凸轮轴加工工艺
凸轮轴机械加工工艺

以CA 6102 发动机为例, 凸轮的升程偏差 为: A、 D 段为±0 . 015mm; B段为±0 . 05mm; C 段为±0 . 025mm。
二、凸轮轴的材料与毛坯
材料: 铸铁:冷硬铸铁、可淬硬的低合金铸铁、 球墨铸铁等。 钢: 中碳钢、渗碳钢。 毛坯制造方法: 精铸和精锻。 直接用棒料加工。
装配式凸轮轴加工线
装配式凸轮轴是将凸轮(精锻) 和轴颈 (机加工件)装配到一根心轴上, 焊接固定其 轴向和角向位置, 如图所示。
装配式凸轮轴可以对单个的凸轮表面 进行渗碳淬火,既可以提高其抗点蚀的能力 和耐磨性, 又可避免使整个凸轮轴产生变形, 明显地提高了产品质量; 同时装配式凸轮轴 还可以减轻凸轮轴的重量并降低生产成本。 因此, 越来越多的汽车制造厂采用了装配式 凸轮轴工艺。
多刀仿形单靠模车削
a) 车刀
b)工具的安装
2.凸轮形面的精加工
凸轮轴切点跟踪磨削加工
凸轮形面磨削的新技术
1)采用立方氮化硼砂轮 2)数控凸轮轴磨床 3)采用多片砂轮高强度砂轮进行高速磨削 4)采用主动测量 、自动补偿、自动修整等装置
(二)凸轮支撑轴颈的磨削
支撑轴颈的磨削可采用多砂轮磨床或无 心磨床, 如Junker 公司的Quick point 设备 可以高效率地磨削凸轮轴支撑轴颈。还有 的公司对凸轮轴的轴颈和桃形在精磨后进 行抛光, 与曲轴的超精加工类似。
工序10:磨正时齿轮轴颈和螺纹轴颈外圆等 外圆端面磨床
工序11:磨齿轮外圆
外圆磨床
工序12:磨四个支承轴颈外圆
外圆磨床
工序13:滚齿
滚齿机
工序14:去齿轮两端毛刺
去毛刺机
工序15:铣键槽
键槽铣床
工序17:车1、4、6、7、9、12凸轮及偏心轮
凸轮轴工艺基础知识-甘驰名-新

凸轮轴工艺基础知识凸轮轴的种类在现代发动机中,凸轮轴的位置已经从下置式改成了上置式。
以往一般采用的下置凸轮轴,即凸轮轴在气缸侧面,由正时齿轮直接驱动。
为了把凸轮轴的转动变换为气门的往复运动,必须使用气门挺杆来传递动力。
这样,往复运动的零件较多,惯性质量大,不利于发动机高速运动。
而且,细长的挺杆具有一定的弹性,容易引起振动,加速零件磨损,甚至使气门失去控制。
上置凸轮轴分为上置单凸轮轴和上置双凸轮轴。
上置单凸轮轴在气缸盖上用一根凸根轴,直接驱动进、排气门,它具有结构简单,适用于高速发动机,但对凸轮轴的加工质量要求较高。
上置双凸轮轴是在缸盖上装有两根凸轮轴,一根用于驱动进气门,另一根用于驱动排气门。
采用顶置双凸轮轴对凸轮轴和气门弹簧的设计和加工要求不高,特别适用于气门V形配置的半球形燃烧室,也便于和四气门配气机构配合使用,在高速强化发动机上应用较多,如ZD30发动机的凸轮轴,每个发动机上有进气凸轮轴和排气凸轮轴各一根,都不需要抛光,而康明斯几种凸轮轴抛光后,凸轮表面粗糙度要求R a0.2,主轴颈表面粗糙度要求R a0.4。
康明斯作业部4B凸轮轴加工工艺:零件号: 3929885 材料:冷激铸铁硬度:HB230-320加工工艺流程:0J毛坯检查10铣端面钻中心孔20 钻油孔去毛刺30打标记35粗磨第三主轴径40粗精车全部轴径,台肩,清根槽并倒角45手动校直47精磨第三主轴径50精磨其余主轴径60精磨小轴径,台肩及第一主轴径前端面70铣键槽100粗精磨全部凸轮105去毛刺110磁粉探伤130抛光140清洗150J最终检查160防锈包装康明斯作业部6B(欧Ⅱ)凸轮轴加工工艺:零件号:3283179 材料:冷激铸铁硬度:HB230-320加工工艺流程:0J毛坯检查 10铣端面钻中心孔 20 钻油孔,去毛刺 30打标记 35粗磨第四主轴径 40粗精车全部轴径,台肩,清根槽并倒角45手动校直 47精磨第四主轴径 50精磨其余主轴径 60精磨小轴径,台肩及第一主轴径前端面70铣键槽 100粗精磨全部凸轮 105去毛刺 110磁粉探伤 130抛光 140清洗150J最终检查 160防锈包装康明斯作业部6C凸轮轴加工工艺:零件号:3923478 材料:冷激铸铁硬度:HB230-320加工工艺流程:0J毛坯检查 10铣端面钻中心孔 20 钻油孔,去毛刺 30打标记35粗磨第四主轴径 40粗精车全部轴径,台肩,清根槽并倒角 45手动校直 47精磨第四主轴径 50精磨其余主轴径 60精磨小轴径,台肩及第一主轴径前端面 70铣键槽 100粗精磨全部凸轮 105去毛刺 110磁粉探伤 130抛光 140清洗 150J最终检查160防锈包装10工序铣端面钻中心孔20工序钻油孔,去毛刺30工序打标记35工序粗磨中间主轴径40工序粗精车全部轴径,台肩,清根槽并倒角47 工序精磨中间主轴径50工序精磨其余主轴径60工序精磨小轴径,台肩及第一主轴径前端面70工序铣键槽100工序粗精磨全部凸轮105工序去毛刺110工序磁粉探伤130工序抛光140工序清洗加工工艺简介:A.凸轮轴强化加工工艺1.凸轮轴毛坯材料为冷激铸铁:a)工艺方法:铸造时,在凸轮轴模具内放冷铁,浇铸后凸轮急速冷却,促使其迅速的凝固,在表面形成莱氏体硬化层。
凸轮轴工艺流程

凸轮轴工艺流程
《凸轮轴工艺流程》
在汽车发动机中,凸轮轴是一个重要的零件,它控制着气门的开闭时间以及排气和进气的顺序。
因此,凸轮轴的制造工艺流程对于发动机的性能和效率都有很大的影响。
凸轮轴的制造工艺流程主要包括以下几个步骤:
1. 材料选择:凸轮轴通常采用优质的合金钢材料制造,以保证其强度和耐磨性。
材料选择是凸轮轴制造的第一步,关乎整个制造工艺的质量和效率。
2. 粗加工:在粗加工阶段,通过车床和铣床对原材料进行切削和成形,初步将凸轮轴的形状和尺寸加工出来。
3. 热处理:凸轮轴经过粗加工后需要进行热处理,以提高其硬度和耐磨性。
热处理通常包括淬火、回火等工艺,确保凸轮轴具有所需的材料性能。
4. 精加工:在精加工阶段,需要进行车削、磨削等工艺,对凸轮轴进行更精细的加工,以确保其表面平整度和尺寸精度。
5. 表面处理:凸轮轴的表面通常需要进行镀铬或其他表面处理,以提高其抗腐蚀性和表面光洁度。
6. 组装:最后,经过上述工艺流程加工完成的凸轮轴将进行组
装,与其他部件一起组装成为完整的汽车发动机。
通过上述工艺流程,凸轮轴可以获得优质的性能和精确的尺寸,从而保证发动机的高效运转和稳定性能。
凸轮轴的工艺流程需要严格的质量控制和精密的加工技术,以确保其质量和可靠性。
凸轮轴加工工艺
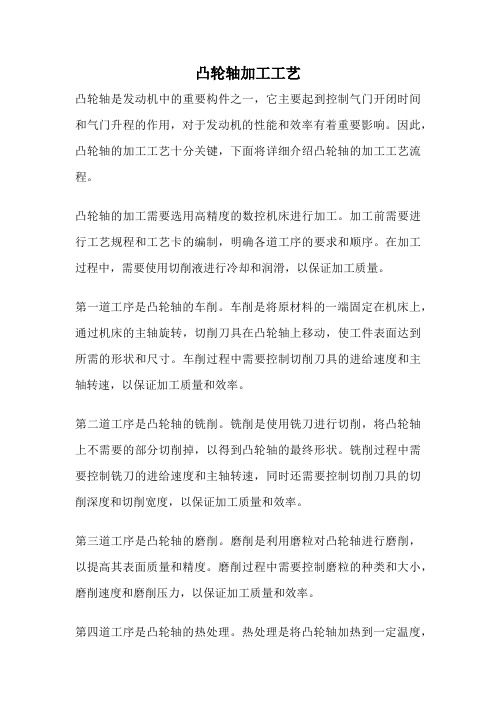
凸轮轴加工工艺凸轮轴是发动机中的重要构件之一,它主要起到控制气门开闭时间和气门升程的作用,对于发动机的性能和效率有着重要影响。
因此,凸轮轴的加工工艺十分关键,下面将详细介绍凸轮轴的加工工艺流程。
凸轮轴的加工需要选用高精度的数控机床进行加工。
加工前需要进行工艺规程和工艺卡的编制,明确各道工序的要求和顺序。
在加工过程中,需要使用切削液进行冷却和润滑,以保证加工质量。
第一道工序是凸轮轴的车削。
车削是将原材料的一端固定在机床上,通过机床的主轴旋转,切削刀具在凸轮轴上移动,使工件表面达到所需的形状和尺寸。
车削过程中需要控制切削刀具的进给速度和主轴转速,以保证加工质量和效率。
第二道工序是凸轮轴的铣削。
铣削是使用铣刀进行切削,将凸轮轴上不需要的部分切削掉,以得到凸轮轴的最终形状。
铣削过程中需要控制铣刀的进给速度和主轴转速,同时还需要控制切削刀具的切削深度和切削宽度,以保证加工质量和效率。
第三道工序是凸轮轴的磨削。
磨削是利用磨粒对凸轮轴进行磨削,以提高其表面质量和精度。
磨削过程中需要控制磨粒的种类和大小,磨削速度和磨削压力,以保证加工质量和效率。
第四道工序是凸轮轴的热处理。
热处理是将凸轮轴加热到一定温度,然后进行冷却,以改变其组织结构和性能。
热处理过程中需要控制加热温度和保温时间,冷却速度和冷却介质,以保证加工质量和效果。
第五道工序是凸轮轴的精密磨削。
精密磨削是对凸轮轴进行进一步的磨削,以提高其精度和表面质量。
精密磨削过程中需要使用高精度的磨削设备和磨粒,同时需要控制磨削参数和工艺,以保证加工质量和效率。
进行凸轮轴的检测和组装。
检测是对加工后的凸轮轴进行尺寸和形状的检测,以确保其符合设计要求。
组装是将凸轮轴安装到发动机中,并进行调试和测试,以确保其正常工作。
凸轮轴的加工工艺包括车削、铣削、磨削、热处理、精密磨削、检测和组装等工序。
在加工过程中需要控制各种参数和工艺,以保证加工质量和效率。
只有通过精密的加工工艺,才能制造出高质量的凸轮轴,提高发动机的性能和效率。
凸轮轴
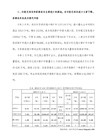
合金铸铁:将接近灰铸铁成份的铁水加入Mn、Cr、Mo、Cu等元素。从而与珠光体形成合金,减少铁素体的数量。合金铸铁的凸轮轴一般用于高转速凸轮轴。如CAC480凸轮轴,凸轮轴整体硬度HB263-311。
由于磨削速度很高,磨削热量来不及传入工件的深处,瞬时聚集在凸轮轴很薄的表层,形成切屑被带走。磨粒切削点的温度达1000?C以上,而内部只有几十度
选用CBN砂轮磨削,磨粒锋利,磨削力小,故磨削区发热量少
CBN显微硬度7300—9000HV,抗弯强度300MPa、抗压强度800--1000MPa、热稳定性1250?C--1350?C。
无进给磨削即光磨,可提高工件的几何精度和降低表面粗糙度参数值,表面粗糙度随光磨次数的增加而降低,细粒度砂轮比粗粒度好
砂轮的修整:修整通常包括整形和修锐,整形是使砂轮达到要求的几何形状和精度,砂轮的几何形状采用数控插补法进行,修锐是除去磨粒间的结合剂,使磨粒露出结合剂一定高度,形成切削刃,磨粒间空隙以容纳切屑。
金刚石滚轮磨削修整的特点:生产率高:以切入法进行修整,修整时间仅需2-10秒,可在进行凸轮轴更换工件时进行修整,不耽误生产节拍,同时由于金刚滚轮的寿命长,修整时间短,大大缩短了辅助时间,单件工件的消耗较低,金刚滚轮的精度较高,修整后的砂轮表面质量也较好。
矿物油冷却液的主要成份是轻质矿物油,加入适量的油溶性防锈添加剂。为了增加矿物油的润滑性能,常加入油性添加剂如脂肪酸等,以提高矿物油在低温低压时的渗透和润滑效果。矿物油的供给方法是喷射法,这样,可以提高供液压力,增大磨削液供给速度,以便将磨削热量迅速带走,并能冲破砂轮高速旋转的气流,使磨削液能有效的进入磨削区,改善磨削效果。由于砂轮的气孔小,磨削液必须经过精密过滤。由于磨削过程所产生的磨屑和砂粒等杂质在磨削液中不断增加,以至磨削液变脏变臭,不仅影响磨削工件的质量,还会危害环境卫生,快速点磨所用的过滤是柱状纸质过滤。
凸轮轴的加工工艺

凸轮轴的加工工艺
凸轮轴的加工工艺一般可以分为以下几个步骤:
1. 材料准备:选择合适的材料,例如高强度的合金钢,进行坯料的选取、检验和处理。
2. 粗加工:采用车床等机床对坯料进行粗加工,包括车削、钻孔、铣削、镗孔等工艺,将坯料轮廓和孔洞等初步加工成型。
3. 热处理:为了提高凸轮轴的硬度和耐磨性,需要对粗加工完成后的轴进行热处理。
具体的方法包括淬火、回火、淬火加回火等。
4. 精加工:将经过热处理的轴进行精加工,包括研磨、铣削、滚压等工艺,使其达到设计要求的尺寸精度和表面质量。
5. 检验:进行轴的各项性能测试和质量检验,包括硬度、尺寸、形状、表面粗糙度等指标的检测。
验收合格后可以进行组装使用。
总的来说,凸轮轴的加工工艺比较复杂,需要对材料、加工工艺、热处理等多个方面进行综合考虑,确保轴的质量和性能达到要求。
凸轮轮轴的加工工艺

材料选择凸轮轴材料的选择:由于轴的载荷通常是变载荷,或变应力,故材料应具有较好的强度和韧性;对轴的表面与支承有相对滑动的轴,还须要求较好的耐磨性。
材料常用材料与热处理:凸轮轴常用材料是20Cr, 20Cr的热处理及主要机构性能(参考)如表13.4.3热处理分析:轴类零件的热处理是保证轴类零件性能的重要工艺过程,它对轴类零件的如下性能有着直接的影响:[6]1)轴类零件的制造精度:组织转变不均匀、不彻底及热处理后形成的残余应力过大轴在热处理后的加工、装配和使用过程中的变形,从而降低轴的精度,甚至报废。
2)轴类零件的强度:热处理工艺制定不当、热处理操作不规范或热处理设备状态不完好,造成被处理轴的强度(硬度)达不到设计要求。
3)轴的工作寿命:热处理造成的组织结构不合理、晶粒度超标等,导致主要性能如轴的韧性、抗磨损性能等下降,影响轴的工作寿命。
4)轴的制造成本:作为轴制造过程的中间环节或最终工序,热处理造成的开裂、变形超差及性能超差,大多数情况下会使轴报废,即使通过修补可以使用,也会增加工时,从而增加了轴的成本。
凸轮轴材料是20Cr,对强度和韧性要求比较高,而表面易磨损需渗碳。
渗碳的目的就是增加轴的耐磨性能、表面硬度、抗拉强度及疲劳极限。
渗碳以后首先要进行淬火,用来提高其硬度和强度极限。
但淬火时会引起内应力使之变脆,所以淬火以后必须要回火,回火的目的就是用来消除淬火后的脆性和内应力,提高其塑性和冲击韧度。
但是对于凸轮轴来说,半成品热处理以前还有一道重要的工序,就是要对第一和第二个凸轮之间的外圆;第五和第六个凸轮之间的外圆用两顶的装加方式进行粗磨。
这样做是因为轴类零件热处理以后会产生变形,既保证其同轴度。
以便在热处理以后以这两个外圆为基准进行校核。
3.5夹具的设计磨床夹具按其通用化的程度和结构特点,可以分为通用夹具、专用夹具、组合夹具和成组可调夹具等等。
凸轮轴加工时采用的是传动夹头,属于组合夹具类型。
组合夹具是在夹具零部件标准化的基础上发展起来的一种新型工艺装备。
车铣技术凸轮轴加工工艺分析

车铣技术凸轮轴加工工艺分析一、引言凸轮轴是发动机的重要部件,它通过与气门相连,控制气门的开启和关闭,是发动机正常运转的关键之一。
凸轮轴的加工工艺直接影响着发动机的性能和质量,因此对凸轮轴的加工工艺进行分析和优化具有重要意义。
本文将对车铣技术在凸轮轴加工中的应用及工艺进行分析。
二、凸轮轴的加工工艺分析1.传统加工工艺传统凸轮轴加工主要采用车削加工、磨削加工和镗削等工艺。
车削加工是指通过车床进行粗加工和精加工,将工件上的多余材料逐渐切除,成型成凸轮轴的外形。
磨削加工则是通过磨床将凸轮轴的表面进行精加工,使其光洁度和精度达到要求。
镗削加工则是利用镗床对凸轮轴的孔件进行加工,确保其尺寸和形位精度。
这种传统的凸轮轴加工工艺存在以下问题:一是加工效率低、成本高,车削、磨削和镗削等多道工序需要耗费大量时间和人力。
二是精度难以保证,特别是对于凸轮轴的各种曲线和凸起等复杂形状难以达到高精度。
三是加工成本高,采用传统工艺生产的凸轮轴成本高昂,不利于降低产品成本和提高市场竞争力。
2.车铣技术的应用车铣技术是一种将车削和铣削工艺相结合的加工方式,它能有效解决传统凸轮轴加工工艺存在的问题。
通过车铣技术,可以在同一设备上进行粗加工、精加工、曲线加工、凸起加工等多种加工操作,大大提高加工效率和精度,降低成本。
车铣技术在凸轮轴加工中的应用主要有以下优势:(1)提高加工效率:车铣技术能够实现一次性成型,不用多次装夹和换刀,大大简化了加工工序,提高了加工效率。
(2)提高加工精度:车铣技术能够在同一设备上进行多种加工操作,能够保证凸轮轴的各种形状和尺寸要求,提高了加工精度。
(3)降低成本:车铣技术的高效率和高精度能够降低加工成本,同时减少了人力和设备的投入,降低了生产成本。
(4)提高产品质量:车铣技术能够提高凸轮轴的加工精度和表面光洁度,提高了产品质量和使用寿命。
采用车铣技术对凸轮轴进行加工,其工艺流程可以分为以下几个步骤:1.凸轮轴的选材:首先要选择适合凸轮轴加工的高强度材料,如40Cr、42CrMo等,以保证凸轮轴的使用寿命和性能。
凸轮轴加工工艺
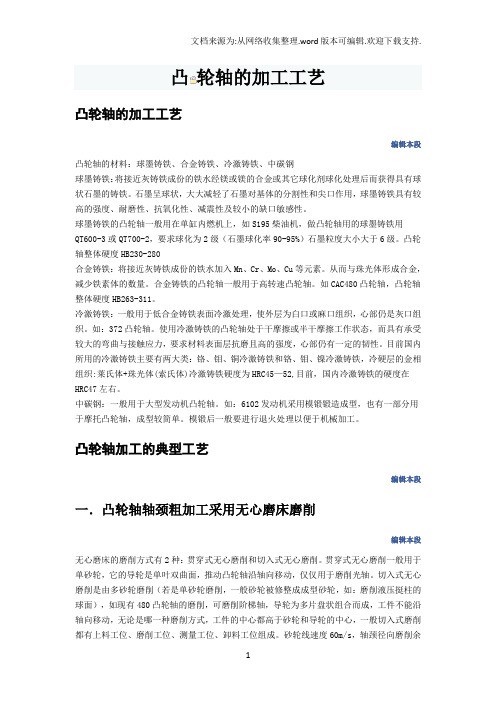
凸轮轴的加工工艺凸轮轴的加工工艺编辑本段凸轮轴的材料:球墨铸铁、合金铸铁、冷激铸铁、中碳钢球墨铸铁:将接近灰铸铁成份的铁水经镁或镁的合金或其它球化剂球化处理后而获得具有球状石墨的铸铁。
石墨呈球状,大大减轻了石墨对基体的分割性和尖口作用,球墨铸铁具有较高的强度、耐磨性、抗氧化性、减震性及较小的缺口敏感性。
球墨铸铁的凸轮轴一般用在单缸内燃机上,如S195柴油机,做凸轮轴用的球墨铸铁用QT600-3或QT700-2,要求球化为2级(石墨球化率90-95%)石墨粒度大小大于6级。
凸轮轴整体硬度HB230-280合金铸铁:将接近灰铸铁成份的铁水加入Mn、Cr、Mo、Cu等元素。
从而与珠光体形成合金,减少铁素体的数量。
合金铸铁的凸轮轴一般用于高转速凸轮轴。
如CAC480凸轮轴,凸轮轴整体硬度HB263-311。
冷激铸铁:一般用于低合金铸铁表面冷激处理,使外层为白口或麻口组织,心部仍是灰口组织。
如:372凸轮轴。
使用冷激铸铁的凸轮轴处于干摩擦或半干摩擦工作状态,而具有承受较大的弯曲与接触应力,要求材料表面层抗磨且高的强度,心部仍有一定的韧性。
目前国内所用的冷激铸铁主要有两大类:铬、钼、铜冷激铸铁和铬、钼、镍冷激铸铁,冷硬层的金相组织:莱氏体+珠光体(索氏体)冷激铸铁硬度为HRC45—52,目前,国内冷激铸铁的硬度在HRC47左右。
中碳钢:一般用于大型发动机凸轮轴。
如:6102发动机采用模锻锻造成型,也有一部分用于摩托凸轮轴,成型较简单。
模锻后一般要进行退火处理以便于机械加工。
凸轮轴加工的典型工艺编辑本段一.凸轮轴轴颈粗加工采用无心磨床磨削编辑本段无心磨床的磨削方式有2种:贯穿式无心磨削和切入式无心磨削。
贯穿式无心磨削一般用于单砂轮,它的导轮是单叶双曲面,推动凸轮轴沿轴向移动,仅仅用于磨削光轴。
切入式无心磨削是由多砂轮磨削(若是单砂轮磨削,一般砂轮被修整成成型砂轮,如:磨削液压挺柱的球面),如现有480凸轮轴的磨削,可磨削阶梯轴,导轮为多片盘状组合而成,工件不能沿轴向移动,无论是哪一种磨削方式,工件的中心都高于砂轮和导轮的中心,一般切入式磨削都有上料工位、磨削工位、测量工位、卸料工位组成。
凸轮轴的加工工艺诠释说明

五、主轴颈快速点磨加工与CBN砂轮
快速点磨是德国勇克公司开发出来的一种先进的外圆高效磨削新工艺,该机床加工凸轮轴只需两顶尖定位夹紧,无需任何夹紧工具,利用前顶尖的高速旋转,通过顶尖和凸轮轴中心孔的摩擦来驱动工件运动,可以实现轴类零件在一次装夹后,用一片砂轮完成7个轴颈、一个端面和一个磨削圆角的工艺。
应用声音传感器严格限制砂轮和金刚滚轮间的距离,主要是防止砂轮修整时砂轮和金刚滚轮发生撞击。砂轮架纵向进给时,传感器测头与砂轮间形成一小的缝隙,砂轮高速旋转压缩砂轮周围的空气,根据空气流通的通道大小不同,所产生的气阻声音大小不一样,从而判断传感器和砂轮间的缝隙而做出反馈,一旦砂轮和金刚滚轮产生接触,修整器自动修整砂轮,而声音传感器能根据声音尖锐响声大小来判断砂轮修整的正确性。
三、凸轮轴的热处理
热处理:将原材料或未成品置于空气或特定介质中,用适当方式进行加热、保温和冷却,使之获得人们所需要的力学或工艺性能的工艺方法。
热处理分类:一般热处理、化学热处理、表面热处理
球墨铸铁凸轮轴一般都是等温淬火。冷却介质为10号、20号锭子油盐浴或碱浴,淬火后经140°C-250°C低温回火,回火后的组织为黑色针叶状马氏体,硬度HRC50-54。
凸轮轴的材料:球墨铸铁、合金铸铁、冷激铸铁、中碳钢
球墨铸铁:将接近灰铸铁成份的铁水经镁或镁的合金或其它球化剂球化处理后而获得具有球状石墨的铸铁。石墨呈球状,大大减轻了石墨对基体的分割性和尖口作用,球墨铸铁具有较高的强度、耐磨性、抗氧化性、减震性及较小的缺口敏感性。
球墨铸铁的凸轮轴一般用在单缸内燃机上,如S195柴油机,做凸轮轴用的球墨铸铁用QT600-3或QT700-2,要求球化为2级(石墨球化率90-95%)石墨粒度大小大于6级。凸轮轴整体硬度
凸轮轴加工工艺
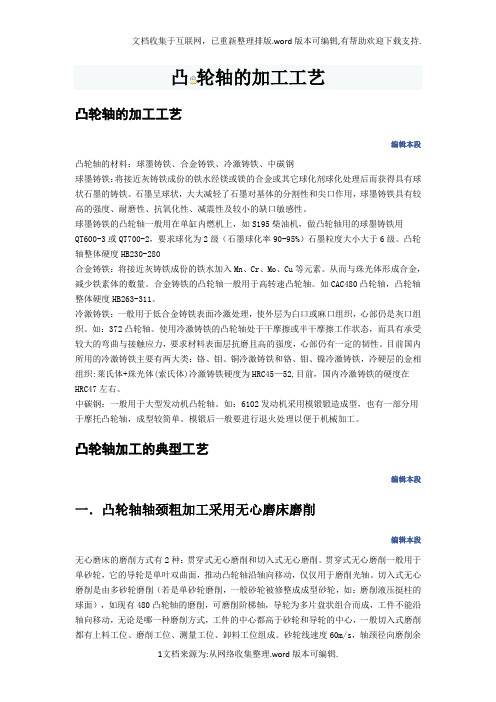
凸轮轴的加工工艺凸轮轴的加工工艺编辑本段凸轮轴的材料:球墨铸铁、合金铸铁、冷激铸铁、中碳钢球墨铸铁:将接近灰铸铁成份的铁水经镁或镁的合金或其它球化剂球化处理后而获得具有球状石墨的铸铁。
石墨呈球状,大大减轻了石墨对基体的分割性和尖口作用,球墨铸铁具有较高的强度、耐磨性、抗氧化性、减震性及较小的缺口敏感性。
球墨铸铁的凸轮轴一般用在单缸内燃机上,如S195柴油机,做凸轮轴用的球墨铸铁用QT600-3或QT700-2,要求球化为2级(石墨球化率90-95%)石墨粒度大小大于6级。
凸轮轴整体硬度HB230-280合金铸铁:将接近灰铸铁成份的铁水加入Mn、Cr、Mo、Cu等元素。
从而与珠光体形成合金,减少铁素体的数量。
合金铸铁的凸轮轴一般用于高转速凸轮轴。
如CAC480凸轮轴,凸轮轴整体硬度HB263-311。
冷激铸铁:一般用于低合金铸铁表面冷激处理,使外层为白口或麻口组织,心部仍是灰口组织。
如:372凸轮轴。
使用冷激铸铁的凸轮轴处于干摩擦或半干摩擦工作状态,而具有承受较大的弯曲与接触应力,要求材料表面层抗磨且高的强度,心部仍有一定的韧性。
目前国内所用的冷激铸铁主要有两大类:铬、钼、铜冷激铸铁和铬、钼、镍冷激铸铁,冷硬层的金相组织:莱氏体+珠光体(索氏体)冷激铸铁硬度为HRC45—52,目前,国内冷激铸铁的硬度在HRC47左右。
中碳钢:一般用于大型发动机凸轮轴。
如:6102发动机采用模锻锻造成型,也有一部分用于摩托凸轮轴,成型较简单。
模锻后一般要进行退火处理以便于机械加工。
凸轮轴加工的典型工艺编辑本段一.凸轮轴轴颈粗加工采用无心磨床磨削编辑本段无心磨床的磨削方式有2种:贯穿式无心磨削和切入式无心磨削。
贯穿式无心磨削一般用于单砂轮,它的导轮是单叶双曲面,推动凸轮轴沿轴向移动,仅仅用于磨削光轴。
切入式无心磨削是由多砂轮磨削(若是单砂轮磨削,一般砂轮被修整成成型砂轮,如:磨削液压挺柱的球面),如现有480凸轮轴的磨削,可磨削阶梯轴,导轮为多片盘状组合而成,工件不能沿轴向移动,无论是哪一种磨削方式,工件的中心都高于砂轮和导轮的中心,一般切入式磨削都有上料工位、磨削工位、测量工位、卸料工位组成。
车铣技术凸轮轴加工工艺分析

车铣技术凸轮轴加工工艺分析随着汽车制造技术的不断发展,车铣技术在车辆发动机零部件加工中发挥着重要作用。
凸轮轴作为发动机的关键部件之一,其加工工艺更是需要经过精密的设计和严格的控制。
本文将对车铣技术凸轮轴加工工艺进行深入分析,探讨其制造工艺、加工工艺及其在汽车制造中的应用。
一、凸轮轴概述凸轮轴是内燃机中的一种重要的传动轴,是用于开闭气门以及协调气门的运动规律的控制元件。
其运动规律与发动机的工作性能、经济性和排放性密切相关。
对凸轮轴的加工质量有着非常高的要求。
二、凸轮轴加工工艺1. 车铣技术在凸轮轴加工中的应用车铣技术是指采用车削和铣削两种切削工艺的综合机床来进行加工。
在凸轮轴的加工中,车铣技术最大的特点是能够实现多种不同工艺的一次性加工。
它不仅节约了生产时间,而且提高了加工精度和表面质量。
2. 加工质量控制凸轮轴的加工过程对其形状精度、表面质量、尺寸精度等方面有着严格要求。
在车铣技术中,加工质量的控制主要从以下几个方面入手:(1)设备精度要求:车铣联合机床的精度需要满足对凸轮轴加工的要求,尤其是在铣削加工中,设备的精度直接影响到工件的加工精度和表面质量。
(2)刀具选择:根据凸轮轴的不同部位和加工要求选择合适的刀具,刀具的材质、刀尖形状、刃口角度等都需要合理选择以保证加工质量。
(3)加工参数控制:包括切削速度、进给速度、切削深度、切削力的调整,以保证加工质量和刀具的寿命。
(4)冷却润滑:在车铣加工过程中,要保证切削过程中的冷却和润滑,以防止工件发热、变形和刀具磨损。
三、凸轮轴制造工艺1. 粗车凸轮轴粗车凸轮轴是凸轮轴加工的第一道工序,主要目的是将原材料实现初始的形状和尺寸精度。
在粗车过程中,需要选用合适的车刀和车刀切削参数,控制好车削的切削深度,以确保车削的加工效率和质量。
2. 精车凸轮轴精车凸轮轴是指对粗车完毕的凸轮轴进行精密加工,包括精度和表面质量的加工。
在精车过程中,需要进行多道工序的铣削加工,根据设计要求进行精密的切削工艺控制。
凸轮轴机械加工工艺

三、主要表面的加工
(一)凸轮形面的加工
1. 凸轮形面的粗加工 凸轮传统的粗加工方法是采用靠模车床及液 压仿形凸轮铣床, 铣削的凸轮尺寸精度和形状精度 都优于车削, 可直接进行精磨。大量生产的凸轮轴 毛坯均采用精锻或精铸成形, 其毛坯精度高, 加工 余量小, 国外不少厂家采用以磨代车的新工艺, 极 大地简化了凸轮形面的加工。对于棒料毛坯, 由于 余量大, 国外先进的方法是采用CNC 凸轮铣床。
工序2:校直
压床
工序3: 车1、2支承轴颈外圆等 凸轮轴轴颈车床
工序4: 车3、4支承轴颈外圆等 凸轮轴轴颈车床
工序5:钻φ7孔
钻床
工序6:校直 压床
工序7:磨第2、3轴颈外圆
外圆磨床
工序8:车凸轮侧面和连接轴颈等 凸轮轴车床
工序8:车凸轮侧面和连接轴颈等 凸轮轴车床
工序9:校直
压床
凸轮轴的主体是一根与汽缸组长度相同 的圆柱形棒体。上面套有若干个凸轮,用 于驱动气门。 凸轮的侧面呈鸡蛋形。其设计的目的在 于保证汽缸充分的进气和排气,具体来说 就是在尽可能短的时间内完成气门的开、 闭动作。
6102发动机凸轮轴
凸轮轴的主要技术要求:
1.轴颈的尺寸精度及各轴颈之间的同轴度; 2.键槽的尺寸和位置精度; 3.止推面相对于支承轴颈轴线的垂直度; 4.凸轮基圆的尺寸精度和相对于支承轴颈 轴线的同轴度; 5.凸轮的周向位置精度(相位角); 6.凸轮的形状精度(曲线升程)等。
工序29:精磨四个支承轴颈外圆
外圆磨床
工序30:精磨凸轮和偏心轮
凸轮磨床
工序31:修整螺纹和去毛刺 工序32:抛光 抛光机
工序33:校直
压床
工序34:清洗 工序35:终检
凸轮轴加工工艺特点及流程

凸轮轴加工工艺特点及流程凸轮轴是发动机配气系统中的关键零件,其加工质量的好坏直接影响着发动机的性能,所以明白其加工工艺特点及流程是很关键的。
以下是小编为你整理推荐凸轮轴加工工艺特点及流程,希望你喜欢。
凸轮轴加工的特点和流程1.工艺特点凸轮轴属于细长轴类零件,要准确控制发动机的进排气门定时开启和关闭,凸轮应具有很高的轮廓精度、相位角度和良好的耐磨性能及整体刚性。
因此,其轴颈和凸轮的加工成为整个凸轮轴加工工艺的重点,其加工多以车削、铣削和磨削工艺及表面强化(淬火、喷丸、氮化)等辅助工艺相结合。
2.工艺流程凸轮轴加工精度要求较高,整个加工内容不可能在一个工序内完成。
为了逐步达到图样要求,因此必须把加工分成几个阶段,以明确各个阶段的目的和任务。
传统的凸轮轴加工工艺一般分成以下几个阶段:粗加工(粗车轴颈、凸轮等)、半精加工(粗磨轴颈、凸轮等)、精加工(精磨轴颈、凸轮等)、光整加工(抛光轴颈、凸轮)。
现代加工工艺过程:一般只有粗加工(车轴颈、铣凸轮等)和精加工(精磨轴颈、凸轮)两个阶段,在保证零件加工质量的同时,大大提高了生产效率,降低了生产制造成本。
凸轮轴两端面及中心孔加工对于一般的轴类零件来说,其轴线即为设计基准。
加工过程中一般采用两顶尖孔作为轴类零件的定位基准。
这不仅避免了工件在多次装夹中因为定位基准的转换而引起的定位误差,也可以用作后续工序的定位基准,即符合“基准统一”的原则。
因此,合理安排两端面及中心孔加工工艺是保证后续工序加工质量的关键。
(1)传统工艺一般采用普通的铣钻组合机床进行铣端面、钻中心孔,靠调整限位挡块的位置保证工件的总长和中心孔的深度。
存在零件总长超差、中心孔深度超差、两端中心孔位置不同心及凸轮轴的主轴颈和凸轮两侧轴向余量不均匀,容易产生黑皮等质量问题。
为了避免把中心孔的形状误差复映到零件的加工精度上,传统的凸轮轴加工工艺在粗加工和热处理之后常安排中心孔的修整工序,保证在精加工过程中中心孔与顶尖的接触精度,提高凸轮轴的加工质量。
最新凸轮轴机械加工工艺-prt课件PPT
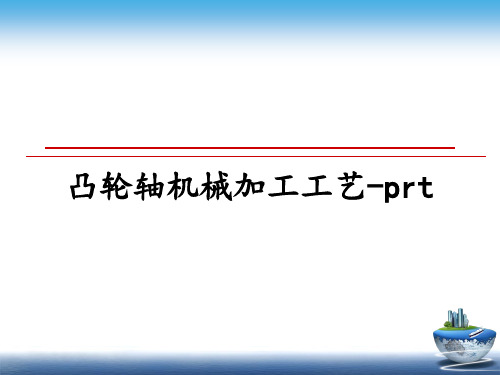
二、加工阶段的划分与工序顺序的 安排
(一)加工阶段的划分 粗加工阶段 半精加工阶段 精加工阶段 光整、精整加工阶段
二、加工阶段的划分与工序顺序的 安排
(二)工序顺序的安排 各支承轴颈、凸轮、偏心轮: 车——粗磨——精磨——抛光 从粗到精,主要表面与次要表面的加工工序交叉 进行。 淬火工序安排在各主要表面的半精加工之前 防止工件经淬火后变形过大造成精加工困难
不自主运动
概述
▪ 不自主运动或称异常运动,为随意肌的某一 部分、一块肌肉或某些肌群出现不自主收缩。 是指患者意识清楚而不能自行控制的骨骼肌 动作。临床上常见的有肌束颤动、肌纤维颤 搐、痉挛、抽搐、肌阵挛、震颤、舞蹈样动 作、手足徐动和扭转痉挛等。一般睡眠时停 止,情绪激动时增强,以往认为是锥体外系 病变所致。
临床表现
▪ 3. 震颤:是由于主动肌与拮抗肌交替收缩引起 的关节不自主的、快速节律性运动,这种运 动可有一定方向,但震幅大小不一,以手部 最常见,其次为眼睑、头和舌部。
▪ 4. 肌阵挛:为肌肉或肌群突发的,短促的闪电 样不自主收缩。可见于正常人,病理性肌阵 挛分为节律性和非节律性两种,以前者多见。
第二节 凸轮轴加工过程概述
发动机总类繁多,凸轮轴的结构形状各 异,但基本形状相差不大。
工序1:铣端面打中心孔 铣钻组合机
中心孔加工是以后加工工序的定位基准 ,在铣端面时,一般只限定5个自由度即可 ,用2个V型块限定4个自由度,轴向自由度 是由凸轮轴3#轴颈前端面或后端面(在产 品设计中,该面应提出具体要求)。目前 普遍采用的是自定心定位夹紧,密齿刀盘 铣削。轴向尺寸保证后端面到毛坯的粗定 位基准尺寸和整个凸轮轴长度
装配式凸轮轴加工线
装配式凸轮轴是将凸轮(精锻) 和轴颈 (机加工件)装配到一根心轴上, 焊接固定其 轴向和角向位置, 如图所示。
凸轮轴加工工艺

凸轮轴的加工工艺凸轮轴的加工工艺编辑本段凸轮轴的材料:球墨铸铁、合金铸铁、冷激铸铁、中碳钢球墨铸铁:将接近灰铸铁成份的铁水经镁或镁的合金或其它球化剂球化处理后而获得具有球状石墨的铸铁。
石墨呈球状,大大减轻了石墨对基体的分割性和尖口作用,球墨铸铁具有较高的强度、耐磨性、抗氧化性、减震性及较小的缺口敏感性。
球墨铸铁的凸轮轴一般用在单缸内燃机上,如S195柴油机,做凸轮轴用的球墨铸铁用QT600-3或QT700-2,要求球化为2级(石墨球化率90-95%)石墨粒度大小大于6级。
凸轮轴整体硬度HB230-280合金铸铁:将接近灰铸铁成份的铁水加入Mn、Cr、Mo、Cu等元素。
从而与珠光体形成合金,减少铁素体的数量。
合金铸铁的凸轮轴一般用于高转速凸轮轴。
如CAC480凸轮轴,凸轮轴整体硬度HB263-311。
冷激铸铁:一般用于低合金铸铁表面冷激处理,使外层为白口或麻口组织,心部仍是灰口组织。
如:372凸轮轴。
使用冷激铸铁的凸轮轴处于干摩擦或半干摩擦工作状态,而具有承受较大的弯曲与接触应力,要求材料表面层抗磨且高的强度,心部仍有一定的韧性。
目前国内所用的冷激铸铁主要有两大类:铬、钼、铜冷激铸铁和铬、钼、镍冷激铸铁,冷硬层的金相组织:莱氏体+珠光体(索氏体)冷激铸铁硬度为HRC45—52,目前,国内冷激铸铁的硬度在HRC47左右。
中碳钢:一般用于大型发动机凸轮轴。
如:6102发动机采用模锻锻造成型,也有一部分用于摩托凸轮轴,成型较简单。
模锻后一般要进行退火处理以便于机械加工。
凸轮轴加工的典型工艺编辑本段一.凸轮轴轴颈粗加工采用无心磨床磨削编辑本段无心磨床的磨削方式有2种:贯穿式无心磨削和切入式无心磨削。
贯穿式无心磨削一般用于单砂轮,它的导轮是单叶双曲面,推动凸轮轴沿轴向移动,仅仅用于磨削光轴。
切入式无心磨削是由多砂轮磨削(若是单砂轮磨削,一般砂轮被修整成成型砂轮,如:磨削液压挺柱的球面),如现有480凸轮轴的磨削,可磨削阶梯轴,导轮为多片盘状组合而成,工件不能沿轴向移动,无论是哪一种磨削方式,工件的中心都高于砂轮和导轮的中心,一般切入式磨削都有上料工位、磨削工位、测量工位、卸料工位组成。
- 1、下载文档前请自行甄别文档内容的完整性,平台不提供额外的编辑、内容补充、找答案等附加服务。
- 2、"仅部分预览"的文档,不可在线预览部分如存在完整性等问题,可反馈申请退款(可完整预览的文档不适用该条件!)。
- 3、如文档侵犯您的权益,请联系客服反馈,我们会尽快为您处理(人工客服工作时间:9:00-18:30)。
凸轮轴的加工工艺凸轮轴的材料:球墨铸铁、合金铸铁、冷激铸铁、中碳钢球墨铸铁:将接近灰铸铁成份的铁水经镁或镁的合金或其它球化剂球化处理后而获得具有球状石墨的铸铁。
石墨呈球状,大大减轻了石墨对基体的分割性和尖口作用,球墨铸铁具有较高的强度、耐磨性、抗氧化性、减震性及较小的缺口敏感性。
球墨铸铁的凸轮轴一般用在单缸内燃机上,如S195柴油机,做凸轮轴用的球墨铸铁用QT600-3或QT700-2,要求球化为2级(石墨球化率90-95%)石墨粒度大小大于6级。
凸轮轴整体硬度HB230-280合金铸铁:将接近灰铸铁成份的铁水加入Mn、Cr、Mo、Cu等元素。
从而与珠光体形成合金,减少铁素体的数量。
合金铸铁的凸轮轴一般用于高转速凸轮轴。
如CAC480凸轮轴,凸轮轴整体硬度HB263-311。
冷激铸铁:一般用于低合金铸铁表面冷激处理,使外层为白口或麻口组织,心部仍是灰口组织。
如:372凸轮轴。
使用冷激铸铁的凸轮轴处于干摩擦或半干摩擦工作状态,而具有承受较大的弯曲与接触应力,要求材料表面层抗磨且高的强度,心部仍有一定的韧性。
目前国内所用的冷激铸铁主要有两大类:铬、钼、铜冷激铸铁和铬、钼、镍冷激铸铁,冷硬层的金相组织:莱氏体+珠光体(索氏体)冷激铸铁硬度为HRC45—52,目前,国内冷激铸铁的硬度在HRC47左右。
中碳钢:一般用于大型发动机凸轮轴。
如:6102发动机采用模锻锻造成型,也有一部分用于摩托凸轮轴,成型较简单。
模锻后一般要进行退火处理以便于机械加工。
凸轮轴加工的典型工艺一.凸轮轴轴颈粗加工采用无心磨床磨削无心磨床的磨削方式有2种:贯穿式无心磨削和切入式无心磨削。
贯穿式无心磨削一般用于单砂轮,它的导轮是单叶双曲面,推动凸轮轴沿轴向移动,仅仅用于磨削光轴。
切入式无心磨削是由多砂轮磨削(若是单砂轮磨削,一般砂轮被修整成成型砂轮,如:磨削液压挺柱的球面),如现有480凸轮轴的磨削,可磨削阶梯轴,导轮为多片盘状组合而成,工件不能沿轴向移动,无论是哪一种磨削方式,工件的中心都高于砂轮和导轮的中心,一般切入式磨削都有上料工位、磨削工位、测量工位、卸料工位组成。
砂轮线速度60m/s,轴颈径向磨削余量可达3.5mm,单件磨削时间18s,单件工时25s。
用无心磨床加工凸轮轴是一种新颖、独特的新工艺,新方法,但又存在一定的局限性,特别是不易磨削轴肩和端面,一般不用于多品种凸轮轴的加工,只用于单一品种、大批量的生产,若要更换所加工的凸轮轴品种,就要更换导轮和砂轮,各砂轮间距需重新调整。
切入式无心磨床的修整一般采用单颗粒金刚石修整,修整器所走的路线是凸字形,修整器靠模各段差值与凸轮轴的各段轴颈差值相等。
粗磨凸轮轴轴颈所用的砂轮都属于碳化物系列,粒度为60,砂轮线速度为45m/。
二、铣端面,钻中心孔中心孔加工是以后加工工序的定位基准,在铣端面时,一般只限定5个自由度即可,用2个V型块限定4个自由度,轴向自由度是由凸轮轴3#轴颈前端面或后端面(在产品设计中,该面应提出具体要求)。
目前普遍采用的是自定心定位夹紧,密齿刀盘铣削。
轴向尺寸保证后端面到毛坯的粗定位基准尺寸和整个凸轮轴长度,鉴于凸轮轴皮带轮轴颈尺寸较小,钻中心孔时一般选用B5中心钻,钻后的孔深用φ10钢球辅助检查,保证球顶到后端面尺寸和2钢球顶部之间的距离,这样可保证以后定位的一致性。
三、凸轮轴的热处理热处理:将原材料或未成品置于空气或特定介质中,用适当方式进行加热、保温和冷却,使之获得人们所需要的力学或工艺性能的工艺方法。
热处理分类:一般热处理、化学热处理、表面热处理球墨铸铁凸轮轴一般都是等温淬火。
冷却介质为10号、20号锭子油盐浴或碱浴,淬火后经140°C-250°C低温回火,回火后的组织为黑色针叶状马氏体,硬度HRC50-54。
合金铸铁和钢件凸轮轴一般采用中频淬火:淬火频率1000-10000Hz,一般选用7000Hz。
也就是感应加热表面淬火,其原理是:将凸轮轴的凸轮放入加热线圈中,由于电流的集肤效应,使凸轮由外层向内加热、升温,使表层一定深度组织转变成奥氏体,而后迅速淬硬的工艺,目前480凸轮轴采用自然回火的方法,其凸轮表面组织为针状马氏体。
凸轮轴经表面热处理:可较大地提高零件的扭转和弯曲疲劳强度和表面的耐磨性。
感应加热淬火变形小、节能、成本低、劳动生产率高、淬火机可放在冷加工生产线上,便于生产管理。
480凸轮轴中频淬火机在感应加热时,要对电源、变压器、感应线圈进行冷却,要求冷却水的温度在25°C-30°C,淬火冷却液的温度为53°C-62°C,若机床本身达不到要求,必须在机床外提一套附加冷却装置,用来给冷却水制冷。
四、凸轮轴的深孔加工在机械加工中L/D>5时的孔加工可称为深孔加工,用普通麻花钻钻深孔时有以下困难。
1.钻头细长。
刚性差,加工时钻头易弯曲和振动,难以保证孔的直线度与加工精度。
2.切屑多,而排除切屑的通道长而狭窄,切屑不容易排出。
3.孔深切削液不易进入,切削温度过高,散热困难,钻头容易断。
深孔钻按工艺的不同可分为在实心物体上钻孔、扩孔、套料3种,而以在实心料上钻孔用得最多,如480凸轮所用的深孔都是由枪钻经2头加工而成的。
每次钻孔深为L/2+10mm。
枪钻钻削是单刃外排屑式的,一般适用于加工φ2-φ20mm孔, L/D>100、表面粗糙度Ra12.5-3.2mm、精度H8-H10级的深孔。
单刃外排屑深孔钻,最早用于加工枪管,故称枪钻,也是φ2-φ6mm深孔加工的唯一办法。
枪钻带有V形切削刃和一个切削液孔的钻头、钻杆、及适用于某专用设备的钻柄组成。
高压切削液(7MPa)通过钻头的小孔送到切削区域内,进行冷却、润滑并帮助排屑,然后再将切屑与切削液顺着V型刀杆排入集中冷却系统中。
钻头为硬质合金,采用焊接式结构。
切削用量一般为0.06-0.1mm/r,为了更好地控制刀具的破损程度,刀具采用径向负荷反馈,一旦刀具切削力达到一定的数值,在数控系统的作用下,刀具能自动退回,从而避免枪钻折断,提高刀具的使用寿命。
磨钝后的刀具换下,再重新进行刃磨后方可使用。
凸轮轴深孔加工冷却液一般用锭子油,虽然油的冷却效果比乳化液差,但油的润滑效果比冷却液要好得多。
五、主轴颈快速点磨加工与CBN砂轮快速点磨是德国勇克公司开发出来的一种先进的外圆高效磨削新工艺,该机床加工凸轮轴只需两顶尖定位夹紧,无需任何夹紧工具,利用前顶尖的高速旋转,通过顶尖和凸轮轴中心孔的摩擦来驱动工件运动,可以实现轴类零件在一次装夹后,用一片砂轮完成7个轴颈、一个端面和一个磨削圆角的工艺。
快速点磨砂轮是横向磨损,在磨损过程中,被磨削的凸轮轴外形尺寸不会因此而发生变化,磨削端面时,砂轮可倾斜±0.5︒,使砂轮与工件的接触面只有传统磨削端面的1/2。
CBN具有良好的导热性,其导热率是硬质合金的13倍,铜的3倍,另外CBN 具有远优于金刚石的热稳定性和化学稳定性(金刚石与铁簇元素易产生亲和作用),可耐1300—1500的高温,并且与铁簇元素有很大的化学惰性,CBN是制作切削黑色金属的理想刀具材料。
CBN属于立方晶系,它的硬度、强度和其它物理性能远远优于刚玉等系列磨料。
在进行磨削过程中CBN自身磨损非常少,在大批量生产过程中,单个零件所需要的成本较小。
砂轮的形状、尺寸变化极小,耐用度较高,修整频次约为刚玉系列的1/20,每次修整量约为刚玉系列的1/25,砂轮与工件的磨削区内磨削温度较低,可避免在磨削的弹性变形阶段工件所产生的裂纹和磨削烧伤等现象的出现。
CBN具有良好的化学稳定性与耐热性,与碳在2000︒C时才起反应,在高温下易与水产生反应。
砂轮的耐用度高,机床的使用率可达97%以上,与一般砂轮磨削相比,可提高功效600%--700%。
当砂轮在宽度方向的磨损量占砂轮宽度的80%时便对砂轮进行修整,砂轮每次修整量为0.006mm,共分3部进行修整,每一步修整量为0.002mm,每修整一次可磨削120根凸轮轴,砂轮线速度为120m/s,可获得较高的金属切除率,使用冷却油做为冷却液,不仅仅是给砂轮和工件提供冷却液,同时也给砂轮和工件提供更好的润滑,同时由于油膜的吸附作用,还可以防止凸轮轴的轴颈表面氧化,防止磨削完后的工件表面生锈。
磨削液的供给是采用喷射法提供的冷却液,冷却较充分,可使砂轮的寿命提高一倍,金属切除率提高一倍以上,同时采用冷却液反冲的方法,冲洗砂轮表面,防止砂轮堵塞,使CBN颗粒始终以锋利的状态对工件进行切削,再加上CBN粒度较小,凸轮轴轴颈单位面积上参加切削的磨粒比一般砂轮要多,轴颈在被切削时所产生的弹性摩擦和变形阶段均较小,因此产生的弹性变形和塑性变形均较小,提高了表面粗糙度,防止表面产生磨削烧伤和因磨粒因素而引起的裂纹。
在磨粒切削阶段,对产生的热应力和变形应力均较小。
由于磨削速度很高,磨削热量来不及传入工件的深处,瞬时聚集在凸轮轴很薄的表层,形成切屑被带走。
磨粒切削点的温度达1000︒C以上,而内部只有几十度选用CBN砂轮磨削,磨粒锋利,磨削力小,故磨削区发热量少CBN显微硬度7300—9000HV,抗弯强度300MPa、抗压强度800--1000MPa、热稳定性1250︒C--1350︒C。
应用声音传感器严格限制砂轮和金刚滚轮间的距离,主要是防止砂轮修整时砂轮和金刚滚轮发生撞击。
砂轮架纵向进给时,传感器测头与砂轮间形成一小的缝隙,砂轮高速旋转压缩砂轮周围的空气,根据空气流通的通道大小不同,所产生的气阻声音大小不一样,从而判断传感器和砂轮间的缝隙而做出反馈,一旦砂轮和金刚滚轮产生接触,修整器自动修整砂轮,而声音传感器能根据声音尖锐响声大小来判断砂轮修整的正确性。
与树脂类结合剂相比,陶瓷结合剂化学性能稳定,耐热、抗酸、碱,气孔率大,工作时不易发热,在磨削过程中易脱落,热膨胀系数小,强度较高,能保持好CBN的几何形状,且磨具易修整。
用于磨削凸轮轴轴颈和端面的CBN砂轮立方氮化硼厚度只有4.5—5MM,并且是粘附在刚性钢盘上,刚性较好。
工件转速与砂轮转速的比为:40/8000无进给磨削即光磨,可提高工件的几何精度和降低表面粗糙度参数值,表面粗糙度随光磨次数的增加而降低,细粒度砂轮比粗粒度好砂轮的修整:修整通常包括整形和修锐,整形是使砂轮达到要求的几何形状和精度,砂轮的几何形状采用数控插补法进行,修锐是除去磨粒间的结合剂,使磨粒露出结合剂一定高度,形成切削刃,磨粒间空隙以容纳切屑。
金刚石滚轮磨削修整的特点:生产率高:以切入法进行修整,修整时间仅需2-10秒,可在进行凸轮轴更换工件时进行修整,不耽误生产节拍,同时由于金刚滚轮的寿命长,修整时间短,大大缩短了辅助时间,单件工件的消耗较低,金刚滚轮的精度较高,修整后的砂轮表面质量也较好。