北京科技大学蔡开科讲座资料 连铸坯(圆坯)质量控制
连铸坯质量控制

连铸坯质量控制连铸坯质量控制引言连铸坯质量是决定钢铁产品质量的重要因素之一。
在连铸过程中,通过控制连铸坯的凝固结晶形貌、尺寸尺寸以及内部缺陷等,可以保证最终钢铁产品的质量稳定性。
本文将介绍连铸坯质量控制的基本原则和常用技术手段。
1. 连铸坯凝固结晶形貌控制1.1 凝固路径设计连铸坯的凝固路径设计是影响凝固结晶形貌的关键因素。
凝固路径包括主要凝固温度区间、凝固速度以及凝固过程中应有的温度梯度等要点。
通过科学合理地设计凝固路径,可以控制连铸坯的凝固结晶形貌,提高产品的均匀性和致密性。
1.2 凝固浸没深度控制凝固浸没深度是指连铸坯在铸机中浸没的深度。
凝固浸没深度的调整可以通过调整浇注速度、浇注高度和结晶器深度等因素来实现。
恰当地控制凝固浸没深度可以优化凝固结构,减少坯壳厚度和缩孔等缺陷的发生。
2. 连铸坯尺寸控制2.1 坯型设计连铸坯的尺寸控制需要科学合理地设计坯型。
坯型设计要考虑连铸机的性能和工艺条件,以及产品需要达到的尺寸要求。
有效的坯型设计可以保证连铸坯尺寸的精确控制,减少修磨损失并提高铸坯产量。
2.2 坯型换边控制连铸坯在连铸过程中,由于挤压力和引拉力的作用,容易发生坯型换边的情况。
坯型换边会导致铸轧过程中尺寸控制困难,甚至导致产品尺寸不合格。
通过控制连铸机的工艺参数和优化设备结构,可以有效地控制坯型换边,提高铸坯质量。
3. 连铸坯内部缺陷控制3.1 结晶器设计结晶器是连铸过程中控制坯内部缺陷的关键设备。
结晶器的设计应考虑到坯内部的流动状态,并通过合理的传热和传质方式,控制连铸坯内的气体和夹杂物等缺陷。
合理的结晶器设计可以有效减少坯内部夹杂物和气体等缺陷的产生。
3.2 液相线保护措施液相线是连铸过程中凝固结构变化的关键位置。
液相线的形成过早或过晚都会导致内部缺陷的产生。
通过合理的冷却水设定和轧制工艺,可以保证液相线的稳定形成,有效控制坯内部缺陷。
结论连铸坯质量控制是保证钢铁产品质量稳定的关键环节。
连铸坯质量控制

《连铸坯质量控制》(之前上传的只讲了1/2,完整版再次传给朋友们共享。
在此祝朋友们好!对中天给予我的方便表示衷心感谢!),第1~第6共6章,占全书的1/3左右。
讲转炉冶炼+炉外精炼的一些基本知识,可以不用看,第7章起真正接触连铸坯质量控制知识。
虽然有《连铸铸钢生产》(河北工业职业技术学院冯捷的职工培训教材)、《连铸铸钢》(武汉科技大学陈雷的教材)、《连续铸钢原理与工艺》(北科大蔡开科、程士富的教材)、《新编连续铸钢工艺及设备》(首钢工学院王雅贞的中专教材)、《品种钢、优特钢连铸900问》(工程院院士干勇主编的冶金科学技术普及读物),但以这本《连铸坯质量控制》(蔡开科的独著)讲的最好。
好就好在深奥的道理用浅显易懂的文字进行了表述,而且极大部分知识正在工厂中应用着并改进着。
所以,我原来的单位——沙钢也将这本教材作为培训用书(我89年7月~07年7月在沙钢工作),许茂清同志制作了100多页的PPT培训讲义。
《连铸坯质量控制》的内容,我的理解为(个人观点,本人学的是机械制造,做了4年多时间钳工,94年以后才自豪奋勇去干炉长,从此和炼钢结下了不解之缘,走上了不归路。
我不是科班出生,我的观点、书中的文本框意见仅供朋友们参考,请中天的朋友们指正!):①一只中间包,从120mm的涂层厚度到换下时<30mm的涂层厚度,这10多个小时侵蚀掉的100kg左右的90mm厚镁质涂料,怎么去除?②控制中心偏析(特别是C、Mn偏析)。
一是工艺参数,包括过热度、拉速(恒速、保持结晶器液面稳定,减少偏析)、比水量等;二是设备参数,a、电磁搅拌,小方坯而言,是M-EMS、还是M-IEMS、还是(M+F)-EMS;b、出足辊后为防止鼓肚,要不要密排辊,密排辊的距离需多少,会不会影响漏钢后冷钢的清理,鼓肚的实质也是解决中心偏析;c、支撑辊对中技术,钢柔性对弧样板自身的弧度准不准、对弧时的操作技巧等,支撑辊对中的目的也是通过减少鼓肚达到减轻中心偏析的目的;d、为什么品种钢如SWRCH6~35K(碳素钢冷镦盘圆用钢)、SCM435(合金钢冷镦盘圆用钢)、L09D70等钢帘线用钢、82A PC钢绞线用钢(见我整理的沙钢高品质线材的研发现状)等必须降低拉速,原因是通过降低拉速,达到二冷缓冷的目的,而缓冷又可增加等轴晶的比率,等轴晶增加了,又可以达到减轻中心偏析(低倍检测)、缩孔、疏松的目的,所以,控速的根本目的是提高质量,改善偏析;e、高温钢的危害,除易漏钢外,还导致柱状晶的比例增加,偏析(宏观、微观)加重,总之,在高效连铸机、优特钢普及的当下,随着钢水过热度的下降,连铸坯凝固过程中柱状晶生长缓慢,等轴晶比例增大,所以低过热度钢水对改善中心偏析有好处;f、F-EMS的安装位置,这一点比较主要,否则就起不到效果,F-EMS要安装在固-液两相区之间,液态比率大约30%,用射钉法检测液态厚度大约1/3处的位置,(F+M)-EMS,可进一步改善偏析;g、新技术的应用,即中间包热交换水口技术(这个技术我没有接触过),但采用这个技术后,可以适当提高钢水过热度,在确保生产顺行的情况下,而达到进一步稳定结晶器钢水的过热度<10℃,这样可以更进一步改善偏析。
连铸坯质量控制-蔡开科
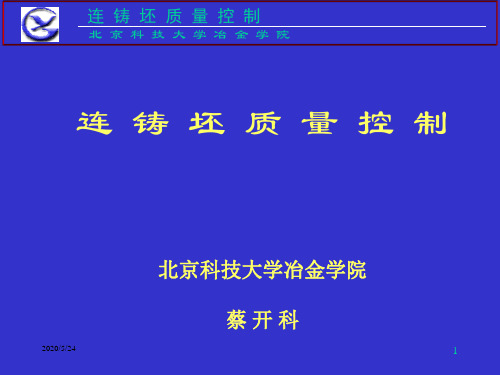
北 京 科 技 大 学 冶 金 学 院
连 铸 坯 质 量 控 制
北京科技大学冶金学院 蔡开科
2019/2/16
1
连 铸 坯 质 量 控 制
北 京 科 技 大 学 冶 金 学 院
目
录
2019/2/16
• 连铸坯质量概念 • 连铸坯洁净度 • 连铸坯裂纹控制 • 连铸坯内部缺陷控制 • 连铸坯形状缺陷控制 • 结论
13
连 铸 坯 质 量 控 制
北 京 科 技 大 学 冶 金 学 院
图2-3(b)金相观察铸坯厚度方向上夹杂物的分布
2019/2/16
14
连 铸 坯 质 量 控 制
北 京 科 技 大 学 冶 金 学 院
2.2.4铸坯表层下Ar气泡+Al2O3夹杂(图2-4)。 • 连铸坯中夹杂物分布,导致轧制产品形成不同缺 陷。
• 转炉吹炼终点: [O] 夹 → 0 , [O] 溶 =600 ~ 900ppm,此时T[O]= [O]溶 • 钢包脱氧合金化: [O] 溶 很低, T[O]=[O]
夹
• 用LECO仪分析的氧为T[O]量,T[O]越高, 说明钢中氧化物夹杂就越多。如AL-K钢, 钢中酸溶铝[Al]s=0.02~0.05%,由AL- O 平衡图可知, [O] 溶 =3 ~ 7ppm. 如连铸坯 中测定T[O]=20ppm,除去[O]溶外,氧化物 夹杂中的氧[O]夹为13~17ppm,说明钢中 5
6
轮胎钢芯线 滚珠 管线 钢轨
2019/2/16
连 铸 坯 质 量 控 制
北 京 科 技 大 学 冶 金 学 院
表 2 产品缺陷与夹杂物关系 钢种 DI 罐用镀锡 板 ERW 管材 镀锡板 深冲深拉用 冷轧钢板 UO 管材 UOE 管 (厚钢板)
炼钢-精炼-连铸钢中夹杂物控制蔡开科

图 3.1 转炉冶炼终点 C-O 关系图 Ⅰ区: [C][O]=0.0027
炉龄<2500 炉 Ⅱ区: [C][O]=0.0031~0.0037
炉龄>2500 炉 处理好溅渣护炉高炉龄与复吹关系,也就是高炉龄与产品质量的矛盾,尤其 是深冲冷轧薄板质量。 (2) 终点温度
9
终点氧含量(ppm)
1800 1600 1400
炼钢-精炼-连铸钢中夹杂物控制
蔡开科 孙彦辉 倪有金 北京科技大学
冶金与生态工程学院 2008 年 9 月
1
目录
1 前言 2 洁净钢概念 3 转炉终点氧活度的控制 4 脱氧和夹杂物的控制 5 浇注过程中的二次氧化产物的控制 6 连铸坯中的夹杂物 7 炼钢生产过程中夹杂物控制对策 8 结语
2
1前 言
T[O]<20ppm 单个 D<13μm 链状 D<200μm
防薄板表面线状缺 陷
防飞边裂纹 防止图象浸蚀
防冷拔断裂 增加疲劳寿命
酸气腐蚀
断裂
5
备注:D 指夹杂物直径
钢中夹杂物对钢质量的影响:
钢的清洁度与产品制造和使用过程中所出现的众多缺陷密切相关,一些厂家 对某些高纯度钢种发生缺陷所作的调查如表 4 所示,可以看出钢中的夹杂物尤其 是大颗粒夹杂物是引起产品缺陷的主要原因。
钢包脱氧合金化后: T[O] = [O]溶+[O]夹 对于 Al-K 钢: [Al]S=0.02-0.05%,[O]溶=4-8ppm(图 4.2),如在连铸坯中测定 T[O]=20ppm, 则说明除[O]溶外,氧化物夹杂[O]夹为 12-18ppm,这说明钢中很干净了。
连铸坯表面裂纹形成及防止(蔡开科)
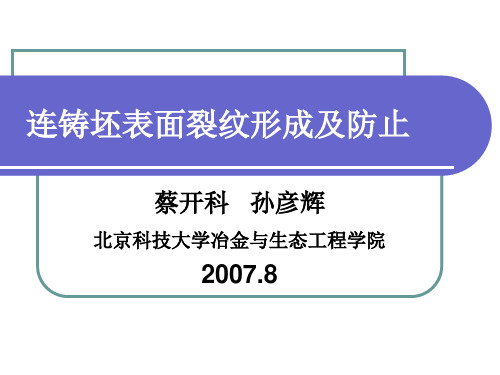
图2-17 结晶器锥度和钢成分对皮下内裂的影响 (断面尺寸240x240mm,拉速0.7m/min)
2 铸坯表面纵裂纹
(7) 结晶器振动
振痕浅,无角部纵裂纹; 振痕深,角部纵裂纹增加; 负滑脱时间值增大,板坯表面纵裂升高;=0.2~0.3s,纵裂降低。 (8) 结晶器钢液流动 水口对中,防止产生偏流;水口材质浸蚀,出口流股不对称,造 成偏流。 水口插入深度合适
图2-8 结晶器液面波动对纵裂纹的影响
图2-9 液面控制方式对纵裂纹的影响
2 铸坯表面纵裂纹
(5) 结晶器热流和冷却
如图2-10所示,90×1000mm 板坯结晶器弯月面以下45mm热流 与纵裂纹指数关系。 ◆低碳钢(0.05%C),结晶器热 流>60Cal/cm2· s(2.1MW/ M2), 纵裂纹增加; ◆中碳钢(0.11%C),结晶器热 流>41Cal/cm2· s(1.7MW/M2),纵裂 纹增加。
3 铸坯(1) 钢成分 C=0.10~0.15%,坯壳厚度不均 匀性强,振痕深,表面易产生凹陷 或横裂纹;生产实践表明,C= 0.15~0.18%或0.15~0.20%时, 振痕浅了,铸坯边部横裂减少; 降低钢中[N],防止氮化物沉淀; (2) 结晶器振动特点 振痕深度增加,横裂纹增加(图 3-4); 振动频率f增加,振痕变浅,横裂纹 减少(图3-5); 负滑脱时间增加,振痕深度增加 (图3-6),方坯tN=0.12~0.15s, 板坯tN=0.20s。
2 铸坯表面纵裂纹
(2) 结晶器钢水流动的合理性
液面波动±3~±5mm
浸入式水口对中,防止偏流 合理的浸入式水口设计(合适的出口直径,倾角) 合适的水口插入深度
(3) 结晶器振动
连铸钢水质量纯净度控制ppm战略(蔡开科)

C
鱼雷罐+喷CaC2
D 铁水罐喷石灰+Mg粉
E
铁水罐CaC2+Mg粉
F 铁水罐喷石灰+Mg粉
G
KR法
H
铁水罐喷镁粉
I
铁水罐喂包芯镁线
脱硫后 [S]/ppm
15 11 15 10.5 10 30 10 20 30
铁水罐 [S]/ppm
22 21 25 10.5 10 30 10 30 30
回硫 ppm
≤900;
70年代
≤800;
80年代
≤600;
90年代
≤100;
2000年后 ≤50。
纯净度是个相对概念,钢中的有害杂质元素降到什么样的 水平决定于钢种和产品的用途。
本文简要评述钢中五大有害元素在炼钢-精炼-连铸过程中 的去除及达到水平。
1. 钢中硫
1.1 钢中硫含量的要求
硫的主要危害:钢中[S]>0.015%时,连铸
碱度一定,渣中(FeO)太高, LP反而下降 ,渣稀会冲刷炉衬。
因此,在BOF渣R=3.0,(FeO)=20%, LP可 达150。
(2)较低的熔池温度
钢中[P]和渣中(MgO)含量的关系
(3)熔池搅拌动力学
在BOF中,LP仅为70~90,在顶底复吹转 炉,增加了熔池搅拌动能,加速了钢水与乳 化渣滴之间脱P反应,故LP比顶吹提高了 35~40%。
对于生产超低硫钢(<30ppm),二次精炼脱硫方法有
出钢渣洗脱硫 钢包渣/金搅拌脱硫 喷石灰粉脱硫 真空室脱硫等 喂钙线脱硫
其[S]含量演变如表所示。
S<30ppm钢水脱硫
工艺 [S]开,ppm [S]终,ppm 脱硫率,% [N]终,ppm
连铸圆坯质量控制

连铸坯质量检验及控制一、连铸坯的内部结构(凝固组织)的一般特征及检验。
连铸坯的检验方法连铸坯的内部结构:经过酸浸(酸洗)或硫印的方法在连铸坯横断面或纵断面上用肉眼或低倍放大镜看到内部组织结果。
硫印硫印是用感光相纸显示试样上硫偏析(合金中各组成元素在结晶时分布不均匀的现象称为偏析)的方法,主要用于钢铁行业铸坯质量的检验。
从铸坯上取纵向或横向试样,试验面加工的光洁度不应低于6。
使用反差大的溴化银表面相纸,把与试样大小相同的相纸放入稀硫酸中浸泡1-2分钟后取出,将相纸对准检查面轻轻覆盖好,将试样与相纸间气泡赶净,待接触2-5分钟后取下,将相纸在流水中冲洗,然后定影烘干,即完成一张硫印。
印基本原理:硫酸与试样上的硫化物(FeS、MnS)发生反应,生成硫化氢气体,硫化氢气体再与感光相纸上的溴化银作用,生成硫化银沉淀在相纸相应的位置上,形成黑色或褐色斑点。
用硫印试验,可显示钢锭、连铸坯中心裂纹、偏析线、低倍结构和夹杂分布等。
酸洗用酸液洗去基体表面锈蚀物和轧皮的过程。
用酸浸或硫印法所显示的组织结构属于宏观结构,是连铸坯和金属材料检验中最为常见的检验技术。
连铸坯的内部结构连铸坯自表面至中心都是由边缘等轴晶区(激冷区)、柱状晶区和中心等轴晶,区三部分组成。
温度梯度较大时,固液两相区(图1)小,有利于柱状晶的生长,而凝固速度较快,则易于生成枝晶间距小的铸造组织,所以连铸坯具有较发达的柱状晶组织,并具有较小的枝晶间距。
(图1)枝晶间距是指相邻同次枝晶间的垂直距离,它是树枝晶组织细化程度的表征。
枝晶间距越小,组织就越细密,分布于其间的元素偏析范围也就越小,故越容易通过热处理而均匀化。
通常采用的有一次枝晶(柱状晶主干)间距d1,和二次分枝间距d2两种。
连铸坯宏观组织的好坏可以用等轴晶所占的比例多少来衡量,轴晶结构致密,加工性能能好。
柱状晶具有明显的方向性,加工性能差,容易导致中心偏析,中心疏松和中心裂纹等缺陷。
二、连铸坯内部凝固结构的控制连铸坯凝固过程的一般特征:从连铸坯的侧面优先凝固,其温度梯度高,凝固速度快,连铸坯内部结晶体成长是不规则的,局部优先生长使内部晶体生长使内部晶体产生“搭桥”等现象,造成因钢水补充不足而出现中心缩孔等缺陷。
BOF-LF-CC生产特殊钢连铸坯的质量控制-蔡开科

0.01%左右。 • 转炉冶炼前期脱磷。 • 终点温度和成分控制较难。
• 日本、韩国的钢厂早就采
用高拉碳法。目前国内不
少厂家也开始由低拉碳走 向高拉碳。如某厂冶炼45 钢生产统计表明终点拉碳 大于0.2%比低拉碳生产成 本降低20.45元/吨钢。冶 炼82B,拉碳[C]=0.4%左 右,吨钢成本节约13元。 终点钢水中a[o]降低(图
渣子来控制夹杂物可塑性。把夹杂物成分控制在相图锰铝 榴石范围内(图8)。当渣碱度为0.9~1.1,钢中酸溶铝 Als<3ppm夹杂物组成为:
•
Al 2 O3
• SiO2 MnO Al2O3 =0.15~0.23
[Mn]
•
[Si] ≥1.7
• 此时可冷拔到0.15~0.23mm,断面收缩率达99.9%,解决
图16 Mn与Si平衡关系
(3)控制Al2O3夹杂形 成
如图17所示,增加[Si]会形成 液态MnO·SiO2夹杂。但对于 高碳Si-K钢,如Si=0.2%则钢 中[Al]s>0.003%,可能有固 态Al2O3析出堵水口。为保持 [Al]s=0.003%水平,则可提 高Si含量以得到液态夹杂。 然而增加[Si]加入SiFe也多, 带入的残余Al也多,成本增 加,也降低了Mn/Si比,促进 了固态SiO2夹杂形成。
6. 连铸工艺优化是控制铸坯中心缺陷的基础
6.1铸坯中心缺陷形貌
• 沿铸坯横向或纵向轴线剖开经硫印或酸浸
后,可显示出低倍结构,沿铸坯纵剖面中心 轴线可发现:
中心疏松
中心缩孔
中心偏析(宏观偏析,它与疏松缩孔伴生)
点状或V形偏析(半宏观偏析)
连铸坯质量的控制

连铸坯的质量控制系统专业:班级:姓名:XXX目录1连铸坯纯净度与产品质量 (1)1.1纯净度与质量的关系 (1)1。
2提高纯净度的措施 (2)2连铸坯质量............................................................ 错误!未定义书签。
2.1 连铸坯的几何形状质量 (3)2。
1.1 铸坯形状缺陷类型 (4)2。
1。
2 铸坯形状缺陷产生原因及防止措施 (4)2.1.3 铸坯鼓肚 (4)2.1.4 铸坯菱变 (4)2。
1。
5 铸坯变成梯形坯 (5)2.2 连铸坯表面质量 (5)2。
2。
1 连铸坯表面振痕 (5)2。
2。
2 振痕形成机理 (5)2。
2.3 振痕对铸坯质量的影响 (6)2。
2。
4 影响振痕深度的因素 (6)2.2.5 减少振痕深度的措施 (7)2。
2.6 铸坯表面裂纹 (7)2。
2。
7 表面纵裂纹 (8)2。
2.8 铸坯角部纵裂纹 (11)2。
2。
9 表面横裂纹 (12)2。
2.10 角部横裂纹 (14)2.2。
11 铸坯表面星状和网状裂纹 (15)2。
2.12 铸坯表面夹渣(杂) (16)2.2。
13 铸坯气孔和气泡 (17)2。
2.14 铸坯表面凹陷 (17)2。
2.15 铸坯表面增碳和偏析 (18)2。
2.16 重皮和重结及结疤 (19)2.3 连铸坯内部质量 (19)2。
3。
1 铸坯内部裂纹 (19)2。
3.2 皮下裂纹 (20)2.3.3 中间裂纹 (20)2.3.4 矫直裂纹 (21)2。
3。
5 压下裂纹 (22)2.3。
6 断面裂纹-——-中心线裂纹 (22)2。
3。
7三角区裂纹 (24)2。
3.8角部附近的裂纹 (25)2.3。
9白点及发纹 (25)2。
3。
10铸坯中心偏析、疏松和缩孔 (25)2.3。
11铸坯内部夹渣(杂) (26)3连铸坯星状缺陷 (27)3.1 鼓肚变形 (27)3。
2 菱形变形 (28)3.3 圆铸坯变形 (28)致谢 (29)摘要连铸坯质量决定着最终产品的质量。
连铸坯质量控制技术

连铸坯质量控制技术引言连铸是一种重要的铸造工艺,用于生产大批量的金属坯料。
连铸坯的质量直接影响到后续工艺的效果和产品的质量。
因此,连铸坯质量控制技术是提高产品质量和降低生产成本的关键。
本文将介绍连铸坯质量控制技术的重要性,并详细探讨了影响连铸坯质量的因素和常用的质量控制方法。
连铸坯质量的重要性连铸坯是下一步金属加工的原料,其质量直接影响到成品的质量。
良好的连铸坯质量可以保证产品的力学性能、表面质量和尺寸精度。
同时,优质的连铸坯还可以减少加工过程中的金属损耗和工时,提高生产效率和经济效益。
此外,连铸坯质量控制也是减少缺陷和事故的重要环节。
通过合理的质量控制措施,可以有效预防坯料的开裂、缺口、气孔等缺陷,避免金属材料的浪费和安全事故的发生。
综上所述,连铸坯质量控制技术对于提高产品质量和生产效率具有重要意义。
影响连铸坯质量的因素连铸坯质量受到多个因素的影响。
以下是一些常见的影响因素:1. 喷水冷却水质量连铸过程中的喷水冷却是保证连铸坯结晶过程良好进行的重要环节。
冷却水的质量对连铸坯表面质量和内部组织均匀性有很大影响。
如果冷却水中含有过多的杂质和氯离子,容易导致坯料表面起泡、气孔等缺陷。
2. 浇注温度和速度浇注温度和速度是影响连铸坯结晶行为的关键参数。
过高的温度和过快的浇注速度会导致坯料表面凝固不均匀,产生质量缺陷。
而过低的温度和过慢的浇注速度则会引起结晶过程延长,出现细晶区、大晶区等组织缺陷。
3. 结晶器结构和材料结晶器是连铸过程中实现坯料结晶的关键部件。
结晶器的结构和材料选择直接影响到连铸坯的结晶行为和组织性能。
不合理的结构设计和材料选择可能导致结晶器磨损、结晶不良等问题。
4. 冷却方式和参数连铸坯的冷却方式和参数选择对坯料的宏观和微观组织均有影响。
合理的冷却方式和参数可以保证连铸坯结晶行为的均匀性和完整性,防止产生缺陷和组织不良现象。
常用的质量控制方法为了确保连铸坯质量的稳定和一致性,可以采用以下几种常用的质量控制方法:1. 自动化控制系统自动化控制系统可以通过实时监测和控制连铸过程的关键参数,如浇注温度、浇注速度和冷却水流量等,来确保连铸坯的质量符合要求。
连铸坯质量控制

连铸坯质量控制连铸坯质量控制1. 引言2. 连铸坯质量特点连铸坯的质量特点主要包括以下几个方面:2.1 凝固结构连铸坯是通过冷却凝固过程形成的,其凝固过程直接影响到坯体的凝固结构。
凝固结构的好坏会对后续的加工以及材料性能产生重要影响。
2.2 化学成分均匀性连铸坯的化学成分均匀性是其质量的重要指标之一。
成分不均匀容易导致后续钢材性能不稳定,从而影响到产品的质量。
2.3 表面缺陷由于连铸坯制造过程中的一些不可避免的因素,气体夹杂、氧化皮等,会在坯体表面形成一些缺陷。
这些表面缺陷会对后续产品的外观质量产生负面影响。
2.4 尺寸偏差连铸坯的尺寸偏差是指坯体的实际尺寸与标准尺寸之间的差异。
尺寸偏差会影响到钢材的加工工艺和成形质量。
3. 连铸坯质量控制因素及措施连铸坯质量的影响因素众多,包括原料质量、连铸工艺参数、设备状况等。
针对这些影响因素,可以采取以下控制措施来提高连铸坯的质量:3.1 原料质量控制通过严格控制原料的化学成分和物理性能,确保连铸坯的化学成分均匀性和机械性能达到要求。
3.2 连铸工艺参数控制连铸工艺参数的合理设置对坯体的凝固结构和表面质量具有决定性影响。
需要通过优化连铸工艺参数,如冷却水流量、浇注速度等,来控制连铸坯的质量。
3.3 设备维护与改进连铸设备的状态对连铸坯质量也有重要影响。
定期进行设备维护和检修,及时处理设备故障,可以保证设备处于良好状态,进而提高连铸坯的质量。
3.4 检测手段与技术利用先进的检测手段和技术,如超声波检测、磁力检测等,可以对连铸坯进行质量检测,及时发现问题并采取相应措施。
4.连铸坯质量控制是钢铁生产中至关重要的环节。
通过对连铸坯质量特点的分析和影响因素的控制,可以采取相应的措施来提高连铸坯的质量。
这不仅对于保证下游产品质量,还对于提高工业生产效益和降低资源消耗具有重要意义。
开展连铸坯质量控制工作是必不可少的。
科技成果——连铸坯质量控制和提升技术

科技成果——连铸坯质量控制和提升技术技术开发单位北京科技大学技术领域钢铁冶金成果简介随着钢铁行业的高速发展,国内外钢铁产量已经达到了饱和状态,提升钢产品的质量成了钢铁行业发展的重要目标。
连铸坯的生产是钢材生产的关键,其连铸坯的质量对后续产品的生产及最终产品质量有重要影响,热轧板带表面缺陷大部分是连铸坯表面缺陷遗传而来。
高质量铸坯的生产成了连铸生产企业和连铸工作者的主要目标。
高温钢液在连铸过程中凝固成型,连铸坯的偏析、裂纹、疏松、夹杂物等质量问题基本上都产生于或源自连铸凝固过程。
要实现高质量铸坯的连铸生产,必须减少甚至消除这些质量缺陷。
(1)连铸坯凝固缺陷研究:针对连铸坯偏析、疏松、缩孔、裂纹开展相关调研,探究凝固缺陷产生机理,分析连铸工艺对连铸坯缺陷的影响规律。
通过调整结晶器一冷强度、二次冷强度、电磁搅拌、机械压下等技术参数,改善连铸坯凝固缺陷。
(2)中间包研究:模拟中间包内钢液流动过程,分析钢液流动的合理性;主要研究中间包内控流装置位置分布、高度设置、不同装置间的配合使用是否达到最优。
具体工作:模拟中间包内钢液流动传热行为,分析钢液温度的变化情况;模拟钢液液面的波动,分析和了解渣-钢界面间的相互作用;模拟中间包内钢水的传质现象,分析钢水在中间包内的停留时间,中间包内的活塞流、全混流以及死区等等。
模拟中间包内底吹气体的作用过程,分析和了解吹气对钢液流动特性的影响。
结晶器凝固钩控制技术结晶器流态模拟仿真(3)结晶器研究:A、结晶器内流场:确定结晶器类型,改变水口类型,水口浸入深度,拉速,结晶器锥度等工艺参数,研究不同工艺参数对结晶器内流场的影响规律,得到液面波动和表面流速量化结果,为工艺参数优化提供科学依据。
B、结晶器卷渣和夹杂物去除的研究:改变水口结构参数(不同水口类型、水口侧孔数、水口倾角、水口底部结构和水口浸入深度等)以及浇铸工艺参数(拉速,浇铸断面,电磁等)会对结晶器内的流场产生影响,进而影响结晶器冷却制度、液面波动、水口开口度等参数。
3-连铸坯中心缺陷的控制-冶金网.
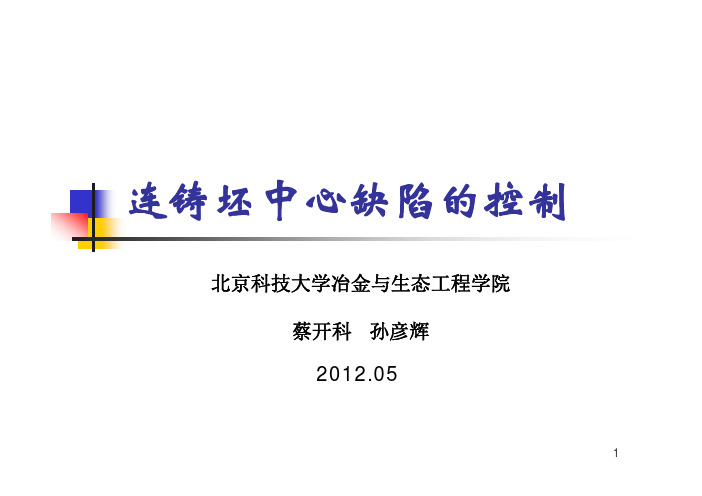
1北京科技大学冶金与生态工程学院蔡开科孙彦辉2012.05连铸坯中心缺陷的控制2目录前言1. 连铸坯中心缺陷概念2. 连铸坯凝固低倍结构3. 铸坯中心缺陷评价4. 连铸坯低倍结构控制5. 连铸工艺优化6. 连铸电磁搅拌技术7. 连铸轻压下技术结语3前言从结晶器拉出来带有液芯的坯壳,在连铸机内边传热、边凝固、边运行而形成很长液相穴的铸坯(少则几米多则十几或二十几米),由于受凝固、传热、传质和工艺的限制,沿液相穴路径常常发生钢水补缩不好,在铸坯完全凝固后,沿铸坯轴向(拉坯方向)某些局部区域常常发现疏松、缩孔和偏析,常称为中心缺陷。
根据钢种和产品用途不同,对连铸坯中心缺陷有严格要求,板坯中心缺陷严重会引起中厚板横向性能尤其是冲击韧性不合格,管线钢抵抗,氢脆(HIC )裂纹能力恶化。
对于中高碳大方坯轧制棒材或线材产品常常会因中心缺陷严重使大方坯低倍检验不合格而导致产品合格率降低。
因此减轻铸坯中心缺陷至不使产品产生废品,这是提高连铸坯内部质量的一个重要任务。
41 连铸坯中心缺陷概念从结晶器拉出来带有液芯的坯壳,在连铸机内边传热、边凝固、边运行而形成很长液相穴的铸坯(少则几米多则十几或二十几米),由于受凝固、传热、传质和工艺的限制,沿液相穴路径常常发生钢水补缩不好,在铸坯完全凝固后,沿铸坯轴向(拉坯方向)某些局部区域常常发现疏松、缩孔和偏析,常称为中心缺陷。
内部缺陷包括:z 中心疏松z 中心缩孔z 中心宏观偏析z V 形偏析(半宏观偏析)5这些缺陷会对轧制产品,尤其是对中厚板性能带来危害:制对铸坯中心硫化物夹杂物延伸使横向性能变坏; 板材冲击韧性下降造成钢材断裂;中心偏析易形成低温转变产物(马氏体和硫化物),造成管线钢氢致裂纹(HIC);高碳钢铸坯中心C、Mn偏析会发生碳化物和马氏体沉淀,引起抗拔脆断;铸坯中心疏松和偏析会引起钢轨呈“S”型断裂; 中心疏松缩孔偏析会使合金钢铸坯低倍检验不合格。
62. 连铸坯凝固低倍结构2.1铸坯低倍结构形成图2-1 铸坯低倍结构连铸坯低倍结构对产品质量有重要影响。
北京科技大学蔡开科讲座资料 连铸坯(圆坯)质量控制
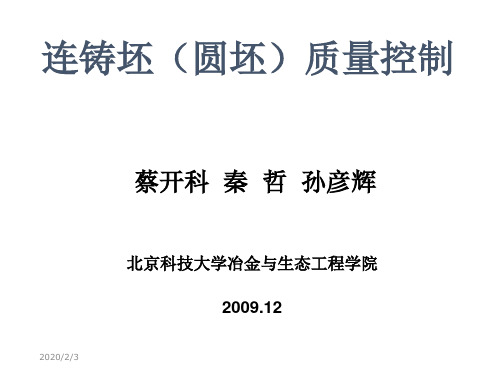
– 二次冷却区:喷水加速铸坯内部热量的传递 ,使其完全凝固
– 三次冷却区:铸坯向空气中辐射传热使铸坯 温度均匀化
2020/2/3
以20钢为例,经过钢水凝固热平衡计算,得出以下 概念:
1) 钢水从结晶器→二冷区→辐射区大约有40%热量放 出来,铸坯才能完全凝固。这部分热量放出的速度决定 连铸机生产率和铸坯质量; 2) 铸坯切割后大约还有60%热量放出来,为了利用这 部分热量,以节约能源,成功开发了:
连铸坯质量概念:
◆ 铸坯洁净度(夹杂物数量、类型、尺寸 、分布)
◆ 铸坯表面质量(表面裂纹、夹渣、气孔 )
◆ 铸坯内部质量(内部裂纹、夹杂物,中 心疏松、缩孔、偏析)
◆ 铸坯形状缺陷(鼓肚、脱方、椭圆)
2020/2/3
从生产流程来看,控制铸坯质量战略原则:
2020/2/3
缺陷的控制策略图
从冶金传输观点,控制铸坯质 量:
2020/2/3
(4)在连铸机内运行的已凝固坯壳的冷 却可看成是经历“形变热处理”过程
带液芯坯壳在连铸机运行过 程中,坯壳承受: – 外力作用(如拉应力、 机械力、鼓肚力…)使 坯壳发生变形 – 坯壳温度变化,发生了 δ→γ→α的反复相变, 相当于“热处理”,影 响铸坯质量 – 奥氏体晶界第二相质点 AlN、Nb(CN)析出
2020/2/3
上述几个方面现象是相互联系和相互制约 的,只有深入认识其规律性,才能在设备 和工艺上制定正确的对策,使连铸机达到 生产效率高和铸坯质量好的目的。
2020/2/3
与方、板坯相比较,圆坯凝固特点是:
(1)圆坯无角部优先凝固。凝固坯壳收缩较均匀,鼓肚少 有发生。
- 1、下载文档前请自行甄别文档内容的完整性,平台不提供额外的编辑、内容补充、找答案等附加服务。
- 2、"仅部分预览"的文档,不可在线预览部分如存在完整性等问题,可反馈申请退款(可完整预览的文档不适用该条件!)。
- 3、如文档侵犯您的权益,请联系客服反馈,我们会尽快为您处理(人工客服工作时间:9:00-18:30)。
(3)防止结晶器卷渣 结晶器液面控制(<±3mm); 结晶器钢水流动的稳定性(SEN设计); 合适的保护渣 (4)提高非稳态浇注的操作水平 加强结晶器液面波动的监控; 加强浇注过程中包钢水重量和中间包恒重浇注的监 控; 加强长水口、SEN保护浇注的效果监控; 坚强管理、提高操作水平。
5) 提高铸坯洁净度措施
钢包自开率
钢包水口开启方式与钢中T[O]关系
钢包自开比烧氧打开钢中T[O]要低10~15ppm 。
长水口操作
无长水口:坯子开浇后 15m长不能做镀Sn板。 长水口:在钢液面开浇, 坯子10m长不能做镀Sn 板。 长水口+破渣器插入钢水 下开浇,坯子长5m即可 做镀Sn板。
总之,在炼钢-精炼-连铸工艺流程生产洁净 钢要控制好四点:
连铸坯(圆坯)质量控制
蔡开科 秦 哲 孙彦辉
北京科技大学冶金与生态工程学院 2009.12
目
录
1.连铸坯质量概念 2.连铸坯(圆坯)凝固特点 3.圆坯洁净度控制 4.圆坯表面纵裂纹控制 5.圆坯内部质量控制 6.圆坯形状缺陷控制 7.结语
1.连铸坯质量概念
连铸坯质量概念:
◆ 铸坯洁净度(夹杂物数量、类型、尺寸、 分布) ◆ 铸坯表面质量(表面裂纹、夹渣、气孔) ◆ 铸坯内部质量(内部裂纹、夹杂物,中心 疏松、缩孔、偏析) ◆ 铸坯形状缺陷(鼓肚、脱方、椭圆)
4
5 6
夹杂物组 组成单一,如Al-K钢,Al2O3, 成 Si-K钢MnO·SiO2
冷却速度 钢中分布 冷却速度越快,生成夹杂物 越细小 细小弥散分布
组成复杂,是多种氧化物复合夹杂物
影响不大 偶然性分布
7
危害程度
较小
较大
2) 铸坯夹杂物来源
采用示踪试验,追踪铸坯中夹杂来源
加示踪剂示意图
3) 结晶器保护渣示踪元素变化
连 铸 坯 凝 固 成 型 过 程
传输行为
热应力应变 应力应变 机械应力应变
•铸坯形状缺陷 聚变 鼓肚
连铸质量控制方 法
传输现象与应力应变行为对铸坯质量的影响
2.连铸坯(圆坯)凝固的基本特点
(1)连铸坯凝固过程实质上是动态热量 传递过程
钢水从液态转变 为固体放出热量:
钢水→固体+Q
放出热量包括:
过热 凝固潜热 物理显热
连铸凝固过程示意图
以20钢为例,钢水凝固冷却到室温放出热量是:
过热 25.2 kJ/kg 潜热 328 kJ/kg 显热 958 kJ/kg 总热量中大约1/3从液体→固体放出,其余 2/3是完全凝固后放出的
钢水在连铸机内凝固是一个热量释放和传递 的过程,铸坯边运行,边放热边凝固,形成 了很长的液相穴(10~20几米),在液相 穴长度上布置了三个冷却区:
从生产流程来看,控制铸坯质量战略原则:
缺陷的控制策略图
从冶金传输观点,控制铸坯质量 :
化学方法 流体流动 溶质分配 凝 固 外加场 热量传递 •铸坯内部缺陷 偏析 铸坯内裂纹 疏松 铸坯的洁净度 夹杂物的上浮 •铸坯表面缺陷 表面纵裂纹 表面横裂纹 表面夹渣 皮下气泡 角部裂纹
晶体周围包围的液体膜 (C=0.4%,S=0.013%)
板坯对角线内裂图
(3)连铸机凝固是分阶段的凝固过程
从结晶器弯月面→凝固终点的很长的液相穴 上,铸坯凝固分为三个阶段:
钢水在结晶器形成初生坯壳 在二冷区接受喷水冷却,使坯壳稳定生长 液相穴末端的凝固坯壳加速生长
由凝固定律求得K值分别是(mm/min1/2): Ⅰ:20,Ⅱ:25,Ⅲ:27~30
说明坯壳收缩形成气隙而热流降低,圆坯 表面形成凹陷,敏感性增加了凹陷处形成 表面纵裂纹,严重时会漏钢。
(3)拉速要高些
圆坯直径等于方坯边长,则圆坯比表面积仅 是方坯的75~80%,在相同的工艺条件下, 拉速可适当提高些。
例如:如Φ330mm的圆坯拉速为0.95m/min, 300×330mm方坯拉速为0.75m/min。
不同开浇方式下沿板坯长度上的质量指数变化
中间包操作
开浇头坯
厂名 铸坯尺寸 /mm 甲 乙 丙 230×1300 70×1350 250×1050 钢种 [N]/ppm 头坯/正常 坯 51.5/21 61/48 63/52 T[O]/ppm 头坯/正常 坯 66.8/26.2 70/34 MA/mg·(10kg )-1 头坯/正常坯 5.0/1.7 32/3.80 23/1.07 MI 头坯/正常坯 173.8/24.6(p pm) 12.9/8.2(个 /mm2) -
由图可知:
ZST-ZDT是裂纹
敏感温度区,
是铸坯产生内 裂纹的根源。
内部裂纹形成机理模式图
带液芯的铸坯,以一个固定速度在连铸机内沿弧形轨道运动。
沿液相穴固/液界面把热量放出传给外界。可看成是在凝固 温度区间(TL-Ts)把液体转变为固体加工过程。然而在固
液界面的临界高温强度为1~3 N/mm2,临界塑性应变为
上述几个方面现象是相互联系和相互制约的,
只有深入认识其规律性,才能在设备和工艺
上制定正确的对策,使连铸机达到生产效率
高和铸坯质量好的目的。
与方、板坯相比较,圆坯凝固特点是:
(1)圆坯无角部优先凝固。凝固坯壳收缩较均匀,鼓肚少 有发生。 (2)圆坯传热面积比方坯要小些。直径同方坯边长相等的 圆坯其表面积比方坯小25%,其结晶器热流强度要大些。
方坯:结晶器热流40~50cal/cm2·s(1.67~2.08MW/m2) 圆坯:结晶器热流50~60cal/cm2·s (2.08~2.5MW/m2) 同样条件下,圆坯热流比方坯高20~25%
Φ178mm圆坯结晶器热流分布
由热流分布图可知: 弯月面下50mm热流很低 弯月面下70~110mm热流升高达到 2~4MW/m2 弯月面下>110mm后热流突然降低,平 均为1.5MW/m2
0.2~0.4%。当凝固坯在铸机运行过程中,受到外部应力作用 (如热应力、鼓肚力、弯曲力、矫直力„)超过了上述的临 界值,在铸坯固/液界面就产生裂纹,直到凝固壳能抵抗外力 为止。
在固液界面由于溶质元素富集(S、P),在树枝间 周围包裹硫化物薄膜,增加了晶界脆性,受外力作 用沿晶界断裂一直到能抵抗塑性变形为止。
铸坯热装热送工艺:铸坯入加热炉温度越高,则节能越 多。铸坯500℃热装入炉节能0.25×106 kJ/t, 800℃热装,节能为0.514×106 kJ/t; 直接轧制工艺:直接轧制比铸坯冷装加热轧制节能 80~85%,大大缩短生产周期。如薄板坯连铸连轧工 艺(CSP 、FTSC)
(2)连铸坯凝固是沿液相穴在凝固温度 内把液体转变为固体的加工过程
IF SPHD 硅钢
丁
150×150
45#
87.7/64.3
46.9/32.8
25/10
16.7/8.2(个 /mm2)
注:MA大型夹杂物;MI微观夹杂物;正常坯是拉速稳定时的铸坯取样。
连浇坯
厂名 铸坯尺寸 /mm 230×1300 70×1350 250×1050 150×150 钢种 [N]/ppm 连浇坯/正常 坯 23/21 59/52 72.9/64.3 T[O]/ppm 连浇坯/正常坯 23/18 53/34 46.8/32.7 MA/mg·(10kg) -1 连浇坯/正常坯 2.29/1.70 6.4/3.8 4.8/1.07 15/10 MI/个.mm-2 连浇坯/正常坯 46.2/24.6(ppm) 8.2/10.7(个 /mm2) 8.5/8.2(个/mm2)
(a)
结晶器保护渣中CeO和SrO变化
(b)
渣中Ce2O、SrO升高,说明钢包渣中包渣下降结晶器渣中。
4) 铸坯中夹杂物
从铸坯中探针分析100个夹杂物,夹杂物含有示踪 元素 Ce2O:0.14%,SrO:0.156%,ZrO2: 0.25%,La2O3:0.41%,Na2O+K2O:1.64%。 粗略计算指出铸坯中夹杂物各自贡献: 外来夹杂物(下渣+卷渣): 41% 二次氧化: 39% 脱氧产物: 20% 防止浇注过程下渣、卷渣和二次氧化物是生产洁净钢的 关键操作。
一次冷却区:钢水在结晶器中形成足够厚的均 匀坯壳,以保证铸坯出结晶器不拉漏 二次冷却区:喷水加速铸坯内部热量的传递, 使其完全凝固 三次冷却区:铸坯向空气中辐射传热使铸坯温 度均匀化
以20钢为例,经过钢水凝固热平衡计算,得出以下 概念:
1) 钢水从结晶器→二冷区→辐射区大约有40%热量 放出来,铸坯才能完全凝固。这部分热量放出的速度 决定连铸机生产率和铸坯质量; 2) 铸坯切割后大约还有60%热量放出来,为了利用 这部分热量,以节约能源,成功开发了:
甲 乙 丙 丁
IF SPHD 硅钢 45#
由以上三个表可以看出:头坯、连浇坯、尾 坯中的T[O]、[N]、大型夹杂、微观夹杂 都明显高于正常坯。因此,提高非稳态浇注 时铸坯的洁净度水平达到稳态浇注水平,对 于提高整体铸坯质量的水平,保持产品质量 的稳定性是非常重要的。
浇注过程把非稳态浇注铸坯质量提高到稳态浇注水平这是提高铸 坯体质量水平的关键,为此: (1)防止二次氧化 保护浇注(∆[N]<3ppm); 碱性包衬; 碱性覆盖剂; 中间包密封充Ar。 (2)防止浇注过程下渣 出钢挡渣操作; 钢包→中间包下渣(如AMEPA系统下渣探测器); 中间包→结晶器下渣如中间包恒重操作、中间包液位高度监测 报警、人工测量中包液面高度等; 提高钢包自开率和钢包长水口操作水平。
圆坯直径与拉速关系图
(4)圆坯结晶器流场。直筒水口流股热中心 下移,对保护渣熔化、液渣层厚度及夹杂物 上浮等有不利影响。 (5)二冷区冷却均匀性更为重要
圆周尽可能均匀冷却,促进坯壳均匀生长; 最小的圆周表面温度回升和热循环,消除热应 力; 矫直时圆坯温度应大于950℃(钢种); 非稳定浇注时,保持合适的冷却速度。