v-精益生产培训资料
-精益生产培训资料

流程图
总结词:梳理流程
详细描述:流程图是一种以图形方式呈现工作流程的工具。 通过绘制流程图,企业可以清晰地梳理各个部门、岗位之间 的职责和协同关系,明确关键流程和瓶颈环节,针对性地进 行优化和改进。
5S管理
总结词:现场管理
详细描述:5S管理是一种现场管理方法,包 括整理(Sort)、整顿(Straighten)、清 洁(Shine)、清洁检查(Check)和素养 (Sustain)。通过实施5S管理,企业可以 提高工作效率、降低成本、保障安全和提高
它关注客户需求,以价值流为导向,采用灵活的组织结构和 生产方式,运用多种管理工具和技能,不断提升企业竞争力 。
精益生产的起源与发展
精益生产起源于日本,经历了“丰田 生产方式”和“精益管理”两个阶段
。
20世纪70年代,日本汽车制造商丰田 公司通过不断改进和创新,提出了一 套独特的管理哲学和生产方式,被称 为“丰田生产方式”,即精益生产的
2023
《-精益生产培训资料》
目录
• 精益生产简介 • 精益生产的主要工具 • 精益生产在不同行业的应用 • 精益生产实施步骤 • 精益生产实施的关键因素
01
精益生产简介
精益生产是什么
精益生产是一种管理哲学和质量控制方法,旨在持续改进和 优化生产过程,提高效率、减少浪费、降低成本,最终实现 高质量、高效率、高收益的长期目标。
加强员工培训
通过培训提高员工的技能和素质,推广精益生产 理念和方法,增强员工的参与意识和主动性。
优化生产流程
通过对生产流程进行全面梳理和优化,消除浪费 和瓶颈环节,提高生产效率和质量水平。
引进先进技术
引进先进的生产技术和设备,提高生产自动化水 平和生产效率。
精益生产培训资料

外部时间:
—可以在机器运行的情况下进行的操作所需 要的时间。
14
第六部分:精益生产之关键点突破
6.2 品种快速切换能力(SMED)提升
初期
内部和外部的 操作没有区分 开
1 区分内部 及外部的 操作
外部
1. 检查表 2. 功能检查 3. 改进部件 和工具的运 输
2 将内部操作 转化为外部 操作
1. 预先准备操
生产工序间的 半成品
5
第五部分:减少库存
5.4 如何有效减少库存
使用最少原物料、在制品及完成品库存,以得到高产 量的整合活动。
Pull
半成品 顧客 最終組裝 半成品 製造 製造 製造 製造 製造 廠商 廠商 製造 製造 製造 製造 廠商 廠商
不生产不需要的东西 高品质、堅強的供应商关系 稳定、可观测的最终产品需求
17
第六部分:精益生产之关键点突破
6.3 生产节拍与拉动绳索的作用
标准时间构成
观测时间 评比 因数 私事 宽放 疲劳 宽放 程序 宽放 特别 宽放 政策 宽放
正常时间 标准时间
18
第六部分:精益生产之关键点突破
6.4 瓶颈与缓冲区突破
突破瓶颈:
找出影响整条生产线生产效率的工序,并加以改善。
缓冲区:
在瓶颈工序设定缓冲库存,以解决问题的经常发生。
19
第六部分:精益生产之关键点突破
6.4 瓶颈与缓冲区突破
瓶颈 工序
作 业 时 间 19 25s 18 20
从上一个产品生产结束到下一个合格产品生产出来并 达到设计速度的时间。
12
第六部分:精益生产之关键点突破
6.2 品种快速切换能力(SMED)提升
精益生产基础培训课件
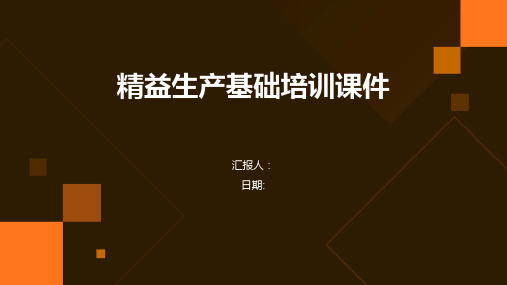
激励机制
建立激励机制,对5S管理表 现优秀的员工给予奖励和表彰
,提高员工积极性。
持续改进
不断优化5S管理流程和方法 ,提高现场管理水平,实现持
续改进。
04
持续改进与PDCA循环
பைடு நூலகம்
持续改进的概念
持续改进的定义
持续改进是一种工作方法,它通 过不断优化和改进企业运营的各 个方面,以实现更高的效率和更
感谢您的观看
THANKS
03
5S管理
定义与目的
定义
5S管理是一种以整理、整顿、清洁、规范和自律为主要内容的现场管理方法。
目的
通过实施5S管理,提高生产现场的效率、质量、安全和环保水平,降低生产成 本,提高企业竞争力。
5S的实践方法
整顿
对现场物品进行分 类、标识和定位, 使现场秩序井然。
规范
制定并执行现场管 理规范,确保现场 秩序和安全。
单元化生产
总结词
单元化生产是一种将生产设备、物料和人员按照工艺流程进行布局的生产方式, 实现小批量、多品种的生产。
详细描述
单元化生产是将生产设备、物料和人员按照工艺流程进行布局,实现小批量、多 品种的生产。这种生产方式可以快速响应市场需求,提高生产效率和灵活性。同 时,单元化生产还可以降低库存成本和减少浪费。
流程优化
根据价值流分析结果,优化流 程和资源配置,提高生产效率 和质量。
评估与反馈
对精益生产的实施效果进行评 估,及时调整实施计划,持续 改进。
02
价值流分析
定义与目的
定义
价值流分析是对企业生产活动中 各环节的价值流动过程进行细致 、全面的分析,以帮助企业识别 出浪费的根源和改进点。
精益生产基础培训
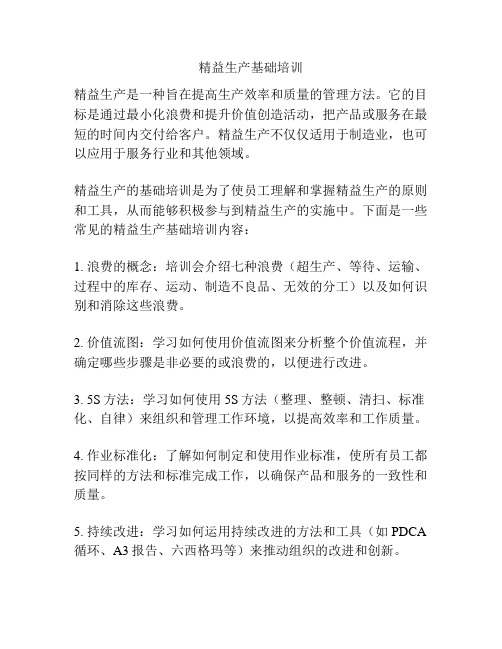
精益生产基础培训精益生产是一种旨在提高生产效率和质量的管理方法。
它的目标是通过最小化浪费和提升价值创造活动,把产品或服务在最短的时间内交付给客户。
精益生产不仅仅适用于制造业,也可以应用于服务行业和其他领域。
精益生产的基础培训是为了使员工理解和掌握精益生产的原则和工具,从而能够积极参与到精益生产的实施中。
下面是一些常见的精益生产基础培训内容:1. 浪费的概念:培训会介绍七种浪费(超生产、等待、运输、过程中的库存、运动、制造不良品、无效的分工)以及如何识别和消除这些浪费。
2. 价值流图:学习如何使用价值流图来分析整个价值流程,并确定哪些步骤是非必要的或浪费的,以便进行改进。
3. 5S方法:学习如何使用5S方法(整理、整顿、清扫、标准化、自律)来组织和管理工作环境,以提高效率和工作质量。
4. 作业标准化:了解如何制定和使用作业标准,使所有员工都按同样的方法和标准完成工作,以确保产品和服务的一致性和质量。
5. 持续改进:学习如何运用持续改进的方法和工具(如PDCA 循环、A3报告、六西格玛等)来推动组织的改进和创新。
6. 团队合作:培训中会鼓励员工之间的合作和团队精神,以便更好地解决问题和实施改进。
7. 管理层支持:培训会强调管理层在精益生产中的角色和重要性,并教授他们如何提供必要的支持和资源。
通过精益生产基础培训,员工可以了解到精益生产的基本原则和技术,提高他们的意识和技能,促使他们能够更好地参与到精益生产的实施中。
这将为组织带来更高的效率和质量,提升竞争力,并满足客户的需求。
精益生产基础培训的核心理念是通过消除浪费和改进流程,实现质量和效率的提升。
在这个培训中,员工们将学习如何利用精益方法和工具来消除浪费、优化流程,并在整个价值链中提供更高价值的产品和服务。
一、浪费的概念浪费是指在生产过程中不增加价值的活动或资源。
常见的七种浪费包括超生产、等待、运输、过程中的库存、运动、制造不良品以及无效的分工。
通过了解和识别这些浪费,员工们可以更好地认识到它们对生产效率和质量造成的负面影响,并找到消除浪费的方法。
精益生产基础培训讲义

與大量生產思想觀念的變革
四.精益生產的精髓
2.“瘦”,豐田式“瘦型”生產方式 “減肥”運動,剔除多余的機構,富余的人力, 把無效益的事情都砍掉.
四.精益生產的精髓
3.在制品是萬惡之源,提倡在制品向零挑戰.
大量生產把一定量的在制品當作 均衡生產的必要條件
严格把控质量关,让生产更加有保障 。2020 年11月 下午8时 21分20 .11.252 0:21No vember 25, 2020
重规矩,严要求,少危险。2020年11 月25日 星期三8 时21分 55秒20 :21:552 5 November 2020
好的事情马上就会到来,一切都是最 好的安 排。下 午8时21 分55秒 下午8 时21分2 0:21:55 20.11.2 5
(4)不重要也不緊急
馬上辦理
輕
好好規劃
重
馬上辦但只花一點時間
或找人代辦 緩
有空再辦
急
c.工作的時段管理
(1)早上八點至十點: 精力顛峰,適合作規劃 (2)早上十點至十二點:注意力及短暫記憶力最強,
適合腦力激蕩會議,訓練等. (3)下午一點至二點:昏昏欲睡,適合互動溝通工作. (4)下午二點至四點:開始清醒,長期記憶力最淺,適
例:
某日一機臺投入24Hour,其中保養1Hour,機故維修
0.5Hour,待料2Hour.則當日:
24-1-0.5-2
稼動率=
×100%=85%
24
可動率=
24-1-0.5 22
×100%=94%
4.平衡率:
各工序平均工時
平衡率 =
×100%
精益生产培训资料(ppt 55页)
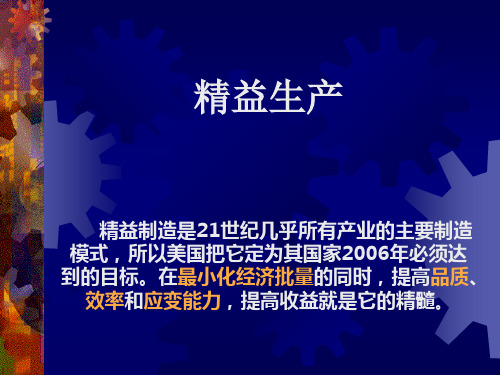
Seiketsu―标准化作业
一旦前面的已经推行,标准化作业 将把这些好经验作为标准保持下去。没 有它现场将到处是坏习惯。要建立一个 机制,使它能够推进标准化作业,还要 鼓励员工参与建立各种标准。前三个S是 靠指令来推行,标准化作业将把它们变 成一种规矩和习惯.
Shitsuke―技能和道德的培养
最终要保持前4个S,必需不断地向员 工宣导维护标准的重要性。建立一个的 系统,使结果可视化,并且能够保持不 断地推进。5S将会深入人心并且能够超 越它最初的定义进入一个持续改进的状 态,持续改进可以实现减少浪费、提高 质量和缩短交货周期。实施5S会提高效 率,改变工作环境和所有员工的精神面 貌。
持续改进(KAIZEN)
持续改进需要包括从操作工到总 经理的所有人的参与,它表示即使 只是一点点改进也能说明公司在持 续的进步,公司内的各个领域都在 不断地进步。
持续改进(KAIZEN)
要在公司里形成一套有效的建议,评价, 采纳,奖励的制度,倡导员工提合理化建议, 培养员工的不满足于现状,追求达到完美的 品质。同时要设立改进的目标,组织各种任 务团队,发挥他们的主观能动性,来实现甚 至超越设定的目标,公司高层应对完成目标 的团队进行奖励,而对没有完成目标的团队 应不予惩罚,而应对他们进行指导,帮助他 们达到目标。
战后的日本经济萧条,缺少资金和外汇。怎样建立日 本的汽车工业?照搬美国的大量生产方式,还是按照 日本的国情,另谋出路,丰田选择了后者。
日本的经济和技术基础与美国相距甚远。日本当时没 有可能全面引进美国成套设备来生产汽车,而且日本 当时所期望的生产量仅为美国的几十分之一。“规模 经济”法则在这里面临着考验。
Seiso―清洁
贯彻5S首先必需进行彻底的大扫除, 然后每天清扫来保持这种进步。清洁卫 生也对发现设备的故障有帮助的,比如 泄漏,破损和不对齐,这些小问题,如 果不及时发现,将会导致设备的失灵和 生产的停顿。定时清洁也是一种检查, 保持清洁是生产系统维护的重要组成部 分,通过清扫可以全面维护生产系统和 消除安全隐患。
精益生产培训资料

精益原则适用范围
• • • • • • • • • • 任何事物都是一个流程;五项原则适用于每个流程 产品开发 订单录入、计划和生产安排 供应商 生产 物流 行政管理系统 财务 人力资源 。。。
要点
目标是提供有效的开发、产品和服务体系,最大限度发挥员工在增值过程中的作用, 同时通过工程、管理和生产流程,努力了解和尽量减少变异来源和影响。
Customer 客户
Material 原料
Stage & Ship 储存&发运
5
什么是精益生产
精益企业的使命
精益生产的目标是建立一个有效的研发、生产、服务体系,使员工为客户创造价值 的能力最大化,同时最大程度地减少各流程和产品变异 的根源和影响,以使企业达成 - 最好的品质 - 最短的周期时间 - 最低的成本 - 最好的安全和高士气
要同时符合以上三个要求的活动才是
‘value added’. 增值的活动。非增值的活动即是”Waste”浪费。
缺陷产品 过度生产 搬运 等待 过多库存 Defective Product Overproduction Transportation Waiting Inventory
9
丰田生产系统
最好的质量-最低的成本-最短的周期最好的安全-高士气 通过消除浪费来缩短生产时间 准时化 正确的零件, 正确的数量, 正确的时间 员工 & 报告团队工作 选择 共同的目 标
决策 交叉培训
自动化 (从源头保证质量)
让问题可视化
节拍时间计划 连续流动 拉动系统
举例
- 材料损失 - 加工工时损失 - 返工工时损失
后果
- 延期出货/客户抱怨 - 辅助材料损失 - 降价损失 -
最新企业-精益生产培训资料

推行精益就是不断消除浪费的改善过程:
消除浪费 消除浪费 消除浪费
没有浪费
浪 费
浪
浪
费
费
目 标
精
益
成
本
企业不断地强化自己的生产过程,随时消除生产过程中的 浪费,力求使生产过程中所用的资源绝对最少,从而使整个生 产看起来很“精”,但又能达到很“益”的结果。
16
第二部分:认识浪费
1. 浪费等于在“烧钱” 2. 制造现场的八大浪费 3. 价值流图与分析方法 4. 价值流图绘制练习
对七个“零”目标理解:
☆ 零切换
☆ 零库存
零 7个“
☆ 零抱怨
”目标 ☆ 零不良
☆ 零故障
☆ 零停滞
☆ 零事故
12
第一部分:精益生产方式概要
1.2 精益生产方式价值-七个零目标
从观念开始改变:
三个公式有何不同? 1、成本 + 利润 = 销售价格
2、利润 = 销售价格 - 成本
3、销售价格 - 成本 = 利润 精益生产首先就是要求转变关注点:
Deliviry
C-成本 (Cost) S-安全 (Safety) M-人员积极性 (Morale)
最佳的品质 最柔性交货 最低的成本 最高安全性 最高员工士气
追求“零”极限
“零”产品不良
“零”故障 “零”停滞 “零”库存 “零”切换 “零”事故
“零”员工抱怨
11
第一部分:精益生产方式概要
1.2 精益生产方式价值-七பைடு நூலகம்零目标
1.精益生产方式简介 2.精益生产方式价值-七个零目标
3
第一部分:精益生产方式概要
1.1 精益生产方式简介
何谓精益生产?
精益生产基础培训资料重点

(1) (2)
售价=成本+利润 利润=售价 -成本 (1) 成本主义
利润
售价
成本
成本主义 成本降低 (2) 成本降低
利润 售价
成本
增加利润的方法
1.提高售价… 需要>供给 2.降低原价… 需要≤供给
售价由客户决定
“减少一成浪费就等于增加一倍销售额” ——大野耐一
假如商品售价中成本占90%,利润为10% 把利润提高一倍的途径: 一、销售额增加一倍 二、从90%的总成本中剥离出10%的不合
美国
-1950年美国工业劳动生产率是日 本的8-9倍
丰田
-1950年汽车制造业的差距至少相差 10倍
-每年人均生产汽车11.5辆
-每年人均生产汽车54.6辆
丰田汽车在2003年获利81.3亿美元,比通用、克莱斯勒、 福特3家公司的获利总和还要高,同时也是过去10年所有汽车 制造商中年度获利最高的,丰田的净利润率比汽车业平均水平 高8.3倍。
态或特性; ➢ 第一次做对的活动;
非增值活动:
➢ 除此之外的所有活动和非客户期望 的特性都被定义为——“浪费”
➢ 不能给客户带来价值、同时增加了 业务运营的成本。
Before
After
Time
Value Added Work Non-Value Added Work
精益意味着通过持续改进消 除整个业务流程中对客户来 讲非增值的活动。
美国
-1896年杜里埃兄弟制造并销售了 13辆四轮汽车 -1908年共有485家汽车制造商 -1914年福特汽车实现了汽车流水 线生产 -1928年通用公司雪佛兰汽车年产 量达到120万辆
丰田
-1896年丰田汽车的创始人丰田佐吉 刚刚发明了“丰田式木制织机” -1933年在丰田自动织机制作所设立 汽车部 -1936年丰田AA型轿车初次问世 -1937年丰田汽车正式成立,产量只 有4000辆
精益生产基础知识培训课件

针对识别出的问题,制定具体的 改进措施和计划。
实施改进措施
实施改进
按照改进计划,逐步实施各项改进措 施。
监控与调整
在实施过程中,密切监控改进效果, 及时调整计划和措施。
持续改进与优化
总结经验教训
对实施的改进措施进行总结,分析成功和失败的原因。
持续优化
根据总结的经验教训,不断优化改进计划,持续推进精益生产。
要点二
增强企业竞争力
通过优化生产和供应链管理,精益生产能够帮助企业获得 竞争优势。
精益生产的优势与局限
01
局限
02
03
04
适用范围有限:精益生产主要 适用于制造业,对于其他行业
可能不太适用。
对员工素质要求高:精益生产 需要员工具备较高的技能和素 质,以及较强的自我管理能力
。
变革阻力:实施精益生产需要 对企业进行深度的变革,可能 会遇到来自员工和管理层的阻
精益生产与传统生产的区别
关注点
精益生产关注价值流 和客户需求,而传统 生产关注产量和效率
。
灵活性
精益生产强调灵活性 和快速响应,而传统 生产更注重稳定性和
计划性。
浪费消除
精益生产通过消除浪 费来提高效益,而传 统生产可能忽略或无
法识别浪费。
员工参与
精益生产鼓励员工参 与改进和优化,而传 统生产可能更注重分
06
总结与展望
精益生产的优势与局限
优势 01
提高生产效率:通过消除浪费和优化流程,精益 02 生产能够帮助企业提高生产效率。
降低成本:通过减少浪费和优化库存,精益生产 03 能够降低企业的成本。
精益生产的优势与局限
要点一
精益生产培训管理资料

• (2)有一个劳动力调节市场,实行劳动力能自然 流动的外部环境。这样,企业才可能成为一个开放 系统,确保企业中劳动方的最优组合。企业可以不 断与外界交换劳动力,吸收适合于本企业需要的人 员、排除不适用的人员,保证劳动力队伍素质的稳 步提高。
中集集团的感悟
• 集团的十六字方针:“内涵优化、 控制风险、巩固提升、创新突破。”
• 精益生产是对传统“大规模生产方式”提出的挑战。
精益生产方式对现代制造业的影响
•
(一)精益生产方式是对传统大量生产方式的扬弃
1989年,美国麻省理工学院总结丰田生产方式,认为 这是制造工业的又一次革命。报告认为日本最有效益的企业 是:采用适度的自动化技术,并对企业整体进行全面的科学 管理;日本最成功的企业是:充分发挥了人的潜力、智慧和 积极性。但是,大多数美国企业过于臃肿,因此报告提出了 “精简、消肿”的对策,并把日本取得成功的生产方式称为 精益生产,表达了丰田生产方式精益求精、以简代繁的特点。
众股份公司,1994年在深圳证券交易所上市,1995年起以集
团架构开始运作。集团致力于为现代化交通运输提供装备和服
务,主要经营集装箱、道路运输车辆、罐式储运设备、机场设
备制造和销售服务。截止2006年底,中集集团总资产229.23
亿元、净资产111.17亿元,在国内和海外拥有50余家全资及
控股子公司,员工近50000人。
品大大减少,节约了流动资金。
•
在生产技术上采用适度的自动化技术又明显提高了生产效率。
所有这一切,都使企业的资源能够得到合理的配置和充分的利
用…
(二)现代制造业应用精益生产方式的优越性 从1990年开始,美国麻省理工学院的学者用了
5年时间,花费了3500万美元的巨资,组织日、美 和欧洲各国50多位专家,在对世界17个国家的90 个汽车制造厂进行广泛调查的基础上,发表实证性 研究报告,认为精益生产的优越性表现在: