验货流程图
成品检验流程图和不良标识

注意事项
当检验数量小于或等于 50 只时,采用全检方式,合格品入库,不合格品予以返工。 当检验数量大于或等于 51 只时,采用抽检的方式,按 GB/T2828 一般检验水平Ⅱ级, AQL=1.5,C=0 执行。 成品检验合格后,方可入库或出货 检验合格的产品或样品需放该批次抽检袋中,并将抽样的批号记录在相关报告中,以便复 核。 不合格品的标识方法 依据产品特点可分别采用下列方法之一: A、用荧光笔在不合格品的醒目位置做标识; B、附不合格品标签; C、置于不合格品区(或隔离区、退货区) 。 颜色标识: 红色-------不合格品 黄色-------让步接收 绿色-------放行或合格品
成品检验流程图
生产人员 成品检验专员 质量主管
开始
生产
成品检验申请
准备检验
包装 入库
实施检验
填写检验报告 出货 执行
审核
下达审核意见
合格品
不合格品
退货处理
结速
返 工
返 修
报 废
成品检验作业指导书
入库检验 生产部门将待检产品送到待检区,成品检验人员核对入库单与待检品的胶料编号、产品名 称和产品编号。 按成品入库单的胶料编号、产品名称,调出该产品的检验标准或产品图纸。 准备必要的设备(卡尺、厚度规)与检验标准或产品图纸。 以每一包装箱作为一检验批。 检验合格后,在该批贴“绿色”的标签。 成品检验人员核对产品的数量及产品名称后,在袋子标签上盖“合格”章,并填写《成品 检验报告》 。 出货检验 按出货通知单内容,安排出货产品,仓库人员通知检验人员验货。 成品检验人员按出库通知单数量检验送检批,检验方式同入库检验。 按检验标准检验允收后,在“报检单”上填写检验状态,并同时填写《出货报告》 。 核对出库单内容、数量正确无误后,予以放行。
来料检验作业流程图
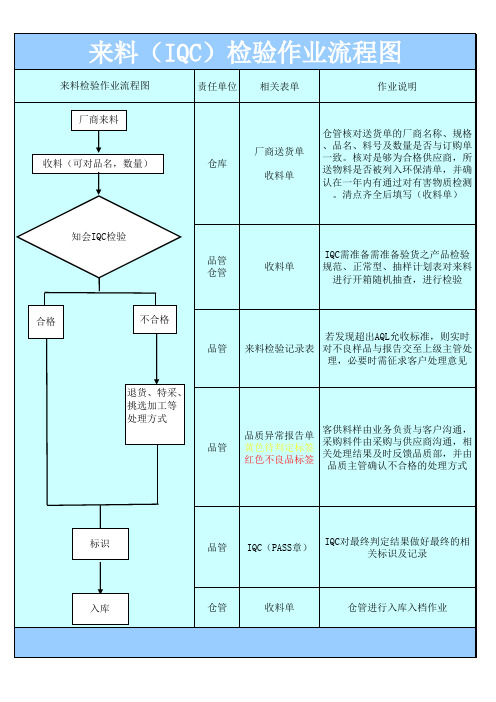
知会IQC检验
品管 仓管
收料单
IQC需准备需准备验货之产品检验 规范、正常型、抽样计划表对来料
进行开箱随机抽查,进行检验
合格
不合格
品管
若发现超出AQL允收标准,则实时 来料检验记录表 对不良样品与报告交至上级主管处
理,必要时需征求客户处理意见
退货、特采、 挑选加工等 处理红色不良品标签
客供料样由业务负责与客户沟通, 采购料件由采购与供应商沟通,相 关处理结果及时反馈品质部,并由 品质主管确认不合格的处理方式
标识 入库
品管
IQC(PASS章)
IQC对最终判定结果做好最终的相 关标识及记录
仓管
收料单
仓管进行入库入档作业
来料(IQC)检验作业流程图
来料检验作业流程图
责任单位 相关表单
作业说明
厂商来料 收料(可对品名,数量)
仓库
厂商送货单 收料单
仓管核对送货单的厂商名称、规格 、品名、料号及数量是否与订购单 一致。核对是够为合格供应商,所 送物料是否被列入环保清单,并确 认在一年内有通过对有害物质检测
。清点齐全后填写(收料单)
超市流程图

商品订单作业检查流程图作业编号:
”表示商品流程,“”表文件流程。
商管收货作业流程图作业编号:
库存更正作业流程图(厂商补损耗) 作业编号:
库存更正作业流程图(商管输入错误)
库存更正作业流程图(库存差异)
库存更正作业流程图(中央厨房)
不同核算体系分店间商品转货流程图作业编号:
不同核算体系分店间商品转货流程图作业编号:
相同核算体系分店间商品转货流程图作业编号:
△流程的结束
商品流动文件流动
代销(无商品)作业流程图作业编号:
注:▽流程的开始
厂商退货作业流程图作业编号:
金融室(销退备用金)作业流程作业编号:
个人收集了温度哦精品文档供大家学习
==============================专业收集精品文档=============================
表示文件流程”表示操作流程(含支票)
==============================专业收集精品文档=============================。
产品检验抽样规定流程图

1.目的:规范来料检验、成品检验之抽样水准、抽样方案以统一检验标准,确保来料及成品的质量稳定、良好。
2.范围:适用本公司IQC进料检验、OQC成品出货检验的所有产品。
3.职责:a)IQC、OQC负责执行本规定b)品管部负责监督执行并视产品实际情况制定、修改本规定4.程序:A.来料检验1)抽样标准:按MIL-STD-105E (等同GB2828-87)Ⅱ级检查水平一次抽样进行2)合格质量水准AQL规定:①电子料MAJOR:0.4;MINOR:2.5②组合料MAJOR:1.0;MINOR:4.03)检查严格度:正常检验4)抽样方式:随机抽样5)抽样批量:每一订单作为一个检查批次以上规定了来料检验通用抽样检验标准,部分物料特别规定的除外,参见具体物料检验标准,特殊情况由物料QE决定。
B.成品出货检验1)抽样标准:按MIL-STD-105E(等同GB2828-87)Ⅱ级检查水平一次抽样方案进行2)合格质量水准AQL规定:①内销有线产品、寻呼机:MAJOR:0.4;MINOR:2.5②内销无线产品:MAJOR:0.65;MINOR:2.5③外销产品:在客户验货标准规定的AQL轻重缺陷均加严一个等级,特殊情况由产品QE决定3)检验严格度:正常检验4)抽样方式:随机抽样5)抽样批量①一般以生产线每小时生产某机型的平均数量作为一个批量,有线电话一般以280PCS为一个批量②根据相应机型的质量控制计划来确定每批批量③生产清机尾数少于50PCS应全检6)抽样标准转移规则正常检验时,若连续五批中有两批经初次检验不合格,则从下一批检验转到加严检验加严检验时,若连续五批中有两批经初次检验合格,则从下一批检验转到正常检验正常检验时,若连续十批经初次检验合格,则从下一批检验转到放宽检验放宽检验时,若有一批不合格,则从下批检验转到正常检验抽样方案见附录1-4。
仓库货物验收入库流程

1湖南鸿豪能源贸易有限公司管理部文件湖南鸿豪能源贸易有限公司仓库收货流程仓库货物验收入库流程图说明:一、发货单位按照双方约定的托运方式,依照《货物订单》的数量、质量、规格将货物运送至《货物订单》指定的交货地点。
二、货到指定收货地点后,货运司机通知仓管员验货。
如交货地系公司仓库的,货运司机必须将货物运送至仓库,找到仓管员,根据仓管员指引,按便于卸货的方式将货车停放好;交货地点系公司仓库以外的其他货运站的,送货司机,必须根据收货方提供的电话通知仓管员到约定交货地点验货。
三、仓管员接到送货司机或送货单位通知后,效验送货单据。
效验内容包括:送货单据是否与《货物订单》内容相符、实际货物是否与《送货单》载记的数量、质量、品名、规格等内容相符。
对于货物与单据不相符者,必须就货、单差异先电话请示公司,根据公司指示,同意收货者,仓管员方可安排卸车验货。
对于交货地点为货运站的,仓管员到达收货地点,发现货、单不符,不得安排提货装车,必须就货、单差异先电话请示公司,根据公司指示,同意收货后,仓管员方可安排验货、提货装车。
四、对于货、单相符或公司指示,同意收货的货物,仓管员分两种情况收货入库:第一、交货地点在公司仓库的:卸车时验货;第二、交货地点系某收货站时,转货装车时验货。
验货内容包括:货物包装、罐装、标签是否完整,货物是否在有效的保质期内,再次核实货物数量是否与送货单相符,其他验货时需要发现的问题。
五、货物验收完毕后,仓库管理员开具收货凭据,收货凭据必须有仓管员签名,并加盖仓库印章。
《收货单》分四联:第一联、客户联,交司机或货运站发货人员转交发货单位;第二联、财务联,交公司财务结算货款;第三联、装卸联,交装卸工结算装卸费用;第四联、仓库联,仓库人员自己留存入库。
《收货单》式样见附表。
六、货物验收完毕,必须及时将到货信息反馈公司财务。
湖南鸿豪能源贸易有限公司管理部1.2湖南鸿豪能源贸易有限公司管理部文件一一年十一月二十三O二日《湖南鸿豪能源贸易有限公司收货单》附表:2.3湖南鸿豪能源贸易有限公司管理部文件湖南鸿豪能源贸易有限公司单收货第一联:客户联收单位送货单位:发货单位::备注:财务联、装卸联、留存联格式不变,只是右上角的分别改成:财务联、装卸联、仓库联。
产品质量检验管理程序(含流程图)
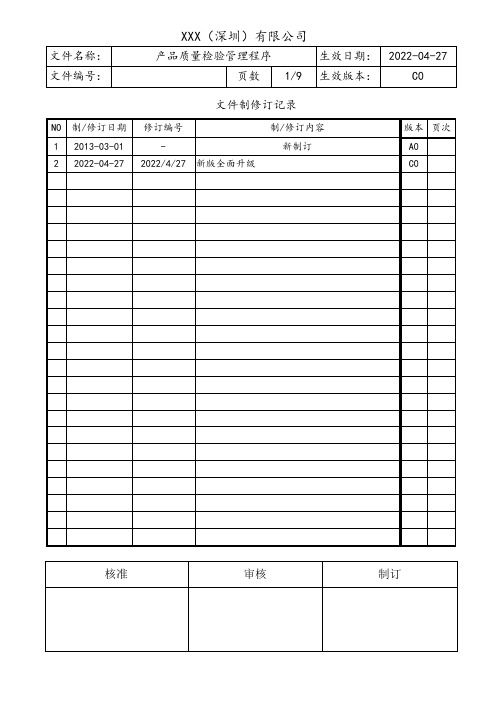
文件制修订记录1.0目的为了有效测量与监控产品从进料、制程、成品及出货各阶段检验作业能始终符合产品工程规范的各项要求。
2.0范围:适用于品管IQC、IPQC、QA过程作业。
3.0权责:3.1品管部:负责各阶段品质检验的执行、标识、追溯的管理、实际验货。
3.2工程部:产品作业标准的制定与检查。
3.3生产部:依生产计划、工程标准、验收标准执行生产作业。
3.4业务部:依订单需求验收出货数量。
3.5资材部:采购物料的外部联络。
4.0定义:无5.0作业内容:5.1进料检验5.1.1收料5.1.1.1供应商依据采购订单交货到公司仓库。
5.1.1.2仓管依据采购订单核对送货单是否一致,如若不符则退货并要求供应商重新交货,符合则点收数量并开出[进货单]。
5.1.1.3仓管将[进货单]连同要求供应商提供的相关文件(如材质报告、检验报告、测试报告等)交品管部,通知IQC进行检验。
5.1.1.4检验参照依据AQL表或依客户端需求作抽样检验。
5.1.1.5品管部IQC接到[进货单]后对供应商所提供的文件进行验证,(有法规环保类要求的产品必须依客户指定或经国家认可有检测能力机构出具的测试报告,如“SGS报告”等);品管部可以根据批量大小、价值贵重程度来对供应商所提供产品的材质进行一次确认。
5.1.1.5下列几项物料必须由品管部进料检验:a)生产性原材料。
b)外发加工产品。
c)包装材料等。
5.1.2需应用下列一种或多种方法进行验收、检验5.1.2.1接收检验及测试:a)核对材质证明(限自购原材料,样品或来料加工产品可不需要提供材质证明),核对供应商提供的相关文件。
b)依《检验标准书》逐项检验与填写[进料检验报告],无《检验标准书》时,依图面求或样板检验,检验结果可直接记录于[进料检验报告]上。
c)凡属客户提供来料进行加工,如无图面,依据客户提供的规格进行检验;如既无规格又无图面,IQC只针对其外观进行检验并记录于[进料检验报告]上。
设备验收质量控制流程图

设备验收质量控制流程图英文回答:The process of quality control for equipment acceptance can be depicted in a flowchart. This flowchart outlines the steps involved in ensuring the quality of the equipment being accepted. The following is a description of the flowchart:1. Start: The process begins with the start symbol, indicating the initiation of the quality control processfor equipment acceptance.2. Document Review: The first step is to review the relevant documentation, including the equipment specifications, manuals, and any other related documents. This helps in understanding the requirements and specifications of the equipment.3. Inspection: The next step is to conduct a physicalinspection of the equipment. This involves visually examining the equipment to check for any damages, defects, or discrepancies.4. Testing: After the inspection, the equipment needs to undergo various tests to ensure its functionality and performance. These tests may include functionality tests, performance tests, safety tests, and any other specific tests as per the equipment requirements.5. Test Results Evaluation: The test results are then evaluated to determine whether the equipment meets the specified requirements. This evaluation may involve comparing the test results with the predefined acceptance criteria or standards.6. Non-Conformance Handling: If any non-conformance or deviation from the specified requirements is identified during the evaluation, it needs to be addressed. This may involve documenting the non-conformance, investigating the root cause, and implementing corrective actions.7. Acceptance Decision: Based on the evaluation of the test results and non-conformance handling, a decision is made regarding the acceptance of the equipment. If the equipment meets all the specified requirements and any identified non-conformances are resolved, it can be accepted. Otherwise, further actions may be required, such as retesting or rejection of the equipment.8. Documentation: Finally, the acceptance decision and all the relevant information, including the test results, non-conformance reports, and any other supporting documents, are documented for future reference.End: The process ends with the end symbol, indicating the completion of the quality control process for equipment acceptance.中文回答:设备验收质量控制流程图描述了设备验收过程中的质量控制步骤。
客户验货流程图

附注:如客户验货数量上,可酌情考虑不借用生产部人员,品质部和业务当时予以还原。
作业流程 通知相关部门 仓库或生产准备
客户验货
仓库或生产数据管控 品质全程跟踪 验货OK
产品还原 Y
收货放置
客户验货流程图
相关说明
权责单位
使用表单
业务提前通知品质、生产、仓 库和PMC
业务部
邮件或内部联络函
PMC通知验货准备,货在生产
部,生产部准备;货在仓库, 仓库作相应准备;比如哪些产
生产部或仓库
品、摆放区域、产品数量等等
由业务主导,并发函生产部借 人(注明人员数量和借用时 间),生产部人员由业务安 排,负责搬运、拆产品、包装 产品和还原入库
业务部
邮件或电话通知 内部联络函
如产品须出库或出车间,由业 务打借条(白条也行)处理, 事后还货时借条收回
生产部、仓库 、业务
借条
品质部负责解释、协助和品质 确认,如有异常则须贴不合格 标识,并开出品质异常单,具 体按成品检验流程处理
品质部
Hale Waihona Puke 品质异常单业务安排生产部人员原则上即 时还原包装,以免混乱。
业务部
业务安排生产人员还原产品, 并送至原借出地方,并和生产 或仓库交接清楚。
业务部
生产部或仓库收货点收,并按
规定放置标识,如客户在仓库 开机看外观未拿出仓库测试, 则原则上现场即时还原,如须
生产部、仓库 、业务
打包装带则由仓管员负责处理
验货的流程

验货的流程验货的流程主要包括以下几个步骤:1. 选择合适的验货员:根据产品的特点和复杂程度,选择具备相关经验和专业知识的验货员进行验货。
2. 预约验货时间和地点:与供应商或厂家协商确定验货时间和地点,确保所有相关人员都可以参与。
3. 准备验货工具和材料:根据产品的特点和验货的要求,准备好相应的验货工具和材料,例如测量工具、电池、电源等。
4. 制定验货标准和流程:根据产品的规格和质量要求,制定详细的验货标准和流程,包括外观、尺寸、功能、性能等方面的检查项目和要求。
5. 到货验收:验货员到达验货地点后,首先进行到货验收,即核对货物的数量和包装是否完好,并与供应商确认订单信息是否一致。
6. 外观检查:验货员对产品的外观进行检查,包括表面是否有划痕、变形、脱漆等问题,确保产品外观符合要求。
7. 尺寸检测:针对需要准确尺寸的产品,验货员使用相应的测量工具对产品的尺寸进行检测,确保产品尺寸符合要求。
8. 功能和性能测试:验货员对产品的功能和性能进行测试,包括开关、按键、连接性能等方面,确保产品能够正常使用。
9. 安全性检查:对需要符合安全标准的产品,验货员进行相关测试和检查,确保产品符合安全要求,例如电气安全、化学物质的含量等。
10. 记录和整理结果:验货员将验货过程中的检查结果进行详细记录,并整理成验货报告,包括产品的质量情况、存在的问题和建议等。
11. 汇报和沟通:验货员将验货结果和报告汇报给相关的部门或人员,与供应商或厂家进行沟通,商讨解决存在问题的措施。
12. 返工或退换货处理:如果产品存在质量问题或不符合要求,与供应商或厂家商讨解决办法,可能需要返工修复或退换货。
13. 跟踪和监督:对于未解决的问题,验货员需要进行跟踪和监督,确保问题得到解决并保证产品质量。
14. 签收确认:在验货过程结束后,由相关部门或人员进行签收确认,确认验货结果和产品的质量情况。
总结:验货的流程包括准备工作、到货验收、外观检查、尺寸检测、功能和性能测试、安全性检查、记录整理、汇报沟通、返工退换货处理、跟踪监督和签收确认等步骤。
供货流程图

客户下达订单 审单分类统计
经理下达分配任务
订单部审核订单, 品名、 数量、质量、规格、 送货
时间等, 经理签字确认。
采购员前往各供货点采购食材 食材出货前检测
检测合格后食材分类装
过称, 登记。抽检质
量, 留样。
品检员在 "出货检验
单” 上签字。
发货 客户收货 售后服务及改进
根据客户分布情况安排好送
货线路, 准时发车送货。
货物达到客户指定地点后, 由甲方人员验货, 食材检测
含格后. 方可卸货入库
及时处理客户的投诉及建
议。提出改进方案 ;
海关验货流程
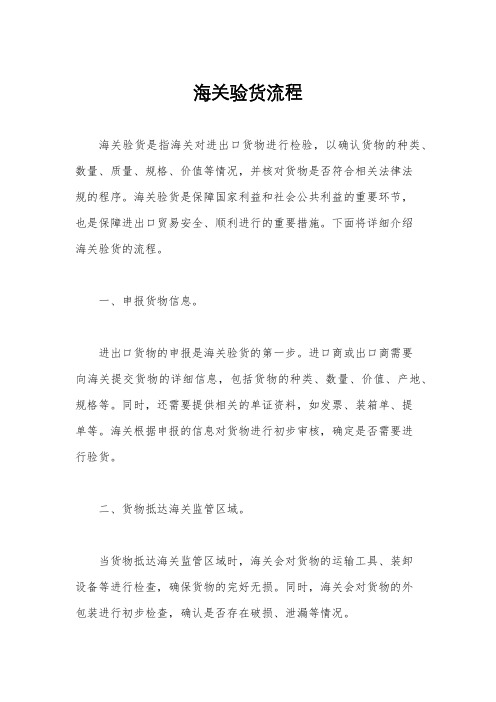
海关验货流程海关验货是指海关对进出口货物进行检验,以确认货物的种类、数量、质量、规格、价值等情况,并核对货物是否符合相关法律法规的程序。
海关验货是保障国家利益和社会公共利益的重要环节,也是保障进出口贸易安全、顺利进行的重要措施。
下面将详细介绍海关验货的流程。
一、申报货物信息。
进出口货物的申报是海关验货的第一步。
进口商或出口商需要向海关提交货物的详细信息,包括货物的种类、数量、价值、产地、规格等。
同时,还需要提供相关的单证资料,如发票、装箱单、提单等。
海关根据申报的信息对货物进行初步审核,确定是否需要进行验货。
二、货物抵达海关监管区域。
当货物抵达海关监管区域时,海关会对货物的运输工具、装卸设备等进行检查,确保货物的完好无损。
同时,海关会对货物的外包装进行初步检查,确认是否存在破损、泄漏等情况。
三、货物抽验。
海关会根据风险管理的原则,对部分货物进行抽验。
抽验的货物将被送往验货场所,进行详细的检查。
验货人员将对货物进行拆包、抽样、称重、测量等操作,以确认货物的实际情况是否与申报信息一致。
四、检验报告。
验货人员将根据实际情况编制检验报告,报告中将详细记录货物的种类、数量、质量、规格、价值等情况,并对发现的问题进行说明。
检验报告将作为海关批准放行货物的依据,也是进出口商申报报关单的重要依据。
五、放行货物。
根据检验报告的结果,海关将决定是否放行货物。
如果货物符合相关法律法规的要求,海关将予以放行,并出具放行通知书。
进口商或出口商凭借放行通知书可以办理进出口报关手续,完成进出口货物的清关手续。
六、异常处理。
如果货物在验货过程中发现异常情况,如数量与申报不符、质量不合格、规格不符合要求等,海关将根据情况对货物进行处理。
可能的处理方式包括退运、罚款、销毁等。
同时,海关还会对相关企业进行责任追究,确保进出口企业依法合规经营。
总结。
海关验货是保障进出口贸易安全、顺利进行的重要环节。
通过严格的验货流程,可以有效防范假冒伪劣产品、非法走私等行为,保障国家利益和社会公共利益。
例行检验及成品确认检验控制程序(含流程图)
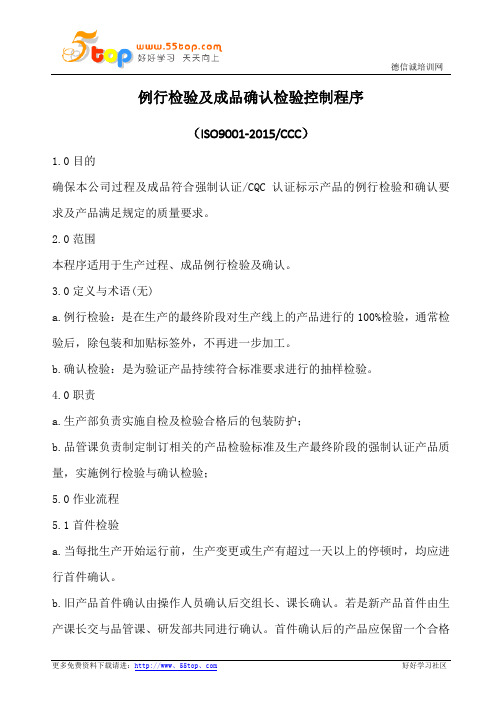
例行检验及成品确认检验控制程序(ISO9001-2015/CCC)1.0目的确保本公司过程及成品符合强制认证/CQC认证标示产品的例行检验和确认要求及产品满足规定的质量要求。
2.0范围本程序适用于生产过程、成品例行检验及确认。
3.0定义与术语(无)a.例行检验:是在生产的最终阶段对生产线上的产品进行的100%检验,通常检验后,除包装和加贴标签外,不再进一步加工。
b.确认检验:是为验证产品持续符合标准要求进行的抽样检验。
4.0职责a.生产部负责实施自检及检验合格后的包装防护;b.品管课负责制定制订相关的产品检验标准及生产最终阶段的强制认证产品质量,实施例行检验与确认检验;5.0作业流程5.1首件检验a.当每批生产开始运行前,生产变更或生产有超过一天以上的停顿时,均应进行首件确认。
b.旧产品首件确认由操作人员确认后交组长、课长确认。
若是新产品首件由生产课长交与品管课、研发部共同进行确认。
首件确认后的产品应保留一个合格品放在生产现场直到该班或该批生产完成时为止。
c.生产各课组长根据所生产品名、品号找出相应图纸资料详细核对,确认所有工作准备情况,记录于《首件检验表》。
5.2自检与过程检验a.生产过程中各工序作业人员完工后,必须进行自主检验,发现缺陷自行修复;自主检验合格后的产品,才能转入下道工序;下道工序若发现上道工序流下的产品有问题时应退回上道工序修复。
b.生产组长依据工程图纸,检验标准,结合抽检方法(一般是2H一次)和实际情况进行抽样检验,并填写相关记录报表做出判定结果。
c.判定合格:制程IPQC在《产品标识卡》上盖合格章,生产人员方可转交下一工序生产作业。
d.判定不合格:生产部人员按《不合格品管制程序》处理。
e.生产各组每月对各类不良进行记录,并定期汇总,作为分析和改进的依据。
f.生产各课要对出现的不合格问题进行分析并采取纠正预防措施。
5.3例行检验和最终检验a.例行检验是在生产的最终阶段由生产单位依照《强制认证产品质量要求》《强制认证产品的例行检验规程》对生产线上的产品进行的100%检验,并填写《例行检验报告》。
验货流程全攻略
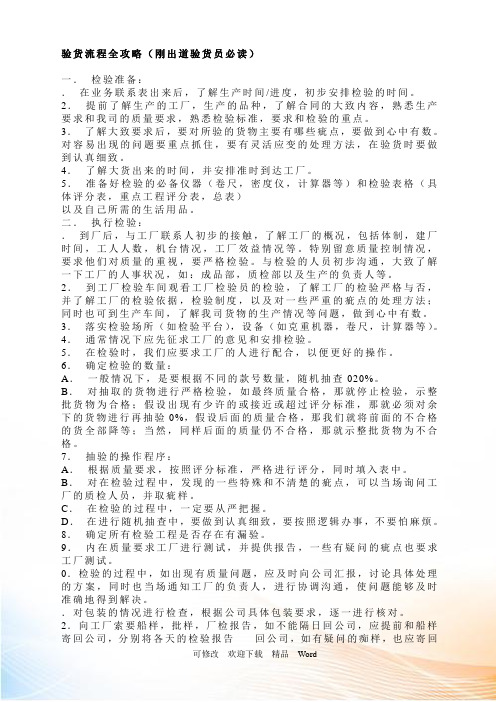
验货流程全攻略(刚出道验货员必读)一.检验准备:.在业务联系表出来后,了解生产时间/进度,初步安排检验的时间。
2.提前了解生产的工厂,生产的品种,了解合同的大致内容,熟悉生产要求和我司的质量要求,熟悉检验标准,要求和检验的重点。
3.了解大致要求后,要对所验的货物主要有哪些疵点,要做到心中有数。
对容易出现的问题要重点抓住,要有灵活应变的处理方法,在验货时要做到认真细致。
4.了解大货出来的时间,并安排准时到达工厂。
5.准备好检验的必备仪器(卷尺,密度仪,计算器等)和检验表格(具体评分表,重点工程评分表,总表)以及自己所需的生活用品。
二.执行检验:.到厂后,与工厂联系人初步的接触,了解工厂的概况,包括体制,建厂时间,工人人数,机台情况,工厂效益情况等。
特别留意质量控制情况,要求他们对质量的重视,要严格检验。
与检验的人员初步沟通,大致了解一下工厂的人事状况,如:成品部,质检部以及生产的负责人等。
2.到工厂检验车间观看工厂检验员的检验,了解工厂的检验严格与否,并了解工厂的检验依据,检验制度,以及对一些严重的疵点的处理方法;同时也可到生产车间,了解我司货物的生产情况等问题,做到心中有数。
3.落实检验场所(如检验平台),设备(如克重机器,卷尺,计算器等)。
4.通常情况下应先征求工厂的意见和安排检验。
5.在检验时,我们应要求工厂的人进行配合,以便更好的操作。
6.确定检验的数量:A.一般情况下,是要根据不同的款号数量,随机抽查020%。
B.对抽取的货物进行严格检验,如最终质量合格,那就停止检验,示整批货物为合格;假设出现有少许的或接近或超过评分标准,那就必须对余下的货物进行再抽验0%,假设后面的质量合格,那我们就将前面的不合格的货全部降等;当然,同样后面的质量仍不合格,那就示整批货物为不合格。
7.抽验的操作程序:A.根据质量要求,按照评分标准,严格进行评分,同时填入表中。
B.对在检验过程中,发现的一些特殊和不清楚的疵点,可以当场询问工厂的质检人员,并取疵样。
生产、计划、采购、物流、仓储、QA、QC流程图

扫描产品/记录车牌 /开始结束时间
多交货单可以 同时过帐
下载退货单 采集收货信息
读取交货单
采集方式:手输数量 /扫托盘码/扫桶码
是
否
否
一
致
是
收货
获取上架指引
记录上架信息
后 台 自 动 邮 件 通 知
收到邮件
确认上架信息
使之符合 实际上架
情况
上架
确认
人 工SAP处理 收货产生49凭证
下载转仓信息
需 要
PD A 业 务 功 能 概 况
工厂收货 外购收货 关企收货 套装收货 退货收货 转仓收货
品检 上架 确认
仓库
发货拣配 发货扫描 发货装车
转
盘
发货验货
储
点
收货-外购收货流程 输入采购单
填写供应商批次
内部批次可以为空, 自动生成 ; 供应商 批次,生产日期
收货-退 货收货流 程图
收货
后台自动邮件通知
输入转仓单 (物料凭证)
要 收 货
315
311
收货
①
获取上架指引 ② 确认上架信息
③
上架
使之符合实际 上架情况
确认 ④
发货-拣配流程图
输入交货单 选择拣配单下载
备货检查 拣配单完成确认
可扫描或 输入
输入物料凭证 备料检查
输入转仓信息 确认
发货-装 车扫描流 程图
输入拣配单
采集防窜货资料
转 储移 位 流 程 图
收到邮件
获取上架指引 确认上架信息
使之符合实际 上架情况
质检
上架
确认
收货-关 企收货流 程图
过程流程图[出货检验流程]
![过程流程图[出货检验流程]](https://img.taocdn.com/s3/m/2073f628bdd126fff705cc1755270722182e5957.png)
过程流程图[出货检验流程](1)首件检验:首件检验也称为“首检制”,长期实践经验证明,首检制是一项尽早发现问题、防止产品成批报废的有效措施。
通过首件检验,可以发现诸如工夹具严重磨损或安装定位错误、测量仪器精度变差、看错图纸、投料或配方错误等系统性原因存在,从而采取纠正或改进措施,以防止批次性不合格品发生通常在下列情况下应该进行首件检验:一,一批产品开始投产时;二,设备重新调整或工艺有重大变化时;三,轮班或操作工人变化时;四,毛坯种类或材料发生变化时首件检验一般采用“三检制”的办法,即操作工人实行自检,班组长或质量员进行复检,检验员进行专检。
首件检验后是否合格,最后应得到专职检验人员的认可,检验员对检验合格的首件产品,应打上规定的标记,并保持到本班或一批产品加工完了为止对大批大量生产的产品而言,“首件”并不限于一件,而是要检验一定数量的样品。
特别是以工装为主导影响因素(如冲压)的工序,首件检验更为重要,模具的定位精度必须反复校正。
为了使工装定位准确,一般采用定位精度公差预控法,即反复调整工装,使定位尺寸控制在1/2公差范围的预控线内。
这种预控符合正态分布的原理,美国开展无缺陷运动也是采用了这种方法。
在步步高工作期间,他们对IPQC的首件检查非常重视,毕竟国内从事AV家电生产的企业,工艺自动化程度低,主要依赖员工的操作控制。
因此,新品生产和转拉时的首件检查,能够避免物料、工艺等方面的许多质量问题,做到预防与控制结合。
(2)巡回检验巡回检验就是检验工人按一定的时间间隔和路线,依次到工作地或生产现场,用抽查的形式,检查刚加工出来的产品是否符合图纸、工艺或检验指导书中所规定的要求。
在大批大量生产时,巡回检验一般与使用工序控制图相结合,是对生产过程发生异常状态实行报警,防止成批出现废品的重要措施。
当巡回检验发现工序有问题时,应进行两项工作:一是寻找工序不正常的原因,并采取有效的纠正措施,以恢复其正常状态;二是对上次巡检后到本次巡检前所生产的产品,全部进行重检和筛选,以防不合格品流入下道工序(或用户)巡回检验是按生产过程的时间顺序进行的,因此有利于判断工序生产状态随时间过程而发生的变化,这对保证整批加工产品的质量是极为有利的。
04客户验货流程图
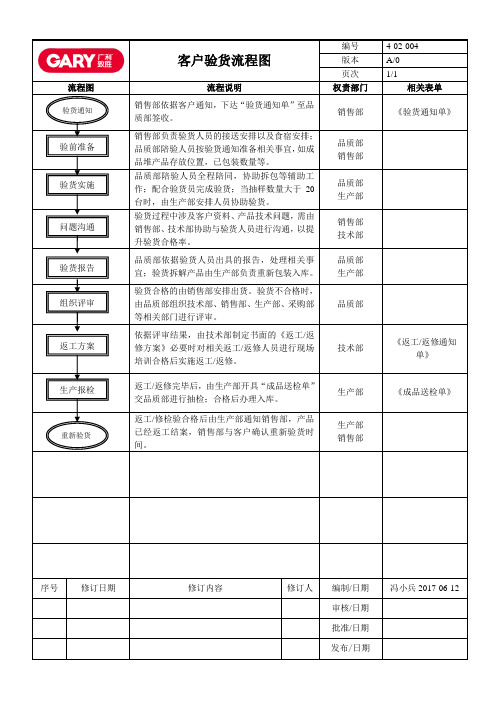
《返工/返修通知 单》
《成品送检单》
序号
修订日期
修订内容
修订人
编制/日期 审核/日期 批准/日期 发布/日期
冯小兵 2017-06-12
流程图
验货通知
验前准备 验货实施 问题沟通 验货报告 组织评审 返工方案 生产报检
重新验货
客户验货流程图
流程说明
销售部依据客户通知,下达“验货通知单”至品 质部签收。
销售部负责验货人员的接送安排以及食宿安排; 品质部陪验人员按验货通知准备相关事宜,如成 品堆产品存放位置,已包装数量等。 品质部陪验人员全程陪同,协助拆包等辅助工 作;配合验货员完成验货;当抽样数量大于 20 台时,由生产部安排人员协助验货。 验货过程中涉及客户资料、产品技术问题,需由 销售部、技术部协助与验货人员进行沟通,以提 升验货合格率。
品质部依据验货人员出具的报告,处理相关事 宜;验货拆解产品由生产部负责重新包装入库。
验货合格的由销售部安排出货。验货不合格时, 由品质部组织技术部、销售部、生产部、采购部 等相关部门进行评审。
依据评审结果,由技术部制定书面的《返工/返 修方案》必要时对相关返工/返修人员进行现场 培训合格后实施返工/返修。
编号 版本 页次 权责部门 销Байду номын сангаас部
品质部 销售部
品质部 生产部
销售部 技术部 品质部 生产部
品质部
技术部
返工/返修完毕后,由生产部开具“成品送检单” 交品质部进行抽检;合格后办理入库。
返工/修检验合格后由生产部通知销售部,产品 已经返工结案,销售部与客户确认重新验货时 间。
生产部
生产部 销售部
4-02-004 A/0 1/1