扩孔切削参数参考表
常用切削参数表

超过机床最大转速。)(安全距离3mm。)
常用切削参数表
切削刀具/切削类型 粗铣 盘铣刀 精铣 立铣刀 铰刀 粗镗刀(2刃) 粗镗刀(2刃) 精镗刀(1刃) 麻花钻 合金钻头 可转位钻头 扩孔钻 普通丝锥 合金丝锥 螺纹铣刀 粗镗刀 麻花钻 铣 铰 粗镗 半精镗 精镗 切削速度(m/min) 100-120 150-180 80—100 3—8 100-120 120-140 160-180 30 80 80 30 20 4 70-90 160 30 每齿进给(mm/齿) 0.2 0.1 0.2 0.1 0.2 0.15 0.1 0.15 0.15 0.2 0.15 螺距P(mm/r) 螺距P(mm/r) 0.15 0.15 0.15
钻
扩 攻丝 铣螺纹 倒角
切削条件:无内冷,一般材料(如钢、铸离3mm。)
削参数表
备注 总加工长度=加工长度+1个刀具直径+20mm 齿数按实际刀具 注意:退刀时间(齿数按实际刀具) 2齿 2齿 1齿 2齿(注意:加工长度计算考虑刀尖3mm、出孔口3mm) 2齿 1齿 2齿 注意:退刀时间(1齿) 注意:退刀时间(1齿) 齿数按实际刀具 1齿 直径比螺纹孔大6-8mm左右(2齿)
钳工课题钻孔锪孔扩孔铰孔

钳工(qiángōng)基础知识培 训
(4)横刃斜角检查 ;横刃应从中间把两主切削刃和两Φ后面平均分开 ,横刃最 斜角为 50°— 55°。 (5)后刃检查 ,两后面应光洁平整略低于主切削刃 。 (6)试钻检查 ,对要求高的钻头应进行试钻 ,用同等材料(cáiliào)在钻床上试钻 ,要求 两切屑排出及钻削轻快效率高 ,钻后直径达标准 ,孔壁应光洁。
图-1 标准麻花钻的刃磨角度 图 -2 标准麻花钻的刃磨方法
第十五页,共九十页。
钳工(qiángōng)基础知识培 训
为保证钻头中心处磨出较大的后角 ,还应作适当的右移运动 , 刃磨时两手动作 的配合要谐调自然 ,不断反复 ,两后面经常轮换 ,至达到刃磨要求为止。 ( 4)钻头的冷却。钻头刃磨压力不宜(bùyí)过大 ,并要求经常浸入水中冷却 ,以 防止因过退火而降低硬度 ,关键在于刃磨时压力要适宜 ,以不使钻头发蓝为宜。
钳工(qiángōng)基础知识培 训
(3)主偏角检查 ,把钻 头切削部分向上竖起 ,两 眼平视 ,由于两主切削 刃一前一后会产生视 差 ,往往感到左刃尖 (前刃 )高于右刃尖 (后 刃 ) ,所以(suǒyǐ)要旋转 180°反复看几次 ,如果结 果一样 , 说明主偏角对 称。
第十七页,共九十页。
检查方法有两种 :一种是用角度样板检验 ,另一种是用目测检验。检验项目 有 6个 ,即锋角、切削刃、偏角、刃斜角、刃面钻头角度的检查。
目测的方法是 :
( 1)顶角检查 ,约等于 120°,由两主切削刃的夹角构成 。 ( 2)主切削刃检查 ,两主切削刃长度相等 ,可用钢尺、标卡尺测量 。
第十六页,共九十页。
钻孔: 用钻头在实体材料(cáiliào)上加工圆孔的方法称为
钻孔。 钻孔时,工件固定,钻头安装在钻床主轴
钻孔(扩孔与铰孔)

钻孔(扩孔与铰孔)各种零件的孔加工,除去一部分由车、镗、铣等机床完成外,很大一部分是由钳工利用钻床和钻孔工具(钻头、扩孔钻、铰刀等)完成的。
钳工加工孔的方法一般指钻孔、扩孔和铰孔。
用钻头在实体材料上加工孔叫钻孔。
在钻床上钻孔时,一般情况下,钻头应同时完成两个运动;主运动,即钻头绕轴线的旋转运动(切削运动);辅助运动,即钻头沿着轴线方向对着工件的直线运动(进给运动),钻孔时,主要由于钻头结构上存在的缺点,影响加工质量,加工精度一般在IT10级以下,表面粗糙度为Ra12.5μm左右、属粗加工。
一、钻床常用的钻床有台式钻床、立式钻床和摇臂钻床三种,手电钻也是常用的钻孔工具。
1.台式钻床简称台钻,是一种在工作台上作用的小型钻床,其钻孔直径一般在13mm以下。
台钻型号示例:Z 4 0 1 2主参数:最大钻孔直径型号代号:台式钻床类别代号:钻床由于加工的孔径较小,故台钻的主轴转速一般较高,最高转速可高达近万转/分,最低亦在400转/分左右。
主轴的转速可用改变三角胶带在带轮上的位置来调节。
台钻的主轴进给由转动进给手柄实现。
在进行钻孔前,需根据工件高低调整好工作台与主轴架间的距离,并锁紧固定(结合挂图与实物讲解示范)。
台钻小巧灵活,使用方便,结构简单,主要用于加工小型工件上的各种小孔。
它在仪表制造、钳工和装配中用得较多。
2.立式台钻简称立钻。
这类钻床的规格用最大钻孔直径表示。
与台钻相比,立钻刚性好、功率大,因而允许钻削较大的孔,生产率较高,加工精度也较高。
立钻适用于单件、小批量生产中加工中、小型零件。
3.摇臂钻床它有一个能绕立柱旋转的摇臂、摇臂带着主轴箱可沿立柱垂直移动,同时主轴箱还能摇臂上作横向移动。
因此操作时能很方便地调整刀具的位置,以对准被加工孔的中心,而不需移动工件来进行加工。
摇臂钻床适用于一些笨重的大工件以及多孔工件的加工。
二、钻头钻头是钻孔用的刀削工具,常用高速钢制造,工作部分经热处理淬硬至62~65HRC。
钻孔时的切削用量
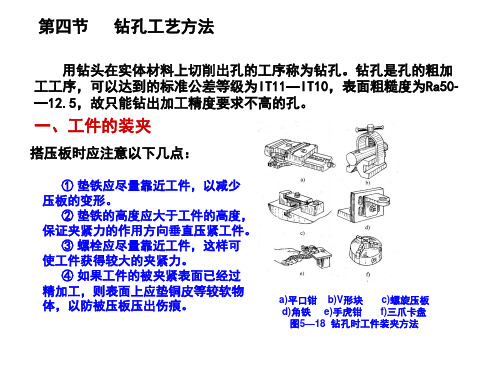
钻孔工艺方法
用钻头在实体材料上切削出孔的工序称为钻孔。钻孔是孔的粗加 工工序,可以达到的标准公差等级为IT11—IT10,表面粗糙度为 Ra50—12.5,故只能钻出加工精度要求不高的孔。
一、工件的装夹
搭压板时应注意以下几点:
① 垫铁应尽量靠近工件,以减少 压板的变形。 ② 垫铁的高度应大于工件的高度, 保证夹紧力的作用方向垂直压紧工件。 ③ 螺栓应尽量靠近工件,这样可 使工件获得较大的夹紧力。 ④ 如果工件的被夹紧表面已经过 精加工,则表面上应垫铜皮等较软物 体,以防被压板压出伤痕。
a)平口钳 b)V形块 c)螺旋压板 d)角铁 e)手虎钳 f)三爪卡盘 图5—18 钻孔时工件装夹方法
第四节
钻孔工艺方法
二、一般工件的钻孔方法
钻孔开始,先调整钻头和工件的位置,使钻尖 对准钻孔中心,然后试钻一浅坑。
通孔在将要钻穿时,必须减小进给量,如果 采用自动进给,要改换成手动进给。 钻不通孔时,可按钻孔深度调整挡块, 并通过测量实际尺寸来控制钻孔深度。 钻深孔时,一般钻进深度达到钻头直径 的3倍时,要退出钻头排屑,以后每钻进一定深度, 提起钻头排屑一次,以免切屑阻塞而扭断钻头。 钻直径较大的孔(一般直径大于 30mm),可分两次钻削,先选用0.5—0.7倍的钻 头直径钻底孔,然后再用所需直径钻头扩孔。
三、钻孔时切削液的使用
表5-9 钻孔时使用的切削液
工件材料 切削液(体积分数)
各类结构钢
不锈钢,耐热钢 纯铜、黄铜、青铜 铸铁 铝及铝合金 有机玻璃
3—5%乳化液,7%硫化乳化液
3%肥皂加2%亚麻油水溶液,硫化切削油 不用,5%—8%乳化液 不用,5%—8%乳化液,煤油 不用,5%—8%乳化液,煤油,煤油与菜油的混合油 5%—8%乳化液,煤油
(完整版)钻削切削用量选择参考表

180~230
6
钛及钛合金(纯钛)
110~200
30
钛及钛合金(α及α+β)
300~360
12
钛及钛合金(β)
275~350
7.5
碳
18~21
塑料
30
硬橡胶
30~90
四、硬质合金钻头切削用量选择
钻孔的进给量(mm/r)
钻头直径do(mm)
σb550~85①
淬硬钢硬度HRC≤40
淬硬钢硬度HRC40
125~175
24
中碳钢(~0.50C)
175~225
20
高碳钢(~0.90C)
175~225
17
合金低碳钢(0.12~0.25C)
175~225
21
合金中碳钢(0.25~0.65C)
175~225
15~18
马氏体时效钢
275~325
17
不锈钢(奥氏体)
135~185
17
不锈钢(铁素体)
135~185
0.47~0.56
25~30
0.45~0.55
0.32~0.40
0.27
30~50
0.60~0.70
0.40~0.50
0.30~0.40
1.0~1.2
0.70~0.80
注:
1.表列数据适用于在大刚性零件上钻孔,精度在H12~H13级以下(或自由公差),钻孔后还用钻头、扩孔钻或镗刀加工,在下列条件下需乘修正系数;
不带护锥及带护锥的60°复合中心钻
5
0.06
12~25
不带护锥及带护锥的60°复合中心钻
6.3
0.08
12~25
机械加工切削参数表

常用材料机械加工切削参数推荐表共 26 页2015年9月目录1 切削用量选定原则 ........................................2 车削加工切削参数推荐表 ..................................2.1 车削要素..............................................2.2 车削参数.............................................3 铣削加工切削参数推荐表 ..................................3.1 铣削要素..............................................3.2 铣削参数..............................................4 磨削加工切削参数推荐表 ..................................4.1 磨削要素 (23)4.2 平面磨削..............................................4.3 外圆磨削..............................................4.4 内圆磨削..............................................1 切削用量选定原则选择机械加工切削用量就是指具体确定切削工序的切削深度、进给量、切削速度及刀具耐用度。
选择切削用量时,要综合考虑生产率、加工质量和加工成本。
从切削加工生产率考虑:切削深度、进给量、切削速度中任何一个参数增加一倍,都可提高生产率一倍。
从刀具耐用度考虑:应首先采用最大的切削深度,再选用大的进给量,然后根据确定的刀具耐用度选择切削速度。
从加工质量考虑:精加工时,采用较小的切削深度和进给量,采用较高的切削速度。
F进给量

铣削切削参数计算表(附例证)铣削切削参数计算表符号术语单位公式V 切削速度m/minN 主轴转速r/minVf 工作台进给量(进给速度)mm/min Vf=fznznmm/r Vf=fnnfz 每齿进给量mmfn 每转进给量mm/rQ 金属去除率cm3/minDe 有效切削直径mm3.3.1计算切削用量(1)钻Φ23的孔。
①进给量小直径钻头主要受钻头的刚性及强度限制大,在条件允许的情况下,应取较大的进给量,以降低加工成本,提高生产效率。
普通麻花钻削进给量可以按以下经验公式计算:f =(0.01~0.02)d0 (3-1)f—进给量d0??—孔的直径则由(3-1)得:f =(0.01~0.02)×23=0.23~0.46由于零件在加工23mm孔时属于低刚度零件,故进给量应乘系数0.75,则f=(0.23~0.46)×0.75=0.1725~0.3mm/r,查表得出,现取f=0.25mm/r。
此工序采用Φ23的麻花钻。
所以进给量f= 0.25mm/z②钻削速度表3-2普通高速钢钻头钻削速度参考值单位:m/min工件材料低碳钢中、高碳钢合金钢铸铁铝合金钢合金切削速度25-30 20-25 15-20 20-25 40-70 20-40切削速度:根据表3-2可得切削速度V=20m/min。
根据手册可得:nw=300r/min,故切削速度为③切削工时l=23mm,l1=13.2mm.查《工艺手册》可得,切削工时计算公式:(3-2)1—切出量2—切出量—行程量①扩孔的进给量由《切削用量手册》可得得扩孔钻扩Φ24.8的孔时的进给量,并根据机床规格选取F=0.3 mm/z②切削速度扩孔钻扩孔的切削速度,由《工艺手册》可得:V=0.4V 钻(3-3)其中V 钻为用钻头钻同样尺寸的实心孔时的切削速度.故V=0.4×21.67=8.668m/min按机床选取nw =195r/min.③切削工时切削工时时切入1=1.8mm,切出2=1.5mm,根据公式(3-2)得:①粗铰孔时的进给量根据有关资料介绍,铰孔时的进给量和切削速度约为钻孔时的1/2~1/3,故F=1/3f钻=1/3×0.3=0.1mm/r (3-4)所以:V=1/3V钻=1/3×21.67=7.22m/min②切削速度按机床选取nw=195r/min,所以实际切削速度③切削工时切削工时,切入l2=0.14mm,切出l1=1.5mm.,根据公式(3-2)得①精铰孔时的进给量根据有关资料介绍,铰孔时的进给量和切削速度约为钻孔时的1/2~1/3,故根据公式(3-4)可得:V=1/3V钻=1/3×21.67=7.22m/min②切削速度按机床选取nw=195r/min,所以实际切削速度③切削工时切削工时,切入l2=0.06mm,切出l1=0mm,根据公式(3-2)得:(2)铣φ55的叉口的上、下端面。
确定切削用量及基本工时

(五)确定切削用量及基本工时。
工序Ⅰ:车削A面。
1.加工条件。
工件材料:灰口铸铁HT200。
σb=145 MP a。
铸造。
加工要求:粗、半精车A面并保证28mm的工序尺寸,R a=3.2µm机床C3163-1。
转塔式六角卧式车床。
刀具:刀片材料。
r =12. a o=6-8 b= -10 o=0.5 K r=90 n=15 2、计算切削用量。
(1)已知长度方向的加工余量为3±0.8mm 。
实际端面的最大加工余量为3.8mm 。
故分二次加工(粗车和半精车)。
长度加工公差IT 12级取-0.46 mm (入体方向)(2)进给量、根据《切削简明手册》(第3版)表1.4 当刀杆尺寸为16mm×25mm,ae≤3mm时,以及工件直径为Φ60mm时(由于凸台B 面的存在所以直径取Φ60mm)ƒ=0.6-0.8mm/r.按C3163-1车床说明书取ƒ=0.6mm/n。
由于存在间歇加工所以进给量乘以k=0.75—0.85 所以:实际进给量f=0.6×0.8=0.48 mm/r按C3163-1车床说明书ƒ=0.53mm/r(3)计算切削速度。
按《切削简明手册》表 1.27 ,切削速度的计算公式为(寿命选T=60min)刀具材料YG6V=C v/(T m·a p x v·f y v) ·kv其中:C v=158 x v=0.15 y v=0.4 M=0.2修正系数K o见《切削手册》表1.28k mv=1.15 k kv=0.8 k krv=0.8 k sv=1.04 k BV=0.81∴Vc =158/( 600.2·20.15·0.530.4) ·1.15·0.8·0.8·0.81·0.97=46.9(m/min)(4)确定机床主轴转速 ns=1000v c/ dw=229.8(r/min)按C3163-1车床说明书n=200 r/min所以实际切削速度V=40.8m/min(5)切削工时,按《工艺手册》表6.2-1由于铸造毛坯表面粗糙不平以及存在硬皮,为了切除硬皮表层以及为下一道工步做好准备T m=(L+L1+L2+L3)/n w x f=0.33(min) L=(65-0)/2=32.5 L1=3、L2=0、L3=02、精车1)已知粗加工余量为0.5mm。
(完整版)加工中心新刀具常用切削参数参照表1
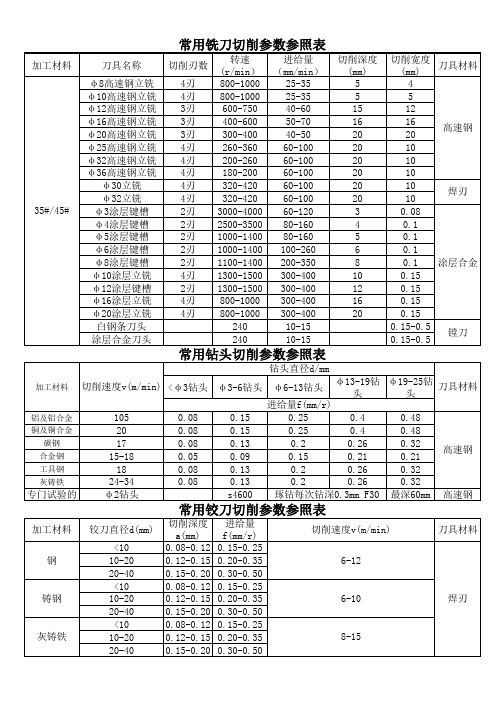
常用圆鼻刀切削参数参照表
加工材料 ZG275-485H
35#/45#
刀具名称
φ16圆鼻刀 φ20圆鼻刀 φ25圆鼻刀 φ25圆鼻刀 φ40圆鼻刀 φ40圆鼻刀 φ63圆鼻刀 φ63圆鼻刀 φ25圆鼻刀 φ32圆鼻刀 φ40圆鼻刀
用途
精加工 精加工 粗加工 精加工 粗加工 精加工 粗加工 精加工 粗加工 粗加工 粗加工
专门试验的
φ2钻头
s4600 琢钻每次钻深0.3mm F30 最深60mm 高速钢
常用铰刀切削参数参照表
加工材料 钢
铰刀直径d(mm)
<10 10-20
切削深度 进给量 a(mm) f(mm/r)
0.08-0.12 0.15-0.25 0.12-0.15 0.20-0.35
切削速度v(m/min) 6-12
2刃 1100-1400 200-350
8
0.1 0.1 涂层合金
φ10涂层立铣
4刃 1300-1500 300-400
10
0.15
φ12涂层键槽
2刃 1300-1500 300-400
12
0.15
φ16涂层立铣
4刃 800-1000 300-400
16
0.15
φ20涂层立铣
4刃 800-1000 300-400
800
60
800
20
700
50
400
60
400
80
120
40-50
120
40-50
用途
钻孔 扩孔 钻孔 钻孔 扩孔 精铰孔 精铰孔
切削宽度 (mm)
刀具材料
高速钢 合金 高速钢 高速钢 高速钢 合金 焊刃
扩孔、锪孔与铰孔 PPT

二、锪孔与锪钻
锪孔是用锪钻刮平孔的端面或切出沉孔的加工 方法。
1.锪钻的种类和特点 锪钻分为柱形锪钻、锥形锪钻和端面锪钻三 种。 1)柱形锪钻 锪圆柱形埋头孔的锪钻。
柱形锪钻起主要切削作用的是端面刀刃, 螺旋槽的斜角就是它的前角(γo=βo=15°), 后角αo=8°。 柱形锪钻前端有导柱,导柱直径与工件上的孔 为紧密的间隙配合,以保证有良好的定心和导 向。 一般导柱是可拆的,也可把导柱和锪钻做成一 体。
颈部 柄部
工作部分
切削部分
校准部分
铰刀的主要结构参数有直径(D), 切削锥角,切削部分和校准部分的前角 (γo )、后角(αo), 校准部分刃带宽 度( f),齿数(z)等。 一般手用铰刀 φ =30′~1°30′ 通孔时φ =15°; 铰削铸铁及脆性材料φ =3°~5° 不通孔时φ =45°
3)端面锪钻 用来锪平孔口端面的锪 钻称为端面锪钻, 如图所示。其端面刀齿 为切削刃,前端导柱用 来导向定心,以保证孔 端面与孔中心线的垂直 度。
2.用麻花钻改磨锪钻 标准锪钻有多种规格, 但一般适用于成批大量 生产,不少场合使用由 麻花钻改磨的锪钻。 1.用麻花钻改磨柱形锪 钻 如图所示为用麻花钻改 磨的柱形锪钻。图(a) 所示为带导柱的锪钻。 图(b)所示为不带导柱 的锪钻,刃磨角度如图 中所示。
(2)切削角度 铰孔的切削余量很小,切削变形也小,一般 铰刀切削部分的前角γo =0°~3°,校准部 分的前角γo =0°,使铰削接近于刮削,可减 小孔壁粗糙度。铰刀切削部分和校准部分的后 角都磨成6°~8°。 (3)校准部分刃带宽度 校准部分的刀刃上留有无后角的棱边,其作 用是引导铰刀铰削方向和修整孔的尺寸,同时 也便于测量铰刀的直径。为了减小棱边与孔壁 的摩擦,棱边一般很窄,通常 f =0.1~0.了避免铰刀校准部分的后面摩擦孔壁,在 校准部分应磨出倒锥。 用机用铰刀铰孔时, 倒锥 量较大(0.04~ 0.08 mm),校准部分有圆柱形校准部分和倒 锥校准部分两段。 手用铰刀切 削速度低,全靠校准部分导向, 所以校准部分较长,整个校准部分都做成倒锥, 而不做成圆柱,倒锥量较小(0.005~0.008 mm)。
数控切削参数表

碳素结构钢的力学性能(GB700-88)注:A、B、C为质量等级,D级为优质级。
铣削加工常用切削速度经验值(m/min)铣削时的切削速度铣削加工每齿进给量推荐值(mm/z)数控铣削每齿进给量经验值H13~H7孔加工方式余量(孔长度小于5倍直径)注:当孔径≤30mm、直径余量≤4mm和孔径>30~80mm、直径余量≤6mm时,采用一次扩孔或一次镗孔。
H7与H8级精度孔加工方式及余量(在实体材料上加工) (mm)注:在铸铁上加工直径为30mm与32mm的孔可用Ф28与Ф30钻头钻一次。
按H7与H8级精度加工已预先铸出或热冲出的孔 (mm)注:1.如果铸出的孔有很大的加工余量时,则第一次粗镗可分为两次或多次;2.如果只进行一次半精镗,由其加工余量为表中“半精镗”和“粗铰或二次半精镗”加工余量之和。
平面精铣、磨削加工方式余量(mm)注:1. 精铣时,最后一次行程前留的雨量应该≥。
2.热处理零件磨削的加工余量系将表中值乘以。
高速钢钻头加工钢件的切削用量高速钢钻头加工铝件的切削用量高速钢钻头扩孔、钻孔的切削用量 (mm/r)高速钢铰刀铰孔的切削用量攻螺纹切削速度 (m/min)钻孔的进给量镗孔切削用量硬质合金端面铣刀的铣削用量不锈钢的铣削用量不锈钢的铣削用量硬质合金车刀粗车外圆及端面的进给量注:1、加工断续表面及有冲击的工件时,表内进给量应乘系数K=~;2、在无外皮加工时,表内进给量应乘第数K=;3、加工耐热钢及其合金时,进给量不大于1mm/r;4、加工淬硬钢时,进给量应减小。
当钢的硬度为44~56HRC时,乘系数K=;当钢的硬度为57~62HRC时,乘系数K=。
5、可转位刀片的允许最大进给量不应超过其刀尖圆弧半径数值的80%。
硬质合金外圆车刀半精车的进给量(参考值) mm/r注:rε=,用于12×12以下刀杆,rε=1mm,用于30×30以下刀杆,rε=2mm,用于30×45及以上刀杆。
钻头切削参数表

14~25
90~118
可锻铸 铁
112~126
~71
27~37
20~30
90~118
球墨铸 铁
190~225
~98
18
14~25
90~118
塑料
30
15~25
118
硬橡胶
30~90
10~20
90~118
(2
加工材料
拉强度抗(T
b/MPa
硬度HBS
进给量f/(mm/r)切削速度V/(m/min)
硬橡胶
30~60
热固性树 脂
60~90
塑料
30~60
玻璃
手进
玻璃纤维 复合材料
198
钻孔切削用量的选
(1)咼速钢钻头钻削不同材料的切削用量
加工
材料
硬度
切削速
度V/(m/
mi n)
钻头直径d/mm
钻头 螺旋 角
/(°)
钻尖角/(°)
布氏
HBS
洛氏
HRB
<3
3~6
6~13
13~19
19~25
进给量f/(mm/r)
铝及铝合
金
45~105
~62
105
32~42
90~118
铝及铝合金
高加 工性
~0.9
0C
175~225
88~96
17
25~35
118
合金钢
~0.25
C
175~225
88~98
21
25~35
118
〜0.65
C
175~225
88~98
15~18ቤተ መጻሕፍቲ ባይዱ
数控切削参数表
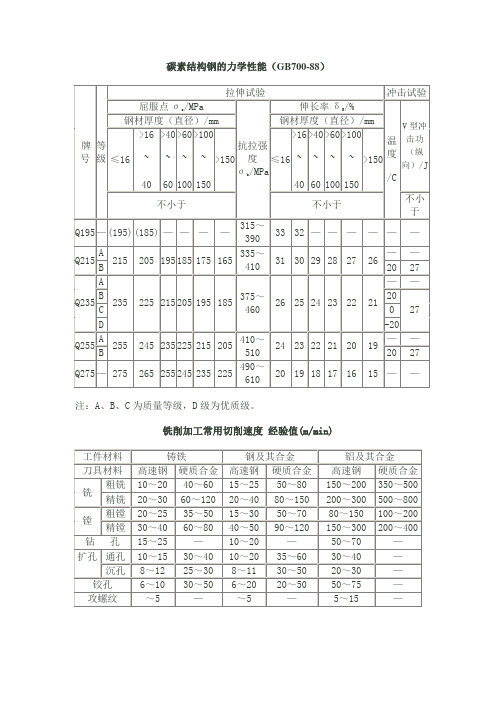
碳素结构钢的力学性能(GB700-88)注:A、B、C为质量等级,D级为优质级。
铣削加工常用切削速度经验值(m/min)铣削时的切削速度铣削加工每齿进给量推荐值(mm/z)数控铣削每齿进给量经验值H13~H7孔加工方式余量(孔长度小于5倍直径)注:当孔径≤30mm、直径余量≤4mm和孔径>30~80mm、直径余量≤6mm时,采用一次扩孔或一次镗孔。
H7与H8级精度孔加工方式及余量(在实体材料上加工) (mm)注:在铸铁上加工直径为30mm与32mm的孔可用Ф28与Ф30钻头钻一次。
按H7与H8级精度加工已预先铸出或热冲出的孔 (mm)注:1.如果铸出的孔有很大的加工余量时,则第一次粗镗可分为两次或多次;2.如果只进行一次半精镗,由其加工余量为表中“半精镗”和“粗铰或二次半精镗”加工余量之和。
平面精铣、磨削加工方式余量(mm)注:1. 精铣时,最后一次行程前留的雨量应该≥。
2.热处理零件磨削的加工余量系将表中值乘以。
高速钢钻头加工钢件的切削用量高速钢钻头加工铝件的切削用量高速钢钻头扩孔、钻孔的切削用量 (mm/r)高速钢铰刀铰孔的切削用量攻螺纹切削速度 (m/min)钻孔的进给量镗孔切削用量硬质合金端面铣刀的铣削用量不锈钢的铣削用量不锈钢的铣削用量硬质合金车刀粗车外圆及端面的进给量注:1、加工断续表面及有冲击的工件时,表内进给量应乘系数K=~;2、在无外皮加工时,表内进给量应乘第数K=;3、加工耐热钢及其合金时,进给量不大于1mm/r;4、加工淬硬钢时,进给量应减小。
当钢的硬度为44~56HRC时,乘系数K=;当钢的硬度为57~62HRC时,乘系数K=。
5、可转位刀片的允许最大进给量不应超过其刀尖圆弧半径数值的80%。
硬质合金外圆车刀半精车的进给量(参考值) mm/r注:rε=,用于12×12以下刀杆,rε=1mm,用于30×30以下刀杆,rε=2mm,用于30×45及以上刀杆。
U钻切削参数
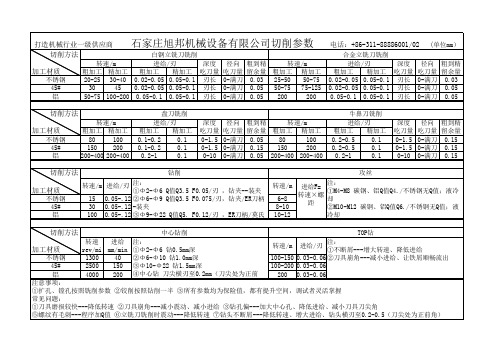
45#
30
45 0.02-0.05 0.05-0.1 刃长 0-满刀 0.05 50-75 75-125
铝
50-75 100-200 0.05-0.1 0.05-0.1 刃长 0-满刀 0.05 200
200
电话:+86-311-88886001/02 (单位mm)
合金立铣刀铣削
进给/刃
深度 径向 粗到精
盘刀铣削
进给/刃
粗加工 精加工
0.1-0.2 0.1
0.1-0.2 0.1
0.2-1
0.1
深度 径向 粗到精
转速/m
吃刀量 吃刀量 留余量 粗加工 精加工
0-1.5 0-满刀 0.05 80
100
0-1.5 0-满刀 0.15 150
200
0-10 0-满刀 0.05 200-400 200-400
100-200 0.03-0.06
铝
4000 200 ④中心钻 刀尖横刃至0.2mm(刀尖处为正前
200 0.03-0.06
注意事项:
①扩孔、镗孔按照铣削参数 ②铰削按照钻削一半 ③所有参数均为保险值,都有提升空间,调试者灵活掌握
常见问题:
①刀具磨损较快---降低转速 ②刀具崩角---减小震动、减小进给 ③钻孔偏---加大中心孔、降低进给、减小刀具刀尖角
冷却
切削方法
中心钻削
TOP钻
加工材质
转速 进给 注: rev/mi mm/min ①Φ2-Φ6 钻0.5mm深
转速/m
进给/刃
注: ①不断屑---增大转速、降低进给
不锈钢
1300 40 ②Φ6-Φ10 钻1.0mm深
1ห้องสมุดไป่ตู้0-150 0.03-0.06 ②刀具崩角---减小进给、让铁屑顺畅流出
车削刀具切削参数参考表

120~180
150~200
120~180
60~120
25~50
80~160
60~160
40~70
60~100 15~25
走刀式电 进刀量 脑车 mm/rev
0.2~0.5
0.02~0.3
0.03~0.15
0.03~0.12
根据螺距大小 确定进刀量
0.02~0.15
0.03~0.12
根据钻头大小 确定进刀量
M =π×D×(L/F)×N÷1000 (M 刀具切削长度(寿命m), D直径mm , L零件长度mm, F进给量, N 加工零件数量) 例子:已知刀具加工寿命为 5000m ,加工材料直径Φ10. ,进给量F为0.1,切削长度为10.0mm,求刀具在寿命范围内能加工多少工件?
N = M*1000/[π×D×(L/F)] =5000*1000/[3.14*10*(10/0.1)] = 1592 pcs
注: 以上数据均参考京瓷、NTK、NACHI等切削工具书。
500~ 3000
硬质合金 麻花钻
丝锥
切削速度 m/min
150~200
180~250
150~200
80~150
25~50
100~200
80~200
40~70
60~100 15~25
走芯式电 进刀量 脑车 mm/rev
寿命 m
0.2~0.5
0.02~0.3
0.03~0.15
0.03~0.12
根据螺距大小 确定进刀量
0.02~0.15
切削速度 m/min
80~120
70~120
50~110
40~80
15~35
机械加工切削全参数表

切削全参数表Document serial number【UU89WT-UU98YT-UU8CB-UUUT-UUT108】常用材料机械加工切削参数推荐表共26页2015年9月1切削用量选定原则选择机械加工切削用量就是指具体确定切削工序的切削深度、进给 量、切削速度及刀具耐用度。
选择切削用量时,要综合考虑生产率、加 工质量和加工成本。
从切削加工生产率考虑:切削深度、进给量、切削速度中任何一个 参数增加一倍,都可提高生产率一倍。
从刀具耐用度考虑:应首先采用最大的切削深度,再选用大的进给 量,然后根据确定的刀具耐用度选择切削速度。
从加工质量考虑:精加工时,采用较小的切削深度和进给量,采用 较高的切削速度。
2车削加工切削参数推荐表 车削要素切削速度v :工件旋转的线速度,单位为m/min 。
进给量f:工件每旋转一周,工件与刀具相对位移量,单位为mm/r 。
切削深度与:垂直于进给运动方向测量的切削层横截面尺寸,单位为 mni ©Ra :以轮廓算术平均偏差评定的表面粗糙度参数,单位为Um 。
L :工件直径,单位为mm 。
切削速度与转速关系:外圆车削示意图 内圆车削示意图Tidn nd / •v = = m/mm1000 318.3lOOOv 318.3v / .n = ---- = ----- r/mm血dV:切削速度,工件旋转的线速度,单位为m/min。
n:工件的转速,单位为r/mino d:工件观察点直径,单位为皿。
车削参数45钢热轧状态(硬度:187HB)外圆车削45钢热轧状态(硬度:187HB)内圆车削45钢调质状态(硬度:28〜32HRC)外圆车削45钢调质状态(硬度:28〜32HRC)内圆车削40Cr钢热轧状态(硬度:212HB)外圆车削40Cr钢热轧状态(硬度:212HB)内圆车削40Cr钢调质状态(硬度:28〜32HRC)外圆车削40Cr钢调质状态(硬度:28〜32HRC)内圆车削H62硬化状态(硬度:164HB)外圆车削H62硬化状态(硬度:164HB)内圆车削2A12-T4固溶处理并时效状态(硬度:105HB)外圆车削2A12-T4固溶处理并时效状态(硬度:105HB)内圆车削TC4固溶处理并时效状态(硬度:320〜380HB)外圆车削TC4固溶处理并时效状态(硬度:320-380HB)内圆车削3铳削加工切削参数推荐表铳削要素铳削速度v:铳刀旋转运动的线速度,单位为m/min。
铝合金切削参数
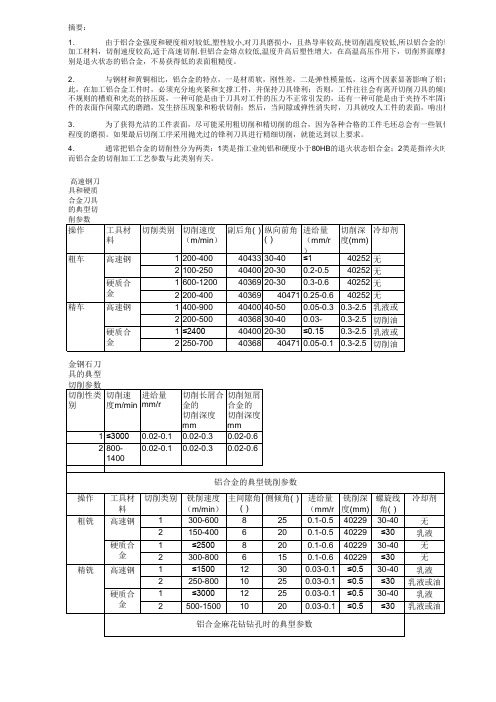
摘要:1.由于铝合金强度和硬度相对较低,塑性较小,对刀具磨损小,且热导率较高,使切削温度较低,所以铝合金的切削加工性较好,加工材料,切削速度较高,适于高速切削.但铝合金熔点较低,温度升高后塑性增大,在高温高压作用下,切削界面摩擦力很大。
容易粘别是退火状态的铝合金,不易获得低的表面粗糙度。
2.与钢材和黄铜相比,铝合金的特点,一是材质软,刚性差,二是弹性模量低,这两个因素显著影响了铝合金的切削加工性此,在加工铝合金工件时,必须充分地夹紧和支撑工件,并保持刀具锋利;否则,工件往往会有离开切削刀具的倾向。
有时工件的表不规则的槽痕和光亮的挤压斑,一种可能是由于刀具对工件的压力不正常引发的,还有一种可能是由于夹持不牢固而引起振颤时,刀件的表面作间隙式的磨蹭,发生挤压现象和粉状切削;然后,当间隙或弹性消失时,刀具就咬人工件的表面,啃出槽痕。
3.为了获得光洁的工件表面,尽可能采用粗切削和精切削的组合,因为各种合格的工件毛坯总会有一些氧化层,致使刀具受程度的磨损。
如果最后切削工序采用抛光过的锋利刀具进行精细切削,就能达到以上要求。
4.通常把铝合金的切削性分为两类:1类是指工业纯铝和硬度小于80HB的退火状态铝合金;2类是指淬火时效状态的变形铝而铝合金的切削加工工艺参数与此类别有关。
高速钢刀具和硬质合金刀具的典型切金钢石刀具的典型铝合金攻螺纹前的钻孔的典铝合金的典型镗孔铝合金的典型铰孔注:冷却剂为煤油-松节油(5:4)混合物;或用约33°E 的矿物油,或优质油.干铰孔的质量不高合金的切削加工性较好,属于易界面摩擦力很大。
容易粘刀;特响了铝合金的切削加工性。
因具的倾向。
有时工件的表面出现不牢固而引起振颤时,刀具在工,啃出槽痕。
一些氧化层,致使刀具受到相当指淬火时效状态的变形铝合金。
m/r)5-40。
机械加工切削全参数表

机械加⼯切削全参数表机械加⼯切削全参数表 Document serial number【UU89WT-UU98YT-UU8CB-UUUT-UUT108】常⽤材料机械加⼯切削参数推荐表共 26 页2015年9⽉⽬录1 切削⽤量选定原则选择机械加⼯切削⽤量就是指具体确定切削⼯序的切削深度、进给量、切削速度及⼑具耐⽤度。
选择切削⽤量时,要综合考虑⽣产率、加⼯质量和加⼯成本。
从切削加⼯⽣产率考虑:切削深度、进给量、切削速度中任何⼀个参数增加⼀倍,都可提⾼⽣产率⼀倍。
从⼑具耐⽤度考虑:应⾸先采⽤最⼤的切削深度,再选⽤⼤的进给量,然后根据确定的⼑具耐⽤度选择切削速度。
从加⼯质量考虑:精加⼯时,采⽤较⼩的切削深度和进给量,采⽤较⾼的切削速度。
2 车削加⼯切削参数推荐表车削要素切削速度v:⼯件旋转的线速度,单位为m/min。
进给量f:⼯件每旋转⼀周,⼯件与⼑具相对位移量,单位为mm/r。
切削深度a:垂直于进给运动⽅向测量的切削层横截⾯尺⼨,单位为pmm。
Ra :以轮廓算术平均偏差评定的表⾯粗糙度参数,单位为µm。
d:⼯件直径,单位为mm。
w外圆车削⽰意图内圆车削⽰意图切削速度与转速关系:3.3181000nddnv ==π m/mindvd v n 3.3181000==π r/min v :切削速度,⼯件旋转的线速度,单位为m/min 。
n :⼯件的转速,单位为r/min 。
d :⼯件观察点直径,单位为mm 。
车削参数45钢热轧状态(硬度:187HB )外圆车削45钢热轧状态(硬度:187HB )内圆车削45钢调质状态(硬度:28~32HRC)外圆车削32HRC)内圆车削45钢调质状态(硬度:28~40Cr钢热轧状态(硬度:212HB)外圆车削40Cr钢热轧状态(硬度:212HB)内圆车削40Cr钢调质状态(硬度:28~32HRC)外圆车削28~32HRC)内圆车削40Cr钢调质状态(硬度:H62硬化状态(硬度:164HB)外圆车削H62硬化状态(硬度:164HB)内圆车削2A12-T4固溶处理并时效状态(硬度:105HB)外圆车削2A12-T4固溶处理并时效状态(硬度:105HB)内圆车削TC4固溶处理并时效状态(硬度:320~380HB)外圆车削380HB)内圆车削TC4固溶处理并时效状态(硬度:320~3 铣削加⼯切削参数推荐表铣削要素铣削速度v :铣⼑旋转运动的线速度,单位为m/min 。
切削余量、基本公示计算

确定切削用量及基本工时切削用量一般包含切削深度、进给量及切削速度三项。
确定方法是先确定切削深度、进给量、在确定切削速度。
6.1 工序2数据计算本工序为粗车(车端面、外圆、镗孔)。
资料为45钢,Rm=670MPa,锻件有外皮,机床为C6140型卧式车床,共建装夹在自定心卡盘。
选用刀具为YT5硬质合金可转位刀;由表1.30*得C6140机床的中心高200mm,选刀杆尺寸,刀片厚度4.5mm,刀具形状为卷屑槽带倒棱型前面刀,前角,后角,主偏角,副偏角,刃倾角,刀尖圆弧半径。
切端面2mm,粗车外圆至。
(1)切端面1).确定切削深度:端面单边加工余量为2mm ,考虑模锻公差后其最大单边余量3.2mm,取。
2).确定进给量f:由表1.4*,在粗车钢料、刀杆尺寸为、、工件直径时,,根具机床C6140(表4.2-9)选择机床的横向进给量。
3).确定切削速度v:根据表1.10*,用YT15硬质合金车刀加工Rm=600~700MPa钢料,,,切削速度。
切削速度修正系数:,,,,。
故,。
按C6140机床转速(表4.2-8)选择,则由得实际切削速度。
(2)粗车外圆1).确定背吃刀量:外圆总加工余量为3.5mm,单边余量为1.75mm,一次走刀完成,=1.75mm.。
2).确定进给量f:由表1.4*,在粗车钢料、刀杆尺寸为、、工件直径时,,根具机床C6140(表4.2-9)选择机床的纵向进给量。
3).确定切削速度v:根据表1.10*,用YT15硬质合金车刀加工Rm=600~700MPa钢料,,,切削速度。
切削速度修正系数:,,,,。
故,。
按C6140机床转速(表4.2-8)选择,则由得实际切削速度。
(4)工时计算1).辅助时间:装夹工件的时间1.5min,变换刀架的时间为 0.2 min,变速或变换进给量的时间为0.5min,启动调节切削液时间为 0.2min,共计 T f =2.4min。
2).根据计算基本时间:总时间为4.111min。