钒钛磁铁精矿一步煤基直接还原—熔分的研究
钒钛磁铁矿直接还原过程中钛酸镁生成及机理研究
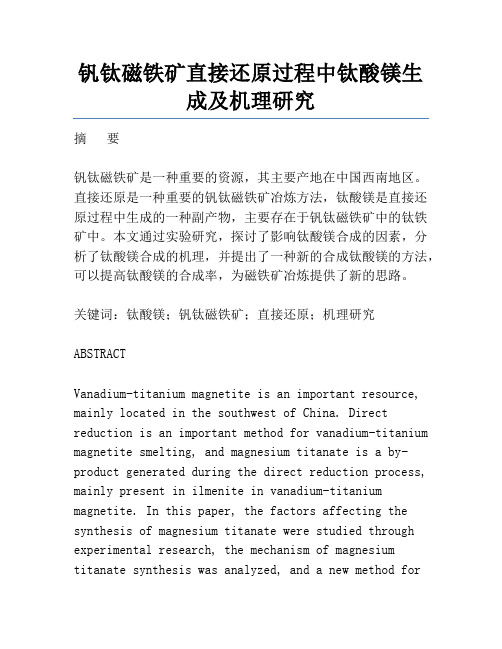
钒钛磁铁矿直接还原过程中钛酸镁生成及机理研究摘要钒钛磁铁矿是一种重要的资源,其主要产地在中国西南地区。
直接还原是一种重要的钒钛磁铁矿冶炼方法,钛酸镁是直接还原过程中生成的一种副产物,主要存在于钒钛磁铁矿中的钛铁矿中。
本文通过实验研究,探讨了影响钛酸镁合成的因素,分析了钛酸镁合成的机理,并提出了一种新的合成钛酸镁的方法,可以提高钛酸镁的合成率,为磁铁矿冶炼提供了新的思路。
关键词:钛酸镁;钒钛磁铁矿;直接还原;机理研究ABSTRACTVanadium-titanium magnetite is an important resource, mainly located in the southwest of China. Direct reduction is an important method for vanadium-titanium magnetite smelting, and magnesium titanate is a by-product generated during the direct reduction process, mainly present in ilmenite in vanadium-titanium magnetite. In this paper, the factors affecting the synthesis of magnesium titanate were studied through experimental research, the mechanism of magnesium titanate synthesis was analyzed, and a new method forsynthesizing magnesium titanate was proposed. The proposed method can effectively increase the synthesis rate of magnesium titanate and provide a new idea for magnetite smelting.Keywords: Magnesium titanate; Vanadium-titanium magnetite; Direct reduction; Mechanism research一、引言钒钛磁铁矿是一种重要的铁矿石资源,其中含有大量的钛、钒等有价元素。
钒钛铁精矿转底炉直接还原-电炉熔分工艺与理论研究的开题报告

钒钛铁精矿转底炉直接还原-电炉熔分工艺与理论研究的开题报告一、选题背景及研究意义钒钛铁精矿是一种重要的非金属矿产资源,具有广泛的应用前景。
其中,钒元素是一种重要的金属元素,广泛应用于冶金、化工、航天等领域。
目前,大多数钒钛铁精矿采用的是传统的炉法冶炼技术,如炉渣碱性熔锌法、氯化法等,但存在着成本高、排放量大等问题。
因此,针对这些问题,本研究将提出一种新型的钒钛铁精矿转底炉直接还原-电炉熔分工艺。
该工艺采用了底吹氧气的还原技术,将钒钛铁精矿还原成金属钒和钛的矿物,然后进行电炉熔分,将钒和钛分离开来,达到提高产率、降低成本和污染排放的目的。
二、主要研究内容1. 钒钛铁精矿转底炉直接还原技术研究本研究将结合国内外的研究成果,综合分析各种底吹氧气还原技术的优缺点,选定最佳的工艺参数,确定适宜的还原温度、还原时间、氧气流量等条件。
2. 钒的电炉炼制技术研究通过对钒的物理化学性质和电炉炼制原理的分析,确定钒的熔点、氧化还原平衡控制点,探讨电炉炼制技术的工艺参数。
3. 钛的电炉炼制技术研究本研究将重点研究钛的电冶炼技术,探讨钛的熔点和熔白化还原的控制条件,确定电炉炼制工艺的最佳参数。
4. 工艺流程设计与优化通过对各个环节的研究,建立钒钛铁精矿转底炉直接还原-电炉熔分的工艺流程,并对每个环节的技术参数进行优化,减少废气、废水和固体废物排放,达到环保的目的。
三、研究思路和方法本研究将采用实验室对原材料和硫酸钛矿的化学组成和物理性质进行分析,确立钒和钛的还原控制点和熔点。
同时,采用热重分析、物理力学测试等实验手段,研究钒和钛的熔白化还原过程和机理。
在试验基础上,开展工艺流程设计和参数优化等理论研究。
四、预期成果1. 建立钒钛铁精矿转底炉直接还原-电炉熔分的工艺流程,并研究优化各个环节的技术参数,提高资源利用率。
2. 阐明钒和钛的熔白化还原过程和机理,为钒、钛的电炉炼制提供技术支撑。
3. 减少废气、废水和固体废物排放,达到环保的目的。
新西兰钒钛海砂磁铁矿冶炼工艺分析

第45卷第4期2017年8月现代冶金Modern M etallurgyV ol. 45 No. 4A u g. 2017新西兰钒钛海砂磁铁矿冶炼工艺分析李志强,张洋(南京钢铁股份有限公司,江苏南京210035)摘要:介绍了新西兰机钬海砂磁铁矿冶炼工艺,并与传统高炉炼铁工艺进行了比较与分析;此工艺成熟稳定、工序 少、环境友好、资源丰富、成本低,是值得推广发展的一项革命性技术。
关键词!机钬;海砂矿;煤基直接还原;回转窑;多层炉中图分类号:T F521; T F533. 2引言钢铁厂铁水的生产工艺基本可分成以下三大 类:A:气-固热交换熔化还原,如高炉、CO REX;B:预还原-电弧炉熔分,如煤基回转窑B电弧 炉、气基竖炉B电弧炉;C气-液热交换熔融还原,如H ISM ELT、AUS-IRON。
高炉流程经过上千年的发展,目前已确立霸主地 位:规模大、单座装置年产能可达300万吨以上,工艺 操作极为成熟,焦比已接近理论计算值,设备制造已 系列化,资源供应有保障;气基竖炉受天然气价格影 响竞争力下降;煤基回转窑在印度等缺少焦煤的地区仍在运行;熔融还原工艺目前尚无商业化运作。
对新西兰钢厂的海砂矿采选、冶炼生产线进行 考察,同时对海砂矿资源进行了初步调查,与高炉炼 铁工艺进行了比较与分析,新西兰钒钛海砂磁铁矿 冶炼工艺颇具特色。
1新西兰钒钛海砂磁铁矿直接还原工艺11工艺流程新西兰钢厂炼铁工艺以钒钛海砂磁铁矿和褐煤 为原燃料(指标如表1、表2所示),经多层炉干燥和 预热,回转窑预还原,矿热炉终还原、渣铁分离这三 道生产工序(如图1所示),生成铁水和炉渣,铁水送 至转炉炼钢工序进行提钒和炼钢。
表1海砂矿精矿参照指标/ "!(T Fe)!(CaO)!(SiO2)!(TiO2)!(A l2O3)!(MgO)!(P)!(V2O5)!(MnO)!(S)57 1.5 3.9 7.7 3.7 3.4 0.035 0.45 0.66 0.004多层炉回转窑储藏和混合图1工艺流程图收稿日期=2017-04-25作者简介:李志强(960—),男,高级工程师。
攀枝花钒钛磁铁矿直接还原新工艺流程-攀枝花交流材料

(4)目前,正在开展前期示范生产线放大的可研工作。
转底炉煤基直接还原-电炉熔分冶炼 钒钛磁铁矿新工艺
1、四川龙蟒集团
(1)自2003年起,四川龙蟒集团与攀枝花学院合作研究,进行了大 量钒钛铁精矿生球团制备、转底炉直接还原和电炉熔分工艺试验。
(2)2006-2007年,建成一期7万吨/年示范生产线,进行了3轮工业 性试验。
(3)2008年,进行示范生产线放大,启动了年处理铁精矿20万吨的 二期工程;
攀 枝 花 钒 钛 磁 铁 矿 区 分 布
攀枝花钒钛磁铁矿资源储量
钒钛磁铁矿保有储量
67.3亿吨
钛资源量保有储量
4.28亿吨
钒资源保有储量
1047.86万吨
铬保有储量
696万吨
钴保有储量
152万吨
钪保有储量
23万吨
镓保有储量
21万吨
攀枝花钒钛磁铁矿资源 综合开发利用情况
攀枝花钒钛磁铁矿经过四十多年 的开发,已形成了钒材料、钛材料、 钢铁新材料系列产品。2001年被国 家科技部批准为攀枝花国家新材料 成果转化及产业化基地。2007年新 材料产业实现产值110亿元,成为攀 枝花经济增长的新亮点。
攀枝花---国家新材料成果转化及产业化基地
2001年12月18日,国家科技部批准攀枝花为国家新材 料成果转化及产业化基地,并给予了大力支持。
攀 枝 花 钒 钛 磁 铁 矿 资 源 综 合 开 发 工 艺 流 程 图
钢铁产业
攀枝花钢铁产业作为主导产业,目前已形成年产生铁600多万 吨、钢600多万吨的能力;
1、可全部回收钒钛铁精矿中的钛资源。经转底炉还原后的金 属化球团经过电弧炉熔化分离后,可得到含量为50%以上 的熔分钛渣和含钒生铁,实现铁钒与钛的分离。熔分钛渣 可用于硫酸法钛白生产原料。
电炉熔分工艺处理钒钛磁铁矿

电炉熔分工艺处理钒钛磁铁矿电炉熔分工艺处理钒钛磁铁矿一、引言钒钛磁铁矿是一种重要的钛资源,广泛应用于冶金、化工、建材等领域。
然而,由于其复杂的化学成分和矿物结构,其加工和利用一直面临着挑战。
电炉熔分工艺是一种被广泛采用的处理钒钛磁铁矿的方法。
该方法通过利用电炉的高温和电能,将钒钛磁铁矿矿石在还原气氛下进行熔融和分离,以获得钛铁合金和钒铁合金等有价值的产品。
本文将深入探讨电炉熔分工艺处理钒钛磁铁矿的原理、技术及其在实际应用中的优势和发展前景。
二、电炉熔分工艺的原理及技术(1)原理概述电炉熔分工艺是利用电炉高温和电能的特点,将钒钛磁铁矿在还原条件下进行熔融和分离的过程。
在这个过程中,钒和铁进入钒铁合金,而钛则进入钛铁合金。
这种工艺的基本原理是根据各元素的熔点和还原性能的不同,通过合理的炉内温度和还原气氛控制,实现钒、铁、钛的分离和提取。
(2)技术要点在电炉熔分工艺中,关键的技术要点包括矿石预处理、还原条件控制、温度控制和产物分离等。
矿石预处理是为了提高矿石中有价值元素的回收率和产物质量。
常见的矿石预处理方法包括碎石、磁选和浸出等。
还原条件控制对于熔分工艺的成功与否至关重要。
合理的还原条件能够保证有价值元素的还原率和产物质量。
常用的还原条件包括还原剂种类和用量,还原温度和还原时间等。
温度控制是电炉熔分工艺中一个关键的环节。
适当的温度能够保证矿石充分熔化和元素的分离,同时避免产生不良的副反应。
温度控制的方法包括调整电炉电极的位置和电流强度等。
产物分离是电炉熔分工艺中的一项重要工作。
通过合理的分离装置,将钒铁合金和钛铁合金等产品分离出来,以提高产品质量和价值。
三、电炉熔分工艺的优势和发展前景电炉熔分工艺作为一种兼具深度和广度的处理钒钛磁铁矿的方法,具有以下优势和发展前景。
电炉熔分工艺对于复杂矿石的处理能力强。
由于钒钛磁铁矿的化学成分和矿物结构多样复杂,传统的处理方法存在着诸多限制。
而电炉熔分工艺通过熔融和分离的方式,能够有效地处理各种类型的矿石,实现有价值元素的高效提取。
我国钒钛磁铁矿直接还原分析

我国钒钛磁铁矿直接还原分析摘要本文概括地介绍了我国钒钛磁铁矿资源分布情况。
钒钛磁铁矿是重要的资源,世界各国的研究及生产实践表明,使用高炉冶炼法钒钛磁铁矿是难以冶炼的铁矿石。
因此钒钛磁铁矿冶炼大量使用非高炉冶炼法,即采用直接还原法。
本文详细地阐述了直接还原法中隧道窑、回转窑、转底炉、竖炉这四种常见炉的结构、反应原理、国内工艺现状及反应特点,并指出了我国钒钛磁铁矿直接还原工艺的发展方向。
关键词钒钛磁铁矿直接还原隧道窑回转窑转底炉竖炉前言目前国外钒钛磁铁矿主要分布在南非、前苏联、新西兰、加拿大、印度等地。
我国钒钛磁铁矿矿床分布广泛,储量吩咐,储量和开采量居全国铁矿的第3位。
已探明储量98.3亿吨,远景储量达300亿吨以上,主要分布在四川攀枝花地区、河北承德地区、陕西洋县、甘肃什斯镇、广东兴宁几山西代县等地区。
钒钛磁铁矿冶炼的利用问题,远在上19世纪上半叶,瑞典、挪威、美国、英国都进行过试验,均未取得结果。
20世纪30年代开始日本、前苏联开始在不同容积的高炉上研究冶炼钒钛磁铁矿的工艺,结论是:炉渣中TiO2 限制在16%以下,实际生产中采用配10%—15%的普通矿冶炼含钒生铁,渣中TiO2为9%—10%,TiO2含量越高冶炼难度越大。
世界各国的研究及生产实践表明,钒钛磁铁矿是难以冶炼的铁矿石。
通过多年的努力,钒钛磁铁矿已解决高炉冶炼等多项技术难题,逐渐形成了以高炉-转炉流程为主的综合回收其中铁、钒和钛的技术路线,实现了铁、钒和钛元素的大规模化利用,形成了铁钒钛系列产品的大规模工业生产能力。
然而高炉-转炉流程最大的缺点是:为了利用钒钛磁铁矿中的铁和钒浪费了大量的高钛型炉渣,造成钛资源的严重浪费,又造成很大的污染,从而形成了巨大的环境压力,所以开发适宜钒钛磁铁矿综合回收利用的工艺流程势在必行。
本文对钒钛磁铁矿煤基直接还原工艺的炉体结构、原理、特点、现状、投资价格进行简单探讨,指出煤制气-竖炉直接还原工艺为还原钒钛磁铁矿的发展提供新的途径。
国内钒钛磁铁矿利用研究综述

国内钒钛磁铁矿利用研究综述摘要:钒钛磁铁矿经济价值极高,高效绿色开发钒钛磁铁矿资源为当今热点。
本文对钒钛磁铁矿资源分布、综合利用现状及尾矿处理等方面进行分析,重点探讨了高炉法、预还原-电炉法、还原-磨选法和钠化焙烧法处理钒钛磁铁矿的研究现状和工艺优缺点。
并对钒钛磁铁矿尾矿利用工艺进行总结归纳,为钒钛磁铁矿资源的高效综合利用方法提供一定思路。
关键词:钒钛磁铁矿;选冶;概况;建议钒钛磁铁矿是铁、钒和钛资源的重要来源,在世界范围内广泛分布,我国钒钛磁铁矿储量超过180亿t(张树石,2021)。
钒钛磁铁矿成分和结构复杂,是世界公认的难治炼矿种。
根据2019年数据,我国铁矿石对外依存度在80%以上(武秋杰等,2020)。
目前,我国铁矿资源面临着较为严重的形势,需要进一步加强对铁矿的成矿机理和成矿规律等进行更深入的研究以及对现有矿石资源进行更充分的利用。
1 钒钛磁铁矿资源概况作为钒、钛资源的主要载体矿物,钒钛磁铁矿在全球储量丰富、分布广泛。
资料显示,钒钛磁铁矿资源主要集中在俄罗斯、南非、中国、美国、加拿大、挪威、芬兰、印度和瑞典等少数国家和地区。
其中,中国、南非、俄罗斯和美国的储量分别占全球储量的36%、31%、18%和10%。
目前世界上钒钛磁铁矿主要分为两大类:其一为岩体型,主要产地为南非和我国的攀枝花地区;另一种为海砂型,主要产于菲律宾和印尼等地(赵伟,2019)。
我国钒钛磁铁矿资源丰富,已探明储量达180多亿t,主要分布在四川攀枝花、河北承德、陕西汉中等地。
其中仅攀西地区钒钛磁铁矿资源储量就高达100亿t以上,且分布相对集中,是我国最大的钒钛磁铁矿产地。
河北承德地区是我国北方钒钛磁铁矿基地,其钒钛磁铁矿储量仅次于攀西地区,位居全国第二位(王勋,2019)。
2 钒钛磁铁矿综合利用方法钒钛磁铁矿成分和结构复杂,是世界公认的难治炼矿种,目前其综合利用工艺包括高炉法和非高炉法。
高炉法采用高炉冶炼结合转炉提钒工艺,以实现铁、钒和钛资源的分离提取;非高炉法主要包括还原-电炉法、直接还原-磨选法及钠化提钒-直接还原-电炉法,虽然治炼工艺较多,但在经济环保前提下实现高效回收钒、钛资源存在困难。
电炉冶炼钒钛直接还原铁提钒炼钢工艺试验

电炉冶炼钒钛直接还原铁提钒炼钢工艺试验在现代冶金工业中,通过电炉冶炼钒钛直接还原铁提钒炼钢工艺试验是一项备受关注的技术。
这一工艺的迅猛发展得益于对金属矿石资源的深入开发和利用,同时也为提高工业生产效率和减少对传统资源的依赖提供了新的可能性。
本文将从不同角度对这一工艺进行全面评估,并探讨其深度和广度。
让我们来看一下电炉冶炼钒钛直接还原铁提钒炼钢工艺试验的基本原理。
在这一工艺中,通过高温电弧将含钒钛矿石进行还原熔炼,得到高纯度的铁和钒钛合金。
这一工艺的优势在于可以直接利用矿石资源,减少了传统冶炼工艺中的预处理环节,提高了冶炼效率和降低了成本。
通过合理控制还原条件和合金配比,可以得到满足不同工业需求的高品质合金产品。
在实际应用中,电炉冶炼钒钛直接还原铁提钒炼钢工艺试验也面临诸多挑战和问题。
首先是能源消耗和环境污染的问题。
高温电弧冶炼需要大量电能,而且在炼钢过程中会产生大量烟尘和废渣,对环境造成严重影响。
其次是技术参数的控制和优化问题。
电弧冶炼过程中需要严格控制温度、氧化还原条件和合金成分,以确保产品合金品质达标。
这些都需要在工艺试验中进行深入研究和实践,以不断优化和改进工艺的稳定性和可靠性。
电炉冶炼钒钛直接还原铁提钒炼钢工艺试验是一项技术前景广阔的冶金工艺。
通过对其深度和广度的评估,我们可以发现其在资源利用、生产效率和产品品质方面的巨大潜力。
然而,也需要重视其在能源消耗、环境污染和工艺优化方面所面临的问题和挑战。
只有通过不断的实验和改进,才能真正实现这一工艺的可持续发展和商业化应用。
个人观点上,我认为电炉冶炼钒钛直接还原铁提钒炼钢工艺试验是一项有着巨大应用前景和发展空间的技术。
通过不断的研究和实践,可以不仅提高钒钛资源的利用率,减少对传统铁矿石资源的依赖,同时也为提高钒钛合金产品品质和降低生产成本提供了可能。
然而,需要克服的技术和环境问题也不可忽视,需要工程技术人员和环保专家共同努力,以实现这一工艺的商业化应用和可持续发展。
钒钛磁铁矿精矿钙化焙烧直接提钒研究
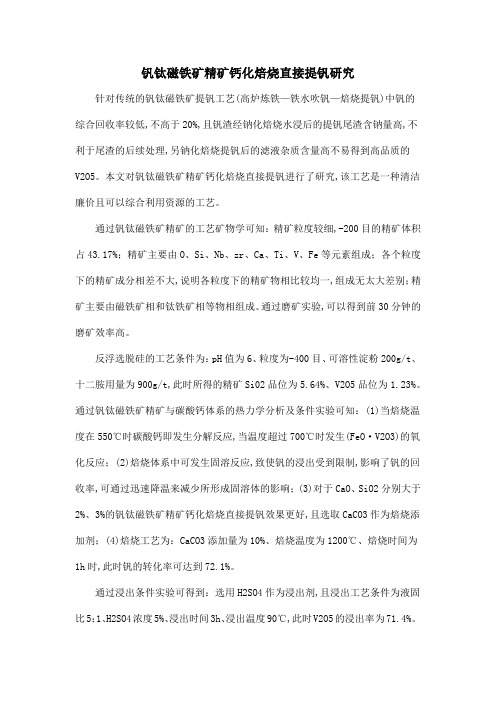
钒钛磁铁矿精矿钙化焙烧直接提钒研究针对传统的钒钛磁铁矿提钒工艺(高炉炼铁—铁水吹钒—焙烧提钒)中钒的综合回收率较低,不高于20%,且钒渣经钠化焙烧水浸后的提钒尾渣含钠量高,不利于尾渣的后续处理,另钠化焙烧提钒后的滤液杂质含量高不易得到高品质的V2O5。
本文对钒钛磁铁矿精矿钙化焙烧直接提钒进行了研究,该工艺是一种清洁廉价且可以综合利用资源的工艺。
通过钒钛磁铁矿精矿的工艺矿物学可知:精矿粒度较细,-200目的精矿体积占43.17%;精矿主要由O、Si、Nb、zr、Ca、Ti、V、Fe等元素组成;各个粒度下的精矿成分相差不大,说明各粒度下的精矿物相比较均一,组成无太大差别;精矿主要由磁铁矿相和钛铁矿相等物相组成。
通过磨矿实验,可以得到前30分钟的磨矿效率高。
反浮选脱硅的工艺条件为:pH值为6、粒度为-400目、可溶性淀粉200g/t、十二胺用量为900g/t,此时所得的精矿Si02品位为5.64%、V2O5品位为1.23%。
通过钒钛磁铁矿精矿与碳酸钙体系的热力学分析及条件实验可知:(1)当焙烧温度在550℃时碳酸钙即发生分解反应,当温度超过700℃时发生(FeO·V2O3)的氧化反应;(2)焙烧体系中可发生固溶反应,致使钒的浸出受到限制,影响了钒的回收率,可通过迅速降温来减少所形成固溶体的影响;(3)对于CaO、SiO2分别大于2%、3%的钒钛磁铁矿精矿钙化焙烧直接提钒效果更好,且选取CaCO3作为焙烧添加剂;(4)焙烧工艺为:CaCO3添加量为10%、焙烧温度为1200℃、焙烧时间为1h时,此时钒的转化率可达到72.1%。
通过浸出条件实验可得到:选用H2SO4作为浸出剂,且浸出工艺条件为液固比5:1、H2SO4浓度5%、浸出时间3h、浸出温度90℃,此时V2O5的浸出率为71.4%。
我国煤基直接还原炼铁工艺发展
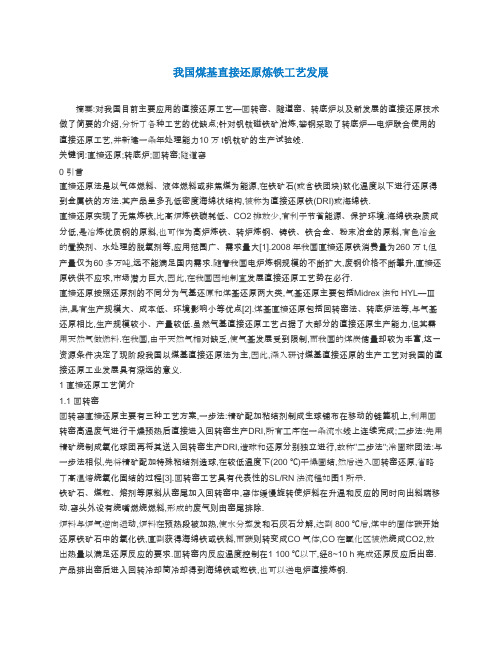
我国煤基直接还原炼铁工艺发展摘要:对我国目前主要应用的直接还原工艺—回转窑、隧道窑、转底炉以及新发展的直接还原技术做了简要的介绍,分析了各种工艺的优缺点;针对钒钛磁铁矿冶炼,攀钢采取了转底炉—电炉联合使用的直接还原工艺,并新建一条年处理能力10万t钒钛矿的生产试验线.关键词:直接还原;转底炉;回转窑;隧道窑0 引言直接还原法是以气体燃料、液体燃料或非焦煤为能源,在铁矿石(或含铁团块)软化温度以下进行还原得到金属铁的方法.其产品呈多孔低密度海绵状结构,被称为直接还原铁(DRI)或海绵铁.直接还原实现了无焦炼铁,比高炉炼铁碳耗低、CO2排放少,有利于节省能源、保护环境.海绵铁杂质成分低,是冶炼优质钢的原料,也可作为高炉炼铁、转炉炼钢、铸铁、铁合金、粉末冶金的原料,有色冶金的置换剂、水处理的脱氧剂等,应用范围广、需求量大[1].2008年我国直接还原铁消费量为260 万t,但产量仅为60多万吨,远不能满足国内需求.随着我国电炉炼钢规模的不断扩大,废钢价格不断攀升,直接还原铁供不应求,市场潜力巨大,因此,在我国因地制宜发展直接还原工艺势在必行.直接还原按照还原剂的不同分为气基还原和煤基还原两大类,气基还原主要包括Midrex法和HYL—Ⅲ法,具有生产规模大、成本低、环境影响小等优点[2].煤基直接还原包括回转窑法、转底炉法等,与气基还原相比,生产规模较小、产量较低.虽然气基直接还原工艺占据了大部分的直接还原生产能力,但其需用天然气做燃料.在我国,由于天然气相对缺乏,使气基发展受到限制,而我国的煤炭储量却较为丰富,这一资源条件决定了现阶段我国以煤基直接还原法为主,因此,深入研讨煤基直接还原的生产工艺对我国的直接还原工业发展具有深远的意义.1 直接还原工艺简介1.1 回转窑回转窑直接还原主要有三种工艺方案,一步法:精矿配加粘结剂制成生球铺布在移动的链篦机上,利用回转窑高温废气进行干燥预热后直接进入回转窑生产DRI,所有工序在一条流水线上连续完成;二步法:先用精矿烧制成氧化球团再将其送入回转窑生产DRI,造球和还原分别独立进行,故称"二步法";冷固球团法:与一步法相似,先将精矿配加特殊粘结剂造球,在较低温度下(200 ℃)干燥固结,然后送入回转窑还原,省略了高温焙烧氧化固结的过程[3].回转窑工艺具有代表性的SL/RN法流程如图1所示.铁矿石、煤粒、熔剂等原料从窑尾加入回转窑中,窑体缓慢旋转使炉料在升温和反应的同时向出料端移动.窑头外设有烧嘴燃烧燃料,形成的废气则由窑尾排除.炉料与炉气逆向运动,炉料在预热段被加热,使水分蒸发和石灰石分解,达到800 ℃后,煤中的固体碳开始还原铁矿石中的氧化铁,直到获得海绵铁或铁料,而碳则转变成CO气体,CO在氧化区被燃烧成CO2,放出热量以满足还原反应的要求.回转窑内反应温度控制在1 100 ℃以下,经8~10 h完成还原反应后出窑.产品排出窑后进入回转冷却筒冷却得到海绵铁或粒铁,也可以送电炉直接炼钢.与高炉工艺相比较,回转窑工艺设备简单,投资少,适用于地方钢铁工业,弥补了高炉—转炉工艺的不足,此外,回转窑还适用于复合矿冶炼,冶金灰尘及各种工业废渣的回收利用,减少环境污染,降低了钢铁生产能耗.同时,回转窑工艺也存在一些缺点,包括窑内结圈、还原温度低(1 100 ℃以下)、流程长、对块矿或球团矿冷强度要求高、要求使用低硫煤等[4].我国山东鲁中矿山公司通过采取提高冷固烧结球团的冷热态强度、加强还原煤的选择和管理、优化回转窑的送风、抛煤、控温温度等措施,预防并降低回转窑结圈,取得了较好的收效.图1 SL/RN法工艺流程1.2 隧道窑隧道窑工艺即将精矿粉、煤粉、石灰石粉,按照一定的比例和装料方法,分别装入还原罐中,然后把罐放在罐车上,推入条形隧道窑中或把罐直接放到环形轮窑中,料罐经预热到1 150 ℃加热焙烧和冷却之后,得到直接还原铁.目前江苏永钢集团拥有两条260 m长煤气隧道窑,为亚洲最长隧道窑.隧道窑生产海绵铁工艺流程如图2所示.图2 隧道窑生产海绵铁工艺流程煤基隧道窑直接还原工艺具有技术成熟、作简单的特点,可因地制宜采用此工艺,利用当地小型分散的铁矿及煤矿资源优势,发展直接还原铁生产,为电炉提供优质原料.但是,总体上讲,我国隧道窑直接还原中存在生产规模较小、能耗高、污染严重、缺乏稳定的原料供应渠道等问题[5],所以,提高机械化程度、改变原料入炉方式、改进燃料及其燃烧、增设余热回收等成为各厂家不断努力改进工艺的方向.我国已建成或正在建设的隧道窑有100多座,约70多个单位规划建设产能5~30 万t/a的隧道窑直接还原铁厂,在不断总结实践经验的基础上,改进现行工艺,开发出诸如大型隧道窑直接还原、AMR—CBI隧道窑直接还原工艺、宽体球状海绵铁隧道窑、L-S快速还原工艺等多种新技术,掀开了隧道窑工艺规模扩大、产能提高、机械及自动化提升的序幕.1.3 转底炉转底炉煤基直接还原是最近几十年间发展起来的炼铁新技术,代表工艺为Fastmet,它由美国Midrex公司与日本神户制钢于20世纪60年发,是采用环形转底炉生产直接还原铁的一种方法.经过多年的半工业性试验和深入的可行性研究,现已完成工艺作参数和装置设计的优化.Fastmelt和ITmk3工艺是在此基础上增加对直接还原铁的处理.图3显示了这三种以转底炉为主体的直接还原工艺流程.图3 转底炉直接还原工艺流程煤粉与铁精粉按比例混匀制成球团,干燥后以1~3层球铺放在转底炉床面,随着炉底的旋转,炉料依次经过预热区、还原区和冷却区.还原区内球团被加热到1 250~1 350 ℃,由于煤粉与铁氧化物紧密接触,铁氧化铁被碳迅速还原成DRI,成品在800~1 000 ℃左右连续从转底炉卸出.球团矿在炉底停留8~30 min,这取决于原料特性、料层厚度及其他因素,成品可作电炉热装炉料或者转炉炉料,也可冷却或生产热压块(HBI).Fastmet工艺技术特点:①在高温敞焰下加热实现快速还原,反应时间只需10~20 min,生产效率高;②原料来源广泛,铁原料方面,除使用高品位粉矿、精矿外,还可用氧化铁皮、代油铁泥、炼钢粉尘、含En、Pb、As等有害杂质的铁矿等;还原剂方面,除煤以外焦末、沥青均可利用,不必担心出现结圈问题;③炉料相对炉底静止,对炉料强度要求不高;④废气中含有大量显热,可用作预热空气、干燥原料等[6]. Fastmelt工艺流程基本与Fastmet一致,只是在后续添加一个熔炉来生产高质量的液态铁水.Itmk3工艺是使金属化球团在转底炉中还原时熔化,生成铁块(Nuggets),同时脉石也熔化,形成渣铁分离.当然转底炉也存在着设备复杂、炉内气氛难控制、传热效率低以及对还原剂硫含量要求严格的缺点.就目前转底炉工艺开发的水平和规模而论,与高炉还有较大差距,但仍存在发展的广阔空间,天津荣程联合钢铁集团已兴建一条100万t级Fastmet生产线,建成目前世界最大的转底炉.另外,用转底炉可处理一些特殊铁矿,如含锌、铅、砷等有害杂质,或含镍、钒、钛等有用元素,均可利用转底炉的工艺优势,或高温挥发,或选择性还原,配合后续工艺,实现资源综合利用.马钢尘泥脱锌转底炉工程项目于2008年5月开工建设,2009年7月6日正式竣工投产,建成了整套转底炉(RHF)脱锌工艺技术装置,不仅解决了含锌尘泥循环利用的后顾之忧,而且将综合利用技术上升到高品质资源化水平.1.4 其他新工艺1.4.1 PF法煤基竖炉直接还原工艺中冶集团北京冶金设备研究设计总院,结合国内情况创新发明了PF法竖炉直接还原工艺.PF法是在吸收K-M法外热式竖炉煤基直接还原工艺的经验基础上,设计的以一种中国特色的罐式还原炉为主反应器的直接还原法.这种工艺技术可靠,技术经济指标在各种煤基直接还原工艺中属先进水平.PF法直接还原工艺流程如图4所示.图4 PF法直接还原工艺流程PF法直接还原工艺主要特点[1]:1)主体设备选用外热式竖炉,预热、还原、冷却三段根据不同的作用和温度选用不同材质和结构,便于传热和化学反应进行,提高热效率和设备寿命.2)原燃料适用性强,对精矿、还原剂和燃料没有特殊要求.3)采用外配碳工艺,还原剂适当过量,扩大了煤的选用范围,造球工艺也因不定量配入煤粉而简化,球团强度较高,DRI质量较好.4)多个反应罐可并列组成任意规模的还原设备,设计和组织生产灵活.1.4.2 低温快速还原新工艺2004年钢铁研究总院提出了低温快速冶金新工艺.新工艺利用纳米晶冶金技术的特点将铁矿的还原温度降低到700 ℃以下.新流程分为气基和煤基两种方法,工艺流程如图5、图6所示.图5 煤基低温快速还原新工艺图6 气基低温快速还原新工艺煤基法使用煤粉为还原剂,在700℃左右快速还原铁精矿粉;气基法使用还原性气体还原铁精矿粉,还原温度可低于600℃.新工艺具有能耗低、环境友好等特点,省去了烧结或造球工艺,缓解了钢铁行业对焦煤的依赖,符合我国国情[7].2 攀钢现状钒钛磁铁矿是攀西地区的特色资源,与普通矿相比,钒钛矿直接还原温度较高、还原时间较长,还原过程产生特有的膨胀粉化现象,因此,存在竖炉结瘤、流化床失流和黏结、回转窑结圈等技术难题.高炉流程冶炼钒钛矿,只回收了铁和钒,钛进入高炉渣没有回收,造成钛资源的大量流失.2005年以来,攀钢科研人员在充分吸收、借鉴新流程及相关研究成果的基础上,通过大量的试验研究,针对钒钛磁铁矿特点,提出并验证了钒钛磁铁矿"转底炉直接还原—电炉深还原—含钒铁水提钒—含钛炉渣提钛"工艺路线,彻底打通了钒钛矿资源综合利用新工艺流程,稳定获得了质量满足要求的低碳生铁、达到GB3283-87要求的片状V2O5和PTA121质量要求的钛白产品.依托该研究成果,攀钢集团攀枝花钢铁研究院于2008年5月4日正式启动了攀钢10 万t/a钒钛矿资源综合利用新工艺中试线工程项目,新建一条转底炉—熔分电炉联合使用,年处理能力10万t钒钛矿的试验生产线,为更深入地研究实践,实现转底炉处理钒钛矿的规模化生产提供了广阔的平台.中试线工艺流程如图7所示.本流程采用硫含量较低的白马铁精矿,还原剂采用无烟煤煤粉,粘结剂为有机粘结剂,原料混合后经高压压球机压球,生球烘干后进入转底炉系统.球团在转底炉内停留10~30 min后出料,金属化球团直接热装进入熔分电炉,在一定温度下还原后,产出含钒铁水及含钛炉渣.继续对铁水进行脱硫、提钒后,得到半钢、脱硫渣及钒渣,半钢进入铸铁机铸铁,生产出铸铁块.钛渣制取钛白,实验室条件下钛回收率达到80%以上;钒渣制取钒氧化物(V2O5),实验室条件下,钒回收率达到65%以上.与高炉流程相比,转底炉流程采用100%钒钛矿冶炼,克服了高炉流程必须配加普通矿的不足,在当前铁资源紧张的形势下,有助于充分发挥攀西地区资源优势,拉动区域经济发展.此外,转底炉流程的铁精矿不需烧结处理,不使用焦炭,从根本上避免了烧结烟气脱硫、焦煤资源采购困难以及环保压力大等问题.3 结语图7 资源综合利用中试线工艺流程煤炭资源总量丰富、焦煤短缺,铁矿资源储量大、富矿少、贫矿和共生矿多是中国钢铁工业面临的现实状况.这种能源、资源结构给煤基直接还原法生产海绵铁的发展提供了机遇.转底炉直接还原技术由于在生产率、规模化、投资费用、单位成本等方面都占有明显的优势,可作为发展直接还原技术的首选工艺.鉴于转底炉处理钒钛磁铁矿技术尚属世界首创,并无较多的经验借鉴,因此要大力开展针对钒钛磁铁矿直接还原的基础研究工作,在实践中借鉴各种直接还原方法已取得的成果,开拓创新,开创钒钛矿直接还原新纪元.参考文献[1] 陈守明,黄超,张金良.煤基竖炉直接还原工艺//2008年非高炉炼铁年会文集.中国金属学会,2008:132-135.[2] 杨婷,孙继青.世界直接还原铁发展现状及分析.世界金属导报,2006.[3] 刘国根,邱冠周,王淀佐.直接还原炼铁中的粘结剂.矿产综合利用,2001(4):27-30.[4] 韩跃新,高鹏,李艳军.白云鄂博氧化矿直接还原综合利用前景.金属矿山,2009 (5):1-6.[5] 魏国,赵庆杰,沈峰满,等.非高炉生产技术进步//2004年全国炼铁生产技术暨炼铁年会文集.2004:878-882.[6] 陶晋. 环形转底炉直接还原工艺现状及发展趋势. 冶金信息工作, 1997.6.[7] 郭培民,赵沛,张殿伟.低温快速还原炼铁新技术特点及理论研究.炼铁,2007,26(1): 57-60.来源:攀枝花钢铁研究院网站。
钒钛磁铁矿提钒工艺技术综述(1)
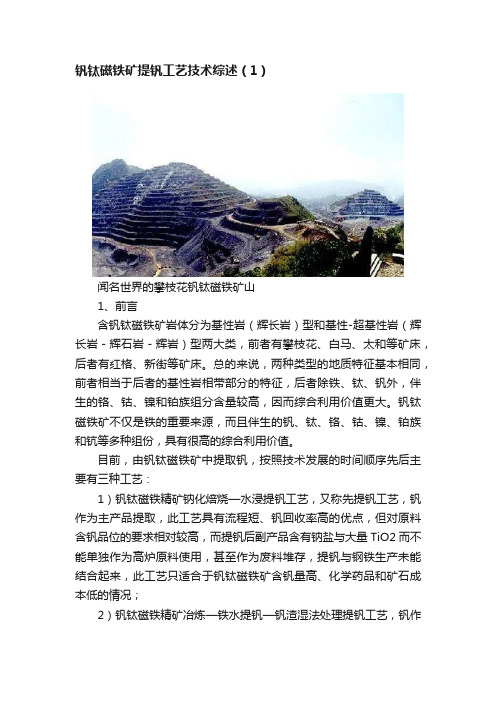
钒钛磁铁矿提钒工艺技术综述(1)闻名世界的攀枝花钒钛磁铁矿山1、前言含钒钛磁铁矿岩体分为基性岩(辉长岩)型和基性-超基性岩(辉长岩-辉石岩-辉岩)型两大类,前者有攀枝花、白马、太和等矿床,后者有红格、新街等矿床。
总的来说,两种类型的地质特征基本相同,前者相当于后者的基性岩相带部分的特征,后者除铁、钛、钒外,伴生的铬、钴、镍和铂族组分含量较高,因而综合利用价值更大。
钒钛磁铁矿不仅是铁的重要来源,而且伴生的钒、钛、铬、钴、镍、铂族和钪等多种组份,具有很高的综合利用价值。
目前,由钒钛磁铁矿中提取钒,按照技术发展的时间顺序先后主要有三种工艺:1)钒钛磁铁精矿钠化焙烧—水浸提钒工艺,又称先提钒工艺,钒作为主产品提取,此工艺具有流程短、钒回收率高的优点,但对原料含钒品位的要求相对较高,而提钒后副产品含有钠盐与大量TiO2而不能单独作为高炉原料使用,甚至作为废料堆存,提钒与钢铁生产未能结合起来,此工艺只适合于钒钛磁铁矿含钒量高、化学药品和矿石成本低的情况;2)钒钛磁铁精矿冶炼—铁水提钒—钒渣湿法处理提钒工艺,钒作为副产品回收,也是目前由钒钛磁铁矿提取钒最主要、经济上最为合理的工艺,此工艺可以利用含钒品位低的原料;3)钒钛磁铁精矿非高炉冶炼—电炉熔分/电炉深还原—熔分渣提钒/铁水提钒工艺,此法能耗低、环保好,钒的收得率高,是提钒技术的发展方向。
目前,前两种钒钛磁铁矿提钒工艺各有优点和缺点,不是单纯的工艺改进和完善,因此,第二种工艺并没有完全替代第一种工艺,而是以第二种工艺为主,两种提钒工艺共存的方式存在。
其中,铁水提钒工艺通过往铁水内吹氧使其内的钒氧化进入渣中,通常称作火法提钒;随后,含钒渣经过破碎、焙烧、浸出、过滤得到钒氧化物的工艺称为湿法提钒。
2 钠化焙烧原矿—水浸提纯钒工艺2.1 工艺现状及特点采用钒钛磁铁精矿钠化焙烧—水浸提钒工艺的钒制品生产厂家主要分布在南非和澳大利亚,全球仍有五六家公司采用该工艺生产氧化钒,其产量约占全球氧化钒总产量的25%~30%。
钒钛磁铁精矿回转窑预还原中试试验研究

钒钛磁铁精矿回转窑预还原中试试验研究栾志华;宋志伟【摘要】回转窑预还原是"磁选―回转窑预还原―电炉熔炼"工艺处理钒钛磁铁矿的关键环节.本文通过中试试验研究了利用该工艺处理莫桑比克Tenge钒钛磁铁矿过程中回转窑预还原指标影响因素,试验给出了钒钛磁铁矿的理化指标及回转窑预还原温度、预还原时间、煤矿比等几个主要工艺技术参数和条件,达到了试验预期目的,确定了"磁选—回转窑预还原—电炉熔炼"未制粒钒钛磁铁精矿的可行性,为工业化生产设计提供了技术依据.【期刊名称】《有色设备》【年(卷),期】2018(000)004【总页数】4页(P10-12,15)【关键词】钒钛磁铁精矿;中试试验;回转窑;预还原;金属化率【作者】栾志华;宋志伟【作者单位】中国有色(沈阳)冶金机械有限公司,辽宁沈阳110141;中国有色(沈阳)冶金机械有限公司,辽宁沈阳110141【正文语种】中文【中图分类】TQ172.6220 前言莫桑比克Baobab公司为了开发其拥有的Tenge矿,进行了Tenge矿的工艺技术开发及可行性研究报告的编制。
该项目决定采用“磁选—回转窑预还原—电炉熔炼”工艺处理钒钛磁铁矿,目的是降低成本、取得良好经济效益。
“磁选—回转窑预还原—电炉熔炼”工艺目前大多数采用首先将钒钛磁铁矿磁选得到精矿,然后将精矿磨细制粒并在低温下预还原为金属化球团,再将金属化球团在电炉内进行冶炼,实现钒钛磁铁精矿的冶炼分离并且获得优质的含钒铁水[1]。
本次中试试验的目的是打破传统工艺,研究钒钛磁铁精矿在未制粒的条件下进行回转窑预还原的可行性,并为工业生产设计提供依据。
因此,本文在研究钒钛磁铁精矿基本特性的基础上,针对回转窑预还原工艺特点,通过中试试验系统地考察预还原温度、预还原时间、煤矿比等几个主要因素对钒钛磁铁精矿未制粒条件下回转窑预还原指标,即有价金属Fe金属化率的影响,最终确定钒钛磁铁精矿未制粒条件下回转窑预还原的可行性及适宜的理想条件。
钒钛磁铁矿含碳球团转底炉直接还原实验研究

第9卷增刊1 过 程 工 程 学 报 V ol.9 Suppl. No.1 2009 年 6月 The Chinese Journal of Process Engineering June 2009收稿日期:2008−10−22,修回日期:2009−02−17作者简介:刘征建(1982−),男,辽宁省黑山县人,博士研究生,钢铁冶金专业,E-mail: liuzhengjian@.钒钛磁铁矿含碳球团转底炉直接还原实验研究刘征建, 杨广庆, 薛庆国, 张建良, 杨天钧(北京科技大学冶金与生态工程学院,北京 100083)摘 要:对转底炉直接还原钒钛磁铁矿新工艺进行了实验研究,将钒钛磁铁矿精矿粉与煤粉等混合,采用压球机压球,并用石油液化气同空气混合燃烧生成的热烟气干燥生球,通过正交实验考察C/O 、焙烧时间和焙烧温度3个因素对金属化率与抗压强度的影响,得出最优的实验方案是:C/O 为1.3,焙烧温度为1330℃,焙烧时间为25 min. 通过XRD 分析发现在金属化率较高的球团中存在假板钛矿.关键词:资源综合利用;钒钛磁铁矿;转底炉;直接还原中图分类号:TF521 文献标识码:A 文章编号:1009−606X(2009)S1−0051−051 前 言钒钛磁铁矿是一种铁、钒、钛等有价元素共生的复合矿,普通高炉冶炼钒钛磁铁矿的弊端日益凸显,一是钛资源流失严重,占钒钛磁铁原矿中钛总量的一半以上;二是高炉炼铁必须使用焦碳,要消耗大量稀缺而昂贵的焦煤资源,而且炼焦过程污染环境严重[1].进入21世纪以来,随着优质含铁原料供应的日趋紧张和环保要求的日益严格,原料适应性强、能耗低、环境友好的直接还原技术获得了快速发展,出现了诸多新工艺和新技术,转底炉直接还原技术是其中较为典型的代表[2]. 转底炉出现于1978年,最初是应含铁废料和粉尘的处理要求而产生的,1995年以后逐步发展成使用普通铁精矿为原料生产DRI 的直接还原新工艺[3−5]. 转底炉直接还原具有高温、快速的工艺特点和炉料与炉底相对静止的设备特点,能较好的满足钒钛磁铁矿直接还原要求[6]. 共性技术的发展为钒钛磁铁矿直接还原创造了良好的外部条件,在此基础上针对钒钛磁铁矿自身特点,开展铁钒与钛高效分离研究、钒钛提取回收技术研究,实现转底炉直接还原—电炉深还原的产业化生产,达到铁、钒、钛元素分离与综合回收利用的目标. 本工作以钒钛磁铁矿精矿粉、煤粉和粘结剂等为原料,设计正交实验进行钒钛磁铁矿含碳球团转底炉直接还原生产金属化球团的基础研究,为后续的装备设计与工业生产探索规律.2 实验原料实验含铁原料采用某产地的钒钛磁铁矿,化学成分如表1所示.表1 钒钛磁铁矿精矿粉成分Table 1 Composition of vanadic titanomagnetite (%, ω)TFe FeO TiO 2V 2O 5 SiO 2 Al 2O 3 CaOMgO51.46 31.0212.430.53 5.96 5.30 1.983.41此钒钛磁铁矿主要由钛磁铁矿、钛铁矿、硫化矿和脉石矿物等4部分组成. 钛磁铁矿是磁铁矿、钛铁晶石、镁铝尖晶石、钛铁矿片晶复合体. 它占总矿物量的44%左右,含铁57%,是回收铁的主要工业矿物. 由于钛磁铁矿中有4种矿物密切共生,磁铁矿为主晶,其他为客晶. 客晶的粒度极细,不能用机械方法使其单体分离,使所得铁精矿中含有较高的钛、钒、镓、镁、钙、铝、硅等元素,铁品位一般较低;钛铁矿占总矿物量的9.5%,除少量赋存于钛磁铁矿外,大部分单体粒状产出,充填于脉石颗粒之间或铁钛氧化物与脉石之间. 含TiO 2 10.7%,是回收钛的工业矿物. 但其含有较高的钙镁,这些杂质以类质同象赋存在钛铁矿中,因此钛精矿中TiO 2含量一般为46%~48%,钙镁含量达7%~8%;硫化矿占总矿物量的1%,其中磁黄铁矿占硫化矿的95%,是回收硫、钴、镍的工业矿物;脉石矿物以钛普通辉石和斜长石为主,钛普通辉石占总矿物的28%~29%,是回收钪的主要矿物,斜长石占18%~19%.所用固体燃料为宁夏太西无烟煤,工业分析结果如表2所示.表2 煤粉工业分析结果Table 2 Industrial analysis of pulverized coal (%, ω)Fixed carbon V olatile Ash86.47 8.58 4.953 正交实验52 过程工程学报第9卷为了准确控制水分的加入量,混料前所有原料在105℃下干燥2 h,每次实验干料重量约为2.5 kg,人工混料30 min左右. 采用对辊压球机造球,压力可调,所造生球为扁圆形.干燥采用鼓风和抽风两种模式,基本流程是液化石油气同空气混合在燃烧室燃烧,生成的热烟气对含水生球进行干燥. 通过调节液化石油气和空气量来调节干燥入口温度和干燥的风速,本实验中入口温度控制在250℃左右,干燥风速为1.0和1.5 m/s,干燥时间选择10, 15和20 min.焙烧在管式炉中进行,干燥球团用吊篮盛装.采用正交实验考察C/O、焙烧温度和焙烧时间3个因素对含碳球团金属化率和抗压强度的影响,水平设计如表3.表3 实验因素与水平Table 3 Factors and levels of the experimentsLevelFactor A,C/OB,roasting temperature (℃)C,roasting time (min)1 1.31250 152 1.51300 203 1.11330 254 实验结果及分析4.1 造球实验本实验造球压强为15 MPa,转速为10 r/min,膨润土配加比例为3%.4.2 干燥实验用C/O为1.3的1#, 2#, 3#生球进行干燥实验,实验结果如表4所示.表4 干燥实验方案及结果Table 4 Scheme and results of drying experimentNo. DryingmethodGas flowvelocity (m/s)Gas flowrate (m3/h)Drying time(min)Weight of greenballs (g)Weight afterdrying (g)Water content ofgreen balls (%)Dehydration rate(%)1 Blast 1 24 10 1627.8 1479.8 11.93 76.192 Blast 1 24 15 1601.7 1429.4 11.89 90.493 Blast 1 24 20 1594.1 1410.4 11.96 96.32 3 Suction 1 24 15 1608.3 1438.2 11.52 91.84通过实验数据可以看出如下规律[7,8].(1) 鼓风干燥和抽风干燥两种形式的干燥效果没有明显差别,实验中没有发现在抽风干燥过程中下部生球有过湿现象和压坏现象发生;(2) 随着烘干时间的增加脱水率逐渐增加,烘干15 min后脱水率可达到90%以上,完全满足要求,延长时间对于烘干效果没有明显影响.4.3 焙烧实验(1) 实验结果对9组焙烧后金属化球团的化学成分和抗压强度分别进行检测,结果如表5所示.表5 金属化球团的化学分析结果及抗压强度Table 5 Chemical analysis and compressive strength of metallized pelletsNo. TFe(%)MFe(%)Metallization rate(%)V2O5(%)TiO2(%)Compressivestrength (N)1 60.40 32.53 53.86 0.48 9.74 2155.672 60.40 47.08 77.95 0.66 13.33 1036.403 65.25 56.11 85.99 0.65 12.06 2395.004 59.21 44.78 75.63 0.51 13.11 1747.205 62.57 55.60 88.86 0.56 9.58 1337.756 66.33 51.94 78.31 0.60 14.36 2273.007 59.71 35.51 59.47 0.47 11.40 635.008 59.94 40.33 67.28 0.41 12.93 650.509 62.90 48.08 76.44 0.63 12.30 1642.80通过以上结果可以看出:(a) 金属化球团的铁品位较精矿粉的铁品位有较大提高,这是因为煤粉中的碳与铁氧化物中的氧发生反应,去除了精矿粉中的部分氧,而残留的煤粉灰分质量远小于铁氧化物失去氧的质量[9].(b) 金属化球团中只有少量V, Ti被还原. 由Ellingham图可知,V2O5, TiO2只有在1500℃以上高温时才能被碳还原[10].(c) 由于C/O与焙烧条件不同各组的金属化率和抗压强度变化较大.(2) 直观分析[11]判断金属化球团质量的两个重要指标就是金属化率和抗压强度,实际生产中一般要求金属化率和抗压强度越高越好. 由表5可知,不同C/O,不同焙烧条件下增刊1 刘征建等:钒钛磁铁矿含碳球团转底炉直接还原实验研究 53各组的金属化率和抗压强度变化较大. 对正交实验结果采用直观分析法进行分析,以找出最佳的工艺条件,结果如表6所示.表6 直观分析法结果Table 6 The results of intuitive analysisTest index No.1 A2 B3 C Metallization rate (%) Compressive strength (N)1 1 1 1 53.86 635.002 1 2 2 77.95 1747.203 1 3 3 85.99 2155.674 2 1 2 75.63 650.505 2 2 3 88.86 1337.75 6 2 3 1 78.31 1036.407 3 1 3 59.47 1642.808 3 2 1 67.28 2273.009 3 3 2 76.44 2395.00K 1 217.80 188.96 199.45 K 2 242.80 234.09 230.02 K 3 203.19 240.74 234.32 κ1 72.60 62.99 66.48 κ2 80.93 78.03 76.67 κ3 67.73 80.25 78.11 Range 13.20 17.26 11.63 MetallizationrateOptimum scheme A2 B3 C3K 1 4537.87 2928.30 3944.40 K 2 3024.65 5357.95 4792.70 K 3 6310.80 5587.07 5136.22 κ1 1512.62 976.10 1314.80 κ2 1008.22 1785.98 1597.57 κ3 2103.60 1862.36 1712.07 Range 1095.38 886.26 397.27 Compressive strengthOptimum scheme A3 B3 C3从以上分析结果可看出,对于金属化率的3个极差由大到小依次为17.26,13.20,11.63,它们所对应的因素依次为B ,A ,C. 所以,各因素对金属化率的影响按大小次序来说应当是B(焙烧温度)、A(C/O)、C(焙烧时间);最好的方案应当是B3A2C3,即, B3:焙烧温度,第3水平,1330℃;A2:C/O ,第2水平,1.5;C3:焙烧时间,第3水平,25 min.同理可知,各因素对抗压强度的影响按大小次序来说应当是A(C/O),B(焙烧温度),C(焙烧时间);最好的方案应当是A3B3C3,即:A3:C/O ,第3水平,1.1;B3:焙烧温度,第3水平,1330℃;C3:焙烧时间,第3水平,25 min.通过综合平衡法对金属化率和抗压强度两个指标进行计算分析,分别得到2个最优方案:对金属化率为A2B3C3;对抗压强度为A3B3C3. 这2个方案并不完全相同,为便于综合分析,将两个指标随因素水平变化的情况用图形表示出来,如图1所示(为了便于分析,将各点用线段连起来,实际上并不是直线).666870727476788082M e t a l l i z a t i o n r a t e (×102%)C/ORoasting temperature(℃)Roasting time(min)1.11.31.58001000120014001600180020002200C o m p r e s s i v e s t r e n g t h (N )C/O125013001350Roasting temperature(℃)152025Roasting time(min)图1 两个指标随因素水平变化的情况Fig.1 Changes of two indexes with variable factors and levels54 过 程 工 程 学 报 第9卷将图1和表6结合起来,综合分析每一个因素对两个指标的影响.(a) C/O 对两个指标的影响. 从表6看出,对抗压强度来讲,C/O 的极差是最大的,也就是说C/O 是影响最大的因素,从图1看,取1.1最好;对金属化率来讲,C/O 的极差不是最大,即不是影响最大的因素,是较次要的因素,取 1.5最好. 从实际的焙烧过程来看,C/O 越高,煤粉配加量越大,煤粉反应后留下的空隙越多,金属化球团的孔隙度越大,抗压强度越低,这与表6的分析结果很吻合. 针对为实现铁、钛、钒资源综合利用而设计的“钒钛磁铁矿转底炉直接还原−电炉深还原−含钒铁水提钒−含钛炉渣提钛”工业流程,其转底炉生产的金属化球团直接热装电炉,所以对金属化球团的抗压强度要求不是很高,加之电炉深还原要求金属化球团有一定的残碳含量,所以C/O 取中间水平1.3为好[12,13].(b) 焙烧温度B 对两个指标的影响. 从表6看出,对金属化率来讲,焙烧温度的极差是最大的,即焙烧温度是影响最大的因素,从图1看出,取1330℃最好;对抗压强度来讲,焙烧温度的极差不是最大,即不是影响最大的因素,是较次要的因素,但也是取1330℃最好,所以对两个指标来讲,焙烧温度均取1330℃最好.(c) 焙烧时间C 对两个指标的影响. 从表6看出,对金属化率和抗压强度来讲,焙烧时间的极差都是最小的,即是影响最小的因素,从图1看出,都是取25 min 最好,所以对两个指标来讲,焙烧时间均取25 min 最好. 从实际的焙烧过程来看,焙烧时间越长,反应越完全,抗压强度越高. 但这并不意味着焙烧时间越长,金属化率就越高,因为随着焙烧时间的延长,球团内部碳逐渐被消耗完,金属化球团会发生再氧化,从而降低金属化率.综合考虑C/O 、焙烧温度、焙烧时间3个因素对金属化率和抗压强度的影响以及工艺流程的实际要求,得出较好的实验方案为:A1:C/O ,第2水平,1.3;B3:焙烧温度,第3水平,1330℃;C3:焙烧时间,第3水平,25 min.从表6可以看出,这里综合分析出来的较好方案A1B3C3,正好是9组实验中的3#实验,其球团的金属化率(85.99%)和抗压强度(2155.67 N)在9组实验结果中的综合效果最好,与通过计算分析得到的结论一致.(3) XRD 分析对9组实验制得的金属化球团进行XRD 分析,可以看出金属铁均已经明显出现,尤其在金属化率较高的3#实验(85.99%)和5#实验(88.86%)制得的金属化球团中可明显看到假板钛矿(Fe 2TiO 5)的出现,如图2和3所示. 1020304050607080900500100015002000I n t e n s i t y (a .u .)2θ (o)102030405060708090050010001500200025002θ (o)I n t e n s i t y (a .u .)图2 C/O=1.3, T =1330℃, t =25 min (3#实验) 图3 C/O=1.5, T =1300℃, t =25 min (5#实验)Fig.2 C/O=1.3, T =1330℃, t =25 min (Exp.3#) Fig.3 C/O=1.5, T =1300℃, t =25 min (Exp.5#)对于钛铁矿在600℃至成渣温度范围内的还原机理、还原途径及其相变化,前人已有相当充分的研究,对1100 K 以上的Fe −Ti −O 系的相平衡关系也已经基本明确,在与钛铁矿还原有关的相图区域内存在3个主要固溶体也得到公认:在Fe −Fe 2O 3−TiO 2组成的三角形中,在1200℃时介于磁铁矿(Fe 3O 4)和钛铁晶石(Fe 2TiO 4)之间、介于赤铁矿(Fe 2O 3)和钛铁矿(FeO·TiO 2)之间、高铁假板钛矿(Fe 2TiO 5)和亚铁假板钛矿(FeTi 2O 5)之间,存在着完全固溶体,它们被认为是立方晶系的尖晶石相、菱形晶系的α-氧化铁固溶体和M 3O 5固溶体. 在达到1300℃并充分反应后,开始还原出假板钛矿,这与XRD 的分析结果相吻合.假板钛矿的生成能够有效提高球团的还原性能,一方面是因为用碳还原假板钛矿的速度要比还原钛铁矿和假金红石的速度快得多;另一方面钛铁矿从坚固的尖晶石结构变为不稳定的假板钛矿结构,形成大量空隙,改善了后续还原过程的动力学条件.增刊1 刘征建等:钒钛磁铁矿含碳球团转底炉直接还原实验研究555 结 论(1) 钒钛磁铁矿精矿粉与煤粉混合造球时,通过控制合适的压球机压力和转速、添加适量的水分和粘结剂可以保证其强度满足转底炉生产的要求.(2) 鼓风干燥和抽风干燥两种形式的干燥效果没有明显差别,风速控制在1 m/s,烘干10~15 min,脱水率可达到90%以上,完全满足生产要求.(3) 综合考虑3个因素对金属化率和抗压强度的影响以及工艺流程的实际要求,得出最优的实验方案是:C/O为1.3,焙烧温度为1330℃,焙烧时间为25 min.(4) 从9组实验得到金属化球团的XRD分析结果可以看出,金属铁均已经明显出现,尤其在金属化率较高的3#实验(85.99%)和5#实验(88.86%)制得的金属化球团中可以明显看到假板钛矿的出现,提高了球团的还原性能.参考文献:[1] 洪流,丁跃华,谢洪恩. 钒钛磁铁矿转底炉直接还原综合利用前景 [J]. 金属矿山,2007, (5): 10−13.[2] 胡俊鸽,吴美庆,毛艳丽. 直接还原炼铁技术的最新发展 [J]. 钢铁研究,2006, 34(2): 53−57. [3] 朱荣,任江涛,刘纲,等. 转底炉工艺的发展与实践 [J]. 北京科技大学学报,2007, 29(增刊1): 171−174.[4] 王定武. 转底炉工艺生产直接还原铁的现况和前景 [J]. 冶金管理,2007, (12): 53−55.[5] 黄洁. 谈转底炉的发展 [J]. 中国冶金,2007, 17(4): 23−25.[6] 杨保祥. 直接还原炼铁工艺现状及攀枝花钒钛磁铁矿处理工艺选择 [J]. 攀枝花科技与信息,2006, 31(3): 4−8.[7] 黄典冰,孔令坛,林宗彩. 生球干燥过程及其数学模型 [J]. 金属学报,1992, (12): 52−57.[8] Nagata K, Kojima R, Murakami T, et al. Mechanisms of Pig-ironMaking from Magnetite Ore Pellets Containing Coal at Low Temperature [J]. ISIJ Int., 2001, 41(11): 1316−1323.[9] Kasai E, Kitajima T, Kawaguchi T. Carbothermic Reduction in theCombustion Bed Packed with Composite Pellets of Iron Oxide and Coal [J]. ISIJ Int., 2000, 40(9): 842−849.[10] 郭汉杰. 冶金物理化学教程(第2版) [M]. 北京:冶金工业出版社,2004. 16.[11] 陈魁. 试验设计与分析(第2版) [M]. 北京:冶金工业出版社,1977. 78−81.[12] 徐萌,张建良,孔令坛,等. 以转底炉技术利用钛资源的基础研究 [J]. 有色金属(冶炼部分), 2005, (3): 24−29.[13] Sohn I, Fruehan R J. The Reduction of Iron Oxides by V olatiles in aRotary Hearth Furnace Process: Part Ⅲ. The Simulation of V olatile Reduction in a Multi-layer Rotary Hearth Furnace Process [J]. Metall.Mater. Trans. B: Process Metall. Mater. Process., 2006, 37(2): 231−238.Research on Direct Reduction of Coal-containing Pellets ofVanadic-titanomagnetite by Rotary Hearth FurnaceLIU Zheng-jian, YANG Guang-qing, XUE Qing-guo, ZHANG Jian-liang, YANG Tian-jun(University of Science and Technology Beijing, Beijing 100083, China)Abstract: The direct reduction of vanadic-titanomagnetite by rotary hearth furnace was studied in laboratory. The vanadic-titanomagnetite was mixed with coal and bentonite, then the green balls were made by pelletizer, and dried by hot gas which was produced by burning the hot gas of liquefied petroleum gas and air. The influential factors of metallized pellet strength and metallization rate, such as C/O, roasting temperature, roasting time, were examined by orthogonal experiments. The C/O, roasting temperature and roasting time of the optimum scheme were 1.3, 1300℃ and 25 min respectively. Pseudobrookite was found in pellets with high metallization rate by XRD.Key words: comprehensive utilization of resources; vanadic-titanomagnetite; rotary hearth furnace; direct reduction。
钒钛磁铁矿提钒工艺技术分析(3)

钒钛磁铁矿提钒工艺技术分析(3)5. 钒渣提纯钒工艺目前,由钒渣提取钒的工艺主要有钠化焙烧和钙化焙烧两种工艺。
5.1 钠化焙烧提钒钒渣中V2O5含量大约是10%~25%,对于从钒渣中提取V2O5的研究有很多,目前最为成熟的技术是钠化焙烧。
其基本原理是:添加苏打或食盐,然后焙烧,将钒转化为水溶性五价钒的钠盐,接着对焙烧产物进行水浸,得到含有少量杂质的含钒浸取液,之后通过酸性铵盐沉淀法制得偏钒酸铵沉淀,对其进行焙烧得到粗V2O5,再经过碱溶、除杂并用铵盐二次沉钒得偏钒酸铵,最后经过焙烧后可制得纯度大于98%的V2O5。
攀钢从钒渣中提取V2O5生产工艺包括氧化焙烧、水浸、净化和沉钒等过程,工艺流程如图13所示。
图13 攀钢V2O5生产工艺流程图5.2 钙化焙烧提钒由于钠化提钒法生产过程中产生大量有害气体(主要为氯气),向外排放含盐废水,对环境造成了严重污染,因此环境友好型的清洁生产技术—钙化焙烧提钒工艺越来越受到人们的重视。
钙化焙烧工艺在生产中没有产生有害烟气,且废水可以永久循环使用。
钙化焙烧提钒工艺是在钒渣中添加钙化合物(如碳酸钙)作熔剂,然后焙烧,使钒氧化成不溶于水的含钒钙盐,如Ca3(VO4)4、Ca(VO3)2和Ca2V2O7,再用酸控制合理的pH值将其浸出,浸出液经过净化后,除去Fe等杂质。
最后采用铵盐法沉钒,制偏酸铵并锻炼得高纯V2O5。
此工艺废气中不含HCl、Cl2等有害气体。
与钠化焙烧提钒工艺相比,钙化焙烧提钒工艺具有如下优点:1)采用石灰或石灰石作添加剂,可避免传统的钠化焙烧法高温焙烧时炉料烧结的问题,提高了焙烧设备的生产效率;2)放宽了对钒渣中氧化钙含量的限制;3)避免了添加剂硫酸钠或氯化钠等钠盐分解释放有害气体对环境造成污染。
此工艺缺点在于:1)浸出液中杂质多,产品中V2O5含量低;2)对浸出设备的耐腐蚀性要求高。
6. 总结(1) 钒钛磁铁精矿钠化焙烧工艺l 提钒流程短、钒回收率高,但是由于其对钒钛磁铁精矿中钒品位要求高、提钒后剩余物料中的铁和钛无法得到有效回收、化学药品消耗量大等原因只限于南非、澳大利亚等局部地区应用。
第四章钒钛磁铁矿直接还原工艺

4.1 回转窑还原工艺4.1.1 回转窑还原工艺流程预热带和还原带两部分。
在预热带物料没有大量吸热的反应,水当量小,虽然热速度比较小,但物料温升却比较大。
由于铁矿石与还原剂密切接触,还原反应约在700℃开始。
物料进入还原带后,还原反应大量进行,反应产生的CO从料层表面逸出,形成保护层,料层内有良好还原气氛。
料层逸出气体与空气燃烧形成稳定的氧化或弱氧化气氛。
因此回转窑还原有两种不同的气体。
窑内还原反应分为二步:CO2 + C = 2CO (1)F n O m + mCO = nFe + mCO2(2)气化反应在高炉冶炼过程是不希望的,而回转窑过程则是不可少的,进行得越快,越有利于窑内还原反应。
在不致产生结圈的前提下,窑内维持较高的温度,不仅有利于燃烧反应快速进行,而且使其窑头喷入的粉煤,窑中加入煤的燃烧生成的CO浓度增加,气化反应得以顺利发展,有利于窑内钒钛磁铁矿的还原反应。
由于气化属增压反应,窑内压力增加对反应不利,所以,当回转窑为了防止大量吸入冷空气而采用正压操作时,其正压值应当尽量的小,做到两兼顾。
攀枝花钒钛磁铁矿由于共生有钒钛等元素,因而它的还原是一个复杂的过程。
尤其在回转窑内,还原剂有气态的CO,H2(H2主要来自煤挥发物和少量的水的反应产物)以及固态的C,而且CO的还原作用又受煤气化反应的制约,这就更增加了过程的复杂性。
通过热力学和动力学的分析,在回转窑的特定条件下,C的还原作用是较为次要的,所以有时为了对窑内铁氧化物的还原过程进行分析计算,将过程简化为还原剂主要是CO和H2,而略去C在其中的直接还原作用。
钒钛磁铁矿球团在回转窑中用煤粉还原的还原历程可以简写为:7)回转窑脱硫入窑硫少量由铁矿石带入,大量(60%~90%)是还原剂和燃烧煤带入的。
钒钛磁铁矿中硫主要呈FeS2,FeS和磁黄铁矿形态。
矿石入窑后,随着温度升高,FeS2开始分解(300~600℃),900℃分解激烈进行。
煤中硫的形态复杂,多为有机硫、硫化物(FeS2,FeS,磁黄铁矿)和硫酸盐(CaSO4,Fe2(S04)3)三种形态。
- 1、下载文档前请自行甄别文档内容的完整性,平台不提供额外的编辑、内容补充、找答案等附加服务。
- 2、"仅部分预览"的文档,不可在线预览部分如存在完整性等问题,可反馈申请退款(可完整预览的文档不适用该条件!)。
- 3、如文档侵犯您的权益,请联系客服反馈,我们会尽快为您处理(人工客服工作时间:9:00-18:30)。
WU Xi 1,2,3,CHEN De-sheng2,3,WANG Li-na2,3, ZHAO Hong-xing2,3,ZHEN Yu-lan2,3,YU Hong-dong2,3,QI Tao2,3
2019 年 第 2 期 有 色 金 属 (冶 炼 部 分 )(http:??ysyl.bgrimm.cn) doi:10.3969/j.issn.1007-7545.2019.02.004
· 15 ·
钒钛磁铁精矿一步煤基直接还原—熔分的研究
吴 喜1,2,3,陈 德 胜2,3,王 丽 娜2,3,赵 宏 欣2,3,甄 玉 兰2,3,于 宏 东2,3,齐 涛2,3
(1.昆明理工大学 冶金与能源工程学院,昆明 650093; 2.中国科学院过程工程研究所 绿色过程与工程重点实验室,北京 100190; 3.中国科学院过程工程研究所 湿法冶金与清洁生产国家工程实验室 ,北京 100190)
摘要:以煤为还原剂、氢氧化钠为添加剂,采用一步 煤 基 直 接 还 原—熔 分 工 艺 对 国 内 某 钒 钛 磁 铁 精 矿 进 行研究。考察温度、时间、氢氧化钠添加量和 配 碳 量 对 还 原—熔 分 效 果、铁 回 收 率 和 钒 迁 移 的 影 响。 结 果表明,在温度1 300 ℃、时间4h、摩尔比 C/Fe=2.6,氢氧化钠添加量50%的最优条件下,铁回收 率 为 99.8%,渣中钒含量为1.34%。渣主要由 Na6Al4Si4O17、CaTiO3、NaAlSiO4 等 组 成,钒 主 要 赋 存 在 含 钛 渣 相 中 ,金 属 铁 相 中 几 乎 无 钒 的 存 在 。 关 键 词 :钒 钛 磁 铁 矿 ;直 接 还 原 ;回 收 率 ;熔 分 中 图 分 类 号 :TF557 文 献 标 志 码 :A 文 章 编 号 :1007-7545(2019)02-0015-06
钛 全 部 进 入 高 炉 渣 未 能 利 用 ,且 高 炉 需 要 炼 焦 ,环 境 污染严重 。 [2] 非高 炉 直 接 还 原 技 术 应 用 而 生,如 直 接 还 原 — 熔 分 工 艺 中 ,钒 进 入 铁 水 ,然 后 在 电 炉 中 熔 化分离,后续提钒 需 要 在 高 温 下 进 行 转 炉 氧 化 造 渣 和 钒 渣 的 钠 化 焙 烧 ,流 程 长 且 能 耗 高 ,需 多 步 高 温 过 程[3];在直接还原—磨选过程中,为使金属颗粒 长 大 需 提 高 还 原 温 度 和 加 入 添 加 剂 ,但 也 未 解 决 钒 、钛 的 利用问题。
(1.School of Metallurgy and Energy Engineering,Kunming University of Science and Technology,Kunming 650093,China; 2.Key Laboratory of Green Process and Engineering,Institute of Process Engineering,CAS,Beijing 100190,China; 3.National Engineering Laboratory of Hydrometallurgy and Clean Production,Institute of Process Engineering, CAS,Beijing 100190,China)
叉 团 队 项 目 资 助 ;中 国 科 学 院 前 沿 科 学 重 点 研 究 项 目 (QYZDJ-SSW-JSC021) 作 者简介:吴喜(1993-),男,湖南衡阳人,硕士研究生;通信作者:王丽娜(1974-),女,北京人,博士,研究员.
· 16 ·
有 色 金 属 (冶 炼 部 分 )(http:??ysyl.bgrimm.cn) 2019 年 第 2 期
Abstract:Vanadium titano-magnetite concentrate was studied by one-step coal-based direct reduction- melting process with coal as reductant and sodium hydroxide as additive.Effects of temperature,time and dosage of sodium hydroxide and carbon on reduction-melting,iron recovery and vanadium migration were investigated.The results show that iron recovery is 99.8% and vanadium content in slag is 1.34% under the optimum conditions including temperature of 1 300 ℃,time of 4h,C/Fe molar ratio of 2.6,and NaOH dosage of 50% .Main components of slag include Na6Al4Si4O17 ,CaTiO3and NaAlSiO4 .Vanadium mainly exists in Ti bearing slag phase while hardly exist in metallic iron phase. Key words:vanadium titano-magnetite;direct reduction;recovery;melting separation
钒钛磁铁矿 含 有 铁、钒、钛 等 有 价 金 属,是 一 种 多元共伴 生 复 杂 铁 矿 资 源,如 何 有 效 分 离 回 收 铁、
钒、钛具有重 要 意 义 。 [1] 现 有 工 业 生 产 采 用 高 炉 冶 炼钒钛磁铁矿,规 模 大、生 产 效 率 高,但 主 要 问 题 是
收 稿 日 期 :2018-10-26 基金项目:国家自然科学基金资助项目(51774260,21506233,21606241,51804289);中国科学院战略金属资源清 洁 利 用 创 新 交