我国轴承零件热处理现状及对策
热处理中的轴承热处理技术

热处理中的轴承热处理技术轴承是机械工业中不可或缺的部分,它的质量直接影响到机器的性能和使用寿命。
轴承的热处理技术是制造高品质轴承的重要一环。
本文将讨论热处理中的轴承热处理技术。
1. 热处理的定义和目的热处理是指将金属制品加热到一定温度,保持一定时间,然后冷却至室温的工艺。
热处理的目的是改变金属材料的组织结构、性质和形状,以获得满足设计要求的性能指标。
在轴承的热处理中,应用最为广泛的是淬火、回火、正火和表面强化等方法。
而这些方法选择的依据则是轴承所要求的性能和工作条件。
2. 淬火技术淬火是一种将金属加热至高温,然后在水或油中迅速冷却的热处理方法。
淬火的目的是将钢的组织变为马氏体,增加硬度和强度。
在轴承的热处理中,淬火主要应用于内、外圈和滚子等零件的加工。
淬火后的零件硬度高、耐磨性好、抗疲劳性能强。
但另一方面,淬火的缺点是易产生裂纹和变形,从而影响轴承的使用效果。
因此,在轴承淬火的过程中,需经过多次淬火和回火操作,以减少材料的内部应力和变形,从而保证轴承的品质。
3. 回火技术回火是指在淬火后,将零件再次加热到中低温度,并保温一定时间,然后迅速冷却的热处理方法。
回火的目的是消除淬火后产生的内应力和提高零件的韧度和韧性。
在轴承的热处理中,回火主要应用于内、外圈及滚子等零件,以消除淬火过程中产生的内应力和提高零件的韧性。
回火的加热温度和保温时间的选择应根据不同材料的工作条件和性能要求来决定。
4. 正火技术正火是指将零件加热至一定温度,然后进行持续保温,最后冷却的热处理方法。
正火的目的是使零件的组织达到均匀化,提高零件的强度和韧性。
在轴承的热处理中,正火通常应用于轴承外壳零件的加工。
正火的加热温度和保温时间的选择应根据材料的性能进行确定,以达到设计要求。
5. 表面强化技术表面强化是指在材料表面形成一层用于提高材料表面耐磨性和抗疲劳性的物理、化学、热力学或机械层。
表面强化一般分为热处理、渗碳、硝化、电火花加工和喷涂等。
改善热处理质量提高轴承寿命

A s atT e r ni n n f nrl c i r n ig2 o r a dt i l er gi ui s ne r b l c: h kevr met ea mah eyr nn 4h us n pc a n jr gi t cs e I wo o o mi n u y ab i n n n a a
维普资讯
・ 8・ 2
哈
尔
滨
轴
承
第2 8卷
下 连续工 作 , 同时 它 的工 作 环境 比较 恶劣 , 以要 所 求 这类轴 承 在制造 时 必须有 较 高 的抗 塑性 变 形能 力 , 的摩擦 磨损 , 的旋转 精度 、 的 尺寸精 度 、 少 好 高 好 的尺寸稳定 性 以及较 长 的使 用寿命 ,这其 中有
I r v n e t r ame t u l y t as e vc f f e r g mp o i gh a e t n ai or ie sr ief eo b a i t q t i n
Wa gQ uiMa igh n Z a o g n il , n c u , h oY n J
Ke r s e r g h g l b l y mae il ywo d :b a i ; ih r i i t ; t r n ea i a
1 前 言
随 着 国民经 济 的发展 ,国 内用 户对轴 承 的性
矿 山机 械设 备 使 用 的 轴 承是 多种 多 样 的 , 其
轴承零件经热处理后会出现哪些问题

轴承零件经热处理后会出现哪些问题轴承零件经热处理后常见的质量缺陷有:淬火显微组织过热、欠热、淬火裂纹、硬度不够、热处理变形、表面脱碳、软点等。
1.过热从轴承零件粗糙口上可观察到淬火后的显微组织过热。
但要确切判断其过热的程度必须观察显微组织。
若在GCr15钢的淬火组织中出现粗针状马氏体,则为淬火过热组织。
形成原因可能是淬火加热温度过高或加热保温时间太长造成的全面过热;也可能是因原始组织带状碳化物严重,在两带之间的低碳区形成局部马氏体针状粗大,造成的局部过热。
过热组织中残留奥氏体增多,尺寸稳定性下降。
由于淬火组织过热,钢的晶体粗大,会导致零件的韧性下降,抗冲击性能降低,轴承的寿命也降低。
过热严重甚至会造成淬火裂纹。
2.欠热淬火温度偏低或冷却不良则会在显微组织中产生超过标准规定的托氏体组织,称为欠热组织,它使硬度下降,耐磨性急剧降低,影响轴承寿命。
3.淬火裂纹轴承零件在淬火冷却过程中因内应力所形成的裂纹称淬火裂纹。
造成这种裂纹的原因有:由于淬火加热温度过高或冷却太急,热应力和金属质量体积变化时的组织应力大于钢材的抗断裂强度;工作表面的原有缺陷(如表面微细裂纹或划痕)或是钢材内部缺陷(如夹渣、严重的非金属夹杂物、白点、缩孔残余等)在淬火时形成应力集中;严重的表面脱碳和碳化物偏析;零件淬火后回火不足或未及时回火;前面工序造成的冷冲应力过大、锻造折叠、深的车削刀痕、油沟尖锐棱角等。
总之,造成淬火裂纹的原因可能是上述因素的一种或多种,内应力的存在是形成淬火裂纹的主要原因。
淬火裂纹深而细长,断口平直,破断面无氧化色。
它在轴承套圈上往往是纵向的平直裂纹或环形开裂;在轴承钢球上的形状有S形、T形或环型。
淬火裂纹的组织特征是裂纹两侧无脱碳现象,明显区别与锻造裂纹和材料裂纹。
4.热处理变形轴承零件在热处理时,存在有热应力和组织应力,这种内应力能相互叠加或部分抵消,是复杂多变的,因为它能随着加热温度、加热速度、冷却方式、冷却速度、零件形状和大小的变化而变化,所以热处理变形是难免的。
我国轴承零件热处理现状及对策

我国轴承零件热处理现状及对策随着主机的高速化、轻量化,轴承的工作条件更加苛刻,对轴承的性能要求越来越高,如更小的体积、更轻的质量、更大的承载容量、更高的寿命和可靠性等。
其中,国产轴承的寿命和可靠性成为近年来越来越突出的问题,开发热处理新技术、提高热处理质量一直是国内外轴承生产企业及相关企事业单位关注的课题。
本文对近年来来年热处理技术的进展进行综述,以期对我国的轴承行业相关人员有所借鉴。
1. 高碳铬轴承钢的退火高碳铬轴承钢的理想退火组织是铁素体基体上分布着细、小、匀、圆的碳化物颗粒的组织,为以后的冷加工及最终的淬回火作组织准备。
目前,除少数企业使用周期式设备外,普遍使用的是无保护气氛的单通道推杆式等温退火炉。
退火的组织和硬度控制已比较成熟可靠,可较容易地把退火组织控制在JB1255标准中的2~3级或细点组织。
存在的问题是能耗偏高、退火后氧化脱碳严重。
近年来,从节能的角度出发,开发了油电复合加热等温退火炉、双室首尾并置(水平或上下)的等温退火炉,节能效果显著,应大力推广;同时,随着毛坯精密成形工艺和设备的出现,开始采用氮基保护气氛等温退火炉,以减少退火过程中的氧化脱碳,降低原材料的消耗和机加工成本。
2. 高碳铬轴承钢的马氏体淬回火常规的高碳铬轴承钢马氏体淬回火工艺的发展主要分3个方面:一是开展淬回火工艺参数对组织和性能影响的基础性研究,如淬回火过程中的组织转变、残余奥氏体的分解、淬回火后的韧性与疲劳性能等;二是淬回火的工艺性能的研究,如淬火条件对尺寸和变形的影响、尺寸稳定性等;三是取缔氧化或保护气氛加热,推广可控气氛加热。
2.1 组织与性能常规马氏体淬火后的组织为马氏体、残余奥氏体和未溶(残留)碳化物组成。
轴承钢淬火后马氏体基体含碳量为0.55%左右,组织形态一般为板条和片状马氏体的混合组织,或称介于二者之间的中间形态—枣核状马氏体,轴承行业上所谓的隐晶马氏体、结晶马氏体;其亚结构主要为位错缠结以及少量的孪晶。
谈轴承热处理的质量和新技术的研发

谈轴承热处理的质量和新技术的研发摘要:当前轴承钢的质量满足了市场需求。
轴承钢工艺及技术要求已全部实现了国家标准,因此本篇文章重点针对于轴承的基本构造特征,以及对轴承用钢热处理技术的基本需求,重点阐述了轴承零件的热处理工艺、轴承热处理的主要工艺问题,以及技术改善方法。
关键词:轴承热处理;质量缺陷;新技术研发引言:轴承钢作为基础零件,良好的热加工性能是增加轴承结构寿命的关键措施。
影响轴承的热处理品质的主要原因包括:原材料的冶金品质、铸造技术和预备热处理技术,还有最终热处理的装备、技术以及淬火的高温冷却材料的选用等。
而对相关企业来说,其热处理品质也受到了足够的关注,为了提高轴承热处理的质量以及新技术研发,需要展开深入探究。
1轴承热处理的概述轴承钢是用来制作滚动轴承的滚动体和套圈,考虑到轴承钢的使用,轴承钢需要具有长时间的使用寿命,具有耐用性以及较好的质量,同时其刚度也需要符合相关标准,保持较低的噪音,具备一定的耐腐蚀性能等,而为满足这些特性需要,对轴承钢的化学结构均匀度、非金属材料中掺杂的数量和种类、碳化物颗粒尺寸和分布状态、脱碳性能等均规定了要求。
滚轮支座零件通常为点接触或线接触的机械构件,需要经受一定的压力,会导致遭受挤压或者剪切状况,在这种环境下需要保持长时间的正常工作,其作用部位通常是在机械的核心或滑膜关节上的核心部分。
所以,机械的准确度、寿命和稳定性都在很大程度上取决于滚轮支座。
针对于各种机械运动的支撑,应用环境较为复杂,因此,不论是普通轴承还是特种专用轴承,它对其寿命、效率和稳定性都有着高度的要求。
但是,对轴承使用的影响因素较多,其中轴承的构成材料尤为重要,还有热处理技术也会影响轴承的耐用性。
轴承的结构特性和工作状态,要求轴承的原材料具有一定的硬度,同时具备较好的耐磨性能以及耐腐蚀性能,也需要根据实际使用环境,准备合适的尺寸。
一般规定轴承的为了符合这些要求,对轴承所使用钢的冶金要求也就必须符合严格的物理化学组成,同时还有严格的碳化物不均衡性的要求;而且,也可能存在外观与内部缺陷。
轴承回火不充分的热处理返工

如果轴承的回火不充分,可以考虑以下几种方法进行返工处理:
1. 重新回火:将轴承重新加热到适当的温度,保持一定时间,然后缓慢冷却。
这可以帮助消除内部应力并改善材料的韧性。
2. 调整回火温度和时间:如果之前的回火温度或时间不足,可以适当提高温度或延长时间来达到更好的效果。
但需要注意避免过度回火,以免影响轴承的硬度和强度。
3. 采用二次回火:在第一次回火后,再次进行回火处理。
这可以进一步降低内部应力,并提高轴承的韧性和稳定性。
4. 进行局部回火:如果轴承的某个区域回火不充分,可以针对该区域进行局部回火处理。
这可以通过局部加热和冷却来实现。
5. 咨询专业人士:如果对回火处理不确定或存在困难,建议咨询专业的热处理工程师或相关技术人员,以获取更准确的建议和指导。
需要注意的是,在进行任何热处理返工之前,必须仔细评估轴承的材料和使用条件,以确保处理方法的可行性和有效性。
同时,正确的操作和设备也是保证处理效果的关键。
轴承热处理、滚动体专用设备研发成果及发展趋势

,
舟电炉有限公司近年来在传统等温
球化退火炉基础上开发研制的轴承
锻件退火专用设备 ,是一 种适 用于
了滚动体成品质量 此外, 相关技术也越来越受到人们的重视, 随着对产 品精度要求的不断提高 已研发出新一代磨具磨料, 如钢球研磨板、 研磨
。
,
液
、
轴承行业大批量连续生产的新型退
火炉。
树脂砂轮、滚子外径超精油石、切削液等。 因此 通过 六五 ”及 t ・ t ,期间广大科技人 员的共 同努力 , 国 十五 , 我
, ,
已基本具备定一个水平的成套轴承滚动体的制造技术和相应的工艺装备
3国内 . 外轴承热处理专用设
而且有的 设备在精度和性能方面已 达到或接近国 业发达国 外工 家同 类产品
备发展趋势
() 1国内轴承热处理专用设备发
水平。
2 滚动体专用设备、 仪器改进和研发成果
.
展趋势 发展和应用贝氏体等温淬 火工艺装备;轴承采用贝氏体等温
基础上,国内已开发研制成功可控
气氛网带炉生产线和可控气氛铸链
炉生产线,并 已系列化生产。目前 中小型轴承套圈的新增热处理装备
基本都是采用这两种生产线,其工 艺和质量水平与国外先进水平相当。 随着技术改造的持续进行,它们将
பைடு நூலகம்
逐步取代原有的输送带炉生产线、
震底炉生产线、 箱式炉等落后炉型。
靠性 。
:嘉
钢 动 机 改 传 开 料 ,闭筒 、 球 冷 系 变 统 式 方采 式 切 自墩 列 了 的 切 式 套
钳送料 、 上冲模座 与机 身固定 ,与 主滑块 分离 、 自动强迫润滑 、 封l 全 全 羽
滚动轴承的热处理

滚动轴承的热处理目的:提高滚动轴承强度、韧性、耐磨性、抗疲劳强度以及良好的尺寸稳定性。
同时通过特殊的热处理是其具有耐腐蚀、耐高温,防磁等特性。
常用的热处理方式有:退火(Th),它是将金属加热到所需的温度并经过一定时间的保温,然后再缓慢冷却(一般是随炉冷却),退火可降低金属的硬度和脆性,增加塑性,消除内应力等。
正火(Z),它是将金属加热到临界温度以上,并经过一定时间的保温,然后在静止的空气中冷却。
正火可以细化晶粒,改善机械性能鱼切削性能。
淬火(C),它是将金属加热到所需温度,保温后放入淬火剂中冷却,是温度骤然降低。
淬火可增加金属的硬度,但会降低其塑性。
回火,它是将淬火后的金属重新加热到一定的温度然后再用一定的方式进行冷却。
根据回火温度的不同回火可分为,高温回火,中温回火以及低温回火。
回火的目的是为了消除因淬火产生的内应力,降低硬度和脆性,以获得所需的机械性能。
调质,即是所说的淬火加高温回火,这样可以得到所需的强度和韧性。
经过调质处理的钢一般叫调质钢,多指中碳钢和中碳合金结构钢。
钢中的主要金相组织:奥氏体(A)它是碳溶于γ-Fe中形成的固溶体,具有面心立方结构,溶碳能力较铁素体强,机械性能随含碳量的变化而变化,由于它是固溶体,所以不论含碳多少,塑性都很好,而且无磁性。
碳素钢在727°C以上平衡组织中才能看见奥氏体,在有些合金钢中,由于合金元素的作用,在室温下也能得到奥氏体。
铁素体(F)它是碳溶于α-Fe中形成的固溶体,具有体心立方结构,溶碳能力极小,所以也叫纯铁体。
其性能也与纯铁极为相似,即强度、硬度很低,塑性韧性很高,在768°C一下又磁性。
渗碳体(Fe3C),铁与碳形成的化合物,含碳高达6.69%,晶格结构很复杂,其硬度大脆性大,强度低塑性几乎为零。
热处理对轴承质量的影响

首先说一点自己的看法;
1.热处理的质量直接影响轴承的寿命,热处理温度过高导致晶粒粗大,容易存在淬火裂纹,淬火温度过低,硬度会稍微的降低,就是所谓的欠热。
2.回火温度过高将导致硬度下降,应力去除的比较好。
回火温度过低,材料的硬度较高但是,应力就很难出去,故轴承钢一般采用150~180的回火温度。
3.预备热处理对轴承寿命的影响,特别是球化处理,如果球化不理想或者不均匀,容易造成碳化物浓度不均,在淬火的时候,套圈的变形量将增加很多,并且胀大或者缩小不具有规律性,容易导致变形大引起的余量不足的报废、
4,锻造对轴承寿命的影响,锻造可算轴承制造的第一道热处理,如果锻造温度过高,晶粒粗大,淬火容易裂开,锻造比小的话容易造成碳化物不均匀,同样会影响淬火的变形和开裂。
锻造次数不够容易遗留锻造组织,要坚决杜绝,锻造的碳化物液析碳化物偏析碳化物带状均会影响最终的淬火处理。
从以上可以看出,锻造退火淬火回火都对轴承的寿命起到决定性的作用,所以如果想做好轴承就应该控制好这4个基本的热处理步骤而不是单纯的控制淬火工序有时候热处理厂家的确吃了很多窝囊呵呵明明是锻造的原因,但是最后一般都会推到热处理。
轴承零件热处理

快冷 炉冷至650℃后出炉
2~5
2~4 时间/h
4.4.4 快速退火
温度/℃
900~910 780±10
30~50 min 正火
2~2.5 退火
冷却 60~90℃/h 至650℃
时间/h
五、套圈的淬火
5.1
淬火的含义 将钢加热到临界点A”c1~AcM之间某一温度, 保温一段时间,然后快速(大于临界速度)冷却 下来的热处理过程叫淬火。
总之,通过热处理改变珠光体中碳化物的形状、粗细和分布,
可以控制钢的强度和硬度,在相同的抗拉强度下,球状的珠 光体比片状的疲劳强度有所提高。
2.5 马氏体——C在α -Fe中的过饱和固溶体,
体心正方晶体。 马氏体最主要的特征就是高硬度、高强度, 其硬度随着马氏体中碳含量的增加而升高, 当碳含量达到0.6%时,淬火钢的硬度接近最 大值,但塑性和韧性却明显下降。
825~ 830
830~ 835
835~ 840
840~ 845
保温时间 min
5~7
6~8
7~10
9~12
11~1 5
14~1 6
16~1 8
18~2 0
20~2 4
24~26
5.6淬火加热时间的计算
在淬火温度范围内,还要根据具体工艺条件来确定
具体的温度和时间,淬火加热时间的计算见下式:
t= a√ s
900~920 880~910
890~900 870~890
3.4 正火工艺的其它工艺要求
1) 正火的保温时间为30~50min;
2) 薄壁锻件,散开空冷或吹风冷却即可; 3) 壁厚较厚的锻件,需采用喷雾、浸油或浸
乳化液等手段快速冷却; 4) 不论何种冷却方法,冷速必须≥50℃/min。
高温环境下轴承紧固件性能的研究与改进方案
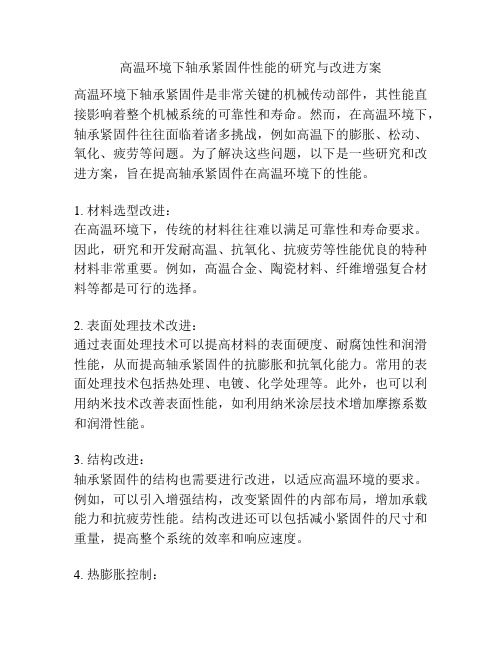
高温环境下轴承紧固件性能的研究与改进方案高温环境下轴承紧固件是非常关键的机械传动部件,其性能直接影响着整个机械系统的可靠性和寿命。
然而,在高温环境下,轴承紧固件往往面临着诸多挑战,例如高温下的膨胀、松动、氧化、疲劳等问题。
为了解决这些问题,以下是一些研究和改进方案,旨在提高轴承紧固件在高温环境下的性能。
1. 材料选型改进:在高温环境下,传统的材料往往难以满足可靠性和寿命要求。
因此,研究和开发耐高温、抗氧化、抗疲劳等性能优良的特种材料非常重要。
例如,高温合金、陶瓷材料、纤维增强复合材料等都是可行的选择。
2. 表面处理技术改进:通过表面处理技术可以提高材料的表面硬度、耐腐蚀性和润滑性能,从而提高轴承紧固件的抗膨胀和抗氧化能力。
常用的表面处理技术包括热处理、电镀、化学处理等。
此外,也可以利用纳米技术改善表面性能,如利用纳米涂层技术增加摩擦系数和润滑性能。
3. 结构改进:轴承紧固件的结构也需要进行改进,以适应高温环境的要求。
例如,可以引入增强结构,改变紧固件的内部布局,增加承载能力和抗疲劳性能。
结构改进还可以包括减小紧固件的尺寸和重量,提高整个系统的效率和响应速度。
4. 热膨胀控制:由于高温环境下材料的热膨胀性能增大,紧固件易出现松动现象。
为了解决这个问题,可以采用一些控制热膨胀的方法。
例如,可以在轴承紧固件与轴承座之间添加弹簧垫片、金属套筒等缓冲材料,以吸收热膨胀引起的松动。
此外,也可以采用预紧力控制技术,即在设计过程中考虑热膨胀因素,使紧固件在高温下保持一定的预紧力,避免松动。
5. 润滑改进:在高温环境下,润滑是非常重要的,可以起到减小摩擦、降低温度和延长寿命的作用。
因此,需要选择耐高温的润滑材料,并采用合适的润滑方式,如液体润滑、固体润滑或气体润滑等。
此外,还可以改进轴承紧固件的润滑系统,增加润滑油的循环和冷却方式,以保证持续有效的润滑。
综上所述,高温环境下轴承紧固件性能的研究与改进是一个复杂而有挑战性的任务。
轴承钢热处理应注意的几个问题

轴承钢热处理应注意的几个问题,很专业硬度1.退火硬度:热处理前要检验退火状态零件的硬度及组织。
GCr15:179-207HB(88-94HRB),其他为179-217HB(88-97HRB)。
若硬度不合格(过高、过低或不均匀),都要认真分析原因,可能对淬火产生影响(如,硬度不够,脱碳,过热,椭圆大等)。
2.淬回火硬度:壁厚不大于12mm时,淬火后≥63HRC,回火后60-65HRC;可能会遇到客户提出特殊的硬度要求,如61-64HRC等,但回火后硬度公差范围要大小于3HRC;正常淬火时,硬度值主要取决于回火温度。
3.硬度均匀性:标准规定,同一零件硬度均匀性一般为1HRC;外径大于200mm,不大于400mm时为2HRC;大于400mm时为3HRC.硬度不合格的表现:(1)硬度高:淬火温度高或加热时间长,冷速过快,碳势高(有增碳)。
(2)硬度低:淬火温度低或加热时间短,冷速慢,碳势低(有脱碳),材料脱碳。
(3)硬度不均匀:淬火温度低或加热时间短,冷速慢,材料脱碳,棍棒阴影。
金相组织1.马氏体正常情况下,GCr15的淬火温度为840 ℃左右,一般不超过850℃。
GCr15SiMn的淬火温度为820℃左右,一般不超过835℃。
过高或过低的温度会造成马氏体的过热或欠热。
标准规定马氏体1—5级合格(微型零件1—3级)。
加严为1—4级。
对于壁厚小(一般6-7mm以下)的产品可以1—3级。
马氏体粗细主要与加热温度和加热时间有关。
2.贝氏体贝氏体等温淬火一般使用的材料为GCr15 和GCr18Mo,GCr15钢加工的零件有效厚度多是控制在30mm内,GCr18Mo可以扩展到65mm。
加热温度:不论是GCr15还是GCr18Mo,温度多865~890℃;等温温度:不论是GCr15还是GCr18Mo,其Ms点一般为225℃,等温温度常用235-245℃。
保温时间:一般不应小于4小时。
按JB/T1255标准评定1-3级合格,贝氏体主要与加热温度和加热时间,等温温度及时间有关。
我国轴承用材料及热处理技术近期发展动态_雷建中

《轴承》2011. №. 9
于公称尺寸 > 150 mm 的套圈,在淬火后普遍采用 压模淬火整形保证小的畸变量。在我国,压模淬 火技术 主 要 用 于 渗 碳 轴 承 零 件 的 淬 火 畸 变 量 控制。
( 2) 畸变量大。轴承零件淬、回火处理后畸 变量较大是轴承行业长期以来一直存在的问题。 其产生的原因众多且复杂,例如原材料中带状碳 化物严重程度、退火组织优劣、冷加工成形应力大 小、热处理工艺及零件摆放方式( 国外著名轴承 公司网带式淬火炉只允许摆放一层,而且每个零 件之间要有间隙,以保证零件周围温度场的均匀 性。而我国绝大部分企业为了提高劳动生产率, 降低生产成本,均采用多层摆放的方式) 、冷却介 质的合理选择及冷却性能的有效保证、入淬火介 质方式等。
近几年来,我国轴承零件锻造的加热方式发 生了根本性变化,基本实现了感应加热的全覆盖。 由于感应加热速度快,心表存在较大的温度差,导 致热轧材中的网状碳化物( 尤其是靠近材料中心 部位附近区域) 将不同程度地遗留在锻件上。
通过对控制热轧材中网状碳化物组织级别的 工艺研究,将促进我国轴承钢生产企业在控轧控 冷技术方面的进步,不仅解决了网状碳化物的问 题,同时可以起到细化碳化物颗粒尺寸和细化奥 氏体晶粒度的“双细化”作用。
另外,目 前 我 国 轴 承 行 业 所 使 用 的 滚 动 体 ( 特别是钢球) 用材料已绝大部分采用热轧盘圆 作为母材,经退火、冷拔制成所需尺寸要求的冷拔
·59·
材。如果不控制热轧盘圆材料中的网状碳化物的 组织级别,在随后的退火过程中也无法加以改善,
不仅造成大量的废品,还降低钢球的压碎载荷和
滚动轴承材料及热处理之“热处理技术进展”

滚动轴承材料及热处理之“热处理技术进展”1、常规淬回火高碳铬类轴承钢通常采用马氏体淬回火,国内外进行了大量的研究,近年来根据轴承应用工况,提出了一些针对性的研究与应用。
ЧЕРМЕНСКИ.О.Н研究了不同温度回火后硬度对轴承性能的影响。
当轴承载荷产生的接触应力超过σn0(σn0=2.57σ0,σ0为在单向拉伸或压缩时开始塑性变形的应力,取σ0.005),在计算可靠性要求不高的轴承寿命时,硬度在58~64HRC范围内寿命的变化可以忽略不计。
对于精密重载部件用球轴承,不允许在工作过程中因微塑性变形积累而使套圈沟道尺寸发生变化,最好采用高温回火(200~250 ℃);对一般用途的轴承,最好的回火温度不是现在的150~160 ℃,而是提高到170~180℃,不降低寿命且承载能力有所提高。
日本学者樋口博和对汽车变速箱轴承提出了3种长寿命热处理措施:1)增加残余奥氏体以提高滚动疲劳寿命(TM处理),对高碳铭轴承钢进行淬火时,通过提高淬火温度增加残余奥氏体含量。
2)提高回火软化抗力(TA处理),进行碳氮共渗时,由于氮在表层的扩散导致残余奥氏体量增多,此外由于氮的固溶,回火软化抗力上升,进而提高疲劳寿命。
3)晶粒微细化(FA处理),使钢材的晶粒尺寸微细化,缩小到传统材料晶粒尺寸的50%以下,以提高疲劳强度,并组合碳氮共渗处理实现进一步长寿命化。
GHEORGHIES.C,STEFANESCU.I.I对高碳铬轴承钢在磁场中进行淬回火后的组织和性能进行了研究。
在磁场中进行热处理时,马氏体晶粒变小且组织均匀,残余奥氏体减少,硬度可提高(1~2)HRC,抗弯强度提高50%,疲劳可靠度提高(承载时组织不易变化)。
对高碳铬轴承钢在淬火后进行深冷处理可以提高耐磨性。
1)在深冷处理过程中,大量的残余奥氏体向马氏体转变,在磨损过程中向碳化物提供强大的支承并抑制其脱落,阻止大的麻点形成;2)由深冷处理产生的细小碳化物析出并均匀分布,也是耐磨性提高的原因,深冷处理试样中碳化物的分布比那些没进行深冷处理的均匀,且碳化物体积分数更高;3)深冷处理提高了马氏体的转变率,使合金基体组织细化,从而达到细晶强化效果,有助于耐磨性的提高。
“十一五”期间轴承热处理节能技术进展浅议

“十一五”期间轴承热处理节能技术进展浅议摘要:通过材料、热处理工艺和装备技术的发展,分析阐述了“十一五”期间我国轴承行业推广和应用热处理节能技术的进展和效果情况,浅析热处理节能技术持续发展需要解决的问题。
关键词:轴承;热处理;节能;发展Abstract: Through the material, heat treatment technology and equipment technology development, analyzes the “ eleven five” period in China bearing industry promotion and application of heat treatment energy saving technology progress and the effect of heat treatment energy saving technology, sustainable development needs to solve the problem.Key words: bearing; heat treatment; energy saving; development我国轴承行业目前已形成较大的产业规模和独立完整的工业体系。
“十一五”末全国轴承行业规模以上企业达1850家,全行业完成轴承产量150亿套,“十一五”期间年均增长速度20.11%;主营业务收入达1260亿元,年均增长速度19.36%;自主创新体系和能力建设取得很大的进展,各种先进制造技术在轴承生产过程中得到广泛应用和推广。
轴承热处理是耗能大户,设备90%以上采用电加热,电耗占轴承制造业电耗的25-30%。
因此,随着国家对节能减排的重视,轴承热处理的节能减排也是保证轴承行业可持续发展的关键环节。
近年来,随着国家节能、减排执法力度的增强,轴承热处理节能问题得到了各企业领导者的重视,在技术改造方面投入有所提高,“十一五”期间轴承热处理节能技术有了明显进展。
轴承内外圈热处理

轴承内外圈热处理一、概述轴承内外圈热处理是指将轴承内外圈材料加热至一定温度,保持一定时间,然后迅速冷却的过程。
该过程可以改善轴承的硬度、韧性和耐磨性,提高轴承的使用寿命和可靠性。
二、热处理工艺1. 加热将轴承内外圈放入加热炉中,加热至所需温度。
加热温度取决于材料种类和要求的性能。
常用的加热方式有电阻加热、气体加热和电弧加热等。
2. 保温将轴承内外圈在所需温度下保持一段时间,使其达到均匀的组织状态。
保温时间也取决于材料种类和要求的性能。
3. 冷却迅速冷却是保证轴承内外圈组织状态稳定的关键步骤。
常用的冷却方式有水淬、油淬和空气冷却等。
三、影响因素1. 温度加热时所选用的温度会对轴承内外圈的硬度、韧性和耐磨性产生影响。
温度过高会导致轴承内外圈的变形和开裂,温度过低则无法达到所需的性能要求。
2. 保温时间保温时间决定了轴承内外圈材料达到均匀状态的时间。
保温时间过短会导致组织不均匀,保温时间过长则会浪费能源和时间。
3. 冷却速率冷却速率对轴承内外圈的硬度、韧性和耐磨性产生重要影响。
冷却速率过快会导致轴承内外圈开裂,冷却速率过慢则无法达到所需的性能要求。
四、常见问题及解决方法1. 轴承内外圈出现开裂现象解决方法:调整加热温度和保温时间,控制冷却速率。
2. 轴承内外圈硬度不足或过硬解决方法:调整加热温度和保温时间,控制冷却速率。
3. 轴承内外圈表面出现气孔或夹杂物解决方法:加强清洁工作,调整加热温度和保温时间,控制冷却速率。
五、结论轴承内外圈热处理是提高轴承使用寿命和可靠性的重要工艺之一。
在实际生产中,应根据材料种类和要求的性能选择合适的加热方式、温度、保温时间和冷却速率,以确保轴承内外圈达到所需的性能要求。
同时,应加强清洁工作,防止出现气孔或夹杂物等质量问题。
滚动轴承热处理标准

滚动轴承热处理标准滚动轴承的热处理是指通过热处理工艺对轴承零件进行加热、保温和冷却等一系列工序,以改变其组织结构和性能,从而达到提高轴承的硬度、耐磨性、抗疲劳性和抗腐蚀性能的目的。
热处理是滚动轴承制造中不可或缺的重要工艺之一,其质量直接关系到轴承的使用寿命和性能稳定性。
首先,滚动轴承的热处理需要严格按照国家标准或行业标准进行操作。
在热处理过程中,应严格控制加热温度、保温时间和冷却速度等参数,确保轴承零件的热处理质量符合标准要求。
同时,热处理过程中的各道工序也需要严格执行标准规定,避免出现热处理失效或质量不合格的情况。
其次,滚动轴承的热处理要根据不同材质和要求进行选择合适的热处理工艺。
常见的热处理工艺包括淬火、回火、渗碳、氮化等,不同的工艺可以使轴承零件达到不同的硬度、强度和耐磨性。
因此,在选择热处理工艺时,需要根据轴承零件的具体材质和使用要求进行合理的选择,以确保轴承的性能和寿命。
另外,滚动轴承的热处理还需要进行严格的质量控制和检测。
在热处理过程中,需要对加热炉温度、保温时间和冷却速度等参数进行实时监测和记录,以确保热处理过程的稳定性和可控性。
同时,还需要对热处理后的轴承零件进行硬度、组织结构和性能等方面的检测,以验证热处理质量是否符合标准要求。
最后,滚动轴承的热处理还需要做好热处理工艺和质量的管理。
在热处理车间,需要建立健全的热处理工艺文件和质量记录,对热处理设备和工艺进行定期检验和维护,确保热处理设备的稳定性和可靠性。
同时,还需要对热处理工艺和质量进行持续改进,提高热处理工艺的稳定性和可靠性,确保滚动轴承的热处理质量稳定可靠。
总之,滚动轴承的热处理是保证轴承质量和性能稳定的重要工艺之一,需要严格按照标准要求进行操作,选择合适的热处理工艺,进行严格的质量控制和检测,做好热处理工艺和质量的管理。
只有这样,才能确保滚动轴承的热处理质量达到标准要求,提高轴承的使用寿命和性能稳定性。
轴承热处理技术及其装备
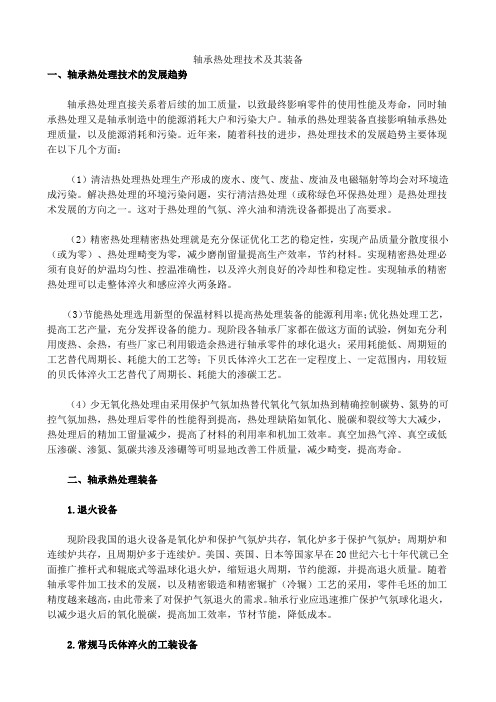
轴承热处理技术及其装备一、轴承热处理技术的发展趋势轴承热处理直接关系着后续的加工质量,以致最终影响零件的使用性能及寿命,同时轴承热处理又是轴承制造中的能源消耗大户和污染大户。
轴承的热处理装备直接影响轴承热处理质量,以及能源消耗和污染。
近年来,随着科技的进步,热处理技术的发展趋势主要体现在以下几个方面:(1)清洁热处理热处理生产形成的废水、废气、废盐、废油及电磁辐射等均会对环境造成污染。
解决热处理的环境污染问题,实行清洁热处理(或称绿色环保热处理)是热处理技术发展的方向之一。
这对于热处理的气氛、淬火油和清洗设备都提出了高要求。
(2)精密热处理精密热处理就是充分保证优化工艺的稳定性,实现产品质量分散度很小(或为零)、热处理畸变为零,减少磨削留量提高生产效率,节约材料。
实现精密热处理必须有良好的炉温均匀性、控温准确性,以及淬火剂良好的冷却性和稳定性。
实现轴承的精密热处理可以走整体淬火和感应淬火两条路。
(3)节能热处理选用新型的保温材料以提高热处理装备的能源利用率;优化热处理工艺,提高工艺产量,充分发挥设备的能力。
现阶段各轴承厂家都在做这方面的试验,例如充分利用废热、余热,有些厂家已利用锻造余热进行轴承零件的球化退火;采用耗能低、周期短的工艺替代周期长、耗能大的工艺等;下贝氏体淬火工艺在一定程度上、一定范围内,用较短的贝氏体淬火工艺替代了周期长、耗能大的渗碳工艺。
(4)少无氧化热处理由采用保护气氛加热替代氧化气氛加热到精确控制碳势、氮势的可控气氛加热,热处理后零件的性能得到提高,热处理缺陷如氧化、脱碳和裂纹等大大减少,热处理后的精加工留量减少,提高了材料的利用率和机加工效率。
真空加热气淬、真空或低压渗碳、渗氮、氮碳共渗及渗硼等可明显地改善工件质量,减少畸变,提高寿命。
二、轴承热处理装备1.退火设备现阶段我国的退火设备是氧化炉和保护气氛炉共存,氧化炉多于保护气氛炉;周期炉和连续炉共存,且周期炉多于连续炉。
风电用齿轮和轴承部件表面热处理研究现状调研

风电用齿轮和轴承部件表面热处理研究现状调研
近年来,随着风力发电技术的不断发展和普及,风电用齿轮和轴承部件的研究也越来越受到关注。
其中,表面热处理技术被广泛应用于提高齿轮和轴承部件的性能和寿命。
目前,国内外对风电用齿轮和轴承部件表面热处理的研究涉及多个方面,主要包括以下内容:
1. 高温渗碳处理技术:高温渗碳可以增加齿轮和轴承部件的硬度和韧性,从而提高其抗疲劳性能和耐磨性能。
2. 等离子氮化处理技术:等离子氮化可以在表面形成一层硬质的氮化物涂层,从而增加齿轮和轴承部件的表面硬度和耐蚀性能。
3. 超声波冷却淬火技术:超声波冷却淬火可以在保证表面硬度的同时,降低齿轮和轴承部件的应力和畸变,从而避免因淬火产生的热应力裂纹。
4. 激光淬火技术:激光淬火可以在表面形成一层高硬度的淬火层,从而提高齿轮和轴承部件的耐磨性和疲劳寿命。
此外,还有一些新兴的表面热处理技术,如等离子体化学气相沉积技术、激光熔覆技术等,在风电用齿轮和轴承部件表面热处理领域也有广泛应用和研究。
总之,风电用齿轮和轴承部件表面热处理是提高风力发电技术应用性和效率的重要手段之一,其研究和发展将进一步推动风电产业的发展。
- 1、下载文档前请自行甄别文档内容的完整性,平台不提供额外的编辑、内容补充、找答案等附加服务。
- 2、"仅部分预览"的文档,不可在线预览部分如存在完整性等问题,可反馈申请退款(可完整预览的文档不适用该条件!)。
- 3、如文档侵犯您的权益,请联系客服反馈,我们会尽快为您处理(人工客服工作时间:9:00-18:30)。
2.3.1淬火变形的控制
淬火加热设备基本采用了保护气氛或可控气氛,可以保证不脱碳,或根据需要进行复碳或渗碳,从而可以大大压缩热处理后的加工余量。但加工余量的可压缩程度往往又受到淬火变形的制约。目前,淬火变形(尤其是畸变)成为控制加工余量的主要因素;且对密封防尘轴承的套圈,淬火畸变将影响防尘盖的压入,进而影响密封性能。因此,减小淬火畸变或实现零畸变将是常规马氏体淬火需要解决的主要问题。因影响淬火畸变的因素繁多,变形的机理较为复杂,所以,每个生产厂家应根据自身的设备和产品特点等多方面的因素,从生产实践中探索出一些控制畸变的、行之有效的措施,如控制工件的摆放、入油方式、淬火油及油温、搅拌等,实现少、无畸变淬火。
1.高碳铬轴承钢的退火
高碳铬轴承钢的理想退火组织是铁素体基体上分布着细、小、匀、圆的碳化物颗粒的组织,为以后的冷加工及最终的淬回火作组织准备。目前,除少数企业使用周期式设备外,普遍使用的是无保护气氛的单通道推杆式等温退火炉。退火的组织和硬度控制已比较成熟可靠,可较容易地把退火组织控制在JB1255标准中的2~3级或细点组织。存在的问题是能耗偏高、退火后氧化脱碳严重。近年来,从节能的角度出发,开发了油电复合加热等温退火炉、双室首尾并置(水平或上下)的等温退火炉,节能效果显著,应大力推广;同时,随着毛坯精密成形工艺和设备的出现,开始采用氮基保护气氛等温退火炉,以减少退火过程中的氧化脱碳,降低原材料的消耗和机加工成本。
2.1组织与性能
常规马氏体淬火后的组织为马氏体、残余奥氏体和未溶(残留)碳化物组成。轴承钢淬火后马氏体基体含碳量为0.55%左右,组织形态一般为板条和片状马氏体的混合组织,或称介于二者之间的中间形态—枣核状马氏体,轴承行业上所谓的隐晶马氏体、结晶马氏体;其亚结构主要为位错缠结以及少量的孪晶。随淬火温度升高或保温时间延长,组织形态逐步由隐晶→结晶→细小针状过度。一般淬火后的正常组织为隐晶+结晶+细小针状马氏体的混合物。一旦出现大量明显的针状马氏体,则组织为不合格组织,应设法避免。
目前,国外的轴承普遍采用所谓的个性化设计,即供应轴承前对轴承的工况条件进行调查,针对工况开展针对性设计,对热处理质量也提出针对性的要求,已使轴承寿命最长。国内对轴承零件的热处理要求统一按JB1255控制,相对较为粗犷,非个性化。应针对轴承工况细化要求,并注意内外圈与滚动体的硬度匹配。
2.2常规马氏体淬火的发展动向
我国轴承零件热处理现状及对策
随着主机的高速化、轻量化,轴承的工作条件更加苛刻,对轴承的性能要求越来越高,如更小的体积、更轻的质量、更大的承载容来越突出的问题,开发热处理新技术、提高热处理质量一直是国内外轴承生产企业及相关企事业单位关注的课题。本文对近年来来年热处理技术的进展进行综述,以期对我国的轴承行业相关人员有所借鉴。
贝氏体组织的突出特点是冲击韧性、断裂韧性、耐磨性、尺寸稳定性好,表面残余应力为压应力。因此适用于装配过盈量大、服役条件差的轴承,如承受大冲击负荷的铁路、轧机、起重机等轴承,润滑条件不良的矿山运输机械或矿山装卸系统、煤矿用轴承等。高碳铬轴承钢BL等温淬火工艺已在铁路、轧机轴承上得到成功应用,取得了较好效果。
2.高碳铬轴承钢的马氏体淬回火
常规的高碳铬轴承钢马氏体淬回火工艺的发展主要分3个方面:一是开展淬回火工艺参数对组织和性能影响的基础性研究,如淬回火过程中的组织转变、残余奥氏体的分解、淬回火后的韧性与疲劳性能等;二是淬回火的工艺性能的研究,如淬火条件对尺寸和变形的影响、尺寸稳定性等;三是取缔氧化或保护气氛加热,推广可控气氛加热。
关于淬回火对性能的影响,国内外也进行了大量研究。洛阳轴承研究所在20世纪80年代开展了“GCr15钢热处理工艺的研究”。研究结果表明:淬火加热为835~865℃、回火为150~180℃時,能获得较好的综力学性能和接触疲劳寿命,845℃淬火時,压碎载荷最高,疲劳寿命最长;随回火温度升高和保温时间的延长,硬度下降,强度和韧性提高。对有特殊要求的零件或采用较高温度回火以提高轴承的使用温度,或在淬火与回火之间进行-50~-78℃的冷处理以提高轴承的尺寸稳定性,或进行马氏体分级淬火以稳定残余奥氏体获得高的尺寸稳定性和较高的韧性。轴承钢淬火加热后在250℃进行短时分级等温空冷,接着进行180℃回火,或在马氏体转变温度等温(马氏体等温淬火),可使淬后的马氏体中碳浓度分布更为均匀,增加稳定的残余奥氏体量,冲击韧性比常规淬回火提高一倍。
3.贝氏体等温淬火
贝氏体等温淬火是近年来国内轴承行业研究的热点。自20世纪80年代开始,洛阳轴承研究所与重庆轴承厂合作,开始了贝氏体等温淬火在铁路轴承上的应用研究,随后与沙河轧机轴承厂开展了贝氏体等温淬火在轧机轴承上的应用研究,均取得了良好的效果,并在JB1255-1991中引入贝氏体等温淬火相关的推荐性技术要求。同时,轴承行业也开始了贝氏体等温淬火的推广应用研究。借助于国家“八五”重点企业技术开发项目“铁路客车轴承”,有关单位对贝氏体等温淬火的组织与性能进行了较为系统的研究,并成功地应用于准高速铁路轴承的生产中。2001年在修订JB1255时,正式将贝氏体等温淬火的技术内容列入标准正式条文。贝氏体淬火工艺在轧机、机车、铁客等轴承上得到较为广泛的推广应用。
2.3.2残余应力及残余奥氏体的控制和评定
我国目前的热检标准中,对残余应力和残余奥氏体没有评定指标限制。大量的研究表明:残余应力影响零件的接触疲劳性能、韧性和磨削裂纹,适当的残余压应力可以提高接触疲劳寿命、防止磨削及安装裂纹的产生;残余奥氏体降低尺寸稳定性,其影响程度与残余奥氏体本身的稳定性、数量和存在部位有关。但适量的残余奥氏体可以提高断裂韧性和接触疲劳性能。多家国外的著名轴承公司已把残余应力和残余奥氏体列入热处理控制指标。因此,进一步开展残余应力和残余奥氏体对热处理后性能的影响及其机理的研究、开展淬回火工艺对残余应力和残余奥氏体影响的研究,进而根据轴承的工况提出残余应力和残余奥氏体的控制指标等等,将是我国轴承行业热处理研究的主要方向之一。