光学镜片外观检查规范
玻璃镜片测试规范
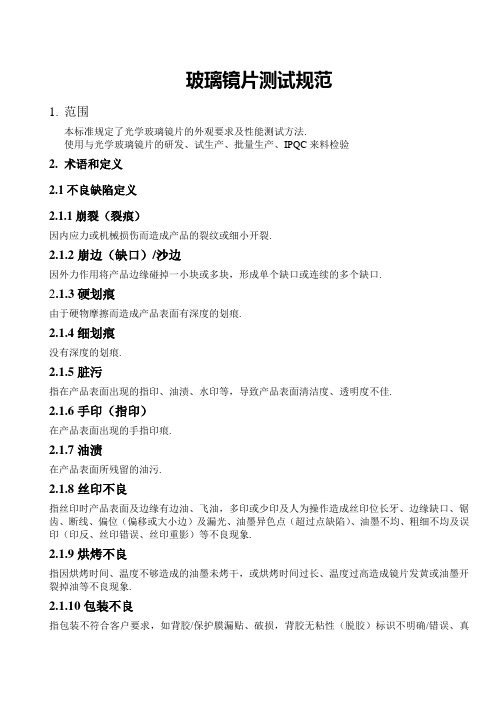
玻璃镜片测试规范1.范围本标准规定了光学玻璃镜片的外观要求及性能测试方法.使用与光学玻璃镜片的研发、试生产、批量生产、IPQC来料检验2.术语和定义2.1不良缺陷定义2.1.1崩裂(裂痕)因内应力或机械损伤而造成产品的裂纹或细小开裂.2.1.2崩边(缺口)/沙边因外力作用将产品边缘碰掉一小块或多块,形成单个缺口或连续的多个缺口.2.1.3硬划痕由于硬物摩擦而造成产品表面有深度的划痕.2.1.4细划痕没有深度的划痕.2.1.5脏污指在产品表面出现的指印、油渍、水印等,导致产品表面清洁度、透明度不佳.2.1.6手印(指印)在产品表面出现的手指印痕.2.1.7油渍在产品表面所残留的油污.2.1.8丝印不良指丝印时产品表面及边缘有边油、飞油,多印或少印及人为操作造成丝印位长牙、边缘缺口、锯齿、断线、偏位(偏移或大小边)及漏光、油墨异色点(超过点缺陷)、油墨不均、粗细不均及误印(印反、丝印错误、丝印重影)等不良现象.2.1.9烘烤不良指因烘烤时间、温度不够造成的油墨未烤干,或烘烤时间过长、温度过高造成镜片发黄或油墨开裂掉油等不良现象.2.1.10包装不良指包装不符合客户要求,如背胶/保护膜漏贴、破损,背胶无粘性(脱胶)标识不明确/错误、真空包装漏气等.2.2不合格的分类按程度不同分为A类不合格、B类不合格、C类不合格三类.2.2.1 A类不合格易导致不安全因素的项目以及导致其基本功能失效的项目.1)镜片破碎2)性能测试不良:抗冲击、附着力、装配.3)尺寸不符:与客户图纸要求不符,影响装配功能.2.2.2 B类不合格可能导致功能失误或降低原有使用功能的项目.外观检测项目内容:如崩边、崩裂、细硬划痕、点缺陷、脏污、烘烤不良、丝印不良、漏光、透光性、色泽、倒边不符要求等.2.2.3C类不合格指对产品的使用性能没有影响或只有轻微影响的项目.1)包装方式不符合客户要求,包装内有异物等.2)标识不全或不符.3)有漏装、多装或错装产品.4)检验记录填写不全或有误.2.3不合格品的定义按不合格类型分为A类不合格品、B类不合格品、C类不合格品.2.3.1 A类不合格品有一个或一个以上A类不合格品,也可能还有B类和C类不合格的单位产品.2.3.2 B类不合格品有一个或一个以上的B类不合格,也可能还有C类不合格的单位产品,但不包含A类不合格的单位产品.2.3.3C类不合格品有一个或一个以上的C类不合格,但不包含A类和B类不合格的单位产品2.4缺陷代码对照表缺陷代码对照表见表1.表1缺陷代码对照表3.外观检验条件及环境的要求.a)距离:人眼与被测无表面的距离为200mm-300mm.b)时间:每片检查时间不超过5-10s(10s内检验不出来的缺陷可以不计)c)检验方法:目视,且监视面与桌面成45°;上下左右转动15°,(透明清晰度、漏光须对光检测,即与灯光呈平行目视检测)d)照明:35w冷白荧光灯,光源距被测物表面400mm-500mm(照度达800Lux-1200Lux).4.检验操作注意事项a)操作人员工作前必须洁净双手,严格执行检验标准,不能误判、漏检.b)产品必须轻拿轻放,按指定的位置放置,标识清楚,随时注意防潮防尘遮盖(无论良品或不良品)c)工作台面必须随时保持干净、整洁.必须以合格的产品转序.5.抽样检验规则1)正常检验批量检查采用GB 2828-87中的一次抽样方案,如批量总数为150片,则样本数位20片.批合格质量水平(AQL)如下所示:AQL取值:— A类不合格品为0.65(性能/尺寸样本数以总样本数的值采用特殊检验水平S-3级正常一次抽样方案)—B类不合格品为1.0(样本数以批量数取样本值,一般检验水平Ⅱ级正常一次抽检方案)—C类不合格品为0.65(样本数以抽样包装箱、袋数取样本值,一般检验水平Ⅱ级正常一次抽检方案)2)加严检验当正常检验时,在连续5批中有两批检验不合格,则从下批起转到加严检验(母体数是150片,抽样32片)3)从加严检验转为正常检验当进行加严检验时,若连续5批检验合格时,则从下批起转到正常检验。
光学镜片外观检作业规范
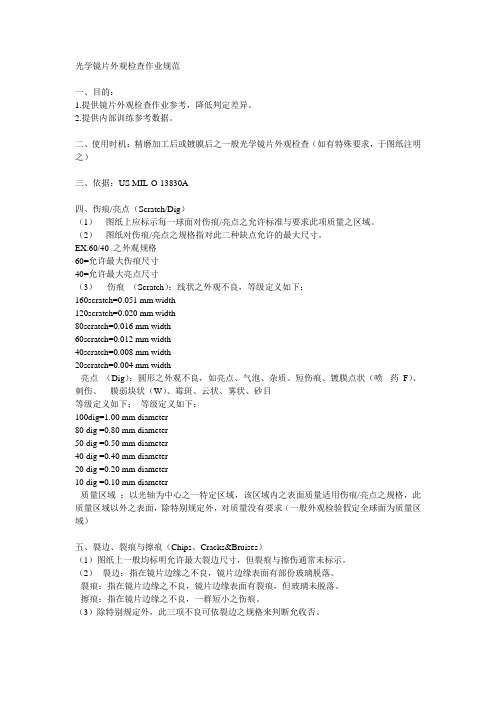
光学镜片外观检查作业规范一、目的:1.提供镜片外观检查作业参考,降低判定差异。
2.提供内部训练参考数据。
二、使用时机:精磨加工后或镀膜后之一般光学镜片外观检查(如有特殊要求,于图纸注明之)三、依据:US MIL-O-13830A四、伤痕/亮点(Scratch/Dig)(1)图纸上应标示每一球面对伤痕/亮点之允许标准与要求此项质量之区域。
(2)图纸对伤痕/亮点之规格指对此二种缺点允许的最大尺寸。
EX.60/40 之外观规格60=允许最大伤痕尺寸40=允许最大亮点尺寸(3)--伤痕(Scratch):线状之外观不良,等级定义如下:160scratch=0.051 mm width120scratch=0.020 mm width80scratch=0.016 mm width60scratch=0.012 mm width40scratch=0.008 mm width20scratch=0.004 mm width--亮点(Dig):圆形之外观不良,如亮点、气泡、杂质、短伤痕、镀膜点状(喷-药F)、刺伤、膜弱块状(W)、霉斑、云状、雾状、砂目等级定义如下:等级定义如下:100dig=1.00 mm diameter80 dig =0.80 mm diameter50 dig =0.50 mm diameter40 dig =0.40 mm diameter20 dig =0.20 mm diameter10 dig =0.10 mm diameter--质量区域:以光轴为中心之一特定区域,该区域内之表面质量适用伤痕/亮点之规格,此质量区域以外之表面,除特别规定外,对质量没有要求(一般外观检验假定全球面为质量区域)五、裂边、裂痕与擦痕(Chips、Cracks&Bruises)(1)图纸上一般均标明允许最大裂边尺寸,但裂痕与擦伤通常未标示。
(2)--裂边:指在镜片边缘之不良,镜片边缘表面有部份玻璃脱落。
vr光学镜片检验标准
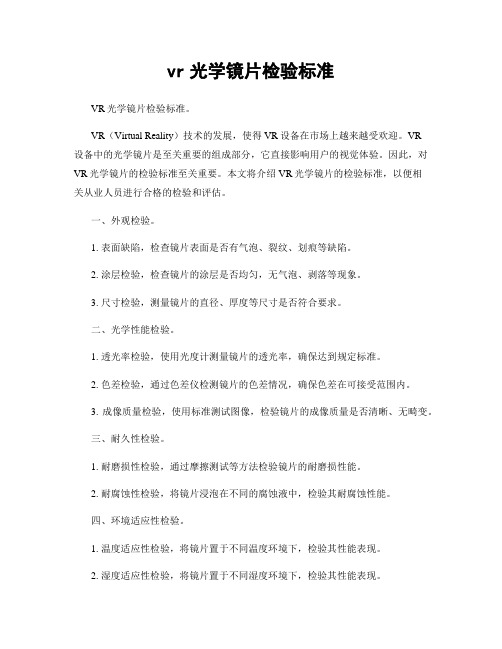
vr光学镜片检验标准VR光学镜片检验标准。
VR(Virtual Reality)技术的发展,使得VR设备在市场上越来越受欢迎。
VR设备中的光学镜片是至关重要的组成部分,它直接影响用户的视觉体验。
因此,对VR光学镜片的检验标准至关重要。
本文将介绍VR光学镜片的检验标准,以便相关从业人员进行合格的检验和评估。
一、外观检验。
1. 表面缺陷,检查镜片表面是否有气泡、裂纹、划痕等缺陷。
2. 涂层检验,检查镜片的涂层是否均匀,无气泡、剥落等现象。
3. 尺寸检验,测量镜片的直径、厚度等尺寸是否符合要求。
二、光学性能检验。
1. 透光率检验,使用光度计测量镜片的透光率,确保达到规定标准。
2. 色差检验,通过色差仪检测镜片的色差情况,确保色差在可接受范围内。
3. 成像质量检验,使用标准测试图像,检验镜片的成像质量是否清晰、无畸变。
三、耐久性检验。
1. 耐磨损性检验,通过摩擦测试等方法检验镜片的耐磨损性能。
2. 耐腐蚀性检验,将镜片浸泡在不同的腐蚀液中,检验其耐腐蚀性能。
四、环境适应性检验。
1. 温度适应性检验,将镜片置于不同温度环境下,检验其性能表现。
2. 湿度适应性检验,将镜片置于不同湿度环境下,检验其性能表现。
五、特殊性能检验。
1. 防辐射性能检验,检验镜片的防辐射性能。
2. 防眩光性能检验,检验镜片的防眩光性能。
以上所述即为VR光学镜片的检验标准,通过严格按照以上标准进行检验,可以确保生产的VR光学镜片质量稳定可靠,从而提升用户的视觉体验。
希望相关从业人员能够严格执行以上标准,确保VR设备的质量和安全性,为用户带来更好的虚拟现实体验。
镜片表面光洁度检验标准
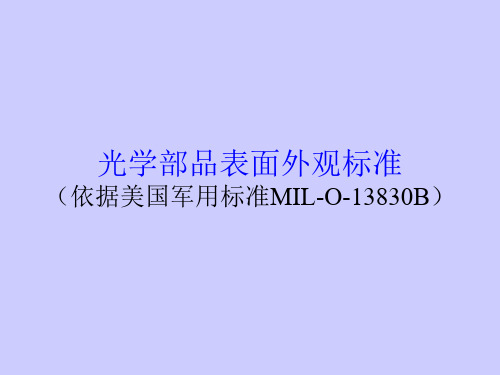
的麻点
50>40元件不合格。
2.每20mm直径上只允许有1个最大麻点。
例 : 元 件 为 20mm , 质 量 指 标 要 求 为 60—40 , 元 件 有 2 个 直 径 0.4mm的麻点元件不合格
元 件 20mm 内 只 有 一 个 直 径 0.4mm的点子,符合本条
0.4mm的点子
元件20mm内有二个直径0.4mm 的点子,元件不合格.
痕长度与元件直径之比所得乘积之 和为:
20×2.2/5+10×7/5=8.8+17=25.8
25.8<40。元件符合40-20
10
麻点:
依据美国军用标准MIL-O-13830B麻点的级数取允许缺陷的 实际直径,规定以1/100mm作为计量单位。如果麻点形状不 规则。则应取最大长度和最大宽度的平均值作为直径。
60#划痕长2mm
最大划痕的长度和为: 2mm+2mm=4mm
40#划痕长4mm
4mm<5mm。符合2条。
但所有级数的划痕乘以划痕长度与元件直径之比所得乘积之和为:
1.60#划痕长度为(2+2);40#划痕长度为(4+4+4) 2.60#划痕乘以划痕长度与元件直径之比为60×(2+2)/20;
40#划痕乘以划痕长度与元件直径之比为40×(4+4+4)/20 3.所有级数的划痕乘以划痕长度与元件直径之比所得乘积之和为:
3
美军标规定对于非圆形元件其直径取相等面积圆的直径。
D
a
面积=π(D/2)2 三角的面积为(低×高)/2=(a ×b)/2
长方形面积=长×宽=a ×b
b
长方形的等效直径D
光学镜片检验标准国标

光学镜片检验标准国标光学镜片是日常生活中常见的光学元件之一,广泛应用于眼镜、相机、显微镜等光学设备中。
为了保证光学镜片的质量,确保其在使用过程中具有良好的成像效果和可靠性,制定了一系列的光学镜片检验标准国标。
本文将详细介绍光学镜片检验的相关标准和方法,并提供具体的实例说明。
一、光学镜片检验标准国标的基本概念和定义1.1 光学镜片光学镜片是用于将光线聚焦或分散的一种光学元件,包括凸透镜、凹透镜、平面镜等。
1.2 光学镜片检验光学镜片检验是针对光学镜片的光学性能、物理性能、外观缺陷等方面进行的一系列检测和评估工作。
国标是指由中国标准化组织制定的标准,用于统一产品质量要求和检验方法的技术规范。
二、光学镜片检验标准国标的主要内容2.1 光学性能检验光学性能检验是评估光学镜片成像效果的重要指标。
国标规定了光学镜片的球差、色差、畸变等性能参数的检验方法和标准值。
2.1.1 球差检验球差是指光线通过透镜时由于折射率的差异而导致的不同焦距的现象。
国标规定了球差的数值范围,通常使用经验公式和检验仪器进行评估和检验。
2.1.2 色差检验色差是指透镜在不同波长光线下折射率的差异,导致成像时产生的色差现象。
国标规定了色差的范围和评价方法,常用的检验仪器包括分光光度计和色差仪等。
2.1.3 畸变检验畸变是指光线通过透镜后,由于透镜形状或透镜表面曲率不均匀而导致成像时的畸变现象。
国标规定了畸变的检验方法和标准,常用的检验手段包括透镜曲率半径仪和光线追迹仪等。
2.2 物理性能检验物理性能检验是评估光学镜片的耐磨性、耐冲击性等力学性能的重要标准。
国标规定了光学镜片在耐磨、耐冲击、耐温变化等方面的检验方法和标准。
2.2.1 耐磨性检验耐磨性是指光学镜片在使用条件下抵抗表面划伤和磨损的能力。
国标规定了耐磨性检验的方法和标准,包括磨损试验机、针尖硬度计等设备的使用。
2.2.2 耐冲击性检验耐冲击性是指光学镜片在受到外力撞击时不会破裂或产生裂纹的能力。
镜片检验标准
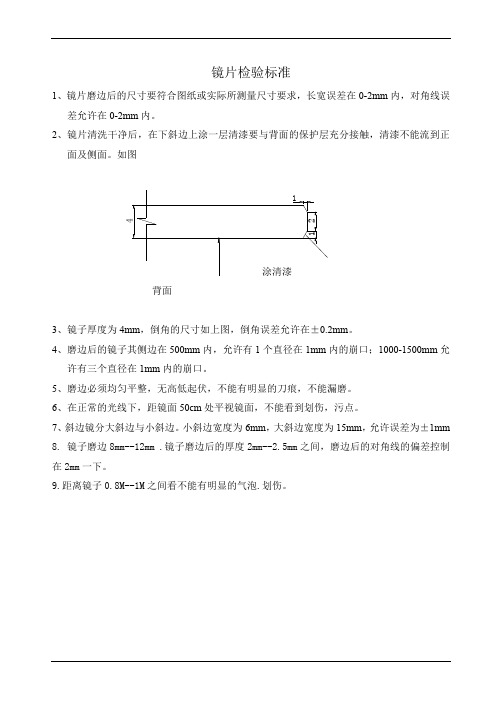
镜片检验标准
1、镜片磨边后的尺寸要符合图纸或实际所测量尺寸要求,长宽误差在0-2mm内,对角线误
差允许在0-2mm内。
2、镜片清洗干净后,在下斜边上涂一层清漆要与背面的保护层充分接触,清漆不能流到正
面及侧面。
如图
背面
3、镜子厚度为4mm,倒角的尺寸如上图,倒角误差允许在±0.2mm。
4、磨边后的镜子其侧边在500mm内,允许有1个直径在1mm内的崩口;1000-1500mm允
许有三个直径在1mm内的崩口。
5、磨边必须均匀平整,无高低起伏,不能有明显的刀痕,不能漏磨。
6、在正常的光线下,距镜面50cm处平视镜面,不能看到划伤,污点。
7、斜边镜分大斜边与小斜边。
小斜边宽度为6mm,大斜边宽度为15mm,允许误差为±1mm
8. 镜子磨边8mm--12mm .镜子磨边后的厚度2mm--2.5mm之间,磨边后的对角线的偏差控制在2mm一下。
9.距离镜子0.8M--1M之间看不能有明显的气泡.划伤。
图1
图2。
镜片外观检验标准不良明细
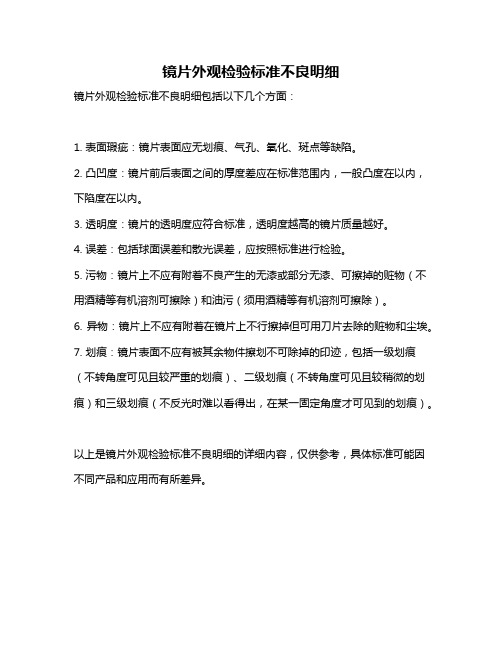
镜片外观检验标准不良明细
镜片外观检验标准不良明细包括以下几个方面:
1. 表面瑕疵:镜片表面应无划痕、气孔、氧化、斑点等缺陷。
2. 凸凹度:镜片前后表面之间的厚度差应在标准范围内,一般凸度在以内,下陷度在以内。
3. 透明度:镜片的透明度应符合标准,透明度越高的镜片质量越好。
4. 误差:包括球面误差和散光误差,应按照标准进行检验。
5. 污物:镜片上不应有附着不良产生的无漆或部分无漆、可擦掉的赃物(不用酒精等有机溶剂可擦除)和油污(须用酒精等有机溶剂可擦除)。
6. 异物:镜片上不应有附着在镜片上不行擦掉但可用刀片去除的赃物和尘埃。
7. 划痕:镜片表面不应有被其余物件擦划不可除掉的印迹,包括一级划痕(不转角度可见且较严重的划痕)、二级划痕(不转角度可见且较稍微的划痕)和三级划痕(不反光时难以看得出,在某一固定角度才可见到的划痕)。
以上是镜片外观检验标准不良明细的详细内容,仅供参考,具体标准可能因不同产品和应用而有所差异。
光学镜片表面外观检测标准

光学镜片表面外观检测标准您的光学工厂一.定义:表面缺陷标准:依据美国军用标准MIL-O-13830B用两组数字表示表面缺陷大小。
例如40/20(或40-20)前者限制划痕大小,后者限制麻点大小。
道子、亮路、伤、擦痕都统称为划痕。
斑点、坑点、点子都称为麻点。
规定长与宽的比大于4:1的为划痕;长与宽的比小于4:1的为麻点。
当元件的不同区域表面光洁度要求不一样时,等效直径的计算以区域进行:表面质量要求高的内区域其等效直径以内区域为准(如有效孔径的区域),表面质量要求低的外区域计算的是整体元件的等效直径。
如下图元件表面质量要求不同,则在判定A区是否符合要求时,应取内圆直径进行计算。
而B区则取整个元件的圆直径划痕:以美国军用标准《MIL-O-13830》的表面质量划痕样板作为各级数划痕的比对标准。
(注意:美军标未指明划痕的计量单位也即未确定划痕的宽度和深度,只能以实际观察样版为标准。
)这里的划痕级数就是通常的划痕号数,标准样版有10#、20#、40#、60#、80# 5个级。
1.当元件的划痕级数超过表面质量要求的划痕级数时,元件不合格。
例如:元件的表面质量要求为60—40,则代表元件的划痕必须≤60#,如果元件有>60#的划痕,则元件不合格。
2.当元件的划痕级数未超过表面质量要求的级数,但元件存在最大划痕时,所有最大划痕的长度之和应不超过元件直径的1/4。
例如:有一长30mm宽10mm的元件,元件的表面质量要求为60—40,有2条60#长为3 mm划痕。
它的等效直径为20mm1/4D为1/4×20=5mm最大划痕的长度和为:3mm+3mm=6mm6mm>5mm元件最大划伤痕的长度和超过元件直径的1/4。
所以元件不合格。
下图是看到的样品(图片是放大的不是实际尺寸)图中的划痕为20#,且长度>1/4D。
对于表面质量要求20-10该产品不合格。
但本次样品未提出表面质量要求,而是要大家自已决定光洁度等级。
镜片表面光洁度检验标准.
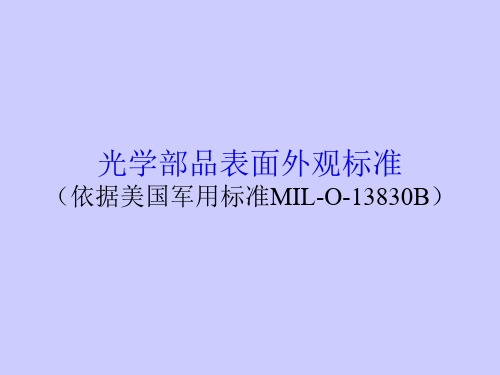
(依据美国军用标准MIL-O-13830B)
一.定义:
表面缺陷标准:依据美国军用标准MIL-O-13830B用两组数字 表示表面缺陷大小。例如40/20(或40-20)前者限制划痕大小, 后者限制麻点大小。 道子、亮路、伤、擦痕都统称为划痕。 斑点、坑点、点子 都称为麻点。 规定长与宽的比大于4:1的为划痕;长与宽的比小于4:1的 为麻点。
7
如左图所示的产品 则20#划痕长度0.7mm。10#划痕 长度2mm对于表面质量要求20-10 该产品最大划痕长度1mm<1/5。
所有级数的划痕乘以划痕长度与元件 直径之比所得乘积之和为: 20 ×0.7/5+10 ×2/5=2.8+2=4.8<10, 该元件划痕可判为20#
10# 20#
8
4.当元件的划痕级数未超过表面质量要求的级数,且元件不存在最大 划痕时,所有级数的划痕乘以划痕长度与元件直径之比所得乘积之和, 不得超过最大划痕级数。
3
美军标规定对于非圆形元件其直径取相等面积圆的直径。
长方形面积=长×宽=a ×b
D
b
长方形的等效直径D
D2
ab
a
面积=π(D/2)2 三角的面积为(低×高)/2=(a ×b)/2 三角等效直径D
h a
对于长方形元件(当长与宽的比 <5 : 1 时)可以用简单公式:等效直径 =(长+ 宽)/2来计算。如左图元件
左图是看到的样品(图片是放大的 不是实际尺寸) 图中的划痕为20#,且长度>1/4D。 对于表面质量要求20-10该产品不 合格。但本次样品未提出表面质量 要求,而是要大家自已决定光洁度 等级。因此该产品划痕可判为40#。
光学镜片检验规范
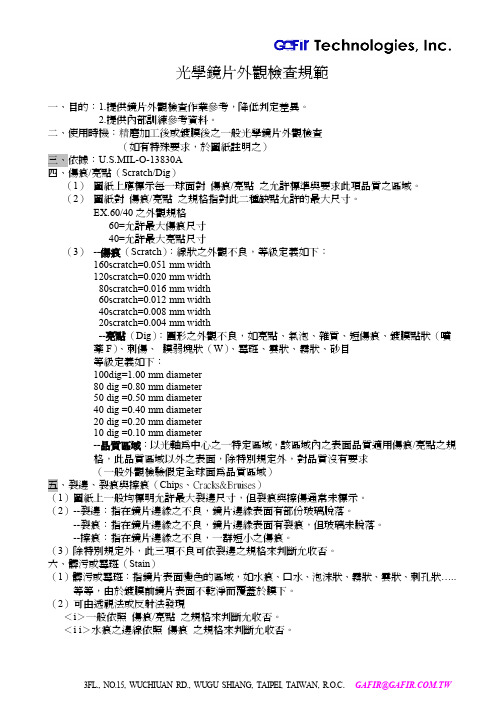
光學鏡片外觀檢查規範一、目的:1.提供鏡片外觀檢查作業參考,降低判定差異。
2.提供內部訓練參考資料。
二、使用時機:精磨加工後或鍍膜後之一般光學鏡片外觀檢查(如有特殊要求,於圖紙註明之)三、依據:-O-13830A四、傷痕/亮點(Scratch/Dig)(1)圖紙上應標示每一球面對傷痕/亮點之允許標準與要求此項品質之區域。
(2)圖紙對傷痕/亮點之規格指對此二種缺點允許的最大尺寸。
EX.60/40之外觀規格60=允許最大傷痕尺寸40=允許最大亮點尺寸(3)--傷痕(Scratch):線狀之外觀不良,等級定義如下:160scratch=0.051 mm width120scratch=0.020 mm width80scratch=0.016 mm width60scratch=0.012 mm width40scratch=0.008 mm width20scratch=0.004 mm width--亮點(Dig):圓形之外觀不良,如亮點、氣泡、雜質、短傷痕、鍍膜點狀(噴藥F)、刺傷、膜弱塊狀(W)、霉斑、雲狀、霧狀、砂目等級定義如下:100dig=1.00 mm diameter80 dig =0.80 mm diameter50 dig =0.50 mm diameter40 dig =0.40 mm diameter20 dig =0.20 mm diameter10 dig =0.10 mm diameter--品質區域:以光軸為中心之一特定區域,該區域內之表面品質適用傷痕/亮點之規格,此品質區域以外之表面,除特別規定外,對品質沒有要求(一般外觀檢驗假定全球面為品質區域)五、裂邊、裂痕與擦痕(Chip s、Cracks&Bruises)(1)圖紙上一般均標明允許最大裂邊尺寸,但裂痕與擦傷通常未標示。
(2)--裂邊:指在鏡片邊緣之不良,鏡片邊緣表面有部份玻璃脫落。
--裂痕:指在鏡片邊緣之不良,鏡片邊緣表面有裂痕,但玻璃未脫落。
光学镜片标准
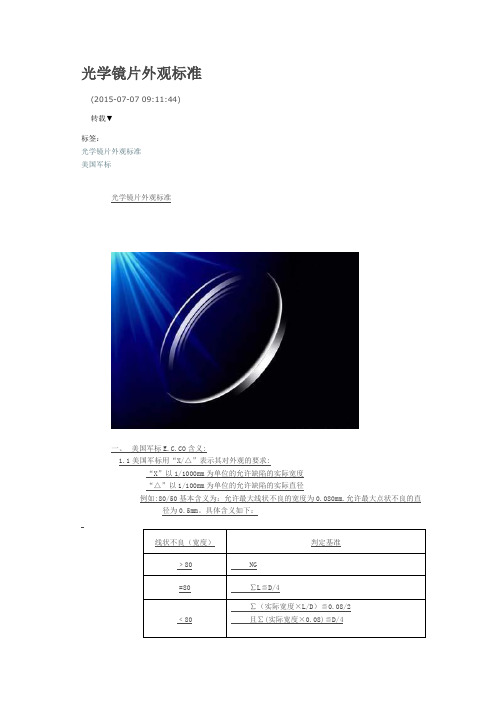
光学镜片外观标准(2015-07-07 09:11:44)转载▼标签:光学镜片外观标准美国军标光学镜片外观标准一、美国军标E.C.CO含义:1.1美国军标用“X/△”表示其对外观的要求:“X”以1/1000mm为单位的允许缺陷的实际宽度“△”以1/100mm为单位的允许缺陷的实际直径例如:80/50基本含义为:允许最大线状不良的宽度为0.080mm.允许最大点状不良的直径为0.5mm。
具体含义如下:线状不良(宽度)判定基准﹥80 NG=80∑L≦D/4﹤80∑(实际宽度×L/D)≦0.08/2且∑(实际宽度×0.08)≦D/4以上字母的含义:L:线状不良的长度D:圆形镜片D=光线有效直径方形镜片=2√长(有效径)﹒宽(有效径)/II棱镜线状不良:D=2√∑各个面积(有效径)/II点状不良:D=2√面积(有效径)/IIN=允许的不良个数一、美国军标的含义:例如:80/50基本含义为:允许最大线状不良的宽度为0.080mm.允许最大点状不良的直径为0.5mm。
2.1.1伤痕:线状划伤的外观不良.2.1.2斑孔:圆点状凹坑之外观不良.2.1.3品质区域:以光轴为中心的一个圆形区域。
在该区域内、表面品质适用伤痕/斑孔的要求。
在此区域外,除特别规定外,无对表面品质之要求。
2.2伤痕的判定基准:2.2.1仅有标准的最大伤痕时:L=1/4*D2.2.2同时有最大伤痕与较小伤痕时:L=1/4*D L+L′=1/2*D2.2.3仅有较小标准的伤痕时: L′=D说明: L:允许最大伤痕总长度D:镜片表面直径L′较小的伤痕换算成最大等值伤痕长度L′∑(实际伤痕/标准最大伤痕)*实际伤痕的长度例1:标准为80/40,镜片直径40mm的镜片,检查镜片表面后发现伤痕如下:#80 伤痕8mm判定:L8mm﹤1/4*40mm=10mm 本片允收例2:标准为80/40,镜片直径40mm的镜片,检查镜片表面后发现伤痕如下:#80 伤痕8mm ; #60 伤痕4mm ; #40 伤痕6mm 判定:L=8mmL=(60/80)*4mm+(40/80)*6mm =6mmL+L=14mm﹤1/2*40mm 本片允收例3:标准80/40,镜片直径40mm的镜片,检查镜片表面后发现伤痕如下:#60 伤痕8mm; #40 伤痕6mm; #20 伤痕8mm判定:L=(60/80)*8mm +(40/80)*6mm+(20/80)*8mm=11mm﹤40mm 本片允收注意:镀膜后膜层上的伤痕标准依图面,伤痕/斑孔的规定应单独计算,不与加工的不良混合。
光学产品外观检验标准
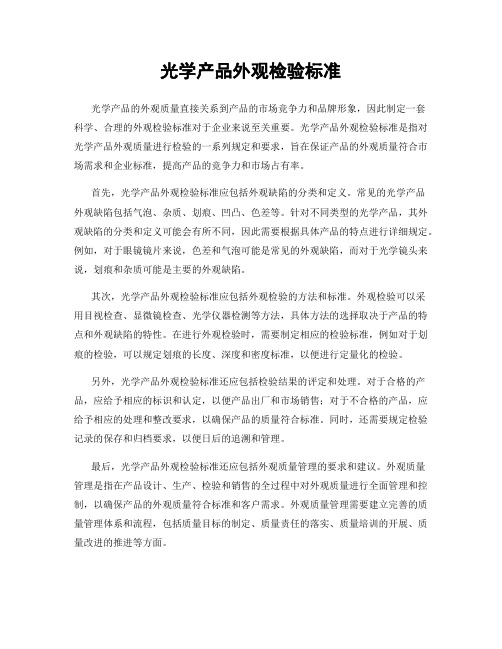
光学产品外观检验标准光学产品的外观质量直接关系到产品的市场竞争力和品牌形象,因此制定一套科学、合理的外观检验标准对于企业来说至关重要。
光学产品外观检验标准是指对光学产品外观质量进行检验的一系列规定和要求,旨在保证产品的外观质量符合市场需求和企业标准,提高产品的竞争力和市场占有率。
首先,光学产品外观检验标准应包括外观缺陷的分类和定义。
常见的光学产品外观缺陷包括气泡、杂质、划痕、凹凸、色差等。
针对不同类型的光学产品,其外观缺陷的分类和定义可能会有所不同,因此需要根据具体产品的特点进行详细规定。
例如,对于眼镜镜片来说,色差和气泡可能是常见的外观缺陷,而对于光学镜头来说,划痕和杂质可能是主要的外观缺陷。
其次,光学产品外观检验标准应包括外观检验的方法和标准。
外观检验可以采用目视检查、显微镜检查、光学仪器检测等方法,具体方法的选择取决于产品的特点和外观缺陷的特性。
在进行外观检验时,需要制定相应的检验标准,例如对于划痕的检验,可以规定划痕的长度、深度和密度标准,以便进行定量化的检验。
另外,光学产品外观检验标准还应包括检验结果的评定和处理。
对于合格的产品,应给予相应的标识和认定,以便产品出厂和市场销售;对于不合格的产品,应给予相应的处理和整改要求,以确保产品的质量符合标准。
同时,还需要规定检验记录的保存和归档要求,以便日后的追溯和管理。
最后,光学产品外观检验标准还应包括外观质量管理的要求和建议。
外观质量管理是指在产品设计、生产、检验和销售的全过程中对外观质量进行全面管理和控制,以确保产品的外观质量符合标准和客户需求。
外观质量管理需要建立完善的质量管理体系和流程,包括质量目标的制定、质量责任的落实、质量培训的开展、质量改进的推进等方面。
综上所述,光学产品外观检验标准是保证产品外观质量符合市场需求和企业标准的重要手段,其制定应包括外观缺陷的分类和定义、外观检验的方法和标准、检验结果的评定和处理、外观质量管理的要求和建议等内容,以确保产品的外观质量稳定、一致、优良,提高产品的市场竞争力和品牌形象。
镜片表面光洁度检验标准

左图是本次样品,图片是放大的 不是实际尺寸. 有 1 个 5# 点 子 , 1 个 3# 点 子 。 (但然这些点子有可能擦掉就 看不到了这里只是作为例子来 说明)。这产品如果不考虑两 点间距可以判定点子为级数5。 为什么?因为产品只有1个最 大点子5#,而所有的点子之和 为 0.05+0.03=0.08<0.1(5# 点 子 的两倍),所有点子可判定为 级数5#。
3
美军标规定对于非圆形元件其直径取相等面积圆的直径。
长方形面积=长×宽=a ×b
D
b
长方形的等效直径D
D2
ab
a
面积=π(D/2)2 三角的面积为(低×高)/2=(a ×b)/2 三角等效直径D
h a
对于长方形元件(当长与宽的比<5:1 时)可以用简单公式:等效直径=(长+ 宽)/2来计算。如左图元件
16
10
麻点:
依据美国军用标准MIL-O-13830B麻点的级数取允许缺陷的 实际直径,规定以1/100mm作为计量单位。如果麻点形状不 规则。则应取最大长度和最大宽度的平均值作为直径。 (注意:美军标的麻点与划痕不同,麻点是可计量的也即麻 点的大小是确定的,50#麻点也即直径D=0.5mm的麻点)
0.125mm 点子直径:
左图看到的样品,图片是放大的不 是实际尺寸. 图中有20#划痕长度2.2mm。10# 划痕长度7mm对于表面质量要求 20-10该产品不合格。对于表面 质量要求40-20则该产品所有级 数乘以划痕长度与元件直径之比所
得乘积之和为: 20×2.2/5+10×7/5=8.8+17=25.8
25.8<40。元件符合40-20
D2
ah
光学镜片检验标准国标
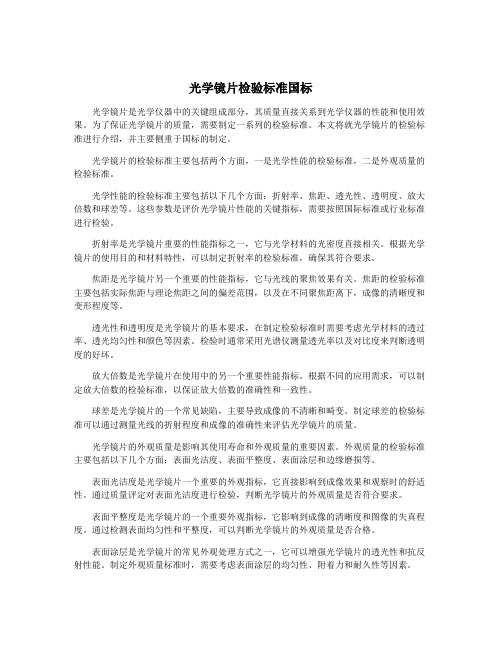
光学镜片检验标准国标光学镜片是光学仪器中的关键组成部分,其质量直接关系到光学仪器的性能和使用效果。
为了保证光学镜片的质量,需要制定一系列的检验标准。
本文将就光学镜片的检验标准进行介绍,并主要侧重于国标的制定。
光学镜片的检验标准主要包括两个方面,一是光学性能的检验标准,二是外观质量的检验标准。
光学性能的检验标准主要包括以下几个方面:折射率、焦距、透光性、透明度、放大倍数和球差等。
这些参数是评价光学镜片性能的关键指标,需要按照国际标准或行业标准进行检验。
折射率是光学镜片重要的性能指标之一,它与光学材料的光密度直接相关。
根据光学镜片的使用目的和材料特性,可以制定折射率的检验标准,确保其符合要求。
焦距是光学镜片另一个重要的性能指标,它与光线的聚焦效果有关。
焦距的检验标准主要包括实际焦距与理论焦距之间的偏差范围,以及在不同聚焦距离下,成像的清晰度和变形程度等。
透光性和透明度是光学镜片的基本要求,在制定检验标准时需要考虑光学材料的透过率、透光均匀性和颜色等因素。
检验时通常采用光谱仪测量透光率以及对比度来判断透明度的好坏。
放大倍数是光学镜片在使用中的另一个重要性能指标。
根据不同的应用需求,可以制定放大倍数的检验标准,以保证放大倍数的准确性和一致性。
球差是光学镜片的一个常见缺陷,主要导致成像的不清晰和畸变。
制定球差的检验标准可以通过测量光线的折射程度和成像的准确性来评估光学镜片的质量。
光学镜片的外观质量是影响其使用寿命和外观质量的重要因素。
外观质量的检验标准主要包括以下几个方面:表面光洁度、表面平整度、表面涂层和边缘磨损等。
表面光洁度是光学镜片一个重要的外观指标,它直接影响到成像效果和观察时的舒适性。
通过质量评定对表面光洁度进行检验,判断光学镜片的外观质量是否符合要求。
表面平整度是光学镜片的一个重要外观指标,它影响到成像的清晰度和图像的失真程度。
通过检测表面均匀性和平整度,可以判断光学镜片的外观质量是否合格。
表面涂层是光学镜片的常见外观处理方式之一,它可以增强光学镜片的透光性和抗反射性能。
镜检作业指导书
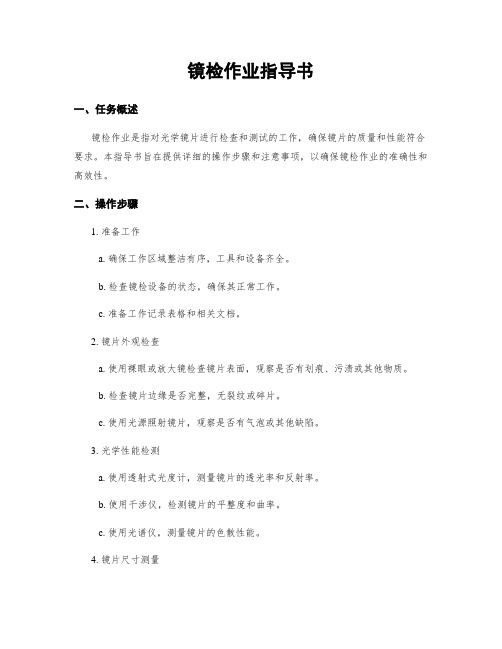
镜检作业指导书一、任务概述镜检作业是指对光学镜片进行检查和测试的工作,确保镜片的质量和性能符合要求。
本指导书旨在提供详细的操作步骤和注意事项,以确保镜检作业的准确性和高效性。
二、操作步骤1. 准备工作a. 确保工作区域整洁有序,工具和设备齐全。
b. 检查镜检设备的状态,确保其正常工作。
c. 准备工作记录表格和相关文档。
2. 镜片外观检查a. 使用裸眼或放大镜检查镜片表面,观察是否有划痕、污渍或其他物质。
b. 检查镜片边缘是否完整,无裂纹或碎片。
c. 使用光源照射镜片,观察是否有气泡或其他缺陷。
3. 光学性能检测a. 使用透射式光度计,测量镜片的透光率和反射率。
b. 使用干涉仪,检测镜片的平整度和曲率。
c. 使用光谱仪,测量镜片的色散性能。
4. 镜片尺寸测量a. 使用千分尺或显微镜,测量镜片的直径、厚度和曲率半径。
b. 检查测量结果是否符合规定的尺寸要求。
5. 数据记录和分析a. 将每个镜片的检测结果记录在工作记录表格中。
b. 分析数据,比较不同镜片之间的差异。
c. 根据检测结果,判断镜片是否合格。
6. 故障排除和维护a. 如果发现镜检设备故障,立即报告维修部门进行维修。
b. 定期清洁和校准镜检设备,确保其正常工作。
三、注意事项1. 操作人员应穿戴适当的个人防护装备,如手套和护目镜。
2. 在进行镜检作业前,应对镜检设备进行校准和测试。
3. 操作过程中要注意避免镜片受到额外的损伤或污染。
4. 操作人员应严格按照操作规程进行操作,不得随意更改或省略步骤。
5. 检测结果应准确记录,确保数据的可追溯性和准确性。
6. 如发现镜片不合格,应立即采取相应的措施,如退货或进行修复。
四、总结镜检作业是确保光学镜片质量和性能的重要工作。
本指导书提供了详细的操作步骤和注意事项,帮助操作人员准确、高效地完成镜检作业。
在进行镜检作业时,操作人员应严格遵守操作规程,保证操作的准确性和可靠性。
通过镜检作业,可以及时发现镜片的缺陷和问题,确保产品的质量和性能符合要求。
光学镜片外观检作业规范
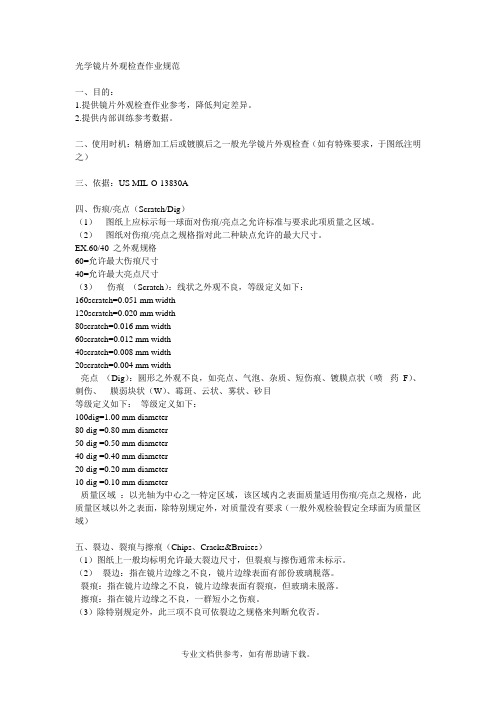
(1)图纸上一般均标明允许最大裂边尺寸,但裂痕与擦伤通常未标示。
(2)--裂边:指在镜片边缘之不良,镜片边缘表面有部份玻璃脱落。
--裂痕:指在镜片边缘之不良,镜片边缘表面有裂痕,但玻璃未脱落。
--擦痕:指在镜片边缘之不良,一群短小之伤痕。
#80伤痕8mm,#60伤痕4mm,#40伤痕6mm
L’=(80/80)×8+(60/80)×4+(40/80)×6=14mm≦【1/2×40=20mm】=>允收
EX.3:规格为80/50,镜片直径40mm的镜片,检查镜片表面后,发现伤痕如下:
#60伤痕8mm,#40伤痕6mm,#20伤痕8mm
L’=(60/80)×8+(40/80)×6+(20/80)×8=10mm≦40mm=>允收L’=(60/80)×8+(40/80)×6+(20/80)×8=10mm≦40mm=>允收
80 dig =0.80 mmdiameter
50 dig =0.50 mmdiameter
40 dig =0.40 mmdiameter
20 dig =0.20 mmdiameter
10 dig =0.10 mmdiameter
--质量区域:以光轴为中心之一特定区域,该区域内之表面质量适用伤痕/亮点之规格,此质量区域以外之表面,除特别规定外,对质量没有要求(一般外观检验假定全球面为质量区域)
(5)镀膜后之反射膜的伤痕标准依照图纸”伤痕/亮点”之规格判定。
十、亮点(Dig)之判断标准:
(1)只有最大亮点时:
N’≦D/(20mm)
允收
D/(20mm)<1时以D/(20mm)=1计算(即镜片表面直径<20mm)
(整理)光学镜片外观检查规范

•光学镜片外观检查规范一、目的:1.提供镜片外观检查作业参考,降低判定差异。
一、目的:1.提供镜片外观检查作业参考,降低判定差异。
2.提供内部训练参考数据。
2.提供内部训练参考资料。
二、使用时机:精磨加工后或镀膜后之一般光学镜片外观检查二、使用时机:精磨加工后或镀膜后之一般光学镜片外观检查(如有特殊要求,于图纸注明之)(如有特殊要求,于图纸注明之)三、依据:USMIL-O-13830A 三、依据:USMIL-O-13830A四、伤痕/亮点(Scratch/Dig)四、伤痕/亮点(Scratch/Dig)(1)图纸上应标示每一球面对伤痕/亮点之允许标准与要求此项质量之区域。
(1)图纸上应标示每一球面对伤痕/亮点之允许标准与要求此项品质之区域。
(2)图纸对伤痕/亮点之规格指对此二种缺点允许的最大尺寸。
(2)图纸对伤痕/亮点之规格指对此二种缺点允许的最大尺寸。
EX.60/40 之外观规格 EX.60/40之外观规格60=允许最大伤痕尺寸 60=允许最大伤痕尺寸40=允许最大亮点尺寸 40=允许最大亮点尺寸(3)--伤痕(Scratch):线状之外观不良,等级定义如下:(3)--伤痕(Scratch):线状之外观不良,等级定义如下:160scratch=0.051 mm width 160scratch=0.051 mm width120scratch=0.020 mm width 120scratch=0.020 mm width80scratch=0.016 mm width 80scratch=0.016 mm width60scratch=0.012 mm width 60scratch=0.012 mm width40scratch=0.008 mm width 40scratch=0.008 mm width20scratch=0.004 mm width 20scratch=0.004 mm width--亮点(Dig):圆形之外观不良,如亮点、气泡、杂质、短伤痕、镀膜点状(喷--亮点(Dig):圆形之外观不良,如亮点、气泡、杂质、短伤痕、镀膜点状(喷药F)、刺伤、膜弱块状(W)、霉斑、云状、雾状、砂目药F)、刺伤、膜弱块状(W)、霉斑、云状、雾状、砂目等级定义如下:等级定义如下:100dig=1.00 mm diameter 100dig=1.00 mm diameter80 dig =0.80 mm diameter 80 dig =0.80 mm diameter50 dig =0.50 mm diameter 50 dig =0.50 mm diameter40 dig =0.40 mm diameter 40 dig =0.40 mm diameter20 dig =0.20 mm diameter 20 dig =0.20 mm diameter10 dig =0.10 mm diameter 10 dig =0.10 mm diameter--质量区域:以光轴为中心之一特定区域,该区域内之表面质量适用伤痕/亮点之规--品质区域:以光轴为中心之一特定区域,该区域内之表面品质适用伤痕/亮点之规格,此质量区域以外之表面,除特别规定外,对质量没有要求格,此品质区域以外之表面,除特别规定外,对品质没有要求(一般外观检验假定全球面为质量区域)(一般外观检验假定全球面为品质区域)五、裂边、裂痕与擦痕(Chips、Cracks&Bruises)五、裂边、裂痕与擦痕(Chips、Cracks&Bruises)(1)图纸上一般均标明允许最大裂边尺寸,但裂痕与擦伤通常未标示。
镜片外观检验培训教材日报XXXX0906

J059 镜片外观标准(3/7)
线状杂物
1.W<0.025mm,L<1mm,间距≥20mm每 片允许二条存在(深度以不泛白为准);
2.0.025mm≤W≤0.035mm,L≤1.5mm,每 片允许1个;W>0.035mm,NG,L>1.5mm NG
J059 镜片外观标准(4/7)
刮花/划伤
1.W<0.025mm,L<1mm,间距≥20mm每 片允许二条存在(深度以不泛白为准);
3、检 测 方 法: 1) 、接触镜片的手指需戴防静电指套,必要时戴防静电手套
2) 、检测员检验时,镜片字体或字母应正对检验员. 3) 、眼睛距镜片应在30—35cm.视线与镜片约呈45度角. 4) 、上下左右翻转镜片15度,视线在镜片上总共停留时间
为8—12秒(熟练时可适当缩短检测时间),未发现不良或 不良缺陷在标准范围内则判定合格.
2.0.025mm≤W≤0.035mm,L≤3mm,每片 允许1个;W>0.035mm,NG,L>3mm NG
J059 镜片外观标准(5/7)
边缘透光
W≤0.05 mm,L≤2mm,允 许;反之NG,另外正面看边缘不 可以有多墨现象;
破损/裂纹
不允许破损/裂纹现象.
J059 镜片外观标准(6/7)
追求卓越,让自己更好,向上而生。2020年11月26日星期 四上午10时48分35秒10:48:3520.11.26
严格把控质量关,让生产更加有保障 。2020年11月 上午10时48分20.11.2610:48November 26, 2020
重规矩,严要求,少危险。2020年11月26日 星期四10时48分35秒10:48:3526 November 2020
- 1、下载文档前请自行甄别文档内容的完整性,平台不提供额外的编辑、内容补充、找答案等附加服务。
- 2、"仅部分预览"的文档,不可在线预览部分如存在完整性等问题,可反馈申请退款(可完整预览的文档不适用该条件!)。
- 3、如文档侵犯您的权益,请联系客服反馈,我们会尽快为您处理(人工客服工作时间:9:00-18:30)。
光学镜片外观检查规范一、目的:1.提供鏡片外觀檢查作業參考,降低判定差異。
一、目的:1.提供镜片外观检查作业参考,降低判定差异。
2.提供內部訓練參考資料。
2.提供内部训练参考资料。
二、使用時機:精磨加工後或鍍膜後之一般光學鏡片外觀檢查二、使用时机:精磨加工后或镀膜后之一般光学镜片外观检查(如有特殊要求,於圖紙註明之)(如有特殊要求,于图纸注明之)三、依據:USMIL-O-13830A 三、依据:USMIL-O-13830A四、傷痕/亮點(Scratch/Dig)四、伤痕/亮点(Scratch/Dig)(1)圖紙上應標示每一球面對傷痕/亮點之允許標準與要求此項品質之區域。
(1)图纸上应标示每一球面对伤痕/亮点之允许标准与要求此项品质之区域。
(2)圖紙對傷痕/亮點之規格指對此二種缺點允許的最大尺寸。
(2)图纸对伤痕/亮点之规格指对此二种缺点允许的最大尺寸。
EX.60/40 之外觀規格EX.60/40之外观规格60=允許最大傷痕尺寸60=允许最大伤痕尺寸40=允許最大亮點尺寸40=允许最大亮点尺寸(3)--傷痕(Scratch):線狀之外觀不良,等級定義如下:(3)--伤痕(Scratch):线状之外观不良,等级定义如下:160scratch=0.051 mm width 160scratch=0.051 mm width120scratch=0.020 mm width 120scratch=0.020 mm width80scratch=0.016 mm width 80scratch=0.016 mm width60scratch=0.012 mm width 60scratch=0.012 mm width40scratch=0.008 mm width 40scratch=0.008 mm width20scratch=0.004 mm width 20scratch=0.004 mm width--亮點(Dig):圓形之外觀不良,如亮點、氣泡、雜質、短傷痕、鍍膜點狀(噴--亮点(Dig):圆形之外观不良,如亮点、气泡、杂质、短伤痕、镀膜点状(喷藥F)、刺傷、膜弱塊狀(W)、霉斑、雲狀、霧狀、砂目药F)、刺伤、膜弱块状(W)、霉斑、云状、雾状、砂目等級定義如下:等级定义如下:100dig=1.00 mm diameter 100dig=1.00 mm diameter80 dig =0.80 mm diameter 80 dig =0.80 mm diameter50 dig =0.50 mm diameter 50 dig =0.50 mm diameter40 dig =0.40 mm diameter 40 dig =0.40 mm diameter20 dig =0.20 mm diameter 20 dig =0.20 mm diameter10 dig =0.10 mm diameter 10 dig =0.10 mm diameter--品質區域:以光軸為中心之一特定區域,該區域內之表面品質適用傷痕/亮點之規--品质区域:以光轴为中心之一特定区域,该区域内之表面品质适用伤痕/亮点之规格,此品質區域以外之表面,除特別規定外,對品質沒有要求格,此品质区域以外之表面,除特别规定外,对品质没有要求(一般外觀檢驗假定全球面為品質區域)(一般外观检验假定全球面为品质区域)五、裂邊、裂痕與擦痕(Chips、Cracks&Bruises)五、裂边、裂痕与擦痕(Chips、Cracks&Bruises)(1)圖紙上一般均標明允許最大裂邊尺寸,但裂痕與擦傷通常未標示。
(1)图纸上一般均标明允许最大裂边尺寸,但裂痕与擦伤通常未标示。
(2)--裂邊:指在鏡片邊緣之不良,鏡片邊緣表面有部份玻璃脫落。
(2)--裂边:指在镜片边缘之不良,镜片边缘表面有部份玻璃脱落。
--裂痕:指在鏡片邊緣之不良,鏡片邊緣表面有裂痕,但玻璃未脫落。
--裂痕:指在镜片边缘之不良,镜片边缘表面有裂痕,但玻璃未脱落。
--擦痕:指在鏡片邊緣之不良,一群短小之傷痕。
--擦痕:指在镜片边缘之不良,一群短小之伤痕。
(3)除特別規定外,此三項不良可依裂邊之規格來判斷允收否。
(3)除特别规定外,此三项不良可依裂边之规格来判断允收否。
六、髒污或霉斑(Stain)六、脏污或霉斑(Stain)(1)髒污或霉斑:指鏡片表面變色的區域,如水痕、口水、泡沫狀、霧狀、雲狀、刺孔狀….. (1)脏污或霉斑:指镜片表面变色的区域,如水痕、口水、泡沫状、雾状、云状、刺孔状….. 等等,由於鍍膜前鏡片表面不乾淨而覆蓋於膜下。
等等,由于镀膜前镜片表面不干净而覆盖于膜下。
(2)可由透視法或反射法發現(2)可由透视法或反射法发现<і>一般依照傷痕/亮點之規格來判斷允收否。
<і>一般依照伤痕/亮点之规格来判断允收否。
<іі>水痕之邊線依照傷痕之規格來判斷允收否。
<іі>水痕之边线依照伤痕之规格来判断允收否。
--------------------------------------------------------------------------------Page 2 Page 23FL., NO.15, WUCHIUAN RD., WUGU SHIANG, TAIPEI, TAIWAN, ROC 3FL., NO.15, WUCHIUAN RD., WUGU SHIANG, TAIPEI, TAIWAN, ROC.***************.TW七、外觀檢驗應具備事項:七、外观检验应具备事项:(1)圖紙:標示外觀要求之規格與區域。
(1)图纸:标示外观要求之规格与区域。
(2)標準板:標示外觀之標準傷痕/亮點之參考樣板。
(2)标准板:标示外观之标准伤痕/亮点之参考样板。
(3)檢驗條件:20W 的日光燈(或100W 的燈泡)。
(3)检验条件:20W的日光灯(或100W的灯泡)。
(4)檢驗環境:前、上、下、左、右均為黑色之不反光物。
(4)检验环境:前、上、下、左、右均为黑色之不反光物。
(5)放大鏡(4 倍):檢查#60 或#60 以下之傷痕。
(5)放大镜(4倍):检查#60或#60以下之伤痕。
八、檢查方式:八、检查方式:(1)透視法:鏡片置於光源前四方形孔之前3 公分偏下,稍微傾斜鏡片檢驗的檢驗方法。
(1)透视法:镜片置于光源前四方形孔之前3公分偏下,稍微倾斜镜片检验的检验方法。
(2)反射法:鏡片置於燈光下的桌面上,前後稍微搖晃鏡片的檢驗方法。
(2)反射法:镜片置于灯光下的桌面上,前后稍微摇晃镜片的检验方法。
--不論透視法或反射法,被測面均朝向檢查員。
--不论透视法或反射法,被测面均朝向检查员。
九、傷痕(Scratch)之判斷標準:九、伤痕(Scratch)之判断标准:(1)只有最大傷痕時:(1)只有最大伤痕时:L’=≦1/4×D允收允收(2)同時有最大傷痕與較小傷痕時:(2)同时有最大伤痕与较小伤痕时:L’=Σ【(W/N)×L】≦1/2×D允收允收(3)只有較小傷痕時:(3)只有较小伤痕时:L’=Σ【(W/N)×L】≦D允收允收L’=傷痕換算之總長度L’=伤痕换算之总长度W=傷痕寬度W=伤痕宽度N=要求之傷痕規格N=要求之伤痕规格L=該級傷痕長度L=该级伤痕长度D=鏡片表面直鏡D=镜片表面直镜(4)EX.1:規格為80/50,鏡片直徑40mm 的鏡片,檢查鏡片表面後,發現傷痕如下:(4)EX.1:规格为80/50,镜片直径40mm的镜片,检查镜片表面后,发现伤痕如下:#80 傷痕8mm #80伤痕8mmL’=8mm≦1/4×40=10mm=>允收L’=8mm≦1/4×40=10mm=>允收EX.2:規格為80/50 鏡片直徑8.2mm 的鏡片檢查鏡片表面後,發現傷痕如下:EX.2:规格为80/50镜片直径8.2mm的镜片检查镜片表面后,发现伤痕如下:#80 傷痕8mm,#60 傷痕4mm,#40 傷痕6mm #80伤痕8mm,#60伤痕4mm,#40伤痕6mmL’=(80/80)×8+(60/80)×4+(40/80)×6=14mm≦【1/2×40=20mm】=>允收L’=(80/80)×8+(60/80)×4+(40/80)×6=14mm≦【1/2×40=20mm】=>允收EX.3:規格為80/50,鏡片直徑40mm 的鏡片,檢查鏡片表面後,發現傷痕如下:EX.3:规格为80/50,镜片直径40mm的镜片,检查镜片表面后,发现伤痕如下:#60 傷痕8mm,#40 傷痕6mm,#20 傷痕8mm #60伤痕8mm,#40伤痕6mm,#20伤痕8mmL’=(60/80)×8+(40/80)×6+(20/80)×8=10mm≦40mm=>允收L’=(60/80)×8+(40/80)×6+(20/80)×8=10mm≦40mm=>允收(5)鍍膜後之反射膜的傷痕標準依照圖紙”傷痕/亮點”之規格判定。
(5)镀膜后之反射膜的伤痕标准依照图纸”伤痕/亮点”之规格判定。
十、亮點(Dig)之判斷標準:十、亮点(Dig)之判断标准:(1)只有最大亮點時:(1)只有最大亮点时:N’≦D/(20mm)允收允收D/(20mm)<1 時以D/(20mm)=1 計算(即鏡片表面直徑<20mm)D/(20mm)<1时以D/(20mm)=1计算(即镜片表面直径<20mm)(2)同時有最大亮點與較小亮點時:N’=Σ【(d’/d×N)】≦2×(D/(20mm))允收(2)同时有最大亮点与较小亮点时:N’=Σ【(d’/d×N)】≦2×(D/(20mm))允收N’=亮點換算之最多允許個數d=亮點大小N’=亮点换算之最多允许个数d=亮点大小d=要求之亮點規格d=要求之亮点规格N=該級亮點個數N=该级亮点个数D=鏡片表面直徑D=镜片表面直径(3)EX.1:規格為80/50,鏡片直徑12mm 的鏡片,檢查鏡片表面後,發現亮點如下:(3)EX.1:规格为80/50,镜片直径12mm的镜片,检查镜片表面后,发现亮点如下:#50 亮點1 個#50亮点1个N’=1 個=(12/20=1 個)=>允收N’=1个=(12/20=1个)=>允收EX.2:規格為80/50,鏡片直徑40mm 的鏡片,檢查鏡片表面後,發現亮點如下:EX.2:规格为80/50,镜片直径40mm的镜片,检查镜片表面后,发现亮点如下:#50 亮點1 個#50亮点1个N’=1 個≦(40/20=2 個)=>允收N’=1个≦(40/20=2个)=>允收--------------------------------------------------------------------------------Page 3 Page 33FL., NO.15, WUCHIUAN RD., WUGU SHIANG, TAIPEI, TAIWAN, ROC 3FL., NO.15, WUCHIUAN RD., WUGU SHIANG, TAIPEI, TAIWAN, ROC.***************.TWEX.3:規格為80/50,鏡片直徑40mm 的鏡片,檢查鏡片表面後,發現亮點如下:EX.3:规格为80/50,镜片直径40mm的镜片,检查镜片表面后,发现亮点如下:#50 亮點1 個,#40 亮點1 個,#20 亮點3 個#50亮点1个,#40亮点1个,#20亮点3个N’=(50/50)×1+(40/50)×1+(20/50)×3=3 個≦2×(40/20)=4 個=>允收N’=(50/50)×1+(40/50)×1+(20/50)×3=3个≦2×(40/20)=4个=>允收EX.4:規格為80/50,鏡片直徑40mm 的鏡片,檢查鏡片表面後,發現亮點如下:EX.4:规格为80/50,镜片直径40mm的镜片,检查镜片表面后,发现亮点如下:#50 亮點0 個,#40 亮點2 個,#20 亮點5 個#50亮点0个,#40亮点2个,#20亮点5个N’=(50/50)×0+(40/50)×2+(20/50)×5=3.6 個≦2×(40/20)=4 個=>允收N’=(50/50)×0+(40/50)×2+(20/50)×5=3.6个≦2×(40/20)=4个=>允收(4)鍍膜後反射檢查膜上之亮點標準依照圖紙傷痕/亮點的規格(4)镀膜后反射检查膜上之亮点标准依照图纸伤痕/亮点的规格(5)計算等值亮點時,0.002mm 至0.005mm 的亮點可忽略(5)计算等值亮点时,0.002mm至0.005mm的亮点可忽略十一、簡易換算表:十一、简易换算表:(1)傷痕(Scratch)(1)伤痕(Scratch)最大傷痕→最大伤痕→傷痕規格↓伤痕规格↓#120#80#60#40#20#10#1201/4D1.5D3.0D6.0D12.0D#801/4D1.3D2.0D4.0D8.0D#601/4D1.5D3.0D6.0D#401/4D2.0D4.0D#201/4D2.0D#101/4D(2)亮點(Dig)(2)亮点(Dig)直徑(mm)直径(mm)允收最大亮點數允收最大亮点数允收最大等值亮點數允收最大等值亮点数0-201220-402440-603660-804880-100510100-12012120-140 714。