电石渣水泥相关资料
利用电石渣生产水泥

利用电石渣生产水泥1 引言建设节约型社会、发展循环经济已成为人们的共识,处理电石渣的传统方式已不能适应社会发展的要求,甚至被政府环保部门明令禁止,如何有效地处理电石渣已经成为各生产厂可持续发展的“瓶颈”问题。
只有水泥工业把电石渣作为代替石灰石质原料,对电石渣消耗量最大、最为彻底、技术上也最为成熟,因此作为原料生产水泥成为综合利用电石渣的主要途径。
有效地综合利用电石渣,对保护环境、节约土地和水资源及实现经济可持续发展具有显著的生态和社会效益。
合肥水泥研究设计院十分注重水泥行业的循环经济发展,研究各种工业废渣在水泥生产中的综合利用,一直致力于用电石渣生产水泥的综合技术与装备的开发研究,采用多种水泥生产工艺消化电石渣并取得显著成绩;继在安徽皖维高新材料股份有限公司成功采用电石渣掺量15%干磨干烧工艺生产水泥的基础上,适时地提出能否用新型干法生产工艺煅烧高掺量电石渣的新课题,即用电石渣替代70~80%石灰石或全部石灰石生产水泥熟料,该课题的意义在于:1.1、由于电石渣的特性和电石渣配料生料的特殊性,业内人士一直有新型干法生产工艺不适合煅烧高掺量电石渣生料的观点,如果该项技术有所突破,将为预分解技术处理其它工业废渣带来新的启迪,为形成一套优质、高效、节能、环保以及单条生产线规模大型化的现代水泥生产方法提供良好的示范。
1.2、该项技术与带压滤湿法回转窑生产工艺相比节煤30%,同时每生产1吨熟料节水0.15吨,与湿磨干烧生产工艺相比节水0.66吨。
对于煤炭储采比不足百年的中国来说节能尤其重要,不能以处理电石渣消耗大量能源为代价。
1.3、生产1吨熟料需要消耗1.28吨优质石灰石,同时向大气中排放0.57吨CO2,用电石渣替代石灰石生产水泥熟料,可以减轻我国石灰石矿的开采和减少CO2排放。
1.4、随着煤化工行业科学技术的不断进步,生产过程中电石渣以干基(含水分10-12%)排放,将为新型干法生产工艺煅烧高掺量电石渣提供捷径。
电石渣代替石灰石生产水泥生料配料工艺
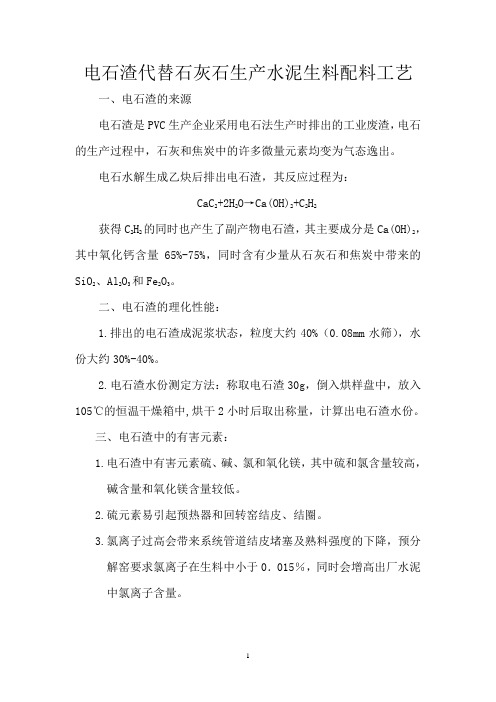
电石渣代替石灰石生产水泥生料配料工艺一、电石渣的来源电石渣是PVC生产企业采用电石法生产时排出的工业废渣,电石的生产过程中,石灰和焦炭中的许多微量元素均变为气态逸出。
电石水解生成乙炔后排出电石渣,其反应过程为:CaC2+2H2O→Ca(OH)2+C2H2获得C2H2的同时也产生了副产物电石渣,其主要成分是Ca(OH)2,其中氧化钙含量65%-75%,同时含有少量从石灰石和焦炭中带来的SiO2、Al2O3和Fe2O3。
二、电石渣的理化性能:1.排出的电石渣成泥浆状态,粒度大约40%(0.08mm水筛),水份大约30%-40%。
2.电石渣水份测定方法:称取电石渣30g,倒入烘样盘中,放入105℃的恒温干燥箱中,烘干2小时后取出称量,计算出电石渣水份。
三、电石渣中的有害元素:1.电石渣中有害元素硫、碱、氯和氧化镁,其中硫和氯含量较高,碱含量和氧化镁含量较低。
2.硫元素易引起预热器和回转窑结皮、结圈。
3.氯离子过高会带来系统管道结皮堵塞及熟料强度的下降,预分解窑要求氯离子在生料中小于0.015%,同时会增高出厂水泥中氯离子含量。
四、电石渣生产水泥工艺的原燃料:1.生料配料用原料:电石渣、硅废石、粉煤灰、钢渣。
其中电石渣成分见表:2.进厂电石渣主要控制指标:备注:经烘干后电石渣的水份应小于2.0%3.生料配料用燃料:生料配料用燃料全部使用烟煤,无搭配使用情况,原煤的质量控制指标及使用平均值见下表:4.生料配料用煤粉控制指标及实际值见下表:五、生、熟料相关工艺参数1.生料分解率:≥90%2.熟料三率值:KH=0.90 SM=2.35 IM=1.453.熟料游离氧化钙:0.3%-1.3%4.熟料立升重:1280kg/L六、生料荧光曲线标定:1.电石渣生产水泥的生料曲线标定与石灰石生产水泥生料曲线基本相同,主要增加碱、硫、氯的含量。
2. 电石渣生产水泥的生料曲线标定:接近生产,按比例配制小样7-8个,进行化学全分析,根据化学全分析的结果进行荧光曲线的标定。
电石渣水泥相关资料
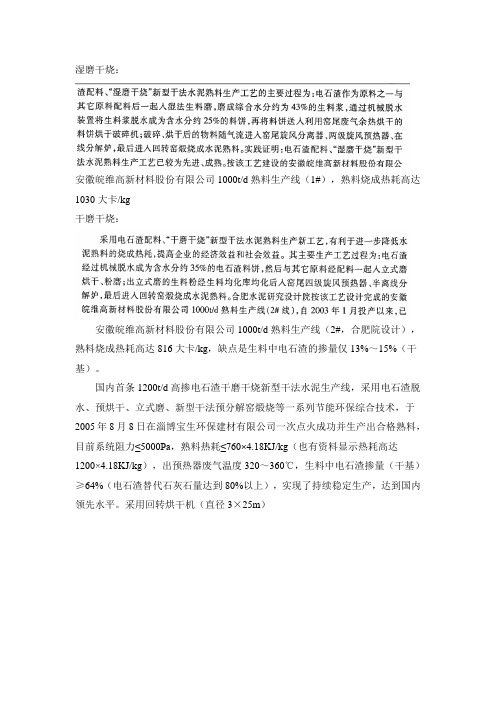
湿磨干烧:安徽皖维高新材料股份有限公司1000t/d熟料生产线(1#),熟料烧成热耗高达1030大卡/kg干磨干烧:安徽皖维高新材料股份有限公司1000t/d熟料生产线(2#,合肥院设计),熟料烧成热耗高达816大卡/kg,缺点是生料中电石渣的掺量仅13%~15%(干基)。
国内首条1200t/d高掺电石渣干磨干烧新型干法水泥生产线,采用电石渣脱水、预烘干、立式磨、新型干法预分解窑煅烧等一系列节能环保综合技术,于2005年8月8日在淄博宝生环保建材有限公司一次点火成功并生产出合格熟料,目前系统阻力≤5000Pa,熟料热耗≤760×4.18KJ/kg(也有资料显示热耗高达1200×4.18KJ/kg),出预热器废气温度320~360℃,生料中电石渣掺量(干基)≥64%(电石渣替代石灰石量达到80%以上),实现了持续稳定生产,达到国内领先水平。
采用回转烘干机(直径3×25m)1、电石渣干排(水分含量3%~5%)和湿排(电石渣压滤后水分38%~45%)2、利用电石渣生产水泥的优势在于:(1)利用电石渣生产水泥比采用石灰石生产水泥熟料烧成热耗有所降低,如替代60%石灰石时,熟料烧成热耗约降低8%;替代80%石灰石时,熟料烧成热耗约降低15%。
(2)与带压滤半湿法回转窑生产工艺相比节煤46%,与湿磨干烧相比节煤20%,对于煤炭储采比不足百年的中国来说节能尤其重要,不能以处理电石渣而消耗大量能源为代价。
(3)由于带压滤半湿法回转窑和湿磨干烧生产工艺必须将其它组分加水粉磨成合格的料浆,每生产1吨熟料需要多消耗0.15吨水,带来水资源和能源的浪费。
(4)生产1吨熟料需要消耗1.28吨优质石灰石,同时向大气中排放0.57吨CO2,用电石渣替代石灰石生产水泥熟料,可以减轻我国石灰石资源不足和减少CO2排放;(5)随着煤化工行业科学技术的不断进步,生产过程中电石渣以干基(含水分10-12%)排放,将为新型干法生产工艺煅烧高掺量电石渣提供捷径。
电石渣生产水泥简介
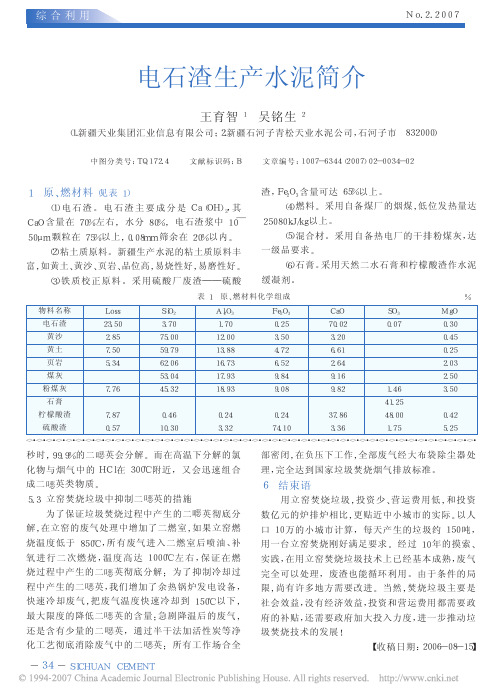
化物与烟气中的 HCl 在 300℃附近, 又会迅速组合 理, 完全达到国家垃圾焚烧烟气排放标准。
成二哐恶英类物质。 5.3 立窑焚烧垃圾中抑制二哐恶英的措施
为了保证垃圾焚烧过程中产生的二哐恶英彻底分 解, 在立窑的废气处理中增加了二燃室, 如果立窑燃 烧温度低于 850℃, 所有废气进入二燃室后喷油、补 氧 进 行 二 次 燃 烧 , 温 度 高 达 1000℃左 右 , 保 证 在 燃 烧过程中产生的二哐恶英彻底分解; 为了抑制冷却过 程中产生的二哐恶英, 我们增加了余热锅炉发电设备, 快速冷却废气, 把废气温度快速冷却到 150℃以下, 最大限度的降低二哐恶英的含量; 急剧降温后的废气, 还是含有少量的二哐恶英, 通过半干法加活性炭等净 化工艺彻底消除废气中的二哐恶英; 所有工作场合全
广, 中国建材机械工业协会耐磨材料及抗磨技术 分会和新世纪水泥导报杂志社决定在郑州举办以 “提高耐磨材料应用水平, 降低水泥企业运营成 本”为主题的第二届水泥工业用耐磨材料技术研 讨会, 本次会议集专家论坛、技术交流和产品展示 于一体, 还将举行《水泥工业耐磨材料与技术应用 手册》首发及赠书仪式。本次会议由郑州机械研究 所特种焊接材料研究室和洛阳鹏飞耐火材料有限 公司协办。
( 1) 电石渣生产水泥国内不足 10 条生产线, 大 多采用湿法窑生产, 而我公司采用湿磨干烧工艺非 常成功。
( 2) 电石渣生 产 水 泥 、熟 料 热 耗 低 , 因 为 CaCO3 分解温度为 750°C, 而电石渣中 Ca(OH)2 分解温度仅 为 580°C, 两者吸热差为 501.6kJ /kg。
( 3) 电石渣是乙炔气生产中的废渣, 充分利用了 它具有环保和循环经济的意义。
【收稿日期: 2006- 07- 14】
利用电石渣生产水泥的研究

利用电石渣生产水泥的研究
电石渣主要化学成分是氢氧化钙约占70%左右,因此可代替石灰石,氢氧化
钙比石灰石中的碳酸钙易分解,因此掺电石渣后对水泥熟料强度和产量提高,降低热耗大有好处,,通过用电石渣代替石灰石生产水泥工艺的实验研究发现:电石渣能代替石灰石生产优质水泥,配热大约为3135 kJ/kg(熟料)。
随着电石渣掺量增大、料球易烧性越好、熟料质量越高,三率值以三高为好。
在机立窑水泥厂中,利用现有的设备条件、采用新技术,把湿电石渣和粘土、粉煤灰、煤等按生料进行配比,制成含水量50-55%的料浆,并用此浆代替立窑成球用水,经计量加入到双轴搅拌机中,与生料磨制备的正常生料混合搅拌均匀后进入成环球盘,制成含有一定电石渣量的料球,入机立窑煅烧生产水泥熟料,进行试生产研究表明:该技术是成功的,黑生料球性能好、煅烧操作容易、熟料质量高,各项工艺指标都达到要求。
这一新工艺具有明显的增产节能效果。
主要表现在: CaO含量高达65%,改善了生料的易烧性;电石渣中的Ca(OH)<sub>2</sub>分解温度比石灰石中的CaCO<sub>3</sub>的分解温度低很多,烧
成热耗较低;减少石灰石用量,不仅节约了不可再生资源石灰石的用量,而且还解决了多年来因废渣污染无法处理带来的难题,使资源得到了充分合理的利用,改善了生态环境。
电石渣制水泥脱硝协同氨逃逸技术路径
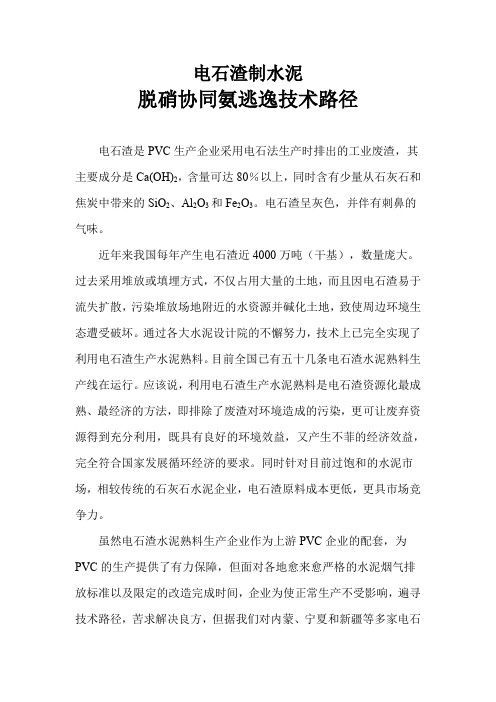
电石渣制水泥脱硝协同氨逃逸技术路径电石渣是PVC生产企业采用电石法生产时排出的工业废渣,其主要成分是Ca(OH)2,含量可达80%以上,同时含有少量从石灰石和焦炭中带来的SiO2、Al2O3和Fe2O3。
电石渣呈灰色,并伴有刺鼻的气味。
近年来我国每年产生电石渣近4000万吨(干基),数量庞大。
过去采用堆放或填埋方式,不仅占用大量的土地,而且因电石渣易于流失扩散,污染堆放场地附近的水资源并碱化土地,致使周边环境生态遭受破坏。
通过各大水泥设计院的不懈努力,技术上已完全实现了利用电石渣生产水泥熟料。
目前全国已有五十几条电石渣水泥熟料生产线在运行。
应该说,利用电石渣生产水泥熟料是电石渣资源化最成熟、最经济的方法,即排除了废渣对环境造成的污染,更可让废弃资源得到充分利用,既具有良好的环境效益,又产生不菲的经济效益,完全符合国家发展循环经济的要求。
同时针对目前过饱和的水泥市场,相较传统的石灰石水泥企业,电石渣原料成本更低,更具市场竞争力。
虽然电石渣水泥熟料生产企业作为上游PVC企业的配套,为PVC的生产提供了有力保障,但面对各地愈来愈严格的水泥烟气排放标准以及限定的改造完成时间,企业为使正常生产不受影响,遍寻技术路径,苦求解决良方,但据我们对内蒙、宁夏和新疆等多家电石渣企业走访交流,各企业尚未找到理想的技术路径,面对即将实施的新标准,大家都忧心如焚。
电石渣水泥熟料生产线和传统的石灰石产线相比在烟气成分上有其特殊性,烟气污染物治理难度更大,而其中尤为困难的是氨逃逸的达标治理,原因在于在电石水解制乙炔过程中,电石中杂质也参与反应生成Ca(OH)2和其他气体,杂质Ca3N2遇水会分解出氨:Ca3N2+6H2O﹦3Ca(OH)2+2NH3↑因此,在粉磨(生料磨)烘干电石渣过程中和原料进入分解炉时均会析出氨,加上前端SNCR过量喷氨,势必导致氨逃逸严重超标,少则几十毫克,多则几百毫克,的确让人触目惊心。
目前绝大部分电石渣水泥熟料产线在二氧化硫和颗粒物已经可以满足达标排放(可实现超低排放),难点就在氮氧化物和氨逃逸协同达标治理。
利用电石渣生产水泥.docx

利用电石渣生产水泥1 引言建设节约型社会、发展循环经济已成为人们的共识,处理电石渣的传统方式已不能适应社会发展的要求,甚至被政府环保部门明令禁止,如何有效地处理电石渣已经成为各生产厂可持续发展的“瓶颈” 问题。
只有水泥工业把电石渣作为代替石灰石质原料,对电石渣消耗量最大、最为彻底、技术上也最为成熟,因此作为原料生产水泥成为综合利用电石渣的主要途径。
有效地综合利用电石渣,对保护环境、节约土地和水资源及实现经济可持续发展具有显著的生态和社会效益。
合肥水泥研究设计院十分注重水泥行业的循环经济发展,研究各种工业废渣在水泥生产中的综合利用,一直致力于用电石渣生产水泥的综合技术与装备的开发研究,采用多种水泥生产工艺消化电石渣并取得显著成绩;继在安徽皖维高新材料股份有限公司成功采用电石渣掺量15%干磨干烧工艺生产水泥的基础上,适时地提出能否用新型干法生产工艺煅烧高掺量电石渣的新课题,即用电石渣替代70〜80%石灰石或全部石灰石生产水泥熟料,该课题的意义在于:1.1、由于电石渣的特性和电石渣配料生料的特殊性,业内人士一直有新型干法生产工艺不适合煅烧高掺量电石渣生料的观点,如果该项技术有所突破,将为预分解技术处理其它工业废渣带来新的启迪,为形成一套优质、高效、节能、环保以及单条生产线规模大型化的现代水泥生产方法提供良好的示范。
1.2、该项技术与带压滤湿法回转窑生产工艺相比节煤30%,同时每生产1 吨熟料节水0.15 吨,与湿磨干烧生产工艺相比节水0.66吨。
对于煤炭储采比不足百年的中国来说节能尤其重要,不能以处理电石渣消耗大量能源为代价。
1.3、生产1吨熟料需要消耗1.28吨优质石灰石,同时向大气中排放0.57吨CO2,用电石渣替代石灰石生产水泥熟料,可以减轻我国石灰石矿的开采和减少CO?排放。
1.4、随着煤化工行业科学技术的不断进步,生产过程中电石渣以干基(含水分10-12%)排放,将为新型干法生产工艺煅烧高掺量电石渣提供捷径。
电石渣替代石灰石沫生产水泥熟料浅析

电石渣替代石灰石沫生产水泥熟料浅析摘要:早在上世纪七八十年代,国外就已经开始使用电石渣进行水泥的生产,它甚至已经成为了水泥生产最主要的材料,部分用于水泥的混合材料,因为受到多种原因的限制,所以在实际操作的过程当中,依然存在较多的问题,需要进行解决。
我国最早使用电石渣进行水泥厂的生产工作是在上世纪70年代,电石渣可以代替部分石灰石,它主要用于立窑水泥厂当中,最关键的技术是对水分的影响进行充分的消除。
因为电石渣当中含有残余的气体,所以它不能作为水泥混合材料使用。
本文主要针对湿法生产水泥以及干法生产水泥的优势和缺点进行探讨,并且以技术指标作为基础,分析它使用的社会效益以及经济效益,探讨电石渣代替石灰石的具体优势。
关键词:石灰石;水泥熟料;电石渣;分析本文主要针对电石渣代替石灰石生产水泥熟料的相关内容进行探讨,并以传统意义上的电石渣作为基础,分析它代替石灰石作为原料进行实际生产的过程当中及相关的技术利弊,在实际操作时对后期生产的效率有可能产生的影响。
在使用电石渣代替石灰石作为原料进行生产时,不仅可以达到提高产品生产经济效益的目的,同时也可以增加节能减排保护环境的社会效益,两者在实际操作时相关的技术指标存在比较明显的差异,本次课题主要针对相关的内容进行探讨。
1.历史上电石渣的使用在19世纪60年代国外就已经关注电石渣在水泥生产工作当中产生的价值以及具体的工艺技术,经过多年的研究以及实践操作之后已经逐渐成为水泥生产的主要原料,其在水泥生产工作当中占据着重要的地位。
有一小部分类型的电石,它可以用于水泥的混合材料的制作工作,从实际操作的效果以及后期的应用价值来看,电石渣的使用也存在一些客观的缺陷,其中最突出的问题就是它的水分有限。
所以大部分水泥厂在使用电石渣进行水泥生产操作时,会优先选择湿法水泥的生产方式。
从目前我国电石渣用于水泥生产的实际情况来看,在上世纪70年代,也就是与国外时间相比推迟20年左右,有几家水泥厂曾经使用电石渣代替石灰石进行水泥的生产工作,但是因为水分的问题无法得到有效的解决,所以整体的应用效果并不是非常的明显。
电石渣研究报告
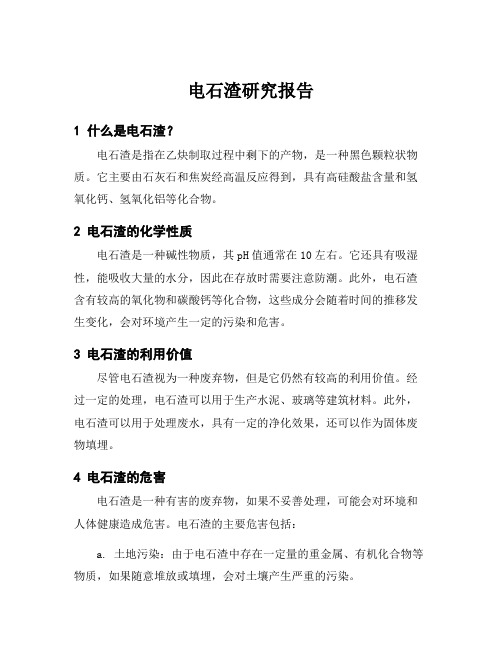
电石渣研究报告1 什么是电石渣?电石渣是指在乙炔制取过程中剩下的产物,是一种黑色颗粒状物质。
它主要由石灰石和焦炭经高温反应得到,具有高硅酸盐含量和氢氧化钙、氢氧化铝等化合物。
2 电石渣的化学性质电石渣是一种碱性物质,其pH值通常在10左右。
它还具有吸湿性,能吸收大量的水分,因此在存放时需要注意防潮。
此外,电石渣含有较高的氧化物和碳酸钙等化合物,这些成分会随着时间的推移发生变化,会对环境产生一定的污染和危害。
3 电石渣的利用价值尽管电石渣视为一种废弃物,但是它仍然有较高的利用价值。
经过一定的处理,电石渣可以用于生产水泥、玻璃等建筑材料。
此外,电石渣可以用于处理废水,具有一定的净化效果,还可以作为固体废物填埋。
4 电石渣的危害电石渣是一种有害的废弃物,如果不妥善处理,可能会对环境和人体健康造成危害。
电石渣的主要危害包括:a. 土地污染:由于电石渣中存在一定量的重金属、有机化合物等物质,如果随意堆放或填埋,会对土壤产生严重的污染。
b. 水源污染:电石渣中含有一定量的有机物和盐类等物质,在大量堆积或填埋时,会对周围的水源造成严重的污染。
c. 空气污染:电石渣中的大量碳酸钙会与二氧化硫等气体反应,形成大量细小的硫酸钙颗粒,这些颗粒会引起空气污染。
d. 对健康的危害:长期接触电石渣会对人体健康产生不良影响,可能导致吸入性肺结核、慢性鼻炎、慢性支气管炎等疾病。
5 电石渣的处理方法为了减少电石渣对环境和人类健康的危害,必须对其进行妥善处理。
电石渣的处理方法主要包括填埋、焚烧和利用等。
其中,填埋和焚烧是传统的处理方式,但是会产生二次污染,同时极易引起环境和健康问题。
利用是当前的主要处理方式,通过将电石渣加工利用为一定的建筑材料等,不仅能减少其对环境的危害,还能降低生产成本,是一种可持续发展的处理方法。
6 结论电石渣是一种有害的废弃物,必须采取有效的措施进行处理。
尽管其存在一定的利用价值,但在处理时必须确保其对环境和人类健康的安全和健康没有危害。
利用电石渣生产水泥工艺设计课程
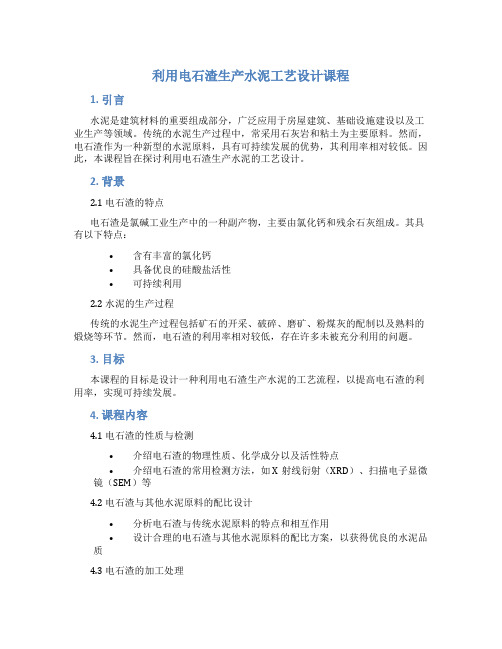
利用电石渣生产水泥工艺设计课程1. 引言水泥是建筑材料的重要组成部分,广泛应用于房屋建筑、基础设施建设以及工业生产等领域。
传统的水泥生产过程中,常采用石灰岩和粘土为主要原料。
然而,电石渣作为一种新型的水泥原料,具有可持续发展的优势,其利用率相对较低。
因此,本课程旨在探讨利用电石渣生产水泥的工艺设计。
2. 背景2.1 电石渣的特点电石渣是氯碱工业生产中的一种副产物,主要由氯化钙和残余石灰组成。
其具有以下特点:•含有丰富的氯化钙•具备优良的硅酸盐活性•可持续利用2.2 水泥的生产过程传统的水泥生产过程包括矿石的开采、破碎、磨矿、粉煤灰的配制以及熟料的煅烧等环节。
然而,电石渣的利用率相对较低,存在许多未被充分利用的问题。
3. 目标本课程的目标是设计一种利用电石渣生产水泥的工艺流程,以提高电石渣的利用率,实现可持续发展。
4. 课程内容4.1 电石渣的性质与检测•介绍电石渣的物理性质、化学成分以及活性特点•介绍电石渣的常用检测方法,如X射线衍射(XRD)、扫描电子显微镜(SEM)等4.2 电石渣与其他水泥原料的配比设计•分析电石渣与传统水泥原料的特点和相互作用•设计合理的电石渣与其他水泥原料的配比方案,以获得优良的水泥品质4.3 电石渣的加工处理•介绍电石渣的处理过程,如研磨、煅烧和冷却等•分析不同加工处理对电石渣活性的影响,以探索最佳加工工艺4.4 电石渣水泥的性能测试•介绍常用的水泥性能测试方法,如抗压强度、凝结时间、硫酸盐侵蚀等•对比分析电石渣水泥与传统水泥的性能差异,并评估其适用性5. 实验项目本课程将设计一系列与电石渣生产水泥工艺相关的实验项目,包括:•电石渣的物理化学性质测试•电石渣与其他水泥原料的配比设计实验•电石渣加工处理实验•电石渣水泥性能测试实验6. 课程评估学生将根据课程内容进行实验、报告撰写以及小组讨论等形式的评估。
评估内容将包括实验设计、数据分析、报告书写以及实验结果的评估等方面。
水泥预分解系统利用电石渣技术介绍
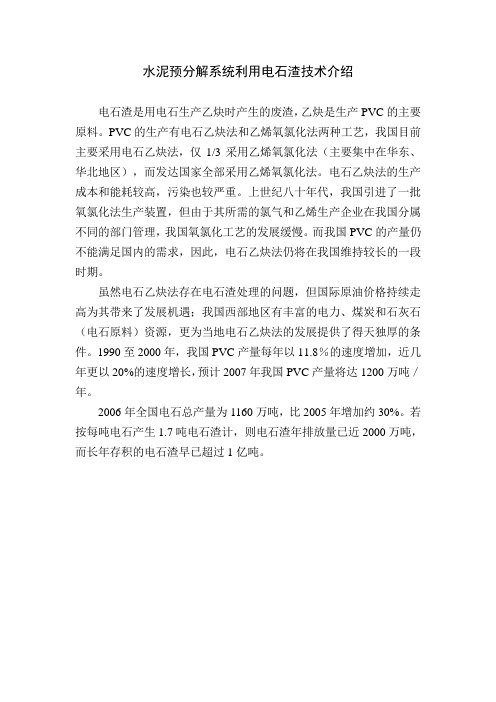
水泥预分解系统利用电石渣技术介绍电石渣是用电石生产乙炔时产生的废渣,乙炔是生产PVC的主要原料。
PVC的生产有电石乙炔法和乙烯氧氯化法两种工艺,我国目前主要采用电石乙炔法,仅1/3采用乙烯氧氯化法(主要集中在华东、华北地区),而发达国家全部采用乙烯氧氯化法。
电石乙炔法的生产成本和能耗较高,污染也较严重。
上世纪八十年代,我国引进了一批氧氯化法生产装置,但由于其所需的氯气和乙烯生产企业在我国分属不同的部门管理,我国氧氯化工艺的发展缓慢。
而我国PVC的产量仍不能满足国内的需求,因此,电石乙炔法仍将在我国维持较长的一段时期。
虽然电石乙炔法存在电石渣处理的问题,但国际原油价格持续走高为其带来了发展机遇;我国西部地区有丰富的电力、煤炭和石灰石(电石原料)资源,更为当地电石乙炔法的发展提供了得天独厚的条件。
1990至2000年,我国PVC产量每年以11.8%的速度增加,近几年更以20%的速度增长,预计2007年我国PVC产量将达1200万吨/年。
2006年全国电石总产量为1160万吨,比2005年增加约30%。
若按每吨电石产生1.7吨电石渣计,则电石渣年排放量已近2000万吨,而长年存积的电石渣早已超过1亿吨。
图4-41.电石渣性能研究电石是由石灰和焦碳用电弧法加热至2000℃~2200℃熔融制得的:2CaO+6C+O2=2 CaC2+2CO2电石水解时产生乙炔:CaC2+2H2O=C2H2+Ca(OH)2电石渣微量元素含量很低,所配生料的最低共溶点由1250℃提高至1300℃,可能熟料较难煅烧。
根据我们对某电石渣的热分析,分解温度380~520℃(吸热峰为475℃),比纯Ca(OH)2的低,电石渣所含杂质可能会降低其Ca(OH)2分解温度。
1.1松散密度用量筒测定了几个试样的松散密度,对比各试样的松散密度:电石渣为石灰石的51%,电石渣分解物为石灰石分解物的64%,电石渣生料分解物为普通生料分解物的85%。
电石渣水泥
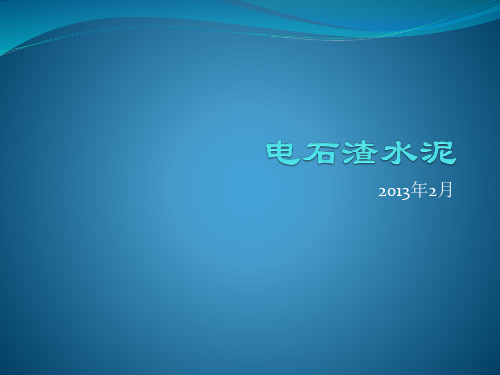
电石渣水泥简介
电石渣熟料:在水泥熟料生产过程中,用电石渣
( Ca(OH)2 )替代石灰石( CaCO₃ )配料,配合硅 质和铁质校正原料烧成后的熟料。
电石渣水泥:由电石渣熟料、混合材、石膏等配比磨
细制成的水硬性胶凝材料。
电石渣来源
电石渣:电石(CaC2)水解获取乙炔气后的以氢氧化
5、直接入磨干磨干烧新型干法
合肥水泥研究设计院开发的直接入磨干磨干烧新型干法 工艺,该工艺被应用于安徽皖维高新材料股份有限公司的2 号1000t/d水泥熟料生产线上,于2003年1月建成投产。含 水分80%的电石渣浆由XMZG300/1250厢式自动压滤机制成 水分小于35%的滤饼,然后由刮板输送机输送至进磨皮带, 窑尾废气作为烘干原料的主要热源,全部引入ML2619立式 辊磨机,出磨气体进入2-φ3.2m高效旋风分离器,分离后 物料输送至均化库均化,物料均化后计量后喂入C2旋风预 热器出口风管,由C3旋风预热器分离进入分解炉,然后由 C4旋风预热器分离入2-φ3.2mX52m回转窑煅烧成水泥熟料。 该工艺仍然需要消耗大量的热量来烘干原料当中的水分, 相比以上工艺较先进。
3、生产生石灰作为电石原料 前文提到美国肯塔基州路易斯维尔城炼气厂(AirReduction Plant),很 早意识到电石渣浆处理的紧迫性。在1948年建成日产60t生石灰试验装置。在 1959年至1962年建成二套330t/a生石灰生产装置。运行安全可*、年开工天数 近350天。 电石生产石灰工艺:脱水后得到含固量60%的电石废渣,用螺旋运输机输 送,在造粒机长度四分之三处均匀分配至造粒机内,造粒制成5~20mm大小 不等的园球,再经气流干燥炉(350℃)干燥,回转炉(900~1000℃)煅烧。 干燥炉内物料的干燥是利用回转炉内来的热废气干燥的。煅烧成的回收石灰 流入缷料斗,装车运送到电石厂作电石原料。 此方法技术路线可行,作为探索生产石灰,应是最好的治理方法,这是因 为:第一,生产石灰的投资不到生产水泥的十分之一;第二,石灰是电石生产的原 料,不存在另寻市场的问题,以钙为载体实现电石废渣—石灰—电石—电石废渣 这样的闭路循环;第三,减少制约自身的因素,电石法PVC可将规模进一步扩大, 以提高竞争力,同时也保护了石灰石矿源,新的电石废渣制石灰所产生的经济效 益和社会效益远非其他治理方法可比。 但能耗大,回收石灰重作电石原料也只能掺入电石原料的20%,不宜过 多,因为回收石灰中含硫、磷杂质多,将影响电石质量。
电石渣
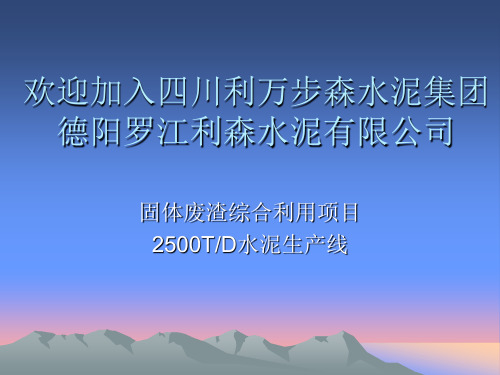
• 一般在线式管道分解炉头尾煤大致比例为 40%:60%,但电石渣水泥新型干法线我 估计大约为1:1(以电厂渣100%代替石灰 石计算)。同理窑用风与炉用风比例也发 生了变化。所以在生产调试中不能套用传 统新型干法水泥生产线的操作参数。另外 在生产中,根据峨眉山市水泥厂用电石渣 配料的经验,当电石渣用量达到生料的 20%时,即感觉尾煤用量下降,头煤比例 明显增大,同时产生的情况是第三级旋风 筒锥体容易堵塞。
• 管道分解炉下锥体三次风进风口不是按蜗 壳形状设计制作安装,在高温和高速料流 冲刷下,损坏漏风严重,影响煅烧。改进 措施:改进设计,按要求现场进行制作整 改。
• 由于对干电石渣的容重没有足够的了解, 系统按普通生料容重配置输送设备,造成 其能力严重不足。改进措施:对相关提升 机、空气斜槽、拉运机进行更换。
• 在熟料配料方案的选择上,由于电石渣 CaO%较高,配料方案选择的余地比较大。 作为新型干法水泥生产,烧成上容易控制,
建议采用高硅率配方: KH0.91±0.02,n3.0±0.01,P1.5±0.01,Fe2 O33.0左右。这种配方的优点是熟料结粒细 小均齐,不易结圈起块,冷却效果好;强 度高,水化热低;与水泥外加剂相容好。
象条件影响 。南方雨水量大,蒸发量小,含水量 高(一般在50%~60%),呈厚浆状。根本无法 挖掘和利用。 • 生产生石灰作为电石原料 :技术路线可行,但能 耗大,回收石灰中作电石原料也只能掺入电石原 料的20%,不宜过多,因为回收石灰中含硫、磷 杂质多,将影响电石质量。
电石废渣的处理方法
• 生产轻质砖 :该砖应用广,既作到了电石 废渣的综合利用,提高了经济效益,变废 为宝,也保护了环境。但是电石废渣作为 钙质原料加入,其加入量有限(≤15%~35 %), 难以消化完全。电石废渣:水泥:碎石: 煤渣=3.2:1.1:3.2:2.5 。
电石渣水泥项目产业政策
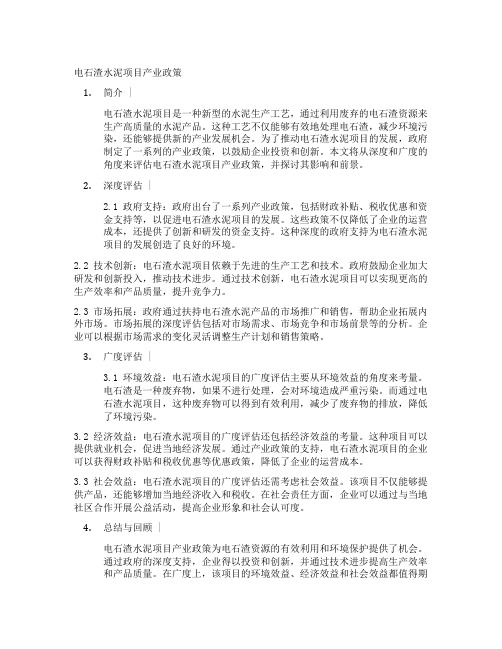
电石渣水泥项目产业政策1.简介 |电石渣水泥项目是一种新型的水泥生产工艺,通过利用废弃的电石渣资源来生产高质量的水泥产品。
这种工艺不仅能够有效地处理电石渣,减少环境污染,还能够提供新的产业发展机会。
为了推动电石渣水泥项目的发展,政府制定了一系列的产业政策,以鼓励企业投资和创新。
本文将从深度和广度的角度来评估电石渣水泥项目产业政策,并探讨其影响和前景。
2.深度评估 |2.1 政府支持:政府出台了一系列产业政策,包括财政补贴、税收优惠和资金支持等,以促进电石渣水泥项目的发展。
这些政策不仅降低了企业的运营成本,还提供了创新和研发的资金支持。
这种深度的政府支持为电石渣水泥项目的发展创造了良好的环境。
2.2 技术创新:电石渣水泥项目依赖于先进的生产工艺和技术。
政府鼓励企业加大研发和创新投入,推动技术进步。
通过技术创新,电石渣水泥项目可以实现更高的生产效率和产品质量,提升竞争力。
2.3 市场拓展:政府通过扶持电石渣水泥产品的市场推广和销售,帮助企业拓展内外市场。
市场拓展的深度评估包括对市场需求、市场竞争和市场前景等的分析。
企业可以根据市场需求的变化灵活调整生产计划和销售策略。
3.广度评估 |3.1 环境效益:电石渣水泥项目的广度评估主要从环境效益的角度来考量。
电石渣是一种废弃物,如果不进行处理,会对环境造成严重污染。
而通过电石渣水泥项目,这种废弃物可以得到有效利用,减少了废弃物的排放,降低了环境污染。
3.2 经济效益:电石渣水泥项目的广度评估还包括经济效益的考量。
这种项目可以提供就业机会,促进当地经济发展。
通过产业政策的支持,电石渣水泥项目的企业可以获得财政补贴和税收优惠等优惠政策,降低了企业的运营成本。
3.3 社会效益:电石渣水泥项目的广度评估还需考虑社会效益。
该项目不仅能够提供产品,还能够增加当地经济收入和税收。
在社会责任方面,企业可以通过与当地社区合作开展公益活动,提高企业形象和社会认可度。
4.总结与回顾 |电石渣水泥项目产业政策为电石渣资源的有效利用和环境保护提供了机会。
利用废弃的电石渣、粉煤灰制成水泥

,
月 上 旬 在 兰 州 通 过 有 关 部 门组 织 的 鉴 定
, ,
据 专家 的 透
, 、 。
地 处 兰 州 市红 古 区 的 兰 州 水 泥 厂 与 兰 州 维 尼 纶 厂 盐 锅 峡化 工 厂 等企 业 相 毗邻 而 这 些 企 业 分 别 在 生 产 过 程 中 排 放 出 各 种废 弃 物 如
年 第
期
建 材 工业信息
芝
中 彝 毫 冷 乌合 司物 爵 教 载霭 通通 选 脸收
中 国 高 岭 上 公 司 阳 西 竖 井 三 期 技 改工程 日 前 竣 工 经 中 国 非 金 属 矿 总 公 司 和 江 苏省 建 材 局 组 织 专 家验 收 形成年 开采 能力 1 0 万
卜
, ,
以 内涵 为 主 的扩大再 生 产 近几年 狠抓 了 桃 园 阳 西 和 沙墩 头 等矿井 的技术 改造
甘肃 省 兰 州 水 泥 厂 利 用 各 地废 弃的 粉煤 灰
和 废 石渣 生 产混合 硅 酸盐 于
9
,
粉 煤 灰 制 成 水 泥
健 康 生 活 环境均 有 影 响
, ,
、 。
利 用 废 弃的 电石 渣
,
、
425”
、
525”
.
水泥 并
。
粉 煤 灰 制 水 泥 化废 为 利 减少 环 境污 染 且 能 增 加 可 观 的 经 济效 益 一 举 数 得
。
,
、
桃 园矿 已 于
、
t
以
去年建成 年产
8 m 中段 生 产 9
,
7
,
万
t
能力 阳 西矿 井 一 二期 工
,
电石渣主要成分
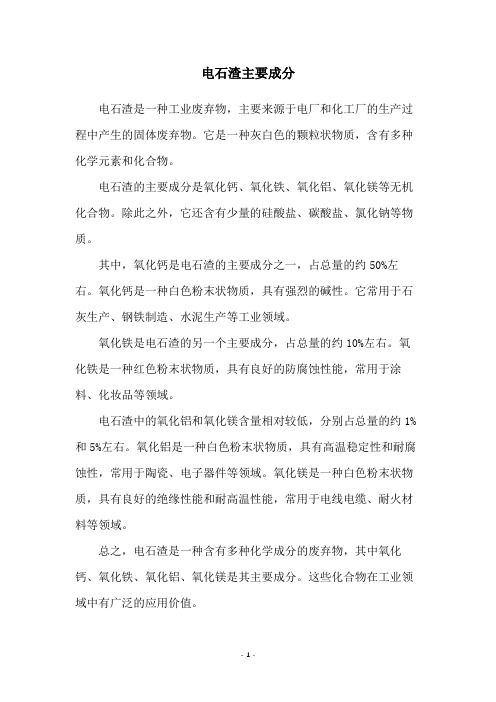
电石渣主要成分
电石渣是一种工业废弃物,主要来源于电厂和化工厂的生产过程中产生的固体废弃物。
它是一种灰白色的颗粒状物质,含有多种化学元素和化合物。
电石渣的主要成分是氧化钙、氧化铁、氧化铝、氧化镁等无机化合物。
除此之外,它还含有少量的硅酸盐、碳酸盐、氯化钠等物质。
其中,氧化钙是电石渣的主要成分之一,占总量的约50%左右。
氧化钙是一种白色粉末状物质,具有强烈的碱性。
它常用于石灰生产、钢铁制造、水泥生产等工业领域。
氧化铁是电石渣的另一个主要成分,占总量的约10%左右。
氧化铁是一种红色粉末状物质,具有良好的防腐蚀性能,常用于涂料、化妆品等领域。
电石渣中的氧化铝和氧化镁含量相对较低,分别占总量的约1%和5%左右。
氧化铝是一种白色粉末状物质,具有高温稳定性和耐腐蚀性,常用于陶瓷、电子器件等领域。
氧化镁是一种白色粉末状物质,具有良好的绝缘性能和耐高温性能,常用于电线电缆、耐火材料等领域。
总之,电石渣是一种含有多种化学成分的废弃物,其中氧化钙、氧化铁、氧化铝、氧化镁是其主要成分。
这些化合物在工业领域中有广泛的应用价值。
- 1 -。
电石渣
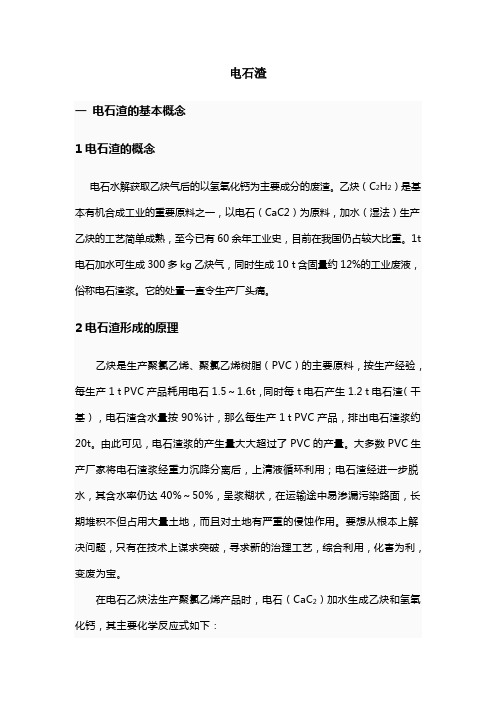
电石渣一电石渣的基本概念1电石渣的概念电石水解获取乙炔气后的以氢氧化钙为主要成分的废渣。
乙炔(C2H2)是基本有机合成工业的重要原料之一,以电石(CaC2)为原料,加水(湿法)生产乙炔的工艺简单成熟,至今已有60余年工业史,目前在我国仍占较大比重。
1t电石加水可生成300多kg乙炔气,同时生成10 t含固量约12%的工业废液,俗称电石渣浆。
它的处臵一直令生产厂头痛。
2电石渣形成的原理乙炔是生产聚氯乙烯、聚氯乙烯树脂(PVC)的主要原料,按生产经验,每生产1 t PVC产品耗用电石1.5~1.6t,同时每t电石产生1.2 t电石渣(干基),电石渣含水量按90%计,那么每生产1 t PVC产品,排出电石渣浆约20t。
由此可见,电石渣浆的产生量大大超过了PVC的产量。
大多数PVC 生产厂家将电石渣浆经重力沉降分离后,上清液循环利用;电石渣经进一步脱水,其含水率仍达40%~50%,呈浆糊状,在运输途中易渗漏污染路面,长期堆积不但占用大量土地,而且对土地有严重的侵蚀作用。
要想从根本上解决问题,只有在技术上谋求突破,寻求新的治理工艺,综合利用,化害为利,变废为宝。
在电石乙炔法生产聚氯乙烯产品时,电石(CaC2)加水生成乙炔和氢氧化钙,其主要化学反应式如下:CaC2+2H2O→C2H2+ Ca(OH)2+127.3 KJ/克分子在电石和水反应同时,电石中杂质也参与反应生成氢氧化钙和其他气体:CaO+H2O→Ca(OH)2CaS+2H2O→Ca(OH)2+H2S↑Ca3N2+6H2O→3Ca(OH)2+2NH3↑Ca3P2+6H2O→3Ca(OH)2 +2PH3↑Ca2Si+4H2O→2Ca(OH)2 + SiH4↑Ca3As2+ 6H2O→3Ca(OH)2 + 2AsH3↑Ca(OH)2在水中溶解度小,固体Ca(OH)2微粒逐步从溶液中析出。
整个体系由真溶液向胶体溶液、粗分散体系过渡,微粒子逐步合并、聚结、沉淀,在沉淀过程中又因粒子互相碰撞、挤压,促使颗粒进一步结聚、长大、失水,沉淀物逐步变稠,俗称电石渣浆。
电石渣配料生产水泥熟料新工艺的开发与应用

电石渣配料生产水泥熟料新工艺的开发与应用1 概述电石渣是在乙炔气、聚氯乙烯、聚乙烯醇等工业产品生产过程中,电石(CaC2)水解后产生的沉淀物(工业废渣),主要成分为Ca(OH)2。
CaC2(电石)+2H2O→C2H2↑(乙炔气)+Ca(OH)2↓(电石渣)每吨电石水解后约可产生1.15吨电石渣(干料),电石渣的堆放不仅占用大量的土地,而且因电石渣易于流失扩散,会污染堆放场地附近的水资源、碱化土地;长时间堆放还可能因风干起灰,污染周边环境。
电石渣属难以处理的工业废弃物之一。
上世纪七十年代,我国就开始将电石渣用作生产水泥熟料的原料之一。
当时,电石渣配料主要采用湿法长窑工艺生产水泥熟料,后来电石渣配料又发展了立窑、半湿法料饼入窑、立波尔窑、五级旋风预热器窑等多种工艺生产水泥熟料,但这些生产工艺的技术经济指标相对落后,而且不符合国家的相关产业政策,不适宜广泛推广。
技术相对较先进的电石渣配料、“湿磨干烧”工艺生产新型干法水泥熟料,其熟料烧成热耗超过1000×4.18 kj/kg,这比同规模、采用通常原料配料生产新型干法水泥熟料高出近30%,即每吨熟料多耗标准煤约30kg。
以日产水泥熟料1000吨规模计算,全年多耗标准煤约9000吨。
采用电石渣配料、“湿磨干烧”工艺生产新型干法水泥熟料的主要生产工艺过程为:电石渣作为原料之一与其它原料配料后一起入湿法生料磨,磨成综合水分约为43%的生料浆,然后通过机械脱水装置将生料浆脱水成为含水分约25%的料饼,再将料饼送入利用窑尾废气余热烘干的料饼烘干破碎机;破碎、烘干后的物料随气流进入窑尾旋风分离器、两级旋风预热器、在线分解炉,最后进入回转窑煅烧成水泥熟料。
实践证明:电石渣配料、“湿磨干烧”工艺生产新型干法水泥熟料,技术上已较为先进、成熟,按该工艺建设并已运行四年半的1000t/d水泥熟料生产线主要缺点是:熟料烧成热耗较高,达1030×4.18 kj/kg。
电石渣特性

4、熟料形成热不同
电石渣在烘干、储存、预热过程中与烟气的接触时间较长,部分物料 生成CaCO3,新生态的CaO 会吸收CO2还原成CaCO3,它们的重新 分解影响熟料形成热。 电石渣的分解温度及分解反应热较低,电石渣配料的熟料形成热,比
普通生料低。随着电石渣掺量的增加,熟料的形成热会降低。通过计
算可以得出,若电石渣在烘干、储存、预热过程中20%的Ca(OH)2吸 收CO2生成CaCO3,由电石渣完全替代石灰石配料的熟料形成热比常
电石渣中Ca(OH)2的不稳定性
1)Ca(OH)2+CO2→CaCO3+H2O(g) (放热反应)常温~550 ℃ 2)Ca(OH)2 3)CaCO3
↔
CaO+H2O(g) (吸热反应)450~550 ℃
↔
CaO+CO2(g) (吸热反应)850~900 ℃
反应1)随着温度升高反应缓慢加速,300 ℃以上反应明显加速,450 ~550℃ 反应2)发生,550~850 ℃反应3)的逆反应发生,反应速度比较缓慢。
除电石渣生产水泥外,还可利用电石渣生产各种级别的轻质碳酸
钙,包括高质量轻质碳酸钙产品。利用废渣、废气生产高附加值 产品,不仅实现了节能、减排的循环经济理念,而且还在此过程 中,提升了产品价值。经过多年研究已掌握了大量的关键技术。
二、电石渣的来源
电石渣是电石法乙炔生产过程中电石水解反应的副产物。
化学反应式: CaC2+2H2O→C2H2+ Ca(OH)2+127.3 KJ/mol 电石渣化学组成:由于电石是由石灰和焦碳在还原气氛下经高 温熔融后制得,故电石渣除含90%以上的Ca(OH)2,其余成分 源于石灰和焦碳中带入的杂质,主要为:Si、Al、Fe、Mg的 氧化物,某些地区S含量偏高,若为氯碱化工生产厂排出的电
- 1、下载文档前请自行甄别文档内容的完整性,平台不提供额外的编辑、内容补充、找答案等附加服务。
- 2、"仅部分预览"的文档,不可在线预览部分如存在完整性等问题,可反馈申请退款(可完整预览的文档不适用该条件!)。
- 3、如文档侵犯您的权益,请联系客服反馈,我们会尽快为您处理(人工客服工作时间:9:00-18:30)。
湿磨干烧:安徽皖维高新材料股份有限公司1000t/d熟料生产线(1#),熟料烧成热耗高达1030大卡/kg干磨干烧:安徽皖维高新材料股份有限公司1000t/d熟料生产线(2#,合肥院设计),熟料烧成热耗高达816大卡/kg,缺点是生料中电石渣的掺量仅13%~15%(干基)。
国内首条1200t/d高掺电石渣干磨干烧新型干法水泥生产线,采用电石渣脱水、预烘干、立式磨、新型干法预分解窑煅烧等一系列节能环保综合技术,于2005年8月8日在淄博宝生环保建材有限公司一次点火成功并生产出合格熟料,目前系统阻力≤5000Pa,熟料热耗≤760×4.18KJ/kg(也有资料显示热耗高达1200×4.18KJ/kg),出预热器废气温度320~360℃,生料中电石渣掺量(干基)≥64%(电石渣替代石灰石量达到80%以上),实现了持续稳定生产,达到国内领先水平。
采用回转烘干机(直径3×25m)1、电石渣干排(水分含量3%~5%)和湿排(电石渣压滤后水分38%~45%)2、利用电石渣生产水泥的优势在于:(1)利用电石渣生产水泥比采用石灰石生产水泥熟料烧成热耗有所降低,如替代60%石灰石时,熟料烧成热耗约降低8%;替代80%石灰石时,熟料烧成热耗约降低15%。
(2)与带压滤半湿法回转窑生产工艺相比节煤46%,与湿磨干烧相比节煤20%,对于煤炭储采比不足百年的中国来说节能尤其重要,不能以处理电石渣而消耗大量能源为代价。
(3)由于带压滤半湿法回转窑和湿磨干烧生产工艺必须将其它组分加水粉磨成合格的料浆,每生产1吨熟料需要多消耗0.15吨水,带来水资源和能源的浪费。
(4)生产1吨熟料需要消耗1.28吨优质石灰石,同时向大气中排放0.57吨CO2,用电石渣替代石灰石生产水泥熟料,可以减轻我国石灰石资源不足和减少CO2排放;(5)随着煤化工行业科学技术的不断进步,生产过程中电石渣以干基(含水分10-12%)排放,将为新型干法生产工艺煅烧高掺量电石渣提供捷径。
3、据相关实验得知900℃以下时电石渣配料与常规生料的差异如下:(1)电石渣中Ca(OH)2分解温度与CaCO3不同。
电石渣中含有较多毛细水和结晶水,分解温度较低,电石渣中Ca(OH)2的分解温度约580℃左右,低于CaCO3的分解温度。
(2)Ca(OH)2分解吸热与CaCO3不同,前者分解吸热为1160kJ/kg,而后者为1660kJ/kg;(3)电石渣颗粒较细,脱水较早,在温度较高的旋风筒和分解炉锥部易产生堵塞,不利于连续稳定生产;(4)熟料形成热不同:电石渣在原料中占63.5%时所配生料的熟料形成热为1025kJ/kg,约为普通生料的熟料形成热的3/5。
因此电石渣配料生产水泥熟料时,必须充分考虑预热器、分解炉的结构;电石渣的掺入量越大,对预热器、分解炉的结构设计影响也越大。
“湿磨干烧”生产工艺主要过程:电石渣作为原料之一与其它原料配料后一起进入湿法生料磨,磨成综合水分约43%的生料浆,通过机械脱水装置(压滤机)将生料浆脱水成为含水分约25%的料饼,再将料饼送入利用窑尾废气余热烘干的料饼烘干破碎机;破碎、烘干后的物料随气流进入窑尾旋风分离器、两级旋风预热器、在线分解炉,最后进入回转窑煅烧。
安徽皖维高新材料股份有限公司1000t/d熟料生产线(1#),熟料烧成热耗高达1030大卡/kg;湿磨干烧一般选用锤式烘干破碎机,其具有较强的烘干破碎能力,特别是对水分含量高、软而非磨蚀性的原料效果明显。
“干磨干烧”生产工艺主要过程:电石渣经过机械脱水(压滤机)成为含水分约35%的电石渣料饼,然后与其它原料经配料一起入立式磨烘干、粉磨;出立式磨的生料粉经生料均化库均化后经窑尾预热器、分解炉,最后进入回转窑煅烧。
安徽皖维高新材料股份有限公司1000t/d熟料生产线(2#,合肥院设计),熟料烧成热耗高达816大卡/kg,缺点是生料中电石渣的掺量仅13%~15%(干基)。
4、问题:(1)电石渣烘干后废气浓度高,对收尘设备产生粘堵和腐蚀。
5、6、入磨物料综合水分为11%~14%原料易磨。
7、8、9、10、11、12、利用电石渣生产水泥的反思与展望作者:崔冬梅,肖其中,周宏建单位:合肥水泥研究设计院摘要:利用电石渣制水泥通常采用“干磨干烧”或“湿磨干烧”工艺,本文通过对两种工艺过程的对比分析,指出各自优缺点,作出评价;并对利用电石渣制水泥的工艺选择,提出一些个人看法与建议。
(2)电石渣的特性与水泥生产概况电石渣是电石法PVC的生产过程中,电石水解后产生的废渣。
电石渣的主要成分是Ca(OH)2,其化学成分CaO含量高达70%。
从乙炔发生器中排出的电石渣水分高达90%以上,经沉降池浓缩后,水分仍有75~80%,正常流动时的水分在50%以上。
电石渣容易造成环境污染,且难以治理,严重制约了电石法PVC工业的发展。
电石渣成分均匀,含钙量高,是优质的水泥原料,用来代替石灰石生产水泥是用量最大、利用也最为彻底的方法,解决了化工生产厂家的后顾之忧。
利用电石渣生产水泥通常采用“湿磨干烧”或预烘干“干磨干烧”工艺:山东淄博(1200t/d)采用“干磨干烧”工艺,在2005年成功运行1年后停产至今,四川德阳(1500t/d)、四川乐山(2500t/d)这2条生产线也采用“干磨干烧”工艺,并于2008年建成投产,但由于电石渣供应问题没有解决,电石渣的掺入量尚末达到设计要求;此外尚有多条采用“湿磨干烧”工艺的水泥生产线。
化工厂家通过调整工艺,可以使得新出厂电石渣中Cl-含量达到“干磨干烧”或“湿磨干烧”工艺的要求;而历年积累的电石渣大都存在Cl-超标的问题,只能通过少掺或采用湿法、立窑、中空窑煅烧工艺加以解决,不在本文讨论之列。
2008年,国家发展改革委办公厅印发《关于鼓励利用电石渣生产水泥有关问题的通知》,以下简称《通知》。
《通知》规定新建电石渣水泥生产线装置必须采用新型干法水泥生产工艺;现有电石渣水泥生产线可以采用“湿磨干烧”生产工艺进行改造[1]。
这个规定有些不妥。
(3)“干磨干烧”与“湿磨干烧”两种工艺过程的对比分析a)从原料水分的去除来看,机械脱水无疑是最经济的方式,所以不管是“湿磨干烧”还是“干磨干烧”,都先采用压滤机对原料进行脱水。
“湿磨干烧”是将生料浆进行压滤后送入破碎烘干机;“干磨干烧”则是先将电石渣浆压滤后再进行预烘干。
由于电石渣颗粒微细,分散度很高,具有多孔状结构,保水性极强,单独脱水的脱水率很低。
采用厢式压滤机脱水后,电石渣滤饼水分在35%左右。
而压滤生料浆时,由于其它易脱水原料的掺入,其保水性下降,生料滤饼的水分可降至27%。
以电石渣干基配比60%、其它原料平均含水率5%计算,“干磨干烧”工艺每吨干基生料带入水为0.6×35÷(100-35)+0.4×5÷(100-5)=0.344吨,带入水分的99%在预烘干和生料粉磨两个阶段内蒸发;“湿磨干烧”则为27÷(100-27)=0.370吨,主要在破碎烘干机内蒸发。
由此可见在后续工序利用热能脱水时,“湿磨干烧”比“干磨干烧”多出0.026吨水。
利用热能脱水往往是迫不得已才采用的方式,在这一点上,“干磨干烧”略占优势,“湿磨干烧”最为人所诟病的就是除电石渣外的原料要先加水再脱水,其结果是蒸发水量仅仅多出7%。
b)预烘干“干磨干烧”工艺选用回转式烘干机对压滤过的电石渣滤饼进行预烘干,使其水分由35%降至10%左右,这部分烘干热耗达1000kJ/kg-cl,加上烧成热耗3100kJ/kg-cl,合计熟料热耗高达4100kJ/kg-cl,与“湿磨干烧”工艺相当,节煤效果并不显著。
另外还有一个现象:电石渣滤饼在回转式烘干机内翻滚后,逐渐密实并形成球状,获得一定的强度,需要重新破碎,同“湿磨干烧”先加水再脱水一样,有违反工艺路线之嫌。
c)电石渣成分均匀,只须烘干便可成为优质的水泥钙质原料,现预烘干“干磨干烧”工艺采用立磨对配合料进行最终的烘干兼粉磨,生料产量为75t/h时,立磨本身装机功率为575kW,加上立磨风机900kW,主机功率达1475kW。
而在原料中需要粉磨的硅铝质、铁质及其它钙质原料仅占40%,即在30t/h左右,若选用球磨机对这部分物料进行粉磨,则只须选用一台Ф2.4×10m中卸烘干磨便完全可以满足要求,其主机功率仅为570kW。
两种方案主机功率差别竟达905kW,产量为45t/h,初水分为10%的粉料的烘干、混合要占用905kW的装机功率,可见采用立磨粉磨以电石渣为主的原料并不节电。
随着煤化工行业科学技术的不断进步,电石渣干排技术日益成熟,这为新型干法生产水泥提供了捷径,利用立磨粉磨电石渣生料浪费电能的缺陷将更为突出。
“湿磨干烧”采用破碎烘干机对压滤过的生料滤饼进行烘干、破碎,在获得相同生料的情况下,它的主机装机功率为450kW,加上湿法开流磨750kW,合计为1200kW,低于“干磨干烧”。
(“湿磨干烧”要多用四台压滤机,主机功率为4×5.5kW;“干磨干烧”则需另加两台烘干机,主机功率为2×110kW,均末计入)。
在电耗方面,“湿磨干烧”有优势。
(4)对“干磨干烧”与“湿磨干烧”两种工艺的评价a)通过上述对比可以发现:在电石渣掺量较大时,“湿磨干烧”工艺的电耗、投资指标均优于“干磨干烧”;其蒸发水量高于“干磨干烧”7%,热耗却不相上下,此中原因出在电石渣预烘干环节。
从能量守恒的角度来看:水分蒸发的过程就是吸热的过程,降低热耗的途径有两个,一是降低物料水分,二是提高热交换效率。
机械脱水是最经济的方式,它的能力要尽力发挥,在它的能力达到极限之后,就只能在提高热交换效率上多做工作了。
回转式烘干机在烘干电石渣滤饼时,其效率显然没有在悬浮状态下效率高。
回转式烘干机与破碎烘干机热效率的差异,在热耗上得到了极好的体现。
在传统水泥生产中,对于大宗湿物料,20年前水泥界就有共识:当原料水分超过10%或粘性过大时,均应排除干法工艺,否则物料烘干热耗将超过干法生产所能节省的热耗。
这个10%即是生料磨所能烘干原料的水分极限,现在普遍采用立式磨,这个数据可提高至12~14%。
例如:我国两个设计院在对峨眉水泥厂扩建年产70万吨新生产线的可行性研究中,就曾用全干法烘干工艺与“湿磨干烧”工艺进行对比,在分析中发现:全干法生产每年在熟料烧成热耗上虽比“湿磨干烧”节约标煤7052t,但原料的烘干热耗增加标煤9619t,水泥综合电耗又增加标煤2580t,使其综合能耗高于“湿磨干烧”方案5147t标煤,再加之干法投资高于“湿磨干烧”,其最优方案应选择“湿磨干烧”[2]可见,仅因“湿磨干烧”熟料烧成热耗指标高于全干法,就认为“湿磨干烧”属于中间技术,不宜于广泛采用是不科学的。