工艺安全和风险管理
生产工艺安全管理要求范本
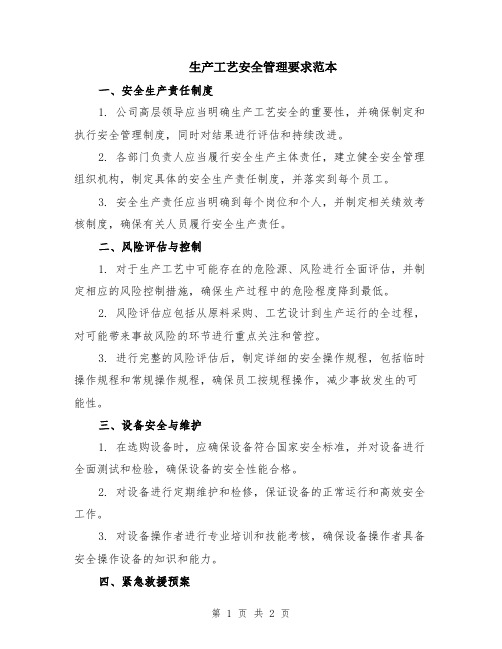
生产工艺安全管理要求范本一、安全生产责任制度1. 公司高层领导应当明确生产工艺安全的重要性,并确保制定和执行安全管理制度,同时对结果进行评估和持续改进。
2. 各部门负责人应当履行安全生产主体责任,建立健全安全管理组织机构,制定具体的安全生产责任制度,并落实到每个员工。
3. 安全生产责任应当明确到每个岗位和个人,并制定相关绩效考核制度,确保有关人员履行安全生产责任。
二、风险评估与控制1. 对于生产工艺中可能存在的危险源、风险进行全面评估,并制定相应的风险控制措施,确保生产过程中的危险程度降到最低。
2. 风险评估应包括从原料采购、工艺设计到生产运行的全过程,对可能带来事故风险的环节进行重点关注和管控。
3. 进行完整的风险评估后,制定详细的安全操作规程,包括临时操作规程和常规操作规程,确保员工按规程操作,减少事故发生的可能性。
三、设备安全与维护1. 在选购设备时,应确保设备符合国家安全标准,并对设备进行全面测试和检验,确保设备的安全性能合格。
2. 对设备进行定期维护和检修,保证设备的正常运行和高效安全工作。
3. 对设备操作者进行专业培训和技能考核,确保设备操作者具备安全操作设备的知识和能力。
四、紧急救援预案1. 制定完善的紧急救援预案,包括应急演练、事故调查和信息反馈等环节,确保能够及时有效地应对各类突发事件。
2. 各部门应当组织紧急救援培训,并制定相关的紧急情况通讯方式,确保在突发事件发生时能够迅速组织救援和报告上级。
五、安全培训与教育1. 对全体员工进行定期的安全培训和教育,确保员工具备安全意识和应急处理能力。
2. 加强对特定工种、危险较大的工作环节人员的培训,提高其专业知识和技能。
3. 结合实际情况开展安全知识宣传教育活动,提高员工对安全事故的防范和应对能力。
六、监督检查与评估1. 设立专门的安全检查机构,定期对生产工艺进行全面监督和检查,发现问题及时整改,确保安全风险在控制之内。
2. 开展安全生产评估,对公司的安全管理制度和安全生产管理工作进行全面评估和改进。
工艺流程中的风险评估与控制
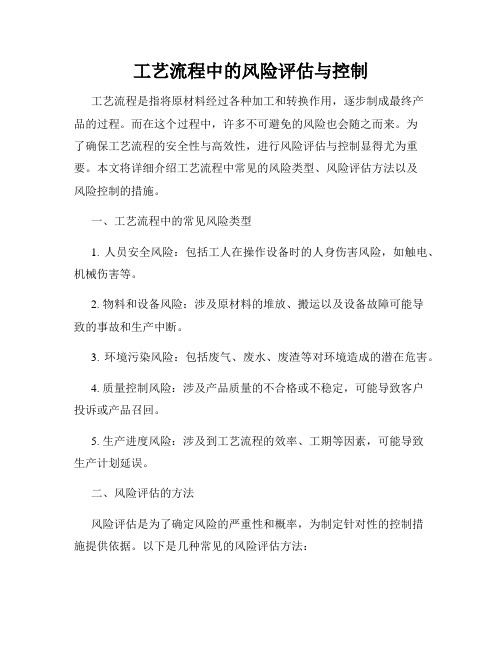
工艺流程中的风险评估与控制工艺流程是指将原材料经过各种加工和转换作用,逐步制成最终产品的过程。
而在这个过程中,许多不可避免的风险也会随之而来。
为了确保工艺流程的安全性与高效性,进行风险评估与控制显得尤为重要。
本文将详细介绍工艺流程中常见的风险类型、风险评估方法以及风险控制的措施。
一、工艺流程中的常见风险类型1. 人员安全风险:包括工人在操作设备时的人身伤害风险,如触电、机械伤害等。
2. 物料和设备风险:涉及原材料的堆放、搬运以及设备故障可能导致的事故和生产中断。
3. 环境污染风险:包括废气、废水、废渣等对环境造成的潜在危害。
4. 质量控制风险:涉及产品质量的不合格或不稳定,可能导致客户投诉或产品召回。
5. 生产进度风险:涉及到工艺流程的效率、工期等因素,可能导致生产计划延误。
二、风险评估的方法风险评估是为了确定风险的严重性和概率,为制定针对性的控制措施提供依据。
以下是几种常见的风险评估方法:1. 事件树分析法(ETA):通过分析事件链的不同可能路径,确定风险事件发生的概率和结果。
2. 安全风险矩阵法:将风险根据其可能性和影响程度进行分类,以确定重点关注的风险。
3. 失效模式与影响分析法(FMEA):将系统的故障原因、失效模式和潜在影响进行评估,找出可能导致严重后果的风险。
4. 层次分析法(AHP):通过构建层次结构模型,对不同风险因素进行排序评估,以确定最重要的风险。
三、风险控制的措施在进行风险控制时,需要结合具体的风险特点,采取相应的措施来减少或消除风险的发生。
以下是几种常见的风险控制措施:1. 设备保养和维修:定期检查和维护设备,确保其正常运转,减少设备故障的风险。
2. 操作规程和培训:制定详细的操作规程,对工人进行培训,提高其操作的标准化和安全意识。
3. 紧急预案和演练:制定应急预案,定期进行演练,以提高应对突发事件的能力。
4. 质量管控和检测:建立完善的质量管理体系,进行严格的质量检测,确保产品符合标准要求。
工艺流程的风险评估与风险管理措施
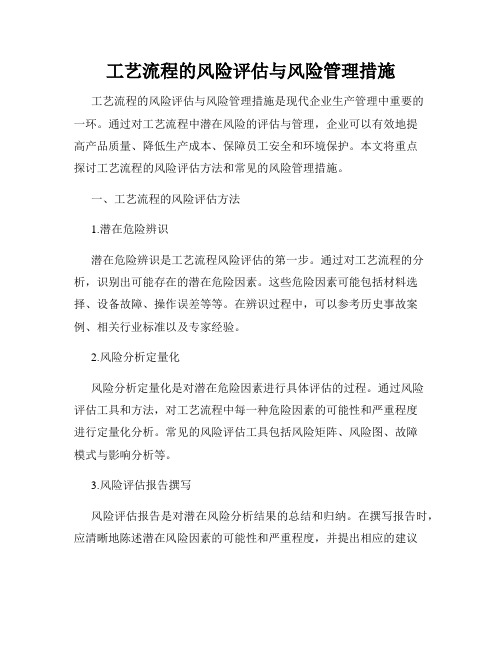
工艺流程的风险评估与风险管理措施工艺流程的风险评估与风险管理措施是现代企业生产管理中重要的一环。
通过对工艺流程中潜在风险的评估与管理,企业可以有效地提高产品质量、降低生产成本、保障员工安全和环境保护。
本文将重点探讨工艺流程的风险评估方法和常见的风险管理措施。
一、工艺流程的风险评估方法1.潜在危险辨识潜在危险辨识是工艺流程风险评估的第一步。
通过对工艺流程的分析,识别出可能存在的潜在危险因素。
这些危险因素可能包括材料选择、设备故障、操作误差等等。
在辨识过程中,可以参考历史事故案例、相关行业标准以及专家经验。
2.风险分析定量化风险分析定量化是对潜在危险因素进行具体评估的过程。
通过风险评估工具和方法,对工艺流程中每一种危险因素的可能性和严重程度进行定量化分析。
常见的风险评估工具包括风险矩阵、风险图、故障模式与影响分析等。
3.风险评估报告撰写风险评估报告是对潜在风险分析结果的总结和归纳。
在撰写报告时,应清晰地陈述潜在风险因素的可能性和严重程度,并提出相应的建议和措施以降低风险。
报告的内容要简明扼要,结构清晰,以便管理层能够快速理解和采纳。
二、风险管理措施1.工艺流程优化通过工艺流程的优化,可以减少潜在风险的发生。
优化包括合理选择原材料、改进设备设计、优化操作步骤等。
工艺流程优化的目标是提高产品质量、降低生产成本、提升生产效率。
2.建立标准作业程序(SOP)标准作业程序是对工艺流程中操作步骤进行规范化管理的文件。
通过建立SOP,企业可以避免操作错误和疏漏,减小人为因素对工艺流程的风险影响。
3.安全培训与教育通过对员工进行安全培训和教育,提高员工的安全意识和操作技能。
培训内容可以包括工艺流程中的危险因素、风险控制措施以及紧急情况下的应急处理方法。
4.定期巡检与维护定期对工艺流程中的设备进行巡检和维护,确保设备的正常运行和安全性。
同时,对设备进行故障预测和预防性维护,及时消除潜在隐患。
5.风险监测与持续改进风险管理是一个持续的过程,企业应定期对工艺流程进行风险监测和评估。
新工艺的安全风险评估与控制措施
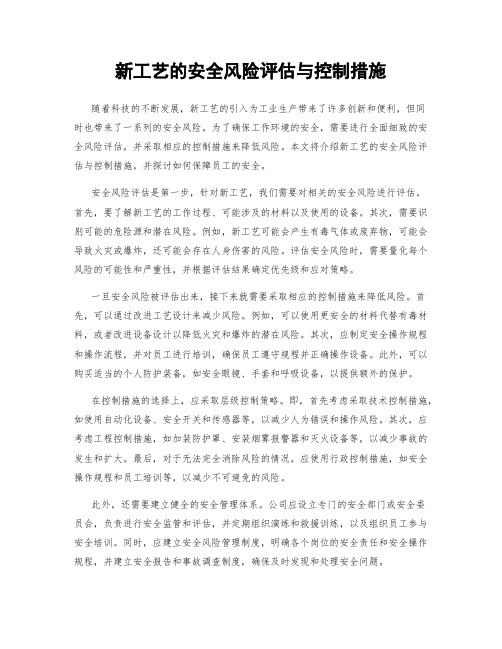
新工艺的安全风险评估与控制措施随着科技的不断发展,新工艺的引入为工业生产带来了许多创新和便利,但同时也带来了一系列的安全风险。
为了确保工作环境的安全,需要进行全面细致的安全风险评估,并采取相应的控制措施来降低风险。
本文将介绍新工艺的安全风险评估与控制措施,并探讨如何保障员工的安全。
安全风险评估是第一步,针对新工艺,我们需要对相关的安全风险进行评估。
首先,要了解新工艺的工作过程、可能涉及的材料以及使用的设备。
其次,需要识别可能的危险源和潜在风险。
例如,新工艺可能会产生有毒气体或废弃物,可能会导致火灾或爆炸,还可能会存在人身伤害的风险。
评估安全风险时,需要量化每个风险的可能性和严重性,并根据评估结果确定优先级和应对策略。
一旦安全风险被评估出来,接下来就需要采取相应的控制措施来降低风险。
首先,可以通过改进工艺设计来减少风险。
例如,可以使用更安全的材料代替有毒材料,或者改进设备设计以降低火灾和爆炸的潜在风险。
其次,应制定安全操作规程和操作流程,并对员工进行培训,确保员工遵守规程并正确操作设备。
此外,可以购买适当的个人防护装备,如安全眼镜、手套和呼吸设备,以提供额外的保护。
在控制措施的选择上,应采取层级控制策略。
即,首先考虑采取技术控制措施,如使用自动化设备、安全开关和传感器等,以减少人为错误和操作风险。
其次,应考虑工程控制措施,如加装防护罩、安装烟雾报警器和灭火设备等,以减少事故的发生和扩大。
最后,对于无法完全消除风险的情况,应使用行政控制措施,如安全操作规程和员工培训等,以减少不可避免的风险。
此外,还需要建立健全的安全管理体系。
公司应设立专门的安全部门或安全委员会,负责进行安全监管和评估,并定期组织演练和救援训练,以及组织员工参与安全培训。
同时,应建立安全风险管理制度,明确各个岗位的安全责任和安全操作规程,并建立安全报告和事故调查制度,确保及时发现和处理安全问题。
最后,要保障员工的安全,需要加强安全意识和培养安全文化。
工艺安全风险分析

风险评估:评估风险等级, 确定风险控制措施
风险识别:识别工艺安全风险, 包括设备、工艺、人员等方面
制定风险管理计划:明确风 险管理目标、范围、方法等
风险控制:制定风险控制措施, 包括技术、管理、培训等方面
风险监控:定期监控风险控制 措施的实施情况,确保风险得
到有效控制
风险报告:定期向管理层报告 风险管理情况,确保风险管理
事故原因:分析 事故发生的主要 原因,如人为因 素、设备故障、 管理缺陷等
事故后果:介绍 事故造成的人员 伤亡、经济损失、 社会影响等后果
确定风险源:识别可能存在的风险源, 如设备故障、操作失误等
风险评估:对风险源进行评估,确定风 险等级和影响范围
实施应对措施:按照制定的应对措施进 行实施,确保风险得到有效控制
得到有效执行
培训内容:工艺安 全风险管理知识、 法律法规、案例分 析等
培训方式:线上 培训、线下培训、 研讨会等
培训对象:员工、 管理人员、技术 人员等
意识提升:提高员工 对工艺安全风险的认 识和重视,增强安全 意识和责任感
定期评估:对工艺安全风险管理体系进行定期评估,确保其有效性和适用性
持续改进:根据评估结果,对工艺安全风险管理体系进行持续改进,提高其安全性和可靠性
原理:通过分析事故发生的原因和后果,找出可能导致事故发生的因素 步骤:确定目标事件、分析原因、确定后果、绘制事故树
优点:能够全面、系统地分析事故发生的原因和后果,有助于制定预防措施
应用:广泛应用于化工、石油、电力、航空等领域
风险矩阵法通过分析风险发生 的可能性和后果的严重性,来 确定风险的等级。
风险识别:识别可能存在的风险,如设备 故障、操作失误等
风险评估:对识别出的风险进行评估,确 定风险等级和影响程度
工艺流程的安全风险评估与管理
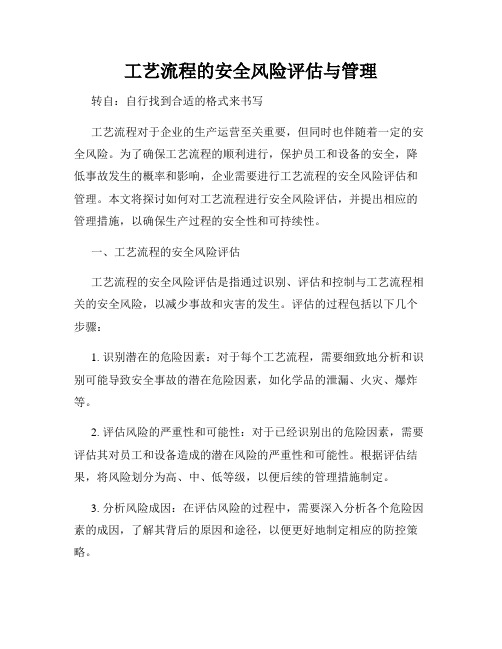
工艺流程的安全风险评估与管理转自:自行找到合适的格式来书写工艺流程对于企业的生产运营至关重要,但同时也伴随着一定的安全风险。
为了确保工艺流程的顺利进行,保护员工和设备的安全,降低事故发生的概率和影响,企业需要进行工艺流程的安全风险评估和管理。
本文将探讨如何对工艺流程进行安全风险评估,并提出相应的管理措施,以确保生产过程的安全性和可持续性。
一、工艺流程的安全风险评估工艺流程的安全风险评估是指通过识别、评估和控制与工艺流程相关的安全风险,以减少事故和灾害的发生。
评估的过程包括以下几个步骤:1. 识别潜在的危险因素:对于每个工艺流程,需要细致地分析和识别可能导致安全事故的潜在危险因素,如化学品的泄漏、火灾、爆炸等。
2. 评估风险的严重性和可能性:对于已经识别出的危险因素,需要评估其对员工和设备造成的潜在风险的严重性和可能性。
根据评估结果,将风险划分为高、中、低等级,以便后续的管理措施制定。
3. 分析风险成因:在评估风险的过程中,需要深入分析各个危险因素的成因,了解其背后的原因和途径,以便更好地制定相应的防控策略。
4. 制定监测和控制措施:基于对风险的评估和分析结果,制定相应的监测和控制措施,包括设备的安全保护措施、操作规范和紧急预案等,以降低风险的发生概率和减少事故的影响。
二、工艺流程的安全风险管理工艺流程的安全风险管理是指对评估结果进行管理和控制,以确保工艺流程的安全性。
1. 建立安全管理制度:企业应建立相应的安全管理制度,包括安全责任制、安全培训制度、安全检查与监督制度等,明确工艺流程安全的管理责任和流程。
2. 加强人员培训和意识提升:通过定期的培训和教育,提高员工对工艺流程安全的认识和意识,并掌握相应的应急处理能力,以应对突发事件。
3. 实施监测和检查:通过定期的监测和检查,及时了解工艺流程的运行状态和潜在风险的变化,发现问题并采取相应的措施进行处理。
4. 强化设备维护和更新:定期对工艺流程中的设备进行维护和检修,确保设备的正常运行,减少因设备故障而引发的安全风险。
工艺安全风险管理制度

一、总则为了加强工艺安全管理,预防事故发生,保障员工生命财产安全,根据国家有关法律法规及公司安全生产规章制度,特制定本制度。
二、适用范围本制度适用于公司所有涉及工艺操作、研发、设计、施工、维护等环节的安全管理工作。
三、管理原则1. 安全第一,预防为主,综合治理;2. 责任到人,分工明确,齐抓共管;3. 科学管理,持续改进,不断提高安全管理水平。
四、组织机构及职责1. 安全生产委员会负责制定、修订和实施工艺安全风险管理制度,组织安全生产大检查,对工艺安全风险进行评估和管控;2. 生产部门负责工艺操作、研发、设计、施工、维护等环节的安全管理工作,确保工艺安全风险得到有效控制;3. 技术部门负责工艺技术的研究、开发、应用,对工艺安全风险进行评估,提出控制措施;4. 设备管理部门负责设备的安全管理,确保设备运行符合安全要求;5. 质量管理部门负责工艺质量监督,确保工艺安全风险在质量可控范围内;6. 人力资源部门负责员工安全教育培训,提高员工安全意识。
五、工艺安全风险评估与管控1. 识别危险源:对工艺操作、研发、设计、施工、维护等环节进行危险源识别,建立危险源清单;2. 评估风险:对识别出的危险源进行风险评估,确定风险等级;3. 制定控制措施:针对不同风险等级,制定相应的控制措施,包括技术措施、管理措施、个体防护措施等;4. 实施控制措施:按照控制措施要求,组织实施,确保措施落实到位;5. 监督检查:定期对工艺安全风险管控措施进行检查,确保措施有效执行。
六、应急管理与事故处理1. 制定应急预案:针对可能发生的工艺安全事故,制定相应的应急预案,明确应急组织、应急措施和应急程序;2. 应急演练:定期组织应急演练,提高应急处置能力;3. 事故报告:发生工艺安全事故时,及时上报,按照事故处理程序进行调查处理;4. 事故原因分析:对事故原因进行深入分析,制定整改措施,防止类似事故再次发生。
七、培训与教育1. 新员工入职培训:对新员工进行工艺安全知识培训,提高安全意识;2. 定期培训:对员工进行定期安全培训,更新安全知识,提高安全技能;3. 安全知识竞赛:举办安全知识竞赛,激发员工学习安全知识的积极性。
化学工程与化学工艺的安全与风险管理

化学工程与化学工艺的安全与风险管理化学工程与化学工艺是一门涉及化学反应、物料转化和工业生产的学科,它在社会发展和经济建设中起着重要的作用。
然而,与化学相关的工程和工艺过程中存在一系列的安全隐患和风险,如化学品泄漏、爆炸事故、环境污染等。
因此,对于化学工程与化学工艺的安全与风险管理显得尤为重要。
一、安全风险评估与预防在化学工程与化学工艺的设计和实施过程中,必须进行全面的安全风险评估与预防措施的制定。
安全风险评估应包括对潜在风险的识别、分析和评估,以及建立相应的预警机制和应急预案。
预防措施需要从源头上控制风险,采用可行的技术和措施进行事故防范,如设备密封、防爆装置、自动控制系统等。
二、规范操作与安全培训在化学工程与化学工艺的实施过程中,必须严格遵守操作规程和工艺要求。
规范操作流程可以最大程度地减少操作失误和事故的发生。
同时,对从事化学工程与化学工艺的人员进行系统的安全培训,提高其安全意识和应急处理能力,是必不可少的。
三、安全设备与监测系统化学工程与化学工艺中采用各种设备进行物质转化和反应,因此必须确保这些设备的安全性与可靠性。
在设备的设计和制造过程中,应考虑到安全因素,采用符合标准的材料和技术,确保设备能够承受各种工况和应急情况。
同时,建立完善的监测系统,对化学工程与化学工艺的各个环节进行实时监测和报警,及时处理潜在的风险。
四、应急处理与事故调查尽管采取了一系列的预防措施,但事故仍有可能发生。
因此,必须建立完善的应急处理机制和事故调查程序。
应急处理需要进行事前演练和培训,设立专门的事故处理人员和机构,明确责任和权限,并建立紧急救援通道。
事故调查应及时展开,查明事故原因,并总结教训,以便提高安全措施和工艺设计的水平。
五、法律法规与标准要求化学工程与化学工艺的安全与风险管理需要依据法律法规和标准要求进行。
国家和地方政府应出台相关的法律法规,以明确责任和义务,并对不履行安全管理责任的单位和个人进行处罚。
同时,行业组织和标准化机构应推动制定行业标准和规范,提高行业整体的安全意识和管理水平。
食品加工安全和风险管理制度
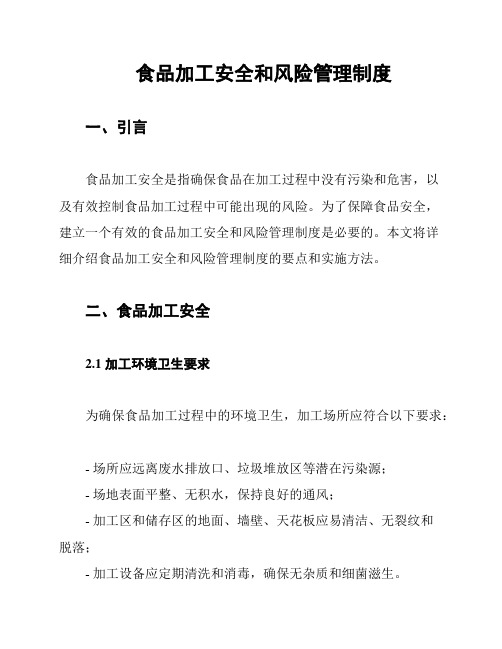
食品加工安全和风险管理制度一、引言食品加工安全是指确保食品在加工过程中没有污染和危害,以及有效控制食品加工过程中可能出现的风险。
为了保障食品安全,建立一个有效的食品加工安全和风险管理制度是必要的。
本文将详细介绍食品加工安全和风险管理制度的要点和实施方法。
二、食品加工安全2.1 加工环境卫生要求为确保食品加工过程中的环境卫生,加工场所应符合以下要求:- 场所应远离废水排放口、垃圾堆放区等潜在污染源;- 场地表面平整、无积水,保持良好的通风;- 加工区和储存区的地面、墙壁、天花板应易清洁、无裂纹和脱落;- 加工设备应定期清洗和消毒,确保无杂质和细菌滋生。
2.2 原料和辅料安全管理为确保食品加工过程中的原料和辅料的安全性,应采取以下措施:- 原料和辅料的采购应从正规厂商、注册供应商购买,避免采购假冒伪劣商品;- 原料和辅料应检验合格后方可使用,检验内容主要包括外观、感官特性、检验项目等;- 不同种类的原料和辅料应区分存放并妥善保管;- 严格遵循食品加工中的卫生操作规程,如洗手、穿戴防护服等。
2.3 加工工艺控制为确保食品加工的工艺质量,应采取以下措施:- 加工工艺应符合食品加工的标准和规定;- 加工设备应定期维护和保养,确保其正常运行;- 建立加工工艺管控记录,记录工艺参数的调整、异动等情况;- 加工中的关键参数应进行实时监测和控制,确保产品质量的稳定性。
三、风险管理制度3.1 风险评估和分级食品加工过程中存在各种潜在的风险,应进行风险评估和分级:- 针对每个环节进行风险评估,包括原料采购、加工过程、包装和储存等;- 根据风险评估结果,进行风险分级,确定关键环节和高风险环节。
3.2 风险控制和纠正措施针对高风险环节,应采取以下风险控制和纠正措施:- 制定详细的操作规程和操作指南;- 加强员工的培训和监督,确保操作规程的贯彻执行;- 建立定期检查和巡视制度,及时发现和纠正潜在风险;- 建立风险记录和故障处理记录,为风险分析提供数据支持。
化学工程与化学工艺的安全管理与风险控制

化学工程与化学工艺的安全管理与风险控制化学工程与化学工艺是一门旨在将化学原理应用于实际生产中的学科,涉及到复杂的化学反应、物质转化过程以及高压、高温等危险因素。
在化工生产中,安全管理与风险控制是至关重要的,它们可以帮助防止事故的发生,保护工作人员的生命安全和财产安全。
本文将探讨化学工程与化学工艺的安全管理与风险控制的重要性,以及一些常用的方法和策略。
1.安全管理的重要性安全管理是化学工程与化学工艺中不可或缺的一部分。
它的主要目标是确保生产过程的安全性,预防事故的发生,并在事故发生时能迅速、有效地应对。
一个好的安全管理系统可以保护工作人员的生命安全、确保环境的可持续发展,并减少生产过程中的经济损失。
2.风险评估与控制风险评估是安全管理的基础,通过对潜在风险的识别和评估,可以制定相应的控制措施。
风险评估应该全面而系统,考虑到生产过程中的各种因素,包括化学反应的特性、原料质量、设备状态等。
常用的风险评估方法有层次分析法、故障模式与效应分析等。
在评估完成后,制定相应的控制措施至关重要。
对于高风险的操作和设备,可以采取防火、防爆、泄漏控制等措施。
此外,应加强设备维护和管理,定期进行检修和保养,确保设备处于最佳状态。
3.培训和意识提高安全管理不仅仅是制定规章制度和标准操作程序,更重要的是加强员工的培训和意识提高。
通过培训,员工可以了解化学工程与化学工艺过程中的潜在风险,学习正确的操作方法和应对危险情况的技能。
此外,要加强安全意识的宣传和教育,提高员工对安全问题的重视程度。
通过组织安全知识竞赛、撰写安全经验分享等方式,提高员工对安全管理的认识和参与度。
4.事故应急管理事故的发生是无法完全避免的,因此事故应急管理也是安全管理的重要一环。
一个高效的事故应急管理系统可以最大限度地减少事故带来的损失。
事故应急管理应包括事故报警机制、事故应对预案、应急救援队伍组建等。
在事故发生时,应立即启动应急预案,及时采取措施进行事故控制和处理。
新工艺条件下的安全管理措施评估与风险控制

新工艺条件下的安全管理措施评估与风险控制随着科技的不断进步和工业技术的不断革新,新的工艺条件下的安全管理措施评估与风险控制变得至关重要。
在新工艺条件下,新材料、新设备和新工艺的应用为工业生产带来了巨大的变化和挑战,同时也对安全管理提出了更高的要求。
首先,安全管理措施评估是确保工业生产达到最高安全标准的关键步骤。
在新工艺条件下,对新材料、新设备和新工艺进行全面评估是必要的。
评估过程包括对材料的物理特性、设备的性能参数以及工艺的运行情况进行分析,以确定潜在的安全风险和危险点。
通过对工艺的全面评估,可以及时发现并解决存在的安全隐患,确保生产过程中人员和设备的安全。
其次,风险控制是在新工艺条件下保障生产安全的重要手段。
通过对潜在风险和危险点的控制,可以降低事故发生的概率和严重程度。
其中,一种常见的风险控制方法是通过工程控制措施来减少潜在的危险。
例如,合理设计工艺流程、设备和设施,采用先进的监测和控制系统,以及实施自动化和远程控制等措施,可以减少人为操作的风险,提高生产过程的稳定性和安全性。
另外,还可以采取预警系统、应急预案、安全培训和定期检查等措施来降低事故发生的可能性。
此外,加强员工培训是确保工业生产安全的关键环节。
在新工艺条件下,新技术和新设备的应用为员工带来了新的工作要求和技能需求。
因此,为员工提供全面的培训和教育,使其具备应对新风险和危险的能力是非常重要的。
培训内容可以包括对新设备和工艺的操作规程、安全操作规范、事故防范知识和应急处理技能的培训等。
通过培训,员工的安全意识和操作技能可以得到有效提升,从而降低事故发生的风险。
最后,建立健全的监管和管理体系是保障工业生产安全的基础。
在新工艺条件下,监管和管理体系的作用至关重要。
政府和相关监管部门应加大对新工艺条件下的安全管理措施评估与风险控制的监管力度,制定和完善相关法律法规和标准,确保企业按照规定进行安全管理。
同时,企业也应加强内部管理,建立健全的安全管理体系,完善安全生产责任制和内部安全管理规章制度,加强安全生产监测和风险评估,提高应急处理能力,确保生产过程安全可控。
高风险施工工艺与安全防范

制定安全管理制度:明确安全管理职责、权限和流程 建立安全培训体系:定期进行安全培训,提高员工安全意识和技能 实施安全检查与评估:定期进行安全检查,及时发现和纠正安全隐患 建立安全信息管理系统:实时监控施工现场安全状况,及时预警和处理安全事故
定期举办安全知识讲座, 提高员工安全意识
组织安全技能培训,提高 员工安全操作能力
建立产学研用 合作机制,促 进技术创新与
交流
加强高校与企 业的合作,推 动科研成果转
化
举办学术会议、 研讨会,促进 学术交流与合
作
建立技术交流 平台,促进技 术成果共享与
推广
PART SEVEN
加强安全教育,提高员工安全意识 建立安全责任制,明确安全责任 加强安全检查,及时发现和纠正安全隐患 加强安全培训,提高员工安全技能和素质
,
汇报人:
CONTENTS
添加目录标题
高风险施工工 艺概述
高风险施工工 艺的风险因素
高风险施工工 艺的安全防范 措施
高风险施工工 艺的安全监管 与评估
高风险施工工 艺的安全技术 创新与发展
PART ONE
PART TWO
高风险施工工艺:指在施工过程中存在较高安全风险的工艺,如高空作业、地下作业等。
PART FIVE
建立完善的安全监管制度
明确安全监管的责任主体
制定详细的安全监管计划
定期进行安全监管评估和 整改
定期进行安全评估,确保施工 工艺的安全性
定期进行安全检查,及时发现 并纠正安全隐患
制定安全评估与检查计划,确 保评估与检查的及时性和有效 性
建立安全评估与检查记录,便 于追溯和改进
定期检查:对高风险施工工艺进行 定期检查,及时发现安全隐患危险化学品作业:如石油、天然气 Nhomakorabea化 工等
工艺安全管理要素概览

工艺安全管理要素概览工艺安全管理是一个综合性的管理体系,用于确保企业在生产过程中的安全性和合规性。
它涵盖了多个要素,包括安全文化、风险管理、培训教育等。
本文将对工艺安全管理的要素进行概览和介绍,并探讨其重要性与实施方法。
一、安全文化安全文化是指企业内部的安全价值观、安全行为和安全氛围。
在工艺安全管理中,建立和培养良好的安全文化至关重要。
企业应该通过示范作用、安全意识教育和奖惩机制等方式,强调员工对安全的重视,并使其成为企业文化的一部分。
二、风险管理风险管理是工艺安全管理的核心要素之一。
它包括评估、识别和控制生产过程中的各种潜在风险。
企业应该制定相应的风险评估和管理制度,确保员工能够正确识别风险,并采取适当的防控措施。
企业还应该建立紧急应对机制,以应对突发事件和事故。
三、培训教育培训教育是提高员工安全意识和技能的重要手段。
工艺安全管理要求企业对员工进行相关的培训,包括操作规程、紧急处理、应急救援等方面的知识和技能。
通过培训教育,员工能够了解自己的责任和义务,提高对安全事项的敏感度,从而降低事故发生的概率。
四、监测和改进工艺安全管理要求企业不断监测和改进其安全管理体系。
通过设立监测指标、开展巡检和定期检查等方式,企业可以及时发现问题和隐患,并采取相应的措施进行改进。
企业还应该进行经验总结和教训学习,以避免类似事故的再次发生。
以上仅是工艺安全管理要素的一个概览,每个要素都具有其独特的重要性和实施方法。
在实际操作中,企业还需根据自身的特点和需求,进一步细化和完善其安全管理体系。
通过健全的工艺安全管理,企业可以最大程度地降低生产过程中的风险,确保员工和设施的安全,提升企业的竞争力和可持续发展能力。
个人观点与理解:工艺安全管理是企业生产和经营活动中至关重要的一环。
它涉及到员工的生命安全、企业的声誉和社会的稳定。
在我看来,安全文化是工艺安全管理的基础,只有形成了共同的价值观和行为准则,员工才能自觉遵守安全规定,履行自己的职责。
工艺技术风险管控与措施

工艺技术风险管控与措施工艺技术风险管控与措施工艺技术风险是在企业生产过程中可能出现的各种技术问题和潜在的危险因素。
企业在进行工艺技术的研发与应用过程中,必须认真对待风险的防范与控制,以确保生产顺利进行,保障员工与环境的安全。
下面将介绍一些常见的工艺技术风险管控与措施。
首先,建立完善的风险评估体系。
企业应该根据自身的生产工艺特点,建立起科学的风险评估指标和评价体系,明确风险的来源、性质和潜在危害,对可能引发的事故进行评估和预警。
其次,制定科学合理的工艺流程和操作规程。
企业应该通过详细的工艺流程和操作规程,规范每一个生产环节的操作步骤,避免人为失误和操作不当引发风险事故。
同时,要建立培训制度,对员工进行工艺技术操作的培训和考核,提高员工的专业水平和操作技能。
再次,加强设备的维护和管理。
企业应该定期检查、维护设备,确保设备的正常运转和性能稳定。
对于老化、损坏或存在安全隐患的设备,要及时进行维修或更换,以消除潜在的风险。
另外,进行及时有效的事故处理和应急预案。
即使进行了严格的管控措施,事故仍然有可能发生。
企业应根据不同的事故类型,制定相应的应急预案,对可能出现的风险事故进行应急演练,提高员工的应急处理能力。
此外,加强监督和检查工作。
企业应建立健全的监管机制,加强对各个环节的监督和检查,确保风险管控措施的落实情况。
并且还应加强与行业监管部门的沟通与合作,不断跟踪行业最新的风险管控技术和措施,及时更新和改进自己的风险管理体系。
最后,进行经验总结和持续改进。
在工艺技术应用中,企业应不断总结经验,及时对存在的问题和风险进行改进和优化。
并且要建立与员工之间的沟通渠道,主动听取员工的意见和建议,共同为企业的风险管控工作做出贡献。
总之,工艺技术风险管控是企业管理中的重要环节,只有加强风险管理和防范措施,才能确保企业的安全生产和稳定运营。
企业应高度重视工艺技术风险管控工作,加强自身的风险管理能力和技术水平,为员工的安全和企业的发展保驾护航。
控制工艺风险的保证措施

控制工艺风险的保证措施为了确保工艺过程的安全性和可持续性,控制工艺风险的保证措施至关重要。
本文将探讨几个关键的控制工艺风险的措施,以确保工业生产的安全和顺利进行。
一、正确使用个人防护装备正确的个人防护装备的使用对于降低工艺风险至关重要。
无论是在化学品管理领域、高温环境下的工作还是与有害物质接触的工作,员工都应受过培训,了解并正确使用相应的个人防护装备。
这些装备包括但不限于防护眼镜、耳塞、呼吸器、手套和防护服等。
此外,企业还应定期检查、维护和更新个人防护装备,以确保其性能和有效性。
二、风险评估和预防措施风险评估是确定和评估工艺风险的关键步骤。
企业应建立一个评估风险的系统,以了解可能的风险和危害的来源。
然后,应采取相应的预防措施来降低或消除这些风险。
这可能包括工艺参数的调整、添加或提升工艺设备的安全功能、改变作业流程或引入其他控制措施。
通过不断改进风险评估和预防措施,企业可以不断提高工艺的安全性和可靠性。
三、应急响应计划应急响应计划是处理突发事件的关键工具。
在工艺过程中,意外事故和紧急情况难以避免,但一个完善的应急响应计划可以减轻损失,并迅速恢复生产。
企业应确保员工接受了相应的培训,熟悉应急响应计划,并进行定期演练以检验其有效性。
此外,应急设备和安全系统的定期检查和维护也是确保应急响应计划有效性的必要措施。
四、标准操作规程标准操作规程(SOP)是确保工艺过程的稳定性和可控性的重要工具。
SOP是书面的工作指导,详细说明了各项工艺操作的步骤和要求。
员工必须接受培训并严格按照SOP执行工作。
通过标准化操作,企业可以减少人为失误和操作风险,提高工艺的一致性和可靠性。
五、定期检查和维护定期检查和维护工艺设备是确保其正常运行以及风险控制的关键步骤。
企业应建立一个定期检查和维护计划,以检查工艺设备的性能和安全性,并采取必要的维护措施。
这可以通过定期检查关键设备的状态、检查管道和阀门的泄漏、清洗和更换过滤装置等来实现。
化工工艺安全—工艺安全管理

工艺安全分析
在工艺装置设备整个生命周期开展工艺安全分析
工艺安全分析
实现优秀操作
工艺 人
设备 通过专业操作
工艺安全分析
管理层的领导力和 承诺
安全文化
工艺安全的一个基本出发点是预防工艺物料(或能量)泄漏。 石油化工行业发生的工艺安全事故通常表现为着火、爆炸或者有毒物暴
露等不同的形式,但都可以归咎于物料的泄漏或能量的释放。 “工艺安全”所倡导的事故预防:强调采用系统的方法对工艺危害进行
分析。根据工艺系统或生产设施不同生命周期或阶段的特点,采取不同的方 式辨别存在的危害、评估危害可能导致的事故频率及后果,以此为基础,设 法消除危害以避免事故,或减轻危害可能导致的后果。 工艺安全的侧重点是工艺系统或生产设施本身。
识别危险
设计
建造艺安全过程包括操作设施的完整的生命周期,并基于 清楚地识别潜在危险,这些危险与这些设施和控制这些 危险的风险管理活动相关。
工艺安全管理的主要目的:是预防有毒有害、易燃易爆 或能量的意外泄漏,特别是防止它们泄漏到员工或其他 人员活动的区域,使相关人员遭受伤害。
传统的“安全”主要是指使用各类个人防护用品和建立相应的规章制度来保护 作业人员,防止发生人员伤害事故。 “工艺安全”所倡导的事故预防方法有别于以上传统的做法,它强调采用系统 的方法对工艺危害进行辨识,根据设施不同生命周期或阶段(研发、设计、投 产前和生产过程中)的特点,采取不同的方式辨别存在的危害、评估危害可能 导致的事故频率及后果,并以此为基础,设法消除危害以避免事故,或减轻危 害可能导致的事故后果。工艺安全重视应用以往设计的经验教训,强调严格执 行相关的设计标准和规范。工艺安全的理念和危害控制技术可以应用于各种流 程工业,例如化工、石化、炼油、海上采油、制药及冶金等。
化工工艺设计中的安全风险及控制方法

化工工艺设计中的安全风险及控制方法摘要:化工工艺设计是一个高度技术性、综合性强、安全性高的领域。
在化工工艺设计中,存在着各种各样的安全风险,如化学品安全性、设备安全性和操作风险等。
为了避免安全事故的发生,必须对安全风险进行分析和控制。
本文从化工工艺设计的特点出发,对化工工艺设计中的安全风险进行了分析,并提出了一些控制方法,以便为化工工艺设计中的安全管理提供一些参考。
关键词:化工工艺设计;安全风险;安全性评估;技术手段;危险管理;一、化工工艺设计的特点化工工艺设计是指对化工生产过程在技术、经济、安全等方面的设计与优化。
化工工艺设计的特点如下:(一)高度技术性化工工艺设计主要是面向化工制品和化工生产过程,需要具备高度技术性。
设计涉及诸多工艺原理和技术要求,需要考虑到化学反应、热传递、质量传递、材料选择、设备设计等因素。
因此,化工工艺设计需要具备扎实的基础知识和专业技能,才能保证生产过程的顺利实施。
(二)综合性强化工工艺设计的综合性相当强,需要兼顾经济效益、生产效率、产品质量、环境保护等多种因素。
设计的过程中涉及到成本核算、资源利用率、自动化程度、维修保养等多个方面,需要在各种因素之间进行综合权衡,力求达到最佳的效益。
(三)安全性高化工工艺设计需要高度关注生产安全问题,化学物质和反应条件的特殊性,使化工工艺生产过程存在较高的安全风险。
因此,在进行工艺设计时,需要充分考虑生产过程中存在风险,同时设计各种安全保障措施,确保员工及周围环境的安全。
二、化工工艺设计中的安全风险分析化工工艺设计中的安全风险分析是一个非常重要的工作,主要目的是为了预防和减少事故的发生,确保生产过程的安全性和稳定性。
在进行安全风险分析时,需要关注以下三个方面。
(一)化学品的安全性分析化工企业的生产过程中需要使用各种化学品,这些化学品的安全性非常重要。
在进行化学品的安全性分析时,需要根据其物理属性、化学性质以及毒性等因素进行综合评估,并且判断其与其他化学物质的相互作用情况,以确保其安全性。
- 1、下载文档前请自行甄别文档内容的完整性,平台不提供额外的编辑、内容补充、找答案等附加服务。
- 2、"仅部分预览"的文档,不可在线预览部分如存在完整性等问题,可反馈申请退款(可完整预览的文档不适用该条件!)。
- 3、如文档侵犯您的权益,请联系客服反馈,我们会尽快为您处理(人工客服工作时间:9:00-18:30)。
Process Hazards Analysis
Quality Assurance
Prestart-Up Safety Reviews Mechanical Integrity
Copyright © 2004 E. I. du Pont de Nemours and Company. All rights reserved
5/17/2006 DUPONT
6
Technology Spokes
•Process Technology
• Hazards of materials • Process Design Basis • Equipment Design Basis
•Process Hazards Analysis
• New or modified Facilities • Baseline and cyclic PHA’s which include consequence analysis and layers of protection • Human factors, facility siting, ISP
5/17/2006 DUPONT
Strong teamwork Common shared values Up to date documentation Absence of shortcuts Excellent Housekeeping
11
Highly Toxic Materials (HTM) Management
• • • • • Maintenance Procedures Testing and Inspection Mechanic Training and Qualification Reliability Engineering Analysis Quality control for spare parts
•
Contractor Safety
• • • • Selection based on past performance Contractor qualifications and training Knowledge of hazards and controls Field Auditing
•
•
Pre Start-up Safety Review
• • Final checkpoint for new or modified equipment Facility safe to operate IAW PSM req’s
•
Management of Subtle Change
• • Minor field changes not considered Replacement in Kind (RIK) Appropriate review and authorization
•Operating Procedures and Safe Work Practices
• Detailed Operating procedures and standard conditions • Specific work practice requirements
• • • Work Permits Alarm and interlock bypasses Integrity checks
Process Safety and Risk Management
Aldo Morell Director, Safety, Health and Environment 10 May, 2006
2
The DuPont Approach to Managing Process Safety Risk
5/17/2006 DUPONT
4
Process Safety and Risk Management Model
Auditing Emergency Planning and Response Management of Change Incident Investigation and Reporting Contractor Safety and Performance Training and Performance Management of “Subtle” Change
5/17/2006 DUPONT
9
Personnel Spokes (cont’d)
• Management of Subtle Change
• • Manage changes in line organization to maintain knowledge and expertise Demonstrate competency within 90 days
5General Aspets of PSM• Application of the global PSM model for two main types of manufacturing/operations within each process and site
• Higher Hazard Processes (HHP) • Lower Hazard Operations (LHO)
10
Operational Discipline
Leadership by example Sufficient and capable resources Employee involvement Active lines of communication Practice Consistent with Procedures
Today
5/17/2006 DUPONT
3
Process Safety and Risk Management
Concept: Application of management controls to hazardous processes and operations in a way that hazards are identified, understood, and controlled so that process-related injuries and incidents can be eliminated. Focuses on These Resources: Technology Facilities Personnel
• Auditing
• • • •
5/17/2006 DUPONT
1st party site based PSM audit process to measure performance on 14 elements 2nd party PSM audit procedures and scoring Audit protocols and reporting/trending Collection and tracking of recommendations
5/17/2006 DUPONT
8
Personnel Spokes
• Training and Performance
• • • Basic Skills, knowledge, job task focus Ability to conduct tasks IAW operating procedures and process technology Refresher training and skill demo
• Integrated system to identify, manage and reduce process related hazards and risks • Basic platform to assimilate other SHE needs and issues related to process operations (one system vs five) • A highly effective method to manage change across manufacturing and R&D • A tool to achieve and maintain regulatory compliance
•Management of Change
• SHE implications of change • Trial Evaluation • Impact on hazards and technology
5/17/2006 DUPONT
7
Facilities Spokes
• Mechanical Integrity
• Emergency Planning and Response
• • • Written procedures for emergency conditions (roles, communication, equipment) Coordination with external resources Routine exercises with critiques
•
Quality Assurance
• • • Bridge gap between design and initial installation Detailed Equipment Specifications Procurement, Evaluation, and Acceptance through field installation
• • Separate HTM guardian teams for highly toxic materials - all global user sites Special focus to ensure absolute consistency in handling our most hazardous toxics (combination of acute toxicity and high vapor pressure) Individual Guardian Manuals - prescriptive reqs on HTM safety technologies, procedures, and materials Separate 2nd party audit process (3 yr frequency) Guardian team Leaders participate on external industry groups where they exist (e.g. ACC phosgene panel , HCN users group ) Also includes a Transportation Risk Assessment methodology