第6章机械加工质量
第6章轴类零件1

4)车削圆锥面 轴类零件上圆锥面的车削方法参表6-1-7。
表6-1-7 轴类零件上圆锥面的车削方法
序号 车削方法
操作示意图
操作方法
1
转动小滑板车削 圆锥面
a)
先把小滑板转过一个圆锥斜角α/2,然后手动进给完成圆 锥面车削。
b)
2
偏移尾座车削圆 锥面
a)
将尾座横向移动一个距离S,使工件的回转轴线与车床主轴 线的夹角等于圆锥斜角α/2,然后纵向自动进给车削圆锥 面。这种方法不能加工锥度太大的工件(α<8°)和内锥面。
磨削方 法
磨削过程
表6-1-8 中心磨削的磨削方法
加工示意图
纵磨法
砂轮旋转为主运动,工件旋转和往复 运动实现圆周进给和轴向进给,砂轮 架水平进给实现径向进给运动。工件 往复一次,外圆表面轴向切去一层金 属,直至加工到图样要求尺寸。
横磨法
磨削时没有工件往复运动,砂轮连续 的横向进给直到磨削至工件尺寸。
图6-1-7 典型的成形面零件
图6-1-8 常见的成形车刀
7) 轴类零件的磨削加工 轴类零件上与其他零部件配合的表面,其尺寸精度、几何公差和表面结 构要求较高,常在半精车后通过磨削加工来达到要求。磨削加工是以砂轮 作为切削工具进行切削的加工方法。多应用在淬硬外圆表面的加工,一般 半精加工之后进行,也可在毛坯外圆表面直接进行磨削加工,因此,磨削 加工既是精加工手段,又是高效率机械加工手段之一。磨削加工的精度可 达IT5~IT8,表面结构为Ra0.1~0.16µm。
6.1轴类零件的机械加工与品质 检验技术基础1
6.1.1
轴类零件概述
6.1.2
轴类零件的加工方法
铰铰链链四四杆杆机机构构的的性性质质
机械制造技术基础复习资料
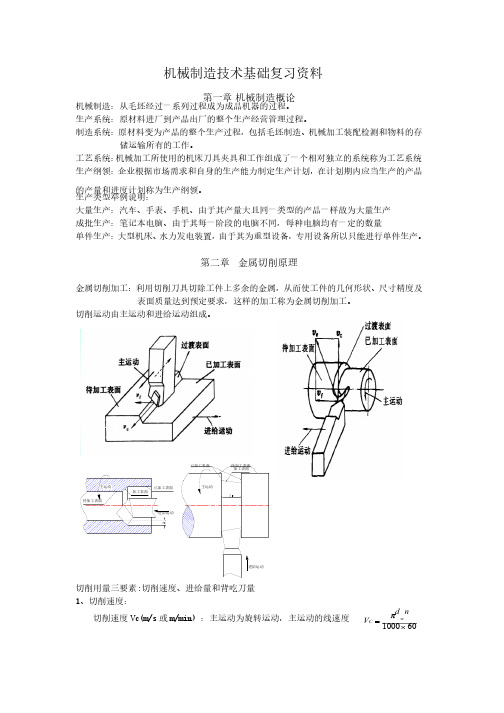
机械制造技术基础复习资料机械制造技术基础复习资料第一章第一章 机械制造概论机械制造概论机械制造:从毛坯经过一系列过程成为成品机器的过程。
机械制造:从毛坯经过一系列过程成为成品机器的过程。
生产系统:原材料进厂到产品出厂的整个生产经营管理过程。
生产系统:原材料进厂到产品出厂的整个生产经营管理过程。
制造系统:原材料变为产品的整个生产过程,原材料变为产品的整个生产过程,包括毛坯制造、包括毛坯制造、机械加工装配检测和物料的存 储运输所有的工作。
储运输所有的工作。
储运输所有的工作。
工艺系统:机械加工所使用的机床刀具夹具和工作组成了一个相对独立的系统称为工艺系统机械加工所使用的机床刀具夹具和工作组成了一个相对独立的系统称为工艺系统 生产纲领:企业根据市场需求和自身的生产能力制定生产计划,在计划期内应当生产的产品的产量和进度计划称为生产纲领。
的产量和进度计划称为生产纲领。
生产类型举例说明:生产类型举例说明:大量生产:汽车、手表、手机、由于其产量大且同一类型的产品一样故为大量生产大量生产:汽车、手表、手机、由于其产量大且同一类型的产品一样故为大量生产 成批生产:笔记本电脑、由于其每一阶段的电脑不同,每种电脑均有一定的数量成批生产:笔记本电脑、由于其每一阶段的电脑不同,每种电脑均有一定的数量单件生产:大型机床、水力发电装置,由于其为重型设备,专用设备所以只能进行单件生产。
第二章第二章 金属切削原理金属切削原理金属切削加工:利用切削刀具切除工件上多余的金属,利用切削刀具切除工件上多余的金属,从而使工件的几何形状、从而使工件的几何形状、尺寸精度及 表面质量达到预定要求,这样的加工称为金属切削加工。
表面质量达到预定要求,这样的加工称为金属切削加工。
表面质量达到预定要求,这样的加工称为金属切削加工。
切削运动由主运动和进给运动组成。
切削运动由主运动和进给运动组成。
切削用量三要素切削用量三要素::切削速度、进给量和背吃刀量切削速度、进给量和背吃刀量1、切削速度:、切削速度:切削速度Vc(m/s 或m/min) m/min) :主运动为旋转运动,主运动的线速度:主运动为旋转运动,主运动的线速度:主运动为旋转运动,主运动的线速度 601000´=nd V wC p进给运动加工表面待加工表面待加工表面主运动已加工表面加工表面进给运动已加工表面主运动主运动为往复直线运动6010002´=rC Ln V2、进给量:工件或刀具每回转一周时二者沿进给方向相对位移。
(完整版)机械制造工程学习题及答案_超级完整

第一章绪论思考下列问题:1.机械制造工业的发展历史和现状。
2.机械制造工业在国民经济中的地位作用。
3.本课程的主要任务和要求。
第二章金属切削加工的基础知识一、填空题1. 在加工中,刀具和工件之间的相对运动称为切削运动,按其功用可分为主运动和进给运动。
其中主运动消耗功率最大。
2. 切削用量三要素是指切削速度、进给量和背吃刀量。
*3. 刀具静止角度参考系的假定条件是假定安装条件和假定运动条件。
4. 常用的切削刃剖切平面有正交平面、法平面、背平面和假定工作平面,它们可分别与基面和切削平面组成相应的参考系。
5. 在正交平面内度量的前刀面与基面之间的夹角称为前角,后刀面与切削平面之间的夹角称为后角。
6. 正交平面与法平面重合的条件是刃倾角为0 。
7. 基准平面确定后,前刀面由前角和刃倾角两个角确定;后刀面由后角和主偏角两个角确定;前、后刀面确定了一条切削刃,所以一条切削刃由前角、后角、刃倾角、主偏角四个角度确定。
8. 用以确定刀具几何角度的两类参考坐标系为刀具标注角度参考系和刀具工作角度参考系。
二、判断题(正确的打√,错误的打×)1. 在切削加工中,进给运动只能有一个。
(×)2. 背平面是指通过切削刃上选定点,平行于假定进给运动方向,并垂直于基面的平面。
(×)3. 其它参数不变,主偏角减少,切削层厚度增加。
(×)4. 其它参数不变,背吃刀量增加,切削层宽度增加。
(√)5. 主切削刃与进给运动方向间的夹角为主偏角K。
(×)r*6. 车削外圆时,若刀尖高于工件中心,则实际前角增大。
(√)7. 对于切断刀的切削工作而言,若考虑进给运动的影响,其工作前角减少,工作后角增大。
(×)*8. 当主偏角为90时,正交平面与假定工作平面重合。
(√)9. 切削铸铁类等脆性材料时,应选择K类(YG类)硬质合金。
(√)10. 粗加工时,应选择含钴量较低的硬质合金。
(×)三、名词解释1. 基面过切削刃上选定点垂直于主运动方向的平面。
机械制造技术基础第六章 习题及答案

第六章习题一.单项选择题1.退火处理一般安排在; ( )a、毛坯制造之后b、粗加工后c、半精加工之后d、精加工之后2.轴类零件定位用的顶尖孔是属于: ( )a、精基准b、粗基准c、辅助基准d、自为基准3.加工箱体类零件时常选用一面两孔作定位基准,这种方法一般符合 ( )a、基准重合原则b、基准统一原则c、互为基准原则d、自为基准原则4.合理选择毛坯种类及制造方法时,主要应使 ( )a、毛坯的形状尺寸与零件的尽可能接近b、毛坯方便制造,降低毛坯成本c、加工后零件的性能最好d、零件总成本低且性能好5.自为基准多用于精加工或光整加工工序,其目的是: ( )a、符合基准重合原则b、符合基准统一原则c、保证加工面的形状和位置精度 d、保证加工面的余量小而均匀6.调质处理一般安排在: ( )a、毛坯制造之后b、粗加工后c、半精加工之后d、精加工之后7.精密齿轮高频淬火后需磨削齿面和内孔,以提高齿面和内孔的位置精度,常采用以下原则来保证 ( )a、基准重合b、基准统一c、自为基准d、互为基准8.淬火处理一般安排在: ( )a、毛坯制造之后b、粗加工后c、半精加工之后d、精加工之后9.在拟定零件机械加工工艺过程、安排加工顺序时首先要考虑的问题是 ( )a、尽可能减少工序数;b、精度要求高的主要表面的加工问题;c、尽可能避免使用专用机床;d、尽可能增加一次安装中的加工内容。
10.零件上孔径大于30mm的孔,精度要求为IT9,通常采用的加工方案为( )a、钻-镗b、钻-铰c、钻-拉d、钻-扩-磨11.编制零件机械加工工艺规程、生产计划和进行成本核算最基本的单元是( )a、工步b、工位c、工序d、走刀12.零件在加工过程中,粗基准一般选择: ( )a、工件的毛坯面b、工件的已加工表面c、工件上的大平面13.单件小批生产装配精度要求高组成环多应选()法装配。
a、完全互换法b、分组互换法c、调整法d、修配法14.若装配精度要求高组成环少(3环)大批量生产时应选()法装配。
《机械制造工程》习题汇总1
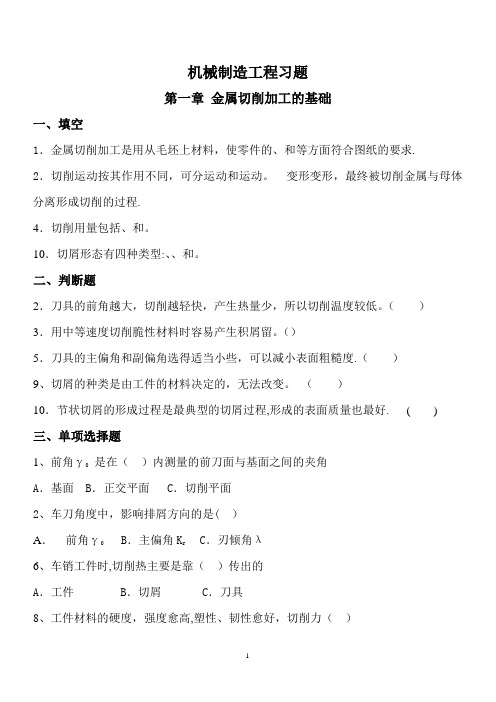
机械制造工程习题第一章金属切削加工的基础一、填空1.金属切削加工是用从毛坯上材料,使零件的、和等方面符合图纸的要求.2.切削运动按其作用不同,可分运动和运动。
变形变形,最终被切削金属与母体分离形成切削的过程.4.切削用量包括、和。
10.切屑形态有四种类型:、、和。
二、判断题2.刀具的前角越大,切削越轻快,产生热量少,所以切削温度较低。
()3.用中等速度切削脆性材料时容易产生积屑留。
()5.刀具的主偏角和副偏角选得适当小些,可以减小表面粗糙度.()9、切屑的种类是由工件的材料决定的,无法改变。
()10.节状切屑的形成过程是最典型的切屑过程,形成的表面质量也最好. ( )三、单项选择题1、前角γ0是在()内测量的前刀面与基面之间的夹角A.基面 B.正交平面 C.切削平面2、车刀角度中,影响排屑方向的是( )A.前角γ0 B.主偏角K r C.刃倾角λ6、车销工件时,切削热主要是靠()传出的A.工件 B.切屑 C.刀具8、工件材料的硬度,强度愈高,塑性、韧性愈好,切削力()A.愈小 B.愈大 C.基本不变14.切削铸铁和青铜等脆性材料时产生切削形态为()A.带状切削 B.崩碎切削C.节状切削 D.粒状切削四、简答题1.金属切削过程存在哪三个变形区,各个变形区有什么变形特点?3.简述影响切削温度的主要因素有哪些?4.简述切削热的来源及其影响因素.第三章机械制造过程与工艺一、填空题3.工艺过程包括毛坯制造、、零件热处理、和检验试车等。
13.加工余量确定方法有、和分析计算法。
16.工艺成本包括费用和费用两大部分。
17.加工精度包括精度、精度和相互位置精度三个方面。
19.获得零件形状精度的方法有、、和成形法。
二、判断题1.在机械加工中,一个工件在同一时刻只能占据一个工位。
( )3.在一道工序中只能有一次安装。
( )7.在尺寸链中只有一个封闭环.( )12.一个表面的加工总余量等于该表面的所有加工余量之和。
( )17.延长工作时间是提高劳动生产率的一种方法。
机械制造基础第六章 第一、二、三节
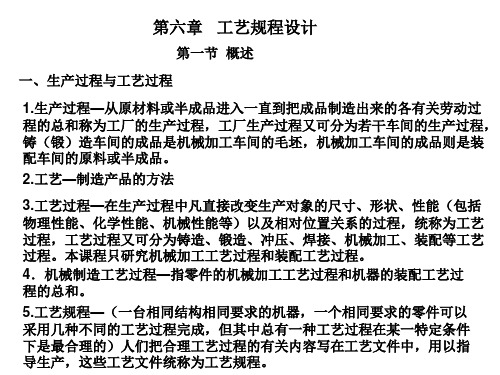
粗拉 IT9~10 Ra 1.25~5
饺 IT6~9 Ra 0.32~10
精镗 IT7~9 Ra 0.63~5
粗磨 IT9~11 Ra1.25~10
精拉 IT7~9 Ra0.16~0.63
推 IT6~8 Ra0.08~1.25
手饺 IT5
Ra0.08~1.25
精磨 IT7~8 Ra0.08~0.63
3.工艺过程—在生产过程中凡直接改变生产对象的尺寸、形状、性能(包括 物理性能、化学性能、机械性能等)以及相对位置关系的过程,统称为工艺 过程,工艺过程又可分为铸造、锻造、冲压、焊接、机械加工、装配等工艺 过程。本课程只研究机械加工工艺过程和装配工艺过程。 4.机械制造工艺过程—指零件的机械加工工艺过程和机器的装配工艺过 程的总和。
(6)选择不同的生产模式和制造技术的准则是什么?过去是——质量、生 产率、成本也称为切削加工的技术指标;现在是——T(交货时间)、Q (质量)、C(成本)、S(服务)
2.生产组织方式(三种)
(1)生产全部零件,并组装整机 特点:1)必须拥有加工所有零件及部装、总装的设备,形成大而全,小 而全的企业。 2)市场一旦有变化适应性差 3)设备负载不平衡,固定资产利用率低。 4)定岗人员忙闲不均,不便管理,难以调动全员积极性。
半精铣 IT8~11 Ra 2.5¬10
机械制造基础第六章习题及答案

第六章习题与答案6-1为了加工出各种回转表面,车床必须具备哪些运动?答:1)工件的旋转运动;2)刀具的直线移动。
6-2车削加工中使用的刀具可分为哪几种?答:车削加工刀具可分为外圆车刀、端面车刀、割刀、镗刀和成形车刀。
6-3车削加工时,工件的装夹方式有哪些?答:1)卡盘或花盘安装;2)使用顶尖安装。
6-4按加工精度和表面粗糙度要求,车削加工可分为哪几种?答:按加工精度和表面粗糙度,车削加工可分为粗车、半精车、精车和精细车。
6-5试述铣削过程。
答:铣削加工时工件的直线或曲线运动为进给运动,铣刀的旋转运动为主运动。
铣削过程中有多把旋转的车刀在作切削加工。
铣刀刀齿切入工件是一个断续地、周期地受冲击的切削过程。
铣削时,切削厚度h D是变化的,由于刀齿刃口有圆弧半径,刀齿最初切入工件时,理论上h D为零,刀刃将在工件表面上滑走一段距离,直至h D大于刀齿刃口的圆弧半径时,才能切入工件。
铣削过程中,刀齿断续地进行切削,并且切削厚度不断地变化,使得铣削力和扭矩不断变化。
此外,刃磨后铣刀上各刀齿很难保证处于同一圆周或端面上,导致铣削力产生波动,因而使机械加工系统发生振动,造成铣削过程的不平稳,降低了工件表面的加工质量。
6-6铣削与车削过程相比,具有哪些不同之处?答:1)断续的切削过程;2)切削厚度变化;3)铣削力变化;4)切屑的变形程度大。
6-7平面的铣削方式有哪些?各有哪些优缺点?答:铣削加工平面可以用周铣法,也可以用端铣法。
用圆柱铣刀的圆周刀齿来铣削工件表面的铣削方法称为周铣法。
周铣法可以利用多种形式的铣刀,周铣法可分为顺铣和逆铣。
顺铣法有利于提高加工表面的质量,有利于提高刀具的耐用度和工件装夹的稳定性,但容易引起工作台窜动,使进给速度不平稳,影响加工表面的粗糙度,严重时还会发生打刀现象。
逆铣法使刀齿磨损加剧,使工件产生加工硬化现象,并增加了表面粗糙度。
因此,逆铣多用于粗加工。
用端铣刀的端面刀齿来铣削工件表面的铣削方法称为端铣法。
第六章习题答案机械制造工艺学
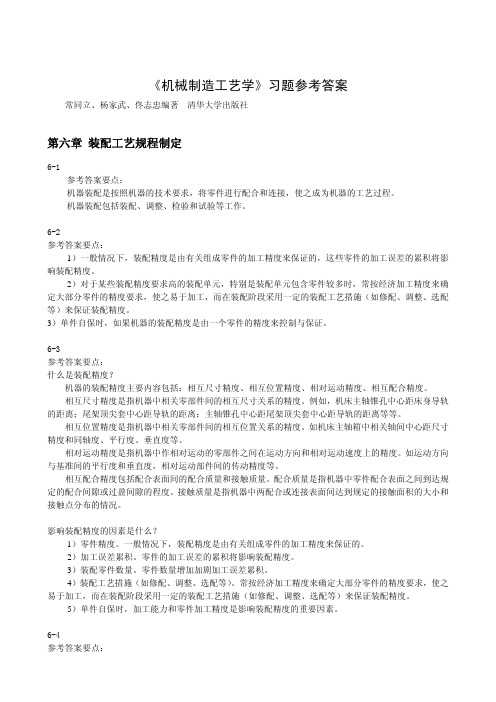
2
2
Δ0 = Δ1 - Δ2 - Δ 4 - Δk 解得: Δk = -0.107
⑧计算中间尺寸
Akm = Ak + Δk = 7 + (-0.107) = 6.893
初步拟定补偿环的尺寸 Akc = 6.893± 0.018
⑨验算装配后封闭环的极限尺寸
L0E max = A0m + 1 T 0L = 0.1+ 1 × 0.222 = 0.211
⑥计算协调环平均尺寸,除协调环之外各环的中间偏差
Δ0 = 0.15 + 0.05 = 0.1 2
Δ2 = - 0.018 = -0.009 2
Δ3 = - 0.015 = -0.0075 2
Δ4 = - 0.018 = -0.009 2
由 Δ0 = Δ1 - Δ2 - Δ3 - Δ4 得 Δ1 = 0.0745
③选择 A3 为修配环,属于“越修越大”的情况
④查表可得:T1 = 0.1 T2 = T4 = 0.043 T3 = Tk = 0.03(6 经济加工精度 IT 9)
按照入体原则,确定上述各组成环的尺寸
A2
=
A4
=
17
0 -0.043
mm
A1 = 41-00.1 mm
⑤计算封闭环实际公差 T 0L = T1 + T 2 + Tk + T 4 = 0.222
修配装配法是将装配尺寸链中各组成环的公差相对于互换装配法所求之值增大使其能按现有生产条件下较经济的加工精度制造装配时通过去除补偿环或称修配环是预先选定的某一组成环部分材料改变其实际尺寸使封闭环达到精度要求的装配方法
《机械制造工艺学》习题参考答案
常同立、杨家武、佟志忠编著 清华大学出版社
机械制造技术基础第六章
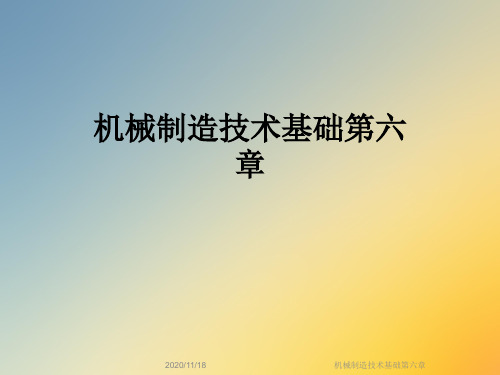
机械制造技术基础第六章
第四节 工艺尺寸链
一、尺寸链及尺寸链计算公式
1. 在工件加工和机器装配过程中,由相互连
接的尺寸形成的封闭尺寸组,称为尺寸链。
图6-10 尺寸链示例
机械制造技术基础第六章
2.基准面在加工时经过转换的情况
在复杂零件的加工过程中,常常出现定位基 准不重合或加工过程中需要多次转换工艺基准时, 工序尺寸的计算就复杂多了,不能用上面所述的 反推计算法,而是需要借助尺寸链的分析和计算, 并对工序余量进行验算以校核工序尺寸及其上下 偏差,在下节详述。
3.孔系坐标尺寸的计算
机械制造技术基础第六章
3.尺寸精度的获得方法 (1)试切法 (2)定尺寸刀具法 (3) (4)自动控制法
机械制造技术基础第六章
四、机械加工工艺与生产类型
1.
生产类型的划分依据是产品或零件的年生产 纲领,产品的年生产纲领就是产品的年生产量。
N=Qn(1+a%)(1+b%)
ቤተ መጻሕፍቲ ባይዱ
式中
N——零件的年产纲领(件/年)
机械制造技术基础第六章
4.极值法解尺寸链的计算公式
图6-12 基本尺寸、极限偏差、公差与中间偏差
机械制造技术基础第六章
4.极值法解尺寸链的计算公式
(1)封闭环基本尺寸A0等于所有增环基本尺寸 (Ap)之和减去所有减环基本尺寸 (Aq)
k
m
A0=∑Ap-∑Aq
p=1 q=k+1
式中 m—— k——
2)应使工艺过程具有较高的生产率,使产品尽 3) 4)注意减轻工人的劳动强度,保证生产安全。
中南大学机械工艺制造习题与答案

第1章思考题1、有人说:“工件在夹具中装夹,只要有6个定位支承点就是完全定位",“凡是少于6个定位支承点,就是欠定位”,“凡是少于6个定位支承点,就不会出现过定位”,上面这些说法都对吗?为什么?试举例说明.2、“工件夹紧后,位置不动了,其所有自由度就都被限制了”,这种说法对吗?为什么?3、某机床厂年产CW6140普通车床500台,已知机床主轴的备品率为20%,废品率为4%,试计算主轴的年生产纲领。
此主轴属于何种生产类型?工艺过程应有什么特点?4、如图1所示一批工件,钻4-φ15孔时,若加工过程分别为:(1)用4轴钻同时钻4个孔;(2)先钻1个孔,然后使工件回转90度钻下一个孔,如此循环操作,直至把4个孔钻完。
以上两种加工情况各有几个工步和工位?图1 工件5、根据六点定位原理,分析图2所示定位方案中定位元件限制自由度的情况。
图2 定位分析3—活动锥销6、图3所示为某箱体零件的零件图及工序图,试在图中指出:(1)铣削平面2时的设计基准,定位基准及测量基准;(2)镗孔4时的设计基准,定位基准及测量基准.图3 基准分析第1章思考题答案1、有人说:“工件在夹具中装夹,只要有6个定位支承点就是完全定位”,“凡是少于6个定位支承点,就是欠定位”,“凡是少于6个定位支承点,就不会出现过定位”,上面这些说法都不对.例如:在球体上铣通平面只需一个定位支承点限制一个自由度就可满足要求,而这种定位方式并不是欠定位。
2、“工件夹紧后,位置不动了,其所有自由度就都被限制了”,这种说法不对。
因为在分析定位时不应考虑力的影响。
“工件的自由度被限制”,是指工件在某座标方向上有了确定的位置,而不是指工件在受到使之脱离支承点的外力时,不能运动。
“工件夹紧后,位置不动了",这是夹紧的任务,并不一定就说明工件的所有自由度就都被限制了。
4、都只有1个工步。
工位:(1)1;(2)45、限制5个自由度6、(1)铣削平面2时的设计基准:3;定位基准:1;及测量基准:1 (2)镗孔4时的设计基准:5;定位基准:1及测量基准:不定第2章思考题1、试分析下图所示的三种加工情况,加工后工件表面会产生何种形状误差?假设工件的刚度很大,且车床床头刚度大于尾座刚度。
机械制造技术基础课程教学大纲

《机械制造技术基础》课程教学大纲一、课程基本信息二、教学内容及基本要求第一章导论教学目的:1. 了解机械制造业的作用、发展现状和趋势.2。
明确本课程的学习目的和方法.教学重点和难点:让大家认识到目前我国机械制造业水平的现状及与西方发达国家(德、日等)的差距.主要教学内容及要求:了解机械制造业在国民经济中的作用及发展,了解目前我国机械制造业水平的现状及与西方发达国家(德、日等)的差距,了解制造技术、制造系统等概念,了解先进制造技术的发展趋势,掌握本课程的学习目的和方法。
第二章金属切削基本知识教学目的:1。
使学生了解和掌握金属切削原理的基本理论,为后续内容的学习打下基础。
2。
能正确分析工件的特性,选择合适的刀具及切削用量.教学重点和难点:1.金属切削过程的基本知识、基本规律。
2.切削用量与切削力、切削温度、刀具寿命、加工质量的关系.3.刀具几何参数与切削力、切削温度、刀具寿命、加工质量的关系。
主要教学内容及要求:1.了解车刀结构、掌握刀具标注角度参考系中的正交平面参考系内,刀具几何角度标注方法.2.掌握切削力的形成,分解及影响因素,掌握切削热的来源,传散及影响因素.3.掌握刀具磨损及刀具寿命的有关规律。
4.熟悉工件材料加工性,刀具材料、刀具几何参数及切削用量的选择方法.5.掌握砂轮特性及影响因素,了解磨削运动、磨削力及磨削过程的特点。
第三章制造工艺装备教学目的:1. 掌握关键表面成形方法,能够合理选用加工机床。
2. 能正确选择工件的定位及装夹方式,了解机床夹具设计的基本原理和方法.教学重点和难点:1.金属切削机床的分类、型号和主要技术参数;工件表面成形方法。
2.工件表面成形方法与机床运动分析。
3.机床传动链的分析与计算。
4.六点定位原理;常用定位元件限制的自由度;夹紧力的确定。
主要教学内容及要求:1.了解常用金属切削刀具的种类、用途及特性。
2.了解金属切削机床的分类、型号和主要技术参数。
3.掌握工件表面成形方法与机床运动分析。
机械制造工程原理习题集
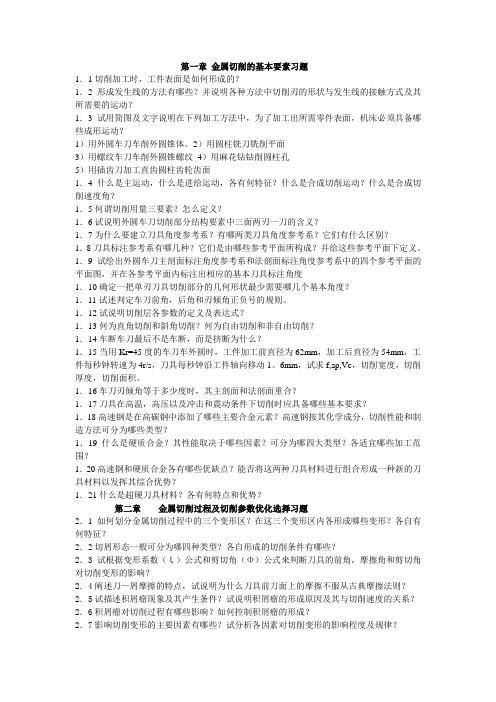
第一章金属切削的基本要素习题1.1切削加工时,工件表面是如何形成的?1.2形成发生线的方法有哪些?并说明各种方法中切削刃的形状与发生线的接触方式及其所需要的运动?1.3试用简图及文字说明在下列加工方法中,为了加工出所需零件表面,机床必须具备哪些成形运动?1)用外圆车刀车削外圆锥体。
2)用圆柱铣刀铣削平面3)用螺纹车刀车削外圆锥螺纹4)用麻花钻钻削圆柱孔5)用插齿刀加工直齿圆柱齿轮齿面1.4什么是主运动,什么是进给运动,各有何特征?什么是合成切削运动?什么是合成切削速度角?1.5何谓切削用量三要素?怎么定义?1.6试说明外圆车刀切削部分结构要素中三面两刃一刀的含义?1.7为什么要建立刀具角度参考系?有哪两类刀具角度参考系?它们有什么区别?1.8刀具标注参考系有哪几种?它们是由哪些参考平面所构成?并给这些参考平面下定义。
1.9试绘出外圆车刀主剖面标注角度参考系和法剖面标注角度参考系中的四个参考平面的平面图,并在各参考平面内标注出相应的基本刀具标注角度1.10确定一把单刃刀具切削部分的几何形状最少需要哪几个基本角度?1.11试述判定车刀前角,后角和刃倾角正负号的规则。
1.12试说明切削层各参数的定义及表达式?1.13何为直角切削和斜角切削?何为自由切削和非自由切削?1.14车断车刀最后不是车断,而是挤断为什么?1.15当用Kr=45度的车刀车外圆时,工件加工前直径为62mm,加工后直径为54mm,工件每秒钟转速为4r/s,刀具每秒钟沿工件轴向移动1。
6mm,试求f,ap,Vc,切削宽度,切削厚度,切削面积。
1.16车刀刃倾角等于多少度时,其主剖面和法剖面重合?1.17刀具在高温,高压以及冲击和震动条件下切削时应具备哪些基本要求?1.18高速钢是在高碳钢中添加了哪些主要合金元素?高速钢按其化学成分,切削性能和制造方法可分为哪些类型?1.19什么是硬质合金?其性能取决于哪些因素?可分为哪四大类型?各适宜哪些加工范围?1.20高速钢和硬质合金各有哪些优缺点?能否将这两种刀具材料进行组合形成一种新的刀具材料以发挥其综合优势?1.21什么是超硬刀具材料?各有何特点和优势?第二章金属切削过程及切削参数优化选择习题2.1如何划分金属切削过程中的三个变形区?在这三个变形区内各形成哪些变形?各自有何特征?2.2切屑形态一般可分为哪四种类型?各自形成的切削条件有哪些?2.3试根据变形系数(ξ)公式和剪切角(Φ)公式来判断刀具的前角,摩擦角和剪切角对切削变形的影响?2.4阐述刀—屑摩擦的特点,试说明为什么刀具前刀面上的摩擦不服从古典摩擦法则?2.5试描述积屑瘤现象及其产生条件?试说明积屑瘤的形成原因及其与切削速度的关系?2.6积屑瘤对切削过程有哪些影响?如何控制积屑瘤的形成?2.7影响切削变形的主要因素有哪些?试分析各因素对切削变形的影响程度及规律?2.8分析切削力的来源?切削合力为什么要分解为三个切削力?并说明各切削分力的定义及其作用。
机械制造技术基础-卢秉恒 答案 第六章

6-9 一般情况下,机械加工过程都要划分为几个阶 段进行,为什么?
解:加工过程可以划分为以下几个阶段:①粗加工阶段
②半精加工阶段③精加工阶段④光整加工阶段
划分加工阶段的原因是:①粗加工阶段中切除金属较多,
产生的切削刀和切削热都增多,所需的夹紧力也比较
大,因而加工的零件内应力和变形也较大,不能够满 足要求,所以要分为以上四个阶段。 ②可合理的使用机床设备。 ③为了在加工过程中插入热处理工序,同时让热处理发 挥充分的效果。
6-12:试分析影响工序余量的因素,为什么在计算 本工序加工余量时必须考虑本工序装夹误差的影响
因为:①上工序的表面粗糙度(Ra)②上工序的表面破
坏层(Da)③上工序的尺寸公差(Ta)④需要单独考虑 的误差⑤ 本工序的安装误差 本工序的装夹误差包括定位误差和夹紧误差,这两种误 差会影响加工时的磨削余量等,所以计算本工序加工余 量,需考虑工序装夹误差。
6-11:什么是加工余量、工序余量和总余量?
答:在由毛坯变为成品的过程中,在某加工表面上切除
金属层的总厚度称为该表面的加工总余量
每一道工序所切除的金属层厚度称为工序间加工余量
对于外圆和孔等旋转表面而言,加工余量是从直径上
考虑的,称为对称余量,即实际所切削的金属层厚度 是直径上的加工余量之半。平面的加工余量则是单边 余量,它等于实际所切除的金属层厚度
加工右端面时的设计基准与定位基准重合
∴A1的工序尺寸就等于设计尺寸
6-17 解:
其中25+0-0.3为封闭环,A3为减环,50+0-0.1为增环 ∴A3=50-25=25㎜ ES(A3)=0.3-0.1=0.2㎜ EI(A3)=0 ∴A3的工序尺寸为25+0.2+0
机械制造技术基础第6章习题答案

可调支承:多用于支承工件的粗基准面,支承高度可以 根据需要进行调整,调整到位后用螺母锁紧。一个可调 支承限制一个自由度。
自位支承:由于自位支承是活动的或是浮动的,无论结 构上是两点或三点支承,其实质只起一个支承点的作用 所以自位支承只限制一个自由度,使用自位支承的目的 在于增加与工件的接触点,减小工件变形或减少接触应 力。
5、其它元件及装置:根据加工要求,所设的一些辅助 元件。
6、夹具体:用于连接夹具元件和有关装置使之成为一
个整体的基础元件、夹具通过夹具体与机床连接。
h
1
xy zx y
•此方案过定位
xz
•改进方法:将
固定短V形块3
改为浮动式短V
形块
h
2
6-4试分析比较可调支承、自位支承和辅助支承 的作用和应用范围。
6-1机床夹具由哪几部分组成?各有何作用?
1、定位元件:用来确定工件正确位置的元件。
2、夹紧装置:使工件在外力作用下仍能保持其正确的 定位位置的装置。
3、对刀元件:用于确定或引导刀具相对于夹具定位元 件具有正确位置关系的元件。
4、连接元件:用于确定夹具在机床上具有正确的位置 ,并与机床相连接的元件。
辅助支承:不能作为定位元件,不能限制工件的自由度 ,它只用以增加工件在加工过程中
由 书 P298 式( 6 - 1)可知:
FJ
tan
1
FQ tan(
, 2)
式中: F J 斜楔与接触一面受到
- 斜楔升角 ( );
夹 具 对 它的 反作用力;
1 斜楔与 上部夹具间的 2 斜楔与 上部夹具间的 设工件与夹具间的摩擦
摩擦角 ; 摩擦角 。 系数 为 f 1,工件与工作台
机械制造技术基础第六章习题及答案

机械制造技术基础第六章习题及答案第六章习题⼀.单项选择题1.退⽕处理⼀般安排在; ( )a、⽑坯制造之后b、粗加⼯后c、半精加⼯之后d、精加⼯之后2.轴类零件定位⽤的顶尖孔是属于: ( )a、精基准b、粗基准c、辅助基准d、⾃为基准3.加⼯箱体类零件时常选⽤⼀⾯两孔作定位基准,这种⽅法⼀般符合 ( )a、基准重合原则b、基准统⼀原则c、互为基准原则d、⾃为基准原则4.合理选择⽑坯种类及制造⽅法时,主要应使 ( )a、⽑坯的形状尺⼨与零件的尽可能接近b、⽑坯⽅便制造,降低⽑坯成本c、加⼯后零件的性能最好d、零件总成本低且性能好5.⾃为基准多⽤于精加⼯或光整加⼯⼯序,其⽬的是: ( )a、符合基准重合原则b、符合基准统⼀原则c、保证加⼯⾯的形状和位置精度 d、保证加⼯⾯的余量⼩⽽均匀6.调质处理⼀般安排在: ( )a、⽑坯制造之后b、粗加⼯后c、半精加⼯之后d、精加⼯之后7.精密齿轮⾼频淬⽕后需磨削齿⾯和内孔,以提⾼齿⾯和内孔的位置精度,常采⽤以下原则来保证 ( )b、基准统⼀c、⾃为基准d、互为基准8.淬⽕处理⼀般安排在: ( )a、⽑坯制造之后b、粗加⼯后c、半精加⼯之后d、精加⼯之后9.在拟定零件机械加⼯⼯艺过程、安排加⼯顺序时⾸先要考虑的问题是 ( )a、尽可能减少⼯序数;b、精度要求⾼的主要表⾯的加⼯问题;c、尽可能避免使⽤专⽤机床;d、尽可能增加⼀次安装中的加⼯内容。
10.零件上孔径⼤于30mm的孔,精度要求为IT9,通常采⽤的加⼯⽅案为( )a、钻-镗b、钻-铰c、钻-拉d、钻-扩-磨11.编制零件机械加⼯⼯艺规程、⽣产计划和进⾏成本核算最基本的单元是( )a、⼯步b、⼯位c、⼯序d、⾛⼑12.零件在加⼯过程中,粗基准⼀般选择: ( )a、⼯件的⽑坯⾯b、⼯件的已加⼯表⾯c、⼯件上的⼤平⾯13.单件⼩批⽣产装配精度要求⾼组成环多应选()法装配。
a、完全互换法b、分组互换法c、调整法d、修配法14.若装配精度要求⾼组成环少(3环)⼤批量⽣产时应选()法装配。
机械制造技术基础第六章课后题答案
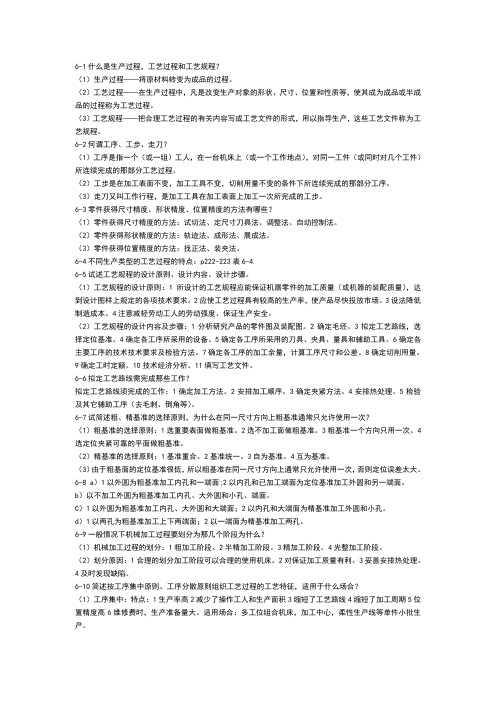
6-1什么是生产过程,工艺过程和工艺规程?(1)生产过程——将原材料转变为成品的过程。
(2)工艺过程——在生产过程中,凡是改变生产对象的形状、尺寸、位置和性质等,使其成为成品或半成品的过程称为工艺过程。
(3)工艺规程——把合理工艺过程的有关内容写成工艺文件的形式,用以指导生产,这些工艺文件称为工艺规程。
6-2何谓工序、工步、走刀?(1)工序是指一个(或一组)工人,在一台机床上(或一个工作地点),对同一工件(或同时对几个工件)所连续完成的那部分工艺过程。
(2)工步是在加工表面不变,加工工具不变,切削用量不变的条件下所连续完成的那部分工序。
(3)走刀又叫工作行程,是加工工具在加工表面上加工一次所完成的工步。
6-3零件获得尺寸精度、形状精度、位置精度的方法有哪些?(1)零件获得尺寸精度的方法:试切法、定尺寸刀具法、调整法、自动控制法。
(2)零件获得形状精度的方法:轨迹法、成形法、展成法。
(3)零件获得位置精度的方法:找正法、装夹法。
6-4不同生产类型的工艺过程的特点:p222-223表6-4.6-5试述工艺规程的设计原则、设计内容、设计步骤。
(1)工艺规程的设计原则:1所设计的工艺规程应能保证机器零件的加工质量(或机器的装配质量),达到设计图样上规定的各项技术要求。
2应使工艺过程具有较高的生产率,使产品尽快投放市场。
3设法降低制造成本。
4注意减轻劳动工人的劳动强度、保证生产安全。
(2)工艺规程的设计内容及步骤:1分析研究产品的零件图及装配图。
2确定毛坯。
3拟定工艺路线,选择定位基准。
4确定各工序所采用的设备。
5确定各工序所采用的刀具、夹具、量具和辅助工具。
6确定各主要工序的技术技术要求及检验方法。
7确定各工序的加工余量,计算工序尺寸和公差。
8确定切削用量。
9确定工时定额。
10技术经济分析。
11填写工艺文件。
6-6拟定工艺路线需完成那些工作?拟定工艺路线须完成的工作:1确定加工方法。
2安排加工顺序。
3确定夹紧方法。
- 1、下载文档前请自行甄别文档内容的完整性,平台不提供额外的编辑、内容补充、找答案等附加服务。
- 2、"仅部分预览"的文档,不可在线预览部分如存在完整性等问题,可反馈申请退款(可完整预览的文档不适用该条件!)。
- 3、如文档侵犯您的权益,请联系客服反馈,我们会尽快为您处理(人工客服工作时间:9:00-18:30)。
机械制造技术基础
6.1.2加工表面质量
表面质量对零件配合性质的影响
表面粗糙度值的大小将影响配合表面的配合质 量。对于间隙配合,粗极度值大会使磨损加大,间 隙增大,破坏了要求的配合性质。对于过盈配合, 装配过程中一部分表面凸峰被挤平,易使工件发生 变形, 影响配合质量.实际过盈量减小,降低了配合 件间的连接强度。 表面物理力学性能的变化易使工件发生变形, 影响配合质量.
机械制造技术基础
6.2.2影响加工精度的因素
传动链的传动误差
传运链的传动误差: 指内
联系的传动链中首、末两端传 动元件之间相对运动的误差。
传动链传动误差, 一般不
影响圆柱面和平面的加工精度, 但在加工工件运动和刀具运动 有严格内联系的表面, 如车削、 磨削螺纹和滚齿、插齿、磨齿 时, 则是影响加工精度的重要 因素。
机械制造技术基础
6.1.1加工精度的概念
加工精度与加工误差
尺寸精度:加工后,零件的实际尺寸与零件尺寸公差 带中心的符合程度。 形状精度:加工后,零件表面的实际几何形状与理想 的几何形状的相符合程度。 位臵精度:加工后,零件有关表面之间的实际位臵与 理想位臵的符合程度。 关系: 三者之间是既有区别又有联系的。通常,形状 公差应限制在位臵公差之内,而位臵误差又要限制 在尺寸公差之内。
表面层的物理力学性能
1)表面层的冷作硬化 是指零件在机械加工中表面层 金属产生强烈的冷态塑性变形后,引起强度和硬度都有 所提高的现象。 2)表面层金相组织的变化 是指在机械加工过程中, 由于切削热的作用引起表面层金属的金相组织发生变化 的现象。 3)表面层残余应力 是指由于加工过程中切削力和切 削热的综合作用,使表面层金属产生内应力的现象。
体支撑孔及与轴承相配合零件有关表面的加工精度和装配精度, 对高速主轴部件进行动平衡,对滚动轴承进行预紧等。
工件回转型(车床)
刀具回转型(镗床)
机械制造技术基础
6.2.2影响加工精度的因素
导轨误差
机床导轨副是机床中确定各主要部件位臵关系的 基准,是实现直线运动的主要部件。 机床导轨的精度要求主要有以下三个方面: ① 导轨在水平面内的直线度误差1 ② 导轨在垂直面内的直线度误差2 ③ 前后导轨的平行度误差(扭曲度)3
用模数铣刀成形铣削齿轮时,模数相同而齿数不同的齿轮, 其齿形参数是不同的
机械制造技术基础
6.2.2影响加工精度的因素
机床误差
机床误差是由机床的制造误差、安装误差和使用中 的磨损引起的。 对加工精度影响较大的有:
(1)主轴回转误差 (2)导轨误差 (3)传动链误差
机械制造技术基础
6.2.2影响加工精度的因素
机械制造技术基础
第6章 机械加工质量
机械制造技术基础
6.2.1 加工原始误差与误差敏感方向
原始误差
工艺系统:机床、夹具、刀具和工件等组成的系统。 原始误差:工艺系统中直接引起加工误差的因素。
原理误差 装卡误差 调整误差 加工前 机床误差 工艺系统静 夹具误差 误差 刀具制造误差 刀具磨损 工艺系统动 加工中工艺系统受力变形 误差 工艺系统受热变形
机械制造技术基础
6.1.2加工表面质量
表面质量对零件疲劳性能的影响
物理力学性能疲劳强度的影响 残余拉应力将使疲劳裂纹扩大,残余压应力能 阻止裂纹扩展,延缓疲劳破坏; 冷作硬化一般伴有残余压应力的产生,可以防 止裂纹产生并阻止已有裂纹的扩展,有利于提高零 件抗疲劳强度; 表面渗碳、淬火等使金属表面产生压应力,对 疲劳强度有利; 镀铬、镍等使金属表面产生拉应力, 对疲劳强度不利。
与初始状态 有关
原始误差
内应力引起的变形 加工后 测量误差
与工艺过程 有关
机械制造技术基础
6.2.1 加工原始误差与误差敏感方向
误差敏感方向
刀具位移为δ时,产生的误差ΔR为:
R OA OA R 2 R cos R cos
' 2 2
___
机械制造技术基础
6.2.2影响加工精度的因素
原理误差
加工原理误差是指由于采用了近似的加工方法、近似的
成形运动或近似的刀具轮廓进行加工所产生的误差。为 了获得规定的加工表面,刀具和工件之间必须实现准确 的成形运动,机械加工中称此为加工原理。 例:齿轮滚齿加工用的滚刀就有两种原理误差:一是近似
廓型原理误差;二是由于滚刀刀刃数有限。
6.1.2加工表面质量
表面质量对零件耐磨性的影响
表面纹理对耐磨性的影响
表面纹理的形状及刀纹方向对耐磨性也有一定影响。原因在于纹 理形状及刀纹方向影响有效接触面积和润滑液的存留。圆弧状、凹 状表面纹理的耐磨性好。尖峰状接触面压强大,耐磨性差。 运动方向与刀纹方向相同时,耐磨性好,垂直时,耐磨性最差。
表面冷作硬化对耐磨性的影响
机械制造技术基础
6.1.2加工表面质量
表面质量对零件抗腐蚀性的影响
零件表面粗糙度值越大,潮湿空气和腐蚀介质越容 易堆积在零件表面四处而发生化学腐蚀,或在凸峰间产 生电化学作用而引起电化学腐蚀,故抗腐蚀性能越差。 表面冷硬和金相组织变化都会产生内应力。零件在 应力状态下工作时,会产生应力腐蚀,若有裂纹,则更 增加了应力腐蚀的敏感性。因此表面内应力会降低零件 的抗腐蚀性能。 表面层的残余压应力能防止腐蚀开裂,残余拉应力 降低耐腐蚀性
机械制造技术基础
6.2.2影响加工精度的因素
传动链的传动误差
减小传动链误差的措施:
① 减少传动环节,缩短传动链, 以减少误差来源。 ② 提高传动元件,特别是末端传 动元件的制造精度和装配精度。 ③ 传动链中按降速比递增的原则 分配各传动副的传动比。 ④ 采用误差校正机构。
机械制造技术基础
6.2.2影响加工精度的因素
机械制造技术基础
6.1.2加工表面质量
表面质量对零件耐磨性的影响
一般情况下,表面粗糙度 值越小,表面耐磨性越好。但 是表面粗糙度值太小,接触表 面分子亲和力大,且润滑液不 易储存,磨损反而加剧。 表面粗糙度的最佳值与零 件的工况有关,工作载荷加大 时,初期磨损量增大,表面粗 糙度的最佳值也增大。
机械制造技术基础
机械制造技术基础
6.2.2影响加工精度的因素
夹具误差 夹具误差:主要是指夹具的定位元件、导向元件及夹具体等零件 的加工与装配误差。 它将直接影响到工件加工表面的位臵精度或尺寸精度,对被 加工工件的位臵精度影响最大。 在设计夹具时,凡影响工件精度的有关技术要求必须给出严 格的公差。粗加工用夹具一般取工件相应尺寸公差的1/5~1/10。 精加工用夹具一般取工件相应尺寸公差的1/2~1/3。 夹具磨损将使夹具的误差增大,从而使工件的加工误差也相 应增大。为了保证工件的加工精度,除了严格保证夹具的制造精 度外,还必须注意提高夹具易磨损件的耐磨性,当磨损到一定限 度以后,必须及时予以更换。
即要求主
机械制造技术基础
6.2.2影响加工精度的因素
主轴回转误差
端面圆跳动:影响车端面时工件端面的垂直度、平面度和工 件的轴向尺寸;影响车螺纹时的螺距。 径向圆跳动:影响工件圆柱面的圆度和圆柱度。
角度摆动 :影响工件圆柱面的圆柱度和端面的形状。
主轴回转误差实际上是上述三种误差形式的合成。
机械制造技术基础
机械制造技术基础
6.2.2影响加工精度的因素
导轨误差 导轨在水平面内的直线度误差1
此项误差使刀尖在水平面内产生移Δy ,造成工件在半 径方向的误差ΔRy (这时ΔRy=Δy), 使工件表面产生圆柱度
误差。
机械制造技术基础
6.2.2影响加工精度的因素
导轨误差
导轨在垂直面内的直线度误差2
2 2 R0 z 2 (R0 Rz )2 R0 2R0RZ Rz2
∴ΔRz≈Δz2/(2R0), 定义工件加工表面法线方向叫做误差的敏 感方向. 设Δy= Δz=0.1mm, R=20mm, 那么ΔRy= Δy=0.1mm, ΔRz=0.00025mm, ΔRy=400ΔRz.
机械制造技术基础
6.2.2影响加工精度的因素
导轨误差 前后导轨的平行度误差(扭曲度)3 由于导轨发生了扭曲, 使 刀尖相对于工件在水平和垂直 两个方向上产生偏移. 设车床 中心高为H, 导轨宽度为B, 则 导轨扭曲量Δ引起工件半径的 变化量ΔRy为: R y : H : B
6.2.2影响加工精度的因素
主轴回转误差 影响主轴回转误差的因素:主轴支撑轴颈的误差、轴承的误差、
轴承的间隙、箱体支撑孔的误差、与轴承相配合零件的误差及主 轴刚度和热变形等。对于不同类型的机床,其影响因素也是不相 同的。
分析主轴采用滑动轴承时主轴的径向圆跳动:分两种情况: 提高主轴回转精度的措施:提高轴承精度,提高主轴轴颈、箱
占成本的比重
机械制造技术基础
6.1 概述
加工质量
尺寸精度
加工精度 零 件 的 加 工 质 量
宏观几何形状精度:圆度、圆柱度、平面度等 位臵精度:同轴度、平行度、圆跳动等
微观几何形状误差:表面粗糙度
表面质量
波度 表层冷作硬化 物理机械性能 表层金相组织变化 表层残余应力
机械制造技术基础
6.1.1加工精度的概念
H R y B
通常, 车床H/B≈2/3;外圆磨床H/B≈1, 可见此项误差对 加工精度影响很大, 会导致工件产生圆柱度误差.
机械制造技术基础
6.2.2影响加工精度的因素
导轨误差
影响导轨误差的其它因素:导轨导向精度, 除受导轨制 造误差的影响外, 还受机床安装是否正确, 地基是否坚固, 导轨的润滑状况, 磨损的均匀性, 导轨的热变形以及运动 部件的重心移动和过大切削力引起的导轨弹性变形等因 素的影响. 提高机床导轨精度的措施:提高机床导轨、溜板的制造 精度及安装精度,采用耐磨合金铸铁、镶钢导轨、贴塑 导轨、滚动导轨、静压导轨、导轨表面淬火等措施提高 导轨的耐磨性,正确安装机床和定期检修 等。