ACC test plan_Template_Charger_V05充电器产品测试项目及要求
士兰微SD45230-评估板_说明书

SD45230_评估板说明书_1.0SD45230 评估板说明书降压型5V/2A 车载充电器声明:♦士兰保留本文档的更改权,恕不另行通知!♦产品提升永无止境,我公司将竭诚为客户提供更优秀的产品!目录1.SD45230降压型5V/2A DEMO规格 (2)2.DEMO原理图 (2)3.DEMO外观 (2)4.元器件列表(BOM) (3)5.测试报告 (3)5.1.测试工具 (3)5.2.开关机测试 (4)5.3.空载-满载动态测试 (5)5.4.输出纹波测试 (6)5.5.输出短路测试 (6)5.6.MOS管DS电压测试 (7)5.7.效率测试 (7)5.8.EMC测试 (9)1.SD45230降压型5V/2A DEMO规格2.DEMO原理图图1 SD45230系统原理图3.DEMO外观4.元器件列表(BOM)5.测试报告5.1.测试工具5.2. 开关机测试Vin=12Vdc ,Po=0W ,开机 Vin=30Vdc ,Po=0W ,开机 通道1:输入电压 5V/格 通道1:输入电压 10V/格 通道2:输出电压 2V/格通道2:输出电压 2V/格Vin=12Vdc ,Po=10W ,开机 Vin=12Vdc ,Po=10W ,关机 通道1:输入电压 5V/格 通道1:输入电压 5V/格 通道2:输出电压 2V/格通道2:输出电压 2V/格Vin=30Vdc ,Po=10W ,开机 Vin=30Vdc ,Po=10W ,关机 通道1:输入电压 10V/格 通道1:输入电压 10V/格 通道2:输出电压 2V/格通道2:输出电压 2V/格5.3. 空载-满载动态测试Vin=12Vdc ,保持时间T=5ms Vin=30Vdc ,保持时间T=5ms Rise rate= Fall rate=0.25A/us Rise rate= Fall rate=0.25A/us 通道1:输出电压 1V/格 通道1:输出电压 1V/格 通道2:输出电流 2A/格通道2:输出电流 2A/格5.4. 输出纹波测试Vin=12Vdc ,Po=10W Vin=30Vdc ,Po=10W 通道1:输出电压纹波20mV/格 通道1:输出电压纹波20mV/格 通道2:输出电流纹波20mA/格通道2:输出电流纹波20mA/格备注:输出电压的纹波跟MOS 管开关的稳定性、电感量大小、输出电容等有关。
拓微集成 TP4055 锂离子电池充电器说明书
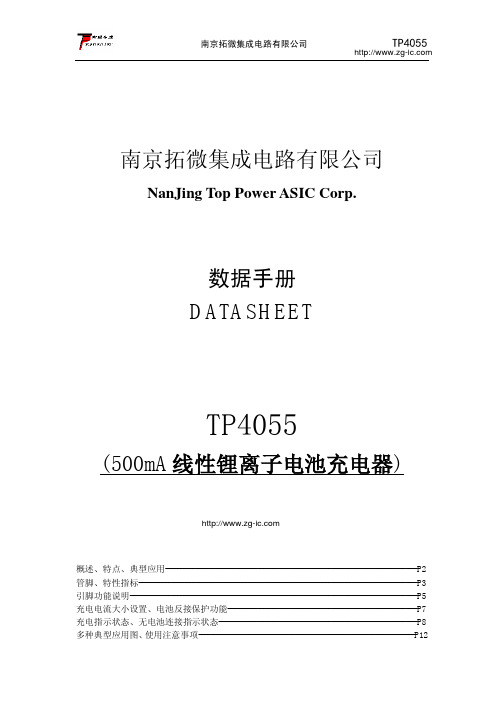
南京拓微集成电路有限公司TP4055南京拓微集成电路有限公司 NanJing Top Power ASIC Corp.数据手册 DATASHEETTP4055(500mA 线性锂离子电池充电器)概述、特点、典型应用-------------------------------------------------------------------------------------P2 管脚、特性指标----------------------------------------------------------------------------------------------P3 引脚功能说明-------------------------------------------------------------------------------------------------P5 充电电流大小设置、电池反接保护功能----------------------------------------------------------------P7 充电指示状态、无电池连接指示状态-------------------------------------------------------------------P8 多种典型应用图、使用注意事项-------------------------------------------------------------------------P12特点·锂电池正负极反接保护;·高达500mA的可编程充电电流;·无需MOSFET、检测电阻器或隔离二极管;·用于单节锂离子电池·恒定电流/恒定电压操作,并具有可在无过热危险的情况下实现充电速率最大化的热调节功能;·可直接从USB端口给单节锂离子电池充电;·最高输入可达9V;·精度达到±1%的4.2V预设充电电压;·自动再充电;·1个充电状态开漏输出引脚;·C/10充电终止;·待机模式下的供电电流为40uA;·2.9V涓流充电;·软启动限制了浪涌电流;·采用5引脚SOT-23封装。
艾顿072907 电源保护设备说明书

Eaton 072907Eaton Moeller® series E-PKZ0 Insulated enclosure, E-PKZ0, H x W x D = 129 x 85 x 124 mm, flush-mounted, rotary handle, black/gray, IP55General specificationsEaton Moeller® series E-PKZ0 Accessory Insulated enclosure0729074015080729075124 mm 129 mm 85 mm 0.224 kgIEC/EN 60947-4-1 CSA Class No.: 3211-05 CSA-C22.2 No. 14 CECSA File No.: 165628 UL UL 508UL Category Control No.: NLRV UL File No.: E36332 CSAProduct NameCatalog Number EANProduct Length/Depth Product Height Product Width Product Weight Certifications0 AAccessoriesIs the panel builder's responsibility. The specifications for the switchgear must be observed.0 W0 WMeets the product standard's requirements.Is the panel builder's responsibility. The specifications for the switchgear must be observed.Does not apply, since the entire switchgear needs to be evaluated.Meets the product standard's requirements.Black-gray rotary knobPE(N) terminalNEMA 1NEMA 12IP55NEMA 3RMeets the product standard's requirements.Meets the product standard's requirements.Is the panel builder's responsibility.eaton-manual-motor-starters-mounting-e-pkz0-accessory-dimensions.eps eaton-manual-motor-starters-enclosure-e-pkz0-accessory-dimensions-002.epseaton-manual-motor-starters-enclosure-e-pkz0-accessory-dimensions-003.epseaton-manual-motor-starters-enclosure-e-pkz0-accessory-dimensions.eps eaton-manual-motor-starters-enclosure-e-pkz0-accessory-3d-drawing-003.epsDA-CE-ETN.E-PKZ0-GIL03402029ZDA-CD-e_pkz0_gDA-CS-e_pkz0_gRated operational current for specified heat dissipation (In) Product category10.11 Short-circuit ratingEquipment heat dissipation, current-dependent PvidHeat dissipation capacity Pdiss10.4 Clearances and creepage distances10.12 Electromagnetic compatibility10.2.5 Lifting10.2.3.1 Verification of thermal stability of enclosuresFitted with:Degree of protection (front side)10.2.3.2 Verification of resistance of insulating materials to normal heat10.2.3.3 Resist. of insul. mat. to abnormal heat/fire by internal elect. effects10.8 Connections for external conductors10.9.2 Power-frequency electric strength DibujoseCAD model Instrucciones de instalación mCAD modelIs the panel builder's responsibility.Degree of protectionIP55NEMA OtherAmbient operating temperature - max40 °C10.7 Internal electrical circuits and connectionsIs the panel builder's responsibility.10.10 Temperature riseThe panel builder is responsible for the temperature rise calculation. Eaton will provide heat dissipation data for the devices.Static heat dissipation, non-current-dependent Pvs0 W10.9.3 Impulse withstand voltageIs the panel builder's responsibility.Enclosure materialPlasticAmbient operating temperature - min-25 °C10.2.2 Corrosion resistanceMeets the product standard's requirements.10.6 Incorporation of switching devices and componentsDoes not apply, since the entire switchgear needs to be evaluated.10.2.4 Resistance to ultra-violet (UV) radiationPlease enquire10.2.7 InscriptionsMeets the product standard's requirements.10.5 Protection against electric shockDoes not apply, since the entire switchgear needs to be evaluated.ModelBuilt-in10.13 Mechanical functionThe device meets the requirements, provided the information in the instruction leaflet (IL) is observed.10.2.6 Mechanical impactDoes not apply, since the entire switchgear needs to beEaton Corporation plc Eaton House30 Pembroke Road Dublin 4, Ireland © 2023 Eaton. Todos los derechos reservados. Eaton is a registered trademark.All other trademarks areproperty of their respectiveowners./socialmediaevaluated.Is the panel builder's responsibility.Does not apply, since the entire switchgear needs to be evaluated.0 W10.9.4 Testing of enclosures made of insulating material 10.3 Degree of protection of assembliesHeat dissipation per pole, current-dependent Pvid。
BYD BF1550 5V1A 手机充电器方案

MTL5500模块AC电源适配器MPA5500及配套配件PCL45USB的说明书

The given data is only intended as a product description and should not be regarded as a legal warranty of properties or guarantee.In the interest of further technical developments, we reserve the right to make design changes.The MPA5500 enables any MTL5500 module that is normally powered from a nominal 24V DC supply (i.e. those that are not loop-powered) to be powered from a high-voltage AC supply.It plugs into the power socket (terminals 13 and 14) of an MTL5500 module and clips securely onto the module housing. The 25V DC power output from the adaptor is sufficient to supply a single module and can be connected to any normal AC power source.MPA5500MPA5500SPECIFICATIONInput voltage85 – 265V AC, (45–65Hz)Efficiency71% typ. at 230V ACPower dissipation1.2W typ at 230V AC.Input terminalsCage-clamp terminals accommodating conductors upto 1.5mm 2stranded or 16AWG single-core Input protectioninternal fuse, not user serviceable Output voltage25Vdc ± 10%Output current120mA at 25VAmbient temperatureOperating: –20 to +60°C Storage: –40 to +80°C MountingPlugs into and clips onto MTL5500 range I/O moduleIt is not for use with any equipment other than MTL5500.Humidity5 to 95% relative humidity MechanicalIngress Protection: IP20Material: polycarbonate Weight: 28g approx.Standards complianceEN 61326, EN 61010SPECIFICATIONPCL45USB hardware LocationSafe area ConnectionsPC side: USB B(F) socketConverter side: cable with 3.5mm jackplug, 3-pole for MTL4500 and MTL5500 range of converters. An adapter cable is provided for other earlier MTL converters.Cable lengthsConverter side (fitted): 1.5mUSB cable A(M) to B(M) (supplied): 2m Ambient temperature limits–10°C to +60°C operating –20°C to +70°C storage Humidity5 to 95% relative humidity (non-condensing)Weight200gPCS45 Configuration softwareCompatible with Windows XP, Win7, Win8.Consult MTL for operation with any other operating system.Software mediumPCS45 supplied on CDUpdates are available at Recommended minimum PC configurationMicrosoft Windows XP, Win7, Win820MB of available hard disc space CD ROM driveAvailable USB portPrinter (local or network)The PCS45/PCL45USB configurator allows MTL converters to be configured from a standard PC running a Microsoft® Windows® operating system. It comprises PC software, provided on a CD (PCS45), and an ATEX certified interfacing link (PCL45USB). Converters can be configured from the safe area, while on-line, and configurations can be saved to disk and printed out when required. It is suitable for use with MTL4000, MTL4500, MTL5000 and MTL5500 range of products.The given data is only intended as a product description and should not be regarded as a legal warranty of properties or guarantee.In the interest of further technical developments, we reserve the right to make design changes.SPECIFICATION See also common specificationAC input range85Vac to 264Vac, 47 to 63Hz DC input range120Vdc to 375Vdc DC output24V (adjustable 24-28V) Output current2.5A (3,75A for 5s)Main interruption holdup time >20ms Efficiency90%Input to Output isolation 4kVacIsolation Input/output to ground 1.5kV a cHousing material AluminiumDimensions L x W x H 121 x 32 x 125mm Weight 370g Wire size0.3 to 3.3mm 2, AWG 22-12 with removable terminals Operating Temperature -20°C to +80°C Storage Temperature -25°C to +85°CSPECIFICATIONAvailable in 4 different lengths:PB - 8T = 8 connectors and loops PB - 16T = 16 connectors and loops PB - 24T = 24 connectors and loops PB - 32T = 32 connectors and loops Insulation material :PVCConductor :24 strands of 0.2mm dia (0.75mm 2) standard copper Insulation thickness :0.5 to 0.8 mm Current rating :12A maxOperating temperature range :–20ºC to +60ºCMax voltage drop on 32 modules drawing 130mA max :0.5VCHOOSING A POWERBUS KITChoose a powerbus where the number of power plugs is greater than or equal to the number of isolators to be powered and if necessary cut the powerbus to the required number of terminations.Note: To reduce the risk of excessive voltage drop or overcurrent do not connectpowerbuses in series.A general purpose 24V dc power supply for use with MTL isolator and barrier product ranges. Single 24V output with adjustable voltage and status indication.For mounting on 35mm top hat DIN rail.(replacement for MTL5991)The given data is only intended as a product description and should not be regarded as a legal warranty of properties or guarantee.In the interest of further technical developments, we reserve the right to make design changes.SPECIFICATIONConstructionGlass reinforced polycarbonate base - DX070Glass reinforced polyester base - DX170Transparent polycarbonate lid ProtectionDust-tight and water-jet proof to IEC529:IP65Lid fixingCaptive fixing screwsWeight (excluding barriers/isolators) kgDX070 0.8DX170 2.6Items providedDIN rail - fittedETL7000 Earth terminals (2 x) - fitted "Take care IS" front adhesive label Cable trunking (DX170 only)Note: Isolators are not included.MountingWall fixing lugs provided. For further details refer to INM5500.Tagging and earth railAccommodates MTL5500 range of accessories.Permitted locationSafe (non-hazardous) areaDIMENSIONS (mm) AND MOUNTINGNote: N. America/Canada - E nclosures are rated NE MA 4X so can be used in Class 1, Division 2 (gases) location, but check with local requirements and ensure all cable entries also conform. Additional warning label will be required on or near the enclosure, see installation details. Not suitable for Class II or III, Division 2 hazardous locations.Approximate capacities (on DIN rail between earth terminals)Number of MTL5500 isolatorsDX0704(2)*DX17010(8)** Use these figures when IMB57 mounting blocks for tagging/earth are included.Ambient temperature limitsDependent on units fitted. See instruction manual INM5500.DX170The given data is only intended as a product description and should not be regarded as a legal warranty of properties or guarantee.In the interest of further technical developments, we reserve the right to make design changes.MTL5500 range of isolators mount quickly and easily onto standard DIN rail. A comprehensive range of accessories simplifies earthing and tagging arrangements.Type AType BTH5000DIN-railSee also‘MTL5500 range of powerbus kits'MOUNTINGTHR2 DIN rail,1m lengthDIN rail to EN50022; BS5584; DIN46277MS010 DIN rail module spacer, 10mm, pack of 5Grey spacer, one required between each MTL5533 or MTL5995-PS and any adjacent module on a DIN rail, to provide 10mm air-circulation space between modulesEARTH RAILS AND TAG STRIPIMB57 Insulating mounting blockOne required at each end of a tagging strip/earth rail. Suitable for low-profile (7.5mm) and high-profile (15mm) symmetrical DIN rail.ETM7 Earth terminal, bag of 50For terminating cable screens and 0V returns on the ERL7earth rail. For cables ≤ 4mm 2. Exact dimension dependent on manufacturer.TAG57 Tagging strip, 1m lengthCut to size. Supplied with tagging strip label suitable for MTL5000 or MTL5500 modules.TGL57 Tagging strip labels, set of 10 x 0.5mSpares replacement, for use with TAG57 tagging strip. Suitable for MTL5000 or MTL5500 modules.INDIVIDUAL ISOLATOR IDENTIFICATIONTH5000 tag holdersEach isolator may be fitted with a clear plastic tag holder, as shown below. Order TH5000, pack of 20.CONNECTORSEach MTL5500 unit is supplied with signal and power connectors, as applicable.Spares replacement connectors are available separately; see ordering information.ERB57S Earth-rail bracket, straightNickel-plated; supplied with two push fasteners, one (14mm,35mm 2) earth-rail clamp and one (10mm, 16mm 2) earth clamp.ERL7 Earth rail, 1m lengthNickel-plated; may be cut to length.warranty of properties or guarantee.In the interest of further technical developments, we reserve the right to make design changes.• Total flexibility • Special functions • Reduce wiring • Signal conditioning • Simplify installation• HART® integrationABB AutomationS100, INFI90, S800EmersonDelta V, M Series, S Series GE Bently-Nevada HIMAHIMaxHoneywellPMIO, C200, C300, UPIO, Safety Manager, USIO Rockwell AutomationICS Triplex, PlantguardSchneider ElectricFoxboro I/A, Triconex Trident/Tricon, Modicon SiemensET200, S7YokogawaCentum R3, VP, Prosafe RS, CS3000The MTL4500/MTL4600 range of backplanes, enclosures and other accessories provide comprehensive, flexible and remarkably compact mounting facilities for system vendors, original equipment manufacturers and end users alike.CUSTOMISED BACKPLANESEaton provides a complete design and manufacturing service for MTL customised backplanes. Customised backplanes give the vendors and users of process control and safety systems the opportunity to integrate MTL4500/MTL4600/HART® modules directly into their system architecture. As there are no hazardous-area circuits on the backplanes, customised versions can be produced without the need for IS certification, so simplifying design and lowering costs.UNIVERSAL CUSTOM BACKPLANESThe 'universal' backplane allows a fast and economic approach to providing a custom interface. Where tight time schedules exist, the backplane can be installed to allow the panel building and wiring to be completed. The customised adapter card can then be plugged in at any time up to integrated test.ADAPTER CARDSAdapter cards already exist for many of the DCS companies. In addition there is a range of general purpose cards that offer reduced wiring for use with specific MTL modules. These are also available in left- and right-hand versions to ease panel wiring.STANDARD MTL BACKPLANESStandard MTL backplanes are available to accommodate 4, 8, 16, or 24 modules using screw-clamp connectors for the safe-area circuits. On an individual backplane, any module can be plugged into any position and module types can be mixed. For 8-, 16- and 24-way backplanes, screw-clamp connectors which plug into the backplanes provide primary and secondary 24V dc power supplies. Power to several 8- or 16-way backplanes can be interconnected to reduce and simplify wiring – see instruction manual INM4500/INM4600 for details.OPTIONAL ACCESSORIESOptional accessories include colour coded tagging strip kits for all three sizes of backplane and earth rail kits for 8 and 16-way versions. Mounting accessories are available for surface (all backplanes), T-section and G-section DIN-rail (8- and 16-way versions), and a horizontal plate for mounting 24-way backplanes in 19-inch racks.WEATHERPROOF ENCLOSURESWeatherproof enclosures are available for applications where separate safe–area enclosures are required for backplanes with modules. Available to accommodate one 4-way or one 8-way backplane, they are manufactured from GRP giving protection against dust and water to IE C529:IP65. The lids are made from transparent high-strength polycarbonate so that LEDs, switches, etc, on the tops of the modules are easy to see.MTL CPS STANDARD BACKPLANESDCS VENDORS/SYSTEMS SUPPORTED:The given data is only intended as a product description and should not be regarded as a legal warranty of properties or guarantee.In the interest of further technical developments, we reserve the right to make design changes.CPS16CPS08CPS24CPS04CPS BACKPLANE DIMENSIONS (mm)Power requirements, Vs21V dc to 35V dc through plug-in connectors Safe–area connectionsCPS: 2.5mm 2screw-clamp terminals – 6 positions per module Weight (without modules or accessories)CPS04: 96g CPS08: 225g CPS16: 419g CPS24: 592gBACKPLANE ACCESSORIESCPS04 CPS04-CCCPS08 CPS08-CCCPS16 CPS16-CCCPS24SCK45 - backplane clips10 x strip of four16 x strip of twoMCK45 - backplane clipsHMP24 - 19" RACK MOUNTING PLATE FOR CPS24-CC - Conformal CoatingThe given data is only intended as a product description and should not be regarded as a legal warranty of properties or guarantee.In the interest of further technical developments, we reserve the right to make design changes.MTL4500 range of backplanes can be customised for specific applications and customer’s requirements. All the signals on the backplane are ‘safe-area’ so custom designs are possible without the need for certification. Eaton offers a fast and efficient customising service upon request.Many installations can benefit from the use of existing custom solutions. These provide reduced system wiring, modularisation of the channels to match the IO card. In addition diagnostics, such and line fault detection, can be grouped prior to connection into the system.Remote cable connections:In addition to the many DCS solutions, listed on a previous page, are backplanes and cables that are ideal when the isolators are mounted in remote cabinets and the signals need to be returned to the system via a multicore cable.CP-DYN RANGEFTASize FunctionMTL modules CP-DYNB-AIOB16ch analogue input /output MTL4541, 4546Y, 4573CP-DYNB-AI250 B 16ch analogue input 1-5V o/p MTL4541, 4573CP-DYNA-2AIO A 16ch analogue input / output MTL4544, 4549Y CP-DYNB-DI B 16ch digital inputMTL4511, 4514CP-DYNB-DILF B 16ch digital input with LFD MTL4514CP-DYNB-2DI B 32ch digital input MTL4513, 4516, 4517CP-DYNB-4DI B 48ch digital input MTL4510CP-DYNA-DO A 8ch digital output MTL4521, 4521L CP-DYNB-DOB16ch digital outputMTL4521, MTL4521LCABLESAll FTAs use the Tyco 20 pin Dynamic range of connectors. Cables are fitted with a mating connector and free ends the other, for connection to the system card.Cable ordering codeCABDYN20-0.50.5m cable CABDYN20-1 1.0m CABDYN20-2 2.0m CABDYN20-3 3.0m CABDYN20-5 5.0m CABDYN20-8 8.0m CABDYN20-10 10m CABDYN20-15 15m CABDYN20-20 20m CABDYN20-25 25m CABDYN20-30 30mDESCRIPTIONFor use when the IS interfaces are remotely mounted from the control system, this series of cable connected FTAs provide a simple plug/socket connection method for IS field devices to any control system. The FTAs come fitted with mounting pillars for surface mounting or may be used with the DIN rail mounting kit to mount on a single DIN rail.The cable connections between the system card and the FTA use the Tyco Dynamic range of connector which provide a reliable and high density solution.CP-DYN DIMENSIONSFor full technical details please contact you local Eaton sales office.The given data is only intended as a product description and should not be regarded as a legal warranty of properties or guarantee.In the interest of further technical developments, we reserve the right to make design changes.ANALOGUE SIGNAL REPEATCPS04-AIRE P backplane may be used to generate a repeat output from a single transmitter source. This includes high integrity loops in general purpose applications. The MTL4641 is used to generate an isolated repeat signal from an existing 4-20mA loop.CPS04-2AIO, 8 channel backplane, is used with IS signals with 2 channel AI or AO modules or with the MTL4544D to generate 4 inputs with repeat outputs.MTL CUSTOM BACKPLANE SOLUTIONSA wide range of backplanes can be offered with application specific functions. System connection options and modularity for individual signal types can be provided to offer significant space and cost savings. Please contact your local Eaton sales office if you wish to discuss your application requirements.PRODUCT MIGRATIONMigration options for legacy MTL4000 range installations are also available. This enables isolators to be easily upgraded, or re-connecting existing isolators to a new control system, with the minimum of disturbance to existing wiring. For more information on product migrationvisit the resource section at CPELCO RANGEA range of dedicated backplanes to interface with MTL4500 range of intrinsically safe isolator modules and the MTL HART maintenance system products. The backplanes offer a standard Elco interface connector for use in systems where the IS interfaces are remote from the DCS.Backplane Function MTL moduleCable CPM08-2AIO 16ch AI 4-20mA MTL4544/4576/4549Y x 8 Elco38 x 1CPM08-2AV 16ch AI 1-5V MTL4544/4576 x 8 Elco38 x 1CPM16-AIO 16ch AIO 4-20mA MTL4541/4573/4546Y Elco38 x 1CPM16-2AIO 32ch AI 4-20mA MTL4544/4576/4549Y x 16 Elco38 x 2CPM16-2AV 32ch AI 1-5V MTL4544/4576 x 16 Elco38 x 2CPM08-DDI 16ch DI MTL4513/4516 Elco38 x 1CPM16-DO 16ch DO MTL4524/4523RElco38 x 1CGM08-DO8ch DOMTL4521/4521L (loop powered)Elco38 x 1For full technical details please contact your local MTL sales office.ORDERING INFORMATIONPlease go to our website at for the latest information regarding safety approvals, certificates and entity parameters.。
Richtek技术公司产品说明书:RT8055高效同步步下电源转换器
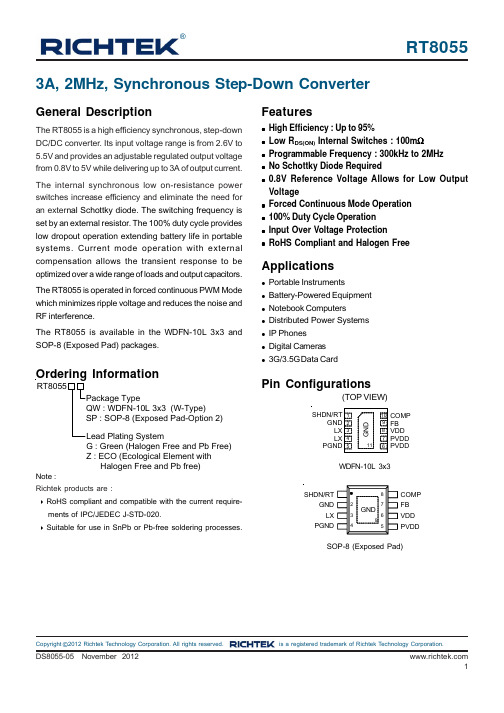
RT8055®©Copyright 2012 Richtek Technology Corporation. All rights reserved. is a registered trademark of Richtek Technology Corporation.Featuresz High Efficiency : Up to 95%z Low R DS(ON) Internal Switches : 100m Ωz Programmable Frequency : 300kHz to 2MHz z No Schottky Diode Requiredz0.8V Reference Voltage Allows for Low Output Voltagez Forced Continuous Mode Operation z 100% Duty Cycle Operation z Input Over Voltage ProtectionzRoHS Compliant and Halogen FreeApplicationsz Portable Instrumentsz Battery-Powered Equipment z Notebook Computersz Distributed Power Systems z IP Phonesz Digital Cameras z3G/3.5G Data CardGeneral DescriptionThe RT8055 is a high efficiency synchronous, step-down DC/DC converter. Its input voltage range is from 2.6V to 5.5V and provides an adjustable regulated output voltage from 0.8V to 5V while delivering up to 3A of output current.The internal synchronous low on-resistance power switches increase efficiency and eliminate the need for an exter nal Schottky diode. The switching frequency is set by an external resistor. The 100% duty cycle provides low dropout operation extending battery life in portable systems. Current mode operation with external compensation allows the transient response to be optimized over a wide range of loads and output capacitors.The RT8055 is operated in forced continuous PWM Mode which minimizes ripple voltage and reduces the noise and RF interference.The RT8055 is available in the WDFN-10L 3x3 and SOP-8 (Exposed Pad) packages.Ordering InformationPin Configurations(TOP VIEW)WDFN-10L 3x33A, 2MHz, Synchronous Step-Down ConverterNote :Richtek products are :` RoHS compliant and compatible with the current require-ments of IPC/JEDEC J-STD-020.` Suitable for use in SnPb or Pb-free soldering processes.COMP FB VDD PVDDPVDDSHDN/RTGND LX PGNDCOMP FB PVDDVDD SOP-8 (Exposed Pad)G : Green (Halogen Free and Pb Free)Z : ECO (Ecological Element with Halogen Free and Pb free)RT8055©Copyright 2012 Richtek Technology Corporation. All rights reserved. is a registered trademark of Richtek Technology Corporation.Typical Application CircuitTable 1. Recommended Component SelectionV OUT Marking InformationJN= : Product Code YMDNN : Date CodeRT8055GQWRT8055GSPRT8055GSP : Product NumberYMDNN : Date CodeJN : Product Code YMDNN : Date CodeRT8055ZQWRT8055©Copyright 2012 Richtek Technology Corporation. All rights reserved. is a registered trademark of Richtek Technology Corporation.Function Block DiagramRT8055©Copyright 2012 Richtek Technology Corporation. All rights reserved. is a registered trademark of Richtek Technology Corporation.Absolute Maximum Ratings (Note 1)zSupply Input Voltage, VDD, PVDD ----------------------------------------------------------------------------−0.3V to 6.5Vz LX Pin Switch Voltage --------------------------------------------------------------------------------------------−0.3V to (PVDD + 0.3V)<10ns ----------------------------------------------------------------------------------------------------------------−5V to 8.5V z Other I/O Pin Voltages -------------------------------------------------------------------------------------------−0.3V to 6.5V z LX Pin Switch Current --------------------------------------------------------------------------------------------4A z Power Dissipation, P D @ T A = 25°CWDFN-10L 3x3-----------------------------------------------------------------------------------------------------1.667W SOP-8 (Exposed Pad)-------------------------------------------------------------------------------------------1.333W z Package Thermal Resistance (Note 2)WDFN-10L 3x3, θJA -----------------------------------------------------------------------------------------------60°C/W WDFN-10L 3x3, θJC -----------------------------------------------------------------------------------------------7.8°C/W SOP-8 (Exposed Pad), θJA -------------------------------------------------------------------------------------75°C/W SOP-8 (Exposed Pad), θJC -------------------------------------------------------------------------------------15°C/W z Junction T emperature ---------------------------------------------------------------------------------------------150°C z Lead Temperature (Soldering, 10 sec.)-----------------------------------------------------------------------260°C z Storage T emperature Range ------------------------------------------------------------------------------------−65°C to 150°C z ESD Susceptibility (Note 3)HBM (Human Body Model)--------------------------------------------------------------------------------------2kVElectrical Characteristics(V DD = 3.3V, T A= 25°C, unless otherwise specified)Recommended Operating Conditions (Note 4)z Supply Input Voltage ----------------------------------------------------------------------------------------------2.6V to 5.5V z Junction T emperature Range ------------------------------------------------------------------------------------ −40°C to 125°C zAmbient T emperature Range ------------------------------------------------------------------------------------ −40°C to 85°CRT8055©Copyright 2012 Richtek Technology Corporation. All rights reserved. is a registered trademark of Richtek Technology Corporation.Note 1. Stresses beyond those listed “Absolute Maximum Ratings ” may cause permanent damage to the device. These arestress ratings only, and functional operation of the device at these or any other conditions beyond those indicated in the operational sections of the specifications is not implied. Exposure to absolute maximum rating conditions may affect device reliability.Note 2. θJA is measured at T A = 25°C on a high effective thermal conductivity four-layer test board per JEDEC 51-7. θJC ismeasured at the exposed pad of the package.Note 3. Devices are ESD sensitive. Handling precaution is recommended.Note 4. The device is not guaranteed to function outside its operating conditions.Note 5. Guaranteed by design.RT8055©Copyright 2012 Richtek Technology Corporation. All rights reserved. is a registered trademark of Richtek Technology Corporation.Typical Operating CharacteristicsOutput Voltage vs. Input Voltage3.303.313.323.333.343.353.363.53.73.94.14.34.54.74.95.15.35.5Input Voltage (V)O u t p u t V o l t a g e (V)Output Voltage vs. Output Current3.263.273.283.293.303.313.323.333.343.353.363.373.380.00.30.60.91.21.51.82.12.42.73.0Output Current (A)O u t p u t V o l t a g e (V)Efficiency vs. Output Current01020304050607080901000.00.30.60.91.21.51.82.12.42.73.0Output Current (A)E f f i c i e n c y (%)Switching Frequency vs. Temperature1.51.61.71.81.92.02.1-50-25255075100125Temperature (°C)S w i t c h i n g F r e q u e n c y (M H z )Switching Frequency vs. Input Voltage1.51.61.71.81.92.02.13.53.73.94.14.34.54.74.95.15.35.5Input Voltage (V)S w i t c h i n g F r e q u e n c y (M H z )V IN UVLO vs. Temperature2.002.052.102.152.202.252.302.352.402.452.50-50-25255075100125Temperature (°C)V I N U V L O (V )RT8055©Copyright 2012 Richtek Technology Corporation. All rights reserved. is a registered trademark of Richtek Technology Corporation.Output RippleTime (500ns/Div)V IN = 5V, V OUT = 3.3V I OUT = 0AV LX (5V/Div)V OUT (5mV/Div)Output Ripple Time (500ns/Div)V IN = 5V, V OUT = 3.3V I OUT = 3A V LX (5V/Div)V OUT(5mV/Div)Reference Voltage vs. Temperature0.7600.7680.7760.7840.7920.8000.8080.8160.8240.8320.840-50-25255075100125Temperature (°C)R e f e r e n c e V o l t a g e (V )Output Current Limit vs. Temperature2.02.53.03.54.04.55.05.56.0-50-25255075100125Temperature (°C)O u t p u t C u r r e n t L i m i t (A)Output Current Limit vs. Input Voltage2.02.53.03.54.04.55.05.56.03.53.73.94.14.34.54.74.95.15.35.5Input Voltage (V)O u t p u t C u r r e n t L i m i t (A)Output Voltage vs. Temperature3.203.223.243.263.283.303.323.343.363.383.40-50-25255075100125Temperature (°C)O u t p u t V o l t a g e (V)RT8055©Copyright 2012 Richtek Technology Corporation. All rights reserved. is a registered trademark of Richtek Technology Corporation.Power On from V INTime (1ms/Div)V IN = 5V, V OUT = 3.3V I OUT = 0AV LX (5V/Div)V IN (2V/Div)V OUT (1V/Div)Load Transient ResponseTime (100μs/Div)I OUT (1A/Div)V OUT(200mV/Div)V IN = 5V, V OUT = 3.3V I OUT = 0A to 2ALoad Transient ResponseTime (100μs/Div)I OUT (1A/Div)V OUT(200mV/Div)V IN = 5V, V OUT = 3.3V I OUT = 0A to 3AUVP ShutdownTime (10μs/Div)V LX (5V/Div)V OUT (1V/Div)V IN = 5V, V OUT = 3.3VRT8055©Copyright 2012 Richtek Technology Corporation. All rights reserved. is a registered trademark of Richtek Technology Corporation.Application InformationThe basic RT8055 application circuit is shown in TypicalApplication Circuit. External component selection is determined by the maximum load current and begins with the selection of the inductor value and operating frequency followed by C IN and C OUT .Output Voltage SettingThe output voltage is set by an external resistive divider according to the following equation :Figure 1. Setting the Output Voltage⎟⎠⎞⎜⎝⎛+×=R2R11V V REF OUT Soft-StartThe RT8055 contains an internal soft-start clamp that gradually raises the clamp on the COMP pin.Operating FrequencySelection of the operating frequency is a tradeoff between efficiency and component size. High frequency operation allows the use of smaller inductor and capacitor values.Operation at lower frequency improves efficiency by reducing internal gate charge and switching losses but requires larger inductance and/or capacitance to maintain low output ripple voltage.The operating frequency of the RT8055 is determined by an external resistor that is connected between the SHDN/RT pin and GND. The value of the resistor sets the ramp current that is used to charge and discharge an internal timing capacitor within the oscillator. The RT resistor value can be determined by examining the frequency vs. R RT curve. Although frequencies as high as 2MHz are possible,the minimum on-time of the RT8055 imposes a minimum limit on the operating duty cycle. The minimum on-time is typically 110ns. Therefore, the minimum duty cycle is equal to 100 x 110ns x f (Hz).Figure 2100% Duty Cycle OperationWhen the input supply voltage decreases toward the outputvoltage, the duty cycle increases toward the maximum on-time. Further reduction of the supply voltage forces the main switch to remain on for more than one cycle eventually reaching 100% duty cycle.The output voltage will then be determined by the input voltage minus the voltage drop across the internal P-MOSFET and the inductor.Low Supply OperationThe RT8055 is designed to operate down to an input supply voltage of 2.6V. One important consideration at low input supply voltages is that the R DS(ON) of the P-Channel and N-Channel power switches increases. The user should calculate the power dissipation when the RT8055 is used at 100% duty cycle with low input voltages to ensure that thermal limits are not exceeded.Slope Compensation and Inductor Peak Current Slope compensation provides stability in constant frequency architectures by preventing sub-harmonic oscillations at duty cycles greater than 50%. It is accomplished internally by adding a compensating ramp to the inductor current signal. Normally, the maximum inductor peak current is reduced when slope compensation is added. In the RT8055, however, separated inductor current signals are used to monitor over current condition.0.00.51.01.52.02.53.002004006008001000R OSC (K )S w i t c h i n g F r e q u e n c y (M H z )(k Ω)where V REF equals to 0.8V typical.The resistive divider allows the FB pin to sense a fraction of the output voltage as shown in Figure 1.RT8055©Copyright 2012 Richtek Technology Corporation. All rights reserved. is a registered trademark of Richtek Technology Corporation.This formula has a maximum at V IN = 2V OUT , where I RMS = I OUT /2. This simple worst-case condition is commonly used for design because even significant deviations do not offer much relief. Choose a capacitor rated at a higher temperature than required.Several capacitors may also be paralleled to meet size or height requirements in the design.The selection of C OUT is determined by the effective series resistance (ESR) that is required to minimize voltage ripple and load step transients, as well as the amount of bulk capacitance that is necessary to ensure that the control loop is stable. Loop stability can be checked by viewing the load transient response as described in a later section.The output ripple, ΔV OUT , is determined by :1V V V V I I OUTININ OUT OUT(MAX)RMS −=⎦⎤⎢⎣⎡+Δ≤ΔOUT L OUT 8fC 1ESR I V This keeps the maximum output current relatively constant regardless of duty cycle.Short Circuit ProtectionWhen the output is shorted to ground, the inductor current decays very slowly during a single switching cycle. A current runaway detector is used to monitor inductor current. As current increasing beyond the control of current loop, switching cycles will be skipped to prevent current runaway from occurring.Inductor SelectionThe inductor value and operating frequency determine the ripple current according to a specific input and output voltage. The ripple current ΔI L increases with higher V IN and decreases with higher inductance.OUT OUT L IN V V I =1f L V ⎡⎤⎡⎤Δ×−⎢⎥⎢⎥×⎣⎦⎣⎦OUT OUT L(MAX)IN(MAX)V V L =1f I V ⎡⎤⎡⎤×−⎢⎥⎢×Δ⎣⎦⎣⎦Having a lower ripple current reduces not only the ESR losses in the output capacitors but also the output voltage ripple. However, it requires a large inductor to achieve this goal.For the ripple current selection, the val ue of ΔI L = 0.4(I MAX )will be a reasonable starting point. The large st ripple current occurs at the highest V IN . To guarantee that the ripple current stays below the specified maximum, the inductor value should be chosen according to the following equation :The inductor's current rating (caused a 40°C temperature rising from 25°C ambient) should be greater than the maximum load current and its saturation current should be greater than the short circuit peak current limit.C IN and C OUT SelectionThe input capacitance, C IN , is needed to filter the trapezoidal current at the source of the top MOSFET . To prevent large ripple voltage, a low ESR input capacitor sized for the maximum RMS current should be used. RMS current is given by :The output ripple is highest at maximum input voltagesince ΔI L increases with input voltage. Multiple capacitors placed in parallel may be needed to meet the ESR and RMS current handling requirements. Dry tantalum, special polymer, aluminum electrolytic and ceramic capacitors are all available in surface mount packages. Special polymer capacitors offer very low ESR but have lower capacitance density than other types. Tantalum capacitors have the highest capacitance density but it is important to only use types that have been surge tested for use in switching power supplies. Aluminum electrolytic capacitors have significantly higher ESR but can be used in cost-sensitive applications provided that consideration is given to ripple current ratings and long term reliability. Ceramic capacitors have excellent low ESR characteristics but can have a high voltage coefficient and audible piezoelectric effects.The high Q of ceramic capacitors with trace inductance can also lead to significant ringing.Using Ceramic Input and Output CapacitorsHigher values, lower cost ceramic capacitors are now becoming available in smaller case sizes. Their high ripple current, high voltage rating and low ESR make them ideal for switching regulator applications. However, care must be taken when these capacitors are used at the input and output. When a ceramic capacitor is used at the inputDS8055-05 November 2012©Copyright 2012 Richtek Technology Corporation. All rights reserved. is a registered trademark of Richtek Technology Corporation.and the power is supplied by a wall adapter through long wires, a load step at the output can induce ringing at the input, V DD . At best, this ringing can couple to the output and be mistaken as loop instability. At worst, a sudden inrush of current through the long wires can potentially cause a voltage spike at V IN large enough to damage the part.Thermal ConsiderationsFor continuous operation, do not exceed absolute maximum junction temperature. The maximum power dissipation depends on the thermal resistance of the IC package, PCB layout, rate of surrounding airflow, and difference between junction and ambient temperature. The maximum power dissipation can be calculated by the following formula :P D(MAX) = (T J(MAX) − T A ) / θJAwhere T J(MAX) is the maximum junction temperature, T A is the ambient temperature, and θJA is the junction to ambient thermal resistance.For recommended operating condition specifications, the maximum junction temperature is 125°C. The junction to ambient thermal resistance, θJA , is layout dependent. For SOP-8 (Exposed Pad) packages, the thermal resistance,θJA , is 75°C/W on a standard JEDEC 51-7 four-layer thermal test board. For WDFN-10L 3x3 packages, the thermal resistance, θJA , is 70°C/W on a standard JEDEC 51-7 four-layer thermal test board. The maximum power dissipation at T A = 25°C can be calculated by the following formulas :P D(MAX) = (125°C − 25°C) / (75°C/W) = 1.333W for SOP-8 (Exposed Pad) packageP D(MAX) = (125°C − 25°C) / (70°C/W) = 1.429W for WDFN-10L 3x3 packageThe maximum power dissipation depends on the operating ambient temperature for fixed T J(MAX) and thermal resistance, θJA . The derating curves in Figure 3 allow the designer to see the effect of rising ambient temperature on the maximum power dissipation.Figure 3. Derating Curve of Maximum Power Dissipation Layout ConsiderationsFollow the PCB layout guidelines for optimal performance of RT8055.`A ground plane is recommended. If a ground plane layer is not used, the signal and power grounds should be segregated with all small-signal components returning to the GND pin at one point that is then connected to the PGND pin close to the IC. The exposed pad should be connected to GND.`Connect the terminal of the input capacitor(s), C IN , as close as possible to the PVDD pin. This capacitor provides the AC current into the internal power MOSFETs.`LX node is with high frequency voltage swing and should be kept within small area. Keep all sensitive small-signal nodes away from the LX node to prevent stray capacitive noise pick-up.`Flood all unused areas on all layers with copper.Flooding with copper will reduce the temperature rise of powercomponents.You can connect the copper areas to any DC net (PVDD,VDD, VOUT , PGND, GND, or any other DC rail in your system).`Connect the FB pin directly to the feedback resistors.The resistor divider must be connected between V OUT and GND.0.00.10.20.30.40.50.60.70.80.91.01.11.21.31.41.50255075100125Ambient Temperature (°C)M a x i m u m P o w e r D i s s i p a t i o n (W )©Copyright 2012 Richtek Technology Corporation. All rights reserved. is a registered trademark of Richtek Technology Corporation.Table 3. Capacitors for C and C Recommended component selection for Typical ApplicationFigure 4. PCB Layout GuideFand GND as closer as possibleLX should befrom this tracenear RT8055Connect the FB pin directly to feedback resistors. TheDS8055-05 November 2012©Copyright 2012 Richtek Technology Corporation. All rights reserved. is a registered trademark of Richtek Technology Corporation.W-Type 10L DFN 3x3 PackageRichtek Technology Corporation5F, No. 20, Taiyuen Street, Chupei City Hsinchu, Taiwan, R.O.C.Tel: (8863)5526789Richtek products are sold by description only. Richtek reserves the right to change the circuitry and/or specifications without notice at any time. Customers shouldobtain the latest relevant information and data sheets before placing orders and should verify that such information is current and complete. Richtek cannot assume responsibility for use of any circuitry other than circuitry entirely embodied in a Richtek product. Information furnished by Richtek is believed to be accurate and reliable. However, no responsibility is assumed by Richtek or its subsidiaries for its use; nor for any infringements of patents or other rights of third parties which may result from its use. No license is granted by implication or otherwise under any patent or patent rights of Richtek or its subsidiaries.HM(Bottom of Package)8-Lead SOP (Exposed Pad) Plastic Package。
ME4055A锂离子电池充电器me4055a 800mA线性

Single Cell Lithium-Ion Batteries ●Constant- Current/Constant- Voltage operation with
thermal regulation to maximize Rate Without risk of overheating. ● Preset 4.2V charge voltage with ±1% accuracy ● Automatic Recharge ●Charges Single Cell Li-Ion Batteries Directly from USB Port ●C/10 charge termination ● 55μA supply current in shutdown ● 2.9V trickle current charge threshold ● Soft-Start limits inrush current ●Charge Status Output Pin ●Available in SOT23-6 Package
CHARGE CURRENT(mA)
700 CONSTANT CURRENT
4.75
600 CONSTANT
500 POWER
CONSTANT 4.5 VOLTAGAE
4.25
400
4.0
300 200 100
0 0
VCC=5V θJA=130℃/W RPROG=1.65K CHARGE TA=25℃ TERMINATED
ME4055AM6G
Pin Num. Symbol
Function
600W 单向电磁波抑制器(TVS)SOD128小型平面接线设备(SMD)塑料包装产品说明书

1. Product profile1.1General description600W unidirectional Transient Voltage Suppressor (TVS) in a SOD128 small and flat leadSurface-Mounted Device (SMD) plastic package, designed for transient overvoltage protection.1.2Features and benefits1.3ApplicationsPower supply protection Automotive application Industrial applicationPower management1.4Quick reference data[1]In accordance with IEC 61643-321 (10/1000μs current waveform).PTVSxP1UP series600 W Transient Voltage SuppressorRev. 2 — 6 January 2011Product data sheetRated peak pulse power: P PPM =600W Very low package height: 1mmReverse standoff voltage range:V RWM =3.3V to 64VSmall plastic package suitable for surface-mounted design Reverse current: I RM =0.001μAAEC-Q101 qualified Table 1.Quick reference data SymbolParameterConditionsMin Typ Max Unit P PPM rated peak pulse power [1]--600W V RWMreverse standoff voltage3.3-64V2. Pinning information[1]The marking bar indicates the cathode.3. Ordering information[1]The series consists of 35types with reverse standoff voltages from 3.3V to 64V.4. MarkingTable 2.PinningPin DescriptionSimplified outline Graphic symbol1cathode [1]2anodesym03512Table 3.Ordering informationType number [1]Package NameDescriptionVersion PTVSxP1UP series-plastic surface-mounted package; 2leadsSOD128Table 4.Marking codesType number Marking code Type number Marking code PTVS3V3P1UP AJ PTVS20VP1UP B3PTVS5V0P1UP AK PTVS22VP1UP B4PTVS6V0P1UP AL PTVS24VP1UP B5PTVS6V5P1UP AM PTVS26VP1UP B6PTVS7V0P1UP AN PTVS28VP1UP B7PTVS7V5P1UP AP PTVS30VP1UP B8PTVS8V0P1UP AQ PTVS33VP1UP B9PTVS8V5P1UP AR PTVS36VP1UP BA PTVS9V0P1UP AS PTVS40VP1UP BB PTVS10VP1UP AT PTVS43VP1UP BC PTVS11VP1UP AU PTVS45VP1UP BD PTVS12VP1UP AV PTVS48VP1UP BE PTVS13VP1UP AW PTVS51VP1UP BF PTVS14VP1UP AX PTVS54VP1UP BG PTVS15VP1UP AY PTVS58VP1UP BH PTVS16VP1UP AZ PTVS60VP1UP BJ PTVS17VP1UP B1PTVS64VP1UP BK PTVS18VP1UPB2--5. Limiting values[1]In accordance with IEC 61643-321 (10/1000μs current waveform).[1]Device stressed with ten non-repetitive ElectroStatic Discharge (ESD)pulses.[2]Soldering point of cathode tab.6. Thermal characteristics[1]Device mounted on an FR4Printed-Circuit Board (PCB), single-sided copper, tin-plated and standard footprint.[2]Device mounted on an FR4PCB, single-sided copper, tin-plated, mounting pad for cathode 1cm 2.[3]Device mounted on a ceramic PCB, Al 2O 3, standard footprint.[4]Soldering point of cathode tab.Table 5.Limiting valuesIn accordance with the Absolute Maximum Rating System (IEC 60134).Symbol ParameterConditionsMin Max Unit P PPM rated peak pulse power [1]-600WI PPMrated peak pulse current[1]-see Table 9 and 10I FSM Non-repetitive peak forward current single half-sine wave; t p =8.3ms-100A T j junction temperature -150°C T amb ambient temperature −55+150°C T stgstorage temperature−65+150°CTable 6.ESD maximum ratings T amb =25°C unless otherwise specified.Symbol Parameter Conditions Min Max Unit Per diode V ESDelectrostatic discharge voltageIEC 61000-4-2 (contact discharge)[1][2]-30kVTable 7.ESD standards complianceStandard ConditionsPer diodeIEC 61000-4-2; level 4 (ESD)>15kV (air); >8kV (contact)MIL-STD-883; class 3 (human body model)>4kVTable 8.Thermal characteristics Symbol ParameterConditions Min Typ Max Unit R th(j-a)thermal resistance fromjunction to ambientin free air[1]--200K/W [2]--120K/W [3]--60K/W R th(j-sp)thermal resistance from junction to solder point[4]--12K/W7. CharacteristicsTable 9.Characteristics per type; PTVS3V3P1UP to PTVS7V0P1UP T j=25°C unless otherwise specified.Type number Reverse standoffvoltageV RWM(V)Breakdown voltageV BR(V)Reverse leakagecurrentI RM(μA)Clamping voltageV CL(V)I R=10mA at V RWM(V)Max Min Typ Max Typ Max Max I PPM(A) PTVS3V3P1UP 3.3 5.20 5.60 6.0056008.075.0 PTVS5V0P1UP 5.0 6.40 6.707.0054009.265.2 PTVS6V0P1UP 6.0 6.677.027.37540010.358.3 PTVS6V5P1UP 6.57.227.607.98525011.253.6 PTVS7V0P1UP7.07.788.208.60310012.050.0Table 10.Characteristics per type; PTVS7V5P1UP to PTVS64VP1UPT j=25°C unless otherwise specified.Type number Reverse standoffvoltageV RWM(V)Breakdown voltageV BR(V)Reverse leakagecurrentI RM(μA)Clamping voltageV CL(V)I R=1mA at V RWM(V)Max Min Typ Max Typ Max Max I PPM(A) PTVS7V5P1UP7.58.338.779.210.25012.946.5 PTVS8V0P1UP8.08.899.369.830.032513.644.1 PTVS8V5P1UP8.59.449.9210.400.011014.441.7 PTVS9V0P1UP9.010.0010.5511.100.005515.439.0 PTVS10VP1UP1011.1011.7012.300.005 2.517.035.3 PTVS11VP1UP1112.2012.8513.500.005 2.518.233.0 PTVS12VP1UP1213.3014.0014.700.005 2.519.930.2 PTVS13VP1UP1314.4015.1515.900.0010.121.527.9 PTVS14VP1UP1415.6016.4017.200.0010.123.225.9 PTVS15VP1UP1516.7017.6018.500.0010.124.424.6 PTVS16VP1UP1617.8018.7519.700.0010.126.023.1 PTVS17VP1UP1718.9019.9020.900.0010.127.621.7 PTVS18VP1UP1820.0021.0022.100.0010.129.220.5 PTVS20VP1UP2022.2023.3524.500.0010.132.418.5 PTVS22VP1UP2224.4025.6026.900.0010.135.516.9 PTVS24VP1UP2426.7028.1029.500.0010.138.915.4 PTVS26VP1UP2628.9030.4031.900.0010.142.114.3 PTVS28VP1UP2831.1032.8034.400.0010.145.413.2 PTVS30VP1UP3033.3035.1036.800.0010.148.412.4 PTVS33VP1UP3336.7038.7040.600.0010.153.311.3 PTVS36VP1UP3640.0042.1044.200.0010.158.110.3 PTVS40VP1UP4044.4046.8049.100.0010.164.59.3PTVS43VP1UP 4347.8050.3052.800.0010.169.48.6PTVS45VP1UP 4550.0052.6555.300.0010.172.78.3PTVS48VP1UP 4853.3056.1058.900.0010.177.47.8PTVS51VP1UP 5156.7059.7062.700.0010.182.47.3PTVS54VP1UP 5460.0063.1566.300.0010.187.1 6.9PTVS58VP1UP 5864.4067.8071.200.0010.193.6 6.4PTVS60VP1UP 6066.7070.2073.700.0010.196.8 6.2PTVS64VP1UP6471.1074.8578.600.0010.1103.05.8Table 10.Characteristics per type; PTVS7V5P1UP to PTVS64VP1UP …continued T j =25°C unless otherwise specified.Type numberReverse standoff voltage V RWM (V)Breakdown voltage V BR (V)Reverse leakage current I RM (μA)Clamping voltage V CL (V)I R =1mAat V RWM (V)MaxMin Typ Max Typ Max Max I PPM (A)8. Test information8.1Quality informationThis product has been qualified in accordance with the Automotive Electronics Council(AEC) standard Q101 - Stress test qualification for discrete semiconductors, and issuitable for use in automotive applications.9. Package outline10. Packing informationTable 11.Packing methodsThe indicated -xxx are the last three digits of the 12NC ordering code.[1]Type number[2]Package Description Packing quantity3000PTVSxP1UP series SOD1284mm pitch, 12mm tape and reel-115[1]For further information and the availability of packing methods, see Section14.[2]The series consists of 35types with reverse standoff voltages from 3.3V to64V.11. Soldering12. Revision historyTable 12.Revision historyDocument ID Release date Data sheet status Change notice Supersedes PTVSXP1UP_SER v.220110106Product data sheet-PTVSXP1UP_SER v.1 Modifications:•Table 6 “ESD maximum ratings”: added.•Section 13 “Legal information”: updated.PTVSXP1UP_SER v.120100527Product data sheet--13. Legal information13.1 Data sheet status[1]Please consult the most recently issued document before initiating or completing a design.[2]The term ‘short data sheet’ is explained in section “Definitions”.[3]The product status of device(s) described in this document may have changed since this document was published and may differ in case of multiple devices. The latest product statusinformation is available on the Internet at URL .13.2 DefinitionsDraft — The document is a draft version only. The content is still under internal review and subject to formal approval, which may result in modifications or additions. Nexperia does not give anyrepresentations or warranties as to the accuracy or completeness of information included herein and shall have no liability for the consequences of use of such information.Short data sheet — A short data sheet is an extract from a full data sheet with the same product type number(s) and title. A short data sheet is intended for quick reference only and should not be relied upon to contain detailed and full information. For detailed and full information see the relevant full data sheet, which is available on request via the local Nexperia salesoffice. In case of any inconsistency or conflict with the short data sheet, the full data sheet shall prevail.Product specification — The information and data provided in a Product data sheet shall define the specification of the product as agreed between Nexperia and its customer, unless Nexperia andcustomer have explicitly agreed otherwise in writing. In no event however, shall an agreement be valid in which the Nexperia product isdeemed to offer functions and qualities beyond those described in the Product data sheet.13.3 DisclaimersLimited warranty and liability — Information in this document is believed to be accurate and reliable. However, Nexperia does not give any representations or warranties, expressed or implied, as to the accuracy or completeness of such information and shall have no liability for the consequences of use of such information.In no event shall Nexperia be liable for any indirect, incidental,punitive, special or consequential damages (including - without limitation - lost profits, lost savings, business interruption, costs related to the removal or replacement of any products or rework charges) whether or not such damages are based on tort (including negligence), warranty, breach of contract or any other legal theory.Notwithstanding any damages that customer might incur for any reason whatsoever, Nexperia’s aggregate and cumulative liability towards customer for the products described herein shall be limited in accordance with the Terms and conditions of commercial sale of Nexperia.Right to make changes — Nexperia reserves the right to makechanges to information published in this document, including without limitation specifications and product descriptions, at any time and without notice. This document supersedes and replaces all information supplied prior to the publication hereof.Suitability for use — Nexperia products are not designed,authorized or warranted to be suitable for use in life support, life-critical or safety-critical systems or equipment, nor in applications where failure or malfunction of a Nexperia product can reasonably be expectedto result in personal injury, death or severe property or environmental damage. Nexperia accepts no liability for inclusion and/or use ofNexperia products in such equipment or applications andtherefore such inclusion and/or use is at the customer’s own risk. Applications — Applications that are described herein for any of these products are for illustrative purposes only. Nexperia makes no representation or warranty that such applications will be suitable for the specified use without further testing or modification.Customers are responsible for the design and operation of their applications and products using Nexperia products, and Nexperiaaccepts no liability for any assistance with applications or customer product design. It is customer’s sole responsibility to determine whether the Nexperia product is suitable and fit for the customer’s applications andproducts planned, as well as for the planned application and use of customer’s third party customer(s). Customers should provide appropriate design and operating safeguards to minimize the risks associated with their applications and products.Nexperia does not accept any liability related to any default,damage, costs or problem which is based on any weakness or default in the customer’s applications or products, or the application or use by customer’s third party customer(s). Customer is responsible for doing all necessary testing for the customer’s applications and products using Nexperia products in order to avoid a default of the applications andthe products or of the application or use by customer’s third partycustomer(s). Nexperia does not accept any liability in this respect.Limiting values — Stress above one or more limiting values (as defined in the Absolute Maximum Ratings System of IEC60134) will cause permanent damage to the device. Limiting values are stress ratings only and (proper) operation of the device at these or any other conditions above those given in the Recommended operating conditions section (if present) or the Characteristics sections of this document is not warranted. Constant or repeated exposure to limiting values will permanently and irreversibly affect the quality and reliability of the device.Terms and conditions of commercial sale — Nexperiaproducts are sold subject to the general terms and conditions of commercial sale, as published at /profile/terms, unless otherwise agreed in a valid written individual agreement. In case an individual agreement is concluded only the terms and conditions of the respective agreement shall apply. Nexperia hereby expressly objects toapplying the customer’s general terms and conditions with regard to the purchase of Nexperia products by customer.No offer to sell or license — Nothing in this document may be interpreted or construed as an offer to sell products that is open for acceptance or the grant, conveyance or implication of any license under any copyrights, patents or other industrial or intellectual property rights.Export control — This document as well as the item(s) described herein may be subject to export control regulations. Export might require a prior authorization from national authorities.Document status[1][2]Product status[3]DefinitionObjective [short] data sheet Development This document contains data from the objective specification for product development. Preliminary [short] data sheet Qualification This document contains data from the preliminary specification.Product [short] data sheet Production This document contains the product specification.© Nexperia B.V. 2017. All rights reserved PTVSXP1UP_SER All information provided in this document is subject to legal disclaimers.Product data sheet Rev. 2 — 6 January 2011 11 of 12Quick reference data — The Quick reference data is an extract of theproduct data given in the Limiting values and Characteristics sections of thisdocument, and as such is not complete, exhaustive or legally binding.13.4 Trademarks Notice: All referenced brands, product names, service names and trademarks are the property of their respective owners.14. Contact informationFor more information, please visit: For sales office addresses, please send an email to: ***************************15. Contents1 Product profile. . . . . . . . . . . . . . . . . . . . . . . . . . 11.1 General description . . . . . . . . . . . . . . . . . . . . . 11.2 Features and benefits. . . . . . . . . . . . . . . . . . . . 11.3 Applications . . . . . . . . . . . . . . . . . . . . . . . . . . . 11.4 Quick reference data . . . . . . . . . . . . . . . . . . . . 12 Pinning information. . . . . . . . . . . . . . . . . . . . . . 23 Ordering information. . . . . . . . . . . . . . . . . . . . . 24 Marking. . . . . . . . . . . . . . . . . . . . . . . . . . . . . . . . 25 Limiting values. . . . . . . . . . . . . . . . . . . . . . . . . . 36 Thermal characteristics . . . . . . . . . . . . . . . . . . 37 Characteristics. . . . . . . . . . . . . . . . . . . . . . . . . . 48 Test information. . . . . . . . . . . . . . . . . . . . . . . . . 78.1 Quality information . . . . . . . . . . . . . . . . . . . . . . 79 Package outline . . . . . . . . . . . . . . . . . . . . . . . . . 710 Packing information . . . . . . . . . . . . . . . . . . . . . 811 Soldering . . . . . . . . . . . . . . . . . . . . . . . . . . . . . . 812 Revision history. . . . . . . . . . . . . . . . . . . . . . . . . 913 Legal information. . . . . . . . . . . . . . . . . . . . . . . 1013.1 Data sheet status . . . . . . . . . . . . . . . . . . . . . . 1013.2 Definitions. . . . . . . . . . . . . . . . . . . . . . . . . . . . 1013.3 Disclaimers. . . . . . . . . . . . . . . . . . . . . . . . . . . 1013.4 Trademarks. . . . . . . . . . . . . . . . . . . . . . . . . . . 1114 Contact information. . . . . . . . . . . . . . . . . . . . . 1115 Contents . . . . . . . . . . . . . . . . . . . . . . . . . . . . . . 12© Nexperia B.V. 2017. All rights reserved For more information, please visit: Forsalesofficeaddresses,pleasesendanemailto:***************************Date of release: 06 January 2011Mouser ElectronicsAuthorized DistributorClick to View Pricing, Inventory, Delivery & Lifecycle Information:N experia:PTVS3V3P1UP,115PTVS64VP1UP,115PTVS10VP1UP,115PTVS11VP1UP,115PTVS12VP1UP,115 PTVS13VP1UP,115PTVS14VP1UP,115PTVS15VP1UP,115PTVS16VP1UP,115PTVS17VP1UP,115 PTVS18VP1UP,115PTVS20VP1UP,115PTVS22VP1UP,115PTVS24VP1UP,115PTVS26VP1UP,115 PTVS28VP1UP,115PTVS30VP1UP,115PTVS33VP1UP,115PTVS36VP1UP,115PTVS40VP1UP,115 PTVS43VP1UP,115PTVS45VP1UP,115PTVS48VP1UP,115PTVS51VP1UP,115PTVS54VP1UP,115 PTVS58VP1UP,115PTVS5V0P1UP,115PTVS60VP1UP,115PTVS6V0P1UP,115PTVS6V5P1UP,115 PTVS7V0P1UP,115PTVS7V5P1UP,115PTVS8V0P1UP,115PTVS8V5P1UP,115PTVS9V0P1UP,115。
FM01BTS FM01BTD 充电器驱动IC说明书

FM01BTS/FM01BTD文件编号:S&CIC1270)充电器驱动IC功能描述FM01BTS/FM01BTD (文件编号:S&CIC1270) 充电器驱动IC电气参数VDD=5V , Vout=5V Ta=25℃, 除非另有说明。
参数 符号 测试条件 最小值 典型值 最大值单位开启电压 VDDon VDD 上升从0开始 5 5.8 -- V 关闭电压 VDDoff 开关打开之后VDD 下降2.5 2.8 -- V 工作电流 IDD 正常工作 -- 1 3 mA 启动电流 IDDst开关打开之前-- 30 50 uA效率 η -- -- 78 -- %前沿消隐时间 -- -- -- 600 -- ns 过温关断点-- -- -- 145 --℃性能介绍参数归纳项目规范 测试输入特性AC 输入电压范围AC 180V~264V AC 180V~264V待机功耗<0.3W 0.22W输出特性DC 输出电压 -- DC 5V~5.5V输出电流典型值(可调)-- 500mA~1A开启延迟时间<1S 0.5S保护开路保护 -- Pass短路保护-- PassFM01BTS/FM01BTDFM01BTS/FM01BTDFM01BTS/FM01BTD(文件编号:S&CIC1270)充电器驱动ICBOM表成品物料:序号名称规格用量备注1 PCB 30×53mm 1.2mm HB纸板 1 --R112 碳膜电阻 1.5M±5% 1/4WR213 碳膜电阻100K±5% 1/4WR3a、R3b24 碳膜电阻 4.7R±1% 1/4WR65 碳膜电阻510R±5% 1/4W1FR6 碳膜电阻10R±5% 1/2W1C17 电解电容 4.7uF/450V±20% 8×12 1C28 插件电容 4.7NF/250V CAP-41C39 电解电容10uF/50V±20% 4×7 110 电解电容10V 1000uF 5×11 1 C4D111 二极管FR107 DO-411D3112 二极管FR107 DO-41D7113 二极管SS34 SMA14 发光二极管∮3mm白发红普亮、短脚 1 LED115 变压器 EE13W卧式(FM01BTS) 1 T116 AC电子线Φ1.5×40mm 黑 2 AC1、AC2变压器规格结构图:骨架类型PIN数目针距排距备注EE13卧式、TDK PC40 4+4 2.5mm 12.1mm 卧式FM01BTS/FM01BTDFM01BTS/FM01BTD(文件编号:S&CIC1270)充电器驱动IC 应用板重要波形:VIN-AC=265V,Iout=1A时,三极管C脚波形如下:(VCE=540V,F=41KHZ)VIN-AC=220V,Iout=1A时,CS脚波形如下:(VCS=800mV,F=43KHZ)FM01BTS/FM01BTD(文件编号:S&CIC1270)充电器驱动ICVIN-AC=220V,Iout=0时,VCC(CH1)、CS(CH2)、C(CH4)波形如下:(VCC=5.2V,VCS=800mA,F=720HZ&2KHZ)VIN-AC=220V,Iout=1A时,VCC(CH1)、CS(CH2)、C(CH4)波形如下:(VCC=5.6V,VCS=800mA,F=41KHZ)FM01BTS/FM01BTD(文件编号:S&CIC1270)充电器驱动IC成品测试技术规范:1、适用范围:以下成品测试技术规范适用于本公司设计生产的FM01BTS、FM01BTD手机直充充电器。
美国ACCU-CHARGER 恒流恒压充电器 12-24V 70AH 40A 充电器 说明书

ACCU-CHARGER®Ferroresonant Industrial Battery Chargers ArraySetting the industry standard for maximumperformancej A choice of 3 interchangeable controls foradded flexibliltyj Quality-built for years of trouble-free servicej Fail-safe design protects batteriesj 100% rated to recharge fully discharged batteriesin 8 hours or lessj Ten-year transformer and diode warrantyj CDAC compatible–applied technology to controlmaterial handling costsj UL listed, CSA certifiedj Designed for maximum performanceThe Accu-Charger sets the industry standard for accuracy, efficiency, flexibility andreliability. Designed to recharge any 100%discharged lead-acid battery in its ampere-hour rating within 8 hours, the Accu-Charger is engineered to provide the maximum in charging performance. The charger uses ferroresonant power conversion circuitry,which is virtually maintenance-free, to provide years of dependable service. The power conversion circuitry maximizes battery life by using a constantly tapering charge which is automatically regulated by the “On Charge”battery voltage. The output current of the Accu-Charger is determined by the state of discharge of the battery. The battery is precisely charged, based on its depth of discharge.j Control optionsDepending on your charging requirements,the Accu-Charger can be controlled by any one of the following controls: AC500, AC1000and AC2000.j Battery/charger safeguardsThe Accu-Charger is internally protected against overload, short circuit, incorrect battery connection and voltage transients.Shorting of the DC output will not damage the charger or cause fuses to blow. Plus, in the event of a component failure, the charging rate will automatically go to “minimum,” thus protecting the battery from damage.j RegulationAccu-Chargers will hold the finish rate of the charge within ±1%, even with line voltage variations as high as ±10%. This protects,and properly charges the battery, even when severe input voltage variations exist.j Single and three phase serviceThe Accu-Charger is available in a variety of single and three phase models, providing multiple AC input voltages as standard. Most models are UL listed, CSA certified, and meet BCI requirements.j RatingThe Accu-Charger is rated to recharge a 100% discharged battery in its ampere-hour rating within eight hours.j Easy to change AC input voltageAC input voltage change-overs take just minutes because of conveniently located taps and quick-connect jumpers.j Adjustable DC outputIn rare instances where changes to the DC output might be required, necessary adjustments are made simple withconveniently located quick-connect jumpers.j WarrantyMinimize repair costs with ten-year original purchaser warranty on power transformer and silicon diodes, plus one-year warranty on other components.j Convection cooled, quietThe Accu-Charger uses no fans to draw in dirty air and has low sound levels for quiet operation.Baked powdered polyester finish Quick connect primary voltage change-over 120/208/240 or 208/240/480, 575Modular designed controls forincreased flexibility Quick connect output voltage tap adjustments UL listed,CSA certifiedColor coded charging cablesWide, hinged door for easy accessOperating and troubleshootingmanualProminently displayed labels• Voltage change-over • Fuse sizes • Charging rateadjustmentnd efficient charging every time!j Automatic operationAfter the battery is connected and the control is initiated, the Accu-Charger will automatically start the charging operation. It will continue to charge the battery until the battery is fully charged at which time the Accu-Charger will automatically terminate the operation.j Interchangeable control design The Accu-Charger is designed to allow the quick and easy installation or removal of the controls. Unmatched in the industry, this design allows controls to be interchanged in minutes for greater control, flexibility and automation of any battery charging operation.j Functional cabinet designThe cabinet is constructed with heavy-gauge sheet metal and finished with a durable, long-lasting powdered polyester baked finish. The cabinet is designed to provide direct access to the AC power connection points and conveniently facilitates any required service.j Flexible cabinet mountingAll case styles can be wall, bench or floor mounted and the B and C cases are stackable to save floor space.j Efficient, low cost operationThe copper-wound, ferroresonant transformer design of the Accu-Charger is extremely efficient, converting AC input power to useable DC output power.j Quality-built for years of trouble- free serviceQuality is the driving force behind the Accu-Charger. Its design allows it to meet the many challenges associated with charging batteries. Unmatched in construction, reliability and value, each Accu-Charger is subject to intensive quality control and test procedures to ensure many years of trouble-free service.“A” Case “B” Case “C” Casej Accu-Charger charging characteristicsThe graph shows recharge data for a complete charge cycle. Notice that as the ampere-hours (A-H) returned to the battery increase, the battery voltage increases and the charging current gradually tapers to a safe finish rate. The recharge rate starts at approximately 20 amperes per 100 ampere-hours of battery capacity at 2.13 volts per cell, then tapers to approximately 4.5 amperes per 100 ampere-hours at about 2.55 volts per cell. To assure complete recharge of a fully discharged battery, the total ampere-hours returned to the battery is a minimum of 107%.j001 extra length charging cable:Permits the charger to be installed up to 20 ft. from the battery location. See data sheet 1311.j002 parallel charging cable with SBX connector: For the simultaneous charging of two batteries, identical in cell size but having different depths of discharge, with one charger. j003 series charging cable:For the simultaneous charging of two batteries, identical in cell size, ampere-hour rating, and depth of discharge, with one charger.j010 wall mounting bracket:For B and C case chargers.j101 remote charger control box:Allows the control to be located up to 20 ft. from the charger, i.e., mezzanine or wall mounted. Note: Wiring connecting control and charger not included.j500 flange mounted fusible disconnect switch: Disconnects power to the charger before door can be opened. For B and C case chargers and 480 volt operation only. Mounted beside door.j512 single point wiring, 2 circuitj513 single point wiring, 3 circuit:Chargers are stacked two or three high, wired for single pointAC connection.Accu-Charger accommodates interchangeable control designDISTRIBUTED BY:jstart/stop control utilizing the patented PT/DV/DT charge termination technique, or rate of change of battery voltage with respect to time. This proprietary technique used in conjunction with the tapered curve of the charger ensures that the battery is precisely charged, never over or under charged. The AC1000 stores 9 items of information for the most recent charge cycle that can be reviewed at the touch of a single button. Other features include digital display,battery/charger mismatch protection, dual back-up timers, delayed start, cool down, refresh charge, forming cycles, extended run time, auto equalize, selectable VT termination, push-to-start and fault lockout operation. The AC1000 uses the combination of the digital ammeter and 4 status LED’s to indicate V/C, Amps and charge status of the charge cycle. See data sheet 1322 for more information.features including a sealed-membrane keypad, refresh charge, extended run time, high-current shutdown, battery/charger mismatch discrimination, new battery recognition after AC fail, automatic or manual equalize operation, and cool down. It uses a PT/DV/DT charge termination technique to ensure that the rate of change for both battery voltage and current always provides an efficient and accurate termination of charge. See data sheet 1320 for more information.jstart/stop control that uses thepatented PT/DV/DT chargetermination technique, or rate ofchange of battery voltage with respectto time. This technique provides anefficient charge every time andprotects the battery from being overor under charged. The AC500features include 72 hour refresh,manual and auto equalize, andprovides safety features such asAC fail recovery, battery/chargerdisconnect shutdown and backup timer protection. Availablewith or without analog ammeter. See data sheet 1323 formore information.With the addition of an optional expansion board, the AC2000Because we continually improve our products,specifications are subject to change without notice.©2000, AMETEK, Inc. Prestolite Power, Troy, OhioData Sheet: 1305 11/00 5M Printed in U.S.A.Replaces: 11/99*Not UL or CSA listed and not available in 50 Hz.NOTE 1: Single phase chargers can be connected to one phase of a three-phase power system.NOTE 2: Contact factory for availability on non-standard voltages, non-standard cell sizes, 50 Hertz chargers, or special applications.NOTE 3: All chargers are furnished with standard nonexplosive-proof battery charging connector and 8 ft. (A case) or 10 ft. (B and C case) output cable.NOTE 4: Standard voltages for single and three phase models are 208/240/480. Alternate voltage configuration 240/480/575.NOTE 5: Not all options are available for models listed, contact factory for availability.Accu-Charger modelsApplicationOutputModel NumberAC Input, AmperesWeight, lbs.No.battery cells 666666666912121212121212121212161818181818181818181818181824242424242424242424243636363636363640404040Recommended battery ampere-hour range for8 hour charge0-180181-250251-380381-450451-510511-600601-750751-880881-1050381-4500-250251-380381-450451-510511-600601-750751-880881-10501051-12001201-1400751-8800-250251-380381-450451-510511-600601-750751-880881-965661-1020966-10501051-12001201-14001401-1600181-2500-380181-250381-450451-600601-750751-880881-965881-10501051-12001201-14000-250251-380381-450451-600601-750751-880881-965451-550511-600601-725751-880DC output amperes 2.13 v/cell 365076901021201501762109050769010212015017621024028017650769010212015017619320421024028032050765090120150176193210240280507690120150176193110120750176A case 180A1-6250A1-6380A1-6450A1-6250A1-12380A1-12250A1-18 B case510B1-6600B1-6750B1-6880B1-6450B1-12510B1-12600B1-12750B1-12880B1-12380B1-18450B1-18510B1-18600B1-18*750B1-18250B1-24380B1-24450B1-24C case600C3-6750C3-6880C3-61050C3-6450C3-9450C3-12510C3-12600C3-12750C3-12880C3-121050C3-121200C3-121400C3-12880C3-16380C3-18450C3-18510C3-18600C3-18750C3-18880C3-18965C3-181020C1-181050C3-181200C3-181400C3-181600C3-18250C3-24450C3-24600C3-24750C3-24880C3-24965C3-241050C3-241200C3-241400C3-24250C3-36380C3-36450C3-36600C3-36750C3-36880C3-36965C3-36550C1-40600C3-40725C3-40880C3-401-phase 120/208/240volts 6.0/3.5/3.08.1/4.7/4.113.2/7.6/6.615.0/8.7/7.616.7/9.6/8.41-phase 208/240/480, 575volts (see notes)3.5/3.0/1.5, 1.04.7/4.1/2.0, 1.57.6/6.6/3.3, 2.88.7/7.6/3.8, 3.110.6/9.2/4.6, 3.811.5/10.0/5.0, 4.215.2/13.2/6.6, 5.517.0/15.0/7.5, 6.59.6/8.4/4.2, 3.514.5/12.6/6.3, 5.216.8/14.6/7.3, 6.118.5/16.1/8.1, 6.722.7/19.8/9.9, 8.229.1/25.3/12.7, 10.534.3/29.9/14.9, 12.412.8/11.1/5.6, 4.620.0/17.4/8.7, 7.224.5/21.4/10.7, 8.926.7/23.3/11.6, 9.731.1/27.1/13.5, 11.342.9/37.4/18.7, 15.553.4/46.6/23.3, 19.417.4/15.2/7.6, 6.325.1/21.9/10.9, 9.131.5/27.5/13.7, 11.462.2/54.2/27.1, 22.63-phase 208/240/480, 575volts (see notes)6.1/5.3/2.6, 2.29.0/8.0/4.0, 3.310.5/9.0/4.5, 3.710.7/9.2/4.6, 3.86.7/6/3, 2.58.2/7.1/3.6, 3.09.4/8.2/4.1, 3.411.2/9.7/4.9, 4.114.7/12.9/6.4, 5.317.7/15.5/7.7, 6.421.3/18.6/9.3, 7.723.2/20.1/10.0, 8.528.0/25.0/12.5, 10.523.3/20.3/10.2, 8.511.0/10.0/5.0, 4.013.3/11.6/5.8, 4.815.7/13.7/6.9, 5.717.3/15.1/7.6, 6.322.9/19.9/10.0, 8.324.2/21.1/10.5, 8.825.8/22.5/11.2, 9.329.0/25.2/12.6, 10.533.6/29.3/14.7, 12.237.2/32.4/16.2, 13.548.6/42.4/21.2, 17.68.9/7.7/3.9, 3.217.0/14.8/7.4, 6.222.5/19.6/9.8, 8.228.1/24.5/12.2, 10.235.3/30.8/15.4, 12.836.6/31.9/15.9, 13.241.1/35.8/17.9, 14.943.4/37.8/18.9, 15.755.5/48.4/24.2, 20.112.5/11.0/5.5, 4.520.5/18.0/9.0, 7.527.5/24.0/12.0, 10.032.2/28.1/14.0, 11.743.6/38.0/19.0, 15.8NA/43.0/21.5, 17.9NA/48/24, 2036.6/31.9/16, 13.341.4/36/18, 15NA/47/23.5, 19.6Approx.shipping weight 758595110120185/225190/290205/28529022095105190/280195/283205/285230/295235/310330370410320110190/290205/295215/300225/310290/320370380335385425450550195219285225/2903203803753804504705103103253653904154854903754654905152220 Corporate Drive j Troy, Ohio j 45373-1099 j 800 367 2002。
富力电子 RT9525 单元型立物电池充电器说明书

1DS9525-01 May 2011Linear Single Cell Li-Ion Battery Charger with Auto Power PathGeneral DescriptionThe RT9525 is an integrated single cell Li-ion battery charger with Auto Power Path Management (APPM). No external MOSFET s are required. The RT9525 enters sleep mode when power is removed. Charging tasks are optimized by using a control algorithm to vary the charge rate including pre-charge mode, fast charge mode and constant voltage mode. For the RT9525, the charge current can also be programmed with an external resister.Additionally, the internal thermal feedback circuitry regulates the die temperature to optimize the charge rate for all ambient temperatures. The charging task will always be terminated in constant voltage mode when the charging current reduces to the termination current of 20%I CHG_FAST . Other features include under voltage protection and over voltage protection for the VIN supply.Featuresz 28V Maximum Rating for VIN Powerz Selectable Power Current Limit (0.1A / 0.5A / 1.5A)z Integrated Power MOSFETsz Auto Power Path Management (APPM)zProgrammable Charging Current Timer and Safe Charge Timerz Under Voltage Protection z Over Voltage Protectionz Power Good and Charger Status Indicator z Optimized Charge Rate via Thermal Feedback z 16-Lead WQFN PackagezRoHS Compliant and Halogen FreeApplicationsz Digital CameraszPDAs and Smart Phones zPortable InstrumentsOrdering InformationNote :Richtek products are :` RoHS compliant and compatible with the current require-ments of IPC/JEDEC J-STD-020.` Suitable for use in SnPb or Pb-free soldering processes.Pin Configurations(TOP VIEW)WQFN-16L 3x3BAT TS BAT NC SYS SYS E N 2E N 1G N DI S E T A S Y S O F F V I NT I M E RENP G O O D CHGMarking InformationJG = : Product CodeYMDNN : Date CodeG : Green (Halogen Free and Pb Free)2DS9525-01 May 2011Typical Application Circuit3DS9525-01 May 2011Function Block Diagram4DS9525-01 May 2011Electrical Characteristics(V IN = 5V, V BAT = 4V, T A = 25°C , unless otherwise specification)Absolute Maximum Ratings (Note 1)zSupply Input Voltage, V IN ------------------------------------------------------------------------------------------------−0.3V to 28V z CHG, PGOOD--------------------------------------------------------------------------------------------------------------−0.3V to 28V z Other Pins-------------------------------------------------------------------------------------------------------------------−0.3V to 6V z CHG, PGOOD Continuous Current ------------------------------------------------------------------------------------20mA z BAT Continuous Current (total in two pins) (Note 2)------------------------------------------------------------2.5A z Power Dissipation, P D @ T A = 25°CWQFN-16L 3x3------------------------------------------------------------------------------------------------------------1.471W z Package Thermal Resistance (Note 3)WQFN-16L 3x3, θJA -------------------------------------------------------------------------------------------------------68°C/W WQFN-16L 3x3, θJC ------------------------------------------------------------------------------------------------------7.5°C/W z Lead Temperature (Soldering, 10 sec.)-------------------------------------------------------------------------------260°C z Junction T emperature -----------------------------------------------------------------------------------------------------150°Cz Storage T emperature Range --------------------------------------------------------------------------------------------−65°C to 150°C z ESD Susceptibility (Note 4)HBM (Human Body Mode)----------------------------------------------------------------------------------------------2kV MM (Machine Mode)------------------------------------------------------------------------------------------------------200VRecommended Operating Conditions (Note 5)z Supply Input Voltage, V IN (EN2 = H, EN1 = L)---------------------------------------------------------------------4.45V to 6V z Supply Input Voltage, V IN (EN2 = L, EN1 = X)---------------------------------------------------------------------4.65V to 6V z Junction T emperature Range --------------------------------------------------------------------------------------------−40°C to 125°C zAmbient T emperature Range --------------------------------------------------------------------------------------------−40°C to 85°C5DS9525-01 May 2011To be continued6DS9525-01 May 2011Note 1. Stresses listed as the above “Absolute Maximum Ratings ” may cause permanent damage to the device. These are forstress ratings. Functional operation of the device at these or any other conditions beyond those indicated in the operational sections of the specifications is not implied. Exposure to absolute maximum rating conditions for extended periods may remain possibility to affect device reliability.Note 2. Guaranteed by design.Note 3. θJA is measured in natural convection at T A = 25°C on a high-effective thermal conductivity four-layer test board ofJEDEC 51-7 thermal measurement standard. The measurement case position of θJC is on the exposed pad of the package.Note 4. Devices are ESD sensitive. Handling precaution is recommended.Note 5. The device is not guaranteed to function outside its operating conditions.7DS9525-01 May 2011Typical Operating CharacteristicsLoad Transient ResponseTime (1ms/Div)APPM, 1.5A Mode, V IN = 5V, V BAT = 3.7V R ISETA = 1k Ω, I SYS = 0 to 2ASYSOFF On/Off With Input Power Time (5ms/Div)V BAT (5V/Div)V SYSOFF (5V/Div)V SYS (5V/Div)I BAT(200mA/Div)V IN = 6V, V BAT= 3.7V, 1.5A Mode, R ISETA = 1k ΩV IN = 5V, V BAT = 3.7V, 1.5A Mode, R ISETA = 1k ΩCharger Detect SequenceTime (10ms/Div)V BAT (2V/Div)I BAT(500mA/Div)SYSOFF On/Off Without Input PowerTime (5ms/Div)V BAT (5V/Div)V SYSOFF (5V/Div)V SYS (5V/Div)I BAT(500mA/Div)V IN = NC, V BAT = 3.7V, 1.5A Mode,R ISETA = 1k Ω, R SYS = 10k ΩOVP FaultTime (50μs/Div)V SYS (2V/Div)V IN (10V/Div)V BAT (1V/Div)I BAT(500mA/Div)V IN = 5V to 15V, V BAT = 3.7V,1.5A Mode, R ISETA = 1k Ω, R SYS = 10ΩV INV SYSV BATI BATTime (250μs/Div)V IN (5V/Div)V BAT (2V/Div)I BAT(500mA/Div)V IN = 5V, V BAT = 3.7V, R ISETA = 620ΩBAT(1V/Div)SYS(1V/Div)V BAT = 3.7V, V SYS = GND9DS9525-01 May 2011OVP Threshold Voltage vs. Temperature6.336.366.396.426.456.486.516.54-50-25255075100125Temperature (°C)O V P T h r e s h o l d V o l t a g e (V )Charger Current vs. Temperature0.0068.75137.50206.25275.00343.75412.50481.25550.00-50-25255075100125Temperature (°C)C h a r g e r C u r r e n t (mA )Dropout Voltage (In-Out) vs. Temperature050100150200250300350400450-50-25255075100125Temperature (°C)D r o p o u t V o l t a g e (mV )Dropout Voltage (Bat-Out) vs. Temperature010203040506070-50-25255075100125Temperature (°C)D r o p o u t V o l t a g e(m V )10DS9525-01 May 2011 Application InformationThe RT9525 is a fully integrated single cell Li-ion battery charger ideal for portable applications. The internal thermal feedback circuitry regulates the die temperature to optimize the charge rate for all ambient temperatures. Other features include under voltage protection and over voltage protection.Pre-Charge ModeWhen the output voltage is lower than 2.8V, the chargingcurrent will be reduced to a fast charge current ratio set by R ISETA to protect the battery life time.Fast Charge ModeWhen the output voltage is higher than 3V, the charging current will be equal to the fast charge current set by R ISETA .Constant Voltage ModeWhen the output voltage is near 4.2V and the charging current falls below the termination current, after a deglitch time check of 25ms, the charger will become disabled and CHG will go from L to H.Re-Charge ModeWhen the chip is in charge termination mode, the charging current will gradually go down to zero. However, once the voltage of the battery drops to below 4V, there will be a deglitch time of 100ms, and then the charging current will resume again.Charging Current DecisionThe charge current can be set according to the following equations :I CHG_FAST = V ISETA / R ISETA x 300 (A)I CHG_PRE = 10% x I CHG_FAST (A)where V ISETA unit = V; R ISETA unit = ΩTime FaultThe Fast Charge Fault Time can be set according to the following equations :Fast Charge Fault Time : t FCHG = 14400 x C TIMER (s)Pre-Charge Fault Time : t PCHG = 1/8 x t FCHG (s)where C TIMER unit is μF.During the fast charge phase, several events may increase the timer duration.For example, the system load current may have activated the APPM loop which reduces the available charging current, the device has entered thermal regulation because the IC junction temperature has exceeded T REG .During each of these events, if 3V < V BAT < 4V, the internal timers are slowed down proportionately to the reduction in charging current. However, once the duration exceeds the fault time, the CHG output will flash at approximately 2Hz to indicate a fault condition and a charger current ~1mA.t FCHG_true = t FCHG xt FCHG_true : modified timer in fast charge t FCHG : original timer in fast charget FCHG = 14400 sec x ( )t PCHG =t PCHG : timer in pre-charge Time fault release :(1) Re-plug power (2) Toggle /EN(3) Enter/Exit USB suspend mode (4) Removes Battery (5) OVPNote that the fast charge fault time is independent of the charge current.Power GoodVIN Power Good (PGOOD = L)ISETA2V TIMERC 1μF FCHGt 8DS9525-01 May 2011Charge EnableWhen EN is low, the charger turns on. When EN is high,the charger turn off. EN is pulled low for initial condition.Battery Pack Temperature MonitoringThe RT9525 features an external battery pack temperaturemonitoring input. The TS input connects to the NTC thermistor in the battery pack to monitor battery temperature and prevent dangerous over temperature conditions. If at any time the voltage at TS falls outside of the operating range, charging will be suspended. The timers maintain their values but suspend counting. When charging is suspended due to a battery pack temperature fault, the CHG pin remains low and continues to indicate charging.When temperature reaches at “Too Cold ” state,R NTC = R COLDWhen temperature reaches at “Too Hot ” state,R NTC = R HOTFrom (1), (2), the R T1 and R T2 can be calculated by the following equations :T1COLD T2NTC T1COLD T2NTC (R + R )R I = 2.1V (V)(R + R ) + R where I = 75 A (typ.)μ××T1HOT T2NTC T1HOT T2(R + R )R I = 0.3V (V)(R + R ) + R ×× (1)(2)HOT COLD T1T1 HOT 1500(R + R )R 3000μμ−×=+Figure 1R Suspend ModeSet EN1 = EN2 = H, and the charger will enter Suspend Mode. In Suspend Mode, CHG is in high impedance and I SUS(MAX) < 330μA.Power SwitchFor the RT9525, there are three power scenarios :(1) When a battery and an external power supply (USB or adapter) are connected simultaneously :If the system load requirements exceed that of the input current limit, the battery will be used tosupplement the current to the load. However, if the system load requirements are less than that of the input current limit, the excess power from the external power supply will be used to charge the battery.(2)When only the battery is connected to the system :The battery provides the power to the system.(3)When only an external power supply is connected to the system :The external power supply provides the power to the system.APPM Profile 1.5A ModeI BAT I SYSI V INV BAT V INV SYS V ADPM Thermal Regulation and Thermal Shutdown The RT9525 provides a thermal regulation loop function to monitor the device temperature. If the die temperature rises above the regulation temperature, T REG , the charge current will automatically be reduced to lower the die temperature. However, in certain circumstances (such as high VIN, heavy system load, etc.) even with the thermal loop in place, the die temperature may still continue to increase. In this case, if the temperature rises above the thermal shutdown threshold, T SD , the internal switch between VIN and SYS will be turned off. The switch between the battery and SYS will remain on, however, to allow continuous battery power to the load. Once the die temperature decreases by ΔT SD , the internal switch between VIN and SYS will be turned on again and the device returns to normal thermal regulation.Input DPM ModeFor the RT9525, the input voltage is monitored when the USB100 or USB500 is selected. If the input voltage is lower than V DPM , the input current limit will be reduced to stop the input voltage from dropping any further. This can prevent the IC from damaging improperly configured or inadequately designed USB sources.APPM ModeOnce the sum of the charging and system load currents becomes higher than the maximum input current limit,the SYS pin voltage will be reduced. When the SYS pin voltage is reduced to V APPM , the RT9525 will automatically operate in APPM mode. In this mode, the charging current is reduced while the SYS current is increased to maintain system output. In APPM mode, the battery termination function is disabled.Battery Supplement Mode Short Circuit Protect In APPM mode, the SYS voltage will continue to drop if the charge current is zero and the system load increases beyond the input current limit. When the SYS voltage decreases below the battery voltage, the battery will kick in to supplement the system load until the SYS voltage rises above the battery voltage.While in supplement mode, there is no battery supplement current regulation. However, a built in short circuit protection feature is available to prevent any abnormal current situations. While the battery is supplementing the load, if the difference between the battery and SYS voltage becomes more than the short circuit threshold voltage,SYS will be disabled. After a short circuit recovery time,t SHORT_R , the counter will be restarted. In supplement mode, the battery termination function is disabled. Note that for the battery supply mode exit condition, V BAT −V SYS < 0V.Battery Disconnect (SYSOFF input)The RT9525 features a SYSOFF input that allows the user to turn off the switch to disconnect the battery from the SYS pin.DS9525-01 May 2011I BAT I SYSI USB T1T2T3T4T5T6T7V BATV USB V SYS V APPM USB 500mA ModeThermal ConsiderationsFor continuous operation, do not exceed absolute maximum junction temperature. The maximum power dissipation depends on the thermal resistance of the IC package, PCB layout, rate of surrounding airflow, and difference between junction and ambient temperature. The maximum power dissipation can be calculated by the following formula :P D(MAX) = (T J(MAX) − T A ) / θJAwhere T J(MAX) is the maximum junction temperature, T A is the ambient temperature, and θJA is the junction to ambient thermal resistance.For recommended operating condition specifications of the RT9525, the maximum junction temperature is 125°C and T A is the ambient temperature. The junction to ambient thermal resistance, θJA , is layout dependent. For WQFN-16L 3x3 packages, the thermal resistance, θJA , is 68°C/W on a standard JEDEC 51-7 four-layer thermal test board.The maximum power dissipation at T A = 25°C can be calculated by the following formula :P D(MAX) = (125°C − 25°C) / (68°C/W) = 1.471W for WQFN-16L 3x3 packageThe maximum power dissipation depends on the operating ambient temperature for fixed T J(MAX) and thermal resistance, θJA . For the RT9525 package, the derating curve in Figure 2 allows the designer to see the effect of rising ambient temperature on the maximum power dissipation.Figure 2. Derating Curve for the RT9525 Package0.000.200.400.600.801.001.201.401.60255075100125Ambient Temperature (°C)M a x i m u m P o w e r D i s s i p a t i o n (W )Layout ConsiderationsThe RT9525 is a fully integrated low cost single cell Li-Ionbattery charger ideal for portable applications. Careful PCBlayout is necessary. For best performance, place allperipheral components as close to the IC as possible. Ashort connection is highly recommended. The followingguidelines should be strictly followed when designing aPCB layout for the RT9525.` Input and output capacitor should be placed close to IC andconnected to ground plane. The trace of input in the PCBshould be placed far away from the sensitive devices ANDshielded by the ground.` The GND and exposed pad should be connected to a strongground plane for heat sinking and noise protection.` The connection of R ISETA should be isolated from othernoisy traces. A short wire is recommended to prevent EMIand noise coupling.Figure 3. PCB Layout GuideDS9525-01 May 2011Richtek Technology CorporationHeadquarter5F, No. 20, Taiyuen Street, Chupei City Hsinchu, Taiwan, R.O.C.Tel: (8863)5526789 Fax: (8863)5526611Information that is provided by Richtek Technology Corporation is believed to be accurate and reliable. Richtek reserves the right to make any change in circuit design, specification or other related things if necessary without notice at any time. No third party intellectual property infringement of the applications should be guaranteed by users when integrating Richtek products into any application. No legal responsibility for any said applications is assumed by Richtek.Richtek Technology CorporationTaipei Office (Marketing)5F, No. 95, Minchiuan Road, Hsintien City Taipei County, Taiwan, R.O.C.Tel: (8862)86672399 Fax: (8862)86672377Email:*********************W-Type 16L QFN 3x3 Package。
建立NPI线评估报告

关于成立NPI生产线的评估报告
一.目的:
为了迎合公司长远发展,根据市场需求,对高端、高仿产品的制造和导入能够快速的做出反应,新产品能够缩短验证周期,提前抢占市场,加强竞争优势,在交货方面能够快速的清尾,小批量生产、产线效率异常疏导、新员工技能操作指导、高端产品的生产等,综合各方面因素从长远考虑,公司高层决定成立一支由专长技能尖子兵组成的小组,形成一支类似特种兵形式的特殊小组(我司暂命名为NPI小组);二.线体规划与生产流程:
预置NPI产线为T1-T2,U型流水线模式;
三.设备清单:
1.行业设备参考清单:
2. 目前我司设备清单:
设备清单.xls
3. 设备需求清单:
四. 人力配置:
从产线技术能手挑选后进行培训,根据人员综合情况考察后录入NPI 线员工,编制10-15人左右,加入特种兵小团队的效应会给整个制造带来技术学习动力; 具体录用参照《鹏翔员工技能比赛报告》结果为依据;团队建立后进行一系列培训,使每个人都能独当一面,素质和技能、执行力得到理想效果;
鹏翔科技员工活动项目报告.ppt
军训的目的和意义.
ppt
五.后期实施与规划:
前期由领导协调一小批高端机型,用于工厂的经验摸索与实际线体配置评估使用;作为练兵平台,对NPI团队进行实际能力评估;
产线主要管控点为防尘措施,增加防尘箱构思,用实物机型做详细的线体规划与配置等细节工作;。
MIC45205评估板:26V 6A DC-到-DC电源模块,超轻负载和超速控制是Micrel公司的

MIC45205 Evaluation Board26V/6A DC-to-DC Power ModuleGeneral DescriptionMicrel’s MIC45205 is a synchronous step-down regulatormodule, featuring a unique adaptive ON-time controlarchitecture. The module incorporates a DC-to-DCcontroller, power MOSFETs, bootstrap diode, bootstrapcapacitor, and an inductor in a single package; simplifyingthe design and layout process for the end user.This highly integrated solution expedites system designand improves product time-to-market. The internalMOSFETs and inductor are optimized to achieve highefficiency at a low output voltage. The fully optimizeddesign can deliver up to 6A current under a wide inputvoltage range of 4.5V to 26V, without requiring additionalcooling.The MIC45205-1 uses Micrel’s HyperLight Load®(HLL)MIC45205-2 uses Micrel’s Hyper Speed Control™architecture which enables ultra-fast load transientresponse, allowing for a reduction of output capacitance.The MIC45205 offers 1% output accuracy that can beadjusted from 0.8V to 5.5V with two external resistors.The basic parameters of the evaluation board are:•Input: 4.5V to 26V•Output 0.8V to 5V at 6A•600kHz Switching Frequency−Adjustable 200kHz to 600kHzDatasheets and support documentation are available onMicrel’s web site at: .RequirementsThe MIC45205-1 and MIC45205-2 evaluation boardrequires only a single power supply with at least 10Acurrent capability. No external linear regulator is requiredto power the internal biasing of the IC because theMIC45205 has an internal PVDD LDO. In the applicationswith VIN < +5.5V, PVDD should be tied to VIN to bypassthe internal linear regulator. The output load can either bea passive or an active load.PrecautionsThe MIC45205 evaluation board does not have reversepolarity protection. Applying a negative voltage to the VINand GND terminals may damage the device. Themaximum VIN of the board is rated at 26V. Exceeding 30Von the VIN could damage the device.Getting Started1. VIN SupplyConnect a supply to the VIN and GND terminals,paying careful attention to the polarity and the supplyrange (4.5V < VIN < 26V). Monitor IIN with a currentmeter and monitor input voltage at VIN and GNDterminals with a voltmeter. Do not apply power untilStep 4.2. Connect Load and Monitor OutputConnect a load to the VOUT and GND terminals. Theload can be either a passive (resistive) or an active (asin an electronic load) type. A current meter may beplaced between the VOUT terminal and load tomonitor the output current. Ensure the output voltageis monitored at the VOUT terminal.3. Enable InputThe EN pin has an on board 100kΩpull-up resistor(R10) to VIN, which allows the output to be turned onwhen PVDD exceeds its UVLO threshold. An ENconnector is provided on the evaluation board forusers to easily access the enable feature. Applying anexternal logic signal on the EN pin to pull it low orusing a jumper to short the EN pin to GND will shut offthe output of the MIC45205 evaluation board.4. Turn PowerTurn on the VIN supply and verify that the outputvoltage is regulated to 5V.Ordering InformationPart Number DescriptionMIC45205-1YMP EV MIC45205-1 Evaluation BoardMIC45205-2YMP EV MIC45205-2 Evaluation BoardFeaturesFeedback ResistorsThe output voltage on the MIC45205 evaluation board, which is preset to 5.0V, is determined by the feedback divider, as illustrated in Equation 1:+×=BOTTOMREF OUT R R141V V Eq. 1where V REF = 0.8V, and R BOTTOM is one of R3 thru R9. Leaving the R BOTTOM open by removing all jumpers on the feedback headers gives a 0.8V output voltage. All other voltages not listed above can be set by modifying R BOTTOM value according to Equation 2:REFOUT REFBOTTOM V V V R1R −×=Eq. 2Note that the output voltage should not be set to exceed 5V.Table 1. Typical Values of Some Components V OUT VIN R14(Top Feedback Resistor)R(Bottom Feedback Resistor)C14 (C ff ) C OUT 1.0V 5V to 26V 10kΩ 40.2kΩ 2.2nF 100µF/6.3V 1.2V 5V to 26V 10kΩ 20.0kΩ 2.2nF 100µF/6.3V 1.5V 5V to 26V 10kΩ 11.5kΩ 2.2nF 100µF/6.3V 1.8V 5V to 26V 10kΩ 8.06kΩ 2.2nF 100µF/6.3V 2.5V 5V to 26V 10kΩ 4.75kΩ 2.2nF 100µF/6.3V 3.3V 5V to 26V 10kΩ 3.24kΩ 2.2nF 100µF/6.3V 5V7V to 26V10kΩ1.91kΩ2.2nF100µF/6.3VSW NodeA test pad is placed for monitoring the switching waveform, which is one of the most critical waveforms for the converter.Current LimitThe MIC45205 uses the R DS(ON) of the low-side MOSFET and external resistor connected from the ILIM pin to the SW node to decide the current limit.Figure 1. MIC45205 Current-Limiting CircuitIn each switching cycle of the MIC45205, the inductor current is sensed by monitoring the low-side MOSFET in the OFF period. The sensed voltage V(ILIM)is compared with the power ground (PGND) after a blanking time of 150ns. In this way the drop voltage over the resistor R15 (V CL) is compared with the drop over the bottom FET generating the short current limit. The small capacitor (C15) connected from ILIM pin to PGND filters the switching node ringing during the off-time allowing a better short-limit measurement. The time constant created by R15 and C15 should be much less than the minimum off time.The V CL drop allows programming of short limit through the value of the resistor (R15) if the absolute value of the voltage drop on the bottom FET is greater than V CL. In that case the V(ILIM)is lower than PGND and a short circuit event is triggered. A hiccup cycle to treat the short event is generated. The hiccup sequence including the soft-start reduces the stress on the switching FETs and protects the load and supply for severe short conditions. The short-circuit current limit can be programmed by using Equation 3:()CLCL)ON(DSPPLCLIMIVR)5.0II(R15+××D−=Eq. 3 where:I CLIM = Desired current limitR DS(ON) = On-resistance of low-side power MOSFET, 16mΩ typicallyV CL= Current-limit threshold (typical absolute value is 14mV per Electrical Characteristics in the MIC45205 data sheet)I CL= Current-limit source current (typical value is 80µA, per Electrical Characteristics in the MIC45205 data sheet). ΔI L(PP)= Inductor current peak-to-peak, since the inductor is integrated, use Equation 4 to calculate the inductor ripple current.The peak-to-peak inductor current ripple is:LfV)V(VVIswIN(MAX)OUTIN(MAX)OUTL(PP)××−×=D Eq. 4The MIC45205 has 1.0µH inductor integrated into the module. In case of hard short, the short limit is folded down to allow an indefinite hard short on the output without any destructive effect. It is mandatory to make sure that the inductor current used to charge the output capacitance during soft start is under the folded short limit; otherwise the supply will go in hiccup mode and may not be finishing the soft start successfully.The MOSFET R DS(ON) varies 30 to 40% with temperature. Therefore, it is recommended to add a 50% margin to I CLIM in the above equation to avoid false current limiting due to increased MOSFET junction temperature rise. With R15 = 1.37kΩ and C15 = 15pF, the typical output current limit is 8A.Setting the Switching FrequencyThe MIC45205 switching frequency can be adjusted by changing the value of resistors R1 and R2. The switching frequency also depends on VIN, V OUT and load conditions.Figure 2. Switching Frequency AdjustmentEquation 5 gives the estimated switching frequency:2R 1R 2R f f O SW +×=Eq. 5where: f O = 600kHzR1 = 100k Ω (recommended)R2 is selected to set the required switching frequency as shown in Figure 3:Figure 3. Switching Frequency vs. R2MIC45205 Evaluation Board SchematicFigure 4. Schematic of MIC45205 Evaluation BoardBill of MaterialsItem Part Number Manufacturer Description Qty. C1 B41125A7227M TDK(1)220µF/35V, ALE Capacitor (optional) 1 C1X, C6, C9,C10, C7, C13Open 6 C3 C3216X5R1H106M160AB TDK 10uF/50V, 1206, X5R, 10%, MLCC 1 C2, C4, C8 GRM188R71H104KA93D Murata(2)0.1µF/50V, X7R, 0603, 10%, MLCC 3 C5 C3216X5R0J107M160AB TDK 100µF/6.3V, X5R, 1206, 20%, MLCC 1 C12 C1608C0G1H222JT TDK 2.2nF/50V, NP0, 0603, 5%, MLCC 1 C11 GRM1885C1H150JA01D Murata 15pF/50V, NP0, 0603, 5%, MLCC 3 CON1, CON2,CON3, CON48174 Keystone(3)15A, 4-Prong Through-Hole Screw Terminal 4 J1 M50-3500742 Harwin(4)Header 2x7 1 J2, J3, J4,TP3 − TP590120-0122 Molex(5)Header 2 6 JPx1, JPx2 Open 2 R1, R10 CRCW0603100K0FKEA Vishay Dale(6)100kΩ, 1%, 1/10W, 0603, Thick Film 2 R2, R12,R13, R16Open 4 R3 CRCW060340K2FKEA Vishay Dale 40.2kΩ, 1%, 1/10W, 0603, Thick Film 1 R4 CRCW06020K0FKEA Vishay Dale 20kΩ, 1%, 1/10W, 0603, Thick Film 1 R5 CRCW060311K5FKEA Vishay Dale 11.5kΩ, 1%, 1/10W, 0603, Thick Film 1 R6 CRCW06038K06FKEA Vishay Dale 8.06kΩ, 1%, 1/10W, 0603, Thick Film 1 R7 CRCW06034K75FKEA Vishay Dale 4.75kΩ, 1%, 1/10W, 0603, Thick Film 1 R8 CRCW06033K24FKEA Vishay Dale 3.24kΩ, 1%, 1/10W, 0603, Thick Film 1 R9 CRCW06031K91FKEA Vishay Dale 1.91kΩ, 1%, 1/10W, 0603, Thick Film 1 R11 CRCW060349K9FKEA Vishay Dale 49.9kΩ, 1%, 1/10W, 0603, Thick Film 1 R14 CRCW060310K0FKEA Vishay Dale 10kΩ, 1%, 1/10W, 0603, Thick Film 1 R15 CRCW06031K37FKEA Vishay Dale 1.37kΩ, 1%, 1/10W, 0603, Thick Film 1 R17, R18, R19 RCG06030000Z0EA Vishay Dale 0Ω Resistor, 1%, 1/10W, 0603, Thick Film 3 TP6 − TP9,JPx3, JPx41502-2 Keystone Single-End, Through-Hole Terminal 6U1 MIC45205-1YMPMicrel, Inc.(7)26V/6A DC-to-DC Power Module 1 MIC45205-2YMPNotes:1. TDK: .2. Murata: .3. Keystone: .4. Harwin: 5. Molex: .6. Vishay-Dale: .7. Micrel: .PCB Layout RecommendationsMIC45205 Evaluation Board Top LayerMIC45205 Evaluation Board Copper Layer 2PCB Layout Recommendations (Continued)MIC45205 Evaluation Board Copper Layer 3MIC45205 Evaluation Board Bottom LayerMICREL, INC. 2180 FORTUNE DRIVE SAN JOSE, CA 95131 USATEL +1 (408) 944-0800 FAX +1 (408) 474-1000 WEB Micrel, Inc. is a leading global manufacturer of IC solutions for the worldwide high-performance linear and power, LAN, and timing & communications markets. The Company’s products include advanced mixed-signal, analog & power semiconductors; high-performance communication, clock management, MEMs-based clock oscillators & crystal-less clock generators,Ethernet switches, and physical layer transceiver ICs. Company customers include leading manufacturers of enterprise, consumer, industrial, mobile, telecommunications, automotive, and computer products. Corporation headquarters and state-of-the-art wafer fabrication facilities are located in San Jose, CA, with regional sales and support offices and advanced technology design centers situated throughout the Americas, Europe, and Asia. Additionally, the Company maintains an extensive network of distributors and reps worldwide.Micrel makes no representations or warranties with respect to the accuracy or completeness of the information furnished in this datasheet. This information is not intended as a warranty and Micrel does not assume responsibility for its use. Micrel reserves the right to change circuitry, specifications and descriptions at any time without notice. No license, whether express, implied, arising by estoppel or otherwise, to any intellectual property rights is granted by this document. Except as provided in Micrel’s terms and conditions of sale for such products, Micrel assumes no liability whatsoever, and Micrel disclaims any express or implied warranty relating to the sale and/or use of Micrel products including liability or warranties relating to fitness for a particular purpose, merchantability, or infringement of any patent, copyright, or other intellectual property right.Micrel Products are not designed or authorized for use as components in life support appliances, devices or systems where malfunction of a product can reasonably be expected to result in personal injury. Life support devices or systems are devices or systems that (a) are intended for surgical implant into the body or (b) support or sustain life, and whose failure to perform can be reasonably expected to result in a significant injury to the user. A Purchaser’s use or sale of Micrel Products for use in life support appliances, devices or systems is a Purchaser’s own risk and Purchaser agrees to fully indemnify Micrel for any damages resulting from such use or sale.© 2014 Micrel, Incorporated.。
TP5100U 2A开关降压锂电池充电器芯片说明书
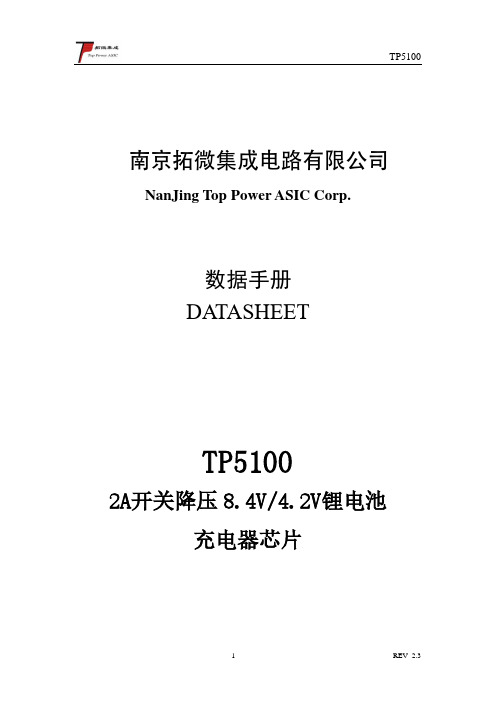
南京拓微集成电路有限公司NanJing Top Power ASIC Corp.数据手册DATASHEETTP51002A开关降压8.4V/4.2V锂电池充电器芯片概述TP5100是一款开关降压型双节8.4V/单节4.2V 锂电池充电管理芯片。
其QFN16超小型封装与简单的外围电路,使得TP5100非常适用于便携式设备的大电流充电管理应用。
同时,TP5100内置输入过流、欠压保护、芯片过温保护、短路保护、电池温度监控。
TP5100具有5V-12V 输入电压,对电池充电分为涓流预充、恒流、恒压三个阶段,涓流预充电电流、恒流充电电流都通过外部电阻调整,最大充电电流达2A 。
TP5100采用频率400kHz 的开关工作模式使它可以使用较小的外围器件,并在大电流充电中仍保持较小的发热量。
TP5100内置功率PMOSFET 、防倒灌电路,所以无需防倒灌肖特基二极管等外围保护。
特性■双/单节8.4V/4.2V 锂电池充电■内置功率MOSFET,开关型工作模式,器件发热少,外围简单■可编程充电电流,0.1A--2A ■可编程预充电电流,20%--100%■红绿LED 充电状态指示■芯片温度保护,过流保护,欠压保护■电池温度保护、电池短路保护■开关频率400KHz ,可用电感4.7uH-22uH ■PWR_ON-电源、电池供电切换控制■小于1%的充电电压控制精度■涓流、恒流、恒压三段充电,保护电池■采用QFN16 4mm*4mm 超小型封装绝对最大额定值■静态输入电源电压(VIN ):18V ■BA T :0V ~9V■BA T 短路持续时间:连续■最大结温:120℃■工作环境温度范围:-20℃~85℃■贮存温度范围:-30℃~125℃■引脚温度(焊接时间10秒):260℃应用■便携式设备、各种充电器■智能手机、PDA 、移动蜂窝电话■MP4、MP5播放器、平板电脑■航模、电动工具、对讲机典型应用VINBATTP5100CHRGSTDBY LXVSVIN=12V10uF1K1415 1. 4. 5. 162.3897GND TS1110u F10uHRs=0.06710u FVS 8.4V 2SLiG RCSR N T CR 1VREG RTRICK0.1uF1012130.1uF0.1u F0.1u FPWR_ON-6BAT+S S 34R 250K0.2Ω(建议两个0.4并联,1206封装)3Ω0.1nF 图1 TP5100为8.4V 双节锂离子电池1.5A 充电应用示意图(如需更高耐压,LX 端RC 电路需接入)VINBATTP5100CHRGSTDBYLXVSVIN=5-12V10uF1K1415 1. 4. 5. 162.3897GND TS1110u F10uHRs=0.06710u FVS4.2V LiG RCSR N T CR 1VREG RTRICK0.1uF1012130.1uF0.1u F0.1u FPWR_ON-6BAT+S S 34R 250K3Ω0.1nF 0.2Ω(建议两个0.4并联,1206封装)图2 TP5100为4.2V 单节锂离子电池1.5A 充电应用示意图封装/订购信息16引脚4mm*4mmQFN16封装顶视图(散热片接地)订单型号TP5100-QFN16器件标记 TP5100 实物图片TP5100功能方框图图3 TP5100功能框图电特性表1 TP5100电特性能参数凡注●表示该指标适合8.4V 、4.2V 模式,否则仅指8.4V ,T A =25℃,VIN=9V ,除特别注明。
Agilent 6680A系列单输出5000W DC 电源,GPIB数据手册 可靠的制造测试和长时间
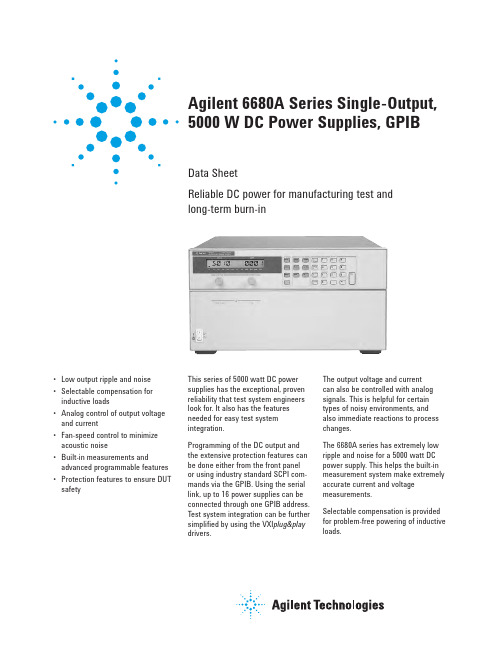
Agilent 6680A Series Single-Output, 5000 W DC Power Supplies, GPIB Data SheetReliable DC power for manufacturing test andlong-term burn-inThis series of 5000 watt DC power supplies has the exceptional, proven reliability that test system engineers look for. It also has the features needed for easy test system integration.Programming of the DC output and the extensive protection features can be done either from the front panel or using industry standard SCPI com-mands via the GPIB. Using the serial link, up to 16 power supplies can be connected through one GPIB address. Test system integration can be further simplified by using the VXI plug&play drivers. The output voltage and currentcan also be controlled with analog signals. This is helpful for certain types of noisy environments, and also immediate reactions to process changes.The 6680A series has extremely low ripple and noise for a 5000 watt DC power supply. This helps the built-in measurement system make extremely accurate current and voltage measurements.Selectable compensation is provided for problem-free powering of inductive loads.• Low output ripple and noise• Selectable compensation for inductive loads• Analog control of output voltage and current• Fan-speed control to minimize acoustic noise• Built-in measurements and advanced programmable features • Protection features to ensure DUTsafetySpecifications23Agilent models: 6680A, 6681A, 6682A, 6683A, 6684ATopSupplemental characteristics for all model numbersDC floating voltage: Output terminals can be floated up to ± 60 VDC from chassis groundRemote sensing: Up to half the rated output voltage can be dropped in each load lead. The drop in the load leads subtracts from the voltage available for the load.Command processing time: Average time required for the output voltage to begin to change following receipt of digital data is 20 ms for power supplies connected directly to the GPIB.Modulation: (Analog programming of output voltage and current):Input signal: 0 to –5 V for voltage, 0 to +5 V for currentInput impedance: 30 kΩ or greater AC input (47 to 63 Hz):180 to 235 VAC (line-to-line, 3 phase), 27.7 A rms maximum worst case, 21.4 A rms nominal; 360 to 440 VAC, 14.3 A rms maximum worst case, 10.7 A rms nominal (maximum line current includes 5% unbalanced phase voltage condition.) Output voltage derated 5% at 50 Hz and below 200 VAC Input power: 7350 VA and 6000 W maximum; 160 W at no loadGPIB interface capabilities:SH1, AH1, T6, L4, SR1, RL1, PP0, DC1, DT1, E1, and C0. IEEE-488.2 and SCPI command set.Software driver: • IVI-COM • VXI plug&playSize:425.5 mm W x 221.5 mm H x 674.7 mm D (16.75 in x 8.75 in x 25.56 in)Weight: Net, 51.3 kg (113 lbs); shipping, 63.6 kg (140 lbs)Warranty: One yearAgilent Email Updates/find/emailupdatesGet the latest information on the products and applications you select.Agilent Channel Partnersw w w /find/channelpartners Get the best of both worlds: Agilent’s measurement expertise and product breadth, combined with channel partner convenience.For more information on AgilentTechnologies’ products, applications or services, please contact your local Agilent office. The complete list is available at:/fi nd/contactusAmericas Canada (877) 894 4414Brazil (11) 4197 3600Mexico01800 5064 800United States(800) 829 4444Asia Pacifi cAustralia 1 800 629 485China 800 810 0189Hong Kong 800 938 693India 1 800 112 929Japan 0120 (421) 345Korea 080 769 0800Malaysia 1 800 888 848Singapore 180****8100Taiwan 0800 047 866Other AP Countries (65) 375 8100Europe & Middle East Belgium 32 (0) 2 404 93 40 Denmark 45 45 80 12 15Finland 358 (0) 10 855 2100France 0825 010 700**0.125 €/minuteGermany 49 (0) 7031 464 6333Ireland 1890 924 204Israel 972-3-9288-504/544Italy39 02 92 60 8484Netherlands 31 (0) 20 547 2111Spain 34 (91) 631 3300Sweden0200-88 22 55United Kingdom 44 (0) 118 927 6201For other unlisted countries: /fi nd/contactusRevised: January 6, 2012Product specifications and descriptions in this document subject to change without notice.© Agilent Technologies, Inc. 2012Published in USA, March 14, 20125990-9307EN/find/6680Agilent Advantage Services is committedto your success throughout your equip-ment’s lifetime. To keep you competitive, we continually invest in tools andprocesses that speed up calibration and repair and reduce your cost of ownership. You can also use Infoline Web Services to manage equipment and services more effectively. By sharing our measurement and service expertise, we help you create the products that change our world./quality/find/advantageservicesQuality Management SystemQuality Management Sys ISO 9001:2008DEKRA Certified Ordering informationThe 6680A power supplies come with full documentation on CD-ROM. The CD-ROM includes user’s guide, programming guide, service manual, quick start guide, and application notes.Opt 208 180 to 235 VAC, 3 phase, 47 to 63 HzOpt 400 360 to 440 VAC, 3 phase, 47 to 63 HzOpt 602 Two bus bar spacers for paralleling power supplies (p/n 5060-3514)Opt 0L1 Printed user’s and programming guidesOpt 0B3 Printed service manual Accessories1CM028A* Rack mount flange kit 88.1 mm H (3U) and 132.6 mm H (2U) – 4 brackets (5U total)1CP014A* Double rack mount flange and handle kit 88.1 mm H (2U) and 132.6 mm H (3U)E3663AC Support rails for Agilent rack cabinetsp/n 5080-2148 Serial link cable 2 m (6.6 ft.)p/n 5060-3513 Three 30 A replace-ment fuses for 180 to 235 VAC line p/n 5060-3512 Three 16 A replace-ment fuses for 360 to 440 VAC lineApplication notes6671A/72A/81A/82A/90A System DC Power Supplies Product Overview 5988-3050ENAgilent DC Power Supplies for Base Station Testing , 5988-2386EN 10 Practical Tips You Need to Know About Your Power Products , 5965-8239E* Support rails required。
Fluke FEV100 电动汽车充电站适配器套件说明书

Fluke FEV100 Adapter Kit for Electric Vehicle Charging StationsVEHICLE SIMULATIONCP Control Pilot state simulation tests different charging statesGROUNDING PROTECTIONPE Pre-Test for dangerous voltageGFCI TESTINGStay protected from and check risk of electric shockCOMPATIBILITYIntegrates into Fluke portfolio of test and measurement toolsSAE J1772Complies with North American standardsTest the functionality and safety of electrical vehicle charging stations, easily and reliablyTest the safety and performance of type 1, level 1 or level 2 elec-tric vehicle ac charging stations (EVSEs) with the Fluke FEV100. This test adapter simulates the presence of an electrical vehicle, allowing you to conduct tests in combination with appropriate test instruments such as a digital multimeter or oscilloscope. Use the FEV100 to verify an EVSE is working properly after install and during periodic maintenance, or troubleshoot an EVSE if it is not delivering the appropriate charge.SafetyEVSE charging cables may become damaged over the course of use, increasing electric shock risks to users. Stay protected from and check risk of electric shock with the GFCI trip test. This function verifies the breaker of the EVSE is connected by detecting ground faults. Additionally, the PE grounding protection pre-test veri-fies that there is no presence of dangerous voltage at the ground terminal.Simplicity and conveniencePerform a variety of tests including ground fault checks, insula-tion of wires, measuring voltage and duty cycle to see max current available for charging all with one adapter that safely integrates with the Fluke portfolio of test and measurement tools. There is no need to bring an electric vehicle onsite for EVSE troubleshooting: the adapter acts as an electric vehicle when connected to an EVSE for easy performance and maintenance testing.How to test a charging stationOnce an EVSE recognizes it is connected to a “car” and is ready for charging, the adapter tests if the EVSE is performing the way it should be. 1. Perform the safety grounding protection pre-test to verify that no dangerous voltage is present in the grounding circuit. If the indica-tor lights up, it is possible that the electrical wiring has been set up improperly or there is a grounding malfunction. In this instance stop further testing immediately and check for a possible wiring fault of the ground conductor. 2. Verify station output voltage using an additional meter, such as the 87V digital multimeter.3. Verify station maximum preset charge current using CP terminals and a meter with a duty cycle function or an oscilloscope.4. Simulate the error states as described in the SAE J1772 standard: CP error “E”, GFCI trip test, and grounding error.CP error “E” simulationThe standard SAE J1772 defines Error “E” as a state when charging station is: disconnected from vehicle, disconnected from utility, there is a loss of utility power or control pilot is short to control pilot reference (ground). This error simulation tests the station to ensure that if there is an issue with the CP of the vehicle, the station and utility will not supply a charge to the vehicle.GFCIEach EVSE is required to be equipped with GFCI protection. On many stations, the GFCI protection is fully automatic and does not need a manual reset after the GFCI circuit is tripped.Ground Error (Ground Fault) simulationThe Ground Error button simulates an interruption of the ground conductor. As a result, the pending charging process is aborted and new charging processes are prevented.Advanced tests such as insulation resistance, power quality, analysis of the control pilot wave-form and loop impedance can also be done using the adapter in conjunction with appropriate test and measurement equipment.Verifying charging voltage with vehicle simulationThe CP state rotary switch selector simulates various vehicle states when the test adapter is connected to the charging station. Vehicle states are simulated with different resistances con-nected between CP and PE conductors.Ordering informationFluke FEV100 Adapter Kit for Electric Vehicle Charging StationsIncluded• Fluke FEV100/BASIC Test Adapter• Fluke FEV-CON/TY1 Type 1 Connector & Cable • Soft Carrying Case • User Manual • 3-year warrantyVisit to get complete details on these products or ask your local Fluke sales representative.The FEV100 is compatible with the Fluke portfolio of test and measurement tools. Take critical measurements such as voltage, waveform, loop impedance and resistance.Recommended tools for use with the FEV100• 87V Industrial Multimeter• 376 FC True-RMS Clamp Meter with iFlex • 1587 FC Insulation Multimeter• 1738 Three-Phase Power Quality Logger • 1630-2 FC Earth Ground Clamp • BT521 Advanced Battery Analyzer• 1664 FC Installation Multifunction Testers• 125B Industrial ScopeMeter® Handheld OscilloscopeFluke CorporationPO Box 9090, Everett, WA 98206 U.S.A.Fluke Europe B.V.PO Box 1186, 5602 BD Eindhoven, The NetherlandsFor more information call:In the U.S.A. (800) 443-5853 or Fax (425) 446-5116In Europe/M-East/Africa +31 (0) 40 2675 200 or Fax +31 (0) 40 2675 222In Canada (800)-36-FLUKE or Fax (905) 890-6866From other countries +1 (425) 446-5500 or Fax +1 (425) 446-5116Web access: ©2021 Fluke Corporation.Specifications subject to change without notice. Printed in U.S.A. 11/2021 211051-210646-en Modification of this document is not permitted without written permission from Fluke Corporation.Fluke. Keeping your world up and running.®。
- 1、下载文档前请自行甄别文档内容的完整性,平台不提供额外的编辑、内容补充、找答案等附加服务。
- 2、"仅部分预览"的文档,不可在线预览部分如存在完整性等问题,可反馈申请退款(可完整预览的文档不适用该条件!)。
- 3、如文档侵犯您的权益,请联系客服反馈,我们会尽快为您处理(人工客服工作时间:9:00-18:30)。
qty.O Test Specification Rationalist
time
Proto Status Description rootcause action Proto PIO Lot0Remark
Environmental tests
Accelerated climatic aging test ( Damp heat test )T123307328Days Accelerated climatic aging test (Thermal cycle test )T123307328Days Hot/Cold test in storage T1233005 3 Days 4
4
Hot/Cold test in operation T1233006 3 Days Damp Heat test T1233007 3 Days 44Thermal shock test T123300850H 4
4
Dew test 结露实验T1233009 3 Days Dust wind test 吹沙尘实验T1233010 2 Days IP4x test
T1233046 2 H Dust and key strike test
T1233026 2 Days Salt mist test (Just for informantion)T1233012 3 Days 3
3
IP x1 rain test
T1233047 2 Days IP x2 rain test(only for out door projects)T1233048 2 Days IP x3 rain test(only for out door projects)T1233049 2 Days End user rain test T1233050
7 Days
Solidity tests
Drop test on marble (1.2m)
T1233019
1 Days
8
8
1. 1.2m Drop tets 5pcs ;
2. Thermal shock test
T1233008 + 1.2M drop test:T1233019 3pcs.
Free falls 0,5m repeated T1233020 1 Days 44
Mini drops endurance test T1233021 3 Days Torsion endurance test 扭曲试验
T12330880.5 Days Window press endurance test 视窗平压实验T12330410.5 Days Obverse press endurance test 正面平压T12330420.5 Days Whole press endurance test 整机压力实验T12330430.5 Days Random Vibration Test 随机振动T1233013 2 Days 33
Sinusoidal vibration test 正弦振动T1233014 2 Days Torsion test
T1233088 5 Days Bending test / Flexion endurance test (clamshell & slider)T1233045 5 Days Window Impact Test 视窗冲击实验T1233040 2 H USB push test/ Audio jack push test T123308991Days 55Pulling test (Flip)T12120111Days Pull Test 拉力测试(cable)
T1212011
1Days
3
3
Cable 部分
reuse other tests
Special Test for touch lens
Special Test for clamshell, slider phone XXX Proto QUALIFICATION PLAN
reuse other test
Test for mechanical evaluation
Mandatory test
Managed by outside lab or partly by.Managed by supplier。