曲轴的受力情况分析及主要强化方式
曲轴滚压变形分析与滚压校直工艺研究

制变形过程时加大一定的过剩变形量以抵消它,故要选取适 当的滚压过盈 量。滚压加工后的金属表面由于发生了晶内及晶间的破坏,晶格产生 了畸
变, 故经受冷变形后 的金属及合金 , 其塑性随所受的变形程度 的增加而急剧 下降, 在极限情况下可达到接近于完全脆性 的状态。 另外, 由于晶格 畸变 , 出 现应力、 晶粒 的细化等, 工件表 面微观 凹凸不平烫光压平 , 表面粗糙度 明显 改善。 金属的抗力指标则随变形程度 的增加而有所提高, 从而使工件表面耐 磨性及疲 劳强度有明显改善。 2 、 曲轴滚压校直
1 、 氮 化
曲轴氮化包括 气体软氮化、 离 子氮化和盐浴氮化等 氮化能提高 曲 轴疲 劳强度 的2 0 %一 6 0 %, 适用于各类 曲轴 。
2 、 喷 丸
曲轴经喷丸处理后能提高疲劳强度的2 0 % - 4 0 %,但因喷丸时须保护轴
颈表 面 , 故采用较少。 3 、 圆角 与 轴 颈 同 时感 应 淬 火
该强化方式应用于球铁 曲轴时, 能提 高疲劳强度的2 0 %, 而应用于钢轴
时, 则 能提 高 1 0 0 %以上 , 故在 钢 轴 中应 用 比较 普遍 。 4 、 圆角 滚 压
由于国内只有少数厂家实现了 曲轴 圆角滚压强化工艺,且大多数采用 的相关工艺设备是国外引进的 , 故无具体数据。根据统计资料 : 球铁 曲轴经 圆角滚压 后寿命可提高8 0 %一 2 0 0 %,钢轴 经圆角滚 压后寿命可 提高7 0 %一
图1 曲轴 液 压 住 置 示 意 图
大而且受力复杂 , 并且承受交变负荷的冲击作用。同时 , 曲 轴 又是 高速旋转 件, 因此 , 要求 曲轴具有足够的刚度和强度 , 具有 良好的承受冲击载荷的能
力, 耐 磨 损 且润 滑 良好 。
滚压强化概述
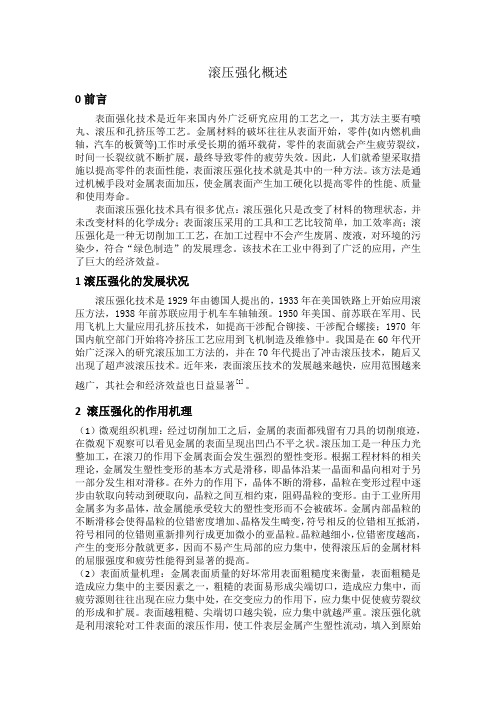
滚压强化概述0前言表面强化技术是近年来国内外广泛研究应用的工艺之一,其方法主要有喷丸、滚压和孔挤压等工艺。
金属材料的破坏往往从表面开始,零件(如内燃机曲轴,汽车的板簧等)工作时承受长期的循环载荷,零件的表面就会产生疲劳裂纹,时间一长裂纹就不断扩展,最终导致零件的疲劳失效。
因此,人们就希望采取措施以提高零件的表面性能,表面滚压强化技术就是其中的一种方法。
该方法是通过机械手段对金属表面加压,使金属表面产生加工硬化以提高零件的性能、质量和使用寿命。
表面滚压强化技术具有很多优点:滚压强化只是改变了材料的物理状态,并未改变材料的化学成分;表面滚压采用的工具和工艺比较简单,加工效率高;滚压强化是一种无切削加工工艺,在加工过程中不会产生废屑、废液,对环境的污染少,符合“绿色制造”的发展理念。
该技术在工业中得到了广泛的应用,产生了巨大的经济效益。
1滚压强化的发展状况滚压强化技术是1929年由德国人提出的,1933年在美国铁路上开始应用滚压方法,1938年前苏联应用于机车车轴轴颈。
1950年美国、前苏联在军用、民用飞机上大量应用孔挤压技术,如提高干涉配合铆接、干涉配合螺接;1970年国内航空部门开始将冷挤压工艺应用到飞机制造及维修中。
我国是在60年代开始广泛深入的研究滚压加工方法的,并在70年代提出了冲击滚压技术,随后又出现了超声波滚压技术。
近年来,表面滚压技术的发展越来越快,应用范围越来越广,其社会和经济效益也日益显著]1[。
2 滚压强化的作用机理(1)微观组织机理:经过切削加工之后,金属的表面都残留有刀具的切削痕迹,在微观下观察可以看见金属的表面呈现出凹凸不平之状。
滚压加工是一种压力光整加工,在滚刀的作用下金属表面会发生强烈的塑性变形。
根据工程材料的相关理论,金属发生塑性变形的基本方式是滑移,即晶体沿某一晶面和晶向相对于另一部分发生相对滑移。
在外力的作用下,晶体不断的滑移,晶粒在变形过程中逐步由软取向转动到硬取向,晶粒之间互相约束,阻碍晶粒的变形。
曲轴滚压力与疲劳强度分析

曲轴滚压力与疲劳强度分析作者:文/ 黄中顺蒲鹰邓玉婷来源:《时代汽车》 2020年第13期黄中顺蒲鹰邓玉婷桂林福达曲轴有限公司广西桂林市 541199摘要:曲轴是发动机的核心零部件,在发动机工作过程中它承受连杆传来的力,并将其转变为转矩通过曲轴输出并驱动发动机上其他附件工作。
曲轴受到旋转质量的离心力、周期变化的气体惯性力和往复惯性力的共同作用,使曲轴承受弯曲扭转载荷的作用。
因此要求曲轴有足够的强度和刚度,随着国内市场对小排量、增压发动机性能的要求不断提高,曲轴结构在轻量化的同时也要求具有较高的疲劳强度,而对强度影响最大的就是曲轴的强化方式及参数,因此,研究曲轴的滚压力与疲劳强度的关系是每个新型号曲轴开发过程中必不可少的一项工作。
关键词:曲轴滚压力疲劳强度Analysis of the Crankshaft Rolling Pressure and Fatigue StrengthHuang Zhongshun,Pu Ying,Deng YutingAbstract:The crankshaft is the core component of the engine. During the operation of the engine, it bears the force transmitted by the connecting rod and converts it into torque to output through the crankshaft and drive otheraccessories on the engine to work. The crankshaft is subjected to the centrifugal force of the rotating mass, the periodically changing gas inertia force and the reciprocating inertia force, so that the crank bearing is subjected to the bending and torsional load. Therefore, the crankshaft is required to have sufficient strength and rigidity. With the continuous improvement of the domestic market's requirements for small displacement and supercharged engine performance, the crankshaft structure is required to have high fatigue strength while being lightweight, which has the greatest impact on strength. It is the strengthening method and parameters of the crankshaft. Therefore, studying the relationship between the rolling pressure and fatigue strength of the crankshaft is an indispensable task in the development of each new type of crankshaft.Key words:crankshaft, rolling pressure, fatigue strength本文通过对我公司目前加工的一款小排量发动机曲轴采用不同滚压力进行试验,以验证滚压力对曲轴疲劳强度的影响,该款曲轴排量为1.0T,材料为球墨铸铁QT700-2。
发动机曲轴强度分析
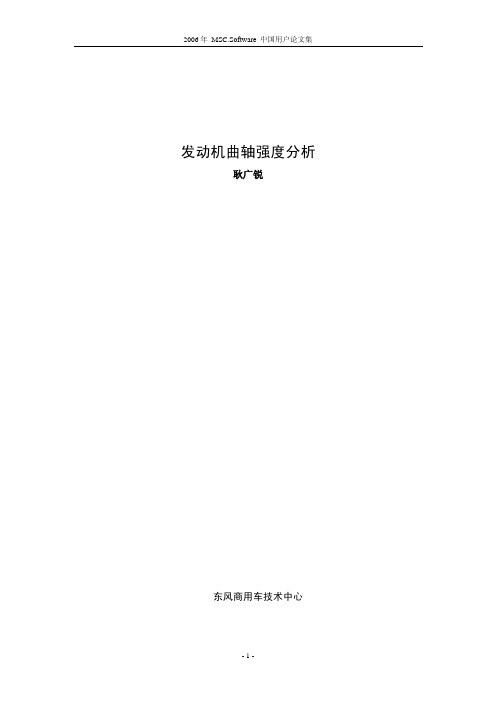
新方案一 2.21 2.35
新方案二 2.22 2.41
新方案三 1.95 2.18
4 分析结论
4.1 强度
从表 3 可以看出,压工况下新方案一曲轴的应力比现生产应力要稍高一些,最大增幅 (内圆角)为 18%(45Mpa),新方案二较新方案一曲柄销增大了 3mm(增大 3.6%),但外圆角应 力几乎没有改变,内圆角应力略有降低(8Mpa,降 2.8%),说明增加曲轴的曲柄销直径对降 低圆角的应力水平效果较小;新方案三与新方案一相比圆角半径减小 0.5mm(减小 9%),外 圆角应力增大 14.5%(42Mpa),内圆角应力增大 7.9%(23Mpa),说明曲轴内、外圆角半径对 圆角的应力水平影响显著,圆角的应力水平与圆角半径成反比。
nσ
=
σ
aka
(
σ −1 βεσ )
+ ϕσ σ
m
kσ =1.0。
β=1.3。
-5-
(1)
2006 年 MSC.Software 中国用户论文集
εσ=0.64
ϕσ
=
2σ −1 − 1.5σ −1 1.5σ −1
= 0.33
考虑到多缸发动机曲轴一般扭转振动以及动载荷对曲轴的冲击作用将增大曲轴应力。
因此,再引用动力强化系数 λd 和动荷系数 C 修正原有的安全系数 nσ :
4.2 安全系数
一般钢曲轴的安全系数大于 1.5 即可,从表 5 可以看出,新设计曲轴各方案的安全系 数均已达到曲轴设计所规定的许用范围之内,但略小于现生产。
5 参考文献
[1] MSC Nastran Quick Reference Guide[k]. [2] 陆际清,沈祖.汽车发动机设计[M]. 北京:清华大学出版社,1993.
曲轴的工作条件和要求

曲轴的工作条件和要求
曲轴是内燃机中的重要部件,主要用于转换活塞的往复运动为旋转运动,并通过连杆将动力传输到其他部件。
曲轴的工作条件和要求如下:
1. 强度要求:曲轴需要承受高压力和高转速的工作环境,因此需要具备足够的强度和硬度,以保证不会出现变形、断裂等现象。
2. 刚度要求:曲轴在工作过程中会受到很大的惯性力和振动力的作用,因此需要具备足够的刚度,以减小振动和避免共振现象的发生。
3. 平衡要求:由于曲轴在工作时会出现不平衡力矩,因此需要进行动平衡处理,以减小振动和噪音。
4. 表面质量要求:曲轴的表面需要具备一定的光洁度和平滑度,以减小摩擦损失和磨损,提高工作效率。
5. 耐磨性要求:曲轴经常处于高速旋转状态,容易与其他部件产生接触,因此需要具备良好的耐磨性,以延长使用寿命。
6. 工作温度要求:曲轴在工作过程中会受到高温环境的影响,因此需要具备良好的高温抗性和热稳定性。
总结来说,曲轴的工作条件和要求包括强度、刚度、平衡、表
面质量、耐磨性和工作温度等方面,以保证其正常运转和延长使用寿命。
曲轴圆角滚压强化方式的基本原理

曲轴圆角滚压强化方式的基本原理
曲轴的圆角部位具有特殊性,所以很容易产生疲劳破坏,所以除了对圆角进行淬火外,我们还要采取另外一种强化方式-圆角滚压。
曲轴在发动机工作的过程中,会受到弯曲、扭转、拉压等交变应力的作用。
曲轴的圆角过渡处在曲轴中是相当薄弱的部位,尤其是连杆轴颈和主轴颈的过渡处,在生产过程中经过磨削加工后留下的刀痕处是最脆弱的地方,因此,我们要通过圆角滚压来增强圆角的强度。
图4.3.1-1曲轴圆角区域的显微硬度
曲轴的圆角滚压强化方法就是指在滚轮的压力作用下,在曲轴的连杆轴颈和主轴颈的过渡圆角处,形成一条滚压塑形变形带来达到强化圆角的效果的一种强化方式。
圆角滚压强化方法是提高曲轴的疲劳强度最行之有效的手段之一,它是实现曲轴生产过程中“以铁代钢”的关键工艺环节。
据统计资料显示,球墨铸铁曲轴材料的曲轴经过圆角滚压处理后,它的寿命可以提高百分之八十到百分之二百,钢制材料的曲轴经过圆角滚压处理后,它的寿命可以提高百分之七十到百分之一百五十。
由于圆角滚压强化工艺对生产技术要求较高,因此国内能实现曲轴圆角滚压工艺的厂家不多,而且采用的相关生产设备基本上都是从国外引进的,针对这一现象,我们进行了多项试验,以期设计出适合朝柴曲轴生产的方法。
大功率曲轴跳动超差的原因剖析及其解决措施
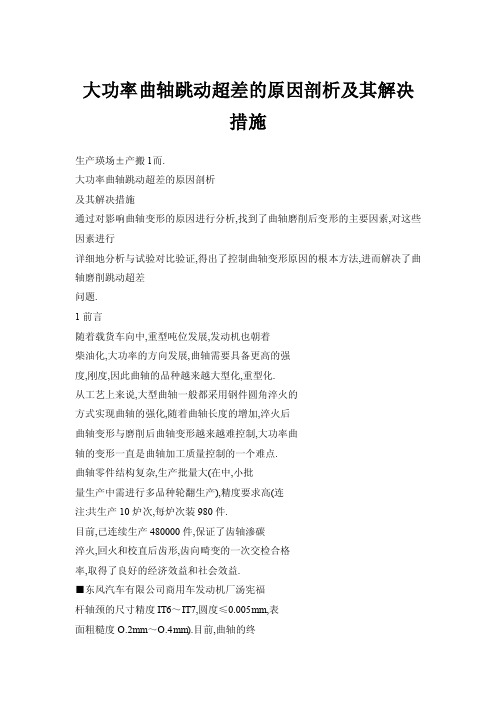
大功率曲轴跳动超差的原因剖析及其解决措施生产瑛场±产搬l而.大功率曲轴跳动超差的原因剖析及其解决措施通过对影响曲轴变形的原因进行分析,找到了曲轴磨削后变形的主要因素,对这些因素进行详细地分析与试验对比验证,得出了控制曲轴变形原因的根本方法,进而解决了曲轴磨削跳动超差问题.1前言随着载货车向中,重型吨位发展,发动机也朝着柴油化,大功率的方向发展,曲轴需要具备更高的强度,刚度,因此曲轴的品种越来越大型化,重型化.从工艺上来说,大型曲轴一般都采用钢件圆角淬火的方式实现曲轴的强化,随着曲轴长度的增加,淬火后曲轴变形与磨削后曲轴变形越来越难控制,大功率曲轴的变形一直是曲轴加工质量控制的一个难点.曲轴零件结构复杂,生产批量大(在中,小批量生产中需进行多品种轮翻生产),精度要求高(连注:共生产10炉次,每炉次装980件.目前,已连续生产480000件,保证了齿轴渗碳淬火,回火和校直后齿形,齿向畸变的一次交检合格率,取得了良好的经济效益和社会效益.■东风汽车有限公司商用车发动机厂汤宪福杆轴颈的尺寸精度IT6~IT7,圆度≤0.005mm,表面粗糙度O.2mm~O.4mm).目前,曲轴的终/]nz仍普遍采用磨削工艺,为满足曲轴日益提高的加工要求,对曲轴磨床提出了很高的要求,现代曲轴磨床除了要有很高的静态,动态刚度和很高的N-r-精度外,还要求有很高的磨削效率和更多的柔性.基于此,目前连杆轴颈磨床的磨削工艺已越来越多地使用跟踪磨削工艺,决定了目前的磨削工艺只能是先磨全部的主轴轴颈再磨全部的连杆轴颈,这也在无形中增加曲轴变形的控制难度.由于曲轴在装配过程中,与轴瓦间的配合有较高要齿项不接触工装装炉圈5改进后装炉方式圈2010年第7期汽车工艺与材料AT&M129.生导琐场求,故对主轴轴颈跳动要求较高,对六缸大功率发动机而言,特别要控制3,4,5主轴轴颈跳动,以免在发动机运行时发生曲轴的"抱瓦"或"拉瓦"等质量事故.我厂采用的加工工艺为主轴轴颈及连杆轴颈圆角淬火一低温回火一修整中心孔一磨全部的主轴轴颈一磨全部的连杆轴颈,且在加工过程中不允许对曲轴进行校直.在我厂某一大功率曲轴的生产调试过程中,磨削后出现第3,4,5主轴轴颈跳动超差,实际情况第3,5t轴轴颈跳动平均值为0.082mm,最大为0.13mm,偏于公差上限,第4主轴轴颈跳动平均值为0.1mm,最大为0.14mm,通过统计废品率达到了10%~35%,跳动超差直接导致曲轴报废,因此解决曲轴磨削工序变形超差的质量问题势在必行.2大功率曲轴磨削跳动超差的原因分析2.1当瞬时应力大于材料的弹性极限时,产生了曲轴的不均匀塑性变形曲轴在磨削时除了所受的磨削力外,还存在淬火时工件内部产生的残余应力,虽然经过回火工序,该残余应力得到释放,但不可能完全释放.还有在磨削时因偏磨产生的组织应力.当存在磨削烧伤时,因组织转变而形成组织应力.在磨削主轴轴颈和连杆轴颈时,因有中心架抵消磨削力,因此曲轴所受的瞬时力大于材料弹性极限的可能性很小,曲轴在磨NH,1-所受的磨削力是不可能消除的,所以这种情况并不是产生曲轴变形的主要原因.通过多次调整磨削参数,磨削方式及磨削顺序,都无法从根本上解决磨削后曲轴的变形超差问题,这样间接证明了磨削工序并不是曲轴变形的主要原因. 2_2磨削过程中释放的残余应力导致曲轴变形曲轴内部的残余应力,主要是在淬火过程中因热胀冷缩的体积变化,以及因相变时新旧两相比容差异而发生的体积变化形成的.该残余应力的大小决定了曲轴淬火变形的大小:该残余应力经过回火后部分得到释放,但不可能完全释放.因此,在磨削时剩余残余应力释放导致曲轴变形.2.3轴颈内外两侧受力不均.导致曲轴变形淬火后曲轴表面存在很大的压应力,该压应力从表面向内部递减,磨削时如果偏磨,将造成曲轴表面压应力的变化,在相对方向不均衡的情况下,导致曲轴变形.为了验证残余应力及偏磨对曲轴变形的影响,做了如下试验.(1)在前期加工的曲轴中挑取淬火后第4主轴轴颈跳动在O9~10mm之间的曲轴3根,这3根曲轴淬火前全部是合格曲轴,对这3根曲轴的相位进行测量,测量结果见表1.相位全部因淬火变形而发生变化,该3根曲轴中心孔修正后,第4主轴轴颈跳动在0.6~0.8mm之间;磨削后第3,4,55轴轴颈跳动全部超差,第4主轴轴颈跳动全部为0.16mm,第3,5主轴轴颈跳动为O.13~0.15mm.由此可见,淬火变形导致连杆轴颈相位变化,后续磨削时产生偏磨, 曲轴跳动超差:淬火后内应力过大,导致后续磨削时内应力释放,曲轴跳动超差.(2)加工3根内铣相位为15'的曲轴,相位超差3.~5..淬火后曲轴变形控制在O.6mm以内:中,CqL 修正后,第4主轴轴颈跳动控制在O.35mm以内:磨削后第4主轴轴颈跳动为0.15~0.18mm,3根曲轴跳动全部超差.30f汽车T艺与材料AT&M2010年第7期.生亭礤锚经过以上分析发现,曲轴磨削后变形超差的主要原因如下.(7)淬火后曲轴内应力过大,导致曲轴变形超差.虽经回火后应力得到一定的释放,但仍有较大的残余应力带到了磨削工序中.在曲轴磨削过程中,残余应力持续释放而导致跳动超差.(2)因淬火变形导致曲轴相位发生变化,致使磨削时连杆轴颈发生偏磨,导致曲轴因受力不均产生变形.通过以下方法可解决磨削后的曲轴变形.(1)控制淬火后的曲轴变形.(2)控制曲轴的内应力.(3)降低曲轴的变形量,减少曲轴偏磨.(4)通过更改磨削工艺,控制曲轴内应力的释放,避免曲轴变形超差.3曲轴淬火变形,内应力过大的原因分析及其解决措施3.1影响曲轴变形的原因分析(1)由于热胀冷缩和组织转变,发生了体积的变化,导致材料内部产生应力.当瞬时应力大于材料的弹性极限时,产生了曲轴的不均匀塑性变形;当轴颈淬火层深不均匀和轴颈侧面的淬火高度过高时,特别是连杆轴颈与第4主轴轴颈层深不均匀和轴颈侧面的淬火高度过高(连杆轴颈内外结构不一样,直接导致淬火层深不均匀和侧面淬火高度过高对整个曲轴的变形影响最大),轴颈的塑性变形不一样,引起曲轴变形.(2)曲轴在加热和冷却过程中,因为热胀冷缩和组织转变而引起曲轴整体长度变化,此时要求曲轴可以自由伸缩,尾架顶紧力不能太大,如果太大则曲轴将会发生塑性变形.(3)毛坯内应力和机械加工应力的存在,对淬火过程中的瞬时应力有叠加作用,导致曲轴产生不均匀的塑性变形.(4)盐轴在淬火过程中,感应器对曲轴的压力不能太大,力度调整到感应器在淬火过程中正好不脱离曲轴,特别是在曲柄的上,下支点,感应器对曲轴的压力不能差别太大,否则直接引起曲轴的变形.3.2表面感应淬火内应力形成的一般规律零件在加热和冷却过程中,将发生热胀冷缩的体积变化,以及因相变时新旧两相比容差异而发生体积变化.热传导过程中由于零件的表面比心部先加热或冷却,在截面上各部分之间存在温差,致使零件表面和心部不能在同--8,1-期发生上述的体积变化,各部分体积变化相互牵制而产生内应力.加热或冷却速度越大,在零件截面上的温差增大,形成的内应力便越大.热处理过程中所形成的内应力可称为瞬时应力;热处理后在零件内存在的应力则称为残余应力.瞬时应力随着温度的变化而改变其应力大小和方向.如果瞬时应力始终小于材料的弹性极限时,则引起瞬时应力的原因消失后,瞬时应力随即消失;但若瞬时应力大于材料的弹性极限而弓1起不均匀塑性变形,那么当造成应力的原因消失后而保留在零件之中的内应力即为残余应力.根据内应力形成的原因不同,又可分为由温差引起的胀缩不均匀而产生的热应力和由相变不同期及组织不均匀产生的组织应力.3.3解决层深均匀性和侧面淬火高度的措施分析该大功率曲轴生产线所用淬火机是进口法国的EFD淬火机,进口感应器不但价格昂贵,而且热效率极低,因此有必要对进口感应器国产化.在使用进口感应器调试过程中,层深均匀性和淬火后曲轴变形均未得到解决.根据切片结果,对感应器有效圈进行了改进,层深均匀性得到了一定程度的提高,但是侧面淬火深度和高度,仍有一定的缺陷,因此淬火后曲轴变形超差的质量问题,仍未得到彻底解决.通过两轮国产化感应器中间试验,根据前期切片结果,又对感应器有效圈进行了优化试验,层深均匀性和侧面淬火高度均得到彻底解决.为了获得均匀的有效硬化层深度,在感应加热周期内,圆角区要比圆柱区提供更多的能量,以弥补热传导损失的热量.2o10年第7期汽车工艺与材料AT&Ml31.生产碗场由传热学可知,沿某方向通过微区面积ds=dyXdz的热流量是:dqx=/1X(dT/dX)XdsXdt(1)式中,为材料的导热系数;d7-/dX为沿方向该点的温度梯度:df为微量时间.由上式可知,热传导损失的热量与导热系数,温度梯度,导热面积和加热时间成正比.同一轴颈加热时,圆角区和圆柱区的导热系数和加热时间是相同的.导热面积可以分别计算出来,但是两处的温度梯度不同,而且随加热时间而变,要精确计算温度梯度对热流量的影响是十分困难的.定性分析和实践表明,感应加热时,圆角区的升温快,因为沿加热层深度方向和加热区的边缘温度梯度大,热流量损失大,相反则圆柱区的热量损失小.切片试样及切片结果,正好与分析的状况相同.由于有效圈几何形状设计不合理且焊点较多,导致感应器效率低,为了满足层深的工艺要求,必须增加加热时间,加热时间过长导致淬火后变形量过大而造成曲轴报废,此期间曲轴淬火后跳动超差的废品率达到了60%~70%.具体淬火参数见表2.进口感应器有效圈结构见图1.轴颈功率/kw加热时I'~/s冷却时l'~/s备注王袖轴颈2—6180/160/14016/22/2216/16/163组参连许轴颈1~6120~180璃零龠蘑I王轴轴颈318022||蔼∞王轴轴颈1||.180一16薯l虽然影响圆角区温度和圆柱区温度的因素除了热传导之外,还有表面热辐射损失,但是由于加热时间短(12~14s左右),热损失之差不大于3%,可以忽略不计.因此,感应器的设计就是要使圆角处得到足够的热量.(1)进口感应器优,缺点分析进口感应器采用的是有效圈圆弧段与曲轴轴颈表面成45.的结构形式,形状采用的是异型结构(见图1).该感应器有效圈圆弧段设计完全基于使圆角处得到足够的热量,有效圈圆弧段磁场直接作用在圆角和侧面直接加热,而轴颈处硅钢片数量太少,因圆角处的热量损失最大,如果轴颈处热量仅靠圆角处的热量传递,在短时间内不能满足轴颈层深的需要,这是造成感应器效率低的主要原因.该感应器有效圈不是一个整体,由很多部分焊接而成,焊点很多,功率损失大,这是造成感应器效率低的次要原因.此种感应器有效圈圆弧段设计极易出现马鞍形淬火层深,圆角处与轴颈处层深差别太大.如果欲满足轴颈层深的工艺要求,必须增加加热时间,当时的加热时间为22~24S,加热时间越长,曲轴变形越大.采用这种结构形式,能很好地保证侧面淬火高度.查阅前期曲轴的图1进口感应器有效圈结构(2)第一轮感应器优,缺点分析第一轮感应器采用的是有效圈圆弧段与曲轴轴颈表面成0.的结构形式,有效圈是由1OmmX1Omm的标;隹矩形铜管制作而成(见图2).该感应器有效圈圆弧段磁场直接作用在侧面和轴颈上,直接对侧面和轴颈加热,而圆角处大部分热量是由轴颈和侧面传32J汽车T艺与材料AT&M2010年第7期生产碗场.±搬汤导而来,再加上轴颈处还有部分硅钢片,且该感应器有效圈圆弧段是一整根铜管弯制而成,没有焊点,从而使感应器效率得到极大提高.因此种有效圈圆弧段设计极易出现侧面深度太深,圆角处深度太浅,层深不均匀,故引起曲轴变形.由于感应器热效率的提高,淬火功率和淬火时间都有了适当的缩短,曲轴变形与进口感应器相比,下降了很多,但是仍旧存在40%的废品,因此进~步对感应器有效圈结构进行改进势在必行,具体淬火参数见表3.第一轮感应器有效圈结构见图2.轴颈功率/kW加热时1~1/s冷却时I'~1/s备注图2第一轮感应器有效圈结构(3)第二轮改进感应器优,缺点分析第二轮改进感应器采用的是前有效圈左侧圆弧段与曲轴轴颈表面成0.,前有效圈右侧圆弧段与曲轴轴颈表面成45.,后有效圈左侧圆弧段与曲轴轴颈表面成45.,后有效圈右侧圆弧段与曲轴轴颈表面成0.的结构形式,有效圈是由6mm×12mm的异形铜管制作而成,见图3.该感应器有效圈圆弧段磁场--N直接作用在圆角和侧面上,直接对侧面和圆角加热i而另一侧有效圈圆弧段磁场直接作用在侧面和轴颈上,对轴颈与侧面加热i再加上轴颈处还有部分硅钢片,且该感应器有效圈圆弧段是一整根异形铜管弯制而成,没有焊点.f!t~IL,该感应器效率很高.该感应器很好地保证了侧面淬火高度(侧面淬火高度工艺要求为6min).前有效圈剖面图后有效圈剖面图图3第二轮改进感应器有效圈结构2o1o年第7期汽车I艺与材料AT&Mf33生产硬场该感应器综合了进口感应器和第一轮感应器所有优点,同时避免了以上两种感应器的缺点,感应器的效率和稳定性都有了很大的提高,加热功率和加热时间又在第一轮感应器的基础上进行了缩短,切片结果显示,层深均匀性及侧面淬火高度全部优于前两轮感应器切片结果,具体淬火参数见表4,淬火层深切片数据见表5.轴颈功率/kW加热时间/s冷却时I'~1/s备注轴颈左罢淬右星淬轴曩火3.4毛坯内应力的控制方法(1)在前期生产过程中,毛坯厂为了节省节拍时间,缩短了曲轴的正火时间,因此为了降低曲轴毛坯的内部应力,必须保证正火炉温的均匀性和正火的时间,以保证内部组织的均匀性,避免产生内应力. (2)在目前国内的锻造水平下,如dC11曲轴毛坯.国内很难保证一次锻造成形,锻造后很多地方不能满足毛坯图纸的工艺要求.为了降低废品率,毛坯厂对不能满足工艺要求的部位(如充不满,有凹陷等)进行堆焊,而堆焊后又没有按照正规的热处理工艺进行去应力退火,因此为了消除堆焊产生的内部应力,对毛坯厂提出了以下2点要求.a.尽量避免对毛坯进行堆焊.b.对部分必须堆焊的毛坯,按正规热处理工艺进行去应力退火.3.5尾架顶紧力与感应器配重的调整(1)为了保证曲轴在淬火过程中的自由伸缩,尾架项紧力应尽可能小,经过2轮工艺试验,尾架项紧力由2X10Pa降低为O5X1OPa,益轴淬火后第4主轴轴颈跳动量平均降低O.18mm.(2)为了防止曲轴在淬火过程中产生塑性变形,必须尽量降低感应器对曲轴的压力,特别是在曲柄上,下支点的压力,如果曲柄上,下支点的压力差太大,则外力叠加后导致曲轴产生塑性变形.3.6淬火工序改进前,后数据对比分析在该曲轴前期投产过程中,淬火后曲轴变形过大一直是曲轴生产线质量控制的一个难点,整条曲轴生产线因为淬火后曲轴变形过大而无法顺利生产.曲轴生产线的淬火工序废品率一直居高不下,废品率达到了40%之多(回火后第4主轴轴颈跳动工艺要求为0.8 mm),回火后国产毛坯的第4主轴轴颈跳动平均在O.79mm.为了挽救曲轴,部分跳动超差的曲轴不得不继续下流,靠磨床来挽救,这不但造成了对磨床的损害,而且造成人力,物力的极大浪费.改进前,国34I汽车工艺与材料AT&M2010年第7期.生产琐扬产毛坯回火后曲轴第4主轴轴颈跳动数据见表6.两轮的国产化感应器中间试验,对感应器有效圈结构进行了改进,调整了尾架项紧压力和感应器压力,有效地控制了毛坯内应力的产生.目前,淬火后曲轴变形已基本得到很好地控制,淬火后国产毛坯的第4主轴轴颈跳动平均在0.28mm左右,回火后基本能控制在0.22mm左右,废品率控制在1%以内(淬火后第4主轴轴颈跳动工艺要求为08mm,回火后第4主轴轴颈跳动工艺要求为O.6mm),很好地满足了后续加工工艺的要求.改进后国产毛坯淬火,回火后曲轴第4主轴颈跳动数据见表7.4减少偏磨,避免曲轴因表面应力分布不均而产生变形在磨削主轴轴颈时,以顶尖孑L为基;隹,要想避免曲轴产生偏磨,必须控制曲轴淬火的变形.根据前面零件号淬火回火的分析可知,曲轴在淬火时因应力的作用,变形不可避免.特别对大功率曲轴而言,目前需要解决的是尽量降低曲轴的变形量,通过修正中心孔来降低轴颈对顶尖的跳动,尽而减少曲轴的偏磨,避免曲轴因表面应力分布不均而产生变形.目前,我厂曲轴中心孔修正采用的方法是以第2,6主轴轴颈中心轴线为基准,设备修正后的中心孔中心连线与第2,6主轴轴颈中心轴线理论上应重合, 也就是说,修正后的中心孔反映第2,6主轴轴颈中心轴线.从目前现场加工的曲轴来看,对后续减少偏磨量的效果明显,修正效果很好.该修正方法仅适合于淬火后变形规则的曲轴,如果淬火后出现"S"曲轴,该修正方法对磨削将产生不利影响.5更改磨削工艺,控制曲轴内应力的释放,避免曲轴变形超差为了将曲轴内部应力进行释放,可以先对曲轴主轴轴颈进行预磨(必须保证轴颈圆度),然后再磨削全部连杆轴颈,这样可以提前将曲轴内部应力进行释2010年第7期汽车T艺与材料A T&M『35生产碗琶放,最后再精磨全部主轴轴颈,这种磨削方式可以在保证曲轴质量的同时,避免曲轴变形超差.采用这种方法的前提是必须新增磨床或改为双砂轮磨床,我厂该曲轴线已不可能采用该方式.后期再建新的生产线时,可以提前考虑采用这种磨削方式或采用双砂轮磨床,以避免曲轴因前序内应力过大而产生曲轴变形超差.6磨削工序改进前后效果对比验证改进前,因淬火后曲轴内应力较大,曲轴变形过大,磨削后因内应力释放,一直存在着磨削工序跳动超差的质量问题(工艺要求第2,3,5,6主轴轴颈跳动为0.1mm,第4主轴轴颈跳动为0.13mm).实际情况第3,5主轴轴颈跳动平均值为0082mm,最大为0.013mm,第4主轴轴颈跳动平均值为01mm,最大为O.14mm.通过对多批曲轴分批进行统计,磨削工序废品率达到了10%~35%之多,改进前磨削工序后曲轴第3,4,5主轴轴颈跳动数据见表8.零件号第3主轴颈第4主轴颈第5A.轴颈通过对感应器有效圈的改进设计及毛坯应力的控制,对尾架项紧力和感应器配重调整,解决了曲轴淬火变形,降低了曲轴的内应力,进而彻底解决了磨削后曲轴变形超差.通过对该工序160件曲轴进行跟踪检测,结果没有一根曲轴磨削后跳动出现超差,该工序因跳动超差的废品率降为零,第3主轴轴颈跳动平均值为0044mm,第5主轴轴颈跳动平均值为0.045mm,第4主轴轴颈跳动平均值为0.047mm,改进后磨削工序后曲轴第3,4,5i轴轴颈跳动数据详见表9.零件号第3主轴颈第4主轴颈第5主轴颈7G00087GOOlO7G00057Go0237C-00227G0127G0o067G00147G00177G0O16002…q∞|薯0:03&077结束语欢迎订购EEC指令(中英文对照版)0为了满足目前我国汽车行业对国外汽车法规了解和掌握的迫切需要,国家汽车质量监督检验中心(长春)与莱茵技术(上海)有限公司北京办事处合作组织汽车行业专业人士翻译了最新EEC指令,并委托《汽车文摘))杂志编辑出版.全套,丑EC指令共计58本,并附光盘一张,为中英文逐页对照形式,便于使用.黪.该EEC指令由《汽车文摘》杂志编辑部负责向汽车行业各企业推广销售,价格为7500~L/套,欢迎各企业来电咨询嗡受一联系人:杜女士电话:0431:85789859传真:0431:85789810E—mail:**************** I36f汽车212艺与材料AT&M2010年第7期∞∞∞O.OOOOO^U^OO^嘶∞∞叭∞O0OOOOOO0。
曲轴吊运、装夹变形分析及措施
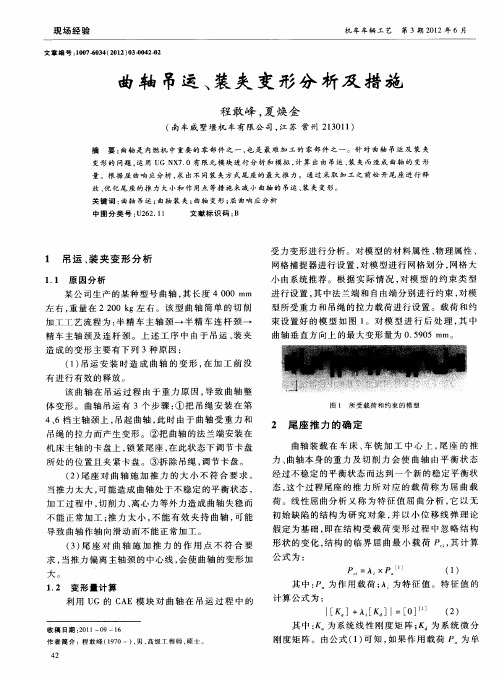
束设 置好 的模 型 如 图 1 。对 模 型 进 行 后 处 理 , 中 其
曲轴 垂 直 方 向上 的 最 大 变 形 量 为 0 5 0 . 9 5mm。
1 吊运 、 夹 变 形 分 析 装
1 1 原 因分 析 .
受 力变形 进行 分析 。对模 型 的材料属 性 、 物理属 性 、 网格捕 捉器进 行设 置 , 对模 型 进行 网格划 分 , 网格 大
小 由系统推荐 。根 据 实 际情 况 , 对模 型 的约束 类 型
进 行设 置 , 中法 兰端 和 自由端分别 进行 约束 , 其 对模
顶 紧后 , 不拆 除 吊绳 , 吊绳 在 曲轴 上 呈悬 浮 状 态 , 再
在 第 4档 主轴 颈 上 支 撑 托 架 , 不是 中心 架 。 因 为 而
曲轴 变形 能在 轴 向方 向上 进 行 释放 , 放 后 再 顶 紧 释
尾 座顶 尖 。
优 化前 采用 一夹一 顶 , 尾座推 力 为 1 0 根 25 0N,
下 面根据 此 2种 装 夹 状 态 来 求 曲 轴 的 屈 曲 临界 载
荷 , 就是 尾座 的最 大理论 推 力 。 也
小 为 40 1N。 因此 , 4 此种 装 夹方 式在 实际生 产 中是 不适 合 的。
没 有托架 时 一 样 , 径 向最 大 的变 形 量 为0 0 6 9 其 .7 5
mm。可见 中心托 架不 但能 提高 曲轴 的刚性 , 而且 能
减 轻尾 座对 曲轴施 加偏 心力 的影 响 。
0 1m 之 内 。 . m
曲轴变力圆角滚压强化及变形的规律研究的开题报告

曲轴变力圆角滚压强化及变形的规律研究的开题报告一、研究背景曲轴是汽车发动机的重要部件之一,其承受着高频、大幅度和复杂的载荷,尤其是在高转速和高扭矩时更容易出现断裂、疲劳和变形等问题。
为了提高曲轴的耐久性和寿命,曲轴的加工工艺和材料技术得到不断的研究和改进。
其中,强化技术是一个有效的手段,可以通过增强材料的内部结构和表面硬度来提高曲轴的抗疲劳性能和扭转刚度,从而减少变形和裂纹的发生。
目前,曲轴强化技术主要有化学沉积、气氛渗碳、等离子喷涂、激光表面处理、磁场强化和滚压等方法。
滚压技术是一种具有广泛应用前景的曲轴强化方法,它可以在曲轴表面形成一层厚度较小但具有高强度和高韧性的改性层,能够有效地提高曲轴的表面硬度和强度,减少表面裂纹和疲劳损伤。
在滚压强化过程中,圆角处是一个特殊的表面形状,其直接受到滚压变形的影响,容易产生塑性变形和残余应力等不利因素。
因此,如何探究曲轴变力圆角滚压强化的变形规律及其对曲轴性能的影响,对于提高曲轴加工质量和性能有着重要意义。
二、研究目的和意义本研究旨在通过实验和数值模拟方法,探究曲轴变力圆角滚压强化的变形规律和影响因素,包括圆角半径、滚压力和滚压速度等方面。
具体目标如下:1.建立曲轴变力圆角滚压强化的数值模拟模型,分析曲轴滚压过程中圆角处的应力和变形规律。
2.设计曲轴滚压实验,测量曲轴在不同滚压条件下的表面形貌、硬度和残余应力等性能指标。
3.通过实验和模拟相结合的方法,分析不同滚压参数对曲轴滚压强化的影响,并探究圆角半径、滚压力和滚压速度等因素的优化策略。
4.对实验和模拟结果进行对比和分析,总结曲轴变力圆角滚压强化的变形规律和影响因素,并为曲轴加工工艺和强化技术的进一步研究提供理论支持和实验基础。
三、研究内容和方法本研究包括以下几个方面的内容:1.曲轴变力圆角滚压强化的理论分析,包括曲轴滚压过程中的应力分布、变形规律、塑性变形和残余应力等基本理论问题。
2.曲轴滚压强化的数值模拟分析,采用有限元软件建立曲轴模型,模拟曲轴滚压过程中的应力变化、变形分布和残余应力等性能。
曲轴初步分析

曲轴初步分析(1)重量检查:通过PRO/E软件本身自带一些分析计算功能,比如表面积、体积、质量、转动惯量、中心坐标、简单的运动分析、简单的CAE分析、工艺检查等等多种有用的功能,这些功能在我们设计工程师的工作中增加了很多便利,能够使我们在设计工作时对所设计零件的状态信息很方便的获得,从而少走很多弯路。
现在执行质量分析命令,得到一系列和质量有关的信息见图2.6。
从中可以看出曲轴在X、Y轴质心坐标都已经小于0.0021了,因此整体来说曲轴质心分布是比较理想的,曲轴的静平衡达到设计要求。
(2)平衡分析1)首先对曲柄连杆机构在工作时的受力状况进行简单的描述。
(a)惯性力:对于曲拐惯性力的分解见图2.7。
2)根据以上理论,对曲轴的平衡率进行计算:首先进行曲拐分割分析,主要是分析曲轴单个曲拐的平衡率,根据AVL资料中,对于小型发动机曲轴单拐平衡率(连杆大头换算当量质量在曲柄销上)控制在不低于60%即可。
切割方法是将曲拐分割成曲拐、平衡块等部分,分别在PRO/E中进行质量属性测量。
测量时的坐标系方向:X向为沿轴向指向前,Y轴为沿曲拐法向指向外,Z轴为沿竖直方向指向第1曲拐向上。
把测得结果根据测量的结果,分别计算各个曲拐的平衡率。
因为本机设计为8平衡块对称结构,因此可以在静平衡计算中,采取简化到曲拐的方法,可以节省数模准备和计算的时间,对计算的精度没有任何影响。
从曲轴平衡分析表中可以看出第一曲拐含连杆大头在内平衡率在75.71%;第二曲拐含连杆大头在内平衡率在75.83%;第三曲拐含连杆大头在内平衡率在75.83%;第四曲拐含连杆大头在内平衡率75.71%。
根据AVL公司的推荐,平衡率达到60%以上已经满足设计要求了。
3)对曲轴进行动平衡计算:(a)连杆当量回转质量的确定,根据连杆的3维数模,可以用PRO/E软件测量出连杆的总重量、质心位置,通过根据质量分解计算出连杆大头的等效回转质量m2=0.22500kg。
【维修课堂】发动机曲轴弯扭原因分析及校正方法
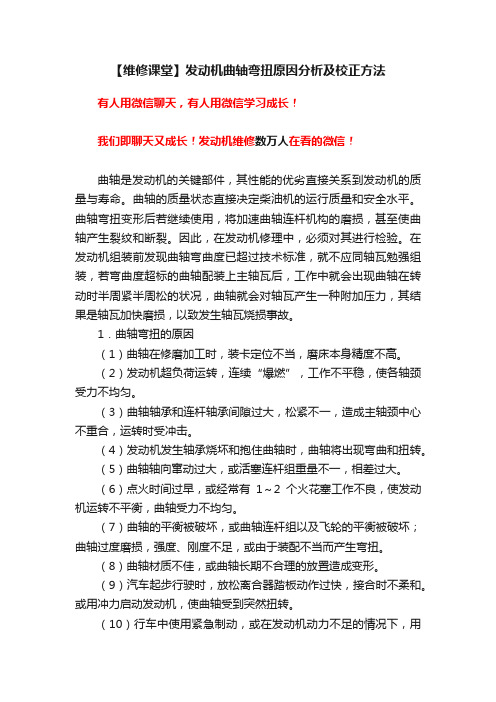
【维修课堂】发动机曲轴弯扭原因分析及校正方法有人用微信聊天,有人用微信学习成长!我们即聊天又成长!发动机维修数万人在看的微信!曲轴是发动机的关键部件,其性能的优劣直接关系到发动机的质量与寿命。
曲轴的质量状态直接决定柴油机的运行质量和安全水平。
曲轴弯扭变形后若继续使用,将加速曲轴连杆机构的磨损,甚至使曲轴产生裂纹和断裂。
因此,在发动机修理中,必须对其进行检验。
在发动机组装前发现曲轴弯曲度已超过技术标准,就不应同轴瓦勉强组装,若弯曲度超标的曲轴配装上主轴瓦后,工作中就会出现曲轴在转动时半周紧半周松的状况,曲轴就会对轴瓦产生一种附加压力,其结果是轴瓦加快磨损,以致发生轴瓦烧损事故。
1.曲轴弯扭的原因(1)曲轴在修磨加工时,装卡定位不当,磨床本身精度不高。
(2)发动机超负荷运转,连续“爆燃”,工作不平稳,使各轴颈受力不均匀。
(3)曲轴轴承和连杆轴承间隙过大,松紧不一,造成主轴颈中心不重合,运转时受冲击。
(4)发动机发生轴承烧坏和抱住曲轴时,曲轴将出现弯曲和扭转。
(5)曲轴轴向窜动过大,或活塞连杆组重量不一,相差过大。
(6)点火时间过早,或经常有1~2个火花塞工作不良,使发动机运转不平衡,曲轴受力不均匀。
(7)曲轴的平衡被破坏,或曲轴连杆组以及飞轮的平衡被破坏;曲轴过度磨损,强度、刚度不足,或由于装配不当而产生弯扭。
(8)曲轴材质不佳,或曲轴长期不合理的放置造成变形。
(9)汽车起步行驶时,放松离合器踏板动作过快,接合时不柔和。
或用冲力启动发动机,使曲轴受到突然扭转。
(10)行车中使用紧急制动,或在发动机动力不足的情况下,用高挡低速勉强行驶。
2.曲轴弯扭的检验(1)曲轴弯曲的检验检验前需先将曲轴擦洗干净,将曲轴的两端放在检验平板的V形架上,或用顶针顶住曲轴两端的中心孔将其顶在车床上,以前后端未发生磨损部分为基面(前端以正时齿轮轴颈,后端以装飞轮的凸缘)校对中心水平后,用百分表进行测量。
测量时,百分表的量头对准曲轴中间的一道(被检验曲轴的主轴颈个数为单数时)或两道(被检验曲轴的主轴颈个数为双数时)曲轴轴颈,用手慢慢转动曲轴一圈后,百分表上所指的最大和最小的两个读数之差的1/2,即为曲轴的弯曲度。
利用ANSYS软件对曲轴的受力进行分析

第25卷 第18期2009年9月甘肃科技Gansu Science and Technol ogyV ol .25 N o .18Sep . 2009利用AN SYS 软件对曲轴的受力进行分析郝 伟(广东机电职业技术学院,广东广州510515)摘 要:采用ANSYS 软件有限单元法,对云南内燃机厂生产的4100汽油机的曲轴进行有限元分析,在分析过程中通过建立模型、选取合适的单元及网格划分,对曲轴进行了静强度、刚度和疲劳强度的分析,为汽油机曲轴设计提供了理论依据。
关键词:曲轴;有限元分析;受力分析中图分类号:TK403 曲轴是汽车发动机中最重要而且承载最复杂的零件,被称为发动机的心脏,其结构参数不仅影响着整机的尺寸和重量,而且在很大程度上影响着发动机的可靠性与寿命。
随着发动机的不断强化,曲轴的工作条件愈加苛刻,保证曲轴的工作可靠性至关重要,因此,在研制过程中需给予高度重视。
由于曲轴的形状及其载荷比较复杂,建立在精度较高的曲轴实体模型基础上的受力分析一般要借助大型有限元软件。
有限元软件是分析各种结构问题的强有力的工具,使用有限元软件可方便地对曲轴进行分析,并为曲轴的设计和改进提供理论依据。
1 有限元模型的建立(1)曲轴参数。
以云南内燃机厂生产的4100汽油机曲轴为研究对象进行有限元分析。
该曲轴为全支承式,总长743mm ,主轴颈直径为85mm ,连杆轴颈直径为75mm 。
在分析计算中采用整体曲轴模型,用CAD 建立曲轴的几何模型。
实体建模时把各种小的倒角和圆角以及油孔都考虑进去,在划分网格时会非常复杂,并且会产生很多不良的单元,反而使计算出现较大的误差,曲轴受力最大处在连杆轴颈和主轴颈过渡圆角处。
考虑到这些因素,在对曲轴进行实体建模时忽略小的倒角和圆角以及油孔,而位于连杆轴颈和主轴颈处的圆角是分析的对象,不能忽略。
(2)曲轴模型。
将用CAD 绘制好的三维曲轴图形导入到ANSYS 软件,用Hex -Dom inant 网格划分方法,最终形成的曲轴有限元模型,如图1所示,共有62013个单元,194110个节点。
曲轴设计中受力分析
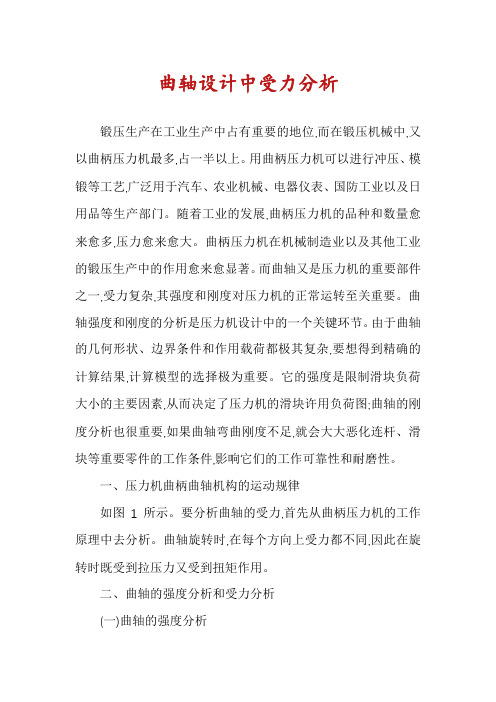
曲轴设计中受力分析锻压生产在工业生产中占有重要的地位,而在锻压机械中,又以曲柄压力机最多,占一半以上。
用曲柄压力机可以进行冲压、模锻等工艺,广泛用于汽车、农业机械、电器仪表、国防工业以及日用品等生产部门。
随着工业的发展,曲柄压力机的品种和数量愈来愈多,压力愈来愈大。
曲柄压力机在机械制造业以及其他工业的锻压生产中的作用愈来愈显著。
而曲轴又是压力机的重要部件之一,受力复杂,其强度和刚度对压力机的正常运转至关重要。
曲轴强度和刚度的分析是压力机设计中的一个关键环节。
由于曲轴的几何形状、边界条件和作用载荷都极其复杂,要想得到精确的计算结果,计算模型的选择极为重要。
它的强度是限制滑块负荷大小的主要因素,从而决定了压力机的滑块许用负荷图;曲轴的刚度分析也很重要,如果曲轴弯曲刚度不足,就会大大恶化连杆、滑块等重要零件的工作条件,影响它们的工作可靠性和耐磨性。
一、压力机曲柄曲轴机构的运动规律如图1所示。
要分析曲轴的受力,首先从曲柄压力机的工作原理中去分析。
曲轴旋转时,在每个方向上受力都不同,因此在旋转时既受到拉压力又受到扭矩作用。
二、曲轴的强度分析和受力分析(一)曲轴的强度分析曲轴强度计算的主要工作是曲轴的应力计算,在此基础上计算曲轴疲劳强度。
一般情况下曲轴强度计算可以用经验算法或者二维有限元算法来校核,其计算结果有一定的参考价值和可信度,但是两种算法结果都难以看到应力随曲轴工作时的变化情况,实际上曲轴工作时处于复杂受力状态,建模过程中简化不当会使计算结果产生较大误差。
在此我们对JB23-63曲柄压力机的曲轴进行三维有限元计算。
(二)曲轴的受力分析曲轴的强度计算所考虑的载荷,从上面曲柄曲轴机构的运动规律图中可以看出,除滑块通过连杆传到连杆轴颈上的力之外,还应考虑曲轴本身不平衡的惯性力,即曲轴是在往复和旋转运动质量的惯性力以及它们的力矩(扭矩和弯矩)共同作用下工作的,使曲轴既扭转又弯曲,产生疲劳应力状态。
曲轴结构强度研究的重点是弯曲疲劳强度。
汽车曲轴工作原理及故障产生和维修
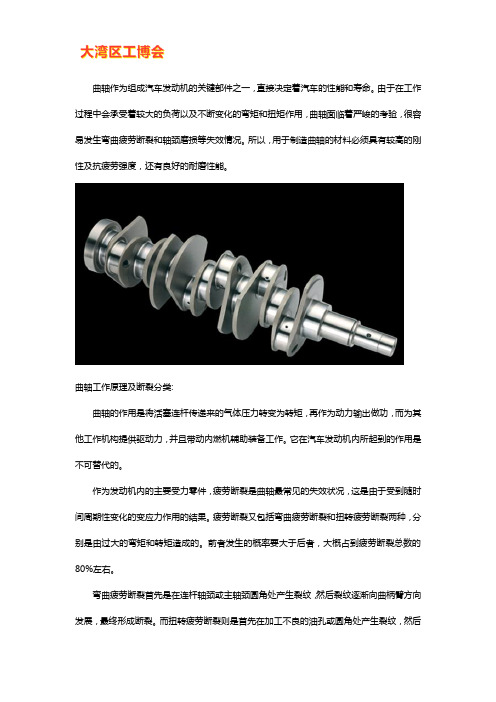
曲轴作为组成汽车发动机的关键部件之一,直接决定着汽车的性能和寿命。
由于在工作过程中会承受着较大的负荷以及不断变化的弯矩和扭矩作用,曲轴面临着严峻的考验,很容易发生弯曲疲劳断裂和轴颈磨损等失效情况。
所以,用于制造曲轴的材料必须具有较高的刚性及抗疲劳强度,还有良好的耐磨性能。
曲轴工作原理及断裂分类:曲轴的作用是将活塞连杆传递来的气体压力转变为转矩,再作为动力输出做功,而为其他工作机构提供驱动力,并且带动内燃机辅助装备工作。
它在汽车发动机内所起到的作用是不可替代的。
作为发动机内的主要受力零件,疲劳断裂是曲轴最常见的失效状况,这是由于受到随时间周期性变化的变应力作用的结果。
疲劳断裂又包括弯曲疲劳断裂和扭转疲劳断裂两种,分别是由过大的弯矩和转矩造成的。
前者发生的概率要大于后者,大概占到疲劳断裂总数的80%左右。
弯曲疲劳断裂首先是在连杆轴颈或主轴颈圆角处产生裂纹,然后裂纹逐渐向曲柄臂方向发展,最终形成断裂。
而扭转疲劳断裂则是首先在加工不良的油孔或圆角处产生裂纹,然后裂纹逐渐向与轴线成45度角的方向发展。
曲轴断裂的主要原因:首先是曲轴机油长期使用发生了变质,或者是严重的超载、超挂等行为,造成发动机长期超负荷运行而出现烧瓦事故。
发动机烧瓦,会造成曲轴受到严重磨损而发生断裂。
其次是经过维修的发动机装车以后,没有经过磨合期就直接超载超挂运转。
发动机长期超负荷运行,使曲轴负荷超出了可以承受的限度。
再有是在修理曲轴的过程中,使用了堆焊这种焊接工艺。
这种工艺会破坏曲轴的动力平衡,如果又没有做其他的平衡校验,会导致不平衡量超标,从而引起发动机较大的振动,造成曲轴断裂。
最后是路况不佳的结果,如果车辆再严重超载超挂,发动机经常在扭振临界转速内运行,减振器的作用失效,这样也会造成曲轴扭转振动疲劳破坏而断裂。
曲轴维修的注意事项:第一,在曲轴维修过程中,应仔细检查曲轴上有没有裂纹、弯曲、扭曲等缺陷存在,以及主轴瓦与连杆轴瓦的磨损情况。
内燃机曲轴动力学响应及受力分析
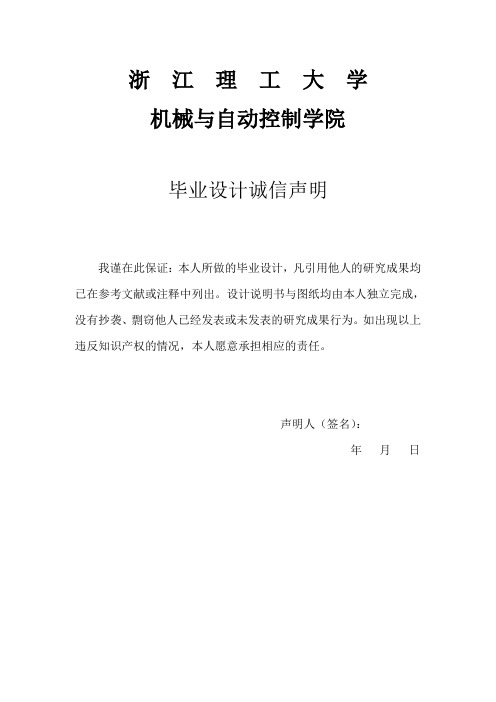
浙江理工大学机械与自动控制学院毕业设计诚信声明我谨在此保证:本人所做的毕业设计,凡引用他人的研究成果均已在参考文献或注释中列出。
设计说明书与图纸均由本人独立完成,没有抄袭、剽窃他人已经发表或未发表的研究成果行为。
如出现以上违反知识产权的情况,本人愿意承担相应的责任。
声明人(签名):年月日摘要按照产品的传统设计方法,为获得较好的设计方案,在产品定型生产之前必须制造物理样机,并对物理样机进行试验测试,如不满足性能要求,就必须对原设计方案进行修改和优化。
这种传统的设计方法需要耗费大量的人力和财力。
本文采用现代设计方法,在测录载荷数据的基础上,对各零部件进行多体动力学仿真分析,根据仿真结果用有限元方法分析零部件的应力分布,在此基础上预测零部件的疲劳寿命。
这样做一般只需要一次实物模型的疲劳试验就可基本完成设计任务,大大缩短了设计周期,节省了开发费用。
内燃机是各类汽车、工程机械的主要配套动力。
作为内燃机的主要受力零部件,曲轴的动力学特性涉及到整机NVH,疲劳强度等重要指标。
对曲轴进行动力学分析是内燃机设计中所需要进行的重要工作,具有重要工程意义。
本文以S195柴油机曲轴为对象,着重完成了以下主要设计工作:1)采用Pro/E进行曲轴的CAD模型建立;2)采用Altair Hyperworks进行曲轴的网格划分;3)采用ABAQUS进行曲轴模型的动静缩减;4)采用AVL Excite进行动力学分析;5)采用ABAQUS进行应力恢复;6)结果提取、整理和疲劳分析。
关键词:柴油机曲轴;动力学仿真;疲劳;有限元;HyperMesh;AVL ExciteAbstractIn accordance with the traditional method of mechanical design, the physical prototype has to been manufactured and testing before producing the mechanical products. The original prototype has to been modified and optimized to obtain a better design if it does not meet the requirements of actual performance. It’s obviously that the traditional design method will take a lot of labor and finance. The article takes the modern method of multi-body dynamics simulation for various mechanical parts on the basis of recorded load date, obtains the stress distribution of parts with the finite element analysis. The article predicts the fatigue life of the mechanical parts. With the method of multi-body dynamics simulation, one prototype will meet the basic task of mechanical design. It will greatly reducing the design cycle, saving costs of design. Diesel engine is the main power source of automobiles, engineering machinery. As the main bearing components of diesel engine, the dynamic features of crankshaft are crucial to the machine NVH, fatigue evaluation and other important indicators. Hence, it has important engineering significance to do the work of dynamic analysis of crankshaft. The contents of the design are listed as followers:1)The CAD modeling of the crankshaft with Pro/E software;2)Meshing of the CAD model of the crankshaft with Altair Hyperworks;3)Condensation of the model of the crankshaft with ABAQUS;4)Dynamic analysis of the model of the crankshaft with A VL Excite Software;5)The stress analysis with ABAQUS;6)The fatigue analysis and results.Key words:Crankshaft; Dynamics simulation; Fatigue; FEA; HyperMesh; A VLExcite目录摘要Abstract第一章绪论 (1)1.1背景概述与研究意义 (1)1.2内燃机动力学仿真研究综述 (1)1.3本文工作任务、工作目标和内容 (2)1.3.1工作任务 (2)1.3.2工作目标 (2)1.3.3设计内容 (3)第二章S195柴油机曲轴的几何建模和仿真参数准备 (4)2.1 S195柴油机简介 (4)2.2 S195柴油机主要特性参数 (4)2.3 S195柴油机的CAD建模 (4)2.3.1 Pro /Engineer软件简介 (4)2.3.2曲轴CAD建模简述 (5)第三章曲轴动力学建模的前处理 (6)3.1前处理主要内容的概述 (6)3.1.1有限元网格划分 (6)3.1.2有限元动静缩减 (6)3.2 曲轴飞轮组网格划分 (7)3.2.1 HyperMesh软件简介 (7)3.2.2划分过程简介 (7)3.3动静缩减 (9)第四章动力学仿真Excite模型的建立 (11)4.1 Exite软件的简介及应用 (11)4.2 Excite建模过程概述 (12)4.2.1定义发动机轴系参数 (12)4.2.2定义体单元和连接单元,定义力学耦合关系 (13)4.2.3定义外载工况 (18)4.3模型的仿真控制设置 (20)第五章S195柴油机动力学仿真结果分析及应用 (22)5.1典型工况的动力学特性 (22)5.2静应力分析和疲劳分析 (24)第六章总结 (30)参考文献 (31)致谢 (32)附录清单 (33)浙江理工大学本科毕业论文第一章绪论1.1背景概述与研究意义按照产品的传统设计方法,为获得较好的设计方案,在产品定型生产前必须制造虚拟样机,并对虚拟样机进行试验测试,如不能满足性能要求,就必须对原设计方案进行修改和优化。
发动机曲轴材料、强化工艺与疲劳强度
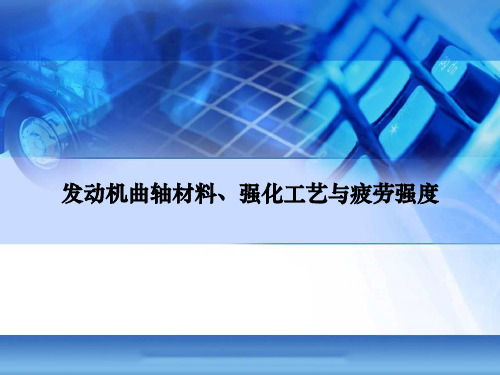
三、曲轴的强化工艺
3.2 圆角表面感应淬火
工艺难点 感应淬火变形 淬硬层形貌与深度 圆角表面机加工质量 磨削裂纹
19
三、曲轴的强化工艺
3.2 圆角表面感应淬火
优点与缺点
优点:钢的强化效果显著 效率较高 可同时提高曲轴的强度和耐磨性
缺点:工艺难度大 设备费用较高 产生电磁干扰 不适用于球铁
34
四、曲轴材料与强化工艺选择
球铁曲轴的应用
广泛用于汽油机和低爆压柴油机,爆压低于145bar的柴油机也有应用。
球铁曲轴优点
成本低-约为钢曲轴的50%-60% 重量轻-较钢曲轴轻8%-10% 阻尼高-吸振性好,减小振动与噪声 耐磨性好-石墨具有自润滑作用 节约资源 节约能源
35
四、曲轴材料与强化工艺选择
目前基本上都是珠光体球铁 奥贝球铁曲轴尚在开发中
10
二、曲轴的材料
2.2 球墨铸铁
材料疲劳强度数据
球铁材料的疲劳强度
牌号 QT600-3
SG600 QT700-2
SG700 FGS700-2
QT800-2 SG800 SG900 FGS900-2
抗拉强度,MPa 600 700 800 900
20
三、曲轴的强化工艺
3.3 圆角滚压
属于一种表面局部性机械强化工艺 强化机理
曲轴轴颈圆角处的材料在滚轮的高接 触应力作用下发生强烈的塑性变形,结果 在圆角表层形成了数值很高、层深可达数 毫米的残余压应力场;
表层材料的形变强化
全自动4头滚压机
21
三、曲轴的强化工艺
3.3 圆角滚压
强化效果
材料
滚压前疲劳极限
发动机曲轴材料、强化工艺与疲劳强度
曲轴受力
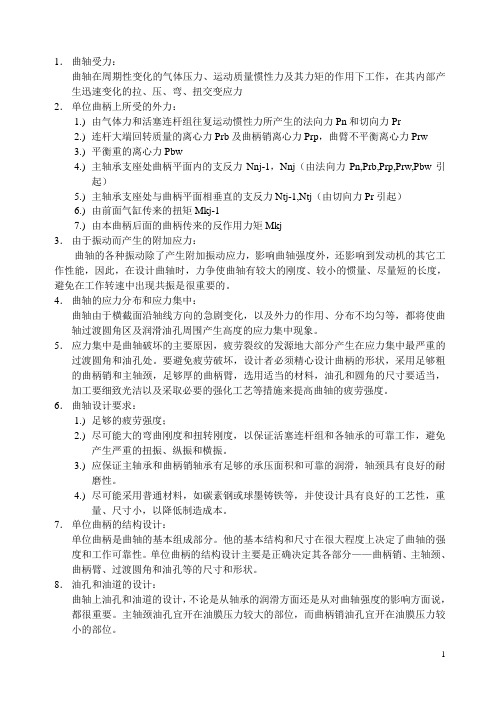
1.曲轴受力:曲轴在周期性变化的气体压力、运动质量惯性力及其力矩的作用下工作,在其内部产生迅速变化的拉、压、弯、扭交变应力2.单位曲柄上所受的外力:1.)由气体力和活塞连杆组往复运动惯性力所产生的法向力Pn和切向力Pr2.)连杆大端回转质量的离心力Prb及曲柄销离心力Prp,曲臂不平衡离心力Prw3.)平衡重的离心力Pbw4.)主轴承支座处曲柄平面内的支反力Nnj-1,Nnj(由法向力Pn,Prb,Prp,Prw,Pbw引起)5.)主轴承支座处与曲柄平面相垂直的支反力Ntj-1,Ntj(由切向力Pr引起)6.)由前面气缸传来的扭矩Mkj-17.)由本曲柄后面的曲柄传来的反作用力矩Mkj3.由于振动而产生的附加应力:曲轴的各种振动除了产生附加振动应力,影响曲轴强度外,还影响到发动机的其它工作性能,因此,在设计曲轴时,力争使曲轴有较大的刚度、较小的惯量、尽量短的长度,避免在工作转速中出现共振是很重要的。
4.曲轴的应力分布和应力集中:曲轴由于横截面沿轴线方向的急剧变化,以及外力的作用、分布不均匀等,都将使曲轴过渡圆角区及润滑油孔周围产生高度的应力集中现象。
5.应力集中是曲轴破坏的主要原因,疲劳裂纹的发源地大部分产生在应力集中最严重的过渡圆角和油孔处。
要避免疲劳破坏,设计者必须精心设计曲柄的形状,采用足够粗的曲柄销和主轴颈,足够厚的曲柄臂,选用适当的材料,油孔和圆角的尺寸要适当,加工要细致光洁以及采取必要的强化工艺等措施来提高曲轴的疲劳强度。
6.曲轴设计要求:1.)足够的疲劳强度;2.)尽可能大的弯曲刚度和扭转刚度,以保证活塞连杆组和各轴承的可靠工作,避免产生严重的扭振、纵振和横振。
3.)应保证主轴承和曲柄销轴承有足够的承压面积和可靠的润滑,轴颈具有良好的耐磨性。
4.)尽可能采用普通材料,如碳素钢或球墨铸铁等,并使设计具有良好的工艺性,重量、尺寸小,以降低制造成本。
7.单位曲柄的结构设计:单位曲柄是曲轴的基本组成部分。
- 1、下载文档前请自行甄别文档内容的完整性,平台不提供额外的编辑、内容补充、找答案等附加服务。
- 2、"仅部分预览"的文档,不可在线预览部分如存在完整性等问题,可反馈申请退款(可完整预览的文档不适用该条件!)。
- 3、如文档侵犯您的权益,请联系客服反馈,我们会尽快为您处理(人工客服工作时间:9:00-18:30)。
曲轴的受力情况分析及主要强化方式
在汽车发动机中,曲轴是承受负荷最大的部件,在发动机工作时,曲轴的各部分会受到弯曲、扭转、拉压和剪切等力的作用。
曲轴时常处于高速旋转的运动状态之中,这会很容易造成磨损和发热烧损,因此要求轴颈表面要有很好的表面耐磨度,同时要防止曲轴的疲劳断裂,在曲轴常见的故障中,因弯曲疲劳断裂引起的故障率高达百分之八十以上。
为了保证发动机正常地、可靠地工作,这就要求曲轴要有足够的强度、耐磨性、刚度和平衡精度,因此,我们在曲轴的制造过程中,必须对曲轴进行强化处理。
对曲轴的强化处理指的是在不改变曲轴的结构的前提下,采用物理的、化学的以及机械的方法,使曲轴得到尽可能大的强化度,以达到提高曲轴的各项力学性能的目的。
在现实生产中,我们可以依据曲轴的工况和实际技术要求,选择一种或多种强化手段对曲轴进行强化处理。
常见的对曲轴强化处理方式主要有以下几种:轴颈表面和圆角淬火强化方式、圆角滚压强化方式、氮化强化方式和碳氮共渗强化方式等。