视频内窥设备辅助下的航空发动机压气机转子叶片原位修复技术研究
内窥检测技术在MA600飞机维修中的应用

内窥检测技术在MA600飞机维修中的应用摘要:内窥检查是航空器视情维修的五大工具之一,已被广泛应用到安装涡轮发动机的运输飞机的维修工作中,并发挥着越来越重要的作用。
该文以国产MA600飞机为例,介绍了内窥检测在该机型的应用范围和检测重点。
使维修人员能够熟练掌握内窥检测的方法,进而提高MA600飞机维修质量,保证飞行安全。
关键词:内窥检查视情维修飞行安全内窥检查又被称为孔探检查,是指借助于专用的光电仪器(工业内窥镜)对航空器内部肉眼无法直接接近的区域进行检查,属于无损探伤行业中的一种新兴的目视检查方法。
目前民航飞机维修已逐步从定期维修向视情维修发展,而内窥检查作为视情维修的五大工具之一,已被广泛应用到安装涡轮发动机的运输飞机的维修工作中,并发挥着越来越重要的作用。
例如中国民航飞行学院新引进用于飞行训练的两架国产MA600支线客机,在其发动机手册中就明确提出了定期进行内窥检查的要求。
但由于我国通用航空领域内的飞机以往以小型活塞发动机飞机为主,而这些厂家的维修手册中无定期孔探的检查要求,再加之掌握内窥技术不仅需要操作人员熟悉所检测航空器特别是发动机的内部结构,还需要具有丰富的内窥镜检测操作经验和对检测结果进行分析和判断的能力。
因此对于绝大数通航维修人员来说内窥检测比较陌生,对内窥检测技术的掌握还有待加强。
为便于通用航空维修人员能够尽快地掌握这一先进技术,并将其应用到维修工作中来,笔者就以MA600飞机为例,介绍一下内窥检测在该机型的应用范围和检测重点。
1应用范围按内窥检查在MA600飞机上的应用范围和重要程度,MA600飞机内窥检测可以分为发动机内窥检测、飞机结构内窥检测、内窥镜打磨修理、利用内窥镜取出内部异物和内窥镜无损检测五大部分。
1.1发动机内窥检测是指在不分解发动机的条件下使用内窥镜设备通过专用的内窥镜接近孔,拆除点火电嘴、燃油喷嘴后的孔洞或放气活门等开口,检查发动机内部的硬件状况。
发动机组成:MA600飞机上安装的PW127J发动机为加拿大普惠公司生产的三转子涡轮螺旋桨发动机,其核心机由1级低压压气机、1级高压压气机,燃烧室、1级高压涡轮、1级低压涡轮和2级动力涡轮组成。
航空发动机压气机叶片检修技术
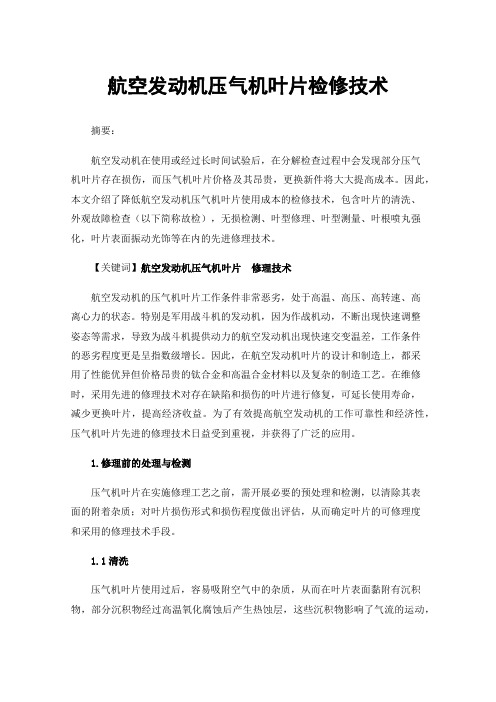
航空发动机压气机叶片检修技术摘要:航空发动机在使用或经过长时间试验后,在分解检查过程中会发现部分压气机叶片存在损伤,而压气机叶片价格及其昂贵,更换新件将大大提高成本。
因此,本文介绍了降低航空发动机压气机叶片使用成本的检修技术,包含叶片的清洗、外观故障检查(以下简称故检),无损检测、叶型修理、叶型测量、叶根喷丸强化,叶片表面振动光饰等在内的先进修理技术。
【关键词】航空发动机压气机叶片修理技术航空发动机的压气机叶片工作条件非常恶劣,处于高温、高压、高转速、高离心力的状态。
特别是军用战斗机的发动机,因为作战机动,不断出现快速调整姿态等需求,导致为战斗机提供动力的航空发动机出现快速交变温差,工作条件的恶劣程度更是呈指数级增长。
因此,在航空发动机叶片的设计和制造上,都采用了性能优异但价格昂贵的钛合金和高温合金材料以及复杂的制造工艺。
在维修时,采用先进的修理技术对存在缺陷和损伤的叶片进行修复,可延长使用寿命,减少更换叶片,提高经济收益。
为了有效提高航空发动机的工作可靠性和经济性,压气机叶片先进的修理技术日益受到重视,并获得了广泛的应用。
1.修理前的处理与检测压气机叶片在实施修理工艺之前,需开展必要的预处理和检测,以清除其表面的附着杂质;对叶片损伤形式和损伤程度做出评估,从而确定叶片的可修理度和采用的修理技术手段。
1.1清洗压气机叶片使用过后,容易吸附空气中的杂质,从而在叶片表面黏附有沉积物,部分沉积物经过高温氧化腐蚀后产生热蚀层,这些沉积物影响了气流的运动,导致压气机的效率下降,同时沉积物也掩盖了叶片表面的损伤,不便于检测。
因此,叶片在进行检测和修理前,要清除沉积物。
1.2故检叶片修理前,需针对其外部的损伤类型,损伤程度等进行故检,以判断是否可以继续使用,及确定相应的修理方案。
故检是维修过程的重要工序,整个发动机的制造(维修)成本控制,很大部分来自故检工序,因此众多维修厂都对故检工作极为重视。
1.3无损检测无损检测是在不损害或不影响叶片使用性能,不伤害叶片内部组织的前提下,利用叶片内部结构异常或缺陷存在引起的热、声、光、电、磁等反应的变化,以物理或化学方法为手段,对叶片内部及表面的结构、状态及缺陷的类型、数量、形状、性质、位置、尺寸、分布及其变化进行检查和测试的方法。
航空发动机压气机叶片型面检测技术

中,控制系统采用上控机,以TR008
数控系统平台为基础进行开发,实现
了测量仪的运动控制、数据采集、光
栅准确计数等功能。TR008是清华 大学精仪系制造工程研究所正存开 发和完善的普及型数控系统平台,其 软件争郜由c程序设计语言实现。 处理系统采用PC机,以基于Win一 dows系统的MATLAB作为软件开 发1二具,以实现测量数据的处理、曲 线拟合造型、参数辨识等功能。两台 不同系统计算机之间的数据传输采 用了建立无盘工作站的方法来实现,
3陈凯云,叶佩青,俞学兰,等·航空压
主嚣!盖i雷::型苎i竺研究·仪器仪表
4张国雄.三坐标测量机.天津:天津 大学出版社,1999.113~117(责编晓霸)
48航牵翩造技术·2007年第1l期
万方数据
青海大学机械系 清华大学精仪系
俞学兰 叶佩青
叶片是关系到发动机性能的高负荷零件。严格控制叶 片的制造质量,是叶片制造中的关键问题。因此,叶片的检 测技术非常重要,在叶片制造的总工作量中叶片检测工作 量占相当大的EE例。
俞学兰 硕士。青海大学机械系讲师,主
要研究方向为数控加工。
叶片是关系到发动机性能的高 负荷零件。严格控制叶片的制造质 量,是叶片制造中的关键问题。因此, 叶片的检测技术:{}常重要,在叶片制 造的总工作量中叶片检测工作量占 相当大的比例“1。
即为理想标准叶片; 失真或无法计算的现象,而激光测量
制造误差很小时即 仪n J以真实地反映叶片边缘的形状。
为样板叶片,此时制 表2从测量的精度、速度以及可靠性
圈3二维图形显示界面
造误差对测量结果 等方面将四坐标激光测量仪与三坐
的影响不明显。在 标测量机两种测量方式进行叶片测
密转台,配合非接触式激光测头进行 试验巾选用某型样板叶片对测量结 量的结果进行了比较。
航空发动机叶片的无损检测毕业设计说明书
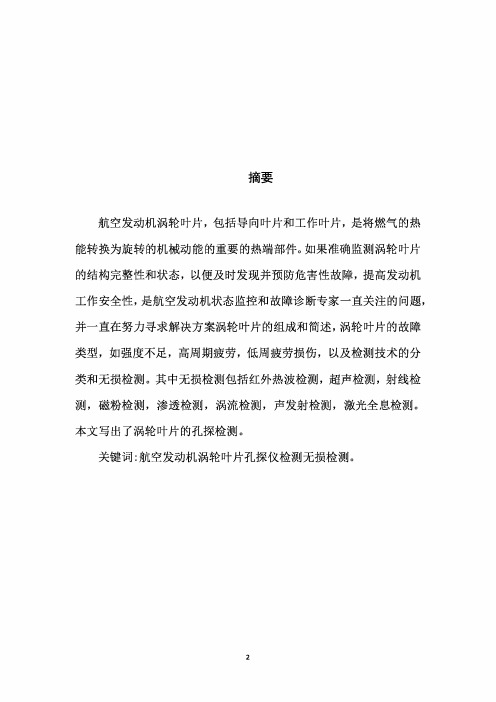
摘要航空发动机涡轮叶片,包括导向叶片和工作叶片,是将燃气的热能转换为旋转的机械动能的重要的热端部件。
如果准确监测涡轮叶片的结构完整性和状态,以便及时发现并预防危害性故障,提高发动机工作安全性,是航空发动机状态监控和故障诊断专家一直关注的问题,并一直在努力寻求解决方案涡轮叶片的组成和简述,涡轮叶片的故障类型,如强度不足,高周期疲劳,低周疲劳损伤,以及检测技术的分类和无损检测。
其中无损检测包括红外热波检测,超声检测,射线检测,磁粉检测,渗透检测,涡流检测,声发射检测,激光全息检测。
本文写出了涡轮叶片的孔探检测。
关键词:航空发动机涡轮叶片孔探仪检测无损检测。
目录摘要 (2)绪论 (1)第一章涡轮叶片的简述 (2)1.1涡轮的工作叶片 (2)1.2导向叶片 (2)第二章故障类型 (3)2.1强度不足及其故障模式 (3)2.2高周期疲劳损伤及其故障模式 (3)2.3低周疲劳损伤及故阵模式 (3)2.4涡轮叶片的常见故障及概率 (3)2.5注意事项 (5)第三章机上孔探检测 (6)3.1涡轮叶片的机上孔探检查 (6)3.2涡轮叶片的不同部位孔探检查 (6)3.3孔探技术的发展和实际应用的需求 (7)3.4修理车间检测前的清洗预处理 (7)3.5叶片完整性检查 (8)3.6探孔注意事项 (8)第四章涡轮叶片孔探案例分析 (9)4.1高压涡轮叶片断裂 (9)4.2典型案例分析 (10)4.3叶片断裂的原因 (11)4.4叶片修理与孔探检测 (13)4.5总结 (14)参考资料 (15)致谢 (16)航空发动机涡轮叶片无损检测技术绪论航空发动机涡轮叶片,包括导向叶片和工作叶片,是将燃气的热能转换为旋转的机械动能的重要的热端部件。
基于提高推重比和单位推力的需要,涡轮前燃气温度日益提高,目前国外新型的航空燃气涡轮发动机涡轮前的温度已达到1700K以上。
涡轮叶片在高压腐蚀性燃气的神击下高速旋转,除承受巨大的拉应力外,还承受频率、幅值变化都很大的交变拉应力和扭转应力,此外还存在高温氧化、热腐蚀和磨损问题。
航空发动机涡轮叶片叶尖损伤修复自适应加工技术研究与应用

摘要:损伤的涡轮叶片修复对航空发动机的检修及延寿具有重要意义。综述了某镣基铸造高温合金涡轮
工作叶片修复技术的研究进展,重点介绍了叶尖部位自适应机械加工的修复方法 ,深入阐述了试验
加工过程与验证结果,并对涡轮叶片修复技术的发展前景进行了展望。
关键词:航空发动机;涡轮工作叶片;叶尖修复;自适应加工;数控抛光
WU Zhixin①,ANGGEI Lama①,ZHANG Yun®,LIU Dejian③ (①AECC Shenyang Liming Aero-Engine Co., Ltd., Shenyang 110043, CHN ;②North China University
of Technology, Beijing 100041, CHN;③Beihang University, Beijing 100191, CHN)
用§9“刻出滋**和雷
2021年第7期
料及飞机部装零部件等的自适应制造及维修,在设备 支持上支持铳削、磨削、激光熔覆、激光打孔、机器人打 磨、等离子处理和增材等应用。 2.1自适应加工技术路线
针对涡轮工作叶片叶尖修复工艺的难点,即:每片 修复的叶片的变形不一致,装夹的位置、角向不同,原 有精铸精度的问题,诸如以上的实际问题都可以通过 自适应加工技术快速地在线检测每一件待加工零件或 部位,了解实际形状及位置分布,然后系统通过测量的 数据,重新构造与设计相符的目标数模,生成唯一的个 性化路径轨迹以满足产品制造,最终与设计、实物 相符。
上述研究表明,航空发动机叶片修复是国内外航 空领域研究的一个热点。在修复的机加工领域,重点 是实现修复区域与非破损区域之间的光滑搭接,以及 修复后的高精度成形。因此,本文在上述修复研究的 基础上,以破损涡轮工作叶片为例,开展叶尖损伤修复 的自适应加工技术应用研究,保证修复后叶片的加工 区域与非加工区域能实现光滑过渡搭接,且整体修复 型面满足修复叶片的最终公差要求。
基于航空发动机产品需求的压气机技术研究
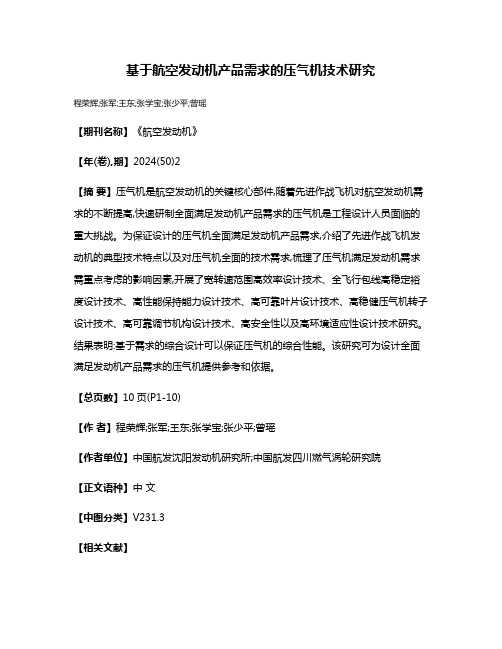
基于航空发动机产品需求的压气机技术研究
程荣辉;张军;王东;张学宝;张少平;曾瑶
【期刊名称】《航空发动机》
【年(卷),期】2024(50)2
【摘要】压气机是航空发动机的关键核心部件,随着先进作战飞机对航空发动机需求的不断提高,快速研制全面满足发动机产品需求的压气机是工程设计人员面临的重大挑战。
为保证设计的压气机全面满足发动机产品需求,介绍了先进作战飞机发动机的典型技术特点以及对压气机全面的技术需求,梳理了压气机满足发动机需求需重点考虑的影响因素,开展了宽转速范围高效率设计技术、全飞行包线高稳定裕度设计技术、高性能保持能力设计技术、高可靠叶片设计技术、高稳健压气机转子设计技术、高可靠调节机构设计技术、高安全性以及高环境适应性设计技术研究。
结果表明:基于需求的综合设计可以保证压气机的综合性能。
该研究可为设计全面满足发动机产品需求的压气机提供参考和依据。
【总页数】10页(P1-10)
【作者】程荣辉;张军;王东;张学宝;张少平;曾瑶
【作者单位】中国航发沈阳发动机研究所;中国航发四川燃气涡轮研究院
【正文语种】中文
【中图分类】V231.3
【相关文献】
1.某航空发动机压气机转子叶片进、排气边处的加工技术研究
2.视频内窥设备辅助下的航空发动机压气机转子叶片原位修复技术研究
3.航空发动机压气机叶片表面清洗技术研究
4.基于多层感知机的航空发动机压气机盘应力和温度预测
因版权原因,仅展示原文概要,查看原文内容请购买。
科技成果——燃气轮机叶片及热端部件修复再制造技术

科技成果——燃气轮机叶片及热端部件修复再制造技术所属行业装备制造适用范围燃气轮机修复成果简介1、技术原理燃机是一种高效、节能、低污染的动力设备,广泛地应用于地面发电、能源动力、航空航天等领域。
随着燃机性能的提高,其热端部件所使用的材料性能也不断提高,以往可以用常规焊接工艺修缮的工件现已经不能采用,而如今的热端部件的制造仅仅掌握在国外的几家大型公司,其价值昂贵,往往一台份叶片的价格近5000万美元(9E、9F等机组),国产叶片也近4000万人民币所以叶片的损伤是目前国内使用单位最大的经济损失与压力,这样就急需要开发研制新方法、新工艺来解决。
激光作为一种特种能量源,发展激光辐照下的粉末熔铸生长和激光显微积分焊以及激光微弧沉积复合修复工艺。
其中粉末冶金法是公司在激光修复技术之外的一项重大突破。
粉末冶金过程为:粉末-成形-烧结,通过粉末组成的优化选择可实现工件的近、等强度的无损求原修复;通过可塑粉末体随工件基体几何结构抹塑成形,可实现工件的大面积、大孔洞、大间隙和较大厚度的无损求原修复。
对于高温合金,尤其是含Al+Ti量高的镍基高温合金,由于其难熔焊修复的问题,采用粉末冶金修复再制造技术应是十分有意义的,在发动机叶片及热端部件修复再制造中具有广阔的应用前景。
2、关键技术与装备(1)针对不同叶片片体基材烧结界面的冶金化程度即双金属界面液态相容性;(2)针对大缺陷处的烧结如何解决由于金属收缩比不同产生的裂纹;(3)控制烧结真空度与烧结温度,对空心型腔结构烧结时不会发生烧结粉末熔化点时的流动,也可称为仿型烧结技术;(4)烧结后烧结区的强度应不低于本体强度的70%,性能要达到基体性能的90%。
装备:TFL-H6KWCO2激光器一台成套设备;ZKSX-DC-02、ZKSX3004固态激光器二台;YAG500W、SF-1GX-500B激光器二台;DS-300电弧喷涂机、N-800等离子喷涂机各一台;等离子堆焊机一台;VHB-181830H、VHB-6612H多用途真空热处理炉二台;多功能微弧增材制造机(专利产品)若干台。
航空发动机涡轮叶片精密成形技术分析
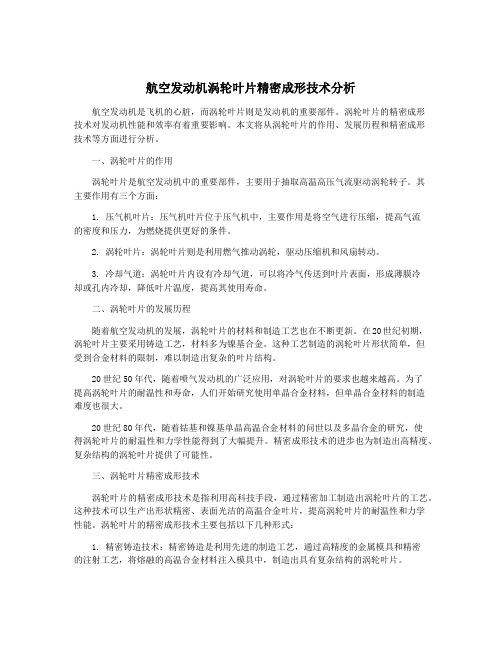
航空发动机涡轮叶片精密成形技术分析航空发动机是飞机的心脏,而涡轮叶片则是发动机的重要部件。
涡轮叶片的精密成形技术对发动机性能和效率有着重要影响。
本文将从涡轮叶片的作用、发展历程和精密成形技术等方面进行分析。
一、涡轮叶片的作用涡轮叶片是航空发动机中的重要部件,主要用于抽取高温高压气流驱动涡轮转子。
其主要作用有三个方面:1. 压气机叶片:压气机叶片位于压气机中,主要作用是将空气进行压缩,提高气流的密度和压力,为燃烧提供更好的条件。
2. 涡轮叶片:涡轮叶片则是利用燃气推动涡轮,驱动压缩机和风扇转动。
3. 冷却气道:涡轮叶片内设有冷却气道,可以将冷气传送到叶片表面,形成薄膜冷却或孔内冷却,降低叶片温度,提高其使用寿命。
二、涡轮叶片的发展历程随着航空发动机的发展,涡轮叶片的材料和制造工艺也在不断更新。
在20世纪初期,涡轮叶片主要采用铸造工艺,材料多为镍基合金。
这种工艺制造的涡轮叶片形状简单,但受到合金材料的限制,难以制造出复杂的叶片结构。
20世纪50年代,随着喷气发动机的广泛应用,对涡轮叶片的要求也越来越高。
为了提高涡轮叶片的耐温性和寿命,人们开始研究使用单晶合金材料,但单晶合金材料的制造难度也很大。
20世纪80年代,随着钴基和镍基单晶高温合金材料的问世以及多晶合金的研究,使得涡轮叶片的耐温性和力学性能得到了大幅提升。
精密成形技术的进步也为制造出高精度、复杂结构的涡轮叶片提供了可能性。
三、涡轮叶片精密成形技术涡轮叶片的精密成形技术是指利用高科技手段,通过精密加工制造出涡轮叶片的工艺。
这种技术可以生产出形状精密、表面光洁的高温合金叶片,提高涡轮叶片的耐温性和力学性能。
涡轮叶片的精密成形技术主要包括以下几种形式:1. 精密铸造技术:精密铸造是利用先进的制造工艺,通过高精度的金属模具和精密的注射工艺,将熔融的高温合金材料注入模具中,制造出具有复杂结构的涡轮叶片。
2. 精密锻造技术:精密锻造是通过将金属加热至塑性变形温度,再施加压力,使金属产生塑性变形,从而制造出精密的涡轮叶片。
探析航空发动机叶片叶尖间隙检测技术
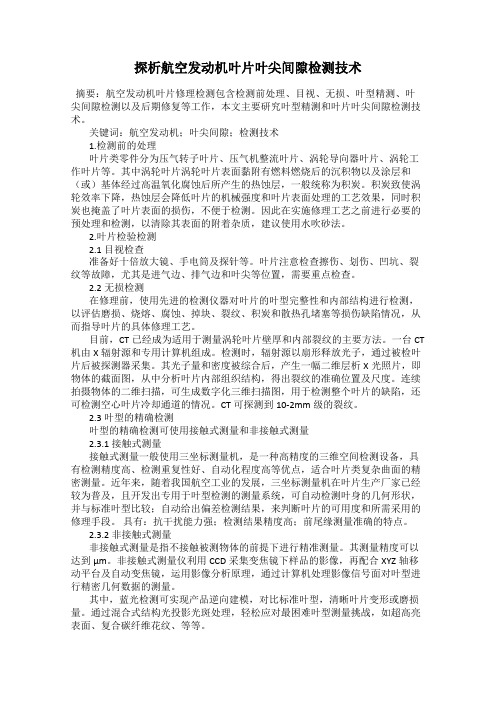
探析航空发动机叶片叶尖间隙检测技术摘要:航空发动机叶片修理检测包含检测前处理、目视、无损、叶型精测、叶尖间隙检测以及后期修复等工作,本文主要研究叶型精测和叶片叶尖间隙检测技术。
关键词:航空发动机;叶尖间隙;检测技术1.检测前的处理叶片类零件分为压气转子叶片、压气机整流叶片、涡轮导向器叶片、涡轮工作叶片等。
其中涡轮叶片涡轮叶片表面黏附有燃料燃烧后的沉积物以及涂层和(或)基体经过高温氧化腐蚀后所产生的热蚀层,一般统称为积炭。
积炭致使涡轮效率下降,热蚀层会降低叶片的机械强度和叶片表面处理的工艺效果,同时积炭也掩盖了叶片表面的损伤,不便于检测。
因此在实施修理工艺之前进行必要的预处理和检测,以清除其表面的附着杂质,建议使用水吹砂法。
2.叶片检验检测2.1 目视检查准备好十倍放大镜、手电筒及探针等。
叶片注意检查擦伤、划伤、凹坑、裂纹等故障,尤其是进气边、排气边和叶尖等位置,需要重点检查。
2.2无损检测在修理前,使用先进的检测仪器对叶片的叶型完整性和内部结构进行检测,以评估磨损、烧熔、腐蚀、掉块、裂纹、积炭和散热孔堵塞等损伤缺陷情况,从而指导叶片的具体修理工艺。
目前,CT已经成为适用于测量涡轮叶片壁厚和内部裂纹的主要方法。
一台CT 机由X辐射源和专用计算机组成。
检测时,辐射源以扇形释放光子,通过被检叶片后被探测器采集。
其光子量和密度被综合后,产生一幅二维层析X光照片,即物体的截面图,从中分析叶片内部组织结构,得出裂纹的准确位置及尺度。
连续拍摄物体的二维扫描,可生成数字化三维扫描图,用于检测整个叶片的缺陷,还可检测空心叶片冷却通道的情况。
CT可探测到10-2mm级的裂纹。
2.3 叶型的精确检测叶型的精确检测可使用接触式测量和非接触式测量2.3.1 接触式测量接触式测量一般使用三坐标测量机,是一种高精度的三维空间检测设备,具有检测精度高、检测重复性好、自动化程度高等优点,适合叶片类复杂曲面的精密测量。
近年来,随着我国航空工业的发展,三坐标测量机在叶片生产厂家已经较为普及,且开发出专用于叶型检测的测量系统,可自动检测叶身的几何形状,并与标准叶型比较;自动给出偏差检测结果,来判断叶片的可用度和所需采用的修理手段。
航空发动机常见孔探检测路径的研究

航空发动机常见孔探检测路径的研究陈裕芹【期刊名称】《内江科技》【年(卷),期】2013(034)010【总页数】2页(P114-115)【作者】陈裕芹【作者单位】广州民航职业技术学院【正文语种】中文由于航空发动机各部位内部结构的复杂性,以及各部位孔探检查时所采用的设备的不同,而使得不同型发动机及其不同部位有不同的孔探检查路径。
对于这些不同的孔探路径的总结与掌握,对航空发动机孔探初学人员和工作人员具有很好的指导意义。
航空发动机是飞机的心脏,除了给飞机提供动力之外,还给飞机的许多重要系统提供动力或气源。
因此,它的健康状况直接影响到飞机的飞行安全。
发动机健康状况的检查主要是通过对其进行孔探检查。
孔探是指利用发动机壳体上的孔探口,在不分解发动机的情况下,用孔探仪对发动机进行可视检查。
而且,孔探越来越成为节省发动机维修成本和其日常监控的有效途径。
航空发动机中,43%的故障由孔探发现,而且根据波音公司提供的资料表明,在被拆下的发动机中90%以上是根据孔探检查出的[1]。
由此可见,孔探工作对于航空发动机的健康管理,对于飞行安全都起着非常重要的作用。
而在航空发动机的孔探工作中,可以使用硬杆镜或者柔性镜进行,而且发动机各部位的结构不同,因此不同部位有不同的孔探路径与检查特点。
对这些常见的不同孔探路径的了解和掌握,对孔探人员做好各型航空发动机的孔探工作有很好的指导作用。
航空发动机需要孔探的位置主要是热端部件,如燃烧室和涡轮。
波音维修方案中的孔探检查工作,主要集中在高压涡轮转子叶片和进口导向叶片、燃烧室以及低压涡轮进口导向叶片。
因为这些部件所处的环境恶劣,在高温、高压、高转速的环境下,发动机的部件会逐渐老化,致使整个发动机的性能衰退,EGT裕度下降[2]。
因此,这些部位都有专门设计用来孔探检查的孔探口。
除此之外,对于在评判鸟击后对发动机压气机的损伤程度,在压气机一般也设计有孔探口。
除了专用的孔探口之外,在发现缺陷后需要全面检查时,也会打开不常用的一些孔探口,如点火嘴安装座、燃油喷嘴安装座、引气口等等。
航空发动机涡轮转子叶片失效原因分析

航空发动机涡轮转子叶片失效原因分析航空发动机是现代航空工业的核心技术之一,其性能的提升和可靠性的保障对于飞行安全和航空运输运营的重要性自然不言而喻。
当前,随着航空工业和科技的不断发展,航空发动机的技术含量日益增加,其恶劣工作环境和高要求的性能指标也让其面临着更加复杂和严峻的挑战。
航空发动机涡轮转子叶片作为发动机的核心组成部件,其失效原因的分析和研究一直是航空工程技术的热门话题。
本文将从航空发动机的结构和工作原理入手,探究航空发动机涡轮转子叶片失效的原因,并查阅相关文献和实验数据,深入探讨其解决方案和工程实践的应用情况。
一、航空发动机涡轮转子叶片的结构和工作原理航空发动机的涡轮转子是由多片叶片组成的,每片叶片的形状和尺寸都是高度精密设计和制造的。
叶片的主要功能是将高温高压气体能转化为高速旋转的机械能,驱动着气轮机、压气机和其他发动机组件的运转。
叶片的形状、材料和数量等参数都对其性能和失效风险产生着直接的影响。
在工作过程中,叶片不断受到气体的高温高压冲击和旋转惯性力的影响,其表面和内部的应力分布和温度场变化相当复杂,容易发生弹性、塑性、蠕变和损伤等失效模式。
降低叶片失效和延长使用寿命是航空发动机设计和维护的重要任务,需要对其失效机理进行深入的分析和探讨。
二、航空发动机涡轮转子叶片失效原因分析在航空工程实践中,航空发动机涡轮转子叶片的失效模式主要包括疲劳断裂、高温蠕变、氧化和腐蚀等。
这些失效模式的共同点是对叶片材料和结构造成了不同形式的损伤和变形,导致了其性能和寿命的降低。
1. 疲劳断裂疲劳断裂是叶片失效的常见模式,主要由于叶片在高速旋转和高温高压的气流作用下,不断受到往复应力的影响,导致材料的微小裂纹和变形,最终致使叶片断裂。
疲劳断裂的特点是无法预测和发现裂纹的位置和大小,需要在实验室和现场进行非破坏性检测和监测。
航空工程技术的发展和实践中,通过改进叶片材料、加强制造工艺和提高质量管理水平,疲劳断裂的风险得到了一定程度的缓解,但仍需进一步加强研究和监测。
发动机孔探检查过程中的风险管理

发动机孔探检查过程中的风险管理范海清(深圳航空有限责任公司 维修工程部)摘要:笔者根据多年的工作经验,对发动机孔探检查过程中可能存在的风险进行归纳汇总,通过实例和图片说明控制风险的必要性,并给出缓解风险的措施以供参考。
关键词:内窥镜 孔探检查 风险管理 危险源由于视频内窥镜有诸多优点,例如有拍照、录像、测量等功能,越来越受到飞机维修单位的青睐,成为发动机孔探检查的得力工具。
但是事物都是有两面性的,视频内窥镜也有弱点,如在使用过程中处理不当就可能导致严重的后果和巨大经济损失。
据了解,国内外多家航空公司发生过孔探设备损伤、内窥镜镜头掉落或卡阻在发动机内的情形,甚至已有公司因此而更换发动机,本文将通过风险管理的模式查找视频内窥镜在发动机孔探检查过程中的危险源,并提出缓解措施,以期将风险控制在可接受的水平内,达到安全维修的目的。
一、 危险源识别虽然航空发动机的型号和生产厂家很多,但是对于发动机的核心机来说,都是大同小异的,都有压气机、燃烧室、涡轮等部分,孔探检查也主要围绕这些高转动、高振动、高温区域进行,危险源通常也和这些部位相关。
1、危险源的范围包括以下几方面:1) 人的因素,即孔探人员在操作过程中的失误或错误观点。
孔探员如对孔探设备使用不够熟练、对检查部位了解的不充分、对检查工卡理解的不透彻,都可能出现人为失误。
2) 物的因素,即视频内窥镜存在磨损、老化、故障等客观现象,如维护、修理的不及时,就可能造成设备受损或发生意外事件。
3) 环境的因素,即使用视频内窥镜的环境是否存在潜在的危险源,例如冰、霜、雨、雪、风等自然环境。
如没有严格遵守视频内窥镜对环境温度的要求,温度过高或过低都可能造成损伤。
4) 管理的因素,即对孔探人员的培训、复训、授权、专职、兼职等。
如没有建立孔探员的培训、复训等制度,孔探人员就无法学到足够技能以及新方法、新知识,无法一直胜任孔探工作。
2、危险源识别的渠道1) 被动识别,即从已经发生的孔探设备损伤事件中寻找,可以是本公司的,也可以是行业内的事件。
航空发动机转子动平衡方法探究

航空发动机转子动平衡方法探究摘要:当航空发动机转子处于高速运转状态时,转子质心将会偏离旋转中心,导致发动机振动。
如果发动机振动来源于质量不平衡,就会降低发动机的性能,严重者使发动机零件受损,甚至是导致发动机停转。
面对这种现象,就需要对发动机进行维护,也就是让发动机转子动平衡,即用平衡机将转子的不平衡度测量配平,使转子的不平衡量相对趋于稳定水平。
鉴于此,本文立足于航空发动机转子动平衡概述,围绕动平衡方法展开如下探讨。
关键词:航空发动机;转子动平衡;振动;平衡方法引言如果航空发动机转子系统在处于高温、高速以及高压状态下的时候,很容易出现点变形,从而达到发动机整机振动,严重者还会影响发动机的正常使用。
通过分析航空发动机转子动平衡不平衡的原因,发现航空发动机转子动平衡方法的使用存在着一定的缺陷,在此基础之上,优化改进平衡方法,并且通过分析计算工装误差的方法,能够有效解决转子动平衡振动问题。
1.航空发动机转子动平衡概述航空发动机转子产生振动和噪声的主要原因是由于转子不平衡引起的,这种现象会直接影响发动机的使用寿命和使用性能。
因此,对于转子动平衡技术的研究意义重大,特别是对航空发动机柔性转子动平衡技术的研究具有非常重要的现实意义。
我们经常见到的用于旋转运动中的零件主要有主轴、各种驱动轴、涡轮转子以及电动机等,这些机械设备有着共同的特点,即均为旋转体。
如果旋转体处于理想的旋转状态时,此时轴承上的压力和不旋转时轴承上的压力相同,将这种旋转体称为平衡旋转体。
但是,在毛坯缺陷、材料均匀性不达标以及加工错误等因素的影响下,旋转体上的每个微小颗粒产生的离心惯性将难以抵消,最终将使轴承作用于机械以及基础上的离心惯性力引起振动,进而产生噪声,加剧轴承的磨损程度,这样一来,机械设备的使用寿命也将会被缩短,甚至对机械设备造成破坏性事故[1]。
为此,面对这种现象,必须通过对转子进行平衡,从而将其精确度控制在合理的范围内,或者通过减小机械振动幅度使转子处于平衡状态。
航空发动机转子叶尖间隙及同心度变化规律研究

航空发动机转子叶尖间隙及同心度变化规律研究张龙;韩鹏卓;刘忠奎;周笑阳【摘要】航空发动机转子叶尖间隙及同心度是影响发动机性能和安全的重要参数.组建了一套电容法测试系统,并成功用于发动机风扇转子叶尖间隙及同心度测量.通过分析测量数据,得到了发动机风扇转子叶尖间隙及同心度随转速和时间的变化规律.结果表明:慢车以下状态时,转速升高,转子叶尖间隙减小,转子向下偏移;慢车以上状态时,转速升高,转子叶尖间隙减小,转子向上偏移;最大状态时,部分测点存在较大叶尖间隙,同心度均不为零.【期刊名称】《燃气涡轮试验与研究》【年(卷),期】2017(030)001【总页数】4页(P44-47)【关键词】航空发动机;转子;叶尖间隙;同心度;电容法;测试系统【作者】张龙;韩鹏卓;刘忠奎;周笑阳【作者单位】中国航发沈阳发动机研究所,沈阳110015;中国航发沈阳发动机研究所,沈阳110015;中国航发沈阳发动机研究所,沈阳110015;中国航发沈阳发动机研究所,沈阳110015【正文语种】中文【中图分类】V231.3随着气动设计与试验方法的不断改进,航空发动机已发展到一个很高的技术水平,压气机和涡轮效率可分别达到86%、90%以上[1]。
要进一步提高压气机和涡轮效率,除注重气流参数选择外,还应提高发动机结构设计水平,在保证安全的前提下尽可能减小转子叶尖间隙及同心度。
国外在发动机转子叶尖间隙测试技术的应用,及如何减小转子叶尖间隙方面做了大量研究。
CFM国际公司在开始研制CFM56发动机时,就努力缩小转子的叶尖间隙及同心度而又使其摩擦最小[2]。
美国GE公司研制了一种小型不冷却测试装置,可在运转条件下测量高压涡轮转子叶尖间隙及同心度。
目前,美、欧主要发动机公司已逐步将叶尖间隙传感器作为发动机的一部分,以便给叶尖间隙主动控制提供更经济、便捷、准确的数值基础[3]。
国内在转子叶尖间隙及同心度对发动机性能影响计算方面的研究十分广泛[4-8],但转子叶尖间隙测试技术的应用方面研究却很少[9-11]。
航空发动机涡轮叶片修理技术

Repair Technologies for Blades of Aero-engine Turbine
积炭质地坚硬,黏附力强,因此,清除积炭是一项 较困难的工作。长期以来,各国的航空发动机维修基地 都在致力研究高效和高可靠性的清洗液和清洗工艺,目 前已取得相当的成果。西安航空发动机公司在从英国引 进技术的基础上,研制出四种不同成分配方、不同清除 功用的清洗液和分步的清洗工艺,在某型发动机上使用 表明清洗效果良好。美国则推行无毒清洗技术,如用碱 性清洗液和塑料丸取代氯氟烃溶剂;而一些航空公司已 经采用在清理表面积附时间长、易于用水清洗不留残物 的凝胶工艺(SPOPL)。SNECMA公司在20世纪80年代开发了 氟化氢(HF)离子清理技术,后来被美国FAA及诸如GE公司 等发动机制造商广泛应用,这种方法特别适用于进行叶 片表面处理(如化学气相沉积)前的预先清理,而且不污 染环境。
Hale Waihona Puke Repair Technologies for Blades of Aero-engine Turbine
CT检测仪: CT检测仪:适用于测量涡轮叶片壁厚和内部裂纹 检测仪
Repair Technologies for Blades of Aero-engine Turbine
叶型的精确检测 叶型的精确检测 的精确 目前,在坐标测量机 (CMM)的基础上,编制微 机控制自动检测所用的应 用软件,发展研制了检测 涡轮叶片的叶身几何形状 的坐标测量系统(CMMS), 可自动检测叶身的几何形 状,并与标准叶型比较; 自动给出偏差检测结果, 来判断叶片的可用度和所 需采用的修理手段。
Repair Technologies for Blades of Aero-engine Turbine
某型发动机进气处理机匣及静子叶片打伤的故障分析及修复

某型发动机进气处理机匣及静子叶片打伤的故障分析及修复摘要:航空发动机在外厂使用过程中吸入外来物造成进气处理机匣的扰流片、静子叶片发生不同程度的打伤故障,针对此故障分析故障产生原因,并制定了初步的修理方案,同时经过研究讨论,基于打伤部位结构的特殊性,我们提出修理方案中的难点并加以改进,确定最终的修理方案,最终使产品达到较为理想的状态,同时针对故障原因给出两点预防措施。
关键词:机匣;打伤;锉修;着色一、故障情况我厂修理的某型发动机在外场使用过程中进入外来物,导致压气机机匣以及压气机转子叶片发生不同程度的打伤故障。
打伤由进气处理机匣开始,转子叶片,静子叶片均有较严重的打伤痕迹。
对故障发动机进行分解、故检后发现本台发动机的进气处理机匣扰流片有8片打伤较严重,其中最深处约1.5mm;第2级静子叶片进气边有一处打伤较为严重,深度约3mm,长度约1cm。
打伤情况见图1、图2。
图1 扰流片打伤情况图2 静子叶片打伤情况二、故障分析及修理方案飞机在地面试车或空中飞行的过程中容易有外来物随着高速的气流吸入发动机,常见的外来物包括硬物体、软物体、鸟类等。
压气机作为航空发动机的前端部件,在发动机吸入外来物时,是最先受到撞击的,因此极易发生打伤、击穿甚至撕裂等故障。
航空发动机在吸入外来物的瞬间,很难将外来物完全击碎,外来物及其碎片在离心力的作用下将沿着机匣内壁和叶片之间向后移动,因此压气机机匣和叶片将是损伤的高发区域。
压气机转子属于发动机的重要件,主要通过转子叶片高速旋转将叶片的机械功加给空气,使空气的压力,密度,温度得到提高,工艺中对于转子叶片打伤程度有较严格的要求,超过工艺的打伤必须更换新品叶片。
压气机机匣与压气机转子一同构成气流流动的通道,对进入发动机的空气进行减速增压,一部分输送到燃烧室进行燃烧,另一部分用于发动机冷却,封严等作用。
其中,压气机机匣的作用是通过静子叶片间的扩散通道组织气流,主要承受来自气流的压力。
航空发动机转子动平衡方法探究

航空发动机转子动平衡方法探究发布时间:2022-03-10T02:38:37.643Z 来源:《新型城镇化》2022年3期作者:白云鹏[导读] 转子不平衡是造成转子过度振动和产生噪声的主要原因之一,会对发动机的工作性能和使用寿命造成直接影响。
国营长虹机械厂广西桂林 541002摘要:当航空发动机转子高速旋转时,转子质心与旋转中心偏离会引起发动机振动。
由于质量不平衡引起的发动机振动容易导致发动机性能下降,严重损坏发动机零件,甚至导致发动机停转。
发动机维护时,必须动态平衡转子,将转子的不平衡度用平衡机测量配平后,转子的不平衡量会达到相对稳定的水平。
关键词:航空、发动机、转子、动平衡、方法1航空发动机转子动平衡概述转子不平衡是造成转子过度振动和产生噪声的主要原因之一,会对发动机的工作性能和使用寿命造成直接影响。
因此,研究转子动平衡技术,尤其是航空发动机的柔性转子动平衡技术具有重要意义。
常用机械包含大量用于旋转运动的零件,例如各种驱动轴、主轴、电动机和涡轮转子,这些被统称为旋转体。
当旋转体理想旋转时,轴承上的压力与不旋转时轴承上的压力相同,这种旋转体是平衡旋转体。
但是,由于各种因素,例如材料不均匀、毛坯缺陷、加工和组装错误,甚至是设计中的几何形状不对称,旋转体上的每个微小颗粒产生的离心惯性力无法相互抵消,都会使轴承作用在机械及其基础上的离心惯性力引起振动,产生噪声,加速轴承磨损,缩短机械使用寿命并可能造成破坏性事故。
2现有转子平衡方法的应用缺陷以某台进厂维修排故级别的发动机为例,发动机故障原因是因为EGT温度超高,压气机转子组件拆下后没有进行及时分解。
当按要求磨削高压压气机之后,需要重新对其进行平衡。
在平衡过程中发现,在平衡机数次旋转中,其初始不平衡量的大小均不一致。
设备厂家和OEM针对此类现象给出的原因是HPC转子的叶片有所松动,这两个厂家给出的故障排除建议分别是清洗内腔灰尘和根据8点法对转子组件进行平衡。
航空发动机孔探检查过程的风险管理

航空发动机孔探检查过程的风险管理作者:***来源:《航空维修与工程》2018年第10期摘要:对发动机孔探检查工作中存在的风险事件进行识别,通过实例加以分析,给出缓解风险的措施以及工作体系构建、流程优化、人员能力培养等方面的建议,以供同行参考。
关键词:发动机;孔探检查;风险管理;危险源;应对措施0 引言发动机试验过程中的孔探检查是通过工业内窥镜(孔探仪)对发动机内部结构进行检查,为研制过程提供状态变化信息积累,能及时发现发动机的内部结构损伤,持续跟踪损伤的扩展,是降低发动机试验过程发生损伤造成重大影响的有效措施。
随着国家战略的实施以及重大专项的成立,国内某航空发动机研究所研制任务不断扩展,试验过程中的发动机装配、分解及试车任务的增加使得常规发动机孔探检查工作任务不断增多。
研制人员对试验过程中发动机零部件故障或故障排除措施尤为关注,监控检查故障发生点的需求对发动机孔探检查技术提出了更高的要求,使发动机孔探检查工作逐渐成为了被关注的重要工作点。
新研型号对孔探检查及其历史故障监控提出了新的要求,但研究所目前设备资源配备却不足,这在一定程度上增加了孔探检查工作的风险。
孔探检查工作现状与发动机研制需求之间的矛盾逐渐突出,如果处理不当,可能导致严重的后果和巨大的经济损失。
为适应发动机研制的需求,本文以国内某航空发动机研究所孔探检查工作为例,通过风险管理的模式,查找孔探检查过程中的危险源,对发动机孔探检查工作中存在的风险事件进行识别,并给出缓解风险的措施以及工作体系构建、流程优化、人员能力培养等方面的建议。
1 风险管理策略按照风险管理策略,将对存在的风险因素进行合理分类和管理、制定积极应对措施、降低风险发生的可能和影响程度设定为风险管理目标;依据本单位的实际工作情况以及相关工作标准,制定适宜的风险评估准则;将风险发生的可能性判据分为一般情况不会发生、极少情况下发生、某些情况下发生、较多情况下发生、常常发生等五个等级;从是否会对技术性能产生何种影响、是否延误进度、增加的成本是否超出预算的百分比等级三个方面对风险后果的严重性进行判定;采用风险矩阵将风险等级确定为高(G)、中(Z)、低(D)三个等级。
- 1、下载文档前请自行甄别文档内容的完整性,平台不提供额外的编辑、内容补充、找答案等附加服务。
- 2、"仅部分预览"的文档,不可在线预览部分如存在完整性等问题,可反馈申请退款(可完整预览的文档不适用该条件!)。
- 3、如文档侵犯您的权益,请联系客服反馈,我们会尽快为您处理(人工客服工作时间:9:00-18:30)。
视频内窥设备辅助下的航空发动机压气机转子叶片原位修复技术研究
作者:孙永曹平亚刘乃刚
来源:《中国科技纵横》2012年第12期
摘要:压气机转子叶片是航空发动机的关键零部件之一,对发动机的整体性能特别是安全性和可靠性影响重大。
压气机转子叶片数量多、工作条件恶劣,尤其高速旋转时所承受的离心负荷大、叶尖速度高因此常常会被外来物打伤,造成卷边、开裂、掉块等故障。
本文针对某型航空发动机,利用视频内窥叶片磨削设备和对设备改装,完成了该型发动机所有级压气机叶片原位损伤修复技术,有效的降低了发动机维修效率和维修成本,保障了装备完好率,提高了发动机的外场可维护性。
关键词:压气机叶片外来物打伤原位修复技术视频内窥技术损伤的容限设计
当飞机起飞、降落和低空飞行时,由于发动机进气产生的巨大吸引力,环境中沙尘、石块、飞鸟、金属碎片、冰块等很容易被吸入发动机气流通道,打伤发动机风扇/压气机叶片。
由外来物体对发动机风扇和压气机叶片造成的损伤,均被称为“外来物损伤”(Foreign object damage,以下简称FOD)。
可以说自喷气式发动机投入使用以来, FOD问题给发动机和飞机飞行安全巨大的危害,严重的FOD事件,叶片可能被直接打断,或被打伤后因承载能力严重下降,叶片在很短的时间内即发生断裂失效。
脱落的叶片碎片可能会打在其他叶片或发动机机匣上,造成一连串的打伤甚至叶片非包容事故,造成严重的等级飞行事故。
对于众多的FOD事件,大多数都是不太严重的,如图1所示的小缺口,只有毫米级,虽然短时间内不会造成严重事故,但如果对这类FOD问题不进行处理,或者检查时没有及时发现,FOD缺口可能会在载荷作用下发生裂纹萌生和扩展,导致叶片的断裂失效,最终也可能会酿成严重的飞行事故。
为此,FOD的叶片及时发现和修复对于发动机意义重大。
严重FOD必须进行更换叶片,修复时间较长,成本也较高,为了降低整个发动机使用寿命周期的成本、缩短发动机的维修时间,对于容许损伤范围内的FOD,外场原位(发动机装机状态)修复是十分必要的。
1、叶片损伤容许技术
90年代初, 美国MIL-E-5007D(1973)中的对FOD的容限设计提出要求,即等效为应力集中系数Kt≤3的缺口容限设计。
英国国防部2006年1月发布了其新版的发动机设计规范DEF STAN 00-970 PART
11ENGINES也对FOD的容限设计提出类似的要求。
FOD概率容限设计准则的提出和发展,基于真实FOD对叶片裂纹扩展极限的影响,符合外场FOD事件的强烈随机性特征,另一方面,为发展这一准则所产生的大量真实FOD及其对叶片强度影响的试验和分析数据,对制定更为科学、合理的外场FOD事件的判废标准和维修规范。
国内现行的航空发动机设计规范GJB241-87和GJB242-87对FOD容限设计的要求采用了美国MIL-E-5007D中的要求。
目前,随着多型号发动机的研制和正式列装,国内FOD容限得到了发展。
2、发动机叶片损伤原位检测技术
所谓原位,即不必拆卸发动机,发动机处于装机状态。
外场应用工业视频内窥设备可以对叶片损伤进行原位检查和测量。
将工业视频内窥镜设备(图1)的柔性光纤通过发动机机匣上的观察窗口,沿气流通道几何型面多次弯曲穿越,最终到达指定位置进行检查和测量。
目前,国际上多家厂商提供的视频内窥镜设备都可操纵镜头进入发动机内部。
如从静子机匣发动机观察窗进入,使用侧视镜头对转子叶片检查和测量,每次可以检查1片叶片,转动发动机完成该级所有转子叶片的损伤检查和确定损伤尺寸。
精确测量主要有以下几种方法。
图1 工业视频内窥镜设备
2.1 激光测量法
激光测量不需要更换视频内窥镜设备的镜头、不需要分屏、不需要复杂的瞄准操作。
激光测量的灵敏度精度0.1mm以上,能够满足航空发动机技术使用规范对压气机转子叶片的损伤测量精度的要求。
2.2 阴影测量法
阴影测量法,原理是利用阴影投射及三角几何原理的阴影投射探头测量技术。
测量精度与放大倍数相关。
在放大5以上倍数时,精度可以达到0.1mm以上,测量时需要更换设备的镜头。
2.3 双物镜测量法
双物镜测量法,视频内窥镜设备可以延长人眼的视距,改变视线的方向,方便地观测航空发动机内部的情况,但是为了在有限的孔径内获得大的观察范围,视频内窥镜设备不得不采用大视场的广角物镜,使内窥图像存在明显的光学畸变(桶形畸变)。
因此,需要视频内窥镜操作人员具备发动机专业的知识,对所观测的叶片形状有清晰的了解。
精度可以达到0.1mm以上,测量时需要更换设备的镜头。
2.4 三维立体相位扫描测量法
三维立体相位扫描测量技术,基于相移进行检测区域的相位扫描,建立被测物的三维立体模型,是目视检测领域一个里程碑性质的新技术,但瞄准操作不容易控制。
(如图2)精度可以达
到0.1mm以上,测量时不需要更换设备的镜头。
图2 三维立体相位扫描测量法
以上几种测量方法精度可以达到0.1mm以上,整个系统测量误差可以控制在5%以内,均可以完成发动机叶片损伤的精确测量,按照对叶片损伤容限判定叶片的修理模式。
3、损伤容限内的压气机叶片原位修复
3.1 工具的选择
对于可达的风扇一级转子,可以选择手动、电动锉修。
而对于手工作业不可达的其余各级
叶片,必须选择合适的工具。
正如现代医学的微创手术一样,发动机压气机叶片原位修复技术是针对航空发动机的微创
手术。
在发动机装机的条件下,将内窥叶片修理工具的磨头沿叶片观察窗口进入发动机气流通道,在内窥镜监测下发动机叶片上的微小损伤或裂纹进行修复(如图3)。
图3 叶片原位修理过程
内窥叶片修理工具(如图4)的结构类似于传统的光学内窥镜,它的轴穿过标准内窥镜通道,磨头向前延伸,将磨头调节到垂直90度,可以迅速接触待修磨的物体。
马达驱动磨头的转速达每分钟数千转(0~5000RPM连续可调)。
整个打磨过程可通过WOLF高分辨率的光学系统监测观察也通过内窥镜视频系统观察。
图4 内窥叶片原位修复仪器基本结构
1打磨头 2专用转接座 3外套 4机匣 5变速旋钮
6角度调节旋钮 7锁定项圈 8开关 9紧定螺钉
10手柄(内置电机) 11紧定滑轨 12光导接头
13目镜调焦旋钮 14电源线A 探杆B目镜
3.2 修理过程中的注意事项
(1)由于内窥叶片修理工具为刚性设计,操作者可以直接施力于被损伤的叶片,可以“亲身感受”打磨得过程。
磨头以安全的方式固定,不会掉落到发动机内部。
并能选择不同长度的磨头。
如:圆锥型头部的磨削头、半球型头部的磨削头、及其他各种异形磨削头、圆锥型头部的抛光头、球型抛光头及其他各种异形磨削头(图5)。
图5 各类磨头
(2)外场实际应用中,叶片损伤处磨修深度不能超过最大允许损伤深度+0.6mm,沿叶片边缘往上下两方向的磨修尺寸,应比损伤深度大3~6倍。
由于压气机叶片对微小裂纹的敏感性,在用磨削头磨削叶片损伤处后,至少应留出0.6mm深度用抛光头处理。
(3)在叶片进气边或排气边的叶尖部位如图6左。
由于航空发动机叶片与机匣间隙较小,对于叶尖有损伤的叶片,为了防止磨头损伤机匣,必须采取带圆锥型头部的打磨头。
在叶片进气边或排气边的其他部位可采用带有半球型头部的磨头。
在叶片确定叶片可以原位修复后,需要选定更细磨头进行抛光处理。
(4)对于宽弦的叶片(如二级风扇)长磨头也无法达到,需要改装加长磨头,并需要控制磨削转速,并采用8毫米以上探杆,降低加长磨头引起的跳动。
4、结语
外场应用工业视频内窥设备可以完成叶片损伤原位检查和测量,并依据发动机叶片容许损伤技术确定修复方式,针对叶片损伤程度制定可靠的修理工艺流程,最后利用内窥叶片修理设备完成压气机叶片原位修复。
保证FOD发动机在外场原位的快速修复,保障装备的完好率,提高了发动机的外场可维护性,同时也有效的降低了发动机维修效率和维修成本。
参考文献
[1]叶片外物损伤容限设计的本质特点及设计准则的发展.南京航空航天大学能源与动力学院.《航空动力学报》,2008年第12期.。