0Cr19Ni9不锈钢管道裂纹产生原因分析及焊接处理
奥氏体不锈钢管道焊缝裂纹产生原因分析[1]
![奥氏体不锈钢管道焊缝裂纹产生原因分析[1]](https://img.taocdn.com/s3/m/14719fd73186bceb19e8bbb0.png)
$
母材化学成分 & 质量分数 #
+ -< H#+F&/&$ !$1$!$ !$1I0 H#+FA&/&# !$1$!0 !&1$$
表! 材料 母材力学性能 室温
材料
,= D +E F< ,G ’ !#1$$ !$1$%$ !$1$!$ &I1$$8#$1$$ .1$$8$$ !#1$$ !$1$%$ !$1$!$ &I1$$8&/1$$ &&10$8
$ #1#08#1I0
惠维山
& 核工业 %I& 厂 ! 甘肃 兰州 I!$$"0 #
摘要 ) 国内某电站在建造过程中 ! 部分奥氏体不锈钢厚壁管在焊接后进行 D5 检验时发现焊缝存在大量裂纹 $ 经分析研究 ! 认为裂纹的 产生原因与焊缝熔敷金属中 % 铁素体含量偏低 % D ! -< 含量偏高 % 焊接应力大等因素有关 $ 为 此 对 焊 缝 产 生 裂 纹 的 原 因 进 行 了 分 析 ! 为 不锈钢厚壁管的焊接积累了经验 $ 关键词 ) 奥氏体不锈钢 * 厚壁管 * 焊缝裂纹 * 原因分析 中图分类号 ) 57%0I9" 文献标识码 ) N
焊条采用锦州锦泰焊条厂生产的不锈钢焊条! 型号为
’!&"()&" " 相 当 于 *++,-#./0#! 规 格 !!1# 22 $ 该 批 焊 条 总
计 & $$$ 34 ! 其化学成分及力学性能复验值见表 ! 及表 % 所示 $
表" 焊条化学成分及复验值 " 质量分数 ( "% (
不锈钢焊接热裂的原因及解决方法

一、304不锈钢是奥氏体不锈钢,相当于1Cr19Ni9.SUS304不锈钢是0Gr18Ni9的材质,产生热裂纹的可能性比较大,奥氏体不锈钢有一个特点:他在900多度以上时是奥氏体,900多度以下至600多度时是马氏体,温度继续下降,就又转变为奥氏体。
焊接时接口开裂就是在马氏体阶段开裂的。
解决的方法:减小一下焊接时的热输入量,加大焊后水冷却的工艺,使其在马氏体阶段的时间缩短,避免焊件在敏感的温度区间停留,接口就不会裂了。
二、不锈钢的焊接1、奥氏体不锈钢的焊接不锈钢是不锈钢和耐酸钢的总称,钢中所加合金元素在10%(质量分数)以上,属于高合金钢。
它包括奥氏体型、马氏体型、铁素体型、奥氏体-马氏体型和沉淀硬化型五类。
焊接奥氏体不锈钢(0Cr18Ni9、00Cr18Ni9、0Cr18Ni12Mo2、0 0Cr18Ni12Mo2、0Cr18Ni9Ti、1Cr18Ni9Ti、1Cr18Ni12Mo3Ti 等)主要问题是热裂纹――焊接过程中,焊缝和热影响区金属冷却到固相线附近的高温区所产生的焊接热裂纹、脆化、晶间腐蚀――沿金属晶粒边界发生的腐蚀破坏现象。
和应力腐蚀开裂――金属材料(包括焊接接头)在一定温度下受腐蚀介质和拉应力的共同作用而产生的裂纹。
此外,因导热性差,线膨胀系数大,焊接变形也大。
1)热裂纹与结构钢相比,它的热裂纹倾向较大,在焊缝及热影响区均可能出现热裂纹。
最常见的是焊缝结晶裂纹--在焊缝凝固过程的后期所形成的焊接裂纹,时在热影响区和多层焊层间还会出现液化裂纹。
含镍量越高,产生热烈倾向越大,而且越不容易控制。
;防止措施:a.严格限制硫、磷等杂质的含量。
b.调整焊缝金属组织,以奥氏体为主的γ+δ双相组织具有良好抗裂性。
c.调整焊缝金属合金成分,在单相稳定奥氏钢中适当增加锰、碳、氮的含量。
d.采用小线能量及小截面焊道2)接头脆化奥氏体钢焊接接头的低温脆化和高温脆化是值得注意的问题防止措施:a.严格控制焊缝中铁素体含量(体积分数)2~7%,因为475℃脆化和δ相脆化易出现在铁素体中。
不锈钢无缝管焊接裂纹的原因

不锈钢无缝管焊接裂纹的原因不锈钢无缝管焊接裂纹的原因可能包括以下几点:1.热裂纹:热裂纹是焊接冷却过程中高温阶段产生的裂纹,主要存在于焊接金属中,少量存在于近缝部。
分为结晶(凝固)裂纹、液化裂纹和多边化裂纹。
其中晶体裂纹是常见的裂纹,主要发生在杂质元素多的碳钢焊接中。
2.再热裂纹:厚板焊接结构消除应力处理过程中,在热影响区的粗晶区存在不同程度的应力集中时,由于应力松弛所产生附加变形大于该部位的蠕变塑性,则产生再热裂纹。
产生温度通常在为550℃~650℃。
3.冷裂纹:焊接接头冷却到较低温度下(对于钢来说在M。
温度以下)产生的裂纹称为冷裂纹。
冷裂纹可在焊后立即出现,也有可能经过一段时间(几小时、几天甚至更长时间)才出现,这种裂纹又称延迟裂纹,它是冷裂纹中比较普遍的一种形态,具有更大的危险性。
4.应力腐蚀裂缝:某些焊接结构(如容器和管道等),在腐蚀介质和应力的共同作用下产生的延迟开裂;在任何温度下可发生;裂纹发生的位置通常位于焊缝和热影响区;裂纹形态为沿晶或穿晶。
5.层状撕裂:主要是由于钢板中存在分层的夹杂物(沿轧制方向),在焊接时产生垂直于轧制方向的应力,致使在热影响区或稍远的地方,产生“台阶”式层状开裂;产生温度通常在约400℃以下;裂纹发生的位置通常位于热影响区附近;裂纹形态为穿晶或沿晶。
6.工艺不良:不锈钢焊接过程中,如果焊接参数设置不当、热输入过大或者焊接速度过快,都可能导致焊接区域内应力过高,从而导致裂纹的产生。
7.材质问题:不锈钢本身性质不佳,如果存在夹杂物、气孔等缺陷,那么焊接时这些缺陷就会聚集在一起,形成较大的缺陷区域,从而导致裂纹的产生。
8.环境因素影响:不锈钢焊接时,环境的氧气、水分等物质会对焊接区域的化学成分产生影响。
如果焊接区域处于高温高压环境下,比如制备压力容器时,热应力增大,易导致裂纹的产生。
为了防止不锈钢无缝管焊接出现裂纹,应严格按照操作规程进行焊接,选用合格的焊材,避免在环境恶劣的条件下进行焊接。
不锈钢开裂补焊方法
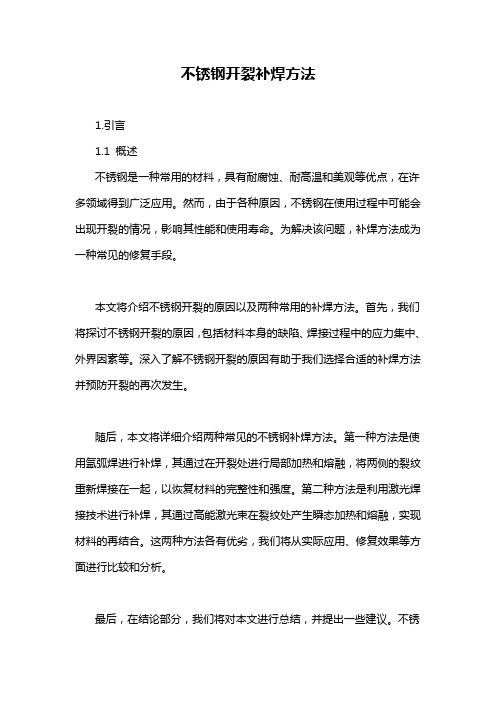
不锈钢开裂补焊方法1.引言1.1 概述不锈钢是一种常用的材料,具有耐腐蚀、耐高温和美观等优点,在许多领域得到广泛应用。
然而,由于各种原因,不锈钢在使用过程中可能会出现开裂的情况,影响其性能和使用寿命。
为解决该问题,补焊方法成为一种常见的修复手段。
本文将介绍不锈钢开裂的原因以及两种常用的补焊方法。
首先,我们将探讨不锈钢开裂的原因,包括材料本身的缺陷、焊接过程中的应力集中、外界因素等。
深入了解不锈钢开裂的原因有助于我们选择合适的补焊方法并预防开裂的再次发生。
随后,本文将详细介绍两种常见的不锈钢补焊方法。
第一种方法是使用氩弧焊进行补焊,其通过在开裂处进行局部加热和熔融,将两侧的裂纹重新焊接在一起,以恢复材料的完整性和强度。
第二种方法是利用激光焊接技术进行补焊,其通过高能激光束在裂纹处产生瞬态加热和熔融,实现材料的再结合。
这两种方法各有优劣,我们将从实际应用、修复效果等方面进行比较和分析。
最后,在结论部分,我们将对本文进行总结,并提出一些建议。
不锈钢开裂问题对许多行业都具有一定的影响,因此,我们需要加强对材料质量的控制和焊接工艺的改进,以减少不锈钢开裂的发生。
同时,在补焊过程中,应根据具体情况选择合适的补焊方法,并结合预防措施,提高不锈钢的使用寿命和性能。
通过本文的阐述,相信读者能够更好地了解不锈钢开裂补焊方法,并在实际应用中做到理论与实践相结合,为相关行业的发展和生产提供有益的参考。
1.2 文章结构文章结构的设计是为了使读者能够清晰地了解整篇文章的框架和内容安排。
本文将按照下述结构进行分析和论述:2.正文:2.1 不锈钢开裂的原因2.2 补焊方法一2.3 补焊方法二2.1 不锈钢开裂的原因在这一部分,我们将详细探讨导致不锈钢开裂的可能原因。
不锈钢是一种耐腐蚀材料,但在特定条件下仍可能发生开裂现象。
我们将介绍热裂纹和冷裂纹两种常见的开裂形式,并深入分析它们的成因。
同时,我们会探讨一些特殊情况下引起开裂的特殊因素。
不锈钢焊接缺陷以及应对措施
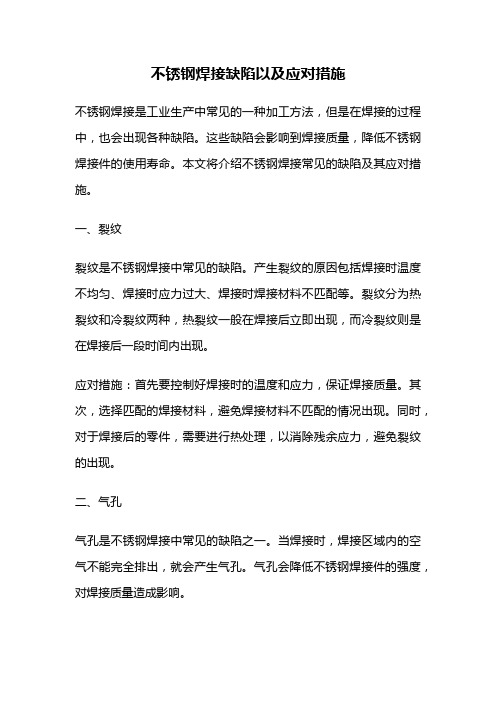
不锈钢焊接缺陷以及应对措施不锈钢焊接是工业生产中常见的一种加工方法,但是在焊接的过程中,也会出现各种缺陷。
这些缺陷会影响到焊接质量,降低不锈钢焊接件的使用寿命。
本文将介绍不锈钢焊接常见的缺陷及其应对措施。
一、裂纹裂纹是不锈钢焊接中常见的缺陷。
产生裂纹的原因包括焊接时温度不均匀、焊接时应力过大、焊接时焊接材料不匹配等。
裂纹分为热裂纹和冷裂纹两种,热裂纹一般在焊接后立即出现,而冷裂纹则是在焊接后一段时间内出现。
应对措施:首先要控制好焊接时的温度和应力,保证焊接质量。
其次,选择匹配的焊接材料,避免焊接材料不匹配的情况出现。
同时,对于焊接后的零件,需要进行热处理,以消除残余应力,避免裂纹的出现。
二、气孔气孔是不锈钢焊接中常见的缺陷之一。
当焊接时,焊接区域内的空气不能完全排出,就会产生气孔。
气孔会降低不锈钢焊接件的强度,对焊接质量造成影响。
应对措施:在焊接前,需要对焊接区域进行清洁,以避免杂质的存在。
焊接时,需要控制好焊接的电流和气体流量,保证焊接区域内的空气完全排出。
如果出现气孔,需要对焊接区域进行修补,直至完全消除气孔。
三、未焊透未焊透是不锈钢焊接中另一种常见的缺陷。
未焊透是指焊接区域内的焊接材料没有完全熔化,没有形成完整的焊接缝。
未焊透会导致焊接件的强度降低,影响焊接质量。
应对措施:在焊接前,需要对焊接区域进行清洁,以避免杂质的存在。
焊接时,需要控制好焊接的电流和焊接速度,保证焊接材料可以完全熔化。
如果出现未焊透的情况,需要对焊接区域进行修补,直至完全焊接透。
四、焊接变形焊接变形是不锈钢焊接中常见的问题之一。
当焊接时,由于焊接区域内温度的变化,会导致零件发生变形。
焊接变形会影响不锈钢焊接件的尺寸精度和装配质量。
应对措施:首先要选择合适的焊接方法和焊接参数,控制好焊接时的温度和应力。
其次,需要在焊接前进行预热,以减少焊接区域内的应力。
在焊接后,需要对焊接区域进行热处理,以消除残余应力,避免焊接变形的出现。
焊接裂纹产生原因及防治

焊接裂纹产生原因及防治背景焊接裂纹就其本质来分,可分为热裂纹、再热裂纹、冷裂纹、层状撕裂等。
下面仅就各种裂纹的成因、特点和防治办法进行具体的阐述。
1.热裂纹在焊接时高温下产生的,故称热裂纹,它的特征是沿原奥氏体晶界开裂。
根据所焊金属的材料不同(低合金高强钢、不锈钢、铸铁、铝合金和某些特种金属等),产生热裂纹的形态、温度区间和主要原因也各不相同。
目前,把热裂纹分为结晶裂纹、液化裂纹和多边裂纹等三大类。
1)结晶裂纹主要产生在含杂质较多的碳钢、低合金钢焊缝中(含S,P,C,Si缝偏高)和单相奥氏体钢、镍基合金以及某些铝合金焊缝中。
这种裂纹是在焊缝结晶过程中,在固相线附近,由于凝固金属的收缩,残余液体金属不足,不能及时添充,在应力作用下发生沿晶开裂。
防治措施:在冶金因素方面,适当调整焊缝金属成分,缩短脆性温度区的范围控制焊缝中硫、磷、碳等有害杂质的含量;细化焊缝金属一次晶粒,即适当加入Mo、V、Ti、Nb等元素;在工艺方面,可以通过焊前预热、控制线能量、减小接头拘束度等方面来防治。
2)近缝区液化裂纹是一种沿奥氏体晶界开裂的微裂纹,它的尺寸很小,发生于HAZ近缝区或层间。
它的成因一般是由于焊接时近缝区金属或焊缝层间金属,在高温下使这些区域的奥氏体晶界上的低熔共晶组成物被重新熔化,在拉应力的作用下沿奥氏体晶间开裂而形成液化裂纹。
这一种裂纹的防治措施与结晶裂纹基本上是一致的。
特别是在冶金方面,尽可能降低硫、磷、硅、硼等低熔共晶组成元素的含量是十分有效的;在工艺方面,可以减小线能量,减小熔池熔合线的凹度。
3)多边化裂纹是在形成多边化的过程中,由于高温时的塑性很低造成的。
这种裂纹并不常见,其防治措施可以向焊缝中加入提高多边化激化能的元素如Mo、W、Ti等。
2、再热裂纹通常发生于某些含有沉淀强化元素的钢种和高温合金(包括低合金高强钢、珠光体耐热钢、沉淀强化高温合金,以及某些奥氏体不锈钢),他们焊后并未发现裂纹,而是在热处理过程中产生了裂纹。
探究不锈钢管道裂纹产生原因分析及裂纹处理

探究不锈钢管道裂纹产生原因分析及裂纹处理摘要:对OCrl9Ni9不锈钢管道裂纹产生原因进行了分析,并对裂纹焊接处理的有关问题进行了阐述,同时叙述了具体挖补修复方法及焊接修复过程。
关键词:0Cr19Ni9不锈钢;晶界腐蚀开裂;工作应力;焊接裂纹;挖补修复0 前言电厂化学水工艺水管道规格219mm×10mm。
材质为0Cr19Ni9,满负荷连续运行,同时管道振动过大,工艺水又具有较强的腐蚀性且温度又高。
在管道膨胀弯的焊缝的热影响区产生了长约15Omm的纵向裂纹。
l 裂纹产生原因的分析1.1母材及填充材料使用不当管道使用的是0Cr19Ni9(美304),不锈钢的化学成分为:(C)≤0.08%,(Cr)为l8.0%~20.0%,(Ni)为8.O%~10.0%,由此可知,这类不锈钢的C含量与一般的奥氏体不锈钢C含量相当,并非超低碳不锈钢.并且没有加入稳定碳化物的Ti,Nb元素。
如果在焊接时没有避开450~850℃的危险温度区间,并且没有选用含Ti,Nb元素的焊接材料,就会在热影响区形成脆性大、塑性低的碳化铬,从而使热影响区、熔合线上产生晶界腐蚀裂纹。
1.2 焊接工艺不合理焊缝较宽,成形粗糙,弧坑较大,焊趾明显咬肉。
由此可以断定,焊接时所用焊条直径较大,焊接电流也较大,焊速慢,停留时间过长,没有避开450~850℃危险温度区间,道间温度控制也未见成效。
这是形成晶界腐蚀裂纹的又一原因。
为了保证装置在短期内恢复运行,就对裂纹进行了直接补焊。
(1)首先做好一切焊前准备工作,在距裂纹2个端点各l0 mm处钻φ6 mm的止裂孔,以防打磨、焊接过程中裂纹蔓延。
然后用角向磨光机磨出α=60°,b=3.2 mm,p=1.5 mm 的坡口。
坡口长度为止裂孔间的距离,并过止裂孔磨出焊缝与母材的过渡面,再将坡口两边的油、锈等杂物清理干净。
(2)采用ZX7—400A焊机,直流反接,焊材为A132,3.2 mm,进行打底、填充及盖面,焊接电流为1l0 A。
不锈钢焊缝裂纹产生的原因的重新陈述

不锈钢焊缝裂纹产生的原因的重新陈述不锈钢焊缝裂纹产生的原因的重新陈述在不锈钢焊接过程中,焊缝裂纹的产生是一个常见的问题。
虽然在之前的文章中已经探讨过这个主题,但现在我将重新陈述关于不锈钢焊缝裂纹产生原因的深入讨论。
我将从多个方面分析这个问题,以便我们更全面地理解不锈钢焊缝裂纹产生的原因。
1. 焊接材料选择不当:不锈钢焊缝裂纹的产生可以归因于焊接材料的选择不当。
不同等级的不锈钢具有不同的化学成分和热处理特性,因此选择合适的焊接材料对于避免焊缝裂纹至关重要。
当焊接材料的化学成分与母材不匹配时,焊缝裂纹的风险就会增加。
2. 母材的应力集中:母材中的应力集中也是导致不锈钢焊缝裂纹产生的原因之一。
当焊接过程中施加的热应力与存在的局部应力相结合时,焊缝周围的母材就会受到更大的应力,从而增加了焊缝裂纹的形成风险。
3. 焊接过程的热控制不当:热控制是焊接过程中至关重要的方面。
不当的热输入或冷却速度可能导致焊缝区域的热循环不均匀,从而引发焊缝裂纹。
热输入过高可能导致焊缝区域过热,而热输入过低则可能导致冷凝速度过快,这两种情况都会增加焊缝裂纹的风险。
4. 焊接残余应力:焊接过程中产生的残余应力也是不锈钢焊缝裂纹产生的原因之一。
焊接会改变材料的晶体结构并引入残余应力,当这些应力超过材料的强度极限时,焊缝裂纹可能会出现。
5. 焊接操作技术不当:不正确的焊接操作技术也会导致焊缝裂纹的形成。
这包括焊接速度、焊接电流和焊接电压的控制不当,以及不适当的焊接角度和焊接位置等因素。
这些技术问题可能会导致焊接过程中的应力不均匀,从而引发焊缝裂纹。
不锈钢焊缝裂纹的产生是由多种因素共同作用导致的。
正确选择焊接材料、控制焊接过程中的热量和应力、遵循正确的焊接操作技术等都是避免焊缝裂纹的关键。
只有全面理解这些原因,我们才能更好地避免不锈钢焊缝裂纹的产生,并确保焊接质量的稳定性和可靠性。
我对这个问题的理解是,不锈钢焊缝裂纹产生的原因是一个复杂且多方面的问题。
不锈钢焊缝热影响区出现裂纹的原因

不锈钢焊缝热影响区出现裂纹的原因引言:不锈钢作为一种常见的材料,广泛应用于许多领域,如航空航天、化工、建筑等。
在焊接过程中,常常会出现焊缝热影响区裂纹的问题,这给不锈钢的使用和维护带来了困扰。
本文将探讨不锈钢焊缝热影响区出现裂纹的原因,并提出相应的解决方法。
一、热影响区的定义和特点不锈钢焊缝热影响区是指在焊接过程中,焊缝周围的区域受到热影响而发生微结构和性能变化的区域。
热影响区具有以下特点:1. 高温:焊接过程中,热影响区温度较高,一般处于临界温度以上。
高温会引起不锈钢晶粒的长大和相变,从而导致热影响区的性能变化。
2. 快速冷却:焊接结束后,热影响区会经历快速冷却过程,冷却速度较快。
快速冷却会导致不锈钢晶粒的细化和残余应力的产生,进而引发裂纹的形成。
二、裂纹形成的原因1. 残余应力:焊接过程中,由于热量的不均匀分布和快速冷却,热影响区内会形成残余应力。
残余应力是裂纹形成的主要原因之一。
当残余应力超过材料的强度极限时,就会导致裂纹的形成。
2. 晶粒长大和相变:高温会引起不锈钢晶粒的长大和相变,这会导致晶界的断裂和裂纹的生成。
尤其是在焊接过程中,由于热量集中和焊接速度较快,晶粒的长大和相变更加明显,容易引发裂纹。
3. 焊接变形:焊接过程中,由于热膨胀和热收缩的影响,不锈钢焊缝周围会发生变形。
焊接变形会导致局部应力集中,从而增加了裂纹的形成概率。
三、预防和解决方法为了预防和解决不锈钢焊缝热影响区裂纹的问题,可以采取以下方法:1. 控制焊接参数:合理控制焊接电流、电压、焊接速度等参数,避免热输入过大或过小,减少热影响区的温度梯度和冷却速度,从而降低裂纹的形成概率。
2. 采用适合的焊接工艺:选择合适的焊接工艺,如预热、后热处理等,可以改变热影响区的组织和性能,减少裂纹的产生。
预热可以提高材料的塑性和韧性,后热处理可以消除残余应力。
3. 使用适当的填充材料:选择合适的填充材料,可以改变热影响区的组织和性能,提高焊缝的抗裂性能。
不锈钢管件裂纹的产生原因分析及处理

结论 、 硬度 、 无损检测结果等均合格 。除化学成分、 机械性能、 热处理结果及无损检测报告符合 产品标
图 1 存在 裂纹缺 陷的管件
准的规定外 , 合金钢管件的金相分析结果还应符合 产品标准的规定 , 但在产品质量证 明书中未体现晶 间腐蚀 的检测结果 。
3 3 现场 施工 .
当, 容易导致局部腐蚀 , 而晶问腐蚀是不锈钢管局部
腐 蚀 中最危 险 的破 坏形 式之一 。 随后 厂 家给 出 了产 生裂 纹 的原 因 : 批管 件 在 该
热处理 过程 中 , 由于热处 理炉一 组 电炉 丝损 坏 , 致 导
[ ] 中华人 民共 和国化学 工业部 .工业 金属 管道 工程施 2
焊缝热影响区内, 呈周向贯穿性分布, 部分焊缝周围 有密布裂纹缺陷。部 分三通的裂纹累积长度超过 D 20 N 5 周长的 5 % , 0 并且均分布在焊缝 的底部 , 如
图 1所示 。
看 出: 学成分、 械性能均符合 产 品标准 A T 化 机 SM A 1/ 32 0 32 A 1M一 7的要求, 原材料检验报告 中化学 成分 、 机械性 能 、 观及 尺寸 等 试验 结果 均符 合 外 A T 3 2A 1M一 7规范要求 , S M A 1/ 32 0 判定合格。
检测结 论 为合格 。
3 3 2 施 工质 量控 制 ..
有腐蚀 介质存 在 的条件下 , 生 晶间腐 蚀 , 是导 致 发 这 贯穿性 周 向裂 纹产 生 的直 接原 因 。 同时还 存 在 一些 间 接原 因 : 管件 制 造商 质 量 该 保证体 系运转 不正 常 , 出厂检验 制度 执行不严 格 , 出 厂资料 编制不 规范 ; 施工 单位 、 监理单 位对进 入现 场
CrMo钢管线焊接裂纹产生原因分析及预防措施

CrMo钢管线焊接裂纹产生原因分析及预防措施摘要:裂纹是焊缝最危险的缺陷。
焦化装置的CrMo钢管线焊接时有10道焊口出现了不同的微裂纹、星形裂纹、断裂状裂纹。
通过分析认为,星形裂纹为热裂纹,因焊前未清根产生,微裂纹是由于钢材本身的淬硬性引起,断裂状裂纹为冷裂纹,它产生的原因一是由于焊缝急冷、急热,焊缝中的氢来不及逸出而致开裂,二是焊缝周围较大的拘束应力——残余应力而导致。
本文针对裂纹产生原因进行分析并提出几点预防措施。
关键词:CrMo钢焊接裂纹分析1.前言中油辽河石化分公司2004年投产的100万吨/年延迟焦化装置部分非标设备及配套工艺由我院设计,其中的主要工艺管线多为CrMo钢,仅管道焊口就有1693道之多。
虽然施工时对焊接条件和焊接工艺要求非常严格,焊接一次合格率也很高,但在进行无损检测时,发现有些焊口仍然有裂纹。
因为裂纹是焊缝最危险的缺陷,存在安全隐患,故本文对裂纹的情况及产生原因作以简单介绍分析,以供施工借鉴。
2.施工现场的裂纹情况焦化装置CrMo钢管线2004年2月开始预制,5月中旬安装结束。
在CrMo 钢管线焊接初期,通过射线探伤发现有10道焊口的14处出现裂纹,其中3道裂纹呈断裂状(P1048、P1049、P1020),其余为微裂纹及星形裂纹。
其中断裂状裂纹情况如下表:3.裂纹产生原因分析在焊接生产中出现的裂纹是多种多样的,根据焊接时裂纹产生时的温度不同分成热裂纹和冷裂纹两大类,通常把焊缝结晶过程中高温状态下形成的裂纹称为热裂纹,在冷却过程中较底温度下形成的裂纹称为冷裂纹。
3.1.热裂纹是在焊接过程中产生的,像焦化装置抽检出现的星形裂纹即属此类,是组对焊口点焊后再焊前清根不彻底而产生的。
3.2.冷裂纹是焊接接头在冷却过程中产生的,多呈延迟形式,一般是在焊后2~3天出现,但也有的是焊后2~3个月,甚至更长。
冷裂纹的产生包括三方面因素:3.2.1.焊接接头的淬硬性。
Cr5Mo、15CrMo钢均属珠光体耐热钢,钢材本身具有较大的淬硬倾向,焊接过程中极易产生延迟裂纹,像焦化抽查发现的微裂纹即属此类。
关于钢结构焊接裂纹产生原因及预防措施探究
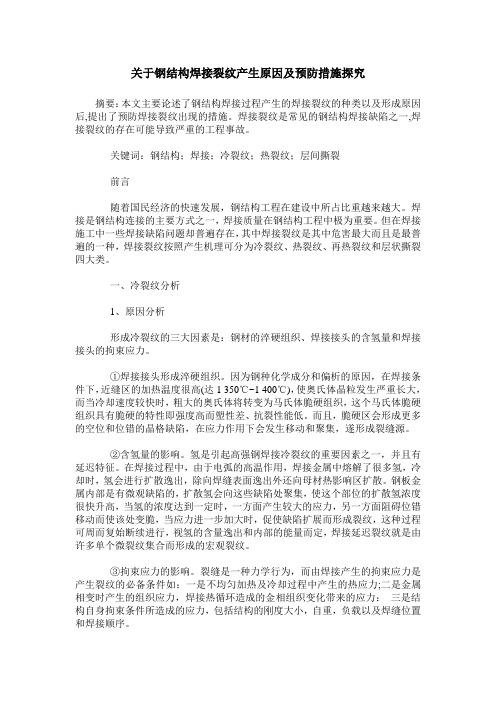
关于钢结构焊接裂纹产生原因及预防措施探究摘要:本文主要论述了钢结构焊接过程产生的焊接裂纹的种类以及形成原因后,提出了预防焊接裂纹出现的措施。
焊接裂纹是常见的钢结构焊接缺陷之一,焊接裂纹的存在可能导致严重的工程事故。
关键词:钢结构;焊接;冷裂纹;热裂纹;层间撕裂前言随着国民经济的快速发展,钢结构工程在建设中所占比重越来越大。
焊接是钢结构连接的主要方式之一,焊接质量在钢结构工程中极为重要。
但在焊接施工中一些焊接缺陷问题却普遍存在,其中焊接裂纹是其中危害最大而且是最普遍的一种,焊接裂纹按照产生机理可分为冷裂纹、热裂纹、再热裂纹和层状撕裂四大类。
一、冷裂纹分析1、原因分析形成冷裂纹的三大因素是:钢材的淬硬组织、焊接接头的含氢量和焊接接头的拘束应力。
①焊接接头形成淬硬组织。
因为钢种化学成分和偏析的原因,在焊接条件下,近缝区的加热温度很高(达1 350℃~1 400℃),使奥氏体晶粒发生严重长大,而当冷却速度较快时,粗大的奥氏体将转变为马氏体脆硬组织,这个马氏体脆硬组织具有脆硬的特性即强度高而塑性差、抗裂性能低。
而且,脆硬区会形成更多的空位和位错的晶格缺陷,在应力作用下会发生移动和聚集,遂形成裂缝源。
②含氢量的影响。
氢是引起高强钢焊接冷裂纹的重要因素之一,并且有延迟特征。
在焊接过程中,由于电弧的高温作用,焊接金属中熔解了很多氢,冷却时,氢会进行扩散逸出,除向焊缝表面逸出外还向母材热影响区扩散。
钢板金属内部是有微观缺陷的,扩散氢会向这些缺陷处聚集,使这个部位的扩散氢浓度很快升高,当氢的浓度达到一定时,一方面产生较大的应力,另一方面阻碍位错移动而使该处变脆,当应力进一步加大时,促使缺陷扩展而形成裂纹,这种过程可周而复始断续进行,视氢的含量逸出和内部的能量而定,焊接延迟裂纹就是由许多单个微裂纹集合而形成的宏观裂纹。
③拘束应力的影响。
裂缝是一种力学行为,而由焊接产生的拘束应力是产生裂纹的必备条件如:一是不均匀加热及冷却过程中产生的热应力;二是金属相变时产生的组织应力,焊接热循环造成的金相组织变化带来的应力:三是结构自身拘束条件所造成的应力,包括结构的刚度大小,自重,负载以及焊缝位置和焊接顺序。
Ni9钢氩弧焊焊接工艺及产生裂纹的预防措施

Ni9钢氩弧焊焊接工艺及产生裂纹的预防措施摘要:Ni9钢属于低温用低碳钢,被广泛于大型液化天然气的的低温储罐。
本文针对LNG低温储罐用Ni钢,重点阐述了其氩弧焊焊接工艺以及焊接过程中容易出现裂纹的原因和预防措施。
关键词:Ni9钢;氩弧焊;裂纹1.前言2007年,我单位为建设集团天宇设计研究院进行了Ni9钢的焊接工艺研究试验,针对焊接研究过程中,焊缝出现过的热裂纹和冷裂纹缺陷,总结出了本文的焊接工艺和裂纹的预防措施。
2.焊前准备和焊接工艺在焊接前用丙酮清理焊件表面,特别是坡口及其附近,然后用棉纱擦净焊件表面,其作用主要是去除焊件表面的油污和有机物。
晾干待用。
焊接工艺如表1所示:表1.Ni9钢钨极氩弧焊的焊接工艺焊前不需要进行预热,但是焊丝必须用丙酮进行清理,以避免污垢对焊接性能的影响。
焊接热输入不应过大,一般在35kJ/cm以下。
焊接时必须控制层间温度在100℃以下。
焊接时应采取措施消除弧坑裂纹和收弧裂纹。
具体措施是:打底焊时用穿透法焊接,把弧坑留在背面,另外清根后背面要有合适的坡口形状,避免出现深而窄的坡口;收弧时应尽量减少熔池尺寸,在坡口边缘或者焊道外缘收弧。
打磨方式尽量用砂轮打磨,最好不用碳弧气刨打磨。
3.Ni9钢焊接过程中常出现的问题对于Ni9钢的钨极氩弧焊,由于焊接冶金反应和热循环的作用,使得Ni9钢的低温性能降低,冷、热裂纹倾向增大。
3.1冷裂纹Ni9钢在进行氩弧焊,特别是进行横焊和立焊时极易出现冷裂纹,这也是氩弧焊焊接Ni9钢最易遇到的问题。
出现冷裂纹的原因有以下几种:(1)焊件表面特别是焊件坡口处含有机物过多和焊丝扩散氢含量过高引起的焊缝氢含量多大。
(2)焊接接头处应利过大,基本包括热应力、拘束应力和组织应力。
(3)电流不稳定或者换丝时出现温度梯度。
3.2热裂纹热裂纹是氩弧焊焊接过程中比较常见一种裂纹缺陷,它的产生跟焊缝金属结晶过程中的低熔点杂质的数量和分布有关,其具有高温沿晶断裂性质。
焊接裂纹形成的原因及防止措施
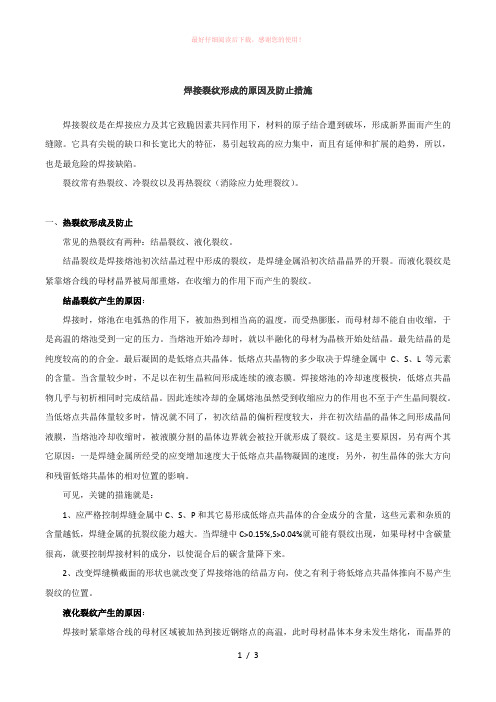
焊接裂纹形成的原因及防止措施焊接裂纹是在焊接应力及其它致脆因素共同作用下,材料的原子结合遭到破坏,形成新界面而产生的缝隙。
它具有尖锐的缺口和长宽比大的特征,易引起较高的应力集中,而且有延伸和扩展的趋势,所以,也是最危险的焊接缺陷。
裂纹常有热裂纹、冷裂纹以及再热裂纹(消除应力处理裂纹)。
一、热裂纹形成及防止常见的热裂纹有两种:结晶裂纹、液化裂纹。
结晶裂纹是焊接熔池初次结晶过程中形成的裂纹,是焊缝金属沿初次结晶晶界的开裂。
而液化裂纹是紧靠熔合线的母材晶界被局部重熔,在收缩力的作用下而产生的裂纹。
结晶裂纹产生的原因:焊接时,熔池在电弧热的作用下,被加热到相当高的温度,而受热膨胀,而母材却不能自由收缩,于是高温的熔池受到一定的压力。
当熔池开始冷却时,就以半融化的母材为晶核开始处结晶。
最先结晶的是纯度较高的的合金。
最后凝固的是低熔点共晶体。
低熔点共晶物的多少取决于焊缝金属中C、S、L等元素的含量。
当含量较少时,不足以在初生晶粒间形成连续的液态膜。
焊接熔池的冷却速度极快,低熔点共晶物几乎与初析相同时完成结晶。
因此连续冷却的金属熔池虽然受到收缩应力的作用也不至于产生晶间裂纹。
当低熔点共晶体量较多时,情况就不同了,初次结晶的偏析程度较大,并在初次结晶的晶体之间形成晶间液膜,当熔池冷却收缩时,被液膜分割的晶体边界就会被拉开就形成了裂纹。
这是主要原因,另有两个其它原因:一是焊缝金属所经受的应变增加速度大于低熔点共晶物凝固的速度;另外,初生晶体的张大方向和残留低熔共晶体的相对位置的影响。
可见,关键的措施就是:1、应严格控制焊缝金属中C、S、P和其它易形成低熔点共晶体的合金成分的含量,这些元素和杂质的含量越低,焊缝金属的抗裂纹能力越大。
当焊缝中C>0.15%,S>0.04%就可能有裂纹出现,如果母材中含碳量很高,就要控制焊接材料的成分,以使混合后的碳含量降下来。
2、改变焊缝横截面的形状也就改变了焊接熔池的结晶方向,使之有利于将低熔点共晶体推向不易产生裂纹的位置。
钢结构焊接裂纹的原因及防治措施

钢结构焊接裂纹的原因及防治措施钢结构是现代建筑中常见的结构形式之一,它具有重量轻、强度高、施工速度快等优点,因此被广泛应用于各类建筑工程中。
然而,在钢结构的制造和施工过程中,焊接裂纹往往成为一个常见的质量问题。
本文将探讨钢结构焊接裂纹的形成原因,并提出相应的防治措施。
一、焊接裂纹的形成原因1.1 材料问题钢材的组织结构和化学成分不合理是导致焊接裂纹的主要原因之一。
当钢材中含有含碳、硫、磷等含量超过规定标准的元素时,焊接时易产生高硬度和脆性物质,从而引发裂纹的形成。
1.2 焊接参数不当焊接过程中,焊接电流、焊接速度、焊接温度等焊接参数的选择不当,都可能导致焊接裂纹的生成。
例如,焊接电流过大会导致材料过热,从而在焊接接头中产生裂纹。
1.3 体积收缩差异钢材在焊接过程中会受到热量的影响而发生热胀冷缩,而焊接接头中的同时发生焊接金属的热收缩和焊接基体的冷缩,而两者之间的体积收缩差异可能引起焊接裂纹的形成。
1.4 焊接应力焊接过程中,焊接热量引入工件,产生应力集中,而大的应力集中可能导致焊接裂纹的生成。
特别是当焊接接头应力集中点的应力超过材料的承载极限时,裂纹便会发生。
二、焊接裂纹的防治措施2.1 材料严格控制在钢结构的制造和施工过程中,应严格控制材料的质量。
选用质量合格、符合要求的钢材,特别是控制其中的碳含量、硫含量、磷含量等关键成分的含量。
2.2 合理选择焊接参数在焊接过程中,应根据具体的钢材和焊接需求,合理选择焊接参数。
通过调整焊接电流、焊接速度、焊接温度等参数,确保焊接接头的均匀加热,避免产生过度应力。
2.3 预热和后续热处理对于较大尺寸、厚度较大的焊接接头,应进行预热处理。
通过预热可以减少焊接接头的冷缩和应力积聚,从而减少焊接裂纹的产生。
同时,在焊接完成后,可采取适当的后续热处理,通过热处理来消除残余应力。
2.4 控制焊接应力在焊接过程中,应合理控制焊接应力。
可以通过选用合适的焊接顺序、采用适当的焊接顺序交替焊接等方法,来减少焊接接头中的应力集中,降低焊接裂纹的风险。
不锈钢导管开裂原因分析

weld defects are mostly correlated with the high welding temperature and the improper lap joim design.
Key words:stainless steel pipe;cracking;braze welding;porosity;grain growing
Fig.3 Sidesteps on the fracture surface
图7焊角部位发附近区域的表面蟛貌 Fig,7 SurfacemorphologyoftheweldOOITierandthe
neighboring area
210
万方数据
《金属热处理》2007年第32卷(增TU)
1.2显微组织检查 垂直导管焊缝和裂纹取样进行金相检查。裂纹贯
其次,导管为高频感应钎焊,加热和冷却速度都
不容易控制,而HICuNi30-2—0.2钎料的熔化温度和 1Crl8Ni9Ti钢的晶粒长大温度很接近,对焊接温度的 要求又很严,所以焊接时应注意适当加快加热时间、 加快冷却速度,如仍无法避免品粒长大,可以改用熔 点相对较低的HICu.2a焊料进行钎焊。
4结论
图2焊缝裂纹断口宏观形貌 Fig.2 Macrograph ofthe crack surface 观察焊缝焊角及其邻近区域,焊角表面的枝晶 露头较其它部位明显,见图7。
幽6导管基体中的疲劳条带 Fig.6 Fatigue striation in the steel base material
图3焊缝裂纹断口表面台阶
不锈钢导管开裂原因分析
姜涛,李运菊,赵旭 (北京航空材料研究院中国航空工业失效分析中心,北京 100095) 摘要:某型不锈钢导管通过高频感应加热钎焊与套管相连,在充油疲劳试验中发生多起早期开裂漏油故障。对 导管裂纹、裂纹断I:l、显微组织进行了观察,对显微硬度进行了测定。研究结果表明,开裂从钎焊焊角附近的 外表面起始,向导管基体延伸并在导管基体中发生高周疲劳扩展。钎焊焊缝的枝品间显微疏松导致的应力集中 与微裂纹效应阻及近焊缝区母材晶粒长大是导管早期疲劳开裂的主要原因。焊接缺陷的产生主要与焊接温度过 高、搭接接头设计不合理有关。 关键词:不锈钢导管;开裂;钎焊;疏松:晶粒长大
不锈钢方管断裂的原因及处理方法

不锈钢方管断裂的原因及处理方法不锈钢方管作为一种重要的建筑材料,其具有耐腐蚀、耐高温、强度高等优点,在各个领域得到广泛应用。
然而,不锈钢方管在使用过程中有时会出现断裂现象,严重影响管道的正常运行。
以下将从不锈钢方管断裂的原因和处理方法两个方面进行探讨。
首先,不锈钢方管断裂的主要原因可归结为以下几点:1.材料本身缺陷:不锈钢方管在生产过程中存在一定的制造缺陷,如夹杂物、气孔、夹捏等,这些缺陷会导致管道的强度和韧性下降,从而引发断裂。
2.外部因素的影响:不锈钢方管在使用过程中常常受到外部力的作用,如挤压、弯曲、拉伸、冲击等,如果超出了材料的承受能力,就会导致断裂。
3.焊接质量不良:不锈钢方管在连接过程中常常需要进行焊接,如果焊接质量不好,如焊接接头有裂纹、气孔等缺陷,就会降低管道的强度和韧性,易于发生断裂。
其次,针对不锈钢方管断裂问题,可以采取一些处理方法:1.加强生产和质量检验:对于不锈钢方管的生产过程,要加强管材内部和外部的质量检验,确保不存在夹杂物、气孔等缺陷,同时加强对焊接接头的质量检验,确保焊接质量良好。
2.合理选择和使用:在使用不锈钢方管的过程中,要根据实际情况选择合适的材料和尺寸,避免超负荷使用,同时要注意管道的安装和维护,避免外部力对管道产生过大的影响。
3.加强管道的支撑和固定:为了避免管道因外部力作用而产生振动和位移,应加强对管道的支撑和固定,保证管道的稳定性和安全性。
4.定期检测和维护:对于已经使用的不锈钢方管,要定期进行检测和维修,检查管道是否存在裂纹、疲劳等问题,及时处理和修复,以确保管道的可靠运行。
总之,不锈钢方管断裂问题的产生是多种因素综合作用的结果。
通过加强不锈钢方管的生产质量、合理使用管道、加强管道的支撑和固定以及定期检测和维护等方法,能够有效预防和处理不锈钢方管的断裂问题,保证管道的正常运行和使用寿命。
关于不锈钢焊缝开裂质量报告整改方案

关于不锈钢焊缝开裂质量报告整改方案一、引言不锈钢焊缝开裂是焊接过程中常见的质量问题之一,其可能导致焊接件的强度和密封性下降,进而影响整体工程质量。
本文针对不锈钢焊缝开裂质量问题,提出了一套整改方案,旨在解决该问题并提升焊接质量。
二、问题分析不锈钢焊缝开裂主要有以下几个原因:1. 焊接参数不合理:焊接过程中,焊接电流、电压、焊接速度等参数的不合理选择可能导致焊缝过热或过冷,从而引发开裂问题。
2. 焊接材料质量问题:不锈钢焊接材料的质量差异会对焊缝的开裂倾向产生影响,如硫含量过高、杂质过多等。
3. 焊接工艺不当:焊接工艺中的预热、间隙控制、焊接顺序等环节若处理不当,也可能导致焊缝开裂。
4. 焊接环境不良:焊接环境中存在的氧气、水分等会对焊接质量产生不良影响,如生成气孔、氧化等,从而增加焊缝开裂的风险。
三、整改方案为解决不锈钢焊缝开裂质量问题,我们提出以下整改方案:1. 优化焊接参数:根据不同焊接材料和工件厚度,合理选择焊接电流、电压和焊接速度,确保焊接过程中的热输入均匀分布,避免焊缝过热或过冷。
2. 选择高质量的焊接材料:选用低硫、低杂质的不锈钢焊接材料,确保焊缝的质量稳定性和可靠性。
3. 优化焊接工艺:合理控制焊接预热温度和间隙,采用适当的焊接顺序,确保焊接过程中的温度梯度适中,避免焊缝开裂的风险。
4. 提升焊接环境:优化焊接环境,减少氧气和水分的存在,采取防护措施,避免氧化和气孔等不良现象的发生。
四、实施步骤1. 设立焊接参数优化小组:由焊接工程师、质量工程师和工艺工程师组成,共同制定焊接参数优化方案。
2. 选用高质量焊接材料:与供应商保持密切合作,选择低硫、低杂质的不锈钢焊接材料,并进行质量监控。
3. 优化焊接工艺:根据焊接材料和工件的特性,制定焊接工艺文件,明确焊接顺序、预热温度和间隙要求,并进行工艺验证。
4. 完善焊接环境:改善焊接工作区域的通风设施,减少氧气和水分的存在,防止不良环境对焊接质量的影响。
管道焊接工程中焊缝裂纹形成机理及预防措施研究
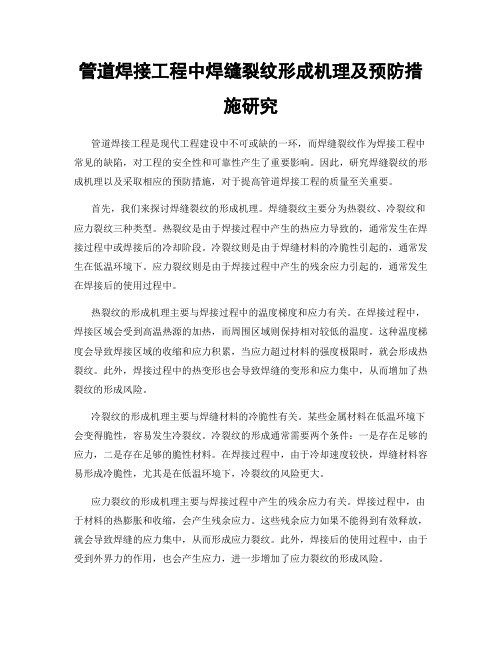
管道焊接工程中焊缝裂纹形成机理及预防措施研究管道焊接工程是现代工程建设中不可或缺的一环,而焊缝裂纹作为焊接工程中常见的缺陷,对工程的安全性和可靠性产生了重要影响。
因此,研究焊缝裂纹的形成机理以及采取相应的预防措施,对于提高管道焊接工程的质量至关重要。
首先,我们来探讨焊缝裂纹的形成机理。
焊缝裂纹主要分为热裂纹、冷裂纹和应力裂纹三种类型。
热裂纹是由于焊接过程中产生的热应力导致的,通常发生在焊接过程中或焊接后的冷却阶段。
冷裂纹则是由于焊缝材料的冷脆性引起的,通常发生在低温环境下。
应力裂纹则是由于焊接过程中产生的残余应力引起的,通常发生在焊接后的使用过程中。
热裂纹的形成机理主要与焊接过程中的温度梯度和应力有关。
在焊接过程中,焊接区域会受到高温热源的加热,而周围区域则保持相对较低的温度。
这种温度梯度会导致焊接区域的收缩和应力积累,当应力超过材料的强度极限时,就会形成热裂纹。
此外,焊接过程中的热变形也会导致焊缝的变形和应力集中,从而增加了热裂纹的形成风险。
冷裂纹的形成机理主要与焊缝材料的冷脆性有关。
某些金属材料在低温环境下会变得脆性,容易发生冷裂纹。
冷裂纹的形成通常需要两个条件:一是存在足够的应力,二是存在足够的脆性材料。
在焊接过程中,由于冷却速度较快,焊缝材料容易形成冷脆性,尤其是在低温环境下,冷裂纹的风险更大。
应力裂纹的形成机理主要与焊接过程中产生的残余应力有关。
焊接过程中,由于材料的热膨胀和收缩,会产生残余应力。
这些残余应力如果不能得到有效释放,就会导致焊缝的应力集中,从而形成应力裂纹。
此外,焊接后的使用过程中,由于受到外界力的作用,也会产生应力,进一步增加了应力裂纹的形成风险。
为了预防焊缝裂纹的形成,我们可以采取一系列的预防措施。
首先,控制焊接过程中的温度梯度和应力是关键。
可以通过合理的焊接工艺参数和焊接顺序来减小温度梯度和应力的产生,从而降低热裂纹的风险。
其次,选择合适的焊接材料也是重要的一步。
应选择具有良好韧性和抗冷脆性的材料,以减少冷裂纹的发生。
焊接裂纹成因分析及其防治措施
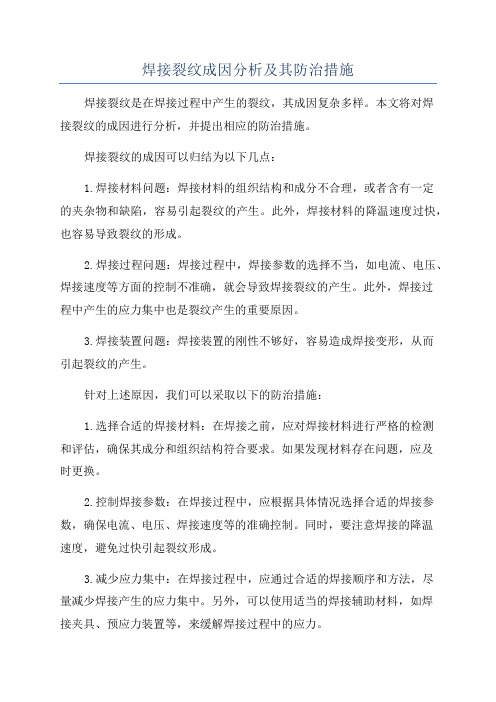
焊接裂纹成因分析及其防治措施焊接裂纹是在焊接过程中产生的裂纹,其成因复杂多样。
本文将对焊接裂纹的成因进行分析,并提出相应的防治措施。
焊接裂纹的成因可以归结为以下几点:1.焊接材料问题:焊接材料的组织结构和成分不合理,或者含有一定的夹杂物和缺陷,容易引起裂纹的产生。
此外,焊接材料的降温速度过快,也容易导致裂纹的形成。
2.焊接过程问题:焊接过程中,焊接参数的选择不当,如电流、电压、焊接速度等方面的控制不准确,就会导致焊接裂纹的产生。
此外,焊接过程中产生的应力集中也是裂纹产生的重要原因。
3.焊接装置问题:焊接装置的刚性不够好,容易造成焊接变形,从而引起裂纹的产生。
针对上述原因,我们可以采取以下的防治措施:1.选择合适的焊接材料:在焊接之前,应对焊接材料进行严格的检测和评估,确保其成分和组织结构符合要求。
如果发现材料存在问题,应及时更换。
2.控制焊接参数:在焊接过程中,应根据具体情况选择合适的焊接参数,确保电流、电压、焊接速度等的准确控制。
同时,要注意焊接的降温速度,避免过快引起裂纹形成。
3.减少应力集中:在焊接过程中,应通过合适的焊接顺序和方法,尽量减少焊接产生的应力集中。
另外,可以使用适当的焊接辅助材料,如焊接夹具、预应力装置等,来缓解焊接过程中的应力。
4.加强装置刚性:焊接装置应具备足够的刚性和稳定性,避免焊接过程中产生的振动和位移,从而减少焊接变形,并防止裂纹的出现。
总结起来,要防止焊接裂纹的发生,需要从焊接材料、焊接过程和焊接装置三个方面进行综合考虑和控制。
只有合理选择材料、准确控制焊接参数、减少应力集中和加强装置刚性,才能够有效防止焊接裂纹的产生。