压铸带冷却浇口套制作工艺
浇口套的工艺路线

一、零件的工艺分析二、毛坯选择和基准的确定三、拟定工艺路线1 选择加工方法φ40(IT10、Ra=6.3):粗车一半精车φ30(IT6、Ra=0.8):粗车一半精车一粗磨一精磨R8球面:粗车一半精车一粗磨(研磨)小锥孔:钻一铰一精铰一研磨端面、轴肩、槽:粗车一半精车2 划分工艺阶段零件需热处理,可以热处理为界分为粗、精两个加工阶段;3 确定划分工序原则零件为单件生产,以工序集中的原则划分工序较好;4 确定加工顺序粗车端面、粗车φ40外圆(留余量)、粗车端面、半精车端面、钻φ4孔、粗车φ30外圆、退刀槽、半精车φ30外圆、退刀槽、铰锥孔(留研磨余量)、半精车端面(保证长度尺寸)、半精车外圆φ40、车R8球面、研磨锥孔、球面、磨φ30外圆5 拟定工艺方案并比较其优劣工艺方案一:备料(锻、退火)—→车(粗车端面、粗车φ40外圆(留余量)、粗车端面、半精车端面、钻φ4孔、粗车φ30外圆、退刀槽、半精车φ30外圆、退刀槽、铰锥孔(留研磨余量)、半精车端面(保证长度尺寸)、半精车外圆φ40、车R8球面) —→检验—→热处理(硬度HRC60~64)—→研磨(研磨锥孔、球面)—→磨削(磨φ30外圆)—→检验工艺方案二:备料(锻、退火)—→车(粗车端面、半精车端面、钻φ4孔、粗车φ30外圆、退刀槽、半精车φ30外圆、退刀槽、铰锥孔(留研磨余量)、粗车端面、半精车端面(保证长度尺寸)、粗车φ40外圆、半精车外圆φ40、车R8球面) —→检验—→热处理(硬度HRC60~64)—→研磨(研磨锥孔、球面)—→磨削(磨φ30外圆)—→检验比较:方案一有三个安装,优点是大部分加工以精基准定位,装夹可靠,加工精度容易保证;方案二只有两个安装,虽然辅助工时减少,但大部分加工以粗基准定位,装夹不是很可靠,加工精度难以保证;本零件为单件生产,以保证加工精度为要,确定方案一为该零件的加工工艺路线。
6 确定工艺路线四、查各工序加工余量φ40(IT10、Ra=6.3):粗车(2)一半精车(1.4)φ30(IT6、Ra=0.8):粗车(2)一半精车(1.3)一粗磨(0.12)一精磨(0.08)〔磨(0.2)〕端面:粗车(1〔锻件粗糙应适当加大余量至2〕)一半精车(1) 一磨(轴肩0.3)R8球面:粗车一半精车一粗磨(研磨)小锥孔:钻一铰一精铰一研磨五、计算各工序尺寸并确定其公差(2)侧型芯滑块的加工1)结构:如图2-15所示。
精密铸造铸件工艺及浇冒口系统设计

第六章铸件工艺设计第一节概述为了生产优质而价廉的包模铸件,做好工艺设计是十分重要的。
在做工艺设计之前,首先要考虑选用包模铸造工艺生产时,在质量、工艺和经济方面的几个问题。
1.铸件质量的可靠性对于铸件质量上的要求,一般是包括两个方面,一是保证技术要求的尺寸精度、几何精度和表面光洁度,二是保证机械性能和其它工作性能等内在质量方面的要求。
包模铸造具有少切削、无切削的突出优点。
近年来,由于冶金技术、制模、制壳材料和工艺以及检测技术等方面的发展,包模铸件的外部和内在质量不断提高,所以它的应用范围愈来愈广。
不少锻件、焊接件、冲压件和切削加工件,都可以用熔模铸造方法生产。
这对于节约机械加工工时和费用,节约金属材料,提高劳动生产率和降低成本都具有很大意义。
但是,熔模铸造生产的铸件,由于冶金质量、热型浇注引起的晶粒粗大、表面脱碳以及内部缩松等方面的原因,铸件的机械性能(尤其是塑性),还存在一些缺陷。
对于某些受力大和气密性要求高的铸件,采用包模铸造时,应充分考虑零件在产品上的作用和性能要求,以确保其使用可靠。
有些结构件改用包模铸造生产时,必须考虑原用合金的铸造性能是否能满足零件的质量要求,否则就需要更改材质。
2.生产工艺上的可能性和简易性熔模铸造虽然可以铸造形状十分复杂的、加工量甚少甚至不加工的零件,但零件的材质、结构形状、尺寸大小和重量等,必须符合熔模铸造本身的工艺要求。
如铸件最小壁厚、最大重量、最大平面面积、最小孔槽以及精度和光洁度要求等,都要考虑到工艺上的可能性和简易性。
3.经济上的合理性采用包模铸造在经济上是否合理,要从多方面考虑。
按每公斤的价格来说,包模铸件与同类型锻件相近甚至还高些,但是由于大幅度减少了加工量,因而零件最终成本还是低的。
但也有些零件,可以利用机械化程度较高的方法生产,例如用自动机床高速加工、精密锻造、冷挤压、压力铸造等等,这时,用包模铸造法生产在经济上的优越性就不一定显著,甚至成本还可能高一些,所以在这种情况下,就不一定选用这种方法了。
铝合金轮毂低压铸造浇口套的改进
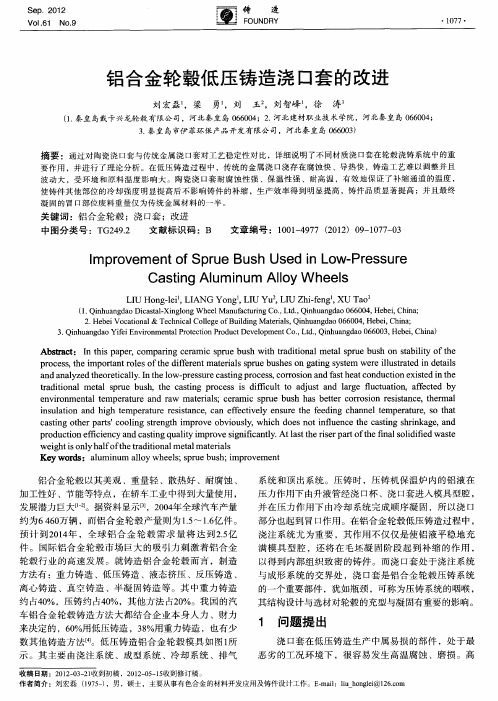
以得到 内部组 织致 密 的铸件 。而 浇 口套处 于浇 注系统 与成 形 系统 的交 界处 ,浇 口套是 铝合金 轮毂 压铸 系统 的一个 重要部件 ,犹如瓶颈 ,可称 为压铸 系统 的咽喉 , 其结构设 计与选材对 轮毂 的充 型与凝 固有重要 的影响 。
1 问题 提 出
浇 口套在低 压铸 造生 产 中属易 损 的部件 ,处 于最 恶劣 的工 况环 境下 ,很容 易 发生高 温腐 蚀 、磨损 。高
收稿 日期 :2 1- 3 2 收到初稿 ,2 1- 5 1 收到修订稿 。 020— 1 02 —5 0 作 者简 介:刘宏磊 (9 5 ) 17 一 ,男 ,硕士 ,主要从事有色合金的材料开发应用及铸件设计工作 。E mal i h n li 16cm — i u o ge@ 2 . :l o
系统和 顶 出系统 。压铸 时 ,压铸 机保 温炉 内 的铝 液在
压力作 用下 由升液管经浇 口杯 、浇 口套进入模 具型腔 ,
并 在压 力作用 下 由冷却 系 统完成顺 序 凝 固 ,所 以浇 口 部分也 起到 冒 口作 用 。在铝合 金轮 毂低压铸造 过程 中 , 浇 注系 统尤 为重要 ,其 作用 不仅 仅是 使铝 液平稳 地充
t dt n lmea s re b s h at g po esi dfc l t duta d lref c ain f ce y r io a a i tl pu u} te cs n rc s S i ut o aj s n ag u t t ,af td b L i 五 l u o e
S .2 2 ep 01
V . NO. oI 61 9
铸
造
FOUNDRY
铝合金轮 毂低 压铸造浇 口套 的改进
压铸工艺

压铸工艺模锻工艺简介压铸模锻工艺是一种在专用的压铸模锻机上完成的工艺。
它的基本工艺过程是:金属液先低速或高速铸造充型进模具的型腔内,模具有活动的型腔面,它随着金属液的冷却过程加压锻造,既消除毛坯的缩孔缩松缺陷,也使毛坯的内部组织达到锻态的破碎晶粒。
毛坯的综合机械性能得到显著的提高。
另外,该工艺生产出来的毛坯,外表面光洁度达到7级(Ra1.6),如冷挤压工艺或机加工出来的表面一样,有金属光泽。
所以,我们将压铸模锻工艺称为“极限成形工艺”,比“无切削、少余量成形工艺”更进了一步。
压铸模锻工艺还有一个优势特点是,除了能生产传统的铸造材料外,它还能用变形合金、锻压合金,生产出结构很复杂的零件。
这些合金牌号包括:硬铝超硬铝合金、锻铝合金,如LY11、LY12、6061、6063、LYC、LD等)。
这些材料的抗拉强度,比普通铸造合金高近一倍,对于铝合金汽车轮毂、车架等希望用更高强度耐冲击材料生产的部件,有更积极的意义。
一、压铸简介压力铸造简称压铸,是一种将熔融合金液倒入压室内,以高速充填钢制模具的型腔,并使合金液在压力下凝固而形成铸件的铸造方法。
压铸区别于其它铸造方法的主要特点是高压和高速。
①金属液是在压力下填充型腔的,并在更高的压力下结晶凝固,常见的压力为15—100MPa。
②金属液以高速充填型腔,通常在10—50米/秒,有的还可超过80米/秒,(通过内浇口导入型腔的线速度—内浇口速度),因此金属液的充型时间极短,约0.01—0.2秒(须视铸件的大小而不同)内即可填满型腔。
压铸机、压铸合金与压铸模具是压铸生产的三大要素,缺一不可。
所谓压铸工艺就是将这三大要素有机地加以综合运用,使能稳定地有节奏地和高效地生产出外观、内在质量好的、尺寸符合图样或协议规定要求的合格铸件,甚至优质铸件。
1、压铸机(1)压铸机的分类压铸机按压室的受热条件可分为热压室与冷压室两大类。
而按压室和模具安放位置的不同,冷室压铸机又可分为立式、卧式和全立式三种形式的压铸机。
压铸模具更换浇口套分流锥作业标准
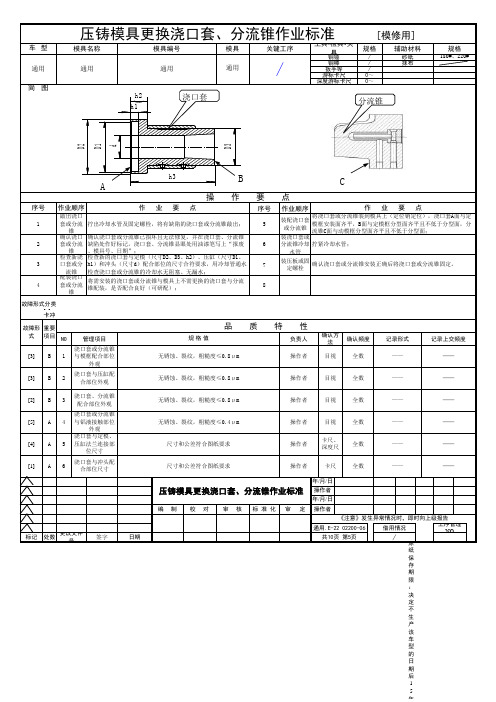
模具序号作业顺序5装配浇口套或分流锥6装浇口套或分流锥冷却水管7装压板或固定螺栓8[1]卡冲NO [3]B1[3]B 2[2]B 3[5]A 4[4]A 5[1]A 6编 制校 对审 核标 准 化审 定标记处数签字日期原纸保存期限:决定不生产该车型的日期后15年更改文件号共10页 第5页/《注意》发生异常情况时,即时向上级报告操作者操作者通用.E-22 02200-06借用情况工序管理NO——压铸模具更换浇口套、分流锥作业标准年/月/日浇口套与冲头配合部位尺寸尺寸和公差符合图纸要求操作者卡尺全数——年/月/日——浇口套与定模、压缸法兰连接部位尺寸尺寸和公差符合图纸要求操作者卡尺、深度尺全数————浇口套或分流锥与铝液接触部位外观无锈蚀、裂纹,粗糙度≤0.4μm 操作者目视全数————浇口套、分流锥配合部位外观无锈蚀、裂纹,粗糙度≤0.8μm 操作者目视全数————浇口套与压缸配合部位外观无锈蚀、裂纹,粗糙度≤0.8μm 操作者目视全数——记录上交频度浇口套或分流锥与模框配合部位外观无锈蚀、裂纹,粗糙度≤0.8μm操作者目视全数————故障形式分类故障形式重要项目品 质 特 性管理项目规 格 值负责人确认方法确认频度记录形式3检查新浇口套或分流锥检查新的浇口套与定模(尺寸D2、D3、h2)、压缸(尺寸D1、h1)和冲头(尺寸d)配合部位的尺寸合符要求,用冷却管通水检查浇口套或分流锥的冷却水无阻塞、无漏水;确认浇口套或分流锥安装正确后将浇口套或分流锥固定。
4配装浇口套或分流锥将需安装的浇口套或分流锥与模具上不需更换的浇口套与分流锥配装,是否配合良好(可研配);1敲出浇口套或分流锥拧出冷却水管及固定螺栓,将有缺陷的浇口套或分流锥敲出;将浇口套或分流锥装到模具上(定位销定位),浇口套A面与定模框安装面齐平,B面与定模框分型面齐平且不低于分型面,分流锥C面与动模框分型面齐平且不低于分型面;2确认浇口套或分流锥确认浇口套或分流锥已损坏且无法修复,并在浇口套、分流锥缺陷处作好标记,浇口套、分流锥显眼处用油漆笔写上“报废、模具号、日期”;拧紧冷却水管;操 作 要 点序号作业顺序作 业 要 点作 业 要 点0~简 图通用通用通用通用/深度游标卡尺/游标卡尺0~/砂纸180#、220#铜棒/抹布铜锤扳手等压铸模具更换浇口套、分流锥作业标准 [模修用]车 型模具名称模具编号关键工序工具•检具•夹具规格辅助材料规格4h 1h2h3dD 1D 2D 3浇口套分流锥ABC。
压铸件的工艺流程
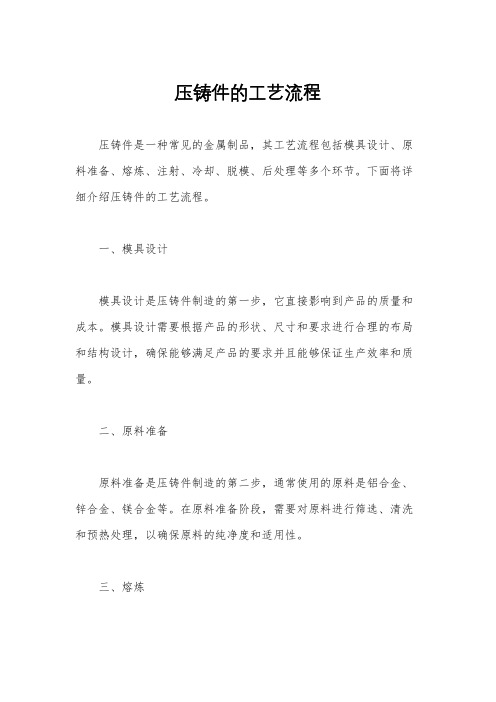
压铸件的工艺流程压铸件是一种常见的金属制品,其工艺流程包括模具设计、原料准备、熔炼、注射、冷却、脱模、后处理等多个环节。
下面将详细介绍压铸件的工艺流程。
一、模具设计模具设计是压铸件制造的第一步,它直接影响到产品的质量和成本。
模具设计需要根据产品的形状、尺寸和要求进行合理的布局和结构设计,确保能够满足产品的要求并且能够保证生产效率和质量。
二、原料准备原料准备是压铸件制造的第二步,通常使用的原料是铝合金、锌合金、镁合金等。
在原料准备阶段,需要对原料进行筛选、清洗和预热处理,以确保原料的纯净度和适用性。
三、熔炼熔炼是将原料加热至熔化状态的过程,通常使用电炉或燃气炉进行熔炼。
在熔炼过程中,需要控制炉温和炉内气氛,确保原料能够完全熔化并且保持一定的温度。
四、注射注射是将熔化的金属液注入模具腔体的过程,通常使用压铸机进行注射。
在注射过程中,需要控制注射速度和压力,确保金属液能够充分填充模具腔体并且形成完整的产品形状。
五、冷却冷却是将注射后的模具进行冷却的过程,通常使用冷却水或风冷设备进行冷却。
在冷却过程中,需要控制冷却速度和温度,确保产品能够快速冷却并且保持一定的结构和硬度。
六、脱模脱模是将冷却后的产品从模具中取出的过程,通常使用振动或冲击的方式进行脱模。
在脱模过程中,需要注意保护产品表面,避免产生划痕或变形。
七、后处理后处理是对脱模后的产品进行去除余料、修磨、喷漆等加工的过程。
在后处理过程中,需要根据产品的要求进行相应的处理,以确保产品的表面光滑、尺寸精度和表面质量。
总结压铸件的工艺流程包括模具设计、原料准备、熔炼、注射、冷却、脱模、后处理等多个环节,每个环节都需要严格控制和操作,以确保产品的质量和成本。
压铸件制造是一个复杂的工艺过程,需要生产厂家具备一定的设备和技术实力,以满足客户的需求。
压铸模具更换浇口套、分流锥作业标准

浇口套与定模、 [4] A 5 压缸法兰连接部
位尺寸
[1]
A
Hale Waihona Puke 6浇口套与冲头配 合部位尺寸
标记 处数 更改文件号 签字
日期
品质
规格值
无锈蚀、裂纹,粗糙度≤0.8μm
特性
负责人
确认方法 确认频度
操作者
目视
全数
记录形式 ——
记录上交频度 ——
无锈蚀、裂纹,粗糙度≤0.8μm
操作者
目视
全数
——
——
无锈蚀、裂纹,粗糙度≤0.8μm
车型 通用 简图
模具名称 通用
压铸模具更换浇口套、分流锥作业标准
模具编号 通用
模具 通用
关键工序
/
工具•检具•夹
具
铜锤 铜棒 扳手等 游标卡尺 深度游标卡尺
规格
/ / / 0~250mm 0~200mm
辅助材料
砂纸 抹布
h2
浇口套
h1
分流锥
规格
180#、220#
D2 D1 d D3
序号
1 2 3 4
通用.E-22 02200-06 共10页 第5页
借用情况
/
工序管理NO
原 纸 保 存 期 限 : 决 定 不 生 产 该 车 型 的 日 期 后
15 年
A
作业顺序
h3
B
操作
作业要点
敲出浇口套 或分流锥
拧出冷却水管及固定螺栓,将有缺陷的浇口套或分流锥敲出;
确认浇口套 或分流锥
确认浇口套或分流锥已损坏且无法修复,并在浇口套、分流锥缺 陷处作好标记,浇口套、分流锥显眼处用油漆笔写上“报废、模 具号、日期”;
压铸成型工艺

定义与特点高效率生产周期短,适用于大批量生产。
高精度压铸成型工艺能够实现较高的尺寸精度和表面光洁度。
定义压铸成型是一种金属铸造工艺,通过高压将熔融金属注入金属模具中,快速冷却凝固后得到所需形状的零件或产品。
优良力学性能压铸件具有优良的力学性能和耐磨性。
广泛适应性可用于铸造各种合金,如铝合金、锌合金、铜合金等。
压铸成型工艺的应用领域电子工业建筑五金散热器、外壳、连接器等。
门窗五金、卫浴五金等。
汽车工业家用电器其他领域发动机零件、车身结构件、传动系统零件等。
洗衣机零件、电视机零件、空调零件等。
航空航天、军事、医疗器械等。
发展历程及现状发展历程压铸成型工艺起源于19世纪末,随着工业革命的推进和金属加工技术的发展,逐渐成为一种重要的金属成型方法。
20世纪中期以后,随着压铸机和模具制造技术的进步,压铸成型工艺得到了快速发展。
现状目前,压铸成型工艺已经成为一种成熟的制造技术,广泛应用于各个领域。
随着新材料、新工艺的不断涌现,压铸成型工艺也在不断发展和完善,向着更高精度、更高效率、更环保的方向发展。
同时,随着数字化、智能化技术的应用,压铸成型工艺的自动化和智能化水平也在不断提高。
03在压铸过程中,金属液在高压下快速充填模具型腔,确保金属液充分占据型腔并复制模具表面的细节。
高压充填原理金属液在凝固过程中会产生收缩,压铸工艺通过控制压射压力和速度,以及模具温度等因素,实现对凝固收缩的补偿。
凝固收缩补偿当金属液完全凝固后,通过开模机构将模具分型面打开,利用顶出机构将压铸件从模具中顶出。
压铸件脱模压铸成型工艺原理压铸机类型及结构热室压铸机主要用于锌、镁等低熔点合金的压铸。
其压室直接浸在保温坩埚的金属液中,结构简单、紧凑、易于维护。
冷室压铸机适用于铝、铜等高熔点合金的压铸。
其压室与保温炉分开,通过给汤机将金属液浇入压室。
冷室压铸机分为卧式和立式两种结构。
压铸机主要部件包括合模机构、压射机构、液压系统、电气控制系统等。
其中,合模机构用于实现模具的开合和锁紧;压射机构用于提供金属液的充填压力和速度;液压系统为压铸机提供动力;电气控制系统负责整个压铸过程的自动化控制。
压铸模具设计分析之浇注系统,流道宽度厚度横截面积大小的由来

压铸模具设计分析之浇注系统,流道宽度厚度横截面积大小的由来之前我们讲解了关于压铸件的工艺分析,现在浇注系统设计压铸模的浇注系统是压铸机压室内熔融的金属液在高温高压高速状态下充填压铸模型腔的通道,是压铸模设计的重要环节。
浇注系统的设计必须采用理论和实践相结合的方法。
浇注系统设计浇道的形式-按位置可分为侧浇口,环形浇口,中心浇口三类浇注系统设计内浇口的设计-基本方式内浇口的设计-基本类型内浇口面积的确定-计算公式内浇口厚度的确定-经验数据横浇道的基本结构设计横浇道的基本结构设计横浇道的基本结构设计浇道结构设计的要点:计算每一横浇道的分支-是设计师的基本功1横浇道的截面积应从直浇道到内浇口保持均匀或逐渐缩小,不允许有突然的扩大或缩小现象,以免产生涡流。
对于扩张式横浇道,其人口处与出口处的比值一般不超过1 :1.5,对于内浇口宽度较大的铸件,可超过此值。
圆弧形状的横浇道可以减少金属液的流动阻力,但截面积应逐渐缩小,防止涡流裹气。
圆弧形横浇道出口处的截面积应比人口处减小10%~ 30 %。
横浇道与内浇口的连接形式内浇口连接段L宜短些,便于压铸后道去除浇口突出毛刺排溢系统的设计-溢流槽常说的渣包究竟要开多大?溢流槽容积表溢流槽的截面形状排溢系统的设计-排气槽1排气道的总截面积一-般不小于内浇口总截面积的50%,但不得超过内浇口的总截面积。
2当需要增大排气道截面积时,以增大排气道的宽度或增加排气道的数量为宜。
不应过分增加排气道的厚度,以防止金属液的溅出。
3应尽量避免金属液过早地封闭分型面和排气道, 削弱排气功能。
4设计排气道应留有修正的余地,并在试模现场,结合实际,随时补充和调整。
⑤排气道应便于清理,保持排气道的有效功能。
5排气道可与溢流槽连接,但排气道应避免相互串通,以免排气干扰受阻。
6在直对操作区或人员流动的区域,不应设置平直引出的排气道,以免高温的金属液和气体向外喷溅伤人。
溢流槽容积表溢流槽的截面形状排溢系统的设计-排气槽1排气道的总截面积一-般不小于内浇口总截面积的50%,但不得超过内浇口的总截面积。
压铸模的浇口套及分流锥的设计
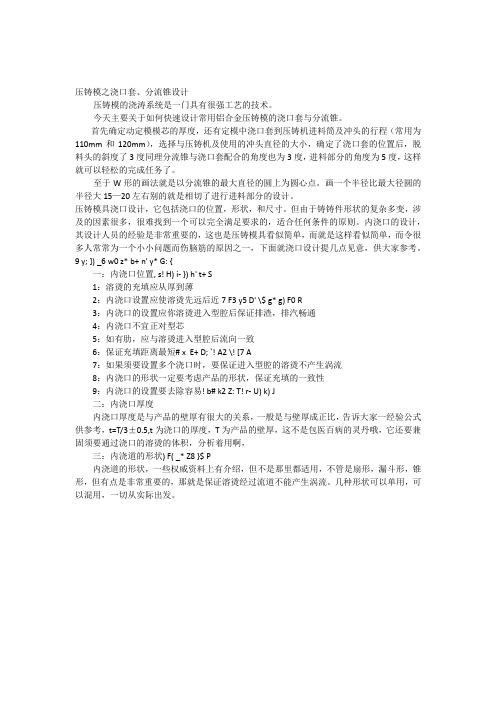
压铸模之浇口套、分流锥设计压铸模的浇涛系统是一门具有很强工艺的技术。
今天主要关于如何快速设计常用铝合金压铸模的浇口套与分流锥。
首先确定动定模模芯的厚度,还有定模中浇口套到压铸机进料筒及冲头的行程(常用为110mm和120mm),选择与压铸机及使用的冲头直径的大小,确定了浇口套的位置后,脱料头的斜度了3度同理分流锥与浇口套配合的角度也为3度,进料部分的角度为5度,这样就可以轻松的完成任务了。
至于W形的画法就是以分流锥的最大直径的圆上为圆心点。
画一个半径比最大径圆的半径大15—20左右别的就是相切了进行进料部分的设计。
压铸模具浇口设计,它包括浇口的位置,形状,和尺寸。
但由于铸铸件形状的复杂多变,涉及的因素很多,很难找到一个可以完全满足要求的,适合任何条件的原则。
内浇口的设计,其设计人员的经验是非常重要的,这也是压铸模具看似简单,而就是这样看似简单,而令很多人常常为一个小小问题而伤脑筋的原因之一,下面就浇口设计提几点见意,供大家参考。
9 y; ]) _6 w0 z* b+ n' y* G: {一:内浇口位置, s! H) i- }) h' t+ S1:溶烫的充填应从厚到薄2:内浇口设置应使溶烫先远后近7 F3 y5 D' \$ g* g) F0 R3:内浇口的设置应你溶烫进入型腔后保证排渣,排汽畅通4:内浇口不宜正对型芯5:如有肋,应与溶烫进入型腔后流向一致6:保证充填距离最短# x E+ D; `! A2 \! [7 A7:如果须要设置多个浇口时,要保证进入型腔的溶烫不产生涡流8:内浇口的形状一定要考虑产品的形状,保证充填的一致性9:内浇口的设置要去除容易! b# k2 Z: T! r- U) k) J二:内浇口厚度内浇口厚度是与产品的壁厚有很大的关系,一般是与壁厚成正比,告诉大家一经验公式供参考,t=T/3±0.5,t为浇口的厚度,T为产品的壁厚,这不是包医百病的灵丹哦,它还要兼固须要通过浇口的溶烫的体积,分析着用啊,三:内浇道的形状) F( _* Z8 }$ P内浇道的形状,一些权威资料上有介绍,但不是那里都适用,不管是扇形,漏斗形,锥形,但有点是非常重要的,那就是保证溶烫经过流道不能产生涡流。
压铸的工艺过程,特点,优点

压铸模锻工艺简介压铸模锻工艺是一种在专用的压铸模锻机上完成的工艺。
它的基本工艺过程是:金属液先低速或高速铸造充型进模具的型腔内,模具有活动的型腔面,它随着金属液的冷却过程加压锻造,既消除毛坯的缩孔缩松缺陷,也使毛坯的内部组织达到锻态的破碎晶粒。
毛坯的综合机械性能得到显著的提高。
另外,该工艺生产出来的毛坯,外表面光洁度达到7级(Ra1.6),如冷挤压工艺或机加工出来的表面一样,有金属光泽。
所以,我们将压铸模锻工艺称为“极限成形工艺”,比“无切削、少余量成形工艺”更进了一步。
压铸模锻工艺还有一个优势特点是,除了能生产传统的铸造材料外,它还能用变形合金、锻压合金,生产出结构很复杂的零件。
这些合金牌号包括:硬铝超硬铝合金、锻铝合金,如LY11、LY12、6061、6063、LYC、LD等)。
这些材料的抗拉强度,比普通铸造合金高近一倍,对于铝合金汽车轮毂、车架等希望用更高强度耐冲击材料生产的部件,有更积极的意义。
一、压铸简介压力铸造简称压铸,是一种将熔融合金液倒入压室内,以高速充填钢制模具的型腔,并使合金液在压力下凝固而形成铸件的铸造方法。
压铸区别于其它铸造方法的主要特点是高压和高速。
①金属液是在压力下填充型腔的,并在更高的压力下结晶凝固,常见的压力为15—100MPa。
②金属液以高速充填型腔,通常在10—50米/秒,有的还可超过80米/秒,(通过内浇口导入型腔的线速度—内浇口速度),因此金属液的充型时间极短,约0.01—0.2秒(须视铸件的大小而不同)内即可填满型腔。
压铸机、压铸合金与压铸模具是压铸生产的三大要素,缺一不可。
所谓压铸工艺就是将这三大要素有机地加以综合运用,使能稳定地有节奏地和高效地生产出外观、内在质量好的、尺寸符合图样或协议规定要求的合格铸件,甚至优质铸件。
1、压铸机(1)压铸机的分类压铸机按压室的受热条件可分为热压室与冷压室两大类。
而按压室和模具安放位置的不同,冷室压铸机又可分为立式、卧式和全立式三种形式的压铸机。
冲压,压铸,模锻,低压铸造等26种常见金属成型工艺
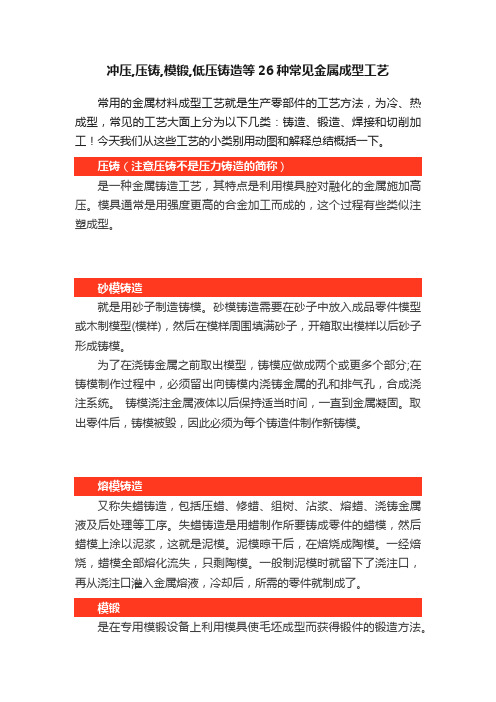
冲压,压铸,模锻,低压铸造等26种常见金属成型工艺常用的金属材料成型工艺就是生产零部件的工艺方法,为冷、热成型,常见的工艺大面上分为以下几类:铸造、锻造、焊接和切削加工!今天我们从这些工艺的小类别用动图和解释总结概括一下。
是一种金属铸造工艺,其特点是利用模具腔对融化的金属施加高压。
模具通常是用强度更高的合金加工而成的,这个过程有些类似注塑成型。
就是用砂子制造铸模。
砂模铸造需要在砂子中放入成品零件模型或木制模型(模样),然后在模样周围填满砂子,开箱取出模样以后砂子形成铸模。
为了在浇铸金属之前取出模型,铸模应做成两个或更多个部分;在铸模制作过程中,必须留出向铸模内浇铸金属的孔和排气孔,合成浇注系统。
铸模浇注金属液体以后保持适当时间,一直到金属凝固。
取出零件后,铸模被毁,因此必须为每个铸造件制作新铸模。
又称失蜡铸造,包括压蜡、修蜡、组树、沾浆、熔蜡、浇铸金属液及后处理等工序。
失蜡铸造是用蜡制作所要铸成零件的蜡模,然后蜡模上涂以泥浆,这就是泥模。
泥模晾干后,在焙烧成陶模。
一经焙烧,蜡模全部熔化流失,只剩陶模。
一般制泥模时就留下了浇注口,再从浇注口灌入金属熔液,冷却后,所需的零件就制成了。
是在专用模锻设备上利用模具使毛坯成型而获得锻件的锻造方法。
根据设备不同,模锻分为锤上模锻,曲柄压力机模锻,平锻机模锻,摩擦压力机模锻等。
辊锻是材料在一对反向旋转模具的作用下产生塑性变形得到所需锻件或锻坯的塑性成形工艺。
它是成形轧制(纵轧)的一种特殊形式。
是一种利用锻压机械对金属坯料施加压力,使其产生塑性变形以获得具有一定机械性能、一定形状和尺寸锻件的加工方法,锻压(锻造与冲压)的两大组成部分之一。
通过锻造能消除金属在冶炼过程中产生的铸态疏松等缺陷,优化微观组织结构,同时由于保存了完整的金属流线,锻件的机械性能一般优于同样材料的铸件。
相关机械中负载高、工作条件严峻的重要零件,除形状较简单的可用轧制的板材、型材或焊接件外,多采用锻件。
金属压铸工艺与模具设计-浇注系统及排溢系统设计
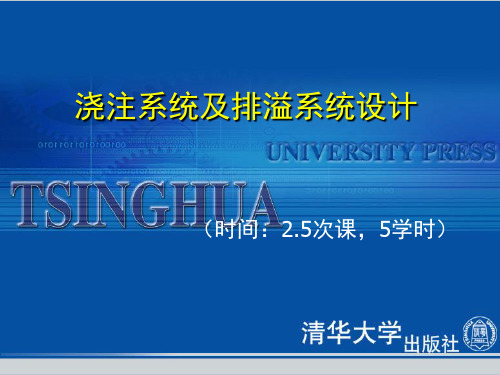
8.1.3 内浇口设计
图8.11 常见压铸件浇注系统形式 (a) 侧浇口;(b) 切线浇口;(c) 缝隙浇口;(d) 环形浇口(1—全环形;2—半环形);
(e)中心浇口;(f)顶浇口;(g)点浇口;(h)多支浇口
8.1.3 内浇口设计
中心浇口一般适用于单型腔模,多用于立式冷压式压铸机或热压室压铸机。如果要用于卧式冷压室压铸 机,设计时应注意直浇道小端进料口应设置在压室的上方,防止压室中浇入金属液后,压射冲头尚未工 作金属液就流入型腔,造成压铸件冷隔或充填不足。同时,定模部分要定距分型,以便取出余料。
浇注系统及排溢系统设计
(时间:2.5次课,5学时)
第8章 浇注系统及排溢系统设计
浇注系统是熔融金属在压力作用下充填模具型腔的通道。排溢系统 包括溢流槽和排气槽。溢流槽的作用是储存混有气体和涂料残渣的 冷污金属液,它与排气槽配合,迅速引出型腔内的气体。在金属液 充填的整个过程中,浇注系统与排溢系统是一个不可分割的整体, 共同对充填过程起着控制作用,是决定压铸件质量的重要因素。因 此,浇注系统和排溢系统的设计是压铸模设计的一个十分重要的环 节。
(6) 点浇口:点浇口适用于压铸件外形基本对称、壁厚均匀、高度不大、顶部无孔的壳类压铸件, 尤其是圆柱形压铸件。它克服了顶浇口与压铸件连接部位面积大,浇口处易缩松的缺点,使压铸件表面 光洁、内部结晶致密。内浇口直径一般为3~4 mm,便于在顺序分型开模时自动被拉断。为了取出浇 注系统凝料,在定模部分必须设计顺序分型机构,模具构造复杂。因此,生产中这类浇口的应用受到一 定的限制。
2. 卧式冷压室压铸机直浇道 卧式冷压室压铸机直浇道由压室和浇口套组成。压室和浇口套可以制成整体,也可以分别制造,如图
8.5、图8.6所示。若是两者分开,则压室是压铸机的附件(通用件),浇口套设在定模板上,随压铸零 件不同而不同。压室内径D与压射冲头直径d的配合是H7/e8;浇口套内径与压射冲头直径d的配合应 制成F8/e8。压室与浇口套在装配时要求同轴度高,否则,压射冲头就不能顺利工作。 在设计直浇道时,要选用合适的压室。压室的选用应该考虑压射比压和压室的充满度。首先考虑的是压 射比压,压室直径与压射比压的平方根成反比。对于铝合金而言,压射比压范围在25~100 MPa内, 压射比压大的可选较小直径的压室;压射比压小的可选较大直径的压室。直浇道的厚度H一般取直径D 的1/3~1/2。浇口套靠近分型面一端的内孔,长度在15~25 mm范围内时要加工出1°30′~2°的 脱模斜度,与直浇道相连接的横浇道一般设在浇口套的上方,防止金属液在压射前流入型腔。 当卧式冷压室压铸机采用中心浇口时,直浇道的设计与立式冷压室压铸机相同。可在浇口套内制成2~ 3条螺旋角小于20°的螺旋槽,在压射冲头的作用下,余料随着开模动作沿着浇口套中的螺旋槽旋转, 而从直浇道上扭断,如图8.7所示。
2019《金属压铸工艺与模具设计》浇注系统及排溢系统设计
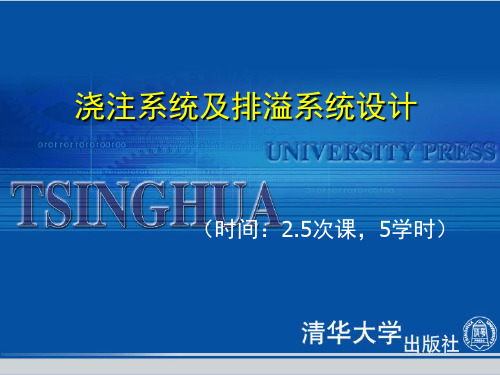
8.1.1 直浇道设计
8.1.1 直浇道设计
8.1.2 横浇道设计
横浇道是连接直浇道和内浇口的通道,横浇道的作用就是把金属液从直浇道引入内浇口内。横浇道的结 构形式和尺寸取决于内浇口的结构、位置、方向和流入口的宽度,而这些因素是根据压铸件的形状、结 构、大小、浇注位置和型腔个数来确定的。
(5) 缝隙浇口:这种浇口金属液流入型腔的形式与侧浇口类似。不同之处在于这种内浇口的深度方 向尺寸大大超过宽度方向尺寸,内浇口沿型腔深度引入金属液,形成长条缝隙顺序充填。这种形式的浇 口排气条件较好,且有利于压力的传递。适用于型腔比较深的模具。为便于加工,常在型腔部分垂直分 型。如有可能,在内浇口对面开设缝隙式溢流槽,则充填效果更佳,但这类浇口去除也困难。
2. 卧式冷压室压铸机直浇道 卧式冷压室压铸机直浇道由压室和浇口套组成。压室和浇口套可以制成整体,也可以分别制造,如图
8.5、图8.6所示。若是两者分开,则压室是压铸机的附件(通用件),浇口套设在定模板上,随压铸零 件不同而不同。压室内径D与压射冲头直径d的配合是H7/e8;浇口套内径与压射冲头直径d的配合应 制成F8/e8。压室与浇口套在装配时要求同轴度高,否则,压射冲头就不能顺利工作。 在设计直浇道时,要选用合适的压室。压室的选用应该考虑压射比压和压室的充满度。首先考虑的是压 射比压,压室直径与压射比压的平方根成反比。对于铝合金而言,压射比压范围在25~100 MPa内, 压射比压大的可选较小直径的压室;压射比压小的可选较大直径的压室。直浇道的厚度H一般取直径D 的1/3~1/2。浇口套靠近分型面一端的内孔,长度在15~25 mm范围内时要加工出1°30′~2°的 脱模斜度,与直浇道相连接的横浇道一般设在浇口套的上方,防止金属液在压射前流入型腔。 当卧式冷压室压铸机采用中心浇口时,直浇道的设计与立式冷压室压铸机相同。可在浇口套内制成2~ 3条螺旋角小于20°的螺旋槽,在压射冲头的作用下,余料随着开模动作沿着浇口套中的螺旋槽旋转, 而从直浇道上扭断,如图8.7所示。
浇口套、压室和压射冲头的配合尺寸
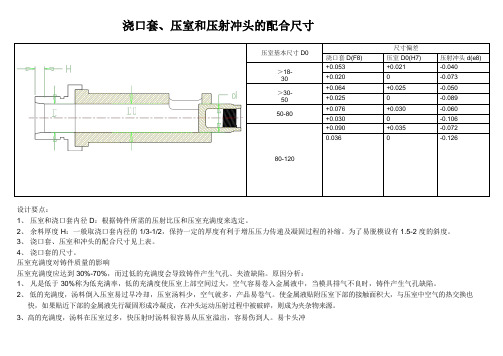
浇口套、压室和压射冲头的配合尺寸
设计要点:
1、压室和浇口套内径 D:根据铸件所需的压射比压和压室充满度来选定。
2、余料厚度 H:一般取浇口套内径的 1/3-1/2,保持一定的厚度有利于增压压力传递及凝固过程的补缩。
为了易脱模设有 1.5-2 度的斜度。
3、浇口套、压室和冲头的配合尺寸见上表。
4、浇口套的尺寸。
压室充满度对铸件质量的影响
压室充满度应达到 30%-70%,而过低的充满度会导致铸件产生气孔、夹渣缺陷。
原因分析:
1、凡是低于 30%称为低充满率,低的充满度使压室上部空间过大,空气容易卷入金属液中,当模具排气不良时,铸件产生气孔缺陷。
2、低的充满度,汤料倒入压室易过早冷却,压室汤料少,空气就多,产品易卷气。
使金属液贴附压室下部的接触面积大,与压室中空气的热交换也
快,如果贴近下部的金属液先行凝固形成冷凝皮,在冲头运动压射过程中被破碎,则成为夹杂物来源。
3、高的充满度,汤料在压室过多,快压射时汤料很容易从压室溢出,容易伤到人。
易卡头冲
提高充满度的方法:1、减少压室直径。
2、缩短压室长度提高充满率。
3、压室中设计分流锥的形式(加长分流锥的长度),减少压室空间,这种形式特别适合有深腔的定模。
4、充满度计算:K=4V/3.14LD2。
式中:K 为压室起始充满度:V 为金属液的体积(M3),L 为压室长度(M),D 为冲头直径(M)。
压铸模设计要点及压铸工艺

压铸模设计要点及压铸工艺压铸模设计要点及压铸工艺金属液在通过浇口时,其填充方式可分为层流式填充、喷射流填充、雾化流填充三种方式。
当浇口速度较低时,填充方式显层流的状态;当速度增加,金属液不再是连续流出,而是呈粗颗粒状喷出;当速度更高时,水则会呈雾状的细微颗粒喷出。
采用层流填充或雾状流填充均可产生令人满意的铸件,粗颗粒流填充因在填充过程中热量损失多而填充不好。
一般而言,浇口愈薄,浇口速度愈高才能达到雾化流的状态金属液进入型腔的流动状态是由流道和内浇口的形式决定的。
目前使用较多的流道形式有扇形流道和锥形流道两种。
浇注系统由直浇道,横浇道和内浇道等三部份组成。
扇形流道较适合于内浇口长度较短的产品,锥形流道适合于内浇口长度较长的产品。
不管是扇形流道还是锥形流道,从流道开始到内浇口其截面积应该逐渐缩小,才能保证控制合金液的流态,并防止气体卷入浇注系统;横浇道应具有一定的长度,可对金属液起到稳流和导向作用压铸模设计要点:一、模架1.外表面要求光亮平整,前后模框加2个打出孔,注意要加在没有镶件的位置,防止零件掉出来。
2.为了防止模板变形,起码做2个支撑柱,一个放在分流锥,一个放在分流锥的上面,注意不要与其他零件干涉。
3.模具底板要做通,便于散热。
4.定位圈内孔表面要求内圆磨后氮化,并沿出模方向抛光。
5.定位圈表面的冷却环底部到分流锥表面的长度一般等于料饼厚度。
固定此冷却环的方式有2种:烧焊和加热压入。
6.分流锥一定要做运水来冷却,且离分流锥表面25-30mm.7.模架四个导柱孔要做撬模槽,深度8-10mm。
8.模架一定要调质处理的,最好是锻打的模架。
二、内模,镶件1. 加工后热处理前做去应力处理。
一般铝合金淬火HRC45+/-1°C,锌合金淬火HRC46+/-1-1°C2.内模的配合公差:一般做到小于模框0.05-0.08mm左右,可以用吊环轻松取出放入模框。
顶针配合公差:大于等于8mm的顶针间隙0.05mm,小于等于6mm的顶针间隙0.025mm。
- 1、下载文档前请自行甄别文档内容的完整性,平台不提供额外的编辑、内容补充、找答案等附加服务。
- 2、"仅部分预览"的文档,不可在线预览部分如存在完整性等问题,可反馈申请退款(可完整预览的文档不适用该条件!)。
- 3、如文档侵犯您的权益,请联系客服反馈,我们会尽快为您处理(人工客服工作时间:9:00-18:30)。
浇口套制作工艺(试行)
我司的浇口套(带冷却水),以前的制作工艺为内外套间隙配合,烧焊密封后整体磨内外圆。
此方法制作的缺点是,浇口套焊接的地方容易开裂、漏水。
浇口套的使用寿命普遍不高,达不到模具正常的使用寿命。
通过查询资料、咨询专业浇口套制作商,现将浇口套的制作工艺调整如下:
1.浇口套内套材料选用H13(SKD61)淬火前粗车,直径留0.4~0.5mm余量(双边)。
长
度方向留0.5~0.6mm余量(双边)。
冷却水槽直接到数,在根部加工R2~R3。
2.浇口套内套外协淬火HRC46~48。
3.浇口套内套外协磨内外圆到图纸尺寸,注意图纸要求的粗糙度。
4.浇口套外套采用45#钢,直接精车到图纸尺寸,外套内孔同内套的外圆留有0.2~
0.5mm(双边)过盈量。
加工时注意达到内孔的粗糙度要求。
5.将浇口套外套加热到650~780摄氏度(附钢材比色表),将外套垂直套入内套的对
应位置,待其冷却后自动抱紧密封。
外套放入时,一定注意冷却水口方向。
6.浇口套同套板研配、装配。
为了方便内外套加热后的装配,减少不必要的失误,浇口套设计、加工时满足以下要求:
1.内外套的配合部分,内套上加工出台阶(附图),台阶高度A大于浇口套内、外套
的单边过盈量。
这样在外套套入内套时,可以起一定的导向作用。
A=0.25MM
钢材比色表
青岛科马精密机械制造有限公司技术部
2009-8-10。