热轧带钢的生产方案和工艺处理步骤
不锈钢热轧带钢工艺流程

不锈钢热轧带钢工艺流程一、原料准备。
不锈钢热轧带钢的原料那可得好好准备呀。
这原料一般就是不锈钢板坯啦。
这些板坯就像是一个个等待变身的小战士呢。
它们在进入热轧工序之前,得先经过一系列的检查,就像我们人去体检一样,得确保它们没有啥缺陷,质量是合格的。
要是有不合格的板坯混进去了,那后面可就麻烦啦。
二、加热。
接下来就是加热这个环节啦。
板坯要被送到加热炉里去烤一烤呢,这个加热炉就像是一个超级大烤箱。
板坯在里面会被加热到一个很高的温度,这样它就变得软软的,就像一块软糖似的,这样就好进行后面的轧制啦。
而且这个温度可不能随便定哦,不同的不锈钢材质需要的加热温度是不一样的呢,就像不同的蛋糕需要不同的烤制温度一样。
如果温度没控制好,那做出来的带钢可能就会有问题啦。
三、轧制。
然后就到轧制啦。
这可是个很关键的步骤呢。
加热后的板坯会被送到轧机里面,轧机就像一个超级大力士,把软软的板坯一点点地轧薄。
轧机的轧辊就像两个大滚轮,不停地转动,把板坯轧成我们想要的厚度。
这个过程中,轧机的压力控制可重要啦,如果压力太大了,板坯可能就会被轧坏,如果压力太小呢,又达不到我们想要的厚度。
而且在轧制的时候,还得时刻注意板坯的形状,可不能让它轧着轧着就变形了呀。
四、卷取。
再之后就是卷取啦。
轧好的钢带就像一条长长的面条,这个时候要把它卷起来啦。
卷取机就像一个大卷筒,把钢带一圈一圈地卷起来,最后就形成了一个钢带卷。
这个钢带卷就像是一个超级大的卷饼一样。
卷取的时候也要注意很多细节呢,比如卷取的张力得合适,如果张力太大,钢带可能会被拉断,如果张力太小,钢带卷可能会卷得松松垮垮的。
五、冷却。
卷取好之后,钢带卷还得冷却一下呢。
就像我们刚做完运动要休息一下一样。
冷却的速度也有讲究哦,如果冷却太快,钢带可能会产生一些内部应力,这对钢带的质量可不好啦。
如果冷却太慢呢,又会影响生产效率。
六、精整。
最后就是精整这个环节啦。
钢带卷在这个环节会进行一些最后的加工处理,比如切割啊、检查表面质量啊之类的。
热轧带钢生产工艺介绍教学课件

05
CHAPTER
设备选型及维护管理
根据产品规格、材质和生产工艺要求,选用合适的轧机类型和规格。
轧机选型
考虑加热质量、能源消耗和设备寿命等因素,选用高效、节能的加热炉。
加热炉选型
根据带钢厚度、宽度和卷重等要求,选用合适的卷取机类型和规格。
卷取机选型
03
建立设备档案
记录设备的运行状况、维护保养情况、故障维修记录等信息,为设备管理提供依据。
学习态度与团队协作
THANKS
感谢您的观看。
应急预案制定
针对可能发生的安全事故,制定应急预案,并定期组织演练,提高应急处理能力。
利用余热回收技术,将生产过程中产生的余热进行回收利用,降低能源消耗。
余热回收
采用高效节能设备,如高效电机、变频器等,降低设备能耗。
节能设备应用
建设能源管理系统,对生产过程中的能源消耗进行实时监控和管理,提高能源利用效率。
能源管理系统建设
定期对节能减排技术应用效果进行评估,总结经验教训,持续改进节能减排工作。
减排效果评估
07
CHAPTER
总结与展望
通过测试、作业等方式评估学生对热轧带钢生产工艺知识的掌握程度。
知识掌握情况
组织学生参与实际生产操作,培养其运用所学知识解决实际问题的能力。
实践能力提升
考察学生在学习过程中的态度、参与度及团队协作能力。
冷却
通过水淬或空冷等方式,将热轧带钢冷却至适当温度,以改善其组织和性能。冷却速度和时间要根据带钢厚度和材质等因素进行控制。
平整
通过平整机对热轧带钢进行平整处理,消除其内应力和形状缺陷,提高带钢的平直度和表面质量。平整时要根据带钢的厚度、材质和表面状况等因素制定合理的平整工艺参数。
热轧带钢生产工艺

热轧带钢生产工艺热轧带钢生产工艺是一种重要的金属加工过程,主要用于将钢坯通过加热和加工,使其变形成为具有一定厚度和宽度的带状产品。
以下是热轧带钢生产过程的简要介绍:1.原材料准备:热轧带钢的原材料是钢坯,通常使用钢厂生产的连铸坯作为原料。
连铸坯经过切割和加热处理后,进入热轧工序。
2.预热和除鳞:钢坯进入预热炉,通过高温加热,使其达到适宜的轧制温度。
在预热的过程中,钢坯表面的氧化铁层会被除去,以确保钢材表面的质量。
3.粗轧:预热后的钢坯进入粗轧机,通过多道次的轧制和变形,使钢坯逐渐变窄、变长,并且增加其表面质量和机械性能。
粗轧过程中,利用轧机的辊轴和轧辊的间隙控制钢材的厚度和压制力。
4.中轧:粗轧后的钢坯进入中轧机,经过进一步的轧制和变形,钢材的宽度和厚度进一步减小。
中轧过程中,轧机的辊轴设定和冷却系统起到了重要的作用,控制了钢材的尺寸和温度。
5.精轧:中轧后的钢坯进入精轧机,通过较小的辊轴间隙和更高的轧制速度,进一步调整钢材的尺寸精度、表面质量和机械性能。
精轧机通常采用多辊式布局,以提高轧制效果和工作效率。
6.冷却和卷取:经过精轧后的钢材需要迅速冷却,以降低其温度,并使其硬度增加,从而提高其机械性能。
冷却方式通常有风冷和水冷两种方式。
冷却后的钢材进入卷取机,通过卷取装置将其卷取成具有一定尺寸的钢卷。
7.整平和切割:卷取后的钢材经过整平工序,通过辊轮的挤压和切割装置的切割,使钢卷表面平整,并切割成具有要求长度的带钢产品。
8.质量检测和包装:生产过程中,对热轧带钢的尺寸精度、表面质量和机械性能进行严格检测。
符合要求的带钢产品经过清洗、包装等工序,最终成为成品,供应给客户使用。
热轧带钢生产工艺是一个复杂的过程,需要严格控制各个工序的参数和运行状态,以确保钢材的品质和性能。
同时,还需关注节能减排和环境保护,提高工艺的可持续性和经济性。
热轧带钢的生产工艺流程

热轧带钢的生产工艺流程
生产工艺流程:
一、原料准备
1、钢种选择:热轧带钢所用的钢种是碳素钢、合金碳素钢或深冷钢等。
2、原料回火:取回火温度较高的原材料,使材料更有韧性,在热轧过程中不易破坏。
二、热轧总体工艺
1、热轧:热轧需要热轧设备和热轧坯,热轧坯需要进行弯曲、拉伸、压缩等,按照要求的尺寸进行金属定型,得到热轧带钢。
2、冷轧:把热轧带钢经过冷轧后进行精调,精调过程中要认真确保尺寸和外观质量要求,保证本次热轧工艺流程可靠有效。
三、热处理
1、回火:热轧后的带钢需要进行回火,回火使得钢材回复到机械性能最佳状态,调节其组织,使得更加柔韧有韧性。
2、淬火:淬火可以使带钢有良好的抗疲劳性和伸长率,用以提高带钢的可靠性。
四、检验
1、外部检查:外部检查是检查带钢在外观上是否有瑕疵以及有多少瑕疵,以及它们是如何影响性能和质量的。
2、抗拉和抗压检验:确保带钢能承受一定数量的压力剪切应力,保证带钢在后续使用中不会发生断裂等异常现象。
五、包装
1、如果是散装,应使用打包带或木箱包装。
2、运输:可选择陆路运输、水路运输、航空运输或综合运输等方式,依据现场的要求进行选择。
600mm热轧带钢工艺方案(2005.5)
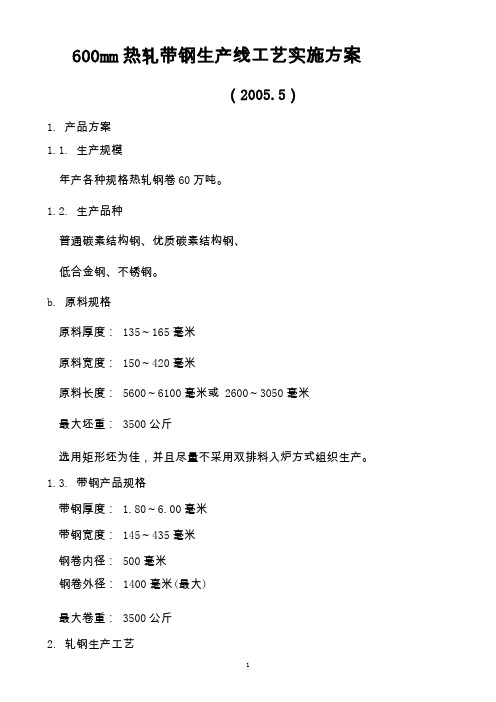
600mm热轧带钢生产线工艺实施方案(2005.5)1. 产品方案1.1. 生产规模年产各种规格热轧钢卷60万吨。
1.2. 生产品种普通碳素结构钢、优质碳素结构钢、低合金钢、不锈钢。
b. 原料规格原料厚度: 135~165毫米原料宽度: 150~420毫米原料长度: 5600~6100毫米或 2600~3050毫米最大坯重: 3500公斤选用矩形坯为佳,并且尽量不采用双排料入炉方式组织生产。
1.3. 带钢产品规格带钢厚度: 1.80~6.00毫米带钢宽度: 145~435毫米钢卷内径: 500毫米钢卷外径: 1400毫米(最大)最大卷重: 3500公斤2. 轧钢生产工艺2.1. 执行标准热轧窄带钢是按国家标准组织生产、检验和交货,主要执行的国家标准有:GB/T13304—91 《钢分类》GB/T699—88 《优质碳素结构钢技术条件》GB/T700—88 《碳素结构钢》GB/T1591—94 《低合金高强度结构钢》GB/T1220—84 《不锈钢棒》YB/T2011—83 《连续铸钢方坯和矩形坯》YB/T001—91 《初轧坯尺寸、外形、重量及允许偏差》YB/T002—91 《热轧钢坯尺寸、外形、重量及允许偏差》GB/T8164—93 《焊接钢管用钢带》GB/T3524—92 《碳素结构钢和低合金结构钢热轧钢带》GB/T710—91 《优质碳素结构钢热轧薄钢板和钢带》GB/T5090—93 《不锈钢热轧钢带》GB/T228—87 《金属拉伸试验方法》GB/T4230—84 《金属压缩试验方法》GB/T6397—86 《金属拉伸试验试样》GB/T709—88 《热轧钢板和钢带的尺寸、外形、重量及允许偏差》GB/T247—97 《钢板和钢带检验、包装、标志及质量证明书的一般规定》2.2. 金属平衡见表一表一:金属平衡表2.3. 生产工艺流程a.热轧带钢生产工艺流程原料准备→排料→加热→出钢→粗轧立轧→粗轧平轧→飞剪切头→精轧→扭转→夹送→蛇振→冷却及在线热检→引头→卷曲及一次打包→冷却及二次打包→翻卷→收集→标记→过秤计量→入库→复检→发货b.热轧窄带钢生产工艺流程简述检查合格的原料经秤重后,接送入车间原料跨码垛;排料于上料辊道输送至炉后,并对正加热炉纵水管,由推钢机推入燃气连续蓄热式加热炉内加热。
热连轧带钢生产工艺

1)立辊轧机
• 立辊轧机位于粗轧机水平轧机的前面,大多数立辊轧机的 牌坊与水平轧机的牌坊连接在一起。立辊轧机主要分为两 大类,即一般立辊轧机和有AWC功能的重型立辊轧机。 • 一般立辊轧机结构简单,主传动电机功率小、侧压能力普 遍较小,而且控制水平低,辊缝设定为摆死辊缝,不能在 轧制过程中进行调节,带坯宽度控制精度不高。 • 有AWC功能立辊轧机结构先进,主传动电机功率大,侧压 能力大,具有AWC功能,在轧制过程中对带坯进行调宽、 控宽及头尾形状控制,不仅可以减少连铸板坯的宽度规格, 而且有利于实现热轧带钢板坯的热装,提高带坯宽度精度 和减少切损。
5、精轧机组
• 精轧机组是成品轧机,布置在粗轧机组中间辊道或热卷箱 的后面,是带钢热连轧线的核心设备。精轧是决定产品质 量的主要工序,带钢的力学性能主要取决于精轧机终轧温 度和卷取温度。
1)精轧机组布置
• 精轧机组的布置有多种形式,在我国的热轧带钢轧机中, 精轧机组的布置主要有5种,如图2-13-18所示。 • 鞍钢1700和攀钢1450的精轧机组布置同属a类 • 武钢1700和本钢1700的精轧机组布置属b类 • 太钢1549和梅钢1422的精轧机组布置属c类 • 宝钢2050和鞍钢1780的精轧机组均布置属 d 或e类
3、粗轧机
粗轧机的水平轧机是把热板坯减薄成适合于精轧机轧制 的中间带坯。粗轧机的布置有四种方案。
1)全连续式
粗轧区设置5~6 台粗轧机进行连续(不可逆)轧制, 这种布置由于粗轧道次限制为5~6 道次,加上设备重量 过大,生产线过长,目前基本不再采用。
2)3/4连续式
3/4连续式粗轧机由可逆式轧机和不可逆式轧机 组成 。这一布置增加了灵活性,缩短了轧线长度, 但设备重量仍较大。
2)定宽压力机
热轧型钢工艺流程
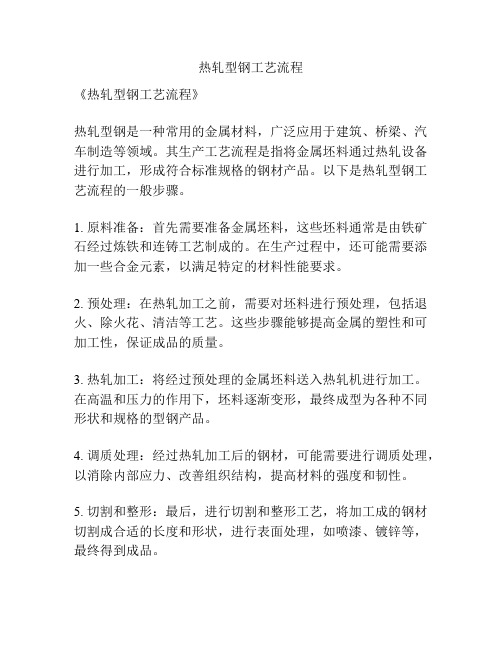
热轧型钢工艺流程
《热轧型钢工艺流程》
热轧型钢是一种常用的金属材料,广泛应用于建筑、桥梁、汽车制造等领域。
其生产工艺流程是指将金属坯料通过热轧设备进行加工,形成符合标准规格的钢材产品。
以下是热轧型钢工艺流程的一般步骤。
1. 原料准备:首先需要准备金属坯料,这些坯料通常是由铁矿石经过炼铁和连铸工艺制成的。
在生产过程中,还可能需要添加一些合金元素,以满足特定的材料性能要求。
2. 预处理:在热轧加工之前,需要对坯料进行预处理,包括退火、除火花、清洁等工艺。
这些步骤能够提高金属的塑性和可加工性,保证成品的质量。
3. 热轧加工:将经过预处理的金属坯料送入热轧机进行加工。
在高温和压力的作用下,坯料逐渐变形,最终成型为各种不同形状和规格的型钢产品。
4. 调质处理:经过热轧加工后的钢材,可能需要进行调质处理,以消除内部应力、改善组织结构,提高材料的强度和韧性。
5. 切割和整形:最后,进行切割和整形工艺,将加工成的钢材切割成合适的长度和形状,进行表面处理,如喷漆、镀锌等,最终得到成品。
总的来说,热轧型钢工艺流程是一个复杂的加工过程,需要多种工艺和设备配合完成。
在整个生产过程中,需要严格控制加工参数、材料质量,以确保最终产品符合规格要求。
同时,还需要关注环保和能源消耗等方面的问题,促进产业的可持续发展。
热轧带钢生产工艺介绍课件

通过调整电机转速和轧制力,实现自动速度控制。
速度波动抑制
通过优化轧机设计和采用先进的控制系统,减少速度波动,提高生 产效率。
04
热轧带钢生产质量问题及 解决方案
板形问题及解决方案
板形不良
板形不良是热轧带钢生产中的常见问题,会导致带钢板形不平整,影响后续加 工和使用性能。
解决方案
针对板形不良问题,可以采取以下措施进行解决:控制轧制温度和速度、调整 辊缝和弯辊力、更换工作辊或支撑辊等。
XX钢厂的热轧带钢产品研发及市场应用案例
• 总结词:XX钢厂通过产品研发及市场应用案例,展示了热轧带钢在汽车、建 筑等领域的应用前景。
• 详细描述:XX钢厂在热轧带钢产品研发方面投入了大量精力,开发了一系列 新型热轧带钢产品。这些产品在强度、韧性、耐腐蚀性等方面具有良好的性能 表现,适用于汽车、建筑等领域。为了推广这些新产品,该钢厂积极与下游客 户进行合作,开展了一系列的市场应用案例。例如,他们与一家汽车制造商合 作,将新型热轧带钢应用于汽车车身制造中,提高了车身的强度和耐腐蚀性, 同时也降低了制造成本。此外,他们还与一家建筑公司合作,将新型热轧带钢 应用于建筑结构中,提高了建筑的结构安全性和稳定性。这些市场应用案例充 分展示了热轧带钢在汽车、建筑等领域的应用前景和市场潜力。
表面质量问题和解决方案
表面粗糙
表面粗糙会使热轧带钢表面不光滑,影响其美观度和使用性能。
解决方案
为了解决表面粗糙问题,可以采取以下措施:定期修磨轧辊、 使用合适的轧制润滑剂、控制轧制温度和速度等。
性能问题及解决方案
强度不足
强度不足是热轧带钢的一个重要问题,会导致带钢在后续加工和使用过程中出现 断裂等现象。
加热温度
- 1、下载文档前请自行甄别文档内容的完整性,平台不提供额外的编辑、内容补充、找答案等附加服务。
- 2、"仅部分预览"的文档,不可在线预览部分如存在完整性等问题,可反馈申请退款(可完整预览的文档不适用该条件!)。
- 3、如文档侵犯您的权益,请联系客服反馈,我们会尽快为您处理(人工客服工作时间:9:00-18:30)。
热轧
160
53
Q275
1600)
12Mn2A, (2.5 ~ 5.0) ×
合金结构钢 16Mn2A (1400 ~
30Cr,40Cr 1600)
热轧
65
22
45Cr,45Mn
不锈钢
牌号
1Cr13, (2.0~6.0)×
0Cr18Ni9 (850~1700)
热轧
75
1Cr18Ni9
1Cr18Ni9Ti
2.1.2 编制产品方案的原则及方法
(1) 国民经济发展对产品的要求,既考虑当前的急需又要考虑将来发展的 需要。
(2) 产品的平衡,考虑全国各地的布局和配套加以平衡。 (3) 建厂地区的条件、生产资源、自然条件、投资等可能性。 (4) 考虑轧机生产能力的充分发挥,提高轧机的生产技术水平。
2.1.3 选择计算产品
钢板和钢带的表面允许有深度和高度不大于厚度公差之半的折印、麻点、划 伤、小拉痕、压痕以及氧化铁皮脱落所造成的表面粗糙等局部缺陷。对表面的薄 层氧化铁皮、轻微铁锈和残余涂料、活痕等不影响表面质量的局部缺陷亦允许存 在。
钢板和钢带表面的局部缺陷,允许用修磨方法清除,但清除深度不得大于钢 板和钢带厚度公差之半。
3.2.1板坯的选择和轧前准备
热轧带钢生产所用的板坯主要是连铸板坯,只有少量尚存初轧机冶金工厂采
用初轧坯。
板坯的选择主要是板坯的几何尺寸和重量的确定。板坯的厚度选择要根据产
品厚度,考虑板坯连铸机和热轧带钢轧机的生产能力。一般板坯的厚度为
150-250mm,最厚为300-350mm。板坯的宽度选择决定于成品宽度,一般板
表 2.2 典型产品
规格
状态
年产量(万 比例(%)
25
技术条件
吨)
Q215
10×1600
热轧
160
30Cr
4.0×1400
热轧
65
1Cr18Ni9 2.0×1000
热轧
75
_
53
见表 2.3
22
见表 2.4
25
见表 2.5
表 2.3 Q215 技术条件
牌号 等级 C
化学成分%
Mn
Si
S
脱氧方
P
法
Q21 A 0.09~ 0.25~ ≤0.30 ≤
后冷却,精整和质量检查等工序,对于特殊要求的钢种,在加热后不需经过热处
理等工序。本车间的生产工艺流程如图 3.1 所示。
图3.1 生产工艺流程图
板坯加热板
除磷
粗轧 机
热卷箱
剪切机
精轧前除磷 (水、蒸汽)
_
钢卷取样
热卷箱炉
钢卷运输
卷取
层流冷却
精轧机
入库
打包、验收
发货
平整分卷
打包、验收、发货
3.2 生产工艺过程简述
屈服点 σs
(N/mm)
抗拉强度 σb (N/mm)
伸长率 δs(%)
在宽度>1000~
1500,厚
30Cr A
≥345
470~630
11
度>1.80~2.00 时
为±0.16
注:表面质量:钢板和钢带的表面不允许有裂纹、结疤、折叠、气泡和夹杂。 钢板和钢带不得有分层。
_
钢板和钢带的表面允许有深度和高度不大于厚度公差之半的折印、麻点、划 伤、小拉痕、压痕以及氧化铁皮脱落所造成的表面粗糙等局部缺陷。对表面的薄 层氧化铁皮、轻微铁锈和残余涂料、活痕等不影响表面质量的局部缺陷亦允许存 在。
图1 某钢厂的步进梁式加热炉 板坯一般加热到1200-1250℃出炉,部分碳素钢和某些低合金结构钢采用 低温出炉工艺,其出炉温度约为1100℃。 3.3.2粗轧 粗轧机组的作用是将加热好的板坯经过除磷、定宽、水平辊和立棍轧制,将 不同规格的板坯轧成厚度为30-60mm,宽度不同的精轧坯,并保证精轧坯要求 的温度。 ①除磷
≥205 ≥570 ≥45
≤90
体型 1150
≤200
快冷
注:特性和用途:经冷加工有高的强度,但伸长率比 1Cr17Ni7 稍差。用 于建筑装饰部件,不锈耐酸的外壳,浮筒以及船舶控制设备的低磁性设备。
_
3 生产工艺流程制定
3.1 制定生产工艺流程的主要依据
所谓生产工艺流程就是把产品的生产工序按次序排列起来。正确制定工艺过 程是轧钢车间工艺设计的重要内容。制定轧钢生产工艺过程的首要目的是为了获 得质量符合要求的产品,其次要在保证质量的基础上追求轧机的高产量,并能做 到降低各种原料、材料消耗,降低产品成本。因此,正确制定产品工艺过程,对 于工艺过程合理化,对于充分发挥轧机作用具有重要意义。
成品带钢经精轧机组后的输出辊道上的层流冷却系统后,使温度降到规定的 卷曲温度,由液压助卷卷曲机卷成钢卷。卷曲完后,由卸卷小车将钢卷托出卷曲 机,经卧式自动打捆机打捆后,再由卧式翻卷机将钢卷翻卷成立卷放在链式运输 机中心位置上,由链式运输机和步进梁运送钢卷,必要时将钢卷送到检查机组打 开钢卷头部进行检查。钢卷经称重打印后根据下一工序决定钢卷的流向。去精整 线的钢卷先翻成卧卷再由运输机送到本车间热钢卷库分别进行加工;去冷轧厂的 钢卷由运输机运到钢卷转运站,再由钢卷运输小车送至冷轧厂。
~ 1.0
10.0
≤ 0.035
≤ 0.03
厚度 6.0~ 厚度≥6.0,宽
8.0,宽度 度 630~
<1000 时 1000 时为±
为±0.60
10
拉力实验
硬度实验
固溶 屈服强
抗拉强
牌号 类型 处理
度σ
伸长率
度σ
HRB
HV
(℃) 0.2(MPa
δs(%)
b(MPa)
)
1010
奥氏 ~
1Cr18Ni9
_
所选的所有计算产品要通过各工序,但不是说第一种计算产品都通过各工 序,而是所有计算产品综合起来看的。
(3)所选的计算产品要与接近。 (4)计算产品要留一定的调整余量,也就是说所选的计算产品要品种灵活, 容易生产多种规格的产品。 本 次 设 计 选 用 的 三 个 典 型 产 品 分 别 是 : Q215(10.0mm × 1600mm) 、 30Cr(4.0mm×1400mm)、1Cr18Ni9(2.0mm×1000mm)。 2.1.4 确定产品大纲
_
的中间带坯。带坯经中间辊道送至切头习剪剪去带坯头、尾,然后经精轧机前除 鳞设备除去带坯表面的氧化铁皮,送入精轧机组轧制。
粗轧机组产生废带坯,由设在中间辊道传动侧的废品推出机推至废品台架 上,切割后用载重小车运走。为了减少带坯在中间辊道上的温降和带坯头尾温差, 在中间辊道上设有保温罩。为减少切损,切头飞剪设有最佳化剪切系统。带坯经 七机架四辊式连轧机组轧制成厚度为 2.0~10.0 的成品带钢。为确保轧制精度和 控制板型,在 F1~F7 精轧机上设有动作灵敏、控制精度高的液压 AGC 厚度自 动控制系统。该控制系统代替过去常规采用的电动活陶器和微张力控制两套系 统。
钢带允许带缺陷交货,但缺陷部分不得超过每卷长度的 8%。
表 2.4 30Cr 的技术条件
牌号 等级 C Mn V
化学成分%
Nb
Si
Ti
S
P
≤ 0.5 0.02 0.015
0.02
≤
≤
≤
30Cr A 0.2 ~ ~
~
~
0.55
0.045 0.045
0 0.8 0.15 0.060
0.20
牌号 等级
厚度偏差
实际生产中为了满足用户客观上的使用要求,每个品种都必须满足形状、尺 寸规格和内部性能的要求。因而,各类产品的分类、编制、牌号、化学成分、品 种规格和尺寸公差、生产技术条件、机械性能、验收规程、试验及包装方法、交 货状态等,国家均有标准规定,如国标、冶标、企标等,如果国家没有标准规定, 可由生产厂家和客户商定。
根据已制定的生产方案,在充分完成产品产量质量要求的前提条件下,用最 大可能的低消耗、最少的设备、最小的车间面积、最低的劳动成本,并有利于产 品的质量的提高和发展,有较好的劳动条件,最好的经济效益,具体的原则包括: 产品的技术条件,生产规模大小,产品成本和工人的劳动条件。
热轧板带生产的一般工艺流程是:原料的清理准备,坯料考虑以下几点: (1)金属与合金的品种、规格、状态及质量要求。 (2)年产量的大小。产量不仅决定工艺过程的特点,同时也对设备选择、 铸锭尺寸、产品规格有着直接的影响。 (3)投资、建设速度、机械化和自动化程度、劳动条件、工人与管理售货 员的数量以及将来的发展。 2.2.2 制定生产方案
钢板和钢带表面的局部缺陷,允许用修磨方法清除,但清除深度不得大于钢 板和钢带厚度公差之半。
钢带允许带缺陷交货,但缺陷部分不得超过每卷长度的 8%。 表 2.5 1Cr18Ni9 的技术条件
牌号
C
Cr
Ni
Si
P
厚度偏差 宽度偏差
S
(mm)
(mm)
1Cr18Ni9
≤ 0.15
17.0 ~
19.0
8.0 ≤
根据设计任务书要求和上述原则,确定车间产 品大纲,见表 2.1。典型产 品见表 2.2。典型产品技术要求见表 2.3 到 2.5。
2.2 生产方案
所谓生产方案量指为完成设计任务书中所规定的产品的生产任务而采取的 生产方法。根据设计规模、产品的质量及经济技术指标的要求,考虑当地的具体 条件,找出合理的生产方案。