生产线平衡(lql)
生产线平衡

生产线平衡生产线平衡是一种优化生产过程的方法,旨在确保各个工序之间的负荷均衡,避免因为某个工序的效率低而导致整个生产线的效率下降。
在制造业中,生产线平衡是提高生产效率和降低生产成本的关键因素之一。
本文将介绍生产线平衡的概念、方法和优势。
概念生产线平衡是指在给定的生产能力和工期要求下,通过调整工序所需的时间和资源,使得各个工序的负荷相对均衡,从而达到提高生产效率和降低生产成本的目的。
生产线平衡需要考虑工序之间的依赖关系、工序的能力和资源限制以及生产线的整体目标。
方法1. 流程图分析首先,可以通过绘制流程图来分析和优化生产线的流程。
流程图可以清晰地展现每个工序的顺序和依赖关系,帮助我们找出潜在的瓶颈和不平衡的地方。
通过观察流程图,可以确定哪些工序需要调整以实现平衡。
2. 工序时间研究确定了需要调整的工序后,可以进行工序时间研究。
工序时间研究的目的是测量每个工序所需的时间和资源,并分析造成时间差异的原因。
通过工序时间研究,可以找出效率低下的工序,并制定相应的改进措施。
3. 任务调度优化任务调度是生产线平衡的关键环节。
在任务调度时,需要合理安排工人和设备的使用,以保证各个工序之间的负荷均衡。
可以使用任务调度算法来优化工序的排程顺序,减少等待时间和负荷不平衡。
优势生产线平衡可以带来多方面的优势,包括:1. 提高生产效率通过平衡各个工序的负荷,可以避免某个工序因为资源不足或效率低下而拖慢整个生产线的节奏。
平衡后的生产线可以更好地利用资源,提高生产效率,缩短生产周期。
2. 降低生产成本生产线平衡可以减少资源的浪费和时间的损失。
通过减少等待时间和调整工序顺序,可以降低生产成本,提高资金利用率。
3. 提高产品质量在平衡的生产线上,各个工序之间的负荷均衡,不会因为某个工序效率低下而导致产品质量下降。
平衡的生产线可以提供更加稳定和可靠的生产环境,有利于提高产品的质量。
4. 增加生产线的灵活性生产线平衡可以适应不同的生产需求和市场变化。
生产线平衡(line balance)
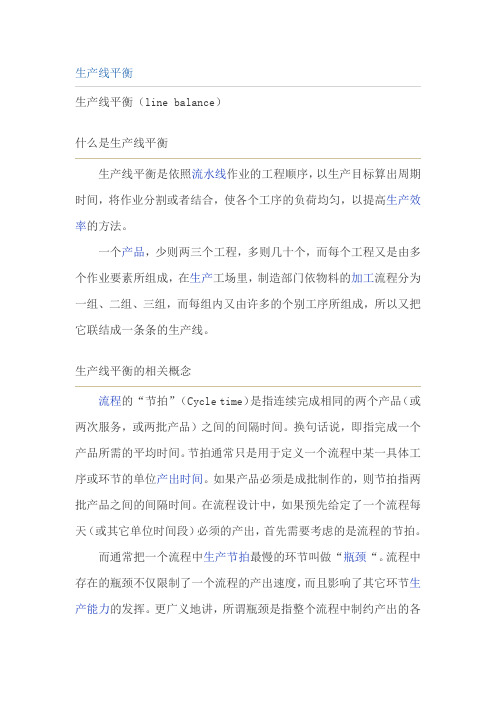
生产线平衡(line balance)什么是生产线平衡生产线平衡是依照流水线作业的工程顺序,以生产目标算出周期时间,将作业分割或者结合,使各个工序的负荷均匀,以提高生产效率的方法。
一个产品,少则两三个工程,多则几十个,而每个工程又是由多个作业要素所组成,在生产工场里,制造部门依物料的加工流程分为一组、二组、三组,而每组内又由许多的个别工序所组成,所以又把它联结成一条条的生产线。
生产线平衡的相关概念流程的“节拍”(Cycle time)是指连续完成相同的两个产品(或两次服务,或两批产品)之间的间隔时间。
换句话说,即指完成一个产品所需的平均时间。
节拍通常只是用于定义一个流程中某一具体工序或环节的单位产出时间。
如果产品必须是成批制作的,则节拍指两批产品之间的间隔时间。
在流程设计中,如果预先给定了一个流程每天(或其它单位时间段)必须的产出,首先需要考虑的是流程的节拍。
而通常把一个流程中生产节拍最慢的环节叫做“瓶颈“。
流程中存在的瓶颈不仅限制了一个流程的产出速度,而且影响了其它环节生产能力的发挥。
更广义地讲,所谓瓶颈是指整个流程中制约产出的各种因素。
例如,在有些情况下,可能利用的人力不足、原材料不能及时到位、某环节设备发生故障、信息流阻滞等,都有可能成为瓶颈。
正如“瓶颈”的字面含义,一个瓶子瓶口大小决定着液体从中流出的速度,生产运作流程中的瓶颈则制约着整个流程的产出速度。
瓶颈还有可能“漂移”,取决于在特定时间段内生产的产品或使用的人力和设备。
因此在流程设计中和日后的日常生产运作中都需要引起足够的重视。
与节拍和瓶颈相关联的另一个概念是流程中的“空闲时间”空闲时间是指工作时间内没有执行有效工作任务的那段时间,可以指设备或人的时间。
当一个流程中各个工序的节拍不一致时,瓶颈工序以外的其它工序就会产生空闲时间。
这就需要对生产工艺进行平衡。
制造业的生产线多半是在进行了细分之后的多工序流水化连续作业生产线,此时由于分工作业,简化了作业难度,使作业熟练度容易提高,从而提高了作业效率。
工厂生产线平衡与瓶颈分析

工厂生产线平衡与瓶颈分析工厂生产线平衡与瓶颈分析是提高生产效率和生产线运作的关键方法,它可以帮助工厂实现更高的产量和更好的产品质量。
本文将介绍生产线平衡的概念、目的和方法,以及如何进行瓶颈分析来识别和解决生产线的瓶颈问题。
一、生产线平衡的概念及目的生产线平衡是指在一定的生产时间内,合理分配各个工序的任务,使得各个工序的生产频率和产量能够达到相对均衡的状态。
其目的是确保整个生产线各个工序的生产速度相匹配,避免因某个工序产能过剩或不足而导致整个生产线效率的低下。
二、生产线平衡的方法1.对各个工序进行评估首先,需要对生产线上的每个工序进行评估,了解其生产能力、生产周期和需求量等。
这可以通过观察和记录生产数据来完成。
评估结果可以帮助我们了解每个工序的重要性和效率状况。
2.分析生产线的瓶颈接下来,需要进行生产线的瓶颈分析。
瓶颈是指限制生产线流量和效率的关键环节,其产能决定了整个生产线的产量。
通过对生产线的观察和数据分析,可以找出生产线上的瓶颈并加以解决。
3.制定平衡计划在了解各个工序的生产能力和生产周期后,可以制定一个平衡计划,确保各个工序的生产速度相匹配。
这可以通过提高瓶颈工序的生产能力,或者通过调整其他工序的生产速度来实现。
4.持续监控和调整平衡计划的实施并不是一次性的,而是需要持续监控和调整的过程。
通过定期检查生产数据和进行生产线观察,可以及时发现问题并采取相应的措施来调整生产线的平衡状态。
三、瓶颈分析的概念及方法瓶颈分析是一种通过识别生产线上的瓶颈来优化生产流程的方法。
其目的是找出生产线上的弱点和限制性因素,以便采取相应措施来提高整个生产线的效率。
1.流程图分析通过绘制生产线的流程图,可以清晰地了解每个工序的顺序和关联性。
在绘制流程图的过程中,可以找出可能存在的瓶颈和生产线上的延误点。
2.时间观察和测量对每个工序的生产时间进行观察和测量,可以帮助我们了解每个工序的生产效率和产能。
通过比较不同工序的生产时间,可以找出生产线上的瓶颈所在。
生产线平衡

生产线平衡生产线平衡生产线平衡是指在生产过程中,通过合理地安排和调配各种生产资源,使得生产过程中的各个环节能够协调配合,达到最佳的生产效果,减少浪费和提高质量。
生产线平衡不仅可以实现生产资源的合理利用,还可以降低生产成本,提高生产效率和质量,从而为企业的发展创造更大的利润空间。
生产线平衡的主要目标是在最短的时间内生产出最大数量的产品,并保证产品质量稳定。
实现这个目标需要根据市场需求制定合适的生产计划,合理分配生产资源,设定生产节拍和工作标准,监测生产过程中的瓶颈和问题,并及时采取措施加以解决。
生产线平衡的实现过程可以分为以下几个步骤:1. 生产计划制定:根据市场需求和企业的生产能力,制定合理的生产计划,明确生产任务和时间节点。
2. 生产资源分配:根据生产计划和生产能力,合理分配所需的生产资源,包括人员、设备、原材料等。
3. 工作标准设定:根据产品的生产要求和企业的生产能力,设定合适的工作标准和生产节拍,确保生产过程中各个环节的协调配合。
4. 生产监控:对生产过程中的各个环节进行监控,及时发现问题和瓶颈,并采取相应的措施进行调整和优化。
5. 优化改进:通过对生产数据的分析和总结,不断优化生产过程和工作标准,减少浪费和提高生产效率和质量。
生产线平衡的重要性:1. 提高生产效率和质量:通过合理利用生产资源和设定工作标准,可以提高生产效率和产品质量,减少生产中的浪费和失误。
2. 降低生产成本:生产线平衡可以减少生产中的浪费和废品,优化生产过程,从而降低生产成本。
3. 提高客户满意度:通过生产线平衡,企业能够按时交付满足客户需求的产品,提高客户满意度和忠诚度,为企业的长期发展打下坚实的基础。
4. 优化人力资源管理:生产线平衡需要遵循一定的生产流程和工作标准,可以优化人力资源的管理和培训,构建有效的生产团队。
5. 改善企业形象:通过生产线平衡,企业可以提高产品质量和生产效率,为客户提供更好的产品和服务,改善企业形象和口碑。
生产线平衡 (2)

生产线平衡
生产线平衡是指在制造过程中,通过合理地分配和安排工
作任务,使得生产线上的工位之间的负荷均衡,从而提高
生产效率和产品质量。
生产线平衡的目标是使得每个工位上的工作时间和工作量
相对均衡,并且生产线的生产节奏能够与市场需求保持一致。
平衡的生产线能够避免工位之间的等待和闲置时间,
减少生产过程中的浪费。
要实现生产线平衡,需要对生产过程进行详细的工作分析,确定每个工位上的工作内容、时间和数量,并结合工人的
技能和经验,合理地分配工作任务。
同时,还需要考虑各
种因素的影响,如不同工序之间的依赖关系、设备的容量
和效率以及工人的疲劳程度等。
生产线平衡可以通过多种方法来实现,包括重新安排工作
顺序、调整工作时间和数量、调整工位布局、提高设备效
率、培训工人等。
同时,可以利用生产线平衡的原理来优
化生产计划和调度,以便更好地满足市场需求和提高生产
效益。
生产线平衡是现代生产管理的重要内容之一,能够有效地
提高生产效率、降低生产成本,提高产品质量和交付能力,进而增强企业的竞争力。
生产线平衡指标

生产线平衡指标生产线平衡指标是指衡量生产线运行效率和生产能力充分利用程度的指标。
它可以帮助企业评估和改进生产流程,提高生产效率,降低成本,增加盈利。
本文将介绍生产线平衡指标的定义、重要性以及常用的衡量方法。
一、生产线平衡指标的定义生产线平衡指标是用来度量生产线各工位之间的工作负载平衡度的指标。
在一个完全平衡的生产线上,每个工位的生产能力、工作量和任务分配是相对均衡的。
而实际生产线上,由于各种因素的影响,工位之间的平衡度往往存在差异。
二、生产线平衡指标的重要性1. 提高生产效率:通过平衡生产线,可以减少生产线上的闲置时间和拥堵情况,提高生产效率。
由于工位之间的平衡度均衡,产品在各个工位之间的流动更加顺畅,从而减少了生产过程中的等待时间和停滞时间,有效提高了生产速度和生产数量。
2. 降低生产成本:平衡生产线可以减少工人和设备的浪费。
在不平衡的生产线上,一些工位的工作负荷可能过重,而其他工位则相对较轻。
这不仅会造成一些工人过度劳累,还会导致其他工人的闲置。
通过平衡生产线,可以合理分配工作负荷,降低员工的加班情况,减少设备的闲置和维护成本。
3. 提高交货能力:生产线平衡可以使产品的生产和交付更加可靠和及时。
通过减少生产线上的不均衡情况,可以避免某些工位由于过载而无法按时完成任务,从而确保产品的按时交付。
三、衡量生产线平衡指标的方法1. Takt时间:Takt时间是指在给定生产需求下,生产一个产品所需的时间。
通过计算Takt时间,可以评估生产线的平衡度。
如果各个工位的工作时间之和等于Takt时间,那么说明生产线是平衡的。
2. 各工位工作负载比例:通过检查各个工位的工作负荷比例,可以判断生产线的平衡情况。
工作负荷比例可以通过计算某个工位的工作时间与Takt时间的比值来得出,工作时间与Takt时间的比值越接近1,说明该工位的工作负荷越合理和平衡。
3. 工位之间的任务可视化:将生产线的任务和工作过程可视化,可以直观地看到工位之间的平衡情况。
生产线平衡

生产线平衡什么是生产线平衡?生产线平衡是指在制造业中,通过合理安排工作站的工作内容和工作时间,使得各个工作站之间的工作负荷达到一致,从而实现整个生产线的高效运行和提高生产效率。
生产线平衡可以有效地减少生产过程中的浪费,并降低生产成本。
生产线平衡的优势1.提高生产效率:通过合理安排工作站的工作负荷,避免因工作站负荷过大或过小而导致的生产效率低下的情况发生,从而提高生产效率。
2.减少生产过程中的浪费:生产线平衡可以避免一些工作站因工作内容过多而产生等待时间,以及其他工作站因工作内容过少而导致的工作站闲置的情况。
这样可以最大程度地减少生产过程中的浪费,提高资源利用率。
3.增强生产线的灵活性:通过生产线平衡,可以使得生产线上各个工作站之间的工作负荷相对均衡,从而增强生产线的灵活性和应对能力。
当需要进行产品类型或生产数量的调整时,可以比较容易地实现,而不需要对整个生产线进行大幅度的调整。
4.提高产品质量:生产线平衡可以减少生产过程中的等待时间和工作站的闲置时间,从而减少了生产线上人为因素对产品质量的影响。
工人在有充足时间完成任务的情况下,可以更加专注和仔细地完成工作,提高产品质量。
实施生产线平衡的步骤1.确定生产线的结构:首先需要明确生产线中包含哪些工作站,以及它们之间的工作关系。
这有助于确定工作站之间的工作负荷平衡目标。
2.测量工作站的工作时间:对于每个工作站,需要测量其完成工作所需的具体时间。
这有助于了解每个工作站的工作负荷情况,为后续的平衡安排提供依据。
3.分配工作到每个工作站:根据上一步测量得到的工作时间,合理地分配工作到每个工作站。
将工作任务合理分配,并确保每个工作站的工作负荷均衡。
4.调整工作站的工作时间:如果发现某些工作站的工作负荷过重或过轻,可以适当调整工作站的工作时间,使得工作负荷达到平衡。
5.定期评估和调整:生产线平衡并非一次性的过程,而是需要定期评估和调整。
随着生产线上产品类型和数量的变化,需要及时地对生产线进行评估和调整,以保持生产线的平衡状态。
生产线平衡概述

生产线平衡概述1. 简介生产线平衡是指在生产过程中,合理分配工作环节的工作量,以实现各个工作环节的协同配合,提高生产效率和产品质量。
生产线平衡的目标是最大限度地优化生产线的运作,避免工作环节之间的阻塞和浪费,提高整体生产效率。
2. 生产线平衡的优势生产线平衡可以带来许多优势,包括: - 提高生产效率:生产线平衡能够避免工作环节之间的堵塞和浪费,使得生产线的运作更加顺畅,从而提高生产效率。
-降低生产成本:通过合理分配工作环节的工作量,能够避免某些环节过度工作,减少生产成本,提高经济效益。
- 提高产品质量:生产线平衡可以确保每个工作环节都能够得到适当的时间和资源,从而提高产品质量,减少次品率。
- 加强员工协作:生产线平衡需要各个工作环节之间的协作和配合,能够增强员工的团队意识和协作能力。
3. 实现生产线平衡的方法要实现生产线平衡,可以采取以下方法: - 流程分析:对生产线上的每个工作环节进行详细分析,确定每个环节所需的时间和资源,找出潜在的瓶颈和浪费,以便进行优化。
- 工作流程设计:根据流程分析的结果,重新设计工作流程,合理分配工作环节的工作量和时间,确保各个环节之间的协调与顺畅。
- 人员培训:对参与生产线的员工进行培训,使他们了解整个生产线的运作和各个工作环节的重要性,提高工作效率和协作能力。
- 设备优化:通过升级和改善设备,提高其性能和稳定性,减少设备故障和停机时间,确保生产线的持续运转。
4. 生产线平衡的实施步骤以下是实施生产线平衡的基本步骤: 1. 确定目标:明确生产线平衡的目标和期望效果,例如提高生产效率、降低生产成本等。
2. 流程分析:对生产线进行详细的流程分析,找出每个环节的工作量、时间和资源需求。
3. 工作流程设计:根据流程分析结果,重新设计工作流程,确定每个环节的工作内容和时间安排。
4. 人员培训:对参与生产线的员工进行培训,让他们了解新的工作流程和各个环节的工作内容。
生产线平衡标准

生产线平衡标准一、引言生产线平衡是指在生产过程中,合理安排生产线上各工序之间的任务分配和工作时间,以确保各个工序能够协调配合,达到最佳的生产效率和质量。
生产线平衡标准是指在实际生产中,对生产线平衡的要求和标准进行规范和约定,以便于实施和监管。
本文将围绕生产线平衡标准展开详细阐述。
二、生产线平衡原则1. 均衡性原则:生产线上各工序的任务分配和工作时间应该尽量均衡,避免出现某个工序负荷过重或者空闲时间过长的情况。
2. 流程连贯性原则:生产线上各个工序之间的任务分配应该保持流程的连贯性,确保生产过程的顺畅进行。
3. 适应性原则:生产线平衡应该根据实际生产情况进行调整,适应订单量、设备状态等因素的变化。
4. 灵活性原则:生产线平衡标准应该具有一定的灵活性,能够根据不同产品、不同工艺进行调整,以满足多样化的生产需求。
三、生产线平衡标准内容1. 任务分配标准:明确规定每个工序应承担的任务量、工作内容和工作顺序,确保任务分配合理。
2. 工作时间标准:确定每个工序的标准工作时间,并根据实际情况进行调整,确保生产线各工序的工作时间相对均衡。
3. 生产能力标准:对每个工序的生产能力进行评估和统计,确保各工序的生产能力与任务量相匹配。
4. 设备利用标准:规定设备的利用率和维护周期,确保设备在生产过程中的稳定运行。
5. 人员配备标准:确定每个工序所需的人员数量和技能水平,确保生产线上有足够的人力资源支持。
四、生产线平衡标准实施1. 制定标准化操作流程:根据生产线平衡标准,制定标准化的操作流程和作业指导书,确保每个工序按照标准进行操作。
2. 培训和考核人员:对生产线上的操作人员进行培训,使其熟练掌握标准化操作流程,并建立绩效考核机制,激励员工按照标准进行操作。
3. 实施监控与调整:通过生产数据的监控和分析,及时发现生产线平衡不足的问题,并进行调整和改进,以保持生产线平衡状态。
五、生产线平衡标准的意义1. 提高生产效率:通过生产线平衡标准,可以避免生产过程中的浪费和闲置,提高生产效率,降低成本。
生产流程生产线平衡
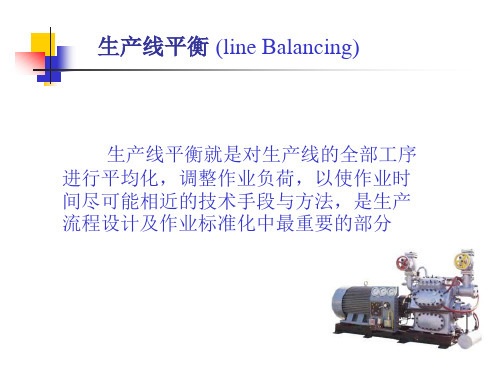
私事宽放率4% 疲劳宽放率8%
作业测定——模特法
生产线平衡措施
ECRS改善法
• 消除(Elimination):什么作业可以不做? • 合并(Combination):那些作业可以合并? • 重排(Rearrange):调整作业的順序是否会更有效率? • 简化(Simplification):是否能简化每一個作业,
生产线平衡意义:
保证生产连续性和均衡性
保证设备、人力的负荷平衡,从而能提高设备、工时 利用率,提高生产效率。
减少在制品,节约物资消耗,加速流动资金的周转, 从而降低生产成本;
生产线平衡概念
节拍(Cycle Time)
CT - 生产节拍 TW - 计划期内有效总工作时间 Q - 计划期内制品数量
生产线平衡概念
装配生产线平衡设计
3)按阶位由大到小排列,并表明各作业要素紧前作业要素
4)作业要素分配
生产线平衡措施
工序的分解和合并是工序同期化常用的方法。 受到机器限制,工序不能分解和合并时
.提高设备的生产效率 .改进工艺和操作方法
………
工作研究(work study)
程序分析 操作分析 动作分析 工作测定
位置约束
产品装配作业受到空间的限制。在大型的生产线上,如 汽车的装配线上,由于产品比作业人员可完成的装配作业 空间大,不能完成其周边的装配作业。
生产线平衡评价指标
生产线平衡率
平滑性系数(Smoothness Index)
生产线平衡概念
生产线平衡的一般数学表达:
给定一个无回路的有向图G=(E,P),节点E表示作 业要素集合,弧P表示生产作业元素之间的先后关系集合。 一个节点j∈E有一个值Tj(j=l,2,…,n)表示作业时间。 生产线平衡问题就是求节点集E的一个划分:
生产线平衡计算

生产线平衡 - 1
定义
生产线平衡(工序同期化):通过技术 组织措施来调整生产线的工序时间定额, 使工作地的单件作业时间等于生产线节 拍,或者与节拍成整数倍关系。
生产线的产出速度等于作业速度最慢的工作地 的产出速度, 因此希望每一工作地的工作任务 大致都相等,减少或消除忙闲不均的现象,这 就是生产线的平衡问题(又称工序同期化)。
目标量:按日或小时要求产 出数量!
生产线平衡 - 4
生产线平衡率
平衡率是衡量工序中各工站节拍符合度的一个 综合比值﹔ 总工序工时总和 平衡率= ----------------------×100% 瓶颈时间×工站数
平衡率的目标:与大设备相连≧85% 其它≧ 95%
生产线平衡 - 5
平衡率100%的意义
产能要求1: 目标每小时要装配3000台风扇。节拍时间应是多少?
生产节拍1:T/T = 3600/3000=1.2 s
产能要求2: 目标每小时要装配1500台风扇。节拍时间应是多少?
生产节拍1:T/T = 3600/3000=2.4 s
产能要求3: 目标每小时要装配1000台风扇。节拍时间应是多少?
工序 A B C D E F G H
C/T(S) 2 1
3.25 1.2 0.5 1 1 2.4
作业描述 装配外框 安装开关 装配马达架 将马达架装入外框 安装扇叶 安装格栅 安装电缆 测试
生产线平衡 - 10
先行工序 无
A 无 A, C D E B F, G
1、确定生产节拍T/T (Tact time)
生产节拍1:T/T = 3600/1000=3.6 s
生产线平衡 - 11
精益生产--生产线平衡

精益生产–生产线平衡简介在现代制造业中,精益生产是一种以减少浪费、提高生产效率为目标的管理理念和工作方法。
而生产线平衡作为精益生产的一个重要概念之一,旨在实现生产线上各工作站的产能平衡,最大限度地提高整个生产线的生产效率。
本文将介绍精益生产中的生产线平衡的基本原理,具体的平衡方法以及实施生产线平衡的好处。
基本原理生产线平衡的基本原理是确保生产线上的每个工作站的产能相等,以避免出现生产线上出现工作站之间的“瓶颈效应”,从而提高整个生产线的产能和效率。
在实践中,生产线平衡需要综合考虑多个因素,包括生产任务的数量和工序的流程等,以使整个生产线的产能得到充分利用,并保持稳定的生产节奏。
平衡方法实施生产线平衡需要采取一系列的方法和工具来分析和优化生产线上各工作站的布局和工作流程。
以下是一些常用的平衡方法:1. 产能分析首先需要对生产线上的每个工作站进行产能分析,明确每个工作站的工作量和产能。
产能分析可以通过测量工作站的工作时间、周期时间以及工作站的生产速率来实现,从而了解每个工作站的生产能力和瓶颈。
2. 操作分析通过对工作站的操作进行分析,确定每个工作站的生产时间,并找出可以优化的操作。
操作分析可以帮助确定每个工作站的最佳工作方式,并减少不必要的浪费,提高生产效率。
3. 任务平衡根据产能分析和操作分析的结果,对生产线上的任务进行平衡,确保每个工作站的任务量相等。
任务平衡可以通过重新安排任务的顺序和数量来实现,以确保工作站之间的产能得到均衡利用。
4. 布局优化根据生产线的设计和布局,在实施生产线平衡时,还可以考虑对工作站的布局进行优化。
布局优化可以使得生产线上的物料流动更加顺畅,减少物料运输时间,提高生产效率。
好处实施生产线平衡可以带来多个方面的好处,包括但不限于以下几点:•提高生产线的产能和效率:通过平衡生产线上的工作站,充分利用每个工作站的产能,提高整个生产线的产能和效率。
•减少浪费:通过优化工作流程和减少不必要的操作,减少生产过程中的浪费,提高资源利用效率。
生产线平衡培训讲义

生产线平衡培训讲义1. 简介本讲义旨在为员工们提供关于生产线平衡的基础知识和技能,帮助大家理解和应用生产线平衡的原理和方法,提高生产效率和品质。
2. 生产线平衡的定义生产线平衡是指在给定的生产资源限制下,通过合理安排工序和工位之间的关系,使生产线上的工作负载均衡,以达到生产效率和品质的最优化。
3. 生产线平衡的重要性生产线平衡是一个关键的生产管理概念,它可以带来以下几个重要好处:•提高生产效率:生产线平衡可以避免工序之间出现短缺或过剩的情况,确保所有工位都能充分利用并平衡负载,从而提高整体生产效率。
•提高生产品质:生产线平衡能够减少工序之间的等待时间和传递时间,降低产品质量问题的发生率,提高生产品质。
•减少工人疲劳度:通过合理平衡工序和工位的负载,避免工人在某些工位上过度集中工作,减少工人疲劳度,增强工作效率和质量。
•降低生产成本:生产线平衡可以避免资源浪费和不必要的生产线停机和重组,从而降低生产成本。
4. 生产线平衡的步骤4.1 收集数据在进行生产线平衡之前,需要首先收集相关数据,包括生产线上每个工序的标准工时、工人数量、设备效率等信息。
4.2 分析数据通过对收集到的数据进行分析,可以得出生产线各工序之间的平均工时、工作负荷等信息,为后续的平衡工作提供依据。
4.3 设计生产线布局根据分析结果,设计合理的生产线布局,使得每个工位的负荷尽量平衡,并考虑到工序之间的依赖关系,确保整体生产线的顺畅运作。
4.4 平衡工序间时间根据设计的生产线布局,对每个工序的时间进行调整,使得工序之间的时间尽量平衡,避免出现等待或拥堵情况。
4.5 平衡人力资源根据工序的时间和工作量,平衡人力资源分配,确保每个工位都有足够的人力投入,避免某些工位过度工作或闲置。
4.6 进一步优化根据实际运行情况,不断收集反馈数据,进一步优化生产线平衡,以达到最佳的生产效果。
5. 生产线平衡的关键要素生产线平衡涉及多个关键要素,包括但不限于:•工序之间的依赖关系•工人数量和技能水平•设备效率和容量•周期时间和标准工时•产品需求和订单量6. 生产线平衡的常见问题和解决方法6.1 工序之间的不平衡如果工序之间的工作量不平衡,会导致某些工位过度工作或闲置。
生产线平衡术

生产线平衡术生产线平衡是一种优化生产流程的方法,通过合理安排工作站、任务分配和工作时间,实现生产线各工序之间的协调和平衡,从而提高生产效率和质量。
以下将探讨几种常见的生产线平衡术及其应用。
1. 工序分析在开始进行生产线平衡之前,首先需要进行工序分析。
通过对生产过程进行仔细观察和记录,了解每个工序的工作内容、工作时间和所需资源等。
通过分析工序间的依赖关系和工作量的分布情况,可以确定生产线上工作站的数量和位置,为后续的平衡操作提供依据。
2. Takt时间Takt时间是指根据客户需求和生产能力计算得出的每个产品生产所需的标准时间。
生产线平衡的目标是在Takt时间内完成每个工序的任务,确保生产线能够按时、按需地交付产品。
通过对每个工序的Takt 时间进行设定,可以为后续的任务分配提供指导。
3. 平衡任务在生产线平衡中,任务分配是关键环节。
合理的任务分配可以避免工作站之间的闲置和过载,确保生产线的高效运转。
根据工序分析和Takt时间的设定,将工作任务合理地分配给每个工作站,使得每个工作站的工作量相对均衡。
同时,还需要考虑员工的专业技能和经验,将任务分配给最合适的员工。
4. 人力资源管理生产线平衡也需要考虑人力资源的合理利用。
在任务分配时,需要根据员工的能力和经验进行合理的安排,避免出现因为个别员工的工作能力不足而导致整个生产线的效率下降。
此外,还需要注意员工的工作负荷和工作环境的安全性,确保员工的身心健康。
5. 持续改进生产线平衡是一个动态的过程,需要持续地进行改进和优化。
通过定期对生产线进行评估和分析,发现问题并及时解决,可以进一步提高生产效率和质量。
同时,也需要与员工进行良好的沟通和反馈,听取他们对生产线的建议和意见,共同推动生产线的改进和发展。
综上所述,生产线平衡术是一种有效的生产管理方法,可以帮助企业提高生产效率和质量,降低生产成本。
通过工序分析、Takt时间的设定、任务分配和人力资源管理等手段,可以实现生产线的协调和平衡。
精益化管理——line balance training(生产线平衡)
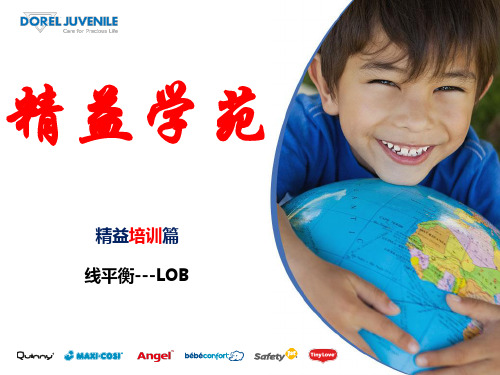
1. 生 定产义线平衡的定义 ② 瓶颈识别
时间 T1
一、定义
T2
瓶颈时间
T3
T4
T5
S1
S2
S3
S4
S5
生产线作业工时最长的工站的标准工时称之为瓶颈。 产出的速度取决于时间最长的工站
工站
一、定义
1. 生 定产义线平衡的定义
③ 节拍、增值时间、交付周期的定义
C/T
流程的“节拍”(Cycle time)是指连续完成同的两个产品(或两次服务,或两批
标准工时是一个熟练工用规定的作业方法以标准速度进行作业时间。 在熟练度、合理性、工作热情及其他所有方面都相同的“标准作业员”以标准的作业放 大及其合理的努力程度进行作业,完成某到工序所需的时间。
一、定义
1. 定义 ⑦ 标准工时的用途
科学化/高效化企业
企业发展与经营管理策略讨论参与
研发体系改善/咨询管理优化/企业流程再造
节拍
产品)之间的间隔时间。换句话说,即指完成一个产品所需的平均时间。节拍通
常只是用于定义一个流程中某一具体工序或环节的单位产出时间。如果产品必
须是成批制作的,则节拍指两批产品之间的间隔时间。在流程设计中,如果预
先给定了一个流程每天(或其它单位时间段)必须的产出,首先需要考虑的是流
程的节拍。
增值时间
增值时间(Valve-Creating Time,VCT) 产品生产过程中,客户愿意付费的工作时间(增值时间)。
平
衡
的
通过线平衡改善可以使用IE手法、动作分析、layout
意
义
实现单元化生产,柔性化生产,提升市场的应变能力
平衡员工心态,平衡工资水平,实现绩效合理化
生产线平衡原理

生产线平衡原理1. 简介在生产过程中,生产线平衡是一种优化生产效率和资源利用的重要方法。
生产线平衡原理是指通过合理安排工作内容和工作站,使生产线上的各个工作站能够均衡地完成任务,达到最高效的生产效率。
本文将介绍生产线平衡的基本原理和实施方法。
2. 生产线平衡的原理生产线平衡的核心原理是追求任务分配的均衡性,即使得每个工作站的工作量相等,制约生产线效率的瓶颈工作站得到优化,从而实现整个生产线的高效运转。
2.1 任务分配任务分配是生产线平衡的核心。
在进行任务分配时,需要考虑以下几个因素:•任务的复杂程度:将简单任务和复杂任务合理地进行分配,以降低工作站之间的任务差异。
•任务的周期性:任务的周期性可以帮助确定任务分配的时间间隔,避免产生工作站之间的任务积压。
•任务的依赖关系:如果存在任务之间的依赖关系,需要合理安排任务的先后顺序,确保前置任务完成后再分配后续任务。
•任务的时间需求:根据任务的时间需求,合理安排工作站的工作时间,并避免任务超时和工作站之间的等待时间。
2.2 工作站优化工作站的优化主要包括以下几个方面:•人员技能培训:提供针对不同任务的相关培训,使工作人员掌握多样化的技能,并减少任务之间的转换时间。
•工作站设备和工具的合理配置:根据任务的不同需求,合理配置工作站的设备和工具,提高工作效率。
•工作站布局和空间利用:合理规划工作站布局,减少不必要的物料运输和工作站之间的距离,提高生产效率。
3. 生产线平衡的实施方法在实施生产线平衡时,可以采用以下方法:3.1 时间研究法时间研究法是一种通过观察和测量工作站的运作时间来分析任务分配和工作站优化的方法。
具体步骤包括:1.记录每个工作站的任务开始时间和结束时间。
2.测量每个任务的工作时间和任务间隔时间。
3.分析任务分配情况,确定工作站之间的任务差异。
4.根据分析结果,调整任务分配和工作站优化方案。
3.2 平衡图法平衡图法是一种通过绘制生产线的平衡图来分析任务分配和工作站优化的方法。
IE手法简介(lql)

今不做何时做我不做谁来做关于I EIE=Industrial Engineering ,工业工程,是关于人员、物料、设备以及能源等整体系统的设计、改善与装置的一门技朮,对系统可能得到的结果予以规定、预测和评估。
企业内IE活动的日常工作事项:1. 作业研究和作业改善2. 标准的设定和维持3. 成本报价4. 工厂管理数据之作成(设备能力,工厂能力,工厂负荷,作业能率等)5. 工程管理(工程计划,进度)6. 设备管理(设备计划,筹办,保养)7. 工具管理(治工具的设计、制作、筹办)8. 质量管理9. 情报管理(图面其它制造情报,实绩报告等)IE七大手法简介一、工程分析:将生产工程和作业方法进行调查分析,来掌握问题点的手法,系从原材料至完成品为止,顺沿着工程的流动把各工程用记号表示之,作成作业流程图。
再集全工程的总括表,经分析结果予以定量化,找出问题。
工程记号三大类:1、稼动---- ○,产生附加价值的作业2、准稼动---◇□→,现状的方式是不可避免的,但大力去改善可以免除的作业3、非稼动----D▽,不产生附加价值的作业。
下面公式为稼动率计算公式:改善的步骤:先把非稼动除去,其次是如何避免准稼动的系统改善,至于稼动须要下工夫,利用种种努力使工时数减少,以提高效果。
制造周期率= E○/E(◇+□+→+D+▽)*100二、搬运工程分析对生产过程中物料的移动距离、经过时间、以及等待在内的整个搬运活动分析。
一般通过操作程序图和流程程序图、流程线图来分析,寻找最短路径。
三、稼动分析(工作抽查work sampling):是人和机械的稼动状态,以瞬时观测周而复始的采取抽样方式,列入对象现象的发生率作业实用上可以满足信赖度和精度,用统计的来推定的方法。
目的:1、设定宽放率2、了解设备的使用情况机台稼动率:相对稼动率=机台利用时间/机台最大可利用时间﹔绝对稼动率=机台利用时间/所有机台最大可利用时间﹔例:*月*日单剖机有3台机使用,使用时间分别为8h(2小时架刀、半小时卫生)、8.5h(1.5小时坏机,半小时卫生)、9h(1小时待料、半小时卫生),本日上班时间为8小时正常上班,2.5小时加班﹔(单剖机共有5台)﹔则此日之稼动率分别为:相对稼动率=8+8.5+9/10.5*3=0.8095=80.95%﹔绝对稼动率=8+8.5+9/10.5*5=0.4857=48.57%﹔四生产线平衡:依照流动生产的工程顺序,从生产目标算出周期时间,将作业分割或结合,使各工程的负荷均匀,提高生产效率的技法,叫做生产线平衡( line Balancing)作业编成率=各工程的作业时间合计/工程中最长的时间*作业者人数(工程数)*100生产线编成损失率=100-作业编成率A、推行步骤:1、单工程时间(ST)测定2、分析表作成(效率评估表)3、计算balance效率和balance loss4、实施line bal ancing ,则时间长的工程分配到时间短的工程5、改善后的pitch diagram 作成,效率计算6、结果比较B、作业编成改善程序1、现状登录(工序、人员、配置、产量/日,不良率)2、QC工程图重审3、作业动作再指导(动作经济原则15条)4、ST重测(周期ST,单工程ST)5、作业编成效率计算6、物流规划定案7、车间输补材料放置区设置(完成品,待检区,合格出货区,不良区,重工区,参观路线)8、改善成果发表五、动作分析:therblig是动作研究,从作业者的动作顺序观察要素动作,不产生附加价值的作业(不合理、不平衡、不需要=3不)或作业者周边的治工具配置等,作为改善检讨之着眼点的手法。
生产线平衡LineBalance

© USI proprietary and confidential
8
二﹑生产线平衡的常见概念
USI SMT线平衡计算公式:
© USI proprietary and confidential
9
二﹑生产线平衡的常见概念
USI SZ的生产线平衡率指标:
SMT>92%; ASM&TEST&PACKYING>88%
1.各工站顺序(作业单位)填入生产流动平衡表內. 2.量测各工序作业时间记入表內. 3.清点各工序人数记入表內. 4.根据分配时间划出柱狀图或曲线图. 5.在最高时间点的工序顶点橫向划一条线. 6.计算平衡率.
SS rrS S S Srr r SrS tr ti i r t11i 0 t0i1% % 0 001% 00% 0
确定生产线平衡改善方向
1、5M方法的改善
2、作业方法的改善
© USI proprietary and confidential
18
三﹑生产线平衡的分析改善
1、5M方法的改善:
(5M:人员,机器设备,物料,作业方法,环境)
减少耗时最长工序作业时间的方法有: 人员(Man):调换作业者;增加作业者;多能工训练; 新手避免工作负荷过重,利用作业员熟练程度的 差异性,平衡作业流程.
24
Q&A
某一生产线﹐按照工程分析设计成10个作业 工序﹐每个工序的时间分別为 18﹑12﹑15﹑14﹑25﹑12﹑41﹑20﹑28﹑12. 你如何來安排生产与人力配置?
© USI proprietary and confidential
25
机器设备(Machine):利用或改良工具、机器;人机 比合理配置;人机同步作业;提高自动半自动化水平; 人机工程分析,提高机械效率.
- 1、下载文档前请自行甄别文档内容的完整性,平台不提供额外的编辑、内容补充、找答案等附加服务。
- 2、"仅部分预览"的文档,不可在线预览部分如存在完整性等问题,可反馈申请退款(可完整预览的文档不适用该条件!)。
- 3、如文档侵犯您的权益,请联系客服反馈,我们会尽快为您处理(人工客服工作时间:9:00-18:30)。
生产线平衡
1 生产线平衡 1.1 基本概念
将作业分成可控制的作业包分配给各个工作地,每一个工作地有一个或者两个工人操作,决定如何将作业分配给工作地这一过程叫生产线平衡。
生产线平衡的目标是分到各个工作地的时间大致相等。
达到生产线完全平衡的障碍主要在于组成具有同样加工时间的作业包是困难的。
1) 由于对设备要求不同或一些活动不相容,把这些活动分配到一个作业包是不行的。
2) 基本作业的时间差异通过作业分组解决不了。
3) 所要求的技术顺序也可能妨碍作业组合。
考虑到下面三个操作:把第一个操作和第三个
操作分配到一个工作地时该工作地的时间正好等于第二个工作地的时间,但是,很明显是不可能的。
1.2 生产线的节拍
节拍是指将完成单位产品所需要的作业分配到各工作地,各个工作地完成其上作业所容许的最大时间,如果节拍是2分钟,那么该生产线将每两分钟完成一个产品。
例如有一套工序,可能最小的节拍等于最长的那个作业时间(1分),可能最大作业时间等与各作业时间之和(0.1+0.7+1.0+0.5+0.2=2.5)。
很明显,最大节拍是所有的作业在一个工作地上完成时出现的,最小作业节拍是分别在五个工作地上完成时出现的。
最小和最大节拍确定了生产线可能的产量范围,产量=OT/CT OT=计划期有效工作时间 CT=节拍
假定一生产线一天运转8小时(480分),节拍为一分钟,则产量为OT/CT=480单位,当节拍为2.5分时,产量= OT/CT=192单位,假如无平行活动(两条生产线),那么产量必定介于192和480之间。
若计划期产量确定后,可计算出节拍。
CT=OT/D D ——计划期产量
例如,产量是每天480单位,节拍是每天480分/每天480单位=1.0分 可用下面的公式求出工作地数的理论最小值:min N t /CT =
∑
t ∑—各作业时间之和
假如计划产量为480,那么为达到这一目标最少需要的工作地数目为 完成单位产品时间2.5分/节拍1分=2.5 取整数3。
1.3 生产线平衡的程序
生产线平衡的方法有很多种,下面介绍一种启发式方法:
1)先分配后续作业最多的作业
2)先分配位置权数最大的作业,位置权数等于该作业及其所有后续作业的时间总和。
程序如下:
1.确定节拍,求出最小所需工作地数
2.从工作地1开始,按顺序给工作地分配作业。
作业的分配按作业下先后顺序图由左
至右进行
3.在每一分配前,利用下列标准确定哪些作业够资格分配给一工作地:
a)所有先行作业都已经被分配
b)该作业时间不超过该工作地的剩余时间
如果没有够资格分配的作业,继续下一工作地
4.每当一个工作分配后,计算出该工作地的剩余时间,剩余时间等于节拍减去工作地
总的作业时间。
5.如果出现两个作业情况都一样的情况,可采用下列方法之一解决:
A.分配加工时间最长的作业
B.分配后续作业最多的作业
6.继续下去直到所有工作都已经被分配
7.计算一些指标。
生产线平衡率=各工序时间和/(人数*CT)*100%
平衡损失率=1-平衡率
例:利用下图,完成:1.画出作业先后顺序图 2.假定一天工作8小时,计算一天要达
(2)CT=OT/D=480/400=1.2分 (3)min N t /CT =∑=3.8/1.2=3.14
1. A 和c 够资格分配,因为a 的后续作业较多,所以先分配a
2. b 和c 够资格分配,由于采用后续作业数最多,所以分配所需时间最长的作业
3. 尽管f 是够资格的,但是他不适合
请读者自己计算平衡率。
韩格逊一伯尼法
该方法又称为位置加权法或阶位法,是1961年由W ·B ·Helgeson 和D .P .Birnie 提出的。
这种方法是首先求出每个作业要素的阶位(或称为位置权重),所谓阶位是作业要素时间与其所有后续作业要素时间的总计,然后根据阶位的高低进行作业安排,优先安排阶位高的
作业要素,从而尽量减少工作地数。
下面举例介绍韩格逊一伯尼法的具体步骤。
.例如:某产品装配共需11
个作业要素,其先后顺序及作业时间(单位:ITlin)如图8—3所示。
假定节拍为10rain ,试进行流水线的平衡。
图8-3某产品装配作业要素示意图
第
一
步,编制作业要素先后矩阵(见表8—1)。
若作业要素i 先于作业要素J .则矩阵元素值为J 的作业时间。
处于对角线上的元素也表明作业时间。
‘ 第二步,计算各作业要素的阶位,计算公式为 i i j
j p
w ττ
∈=+
∑
式中i w ——作业要素i 的阶位;
i τ ——作业要素i 的作业时间;P ——所有在i 作业要素以后的作业要素集合。
从表8—2中可以看出,在矩阵各行相加,即得各作业要素阶位。
第三步,按阶位由大到小排列,并标明各作业要素的紧前作要素(表8—2)
第四步,作业要素的分配。
根据表8—2,按作业要素阶位由到小的顺序,并考虑紧前作业要素和作业时间。
在本例中,首先配作业要素①,其时间为4min ,和节拍相差6min 。
再将
②分配第一
个工作地,仍和节拍差3min 。
若将⑤也可配给第一个工作就
会超出节拍,而将③和④分配给第一个工作地后作业时间之和等于节拍,因此分配给第一个工作地的作业为①、②、③、④。
删除已分配的作业要素,继续按阶位由大到小的顺序分配第二个I作地,将⑤分配给第二个工作地,此时作业时间和节拍相差1min,后续作业要素的时间皆超过lmin,因此分配给第二个工作地的作业为⑤。
继续按上述方法分配,最后的结果见表8—3。
该流水线负荷系表8-3装配作业要素分配表
┏━━━━━━┳━━━━━━━┳━━━━━━━┳━━━━━━━━━━━┓
┃工作地┃作业要素┃作业时间┃工作地负荷系数/%┃
┣━━━━━━╋━━━━━━━╋━━━━━━━╋━━━━━━━━━━━┫
┃ 1 ┃①②③④┃ 10 ┃ 100 ┃
┃ 2 ┃⑤┃ 9 ┃ 90 ┃
┃ 3 ┃⑥⑨⑦┃ 10 ┃ 100 ┃
┃ 4 ┃⑩⑧┃ 9 ┃ 90 ┃
┃ 5 ┃⑩┃ 8 ┃ 80 ┃
┗━━━━━━┻━━━━━━━┻━━━━━━━┻━━━━━━━━━━━┛
上面的已经给出解析方法,现在我做些补充:
1.
上图可根据其紧后作业联系在一起,用笔在草纸上绘出起关系式;最终就可以绘出上面图示了。
1. 1 CT是生产节拍,根据目前要求400pcs的产量,一天8小时共480分钟,所以要求在480/400的时间内出来1pcs产品。
所以CT=1.2分钟
1.2 N nm(工站数)=总时间/除以节拍时间(整数)
1.3 优先顺序:后续作业内容最多的优先作业,依次类推,以至到其总和时间小于等于节拍时间为止定义到一个工站内,然后再进行下道工站的分配决定。
2. 平衡率(定义各站的作业内容后即作业时间也就定了):
平衡率= (这我明白的)
平衡率= = = 79.2%
你解释的我明白了一点,谢谢!
上面说紧后作业又是怎么回事?我不明白啊,
最大工站时间 X 工站数 各站总时间
第1站 1.2 分钟 第2站 0.9分钟
第3站 1.0分钟 第4站 0.7分钟
1.2+0.9+1.0+0.7 1.2 X 4 3.8
4.8
上图可根据其紧后作业联系在一起,用笔在草纸上绘出起关系式;最终就可以绘出上面图示了。
(就是要你给我画出来啊,我找不好啊)
1. 1 CT 是生产节拍,根据目前要求400pcs 的产量,一天8小时共480分钟,所以要求在480/400的时间内出来1pcs 产品。
所以CT=1.2分钟 1.2 N nm (工站数)=总时间/除以节拍时间(整数)
1.3 优先顺序:后续作业内容最多的优先作业,依次类推,以至到其总和时间小于等于节拍时间为止定义到一个工站内,然后再进行下道工站的分配决定。
(就是不明白什么是优先作业啊,什么是后续作业内容最多的优先作业啊?)
2. 平衡率(定义各站的作业内容后即作业时间也就定了):
第二步,计算各作业要素的阶位,计算公式为 i i j
j p
w ττ
∈=+
∑
式中i w ——作业要素i 的阶位;
i τ ——作业要素i 的作业时间;P ——所有在i 作业要素以后的作业要素集合。
从表8—2中可以看出,在矩阵各行相加,即得各作业要素阶位。
上面 是怎么计算的?
什么是作业要素阶梯?我不太明白啊,告诉我了。
谢谢了,昨天我没有加班,但是昨天下午我就看到了,我没有把问题写完,所以昨天没有发给你,今天一早就写好了 呵呵
这里你讲我的明白了,但是你所说的在草稿纸上画画就知道他们的关系了,真是的,我就不是画啊,找不好他门之间的关系啊,你还是帮我画画好吗?告诉我好吗。