旋窑中控操作主要参数
窑炉中控控温操作规程

窑炉中控控温操作规程1. 引言窑炉控温是在窑炉生产过程中对温度进行控制的关键环节。
合理的控温操作能够提高生产效率,保证产品质量。
本文档旨在规范窑炉中控控温操作,确保操作人员能够正确、安全地进行控温操作。
2. 控温设备窑炉中控控温操作一般需要以下设备:•温度传感器:用于测量窑炉内部温度。
•控制系统:用于接收温度传感器的信号,并发送控制信号给窑炉设备。
•人机交互界面:用于操作人员与控制系统进行交互。
3. 控温操作流程3.1. 准备工作在进行控温操作之前,操作人员需要进行以下准备工作:1.检查温度传感器的工作状态,确保传感器正常。
2.检查控制系统的工作状态,确保系统正常。
3.确认窑炉内无人员,并做好安全措施。
3.2. 设置控温参数1.启动控制系统,并进入控温操作界面。
2.根据生产需求和产品要求,设置控温参数,包括目标温度、温度波动范围等。
3.确认参数设置无误后,保存设置并开始控温操作。
3.3. 监测温度变化1.实时监测窑炉内部温度的变化情况。
2.若温度超出了设定的温度波动范围,需要及时采取措施进行调整。
3.4. 温度调整1.当窑炉温度超出目标温度时,根据情况进行温度调整。
2.若温度过高,可以通过增加风量、减少燃料供应等方式进行降温。
3.若温度过低,可以通过减少风量、增加燃料供应等方式进行升温。
3.5. 记录与报告1.在控温操作过程中,操作人员需要记录关键信息,如温度变化、调整措施等。
2.在控温操作完成后,需要整理记录,编写控温报告,并提交给相关部门。
4. 安全注意事项1.在进行控温操作时,严禁随意触碰窑炉设备以及与之相关的电气装置。
2.当窑炉温度异常升高时,应立即停止操作,并及时报告相关人员。
3.在窑炉运行时,不得离开岗位,以防发生意外。
5. 操作规范1.操作人员应经过专业培训,并持有相关资格证书。
2.窑炉控温操作应按照相关标准和规程进行,不得擅自更改控温参数。
3.操作人员需定期维护和保养控温设备,确保设备的正常工作。
窑系统中控操作规程资料

窑系统中控操作规程文件编号:修订状态:颁发日期:实施日期:受控状态:受控发放编号:XXXX水泥有限公司1 目的本规程旨在树立安全第一的观点,统一操作思想,生产合格熟料,实现环保设备稳定达标排放,力求达到优质、稳产、高产、低耗的目的。
2 范围本规程适用于烧成中控操作,即从高温排风机至熟料库顶。
3 指导思想3.1树立安全生产、质量第一的观念,整定出系统最佳操作参数,确保窑长期安全运转及优质高产、低消耗;3.2树立全局观念,与原料系统、煤磨系统、生产品位处互相协调,密切配合;3.3统一操作思想,精心操作,不断摸索总结,达到系统稳定的目的;3.4力求系统热工制度稳定,注意风、料、煤、窑速的配合以消除热工波动;3.5确保燃料完全燃烧,避免CO产生和系统局部高温,防止预热器各旋风筒、TTF型分解炉、窑尾烟室等结皮、堵塞,同时保护窑皮和窑衬,延长窑系统的运转周期;3.6正确调整篦冷机篦床速度和各室风量,防止堆“雪人”。
4 窑系统工艺流程简介4.1 生料入窑部分库底罗茨风机(13/14.17)充气,卸出生料经手动闸板阀(13/14.11)、气动流量控制阀(13/14.12)后由斜槽(13/14.13)送入计量仓(13/14.28)。
生产时,由计量仓内物料重量控制库底气动流量控制阀(13/14.12)开度,维持计量仓料位,为仓下稳定出料提供先决条件。
计量仓下设有三套卸料装置(其中一套为一、二线互相备用)和一台固体流量计和一台入窑生料计量系统,喂料仓下流量控制阀根据入窑生料量调节。
有两出料装置上都配有一台手动闸板阀(13/14.29)、气动流量控制阀(13/14.30),计量仓及其卸料装置由罗茨风机(13/14.17)充气卸料,生料由计量仓通过卸料装置卸出后由斜槽(13/14.06)送至斗式提升机(15c.01)后经空气输送斜槽(15c.02)、电动分料阀(15c.02-1)、回转锁风下料器(15c.04)直接送入窑尾预热器。
窑中控作业指导书

目录1.总则2.工艺流程简介3.职责与权限4.操作规程4.1.点火前的准备4.2.升温投料操作4.3.运行中的监控4.3.1.操作指导思想4.3.2.操作的关键参数及其范围4.3.3.操作中的调节参数4.3.4.窑操作中的控制4.3.5.紧急情况的处理4.4.停窑操作5.安全注意事项安全6.交接班制度7.考察与考核1总则1.1本规程规定了窑操作员的职责范围,工作内容与要求,操作及注意事项,交接班制度以及考核办法。
1.2本规程仅适用于中控室窑操作员.2工艺流程简介当窑、磨正常运行时,来自生料磨的生料及窑尾废气处理收尘下来的料粉经入库提升机、六嘴分料器,不间断地输送入规格为Φ15×45的生料均化库,在库内进行重力及气力均化。
均化库底采用固体冲板流量计对入窑生料进行计量。
生料经斗式提升机送入窑尾预热器内,生料均化库的有效储量5800t,储存期1.1天。
窑尾系统由五级旋风筒和连接旋风筒的联接管道、卸料管以及分解炉构成。
生料粉经计量后由提升机送入二级旋风筒气体出口管道,在气流作用下立即分散、悬浮在气流中,并进入一级旋风筒。
气料分离后,料粉通过重锤翻板阀转到三级旋风筒气体出口管道,并随气流进入二级旋风筒。
这样经过四级热交换后,生料粉得到了充分预热,然后物料进入分解炉内。
来自窑头罩的三次风、窑尾热风为分解炉提供氧气使煤粉燃烧,生料与燃烧后的高温气体进行热交换,其碳酸钙得以充分分解。
预分解后的生料,随气流进入五级旋风筒,经分离后喂入窑内;而废气沿着逐级旋风筒及气体出口管道上升,最后由一级旋风筒出风管排出,经高温风机和增湿塔送往原料粉磨和废气处理系统。
预热分解的料粉喂入窑尾烟室,并借助窑的斜度和旋转、慢慢地向窑头运动,发生一系列物理、化学反应,形成高温熟料。
煅烧后的高温熟料通过窑头罩进入篦冷机冷却。
出窑熟料温度为1350℃,冷却后的出冷却机熟料温度可降至100℃以下。
熟料通过篦冷机活动推板的往复推动,进入冷却机尾部的锤式破碎机,经打碎后落到熟料链斗输送机上,送入熟料库内。
中控室窑操作员作业指导书

中控室窑操作员作业指导书1质量要求1.熟料f-c a o≤1.5%,合格率≥85%。
2.熟料立升重1100±75/L,合格率≥85%。
3.熟料三天强度≥28M p a,二十八天强度≥56M p a,合格率≥90%。
2工艺要求2.1窑头火焰活泼有力,但不扫窑皮。
2.2系统不漏风、不漏料、不喷尘。
2.3窑系统热工稳定,风煤料合理分配,窑炉燃烧比例控制在4:6左右。
2.4入窑物料表现分解率≥90%3作业程序3.1开停车顺序:开机顺序:窑中稀油站——窑头一次风机——点火油泵——窑头喷煤罗茨风机——窑头喂煤称——熟料输送系统——窑头袋收尘系统——冷却机干油泵——破碎机——冷却机——组风机——高温风机稀油站及液力耦合器加油站——窑主电机——高温风机——喂料系统——均化库底充气系统——均化库卸料电磁阀——窑尾一次风机——分解喂煤称——冷却机一、二、三段传动——冷却机二、三组风机。
停机顺序:止料、止分解炉喂煤后的顺序基本相反,但冷却机风机、窑头袋收尘排风机、窑头、窑尾一次风机、高温风机视冷却情况,燃烧器冷却情况而定。
3.2点火操作:3.2.1通知现场巡检工关闭和密封好所有的检查门,检查确认各旋风筒的下料管通畅、翻板阀灵活并将其吊起,测试各空气炮是否正常。
3.2.2检查各机组是否有备妥,确认各设备可正常投入使用。
3.2.3检查窑头点火燃油系统,通知巡检将油嘴清洗干净,油罐油量80%,将油枪架好,进油、回油管接好。
3.2.4煤粉仓要有足够的煤粉储备,够窑、炉升温和投料用(50吨左右)3.2.5启动喂料机组进行倒库,同时检查要喂料输送设备是否正常。
3.2.6启动测试冷却机及熟料输送系统,运行30分钟无异常后停机。
3.2.7启动窑的润滑、冷却系统、检查窑齿轮、托轮的润滑情况,试启动窑主电机(0.6转|分钟)3.2.8启动测试喂料系统及窑头一次风机。
3.2.9做好点火前的准备后,按照指令点火烘窑。
3.2.10启动窑头一次风机,给定适量转速。
窑系统中控作业指导书
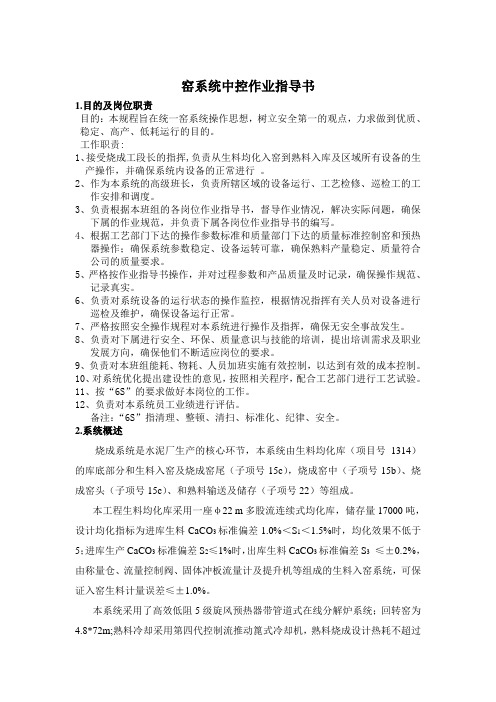
窑系统中控作业指导书1.目的及岗位职责目的:本规程旨在统一窑系统操作思想,树立安全第一的观点,力求做到优质、稳定、高产、低耗运行的目的。
工作职责:1、接受烧成工段长的指挥,负责从生料均化入窑到熟料入库及区域所有设备的生产操作,并确保系统内设备的正常进行。
2、作为本系统的高级班长,负责所辖区域的设备运行、工艺检修、巡检工的工作安排和调度。
3、负责根据本班组的各岗位作业指导书,督导作业情况,解决实际问题,确保下属的作业规范,并负责下属各岗位作业指导书的编写。
4、根据工艺部门下达的操作参数标准和质量部门下达的质量标准控制窑和预热器操作;确保系统参数稳定、设备运转可靠,确保熟料产量稳定、质量符合公司的质量要求。
5、严格按作业指导书操作,并对过程参数和产品质量及时记录,确保操作规范、记录真实。
6、负责对系统设备的运行状态的操作监控,根据情况指挥有关人员对设备进行巡检及维护,确保设备运行正常。
7、严格按照安全操作规程对本系统进行操作及指挥,确保无安全事故发生。
8、负责对下属进行安全、环保、质量意识与技能的培训,提出培训需求及职业发展方向,确保他们不断适应岗位的要求。
9、负责对本班组能耗、物耗、人员加班实施有效控制,以达到有效的成本控制。
10、对系统优化提出建设性的意见,按照相关程序,配合工艺部门进行工艺试验。
11、按“6S”的要求做好本岗位的工作。
12、负责对本系统员工业绩进行评估。
备注:“6S”指清理、整顿、清扫、标准化、纪律、安全。
2.系统概述烧成系统是水泥厂生产的核心环节,本系统由生料均化库(项目号1314)的库底部分和生料入窑及烧成窑尾(子项号15c),烧成窑中(子项号15b)、烧成窑头(子项号15c)、和熟料输送及储存(子项号22)等组成。
本工程生料均化库采用一座φ22 m多股流连续式均化库,储存量17000吨,设计均化指标为进库生料CaCO3标准偏差1.0%<S1<1.5%时,均化效果不低于5;进库生产CaCO3标准偏差S2≤1%时,出库生料CaCO3标准偏差S3≤±0.2%,由称量仓、流量控制阀、固体冲板流量计及提升机等组成的生料入窑系统,可保证入窑生料计量误差≤±1.0%。
窑的正常操作控制
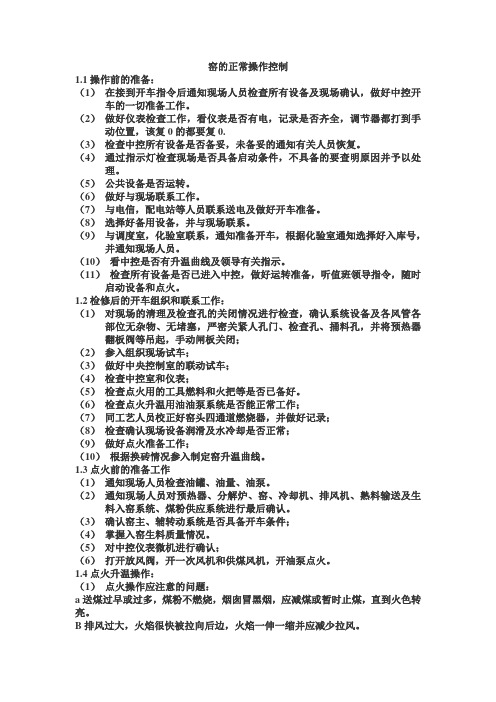
窑的正常操作控制1.1操作前的准备:(1)在接到开车指令后通知现场人员检查所有设备及现场确认,做好中控开车的一切准备工作。
(2)做好仪表检查工作,看仪表是否有电,记录是否齐全,调节器都打到手动位置,该复0的都要复0.(3)检查中控所有设备是否备妥,未备妥的通知有关人员恢复。
(4)通过指示灯检查现场是否具备启动条件,不具备的要查明原因并予以处理。
(5)公共设备是否运转。
(6)做好与现场联系工作。
(7)与电信,配电站等人员联系送电及做好开车准备。
(8)选择好备用设备,并与现场联系。
(9)与调度室,化验室联系,通知准备开车,根据化验室通知选择好入库号,并通知现场人员。
(10)看中控是否有升温曲线及领导有关指示。
(11)检查所有设备是否已进入中控,做好运转准备,听值班领导指令,随时启动设备和点火。
1.2检修后的开车组织和联系工作:(1)对现场的清理及检查孔的关闭情况进行检查,确认系统设备及各风管各部位无杂物、无堵塞,严密关紧人孔门、检查孔、捅料孔,并将预热器翻板阀等吊起,手动闸板关闭;(2)参入组织现场试车;(3)做好中央控制室的联动试车;(4)检查中控室和仪表;(5)检查点火用的工具燃料和火把等是否已备好。
(6)检查点火升温用油油泵系统是否能正常工作;(7)同工艺人员校正好窑头四通道燃烧器,并做好记录;(8)检查确认现场设备润滑及水冷却是否正常;(9)做好点火准备工作;(10)根据换砖情况参入制定窑升温曲线。
1.3点火前的准备工作(1)通知现场人员检查油罐、油量、油泵。
(2)通知现场人员对预热器、分解炉、窑、冷却机、排风机、熟料输送及生料入窑系统、煤粉供应系统进行最后确认。
(3)确认窑主、辅转动系统是否具备开车条件;(4)掌握入窑生料质量情况。
(5)对中控仪表微机进行确认;(6)打开放风阀,开一次风机和供煤风机,开油泵点火。
1.4点火升温操作:(1)点火操作应注意的问题:a送煤过早或过多,煤粉不燃烧,烟囱冒黑烟,应减煤或暂时止煤,直到火色转亮。
旋窑窑操的基础知识

旋窑窑操的基础知识水泥人缘,2007-07-06 20:31:05烧手训练教材一. 熟料组成对烧成之effect.1. 烧成条件:氧化气氛→黑色熟料(是)→黄色熟料(否)2.烧成影饷主要因素:原料化学组成,矿物组成,物理性质(颗粒大小,均匀度).3.窑operatcon, o2/co, cooler 为第一阶段控制, 加减煤,加减料,窑KW, pyroclon 控制, clinker FL 控制之effect, SM,ZM,LSF 对烧成之effect.二. 熟料形成.1. 熟料开始的组成:分解石(CaCO3)石英(SiO2)黏土(SiO2 M2O3 H2O)铁粉(Fe2O3)2. 熟料形成之过程:熟料形成期间可发生之反应以如下温度范围来概述之.200℃以下生料中游离水干燥100〜400℃粘土中结晶水遗失400〜900℃黏土分解成Al2O3+SiO2550〜900℃生料→CaO+CO2>800℃ CA固态反应>850℃ aluminate>830℃ C2S(至1200℃时,完全生成)烧成反应>1260℃出现夜体(溶融物)━1450℃时夜体含量达20〜30%,视化学组成而定,SM↑夜体含量高↑━1260℃烧成反应开始,料中主要含固体C2S,游离CaO及夜体,固体在夜体中形成溶液,使扩散反应加速,C2S+CaO→C3S.C3S是水泥中的主要矿物.>1400℃液体组成,几乎生料中所有之Al2O3+Fe2O3皆在液体中了,CaO 56%, SiO2 7%, Al2O323%, Fe2O3 14%.冷却期间液体熔融物结晶成C3A及C4AF.3.烧成后的熟料矿物组成(具有水硬性)鲑酸三钙C3S━3CaO•SiO2鲑酸二钙C2S━2CaO•SiO2铝酸三钙C3A━3CaO•Al2O3铁铝酸四钙C4AF━4CaO•Al2O3•Fe2O3它们的生成量视温度,滞留时间,冷却速度而定.三. 窑.1. 窑中各带之长度.分解带过渡带烧成带冷却带L/D━14〜17 3〜4D 5D 5〜5.5D 1.5DL/D━10〜11 1.5〜2D 4.5D 3.5〜4D 1D物料停留时间2" 6" 10"2"━20"2.短窑脱酸度,应该保持90〜95%,避免窑内废气温度过高造成进料室及C4下料筛结皮堵塞.脱酸度超标会造成窑内温度分布碆动,引起结圈,结皮.而且,将缩短分解带长度,使过渡带长度过长,窑速上不去,形成懒火焰烧成,失去快速锻烧之优势,产量,品质无法达标.3.熟料中MgO为2%时,熟料烧成温度降50℃,熟料中鰔及硫也会降低.>1260℃时,应该让绝大部份液相生成,以补快速锻烧.4.短窑采用快速锻烧,烧成带相对较短,火焰温度较高,但较短.故熟料粉形成温度要高,原料必须能“吃火”.5.RF:(1).Labahn,otto. and B. Kohihaas cement Engineers´Handbook.Bauverlag Gmbh Wiesbaden and Berlin.4 th ed.1983.(2).H.F.W.Tsylor.Cement chemistry. Academil Prem Ltd.1990.(3).Peray,Kurt E.THE Rotary Cement Kiln, 2nd ed. Ch-emical Publishing 1986 N.F.6.影响预锻窑产量和品质的因素友有许多,如:操作水平,原料及燃料品质,生料成份及预均化程度.生料LSF高,窑内物料松散,不易燃烧及结窑皮,熟料f-CaO高,使须提高温度,降低窑速及产量.生料LSF低,窑内物料紧贴,易形成长厚窑皮,窑皮和结大球使窑的操作状态恶化.所以保持生料的均衡稳定是保持旋窑易燃烧平衡的关键.SM低的生料,熔剂性矿的总量增加,即物料的夜体量增加,易造成窑内结圈结球,使窑内操作恶化,破坏热平衡.采用SM(2.50+_0.10),ZM(1.50+_0.10),LSF(91.5+_1.0)之配料,稳定声料品质,降低标准偏差.SM高,使物料易燃性降低,因Al2O3+Fe2O3含量降低,不利CaO+ SiO2燃结,但预锻窑中需热量少,而热量供应很充分,故可胜任熟料烧成.IM高,使夜体黏度提高,但由于窑中火焰温度高,故也没有问题.LSF高,生料中碳酸盐矿物含量低,减少熟料的形成热,可降低热耗量.MgO在燃结温度下是一种助燃剂,使烧成反应易于进行,但含量过高易使烧成带结球.SO3来自原料及燃料,其在1000℃时形成SO2气体,并在窑系统中生成CaSO4,K2SO4,易在窑后段造成结圈及结料.Na2O及K2O对熟料品质及窑操作均有不良影响,它们在烧成带开始处挥发,随窑气飘到预热机底段,在900℃下凝结下来与SO2,CO2及氯反应,碱份循环易在窑内造成结料及结圈.氯来自原料及煤炭,氯也会在高温下挥发与碱份形成氯化碱在窑中循环,造成预热机底段及窑尾结圈.适合燃煤用的生料若突然改燃油时,会造成难烧,这是因为缺少煤灰中的Al2O3及Fe2O3助燃剂之故.四. 烧成研究构想.1.(1).脱酸度一天一次 ,adj.煤量of pyrodon.(2).ono mlthod 一天一次, adj.窑operation.2. 配料方向:(1).确保入窑生料一致稳定.(2).熟料品质高,易燃性好,烧成带易结皮.(3).连续一致的入窑生料成份,是窑适当操作的最重要因素.五.生料组成对易烧性之影响.生料易烧性:生料在窑中转变成熟料之相对难易程度.可标示将生料烧成良好品质熟料所需之燃料量.生料易烧性视生料组成而定,可用如下来表示:1. 硅率系数(SM).SM= SiO2 / Al2O3+Fe2O3硅率系数增加将使易燃性变差,因为Al2O3及Fe2O3含量使得CaO及SiO2可在较低温度下化合.名词定义易烧:生料须较少之燃料即可烧成熟料.难烧:生料须较多之燃料才可烧成熟料.2. 铝率系数(IM).IM=Al2O3 / Fe2O3铝率系数越高,生料越难烧.当其它成份固定时,铝含量越高越容易烧,因铝可促进CaO及SiO2之‘反应速率.熟料IM=1.4~1.6之间最佳,易烧性好,偏高时,会产生易烧性变差.3.石灰石饱和系数(LSF).LSF=CaO/ 2.8SiO2+1.18Al2O3+0.65Fe2O3熟料LSF在0.99以上时,将相当难烧,且即使升高窑温,熟料中游离石灰含量也舞法降低,反而会损失及窑皮及火砖.LSF在一般值时,窑温升高,熟料中F.L.降低,此时可从F.L.含量来判断窑中temp是否适当,熟料F.L.以控制在0.8%较佳,一般0.4〜1.2%.LSF0.90以下将使熟料F.L.偏太低.4.水硬系数(HM):目前不常用了.HM= CaO / SiO2+Al2O3+Fe2O35.液体含量:熟料在1450℃烧成时将形成半液体状态,此熟料床粘稠外观是烧手观察烧成带时一项很重要的控制参数.液体%(1450℃)=3.0Al2O3+2.25Fe2O3+MgO+Na2O当量总碱份.或=1.13C3A+1.35C4AF+MgO+Na2O当量总碱份,其中MgO含量最高计至2%.熟料中液体含量通常介于25〜27.5%之间,与温度成正比观系.液体含量较高时,烧成带熟料床外观较粘,将使熟料较易烧成.六.烧成性分析.1. 生料成份之改变对窑操作有很大的影响,故烧手应预先掌握入窑的生料之成份变化情况,如Ⅰ型生料改换成Ⅱ型生料.2. 入窑生料之粒度分布状况应尽量均一,减少变化.尤其粗颗粒的生料对烧成性及窑操作稳定性有很大影响.*.Kuehl's烧成指数(BI)= C3S/ C4AF+C3A值越高表示越难烧.*.Peray烧成参数(BF)=100(LSF)+10(SM)-3(MgO+Na2O当量总碱份).值越高表示越难烧.*.经验烧成参数(BF)=x(LSF)+y(SM)-j(MgO+Ma2O当量总碱份).(针对各窑,然后用多重回归分析决定x,y,j值).例:熟料参数计算:熟烧失量0.16 0.16SiO2 22.00 22.15料Al2O3 5.40 5.40Fe2O3 3.40 3.40组CaO 65.00 64.75MgO 2.85 2.85成Na2O当量0.75 0.75总碱份份SO3 0.30 0.30(%) 总计99.86 99.86C3S 55.35 52.43C2S 21.41 24.33C3A 8.56 8.56C4AF 10.34 10.34HM 2.11 2.09SM 2.50 2.53ZM 1.59 1.59LSF 92.6 91.3液体含量(%) 26.38 26.38Kuehl's烧成指数 2.93 2.77Peray烧成参数106.8 105.8七.升重试验.升重及游离石灰石含量可显示熟料的烧成温度是否适当,不过升重试验较迅速只须5分钟,而滚压则约1小时.熟料升重以6m〜12mm,熟料颗粒在1L铁杯中之重量表示之.当熟料成份相同时,过烧熟料的升重高于正常熟料,烧成不良熟料的升重则低于正常熟料烧成良好之熟料升重通常介于1.25Kg至1.35Kg之间,视成份而定八.熟料显微学.1.目的:用来诊断窑烧成及冷却之变化.Ono methocl:窑烧成状况及预测水泥强度.2.C2S+游离CaO+液体→C3S+缓慢冷却→C2S+CaO过烧的熟料:烧成带过长,熟料在烧成temp下暴露时过长,将使液体量增加,生成过多大颗粒C3S结晶,不列于水泥强度.相反地, 烧成temp不够,将生成较小的C3S结晶且量较少,过量的C2S及f-CaO,也不列于水泥强度.九.窑中反应带.九.窑中反应带1.生料组成份对易烧性之影响.1.1 烧成理想状况:如Ono所述.1.2 生料参数介绍.1.3 生料参数与易烧性之关系.2.锻烧带反应:CaCO3→CaO+CO2MgCO3→MgO+CO2将生料完全锻烧脱酸是确保适当烧成熟料之必要条件.定期(如每日)测定C4 F料脱酸度,有助烧窑控制.3.过度带:在火焰尾端,料呈暗色,温度突升至烧成temp.4.烧成带:直接在火焰下端,熟料矿物生成,C3S,C2S,C3A,C4AF,此时中间区域由于热反应,其中料流temp最高且最粘稠.5.冷却带:通常在窑出口3〜6mm内.冷却带长度应适中,使窑落口熟料temp保持在约1370℃,则高温度熟料落入冷却机第一室中将料快速冷却,有利于熟料品质及研磨性.十.窑中结皮及结晶.控制烧成带的结皮良好,有助延长耐火砖寿命,增加窑运转效益.*.窑皮的平衡条件:熟料液体固化温度(1)=窑皮表面温度(2).当(1)<(2)时窑皮熔解脱落(1)>(2)时继续生成窑皮*.液体含量高的熟料较容易生成窑皮.*.热传导好的耐火砖较容易生成窑皮. (因窑皮的temp较低)*.火焰形状将影响窑皮表面temp,对窑皮的形成有决定性的影响:1.火焰过短,有力且宽,会在短截面中释放出大量热熔蚀窑皮.2.长焰有莉于生成窑皮.3.短焰有利于烧成操作,故应控制适当的短焰,以不熔蚀窑皮为原则.十一.操作条件.*.熟料烧成指针:在一给予的饲料量时,藉改变窑速,用煤量及ID风车转速或三者的组合来维持适当的烧成带温度及固定的进料室温度.依重要性,可列为下述四项基本定律.1. 随时保持设备及人员安全.2. 制造烧成良好的熟料(FL及升重正常).3. 连续稳定的操作旋窑(不须或仅略微改变控制条件).此时窑速,烧成带temp及进料室temp在长时间内变动甚微.4. 以最佳的燃料效率获得最高产量.*.在Kiln运转顺利期间,每半小时观察烧成带一次,应在Kiln条件变化发生时就作出调整.*.观察Clinker外观:良好烧成之熟料是黑色,且烧成温度越高,熟料颗粒越大.过烧之熟料颗粒较大,升重较高,FL较低,较密实少孔隙,较黑.烧成不良之熟料则相反,较小较砂.*.火焰颜色应为橘黄色,若变动时应找出原因且调整之.暗红======》冷橘黄 =======》正常白=======》热注:1. 暗料与亮料在火焰下分界点之改变是烧成带条件变化之先兆.在正常操作下,分界点在火焰下距焰尖约1/4处,若它往窑出口移动表示生料较难烧,料量增加,烧成带温度降低,火焰长度变短.若它往窑进口移动表示生料易烧,料量减少,烧成带温度上升,火焰长度变长且有充分温度.烧手可籍稍微调整窑用煤量使分界点维持在适当位置.此分界点不得超过火焰下1/2长度,当太靠近窑出口时,烧手应改变火焰长度(若必时)使分界点与火焰恢复至原来关系.2. 来自冷却机之燃烧空气.当烧成不良之clinker进入cooler后,二次空气中将夹杂大量粉磨入窑而干扰烧成带视觉,此时二次空气温度较低会使煤粉燃点更深入kiln中,烧手应设法观察火焰下方及尾端来作调整措施,而不因烧成带前端颜色受粉磨影响变暗就断定烧成带温度不足.3. 窑皮颜色.在正常操作下,窑皮颜色介于黄,白之间,当变成橘红色或黄色表示烧成带温度降低.当大量生料粉使窑皮温度快速降低时烧手应减慢窑速,避免烧成不良clinker.维持或重建窑皮以保护耐火砖及窑壳,避免过热受损是烧手之重要责任.观察烧成带下述项目w之变化对温度之影响:(1).熟料颜色;(2).熟料大小;(3).火焰附近熟料之行进状况;(4).火焰尾端生料床外观;(5).暗料与亮料之分界点位置;(6).二次空气外观;(7).窑皮状况;(8).火焰形状及颜色.及早侦测任何变化并逐步渐进式的采取调整对策是烧窑的准则.三次管及窑尾O2含量应介于0.7〜3.5%之间,而1〜1.5% O2 是最理想的操作状况.注:1.砂料使烧成带变亮时之对策:略增O2含量,略减用煤量,以提高烧成带temp,降低窑速.2.煤灰软化温度低及煤灰中铁份含量高之煤较易结圈,故应磨得较细.3.窑尾温度过高之微兆:(1).窑在连续操作中,排气中O2含量偏高.(2).烧成带过长,烧成容易,熟料在火焰端很远就形成.(3).耗煤量偏高.4.窑尾温度过低之微兆:(1).窑长期操作时,排气中O2偏高.(2).因生料锻烧不完全就进入烧成带,使烧成不易.十二.水泥化学上一些重要之计算式.1.水硬系数(HM).HM= CaO / SiO2+Al2O3+Fe2O32.铝率系数(IM).IM= Al2O3 / Fe2O33.石灰饱和度(LSF).(1).生料及熟料适用.LSF= CaO*100 / 2.80SiO2+1.18Al2O3+0.65Fe2O3(2).水泥适用.LSF= (CaO-0.70SO3)*100 / 2.80SiO2+1.18Al2O3+0.65Fe2O3 4.液体含量.当熟料在1450℃烧成时,将有以下的液体含量:液体(%)=1.13C3A+1.35C4AF+MgO+Na2O+K2O5.Bogue公式.水泥中化合物成份计算:IM>0.64C3S=4.07CaO-7.6SiO2-6.72Al2O3-1.43Fe2O3-2.85SO3C2S=2.87SiO2-0.754C3SC3A=2.65Al2O3-1.69Fe2O3C4AF=3.04Fe2O36.Na2O当量总碱份(Total Alkalies as Na2O).总碱份=Na2O+0.658K2O7.预热机脱酸度(Percent of Decomposition)C=其中A=预热机称量机上生料烧失量百分比.B=预热机某段旋风筒下料管生料烧失量之比.C=该段旋风筒之脱酸度百分比.众所周知,熟料强度主要来源于硅酸盐矿物,而C3S又是硅酸盐矿物强度的主要提供者。
窑炉中控控温操作规程
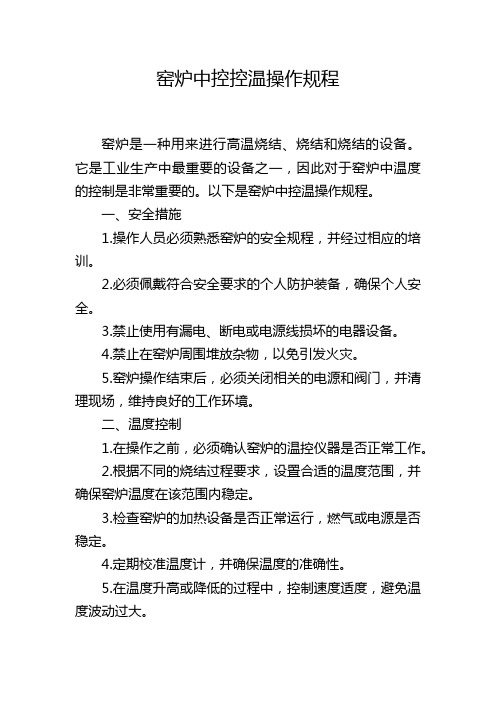
窑炉中控控温操作规程窑炉是一种用来进行高温烧结、烧结和烧结的设备。
它是工业生产中最重要的设备之一,因此对于窑炉中温度的控制是非常重要的。
以下是窑炉中控温操作规程。
一、安全措施1.操作人员必须熟悉窑炉的安全规程,并经过相应的培训。
2.必须佩戴符合安全要求的个人防护装备,确保个人安全。
3.禁止使用有漏电、断电或电源线损坏的电器设备。
4.禁止在窑炉周围堆放杂物,以免引发火灾。
5.窑炉操作结束后,必须关闭相关的电源和阀门,并清理现场,维持良好的工作环境。
二、温度控制1.在操作之前,必须确认窑炉的温控仪器是否正常工作。
2.根据不同的烧结过程要求,设置合适的温度范围,并确保窑炉温度在该范围内稳定。
3.检查窑炉的加热设备是否正常运行,燃气或电源是否稳定。
4.定期校准温度计,并确保温度的准确性。
5.在温度升高或降低的过程中,控制速度适度,避免温度波动过大。
三、冷却控制1.在窑炉烧结过程结束后,必须合理安排冷却的时间和速度。
2.根据窑炉的冷却曲线,设定合适的冷却速度,保证产品质量。
3.确保冷却过程中的环境温度、湿度和通风条件,以确保产品的质量稳定。
4.避免过快或过慢的冷却速度,以免产生产品破裂或变质。
四、记录与报告1.在窑炉操作过程中,必须详细记录温度和冷却速度等关键参数。
2.及时汇总和整理操作记录,并定期向上级报告窑炉的运行状况。
3.对窑炉的异常情况和故障进行及时记录,并向相关部门报告,及时处理。
五、定期维护1.对窑炉进行定期维护,保持设备的良好状态。
2.定期清洁窑炉,确保烟道畅通,燃气或电源供应正常。
3.定期检查窑炉中的温控仪器和传感器的工作状态,确保准确度。
六、紧急情况处理1.在窑炉操作中,如果出现突发情况,如温度过高或过低,必须根据紧急处理程序迅速采取措施。
2.在紧急情况下,必须及时向相关部门报告,并与其他操作人员密切合作,采取必要的措施,以确保人员的安全和设备的正常运行。
通过遵守以上窑炉中控温操作规程,能够有效地提高窑炉的运行效率和产品质量,保证人员的安全,并延长设备的使用寿命。
水泥厂旋转窑系统操作规程

窑系统操作规程目的本规程旨在树立安全第一、预防为主的观点,统一操作思想,生产合格生料,力求达到优质、稳定、高产、低耗的目的。
二、范围本规程适用于窑系统,即从生料库底至熟料库顶和窑头废气处理的所有设备。
三、指导思想1.树立安全生产,质量第一的观念,达到连续、稳定生产;2.严格遵守设备操作规程,精心操作、杜绝违章;3.制定最佳操作参数,做到优质、稳定、高产、低耗,努力做到系统设备安全稳定运行,确保生料库料位,实现安全、文明生产。
一、点火前的检查准备工作:1、现场检查各有关设备的润滑情况及螺栓是否松动,尤其是轮带与垫板间应加足石墨锂基脂。
检查预热器、窑及冷却机内的耐火衬完好情况,有关人员、支架、工具、杂物等是否已全部撤离和清理干净,以及三次风管的积料情况。
将预热器各翻板阀吊起,确认管道畅通无堵后,将翻板阀放下,并严密关闭整个系统的人孔门及捅料孔盖。
确认风机进口风门处于关闭状态。
2、校准燃烧器角度及距窑口距离,喷煤管前段与窑口相距10~20cm,角度以窑中心点略偏向第四象限。
并做好记录。
3、根据工艺要求向窑操提供升温曲线图。
4、确认窑头喂煤仓内有足够的煤粉(可用4小时左右),确认柴油泵站有足够的油量满足点火升温要求。
各专业人员进入岗位并完成各项准备工作。
5、窑操作员、巡检工应对本系统全面检查了解,并将准备工作、检查情况及结果全面真实地写入交接班记录,并将存在的问题向分管上级领导汇报。
接到点火指令后,由生产调度通知原料、煤磨、电气、仪表、自动化等专业人员将各设备、仪器仪表送电,通知水泵房送水,通知现场将本系统所有设备的现场控制转入中控位置,检查各设备、仪器是否备妥。
6、启动相关空压机,风机润滑系统窑减速机润滑系统。
二、点火升温:调整预热器烟囱门开度,使窑罩压力在-30Pa左右。
打开燃烧器上内外流手动风门,相差将放风阀打开,中控室启动一次风机,并调节手动风门至一定开度,压力为0.015Mpa,以内流为准。
启动点火油泵,调整供油油站出口压力。
窑中控操作规程
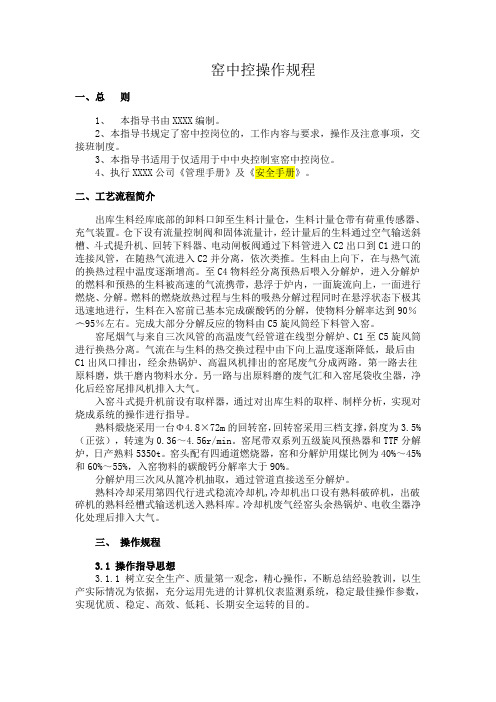
窑中控操作规程一、总则1、本指导书由XXXX编制。
2、本指导书规定了窑中控岗位的,工作内容与要求,操作及注意事项,交接班制度。
3、本指导书适用于仅适用于中中央控制室窑中控岗位。
4、执行XXXX公司《管理手册》及《安全手册》。
二、工艺流程简介出库生料经库底部的卸料口卸至生料计量仓,生料计量仓带有荷重传感器、充气装置。
仓下设有流量控制阀和固体流量计,经计量后的生料通过空气输送斜槽、斗式提升机、回转下料器、电动闸板阀通过下料管进入C2出口到C1进口的连接风管,在随热气流进入C2并分离,依次类推。
生料由上向下,在与热气流的换热过程中温度逐渐增高。
至C4物料经分离预热后喂入分解炉,进入分解炉的燃料和预热的生料被高速的气流携带,悬浮于炉内,一面旋流向上,一面进行燃烧、分解。
燃料的燃烧放热过程与生料的吸热分解过程同时在悬浮状态下极其迅速地进行,生料在入窑前已基本完成碳酸钙的分解,使物料分解率达到90%︿95%左右。
完成大部分分解反应的物料由C5旋风筒经下料管入窑。
窑尾烟气与来自三次风管的高温废气经管道在线型分解炉、C1至C5旋风筒进行换热分离。
气流在与生料的热交换过程中由下向上温度逐渐降低,最后由C1出风口排出,经余热锅炉、高温风机排出的窑尾废气分成两路。
第一路去往原料磨,烘干磨内物料水分。
另一路与出原料磨的废气汇和入窑尾袋收尘器,净化后经窑尾排风机排入大气。
入窑斗式提升机前设有取样器,通过对出库生料的取样、制样分析,实现对烧成系统的操作进行指导。
熟料煅烧采用一台Φ4.8×72m的回转窑,回转窑采用三档支撑,斜度为3.5%(正弦),转速为0.36~4.56r/min。
窑尾带双系列五级旋风预热器和TTF分解炉,日产熟料5350t。
窑头配有四通道燃烧器,窑和分解炉用煤比例为40%~45%和60%~55%,入窑物料的碳酸钙分解率大于90%。
分解炉用三次风从篦冷机抽取,通过管道直接送至分解炉。
熟料冷却采用第四代行进式稳流冷却机,冷却机出口设有熟料破碎机,出破碎机的熟料经槽式输送机送入熟料库。
窑中控操作规程
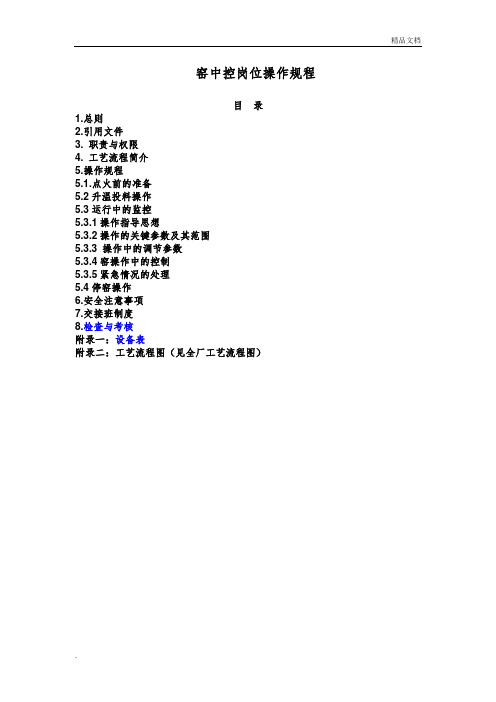
窑中控岗位操作规程目录1.总则2.引用文件3. 职责与权限4. 工艺流程简介5.操作规程5.1.点火前的准备5.2升温投料操作5.3运行中的监控5.3.1操作指导思想5.3.2操作的关键参数及其范围5.3.3 操作中的调节参数5.3.4窑操作中的控制5.3.5紧急情况的处理5.4停窑操作6.安全注意事项7.交接班制度8.检查与考核附录一:设备表附录二:工艺流程图(见全厂工艺流程图)1.总则1.1本规程规定了窑操作员的职责范围,工作内容与要求,操作及注意事项,交接班制度以及考核办法。
1.2本规程仅适用于烧成系统中控室窑操作员.1.3执行本公司《员工手册》.2.引用文件2.1烟台东源水泥公司5000t/d工程《工艺设备表》。
2.2烟台东源水泥公司5000t/d工程《工艺流程图》。
2.3《工艺操作说明书》。
3.职责与权限3.1 接受值班主任的指挥,负责窑喂料、旋风预热器及分解炉、回转窑、篦冷机既熟料烧成工序生产的正常进行;负责对窑喂料巡检工、旋风预热器及分解炉巡检工、回转窑巡检工、篦冷机巡检工的调度、安全等管理。
3.2 根据生产部下达的操作参数标准和质控部下达的质量控制标准控制熟料烧成系统的操作;确保参数稳定、准确,产量熟料稳定,质量符合公司的质量要求。
3.3 严格作业指导书操作,并对过程参数和产品质量及时记录,确保操作规范、记录真实。
3.4 负责对窑喂料、旋风预热器及分解炉、回转窑、篦冷机既熟料烧成工序运行状态的严密监视,根据情况指挥相关人员对设备进行巡检及维护,确保设备运行正常。
3.5 严格按操作规程操作,确保本系统无安全事故发生、并负责对下属进行安全教育。
3.6督促本系统工人做好卫生和环保。
3.7 保持生产内部沟通,对外与机动部、质控部沟通。
3.8 检修期间,指挥、协调本系统人员配合机电维修人员搞好设备检修工作,并参加试车和验收。
3.9 参加生产部及公司组织的会议和培训任务。
4工艺流程简介4.1燃煤:窑头煤粉仓(2720)和窑尾煤粉仓(2721)中储存。
中控窑操安全操作规程
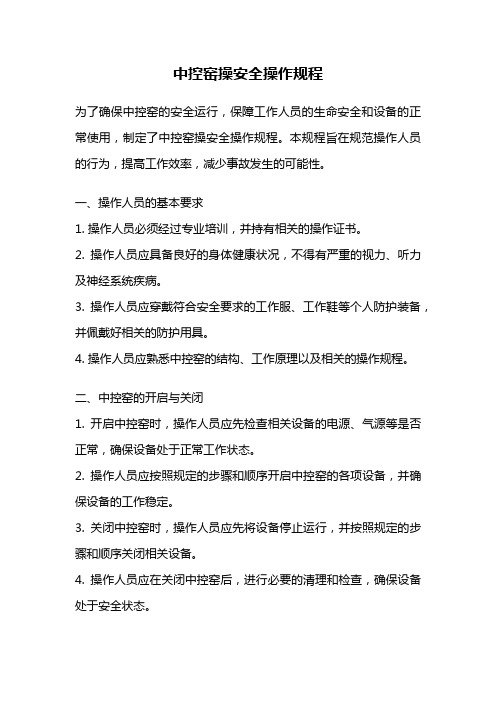
中控窑操安全操作规程为了确保中控窑的安全运行,保障工作人员的生命安全和设备的正常使用,制定了中控窑操安全操作规程。
本规程旨在规范操作人员的行为,提高工作效率,减少事故发生的可能性。
一、操作人员的基本要求1. 操作人员必须经过专业培训,并持有相关的操作证书。
2. 操作人员应具备良好的身体健康状况,不得有严重的视力、听力及神经系统疾病。
3. 操作人员应穿戴符合安全要求的工作服、工作鞋等个人防护装备,并佩戴好相关的防护用具。
4. 操作人员应熟悉中控窑的结构、工作原理以及相关的操作规程。
二、中控窑的开启与关闭1. 开启中控窑时,操作人员应先检查相关设备的电源、气源等是否正常,确保设备处于正常工作状态。
2. 操作人员应按照规定的步骤和顺序开启中控窑的各项设备,并确保设备的工作稳定。
3. 关闭中控窑时,操作人员应先将设备停止运行,并按照规定的步骤和顺序关闭相关设备。
4. 操作人员应在关闭中控窑后,进行必要的清理和检查,确保设备处于安全状态。
三、中控窑的操作1. 操作人员应按照规定的操作流程进行操作,不得擅自变更操作步骤。
2. 操作人员应注意中控窑的工作参数,及时对设备进行调整和修正,确保设备的正常运行。
3. 操作人员应定期对中控窑进行维护和保养,及时更换损坏的零部件,确保设备的可靠性和安全性。
4. 操作人员在操作过程中,应密切关注设备的运行状态,及时发现和处理设备故障,确保设备的正常运行。
5. 操作人员应保持工作区域的整洁,不得乱堆放杂物,以免影响设备的正常运行。
四、中控窑的应急处理1. 操作人员应熟悉中控窑的应急处理流程,掌握相关的应急处理技能。
2. 在中控窑发生故障或意外情况时,操作人员应立即采取紧急停机措施,并按照应急处理流程进行处理。
3. 操作人员应及时向上级报告,并配合相关部门进行故障排除和事故调查工作。
五、操作人员的安全意识1. 操作人员应时刻保持高度的安全意识,严格按照操作规程进行操作,不得违章操作。
旋窑

旋窑旋窑旋窑烧成控制首先必须熟悉生产流程,同时各种操作上的控制点象风压、温度、马达电流、O2含量及CO含量等必须熟悉,这些参数会随着烧成状况的不同而有不同的控制范围,象新窑开始烧成时由于不存在结圈及堵料的问题,相对而言压损会比较小,更接近设计值。
具有三对拖辊的长窑,相对而言拖辊多、摩擦大、功耗大,约为33~35kwh/t.clinker,而短窑仅为25 kwh/t.clinker左右,很少超过26kwh/t.clinker。
对于短窑,避免了三座辊子难以调节,易产生“香蕉窑”的缺点。
每只支持滚轮由两只轴承来支撑,轴承底座采用巴氏合金,承重过大产生温度超过100℃时就会熔掉,起到过载保护的作用。
窑壳在转动过程中会产生滑动,上下限各25mm,因此支持滚轮比胎环宽50mm,Girth Gear比Ring Gear宽50mm。
当窑壳达到下限时液压系统会自动将其重新送上来,大约每班滑上滑下各一次。
以往的做法是利用调节支持滚轮跟窑中心线的夹角将窑壳送到上限,之后,利用石墨块减小滚轮和胎环之间的磨擦,使窑壳凭借自身重力滑到下限。
更简单的作法是将石墨擦干净,并撒上生料粉以使窑壳再向上运动。
双边传动2×380KW主马达经FLENDER齿轮减速接荛性联轴器带动Girth Gear,为防止意外事故,备有寸动马达及汽油发电机。
环齿轮利用弹簧片固定在窑壳上,窑壳和支持滚轮轴承及主传动马达之间设有隔热板,以免高温对机器造成损害。
正常烧成采用短焰燃烧,输煤风车压力小,燃烧器外圈压力大,内圈空气为螺线形(1#、2#、3#),其风量风压一般不会调节,窑外圈空气为螺线形,可以利用其风压的调节来改变火焰形状。
喷煤嘴一般伸到窑落口鼻圈处或第一圈砖的地方,根据烧成情况调节,但注意不要伸到鼻圈之外,以防受二次空气干扰火焰形状。
窑壳在烧成受热后会膨胀约20mm,改变喷煤嘴的相对位置,这一点也要予考虑,特别是短窑系统会严重影响烧成带、冷却带的长度。
台泥英德旋窑操作指南

台泥英德旋窑操作指南1)RSP窑在稳定操作条件下相关的信息与参考点。
在旋窑运转上,烧手必须知道各种参考点的正常值和可容许范围,以资察不正常的偏差而做适当的处理。
稳定状态的正常值与可容许范围如2不正常偏差的影响因素。
(1)进窑室风压如果风压低于-50mmAg则可能I 旋窑窑皮太厚Ii 生料在进窑室斜槽结皮(2)生料在进窑室Q的含量如果O2含量低于%则可能I旋窑与煅烧炉之间的燃烧空气平衡不良――开大节流阀假如煅烧炉的燃烧空气比率因上述动作而变得不适当。
――开大SP IDF入口挡板或增加IDF转速或开大三次空气控制挡板II生料在进窑室斜槽结皮。
检查进窑室CO含量,确认是否在窑尾,进窑室或混合室发生二次燃烧。
(3)进窑室气温如果气温低于850C时,贝U可能I旋窑喂煤量太少熟料品质将会下降入窑气温高于1100C时,则可能I旋窑喂煤量太多II窑尾发生二次燃烧。
将使进窑室与节流阀结皮严重。
(4)旋窑烧成带温度会受回灰量多寡,高温辐射计位置方向的影响。
因此,烧手必须判断符合实际运转的正确值。
ONODA RS系统的烧成带平均温度如Fig。
1如果烧成带温度低于1300C,则可能I窑内掉窑皮II旋窑烧成状况不良。
将造成出黄料和质量不良如果烧成带温度高于1550°C,则可能I旋窑过烧会造成窑内火砖过热而损坏(5)煅烧的空气燃料比(Air fuer ratio )“n”如果低于n =1或高于n =,贝U可能I煅烧炉的燃烧空气控制不良。
在煅烧炉内无法达成有效燃烧(6)煅烧炉出口气温如果煅烧炉出口气温高于950C时,则可能I煅烧炉喂煤量太多会造成脱酸度过高,使煅烧炉,混合室或旋风筒解皮严重如果煅烧炉出口气温低于800 C时,则可能I煅烧炉喂煤量太少和(或)燃料燃烧情况不量实际的喂煤量和(或)煤炭燃烧情况需要确认(7)C5旋风筒出口气温和卸料料温如果气温高于860 C则可能I煅烧炉和(或)旋窑的喂煤,有部分未燃烧而进入C5旋风筒内燃烧II煅烧炉和(或)旋窑的喂煤量过多III煅烧炉和(或)旋窑之间的燃烧空气比率不适当将造成旋风筒结皮严重如果气温低于810C,则可能I煅烧炉的喂煤量太少。
中控窑操作参数的意义与变化

1、窑电流:①窑电流的高低:主要与煅烧温度、窑内通风、掉窑皮等引起的负荷变化有关。
窑头煅烧温度越低,窑内通风越差,窑电流越低。
掉窑皮时窑负荷增大,窑电流会高,但窑内有蛋时一方面窑负荷增大,另一方面窑内通风会变差,两方面的综合作用对窑电流会导致完全相反的两种结果。
②窑电流波动的幅度:主要与窑皮均匀性、是否有蛋、是否擦挂及掉窑皮有关。
窑皮不均匀:波动幅度较大但有规律。
窑内有蛋:波动无规律、波动幅度大,一般还伴随篦下压力和烟室温度的较大波动。
擦挂:波幅大,有异常短时间的高峰值。
掉窑皮:突然升高到一定值后逐步下降或逐步升高后逐步下降,后者一般是后过渡带掉窑皮的电流趋势。
同时会伴随篦下压力的大幅度升高。
2、烟室温度:主要与头煤用量、头煤燃烧情况、分解炉温度控制值、窑内通风情况等有关。
烟室温度的基准值由头煤和窑内通风决定,波动的幅度由分解炉温度波动影响。
烟室温度低:三次风开度大、窑头煤用量偏小、窑内有圈有蛋、烟室和缩口结皮、分解炉温度控制低等。
烟室温度高:窑内通风大、头煤用量大、窑内煅烧温度高或窑头煤不完全燃烧导致煤粉后燃、分解炉温度控制高等。
3、分解炉出口温度:控制分解炉出口温度的意义在于控制分解率。
理论上分解率越高窑产量越高,但是分解率过高有很多害处:结皮严重;预热器耐火材料、内筒挂片寿命缩短;液相提前出现导致结圈、结蛋及结粒粗大的包心料导致f-CaO 高等等。
结合各水泥厂原材料性质和生产操作实际控制分解率为准。
4、头尾煤比例:合理的头尾煤比例是窑热工制度稳定的基础,合理的头尾煤比例主要取决于头煤的合理用量,头煤的合理用量取决于窑内通风,反言之合理的窑内通风取决于头煤用量。
在稳定的工况下头尾煤比例只能在较小范围内波动,这有助于热工制度的稳定。
长期偏离控制范围会导致热工制度的漂移,使窑况变化。
因此操作中头煤的加或者减都应是小幅度和短时间的,例如不超过20min,除非是窑内结圈结蛋导致必须大幅度减头煤才能保证完全燃烧。
旋窑中控操作主要参数
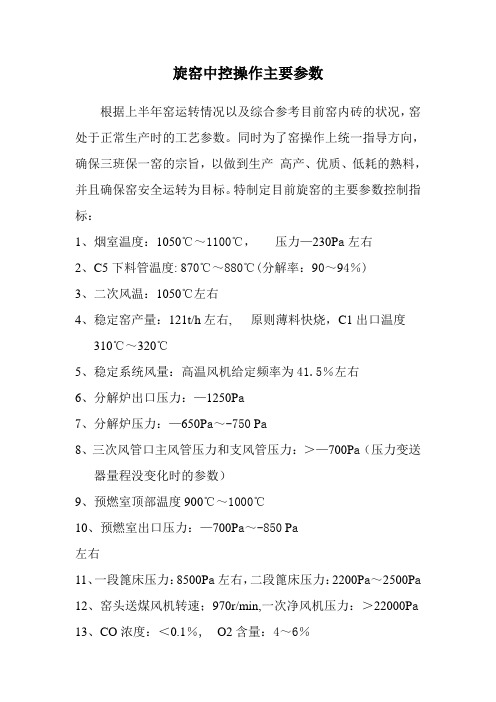
旋窑中控操作主要参数根据上半年窑运转情况以及综合参考目前窑内砖的状况,窑处于正常生产时的工艺参数。
同时为了窑操作上统一指导方向,确保三班保一窑的宗旨,以做到生产高产、优质、低耗的熟料,并且确保窑安全运转为目标。
特制定目前旋窑的主要参数控制指标:1、烟室温度:1050℃~1100℃,压力—230P a左右2、C5下料管温度: 870℃~880℃(分解率:90~94%)3、二次风温:1050℃左右4、稳定窑产量:121t/h左右, 原则薄料快烧,C1出口温度310℃~320℃5、稳定系统风量:高温风机给定频率为41.5%左右6、分解炉出口压力:—1250P a7、分解炉压力:—650P a~-750 P a8、三次风管口主风管压力和支风管压力:>—700P a(压力变送器量程没变化时的参数)9、预燃室顶部温度900℃~1000℃10、预燃室出口压力:—700P a~-850 P a左右11、一段篦床压力:8500P a左右,二段篦床压力:2200P a~2500P a12、窑头送煤风机转速;970r/min,一次净风机压力:>22000P a13、CO浓度:<0.1%,O2含量:4~6%14、窑头电收尘进口温度:<75℃15、增湿塔出口温度:180℃~190℃16、窑头罩压力:-15~-30Pa17、三次风阀开度38%18、头喷煤管的外风100%;60~80%内风;中心风50%(目的保护3~12米处主窑皮),要求窑筒扫温度<230℃19、重点确保头尾煤的稳定,做到及时清仓。
20、中控筒扫温度16米前<210℃,16~37米<250℃,如发现温度超高,必须在第一时间调整并通知现场巡检配合处理。
17米-37米温度偏低也必须及时调整头煤管进出位子进行控制。
以上参数是以窑正常生产时为参考,当窑况发生变化时,其工艺参数可适当超出其范围,但不能大幅度调整,应小调整渐调整以最快速度恢复至正常。
熟料分厂2011年10月6日。
11中控窑操作规程详解

中控室回转窑系统操作规程(试行稿)文件编号:修订状态:试行颁发日期:实施日期:受控状态:受控发放编号:内蒙古君正水泥有限公司二〇〇九年十二月第一章总则本规程用于指导中控室窑系统操作员的工作,以保证窑系统设备的正常运转和工艺操作的正确。
操作人员在理解本规程内容的基础上,掌握系统内每台设备的工作原理、基本结构和性能,能够在实际操作中随时解决出现的各种问题。
在实际生产中,如本规程的部分内容与实际情况有出入时,操作员应及时请示中控室主任,与工艺技术人员协商后进行操作。
根据实际情况定期修改本规程的有关内容。
第二章点火前的准备工作1、联系巡检工确认所有设备内部清洁无杂物,做好各检查孔和人孔门的密封。
2、确认各级下料翻板阀都闪动灵活、处于正确状态,检查后用铁丝吊起翻板阀处于全开位置。
3、确认现场仪表指示正确,与中控室显示一致。
4、确认各级预热器吹堵管畅通,各阀门开关位置正确。
5、确认预热器上清堵工具、安全防护用品配备齐全。
6、联系巡检工检查现场设备、准备好后,将机旁按钮盒的选择开关打到“集中”位置,使全部设备备妥。
7、确认煤粉制备系统能够正常运转,煤粉仓有一定量的存煤。
8、确认空压机能够正常运转,可正常对生料库、空气炮、收尘器、输煤等系统供气。
窑头燃油站油罐内柴油储备充足,油泵供油系统能够正常工作。
9、所有管道阀门开关灵活,开关位置、方向与中控显示一致。
10、确认烘干破系统、喷雾系统能够正常工作。
11、确认废气处理系统能够正常工作。
12、联系烧成工段各岗位巡检工注意,准备点火。
13、启动窑头看火电视。
第三章窑点火和升温1、关闭高温风机入口阀门,开启窑尾点火烟囱帽至一定高度,使窑系统产生微负压。
2、启动一次风机和点火油泵。
3、将火把点燃后,伸进窑内,调整回油阀,控制喷入窑内的燃油量,保证燃油着火。
4、确认柴油点燃后,调整燃烧器内、外风比例,以得到较理想的燃烧状况。
5、升温曲线由技术装备部制定,经总工程师批准后下达,操作员严格按要求进行升温。
窑中心控制室操作规程
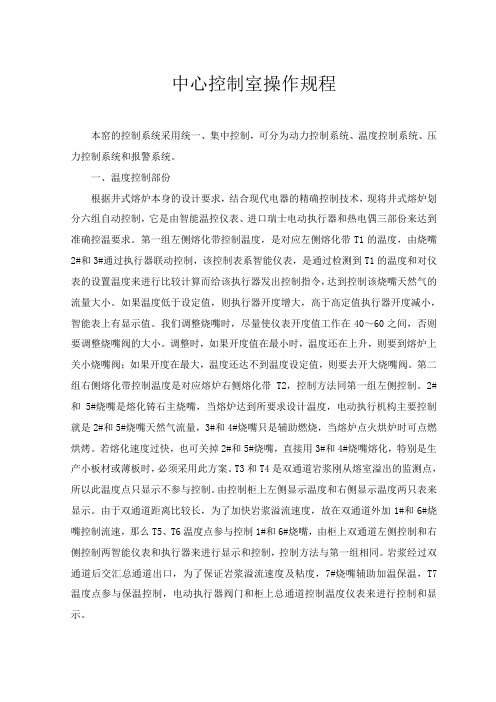
中心控制室操作规程本窑的控制系统采用统一、集中控制,可分为动力控制系统、温度控制系统、压力控制系统和报警系统。
一、温度控制部份根据井式熔炉本身的设计要求,结合现代电器的精确控制技术,现将井式熔炉划分六组自动控制,它是由智能温控仪表、进口瑞士电动执行器和热电偶三部份来达到准确控温要求。
第一组左侧熔化带控制温度,是对应左侧熔化带T1的温度,由烧嘴2#和3#通过执行器联动控制,该控制表系智能仪表,是通过检测到T1的温度和对仪表的设置温度来进行比较计算而给该执行器发出控制指令,达到控制该烧嘴天然气的流量大小。
如果温度低于设定值,则执行器开度增大,高于高定值执行器开度减小,智能表上有显示值。
我们调整烧嘴时,尽量使仪表开度值工作在40~60之间,否则要调整烧嘴阀的大小。
调整时,如果开度值在最小时,温度还在上升,则要到熔炉上关小烧嘴阀;如果开度在最大,温度还达不到温度设定值,则要去开大烧嘴阀。
第二组右侧熔化带控制温度是对应熔炉右侧熔化带T2,控制方法同第一组左侧控制。
2#和5#烧嘴是熔化铸石主烧嘴,当熔炉达到所要求设计温度,电动执行机构主要控制就是2#和5#烧嘴天然气流量,3#和4#烧嘴只是辅助燃烧,当熔炉点火烘炉时可点燃烘烤。
若熔化速度过快,也可关掉2#和5#烧嘴,直接用3#和4#烧嘴熔化,特别是生产小板材或薄板时,必须采用此方案。
T3和T4是双通道岩浆刚从熔室溢出的监测点,所以此温度点只显示不参与控制。
由控制柜上左侧显示温度和右侧显示温度两只表来显示。
由于双通道距离比较长,为了加快岩浆溢流速度,故在双通道外加1#和6#烧嘴控制流速,那么T5、T6温度点参与控制1#和6#烧嘴,由柜上双通道左侧控制和右侧控制两智能仪表和执行器来进行显示和控制,控制方法与第一组相同。
岩浆经过双通道后交汇总通道出口,为了保证岩浆溢流速度及粘度,7#烧嘴辅助加温保温,T7温度点参与保温控制,电动执行器阀门和柜上总通道控制温度仪表来进行控制和显示。
- 1、下载文档前请自行甄别文档内容的完整性,平台不提供额外的编辑、内容补充、找答案等附加服务。
- 2、"仅部分预览"的文档,不可在线预览部分如存在完整性等问题,可反馈申请退款(可完整预览的文档不适用该条件!)。
- 3、如文档侵犯您的权益,请联系客服反馈,我们会尽快为您处理(人工客服工作时间:9:00-18:30)。
旋窑中控操作主要参数
根据上半年窑运转情况以及综合参考目前窑内砖的状况,窑处于正常生产时的工艺参数。
同时为了窑操作上统一指导方向,确保三班保一窑的宗旨,以做到生产高产、优质、低耗的熟料,并且确保窑安全运转为目标。
特制定目前旋窑的主要参数控制指标:
1、烟室温度:1050℃~1100℃,压力—230P a左右
2、C5下料管温度: 870℃~880℃(分解率:90~94%)
3、二次风温:1050℃左右
4、稳定窑产量:121t/h左右, 原则薄料快烧,C1出口温度
310℃~320℃
5、稳定系统风量:高温风机给定频率为41.5%左右
6、分解炉出口压力:—1250P a
7、分解炉压力:—650P a~-750 P a
8、三次风管口主风管压力和支风管压力:>—700P a(压力变送
器量程没变化时的参数)
9、预燃室顶部温度900℃~1000℃
10、预燃室出口压力:—700P a~-850 P a
左右
11、一段篦床压力:8500P a左右,二段篦床压力:2200P a~2500P a
12、窑头送煤风机转速;970r/min,一次净风机压力:>22000P a
13、CO浓度:<0.1%,O2含量:4~6%
14、窑头电收尘进口温度:<75℃
15、增湿塔出口温度:180℃~190℃
16、窑头罩压力:-15~-30Pa
17、三次风阀开度38%
18、头喷煤管的外风100%;60~80%内风;中心风50%(目的
保护3~12米处主窑皮),要求窑筒扫温度<230℃
19、重点确保头尾煤的稳定,做到及时清仓。
20、中控筒扫温度16米前<210℃,16~37米<250℃,如发现温度超高,必须在第一时间调整并通知现场巡检配合处理。
17米-37米温度偏低也必须及时调整头煤管进出位子进行控制。
以上参数是以窑正常生产时为参考,当窑况发生变化时,其工艺参数可适当超出其范围,但不能大幅度调整,应小调整渐调整以最快速度恢复至正常。
熟料分厂
2011年10月6日。