TS16949 APQP 管理程序
TS16949标准教材-APQP

第三阶段:过程的设计和开发
(9)测量系统分析计划(作业标准) (10)初始过程能力研究计划 (11)阶段性评审会议(管理者支持)
著作权科建顾问所有,重制必究
-19-
AE006-G01
第四阶段:产品和过程确认
1.应用试产评价确认制造流程、并鉴别出其它额外须关注事项,以 便订定满足顾客需求的投产控制计划。 2.本阶段输入因素:第三阶段输出项目 3.本阶段输出项目: (1)试产:以正式生产用的工装、设备、环境、操作员、设施及 生产周期(输入至生输出产品)、以确认过程的有效性。 表单\量具再现再生性报告.pdf (2)测量系统评价 (3)初始过程能力研究:针对控制特性分析→PPk (4)生产件批准 :确认由生产工装和过程制造出来的产品符合技 术要求(PPAP)
著作权科建顾问所有,重制必究
-20-
AE006-G01
第四阶段:产品和过程确认
(5)生产确认试验:确认由生产工装或过程制造出来的产品 符合工程标准 (6)包装评价 (7)生产控制计划:亦可使用Ford的Dynamic Control Plan (DCP) (8)质量策划认定并召开阶段性评审会 表单\质量规划总结报告及签署书.pdf ※签署前,小组应予制造现场查证下列事项 ‧是否在所有相关操作现场,均配置控制计划
试 生 产 PPAP 可管 制计划
审查 量试
审查 生产转移 第一次 量产移转 自主检验 生产前沟通 1. 2. 3. 4. 5. 6. 7. 管制计划制作指导书 管制计划检查表 生产图面 制造作业指导书 检验标准 允收标准 材料表 1. 2. 3. 4. 投产管制计划 SPC表 设备/质量检点表 顾客满意度调查 (QCDS)
质量管理五大核心工具APQP、PPAP、SPC、MSA、FMEA(精选)
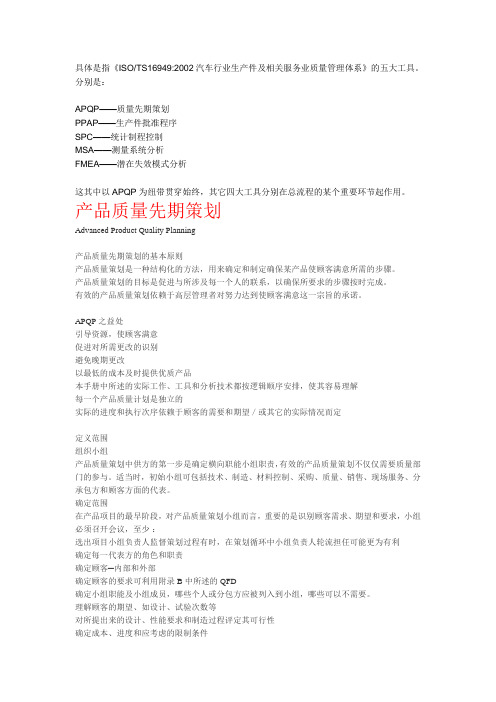
控制计划是控制零件和过程系统的书面描述,单独的控制计划包括三个独立的阶段:
样件:在样件制造过程中,对尺寸测量和材料与性能试验的描述。
试生产:在样件试制之后,全面生产之前所进行的尺寸测量和材料与性能试验的描述。
生产:在大批量生产中,将提供产品/过程特性,过程控制、试验和测量系统的综合文件。
问题的解决
第一阶段之输入
顾客的呼声
市场研究
保修记录和质量信息
小组经验
业务计划/营销策略
产品/过程基准数据
产品/过程设想
产品可靠性研究
顾客输入
第一阶段的输出作为第二阶段的输入
设计目标
可靠性和质量目标
初始材料清单
初始过程流程图
产品和过程特殊特性的初始清单
产品保证计划
管理者支持
顾客的呼声
“顾客的呼声”包括来自内部/外部顾客们的抱怨、建议、资料和信息。
确定范围
在产品项目的最早阶段,对产品质量策划小组而言,重要的是识别顾客需求、期望和要求,小组必须召开会议,至少:
选出项目小组负责人监督策划过程有时,在策划循环中小组负责人轮流担任可能更为有利
确定每一代表方的角色和职责
确定顾客─内部和外部
确定顾客的要求可利用附录B中所述的QFD
确定小组职能及小组成员,哪些个人或分包方应被列入到小组,哪些可以不需要。
APQP之益处
引导资源,使顾客满意
促进对所需更改的识别
避免晚期更改
以最低的成本及时提供优质产品
本手册中所述的实际工作、工具和分析技术都按逻辑顺序安排,使其容易理解
每一个产品质量计划是独立的
实际的进度和执行次序依赖于顾客的需要和期望/或其它的实际情况而定
APQP

4 4 4
APQP几大要点
使产品满足顾客的需要和期望; 不断采取防错措施,预防缺陷,以降低成本和降低产品风险; 从产品的概念设计、设计开发、过程开发、试生产到生产,以 及全过程中的信息反馈、纠正措施和持续改进活动; 团队的努力(横向职能小组是重要方法); 控制计划是重要的输出; 应用各类分析工具:FMEA,MSA,SPC、流程图、QFD、DOE等; 有效的产品质量策划依赖于企业高层管理者对努力达到使顾客 满意这一宗旨的承诺;
第三阶段 过程设计 和开发
第四阶段 产品和 过程确定 试生产
第五阶段 反馈、评定 和纠正措施 批量生产
16 16 16
二、产品质量策划循环图
产品质量策划循环是 一典型计划图,各 个不同的阶段按次 序排列以表示为实 施所述功能的有序 进度。 将产品质量策划描述 为一个循环阐明了 对持续改进的永无 止境追求,这种改 进只能通过在一个 项目中获取经验, 并将其应用到下一 个项目的方式来实 现。 17
19 19 19
计划和确定项目的输入和输出
输 ■ 顾客的呼声 ◆ 市场研究 过 程 ◆ 保修记录和质量信息 : 计 ◆ 小组经验 划 和 ■ 业务计划/营销策略 确 定 ■ 产品/过程基准数据 项 ■ 产品/过程设想 目 ■ 产品可靠性研究 ■ 顾客输入
20 20 20
入
输 ■ 设计目标
出
■ 可靠性和质量目标 ■ 初始材料清单 ■ 初始过程流程图 ■ 产品/过程特殊特性 初始清单 ■ 产品保证计划 ■ 管理者支持
业务计划会对小组给出限制(例如:时间,成本,投资、 产品定位,研究 (R&D)资源),影响其把握的方向。 市场策略会定义目标顾客,பைடு நூலகம்要卖点,以及主要的竞争对 手。
TS16949五大手册
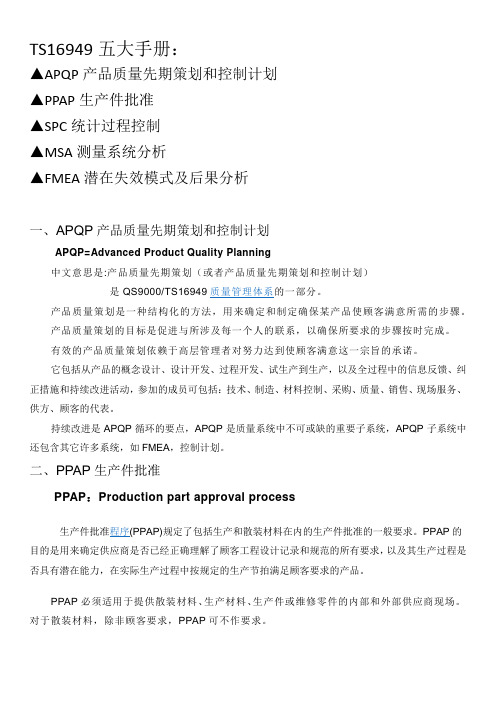
TS16949五大手册:▲APQP产品质量先期策划和控制计划▲PPAP生产件批准▲SPC统计过程控制▲MSA测量系统分析▲FMEA潜在失效模式及后果分析一、APQP产品质量先期策划和控制计划APQP=Advanced Product Quality Planning中文意思是:产品质量先期策划(或者产品质量先期策划和控制计划)是QS9000/TS16949质量管理体系的一部分。
产品质量策划是一种结构化的方法,用来确定和制定确保某产品使顾客满意所需的步骤。
产品质量策划的目标是促进与所涉及每一个人的联系,以确保所要求的步骤按时完成。
有效的产品质量策划依赖于高层管理者对努力达到使顾客满意这一宗旨的承诺。
它包括从产品的概念设计、设计开发、过程开发、试生产到生产,以及全过程中的信息反馈、纠正措施和持续改进活动,参加的成员可包括:技术、制造、材料控制、采购、质量、销售、现场服务、供方、顾客的代表。
持续改进是APQP循环的要点,APQP是质量系统中不可或缺的重要子系统,APQP子系统中还包含其它许多系统,如FMEA,控制计划。
二、PPAP生产件批准PPAP:Production part approval process生产件批准程序(PPAP)规定了包括生产和散装材料在内的生产件批准的一般要求。
PPAP的目的是用来确定供应商是否已经正确理解了顾客工程设计记录和规范的所有要求,以及其生产过程是否具有潜在能力,在实际生产过程中按规定的生产节拍满足顾客要求的产品。
PPAP必须适用于提供散装材料、生产材料、生产件或维修零件的内部和外部供应商现场。
对于散装材料,除非顾客要求,PPAP可不作要求。
三、SPC统计过程控制SPC=Statistical Process Control利用统计的方法来监控过程的状态,确定生产过程在管制的状态下,以降低产品品质的变异,统计过程控制(简称SPC)是一种借助数理统计方法的过程控制工具。
五大手册具体如下

五大手册具体如下:1、FMEA:失效模式和效果分析2、MSA:测量系统分析3、APQP:先期质量策划4、PPAP:生产件批准程序5、SPC:统计过程控制TS16949:国际标准化组织(ISO)于2002年3月公布了一项行业性的质量体系要求,它的全名是“质量管理体系—汽车行业生产件与相关服务件的组织实施ISO9001:2000的特殊要求”,英文为TS16949。
我们从实践角度出发,在背景、目标与意义、内容三方面,对该质量管理体系要求作简要介绍。
1.TS16949的背景和动态为了协调国际汽车质量系统规范,由世界上主要的汽车制造商及协会于1996年成立了一个专门机构,称为国际汽车工作组International Automotive Task Force (IATF) 。
IATF的成员包括了国际标准化组织质量管理与质量保证技术委员会(ISO/TC176),意大利汽车工业协会(ANFIA),法国汽车制造商委员会(CCFA)和汽车装备工业联盟(FIEV),德国汽车工业协会(VDA),汽车制造商如宝马(BMW),克莱斯勒(Daimler Chrysler),菲亚特(Fiat),福特(Ford),通用(General Motors),雷诺(Renault)和大众(Voldswagen)等。
IATF对3个欧洲规范VDA6.1(德国),VSQ(意大利),EAQF(法国)和QS9000(北美)进行了协调,在ISO9001:2000版标准结合的基础上,在ISO/TC176的的认可下,制定出了TS16949 :2002 这个规范。
2002年3月1日,ISO与IATF公布了国际汽车质量的技术规范TS16949:2002,这项技术规范适用于整个汽车产业生产零部件与服务件的供应链,包括整车厂,2002年版的TS16949已经生效,并展开认证工作。
在2002年4月24号,福特,通用和克莱斯勒三大汽车制造商在美国密歇根州底特律市召开了新闻发布会,宣布对供应厂商要采取的统一的一个质量体系规范,这个规范就是TS16949。
APQP过程流程图

工艺过程卡
材料进公司
产品的全工艺过程流程图 下料 锻造 机加工
热处理
顾客财产管理
4
产品和过程确认(加工过程质量确
认)
机加工
组装
压铸 机加工 包装入库 运输
顾客
工艺卡(控制计划) 分工分细表
有顾客要求时按顾客要求编制
无顾客要求时要符合TS16949标准要求 工艺卡(控制计划)中应包括:
·SPC工具的应用 ·全尺寸检测的规定 ·型式试验要求 ·测量器具的确定及正确性
检验条件
检具、标准具、样块、试验设备
检验人员
热工仪表、理化性能试验设备
一览表/精度确定
各表检定有效证据
评审 评审
评审
理化计量人员资格
分类进行分析 培训结果/证书
分析结果
产品检验 产品审核
人员配置/夜班 检验方法/要领/规定 抽样方法(GB/T2828 2829)
审核计划/项目
应包括所有产品
数据分析
结果反馈 生技部、 评 技术部、 审 制造部门
审核依据/标准 接受准则、标准、验收技术条件等 人员资格
全尺寸检测 应包括所有尺寸
图样、工艺卡、顾客要求 全尺寸检测评审 反馈生技部、技术部
有效依据
修定图样 修定工艺卡 修定完善DFMEA、PFMEA
PPAP文件汇总
相关部门
供应商选定/调达
供应商业绩/信誉度/交货期 供应商品质体系审定
生产应急
在任何事故、事件发生时应如何应变顾客订单/需求
减少变差/防措
停电、停水、人员短缺、材料短缺、火灾、设备停机
阶段评审
相关部门,管理层
产品设计开发计划中包 含样件生产计划
TS16949产品实现APQP程序

产品实现策划(APQP)程序发布日期:2006-2-101.0 目的:使产品在开发阶段能够如期完成必要的步骤,以确保新开发产品内在质量、成本、交期等各方面满足顾客需求。
2.0 范围:2.1 本程序规定了产品实现策划原则上应开展的活动、采用的程序或方法。
(当顾客有产品实现策划要求时,按照顾客规定的程序执行)2.2 新开发非现有系列的汽车类压铸件。
3.0 术语:3.1 项目小组:产品实现策划的横向协调小组。
3.2 P-FMEA:过程潜在失效模式及后果分析。
3.3 MSA:测量系统分析。
3.4 PPK:初始过程能力研究。
3.5 PPAP:生产件批准程序(顾客要求时)。
4.0 程序:4.1 图纸及样品提出:4.1.1 市场部向顾客取得新开发产品的图纸、规范或参考样品后,将开发产品的顾客、品名、图号、需求量、希望估价完成日等项填入“估价制造可行性评估表”内,经审核确认,通过文控中心将图纸、样品等资料发行给工程部进行评估。
4.2 估价制造可行性评估:4.2.1 工程部根据图纸、规范、样品进行以下评估:A.产品型态、材料种类、过程设备需求等。
B.产品成形性、图纸、尺寸公差CPK要求及模具开发风险等。
C.压铸件生产循环时间、材料规格、压铸件清理方式、压铸机吨位和相关加工设备等。
4.2.2 工程部必要时会同制造、品管、市场、生管、采购部门或召集项目小组人员针对相关过程工程与需求进行论证,并将有关问题记录于评估表内,如需要可要求相关单位提供评估资料添附于后。
但若为急件或一般性厂内生产中类似产品,经由工程部评估判定者,则可先行转至市场部提供报价,以争取报价时机,待接单后再请相关单位作进一步的评估。
4.3 问题点的确认:4.3.1 工程部评估后对顾客提供的图纸、规范或相关问题点如需作确认澄清时;可通知市场部进行协调或直接与顾客进行协商、确认。
4.3.2 工程部与顾客协商后,如无法立即澄清或如期完成估价时,须通知市场部更改估价完成日期。
TS16949程序文件APQP控制程序

TS16949程序文件APQP控制程序一、目的本程序旨在规范产品质量先期策划(APQP)的过程,确保新产品或更改产品的开发能够满足客户的要求,提高产品质量和生产效率,降低开发成本和风险。
二、适用范围本程序适用于公司所有新产品或更改产品的开发项目。
三、职责1、项目小组负责制定和执行 APQP 计划。
协调各部门之间的工作,确保项目顺利进行。
定期向管理层汇报项目进展情况。
2、销售部门收集客户需求和期望,传递给项目小组。
与客户沟通,获取产品相关信息和反馈。
3、设计部门负责产品的设计和开发。
制定产品规范和技术要求。
4、工艺部门负责制定生产工艺和流程。
设计工装夹具和检具。
5、采购部门负责原材料和零部件的采购。
确保供应商按时提供合格的产品。
6、质量部门制定质量控制计划和检验标准。
参与产品的测试和验证。
7、生产部门负责产品的试制和生产。
提供生产过程中的问题和改进建议。
8、管理层提供资源支持和决策指导。
审批 APQP 计划和相关文件。
四、APQP 过程1、计划和确定项目销售部门获取客户需求和期望,包括产品规格、数量、交付日期等。
项目小组对客户需求进行评估和分析,确定项目的可行性。
制定项目计划,包括项目目标、时间表、任务分配等。
2、产品设计和开发设计部门根据客户需求和项目计划,进行产品设计和开发。
制定产品规范和技术要求,包括材料、尺寸、性能等。
进行设计评审,确保设计满足客户需求和相关标准。
3、过程设计和开发工艺部门根据产品设计,制定生产工艺和流程。
设计工装夹具和检具,确保生产过程的稳定性和一致性。
进行过程评审,确保工艺设计满足生产要求和质量标准。
4、产品和过程的确认生产部门进行产品的试制和生产。
质量部门对试制产品进行测试和检验,验证产品是否满足设计要求和质量标准。
对生产过程进行评估,确认过程的稳定性和可控性。
5、反馈、评定和纠正措施收集客户和内部的反馈意见,对产品和过程进行改进。
对改进措施进行验证和评估,确保问题得到解决。
APQP的详细全面介绍课件

四、APQP的实施
❖ 我们用到一个工具:质量功能展开QFD ❖ 过程中的技巧:涉及部门、内容很多 ❖ 几个比较重要的工具:FMEA、SPC、MSA ❖ 二、产品设计:完全满足客户要求 ❖ 三、过程设计:如手机生产中PFMEA、控制计
划、过程工艺、作业标准等等 ❖ 四、小批量:人、机、料、法、环是否具备 ❖ 五、大批量生产:稳定、质量越来越好 ❖ 5个阶段顾客要求是核心,要不然就是废品 ❖ 5个阶段是最基本的,不是绝对的
五、APQP的具体操作
❖ 3.小组成立后的第一次会议主要议题是初步明确 需开展的工作并据此制定进度计划。从计划的角 度出发,必须明确任务活动,分配和/或其他事项。 小组根据APQP 手册的指引,将项目进行工作分 解,即分解成开展的工作(活动)。展开的工作 需要及组织接口如下:
❖ 根据工作展开及相关职责的确定,小组进一步讨 论了各项工作所需的资源及逻辑关系(对大项目 建议采用网络分析方法和关键路径方法),制定 了甘特图计划。
❖ APQP的目的: ❖ 及时完成关键的任务 ❖ 需要三家协作:客户、供应商、生产商 及时完成客户的需要:质量、进度、成本、甚至服
务等方面 ❖ APQP的好处: ❖ 公司资源有限:将有限的资源得到充分合理的运
用,将资源放在主要过程,促进早期更改,避免 晚期问题,分析问题,低成本提供 ❖ 汽车:发动机、车门、轮胎等几万个零件组成 ❖ 没有策划好:产品到客户手中有隐患
TS16949五大工具培训教材系列之一
APQP 先期产品质量策划程序
一、概述
❖ APQP---也可称为“项目管理” ❖ 例如:开发一款手机,开办一个超市、咖啡店等等都需要
有一个策划 ❖ APQP—侧重于先期策划 ❖ 例:开发一款手机—人、设备、工装模具、测量设备、标
产品设计与开发的流程APQP

根据评审结果,确定最终的设计方案,明确产品的功能、性能、外 观等关键要素。
设计任务书编制
根据确定的设计方案,编制详细的设计任务书,明确设计目标、设计 范围、设计周期等关键信息。
详细设计评审及优化改进
详细设计评审
组织专家团队对详细设计方案进行评审,确保方案符合设计任务 书的要求,并具备可行性和可制造性。
问题分析与处理
对试制过程中出现的问题进行深入分析,找出根本原因,制定针对性措施进行 改进。
试验结果分析和改进措施
试验结果分析
对试制产品进行全面的检测和试 验,收集试验数据,对试验结果 进行深入分析。
改进措施制定
针对试验结果中暴露出的问题, 制定具体的改进措施,包括设计 优化、工艺改进、材料替换等。
分析问题的根本原因,制定针对性的 改进计划,明确改进措施、责任人和 完成时间。
评估改进效果
对改进后的效果进行评估,包括产品 质量、生产效率、客户满意度等方面 的指标,确保改进取得实效。
客户反馈收集、整理和分析
建立客户反馈渠道
通过多种方式收集客户反馈,如调查问卷、 电话访谈、在线评价等。
整理客户反馈
对客户反馈进行整理,分类汇总各类问题, 以便后续分析。
分析客户反馈
运用统计分析方法,对客户反馈进行深入分 析,找出问题的根本原因和关键因素。
制定改进措施
根据分析结果,制定相应的改进措施,以提 高产品质量和客户满意度。
针对问题进行原因调查并采取措施
成立调查小组
针对重大问题或客户集中反馈的问题,成立专门的调查小组进行深入研究。
评审过程流程图的合理性和 可行性
组织相关部门和专家对过程流程图进行评审,确保 其合理性和可行性,提出改进意见和建议。
TS16949质量体系五大工具
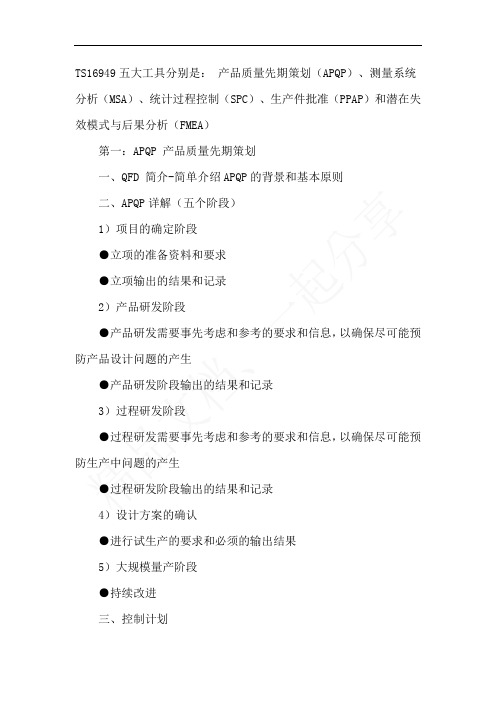
TS16949五大工具分别是:产品质量先期策划(APQP)、测量系统分析(MSA)、统计过程控制(SPC)、生产件批准(PPAP)和潜在失效模式与后果分析(FMEA)第一:APQP 产品质量先期策划一、QFD 简介-简单介绍APQP的背景和基本原则二、APQP详解(五个阶段)1)项目的确定阶段●立项的准备资料和要求●立项输出的结果和记录2)产品研发阶段●产品研发需要事先考虑和参考的要求和信息,以确保尽可能预防产品设计问题的产生●产品研发阶段输出的结果和记录3)过程研发阶段●过程研发需要事先考虑和参考的要求和信息,以确保尽可能预防生产中问题的产生●过程研发阶段输出的结果和记录4)设计方案的确认●进行试生产的要求和必须的输出结果5)大规模量产阶段●持续改进三、控制计划●控制计划在质量体系中的重要地位●控制计划的要求第二:MSA 测量系统分析测量系统必须处于统计控制中,这意味着测量系统中的变差只能是由于普通原因而不是由于特殊原因造成的。
这可称为统计稳定性;测量系统的变差必须比制造过程的变差小;变差应小于公差带;测量精度应高于过程变差和公差带两者中精度较高者,一般来说,测量精度是过程变差和公差带两者中精度较高者的十分之一;测量系统统计特性可能随被测项目的改变而变化。
若真的如此,则测量系统的最大的变差应小于过程变差和公差带两者中的较小者。
一、MSA的目的、适用范围和术语二、测量系统的统计特性三、测量系统变差的分类四、测量系统变差(偏倚、重复性、再现性、稳定性、线性)的定义、图示表达方式五、测量系统研究的准备六、偏倚的分析方法、判定准则七、重复性、再现性的分析方法、判定准则八、稳定性的分析方法、判定准则九、线性的分析方法、判定准则十、量型测量系统研究指南十一、量具特性曲线十二、计数型量具小样法研究指南十三、计数型量具大样法研究指南十四、案例研究第三:PPAP 生产件批准程序PPAP的目的是用来确定供方是否已经正确理解了顾客工程设计记录和规范的所有要求,并且在执行所要求的生产节拍条件下的实际生产过程中,具有持续满足这些要求的潜能,是目前最完善的供应商选择与控制系统。
TS16949质量体系五大工具

TS16949五大工具分别是:产品质量先期策划(APQP)、测量系统分析(MSA)、统计过程控制(SPC)、生产件批准(PPAP)和潜在失效模式与后果分析(FMEA)第一:APQP 产品质量先期策划一、QFD 简介-简单介绍APQP的背景和基本原则二、APQP详解(五个阶段)1)项目的确定阶段●立项的准备资料和要求●立项输出的结果和记录2)产品研发阶段●产品研发需要事先考虑和参考的要求和信息,以确保尽可能预防产品设计问题的产生●产品研发阶段输出的结果和记录3)过程研发阶段●过程研发需要事先考虑和参考的要求和信息,以确保尽可能预防生产中问题的产生●过程研发阶段输出的结果和记录4)设计方案的确认●进行试生产的要求和必须的输出结果5)大规模量产阶段●持续改进三、控制计划●控制计划在质量体系中的重要地位●控制计划的要求第二:MSA 测量系统分析测量系统必须处于统计控制中,这意味着测量系统中的变差只能是由于普通原因而不是由于特殊原因造成的。
这可称为统计稳定性;测量系统的变差必须比制造过程的变差小;变差应小于公差带;测量精度应高于过程变差和公差带两者中精度较高者,一般来说,测量精度是过程变差和公差带两者中精度较高者的十分之一;测量系统统计特性可能随被测项目的改变而变化。
若真的如此,则测量系统的最大的变差应小于过程变差和公差带两者中的较小者。
一、MSA的目的、适用范围和术语二、测量系统的统计特性三、测量系统变差的分类四、测量系统变差(偏倚、重复性、再现性、稳定性、线性)的定义、图示表达方式五、测量系统研究的准备六、偏倚的分析方法、判定准则七、重复性、再现性的分析方法、判定准则八、稳定性的分析方法、判定准则九、线性的分析方法、判定准则十、量型测量系统研究指南十一、量具特性曲线十二、计数型量具小样法研究指南十三、计数型量具大样法研究指南十四、案例研究第三:PPAP 生产件批准程序PPAP的目的是用来确定供方是否已经正确理解了顾客工程设计记录和规范的所有要求,并且在执行所要求的生产节拍条件下的实际生产过程中,具有持续满足这些要求的潜能,是目前最完善的供应商选择与控制系统。
质量五大工具
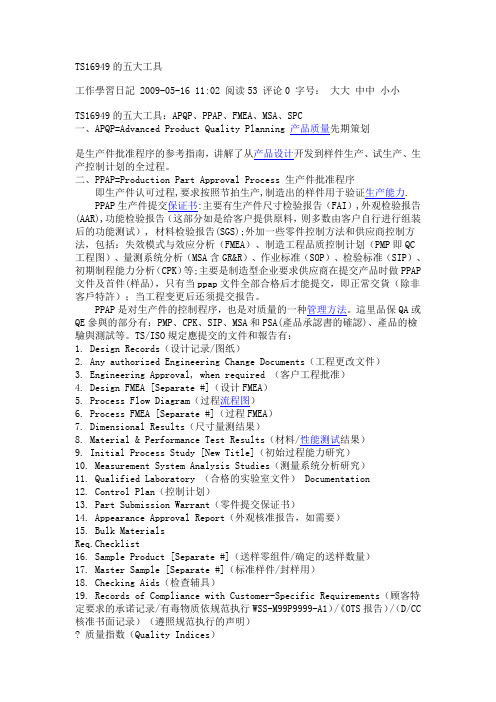
TS16949的五大工具工作學習日記 2009-05-16 11:02 阅读53 评论0 字号:大大中中小小TS16949的五大工具:APQP、PPAP、FMEA、MSA、SPC一、APQP=Advanced Product Quality Planning 产品质量先期策划是生产件批准程序的参考指南,讲解了从产品设计开发到样件生产、试生产、生产控制计划的全过程。
二、PPAP=Production Part Approval Process 生产件批准程序即生产件认可过程,要求按照节拍生产,制造出的样件用于验证生产能力.PPAP生产件提交保证书:主要有生产件尺寸检验报告(FAI),外观检验报告(AAR),功能检验报告(这部分如是给客户提供原料,则多数由客户自行进行组装后的功能测试), 材料检验报告(SGS);外加一些零件控制方法和供应商控制方法,包括:失效模式与效应分析(FMEA)、制造工程品质控制计划(PMP即QC 工程图)、量测系统分析(MSA含GR&R)、作业标准(SOP)、检验标准(SIP)、初期制程能力分析(CPK)等;主要是制造型企业要求供应商在提交产品时做PPAP 文件及首件(样品),只有当ppap文件全部合格后才能提交,即正常交貨(除非客戶特許);当工程变更后还须提交报告。
PPAP是对生产件的控制程序,也是对质量的一种管理方法。
這里品保QA或QE參與的部分有:PMP、CPK、SIP、MSA和PSA(產品承認書的確認)、產品的檢驗與測試等。
TS/ISO規定應提交的文件和報告有:1. Design Records(设计记录/图纸)2. Any authorized Engineering Change Documents(工程更改文件)3. Engineering Approval, when required (客户工程批准)4. Design FMEA [Separate #](设计FMEA)5. Process Flow Diagram(过程流程图)6. Process FMEA [Separate #](过程FMEA)7. Dimensional Results(尺寸量测结果)8. Material & Performance Test Results(材料/性能测试结果)9. Initial Process Study [New Title](初始过程能力研究)10. Measurement System Analysis Studies(测量系统分析研究)11. Qualified Laboratory (合格的实验室文件) Documentation12. Control Plan(控制计划)13. Part Submission Warrant(零件提交保证书)14. Appearance Approval Report(外观核准报告,如需要)15. Bulk MaterialsReq.Checklist16. Sample Product [Separate #](送样零组件/确定的送样数量)17. Master Sample [Separate #](标准样件/封样用)18. Checking Aids(检查辅具)19. Records of Compliance with Customer-Specific Requirements(顾客特定要求的承诺记录/有毒物质依规范执行WSS-M99P9999-A1)/《OTS报告)/(D/CC 核准书面记录)(遵照规范执行的声明)? 质量指数(Quality Indices)– Cpk- 稳定过程的能力指数,s的估计基于子组内变差–Ppk- 性能指数,s的估计基于总体变差? 初始过程研究的接受准则? Index Value > 1.67 :过程满足顾客的要求,批准后可以按照控制计划开始生产。
APQP主要流程如下

APQP中文意思是:产品质量先期策划(或者产品质量先期策划和控制计划)是QS9000/TS16949质量管理体系的一部分。
产品质量策划是一种结构化的方法,用来确定和制定确保某产品使顾客满意所需的步骤。
目标是促进与所涉及每一个人的联系,以确保所要求的步骤按时完成。
有效的产品质量策划依赖于高层管理者对努力达到使顾客满意这一宗旨的承诺。
APQP的特点a)目标明确:满足顾客要求,不断改进。
b)按规定的方法和组织形式进行策划。
c)应用各类分析工具:FMEA,MSA,SPC、流程图,QFD等。
d)保证跨职能活动的效率:横向协调小组。
APQP主要流程如下:1. APQP要素的策划。
2. APQP要素的执行。
3. 通过在FPDS里程碑中的小组来监控执行要素的“质量事件”,以及时间安排。
4. 发出解决方案。
5. 状态报告(至少在FPDS里程碑)。
APQP主要的五个过程,五个里程碑:1 计划和定义本过程的任务:•如何确定顾客的需要和期望,以计划和定义质量大纲;•做一切工作必须把顾客牢记心上;•确认顾客的需要和期望已经十分清楚。
2 产品的设计与开发本过程的任务和要点:•讨论将设计特征发展到最终形式的质量策划过程诸要素;•小组应考虑所有的设计要素,即使设计是顾客所有或双方共有;•步骤中包括样件制造以验证产品或服务满足“服务的呼声”的任务;•一个可行的设计应能满足生产量和工期要求,也要考虑质量、可靠性、投资成本、重量、单件成本和时间目标;•尽管可行性研究和控制计划主要基于工程图纸和规范要求,但是本章所述的分析工具也能猎取有价值的信息以进一步确定和优先考虑可能需要特殊的产品和过程控制的特性;•保证对技术要求和有关技术资料的全面、严格的评审;•进行初始可行性分析,以评审制造过程可能发生的潜在问题。
3 过程设计和开发本过程的任务和要点:—保证开发一个有效的制造系统,保证满足顾客的需要、要求和期望;—讨论为获得优质产品而建立的制造系统的主要特点及与其有关的控制计划。
- 1、下载文档前请自行甄别文档内容的完整性,平台不提供额外的编辑、内容补充、找答案等附加服务。
- 2、"仅部分预览"的文档,不可在线预览部分如存在完整性等问题,可反馈申请退款(可完整预览的文档不适用该条件!)。
- 3、如文档侵犯您的权益,请联系客服反馈,我们会尽快为您处理(人工客服工作时间:9:00-18:30)。
【APQP 管理程序】
版本: B 制订日期:20**-09-20 版次:1生效日期:20**-09-25 页次:1/4 文件编号:
版本/版次: B-1
生效日期: 20**-09-25
页次: 2/4
文件编号: ***
APQP管理程序
1. 目的:
本公司生产新产品(公司没有做过的产品、总公司产品国产化或公司目前产品进行了生产过程等变动需提交客户批准的产品)之前,建立各项必要步骤, 以确保产品满足顾
客的要求和期望。
2.范围:
适用于公司新产品的准备事项。
客户有特别要求时依照客户要求。
3. 责任和权限
3.1公司最高管理者授权成立APQP小组并对小组的活动提供资源等的支持。
3.2 APQP小组主要职责:确定特殊特性、FMEA的开发、对FMEA中风险较高的工序制定
降低风险的对策、控制计划的开发。
3.3 APQP小组的组长:拟定APQP计划,分配小组成员的职责;领导小组成员执行APQP计
划的各项内容,协调产品开发过程中的问题,主持各阶段的会议并对会议的决议事项
进行跟踪确认。
3.4 APQP担当者执行组长分配的工作,并对计划的执行情况进行定期总结汇报,就执行
过程中的问题向组长汇报。
4. 用语定义:
APQP: Advanced Product Quality Planning and Control Plan
即产品质量先期策划和控制计划
5. 计划和确定项目:
5.1技术部在接到客户新品开发要求订单/协议等或图纸之后,由部门负责人初步进行产
品过程开发分析,确认公司的技术能力能否满足客户的产品要求包括相关法律法规
的要求。
然后召集开发技术课、生产管理课、品保、设备保证课、输入输出课、相
关生产课、会计等开会讨论新产品项目确立事宜:
5.1.1开发技术课负责进行产品的背景介绍,分析竞争对手情况、产品的生命周期、
产品定位、市场前景等,并收集/说明产品相关法律法规和特殊特性(对于国
产化的产品),此外应列出产品的BOM表并确认所有材料可获得,必要时应
要求输入输出课支持。
对于新的技术或培训需求由技术部部长确定并提供支
持。
5.1.2相关生产课应进行制造课可行性分析并提供初始的过程流程图、如果涉及新的
过程和设备/模具,还应和设备部门分析确定初始的新设备清单、新模具清单;
版本/版次:B-1
生效日期: 20**-09-25
页次:3/4
文件编号:*** APQP管理程序
5.1.3品保应与生产课、技术开发课共同确定产品的工程规范要求完整并已经理
解;如果有问题技术开发课应负责确认;
5.1.4品保应对是否需要新的检具、检测仪器和试验设备提出具体的说明,并提供
类似产品的质量数据。
5.1.5生产管理课应根据预估的生产量确认公司的生产能力能否满足以及设备的
需求;
5.1.6会计课根据生产过程流程图、BOM表等进行初期的成本分析。
5.1.7公司总经理根据上述各部门的分析以进行决策。
5.2 新产品导入会议的会议记录上应写清客户具体要求和其他输入(包括技术资料清
单/客户提供的工装清单等)及公司的产品保证计划,如正式立项,总经理授权成
立APQP小组,任命小组组长组织策划工作。
5.2.1 APQP小组成员和组长:
1). 技术部门负责人担任组长,并向以下部门要求相关选定成员:
①开发技术课
②品保课
③生产课
④设备保证课
⑤输入输出课(如果有新供应商开发时)
5.3 必要时可以要求供应商和顾客参与(也可让顾客指定顾客代表或公司指定顾客代
表让顾客批准)。
5.4 实施计划书的作成、发行
5.4.1 APQP小组组长作成APQP计划。
计划应确保能满足客户时间进度要求并
应有一定的提前期。
5.4.2计划应明确各阶段召开的会议,至少应包括:新产品立项会议、过程设
计开发检讨会议、试生产安排会议、试生产总结会议、量产前确认会议
等。
5.5 APQP小组在确认所有事项后填写《小组可行性承诺》(对于国产化的产品,可以
省掉)
6. 过程的设计和开发:
本阶段APQP小组应完成以下内容:
1) 过程流程图;
2) 场地平面布局图(根据过程流程图分析产品相关的物流等拟定,相关支持。