车架总成检验基准书
汽车零部件检查基准书模板

零件名称I 容量频次112( ; )一级
(I)2一级
(S)
3一级
4二级
5
三级6
7
8
9
10
11
1213
14编制/日期审核/日期供应商代码批准/日期性能材料
供应商名称
会签代表/日期
尺寸检 查 项 目
规范/公差特性标识检测手段样本
外观
备注中国一汽
检查基准书零件号关重件标识
特性标识中参数识别方法:一级参数,影响安全、主要功能可靠性,有S 、I 标示的需进行标二级参数,影响装配、影响外观性能,不影响安全。
三级参数,对上述影响微弱或无
填写零件关重件属性S 、I 、C 带版本号检查项目一栏填写文字描述,比如:螺杆长度、xx 宽度等。
规范/公差一栏填写技术参数或技术要求,参数格式如下12( ;),数字(公差)。
解放质保工程师编制,日期
解放质保各组主管审核,
日期科室主任批准、日期
序号容量和频次不做规定(涉及检验时机)供应商会签
零件名称I 零件号关重件标识中国一汽
检查基准书插入图纸
对于图中检查项目需编号,编号
与前一页“检查项目序号”相对
应,如下图。
车架检验标准汇总
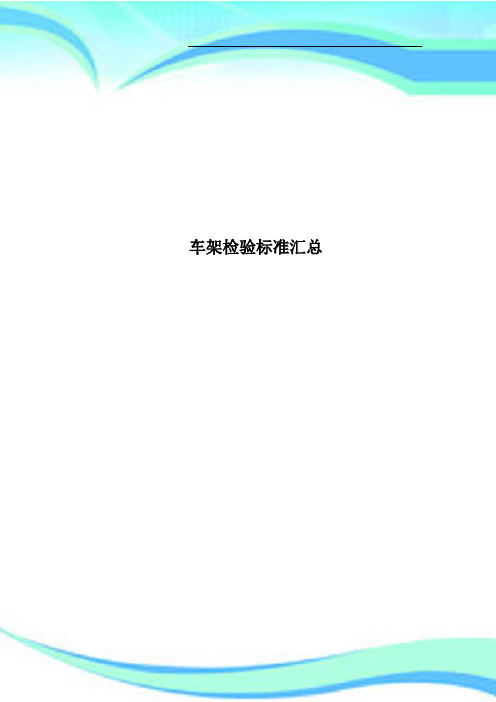
悍马车架检验标准11
悍马二代车架检验标准ﻩ13
世纪凌鹰车架检验标准15
B公主车架检验标准ﻩ16
圆梦车架检验标准ﻩ18
760车架检验标准20
小王子车架检验标准ﻩ21
小旋风车架检验标准ﻩ23
爱虎车架检验标准24
小雨点车架检验标准ﻩ25
中华海棠车架检验标准27
小帅哥车架检验标准29
小帅哥(电摩)车架检验标准…………………………………………………………………..40
风暴阳光(电摩)车架检验标准………………………………………………………………..41
五羊公主(助力车)车架检验标准…………………………………………………………….42
凌鹰(助力车)车架检验标准…………………………………………………………………..43
2.4.3车架上、下、立管直线度
车架上、下、立管直线度在300mm内,公差值为1mm。
2.4.4车架立管轴线与车架尾部中心线误差不大于3mm。
2.4.5车架中心线与平叉固定板中心线垂直度不大于2 mm。
2.4.6车架中心线与中轴中心线垂直度不大于2mm。
2.4.7中轴与平叉中心线平行度误差不大于2 mm。
2.通用技术要求
2.1外观质量
2.1.1车架各部位不得有锐边,毛刺。
2.1.2车架外表面不得有明显的划伤,碰伤,变形。
2.1.3对于外露车架其表面漆膜应符合QB/T1218标准(正视面不得有龟裂和明显的流疤,集结的沙粒,皱皮,漏漆等缺陷)。
2.2焊接要求
2.2.1各焊接处不得有漏焊,焊缝不规范,不充分及长度不够(在重点部位不得缺少3mm)等现象,安装塑件的固定片不得缺焊50%以上。
3.4各焊接处必须符合焊接要求,焊缝不得小于两工件的2/3,焊缝需平整、均匀,不得有焊缝不规范、不充分、长度不够、跑偏等现象。
车架质量检验计划书(修订)

结构分厂车架质量检验计划书为规范车架结构件质量检验,确保车架制作过程符合工艺作业指导书的要求,车架的质量符合图样要求,保证车架转序质量,杜绝不合格品转序引起下道工序的抱怨,特从外观、工艺参数符合性、尺寸、巡查项目控制方面进行策划。
一、日常巡检内容 1、外观2、工艺要求的符合性3、巡查项目序号检查项目标准要求检查方法抽样方法 备注频次数量1焊缝缺陷1)倾斜缸支座焊缝无漏焊、咬边、焊瘤缺陷目测2次/日(上午/下午各1次)抽查数量 ≥10台/次影响外观2)脚踏板外漏焊缝无漏焊、咬边、焊瘤缺陷 3)其它部位的焊缝无漏焊、咬边、焊瘤缺陷 2焊渣、飞溅油箱外壁板、挡泥板上面、倾斜缸支座周边无飞溅、焊渣 2次/日(上午/下午各1次)车架内侧焊渣、飞溅等3焊缝高度焊缝高度符合焊接作业指导书要求检具或焊缝高度测量尺抽查≥1台/次/天焊缝余高 ≤3mm序号 检查项目标准要求检查方法 抽样方法备注 1 自检记录的规范性抽查 规范 目测 2次/日,抽查工序 ≥2个/次2 自检记录项目抽查验证 填写真实,无作假信息抽查项目数据与实测值相符抽查数据:≥2项/次 3 新产品搭焊工位 搭焊符合图样要求 巡查2次/日随机抽查零部件,验证其与图纸符合性,零部件数量≥2件/次4 新员工搭焊工位5 人员变动岗位6图纸更改后产品确认符合图样要求 1次/日,抽查1件/次不同零部件序号 检查项目 标准要求检查方法 抽样方法 备注频次数量1 电流 电流符合要求 目测焊机上电流/电压表2次/日(上午/下午各1次)抽查工序 ≥2个/次与工艺焊接作业指导书上规定值比对2 电压 电压符合要求3焊丝直径 焊丝直径符合工艺要求(工艺要求直径为1.2或1.0)游标卡尺4油箱试漏气压试漏压力为2.5Kg目测气压表 抽查数量 ≥2台/次4、尺寸二、专检内容 1、报检专检数量序号 结构件报检数 抽检数量1 N ≤5 12 5<N ≤203 3 20<N ≤50 54 50<N ≤100 7 5100<N10备注:以上表格摘自《自制件检验规范》中抽查数量内容,结构分厂抽检数量参见结构件一栏。
车架检验标准

一、外观质量1、车架各部位不应有锐边、毛刺。
2、车架外表面不应有明显的划伤、碰伤、压瘪等现象。
3、车架贴花表面应平整,不应有明显的皱花、错花、大面积坏花、歪花、散花、气泡等现象。
4、车架的硬印号码应清晰、永久、唯一。
5、车架焊缝应均匀不应有漏焊、焊渣等现象。
二、装配尺寸1、前管两端孔ФXX+00.084;2、电源锁支架位置按模具定好型;e) 平叉开档尺寸XX+2.20。
三、车架立管平行度:车架立管轴线应在车架中心基准面上,其公差值为1.8㎜。
四、车架平、立叉对称度:车架平、立叉应对称于车架中心基准面,其公差值为6㎜。
五、车架平叉开口垂直度:车架左右平叉接片开口连线应与车架中心基准面垂直,其公差值为1.2㎜。
六、检验规则1、批次确定:以每交货批为一批次。
2、进厂验收项目按产品标准QB1880-2008中7.3条规定执行。
3、进厂验收检验项目按GB/T2828.1-2003标准中规定的二次正常抽样方案。
检查水平为一般检查水平(I),B类接收质量限AQL=4.0,C类接收质量限AQL=6.5。
4、批质量以每百单位产品不合格品数计算。
检查项目、检查水平、不合格分类、接收质量限(AQL)见《车架质量特性检查表》。
5、需要时,进厂验收项目可以到生产厂进行验收检验。
6、进厂验收项目检验后应作好记录,质检部负责保存记录,保存期限为二年。
7、经检验合格的产品办理入库手续;检验不合格,按不合格品管理办理规定处理。
8 外观、焊接质量用目视法进行检验。
8.1、尺寸检验使用专用、通用量具进行检测。
8.2、ФXX+00.084专用量具或游标卡尺测定;8.3、其余尺寸用游标卡尺或卷尺测定。
车架质量特性检查表。
车架检验标准汇总

车架检验标准1. 适用范围1.1本标准适用丁无锡市志达车业有限公司车架外购配件入厂时的检验。
1.2对丁不同款式的车架,可根据本标准附件《各型车架检验标准汇总》的具体要求进行检验。
2. 通用技术要求2.1外观质量2.1.1车架各部位不得有锐边,毛刺。
2.1.2车架外表面不得有明显的划伤,碰伤,变形。
2.1.3对丁外露车架其表面漆膜应符合QB/T1218标准(正视面不得有龟裂和明显的流疤,集结的沙粒,皱皮,漏漆等缺陷)。
2.2焊接要求2.2.1各焊接处不得有漏焊,焊缝不规范,不充分及长度不够(在重点部位不得缺少3mm)等现象,安装塑件的固定片不得缺焊50%以上。
2.2.2焊接面不得处丁不合理受力状态,不得产生不能复原的变形。
2.2.3不允许有虚焊,虚堆。
2.2.4焊接应该米用二氧化碳保护焊和氯弧焊。
2.4精度要求2.4.1车架立管平行度车架立管轴线应在车架中心基准面上,其公差值为 1.8mm.2.4.2车架中接头垂直度车架中接头轴线与车架中心基准面应垂直,公差值为2mm。
2.4.3车架上、下、立管直线度车架上、下、立管直线度在300mm内,公差值为1mm。
2.4.4车架立管轴线与车架尾部中心线误差不大丁 3 mm。
2.4.5车架中心线与平义固定板中心线垂直度不大丁 2 mm。
2.4.6车架中心线与中轴中心线垂直度不大丁2 mm。
2.4.7中轴与平义中心线平行度误差不大丁2 mm。
2.5对丁具体的车型,如果出现与通用标准不符的情况,应该以具体款式的要求为准。
可参加本标准附件的要求进行。
3. 检验规则3.1采用GB2828标准一次抽样,达到技术要求为合格品4. 关丁材料的通用要求:4.1车架的钢管材料:为Q195 (GB/T—700)。
4.2凡是使用钢板制造的车架附件,应该符合冷轧钢板GB 708- 88的要求。
4.3偏撑、中撑弹簧材料:弹黄钢65Mn。
4.4偏撑、中撑轴为35#钢;调质,HB= 180〜220。
车架总称的检验

项目三、车架总称的检验车架是整个汽车的基础件,汽车的各主要总成都安装在它的上面,车架是个受力很复杂的构件,它除了要承受着作用于汽车上的所有静载存以外,还要承受行使时所产生弯曲、扭曲、歪斜、局部变形裂纹,断裂及螺钉松动等损伤。
车架的损伤将降低有关总成的寿命,长期车的使用性能边坏,甚至影响到汽车的行使安全,因此车架的检查和必要修理是汽车修理中一项重要作业内容。
车架是否扭曲、弯曲变形,其几何形状的改变通常是测量钢板销中心距,通过直线和对角拉线法测量,根据测量结果进行综合分析,经检验后,如发现弯曲、扭曲变形超过允许限度,应采用特制机具或车架校正机施行冷压校正。
当车架总的情况良好,仅是个别部位产生不大弯曲时,可直接在车架上校正,如车架损坏严重,应将其全部解体进行检验校正,其检验方法及技术要求如下:1、钢板销孔中心距左右两边相应尺寸之差不得大于2MM,其中三个尺寸以前钢板后支架与后钢板前支架销中心距为最重要。
(CA10B型为2845),因为它直接影响前后桥的平行度,该段尺寸左右相差不应超过1MM。
2、各销孔中心对角线长度差不得超过3MM。
两对角线在交叉处两线间的距离,对角线的交点与车架中心线的偏移及两纵梁侧面对车架中心线的距离均不得超过2MM。
3、若二对角线不等可以认为车架歪斜,若二对线在交点处不相接触可以认为车架有扭转,若二对角的交点外不在车架中心线上或者两纵梁侧面对车架中心线距离不等,表明在车架方向发生弯曲或局部弯曲4、车架纵梁的垂直度和垂直度的检验,若起不符合要求,将影响有关总成的安装,应予校正。
平直度的检查可用拉线法,在车架纵梁上平面的最大弯曲,CA10B、NJ130型前后钢板弹簧支架之间应不大于4MM。
一般车辆在全长应不大于5MM。
,侧面的不直度应不大于1000:1.5MM,表现在纵梁侧面与直角尺尖的缝隙不应该超过1MM,否则可以前纵梁已发生扭曲变形。
5、左右钢板对中心,为了保证前后桥平行,以减小行使阻力和配件的磨损,除对车架行进钢板销孔中心距及对角线检查外还应对左右钢板萧孔的同轴度进行测量。
电动车整车检测基准书

按GB/T3566-1993第23章的规定进 行测量
确认检验
28
整车质量
A
整车质量大于40kgo
台秤
确认检验
29
蓄电池密封性
A
在正常安装、放电条件下不应有渗漏现象。
目测检查
确认检验
30
照明
A
应装有前灯、后灯或反射器,反射器 光学要求按QB2191-1995中5.3的规定
电动车成车 检测基准书
江苏XXX有限公司
标记
处数
更改文号
签名
日期
编制
标准化
图样标记
共4页
审核
批准
SAB
目测、手感
100%
6
欠压、过流保护 功能
A
控制器应具有欠压、过流保护功能和短路保 险装置,欠压保护值为42±0.5V,过流保 护值为18±1A (6管)、22±1A (9管)、28±1A (12管)。在电动车骑行时,调速应 稳定、可靠。
电动车整车性能 检测仪
100%
7
说明书
A
每辆车应具有符合GB17761T999 5. 6耍求 的说明书。
操作、手感
100%
⑦车辆行驶过程中,不得有零部件之间发生 干涉、撞击、异响等异常现象,试验后不 能丧失电动行驶功能
操作、感受
100%
⑧行驶后检查,不得有零部件变形、损坏、 松动、异常磨损、漏气、漏油等不良现象。
目测
100%
11
转向装置
A
方向把应设置限位装置,并且在其回转角范 围内应能绕方向柱灵活地转动;转向轮向左 或向右的转向角<48°,方向柱不应有轴向 松动感;方向把在其转动极限位置均不得与 其它部件发生干涉。制动器、离合器、油门、 操纵调节机构的调节余量应不小于可调节 量的二分之一。操纵拉索、车速里程表软轴、 电缆、制动软管等长度应略有裕度,在方向 把转动时,不得被夹持,不得影响相关零部 件的正常工作。油门转把应灵活,油门开启 后应能自动回位。
检查基准书(后前束连杆总成)20150603

抗拉强度 延伸率 材质
NR橡胶
可靠性 衬套拔脱力 漆膜厚度 表面耐腐蚀 焊道熔深 衬套橡胶硬度 衬套静刚度 衬套扭转刚度
≥5KN 25-30μ m 中性盐雾试验480h后零件表面不出现起泡 、红绣等现象,刮刻线锈蚀不超过10mm。
A C A
1次/批 1次/100件 1次/6个月
3-④ 3-⑤ 3-⑥ 3-⑦
4-③
衬套外径
¢48(-0.1/-0.3)mm
+0.5
B
4-④ 4-⑤ 4-⑥ 4-⑦ 4-⑧ 4-⑨ 5 6
连接杆长度 套管外径 套管高度 连接杆外径尺寸 成品尺寸 成品尺寸
174
C C A C A A C C
(¢48±0.2)mm (30±0.2)mm (¢21.5±0.2)mm (223.9±1.0)mm (7.75±0.3)mm
特性 检查特性
版本号:1 规格
漆面黑色、无划伤露底
编号: 质量等级 检查周期 供方 蓝途
全数
1
外观
焊道较饱满、无明显气孔裂纹 橡胶黑色、无裂纹
C
2-1 2-1-① 2-1-② 2-1-③ 2-1-④ 2-1-⑤ 2-1-⑥ 2-1-⑦ 2-1-⑧ 2-1-⑨ 2-2 3 3-① 3-② 3-③
拉力机 膜厚检测仪 盐雾试验机
○ ○ ○
图纸
QC/T 484-1999
熔深试验抛光机、测量显微镜 硬度测量机 衬套台架试验机 衬套台架试验机
○ × × ×
HB5282-1984 dvp dvp dvp 二级供方提供检验报告 二级供方提供检验报告 二级供方提供检验报告
汽车底盘台架试验机
○
dvp
专用检具 游标卡尺
汽车厂质量保证部技术文件车架纵梁检验作业指导书
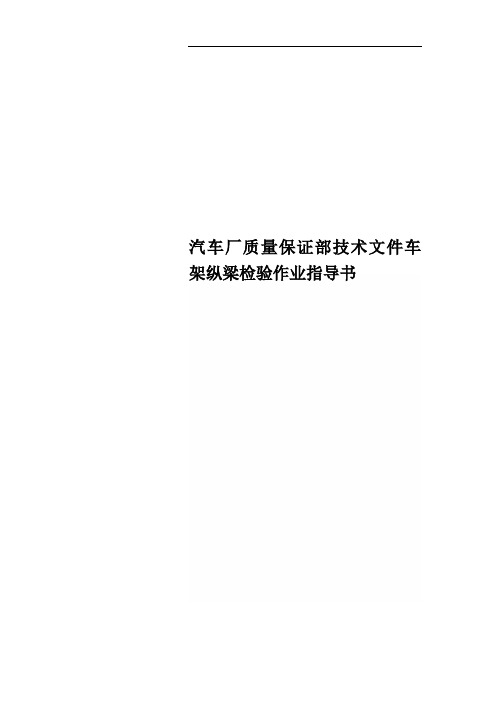
汽车厂质量保证部技术文件车架纵梁检验作业指导书一汽解放青岛汽车厂质量保证部技术文件编号:IPQC-JYZD-2-2009 批准:车架纵梁检验作业指导书2008年12月31日发布 2009年1月1日实施一汽解放青岛汽车厂质量保证部发布前言本检验作业指导书依据有关汽车标准及一汽解放青岛汽车厂技术文件制定。
是一汽解放青岛汽车厂质量保证部技术文件之一。
本检验作业指导书与国家标准、企业标准及相关技术文件相一致。
从实施之日起,原《IPQC-JYZD-2-2008车架纵梁检验作业指导书》同时废止。
各相关部门检验车架纵梁时,都需要按本检验作业指导书的规定执行。
本标准由一汽解放青岛汽车厂质量保证部起草。
本检验作业指导书起草人:吴立新本检验作业指导书审核人:石建通1 主要内容与适用范围本指导书做为车架纵梁各工序质量检验及控制的技术性说明。
本指导书适用于纵梁加工各工序有关部门。
2 术语和定义2.1 落料用冲模沿封闭线冲切板料,冲下来的部分为制件。
2.2 冲孔用冲模沿封闭线冲切板料,冲下来的部分为废料。
2.3 弯曲把平板毛坯、型材弯成一定曲率及角度形成一定形状的冲压工序。
3 制件的检验标准及要求3.1 板料检验纵梁外板及内护板下料尺寸、(侧弯)直线度与工艺要求相符,板料表面平整,不允许有影响定位的严重弯曲、翅头存在,无锈蚀、严重麻纹、明显锤印、切割焊瘤、严重划伤等质量缺陷。
检验频次及其它要求:操作者100%目视,工序检查员按首、中、末检验。
3.2 落料冲孔质量检验3.2.1 落冲模夹紧可靠,各模段对接平顺,相对错位不超过0.2mm。
检验频次及其它要求:落冲前工序检查员检验确认。
3.2.2 纵梁外板或内护板边缘平直无明显错位,落冲边及所有孔落冲毛刺不大于0.2mm,外板前端第一工艺孔到料前端头尺寸公差控制在±2mm,工艺孔位置度为Φ0.5mm,对采用后定位落冲的纵梁外板及内护板,其最后一工艺孔距板料后端头尺寸公差控制在±3mm。
整车终检基准书

B●
●
B●
●
B●
●
B●
●
B●
●
B●
●
B
●●
B●
●
第 1 页,共 24 页
4)长度允差±20mm(设计值)
11
宽度≤2500mm 允差±10mm(设计值)
高度(空载)允差±30mm(设计值)
12 四) 3C一致性
13
1)符合要求 2)贴3C标记
14
1)灯具、灯光开关安装牢固,工作正常,完好 有效
15 16
C●
●
面呈现凹凸不平且无规则
113
线状折皱的现象)
4)A区隐约可见,分布均匀,面积S<200 mm2,不影响外观
C●
●
114
5)C区严重起皱或桔皮,直接影响外观
C●
●
115
6)其它区域或缺陷情况无明显影响外观
不划 分
第 9 页,共 24 页
116
1)A、B区出现>5个
11、针孔(100×100mm2
82
25mm2
2)A区起泡面积(含单个或总面积)有≤
83
25mm2
84
3、起泡(涂层表面呈现鼓 包的现象)
3)B区起泡面积(含单个或总面积)≥80 mm2
85
4)B区起泡面积(含单个或总面积)≤80 mm2
86
5)其它区域起泡
87
1)A区无脱落
第 7 页,共 24 页
A●
●
A●
●
A●
●
B●
●
B●
●
C●
C●
●
面附着颗粒状物质的现象)
108
3)A、B区出现单个直径>0.5 mm
车架总成进货检验指导书

3)焊接缺陷探测
抗扭试验报告;
目测
目测
目测
塞尺
卷尺
游标卡尺
模具查证
角度尺
定期提供试验报告
厂家监控报告
探伤仪
首样查证
15m
3m
0-125mm
0°-360°
厂家证明
每月一次
第三方报告
每年一次
厂家每批进货
No.
修订日期
修订内容
修订单
核准
审查
制定
1)车架表面漆膜质量良好,允许有不严重流挂存在,不允许有密集针孔及桔皮存在;
2)车架各支架装配位置准确,无错装、漏装现象;
3)铆接部位铆钉头与连接件之间、连接件与车架之间间隙不超过0.2MM。
按图纸要求检验
定期要求厂家提供材质检测报告,依GB3273-1989汽车大梁用热扎钢板查证
1)焊接电流电压值;
文件编号:
零部件名称
DAB分类
车架总成进货检验指导书
文件编号
版次
3.0
图号
规格、型号
发行日期
页次
1/1
序号
检验项目
技术要求
验收器具
抽检比例
备注
名称
规
标志:
外观:
尺寸:
材质:
焊接质量
性能
1)应将车架型号、生产序列号刻在车架的固定位置上;
2)车架的固定位置上应贴有产品合格证,并标注出厂日期,加盖合格章;
车架检验标准

车架检验标准1、目的规范检验操作,发现、控制不合格产品,防止不良产品流入下道工序,同时给检验工作提供检验标准。
2、范围适用于上海联孚公司所有外协加工车架的油漆涂装质量检验。
3、引用标准下列标准包括的条文,通过在本检验作业指导书中的引用而构成本检验作业指导书的条文。
在本检验作业指导书发布时,所示版本均为有效。
所有标准都会被修订,使用本检验作业指导书的各方应探讨使用下列标准最新版本的可能性。
GB 6807 钢铁工件涂漆前磷化处理技术条件Q/LQB Y-4-2011 汽车涂层标准GB/T 13452.2-2008 色漆和清漆漆膜厚度的测定GB/T 6739-2006 漆膜硬度铅笔测定法GB/T 9286-1998 漆和清漆漆膜的划格实验4、检验条件4.1检验环境环境整洁,空气清新,不应有明显影响检验作业的热气、湿气、烟尘。
4.2检验人员检验人员辨色力正常,视力在0.8以上(含校正后)。
检验人员应经过培训并得到授权。
4.3检验仪器及量检具漆膜测厚仪、钢板尺、中华牌高级绘图铅笔(H、HB、B三种规格)、单面刀片等。
所有仪器及量检具应符合计量检定要求,并在有效的检定周期。
5、检验内容5.1酸洗磷化质量检验5.1.1外观检验目视检测,磷化后工件的颜色应为浅灰色到深灰色或彩色;膜层应结晶致密、连续和均匀;不允许有下列缺陷:a.疏松的磷化膜层b.表面有机械损伤,有锈蚀或绿斑c.局部无磷化膜(焊缝的气孔和夹渣处除外)d.表面严重挂灰。
5.1.2耐蚀性检验耐蚀性检验通常采用中性盐雾试验(浸入法)和硫酸铜点滴法,根据需要采用合适的方法检验。
a.浸入法将磷化后的工件或试样(已降至室温)浸入3﹪的氯化钠溶液中,在15~25℃下,保持规定的时间,经两小时后取出工件或试样,随之洗净、吹干,目视检查磷化表面是否出现锈蚀,表面无锈渍为合格。
出现锈渍时间越长,说明磷化膜的耐蚀性越好。
b.点滴法室温下,将蓝点试剂滴在磷化膜上,观察其变色时间。
车架检验标准汇总

车架检验标准1. 适用范围1.1 本标准适用于X市志达车业车架外购配件入厂时的检验。
1.2 对于不同款式的车架,可依据本标准附件《各型车架检验标准汇总》的具体要求进行检验。
2. 通用技术要求2.1 外观质量2.1.1 车架各部位不得有锐边,毛刺。
2.1.2 车架外外表不得有明显的划伤,碰伤,变形。
2.1.3 对于外露车架其外表漆膜应符合QB/T1218标准〔正视面不得有龟裂和明显的流疤,集结的沙粒,皱皮,漏漆等缺陷〕。
2.2 焊接要求2.2.1 各焊接处不得有漏焊,焊缝不标准,不充分及长度不够〔在重点部位不得缺少3mm〕等现象,安装塑件的固定片不得缺焊50%以上。
2.2.2 焊接面不得处于不合理受力状态,不得产生不能复原的变形。
2.2.3 不同意有虚焊,虚堆。
2.2.4 焊接应该采纳二氧化碳爱护焊和氩弧焊。
2.4 精度要求2.4.1车架立管平行度车架立管轴线应在车架中心基准面上,其公差值为1.8mm.2.4.2车架中接头垂直度车架中接头轴线与车架中心基准面应垂直,公差值为2mm。
2.4.3车架上、下、立管直线度车架上、下、立管直线度在300mm内,公差值为1mm。
2.4.4 车架立管轴线与车架尾部中心线误差不大于3 mm。
2.4.5 车架中心线与平叉固定板中心线垂直度不大于2 mm。
2.4.6 车架中心线与中轴中心线垂直度不大于2 mm。
2.4.7 中轴与平叉中心线平行度误差不大于2 mm。
2.5 对于具体的车型,如果出现与通用标准不符的情况,应该以具体款式的要求为准。
可参加本标准附件的要求进行。
3. 检验规则3.1 采纳GB2828标准一次抽样,到达技术要求为合格品。
4. 关于材料的通用要求:4.1车架的钢管材料:为Q195〔GB/T—700〕。
4.2但凡使用钢板制造的车架附件,应该符合冷轧钢板GB 708-88的要求。
4.3 偏撑、中撑弹簧材料:弹簧钢65Mn。
4.4 偏撑、中撑轴为35#钢;调质,HB=180~220。
载货汽车车架总成检验评价办法
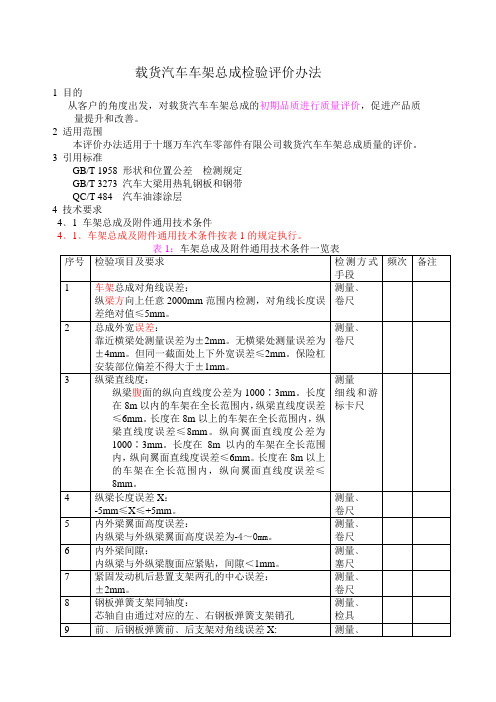
载货汽车车架总成检验评价办法1 目的从客户的角度出发,对载货汽车车架总成的初期品质进行质量评价,促进产品质量提升和改善。
2 适用范围本评价办法适用于十堰万车汽车零部件有限公司载货汽车车架总成质量的评价。
3 引用标准GB/T 1958 形状和位置公差检测规定GB/T 3273 汽车大梁用热轧钢板和钢带QC/T 484 汽车油漆涂层4 技术要求4﹑1 车架总成及附件通用技术条件4﹑1﹑车架总成及附件通用技术条件按表1的规定执行。
表1:车架总成及附件通用技术条件一览表序号检验项目及要求检测方式手段频次备注1 车架总成对角线误差:纵梁方向上任意2000mm范围内检测,对角线长度误差绝对值≤5mm。
测量﹑卷尺2 总成外宽误差:靠近横梁处测量误差为±2mm。
无横梁处测量误差为±4mm。
但同一截面处上下外宽误差≤2mm。
保险杠安装部位偏差不得大于±1mm。
测量﹑卷尺3 纵梁直线度:纵梁腹面的纵向直线度公差为1000∶3mm。
长度在8m以内的车架在全长范围内,纵梁直线度误差≤6mm。
长度在8m以上的车架在全长范围内,纵梁直线度误差≤8mm。
纵向翼面直线度公差为1000∶3mm。
长度在8m以内的车架在全长范围内,纵向翼面直线度误差≤6mm。
长度在8m以上的车架在全长范围内,纵向翼面直线度误差≤8mm。
测量细线和游标卡尺4 纵梁长度误差X:-5mm≤X≤+5mm。
测量﹑卷尺5 内外梁翼面高度误差:内纵梁与外纵梁翼面高度误差为-4~0mm。
测量﹑卷尺6 内外梁间隙:内纵梁与外纵梁腹面应紧贴,间隙<1mm。
测量﹑塞尺7 紧固发动机后悬置支架两孔的中心误差:±2mm。
测量﹑卷尺8 钢板弹簧支架同轴度:芯轴自由通过对应的左﹑右钢板弹簧支架销孔测量﹑检具9 前﹑后钢板弹簧前﹑后支架对角线误差X: 测量﹑-2mm≤X≤+2mm。
卷尺10 左纵梁上前簧前支架到后簧前支架的距离与右纵梁上前簧前支架到后簧前支架的距离的误差≤5mm。
零部件检验基准书

零部件检验基准书零部件名称车架零部件型号豪华款车架零部件重要度G √ Z Y 版本号版次更改描述编制/修订修订时间编制标准化审核审核批准受控√非受控签名日期2016年元月发布零部件检验基准书零部件名称:车架总成零部件型号:版本号项目名称技术要求检验设备重要度G Z Y检验频次抽样方案备注表单核对送货单品名规格与实物一致目测Z 按批检验依据物料检验抽样计划入场验收重量:±1%电子称Z 按批检验入场验收外观材料外观质量:无裂纹、凹坑、皱痕、碰伤、拉痕、锈蚀等缺陷目测Y 按批检验入场验收烤漆质量:涂层光滑、平整、色泽均匀、结合牢固,无划伤、流痕、露底、锈蚀等缺陷;目测Y 按批检验入场验收焊接要求:焊缝应平整均匀,连结处应圆滑过渡,无咬边、凹陷、无漏焊、虚焊、夹渣、裂纹、气孔及飞溅物等缺陷;目测G 按批检验入场验收车头管、主梁管、侧支架连接板、左边管等部位焊接时,起焊和终焊点应在零件焊缝长度上延伸5mm-10mm;游标卡尺G 按批检验入场验收表面处理:黑色电泳。
目测Y 按批检验入场验收同轴度立管的上下装方向轴承处的同轴度误差不大于0.1综合检具G 按批检验入场验收尺寸见附件,其它未注尺寸按封样Z 按批检验入场验收周期和型式检验项目(目前可以根据公司检测能力来选择,必要时要予以委外。
)项目名称实验内容及要求检验设备重要度G Z Y检验频次抽样方案备注焊接熔深焊接熔深:剖切检查平叉头管与方管、后减震支耳、熔深不小于管壁的1/3切割机、卡尺G 次/3月1件入场验收覆层硬度膜硬度:用2H铅笔在试样漆膜表面成45°,以3mm/s的速度,受力均匀地在不同部位往返划痕5次,然后用橡皮揩去石墨灰,不许划穿漆膜。
H铅笔、橡皮Y 次/1月1件入场验收覆层性能中性盐雾试验72h(NSS),无腐蚀生成物、起泡及脱落现象;耐油性:5小时无变化(汽油),耐水性:72小时无变化(50°)盐雾试验箱Y 次/1月1件入场验收主要部件厚度车架前立管厚度2.5﹢0.2,主梁管厚度2.0,主梁管加强板厚度不低于2.0mm游标卡尺G 次/1月1件入场验收振动实验平叉与车架组合震动,配重状态为,车头管方向柱部位10kg,座垫处100kg,电池处30 kg,脚踏处60 kg。
摩托车货架检验指导书

摩托车货架检验指导书摘要:一、引言二、摩托车货架检验标准1.材料要求2.设计要求3.制造要求4.安全性能要求三、检验流程1.检验准备2.现场检验3.检验结果处理4.检验周期四、常见问题及解决方案1.材料不合格2.设计缺陷3.制造质量问题4.安全性能不足五、结论正文:一、引言摩托车货架作为摩托车的重要组成部分,其质量直接影响到驾驶员和乘客的安全。
为了确保摩托车货架的质量,我国制定了严格的检验指导书。
本文将对摩托车货架的检验标准、检验流程以及常见问题进行详细解析,以指导企业和检验人员正确开展摩托车货架检验。
二、摩托车货架检验标准1.材料要求摩托车货架应采用符合国家标准的材料,具有足够的强度、耐腐蚀性和耐磨性。
常见的材料有钢铁、不锈钢、铝合金等。
检验时,需对材料的牌号、规格、力学性能等进行核实。
2.设计要求摩托车货架设计应符合国家相关法规和标准,如GB/T 1416-2009《摩托车车架》、GB 16151-2009《摩托车乘员扶手》等。
设计要求包括结构合理、安装方便、稳定可靠、美观大方等。
3.制造要求摩托车货架的制造应严格按照设计图纸和工艺要求进行,确保产品尺寸、形状和表面质量满足标准。
检验时,应对制造过程进行现场监督,确保产品质量。
4.安全性能要求摩托车货架的安全性能是检验的重要指标。
检验项目包括静态承载能力、动态承载能力、抗风性能、稳定性、刚度等。
安全性能不合格的货架严禁上市销售。
三、检验流程1.检验准备检验前,应制定详细的检验计划,明确检验项目、检验标准、检验人员和检验设备。
同时,对检验人员开展培训,确保他们熟悉检验标准和检验方法。
2.现场检验现场检验分为原材料检验、制造过程检验和成品检验。
检验人员应按照检验计划,对每个环节进行严格把关,确保货架质量。
3.检验结果处理检验完成后,检验人员应对检验数据进行整理、分析,形成检验报告。
对于不合格的项目,应提出整改要求,并督促企业及时整改。
4.检验周期摩托车货架的检验周期应根据产品类型、风险等级等因素确定。
车架检验标准

一、外观质量1、车架各部位不应有锐边、毛刺。
2、车架外表面不应有明显的划伤、碰伤、压瘪等现象。
3、车架贴花表面应平整,不应有明显的皱花、错花、大面积坏花、歪花、散花、气泡等现象。
4、车架的硬印号码应清晰、永久、唯一。
5、车架焊缝应均匀不应有漏焊、焊渣等现象。
二、装配尺寸1、前管两端孔ФXX+00.084;2、电源锁支架位置按模具定好型;e) 平叉开档尺寸XX+2.20。
三、车架立管平行度:车架立管轴线应在车架中心基准面上,其公差值为1.8㎜。
四、车架平、立叉对称度:车架平、立叉应对称于车架中心基准面,其公差值为6㎜。
五、车架平叉开口垂直度:车架左右平叉接片开口连线应与车架中心基准面垂直,其公差值为1.2㎜。
六、检验规则1、批次确定:以每交货批为一批次。
2、进厂验收项目按产品标准QB1880-2008中7.3条规定执行。
3、进厂验收检验项目按GB/T2828.1-2003标准中规定的二次正常抽样方案。
检查水平为一般检查水平(I),B类接收质量限AQL=4.0,C类接收质量限AQL=6.5。
4、批质量以每百单位产品不合格品数计算。
检查项目、检查水平、不合格分类、接收质量限(AQL)见《车架质量特性检查表》。
5、需要时,进厂验收项目可以到生产厂进行验收检验。
6、进厂验收项目检验后应作好记录,质检部负责保存记录,保存期限为二年。
7、经检验合格的产品办理入库手续;检验不合格,按不合格品管理办理规定处理。
8 外观、焊接质量用目视法进行检验。
8.1、尺寸检验使用专用、通用量具进行检测。
8.2、ФXX+00.084专用量具或游标卡尺测定;8.3、其余尺寸用游标卡尺或卷尺测定。
车架质量特性检查表。
车架检验规范(轻型电动车)
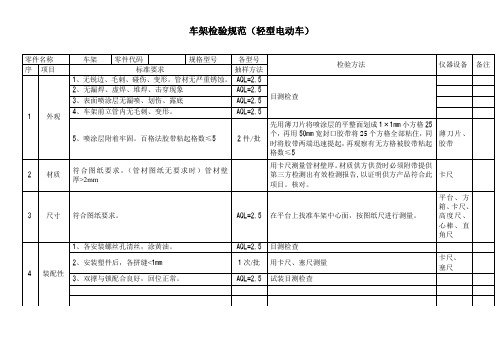
3
尺寸
符合图纸要求。
AQL=2.5
在平台上找准车架中心面,按图纸尺进行测量。
平台、方箱、卡尺、高度尺、心棒、直角尺
4
装配性
1、各安装螺丝孔清丝,涂黄油。
AQL=2.5
目测检查
2、安装塑件后,各拼缝<1mm
1次/批
用卡尺、塞尺测量
卡尺、
塞尺
3、双撑与锁配合良好,回位正常。
AQL=2.5
试装目测检查
平台、卡尺、高度尺、心棒、直角尺
编制/日期
校对/日期
标准化/日期
审核/日期
批准/日期
5、喷涂层附着牢固。百格法胶带粘起格数≤5
2件/批
先用薄刀片将喷涂层的平整面划成1×1mm小方格25个,再用50mm宽封口胶带将25个方格全部粘住,同时将胶带两端迅速提起,再观察有无方格被胶带粘起格数≤5
薄刀片、胶带
2
材质
符合图纸要求,(管材图纸无要求时)管材壁厚>2mm
用卡尺测量管材壁厚。材质供方供货时必须附带提供第三方检测出有效检测报告,以证明供方产品符合此项目。核对。
车架检验规范(轻型电动车)
零件名称
车架
检验方法
仪器设备
备注
序
项目
标准要求
抽样方法
1
外观
1、无锐边、毛刺、碰伤、变形。管材无严重锈蚀。
AQL=2.5
目测检查
2、无漏焊、虚焊、堆焊、击穿现象
AQL=2.5
3、表面喷涂层无漏喷、划伤、露底
AQL=2.5
4、车架前立管内无毛刺、变形。
AQL=2.5
零件名称
车架
零件代码
规格型号
各型号
- 1、下载文档前请自行甄别文档内容的完整性,平台不提供额外的编辑、内容补充、找答案等附加服务。
- 2、"仅部分预览"的文档,不可在线预览部分如存在完整性等问题,可反馈申请退款(可完整预览的文档不适用该条件!)。
- 3、如文档侵犯您的权益,请联系客服反馈,我们会尽快为您处理(人工客服工作时间:9:00-18:30)。
XD-JY01-005
零部件名称:车架总成 零部件型号: 版本号 重要度 GT口 ZT 口 YT 检验频次 抽样方案 □ GT口 ZT ■ YT口 按批检验 GT口 ZT ■ YT口 按批检验 GT口 ZT 口 YT■ V1.0
项目名称 表格核对单 送货单品名规格与实物一致 重量 ±1%
技术要求
检测设备 目 测 电子称 目 测
备注 入厂验收 入厂验收
材料外观质量:无裂纹、凹坑、皱痕、碰伤、拉痕、锈蚀等缺陷 烤漆质量:涂层光滑、平整、色泽均匀、结合牢固,无划伤、流痕、露底 、锈蚀等缺陷; 外观 焊接要求:焊缝应平整均匀,连结处应圆滑过渡,无咬边、凹陷、无漏焊 、虚焊、夹渣、裂纹、气孔及飞溅物等缺陷; 车头管、主梁管、侧支架连接板、左边管等部位焊接时,起焊和终焊点应 在零件焊缝长度长度延伸5mm-10mm; 表面处理:黑色电泳,车架号处涂抹金油 同轴度 尺寸 立管的上下装方向轴承处的同轴度误差不大于0.1 见附件,其它未注尺寸按封样
主要部件厚度 车架前立管厚度2.5 +0.2 主梁管厚度2.0,主梁管加强板厚度不低于2.0mm. 振动试验 平叉与车架组合震动,配重状态为,车头管方向柱部位10kg, 座垫处 100kg,电池处30 kg,脚踏处60 kg在振动频率8Hz, 加速度1.8~2g,振动 30万次,无断裂、变形现象 前立管钢管20﹟无缝: C:0.17-0.23、Si:0.17-0.37、Mn:0.35-0.65、Cr: ≤0.25、Ni≤0.30、Cu≤0.25。 主梁管、左/右边管Q195:C: ≤0.12 ; Mn: ≤0.50; Si:≤0.30ห้องสมุดไป่ตู้S: ≤0.040;P:≤0.035。 覆层附着力 车架精度 “划格法”,附着力不低于1级:1mm间距在切口交叉处涂层有少许薄片分 离,划格区受影响明显不大于5%。 后衣架、电源锁支架:X、Y、Z三个方向按±1mm;塑件装配孔X、Y、Z三个 方向按±1.2mm;其余非关重部位X、Y、Z三个方向按±1.5mm;
目 测
GT口 ZT 口 YT■ 安批检验 依据 物料 检验 抽样 计划 入厂验收
目 测
GT■ ZT 口 YT口
游标卡尺 目 测 综合检具
GT■ ZT 口 YT口 GT口 ZT 口 YT■ GT■ ZT 口 YT口 按批检验 GT口 ZT ■ YT口 按批检验
入厂验收 入厂验收
周期和型式检验项目(目前可以根据公司检测能力来选择,必要时要予以委外。) 项目名称 试验内容及要求: 检测设备 重要度 试验频次 抽样方案 GT口 ZT□ YT口 次/3月 次/1月 次/1月 次/1月 次/1月 1件 1件 1件 1件 1件 备注 入厂验收 入厂验收 入厂验收 入厂验收 入厂验收
GT■ ZT口 YT口 理化分析仪 GT■ ZT口 YT口 胶带、划格器 GT口 三坐标 GT口 ZT■YT口 ZT■YT口
次/6月
1件
提供/委外
材质
次/6月 次/批 次/3月
1件 1件 1件
提供/委外 入厂验收 入厂验收
焊接熔深: 焊接熔深:剖切检查平叉头管与方管、后减震支耳、熔深不小于管壁的1/3 切割机、卡尺 GT■ ZT口 YT口 覆层硬度: 覆层性能 漆膜硬度:用2H铅笔在试样漆膜表面成45°,以3mm/s的速度,受力均匀地 H铅笔、橡皮 GT口 ZT口 YT■ 在不同部位往返划痕5次,然后用橡皮揩去石墨灰,不许划穿漆膜。 中性盐雾试验72h(NSS),无腐蚀生成物、起泡及脱落现象;耐油性:5小 盐雾试验箱 GT口 ZT口 YT■ 时无变化(汽油),耐水性:72小时无变化(50°) 游标卡尺 振动试验台 GT口 ZT口 YT■ GT■ ZT口 YT口