铝合金铸造件检验技术条件
铸件质量检验标准

铸件质量检验标准铸件是一种常见的生产工艺,广泛用于各个行业和领域。
铸件质量的好坏直接影响产品的性能和可靠性,因此进行铸件质量检验至关重要。
本文将介绍铸件质量检验的标准和方法。
一、铸件质量检验的重要性铸件质量检验的目的是确保铸件的尺寸精度、表面质量和机械性能达到设计要求。
一方面,铸件的尺寸精度和表面质量直接影响产品的装配和使用;另一方面,对于承受重载或高温等极端工况的铸件来说,其机械性能的好坏关系到产品的安全可靠性。
二、铸件质量检验的标准铸件质量检验的标准包括国家标准、行业标准和企业自身标准。
国家标准是根据相关法律法规制定的,具有强制性,是衡量铸件质量的重要依据。
行业标准是在国家标准的基础上,由行业协会或行业组织制定的,作为行业内铸件质量的参考指南。
企业自身标准是企业根据生产情况和需求制定的,用于规范和管理内部质量控制。
在铸件质量检验中,常用的国家标准有《铸造铁件技术条件》、《铸铝合金件技术条件》等,而行业标准包括《汽车铝合金压铸铸件技术规范》、《船用铸铁件技术条件》等。
企业自身标准则根据企业具体的生产工艺和要求制定,例如《XX公司铸件质量检验标准》。
三、铸件质量检验的方法铸件质量检验的方法主要包括外观检查、尺寸检测和性能测试。
1. 外观检查外观检查是铸件质量检验中最简单直观的方法。
通过肉眼观察铸件的外观,检查是否有裂纹、砂眼、气孔、夹渣等缺陷。
外观检查可以用目视检查或借助放大镜进行观察。
2. 尺寸检测尺寸检测是铸件质量检验中最常见的方法。
主要是测量铸件的外形尺寸、孔径尺寸和壁厚尺寸等。
常用的尺寸测量工具有游标卡尺、内径卡尺、外径卡尺、深度尺等。
尺寸检测可以帮助判断铸件是否满足设计要求。
3. 性能测试性能测试是铸件质量检验中最关键的方法,主要包括力学性能测试、化学成分分析和金相组织分析。
力学性能测试主要是测试铸件的拉伸、弯曲、冲击等力学性能。
化学成分分析可以确定铸件的材料成分是否符合要求。
金相组织分析可以观察铸件的金相组织结构,评估其机械性能。
铝合金铸件气孔标准
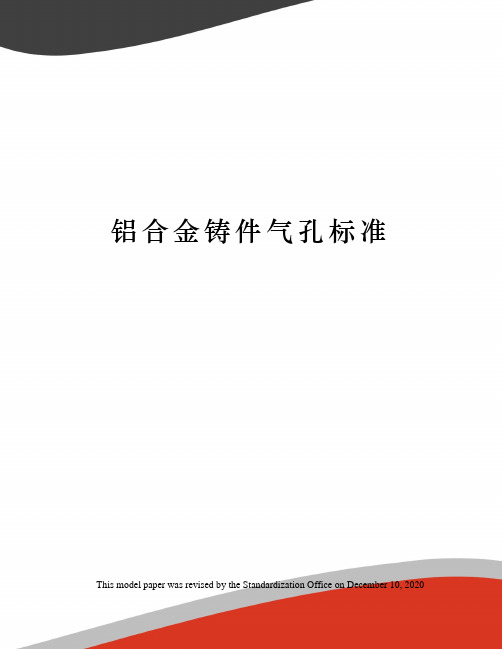
铝合金铸件气孔标准This model paper was revised by the Standardization Office on December 10, 2020铝合金铸件气孔、针孔检验标准一.适用范围本标准规定了铸件气孔、针孔允许存在的范围、大小、数量等技术要求。
本标准规定了铸造铝合金低倍针孔度的分级原则和评级方法。
本标准适用于铝合金的砂型铸造。
适用于评定铸件外表面及需要加工面经加工后的表面气孔、针孔。
二.引用标准GB1173-86铸造铝合金技术条件GB9438-88铝合金铸件技术条件GB10851-89铸造铝合金针孔三.气孔、针孔等孔洞类特征1.位于铸件内部而不延伸到铸件外部的气眼。
(1)气孔、针孔内壁光滑,大小不等的圆形孔眼,单个或成组无规则的分布在铸件的各个部位。
(2)气渣孔其特征同气孔、针孔相似,但伴随有渣子。
2.表面或近表面的孔眼,大部分暴露或与外表面相连。
(1)表面或皮下气孔大小不等的单个或成组的孔眼,位于铸件表面或近表面的部位,其内壁光滑。
(2)表面针孔铸件表面上细小的孔洞,呈现在较大的区域上。
四.具体条件1.砂型、金属型铸件的非加工表面和加工表面,在清整干净后允许存在下列孔洞:(1)单个孔洞的最大直径不大于3mm,深度不超过壁厚1/3,在安装边上不超过壁厚的1/4,且不大于1.5mm,在上述缺陷的同一截面的反面对称部位不得有类似的缺陷。
(2)成组孔洞最大直径不大于2mm,深度不超过壁厚的1/3,且不大于1.5mm。
(3)上述缺陷的数量及边距应符合表一规定表一非加工表面或加工表面总面积小于1000cm2 单个孔洞成组孔洞在10cm×10cm单位面积上孔洞数不多于4个孔洞边距不小于10mm一个铸件的非加工表面或加工面上孔洞总数不多于6个,孔洞边缘距铸件或距内孔边缘的距离不小于孔洞最大直径的2倍以3cm×3cm单位面积为一组,其孔洞数不多于3个在一个铸件上组的数量不多于2组孔洞边缘距铸件边缘或距内孔边缘的距离不小于孔洞最大直径的2倍2.液压、气压件的加工表面上,铸件以3级针孔作为验收基础,要求2级针孔占受检面积的25%以上,局部允许4级针孔,但一般不得超过受检面积的25%,当满足用户对致密性的技术要求时或对其它砂型、金属型铸件允许按低一级的针孔度验收。
铝合金压铸件的标准
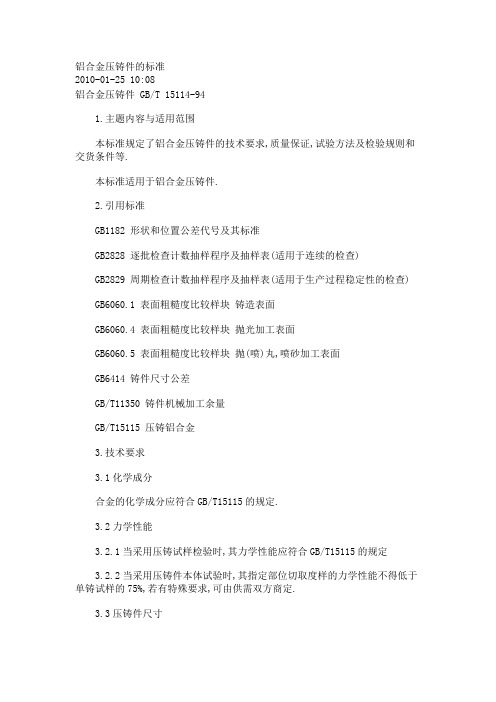
铝合金压铸件的标准2010-01-25 10:08铝合金压铸件 GB/T 15114-941.主题内容与适用范围本标准规定了铝合金压铸件的技术要求,质量保证,试验方法及检验规则和交货条件等.本标准适用于铝合金压铸件.2.引用标准GB1182 形状和位置公差代号及其标准GB2828 逐批检查计数抽样程序及抽样表(适用于连续的检查)GB2829 周期检查计数抽样程序及抽样表(适用于生产过程稳定性的检查)GB6060.1 表面粗糙度比较样块铸造表面GB6060.4 表面粗糙度比较样块抛光加工表面GB6060.5 表面粗糙度比较样块抛(喷)丸,喷砂加工表面GB6414 铸件尺寸公差GB/T11350 铸件机械加工余量GB/T15115 压铸铝合金3.技术要求3.1化学成分合金的化学成分应符合GB/T15115的规定.3.2力学性能3.2.1当采用压铸试样检验时,其力学性能应符合GB/T15115的规定3.2.2当采用压铸件本体试验时,其指定部位切取度样的力学性能不得低于单铸试样的75%,若有特殊要求,可由供需双方商定.3.3压铸件尺寸3.3.1压铸件的几何形状和尺寸应符合铸件图样的规定3.3.2压铸件尺寸公差应按GB6414的规定执行,有特殊规定和要求时,须在图样上注明.3.3.3压铸件有形位公差要求时,其标注方法按GB1182的规定.3.3.4压铸件的尺寸公差不包括铸造斜度,其不加工表面:包容面以小端为基准,有特殊规定和要求时,须在图样上注明.3.4压铸件需要机械加工时,其加工余量按GB/T11350的规定执行.若有特殊规定和要求时,其加工作量须在图样上注明.3.5表面质量3.5.1铸件表面粗糙度应符合GB6060.1的规定3.5.2铸件不允许有裂纹,欠铸,疏松,气泡和任何穿透性缺陷.3.5.3铸件不允许有擦伤,凹陷,缺肉和网状毛刺等腰三角形缺陷,但其缺陷的程度和数量应该与供需双方同意的标准相一致.3.5.4铸件的浇口,飞边,溢流口,隔皮,顶杆痕迹等腰三角形应清理干净,但允许留有痕迹.3.5.5若图样无特别规定,有关压铸工艺部分的设置,如顶杆位置,分型线的位置,浇口和溢流口的位置等由生产厂自行规定;否则图样上应注明或由供需双方商定.3.5.6压铸件需要特殊加工的表面,如抛光,喷丸,镀铬,涂覆,阳极氧化,化学氧化等须在图样上注明或由供需双方商定.3.6内部质量3.6.1压铸件若能满足其使用要求,则压铸件本质缺陷不作为报废的依据.3.6.2对压铸件的气压密封性,液压密封性,热处理,高温涂覆,内部缺陷(气孔,疏孔,冷隔,夹杂)及本标准未列项目有要求时,可由供需双方商定.3.6.3在不影响压铸件使用的条件下,当征得需方同意,供方可以对压铸件进行浸渗和修补(如焊补,变形校整等)处理.4质量保证4.1当供需双方合同或协议中有规定时,供方对合同中规定的所有试验或检验负责.合同或协议中无规定时,经需方同意,供方可以用自已适宜的手段执行本标准所规定的试验和要求,需方有权对标准中的任何试验和检验项目进行检验,其质量保证标准应根据供需双方之间的协议而定.4.2根据压铸生产特点,规定一个检验批量是指每台压铸设备在正常操作情况下一个班次的生产量,设备,化学成分,铸型和操作连续性的任何重大变化都应被认为是新是一个批量开始.供方对每批压铸件都要随机或统计地抽样检验,确定是否符合全部技术要求和合同或铸件图样的规定要求,检验结果应予以记录.5试验方法及检验规则5.1化学成分5.1.1合金化学成分的检验方法,检验规则和复检应符合GB/T15115的规定.5.1.2化学成分的试样也可取自压铸件,但必须符合GB/T15115的规定5.2力学性能5.2.1力学性能的检验方法,检验频率和检验规则就符合GB/T15115的规定.5.2.2采用压铸件本体为试样时,切取部位尺寸,测试形式由供需双方商定.5.3压铸件几何尺寸的检验可按检验批量抽验或按GB2828,GB2829的规定进行,抽检结果必须符合标准3.3的规定.5.4压铸件表面质量就逐检查,检查结果应符合本标准3.5的规定.5.5压铸件表面粗糙度按GB6060.1的规定执行.5.6压铸件需抛光加工的表面按GB6060.4的规定执行,5.7压铸件需喷丸,喷砂加工的表面按GB6060.5的规定执行.5.8压铸件内部质量的试验方法检验规则由供需双方商定,可以包括:X射线照片,无损探伤,耐压试验,金相图片和压铸件剖面等,其检难结果应符合3.6的规定.5.9经浸渗和修补处理后的压铸件应做相应的质量检验.6压铸件的交付,包装,运输与储存6.1当在合同或协议中有要求时,供方应提供需方一份检验证明,用来说明每批压铸件的取样,试验和检验符合标准的规定.6.2合格压铸件交付时,必须有附有检验合格证,其上应写明下列内容:产品名称,产品号,合金牌号,数量,交付状态,制造厂名,检验合格印记和交付时间.有特殊检验项目者,应在检验员合格证上注明检验的条件和结果.6.3压铸件的包装,运输与储存,由供需双方商定。
锌合金、铜合金、铝合金压铸件技术条件

中华人民共和国第一机械工业部部标准锌合金、铝合金、铜合金压铸件技术条件JB 2702—80北京1981中华人民共和国第一机械工业部部标准JB 2702—80 锌合金、铝合金、铜合金压铸件技术条件本标准适用于机电、仪表、汽车、拖拉机等机械工业产品的锌合金、铝合金、铜合金压铸件(以下简称铸件)。
对有特殊要求的铸件,经商议后应在图样中注明。
一、铸件分类及级别1.铸件按使用要求分为两类,见表1。
2.铸件表面质量按使用范围分为三级,见表2。
3.铸件的类别和表面质量的级别应在图样中注明,表示方法如下:Ⅱ-∽铸件表面质量级别铸件分类类别铸件标准代号如有更高要求的部位应在图样中有关面处分别注明。
4.未注明铸件类别、级别和尺寸精度者,均按本标准相关的最低级别处理。
二、尺寸精度5.铸件线性尺寸公差才选用中华人民共和国第一机械工业部发布 1 9 8 1 年 1 月 1 日实施一机部沈阳铸造研究所提出上海电器压铸三、上海电表厂等起草共11页第2页 JB 2702—80⑴铸件的基本尺寸公差按表3选用。
铸件受分型面或模具活动部位影响的尺寸应按表4、表5规定,在基本尺寸公差上再加附加公差。
铸件基本尺寸公差表3线性尺寸受分型面影响时的附加公差表4线性尺寸受模具活动部位影响时的附加公差表5注:一模多铸时,铸件分型面上的投影面积为各铸件投影面积之和附加公差应用示例:JB 2702—80 共11页第3页1 铝合金压铸件的尺寸A为3+0.12mm(基本公差按7级精度),模具活动部位由成形滑块构成,其投影面积为34cm2,由表5查得其附加公差为0.20mm,则A的尺寸公差应为0.12+0.20=0.32(mm) 。
2 在同一铸件上尺寸B为2.5+0.12mm(基本公差按7级精度),模具活动部位由滑块型芯构成,型芯直径为20mm,则其投影面积为3.14cm2,由表5查得其附加公差为0.15mm,则B处的尺寸公并为+0.12/-0.15。
⑵尺寸公差带的位置a.不加工的配合尺寸,孔取正(+),轴取负(-)。
铝合金压铸技术要求

1、范围本标准规定了铝合金压铸件的技术要求、试验方法、检验规那么、交货条件等。
本标准适用于汽车发电机铝合金端盖压铸件。
2、引用标准GB6414铸件尺寸公差铝及铝合金化学分析方法GB288-87金属拉力试验法GB/T13822-92 压铸有色合金试样GB6060.5 外表粗造度比拟样块抛(喷)丸、喷吵加工外表3、技术要求3.1 压铸铝合金的牌号压铸铝合金采用UNS-A03800〔美国,日本ADC10〕可选用材料UNS-A03830 〔美国,日本ADC12〕化学成份见表1表1供给商可选择上述四种牌号的任何一种,如在生产过程中更换其它牌号,需重新进展样件鉴定。
一级回炉料:浇道、化学成份合格的废铸件,后加工次品等不含水分和油污。
二级回炉料:集渣包、坩埚底部剩料、退货废品、存放时间长〔超过10天〕的一级回炉料。
三级回炉料:飞边、溅屑、细小的碎料、带有油污的渣料、因化学成份报废的铸件、从铝渣中捡出的铝粒。
使用单一某级回炉料:一级回炉料最大使用量50%,二级回炉料最大使用量40%。
一级、二级回炉料混合使用:回炉料总量不超过40%,其中二级回炉料最大使用量20%。
三级回炉料:不能直接使用,必须经过重熔、精炼且化学成份分析合格后才能使用,其最大使用量10%,仅与铝锭混合使用。
小颗粒回炉料大块回炉料铝锭,如此循环。
3.2 力学性能采用单铸拉力试样检验,其力学性能应满足抗拉强度≥240Mpa,伸长率≥1%,HB85〔5/250/30〕。
试样尺寸及形状应符合GB/T 13822-92?压铸有色合金试样?的规定。
3.3 压铸件尺寸压铸件的几何形状和尺寸应符合铸件图的规定。
3.4 待加工外表用符号“〞标明,尖头指向被加工面。
例:0.5 表示该外表留有加工余量3.5 外表质量3.5.1 铸件清理后的外表质量铸件的浇口、飞边、溢流口、隔皮等应清理干净,但允许留有清理痕迹。
在不影响使用的情况下,因去除浇口、溢流口时所形成的缺肉或高出均不得超过壁厚的四分之一,并且不得超过1.5 mm。
铝合金铸造件检验技术条件
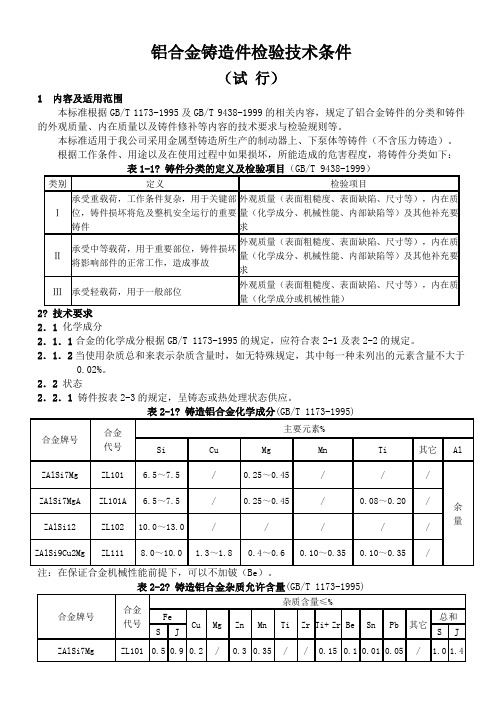
铝合金铸造件检验技术条件(试行)1 内容及适用范围本标准根据GB/T 1173-1995及GB/T 9438-1999的相关内容,规定了铝合金铸件的分类和铸件的外观质量、内在质量以及铸件修补等内容的技术要求与检验规则等。
本标准适用于我公司采用金属型铸造所生产的制动器上、下泵体等铸件(不含压力铸造)。
根据工作条件、用途以及在使用过程中如果损坏,所能造成的危害程度,将铸件分类如下:2?技术要求2.1 化学成分2.1.1合金的化学成分根据GB/T 1173-1995的规定,应符合表2-1及表2-2的规定。
2.1.2当使用杂质总和来表示杂质含量时,如无特殊规定,其中每一种未列出的元素含量不大于0.02%。
2.2 状态2.2.1铸件按表2-3的规定,呈铸态或热处理状态供应。
注:在保证合金机械性能前提下,可以不加铍(Be)。
2.3 机械性能2.3.1 每批铸件应按其类别检验机械性能。
2.3.2 合金及其铸件的机械性能应符合表2-3的规定。
2.4外观质量2.4.1铸件在进行表面粗糙度、表面缺陷、尺寸等外观质量检验之前,飞边、溢流口、隔皮等应清理干净、平整,但不可在非加工表面上留有明显的凿痕,且宽度不得超过2mm。
2.4.2铸件的表面粗糙度Ra为6.3μm以上。
2.4.3非加工表面的浇冒口,应清理到与铸件表面齐平;待加工表面的浇冒口残留量应不大于3mm。
2.4.4清除飞翅、夹砂等多肉类缺陷,铸件的内外表面由于型芯及顶杆的磨损所产生的飞边、毛刺应清除干净。
2.4.5根据顾客图样或技术文件的要求,铸件表面可进行喷砂处理。
2.4.6铸件上作为基准用的部位应平整,不允许存在任何凸起痕迹,装饰面上不允许有推杆痕迹(图样上注明)。
2.4.7非加工表面上,由于模具组合镶并或受分型面影响而形成的铸件表面高低不平差值不得超过0.3mm。
2.4. 8非加工表面上,不允许有超过表2-4(Ⅰ)级规定的花纹、麻面和有色斑点。
2.4.9铸件尺寸应符合图样的要求。
铝合金材料检验试验规范
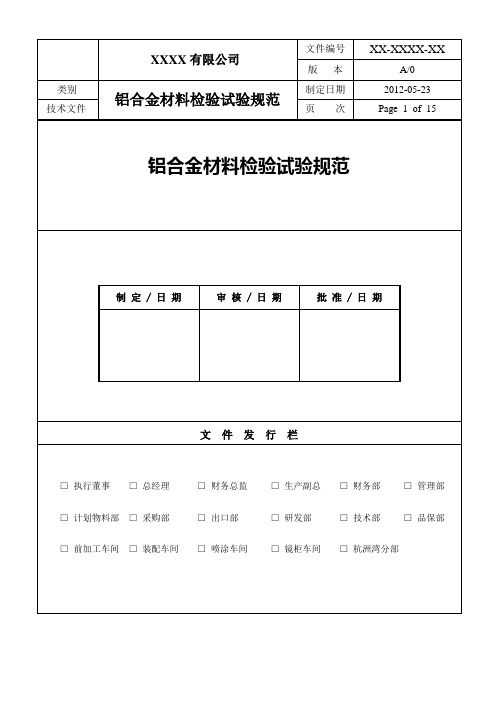
类别铝合金材料检验试验规范制定日期2012-05-23技术文件页次Page 9 of 15a)弯曲试验应在配备下列弯曲装置之一的试验机或压力机上完成:b)配有两支辊和一个弯曲压头的支辊式弯曲装置, 见图1c)配有一个V型器具和一个弯曲压头的V型模具式弯曲装置, 见图2虎钳式弯曲装置, 见图3图1图2 图38.3.2支辊式弯曲装置8.3.2.1 支辊长度和弯曲压头的宽度应大于试样宽度或直径(见图1).弯曲压头的直径由产品标准规定。
支辊和弯曲压头应具有足够的硬度。
8.3.2.2除非中有规定, 支辊间距离L应按照式(1)确定:L=(D+3a)± a/2 (1)注: 此距离在试验期间应保持不变。
8.3.3 V型模具式弯曲装置模具的V形槽其角度应为(180°-a)(见图2), 弯曲角度a应在相关产品零件图中规定。
模具的支承棱边应倒圆, 其倒圆半径应为(1~10)倍试样厚度。
模具和弯曲压头宽度应大于试样宽度或直径并具有足够的硬度。
8.3.4 虎钳式弯曲装置装置由虎钳及有足够硬度的弯曲压头组成(见图3), 可以配置加力杠杆。
弯曲压头直径应按照产品标准要求, 弯曲压头宽度应大于试样宽度或直径。
8.4.试样类别铝合金材料检验试验规范制定日期2012-05-23技术文件页次Page 11 of 15F8.6.试验结果的评定:8.6.1应按照相关产品标准的要求评定弯曲试验结果。
如未规定具体要求, 弯曲试验后不使用放大镜观察, 试样弯曲外表面无可见裂纹应评定为合格。
8.6.2 以相关产品标准要求规定的弯曲角度作为最小值;若规定弯曲压头直径, 以规定的弯曲压头直径作为最大值。
8.7 试验报告a)试验报告至少应包括以下内容:b)本标准编号;c)试样标识(材料牌号, 取样方向)d)试样的形状和尺寸e)试样条件(弯曲压头直径, 弯曲角度)f)与标准的偏差g)试验结果评定9.铝型材管材压扁试验(GB246-2007)9.1 范围规定了测定圆形横截面金属管塑性变形能力的压扁试验方法, 包括显示其缺陷。
铸造铝合金锭检验验收规则
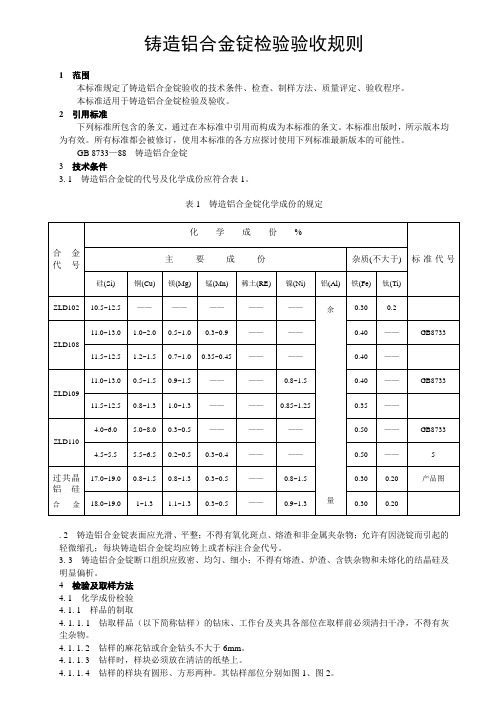
铸造铝合金锭检验验收规则1 范围本标准规定了铸造铝合金锭验收的技术条件、检查、制样方法、质量评定、验收程序。
本标准适用于铸造铝合金锭检验及验收。
2 引用标准下列标准所包含的条文,通过在本标准中引用而构成为本标准的条文。
本标准出版时,所示版本均为有效。
所有标准都会被修订,使用本标准的各方应探讨使用下列标准最新版本的可能性。
GB 8733—88 铸造铝合金锭3 技术条件3. 1 铸造铝合金锭的代号及化学成份应符合表1。
表1 铸造铝合金锭化学成份的规定. 2 铸造铝合金锭表面应光滑、平整;不得有氧化斑点、熔渣和非金属夹杂物;允许有因浇锭而引起的轻微缩孔;每块铸造铝合金锭均应铸上或者标注合金代号。
3. 3 铸造铝合金锭断口组织应致密、均匀、细小;不得有熔渣、炉渣、含铁杂物和未熔化的结晶硅及明显偏析。
4 检验及取样方法4. 1 化学成份检验4. 1. 1 样品的制取4. 1. 1. 1 钻取样品(以下简称钻样)的钻床、工作台及夹具各部位在取样前必须清扫干净,不得有灰尘杂物。
4. 1. 1. 2 钻样的麻花钻或合金钻头不大于6mm。
4. 1. 1. 3 钻样时,样块必须放在清洁的纸垫上。
4. 1. 1. 4 钻样的样块有圆形、方形两种。
其钻样部位分别如图1、图2。
1 2 4 5 1 2(反面)图1 图24. 1. 1. 5 钻孔深度不小于样品厚度的2/3,钻孔时必须先去掉表层氧化皮,然后钻取,样品必须细小,不得有大块铝屑存在,样品倒入样品袋时必须与样品袋的编号一致,并不得混入外来物。
4. 1. 1. 6 化学成份检验不合格时,则应进行复查,样品从该批次铸锭中任取两块,沿其对角线正反面各钻取一点,钻在对角线锭块中小至两端的1/2处,深度为锭块厚度的2/3。
4. 1. 2 检验方法按GB 8733中2. 1执行。
4. 2 断口及外表检验4. 2. 1 对化学成分合格的批次铸造铝合金锭中随机抽取断口及外表样品一至二块。
铸件图的技术条件

5.铸件表面粗糙度的标准。比如,“铸件表面粗糙度按GB6060.1--85《铸件表面粗糙度比较样块》,不低于Ra25;”了指定的表面,大部分表面的防锈处理。比如,“铸件表面涂铁红醇酸底漆;”
7.其余项目执行的标准。比如,“其余按Q/TY014.2《图样通用技术要求》验收铸件。
铸件图的技术条件
技术要求
先从零件图的技术条件中选取铸件验收时需要的技术要求。
常见的技术要求有如下几条:
1.未注明的铸造圆角半径R ;起模斜度 x°;
2.允许的铸造缺陷;不允许的铸造缺陷;允许修补的铸造缺陷及其修补方法;
3.浇冒口余头的高度;比如,“浇冒口余头不高于1mm;”
4.未注明的铸造公差执行的标准,比如“未注明的铸件尺寸公差按Q/YT022.4--92《砂型铸造造型铸件尺寸公差》验收铸件;”
或者“按Q/YT303.2--86《灰铸铁件验收技术条件》验收铸件。”
或者“按Q/YT303.1--86《球墨铸铁件验收技术条件》验收铸件。”
或者“按Q/YT303.3--86《碳钢铸件验收技术条件》验收铸件。”
或者“按Q/YT303.5--86《铝合金铸件验收技术条件》验收铸件。”
或者“按Q/YT303.6--86《高锰钢履带板验收技术条件》验收铸件。”
铸件验收标准

1)、清理干净后最大直径不大于 3mm,深度在铸件壁上不大于壁厚的 1/3,在安装边上不大于其厚度的 1/4,且不得超过 1.5mm 的单个孔洞和清理干净后最大直径不大于 1.5mm,深度不大于壁厚的 1/3,且不
注:铸件在机械加工前后发现的小缺陷,经有关部门同意,补焊后可不进行热处理。 24、补焊处需经表面检查和根据工艺需要进行 X 光透视,透视不得小于补焊面积的两倍。焊区内允许的标准
与 X 光透视标准相同。 注:铸件表面上小的明孔洞,补焊后可不透视,(扩修后<1.5cm2 明孔洞)。 25、翘曲的铸件允许矫正,矫正后应检查有无裂纹,必要时需重复进行热处理。
≥80 ≥100 ≥50 ≥90 ≥70 ≥80 ≥70 90-115 ≥70 85~115 ≥80 ≥70 ≥80 ≥50 80-100
注: 1)硬度值除设计部门规定按表 2 检验外,仅作验收依据。
2)当测得的机械性能数值遇界限值时,按本标准规定的有效位数进行修约,修约按 GB1780 的规定,强
二:技术要求和检验
*** 化学成份 ***
1、每一炉次的合金,必须对以下成份进行光谱分析。合金的化学成份分析结果应符合表 1 的规定。同时,
在铸件上标识炉号及炉次号进行追溯。
注:当测得的化学成分数值遇界限值时,按本标准规定的有效位数进行修约,修约规则按 GB1780r 规定。
表 1 化学成份 %
合金 代号
铝合金铸件综合技术条件
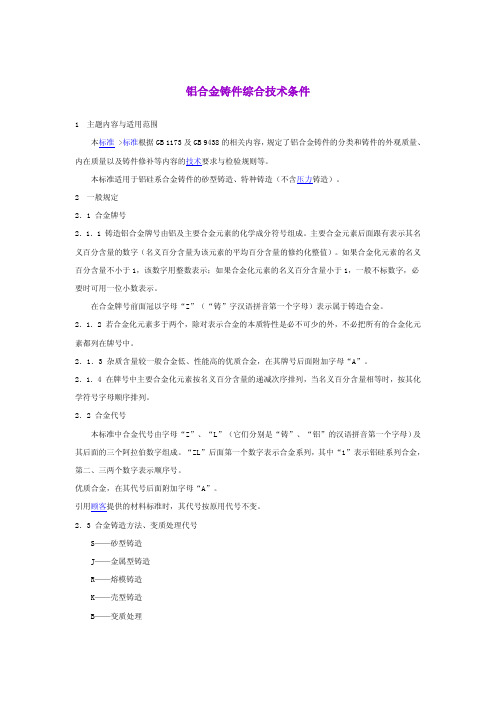
重要铸件
承受中等载荷,用于重要部位,铸件损 外观质量(表面粗糙度、表面缺陷、尺寸等),内在质量 Ⅱ
坏将影响部件的正常工作,造成事故 (化学成分、机械性能、内部缺陷等)及其他补充要求
Ⅲ 承受轻载荷,用于一般部位
外观质量(表面粗糙度、表面缺陷、尺寸等),内在质量 (化学成分或机械性能)
ZAlSi5Cu1MgA ZL105A 0.2 0.2 / / 0.1 0.1 / / / / 0.01 0.05 / 0.5 0.5
ZAlSi8Cu1Mg ZL106 0.6 0.8 / / 0.2 / / / / / 0.01 0.05 / 0.9 1.0
ZAlSi7Cu4
ZL107 0.5 0.6 / 0.1 0.3 0.5 / / / / 0.01 0.05 / 1.0 1.2
J SB、JB、RB
J S、R、J、K
J SB、RB、KB
J、JB S、J、R、K
S、R、K J
S、R、K S、J、R、K
合金 状态
F T2 T4 T4 T5 T5 T5 T6 T7 T8 T4 T4 T5 T5 T5 T6 T6 F F T2 T2 F T1 T6 T6 T1 T5 T5 T6 T7
2
ZAlSi7Mg1A
ZL114A
J、JB
T5
310
3
S
T4
222
4
J
T4
271
6
ZAlSi5Zn1Mg
ZL115
S
T5
271
3.5
J
T5
310
5
S
T4
铝合金铸件气孔标准完整版
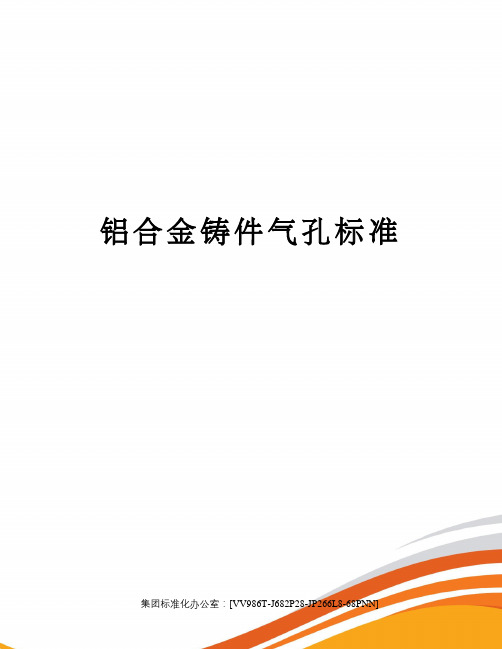
铝合金铸件气孔标准集团标准化办公室:[VV986T-J682P28-JP266L8-68PNN]铝合金铸件气孔、针孔检验标准一.适用范围本标准规定了铸件气孔、针孔允许存在的范围、大小、数量等技术要求。
本标准规定了铸造铝合金低倍针孔度的分级原则和评级方法。
本标准适用于铝合金的砂型铸造。
适用于评定铸件外表面及需要加工面经加工后的表面气孔、针孔。
二.引用标准GB1173-86铸造铝合金技术条件GB9438-88铝合金铸件技术条件GB10851-89铸造铝合金针孔三.气孔、针孔等孔洞类特征1.位于铸件内部而不延伸到铸件外部的气眼。
(1)气孔、针孔内壁光滑,大小不等的圆形孔眼,单个或成组无规则的分布在铸件的各个部位。
(2)气渣孔其特征同气孔、针孔相似,但伴随有渣子。
2.表面或近表面的孔眼,大部分暴露或与外表面相连。
(1)表面或皮下气孔大小不等的单个或成组的孔眼,位于铸件表面或近表面的部位,其内壁光滑。
(2)表面针孔铸件表面上细小的孔洞,呈现在较大的区域上。
四.具体条件1.砂型、金属型铸件的非加工表面和加工表面,在清整干净后允许存在下列孔洞:(1)单个孔洞的最大直径不大于3mm,深度不超过壁厚1/3,在安装边上不超过壁厚的1/4,且不大于1.5mm,在上述缺陷的同一截面的反面对称部位不得有类似的缺陷。
(2)成组孔洞最大直径不大于2mm,深度不超过壁厚的1/3,且不大于1.5mm。
(3)上述缺陷的数量及边距应符合表一规定表一非加工表面或加工表面总面积小于1000cm2单个孔洞成组孔洞在10cm×10cm单位面积上孔洞数不多于4个孔洞边距不小于10mm一个铸件的非加工表面或加工面上孔洞总数不多于6个,孔洞边缘距铸件或距内孔边缘的距离不小于孔洞最大直径的2倍以3cm×3cm单位面积为一组,其孔洞数不多于3个在一个铸件上组的数量不多于2组孔洞边缘距铸件边缘或距内孔边缘的距离不小于孔洞最大直径的2倍2.液压、气压件的加工表面上,铸件以3级针孔作为验收基础,要求2级针孔占受检面积的25%以上,局部允许4级针孔,但一般不得超过受检面积的25%,当满足用户对致密性的技术要求时或对其它砂型、金属型铸件允许按低一级的针孔度验收。
关于铝合金针孔度x光检验标准

关于铝合金针孔度x光检验标准
摘要:
1.铝合金针孔度检验的背景和意义
2.针孔度检验的方法和标准
3.铝合金针孔度检验中的注意事项
4.铝合金针孔度检验的实际应用
正文:
铝合金针孔度检验的背景和意义
铝合金针孔度检验是保证铝合金铸件质量的重要手段之一。
在铝合金铸造过程中,针孔是一种常见的缺陷,它会影响铸件的性能和使用寿命。
因此,对铝合金针孔度进行检验是非常必要的。
针孔度检验的方法和标准
铝合金针孔度检验通常采用X 光透射法。
这种方法可以对铸件内部的针孔进行准确检测。
在检验过程中,需要遵循相关的检验标准,例如GB1173-86《铸造铝合金技术条件》和GB9438-88《铝合金铸件技术条件》等。
铝合金针孔度检验中的注意事项
在进行铝合金针孔度检验时,需要注意以下几点:
1.检验的样本应该具有代表性,以便准确反映整个铸件的情况。
2.检验过程中应该避免受到外部环境的影响,例如温度、湿度等。
3.检验人员应该具备相关的专业知识和技能,以便准确判断检验结果。
4.检验设备应该定期进行维护和校准,以保证检验结果的准确性。
铝合金针孔度检验的实际应用
铝合金针孔度检验在实际应用中具有重要意义。
通过检验,可以及时发现和排除铸件中的针孔缺陷,保证铸件的质量和性能。
同时,检验结果还可以为铸造工艺的改进提供有力的依据。
总之,铝合金针孔度检验是保证铝合金铸件质量的重要手段。
铝铸件企业标准
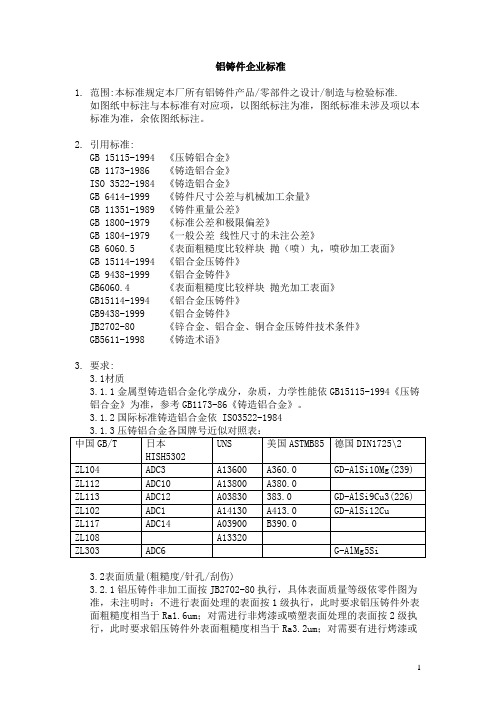
铝铸件企业标准1.范围:本标准规定本厂所有铝铸件产品/零部件之设计/制造与检验标准.如图纸中标注与本标准有对应项,以图纸标注为准,图纸标准未涉及项以本标准为准,余依图纸标注。
2.引用标准:GB 15115-1994 《压铸铝合金》GB 1173-1986 《铸造铝合金》ISO 3522-1984 《铸造铝合金》GB 6414-1999 《铸件尺寸公差与机械加工余量》GB 11351-1989 《铸件重量公差》GB 1800-1979 《标准公差和极限偏差》GB 1804-1979 《一般公差线性尺寸的未注公差》GB 6060.5 《表面粗糙度比较样块抛(喷)丸,喷砂加工表面》GB 15114-1994 《铝合金压铸件》GB 9438-1999 《铝合金铸件》GB6060.4 《表面粗糙度比较样块抛光加工表面》GB15114-1994 《铝合金压铸件》GB9438-1999 《铝合金铸件》JB2702-80 《锌合金、铝合金、铜合金压铸件技术条件》GB5611-1998 《铸造术语》3.要求:3.1材质3.1.1金属型铸造铝合金化学成分,杂质,力学性能依GB15115-1994《压铸铝合金》为准,参考GB1173-86《铸造铝合金》。
3.1.2国际标准铸造铝合金依 ISO3522-19843.2表面质量(粗糙度/针孔/刮伤)3.2.1铝压铸件非加工面按JB2702-80执行,具体表面质量等级依零件图为准,未注明时:不进行表面处理的表面按1级执行,此时要求铝压铸件外表面粗糙度相当于Ra1.6um;对需进行非烤漆或喷塑表面处理的表面按2级执行,此时要求铝压铸件外表面粗糙度相当于Ra3.2um;对需要有进行烤漆或喷塑后处理的表面质量按3级执行,对需要其它形式后理的表面质量要求依后处理方式的具体要求决定,余按3级执行,在可接受范围内的表面质量缺陷不得出现在影响产品使用和机械性能的部位,对存在多种表面处于理形式的零件,按最高级别执行。
汽车用铝合金铸件技术条件-概述说明以及解释

汽车用铝合金铸件技术条件-概述说明以及解释1.引言1.1 概述概述汽车用铝合金铸件技术条件是指在汽车制造过程中,对于使用铝合金材料进行铸造的要求和标准。
随着车辆轻量化趋势的不断发展,汽车制造商越来越倾向于使用轻质材料来替代传统的钢铁材料。
铝合金作为一种重要的轻质材料,在汽车行业中得到了广泛的应用。
汽车用铝合金铸件技术条件的重要性不容忽视。
正确的技术条件可以保证铝合金铸件的质量和性能,同时也能提高生产效率和降低成本。
对于汽车制造商来说,汽车用铝合金铸件的质量和性能直接影响到车辆的安全性和可靠性。
因此,制定合适的技术条件对于保证汽车的品质至关重要。
本文将从以下几个方面对汽车用铝合金铸件技术条件进行详细的探讨。
首先,我们将介绍车辆轻量化趋势,解析为什么轻质材料在汽车制造中的应用越来越广泛。
其次,我们将深入探讨铝合金铸件在汽车行业中的应用,介绍铝合金材料在汽车制造中的优势和挑战。
最后,我们将重点关注汽车用铝合金铸件技术条件的重要性,分析如何制定合适的技术条件以保证铸件的质量和性能。
通过对这些内容的探讨和分析,我们将总结出汽车用铝合金铸件技术条件的关键要点,展望未来该技术的发展前景。
我们希望本文能够帮助读者更好地理解汽车用铝合金铸件技术条件的重要性,并为汽车制造商提供实用的指导和建议。
让我们一起深入研究这一重要的汽车制造技术,为推动汽车工业的发展做出贡献。
1.2 文章结构本篇文章主要分为引言、正文和结论三个部分。
在引言部分,首先概述了本文要讨论的内容——汽车用铝合金铸件技术条件。
接着介绍了文章的结构和目的,以让读者了解本文的整体安排和写作意图。
正文部分分为三个小节。
首先,讨论了当前车辆轻量化趋势,即汽车行业中越来越重视车辆的减重问题,并探讨了轻量化的重要性和影响。
接着,阐述了铝合金铸件在汽车行业中的应用情况,展示了铝合金铸件在解决车辆轻量化问题上的优势以及其在汽车制造中的广泛应用。
最后,重点讨论了汽车用铝合金铸件技术条件的重要性,介绍其对于铸件质量、性能、成本和可靠性的影响,以及对整个汽车制造工艺的重要作用。
半固态铝合金压铸件通用技术条件

半固态铝合金压铸件通用技术条件下载提示:该文档是本店铺精心编制而成的,希望大家下载后,能够帮助大家解决实际问题。
文档下载后可定制修改,请根据实际需要进行调整和使用,谢谢!本店铺为大家提供各种类型的实用资料,如教育随笔、日记赏析、句子摘抄、古诗大全、经典美文、话题作文、工作总结、词语解析、文案摘录、其他资料等等,想了解不同资料格式和写法,敬请关注!Download tips: This document is carefully compiled by this editor. I hope that after you download it, it can help you solve practical problems. The document can be customized and modified after downloading, please adjust and use it according to actual needs, thank you! In addition, this shop provides you with various types of practical materials, such as educational essays, diary appreciation, sentence excerpts, ancient poems, classic articles, topic composition, work summary, word parsing, copy excerpts, other materials and so on, want to know different data formats and writing methods, please pay attention!一、引言随着工业的不断发展,半固态铝合金压铸件作为一种轻质、高强度、耐热性能优良的材料,在航空航天、汽车制造、机械制造等领域得到了广泛应用。
铝合金铸造国家标准

铝合金铸造国家标准铝合金是一种轻质、高强度、耐腐蚀的金属材料,因其优异的性能在航空航天、汽车制造、电子设备等领域得到广泛应用。
而铝合金铸造作为一种常见的加工方法,在生产中也起着至关重要的作用。
为了规范铝合金铸造的生产过程,提高产品质量,我国制定了一系列的国家标准,以确保铝合金铸造产品的质量和安全性。
首先,铝合金铸造国家标准对原材料的要求进行了详细规定。
从铝合金的成分、材料的纯度、晶粒度等方面,都有明确的标准要求。
这些规定可以帮助生产企业选择合适的原材料,确保铸造产品的化学成分和物理性能符合要求。
其次,铝合金铸造国家标准对铸造工艺和设备进行了规范。
从铸造温度、压力、速度到冷却方式、模具设计等方面,都有具体的标准要求。
这些规定可以帮助铸造企业选择合适的工艺参数和设备,保证铸造产品的成型质量和表面光洁度。
此外,铝合金铸造国家标准还对产品质量进行了严格的检测要求。
从产品的尺寸精度、力学性能、表面缺陷、化学成分等方面,都有详细的检测方法和标准数值。
这些规定可以帮助生产企业进行有效的质量控制,确保铸造产品符合客户的要求和标准的要求。
总的来说,铝合金铸造国家标准的制定对于规范铸造生产、提高产品质量、保障产品安全至关重要。
企业应当严格遵守相关标准,加强对生产工艺和质量控制的管理,提高产品的竞争力和市场份额。
同时,相关部门也应当加强对铝合金铸造行业的监督和指导,促进行业的健康发展和技术进步。
总之,铝合金铸造国家标准的制定是我国铝合金铸造行业发展的重要保障,它不仅对企业的生产经营起着指导作用,也有利于提升整个行业的技术水平和竞争力。
希望铝合金铸造企业能够充分认识到国家标准的重要性,积极配合执行,共同推动铝合金铸造行业的发展。
铝合金铸件气孔标准
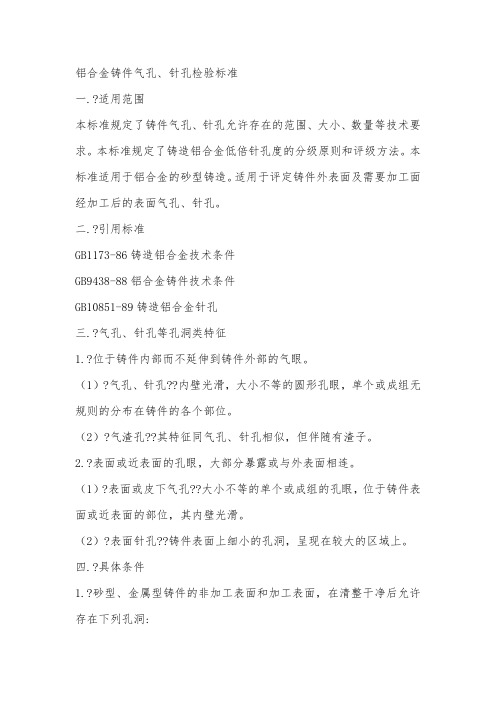
铝合金铸件气孔、针孔检验标准一.?适用范围本标准规定了铸件气孔、针孔允许存在的范围、大小、数量等技术要求。
本标准规定了铸造铝合金低倍针孔度的分级原则和评级方法。
本标准适用于铝合金的砂型铸造。
适用于评定铸件外表面及需要加工面经加工后的表面气孔、针孔。
二.?引用标准GB1173-86铸造铝合金技术条件GB9438-88铝合金铸件技术条件GB10851-89铸造铝合金针孔三.?气孔、针孔等孔洞类特征1.?位于铸件内部而不延伸到铸件外部的气眼。
(1)?气孔、针孔??内壁光滑,大小不等的圆形孔眼,单个或成组无规则的分布在铸件的各个部位。
(2)?气渣孔??其特征同气孔、针孔相似,但伴随有渣子。
2.?表面或近表面的孔眼,大部分暴露或与外表面相连。
(1)?表面或皮下气孔??大小不等的单个或成组的孔眼,位于铸件表面或近表面的部位,其内壁光滑。
(2)?表面针孔??铸件表面上细小的孔洞,呈现在较大的区域上。
四.?具体条件1.?砂型、金属型铸件的非加工表面和加工表面,在清整干净后允许存在下列孔洞:(1)?单个孔洞的最大直径不大于3mm,深度不超过壁厚1/3,在安装边上不超过壁厚的1/4,且不大于1.5mm,在上述缺陷的同一截面的反面对称部位不得有类似的缺陷。
(2)?成组孔洞??最大直径不大于2mm,深度不超过壁厚的1/3,且不大于1.5mm。
(3)?上述缺陷的数量及边距应符合表一规定表一非加工表面或加工表面总面积小于1000cm2单个孔洞成组孔洞在10cm×10cm单位面积上孔洞数不多于4个孔洞边距不小于10mm一个铸件的非加工表面或加工面上孔洞总数不多于6个,孔洞边缘距铸件或距内孔边缘的距离不小于孔洞最大直径的2倍以3cm×3cm单位面积为一组,其孔洞数不多于3个在一个铸件上组的数量不多于2组孔洞边缘距铸件边缘或距内孔边缘的距离不小于孔洞最大直径的2倍2.?液压、气压件的加工表面上,铸件以3级针孔作为验收基础,要求2级针孔占受检面积的25%以上,局部允许4级针孔,但一般不得超过受检面积的25%,当满足用户对致密性的技术要求时或对其它砂型、金属型铸件允许按低一级的针孔度验收。
- 1、下载文档前请自行甄别文档内容的完整性,平台不提供额外的编辑、内容补充、找答案等附加服务。
- 2、"仅部分预览"的文档,不可在线预览部分如存在完整性等问题,可反馈申请退款(可完整预览的文档不适用该条件!)。
- 3、如文档侵犯您的权益,请联系客服反馈,我们会尽快为您处理(人工客服工作时间:9:00-18:30)。
铝合金铸造件检验技术条件(试行)1 内容及适用范围本标准根据GB/T 1173-1995及GB/T 9438-1999的相关内容,规定了铝合金铸件的分类和铸件的外观质量、内在质量以及铸件修补等内容的技术要求与检验规则等。
本标准适用于我公司采用金属型铸造所生产的制动器上、下泵体等铸件(不含压力铸造)。
根据工作条件、用途以及在使用过程中如果损坏,所能造成的危害程度,将铸件分类如下:2 技术要求2.1 化学成分2.1.1合金的化学成分根据GB/T 1173-1995的规定,应符合表2-1及表2-2的规定。
2.1.2当使用杂质总和来表示杂质含量时,如无特殊规定,其中每一种未列出的元素含量不大于0.02%。
2.2 状态2.2.1铸件按表2-3的规定,呈铸态或热处理状态供应。
注:在保证合金机械性能前提下,可以不加铍(Be)。
2.3 机械性能2.3.1 每批铸件应按其类别检验机械性能。
2.3.2 合金及其铸件的机械性能应符合表2-3的规定。
2.4外观质量2.4.1铸件在进行表面粗糙度、表面缺陷、尺寸等外观质量检验之前,飞边、溢流口、隔皮等应清理干净、平整,但不可在非加工表面上留有明显的凿痕,且宽度不得超过2mm。
2.4.2铸件的表面粗糙度Ra为6.3μm以上。
2.4.3非加工表面的浇冒口,应清理到与铸件表面齐平;待加工表面的浇冒口残留量应不大于3mm。
2.4.4清除飞翅、夹砂等多肉类缺陷,铸件的内外表面由于型芯及顶杆的磨损所产生的飞边、毛刺应清除干净。
2.4.5根据顾客图样或技术文件的要求,铸件表面可进行喷砂处理。
2.4.6铸件上作为基准用的部位应平整,不允许存在任何凸起痕迹,装饰面上不允许有推杆痕迹(图样上注明)。
2.4.7非加工表面上,由于模具组合镶并或受分型面影响而形成的铸件表面高低不平差值不得超过0.3mm。
2.4. 8非加工表面上,不允许有超过表2-4(Ⅰ)级规定的花纹、麻面和有色斑点。
2.4.9铸件尺寸应符合图样的要求。
尺寸公差应符合表2-5的规定。
按CT6级选取。
有特殊要求时,应在图样上注明。
2.4.10铸件尺寸公差不包括由于拔模斜度而引起的尺寸增减,但必须保证铸件的最小极限尺寸。
2.4.11铸件壁厚公差一般可降一级选用。
2.4.12错型必须位于表2-5规定的公差值之内。
当需进一步限制错型值时,则应在图样上注明,其值从表2-5或表2-6中选取较小的值,且不得与表2-5中所列值相加。
2.4.13 成批和大量生产铸件的尺寸公差等级按表2-7的规定选取:2.4.14铸件非加工面的粗糙度由顾客在图样中规定。
2.4.15铸件上不允许有冷隔、裂纹、穿透性缺陷及严重的残缺类缺陷(浇不到、未浇满、机械损伤等)的存在。
2.4.16铸件待加工表面上,允许有经加工可去掉的任何缺陷。
2.4.17 在金属型铸件的非加工表面上,允许铸件有分型、顶杆及排气塞等痕迹。
但凸出表面不大于0.3mm或凹下表面不超过0.4mm,且布局合理协调。
2.4.18铸件表面的字母、数字、文字及花纹等应清晰、平整、美观、无缺漏现象。
2.4.19液压、气压件的金属型铸件的加工表面上,允许2级针孔,局部允许3级针孔,但一般不得超过受检面积的25%。
当满足顾客对致密性的技术要求时铸件允许按低一级的针孔度验收。
2.4.20螺纹孔内、螺丝旋入四个牙距之内不允许有缺陷。
四个牙距之外,是否允许有缺陷以及允许缺陷的大小、数量按图样规定。
2.5内部质量2.5.1 铸件内部针孔,当用低倍试验方法检验时,对Ⅰ类铸件或液压、气压件应按2级验收,允许局部有3级针孔,但不得超过受检面积的25%,Ⅱ类铸件按低一级针孔度验收。
2.5.2针孔等级评定:低倍检验按JB/T 7946-1999的规定进行,当有争议时按表2-8的规定:2.5.3铸件经机械加工后的表面不允许有缩松。
2.5.4铸件内部气孔、夹杂,当无特殊规定时,按下列要求验收:2.5.4.1单个气孔或夹杂的最大尺寸不大于3mm,且不超过壁厚的1/3,在安装边上不超过壁厚的1/4,在10cm×10cm面积上的数量不多于3个,边距不小于30mm。
2.5.4.2 尺寸小于0.5mm的单个气孔或夹杂不计。
2.5.4.3 气孔或夹杂距铸件边缘和内孔边缘的距离不小于夹杂或气孔最大尺寸的2倍。
2.5.4.4 上述缺陷所对应的(同一截面)表面,不得有类似缺陷。
2.5.5铸件内不允许有裂纹。
2.5.6铸件固溶处理不允许过烧。
2.6 铸件修补及矫正:2.6.1 可用打磨的方法清除任何缺陷,但打磨后的尺寸应符合铸件尺寸公差的要求。
2.6.2变形的铸件允许用机械方法矫正,矫正后全部检查有无裂纹。
2.6.3 除另有规定外,铸件可用焊补的方法修复。
2.6.4 当采用钨极氩弧焊焊补时,焊补面积、焊补最大深度应符合表2-9的规定。
注:1)焊补面积是指扩修后的面积;2)焊补面积小于2cm² 的焊区不计入焊补数。
2.6.5 同一处焊补不超过三次,焊区边缘间距(包括反面的焊区)不得小于两相邻焊区直径之和。
2.6.6 凡以热处理状态供应的铸件,焊补后需按原状态进行热处理,热处理后的铸件按2.3和3.2条检验机械性能。
当氩弧焊区面积小于2cm²,焊区间距不小于100 mm,可不经热处理。
但在一个铸件上,不得多于五处。
2.6.7焊补区不得有裂纹、分层、未焊透,在任何一焊区中允许有最大直径不大于2 mm,且不超过壁厚的1/3的气孔或夹杂三个,边距不小于10 mm。
直径小于0.5 mm的分散气孔或夹杂不计。
2.6.8在腐蚀介质或气氛中工作的铸件,焊补时不允许使用焊药。
2.6.9除另有规定外,允许对要求致密性的铸件进行渗补处理。
3 试验方法及检验规则3.1化学成分3.1.1 合金的化学成分检验按GB 1198《铝化学分析方法》进行,在保证分析精度的条件下,允许使用其他方法。
3.1.2 对Ⅰ、Ⅱ类铸件,根据其重要程度,每月作为一个批次,每批随机抽查五个熔炼炉次,对主要元素和主要杂质Fe进行分析,其余杂质仅在有必要时或工艺检验时进行分析。
3.1.3对于不承受载荷或承受轻微载荷且没有特殊物理性能和使用要求的Ⅲ类铸件,不进行化学成分分析。
3.1.4 在抽查的一个熔炼炉次中,在全部铸件浇注的持续时间之半时浇注化学成分试样。
亦允许在全部铸件浇注之后浇注化学成分试样。
3.1.5 化学成分试样每炉允许送检两次,只要其中一个试样符合表2-1和表2-2的规定时,则该炉合金化学成分合格。
当抽查的该批次中所有炉次合金化学成分均合格,则该批次合金化学成分合格。
当抽查的单个炉次两个化学试样分析结果都不合格,则该熔炼炉次合金化学成分不合格。
此时应对造成的原因进行分析、纠正,并对存在类似问题的所有炉次进行分析,分析结果不合格的,不合格炉次铸件报废。
同时,应加大比例对该批其它炉次合金进行抽查,再次出现一个或以上炉次化学成分不合格时,则应对该批次所有炉次合金进行化学成分分析。
不合格的炉次作报废处理。
3.1.6化学成分试样也可取自铸件。
但必须符合3.1.4条的规定。
3.1.7配料方法或系数调整时,必须对调整后的前两炉合金进行成分分析。
当两炉合金的化学成分均合格后,方可按批次抽检。
3.2机械性能3.2.1各种不同铸造方法生产的铸件,其机械性能的检验,以其铸型材料为判据。
金属型及金属型低压铸造的铸件,按金属型单铸试样检验。
单铸抗拉试样及铸件切取之本体试样应符合下面的规定:3.2.1.1 单铸试样直径为12±0.25 mm,标距为直径的5倍。
3.2.1.2 试样亦可采用同炉铸件上切取本体加工,试样直径不小于6 mm,标距为直径的5倍。
3.2.2 采用同一热处理工艺的全部铸件,可视为一个批次进行检验。
每一热处理炉次铸件的机械性能,以硬度(HBS)为验收依据,硬度检验在铸件本体上进行,其部位由顾客在图样中规定,如无明确规定,则在铸件需要保证特定硬度的部位检验硬度。
硬度检查按技术要求和表2-3的规定进行。
每一热处理炉次抽查上、中、下三层各一件,如有一件不合格,抽查数量加倍,再不合格允许重复热处理,但一般不超过两次。
3.2.3 铸态供货的铸件,以一个熔炼炉次为一个批次进行检验。
在生产稳定的情况下(包括:原材料、熔炼工艺、试验方法、检验等工序的稳定),在一个班次八小时之内浇注的,不同炉次的同一合金,可视为一个批次进行检验。
其机械性能以硬度(HBS)为验收依据。
每一批次随机抽取三件检查,如有一件不合格,抽查数量加倍,再不合格允许对铸件进行适当的热处理,其硬度仍按原铸态指标验收。
3.2.4 在硬度检验合格的情况下,每月生产的铸件作为一个批次,每批随机抽查五个熔炼炉次,检查其抗拉强度和伸长率。
3.2.5 铸态的抗拉强度和伸长率试样每批首次每一抽查炉次送检一根单铸试样进行测定。
如符合表2-3规定,则该批合金铸态抗拉强度和伸长率合格。
如不符合表2-3规定,允许对不合格炉次每炉再取两根试样重新送检,如每炉的两根试样都合格,则该批合金铸态抗拉强度和伸长率合格,否则该抽查炉次合金铸态抗拉强度和伸长率不合格。
此时应加大抽查比例,再不合格时应对每一熔炼炉次的抗拉强度和伸长率作检查。
对检查结果不合格炉次的铸件允许进行适当的热处理,其机械性能仍按原铸态指标验收。
3.2.6 铸件热处理状态抗拉强度和伸长率试样送检方法按3.2.5条进行。
如仍不合格,允许对不合格热处理炉次铸件重复热处理,但一般不超过两次。
3.2.7 单铸试样之热处理必须与同炉浇注的铸件,采用同一热处理工艺同炉进行。
3.2.8单铸试样带铸皮进行检验。
亦允许车削除去铸皮,此时试样直径为10±0.1 mm。
3.2.9当肉眼发现单铸试样存在铸造缺陷时或由于试验本身故障造成检验结果不合格的,可以不计入检验次数中,更换试样重新送检。
3.2.10 Ⅰ类铸件按以上规定,不合格则该炉铸件报废,Ⅱ、Ⅲ类铸件按以上规定检验仍不合格,则从该炉次中有代表性的铸件上切取试样检验。
检验方法同上,如仍不合格,则该炉次铸件报废。
3.2.11从铸件上切取试样,每个取样部位,一般应切取三根试样。
对于Ⅰ类铸件指定部位的试样,其抗拉强度和伸长率的平均值分别不得小于表3中规定值的80%和50%。
允许其中一根试样的抗拉强度和伸长率小于平均值。
但不得小于规定值的70%和40%。
对于Ⅰ类铸件的非指定部位和Ⅱ类铸件的切取试样,其抗拉强度和伸长率的平均值分别不得小于规定值的75%和50%。
允许其中一根试样的抗拉强度和伸长率小于平均值。
但不得小于规定值的65%和40%。
当Ⅲ类铸件切取试样本体时,其抗拉强度和伸长率不得小于规定值的75%和25%。
3.2.12当铸件的一个取样部位不能切取三根试样时,其抗拉强度和伸长率均不得小于上条中规定的平均值。