程步骤/操作的每一个过 程功能的要求,要求是符合设计意图或其他顾客要 求的规定过程的输入。
• 潜在失效模式(b):潜在失效模式按照过程不能符合 过程要求(含设计意图)来定义.即可能出现的不良 现象或项目。
• 失效的潜在后果(c): 失效的潜在后果按顾客察觉 的失效模式的后果来定义,失效后果应该按照顾客 可能注意到或经历的情况来描述,应记住顾客可以 是内部顾客,也可以是最终使用者;或是可能影响安 全或导致不符合法规的。
月球登陆 • 美国人从此在太空科技上远远的超越苏联 • 美国人是如何办到的…
• FMEA历史 • 1950 Grumman飞机公司 • 1960 NASA应用于Apollo太空计划 • 1970 美国军方Mil-Std-1692 • 1980 美国三大汽车厂 • 1993年2月 QS 9000强制要求, FMEA第一版公布 • 1995年2月 FMEA第二版公布 • 2001年7月 FMEA第三版公布 • 2008年7月 FMEA第四版公布
• 严重度\发生率\控测率和RPN (n): 在预防/ 纠正措施得到执行以后,确定和记录所导致 的严重度\发生率和探测率级别。
• 计算和记录措施导致的风险优先系数 (RPN),所有修改后的排序应予以评审。
六、FMEA的维护
• FMEA是动态性的文件,必要时,在产品或过 程设计更改和更新时进行评审。
严重度评价表
• 失效模式的潜在要因(f):失效的潜在要因按照失效 怎么发生的迹象来定义,按照可纠正或可控制的情 形来描述.失效的潜在要因是设计或过程弱点的显 示,后果就是失效模式。失效模式可能是由一种或 一种以上的要因导致的。
• 发生率(O)(g): 发生率是失效特定要因发生的可能 性,发生可能性的排序值相对绝对值而言更有意义, 在1至10等级范围内评估失效潜在要因的发生可 能性。
• 探测率(D) (i): 探测度是与探测控制栏列出 的最佳探测控制相符的级别.探测率是单独 FMEA范围内的相对排序,为了获得一个较 低的级别,一般来讲须改善计划的探测控制.
• 风险优先系数(RPN) (j): 帮助措施最优排序 的一种方法是使用风险优化系数。
• RPN=严重度(S) X 发生率(O) X 探测率 (D)
• 型号年/项目(D):填入将使用或将分析过程影响 的型号年度和项目(如果知道的话)
• 关键日期(E):填入FMEA的初始日期,但不能超过 预期的生产日期的开始时间,如果是供方组织,日期 不能超过顾客要求的PPAP提交日期.
• FMEA日期(原始的)(F):填入FEMA完成的原始日 期和最新修改日期.
• 核心小组(G):填写负有FMEA开发职责的小组成员 ,联系信息.
• 编制(H):填入负责编制FEMA的工程师/小组领导 的组织的名字和联系信息.
五、FMEA表的内容(a-n区域)
• 过程步骤/过程功能(a1): • 过程步骤:填入识别的所需分析的过程步骤
或操作, 该过程步骤应与过程流程图保持 一致,以确保与其他文件(CP,SOP)的可追溯 性和职系,返修和返工操作也可以包含在内 。 • 过程功能:列出与所分析的每一个过程步骤 或操作相对应的过程功能,过程功能描述操 作的目的或意思。
要因发生率表
• 现有过程控制(h):现有过程控制是可能范围 内可以是预防要因发生或探测失效模式或 应该会发生的要因的控制描述。
• 有2种过程控制可以考虑:
• 预防:消除失效的要因的发生或失效模式的 发生,或降低发生率。
• 探测:识别(探测)失效的要因的发生或失效模 式,以导致相关纠正措施或防范措施的开发 。
• 严重度(s)(d): 严重度是与给定的失效模式最严重 后果相符的值。严重度是在单独FMEA范围内的 相关排序。
• 对等级9或10的不建议修改标准,等级为1的失效模 式不应再进一步分析。
• 分类(e):这栏可用于强调高优先权失效模式或可能 要求额外工程评估的要因,(为标识特殊特性)。
• FMEA中严重度等级识别为9或10的特殊特性,由 于这可能影响工程文件,应该通知负有设计责任的 工程师。
六、FMEA讲义
2020年5月22日星期五
目录
一、什么是 FMEA 工具 二、FMEA与APQP (先期产品品质规划)之关系 三、FMEA-Excel 表格 四、PFMEA的表头(A-H区域) 五、FMEA表的内容(a-n区域) 六、FMEA的维护
一、什么是 FMEA 工具
• 试回想… • 1969年7月20日阿波罗十一号登陆船安全在
• 对于确定是否需要措措,不建议使用RPN极 限法。
探测度评价表
• 建议措施(S) (k): 一般来讲,预防措施(也就是 降低发生率)比探测措施更可取.这样的例子 是防错过程设计的使用比随机的质量检验 或相关检验更好。
• 任何建议措施的意图是降低以下指标的排 序等级:严重度\发生率和探测率。以下是对 降低这些指标方法的解释:
• 降低严重度等级:只有设计或过程修改可降 低严重等级。
• 降低发生率(O)等级:为了降低发生率,过程 和设计修改可能是需要的,发生率级别的降 低可能被通过产品或过程设计的修改消除 和控制一种或一种以上失效模式的要因影 响。
• 降低探测(D)级别:更推荐使用防错方法,探测 方法的重新设计可导致探测率级别的降低 。
• 职责&目标完名字包括目标完成 日期,过程负责工程师/小组领导有责任确保 所有建议措施得到实施或充分阐述。
• 措施结果(m-n): 这个部分识别任何完成措施 的结果和它们对S\O\D级别和RPN的影响。
• 措施采取和完成日期(m):在措施得到执行以 后,填入对采取措施的简要描述和实际完成 日期。