旋风分离器故障汇总
重油催化装置旋风分离器问题分析及改进措施

重油催化装置旋风分离器问题分析及改进措施摘要:三级旋风分离器是决定流化催化裂化炼油系统能量回收装置使用寿命的关键三级分离器是用于炼油工业中针对催化裂化程序的主要回收装置,在炼油系统中担任第三极旋风分离器,在催化裂油程序中,前两级分离装备并没有全部把烟气清理干净,第三级分离器主要任务就是把再生机器旋风分离器未能完成的任务高质量完成,从在再生烟气中分离出催化微粒,为烟气透平机提供高温高压烟气,保证透平机的使用寿命。
关键词:重油催化装置三级旋风分离器问题分析及改进措施重油在催化裂化过程中会造成严重的能量流失问题,大量的能量随着烟气被放空,如果采取一定的技术措施,采用再生烟气能量回收技术,那么得到的结果会是相当可观的。
提高重油催化裂化能量回收技术是非常重要的,针对能量回收,研发制定合格的旋风分离器是至关重要的。
一、三级旋风分离器重油催化裂化过程中会产生较多的具有高温高压的再生烟气,这些烟气有很大的位能,炼油过程中往往会通过烟气轮机来回收再生烟气所具备的能量,烟气产生的同时伴有催化颗粒的产生,损坏烟机,造成烟叶磨损,转盘等部位的损伤,影响烟机的工作效率及使用寿命。
重油催化裂化过程中,对于再生烟气产生的催化颗粒有严格要求,包括含烟浓度和颗粒大小。
在烟气轮机回收压力能的前提工作中,需要对再生烟气进行规划和清理,固化分离,进一步分化再生烟气,按照分化器的分化顺序称之为第三级旋风分离器。
二、旋风分离器的种类旋风分离器的工作原理依据于离心率,利用含尘气体旋转时产生的离心力把粉尘从气流中分离出来,属于一种干式气固分离装置。
1.气流导入方式的不同,分离器分为切流反转式旋风分离器和轴流式旋风分离器。
其中切流反转式分离器是最常见的型号,从筒体的侧面导入烟尘气体,气流旋转向下进入椎体,到达端点之后反转向上,通过排气管排出清洁气体。
轴流式旋风器利用气流旋转原理,尘烟进入筒体之后,呈圆周运动,气流向下向锥体移动,呈螺旋形。
通过重力和离心力的作用,粉尘顺着器壁落入锥体中,轴流式旋风器旋转的切向速度随着锥体的半径变化而变化,切向速度到达临界点的同时气流会由向下螺旋运动变为向上螺旋运动,称之为内旋气流。
旋风分离器的几个问题

旋风分离器的几个问题旋风分离器被广泛的使用已经有一百多年的历史。
它是利用旋转气流产生的离心力将尘粒从气流中分离出来。
旋风分离器结构简单,没有转动部分。
但人们还是对旋风分离器有一些误解。
主要是认为它效率不高。
还有一个误解就是认为所有的旋风分离器造出来都是一样的,那就是把一个直筒和一个锥筒组合起来,它就可以工作。
旋风分离器经常被当作粗分离器使用,比如被当做造价更高的布袋除尘器和湿式除尘器之前的预分离器。
事实上,需要对旋风分离器进行详细的计算和科学的设计,让它符合各种工艺条件的要求,从而获得最优的分离效率。
例如,当在设定的使用范围内,一个精心设计的旋风分离器可以达到超过99.9%的分离效率。
和布袋除尘器和湿式除尘器相比,旋风分离器有明显的优点。
比如,爆炸和着火始终威胁着布袋除尘器的使用,但旋风分离器要安全的多。
旋风分离器可以在1093摄氏度和500ATM的工艺条件下使用。
另外旋风分离器的维护费用很低,它没有布袋需要更换,也不会因为喷水而造成被收集粉尘的二次处理。
在实践中,旋风分离器可以在产品回收和污染控制上被高效地使用,甚至做为污染控制的终端除尘器。
在对旋风分离器进行计算和设计时,必须考虑到尘粒受到的各种力的相互作用。
基于这些作用,人们归纳总结出了很多公式指导旋风分离器的设计。
通常,这些公式对具有一致的空气动力学形状的大粒径尘粒应用的很好。
在最近的二十年中,高效的旋风分离器技术有了很大的发展。
这种技术可以对粒径小到5微米,比重小于1.0的粒子达到超过99%的分离效率。
这种高效旋风分离器的设计和使用很大程度上是由被处理气体和尘粒的特性以及旋风分离器的形状决定的。
同时,对进入和离开旋风分离器的管道和粉尘排放系统都必须进行正确的设计。
工艺过程中气体和尘粒的特性的变化也必须在收集过程中被考虑。
当然,使用过程中的维护也是不能忽略的。
1、进入旋风分离器的气体必须确保用于计算和设计的气体特性是从进入旋风分离器的气体中测量得到的,这包括它的密度,粘度,温度,压力,腐蚀性,和实际的气体流量。
DMTO装置反应器三级旋风分离器故障分析及改造

67中煤陕西公司DMTO装置由洛阳院设计,年处理180万t甲醇(折纯),生产60万t烯烃产品(乙烯+丙烯)。
装置于2014年5月建设完成,同年7月份一次性开车成功。
反应器三级旋风分离器(以下简称三旋)位于反应器下游,将反应气中携带的大量催化剂进行回收,是催化剂回收系统的核心设备之一,对于降低催化剂损耗以及急冷水的固含量起到关键性作用。
1 三旋结构与工作原理三旋由中间筒体、上锥体、上筒体、分离单元等部件组成。
为防止高温催化剂对设备壳体等部件冲刷腐蚀,在其内壁设计有100mm厚LC2级隔热耐磨衬里。
携带大量催化剂的反应气沿三旋矩形入口切线进入,沿轴向外漩涡向下旋转至中间筒体底部后,变为内漩涡沿气体入口管轴向上升,随后进入气体入口管与出口管间夹套,经分离单元气固分离,反应气排入气体出口管至下一设备,催化剂则进入下锥体,由催化剂排出口排出。
2 三旋故障(1)外部表现。
2016年5月,发现三旋中间筒体以及上锥体小端加强段表面油漆局部超温变色,经测温枪对其表面温度进行检测,测得局部最高温度362℃,远超同类衬里冷壁设备金属表面温度计算值[1]。
使用测厚仪对其金属壁厚进行检测,发现中间筒体出现局部减薄,最薄处27.97mm(设计值30mm)。
采取在超温变色区域外围加设大功率风机的措施,对其表面进行物理降温,将温度控制在350℃之下。
将检测数据反馈至设计院,经设计院核算强度后,确认可以继续使用。
在后续生产中,装置人员对超温、减薄部位进行定期、定点检测。
直至装置停工检修,温度及壁厚均未出现波动现象。
(2)三旋内部检查。
2017年4月装置停工检修,打开三旋检查,发现中间筒体底部以上1.7m范围内,衬里全部脱落。
锚固钉未见明显磨损,中间筒体内壁出现局部冲刷腐蚀现象。
上锥体标高47m处,衬里表面出现沟槽,槽深2mm左右,沟槽成螺旋状沿轴向向下逐渐加深直至衬里脱落。
3 故障原因分析1)锥体磨损量与直径成反比。
携带催化剂的反应气沿锥体轴向外漩涡向下运动,锥体上的磨损量沿轴向明显增加,且在锥体下部或最低端达到最大值,锥体下部形成磨损峰值(实际上是个磨损环)。
旋风分离器故障汇总

J阀(旋风分离器)故障(此故障主要出现在国产化的CFB锅炉)。
J阀(旋风分离器)故障主要现象J阀入口静压波动大导致J阀回料不连续,床压、床温出现大幅度的波动,严重时破坏外循环,使尾部受热面积灰严重,造成尾部烟道再燃烧,损坏空预器。
J阀(旋风分离器)故障主要原因1)旋风分离器回料不正常。
旋风分离器因灰位较高而影响了分离器的分离效果,从而使一定量未分离灰进入烟道造成空预器积灰严重,引起J阀入口静压波动。
2)过高的循环倍率造成J阀循环灰量过大,超出J阀流通能力。
3)燃烧工况的突然改变破坏了J阀的循环。
4)流化风配比不恰当,J阀回料未完全流化。
J阀(旋风分离器)故障采取措施1)发现回料不正常时,及时对旋风分离器的风量进行调整,必要时降低锅炉负荷;尾部烟道积灰严重时,加强对其吹灰(注意控制炉膛负压),必要时采用从事故放灰口放灰。
2)适当降低冷渣器用风,适当提高二次风量的比例,降低燃烧风量,保证炉内的燃料和床料在炉内有足够的停留时间,即增加内循环的时间和数量,降低旋风分离器的物料比例。
3)在燃烧工况突然改变导致循环被破坏时,应及时调整锅炉运行参数建立新的平衡。
4)加强对J阀风量配比的经验总结,寻找J阀各部分最优化参数,选择合适流化风量和松动风,建议在风量调定且回料正常时,不宜对该风量做随意变更。
料层差压不能控制的过于低。
当料层过于薄时,一次风量也比较大的时候,一次风所形成的向上托力大大的大于了料层的重力(也就是对一次风的阻力),那么炉内物料将被气流带走,形成了气力输送,就象仓泵输灰一样,那么此时锅炉运行是非常危险的,大量的一次风都从炉膛内吹走了(料层对一次风阻力大大的减小了)。
返料风所需的一次风大量减少,炉膛上部灰浓度大量增加,分离器收集的返料灰增加,返料器所返的灰增加、返料风却减小,将直接引起返料器堵灰,停止返料并有可能返料器内部结焦。
煤粒加入炉膛后,由于一次风气力输送作用被吹到炉膛出口,由旋风分离器收集而进入返料器中,进行燃烧,引起返料器内部高温结焦。
300MW CFB锅炉旋风分离器中心筒变形脱落问题分析

300MW CFB锅炉旋风分离器中心筒变形脱落问题分析旋风分离器是循环流化床锅炉的重要部件,分离器的分离效率直接关系到锅炉的安全经济运行。
旋风分离器中心筒变形下移,造成气体短路引起分离器分离效率下降,分离器中心筒脱落,影响了锅炉的安全经济运行。
本文针对这些问题,分析了原因并采取了一系列措施,取得了一定的效果。
标签:旋风分离器;中心筒变形;措施循环流化床锅炉的旋风分离器是循环流化床锅炉的核心部件之一,中心筒是连接安装在旋风分离器上部部件,即排气管。
它不仅排出分离后的烟气,与分离器的外筒体形成环形通道,进入分离器的烟气绕着中心筒旋转,在离心力和重力作用下,大部分灰粒被分离出来,送回炉膛,以保证燃料多次循环燃烧反应,含有细灰的烟气向上折转成为旋流,由中心筒排出进入尾部烟道。
1 300 MW CFB锅炉及其分离器内蒙古京泰电厂采用DG1089/17.45-II1 型锅炉,锅炉为循环流化床、亚临界参数,一次中间再热自然循环汽包炉、紧身封闭、平衡通风、固态排渣、全钢架悬吊结构、炉顶设密封罩壳。
锅炉主要由一个膜式水冷壁炉膛,三台汽冷式旋风分离器和一个由汽冷包墙包覆的尾部竖井(HRA)三部分组成。
2 分离器出现问题分析2.1 13分离器中心筒变形及参数变化中心筒变形的影响:(1)中心筒变形后,炉膛上部差压低,带来床温升高,回料器温度升高、分離器入口烟温升高。
(2)影响烟气流旋转速度和分布,导致分离效率下降,循环物料浓度降低,锅炉烟气飞灰含碳量升高,锅炉不完全燃烧损失增大,锅炉效率降低。
烟气中的固体颗粒增加还会使过热器和烟道受热面磨损加剧,影响锅炉的安全运行。
(3)中心筒严重变形引起的浇注料脱落,进而使中心筒与烟道接口处超温烧红。
脱落的浇注料引起回料器回料不畅,回料器振动。
具体参数变化如下:机组负荷315MW,13分离器中心筒脱落时参数有较为明显的波动,脱落前后参数变化如下:回料器入口静压由-0.5KPa突升至1.2KPa;分离器出入口差压由1369Pa降至1235Pa;回料器料位有波动,由22.5KPa降至20KPa后升高至25.5KPa,稳定约2分钟后又降至至21.6KPa左右达到平衡状态;伴随床压由5.6KPa降至4.5KPa,炉膛上部差压由1.15KPa降至0.99KPa,锅炉床温由942℃升高至958℃。
重油催化装置三级旋风分离器故障分析及改造

第46卷第2期2009年4月化 工 设 备 与 管 道PROCESS EQU IPM ENT &P I P I NG Vo l 46 N o 2A pr 2009重油催化装置三级旋风分离器故障分析及改造袁超, 丁杰(中国石化镇海炼化分公司,浙江宁波 315207)摘 要:结合重油催化装置2005年停工和2006年三旋改造情况,从第一再生器风量、催化剂性质、单管内部流场等方面分析了PSC 250型单管的失效过程。
阐述了单管改造原理,并提供改造前后数据对比,为三旋运行监控和故障判断提供了依据。
关键词:重油催化裂化; 三级旋风分离器; 单管中图分类号:TQ 051.8文献标识码:B文章编号:1009 3281(2009)01 0023 05Fault Anal ysis and Refor m for 3 Stage Cycl onei n H eavy O il Catal yzing Install ati onYUAN Chao , D ING Jie(SI N OPEC Zhenha iR efinery Branch ,N i ngbo 315207,China )Abstrac t : In comb i nati on w ith the shutdown i n 2005and t he refor m i n 2006of heavy o il ca talyzi ng i nstall a tion ,the fau lt ana l ysis f o r PSC 250p i pe is ca rried out w ith respect to t he a ir capacity o fN o .1regene rato r ,the cata l yst property and the fl ow fie l d i nsi de si ng le p i pe etc .T he refor m m echan is m o f si ng l e p i pe i s descri bed ,and the da ta ob tained be fore and after reform are co m pa red .T h i s paper prov ides the basis for supervisi ng t he ope ration o f 3 stage cyclone and deter m i n i ng the fau lt causes .K eywords : heavy o il cata l y zi ng and cracking ; 3 stage cyclone ; si ng l e p i pe收稿日期:2008 08 04; 修回日期:2008 11 03作者简介:袁超(1980 ),男,浙江宁波人,工程师。
循环流化床锅炉旋风分离器中的事故分析
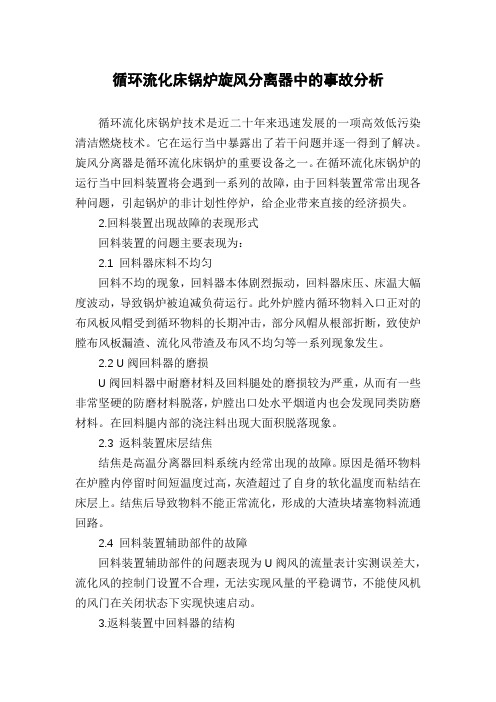
循环流化床锅炉旋风分离器中的事故分析循环流化床锅炉技术是近二十年来迅速发展的一项高效低污染清洁燃烧枝术。
它在运行当中暴露出了若干问题并逐一得到了解决。
旋风分离器是循环流化床锅炉的重要设备之一。
在循环流化床锅炉的运行当中回料装置将会遇到一系列的故障,由于回料装置常常出现各种问题,引起锅炉的非计划性停炉,给企业带来直接的经济损失。
2.回料裝置出现故障的表现形式回料装置的问题主要表现为:2.1 回料器床料不均匀回料不均的现象,回料器本体剧烈振动,回料器床压、床温大幅度波动,导致锅炉被迫减负荷运行。
此外炉膛内循环物料入口正对的布风板风帽受到循环物料的长期冲击,部分风帽从根部折断,致使炉膛布风板漏渣、流化风带渣及布风不均匀等一系列现象发生。
2.2 U阀回料器的磨损U阀回料器中耐磨材料及回料腿处的磨损较为严重,从而有一些非常坚硬的防磨材料脱落,炉膛出口处水平烟道内也会发现同类防磨材料。
在回料腿内部的浇注料出现大面积脱落现象。
2.3 返料装置床层结焦结焦是高温分离器回料系统内经常出现的故障。
原因是循环物料在炉膛内停留时间短温度过高,灰渣超过了自身的软化温度而粘结在床层上。
结焦后导致物料不能正常流化,形成的大渣块堵塞物料流通回路。
2.4 回料装置辅助部件的故障回料装置辅助部件的问题表现为U阀风的流量表计实测误差大,流化风的控制门设置不合理,无法实现风量的平稳调节,不能使风机的风门在关闭状态下实现快速启动。
3.返料装置中回料器的结构U型回料器由立管、布风板、松动室、回料室、风室、舌板等组成。
U型回料器的结构如图1所示。
4.返料器投运时的注意事项及处理措施分离器工作时分离下来的物料落入U型回料器立管,立管下方为松动风侧,以舌板为分界线,另一侧为流化风侧。
实际上,旋风分离器就是一个小型流化床。
在运行时,由于分离器分离下来的物料在立管内聚积,所以松动风侧的压力大于流化风侧的压力。
因此物料在松动风、流化风的作用下,依靠压差的作用顺利的进入料腿,物料经过回料腿进入炉膛进一步燃烧,从而完成整个物料循环过程。
旋风分离器及回料阀阻塞的现象及原因【2015.1.22】

一、旋风分离器及回料阀堵塞时的现象及原因
1.回料阀又称“返料器”,旋风分离器和回料阀都发生堵塞时的主要现象有:
(1)炉膛压力增大;
(2)床压下降【返料不及时】;
(3)尾部烟道负压增大【没有烟气流入】;
(4)烟气阻力增大【没有动力】;
(5)回料阀高料位报警;
(6)回料阀温度上升迅速。
(7)一次风量增大;
(8)汽温、汽压、负荷均下降。
注:我觉得分离器与回料阀阻塞是一个很矛盾的东西,一方面烟气出不去造成炉内压力增大,另一方面物料回不来造成床压减小;
2.常见原因:
(1)回料阀故障:①高压流化风量低,使回料阀堵灰;②风帽损坏,造成风室堵灰;③旋风分离器、立管或回料阀等处耐火保温材料脱落而影响返料,造成堵灰;
(2)回料立管有堵塞,大量的灰由分离器中心管逸出,中心管内壁严重磨穿;
(3)分离器内积灰、结焦;
(4)返料风和松动风的配风不合理;
(5)返料温度过高,已结焦;
(6)给煤中细颗粒比例较大,回料阀内燃烧强烈,造成堵灰结焦;
(7)煤质变化大;
(8)局部床温过低,给煤量过大,大量较细碳粒进入回料阀内强烈燃烧,造成结焦。
探析催化裂化装置旋风分离器机械故障的原因

探析催化裂化装置旋风分离器机械故障的原因摘要:旋风分离器系统在催化裂化装置中用于分离催化剂与油气或催化剂与烟气,是决定催化剂跑损程度的关键设备。
旋风分离器系统主要由旋风分离器、料腿和翼阀等组成,其操作条件比较苛刻,主要是操作温度比较高、入口颗粒浓度比较大。
旋风分离器在长时间的运行过程中会发生各种各样的故障,是FCCU中出现故障频率相对比较高的设备,也是影响装置长周期运行的主要因素之一。
关键词:催化裂化装置;旋风分离器;机械故障;原因1 工艺故障的参数分析1.1 入口速度旋风分离器是利用气流旋转对颗粒产生的离心力进行气、固两相分离的。
颗粒的离心力大小与旋风分离器的入口速度有直接关系。
通常入口速度越大,切向速度越高,离心力越大,分离能力越强,分离效率也越高。
入口速度很大时,内部旋转气流的湍流强度增大,造成颗粒的激烈扩散和反弹,细小颗粒易发生逃逸,使得分离效率下降,所以旋风分离器的性能曲线是个驼峰曲线,存在一个最佳入口速度范围。
若旋风分离器入口速度过高,不仅颗粒的扩散和反弹加剧,同时入口速度过高还会造成催化剂与器壁的激烈撞击导致催化剂的冲击破碎,细小催化剂含量增大,最后导致颗粒的逃逸量增大,旋风分离器的分离效率降低。
某催化裂化装置再生器一级旋风分离器入口速度上限为21 m/s,实际达到25~26 m/s;二级旋风分离器入口速度上限为24 m/s,实际达到28~30 m/s。
此时催化剂的扩散、碰撞、返混、弹跳急剧增大,同时受到较大的冲击破碎,跑损催化剂中粒径为0~40μm颗粒的质量分数超过30%,催化剂耗损达1.2 kg/t。
在旋风分离器存在冲击破碎时,这种跑损催化剂的粒径分布特点是催化剂细粉含量增大,在催化剂粒径>5μm处出现峰值,颗粒粒径呈双峰分布[1,5]。
因旋风分离器的入口速度原因产生的催化剂跑损可以通过装置的操作工艺参数进行校核,如加工处理量、再生烟气量等参数的计算,另一方面旋风分离器的入口速度变化直接影响到其压降变化。
旋风分离器原理和结构
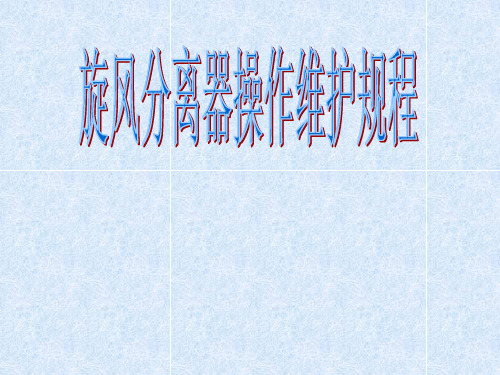
五、维护保养
5.1准备工作 • 清洗维护前向调控中心申请,同意后方可
实施清洗维护操作。 • 准备安全警示牌、可燃气体检测仪、隔离
警示带等。 • 检验分离器和排污罐区周围情况,杜绝一
切火种火源。 • 检验、核实排污罐液面高度。 • 准备有关工具。
五、维护保养
5.2检修维护操作 • 关闭分离器进出口球阀。 • 打开分离器放空阀将压力下降到0.2Mpa左右,打开排污
体声音,判明排放旳是水、固体或是气,一旦听到气 流声,立即关闭排污阀。 设备区、排污罐附近禁止一切火种。 作好排污统计,以便分析输气管内天然气气质和拟定 排污周期。
三、操作措施
4.3排污周期
观察站场分离器液位计,根据液位计旳显示 值来拟定排污周期。
分离器前后压差不小于0.2MPa时进行排污操 作
污。 • 排污完毕后再次检验各阀门状态是否正确。 • 验漏 • 整顿工具和收拾现场。 • 向调控中心报告排污操作旳详细时间和排污成
果。
三、操作措施
4.3排污时旳注意事项
开启阀套式排污阀应缓慢平稳,阀旳开度要适中。 关闭分离器阀套式排污阀应迅速,防止天然气冲击波
动。 操作排污阀带压排污时,要用耳仔细诊听排污管内流
四、常见故障及处理
1、 法兰或连接处泄漏运营或升压过程中,使用皂 液法检验,发觉泄漏时必须立即切换流程,停 运事故分离器,然后进行放空排污操作,压力 降为零后方可进行维修操作。
2、 分离器前后压差增大或流量减小; 运营过程中,因为天然气杂质增多或固体颗粒 较多,引起分离器前后压差增大,当超出 0.2MPa时,表白分离器内部出现堵塞,应及时 停运进行检修。若2台以上分离器同步运营时, 当某台分离器后旳流量计旳流量值比其他支路 小30%(此设定值可在运营时调整)时,表白 这路分离器可能堵塞,需进行检修。
催化旋风分离器机械故障的原因分析

CHENGSHIZHOUKAN 2019/15城市周刊90催化旋风分离器机械故障的原因分析连 仲 中国石油抚顺石化公司石油二厂罗 茜 中国石油抚顺石化公司烯烃厂摘要:近些年来,随着经济发展,现代化建设水平也突飞猛进。
催化裂化装置旋风分离器的操作条件比较苛刻,其温度比较高、分离催化剂的浓度大。
旋风分离器在长时间运行过程中承受各种机械载荷、高温和压力载荷、介质腐蚀,尤其是颗粒的冲蚀和摩擦等作用,某些零部件的功能不可避免会逐渐失效,最后发生各种各样的机械故障,例如冲蚀、磨损、断裂、堵塞等。
这些故障是影响催化裂化装置长周期运行的主要因素之一。
当旋风分离器发生机械故障后,主要的表现形式是分离效率下降,出口催化剂浓度上升,催化剂跑损量增大,压力降和压力也随之发生变化。
这些外部的表现形式与机械故障之间存在着直接的联系,可以通过旋风分离器跑损催化剂的浓度、粒度变化、入口速度和压力降的增大或减小、压力的波动等,对故障做出诊断,确定产生故障的原因和位置,为后续故障的消除提供支持。
关键词:催化旋风分离器;机械故障;原因分析催化裂化工艺中旋风分离器被用来进行催化剂与油气或与烟气的分离,是保证催化裂化装置长周期安全稳定运行的主要设备。
旋风分离器在高温和高浓度的环境下长时间工作有可能发生各种机械故障,例如冲蚀、磨损、断裂、堵塞等,这些故障是导致分离效率下降,催化剂跑损量增大,压力降减小等的主要原因之一。
这些不同的机械故障所引起的操作参数变化和跑损催化剂的物性变化是有所不同的,有些参数是突变的,有些是渐变的,还有一些是波动变化的,这些变化与机械故障之间存在着密切联系。
可以通过跑损催化剂的浓度和粒度的变化,旋风分离器入口速度和压力降的变化对旋风分离器产生机械故障的原因进行诊断和分析。
一、机械故障和催化剂跑剂催化裂化旋风分离器系统通常是由多组多级并联旋风分离器、翼阀料腿、吊柱和拉杆支架等构成。
旋风分离器系统长期处于高浓度气固两相流的流动环境中,一方面承载着不稳定两相流的诱导振动,另一方面受到流动颗粒的冲蚀磨损。
催化裂化再生器旋风分离器失效分析与对策

催化裂化再生器旋风分离器失效分析与对策刘初春,樊继磊,李德生(大连西太平洋石油化工有限公司,辽宁省大连市116600)摘要:介绍了大连西太平洋石油化工有限公司催化裂化装置因第一再生器二级旋风分离器衬里脱落堵塞料腿导致再生器催化剂跑损,简述了催化剂跑损原因的判断过程,分析了催化剂跑损对其循环流化、管线设备以及各系统的影响并提出了应对措施。
通过将新鲜剂加入位置由第一再生器改至第二再生器,并将跑损的催化剂补充回再生系统等调整,将系统平衡剂平均粒径稳定在85~90μm,目的产品收率明显提高,品质改善,其中液化石油气收率由16.0%提高至16.5%以上,汽油收率由40%~41%提高至43%以上,油浆密度由1.04g/cm3提高至1.08g/cm3,油浆收率由10.4%降至9.5%。
实现了装置稳定操作,改善了产品分布,保证了装置大负荷生产。
关键词:催化裂化装置 再生器 旋风分离器 失效 料腿堵塞 催化剂跑损 大连西太平洋石油化工有限公司催化裂化装置原设计负荷2.0Mt/a,2001年对装置进行了扩能改造,改造后处理能力为2.8Mt/a。
装置反应系统采用折叠式提升管反应器,再生系统采用两段再生工艺,第一再生器贫氧,第二再生器富氧,沉降器与第一再生器同轴布置,第一再生器与第二再生器并列式布置。
与多数两段再生催化裂化装置不同,该装置第一再生器和第二再生器均设有三级旋风分离器(三旋)和烟机。
2019年4月1日—5月11日进行了装置停工大检修,检修期间更换了第二再生器一级旋风分离器(一旋)、二级旋风分离器(二旋)及沉降器内提升管反应器出口快分。
5月11日装置恢复生产,至5月16日反 再系统藏量稳定且正常。
5月17日反 再系统藏量开始下降,需要非正常向系统补入平衡剂才能维持系统藏量稳定,连续跟踪确认催化剂的自然跑损量为16t/d,新鲜剂单耗达到1.85kg/t原料。
1 再生器催化剂跑损原因判断及应对处理催化剂出现超常跑损后,装置紧急采取多补充新鲜催化剂和平衡剂维持系统藏量,同时查找催化剂跑损原因。
旋风分离器斜三通管损坏原因分析及措施

旋风分离器斜三通管损坏原因分析及措施旋风分离器斜三通管是热力发电厂气力循环系统中常见的换热器,其损坏对整个循环系统的运行会产生严重影响。
因此,对旋风分离器斜三通管的损坏原因进行深入分析,并给出相应的措施,是确保热力发电厂气力循环系统的安全运行的重要依据。
旋风分离器斜三通管损坏的原因主要有以下几个方面:一是材料质量问题。
旋风分离器斜三通管由不锈钢制成,如果使用非优质材料,容易产生锈蚀而损坏斜三通管。
二是焊接质量问题。
焊接时如果不按照正确的焊接方式,或采用非标准焊材,会造成焊缝不牢固,甚至漏焊等质量问题,进而导致斜三通管出现损坏象。
三是安装质量问题。
如果斜三通管的安装不当,会导致管道的弯曲变形,加速斜三通管损坏。
四是操作质量问题。
在斜三通管操作过程中,如果操作不当,会导致斜三通管出现破损、松动等现象,从而产生损坏。
依据以上分析,为了确保旋风分离器斜三通管的安全使用,应当采取一定的措施,如下:(一)使用材料要求有效的预防损坏的主要措施之一是使用优质的材料,采用高质量的304不锈钢,这样可以大大减少斜三通管的锈蚀情况。
(二)确保焊接质量所有的焊接作业环节都应当按照焊接标准进行,选择标准焊材,拆卸或连接管件之前,应当检查质量,确保每一处焊缝都是完全牢固。
(三)正确安装斜三通管的安装要根据设计和操作要求来进行。
安装好后,要按时进行维护保养,做到及时采取措施修复和补强,以确保斜三通管支架的牢固度。
(四)合理操作在操作斜三通管时,要严格按照操作规程进行,加强安全操作,严格按照技术要求进行安装,尽量减少斜三通管的破损、移动和振动等现象的发生。
总之,旋风分离器斜三通管的损坏,主要是由于材料质量、焊接质量、安装质量及操作质量等问题引起的。
为此,应当采取有效的措施,完善斜三通管的质检管理,以确保其安全可靠,维护热力发电厂气力循环系统的稳定性。
旋风分离器斜三通管损坏原因分析及措施

旋风分离器斜三通管损坏原因分析及措施旋风分离器作为热能互换设备的重要组成部分,其工作的稳定性和可靠性直接关系到整个系统的安全运行。
近期由于旋风分离器斜三通管受损,系统的运行受到了一定的影响,为了确保系统安全运行,本文对于旋风分离器斜三通管受损原因进行分析并提出了相应的改善措施。
一、旋风分离器斜三通管损坏原因1、质选择错误:旋风分离器斜三通管若采用不合格的材料,或者不是防腐蚀要求的材质,则容易发生腐蚀,影响正常使用。
2、毒物质作用:旋风分离器斜三通管容易受到有毒物质的侵蚀作用,如果使用条件不当,容易出现断裂、损坏等情况。
3、行环境:环境因素是影响斜三通管损坏的重要因素,如温度过高、湿度过大等,都会导致斜三通管受损。
4、行条件不当:斜三通管在运行中,如果条件不当的话也会发生损坏,例如操作不当,过度使用等。
二、风分离器斜三通管改善措施1、择合格的材料:对于旋风分离器斜三通管的材料,要求选择防腐蚀的合格材料,以确保在环境各种变化下,保证斜三通管使用寿命。
2、免有毒物质:在使用旋风分离器斜三通管时,要避免接触有毒物质,以免发生腐蚀,确保正常使用。
3、制环境:环境受到良好的控制可以有效防止斜三通管受损,如控制温度和湿度,改善施工环境等。
4、严格操作:只有在正确的操作条件下,才能使斜三通管使用得到最佳状态,不能过度使用,以免损坏斜三通管。
综上所述,旋风分离器斜三通管的损坏原因主要有材质不良,受有毒物质侵蚀,操作不当,以及环境因素。
要保证旋风分离器斜三通管能够正常使用,上述几点在实际操作中都要注意,只有正确的措施和方法才能有效地防止斜三通管的损坏。
为此,本文还针对此类情况建议如下几点措施,正确选择材料,避免有毒物质侵蚀,控制环境,严格操作等,这些措施和方法都有利于降低斜三通管的受损率,保证系统的正常运行。
总之,旋风分离器斜三通管的正常使用与维护是十分必要的,正确选择材料和环境以及严格操作,都有助于减少斜三通管受损,保证旋风分离器的稳定性和可靠性,以保证系统的安全运行。
循环流化床锅炉旋风分离器事故分析与改造措施

循环流化床锅炉旋风分离器事故分析与改造措施【摘要】旋风分离器效率的提高是循环流化床锅炉经济运行的关键,其设备的长期完好运转是循环流化床锅炉稳定运行的关键。
通过对旋风分离器常见事故的分析、总结、提出并实施改造,为循环流化床锅炉满负荷运行提供保证。
【关键词】旋风分离器中心筒分离效率改造措施1 前言循环流化床锅炉的分离机构是循环流化床锅炉的关键部件之一,其主要作用是将大量高温固体物料从气流中分离出来送回燃烧室,以维持燃烧室的快速流化状态,保证燃料和脱硫剂多次循环,反复燃烧和反应,使锅炉达到理想的燃烧效率和脱硫效率。
黑化集团热电分厂的四台济锅生产的YG-75/3.82-M1型循环流化床锅炉采用高温绝热旋风分离器和悬挂中心筒,在运行中出现大量事故。
近几年在实践中对事故的不断分析总结和对设备的不断改造,使锅炉能够长期安全高效稳定运行。
2 旋风分离器中心筒变形脱落的改造措施2.1 问题的提出锅炉投运初期,运行一年以后,6#炉发现旋风分离器处差压增大,分离效率下降,锅炉负荷骤减。
停炉检查发现锅炉中心筒出口处筒壁变形向内突出,四个吊挂开裂两个,造成筒体倾斜。
如继续运行,中心筒就会落入分离器椎体内。
2.2 原因分析中心筒出口与旋风分离器顶棚直接接触,在锅炉启炉和运行中中心筒和分离器顶棚受热膨胀,相互挤压使筒体变形。
进入旋风分离器的烟气一部分由变形处短路,分离效率降低,筒体变形愈加严重。
中心筒是由四根750×80×8mm材料为1Cr25Ni20Si2钢板悬吊,一侧焊接在中心筒外壁上,另一侧焊接在旋风分离器出口外护板上。
在950℃和高速烟气作用下轻微摆动,焊口氧化开裂,造成倾斜和脱落。
2.3 改造措施(1)改变中心筒的结构和材质。
原中心筒由δ8mm的1Cr25Ni20Si2钢板卷制改为δ10mm的0Cr25Ni20钢板卷制,提高其抗压强度和耐热温度。
在筒体外壁上中下三处分别增加了防变形的加强环,出口加强环内焊有8个三角形的加强板。
天然气场站旋风分离器异响分析及处理

天然气场站旋风分离器异响分析及处理摘要:旋风分离器是利用离心力分离气流中固体颗粒或液滴的设备。
基本原理是靠气流切向引入造成的旋转运动,使具有较大惯性离心力的固体颗粒或液滴甩向外壁面分开的一种工业常用分离设备。
2013年,XB管道公司采购了国产厂家(以及简称:HT公司)生产的18台国产旋风分离器,设备投用后连续发生异响,甚至有设备在2次返修后还存在异响,管道公司委托第三方机构调查分析设备异响原因并出具了指导性意见,工厂根据调查分析结论和意见连续调整了设备返修制造参数,最终消除了设备异响问题。
关键词:旋风分离器异响返修分析处理一、设备基本信息2013年,某管道公司天然气场站采购了HT公司制造的18台国产旋风分离器设备,该厂使用的旋风子由上海AL公司参考美国PL公司产品样式制作,采用了焊接样式代替了一体化铸造样式。
该批旋风分离器基本参数为:设计压力12.6MPa,操作压力8.44MPa,设计温度-30~80℃,操作温度-10~60℃,设计年限20年,腐蚀裕量2mm,单台处理量765000Nm³/h,设备压降≤0.05MPa,水压试验压力18MPa,筒内径1480mm,筒体和封头材质16MnDR,设备进出气口内径均为565mm。
设备投产运行不久,旋风分离器陆续发生异响。
二、事件经过2016年8月至2017年1月期间,HT公司返厂第一台编号为CYC3202的旋风分离器(以下简称:CYC3202分离器),投用一个月后再次出现异响。
2019年XB管道公司组织拆解了CYC3202分离器,发现旋风分离器位于进气口侧、旋风管与下管板连接处、旋风管与旋风子连接处存在12处断裂或裂纹。
随即组织召开了多次专家会,结合管道断口分析,最终确定了设备异响的原因为:旋风组件由于管板和旋风管厚度问题,导致在内外压差较大的状况下,旋风组件上下管板和旋风管强度不足,管板沿旋风管轴向产生振动,旋风分离器旋风组件与筒体间由于存在断续焊接和焊缝熔深不足,轴向振动导致管板焊缝断裂,在轴向振动和气流冲击的共同作用下,旋风管的振动声和断裂旋风管碰撞产生的敲击声是异响。
高温旋风分离器中心筒运行中产生的问题与解决方法

高温旋风分离器中心筒运行中产生的问题与解决方法山东省阳光工程设计院马会芹司丽丽250013摘要:针对循环流化床锅炉高温旋风分离器中心筒在使用中出现的各种问题,分析了产生问题的原因,并提出了解决方法。
关键词:旋风分离器中心筒分离效率磨损变形1中心筒简介旋风分离器是循环流化床锅炉的核心部件之一,而中心筒是安装在旋风分离器上的组成部件,即排气管。
它不仅排出分离后的烟气,更与分离器的外筒体形成环形通道,进入分离器的烟气绕着中心筒旋转,在离心力和重力和作用下,大部分灰粒被分离出来,含有细灰的烟气向上折转成为旋流,由中心筒排出进入尾部烟道。
目前中心筒有两种制作工艺:一种是用耐热不锈钢板卷制而成,一种是采用铬镍合金铸造而成的铸件中心筒。
2中心筒运行中产生的问题两种制作工艺制造的中心筒都能基本达到使用要求。
但在实际运行中,用耐热不锈钢板卷制的中心筒容易发生变形,影响烟气流旋转速度和分布,导致分离效率下降,循环倍率降低,锅炉烟气飞灰中的含碳量升高,锅炉不完全燃烧损失增大,锅炉效率降低,使电厂经济性下降。
烟气中的固体颗粒增加还会使过热器和烟道受热面磨损加剧,影响锅炉的安全运行。
铸造的中心筒则由于材质或制造工艺水平低,使铸造的中心筒在运行中出现裂纹、烧损、炭化现象,同样会影响锅炉的安全经济运行。
各锅炉厂的中心筒均不同程度的存在类似问题。
济南锅炉厂2000年生产的75t/h循环流化床锅炉,分离器采用高温旋风分离器。
用不锈钢板卷制的中心筒,在运行中中心筒出现上、下口及筒体变形严重,连接板断裂,十字撑开焊脱落,经过校正中心和重新固定方重新投入使用,坚持运行了8年。
铸造的中心筒问题更为严重,运行几个月就发生变形、炭化烧损现象,严重的甚至整个中心筒烧毁损坏了大半,烧毁的碳化物残片堵塞返料器,迫使锅炉停炉;而变形的中心筒影响烟气流通,分离效率下降,过热器严重磨损直至爆管被迫停炉。
中心筒插入分离器的深度对旋风分离器的分离效率起着决定性的作用。
- 1、下载文档前请自行甄别文档内容的完整性,平台不提供额外的编辑、内容补充、找答案等附加服务。
- 2、"仅部分预览"的文档,不可在线预览部分如存在完整性等问题,可反馈申请退款(可完整预览的文档不适用该条件!)。
- 3、如文档侵犯您的权益,请联系客服反馈,我们会尽快为您处理(人工客服工作时间:9:00-18:30)。
J阀(旋风分离器)故障(此故障主要出现在国产化的CFB锅炉)。
J阀(旋风分离器)故障主要现象J阀入口静压波动大导致J阀回料不连续,床压、床温出现大幅度的波动,严重时破坏外循环,使尾部受热面积灰严重,造成尾部烟道再燃烧,损坏空预器。
J阀(旋风分离器)故障主要原因1)旋风分离器回料不正常。
旋风分离器因灰位较高而影响了分离器的分离效果,从而使一定量未分离灰进入烟道造成空预器积灰严重,引起J阀入口静压波动。
2)过高的循环倍率造成J阀循环灰量过大,超出J阀流通能力。
3)燃烧工况的突然改变破坏了J阀的循环。
4)流化风配比不恰当,J阀回料未完全流化。
J阀(旋风分离器)故障采取措施1)发现回料不正常时,及时对旋风分离器的风量进行调整,必要时降低锅炉负荷;尾部烟道积灰严重时,加强对其吹灰(注意控制炉膛负压),必要时采用从事故放灰口放灰。
2)适当降低冷渣器用风,适当提高二次风量的比例,降低燃烧风量,保证炉内的燃料和床料在炉内有足够的停留时间,即增加内循环的时间和数量,降低旋风分离器的物料比例。
3)在燃烧工况突然改变导致循环被破坏时,应及时调整锅炉运行参数建立新的平衡。
4)加强对J阀风量配比的经验总结,寻找J阀各部分最优化参数,选择合适流化风量和松动料层差压不能控制的过于低。
当料层过于薄时,一次风量也比较大的时候,一次风所形成的向上托力大大的大于了料层的重力(也就是对一次风的阻力),那么炉内物料将被气流带走,形成了气力输送,就象仓泵输灰一样,那么此时锅炉运行是非常危险的,大量的一次风都从炉膛内吹走了(料层对一次风阻力大大的减小了)。
返料风所需的一次风大量减少,炉膛上部灰浓度大量增加,分离器收集的返料灰增加,返料器所返的灰增加、返料风却减小,将直接引起返料器堵灰,停止返料并有可能返料器内部结焦。
煤粒加入炉膛后,由于一次风气力输送作用被吹到炉膛出口,由旋风分离器收集而进入返料器中,进行燃烧,引起返料器内部高温结焦。
在通过冷渣机控制料层时,应尽量保持平稳增减,避免料层的过薄过厚,都将不利于锅炉的经济、安全运行。
旋风分离器不改变结构,提高收集效率,只能依靠入口烟速提高和烟气含灰量提高。
旋风分离器提高了收集效率,可以捕捉到更多的细灰进入返料器,由返料器返入炉内平仰床温。
该炉的分离器是采用高温绝热旋风分离器,左右侧各一只。
旋风分离器的收集效率直接影响着收集的返料灰的多少,影响着锅炉经济运行。
旋风分离器可以满足锅炉的运行,但我们也认为二只分离器效率不一样,由于床温热电偶已不准确,我们已无法分辨出那一侧的温度高和低,但二只分离器中心筒出口温度,也就是高温过热器前烟温始终存在差异,左侧高过前烟温高于右侧高过前烟温50℃左右,左侧低过前烟温高于右侧低过前烟温20℃左右,左侧省煤器前烟温高于右侧省煤器前烟温十几度,直到排烟温度左右差不多,烟道内左侧烟温普通高于右侧烟温,为什么?这个问题我们时常在思考,有个不成熟的想法:认为左侧分离器效率低于右侧分离器效率,左侧旋风分离器分离不彻底,使得一些高温细灰排至烟道内,至使左侧烟温高。
该U型自平衡返料器,我有个疑问,两侧的返料风室总是相差0. 7 kpa ~0.8 kpa左右,是热工仪表误差,还是真的存在风室风压差,返料风有大小?我们争取在以后停炉检查中弄明白这个问题。
密相区中呈现的是缺氧燃烧,稀相区中呈现的是过氧燃烧,是由二次风补充氧气而产生的,也是为了充分燃烧。
循环流化床锅炉燃烧调整的原则在一定的负荷区,在“勤放、少放、稳放”灰渣稳定流化高度的前提下,以床温定风量,以炉膛物料浓度(即炉膛差压值)定锅炉出力;以返料温度、旋风筒进口负压控制炉膛物料浓度;以炉膛下部压力为0负压运行定引风;以放渣、放灰量定燃煤配比。
循环流化床锅炉燃烧调整中最基本的控制点为:床体温度、返料温度、料层差压、炉膛差压、炉膛下部压力及旋风筒进口负压。
其控制参数关系图如下:在负荷一定时:循环灰是锅炉燃烧的热载体,积累到一定程度后,锅炉方可转入正常运行状态。
否则一味加煤赶汽压带负荷,易造成燃烧失常,返料器二次燃烧,超温结焦。
料层差压的控制:料层差压是风室压力与密相区上部压力的差值。
一定风量下合适的料层厚度,是床料良好流化的前提,在运行中要保持适当而稳定的料层差压,为提高煤的燃烧速度,料层差压应控制在8.0~9.0kPa,可通过炉底放渣来实现。
物料浓度的控制:一定的物料浓度对应一定的炉膛差压值,影响制约着锅炉出力。
维护适量稳定的物料浓度是锅炉运行的关键,炉膛差压指炉膛下部压力与炉膛上部压力的差值,通过U型阀返料器底部放灰来控制。
物料浓度过大,返料器不能形成良好的流化工况,极易造成旋风筒聚灰堵塞。
物料浓度过小或一次放的过多,锅炉出力下降,床体温度上升,煤粒燃烧推迟,返料温度也上升易超极限,造成返料器超温结焦。
正常运行中应根据燃煤灰分的高低控制U型阀返料器放灰量,控制旋风筒进口负压不大于700Pa。
断煤及料层薄尤应注意引风不能偏大及给煤量的调整,预防返料中止。
体现物料浓度是否足够,原则上掌握:低负荷运行时,床体温度略高于炉膛上部温度。
中负荷区以上负荷运行时,床温度接近或略高于炉膛上部温度。
增加负荷时应当先少量增加一次风量和二次风量,再增加给煤量,使炉膛差压逐渐增加,然后再逐渐加风加煤交错进行,直到所需出力。
减负荷时,应先减少给煤量,再适当减少一次风量和二次风量,并慢慢地放掉一部分循环灰,以降低炉膛差压,直到所需的出力为至。
锅炉正常运行中,应重点把握炉膛灰浓度的控制及一次风不低于最低安全流化风量两个问题。
防结焦:循环流化床锅炉在不同部位,因不同因素均可导致结焦:在炉膛中:主要致焦因素是煤质和运行,本文不列为重点叙述。
在料腿和返料器中,流通截面最小,汇集了高温循环灰和煤渣,从降温、防止空气进入、防止烟气回窜三方面防止结焦。
降温措施是水冷结构;防止空气进入,措施是防漏和运行调节;防止烟气回窜措施是精确实现设计通道的尺寸。
所以此处防焦的关键一是运行管理,二是施工安装。
在旋风分离器中:旋风分离器的内壁安装有防磨内衬,外壁安装有保温材料,具有高蓄热性,在近于燃烧室的温度下运行,易于二次燃烧而愈发提高分离器内部的温度,一旦超过灰分的变形温度时,即造成结焦。
防磨内衬若施工不良发生局部塌落,塌落的大块成为碳粒的聚集体,形成结焦堵塞。
旋风分离器中存在冷风渗入的现象,此区域的锥体下端和灰渣出口均可能漏入冷风,则相当于引入二次风,助长二次燃烧致结焦。
防止上述两项结焦因素的措施是做好安装施工。
CFB锅炉除了需要监视风烟系统的压力外,还需要监视与控制床压、J阀各部位风压、冷渣器各室风压、炉膛上中下部压力等,以判断燃烧、给煤、排渣、物料再循环等系统的运行是否正常。
基于循环流化床的燃烧机理,需要合理的控制炉膛差压、料层差压、流化风量、循环倍率、蒸发量。
如果炉膛差压过低,有可能是返料量不够,分离效率低造成的。
这将同时造成尾部受热面的加速磨损,过热器、省煤器的磨损泄漏;如果料层差压偏低,则炉膛蓄热量少,一旦给煤出现问题,容易灭火。
如果料层差压偏高,则需较大的流化风量,又增加动力消耗和磨损。
事实证明,超负荷运行,得不偿失,将付出巨大的代价。
根据实际运行情况来看,循环流化床锅炉的负荷最好不要超过额定负荷,以控制在80~95%为理想。
在此负荷下,操作稳定,效率较高,磨损较轻,运行周期较长。
因为,在超负荷情况下,循环倍率增加,流化风量加大,存在后燃现象,造成后部高温,甚者造成返料器结焦,危及锅炉的安全运行。
当床层整体温度低于灰渣变形温度而由于局部超温或低温烧结而引起的结焦称低温结焦,低温焦块是疏松的带有许多嵌入的未烧结颗粒。
床层整体温度水平较高而流化正常时所形成的结焦现象称高温结焦,高温焦块表面上看基本上是熔融的,冷却后呈深褐色并夹杂少量气孔。
运行中的床温、床压和流化都正常情况下出现的缓慢长大的焦块称渐进性结焦,这种结焦是较难察觉的。
炉内结焦是由于高温结焦、低温结焦、渐进性结焦和油煤混燃时间较长以及流化不正常引起的结焦,不论是哪种原因引起的结焦,一旦渣块在床料中存在并随着时间的推移,焦块将象滚雪球似的越滚越大,造成流化更加困难,即结焦影响流化,流化不良易结焦,结果是堵塞排渣管,最后被迫停炉。
床温偏高和炉内流化工况不良是造成结焦的两个最主要的原因。
结焦无论在点火或在正常运行调整中都可能发生,原因也有多种;它不仅会在启动过程或压火时出现在床内,也有可能出现在炉膛以外如旋风分离器的回料褪及回料阀内,灰渣中碱金属钾、钠含量较高时较易发生。
返料温度是指通过返料器送回到燃烧室中的循环灰的温度,它可以起到调节料层温度的作用。
采用高温分离器的循环流化床锅炉,一般返料温度低于料层温度20-30℃,可以保证锅炉稳定燃烧,同时起到调整燃烧的作用。
在锅炉运行中必须密切监视返料温度,出现后燃温度过高有可能造成返料器内结焦,运行时应控制返料温度最高不能超过950℃。
返料温度通过调整给煤量,一、二次风量和返料风量都可以调节,如温度过高,可适当减少给煤量并加大一、二次风量和返料风量,并根据现象判断返料器有无堵塞现象,及时清除,确保返料器正常工作。
料层差压是反映燃烧室料层厚度的参数。
通常将所测得的风室与燃烧室上界面之间的压力差值作为料层差压的监测数值,在运行中都是通过监视料层差压值来得到料层厚度大小的。
料层厚度越大,测得的差压值亦越高。
在运行中,料层厚度大小会直接影响锅炉的流化质量,如料层厚度过大,有可能引起流化不好造成炉膛结焦或灭火。
一般来说,料层差压应控制在7500-9000Pa之间。
料层差压可以通过调节炉底冷渣器转速快慢的方法来调节。
在使用过程中,我们根据所燃用煤种设定料层差压的上限和下限分别为8800Pa和7800Pa作为排放底料开始和终止的基准点。
炉膛差压是反映炉膛内固体物料浓度的参数。
通常将所测得的燃烧室上界面与炉膛出口之间的压力差作为炉膛差压数值。
炉膛差压值越大,说明炉膛内的物料浓度越高,炉膛的传热系数越大,则锅炉负荷可以带得越高,因此在锅炉运行中应根据所带负荷的要求,来调节炉膛差压。
而炉膛差压则通过返料器下的放灰管排放的循环灰量的多少来控制,一般炉膛差压控制在500-1500Pa之间。
我们根据燃用煤种的灰份和粒度设定1300-700Pa 作为开始和终止循环物料排放的基准点。
此外,炉膛差压还是监视返料器是否正常工作的一个参数。
在锅炉运行中,如果物料循环停止,则炉膛差压会突然降低,因此在运行中需要特别注意。
运行中要加强返料器床温的监视和控制。
一般返料器处的床温最高不宜大于950℃。
当返料器床温升得太高时,应减少给煤量和负荷,查明原因后消除。
Y[qBK9运行中监视料层差压及炉膛差压。
正常运行中维持炉膛差压约500~1500Pa之间,料层差压约7000~9500Pa之间。