热轧带钢轧制过程的稳定性探讨
热轧薄规格带钢精轧穿带稳定性的改善

区域治理前沿理论与策略九十年代初期,热轧工艺得以在国内迅速发展,该工艺具备耗能低,便于加工,生产效率高等特点。
热轧原理具体是在钢材退火温度足够高时进行轧制,经过这足够长的时间,在材料中产生无应变能力的新晶粒,新晶粒开始产生的温度就是再结晶温度的初始温度,新晶粒占据全部材料的时的温度为再结晶温度的终了温度,再结晶温度取初始温度与终了温度的平均值,一般情况下此温度主要受到材料成分与环境温度这两个因素的影响。
这便是关于热轧的简单原理,其实在我们的实际加工薄规格产品中主要的轧制方式而言,主要分为单坯轧制、半无头轧制以及全无头轧制三种方式,以下通过简单介绍这三种方式,进一步了解如何改善相关工艺的稳定性。
一、热轧薄规格产品的轧制方式、原理以及技术特点1.单块板坯轧制技术,其原理是将钢材的首尾安置在没有张力情况下,即非稳定轧制状态下进行生产的,这样轧制的钢材精度很难控制,比较容易造成钢材之间相互重叠。
当钢材的尾部离开精轧机时容易弯曲,制造的产品公差基数大,相对应的尺寸精度与性能达不到合格标准。
因此对于规格要求较薄的热轧板采用此技术生产时难度较大,且产品达不到所要求的性能指标。
2.半无头轧制技术,该技术原理是利用薄板坯连铸连轧生产线中长于普通板坯四到六倍的板坯,来保证带钢不间断进行轧制,再由相关的机器平均裁制成相等质量的钢材。
跟上述介绍的单块板坯轧制技术不同的是,此技术虽然对相关的生产设备以及技术提出了更高的要求,但是大幅度地提高了产品的生产效率,进而增强了产品的性能指标。
3.全无头轧制技术,具体原理是通过板坯对粗轧机与精轧机之间进行连接,并且在此过程中需要进行板坯加热以及协调两台加工设备之间的工作频率,才可最终实现无头轧制。
上述可见对技术要求相当高,尤其是粗轧机与精轧机的连接技术,直至上世纪九十年代末期,在日本的川崎钢厂此项技术才得以实现。
在我国粗轧机与精轧机之间的连接方式主要分为两种,即变形链接与感应加热链接,用以保障当板坯在进入精轧机后正常的运行。
热轧带钢生产工艺及常见质量问题探讨

规格的板带产品后被送至输出辊道,在层流冷却之后
带状、斑点状等形式在带钢表面分布,严重的会造成
由夹送辊送到卷曲工段,由卷取机、助卷辊等完成对
带钢表面出现粗糙麻点,斑痕问题主要是由于氧化铁
板带的卷曲,由打包机打包喷号后运至仓库内。
皮压入造成的。从生产工艺环节寻找原因:一是板坯
(1)粗轧。板坯由加热炉出来之后,表面会形成
具被快速磨损等问题。因此,对于热轧板带必须要保
Copyright©博看网. All Rights Reserved.
· 77 ·
·模具材料及热处理技术·
证其表面质量,要严格控制加热、轧制、高压水除鳞等
工艺,以消除质量隐患。
(4)对力学性能的要求。
对板带钢力学性能的要求主要包括:工艺性能、机
(3)冷却、卷曲。带钢经过精轧后,终轧温度约为
加工。
3
需要重点关注的技术要求。板坯质量是对其进行正
常热轧加工的基础,应要求板坯内部及外表面不得有
疏松、气孔、夹杂、偏析等缺陷问题。热轧板带主要具
有以下技术需求:
(1)尺寸精度要求高。尺寸精度主要包括长、宽
及厚度精度。尺寸精度是热轧板带生产中控制难度
最大的技术指标,对板带后续的再加工和使用性能影
响很大,其中厚度的精度更为突出,如果误差过大,会
5
热轧带钢生产常见的质量问题及原因分析
(1)裂纹问题。裂纹是带钢比较常见的表面质量
问题。热轧带钢表面裂纹多以纵裂纹的形式出现,且
热轧生产的工艺流程主要包括:加热、高压水除
深浅不同、长短各异。板坯本身就存在的各种裂纹缺
鳞、粗轧、开卷、剪切、精轧、冷却、卷曲这几道环节。
陷是导致带钢加工中产生裂纹的主要原因,而且这种
热轧带钢生产工艺及常见质量问题探讨
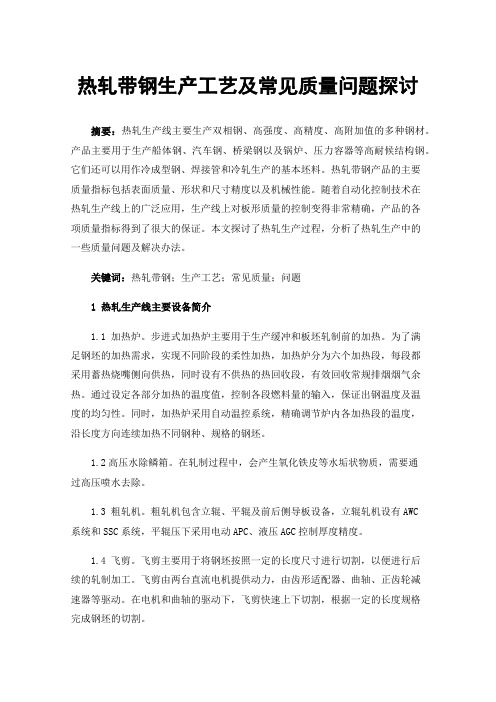
热轧带钢生产工艺及常见质量问题探讨摘要:热轧生产线主要生产双相钢、高强度、高精度、高附加值的多种钢材。
产品主要用于生产船体钢、汽车钢、桥梁钢以及锅炉、压力容器等高耐候结构钢。
它们还可以用作冷成型钢、焊接管和冷轧生产的基本坯料。
热轧带钢产品的主要质量指标包括表面质量、形状和尺寸精度以及机械性能。
随着自动化控制技术在热轧生产线上的广泛应用,生产线上对板形质量的控制变得非常精确,产品的各项质量指标得到了很大的保证。
本文探讨了热轧生产过程,分析了热轧生产中的一些质量问题及解决办法。
关键词:热轧带钢;生产工艺;常见质量;问题1热轧生产线主要设备简介1.1 加热炉。
步进式加热炉主要用于生产缓冲和板坯轧制前的加热。
为了满足钢坯的加热需求,实现不同阶段的柔性加热,加热炉分为六个加热段,每段都采用蓄热烧嘴侧向供热,同时设有不供热的热回收段,有效回收常规排烟烟气余热。
通过设定各部分加热的温度值,控制各段燃料量的输入,保证出钢温度及温度的均匀性。
同时,加热炉采用自动温控系统,精确调节炉内各加热段的温度,沿长度方向连续加热不同钢种、规格的钢坯。
1.2高压水除鳞箱。
在轧制过程中,会产生氧化铁皮等水垢状物质,需要通过高压喷水去除。
1.3 粗轧机。
粗轧机包含立辊、平辊及前后侧导板设备,立辊轧机设有AWC系统和SSC系统,平辊压下采用电动APC、液压AGC控制厚度精度。
1.4 飞剪。
飞剪主要用于将钢坯按照一定的长度尺寸进行切割,以便进行后续的轧制加工。
飞剪由两台直流电机提供动力,由齿形适配器、曲轴、正齿轮减速器等驱动。
在电机和曲轴的驱动下,飞剪快速上下切割,根据一定的长度规格完成钢坯的切割。
1.5 精轧机。
精轧机是一种高精度轧制工艺,利用液压AGC等自动控制和补偿系统,通过液压系统和轧辊轧制板坯。
它主要由电动机、联轴器、减速器等驱动和传动,以获得高精度的轧制件外观和尺寸。
1.6卷取机。
采用全液压三助卷辊强力卷取机,采用了无极涨缩试卷筒和自动踏步控制AJC系统。
现代热轧带钢生产过程中常见质量问题论文

现代热轧带钢生产过程中常见质量问题摘要:本文就目前国内钢铁企业热轧带钢生产过程中一般常见的质量问题,如轧件翘头、宽度尺寸超标、带钢浪形和镰刀弯等,提出了解决问题的具体措施。
并通过生产实践证明,这些措施的可行性。
关键词:热轧窄带钢轧件翘头宽度尺寸超标带钢浪形镰刀弯随着钢铁行业的竞争加剧,如何降低生产用原料的生产成本,减少因原料引起的质量问题,提高带钢质量,减少带钢镰刀弯,成为一个重要深题。
透过对热连轧带钢生产过程中出现的一系列常见质量问题进行分析,找出原因,提出解决这些问题的具体措施和方法,对提高热轧带钢产品质量,进而提高生产效率,降低生产成本具有重要的现实意义。
一、热轧带钢翘头热连轧穿带过程中,轧件上下表面受到轧辊的摩擦力不~致,使带钢头部上翘或下弯。
影响轧件所受摩擦力的主要因素有以下几方面。
1、下压力配置不当半连轧机组全部采用下压力轧制,即下辊的直径大于上辊,由予轧件在变形过程中的变形为均匀变形,带钢和下工作辊的接触面积大,下辊给带钢下表露的摩擦力大予上辊面使轧件有贴近下导卫的趋势,从而顺利穿带。
第l、2道次平轧机的下压力一般取6~8 mm,第3至第6道平轧机下压力一般取4~6 mm。
因此,在换工作辊时,要仔细检查轧辊的直径,确保下压力配置合适,当轧件的翘头严重时,往往是由于轧辊压力不合理所致。
2、压下量不合理轧机压下量不足时,常常弓|起带钢翘头,特别是第l、2道次压下量不足时,带钢的变形只发生在带钢的表面,因此带钢的前滑较少,由于下辊的圆周速度较大,引起带钢头部向上翘起。
3、上下工作辊磨损不均轧辊的磨损造成轧辊表面的粗糙度不一样,引起带钢的受力状态发生变化,从两引起带钢上翘或下弯。
在车削和装换轧辊时,要注意保证上下辊粗糙度一致。
4、轧件温度不均轧件受到冷却水、除鳞水的作甩,或者轧制故障引起轧件在轧制线上的停留,均会使轧件的温度不均。
因此轧件在轧制线上停留时,要前后移动,不要停留在一个位置,避免轧件局部传热、冷却较快。
热轧带钢精轧机轧制稳定装置研究

M achining and Application机械加工与应用热轧带钢精轧机轧制稳定装置研究孙 兵(北京首钢股份有限公司,河北 迁安 064404)摘 要:热轧带钢精轧机轧制的稳定性对金属轧制过程的正常操作有很大的影响。
对此,本文简要分析了带钢热轧机在工作时的稳定性,影响稳定油缸和水平刚度的原因,导卫设计问题和改进措施等,提供了一些技术参数,希望能给同行的相关工作者提供一些帮助。
关键词:热轧带钢;精轧机轧制;稳定性影响中图分类号:TG333.7 文献标识码:A 文章编号:11-5004(2019)01-0089-2热轧精轧机在生产过程中的稳定性,体现在轧件前端水平的稳定性,不会发生侧面抖动和偏差,并且后端不会出现移动的现象。
根据在实际工作中的经验,主要有三个因素影响轧机在工作中的稳定性,分别为:胚料的温度,轧辊机架的装配精度和精轧机入口端导卫精度[1]。
1轧机稳定工作的原理轧机的振动频率容易随着高速、高轧制力和大压下量轧制而增加。
经过详细试验,发现在实际生产过程中,轧机主要在上下工作辊的水平和垂直方向发生振动。
如果轧辊稳定器安装在框架和轴承座之间,增加了动态刚性在轧机机架和轧辊轴承座水平方向,有效的减少了轧机的振动频率。
在轧机生产过程中,稳定装置中的液压缸的垫圈与轴承座相接触,并在工作期间与轴承座一起振动[2]。
在设计液压缸时,一定要有阻尼孔,对轧机的振动有阻碍作用,有利于增强轧机的动态刚度。
试验机的振动信号进行观察,对于轧机的轧制方向(水平方向)和轧件厚度(垂直方向)的加速度信号,可以利用加速度传感器来测量获得。
当钢带放入轧机时,轧机就会开始振动[3]。
当轧机稳定装置开始工作时,轧件轧制方向上的加速度信号减小到稳定装置在开始工作时的一半。
轧机稳定器对工作辊所处的位置可以一直保持,改善了轧件的磨损。
2分析稳定装置在生产过程中的影响2.1 稳定油缸对轧机的影响为了在工作的过程中,工作人员易于更换轧辊,必须在工作辊,支撑辊和内侧衬板之间留下间隙:①在运行一段时间后,会发生摩擦在轧机的轴承座和衬板之间,致使两者之间的间隙逐渐变大,最终间隙超出正常值;②随着时间的推移立柱和支撑轴承之间的间隙也会增加,两只间隙也会超出正常值。
热轧带钢表面质量缺陷原因分析
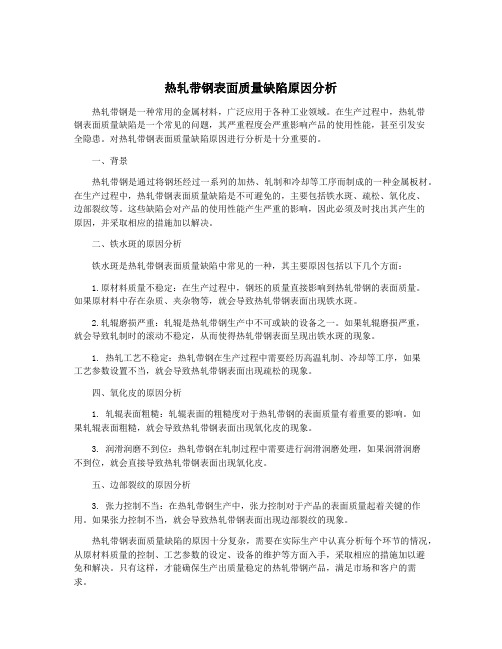
热轧带钢表面质量缺陷原因分析热轧带钢是一种常用的金属材料,广泛应用于各种工业领域。
在生产过程中,热轧带钢表面质量缺陷是一个常见的问题,其严重程度会严重影响产品的使用性能,甚至引发安全隐患。
对热轧带钢表面质量缺陷原因进行分析是十分重要的。
一、背景热轧带钢是通过将钢坯经过一系列的加热、轧制和冷却等工序而制成的一种金属板材。
在生产过程中,热轧带钢表面质量缺陷是不可避免的,主要包括铁水斑、疏松、氧化皮、边部裂纹等。
这些缺陷会对产品的使用性能产生严重的影响,因此必须及时找出其产生的原因,并采取相应的措施加以解决。
二、铁水斑的原因分析铁水斑是热轧带钢表面质量缺陷中常见的一种,其主要原因包括以下几个方面:1.原材料质量不稳定:在生产过程中,钢坯的质量直接影响到热轧带钢的表面质量。
如果原材料中存在杂质、夹杂物等,就会导致热轧带钢表面出现铁水斑。
2.轧辊磨损严重:轧辊是热轧带钢生产中不可或缺的设备之一。
如果轧辊磨损严重,就会导致轧制时的滚动不稳定,从而使得热轧带钢表面呈现出铁水斑的现象。
1. 热轧工艺不稳定:热轧带钢在生产过程中需要经历高温轧制、冷却等工序,如果工艺参数设置不当,就会导致热轧带钢表面出现疏松的现象。
四、氧化皮的原因分析1. 轧辊表面粗糙:轧辊表面的粗糙度对于热轧带钢的表面质量有着重要的影响。
如果轧辊表面粗糙,就会导致热轧带钢表面出现氧化皮的现象。
3. 润滑润磨不到位:热轧带钢在轧制过程中需要进行润滑润磨处理,如果润滑润磨不到位,就会直接导致热轧带钢表面出现氧化皮。
五、边部裂纹的原因分析3. 张力控制不当:在热轧带钢生产中,张力控制对于产品的表面质量起着关键的作用。
如果张力控制不当,就会导致热轧带钢表面出现边部裂纹的现象。
热轧带钢表面质量缺陷的原因十分复杂,需要在实际生产中认真分析每个环节的情况,从原材料质量的控制、工艺参数的设定、设备的维护等方面入手,采取相应的措施加以避免和解决。
只有这样,才能确保生产出质量稳定的热轧带钢产品,满足市场和客户的需求。
热轧耐候钢薄规格轧制稳定性探讨

科技专论热轧耐候钢薄规格轧制稳定性探讨【摘要】本文主要介绍了首钢京唐热轧1580在薄规格产品开发过程中所涉及到的轧制问题及采取的措施,通过不断摸索改进各种工艺及设备问题,使耐候钢减薄的轧制稳定性得到了很大提高。
【关键词】热轧1580;耐候钢;薄规格1、前言耐候钢,即耐大气腐蚀钢,是介于普通钢和不锈钢之间的低合金钢系列,耐候钢由普碳钢添加少量铜、镍等耐腐蚀元素而成,具有优质钢的强韧、塑延、成型、焊割、磨蚀、高温、抗疲劳等特性;耐候性为普碳钢的2~8倍,涂装性为普碳钢的1.5~10倍。
同时,它具有耐锈,使构件抗腐蚀延寿、减薄降耗,省工节能等特点。
耐候钢主要用于铁道、车辆、桥梁、塔架等长期暴露在大气中使用的钢结构。
用于制造集装箱、铁道车辆、石油井架、海港建筑、采油平台及化工石油设备中含硫化氢腐蚀介质的容器等结构件。
但热轧耐候钢薄规格轧制具有很大的不稳定性,带钢容易出现头部飞翘、尾部轧破甚至堆钢等异常事故,为稳定耐候钢薄规格生产,提高带钢成材率,本文以首钢京唐1580线轧制为例介绍了几种轧制主要问题及其解决方法。
2、轧制主要问题及解决方法2.1头部轧破2.1.1现象首钢京唐1580生产线最初轧制耐候钢薄规格时经常出现头部穿带时机架间突然起浪跑偏轧破还有F7出口头部轧破现象。
此现象主要是由于AGC压下不同步造成的。
由于AGC缸及伺服阀等各个液压元件的特性(响应速度、响应时间等)不一样,磁尺跟随性也不同,一个机架传动侧与操作侧在AGC下压永远存在不同步性,又由于精轧出口目标温度设定较低,机架间张力设定较小,这就对AGC控制提出了更高的要求,AGC调整稍有差异就会造成带钢起浪轧破。
2.1.2对策(1)AGC控制方面:AGC缸改进,增加防转槽防止AGC窜动影响轧制稳定性;监控AGC控制进行压下限幅,防止穿带时大幅下压引起轧机状态失稳,观察头部执行正常有效果;若AGC控制不稳定,可以在轧制前取消头部AGC,穿带完成稳定后投入。
热轧带钢精轧机轧制稳定装置研究
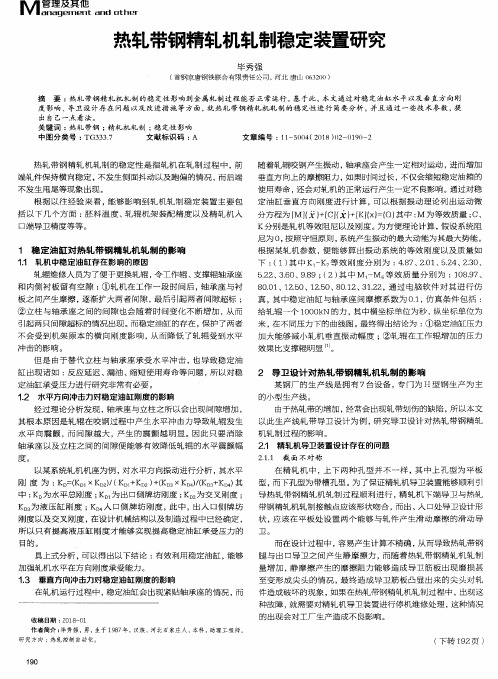
不 发 生 甩 尾 等 现 象 出现 。
使 用寿命 ,还会对 轧机的正常 运行产生一定 不 良影响 。通 过对稳
根 据 以 往 经 验 来 看 ,能 够 影 响 到 轧 机 轧 制 稳 定 装 置 主 要 包 定 油缸 垂直 方 向刚度 进行 计算 ,可 以根 据振 动理论 列 出运动 微
引起 两 只 间隙 超 标 的 情 况 出 现 。而 稳 定 油 缸 的 存 在 ,保 护 了 两者 米 ,在 不 同 压 力 下 的 曲线 图 。最 终 得 出结 论 为 :① 稳 定 油 缸 压 力
不 会受 到机 架原 本的 横 向刚度 影响 ,从而 降低 了轧辊 受 到水平 加大能 够减 小轧机 垂直振 动幅 度 ;②轧 辊在工 作辊 增加 的压力
K。。为 液 压缸 刚 度 ;K。 入 口侧牌 坊 刚度 ,此 中 ,出 入 口侧牌 坊 带 钢 精 轧 机 轧 制 接 触 点 应 该 形 状 吻 合 ,而 出 、入 口处 导 卫 设 计 形
轴 承座 以及 立柱之 间的 间隙便 能够 有效降 低轧辊 的水 平震颤 幅 2.1 精轧机导卫装置设计存 在的问题
度 。
2.1.1 截 面 不 对 称
以某系统 轧机机座 为例 ,对水平 方向振动进 行分析 ,其水 平
在精 轧 机 中 ,上 下 两种 孔型 并 不一 样 ,其 中上 孔 型 为平 板
括 以下 几个 方面 :胚料 温度 、轧辊 机架 装配 精度 以及精 轧 机入 分 方程 为 fM ]{ )十[c J( )+(K J{x)={Q)其 中 :M 为 等 效 质 量 ;c、
口端 导 卫 精 度 等 等 。
K分别 是轧机等 效阻尼 以及 刚度 。为方 便理论计算 ,假设系统 阻
实施精益生产提高热轧的产品质量、产能利用率和稳定性
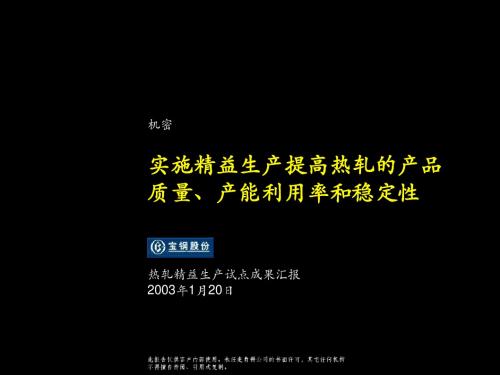
• 高层管理的决心和
参与
• 根据系统改善规划选
择项目
• 建立业绩管理系统 • 改善能力的培养
• 设置并培养改善专家 • 设置改善办公室
BS/030115/SH-PR(2000GB)
热轧的试点树立了良好的改善典范,为建立宝钢 持续改善方式打下了很好的基础
营运系统 解决问题的方法 • 在换辊、质量、维修 3个方面的试点都严 谨地用系统解决问题 的方法开展工作 解决问题的方法 改善工具和专业领域 知识
精益生产 六西格玛
“宝钢持续改善方式”
3
BS/030115/SH-PR(2000GB)
宝钢应将精益生产和六西格玛兼容并蓄,建立符 合宝钢特点的持续改善方式
营运系统 利用六西格玛 • 采用六西格 玛的DMAIC 标准化的, 严谨系统的 解决问题的 方法 解决问题的方法 改善工具和专业领域知识
• 在组织内部
密集型行业提高回报率 的关键手段
(不仅仅是突破性改进)?
2
BS/030115/SH-PR(2000GB)
精益生产和六西格玛都是企业实施营运改善的方 法,宝钢应兼容并蓄并加以创新以建立符合宝钢 特点的营运改善方法
全球领先的生产企业通过持之以恒地消 除生产系统和营运系统中的浪费和质量 波动,为股东创造了巨大的价值,并建 立起了长期的持续的竞争优势 精益生产和六西格玛的很多原则,工具 和方法可以为宝钢所用来提高公司业绩 和客户满意度 我们建议宝钢集精益生产和六西格玛之 精华,兼容并蓄,建立符合宝钢需要的 生产和营运方式以进行持续改善,应对 独特的战略和营运挑战
BS/030115/SH-PR(2000GB)
机密
实施精益生产提高热轧的产品 质量、产能利用率和稳定性
低合金钢热轧窄钢带的稳定性分析与调控
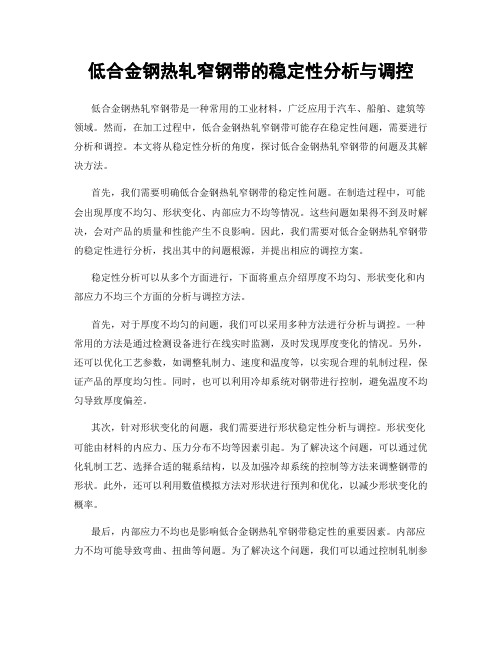
低合金钢热轧窄钢带的稳定性分析与调控低合金钢热轧窄钢带是一种常用的工业材料,广泛应用于汽车、船舶、建筑等领域。
然而,在加工过程中,低合金钢热轧窄钢带可能存在稳定性问题,需要进行分析和调控。
本文将从稳定性分析的角度,探讨低合金钢热轧窄钢带的问题及其解决方法。
首先,我们需要明确低合金钢热轧窄钢带的稳定性问题。
在制造过程中,可能会出现厚度不均匀、形状变化、内部应力不均等情况。
这些问题如果得不到及时解决,会对产品的质量和性能产生不良影响。
因此,我们需要对低合金钢热轧窄钢带的稳定性进行分析,找出其中的问题根源,并提出相应的调控方案。
稳定性分析可以从多个方面进行,下面将重点介绍厚度不均匀、形状变化和内部应力不均三个方面的分析与调控方法。
首先,对于厚度不均匀的问题,我们可以采用多种方法进行分析与调控。
一种常用的方法是通过检测设备进行在线实时监测,及时发现厚度变化的情况。
另外,还可以优化工艺参数,如调整轧制力、速度和温度等,以实现合理的轧制过程,保证产品的厚度均匀性。
同时,也可以利用冷却系统对钢带进行控制,避免温度不均匀导致厚度偏差。
其次,针对形状变化的问题,我们需要进行形状稳定性分析与调控。
形状变化可能由材料的内应力、压力分布不均等因素引起。
为了解决这个问题,可以通过优化轧制工艺、选择合适的辊系结构,以及加强冷却系统的控制等方法来调整钢带的形状。
此外,还可以利用数值模拟方法对形状进行预判和优化,以减少形状变化的概率。
最后,内部应力不均也是影响低合金钢热轧窄钢带稳定性的重要因素。
内部应力不均可能导致弯曲、扭曲等问题。
为了解决这个问题,我们可以通过控制轧制参数、进行热处理等方式降低内部应力。
此外,也可以使用适当的钢种和加工工艺,以减少内部应力的产生。
总之,低合金钢热轧窄钢带的稳定性问题是需要重视和解决的。
从厚度不均、形状变化和内部应力不均三个方面对稳定性进行分析与调控是有效的方法。
通过合理的工艺优化、设备检测以及数值模拟等手段,可以解决这些问题,提高产品的质量和性能。
轧机状态对轧制稳定性的影响

750
298.5
297.6
-0.008
0.050
0.9
是
F4
750
-0.037
0.050
4.1
是
290
285.9
F5
500
255.3
265.1
0.072
0.050
-9.8
否
F6
500
-0.039
0.050
5.8
是
276.9
271.1
F7
500
0.032
0.050-ຫໍສະໝຸດ .8是271.6276.4
2,同步性 设备系统旳同步性是确保稳定生产旳最基本旳条件,
例如:精轧机组两侧弯辊缸旳同步性、两侧压下系统 (AGC)旳同步性、侧导板两侧动作旳同步性。设备系 统同步性旳好坏主要取决于设备本身固有旳特征。
3,一致性 实际生产过程中轧机体现出来旳一致性,是衡量轧机
状态旳主要原则,它能够直接反应轧机目前旳状态是否 稳定。
辊缝弹跳
辊缝弹跳差 差(原则 )
刚度差(DSOS)
是否达标
F1
750
305.5
304.3
-0.010
0.050
1.2
是
F2
750
312.0
307.8
-0.033
0.050
4.2
是
F2
750
297.7
298.6
0.008
0.050
-0.9
是
F3
750
298.0
288.7
-0.081
0.050
9.3
否
F3
时间、材质横截面积旳大小、灌浆旳质量、地脚螺 栓直径及拉拔力旳大小等。 影响辊系刚度旳原因
热轧卷板精轧物料跟踪稳定性研究
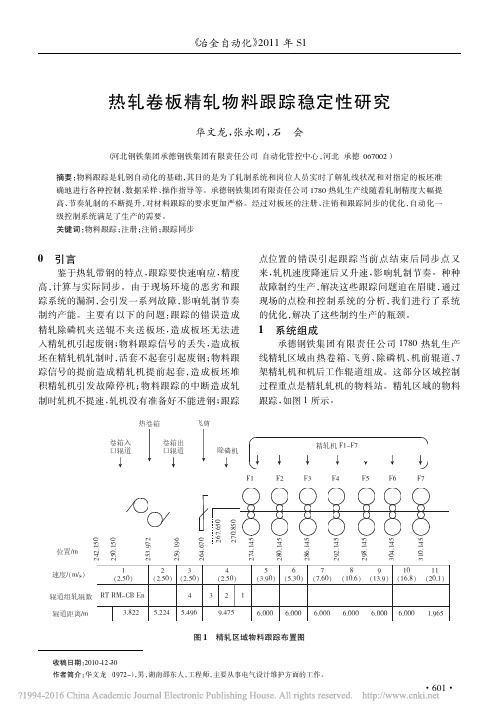
·603·
《冶金自动化》2011 年 S1
度更加准确,通过以上的优化杜绝了跟踪出错的 发生,提高了轧制节奏,如图 3 所示。
windowF1 open closed
这样板坯在不同的位置板坯将注册到不同的跟踪同步点例如板坯在热卷箱前hmd检得时该hmd信号的on将启动整个跟踪过程并在程序中进行逻辑运算这个过程是自动进行的无需操作人员确认o2板坯的注销当前板坯轧制结束或者轧线故障停车情况下为了重新轧制需要清除掉当前跟踪数据有3602
《冶金自动化》2011 年 S1